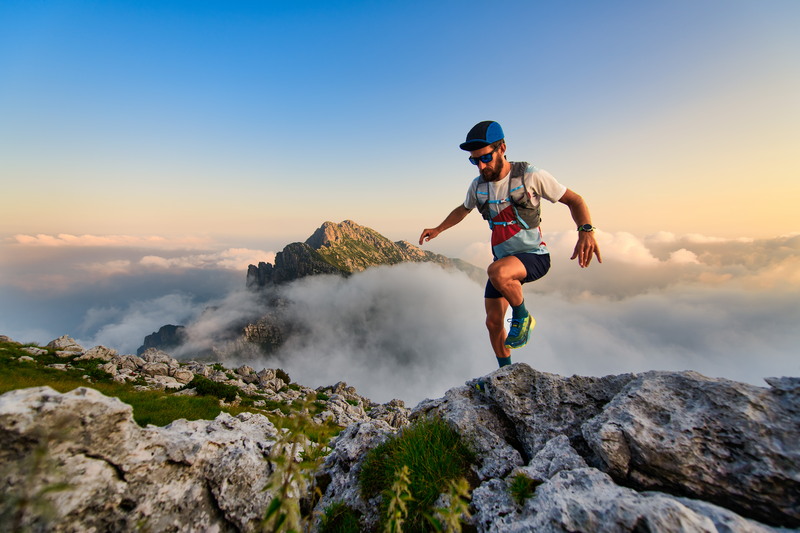
94% of researchers rate our articles as excellent or good
Learn more about the work of our research integrity team to safeguard the quality of each article we publish.
Find out more
ORIGINAL RESEARCH article
Front. Mater. , 05 July 2021
Sec. Structural Materials
Volume 8 - 2021 | https://doi.org/10.3389/fmats.2021.700118
This article is part of the Research Topic Non-BF Slag-based Green Cementitious Materials View all 20 articles
The coal mining technology of fully mechanized solid filling is an efficient and green mining method that integrates “sediment reduction” and “emission reduction.” However, the discharge of wasted gangue and surface subsidence are controlled by the amount of wasted gangue used in filling mining and the compaction rate of gangue filled into a goaf, respectively. To increase the consumption of wasted gangue and reduce surface subsidence, mixed gangue composed of equal-quality washed gangue and crushed gangue is proposed as a raw material for solid filling on the basis of gradation theory. Next, a screening experiment was performed to analyze the grain gradation of different specimens, and a compression experiment was executed to compare and analyze the compression characteristics. The results show that the nonuniformity coefficient of mixed gangue is 55.2 and the curvature coefficient is 1.53, which significantly improve the grain gradation of washed gangue. The degree of relative compaction of mixed gangue is 1.226, which is significantly lower than that of washed gangue, which is 1.33. The deformation modulus of mixed gangue is 23–135 MPa, which is better than that of washed gangue (26–100 MPa), indicating that the compressive resistance of mixed gangue is significantly improved. The case study of the Tangkou mine suggests that mixed gangue greatly promotes the consumption of wasted gangue and can effectively control the surface deformation.
• Mixed waste gangue is used as a filling material for solid backfilling mining.
• The gradation combination of filling gangue was significantly improved.
• More wasted gangue was consumed, and the compressive strength of the filling body was enhanced.
• The compression of the filling body was reduced, and the surface settlement was controlled.
Filling mining is a type of ecological protection mining technology that has been developed in recent years. The usage of this technology can process coal gangue and fly ash, two solid forms of waste from coal mines, and solid waste around cities while replacing coal resources under buildings (structures) such as villages, railways (roads) and overlying aquifers, and on floor pressurized water (referred to as “three under one on”). This is a type of scientific coal mining technology that is in line with the ecological mine development model of “lucid waters and lush mountains are invaluable assets,” advocated by President Xi Jinping, with great promotion and application prospects (Hu and Guo, 2018; Qian et al., 2018; Wang et al., 2018; Dong et al., 2019; Ma et al., 2019; Wang et al., 2020a; Dong et al., 2020; Liu et al., 2020; Ju et al., 2021). To date, three kinds of filling mining technology approaches have been developed in China: solid filling technology (Miao et al., 2010), paste filling technology (Zhou et al., 2010; Sun et al., 2018; Wu et al., 2020a), and high-water filling technology (Feng et al., 2010; Chang et al., 2018). Solid filling technology mainly includes fully mechanized solid filling technology, dumping gangue and filling technology, pneumatic filling technology, and the technology of coal gangue separation in underground coal flow and gangue powder pumping on-site. Due to the relatively mature filling system and equipment (the gangue feeding system, the storage system, and four-column and six-column filling support with a tamping mechanism) and the mining–filling process (single and double interlaced, and coal mining tamping), fully mechanized solid filling technology has become the main development direction of filling mining technology (Hu, 2012; Zhang et al., 2020; Zhang et al., 2019a; Guo et al., 2019). In the implementation of fully mechanized solid filling technology, the control effect of overlying strata and surface subsidence is determined by the final compaction rate of gangue in a goaf, which is equivalent to that of mining in thin coal seams. Therefore, relevant scholars have proposed the concept of “equivalent mining thickness” for surface subsidence control of fully mechanized solid filling technology (Zhang et al., 2011; Huang et al., 2012; Guo et al., 2014; Meng et al., 2020a). In summary, the study of how to reduce the final compaction ratio of gangue filled into goafs has become the key to popularizing applications and effectively predicting the control effect of surface subsidence.
