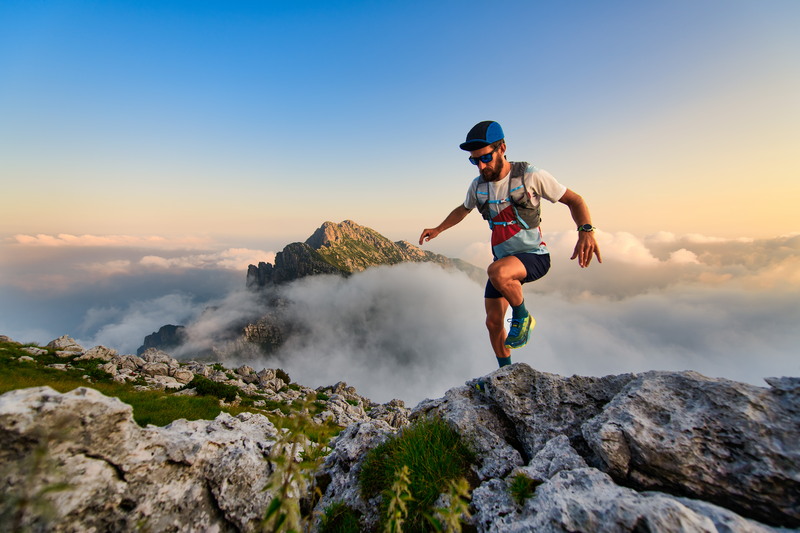
94% of researchers rate our articles as excellent or good
Learn more about the work of our research integrity team to safeguard the quality of each article we publish.
Find out more
ORIGINAL RESEARCH article
Front. Mater. , 19 August 2021
Sec. Polymeric and Composite Materials
Volume 8 - 2021 | https://doi.org/10.3389/fmats.2021.725328
This article is part of the Research Topic Carbon Nanomaterial Filled Polymer Composites for Functional Applications: Processing, Structure, and Property Relationship View all 13 articles
According to the principle of radical polymerization reaction, different polycarboxylates with comb structures were synthesized. With the other two commercial polycarboxylates (C-PCE-1 and C-PCE-2), the effects of all the polycarboxylates on adsorption, hydration, zeta potential, liquid surface tension, and flowability in Portland cement were determined. Compared to O-PCE and C-PCEs, the adsorption value of M-PCE increased by 14.1% and the adsorption rate increased by 24% maximum. O-PCE, C-PCE-1, and C-PCE-2 have a delayed effect on the hydration of the cementitious materials, but M-PCE does not. Due to higher adsorption amount, M-PCE with siloxane groups has an excellent comprehensive performance of zeta potential, liquid surface tension, and flowability in cementitious materials.
Polycarboxylate superplasticizer (PCE) has been extensively used in concrete technology since the 1980s (Plank and Bian, 2010). The side chain of PEO is suspended between the Portland cement particles to exert its steric hindrance effect, thereby dispersing Portland cement (Li et al., 2005; Wang, 2009). Compared with other plasticizers, PCE has advantages in water reduction, slump retention, and compatibility. During the synthesis of polycarboxylates, the active groups can react with the -COOH groups on the main and side chains of the polycarboxylate, and -C=C- double bond can be connected to the main chain.
Many scholars are devoted to improving the structure and performance of PCE. Yu et al. (2016) conducted synthesis using butenyl alkylene polyoxyethylene-polyoxypropylene ether (BAPP) as the macromonomer and 2,2′-azoisobutyronitrile as the initiator for 48 h at 70°Cin N2 atmosphere, which greatly accelerated cement hydration of polycarboxylate. In Liu’s research (Liu et al., 2014), at 130–150°C, polycarboxylate (amide-type PCE) of five amide structures was produced by the amidation reaction between polyacrylic acid (PAA) and amino-terminated methoxy polyethylene glycol (amino-PEG). It was found that the amide-type PCE significantly facilitated the formation of strong hydrogen bonds between amide and polyether chains. Plank et al. (Plank et al., 2016) used acrylic acid and isoprenoxy polyethylene glycol (IPEG) to synthesize polycarboxylates at 60°C and used 13C NMR spectroscopy in characterization, finding that optimal PCE dispersion effect was obtained when the molecular weight (Mw) was about 40,000 in narrow distribution. Lange and Plank (2016) used acrylic acid and ω-methoxy polyethylene glycol methacrylate to synthesize non-adsorbent polycarboxylate within 4 h at 80°C. Research results showed that such non-adsorbent polycarboxylate can also significantly improve the Portland cement flowability at a low water–binder ratio.
In addition to polycarboxylate synthesis by heating, in terms of synthesis at indoor temperature, Jiang et al. (2013) used the redox method to synthesize PCE at indoor temperature (20–40°C). When the dosage was 0.2%, the initial flowability could reach 295 mm. Yang et al. (Yang et al., 2011) used free radical copolymerization of dendritic activated macromers and acrylic acid to synthesize PCE at indoor temperature. However, due to the indoor temperature changes and restrictions in synthesis conditions, the synthesized PCE exhibited unstable performance. Therefore, they believed that PCE synthesized at indoor temperature is still inferior to PCE synthesized at high temperature.
