- 1School of Martials Science and Engineering, Changchun University of Science and Technology, Changchun, China
- 2Key Laboratory of Polymer Physics and Chemistry, Changchun Institute of Applied Chemistry, Chinese Academy of Sciences, Changchun, China
- 3Nanomaterials Physicochemistry Department, Faculty of Chemical Technology and Engineering, West Pomeranian University of Technology, Szczecin, Poland
Poly(butylene succinate) is one of the most promising biodegradable polymers, but its applications are limited by poor flame retardancy. In this work, poly(butylene succinate)/diethylphosphinate (PBS/AlPi) composites were fabricated to investigate the effect of AlPi on their thermal stability, flame retardancy, and mechanical properties. It was found that the high content of AlPi decreased the thermal stability of PBS, and the decrease became stronger under the air atmosphere. When the content of AlPi reached 25wt%, the flame retardancy was improved with limited oxygen index (LOI) of 29.5%, V0 rating in UL-94 vertical burning test, and 49.3% reduction on the peak of heat release rate (PHRR) in cone calorimeter test. Meanwhile, the addition of AlPi could improve the mechanical properties of PBS with high tensile strength and Young’s modulus, which was ascribed to the compatible effect of maleic anhydride-grafted poly(butylene succinate) (PBS-g-MA) with good filler dispersion and strong matrix-particles interaction. Thus, the AlPi was an effective flame retardant to PBS, so that PBS/AlPi composites displayed excellent flame retardancy without seriously sacrificing other comprehensive performances.
Introduction
In the last decade, biodegradable polymers have drawn particular attention due to their advantages of biodegradability, good mechanical properties, easy processing, and chemical resistance (Chen et al., 2017; Chen Y. et al., 2019; Delamarche et al., 2020; He W. et al., 2020; Li et al., 2018; Xiong et al., 2019; Xu et al., 2019; Yang et al., 2020; Zhang et al., 2021; Zhang et al., 2020). As a typical representative, poly(butylene succinate) (PBS) has wide applications in the fields of biomedical materials, transport, construction, electrical industry, and packing materials (Bahrami et al., 2021; Hu et al., 2019; Li et al., 2020; Xue et al., 2019; Zhao et al., 2020). Unfortunately, PBS is flammable as common thermoplastics (Liu et al., 2016; Chen H. et al., 2019; Gu et al., 2019; Hu et al., 2019; He L. et al., 2020), which greatly limits its application in some special fields with high flame retardancy requirements. Therefore, it is an urgent task to improve the flame retardancy of PBS to meet various applications.
To improve the flame retardancy of PBS, an easy and convenient way is to directly add flame retardants for preparing PBS composites (Wang et al., 2019; Yue et al., 2021) because it could meet the current machining technology for continuous production on a large scale. As typical flame retardants, ammonium polyphosphate (APP) and Mg(OH)2 have been used in the PBS system. Hu et al. (Hu et al., 2020) have reported that when 30 wt% APP was added to PBS, the peak of heat release rate (PHRR) and total heat release (THR) decreased by 19 and 25%, respectively. Our previous work (Chen et al., 2016) has also confirmed that the least amount of Mg(OH)2 was 40wt% in the PBS system to reach the V0 rating in the UL-94 vertical burning test. These results indicated that both of them are not high-efficiency flame retardants for PBS. Meanwhile, the processability and mechanical properties of the PBS matrix were seriously deteriorated due to the high addition amount of flame retardants. Consequently, it is still a challenge to improve the flame retardancy of PBS without seriously sacrificing other comprehensive performances.
Dialkylphosphinate salt belongs to a new class of additive-type phosphorus-containing flame retardants (Hou et al., 2021; Liu et al., 2014; Wang et al., 2015). The most important advantage of these salts is their high phosphorus content. Furthermore, they are environmentally friendly flame retardants because no harmful and toxic substances are released during combustion. Especially, aluminum diethylphosphinate (AlPi) is one of the most commonly used dialkylphosphinate salts, which has been widely added to improve the flame retardancy of polyethylene (PE), polyamide 6 (PA6), polyurethane (PU), polybutylece terephthalate (PBT), and epoxy resin (EP) (Ma et al., 2019; Oliwa et al., 2020; Pan et al., 2020; Hu et al., 2021; Liu et al., 2021). It is acceptant that AlPi can not only play a flame retardant role in the condensed phase to promote the formation of polymer carbon but also remove high energy active free radicals in the combustion zone (Liu et al., 2021). However, to the best of our knowledge, the application of AlPi on biodegradable polymer systems was rarely reported.
In this study, AlPi was employed to modify biodegradable PBS, and maleic anhydride-grafted poly(butylene succinate) (PBS-g-MA) was used as their compatibilizer (Chen et al., 2015). The current research aimed to investigate the effect of AlPi on thermal stability, flame retardancy and mechanical properties of PBS composites. The thermal stability was investigated by thermogravimetric analysis (TGA) in nitrogen and air atmospheres, respectively. Furthermore, flame retardancy was evaluated by LOI, Ul-94, and cone calorimeter tests. Meanwhile, the flame retardant mechanism was discussed by analyzing the action of AlPi on the gas phase and condensed phase. Finally, their mechanical properties were studied by tensile and impact tests.
Experimental Section
Materials
PBS (trade name GS PLA, Japan) was bought from Mitsubishi Chemical Corp. (Toyota, Japan). The melt flow index was 4.5 g/10 min at 190°C under 2.16 kg of weight. Aluminum diethylphosphinate (AlPi) was provided by Qingdao Fuslin Chemical Technology Co., Ltd. Maleic anhydride-grafted poly(butylene succinate) (PBS-g-MA) was synthesized via reactive melt-grafting process according to previous literature (Phua et al., 2013b). The ratio of PBS, maleic anhydride, and dicumyl peroxide (DCP) was 100/10/1.5 by weight, and the grafting degree of MA onto PBS (Gd) was 4.2 wt%.