At present, various scholars have performed preliminary experimental studies on compaction and deformation of gangue. Zhang Jixiong conducted compaction deformation tests on loose gangue and obtained the relationship among deformation, hulking coefficient, and compactness of the filling body and strain, as well as the characteristics related to the compaction time in the process of compaction (Miao and Zhang, 2007; Zhang, 2008). Through gangue compaction tests, Ma et al. (2003) summarized the trends of the change in the axial strain, transverse strain, Poisson’s ratio, and elastic modulus of loose gangue in the process of compaction, and analyzed the deformation mechanism of gangue during this process. Xu et al. (2011) adopted an MTS815.02 electrohydraulic servo rock mechanics test system and a self-designed compaction device to analyze the deformation characteristics of gangue–fly ash as a filling material in the compaction process. Hu Bingnan et al. adopted a large container, large particle size, and large load and simulated coal mass to perform 23 simulated gangue compression experiments, obtained the rule that the compression ratio is proportional to the particle size and inversely proportional to the lateral pressure, and analyzed the relationship among the compression ratio, lateral pressure and coal mass strength, particle size, and gangue gradation (Hu and Guo, 2009). Several scholars have studied the compaction characteristics of gangue with different gradations. Zhang Jinhong et al. conducted compression tests on gangue with seven groups of gradation schemes, showing that the content of gangue was maintained with a particle size range of 40–70 mm, and an increased content of gangue with a small particle size can minimize the compression amount of gangue filling materials (Zhang et al., 2012). As the main source of gangue in most domestic coal mines is washed gangue (maximum particle size ≤50 mm), while driving gangue (maximum particle size ≥100 mm) accounts for less gangue, the general treatment method of coal mines is to raise the driving gangue with the raw coal sulfur flow to the surface coal washery and then dispose it off separately (Li and Guo, 2018). The Zhuanlongwan coal mine was taken as an example, where the volume of gangue produced in 2019 was 2.266 million tons, of which the gangue produced by the coal washery accounted for 90% and the gangue produced by driving accounted for 10%. Driving gangue is usually not treated underground but mixed into raw coal sulfur and raised to the surface coal washery. The particle size of the washed gangue processed by the coal washery is basically the same, and the particle size is large. As the pores between the particles cannot be filled completely by the small particles, the bearing effect is limited to a certain extent (Meng et al., 2020b).
Therefore, in order to compare and analyze the grain gradation and compression characteristics of different gangue fillings, this study carried out screening experiment and compression experiment body based on the continuous gradation theory. The grain gradation curve shows that mixed gangue composed of washed gangue, and crushed gangue with equal quality has a certain gap with the theoretical optimal grain gradation, but considering the convenience of on-site construction, mixed gangue with equal quality is the optimal filling material. Simultaneously, the compression test indicates that the compressive properties of gangue with equal mixing mass are significantly increased. Adoption of mixed gangue with equal quality as filling material can effectively reduce the “equivalent mining height,” decrease the surface discharge of gangue, and provide theoretical and reference significance to improve the on-site filling rate of gangue materials.
The gradation of solid particles refers to a continuous gradation that is made up of solid particles with various particle sizes. This represents the quantity of the particle size in the bulk materials composed of different granularities, which is usually expressed as a percentage of the total amount (Fang et al., 2019). The cumulative curve of the particle size distribution obtained from the results of the particle size distribution can clearly reveal the thickness of solid materials, and the uniformity and continuity of the particle size distribution, thus allowing the quality of the material gradation to be determined (Chen et al., 2016; Wang et al., 2020b). The material uniformity or gradation can be analyzed based on the slope of the cumulative curve of the particle diameter. A steeper curve indicates that the sizes of the particles are almost the same, the particles are more uniform, and the gradation is poor, whereas a flat curve indicates that the size of particles is very different, the particles are uneven, and the grading is good (Cai et al., 2020; Wang et al., 2020c; Yao et al., 2020). According to the cumulative curve of the particle size, two quantitative indexes of the particle size distribution,
In the equation,
For a solid material, the following relationship is observed:
For rockfills with a high volume of rock, the specification (DL/T, 2007; DL/T, 2011) only requires that the particle content less than 5 mm shall not exceed 30%, and the fine particle content (less than 0.075 mm) shall not exceed 5%, without clear requirements on the overall composition of gradation; there is also no gradation requirement for transition material and cushion material. For gradation evaluation, currently, only gradation indicators exist, which apply to the largest diameter within 60 mm gradation index of coarse-grained soil; that is, when the nonuniformity coefficient
In the equation for Pd, d is the pore diameter passing through the sieve and D is the maximum particle size.
Fuller’s curve became the theoretical basis for the composition forms of various gradation curves, such as the n-method improved by Talbol. Talbol demonstrated that Fuller’s equation was an ideal gradation curve; in reality, there was a certain range of fluctuation required to achieve the maximum density, so Fuller’s equation was modified into the following expression:
When n = 0.3–0.7, there is good compactness; when n = 0.5, the maximum density curve is a parabola (Huang et al., 2019a; Wu et al., 2020b).
The main source of filling gangue was washed gangue (dmax ≤ 50 mm), which was used to fill gangue directly, and crushed gangue (dmax ≤ 16 mm) was used as auxiliary filling gangue. The experimental materials are sampled on site, washed gangue is directly obtained by the coal washery, the maximum diameter of washed gangue is 50 mm, and crushed gangue whose maximum diameter is less than 16 mm is obtained after the secondary crushing of washed gangue. The gradation parameters of washed gangue and crushed gangue were obtained by using a new standard stone screen, as shown in Table 1 and Table 2, respectively.
In light of Talbol’s method related to n, n is taken as 0.3, 0.5, and 0.7; the maximum particle size is 50 mm; and the corresponding continuous gradation curve diagram and screening gradation curve diagram are drawn in semilogarithmic coordinates, as shown in Figure 1. In the semilogarithmic curve diagram, the abscissa is expressed as the logarithm of the particle size (
According to Tables 1 and 2, p10 of washed gangue is only 1.51%, and the gradation curve of crushed gangue is above the continuous curve; that is, its fine content is far higher than that of the continuous gradation, and p10 is as high as 98.71%. Therefore, crushed gangue of equivalent mass can be mixed into washed gangue to compensate for the serious gradation defect of p10. Simultaneously, the content of coarse material larger than 28 mm for washed gangue is adjusted indirectly under the condition that the whole quality of loose gangue is not changed. Table 3 gives the gradation parameter table of filling gangue after equal-quality mixing, and its gradation curve is plotted in Figure 1. In the gradation curve of mixed gangue, the particle curve of Pd≤ 20 mm is between the curve of n = 0.3 and n = 0.5, and only the particle content of Pd≥ 20 mm is more than that of the continuous gradation curve, indicating that the gradation combination of mixed gangue is significantly better than that of washed gangue and crushed gangue.
