- 1Department of Chemical, Polymer and Composite Materials Engineering, University of Engineering and Technology, Lahore, Pakistan
- 2Department of Chemical Engineering, University of Engineering and Technology, Lahore, Pakistan
- 3Faculty of Civil Engineering and Geosciences, Department of Hydraulic Engineering, Delft University of Technology, Delft, Netherlands
Diverse applications of polymeric materials have prompted development of eco-friendly, efficient, and economical materials. These characteristics can be obtained by incorporating appropriate fillers in the polymeric matrix. The objective of this work is to investigate impact of aqueous glycerol (Gly) treated rice husk (RH) on surface mechanical properties of produced biocomposites. RH was treated with aqueous Gly (75 wt%) and compounded with low density polyethylene (LDPE) at different loadings (10, 20, and 30 wt%). The resulting mixture was thermally pressed in molds to fabricate biocomposites. Surface mechanical properties such as elastic modulus, hardness, creep rate, and plasticity of biocomposites reinforced with untreated and treated RH were investigated using nanoindenter. Experimental values depicted that hardness (H) and elastic modulus (Es) of treated biocomposites were higher than untreated ones. Treated biocomposites showed the noticeable improvement in elastic modulus by 24 and 37% compared to untreated biocomposites at 20 wt% loading and neat LDPE, respectively. Reductions in the creep rate by 20 and 14% were observed for untreated and treated biocomposites, respectively, in comparison to the neat LDPE. H/E ratio was increased by 23 and 18% for treated and untreated biocomposites, respectively, as compared to virgin LDPE. Furthermore, mechanical and structural properties of untreated and treated RH are reported based on nanoindentation response and Fourier transform infrared spectroscopy (FTIR) techniques The study indicated that aqueous glycerol pretreatment can partially strip off non-cellulosic constituents from lignocellulose matrix to generate cellulose-rich pulp for engineered composite applications.
Introduction
Polymeric composites reinforced with synthetic fibers such as glass and carbon fibers have been used for various applications including packaging, structural, automobile, construction, and aerospace sectors due to good thermal and mechanical properties (Moha, 2014; Kumar et al., 2010). Nevertheless, depletion of petroleum resources, global warming, environmental pollution, and high cost of the polymeric composites have encouraged the researchers to develop eco-friendly biocomposites (Xu et al., 2018). Biocomposites endorse the concept of sustainable development. In general, biocomposites are fabricated with polymeric material as a matrix phase and lignocellulosic waste (LGW) as a reinforcing phase. Various polymers such as polyester, polypropylene (PP), high density polyethylene, and low density polyethylene (LDPE) are usually used for the composites fabrication (Marzouk et al., 2015). Among these, LDPE has been attracted the attention of researchers due to its low crystallinity, branching structure, easy processing, good impact resistance, high toughness, and exceptional barrier properties (Nikaeen and Depan, 2019; Yasin et al., 2019). Many types of LGW such as cotton stalk, bagasse, and rice husk (RH) are abundantly available and composed of cellulose, hemicellulose, lignin, and some impurities (wax, pectin, and inorganic materials) (Dixit and Yadav, 2020). LGW is used as a reinforcing material in polymer matrices because of its good thermal, mechanical, and physical properties (Singh et al., 2002; Kord et al., 2020). Additionally, LGW has characteristics of renewability, biodegradability, less abrasiveness, non-corrosive, non-toxic, good strength, and low cost (Avérous and Le Digabel, 2006; Lee et al., 2009).
Formulation of biocomposites depends on the interfacial bonding between hydrophobic polymer and hydrophilic LGW (Mohanty et al., 2001; Kumar et al., 2010). Amorphous components (hemicellulose and lignin) of LGW are the main cause of its hydrophilic nature (Gabhane et al., 2020). This bonding can be enhanced by changing LGW nature from hydrophilic to hydrophobic, contributing towards better mechanical properties of biocomposites (Mahmood et al., 2016; Moniruzzaman et al., 2017). Thus, pretreatment is the most effective and stimulating method to change the nature of LGW by reducing the content of amorphous components (Nosratpour et al., 2018; Dixit and Yadav, 2020). Various types of pretreatments such as alkali pretreatment, acid pretreatment, biological pretreatment, microwave pretreatment, and steam explosion have already been studied on LGW (Ebrahimi et al., 2017). Poor recyclability, low dissolution capacity, and production of byproducts are major drawbacks of above mentioned pretreatments (Mahmood et al., 2016). Furthermore, these pretreatments require high temperature and pressure conditions.
Therefore, development of effective, economical, and environmentally friendly pretreatment method is still a big challenge for efficient utilization of LGW in a polymer matrix. Organosolv pretreatment could be an effective alternative (Sun and Chen, 2008). This pretreatment effectively degrades lignin and breaks internal chemical bonds between cellulose and hemicellulose (Phi Trinh et al., 2016). Cellulose and hemicellulose with no structural change can also be used for production of value added products (Chen et al., 2017). LGW crystallinity is increased due to the removal of amorphous materials (Zhao et al., 2009). Chemicals such as ethanol, methanol, acetone, glycol, and glycerol are commonly used for organosolv pretreatment (Singhal et al., 2018). Glycerol is the most widely utilized having high boiling point and low cost and being non-toxic in nature compared to other organic chemicals (Singhal et al., 2018). LGW pretreatment with glycerol increases the rate of chemical reaction and its reaction can be performed at normal operating conditions (Phi Trinh et al., 2016). Besides, glycerol viscosity can be reduced by adding water which allows high loading of biomass along with the removal of lignin that leads to good interfacial adhesion in biocomposite (Ebrahimi et al., 2017).
To the best of authors’ knowledge, limited studies have been conducted to pretreat lignocellulosic waste with aqueous glycerol for efficient utilization in the engineered composites. The investigation performed in this work provides the detailed information on the effects of aqueous glycerol pretreatment of RH on the surface mechanical properties of fabricated biocomposites with different RH loadings. Mechanical properties such as hardness, elastic modulus, creep behavior, and plasticity index of biocomposites reinforced with treated and untreated RH were analyzed using nanoindenter. Furthermore, structural characteristics and mechanical properties at submicron scale of untreated and treated RH were also studied using FTIR and nanoindentation techniques, respectively.