Preparation of PBS/AlPi Composites
PBS/AlPi composites were prepared by melt compounding in a HAAKE batch intensive mixer (HAAKE Rheomix 600, Karlsruhe, Germany) at 135°C with a rotor speed of 80 rpm; the mixing time was 6 min for each sample. The content of PBS-g-MA (as a compatibilizer) was kept as 15 wt% in all PBS composites, and the content of AlPi was changed from 5 to 25 wt%. For convenience, the obtained samples were designated as PBSxAlPi. Here, x denotes the weight percentage of AlPi in the PBS composites.
Characterization
Thermogravimetric analysis (TGA) was performed on a TA STD Q600 thermal analyzer. The PBS samples with mass 8.0 ± 0.2 mg were heated from room temperature to 600°C at 10°C min−1 under nitrogen and air atmosphere, respectively. The limited oxygen index (LOI) was tested on a JF-3 oxygen index meter (Jiangning, China) with sheet dimensions of 130 × 6.5 × 3.2 mm3, according to ISO4589-1984. The vertical burning testing was carried out according to the UL-94 (ANSI/ASTMD635-77) with sheet dimensions of 125 × 12.7 × 3.2 mm3. Cone calorimeter testing (icone, FTT, United Kingdom) was conducted according to ISO 5660-1. The sample dimension was 100 × 100 × 6 mm3; it was backed by aluminum foil and irradiated at a heat flux of 50 kW m−2. The photographs of residual chars after cone calorimeter testing were collected by a digital camera. The dispersion of AlPi in PBS matrix was examined with the scanning electron microscope (XL30 FESEM FEG, FEI Co.). The samples were fractured in liquid nitrogen, and the fracture surfaces were coated with gold before SEM observation. Uniaxial tensile tests were performed at room temperature with an Instron 1,121 testing machine (Canton, MA). Specimens were compression-molded into sheets with 1 mm thickness, then cut into a dumbbell shape with gauge dimensions of 20 mm × 4 mm × 1 mm. The measurements were conducted at a crosshead speed of 20 mm min−1. At least five runs for each sample were measured and averaged.
Results and Discussion
Thermal Stability of PBS/AlPi Composites
The influence of AlPi on the thermal stability of PBS under nitrogen was investigated by TGA, which reflects the thermal degradation behavior of materials with the increase of temperature (Wang et al., 2020b; Xu D. et al., 2021). As shown in Figure 1A, with the increase of AlPi content, the TGA curves slowly shifted to a low-temperature range. The temperatures corresponding to 5 and 10 wt% weight loss (T5wt% and T10wt%) are essential to evaluate the thermal decomposition of polymers on the onset stage. For PBS5AlPi, T5wt% and T10wt% decreased less than 1°C in comparison with that of neat PBS, indicating that the addition of AlPi with low content has a small impact on the thermal stability of PBS. However, the reduction in thermal stability gradually became larger with high content fillers (Table 1). For example, T5wt% and T10wt% of PBS25AlPi decreased to 15.8 and 14.9°C, respectively. Meanwhile, with the increase of the AlPi loading, Figure 1B exhibited a gradual decrease for Tmax1, corresponding to the maximum weight loss rate of the polymer. Herein, the decrease on T5wt%, T10wt%, and Tmax1 was ascribed to the thermal degradation of PBS during melt compounding because the increase in viscosity with high content of inorganic fillers could result in the sharp rise of temperature under high shear force, promoting the thermal degradation polymer (Fong et al., 2021). In addition, another characteristic peak was present at approximately 472°C (denoted as Tmax2 in Table 1), which should be assigned to the thermal decomposition of AlPi.
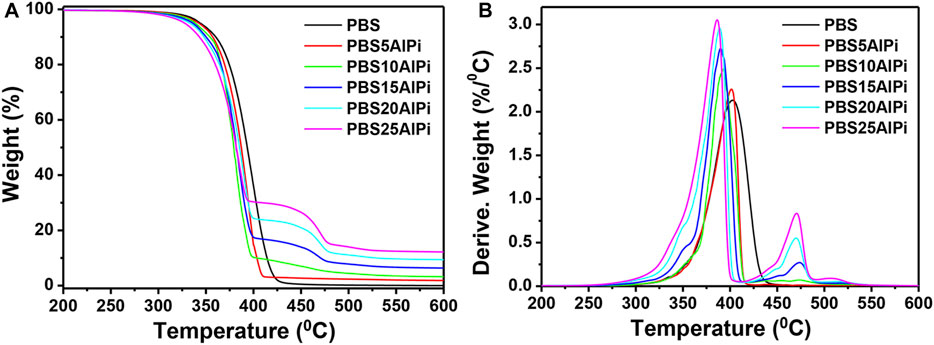
FIGURE 1. TGA (A) and DTG (B) curves of neat PBS and PBS/AlPi composites in nitrogen at 10°C min−1 heating rate.
The thermal stability of PBS/AlPi composites under air was also evaluated, which is more important because the melt processing of polymer materials is usually performed in an air atmosphere. As shown in Figure 2A and Table 2, T5wt%,T10wt%, and Tmax1 exhibited a similar trend to the situation of nitrogen, but the values were relatively smaller owing to the oxidation degradation (Wen et al., 2011). Furthermore, as shown in Figure 2B, Tmax2 appeared at approximately 427°C (45°C lower than that in nitrogen), and the intensity of peaks became much weaker. It is suggested that part of AlPi gradually degraded before Tmax2, which is accompanied by the degradation of PBS chains. Based on these results, the content of AlPi could influence the thermal stability of PBS/AlPi composites, and the decrease in thermal stability became stronger under air atmosphere at higher AlPi loadings.