In this study, organosiloxane modified polyurethane with appropriate molecular weight was used as the side chain to be connected with the polycarboxylate acid backbone, while other functional groups such as carboxyl, hydroxyl, and polyoxyethylene group were introduced into the molecular structure of polycarboxylate. The best indoor temperature synthesis process of polycarboxylate was obtained through orthogonal design. Also, this article studied their interaction with Portland cement and the law of influence, which lays a theoretical basis for the structure design, synthesis, and selection of water reducers.
P·I 42.5 cement, with an average particle size of 36.96 μm, is shown in Table 1. Common commercially available polycarboxylates, C-PCE-1 and C-PCE-2, are shown in Figure 1.
The used synthetic raw materials include isophorone diisocyanate, hydroxy-terminated siloxane, polyether glycol, N-methylpyrrolidone, 1,4-butanediol, dimethylolpropionic acid, P·I 42.5 cement, isopentenyl polyether (TPEG) with molecular weight 2,400; analytically pure acrylic acid (AA), mercaptoacetic acid, p-toluene sulfonic acid, hydroquinone, benzoyl peroxide, polyethylene glycol-200 (PEG-200), hydrogen peroxide, ascorbic acid (Vc), ammonium persulfate, dibutyltin dilaurate, and deionized water. All chemicals are of analytical purity.
In the synthesis of the side chain, alcohol and amine compounds containing hydroxyl or amino groups were introduced in the main chain of polycarboxylate molecules, which increased the number of short branches, promoted alternate distribution of polyether long branches, and branched short chains of the chain extender of alcohol and amine compounds, thereby increasing dispersibility and adaptability of the water reducer. The specific operations are as follows.
Place 22.2 g of isophorone diisocyanate in a three-necked flask, and use a dropping funnel to dropwise add polyethylene glycol 1,000 containing dibutyltin dilaurate (25 g polyethylene glycol 1,000 contained 0.2 g dilaurate and N-methylpyrrolidone solution of dimethylolpropionic acid; 3.35 g dimethylolpropionic acid was dissolved in 5 ml N-methylpyrrolidone). Then, add 50 g water, heat to 70°C, and keep warm, and after that dropwise add a mixed solution of hydroxyl-terminated polysiloxane and 1,4-butanediol (9 g hydroxyl-terminated polysiloxane mixed with 3 g 1,4-butanediol), 2.5 g ethylenediamine, and 1.5 g sodium dodecylbenzene sulfonate. Stir after the addition was complete, and when the mass percentage of free -NCO in the mixed solution was detected to be 16%, stop heating to obtain a polyurethane prepolymer. The principle of side chain reaction was shown in Figure 2.
The designed polycarboxylate molecular structure is shown in Figure 3. To ensure equal molar concentration of double bonds in the system, the molar ratio of acrylic acid to TPEG was adjusted. TPEG 120g, purified water 80ml, and PEG -200 10 g were stirred well in a 250 ml four-necked flask. Then, 0.1 g dibutyltin dilaurate, 1.2 g p-toluenesulfonic acid, and 30% hydrogen peroxide were added to prepare A and B two-component solutions for later use.
Group A: 10.8 g AA, 0.384 g thioglycolic acid, and 25 g deionized water.
Group B: 3.4 g Vc, 0.3 g ammonium persulfate, and 25 g deionized water.
Components A and B were added into the beaker at a rate of 2 ml/min using a peristaltic pump, and the process lasted for about 2.5 h. After keeping it for a period of time, adjust the PH value to 6-7 with NaOH to obtain the polycarboxylate mother liquor M-PCE. The radical polymerization reactions and chemical structure of M-PCE are shown in Figure 3.
In addition, for comparison experiments, the above step 1.3 can be performed separately to synthesize a common unmodified polycarboxylate (O-PCE), as shown in Figure 4. Moreover, in order to control the chain reaction and carry out future research, the concentration of free radicals and the molar ratio of AA and TPEG needed to be adjusted. Please find the orthogonal experiment study in Section 2.1 for details.
The adsorption equilibrium was obtained using a constant temperature shaker before performing suction filtration. The resulting filtrate was centrifuged, and the supernatant was taken out and centrifuged twice. The residual concentration of polycarboxylate in the clear liquid was measured. Then, calculate the amount of polycarboxylate adsorbed to the surface of cement particles using the following formula:
where Qe is the adsorption capacity, unit mg·g−1; C0 is the concentration of polycarboxylate solution before adsorption, unit mg·g−1; Ce is the equilibrium concentration of polycarboxylate after adsorption, unit mg·g−1; V is the solution volume, unit l; and M is the cement mass, unit g.