Experimental
Materials and Reagents
RH was collected from local market near Lahore and sieved through a sieve shaker after crushing in high speed grinder to obtain particle size of 500 µm and dried in oven at 80°C for 1 h. Glycerol (99.0% purity) and low density polyethylene (LDPE) with density of 0.93 g/cm3 were purchased from Poole BH Ltd., England, and local market.
Chemical Pretreatment of RH
RH sample was added in aqueous Gly (75 wt% glycerol and 25 wt% water) with RH to aqueous Gly ratio of 1:10 and pretreated at 90°C for 4 h at 150 rpm in the water bath. The resultant sample was filtered and washed 2 to 3 times with distilled water and dried in oven at 80°C for 24 h till constant weight. Furthermore, amount of lignin content was measured in untreated and pretreated RH as reported by Mahmood et al., 2016. 12.9% of lignin content was found in the RH after the Gly pretreatment while untreated RH contained the 19.5% lignin content.
Manufacturing of Biocomposite Samples
LDPE was mixed with untreated (raw) and pretreated RH with different biomass loadings (10, 20, and 30 wt%) using melt processing method in an internal mixer at a temperature range of 115–130°C for 10 min at 300 rpm. The compounded mixture was put into mold having dimensions of 10 cm × 10 cm × 0.3 cm of target density of 0.4 g/cm3. The mixture placed in the mold was thermally pressed at 180°C and 12 MPa for 10 min and the mold was uniformly cooled down to room temperature under constant pressure of 12 MPa. The fabricated samples were conditioned at room temperature in polythene bags for further characterizations. Figure 1 represents the scheme of biocomposite fabrication.
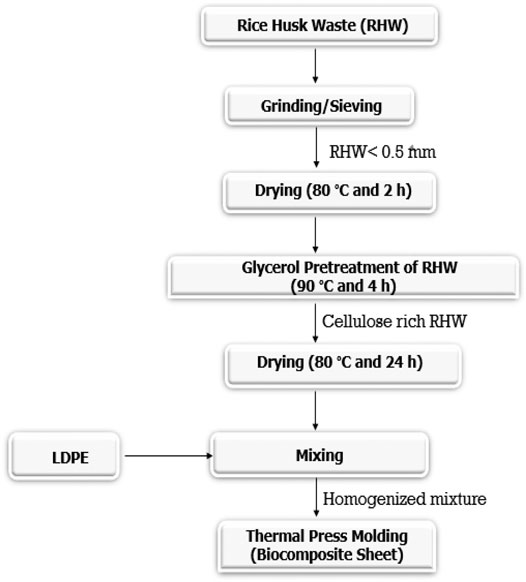
FIGURE 1. Schematic representation of biocomposite fabrication as reported by Sulaiman et al. (2020).
Characterization of Untreated and Treated Rice Husk Particles
The Fourier transform infrared spectroscopy (FTIR) was used to explore the structure of RH which arose after treatment of the fibers. Fiber structures of untreated and pretreated samples were examined using Perkin-Elmer Spectrum One FTIR spectrometer. FTIR spectra of samples were found in the wavelength of 4,000–500 cm−1 at 4 cm−1 resolution.
Mechanical Characterization of Rice Husk Particles and Biocomposite
The mechanical characterization of samples near the surface by indentation is a challenging task. The nano-surface mechanical properties of RH particles and biocomposites were studied using nanoindentation technique. Nanoindentation characterization of filler particles and biocomposites was performed through nanoindenter (Zwick GmbH & Co. KG) containing Berkovich indenter of diamond tip with three-sided pyramid geometry. Indenter radius and effective opening angle are 0.215°µm and 140.6°, respectively. The Berkovich indenter is used for measuring of hardness and elastic modulus of the material. RH particles were fixed on cylindrical holder of an indenter by using double tape. Filler particles were not embedded in the epoxy resin for avoiding the effect of resin on mechanical properties of filler particles. Similarly, each sheet of 3 ± 0.2 mm thickness was fixed on a holder. Peak load of 100 mN was applied on each sheet for obtaining the maximum penetration depth. As a result, load displacement data were obtained. It was used to calculate hardness (H) and modulus (Es). The hardness is the ratio of maximum loading force (Pmax) to projected contact area.
where A is the area of contact indentation tip between indenter at maximum load and sample. The experiments were performed at a peak load of 100 mN in 100 s and creep time 20 s with quasi-continuous stiffness mode (QCSM). Three measurements were performed on each sheet sample.
Results and Discussions
FTIR Analysis for Untreated and Treated Rice Husk
Structural changes in the lignocellulosic biomass can be evaluated through FTIR analysis. Figure 2 depicts FTIR spectrum of untreated and treated RH with aqueous glycerol. Cellulose and hemicellulose characteristic peaks were noted at 3,200–3,300 cm−1 (O-H stretch, H-bonded) and 2,900 cm−1 (C-H stretch) (Diaz et al., 2015). Absorption peak was moved to higher wave number from 3,260.2 cm−1 to 3,307.43 cm−1 for pretreated RH that can be indicated the reconstruction of intermolecular hydrogen bonding in cellulose because of reduction in free hydroxyl groups in hemicellulose and lignin structure (Pan et al., 2017). While peak of 2,900 cm−1 related to C-H bond in cellulose and hemicellulose was not changed prominently after pretreatment, the peak of 1,647.34 cm−1 was assigned to bending mode of absorbed water (Chen et al., 2011). Aromatic structure in lignin was related to absorption band of 1,521.2 cm−1 and decreasing trend of peaks after pretreatment clearly indicated the removal of lignin (Pan et al., 2017). Band at 1,204 cm−1 (C-O stretching signal) was attributed to partial dissolution of lignin and hemicellulose (Wang et al., 2015). Peaks of 1,030 cm−1 and 907.33 cm−1 are assigned to COC group in the glucose structure of cellulose (Jiang and Hu, 2019). Based on FTIR results, we could say aqueous glycerol pretreatment on RH may reduce the partial amorphous compounds (lignin and hemicellulose) and increase the cellulose content with more compact and ordered crystalline structure.