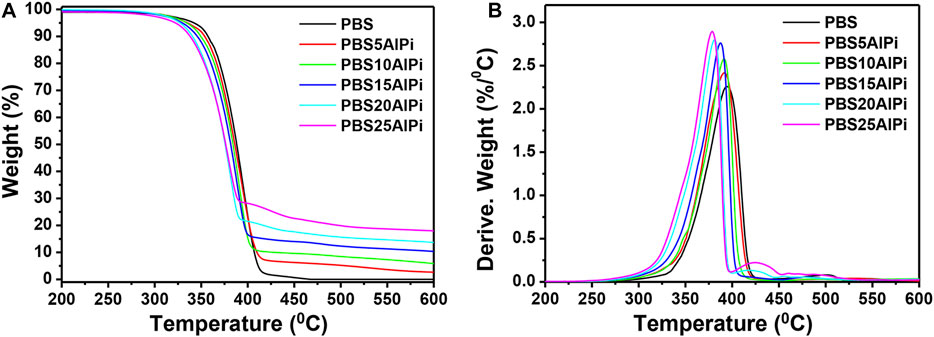
FIGURE 2. TGA (A) and DTG (B) curves of neat PBS and PBS/AlPi composites in air at 10°C min−1 heating rate.
Flammability Properties of PBS Composites
The effect of AlPi on the flame retardancy of PBS matrix was investigated by LOI and UL-94 tests. As listed in Table 3, the LOI values gradually increased with the addition of AlPi content, of which the highest value corresponding to PBS25AlPi could achieve 29.5. Moreover, only when the content of AlPi was 20wt%, the UL-94 rating reached V1. With further increasing the AlPi to 25wt%, the UL-94 rating could pass V0. Besides the flame retardant effect, AlPi displayed a positive effect on the inhibition of dripping. For all PBS/AlPi composites, there was no melt dripping, indicating that AlPi was an effective dropping inhibitor for PBS matrix.
Further, the flame retardancy of PBS/AlPi composites was investigated by cone calorimeter testing, which is useful to provide various important information about fire risk during combustion (Zanetti et al., 2002; Wang et al., 2020a; Xue et al., 2020b; Xu et al., 2020), such as time to ignition (TTI), heat and smoke release, and mass loss. First, heat release rates (HRR) and combustion time curves for PBS samples are shown in Figure 3A, and detailed parameters are listed in Table 3. With the increase of AlPi loading in the PBS system, the ignition time (tign) became shorter, implying that the PBS/AlPi composites were easier to be ignited than neat PBS. However, a gradual decrease for the peaks of HRR (PHRRs) was present. For instance, the PHRR for PBS25AlPi was reduced to 388 kW/m2, which was reduced by 49.3% compared to that for neat PBS (765 kW m−2). Further, Figure 3B shows the curves of total heat release (THR). It is significant that the slope flattened out at the latter half of combustion time, and the final THR value became smaller to a certain extent. These results suggest that AlPi is an effective flame retardant for reducing PHRR and THR.
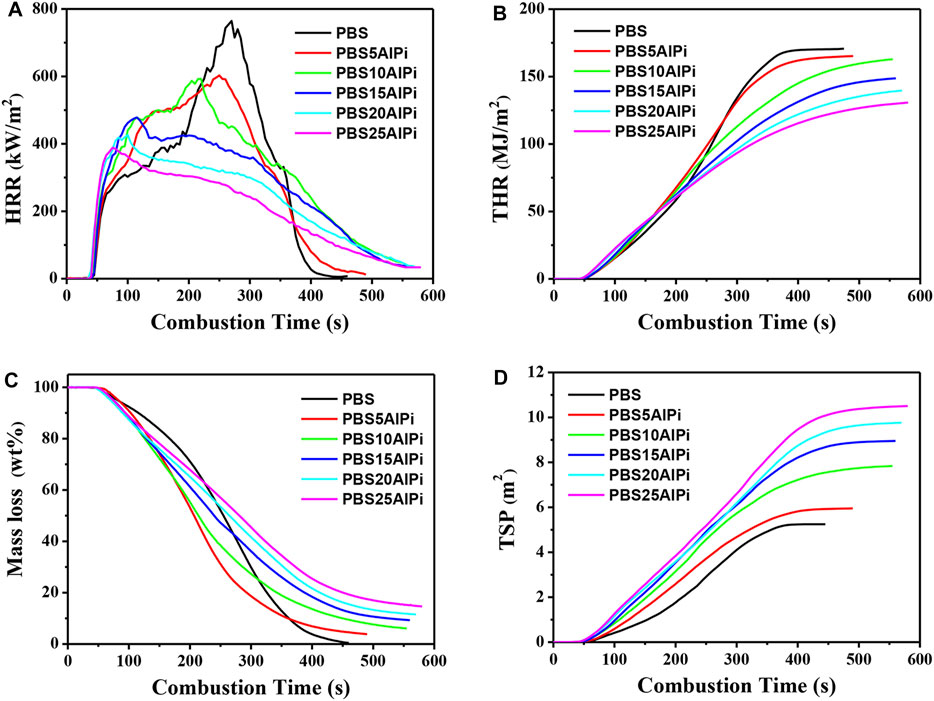
FIGURE 3. PBS samples measured by cone calorimeter test at an external radiant flux of 50 kW m−2: (A) heat release rate curves (HRR); (B) total heat release curves (THR); (C) mass loss curves (ML); (D) total smoke production curves (TSP).
Figure 3C shows the normalized mass loss (ML) curves of PBS samples with combustion time. All PBS/AlPi composites exhibited similar curves, but the slope became smaller with more AlPi fillers, indicating that AlPi as flame retardant could delay the combustion of PBS. Meanwhile, the residual char gradually increased with the increase of AlPi content. Furthermore, the total smoke production (TSP) was evaluated. As shown in Figure 3D, the TSP increased with the addition of AlPi (detailed data are listed in Table 3). The increase in TSP should be related to the radical trapping effect in the gas phase. The decomposition of AlPi could produce P• and PO• radicals (Tang et al., 2020), which could quench H• and HO• radicals so that some derived products were generated as smoke particles.
Besides the trapping radicals in the gas phase, AlPi also contributed to the condensed phase through char formation. As shown in Figure 4A, neat PBS was typical no-char polymers (burned completely without residual char). With the increase of AlPi concentration, the char amount increased and the carbon layer became thicker. It is clear that the cracks gradually became smaller until they disappeared (Figures 4B–F). To further evaluate the microstructure, SEM observation was carried out for the char from PBS25AlPi. Interestingly, the char morphologies from the outer surface and inner surface were different. As shown in Figures 5A,B, the outer surface was covered by flocculent porous carbon, which may come from the deposition of P•/PO•-derived solid products. However, the inner surface was compact and cohesive with high supporting strength (Figures 5C,D). It was a whole bulk with some cavities, which may result from the release of flammable gases into the gas phase zone.