The water reducer solution was prepared according to the designed water–binder ratio and water reducer dosage, mixed with the cementitious material, stirred magnetically for 10 min, oscillated on an oscillator to separate the gelled slurry with a centrifuge for 10 min. The supernatant after separation was taken out and then filtered by suction through a 0.45 μm nylon microporous membrane. The filtrate was transferred to a volumetric flask and diluted 100 times with deionized water. The diluted solution was tested by the Liquid TOC to detect the carbon content, calculate the concentration of PCE water reducer in the solution, and then infer the adsorption. The polycarboxylate PC dosage was 0.2%, the water–cement ratio was 0.4, and the cement dosage was 50 g.
The hydration heat release rate and heat release of the cementitious material paste were quantitatively analyzed using an eight-channel isothermal microcalorimeter. Put 4 g cementitious material in a beaker to test hydration heat of Portland cement sample at the 72nd hour under polycarboxylate solid content of 0.2%, with water–binder ratio of 0.4. The ambient temperature was controlled at 20 ± 1°C.
Put 50 g cementitious material in a beaker, and mix the polycarboxylate (the solid content was 0, 0.1, 0.2, 0.3, 0.4, and 0.5% of the mass of the cementitious material) with certain water in the beaker, with water–binder ratio of 0.4. By stirring at a low rate for 2 min and then at a high rate for 1 min, the Zeta potential of cement paste under different water–binder ratios and polycarboxylate contents was tested.
1) The surface tension test of the synthesized polycarboxylate was carried out under different concentrations using the A-60 automatic surface tension meter manufactured by Kino Industries Co., Ltd. of the United States.
2) Liquid phase surface tension test on Portland cement paste: put 50 g Portland cement in a beaker, fix the water–binder ratio to 0.4, and mix polycarboxylate (the solid content was 0, 0.1, 0.2, 0.3, 0.4, and 0.5% of the mass of the cementitious material) with 20 g water, stir at a low rate for 2 min and then a high rate for 1 min. Afterward, the cement paste was centrifuged to collect the supernatant and test the liquid phase surface tension.
According to GB/T8077-2000 “Test Method for the Homogeneity of Concrete Admixtures,” the initial flowability, 1 and 2 h cement paste flowability was tested by the hollow cylindrical mold test. Flowability of four kinds of polycarboxylates was tested under Portland cement mass of 300 g, water–cement ratio of 0.29, and polycarboxylate solid content of 0.15%.
By investigating the law of synthesis of polycarboxylates at indoor temperature, referring to relevant literature and experimental experience, a four-factor and three-level orthogonal experiment L9 (34) was performed for the synthesis of polycarboxylates at indoor temperature. When using the orthogonal table to arrange the experiment, we can select representative experimental conditions from the multiple experimental conditions and infer better production conditions through a small number of experiments. At the same time, it is possible to make further statistical analysis to get more accurate results. Based on single factor experiments, n (TGA), n (H2O2), n (AA): n (TPEG), n (H2O2): n (APS): n (Vc) are considered as the four primary factors that affect the dispersion performance of ether polycarboxylates. Therefore, a four-factor and three-level orthogonal experiment was designed, as shown in Table 2. The effect of the polycarboxylate synthesized by the above factors on the adsorption of Portland cement was studied, with results shown in Table 3.
To comprehensively evaluate the effect of various factors on the saturated adsorption Qem and surface tension, the composite indicators were obtained after comprehensive processing of the two indicators and listed in the table. The specific method is to firstly set the maximum value of saturated adsorption Qem and surface tension to 100 and the minimum value to 0 so that the other measured values of the two indicators are converted into a percentage system. Considering that the cement paste flowability and macromonomer conversion rate have the same proportion, the composite indicator was calculated by the weighted average of 50% proportion each. In the table, K1–K3 is the mean value of the composite indicators at each level, and R is the range. According to analysis of the above results, it is the best synthesis process and the order of influence decreases sequentially, A1>D2>C2>B3, namely, n (TGA) = 0.01, n (H2O2):n (APS):n (Vc) = 15:1:1, n (AA): n (TPEG) = 2:1, and n (H2O2) = 0.05 mol.
Polycarboxylate was prepared under 40°C for 4 h. The dispersibility was marked as M-PCE, as shown in Table 4.
At 20°C, test the adsorption values of different polycarboxylates against Portland cement, as shown in Figure 5.
FIGURE 5. Adsorbed amount of polycarboxylate molecules on the surface of Portland cement surface at different dosages (20°C).