Compliance Curve (Load Displacement Curve) of Untreated and Treated Rice Husk
Figure 3 represents the compliance curve of untreated and aqueous glycerol (75 wt%) treated RH. Loading-unloading response of the samples was obtained at maximum indentation load of 100 mN with respect to maximum penetration depth of 23 µm. Total 36 indents were applied on each sample with spacing of 60 µm from each other. This spacing was adjusted to avoid the overlapping of internal stress produced around each indent. An indenter penetrates in untreated RH upto 11.95 µm of contact depth at maximum load, as depicted in Figure 3. Loading portion of untreated RH curve starts from 2.5 µm instead of 0 µm. This might be happened due to poor surface detection, imperfections in tip geometry, and poor tip calibration. Figure 3 clearly dictates that untreated RH is harder and stiff material compared to treated RH. This may be due to the presence of lignin and pectin in RH. Maximum indentation displacement of 17.61 µm was achieved in the treated RH at 100 mN load before creeping effect. Though treated RH is softer compared to untreated one. It might be happened because of partial removal of lignin material and increase of cellulose content via pretreatent.
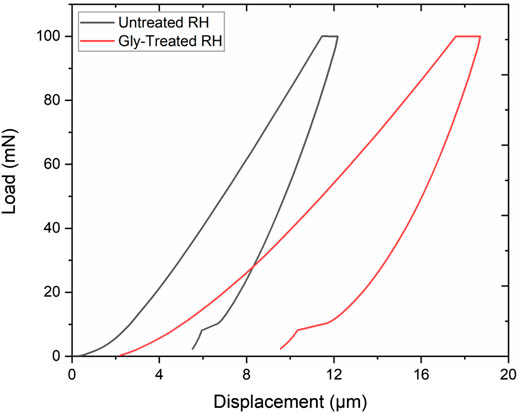
FIGURE 3. Load displacement compliance curves of untreated and aqueous glycerol (75 wt%) treated RH at 100 mN nominally spacing of 60 µm between each indent.
Effect of Pretreatment on Hardness and Modulus
Mechanical properties of materials such as strength and ductility depend on elastic modulus (Es) and hardness (H) (Wallace et al., 2019). Basically, RH is used as a reinforcing material in the biocomposites for many engineering applications. Figures 4A,B describe the effect of chemical pretreatment on H and Es of RH. H and Es are functions of contact depth. Large variations in H and Es values were observed at lower contact depth upto 5 µm for untreated RH. This phenomenon could be happened due to surface roughness, poor determination of surface particles and defects in indenter tip geometry. However, H and Es values become nearly constant after 5 µm, as shown in Figures 4A,B. Even no wide variations in H and Es were noted on the top surface after pretreatment. It indicated the complete removal of impurities such as wax and pectin along with partial removal of lignin from RH. Although Gly-treated RH showed variation in elastic modulus before 5 µm of penetration depth. It may be happened due to poor surface detection. Average H and Es values of untreated and treated sample are given in Table1.
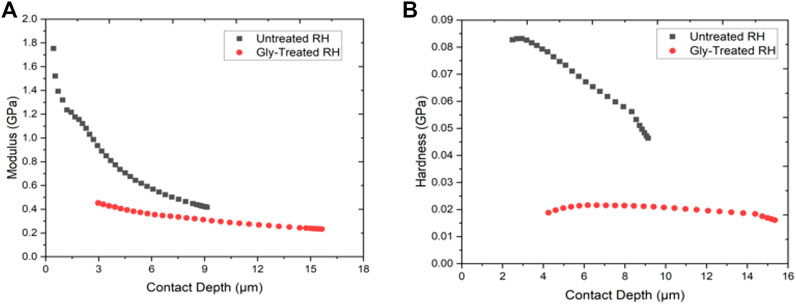
FIGURE 4. Modulus and hardness as a function of contact depth: (A) modulus of untreated and Gly-treated RH; (B) hardness of untreated and Gly-treated RH.

TABLE 1. Average elastic modulus (E) and hardness (H) of untreated and treated RH along with the standard deviations.
Compliance Curve of Biocomposites Reinforced with Untreated and Treated Rice Husk
Figures 5A,B describe the compliance curve of neat LDPE and biocomposites reinforced with untreated and treated RH at different biomass loadings (10, 20, and 30 wt%). Compliance curve of each produced sample shows the median curve of 36 indentation load displacement performed at maximum load of 100 mN at the temperature of 25°C. Spacing between nano-indents was placed 60 µm from each other to minimize the overlapping of internal stress. Basically, indentation cycle of each sample was consisted of three sections: 1) loading section; 2) hold section; 3) unloading section. The loading section was started from 0 to maximum displacement of 20 µm, as depicted in Figures 5A,B. A load hold segment was applied for 20 s to account creeping effect during indentation process. During unloading step, the material came back to unrecoverable depth of 8–12 µm. An unrecoverable depth at zero load was achieved due to plastic deformation in the material. Maximum contact depth of 15.22 μm at 100 mN of load was attained for neat LDPE, while maximum achievable penetration depth in biocomposites based on untreated and treated RH is given in Table 2. Addition of untreated RH in neat LDPE decreased the biocomposites resistance, indicating the surface showed low resistance to indentation penetration by the indenter. It might be happened due to incompatibility of hydrophilic natural filler (RH) and matrix material (LDPE), resulting in poor uniform distribution of RH in the matrix due to which there is poor stress transfer efficiency from matrix to filler particles (Faris et al., 2018). Moreover, higher displacement depth in biocomposites compared to neat LDPE indicated the wrapping of RH particles around LDPE matrix. Interestingly, trend of biocomposites moved to harder side as loading increased from 10 to 20 wt% but at 30 wt% again decreased. This phenomenon could be occurred due to agglomerates formation at higher loadings of filler (Rahman et al., 2010; Yadav and Yusoh, 2019).