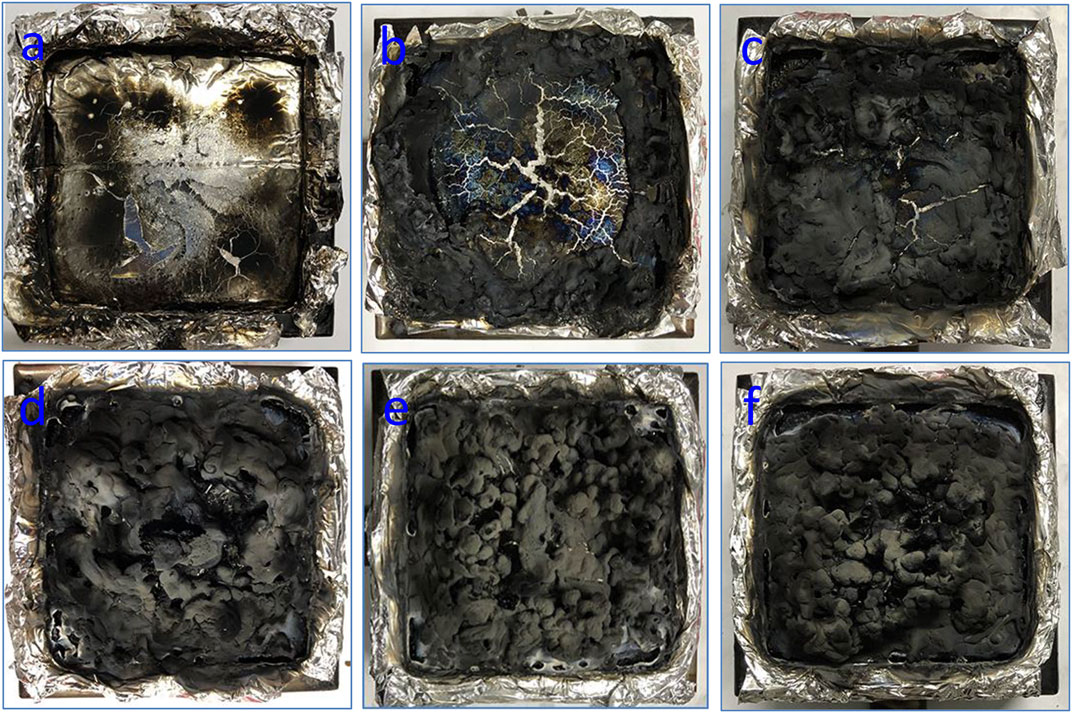
FIGURE 4. Photographs of the residues after the cone calorimeter test from (A) neat PBS, (B) PBS5AlPi, (C) PBS10AlPi, (D) PBS15AlPi, (E) PBS20AlPi, and (F) PBS25AlPi.
Based on the above analysis, a possible enhancement mechanism of AlPi in the PBS system was proposed in Figure 6. It is reported that AlPi could be thermally decomposed to oligomers of phosphinates, diethylphosphinic acid, and aluminum phosphate (Kaya and Hacaloglu, 2014; Vothi et al., 2020). On the one hand, oligomers of phosphinates and diethylphosphinic acid can further be decomposed to P• and PO• radicals in the gas phase, which could quench H• and HO• radicals in the combustion zone, and some derived solid products were generated as the char of outer layer. On the other hand, aluminum phosphate could construct continuous and compact char as the inner layer. The combined char layer can effectively reduce the heat and mass transfer rate and protect the underlying material from burning (Xu Y.-J. et al., 2021). As a result, the improvements on flame retardancy with LOI of 29.5%, V0 in UL-94, and 49.3% reduction on PHRR were presented. In brief, the enhanced flame retardancy of PBS was attributed to the gas–solid flame retardancy mechanism of AlPi.
Mechanical Properties of PBS Composites
The effect of AlPi on the mechanical properties of PBS was investigated by tensile testing. Figure 7 shows the stress-strain curves of neat PBS and PBS/AlPi composites. The detailed data for Young’s modulus, tensile strength, and elongation at break are listed in Table 4. With the increase of AlPi loading, Young’s modulus gradually increased due to the reinforcing effect of AlPi as rigid inorganic particles. The tensile strength firstly increased and then decreased with the increase of AlPi content. For PBS15AlPi, it exhibited the highest value of tensile strength of 35.8 MPa. However, the tensile strengths for all PBS composites were higher than that of neat PBS, which should be ascribed to good compatibility between PBS matrix and AlPi particles. In addition, the elongation at break showed a decreased trend with the addition of AlPi loading, indicating a decreased ductility of the PBS matrix. Similarly, the impact strengths of PBS composites also decreased gradually with the increase of AlPi content (Table 4).
In polymer/filler composites, the dispersion of fillers and interfacial interaction between two components are the most important factors to determine the final mechanical properties (Sun et al., 2017; Wen et al., 2020b; Xue et al., 2020a; Yang et al., 2019). As shown in Figures 8A–F, the fracture surface morphologies of PBS samples were investigated by SEM. It was apparent that AlPi particles were uniformly distributed in the PBS matrix, and no big aggregates were detected. Further, AlPi particles were firmly adhered to the PBS matrix, indicating their strong interfacial interaction (Wen et al., 2020a; Wen et al., 2012). Even for PBS25AlPi with the highest AlPi content, most AlPi particles still exhibited good dispersion without big aggregates, and no debonding cavities were present (blue circles in Figure 8F). In our PBS/AlPi system, 15 wt% PBS-g-MA was added as a compatibilizer, which was helpful to improve the dispersion of fillers and the matrix-particles interaction (Phua et al., 2013a; Chen et al., 2015). As a result, our PBS/AlPi composites exhibited good mechanical properties with high tensile strength and Young’s modulus.