The gradation of washed gangue, crushed gangue, and mixed gangue was evaluated by using the evaluation standard for a solid particle gradation. According to the data in Figure 1 and Tables 1–3 obtained by interpolation, the nonuniformity coefficient of washed gangue is 1.74, the curvature coefficient is 1.09, the nonuniformity coefficient of crushed gangue is 10.08, the curvature coefficient is 1.59, the nonuniformity coefficient of mixed gangue is 55.2, and the curvature coefficient is 1.53, as shown in Table 4. Obviously, the nonuniformity coefficient of washed gangue is small, and it is a poorly graded solid. The nonuniformity coefficients of gangue after crushing and in mixed gangue are large, but the nonuniformity coefficient of gangue after mixing is an excellent graded solid with the largest nonuniformity coefficient.
Because of the complexity of underground work, filling material processing, and the necessity of filling cost control, it is not possible to implement underground large-scale gradation restructuring to obtain a better filling effect. Thus, this study proposes a way to adjust the gradation of gangue filling bodies by mixing equal qualities of washed gangue and crushed waste.
As shown in Figure 2, a WAW-600B microcomputer was used as the compacting and loading equipment to control the electrohydraulic servo universal testing machine. Hydraulic power servo control technology, electrohydraulic servo control technology, computer data acquisition and processing, high-precision material testing equipment with closed-loop control, and automatic detection utilized in this testing equipment can realize the closed-loop control of constant-rate loading, constant-rate deformation, constant-rate displacement, and constant-rate strain to verify the performance of materials (Li et al., 2019).
As the physical drawing of the design shows in Figure 3, all the instruments are made of 45# steel with a yield strength of no less than 355 MPa. The filling gangue apparatus is designed as a steel cylinder with an inner diameter of 125 mm, wall thickness of 10 mm, outer diameter of 145 mm, and height of 300 mm. The experimental charging height is 250 mm, the charging volume is 3.06 × 10–3 m3, and the weight is approximately 4.3 kg. The auxiliary force transmission instrument is a steel cylinder with a diameter of 100 mm, height of 150 mm, and weight of approximately 9.3 kg.
The compaction experiment of filling coal gangue was performed with the above experimental device, according to the method of compaction testing of solid backfilling materials (Nb/T, 2014). In light of the conditions of the apparatuses and equipment, the maximum permissible particle size of the gangue sample was 25 mm, and the sample was prepared by a similar method of gradation. Before the experiment, the mass of each fraction of particle size was measured on the basis of the experimental design scheme and then evenly mixed and loaded into the compacted steel cylinder. The steel cylinder was used to impose the load on the gangue specimen, and experimental data such as the load and compression displacement of gangue were recorded during the loading process. The laboratory gradation tables for washed gangue and gangue with the continuous gradation of Taltol’s n-method (n is 0.3, 0.5, and 0.7) are shown in Tables 5 and 6, respectively, and the laboratory gradation tables of mixed gangue are shown in Tables 7 and 8, respectively.
To reduce the friction between gangue and the steel cylinder wall during the process of compression, a layer of grease was smeared on the inner wall of the steel cylinder before each test, and then the screened gangue was uniformly mixed and filled according to the corresponding gradation table. The charge of each test was controlled at 4,300 g, the initial filling height h0 was measured, and the initial bulk density γ0 was calculated. Force control was adopted in the compaction experiment, the maximum axial compressive stress was set at 185 kN, the loading speed was 1 kN/s, and the preloading speed was 1 mm/min. After loading, the load was automatically unloaded. After the end of the experiment, the height h1 of the compacted specimen was measured, and the final compacted bulk density γ1 was calculated.
The results of the final compression test on gangue specimens are shown in Figure 4.
The experimental data were sorted, and the initial bulk density and compacted bulk density of gangue specimens in each group were obtained, as shown in Table 9. According to changes in the bulk density of coal gangue specimens, it is evident that the initial bulk density of washed gangue is the smallest, close to 14 kN/m3, indicating that the initial bulk volume of washed gangue is the largest and the intergranular void of gangue is the largest. In Taltol’s n-method, when n = 0.7, the bulk density of gangue reaches a maximum of 15.78 kN/m3; that is, the volume of the gangue filling body is the smallest and the intergranular void of gangue is small, and the initial bulk density of mixed gangue is close to the bulk density of the gradation group when n = 0.3. In the final compaction volume of the sample, when n = 0.5, the compaction density is the largest, and the relative compaction is also the largest in the continuous gradation. The compaction volume changes greatly, and the filling effect is poor. The compacted bulk density is basically 19.5 kN/m3, and the relative compaction is the smallest, that is, its volume compression is the smallest. The compaction effect of gangue is greatly improved after mixing.
To further understand the stress–strain properties of coal gangue, the numerical analysis software Origin is used to express the curve in the form of a mathematical model, as shown in Figures 5–9.
Next, the fitting equation of the stress–strain is established, and the fitting degree of the curve is analyzed. According to the observed curve, Eq. 5 is used to fit the stress–strain relationship. The stress–strain relationship of gangue specimens with different particle sizes is shown in Table 10.
In the above equation, a, b and c are constants.