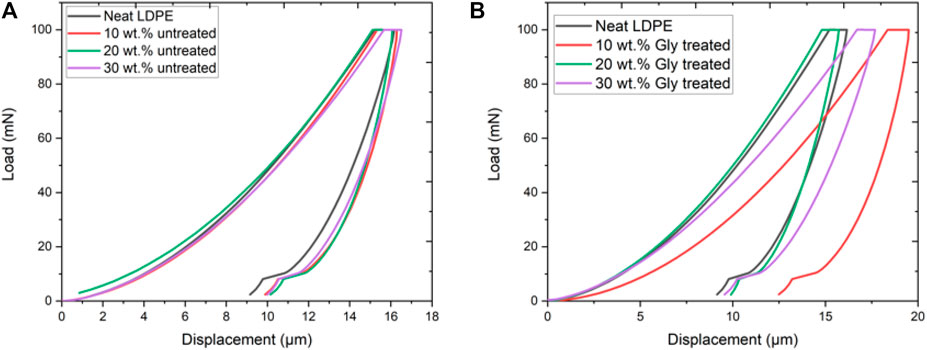
FIGURE 5. Compliance curves of biocomposites with different biomass loadings at a maximum loading of 100 mN: (A) untreated RH reinforced biocomposites; (B) Gly-treated RH reinforced biocomposites.
Figure 5B shows the reinforcement of treated RH into LDPE with loading ratio of 10, 20, and 30 wt%. It was noted that the surface treatment and biomass loading act independently on mechanical properties (Muñoz-Vélez et al., 2018). Generally, treated biocomposites are softer than untreated biocomposites. This could happen due to partial removal of lignin after pretreatment and lignin is the main reason for contributing the rigidity in the biocomposites. It was evident from Figure 5B that treated biocomposites with 10 wt% of loading showed the soft behavior, indicating the wrapping of RH particles throughout matrix phase. While contact depth of 14.7 and 16.7 µm was found at 20 and 30 wt% of treated RH loadings, biocomposites showed harder behavior during loading section at 20 wt% loading of filler. This harder behaviour may be due to the indentation occurred at crystalline region of the biocomposites. In case of 30 wt% loading, material trend was moved again towards softer. The obtained values revealed that the biocomposite at 20 wt% loading showed higher plastic behavior compared with biocomposites at 10 and 30 wt% loading. This behavior might be happened because of uniform distribution and proper mixing of RH in resin, resulting in chance of good adhesion between cellulosic rich fiber and matrix (Irwanto et al., 2020). In comparison with untreated biocomposites, treated RH biocomposites showed the lower plastic behavior and greater elastic recovery at higher loading which indicates the breakage of stiff wall of lignin in the RH after pretreatment (Das et al., 2019).
Effect of Different Biomass Loadings on Hardness and Modulus
Surface mechanical properties of polymers and biocomposites are quantitively measured using hardness. Results of indentation H and Es for neat LDPE and biocomposites based on treated and untreated RH are shown in Figures 6, 7. Indentation H and Es data were gained via performing QCSM experiments on neat LDPE and biocomposites at maximum load of 100 mN. Large variations in H and Es values were observed upto 3 µm contact depth due to the surface roughness of top layer causing poor determination of contact depth, tip geometry defect and environmental effects on the surface, nanoindentation data obtained at shallow depth is (Iqbal et al., 2013; Nikaeen and Depan, 2019). Although no wide variations in H and Es of each sheet were observed after 3 µm, LDPE has average H and Es values of 0.029 and 0.624 GPa, respectively, which is comparable to the literature (Jee and Lee, 2010; Yasin et al., 2019). Hardness of LDPE was continuously decreased from 0.064 to 0.021 GPa and followed to 0.016 GPa in the hold segment (creeping effect). Similarly, decreasing (from 1.533 to 0.405 GPa) trend was observed for modulus. It is concluded that LDPE is harder and tough material which is attributed to dense and compact structure as compared to the biocomposites.
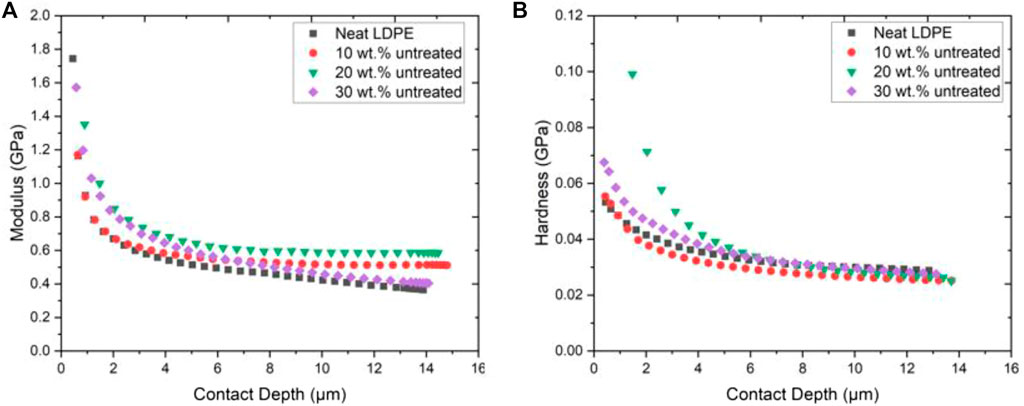
FIGURE 6. Modulus and hardness as a function of contact depth: (A) modulus curves of untreated RH reinforced biocomposites with loadings of 10, 20, and 30 wt%; (B) hardness curves of untreated RH reinforced biocomposites with loadings of 10, 20, and 30 wt%.
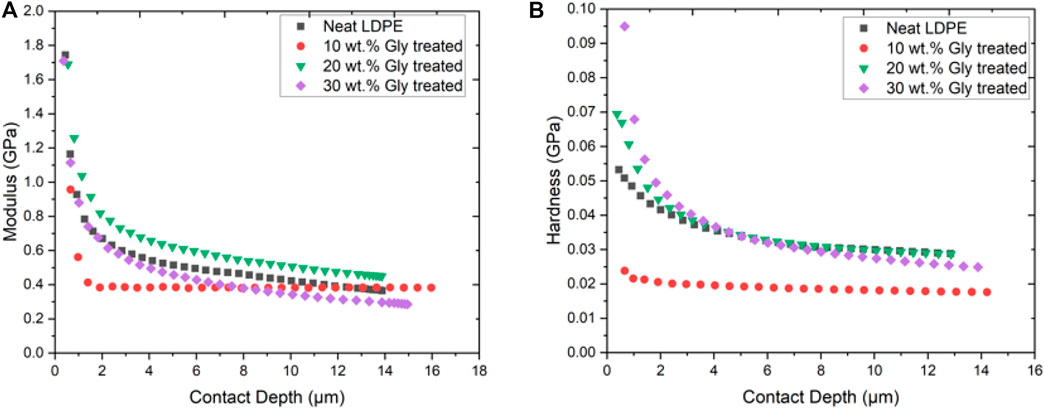
FIGURE 7. Modulus and hardness as a function of contact depth: (A) modulus curves of glycerol-treated RH reinforced biocomposites with loadings of 10, 20, and 30 wt%; (B) hardness curves of glycerol-treated RH reinforced biocomposites with loadings of 10, 20, and 30 wt%.