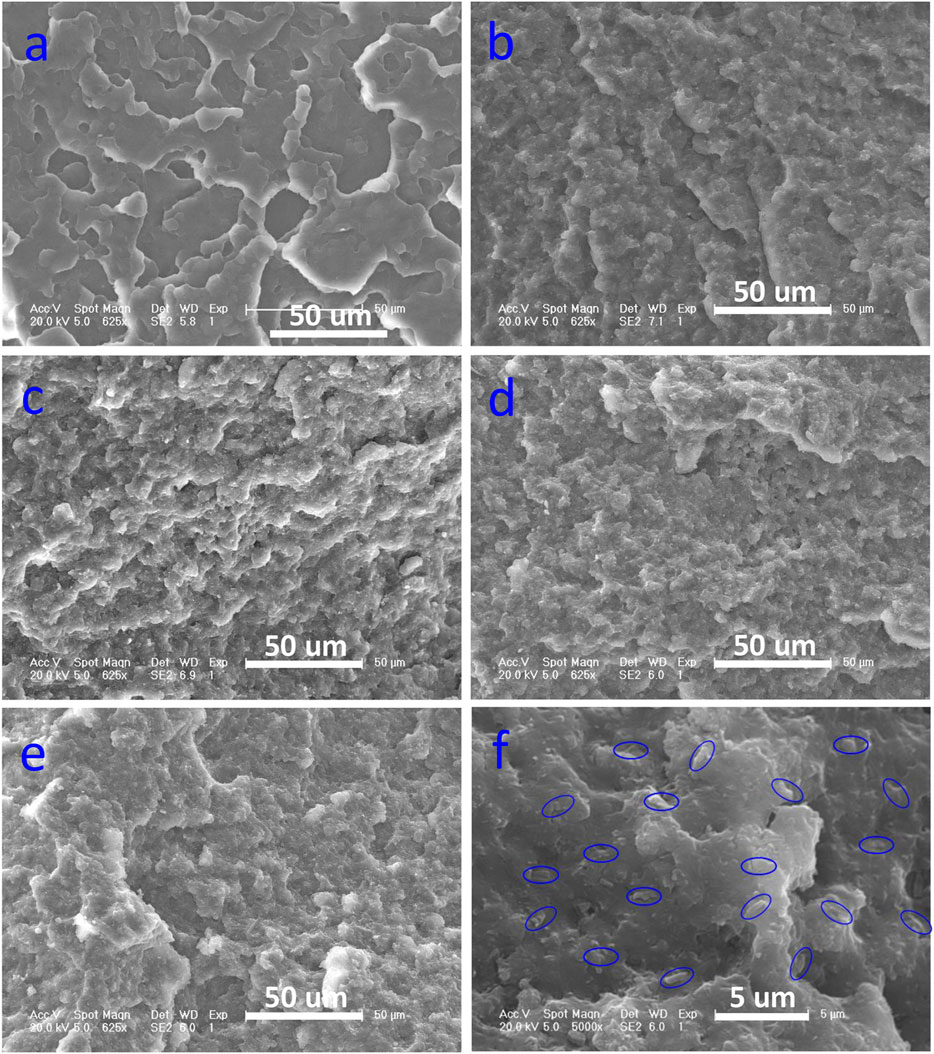
FIGURE 8. SEM micrographs of the brittle-fractured surface of PBS samples: (A) neat PBS, (B) PBS5AlPi, (C) PBS10AlPi, (D) PBS15AlPi, (E) PBS20AlPi, and (F) PBS25AlPi.
Conclusion
PBS/AlPi composites were prepared by melt compounding with PBS-g-MA as a compatibilizer, and the effect of AlPi content on thermal stability, flame retardancy, and mechanical properties was investigated. The TGA results indicated high content of AlPi decreased the thermal stability of PBS, and the decrease became stronger under air atmosphere. Further, the flame retardancy of PBS/AlPi composites was also determined by the AlPi content. For PBS25AlPi, the improved flame retardancy with LOI of 29.5%, V0 rating in UL-94 test, and 49.3% reduction on PHRR was presented. The enhancement was attributed to the gas–solid flame retardancy mechanism of AlPi. In addition, the PBS/AlPi composites displayed good mechanical properties with high tensile strength and Young’s modulus, which was contributed to the compatible effect of PBS-g-MA. This work indicates that AlPi was an effective flame retardant to PBS, but more work is still necessary to decrease the amount of AlPi addition and further balance the comprehensive performances of PBS composites.
Data Availability Statement
The original contributions presented in the study are included in the article/supplementary files; further inquiries can be directed to the corresponding authors.
Author Contributions
YW executed the experiment and wrote the manuscript. DJ, XW, and TT conceived and designed the experiment plan. KaS, KS, KW, and EM revised the manuscript and analyzed the experimental results.
Funding
This work is supported by the National Science Centre Poland OPUS UMO-2018/29/B/ST8/01265 and the National Natural Science Foundation of China (Grants Nos. 51991353 and 51773202).
Conflict of Interest
The authors declare that the research was conducted in the absence of any commercial or financial relationships that could be construed as a potential conflict of interest.
Publisher’s Note
All claims expressed in this article are solely those of the authors and do not necessarily represent those of their affiliated organizations, or those of the publisher, the editors and the reviewers. Any product that may be evaluated in this article, or claim that may be made by its manufacturer, is not guaranteed or endorsed by the publisher.