Table 10 shows that the form of this function can effectively express the stress–strain relationship of gangue, and the correlation coefficient (R-squared) is very close to 1, indicating that the data have a high correlation degree and a small degree of dispersion, and the fitting result is reliable. To compare and analyze the compression performance of gangue at all levels of the above gradation groups under different axial compact loads, fitting equation curves of gangue at all levels are drawn, as shown in Figure 10. To analyze and compare the compression performance of the gangue filling body under the conditions of all levels, the curve of the stress–strain relationship of the gangue filling body is used to obtain the stress under different axial compressive stresses, as shown in Table 11.
When the axial compressive stress reaches 25 MPa (the mining depth is 1,000 m), the strain is regarded as the maximum compression strain. Before the compressive stress reaches 2 MPa, the deformation rate of compression is relatively fast. At this point, the maximum amount of compression of gangue at all levels reaches 26, 47, 44, 37, and 42%. Compared with washed gangue, the final compression deformation of gangue in the continuous gradation groups decreases by 22.15–27.08%, and the compression amount of mixed gangue decreases by 24.25%. Thus, it is evident that the initial compaction ratio and the final compaction ratio are improved to a great extent, and the initial compression rate and the final compaction rate of mixed gangue are also effectively controlled under the condition of continuous gradation. When the axial compressive stress reaches 12.5 MPa (the mining depth is 500 m), the strain is regarded as the maximum compression strain. Before the compressive stress reaches 2 MPa, the compression of gangue at all levels reaches the maximum compression sets of 35, 55, 53, 46, and 51%. At this point, the maximum amount of compression of gangue at all levels reaches 26, 47, 44, 37, and 42%; namely, with the decrease in mining depth, the initial compaction rate of washed gangue decreases, while the initial compaction rate of mixed gangue and the initial compaction rate of gangue in the continuous grading group are improved. Compared with washed gangue, the final compression deformation of gangue in the continuous gradation group is reduced by 13.32–21.51%, and the compression amount of mixed gangue is reduced by 16.60%. After gradation optimization, the compression performance of gangue filling material is significantly improved. Mixed gangue is not the optimal gradation group, but it can prevent large-scale screening and restructuring of particle groups to optimize the gradation of gangue. Compared with washed gangue, mixed gangue still has great advantages in controlling the movement and deformation of overlying strata.
According to the data acquisition results from the experimental machine and the calculation method of the deformation modulus of the loose material, the E–σ curve of the graded specimens in the process of compaction was calculated and drawn by the numerical calculation analysis software Origin, as shown in Figure 11.
According to the E–σ curve, when the axial stress reaches 2 MPa in the lateral constrained compression experiment, the deformation modulus E of coal gangue exhibits a basic linear relationship with the axial compressive stress σ. To describe the relationship between the two, the compressive stress of 2 MPa is regarded as the initial compaction stress. Before the compressive strength reaches 2 MPa, the deformation modulus increases exponentially, and the growth rate of the deformation modulus decreases gradually. After that, the deformation modulus increases linearly, and the anti-compression properties increase gently. Linear fitting was adopted for the data after 2 MPa to obtain the fitting equation of E–σ for the gangue sample group, as shown in Table 12.
In light of the fitting equation, the deformation modulus E increases with increasing compressive stress σ, and the variation range of E is 21–140 MPa in the compressive stress range of 2–30 MPa. The correlation coefficient (R-squared) of the fitting equation is very close to 1, which indicates that the data correlation is high, the degree of dispersion is not large, and the fitting result is reliable.
Most of the ground surface within the 930 mining area of the Tangkou Coal Mine is made up of buildings (structures) of Li temple and Fengtai village. There are Phoenix palace ruins (the third batch of key cultural relic protection units in Shandong Province) and six seven-story residential buildings in the village, as shown in Figure 12. Mining will have an impact on surface buildings (structures). To ensure the normal life of villagers, control surface deformation, and reduce the impact of surface buildings (structures), solid filling mining technology is adopted.
The mining area is approximately 0.3–0.9 km long from north to south and 1.0–1.3 km wide from east to west. The mining area is approximately 0.85 km2. The basic reserves of the mining area are 3.602 million tons, and the recoverable reserves are 2.881 million tons. The western area of the mining area is adjacent to the 130 mining area. Four working faces such as 1,301, 1,302, 1,304, and 1,305 were stopped in the 130 mining area, and water was accumulated in the low-lying areas of the 130 goaf. The seeper area is far away from the mining area, which has no impact on the production of the mining area. In the north, the mining area is adjacent to the protective coal pillar of the industrial square and is 1700 m away from the northern 430 mining area. There are unmined coal areas in the east and south, as shown in Figure 13.
The main mining area is the third upper coal seam, located in the middle of the Shanxi unit, with a full thickness of 2.63–5.11 m. Most of the coal seams in the mining area have a large angle of inclination, generally 7–16°, and the coal seam depth is 1,082–1,222 m.
The filling mining scheme for gangue of the 9,302 working face was optimized, and the gradation of the filling material was improved. After washed gangue and crushed gangue were mixed with equal quality, filling and mining were performed. In actual production, washed gangue is first broken by a crusher and then obtained after scavenging and screening by a screener; crushed gangue is obtained from washed gangue after secondary breakage by a crusher again.
After improving the filling scheme, the solid filling effect of the 9,302 working face is shown in Figures 14, 15. The practical application proves once again that the amount of waste gangue filled in a unit working face is greatly improved by using mixed gangue, the porosity of the filling body is reduced, and the filling ratio of the filling body is improved. According to engineering experience, with the increase in the filling ratio and the roof-contacted filling rate, the mining process can not only consume more wasted gangue but also better control the ground settlement of the mining area.
The stress–strain curves of gangue with different particle gradations all show nonlinear characteristics. The compression modulus increases as the compressive stress increases. With the continuation of the compression process, the rate of change in the compression modulus decreases and tends to stabilize (Zhang et al., 2019b). In the compression test, the specimen contains a large number of pores formed by internal particles. In the initial stage of the compression experiment, as the compressive stress increases, the restraining force of the specimen increases, and the stress concentration between the inner edges of the particles becomes more obvious. When the compressive stress increases to a certain extent, the large particles in the specimen are crushed, and the internal pores are gradually filled (Meng et al., 2019). It is generally believed that the particle diameter and bulk density after compaction tend to be the same after extreme stress compression in tests with different particle sizes (Huang et al., 2019b).