Biocomposites also showed variations in Es and H values with respect to the contact depth, as shown in Figures 6, 7. Anisotropic nature of biocomposites could be the reason of this behavior. Anisotropic nature is because of its constituent materials. Biocomposites are basically composed of LDPE, as a continuous phase (matrix material), which is a semi-crystalline material, and RH, as a disperse phase. RH is further composed of three main components such as cellulose, hemicellulose, and lignin. Cellulose itself is a composite material that consists of crystalline and amorphous components. Lignin and hemicellulose are also amorphous components. On the basis of this concept, biocomposites are the mixture of crystalline and amorphous components, contributing to the variation in hardness and elastic modulus. Furthermore, biocomposites have RH particles dispersion and distrution in the LDPE matrix. It could be believed that biocomposites are consisted of two regions. Top surface region is in which both H and Es were significantly decreased upto 3 µm of contact depth due to surface roughness, environmental effects, poor determination of top surface, and defect in indenter tip geometry (Nikaeen and Depan, 2019). However, no abrupt changes in H and Es were noted after 3–14 µm of contact depth, representing the bulk region of the sheets, as represented in Figures 6, 7. That bulk region is more compact and orderly arranged region compared to the top region.
Though Es and H of biocomposites were increased through addition of untreated and treated RH. Increase of H and Es values was noted with increasing the biomass loading (from 10 to 20 wt%). Increasing values of H and Es were related to the good dispersion of filler particles and better interfacial adhesion of filler particles with the matrix material, resulting to an increase in the stress transfer efficiency from the matrix to the reinforcing material (Yadav and Yusoh, 2019). Hardness of 26% and Es of 37% were increased containing 20 wt% treated RH compared to neat LDPE (Hf and Biocomposites, 2020). However, H and Es suddenly decreased at 30 wt% biomass loading. This trend contradicts the literature values because at higher loading, H and Es values are generally increased. Reduction in hardness and elastic modulus might be haapened due to the formation of agglomerates (Li et al., 2017). While H and Es trend of pretreated biocomposites was noted higher than untreated biocomposites, higher values of H and Es indicated the removal of non-cellulosic impurities after pretreatment (Pan et al., 2017). It was depicted from Figures 6, 7 that H and Es of treated RH biocomposite were also increased as biomass loading increased but remained less than untreated biocomposites. Es and H were increased by 24 and 5% of treated biocomposites (20 wt% loading) in comparison to untreated biocomposites. This may be due to leaching of maximum lignin and disrupting of cellulose structure (Raghavi et al., 2016). It could be suggested that RH pretreatment with glycerol is the most effective pretreatment because impurities such as wax and pectin were eliminated and interfacial adhesion between RH and matrix could be improved. Furthermore, it could be concluded on the basis of obtained results that nanoindentation is a suitable method for determining elastic modulus of the composites. Although elastic modulus obtained through nanoindentation technique could be validated with elastic modulus obtained through tensile and flexural testings.
Creep Behavior of Biocomposites Based on Untreated and Treated Rice Husk
Mechanical properties of polymeric composites largely depend on the creeping effect. Maximum applied load remained constant for a certain time period for analyzing the creeping effect. Figures 8A,B depict the creep rate of neat LDPE and biocomposites based on untreated and treated RH. Creep rate is showing decreasing trend for all samples at peak load of 100 mN. Creep rate of LDPE is decreasing from 56.18 to 41.33 nm/s. It was obvious from Figure 8 that biocomposites showed lower value of creep rate compared to neat LDPE, indicating the improvement in creep resistance of LDPE by introducing the RH (Yadav and Yusoh, 2019). Reduction in creep rate of 7 and 11% was noted for untreated and treated biocomposites with 10 wt% RH loading, respectively. Interestingly, creep rate was reduced to 20 and 18% for the biocomposites containing 20% and 30 wt% untreated RH loading, respectively, as shown in Figure 8A. It is also evident from Figure 8B that creep rate was reduced to 14 and 8% for treated biocomposites reinforced with 20 and 30 wt% treated RH loading, respectively. This phenomenon might be happened due to addition of RH particles in the LDPE material. Additionally, the formation of RH layer which allows more LDPE chain to enter the RH galleries produced maximum interaction between the filler and LDPE matrix. Therefore, molecular mobility was retarded when maximum load remains constant. It was also observed from Figure 8B that creep rate was increased instead of further reducing at 30 wt% loading. It might be happened due to agglomeration of RH particles. It could be concluded that creep behavior was affected by biomass loading because it would change the surface morphology or microscopic structure of polymeric composites.
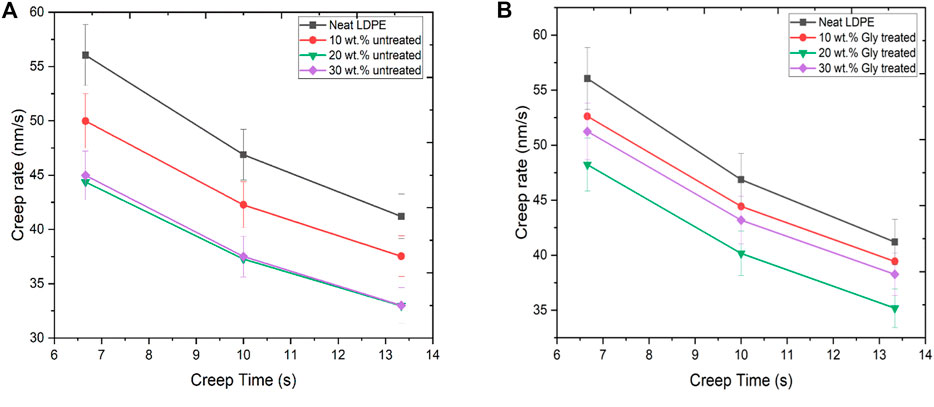
FIGURE 8. Creep rate (nm/s) vs. creep time (s) of untreated and treated biocomposites: (A) untreated biocomposites; (B) treated biocomposites.