References
Bahrami, M., Enciso, B., Gaifami, C. M., Abenojar, J., and Martinez, M. A. (2021). Characterization of Hybrid Biocomposite Poly-Butyl-Succinate/Carbon fibers/Flax Fibers. Composites B-Engineering 221, 109030. doi:10.1016/j.compositesb.2021.109033
Chen, H., Wang, T., Wen, Y., Wen, X., Gao, D., Yu, R., et al. (2019a). Expanded Graphite Assistant Construction of Gradient-Structured Char Layer in PBS/Mg(OH)2 Composites for Improving Flame Retardancy, thermal Stability and Mechanical Properties. Composites B: Eng. 177, 107402. doi:10.1016/j.compositesb.2019.107402
Chen, H., Wen, X., Guan, Y., Min, J., Wen, Y., Yang, H., et al. (2016). Effect of Particle Size on the Flame Retardancy of Poly(butylene succinate)/Mg(OH)2 Composites. Fire Mater. 40 (8), 1090–1096. doi:10.1002/fam.2355
Chen, Q., Wen, X., Chen, H., Qi, Y., Gong, J., Yang, H., et al. (2015). Study of the Effect of Nanosized Carbon Black on Flammability and Mechanical Properties of Poly(butylene Succinate). Polym. Adv. Technol. 26 (2), 128–135. doi:10.1002/pat.3431
Chen, Y., Wang, W., Qiu, Y., Li, L., Qian, L., and Xin, F. (2017). Terminal Group Effects of Phosphazene-Triazine Bi-group Flame Retardant Additives in Flame Retardant Polylactic Acid Composites. Polym. Degrad. Stab. 140, 166–175. doi:10.1016/j.polymdegradstab.2017.04.024
Chen, Y., Xu, L., Wu, X., and Xu, B. (2019b). The Influence of Nano ZnO Coated by Phosphazene/triazine Bi-group Molecular on the Flame Retardant Property and Mechanical Property of Intumescent Flame Retardant Poly (Lactic Acid) Composites. Thermochim. Acta 679, 178336. doi:10.1016/j.tca.2019.178336
Delamarche, E., Mattlet, A., Livi, S., Gerard, J. F., Bayard, R., and Massardier, V. (2020). Tailoring Biodegradability of Poly(butylene Succinate)/poly(lactic Acid) Blends with a Deep Eutectic Solvent. Front. Mater. 7, 7. doi:10.3389/fmats.2020.00007
Fong, M. K., Rahman, M. N. A., Arifin, A. M. T., Haq, R. H. A., Hassan, M. F., and Taib, I. (2021). Characterization, Thermal and Biological Properties of PCL/PLA/PEG/N-HA Composites. Biointerface Res. Appl. Chem. 11 (2), 9017–9026.
Gu, L., Zhang, S., Li, H., Sun, J., Tang, W., Zhao, L., et al. (2019). Preparation of Intumescent Flame Retardant Poly(butylene Succinate) Using Urea Intercalated Kaolinite as Synergistic Agent. Fibers Polym. 20 (8), 1631–1640. doi:10.1007/s12221-019-7999-8
He, L., Shi, Y., Wang, Q., Chen, D., Shen, J., and Guo, S. (2020a). Strategy for Constructing Electromagnetic Interference Shielding and Flame Retarding Synergistic Network in Poly (Butylene Succinate) and Thermoplastic Polyurethane Multilayered Composites. Composites Sci. Tech. 199, 108324. doi:10.1016/j.compscitech.2020.108324
He, W., Song, P., Yu, B., Fang, Z., and Wang, H. (2020b). Flame Retardant Polymeric Nanocomposites through the Combination of Nanomaterials and Conventional Flame Retardants. Prog. Mater. Sci. 114, 100687. doi:10.1016/j.pmatsci.2020.100687
Hou, Y., Xu, Z., Chu, F., Gui, Z., Song, L., Hu, Y., et al. (2021). A Review on Metal-Organic Hybrids as Flame Retardants for Enhancing Fire Safety of Polymer Composites. Composites Part B: Eng. 221, 109014. doi:10.1016/j.compositesb.2021.109014
Hu, C., Bourbigot, S., Delaunay, T., Collinet, M., Marcille, S., and Fontaine, G. (2020). Poly(isosorbide Carbonate): A 'green' Char Forming Agent in Polybutylene Succinate Intumescent Formulation. Composites Part B: Eng. 184, 107675. doi:10.1016/j.compositesb.2019.107675
Hu, C., Bourbigot, S., Delaunay, T., Collinet, M., Marcille, S., and Fontaine, G. (2019). Synthesis of Isosorbide Based Flame Retardants: Application for Polybutylene Succinate. Polym. Degrad. Stab. 164, 9–17. doi:10.1016/j.polymdegradstab.2019.03.016
Hu, Y. X., Zhou, Z. J., Li, S. S., Yang, D., Zhang, S., and Hou, Y. K. (2021). Flame Retarded Rigid Polyurethane Foams Composites Modified by Aluminum Diethylphosphinate and Expanded Graphite. Front. Mater. 7, 629284. doi:10.3389/fmats.2020.629284
Kaya, H., and Hacaloglu, J. (2014). Thermal Degradation of Polylactide/aluminium Diethylphosphinate. J. Anal. Appl. Pyrolysis 110, 155–162. doi:10.1016/j.jaap.2014.08.015
Li, L., Mao, X., Ju, R., Chen, Y., and Qian, L. (2018). Synergistic Effect of Organo-Montmorillonite on Intumescent Flame-Retardant PLA. Ferroelectrics 527 (1), 25–36. doi:10.1080/00150193.2018.1450045
Li, X., Fu, Z., Gu, X., Liu, H., Wang, H., and Li, Y. (2020). Interfacially Located Nanoparticles: Barren Nanorods versus Polymer Grafted Nanorods. Composites Part B: Eng. 198, 108153. doi:10.1016/j.compositesb.2020.108153
Liu, B., Xu, J. C., Xue, H. L., Shu, Z. J., Xu, G. G., Ou, H. X., et al. (2021). Preparation and Properties of Modified Aluminum Diethylphosphinate Flame Retardant for Low-Density Polyethylene. J. Appl. Polym. Sci. 138 (19), e50393. doi:10.1002/app.50393
Liu, J., Chen, J., Liu, X., Sun, S., and Cai, S. (2014). Synthesis of Aluminum Methylcyclohexylphosphinate and its Use as Flame Retardant for Epoxy Resin. Fire Mater. 38 (2), 155–165. doi:10.1002/fam.2169