In the compression experiment, the compressed amount of washed gangue is the largest, that of mixed gangue is greatly reduced compared with that of washed gangue, and that of continuous graded gangue is the smallest. The reason is that the more prominent the edge of large particles is, the more prone it is to stress concentration, which leads to the fragmentation of large particles (Ali et al., 2018; Li et al., 2020a). In the washed gangue specimen, large particles are dominant, and small particles cannot completely fill the pores between the large particles, resulting in an obvious stress concentration between the large particles and maximum compression (Zhang et al., 2012). In the specimen of continuously graded gangue, the small particles basically filled the pores between the large particles and weakened the stress concentration between the large particles, and the specimen compression was the smallest. The particle gradation of mixed gangue is slightly worse than that of continuous graded gangue and is much better than that of washed gangue. The optimization degree of the internal structure of the specimen is also somewhat lower than that of continuous graded gangue and much higher than that of washed gangue, so the specimen compression is in the same way: the compression of washed gangue is the largest, that of continuous gradated gangue is the smallest, and that of mixed gangue is slightly less than that of continuous gradated gangue (Zhang et al., 2018).
Solid filling technology is an economical and effective surface subsidence control technology to solve the problem of “three under” coal holding down. The probability integral model of “equivalent mining height theory” can be used to calculate the surface subsidence of solid filling mining (Li et al., 2020b). The determination of “equivalent mining height” is mainly affected by three aspects: the subsidence of the immediate roof of the working face after mining and before gangue filling, the filling rate of the filling body in the filling process, and the compression of the filling body after filling (Wang et al., 2019).
In solid filling mining, on the premise of ensuring the roof-contacted filling rate, the surface subsidence is mainly affected by the filling rate of the filling body and the compression of the filling body under the compressive stress of the overlying rock after filling (Li et al., 2020c). The optimization of the particle size gradation of the filling body can greatly improve the filling rate of the filling body and enhance the compressive strength of the filling body to reduce its amount of compression. Using gangue with optimized particle size gradation for filling can further curtail the “equivalent mining height” to achieve better control of surface deformation and settlement. The filling body of mixed gangue with equal mass proposed in this study has good grain gradation, a high roof bonding rate, and a small compaction rate, which can effectively reduce the “equivalent mining height” and better reduce the surface deformation. In practical application, filling body of mixed gangue with equal quality has simple flow and convenient construction, which has played a guiding role in the promotion and use of gangue filling mining.
Through the screening experiment of gangue filling materials, the gradation characteristics of washed gangue are optimized to obtain gradation groups of gangue conforming to engineering applications. Laboratory specimens of washed gangue, continuous gradation gangue, and mixed gangue were prepared by a similar gradation method; their compression performance was measured; and the following conclusions were drawn:
1) The screening experiment shows that compared with the ideal gradation, the content of large particle size of washed gangue is too much and the content of small particle size is too little, while the small particle size of crushed gangue is dominant, but the large particle size content is too little. Combined with the continuous gradation curve and the gradation of crushed gangue, it is concluded that the gradation defects of filling gangue can be promoted by mixing two types of gangue with equal quality.
2) The list bulk density of gangue varies in the range of 14–20 kN/m3, and the degrees of relative compaction of washed gangue, continuous graded gangue, and mixed gangue are 1.33, 1.24–1.27, and 1.226, respectively. The degree of relative compaction of the gangue filling body decreases significantly after optimizing gangue gradation.
3) The stress–strain curve of gangue is nonlinear and can be described by a three-factor logarithmic function model. With the change in stress, the final compression rate of continuously graded gangue is 70–80% and that of mixed gangue is 75–85%. After optimizing gangue gradation, the compression of the gangue filling body is significantly reduced.
4) According to the experimental results, when the compressive stress reaches 2 MPa, the constitutive model of the filling body is expressed by a nonlinear elastic model, and the relationship between the deformation modulus and compressive stress is described by linear fitting. With the change in compressive stress, the deformation modulus of washed gangue is 26–100 MPa, the final deformation modulus of continuous graded gangue is 21–140 MPa, and the deformation modulus of mixed gangue is 23–135 MPa. The anti-compression properties of the gangue filling body are significantly improved after optimizing the gradation of gangue.
5) The filling body of mixed gangue composed of washed gangue and crushed gangue with equal quality significantly improves its compressive strength and reduces its compression amount. Although it is not the optimal grain gradation, it is considered that mixed gangue is the optimal gangue filling material considering the convenience of on-site construction.
The original contributions presented in the study are included in the article/Supplementary Material; further inquiries can be directed to the corresponding author.
YD, ZM, and XZ contributed to conception and design of the study. YD and XZ organized the database. JL, JZ and ZM performed the statistical analysis. YD and XZ wrote the first draft of the manuscript. YD, JL, JZ and ZM wrote sections of the manuscript. All authors contributed to manuscript revision, read, and approved the submitted version.
Funding was provided by the National Key R and D Program of China (2018YFC0604705); SDUST Research Fund (grant no. 2018TDJH102); the National Natural Science Foundation of China (grant nos. 51574159, 51974172, 51974173, and 51804179); and the SDUST Research Fund, China Postdoctoral Science Foundation (2015 M572067 and 2016T90662), the Shandong Province Natural Science Foundation Project (ZR2017 MEE055 and 2018GSF116002), and the National Experimental Teaching Demonstration Center of Mining Engineering (Shandong University of Science and Technology) Opening Fund (KYSF20180209).
The authors declare that the research was conducted in the absence of any commercial or financial relationships that could be construed as a potential conflict of interest.
Ali, S., Kamran, E., and Bibhu, M. (2018). Degradation of a Discrete Infilled Joint Shear Strength Subjected to Repeated Blast-Induced Vibrations[J]. Int. J. Mining Sci. Technology 28 (4), 561–571.