H/E of Biocomposites Based on Untreated and Treated Rice Husk
H/E ratio (plasticity index) explains the plastic-elastic behavior of the material. It is the qualitative analysis of scratch performance of the material.Mikic (1974) proposed the plasticity index of perfect cone based on hardness and elastic modulus (Mikić, 1974). Higher values of H/E are the indication of wear improvement. Hardness to modulus ratio of 0.1 is reported for elastic material and 0.01 for pure plastic material in the literature. H/E values of biocomposites were obtained between 0.1 and 0.01 indicating the elastic-plastic nature of the material. Therefore, material with lowest H/E ratio represented the plastic nature of the material. Figures 9A,B illustrate the H/E ratio of neat LDPE and biocomposites based on untreated and treated RH as function of contact depth. Large uncertaintity in H/E exists upto lowest depth of 3 µm, as indicated in Figures 9A,B due to environmental effect on the top surface of sample, defect in indenter tip geometry, and manufacturing process. H/E values of neat LDPE decreased as penetration depth increased. This could be the indication of a reduction in wear resistance or material to plastic deformation.
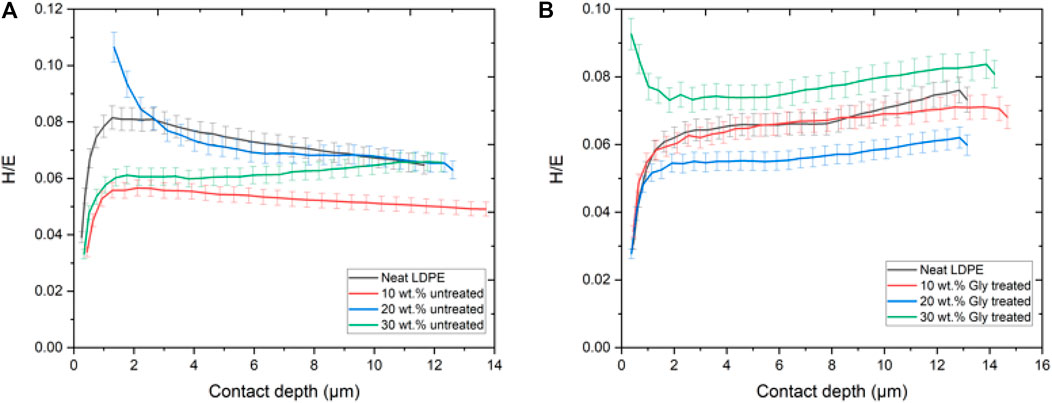
FIGURE 9. Plasticity index (H/E) of biocomposites as a function of contact depth: (A) plasticity index of untreated biocomposites; (B) plasticity index of treated biocomposites.
Lower values of H/E were noted for untreated biocomposites compared to neat LDPE, as represented in Figure 9A. This was happened because of the incorporation of lignocellulosic RH, either untreated or treated. Decreasing trend of H/E was noted at untreated RH loading of 10 wt% representing the increase of material plasticity, resulting in wear resistance decrease. However, H/E value initially decreased and then became constant as contact depth increased. In case of 30 wt% untreated RH loading, H/E ratio gradually increased as contact depth increased. It could be assumed that wear resistance of biocomposites improved as biomass loading increased. Plasticity index of biocomposites based on glycerol-treated RH is shown in Figure 9B. H/E ratio at 10 wt% biomass loading showed the almost same pattern as neat LDPE. H/E ratio was increased by 23 and 18% for treated and untreated biocomposites with 20 wt% loading compared to virgin LDPE. H/E of biocomposites containing 20 wt% treated RH showed higher plasticity, resulting in ductility of material improved. It might be happened because of better distribution of filler particles in LDPE and good interfacial adhesion between filler and matrix phases. Moreover, degree of crystallinity of RH was increased because of the applied chemical pretreatment that ultimately enhanced the fiber-matrix adhesion. While, in case of higher loading of 30 wt%, plasticity decreased. It might be happened because of the filler agglomeration.
Conclusion
The potency of aqueous glycerol pretreatment of rice husk (RH) on mechanical properties of fabricated biocomposites at nanoscale was reported. Aqueous glycerol pretreatment transformed RH into highly crystalline, cellulose-rich fiber with significantly reduced hardness and elastic modulus. Lignin content was reduced to 34% due to glycerol treatment. Compliance curves of untreated and treated RH displayed that stiffness of RH was decreased due to reduction of lignin material. FTIR graph showed that structure of RH was significantly changed. Conversely, biocomposites reinforced with treated RH exhibited higher values of hardness and elastic modulus compared to untreated biocomposites due to removal of non-cellulosic impurities (Hf and Biocomposites, 2020). Elastic modulus and hardness of treated biocomposites were increased by 37 and 26% compared to neat LDPE and 24 and 5%, compared to untreated biocomposites at 20 wt% loading, respectively. Plasticity and creep resistance of biocomposites based on 20 wt% RH loading were significantly changed compared to neat LDPE. This work revealed that pretreatment of RH with eco-friendly chemical is a highly effective method for improving nano-mechanical properties of environmentally friendly composites, although findings of this work could be more elaborated by performing macro-mechanical testing such as tensile and flexural tests on biocomposites.
Data Availability Statement
The raw data supporting the conclusions of this article will be made available by the authors, without undue reservation.
Author Contributions
TI, SY, and HM contributed to conception and design of the study. MS performed the experiments and wrote the first draft of the manuscript. MS and AS performed the analysis of the experimental data. HM supervised the project and acquired the necessary funding. All authors contributed to manuscript revision and read and approved the submitted version.
Conflict of Interest
The authors declare that the research was conducted in the absence of any commercial or financial relationships that could be construed as a potential conflict of interest.