Liu, L., Huang, G., Song, P., Yu, Y., and Fu, S. (2016). Converting Industrial Alkali Lignin to Biobased Functional Additives for Improving Fire Behavior and Smoke Suppression of Polybutylene Succinate. ACS Sust. Chem. Eng. 4 (9), 4732–4742. doi:10.1021/acssuschemeng.6b00955
Ma, C., Wang, J., Yuan, Y., Mu, X., Pan, Y., Song, L., et al. (2019). An Insight into Gas Phase Flame Retardant Mechanisms of AHP versus AlPi in PBT: Online Pyrolysis Vacuum Ultraviolet Photoionization Time-Of-Flight Mass Spectrometry. Combustion and Flame 209, 467–477. doi:10.1016/j.combustflame.2019.08.020
Oliwa, R., Bulanda, K., Oleksy, M., Ostynska, P., Budzik, G., Plocinska, M., et al. (2020). Fire Resistance and Mechanical Properties of Powder-Epoxy Composites Reinforced with Recycled Glass Fiber Laminate. Polimery 65 (4), 280–288. doi:10.14314/polimery.2020.4.4
Pan, Y., Song, L., Wang, W. M., and Zhao, H. T. (2020). Polydimethylsiloxane Wrapped Aluminum Diethylphosphinate for Enhancing the Flame Retardancy of Polyamide 6. J. Appl. Polym. Sci. 137 (35), e49027. doi:10.1002/app.49027
Phua, Y. J., Chow, W. S., and Mohd Ishak, Z. A. (2013a). Organomodification of Montmorillonite and its Effects on the Properties of Poly(butylene Succinate) Nanocomposites. Polym. Eng. Sci. 53 (9), 1947–1957. doi:10.1002/pen.23460
Phua, Y. J., Chow, W. S., and Mohd Ishak, Z. A. (2013b). Reactive Processing of Maleic Anhydride-Grafted Poly(butylene Succinate) and the Compatibilizing Effect on Poly(butylene Succinate) Nanocomposites. Express Polym. Lett. 7 (4), 340–354. doi:10.3144/expresspolymlett.2013.31
Sun, Y., Sun, S., Chen, L., Liu, L., Song, P., Li, W., et al. (2017). Flame Retardant and Mechanically Tough Poly(lactic Acid) Biocomposites via Combining Ammonia Polyphosphate and Polyethylene Glycol. Composites Commun. 6, 1–5. doi:10.1016/j.coco.2017.07.005
Tang, G., Zhou, L., Zhang, P., Han, Z., Chen, D., Liu, X., et al. (2020). Effect of Aluminum Diethylphosphinate on Flame Retardant and thermal Properties of Rigid Polyurethane Foam Composites. J. Therm. Anal. Calorim. 140 (2), 625–636. doi:10.1007/s10973-019-08897-z
Vothi, H., Nguyen, C., Pham, L. H., Kim, J., and Hoang, D. (2020). Degradation Mechanism and Flame Retardancy of Aluminum Phosphonate in Glass Fiber-Reinforced Poly(butylene Terephthalate). Polym. Bull. doi:10.1007/s00289-020-03455-2
Wang, B., Li, P., Xu, Y.-J., Jiang, Z.-M., Dong, C.-H., Liu, Y., et al. (2020a). Bio-based, Nontoxic and Flame-Retardant Cotton/alginate Blended Fibres as Filling Materials: Thermal Degradation Properties, Flammability and Flame-Retardant Mechanism. Composites Part B: Eng. 194, 108038. doi:10.1016/j.compositesb.2020.108038
Wang, B., Xu, Y.-J., Li, P., Zhang, F.-Q., Liu, Y., and Zhu, P. (2020b). Flame-retardant Polyester/cotton Blend with Phosphorus/nitrogen/silicon-Containing Nano-Coating by Layer-By-Layer Assembly. Appl. Surf. Sci. 509, 145323. doi:10.1016/j.apsusc.2020.145323
Wang, Y., Liu, C., Shi, X., Liang, J., Jia, Z., and Shi, G. (2019). Synergistic Effect of Halloysite Nanotubes on Flame Resistance of Intumescent Flame Retardant Poly(butylene Succinate) Composites. Polym. Compos. 40 (1), 202–209. doi:10.1002/pc.24629
Wang, Y., Zhang, L., Yang, Y., and Cai, X. (2015). The Investigation of Flammability, thermal Stability, Heat Resistance and Mechanical Properties of Unsaturated Polyester Resin Using AlPi as Flame Retardant. J. Therm. Anal. Calorim. 122 (3), 1331–1339. doi:10.1007/s10973-015-4875-7
Wen, X., Liu, Z., Li, Z., Zhang, J., Wang, D.-Y., Szymańska, K., et al. (2020a). Constructing Multifunctional Nanofiller with Reactive Interface in PLA/CB-g-DOPO Composites for Simultaneously Improving Flame Retardancy, Electrical Conductivity and Mechanical Properties. Composites Sci. Tech. 188, 107988. doi:10.1016/j.compscitech.2019.107988
Wen, X., Min, J., Tan, H., Gao, D., Chen, X., Szymańska, K., et al. (2020b). Reactive Construction of Catalytic Carbonization System in PP/C60/Ni(OH)2 Nanocomposites for Simultaneously Improving thermal Stability, Flame Retardancy and Mechanical Properties. Composites A: Appl. Sci. Manufacturing 129, 105722. doi:10.1016/j.compositesa.2019.105722
Wen, X., Wang, Y., Gong, J., Liu, J., Tian, N., Wang, Y., et al. (2012). Thermal and Flammability Properties of Polypropylene/carbon Black Nanocomposites. Polym. Degrad. Stab. 97 (5), 793–801. doi:10.1016/j.polymdegradstab.2012.01.031
Wen, X., Zhang, K., Wang, Y., Han, L., Han, C., Zhang, H., et al. (2011). Study of the thermal Stabilization Mechanism of Biodegradable poly(L-Lactide)/silica Nanocomposites. Polym. Int. 60 (2), 202–210. doi:10.1002/pi.2927
Xiong, Z., Zhang, Y., Du, X., Song, P., and Fang, Z. (2019). Green and Scalable Fabrication of Core-Shell Biobased Flame Retardants for Reducing Flammability of Polylactic Acid. ACS Sust. Chem. Eng. 7 (9), 8954–8963. doi:10.1021/acssuschemeng.9b01016