From Figure 5, it can be seen that, as the PCE dosage increases, the microscopic flocculation structure of the cementitious system changes. After the addition of PCE molecule, due to its high negative charge, it will be quickly adsorbed to the surface of the gel particles and early hydration products and generate electrostatic repulsion. On the one hand, the gel particles are wrapped, which delays hydration, and on the other hand, the gel particles wrapped by the hydration product are released, so that the flocculation structure of the gel particles disintegrates. When a sufficient amount of polycarboxylate was added, the flocculation structure in the cementitious system was completely disintegrated, and the gel particles were well dispersed. The results in Figure 6 show, with the extension of reaction time, the adsorption capacity of the two polycarboxylates will gradually increase and approach a saturation value. Self-made polycarboxylates have greater adsorption than C-PCE-1 and C-PCE-2. After the addition of polycarboxylate PCE molecule, due to its high negative charge, it will be quickly adsorbed to the surface of the gel particles and early hydration products and generate electrostatic repulsion. On the one hand, the gel particles are wrapped by a water reducer, which delays hydration, and on the other hand, the gel particles wrapped by the hydration product are released, so that the flocculation structure of the gel particles disintegrates. Therefore, as the reaction time extended, more and more polycarboxylate would adsorb to the surface of the gel particles and its hydration products until the gel particles reached the highest degree of hydration (the highest degree of hydration within 2 h), with adsorption tending to be balanced.
In addition, an obvious common trend is that, within 10–20 min, the adsorption of the water reducer will increase sharply, which can basically reach about 2/3 or even 3/4 of the saturated adsorption. Subsequently, the adsorption will remain relatively stable or there will be a slight decrease. After 0.5 h, adsorption will continue to slowly increase until the saturated adsorption. Adsorption undergoes a rapid increase in the initial stage. With the addition of polycarboxylate, due to its high negative charge, it will be quickly adsorbed to the surface of gel particles and early hydration products and generate electrostatic repulsion. The subsequent relatively stable or small decline is possible because, with the hydration of the gel particles, the gel particles in the cementitious system will desorb from the water reducer molecules. At the same time, the newly added hydration products will create a shielding effect on the water reducer adsorption layer, resulting in a stable or slight decline in adsorption. In the subsequent stage with adsorption slowly increasing to the saturated adsorption, it is generally believed that, as the degree of hydration increases until full hydration, the hydration products continue to increase, making adsorption slowly increase until the saturated adsorption.
According to the graph obtained from the experiment, the Lagergren adsorption rate equation can be used to fit Figure 6 and Figure 7:
where t represents the adsorption time, min; Qe is the adsorption at time t, mg·g−1; Qem is the saturated adsorption at adsorption equilibrium, mg·g−1; F = Qe/Qem; and k represents the apparent adsorption rate constant of the first-order kinetic equation, min−1. Use -Ln (1-F) to plot t for linear fitting. The results are shown in Figures 8, 9. The adsorption rate k can be calculated according to the slope of the straight line, with the calculation results shown in Tables 5-6.
FIGURE 6. Adsorption amount of polycarboxylate molecules on the surface of Portland cement at 20°C (0.2% dosage).
FIGURE 7. Adsorbed amount of polycarboxylate molecules at different times and temperatures (0.2% dosage).
FIGURE 8. Lagergren fitted line of adsorption rate equation of polycarboxylate at cement particle surfaces (20°C).
FIGURE 9. Lagergren fitted line of adsorption rate equation of M-PCE at cement particle surfaces at different temperatures: (A) M-PCE and (B) O-PCE.
TABLE 6. Fitted values of Lageren adsorption rate equation derived from polycarboxylate at cement particles surfaces.
According to the Arrhenius equation, the apparent adsorption activation energy can be calculated:
where k0 represents the pre-exponential factor (frequency factor), min−1; Ea represents the apparent activation energy, KJ·mol−1; R is the molar gas constant, R = 8.3145 × 10–3 kJ·mol-1·K−1; and T is the adsorption temperature, K. Plot 1/T using Lnk, with the result shown in Figure 10. According to the intercept and slope of the straight line, k0 and Ea can be calculated, with the calculation results shown in Tables 5-6.
It can be seen from Tables 5-6 that the correlation coefficient of polycarboxylate on the Lagergren model is greater than 0.93, and the fitting effect is good, indicating that the isothermal adsorption of M-PCE, O-PCE, C-PCE-1, and C-PCE-1 follows the Lagergren model, which is consistent with the results of Hsu (1999) and Peng et al. (2005). The saturated adsorption (Qem) and adsorption rate constant (k) of M-PCE increase from 1.45 mg g−1 and 0.0390 min−1 to 1.77 mg g−1 and 0.0474 min−1, respectively. The saturated adsorption and adsorption rate constant of O-PCE polycarboxylate are only 1.55 mg g−1 and 0.0382 min−1 at 40°C, respectively. In addition, M-PCE has a low slope (k) and apparent activation energy (Ea). This suggests that M-PCE is more easily adsorbed by cement, and the saturated adsorption state can be reached more quickly, as shown in Figure 11. In this study, by replacing the carboxylic acid component with methylsiloxane, the adsorption rate of M-PCE on cement was enhanced. Yu et al. (2016) proved that silicate formed strong covalent bonds with inorganic chains of CSH and siloxane groups. Due to the increased electrostatic interaction between COO- and aluminate, the bigger function of methylsiloxane led to bigger adsorption (Plank et al., 2008). However, the adsorption of electropositive aluminates by ordinary polycarboxylates (O-PCE, C-PCEs) was based on electrostatic interaction with carboxylate groups, so the adsorption effect was weakened.