Publisher’s Note
All claims expressed in this article are solely those of the authors and do not necessarily represent those of their affiliated organizations, or those of the publisher, the editors, and the reviewers. Any product that may be evaluated in this article, or claim that may be made by its manufacturer, is not guaranteed or endorsed by the publisher.
Acknowledgments
The authors are grateful to UET, Lahore (new campus), Pakistan, for providing financial assistance to accomplish this work.
References
Avérous, L., and Le Digabel, F. (2006). Properties of biocomposites based on lignocellulosic fillers. Carbohydr. Polym. 66, 480–493. doi:10.1016/j.carbpol.2006.04.004
Chen, H., Liu, J., Chang, X., Chen, D., Xue, Y., Liu, P., et al. (2017). A review on the pretreatment of lignocellulose for high-value chemicals. Fuel Process. Tech. 160, 196–206. doi:10.1016/j.fuproc.2016.12.007
Chen, X., Yu, J., Zhang, Z., and Lu, C. (2011). Study on structure and thermal stability properties of cellulose fibers from rice straw. Carbohydr. Polym. 85, 245–250. doi:10.1016/j.carbpol.2011.02.022
Das, O., Hedenqvist, M. S., Prakash, C., and Lin, R. J. T., (2019). Nanoindentation and flammability characterisation of five rice husk biomasses for biocomposites applications. Compos. Part A Appl. Sci. Manuf. 125, 105566. doi:10.1016/j.compositesa.2019.105566
Diaz, A. B., Moretti, M. M. d. S., Bezerra-Bussoli, C., Carreira Nunes, C. d. C., Blandino, A., da Silva, R., et al. (2015). Evaluation of microwave-assisted pretreatment of lignocellulosic biomass immersed in alkaline glycerol for fermentable sugars production. Bioresour. Tech. 185, 316–323. doi:10.1016/j.biortech.2015.02.112
Dixit, S., and Yadav, V. L. (2020). Comparative study of polystyrene/chemically modified wheat straw composite for green packaging application. Polym. Bull. 77, 1307–1326. doi:10.1007/s00289-019-02804-0
Ebrahimi, M., Villaflores, O. B., Ordono, E. E., and Caparanga, A. R. (2017). Effects of acidified aqueous glycerol and glycerol carbonate pretreatment of rice husk on the enzymatic digestibility, structural characteristics, and bioethanol production. Bioresour. Tech. 228, 264–271. doi:10.1016/j.biortech.2016.12.106
Faris, N. A., Jaafar, A., Noriman, N. Z., Hamzah, R., Shayfull, Z., and Ghazali, M. F. (2018). LDPE/paddy straw biocomposite: The effect of filler loading. AIP Conf. Proc., 2030. doi:10.1063/1.5066722
Gabhane, J., Kumar, S., and Sarma, A. K. (2020). Effect of glycerol thermal and hydrothermal pretreatments on lignin degradation and enzymatic hydrolysis in paddy straw. Renew. Energ. 154, 1304–1313. doi:10.1016/j.renene.2020.03.035
Hf, P., and Biocomposites, P. C. L. (2020). Applied sciences Characterization of Nano-Mechanical , Surface and Thermal Properties of Hemp Fiber-Reinforced.
Iqbal, T., Briscoe, B. J., Yasin, S., and Luckham, P. F. (2013). Nanoindentation response of poly(ether ether ketone) surfaces-A semicrystalline bimodal behavior. J. Appl. Polym. Sci., a–n. doi:10.1002/app.39723
Irwanto, D., Pidhatika, B., Nurhajati, D. W., and Harjanto, S. (2020). Mechanical properties and crystallinity of linear low density polyethylene based biocomposite film. Mkkp 35, 93. doi:10.20543/mkkp.v35i2.5624
Jee, A.-Y., and Lee, M. (2010). Comparative analysis on the nanoindentation of polymers using atomic force microscopy. Polym. Test. 29, 95–99. doi:10.1016/j.polymertesting.2009.09.009
Jiang, Z., and Hu, D. (2019). Molecular mechanism of anionic dyes adsorption on cationized rice husk cellulose from agricultural wastes. J. Mol. Liquids 276, 105–114. doi:10.1016/j.molliq.2018.11.153
Kord, B., Movahedi, F., Adlnasab, L., and Masrouri, H. (2020). Influence of eco-friendly pretreatment of lignocellulosic biomass using ionic liquids on the interface adhesion and characteristics of polymer composite boards. J. Compos. Mater. 54, 3717–3729. doi:10.1177/0021998320918345
Kumar, R., Yakabu, M. K., and Anandjiwala, R. D. (2010). Effect of montmorillonite clay on flax fabric reinforced poly lactic acid composites with amphiphilic additives. Composites A: Appl. Sci. Manufacturing 41, 1620–1627. doi:10.1016/j.compositesa.2010.07.012
Lee, B.-H., Kim, H.-S., Lee, S., Kim, H.-J., and Dorgan, J. R. (2009). Bio-composites of kenaf fibers in polylactide: Role of improved interfacial adhesion in the carding process. Composites Sci. Tech. 69, 2573–2579. doi:10.1016/j.compscitech.2009.07.015
Li, Q., Li, Y., and Zhou, L. (2017). Nanoscale evaluation of multi-layer interfacial mechanical properties of sisal fiber reinforced composites by nanoindentation technique. Composites Sci. Tech. 152, 211–221. doi:10.1016/j.compscitech.2017.09.030
Mahmood, H., Moniruzzaman, M., Yusup, S., and Akil, H. M. (2016). Particulate composites based on ionic liquid-treated oil palm fiber and thermoplastic starch adhesive. Clean. Techn Environ. Pol. 18, 2217–2226. doi:10.1007/s10098-016-1132-0
Marzouk, W., Bettaieb, F., Khiari, R., and Majdoub, H. (2015). Composite materials based on low-density polyethylene loaded with date pits. J. Thermoplastic Compos. Mater. 30, 1200–1216. doi:10.1177/0892705715618742
Mikić, B. B. (1974). Thermal contact conductance; theoretical considerations. Int. J. Heat Mass. Transf. 17, 205–214. doi:10.1016/0017-9310(74)90082-9
Mohanty, A. K., Misra, M., and Drzal, L. T. (2001). Surface modifications of natural fibers and performance of the resulting biocomposites: An overview. Compos. Inter. 8, 313–343. doi:10.1163/156855401753255422
Moniruzzaman, M., Mahmood, H., Yusup, S., and Akil, H. M. (2017). Exploring Ionic Liquid Assisted Pretreatment of Lignocellulosic Biomass for Fabrication of Green Composite. J. Jpn. Inst. Energ. 96, 376–379. doi:10.3775/jie.96.376
Muñoz-Vélez, M., Hidalgo-Salazar, M., and Mina-Hernández, J. (2018). Effect of content and surface modification of fique fibers on the properties of a low-density polyethylene (LDPE)-Al/fique composite. Polymers 10, 1050–1064. doi:10.3390/polym10101050
Nikaeen, P., and Depan, D. (2019). Surface Mechanical Characterization of Carbon Nanofiber Reinforced Low-Density Polyethylene by Nanoindentation and Comparison with Bulk Properties.