Cai, Z., Zhang, D., Shi, L., Zhong, C., Biao, C., Suyang, S., et al. (2020). Compaction and Breakage Characteristics of Crushed Stone Used as the Backfill Material of Urban Pavement Subsidence. Adv. Civil Eng. 2020, 1–8. doi:10.1155/2020/8889199
Chang, Q., Tang, W., Xu, Y., and Zhou, H. (2018). Research on the Width of Filling Body in Gob-Side Entry Retaining with High-Water Materials. Int. J. Mining Sci. Technology 28 (3), 519–524. doi:10.1016/j.ijmst.2017.12.016
Chen, C., Liu, X., Luo, Z., and Ning, Z. (2016). Study of Strength and Deformation Characteristic of Unbound Granual Material with Different Graain Composition[J]. J. Eng. Geology. 24 (6), 1191–1198. doi:10.13544/j.cnki.jeg.2016.06.019 (in chinese).
Chu, F., Zhu, J., Weng, H., and Ye, Y. (2020). Experimental Study on Maximum Dry Density of Scaled Coarse-Grained Soil[J]. Rock Soil Mech. 41 (5), 1599–1604. doi:10.16285/j.rsm.2019.0780 (in chinese).
Dong, L., Deng, S., and Wang, F. (2020). Some Developments and New Insights for Environmental Sustainability and Disaster Control of Tailings Dam[J]. J. Clean. Prod. 269, 122270. doi:10.1016/j.jclepro.2020.122270
Dong, L., Tong, X., Li, X., Zhou, J., Wang, S., and Liu, B. (2019). Some Developments and New Insights of Environmental Problems and Deep Mining Strategy for Cleaner Production in Mines. J. Clean. Prod. 210, 1562–1578. doi:10.1016/j.jclepro.2018.10.291
Fang, M., Park, D., Singuranayo, J. L., Chen, H., and Li, Y. (2019). Aggregate Gradation Theory, Design and its Impact on Asphalt Pavement Performance: a Review. Int. J. Pavement Eng. 20 (12), 1408–1424. doi:10.1080/10298436.2018.1430365
Feng, G., Sun, C., Wang, C., and Zhou, Z. (2010). Research on Goaf Filling Methods with Super High-Water Materia[J]. J. China Coal Soc. 35 (12), 1963–1968. doi:10.1016/S1876-3804(11)60004-9 (in chinese).
Fuller, W. B., and Thompson, S. E. (1907). The Laws of Proportioning Concrete[J]. Trans. Am. Soc. Civil Eng. 33, 222–298.
Guo, G.-l., Zhu, X.-j., Zha, J.-f., and Wang, Q. (2014). Subsidence Prediction Method Based on Equivalent Mining Height Theory for Solid Backfilling Mining. Trans. Nonferrous Met. Soc. China 24 (10), 3302–3308. doi:10.1016/s1003-6326(14)63470-1
Guo, G., Li, H., and Zha, J. (2019). An Approach to Protect Cultivated Land from Subsidence and Mitigate Contamination from Colliery Gangue Heaps. Process Saf. Environ. Prot. 124 (PartB), 336–344. doi:10.1016/j.psep.2019.03.004
Hu, B. Backfill Mining Technology and Development Tendency in China Coal Mine[J]. Coal Sci. Technology, 2012,40(11):1-5+18. doi:10.13199/j.cst.2012.11.7.hubn.006 (in chinese)
Hu, B., and Guo, A. (2009). Testing Study on Coal Waste Back Filling Material Compression Simulation. J. China Coal Soc. 34 (8), 1076–1080. doi:10.1360/972009-754 (in chinese).
Hu, B., and Guo, W. (2018). Mining Subsidence AREA Status, Synthe-Ses Governance Model and Governance Recommendation [J]. Coal Mining Technology 23 (2), 1–4. doi:10.13532/j.cnki.cn11-3677/td.2018.02.001 (in chinese).
Huang, X., Zhang, X., Li, Z., Chen, Y., Hu, Y., and Liu, P. (2019a). Study on Grain Composition of Manufactured Sand on Basis of Fuller and Tabor Theory[J]. Concrete 354 (4), 97–101. doi:10.3969/j.issn.1002-3550.2019.04.022 (in chinese).
Huang, Y., Li, J., Ma, D., Gao, H., Guo, Y., and Ouyang, S. (2019b). Triaxial Compression Behaviour of Gangue Solid Wastes under Effects of Particle Size and Confining Pressure. Sci. Total Environ 693, 133607. doi:10.1016/j.scitotenv.2019.133607
Huang, Y., Zhang, J., Zhang, Q., Nie, S., and An, B. (2012). Strata Movement Control Due to Bulk Factor of Backfilling Body in Fully Mechanized Backfilling Mining Face[J]. J. Mining Saf. Eng. 29 (02), 162–167. doi:10.3969/j.issn.1673-3363.2012.02.003 (in chinese).
Ju, Y., Nie, X., Zhu, Y., and Xie, H. (2021). In Situ fluidized Mining and Conversion Solution to Alleviate Geological Damage and Greenhouse Gas Emissions Due to Coal Exploitation: A Numerical Analysis and Evaluation. Energy Sci Eng 9 (1), 40–57. doi:10.1002/ese3.812
Li, B., Yan, H., Zhang, J., and Zhou, N. (2020). Compaction Property Prediction of Mixed Gangue Backfill Materials Using Hybrid Intelligence Models: A New Approach[J]. Construction Building Mater. 247, 118633. doi:10.1016/j.conbuildmat.2020.118633
Li, B., Zhou, N., Qi, W., Li, A., Cui, Z., and Trung, N. (2020). Surface Subsidence Control during Deep Backfill Coal Mining: A Case Study[J]. Adv. Civil Eng. 2020, 1–12. doi:10.1155/2020/6876453
Li, G., Liu, Y., Yin, Z., Dano, C., and Hicher, P. (2014). Grading Effect on Critical State Behavior of Granular Materials[J]. Chin. J. Geotechnical Eng. 03 (36), 0452–0458. doi:10.11779/CJGE201403007 (in chinese).