Unlike O-PCE and C-PCEs, M-PCE may produce different hydration effects on Portland cement due to the incorporation of organosiloxane groups. Figure 12 shows the effect of different polycarboxylate dosage on the hydration heat of Portland cement paste under water–binder ratio of 0.4.
FIGURE 12. Influence of polycarboxylate on the hydration of cement pastes: (A) heat evolution and (B) hydration heat.
The main hydration equations in cementitious materials are as follows:
The hydrolysis reaction of organosiloxane is as follows:
As can be seen from Figure 12, incorporation of O-PCE or C-PCEs delayed the hydration of Portland cement. For this reason, the M-PCE molecules adsorbed restrict the diffusion of water and ions in cement mineral and pore solution interface, and the chelation formed inhibited the nucleation and precipitation of hydrate products (Kong et al., 2016). Differently, M-PCE does not delay the hydration of Portland cement, which is mainly due to the fact that the high content of carboxylate groups in PCE brought about more adsorption sites, making cement particles better wrapped and dispersed in the solution. However, polyacrylic acid (PAA) homopolymers formed under excess AA monomers can also be adsorbed on the cement surface, thereby reducing the hydration rate (Zhou et al., 2017). In addition, in Kong’s research (Švegl et al., 2008), polycarboxylates were prepared by grafting tetraethoxysilane into the main chain. Reports have confirmed that polyurethane side chain can be completely hydrolyzed, and the hydrolysates of methanol and ethanol in M-PCE insignificantly decline the main hydration peak, without delay (Scrivener and Nonat, 2011). Therefore, it can be inferred that M-PCE does not delay cement hydration as a result of silane molecules.
After adding C-PCE-1, C-PCE-2, and O-PCE, the heat release rate and total heat release of cement hydration exhibited better mitigation and reduction effects. Due to the incorporation of polycarboxylate, in the initial cement hydration stage, on the one hand, the adsorption of water reducer acted on the surface of cement particles; on the other hand, in the alkaline medium of cement hydration, the active group in the molecular chain of water reducer (such as -COO-, -SO3-) acted with hydration-generated ions (such as Ca2+) to form unstable complexes, which delayed cement hydration and inhibited the precipitation and growth of minerals in the initial phase (Kong et al., 2016). Moreover, the effect strengthened with the increase of dosage; that is, the dissolution peak decreased. Due to adsorption, complexation, and retardation effects of the polycarboxylate side chain on Portland cement, hydration of hydrated minerals was inhibited, and more time was needed to break the hydration energy barrier (Wang and Wang, 2003; Ylmén et al., 2009). Therefore, the longer induction period of hydration was manifested as the delay and weakening of the second exothermic peak. Similarly, with the increase of polycarboxylate dosage, the retardation effect became more obvious, which was manifested as a shift of the second exothermic peak to the right (Ylmén et al., 2010).
The effect of polycarboxylate on the Zeta potential of Portland cement under different dosages is shown in Figure 13.
As seen from the above figure, it can be known that, as the polycarboxylate dosage increases, the absolute value of zeta potential in the cement paste exhibits a downward trend. Zeta potential has a close relation with the electrostatic repulsion between molecules. The Debye–Hückel formula is shown as follows:
where FES is the electrostatic repulsion; ε is the relative permittivity of water; εo is the vacuum permittivity;
The adsorption of polycarboxylate to the Portland cement surface conforms to the Langmuir adsorption equation (LI et al., 2014). It can be seen from formula (4) that, as the polycarboxylate increases, the thickness l of the adsorption layer between two particles remains unchanged. As the distance h gets smaller, the electrostatic repulsion gets smaller (Wang, 2009), the system stability becomes worse, and the zeta potential value decreases. In addition, the zeta potential values of O-PCE, C-PCE-1, and C-PCE-2 are positive, but the value of M-PCE is negative. The main mineral components of cement are C2S, C3S, C3A, and C4AF. The hydration products of C2S and C3S are negatively charged, while those of C3A and C4AF are positively charged. Since aluminate has stronger solubility than silicate, the hydration product is positively charged, and the measured zeta potential is positive (Schmid and Plank, 2021). Although some negatively charged polycarboxylates were added, Zeta potential showed a decreasing trend, but its content remained small, with low water–cement ratio, which, however, did not affect the hydration products of aluminate. Therefore, the zeta potentials of these three polycarboxylates were positive. For M-PCE, the side chain was partially replaced by siloxane with a high negative charge, so M-PCE reduced Zeta potential to a bigger negative value, which is attributed to the higher polymer adsorption, as discussed in Figure 7. When cement particles contacted water, positive ions such as K+ and Na+ were dissolved in the interstitial solution, while SiO33− and AlO33− skeletons were maintained. Such a phenomenon led to a latent cement surface. Therefore, the inner layer is composed of positive ions and the outer layer is composed of negative ions (Zhang and Kong, 2015). The electronegative groups in the main chain will be adsorbed on the electropositive outer layer through electrostatic adhesion. Therefore, the Zeta potential of the cement paste also changed from positive value to negative value. The higher adsorption of anionic polymers against solid particles leads to a decreased Zeta potential and a greater electrostatic barrier effect, while greater electrostatic barrier effect contributes to higher dispersibility (Plank and Hirsch, 2007).