Nosratpour, M. J., Karimi, K., and Sadeghi, M. (2018). Improvement of ethanol and biogas production from sugarcane bagasse using sodium alkaline pretreatments. J. Environ. Manage. 226, 329–339. doi:10.1016/j.jenvman.2018.08.058
Pan, M., Zhao, G., Ding, C., Wu, B., Lian, Z., and Lian, H. (2017). Physicochemical transformation of rice straw after pretreatment with a deep eutectic solvent of choline chloride/urea. Carbohydr. Polym. 176, 307–314. doi:10.1016/j.carbpol.2017.08.088
Phi Trinh, L. T., Lee, J.-W., Lee, H.-J., and Lee, H. (2016). Acidified glycerol pretreatment for enhanced ethanol production from rice straw. Biomass and Bioenergy 94, 39–45. doi:10.1016/j.biombioe.2016.08.017
Raghavi, S., Sindhu, R., Binod, P., Gnansounou, E., and Pandey, A. (2016). Development of a novel sequential pretreatment strategy for the production of bioethanol from sugarcane trash. Bioresour. Tech. 199, 202–210. doi:10.1016/j.biortech.2015.08.062
Rahman, M. R., Islam, M. N., Huque, M. M., Hamdan, S., and Ahmed, A. S. (2010). Effect of chemical treatment on rice husk (RH) reinforced polyethylene (PE) composites. BioResources 5, 854–869. doi:10.15376/biores.5.2.854-869
Singh, A. A., Afrin, S., and Karim, Z. (2002). Green Composites: Versatile Material for Future. doi:10.1007/978-3-319-49382-4)
Singhal, A., Kumar, M., Bhattacharya, M., Kumari, N., Jha, P. K., Chauhan, D. K., et al. (2018). Pretreatment of Leucaena leucocephala wood by acidified glycerol: optimization, severity index and correlation analysis. Bioresour. Tech. 265, 214–223. doi:10.1016/j.biortech.2018.05.084
Sulaiman, M., Iqbal, T., Yasin, S., Mahmood, H., and Shakeel, A. (2020). Study of nano-mechanical performance of pretreated natural fiber in ldpe composite for packaging applications. Materials 13, 4977–4987. doi:10.3390/ma13214977
Sun, F., and Chen, H. (2008). Enhanced enzymatic hydrolysis of wheat straw by aqueous glycerol pretreatment. Bioresour. Tech. 99, 6156–6161. doi:10.1016/j.biortech.2007.12.027
Wallace, C. A., Afzal, M. T., and Saha, G. C. (2019). Effect of feedstock and microwave pyrolysis temperature on physio-chemical and nano-scale mechanical properties of biochar. Bioresour. Bioproc., 6. doi:10.1186/s40643-019-0268-2
Wang, S., Peng, X., Zhong, L., Jing, S., Cao, X., Lu, F., et al. (2015). Choline chloride/urea as an effective plasticizer for production of cellulose films. Carbohydr. Polym. 117, 133–139. doi:10.1016/j.carbpol.2014.08.113
Xu, K., Liu, C., Kang, K., Zheng, Z., Wang, S., Tang, Z., et al. (2018). Isolation of nanocrystalline cellulose from rice straw and preparation of its biocomposites with chitosan: Physicochemical characterization and evaluation of interfacial compatibility. Composites Sci. Tech. 154, 8–17. doi:10.1016/j.compscitech.2017.10.022
Yadav, S. M., and Yusoh, K. B. (2019). Subsurface mechanical properties and subsurface creep behaviour of modified nanoclay-based wood-plastic composites studied by nanoindentation. Polym. Bull. 76, 2179–2196. doi:10.1007/s00289-018-2497-5
Yasin, S., Shakeel, A., Iqbal, T., Ahmad, F., Mehmood, H., Luckham, P. F., et al. (2019). Effect of experimental conditions on nano-indentation response of low density polyethylene (LDPE). J. Macromolecular Sci. A 56, 640–647. doi:10.1080/10601325.2019.1593791
Keywords: rice husk, glycerol, LDPE, pretreatment, nanoindentation
Citation: Sulaiman M, Iqbal T, Yasin S, Mahmood H and Shakeel A (2021) Fabrication and Nanomechanical Characterization of Thermoplastic Biocomposites Based on Chemically Treated Lignocellulosic Biomass for Surface Engineering Applications. Front. Mater. 8:733109. doi: 10.3389/fmats.2021.733109
Received: 29 June 2021; Accepted: 14 September 2021;
Published: 26 October 2021.
Edited by:
Bomou Ma, Donghua University, ChinaReviewed by:
Farkhondeh Hemmati, University of Tehran, IranGiulia Fredi, University of Trento, Italy
Copyright © 2021 Sulaiman, Iqbal, Yasin, Mahmood and Shakeel. This is an open-access article distributed under the terms of the Creative Commons Attribution License (CC BY). The use, distribution or reproduction in other forums is permitted, provided the original author(s) and the copyright owner(s) are credited and that the original publication in this journal is cited, in accordance with accepted academic practice. No use, distribution or reproduction is permitted which does not comply with these terms.
*Correspondence: Ahmad Shakeel, a.shakeel@tudelft.nl