Li, H., and Guo, G. (2018). Surface Subsidence Control Mechanism and Effect Evaluation of Gangue-Backfilling Mining: A Case Study in China, Geofluids 2018. 1–9. doi:10.1155/2018/2785739
Li, J., Huang, Y., Wen, Z., Yingshun, L., Shenyang, O., Huadong, G., et al. (2020). Experimental Study on Acoustic Emission of Confined Compression of Crushed Gangue under Different Loading Rates: Disposal of Gangue Solid Waste[J]. Sustainability 12 (9). 3911. doi:10.3390/su12093911
Li, M., Zhang, J., Wu, Z., Liu, Y., and Li, A. (2019). An Experimental Study of the Influence of Lithology on Compaction Behaviour of Broken Waste Rock in Coal Mine Backfill R. Soc. Open Sci., 6 (4). 182205. doi:10.1098/rsos.182205
Liu, J., Li, X., and Tuan, He. (2020). Application Status and Prospect of Backfill Mining in Chinese Coal Mines [J]. J. China Coal Soc. 45 (1), 141–150. doi:10.13225/j.cnki.jccs.YG19.1063 (in chinese).
Ma, D., Duan, H., Liu, J., Li, X., and Zhou, Z. (2019). The Role of Gangue on the Mitigation of Mining-Induced Hazards and Environmental Pollution: An Experimental Investigation. Sci. Total Environ. 664, 436–448. doi:10.1016/j.scitotenv.2019.02.059
Ma, Z., Pu, H., and Zhang, F. (2003). Study on Compacting Characteristics of Coal Gangue[J]. Ground Press. Strata Control. 20 (1), 95–96. (in chinese).
Meng, Li., Li, A., Zhang, J., Huang, Y., and Li, J. (2020). Effects of Particle Sizes on Compressive Deformation and Particle Breakage of Gangue Used for Coal Mine Goaf Backfill[J]. Powder Technology 360, 493–502. doi:10.1016/j.powtec.2019.10.075
Meng, Li., Zhang, J., Li, A., and Zhou, N. (2020). Reutilisation of Coal Gangue and Fly Ash as Underground Backfill Materials for Surface Subsidence Control[J]. J. Clean. Prod. 254, 120113. doi:10.1016/j.jclepro.2020.120113
Meng, Li., Zhang, J., Wu, Z., and Sun, K. (2019). Calculation and Monitoring Analysis of Stress Distribution in a Coal Mine Gob Filled with Waste Rock Backfill Materials[J]. Arabian J. Geosciences 12 (14), 1–11. doi:10.1007/s12517-019-4584-9
Miao, X., and Zhang, J. (2007). Analysis of Strata Behavior in the Process of Coal Mining by Gangue Backfilling[J]. J. Mining Saf. Eng. (04), 379–382. doi:10.3969/j.issn.1673-3363.2007.04.001 (in chinese).
Miao, X., Zhang, J., and Guo, G. (2010). Study on Waste-Filling Method and Technology in Fully-Mechanized Coal Mining[J]. J. China Coal Soc. 35 (01), 1–6. doi:10.1016/S1876-3804(11)60004-9 (in chinese).
Qian, M., Xu, J., and Wang, J. (2018). Further on the Sustain-Able Mining of Coal[J]. J. China Coal Soc. 43 (1), 1–13. doi:10.13225/j.cnki.jccs.2017.4400 (in chinese).
Sun, Q., Zhang, J., and Zhou, N. (2018). Study and Discussion of Short- Strip Coal Pillar Recovery with Cemented Paste Backfill. Int. J. Rock Mech. Mining Sci. 104, 147–155. doi:10.1016/j.ijrmms.2018.01.031
Wang, C., Lu, Y., Li, Y., Zhang, B., and Liang, Y. (2019). Deformation Process and Prediction of Filling Gangue: A Case Study in China[J]. Geomechanics Eng. 18 (4), 417–426. doi:10.12989/gae.2019.18.4.417
Wang, J., Xie, H., Liu, J., Wu, L., Ren, S., Jiang, P., et al. (2018). Coal Development and Utilization Theory and Technical System of Near Zero Ecological Environment Impact[J]. J. China Coal Soc. 43 (5), 1198–1209. doi:10.13225/j.cnki.jccs.2018.0518 (in chinese).
Wang, K., Yang, P., Yu, G., Yang, C., and Zhu, L. (2020). 3D Numerical Modelling of Tailings Dam Breach Run Out Flow over Complex Terrain: A Multidisciplinary Procedure. Water 12 (9), 2538. doi:10.3390/w12092538
Wang, Q., Zhao, Y., Tseng, M., and Lim, M. (2020). Performance Analysis and Reuse of Construction and Demolition Waste Stone Using Fractal and Gradation Theory[J]. J. Clean. Prod. 271, 122208. doi:10.1016/j.jclepro.2020.122208
Wang, Y., Yin, D., Chen, S., Zhang, L., Liu, D., Sun, Y., et al. (2020). Experimental Study on Properties of Rock-Cemented Coal Gangue-Fly Ash Backfill Bimaterials with Different Coal Gangue Particle Sizes[J]. Adv. Civil Eng. 2020, 1–12. doi:10.1155/2020/8820330
Wu, J., Jing, H., Yin, Q., Yu, L., Meng, B., and Li, S. (2020). Strength and Ultrasonic Properties of Cemented Waste Rock Backfill Considering Confining Pressure, Dosage and Particle Size Effects[J]. Construction Building Mater. 242, 118132. doi:10.1016/j.conbuildmat.2020.118132
Wu, J., Jing, H., Yin, Q., Meng, B., and Han, G. (2020). Strength Prediction Model Considering Material, Ultrasonic and Stress of Cemented Waste Rock Backfill for Recycling Gangue[J]. J. Clean. Prod. 276, 123189. doi:10.1016/j.jclepro.2020.123189
Xu, J., Zhang, J., and Huang, Y. (2011). Experimental Research on the Compress Deformation Characteristic of Waste-Flyash and its Application in Backfilling Fully Mechanized Coal Mining Technology[J]. J. Mining Saf. Eng. 28 (1), 158–162. doi:10.3969/j.issn.1673-3363.2011.01.030 (in chinese).