This study investigates the surface tension of polycarboxylates with different mass fractions and the effect of different polycarboxylate dosages on the liquid phase surface tension of Portland cement, with results shown in Figures 14, 15.
It can be seen from Figures 14, 15 that, as the polycarboxylate mass fraction increases, the solution surface tension displays a continuous downward trend. It is because, under higher mass fraction, there are more hydrophobic groups in the solution, leading to declined surface tension. In addition, we found that M-PCE had the biggest decline in surface tension. From the point of view of liquid phase surface tension of Portland cement, the largest drop was observed after incorporation of M-PCE, with a decrease of 20.4%. For this reason, as the polycarboxylate dosage increases, polycarboxylate molecules cannot be adsorbed and maintained in the liquid phase, so there are more and more hydrophobic groups on the skeleton, such as long-chain alkyl groups, which are directionally aligned on the aqueous solution surface, leading to reduced surface tension of the liquid. M-PCE has the largest decrease in liquid surface tension because the organosiloxane group on the polyurethane side chain in its molecular structure has very strong hydrophobicity (Fan et al., 2012), resulting in its greater surface tension compared to other PCEs as its dosage in the cement increases.
This study investigated the cement paste flowability of polycarboxylates under different dosages as well as flowability retention under dosage of 0.15%, with results shown in Figures 16, 17.
As shown in Figures 16, 17, when the polycarboxylate content increases, the initial flowability of the cement paste increases sharply. As the M-PCE amount increases from 0 to 0.5%, the maximum increase in cement is about 193%. The enhanced dispersibility of M-PCE is due to the chemical bonds being induced by the siloxane groups in the M-PCE and silicate phase promoting the dispersibility of M-PCE (Yan et al., 2017). In addition, due to its chemical structure, M-PCE has longer side chains than PCE (Borget et al., 2005), so M-PCE has better dispersibility in cement, which is consistent with the results of Kong et al. (2015). Regarding the reason for the excellent dispersing ability, the siloxane groups in the polyurethane side chains produced by the hydrolysis of the alkoxy groups in the silane molecules act as anchoring groups, which facilitates the adsorption of silane molecules to cement particles. Moreover, the siloxane chain provides spatial repulsion between the cement particles, which enhances the dispersion effect. The anchoring effect of siloxane groups on cement or hydration products has been confirmed by the enhanced adsorption of silane-modified polycarboxylate superplasticizer in cement paste (Švegl et al., 2008). In addition, it was also found that although M-PCE had the biggest initial flowability, the four polycarboxylates exhibited good flowability retention.
The following conclusions could be drawn based on the above experimental results and discussions:
1) Appropriately increasing the molar ratio of acrylic acid to TPEG under the same circumstances will help improve polycarboxylate dispersion performance. The best indoor temperature synthesis process is as follows: n (TGA) = 0.01, n (H2O2): n (APS): n (Vc) = 15:1:1, n (AA): n (TPEG) = 2:1, and n (H2O2) = 0.05 mol.
2) Since the siloxane groups in Portland cement and polycarboxylate molecules form covalent bonds, M-PCE has higher adsorption than O-PCE and C-PCE, resulting in a higher adsorbability. In addition, compared with O-PCE and C-PCEs, the adsorption amount of M-PCE was increased by 14.1%, and the maximum adsorption rate was increased by 24%.
3) Under the same dosage, the incorporation of M-PCE had a promoting effect on the hydration of Portland cement. Due to the shielding effect of the long-chain alkyl group, O-PCE, C-PCE-1, and C -PCE-2 showed a certain hydration delay effect.
4) The Zeta potential value of M-PCE was negative, but its absolute value was higher than the Zeta potential of the other three polycarboxylates under the same circumstances, indicating that the Portland cement paste was more stable after incorporation of M-PCE.
5) As the PCE dosage increased, the liquid phase surface tension of Portland cement continually decreased, where M-PCE exhibited the smallest change. In terms of cement paste flowability and its retention, M-PCE showed the strongest dispersibility, which was also because the formation of hydrogen bonds in organosiloxane of M-PCE and Portland cement promoted the dispersibility of M-PCE.
The original contributions presented in the study are included in the article/Supplementary Material; further inquiries can be directed to the corresponding author.
SX conceptualized the study, was responsible for methodology, investigated the data, performed data curation and formal analysis, and wrote the original draft. YG was involved in project administration, funding acquisition, and supervision. YT revised the manuscript.