Xu, D., Wang, S., Hu, J., Liu, Y., Jiang, Z., and Zhu, P. (2021a). Enhancing Antibacterial and Flame-Retardant Performance of Cotton Fabric with an Iminodiacetic Acid-Containing N-Halamine. Cellulose 28 (5), 3265–3277. doi:10.1007/s10570-021-03716-x
Xu, L., Wu, X., Li, L., and Chen, Y. (2019). Synthesis of a Novel Polyphosphazene/triazine Bi‐group Flame Retardant In Situ Doping Nano Zinc Oxide and its Application in Poly (Lactic Acid) Resin. Polym. Adv. Technol. 30 (6), 1375–1385. doi:10.1002/pat.4570
Xu, X., Dai, J., Ma, Z., Liu, L., Zhang, X., Liu, H., et al. (2020). Manipulating Interphase Reactions for Mechanically Robust, Flame-Retardant and Sustainable Polylactide Biocomposites. Composites Part B: Eng. 190, 107930. doi:10.1016/j.compositesb.2020.107930
Xu, Y.-J., Qu, L.-Y., Liu, Y., and Zhu, P. (2021b). An Overview of Alginates as Flame-Retardant Materials: Pyrolysis Behaviors, Flame Retardancy, and Applications. Carbohydr. Polym. 260, 117827. doi:10.1016/j.carbpol.2021.117827
Xue, B., He, H.-Z., Huang, Z.-X., Zhu, Z., Xue, F., Liu, S., et al. (2019). Fabrication of Super-tough Ternary Blends by Melt Compounding of Poly(lactic Acid) with Poly(butylene Succinate) and Ethylene-Methyl Acrylate-Glycidyl Methacrylate. Composites Part B: Eng. 172, 743–749. doi:10.1016/j.compositesb.2019.05.098
Xue, Y., Feng, J., Huo, S., Song, P., Yu, B., Liu, L., et al. (2020a). Polyphosphoramide-intercalated MXene for Simultaneously Enhancing thermal Stability, Flame Retardancy and Mechanical Properties of Polylactide. Chem. Eng. J. 397, 125336. doi:10.1016/j.cej.2020.125336
Xue, Y., Shen, M., Zheng, Y., Tao, W., Han, Y., Li, W., et al. (2020b). One-pot Scalable Fabrication of an Oligomeric Phosphoramide towards High-Performance Flame Retardant Polylactic Acid with a Submicron-Grained Structure. Composites Part B: Eng. 183, 107695. doi:10.1016/j.compositesb.2019.107695
Yang, H., Guan, Y., Ye, L., Wang, S., Li, S., Wen, X., et al. (2019). Synergistic Effect of Nanoscale Carbon Black and Ammonium Polyphosphate on Improving thermal Stability and Flame Retardancy of Polypropylene: A Reactive Network for Strengthening Carbon Layer. Composites Part B: Eng. 174, 107038. doi:10.1016/j.compositesb.2019.107038
Yang, H., Yu, B., Xu, X., Bourbigot, S., Wang, H., and Song, P. (2020). Lignin-derived Bio-Based Flame Retardants toward High-Performance Sustainable Polymeric Materials. Green. Chem. 22 (7), 2129–2161. doi:10.1039/d0gc00449a
Yue, X. P., Li, Y., Li, J., and Xu, Y. J. (2021). Improving Fire Behavior and Smoke Suppression of Flame-Retardant PBS Composites Using Lignin Chelate as Carbonization Agent and Catalyst. J. Appl. Polym. Sci. 138, e51199. doi:10.1002/app.5119
Zanetti, M., Kashiwagi, T., Falqui, L., and Camino, G. (2002). Cone Calorimeter Combustion and Gasification Studies of Polymer Layered Silicate Nanocomposites. Chem. Mater. 14 (2), 881–887. doi:10.1021/cm011236k
Zhang, Y., Jing, J., Liu, T., Xi, L., Sai, T., Ran, S., et al. (2021). A Molecularly Engineered Bioderived Polyphosphate for Enhanced Flame Retardant, UV-Blocking and Mechanical Properties of Poly(lactic Acid). Chem. Eng. J. 411, 128493. doi:10.1016/j.cej.2021.128493
Zhang, Y., Xiong, Z., Ge, H., Ni, L., Zhang, T., Huo, S., et al. (2020). Core-Shell Bioderived Flame Retardants Based on Chitosan/Alginate Coated Ammonia Polyphosphate for Enhancing Flame Retardancy of Polylactic Acid. ACS Sust. Chem. Eng. 8 (16), 6402–6412. doi:10.1021/acssuschemeng.0c00634
Keywords: poly(butylene succinate), diethylphosphinate, flame retardancy, polymer composites, comprehensive performances
Citation: Wang Y, Jiang D, Wen X, Tang T, Szymańska K, Sielicki K, Wenelska K and Mijowska E (2021) Investigating the Effect of Aluminum Diethylphosphinate on Thermal Stability, Flame Retardancy, and Mechanical Properties of Poly(butylene succinate). Front. Mater. 8:737749. doi: 10.3389/fmats.2021.737749
Received: 07 July 2021; Accepted: 27 July 2021;
Published: 26 August 2021.
Edited by:
Pingan Song, University of Southern Queensland, AustraliaReviewed by:
Yajun Chen, Beijing Technology and Business University, ChinaYiliang Wang, Karlsruhe Institute of Technology (KIT), Germany
Copyright © 2021 Wang, Jiang, Wen, Tang, Szymańska, Sielicki, Wenelska and Mijowska. This is an open-access article distributed under the terms of the Creative Commons Attribution License (CC BY). The use, distribution or reproduction in other forums is permitted, provided the original author(s) and the copyright owner(s) are credited and that the original publication in this journal is cited, in accordance with accepted academic practice. No use, distribution or reproduction is permitted which does not comply with these terms.
*Correspondence: Dayong Jiang, ZGF5b25namlhbmdjdXN0QDEyNi5jb20=; Xin Wen, aGd3ZW54aW5AMTI2LmNvbQ==; Tao Tang, dHRhbmdAY2lhYy5hYy5jbg==