Yang, Y., Zhao, J., Wang, L., and Liu, X. (2019). Influence of Gradation Characteristics on Filling Standard of Sand Gravel Material for Dam Construction[J]. J. Hydraulic Eng. 11 (50), 1374–1383. doi:10.13243/j.cnki.slxb.20190547 (in chinese).
Yao, Z., Fang, Y., Kong, W., Huang, X., and Wang, X. (2020). Experimental Study on Dynamic Mechanical Properties of Coal Gangue Concrete. Adv. Mater. Sci. Eng. 2020, 1–16. doi:10.1155/2020/8874191
Zhang, J., Tu, S., Cao, Y., Tan, Y., Xin, H., and Pang, J. (2020). Research Progress of Technologies for Intelligent Separation and In-Situ Backfill in Deep Coal Mines in China[J]. J. Mining Saf. Eng. 37 (1), 1–10+22. doi:10.13545/j.cnki.jmse.2020.01.001 (in chinese).
Zhang, J., Yu, Z., and Su, Y. (2012). Experimental Research on Compression Deformation of Coal Gangue Filling Materials[J]. Mining Res. Development 23 (4), 129–131. doi:10.13827/j.cnki.kyyk.2012.03.018 (in chinese).
Zhang, J., Zhang, Q., Ju, F., Zhou, N., Meng, Li., and Zhang, W. (2019). Practice and Technique of green Mining with Integration of Mining, Dressing, Backfilling and X in Coal Resources[J]. J. China Coal Soc. 44 (01), 64–73. doi:10.13225/j.cnki.jccs.2018.5045 (in chinese).
Zhang, J. (2008). Study on Movement Control and Application of Direct Filling Fully Mechanized Coal Mining Strata with Gangue[D]. Xu Zhou: China University of Minging and Technology. (in chinese).
Zhang, J., Zhang, Q., Huang, Y., Liu, J., Zhou, N., and Zan, D. (2011). Strata Movement Controlling Effect of Waste and Fly Ash Backfillings in Fully Mechanized Coal Mining with Backfilling Face. Mining Sci. Technology (China) 21 (5), 721–726. doi:10.1016/j.mstc.2011.03.003
Zhang, P., Zhang, Y., Zhao, T., Tan, Y., and Yu, F. (2019). Experimental Research on Deformation Characteristics of Waste-Rock Material in Underground Backfill Mining[J]. Minerals 9 (2). doi:10.3390/min9020102
Zhang, Yu., Zhou, W., Li, M., Chen, Z., et al. (2018). Experimental Study on Compression Deformation and Permeability Characteristics of Grading Broken Gangue under Stress. [J]. Processes. 6 (12). doi:10.3390/pr6120257
Zhou, H., Zheng, L., and Liang, Li. (2010). Strip Mining Technology with Paste Backfilling[J]. Coal Sci. Technology 38 (02), 10–14. doi:10.13199/j.cst.2010.02.15.liuk.009 (in chinese).
Zhu, J., Guo, W., Wang, Y., and Wen, Y. (2015). Equation for Soil Gradation Curve and its Applicability[J]. Chin. J. Geotechnical Eng. 37 (10), 1931–1936. doi:10.11779/CJGE201510023 (in chinese).
Zhu, S., Deng, S., Ning, Z., and Wang, J. (2017). Gradation Design Method for Rockfill Materials Based on Fractal Theory[J]. Chin. J. Geotechnical Eng. 39 (6), 1151–1155. doi:10.11779/CJGE201706023
Zhu, S., Ning, Z., Zhong, C., Chu, J., and Gao, Z. (2018). Study on Particle Crush and Deformation Characteristics Considering Rockfill Gradation Effect[J]. J. Hydraulic Eng. 07 (49), 0849–0857. doi:10.13243/j.cnki.slxb.20180086 (in chinese).
Keywords: solid filling mining, grain gradation, compression characteristic, deformation modulus, surface deformation, equivalent mining height
Citation: Dong Y, Zhang X, Lin J, Zhao J and Meng Z (2021) Experimental Study on the Compaction and Deformation of Filling Gangue by Reducing Waste Gangue for Filling Mining. Front. Mater. 8:700118. doi: 10.3389/fmats.2021.700118
Received: 25 April 2021; Accepted: 10 June 2021;
Published: 05 July 2021.
Edited by:
Lijie Guo, Beijing General Research Institute of Mining and Metallurgy, ChinaReviewed by:
Yanli Huang, China University of Mining and Technology, ChinaCopyright © 2021 Dong, Zhang, Lin, Zhao and Meng. This is an open-access article distributed under the terms of the Creative Commons Attribution License (CC BY). The use, distribution or reproduction in other forums is permitted, provided the original author(s) and the copyright owner(s) are credited and that the original publication in this journal is cited, in accordance with accepted academic practice. No use, distribution or reproduction is permitted which does not comply with these terms.
*Correspondence: Xinguo Zhang, emhhbmd4ZzEyMjlAMTYzLmNvbQ==
Disclaimer: All claims expressed in this article are solely those of the authors and do not necessarily represent those of their affiliated organizations, or those of the publisher, the editors and the reviewers. Any product that may be evaluated in this article or claim that may be made by its manufacturer is not guaranteed or endorsed by the publisher.
Research integrity at Frontiers
Learn more about the work of our research integrity team to safeguard the quality of each article we publish.