The authors gratefully acknowledge the financial support from National Natural Science Foundation of China (General Program:51978080), National Natural Science Foundation of China and Civil Aviation Administration of China (U1833127), Natural Science Foundation of Hunan Province (2021JJ40602) and Scientific Research Project of Hunan Provincial Department of Education(20B014).
The authors declare that the research was conducted in the absence of any commercial or financial relationships that could be construed as a potential conflict of interest.
All claims expressed in this article are solely those of the authors and do not necessarily represent those of their affiliated organizations, or those of the publisher, the editors, and the reviewers. Any product that may be evaluated in this article, or claim that may be made by its manufacturer, is not guaranteed or endorsed by the publisher.
Borget, P., Galmiche, L., Le Meins, J.-F., and Lafuma, F. (2005). Microstructural Characterisation and Behaviour in Different Salt Solutions of Sodium Polymethacrylate-G-PEO Comb Copolymers. Colloids Surf. A: Physicochemical Eng. Aspects 260, 173–182. doi:10.1016/j.colsurfa.2005.03.008
Fan, W., Stoffelbach, F., Rieger, J., Regnaud, L., Vichot, A., Bresson, B., et al. (2012). A New Class of Organosilane-Modified Polycarboxylate Superplasticizers with Low Sulfate Sensitivity. Cement Concrete Res. 42 (1), 166–172. doi:10.1016/j.cemconres.2011.09.006
Hsu, K. C. (1999). Effect of Addition Time of a Superplasticizer on Cement Adsorption and on Concrete Workability. Cem. Concr. Compos. 21 (5-6), 425–430. doi:10.1016/s0958-9465(99)00030-x
Jiang, Z., Fang, Y., Guo, X., Lin, T., Guan, M., and You, R. (2013). Preparation of an Extra High-Concentration Polycarboxylate Superplasticizer. New Build. Mater. 3, 29–31.
Kong, F.-R., Pan, L.-S., Wang, C.-M., Zhang, D.-L., and Xu, N. (2016). Effects of Polycarboxylate Superplasticizers with Different Molecular Structure on the Hydration Behavior of Cement Paste. Construction Building Mater. 105, 545–553. doi:10.1016/j.conbuildmat.2015.12.178
Kong, X.-M., Liu, H., Lu, Z.-B., and Wang, D.-M. (2015). The Influence of Silanes on Hydration and Strength Development of Cementitious Systems. Cement Concrete Res. 67, 168–178. doi:10.1016/j.cemconres.2014.10.008
Lange, A., and Plank, J. (2016). Contribution of Non-adsorbing Polymers to Cement Dispersion. Cement Concrete Res. 79, 131–136. doi:10.1016/j.cemconres.2015.09.003
Li, C.-Z., Feng, N.-Q., Li, Y.-D., and Chen, R.-J. (2005). Effects of Polyethlene Oxide Chains on the Performance of Polycarboxylate-Type Water-Reducers. Cement Concrete Res. 35 (5), 867–873. doi:10.1016/j.cemconres.2004.04.031
Li, Y., Yang, C., Zhang, Y., Zheng, J., Guo, H., and Lu, M. (2014). Study on Dispersion, Adsorption and Flow Retaining Behaviors of Cement Mortars with TPEG-Type Polyether Kind Polycarboxylate Superplasticizers. Construction Building Mater. 64, 324–332. doi:10.1016/j.conbuildmat.2014.04.050
Liu, X., Wang, Z., Zhu, J., Zheng, Y., Cui, S., Lan, M., et al. (2014). Synthesis, Characterization and Performance of a Polycarboxylate Superplasticizer with Amide Structure. Colloids Surf. A: Physicochemical Eng. Aspects 448, 119–129. doi:10.1016/j.colsurfa.2014.02.022
Peng, J., Qu, J., Zhang, J., Chen, M., and Wan, T. (2005). Adsorption Characteristics of Water-Reducing Agents on gypsum Surface and its Effect on the Rheology of gypsum Plaster. Cement Concrete Res. 35 (3), 527–531. doi:10.1016/j.cemconres.2004.04.016
Plank, J., and Bian, H. (2010). Method to Assess the Quality of Casein Used as Superplasticizer in Self-Levelling Compounds. Cement Concrete Res. 40 (5), 710–715. doi:10.1016/j.cemconres.2010.01.005
Plank, J., and Hirsch, C. (2007). Impact of Zeta Potential of Early Cement Hydration Phases on Superplasticizer Adsorption. Cement Concrete Res. 37 (4), 537–542. doi:10.1016/j.cemconres.2007.01.007
Plank, J., Li, H., Ilg, M., Pickelmann, J., Eisenreich, W., Yao, Y., et al. (2016). A Microstructural Analysis of Isoprenol Ether-Based Polycarboxylates and the Impact of Structural Motifs on the Dispersing Effectiveness. Cement Concrete Res. 84, 20–29. doi:10.1016/j.cemconres.2016.02.010
Plank, J., Pöllmann, K., Zouaoui, N., Andres, P. R., and Schaefer, C. (2008). Synthesis and Performance of Methacrylic Ester Based Polycarboxylate Superplasticizers Possessing Hydroxy Terminated Poly(ethylene Glycol) Side Chains. Cement Concrete Res. 38 (10), 1210–1216. doi:10.1016/j.cemconres.2008.01.007
Schmid, M., and Plank, J. (2021). Interaction of Individual Meta Clays with Polycarboxylate (PCE) Superplasticizers in Cement Investigated via Dispersion, Zeta Potential and Sorption Measurements. Appl. Clay Sci. 207, 106092. doi:10.1016/j.clay.2021.106092
Scrivener, K. L., and Nonat, A. (2011). Hydration of Cementitious Materials, Present and Future. Cement Concrete Res. 41, 651–665. doi:10.1016/j.cemconres.2011.03.026
Švegl, F., Šuput-Strupi, J., Škrlep, L., and Kalcher, K. (2008). The Influence of Aminosilanes on Macroscopic Properties of Cement Paste. Cem. Concr. Res. 38, 945–954. doi:10.1016/j.cemconres.2008.02.006
Wang, B., and Wang, L. (2003). Effects of Super Retarder on the Hydration of Portland Cement. J. Building Mater. 6 (1), 90–94. doi:10.3969/j.issn.1007-9629.2003.01.018
Wang, Z. M. (2009). “Polycarboxylate Superplasticizer-Preparation • Performance and Application (In Chinese),” in Preparation of High Performance Polycarboxylate (Beijing: China Architecture & Building Press), 123–137.
Yan, He., Zhang, X., and Hooton, R. D. (2017). Effects of Organosilane-Modified Polycarboxylate Superplasticizer on the Flowability and Hydration Properties of Cement Paste[J]. Constr. Build. Mater. 132, 112–123. doi:10.1016/j.conbuildmat.2016.11.122
Yang, Y., Ran, Q. P., Liu, J. P., Zhang, Z. Y., and Miao, C. W. (2011). Synthesis of Comb-Branched Polycarboxylate Superplasticizers. New Build. Mater. 7, 54–57. doi:10.3969/j.issn.1001-702X.2011.07.017
Ylmén, R., Jäglid, U., Steenari, B.-M., and Panas, I. (2009). Early Hydration and Setting of Portland Cement Monitored by IR, SEM and Vicat Techniques. Cement Concrete Res. 39 (5), 433–439. doi:10.1016/j.cemconres.2009.01.017
Ylmén, R., Wadsö, L., and Panas, I. (2010). Insights into Early Hydration of Portland limestone Cement from Infrared Spectroscopy and Isothermal Calorimetry. Cement Concrete Res. 40 (10), 1541–1546. doi:10.1016/j.cemconres.2010.06.008
Yu, B., Zeng, Z., Ren, Q., Chen, Y., Liang, M., and Zou, H. (2016). Study on the Performance of Polycarboxylate-Based Superplasticizers Synthesized by Reversible Addition-Fragmentation Chain Transfer (RAFT) Polymerization. J. Mol. Struct. 1120, 171–179. doi:10.1016/j.molstruc.2016.05.035
Zhang, Y., and Kong, X. (2015). Correlations of the Dispersing Capability of NSF and PCE Types of Superplasticizer and Their Impacts on Cement Hydration with the Adsorption in Fresh Cement Pastes. Cement Concrete Res. 69, 1–9. doi:10.1016/j.cemconres.2014.11.009
Keywords: polyurethane-modified, polycarboxylate, radical polymerization, indoor temperature, interaction
Citation: Xiang S, Tan Y and Gao Y (2021) Synthesis of Comb-Polyurethane-Modified Polycarboxylate at Indoor Temperature and Its Interaction With Portland Cement. Front. Mater. 8:725328. doi: 10.3389/fmats.2021.725328
Received: 15 June 2021; Accepted: 23 July 2021;
Published: 19 August 2021.
Edited by:
Eileen Harkin-Jones, Ulster University, United KingdomCopyright © 2021 Xiang, Tan and Gao. This is an open-access article distributed under the terms of the Creative Commons Attribution License (CC BY). The use, distribution or reproduction in other forums is permitted, provided the original author(s) and the copyright owner(s) are credited and that the original publication in this journal is cited, in accordance with accepted academic practice. No use, distribution or reproduction is permitted which does not comply with these terms.
*Correspondence: Yingli Gao, eWluZ2xpZ2FvQDEyNi5jb20=
Disclaimer: All claims expressed in this article are solely those of the authors and do not necessarily represent those of their affiliated organizations, or those of the publisher, the editors and the reviewers. Any product that may be evaluated in this article or claim that may be made by its manufacturer is not guaranteed or endorsed by the publisher.
Research integrity at Frontiers
Learn more about the work of our research integrity team to safeguard the quality of each article we publish.