- 1School of Engineering, Zhejiang A&F University, Hangzhou, China
- 2Zhonghang Monitoring and Testing Technology Research Institute Co., Ltd., Hangzhou, China
- 3Zhejiang Provincial Collaborative Innovation Center for Bamboo Resources and High-Efficiency Utilization, Hangzhou, China
To improve the flame retardancy of bamboo materials, layer by layer (LbL) self-assembly of phytic acid (PA)-polyethyleneimine (PEI) on the surface of shaving super bamboo specimens with different solution concentrations of PA-PEI and times of LbL self-assembly was completed in this study. Fourier transform infrared analysis results showed that PEI was well assembled to the surface of bamboo specimens by a hydrogen bond with PA as intermediation. The application of PA and PEI significantly promoted the formation of carbon residue, as characterized by simultaneous thermal measurements. Particularly, the peak heat release rate and total heat release rate of bamboo self-assembly with 10 wt% PA and 10 wt% of PEI solution were reduced by 19.36 and 22.3%, respectively. The treated bamboo specimen showed increases of 35.56 and 480.70% in fire performance index and residual mass, respectively, compared to the control sample. Besides, yields of CO and CO2 were decreased by 17.77 and 17.07% in comparison with the control group, respectively. The LbL self-assembly with PA-PEI can effectively improve the flame retardancy of bamboo materials by promoting the formation of a residual char layer.
Introduction
Bamboo presents high application prospects and economic value as a substitute for wood due to its similarity to wood in compositions and structures (Scurlock et al., 2000; Zhang X. et al., 2019; Zhang L. et al., 2020). It is traditionally applied to fabricate bamboo-based panels such as plywood, fiberboard, laminated bamboo board, and particleboard. All of these bamboo-based panels have always maintained an important position in the manufacturing of flooring, furniture, and construction due to their unique excellent characteristics, but their high flammability has significantly limited various applications. Therefore, it is necessary to develop flame retardant bamboo-based panels for their practical applications (Guo et al., 2019; Pope et al., 2019).
Most of the previous studies on the preparation of flame retardants focus on green and sustainable flame retardants (He et al., 2020). As a natural non-toxic compound, phytic acid (PA) is abundant in beans, cereals, and oilseeds (Dusková et al., 2001; Fang et al., 2019; Liu et al., 2021). As a biocompatible, environmentally friendly, non-toxic, and easily available organic acid, the content of phosphorus reaches 28%. The phosphorus element makes it a potential green biomass flame retardant. Negative charges were found in the PA solution due to the existence of the special structure that 12 acidic groups were symmetrically connected to a cyclohexanol ring (Jo et al., 2008; Ye et al., 2012; Zeng et al., 2021). The thermal stability and mechanical property of the matrix were declined once combined with PA. It has been reported that the combination of PA and certain metal ions can significantly improve the flame retardant performance of PA (Shen et al., 2016; Fang et al., 2018; Gong et al., 2020). A synergistic effect is observed to generate phosphorus-containing flame retardants with the presence of nitrogen elements, leading to a more excellent flame retardant performance (Nguyen et al., 2013). Therefore, PA is more often combined with some nitrogen-containing compounds such as chitosan, melamine, and polyethyleneimine because the combination results in a synergistic fire-retarding effect once they are used as a flame retardant (Zhang et al., 2014a; Zhang et al., 2014b; Jin et al., 2017; Wang et al., 2019; Zmz et al., 2019). It has been proved that the combination of PA with nitrogen-containing compound will be made into an intumescent flame retardant (IFR) system with PA as an acid source and phosphorus source (Dusková et al., 2001; Zhang et al., 2014a; Jin et al., 2017; Zeng et al., 2021). In addition, a gas source in the IFR system is provided by nitrogen-containing compounds with releasing incombustible gases of N2 and NO2 in the combustion process of composites (Nguyen et al., 2013; Zhang et al., 2014b; Xiong et al., 2019). This flame retardant system is usually evenly dispersed in high molecular polymers to exert a significant flame retardant effect. It has been found that PA is effectively absorbed by the wool fabric and excellent flame retardant performance has been illustrated with the electrostatic interactions between the positively charged amino groups and the negatively charged phytic acid phosphate groups in wool (Cheng et al., 2016a; Cheng et al., 2019).
PA can be effectively combined with cellulose-rich materials to prevent cellulose-rich materials from combusting during the combustion process of materials due to the action of the condensed phase mechanism (Wang et al., 2015; Zhang Z. et al., 2019). However, a further treatment of PA is needed to get a neutral negative charge carried by PA and to make it effectively adhere to the surface of the matrix. Some efforts have been made to prepare an intumescent flame retardant (IFR) solution with PA and uracil to improve the flame retardant performance of the matrix. The IFR solution with PA and uracil has been used to prepare one-step treated wood for excellent flame retardancy. Results revealed that the peak heat release rate, total heat release, smoke production rate, and total smoke production of flame retardant wood were reduced by 41, 30, 61, and 56%, respectively, compared with natural wood (Zhang Y. et al., 2020).
The IFR system completed by the LbL self-assembly technology has been preliminarily introduced to surface modification treatment of shaving super bamboo in this study. PA is selected to provide an acid source and phosphorus source to improve the flame retardant performance, and polyethyleneimine (PEI) provides a gas source for its high nitrogen content and positive charge in solutions (Liu et al., 2016; Ran et al., 2019; Huo et al., 2021). Besides, an LbL self-assembly method was applied to assemble and install PA to be negatively charged and PEI to be positively charged on the surface of shaving super bamboo to fabricate bamboo materials with excellent flame retardant performance (Laachachi et al., 2011; Laufer et al., 2012; Wang et al., 2017; Fang et al., 2019). Herein, we systematically analyze the effects of PA-PEI solution and times of LbL self-assembly on the flame retardancy of bamboo specimens. Besides, PA-PEI LbL self-assembly on the surface of bamboo specimens was analyzed by Fourier transform infrared (FTIR) analysis and simultaneous thermal analysis (STA). Cone calorimeter analysis was completed to investigate further the effect of reagent concentration and times of LbL self-assembly on flame retardant of bamboo specimens LbL self-assembly with PA-PEI. This work provides an insight to a better understanding of the flame retardancy of shaving super bamboo LbL self-assembly with PA-PEI.
Experimental Section
Materials
Shaving super bamboo with demotions of 2000 mm (length: L) ×500 mm (width: W) ×0.6 mm (thickness: T) was obtained from local Bamboo Industry Co., Ltd. Phytic acid (PA, C6H18O24P6, concentration: 50 wt%) with a component of 660 and polyethyleneimine (PEI, CH2CH2NH, AR, concentration: 99 wt%) with a component of 600 were purchased from Aladdin Biochemical Reagent Co., Ltd., Shanghai, China.
Layer by Layer Self-Assembly of Bamboo Specimens With Phytic Acid-Polyethyleneimine
Shaving super bamboo was sawn into chips with the dimension of 100 mm (L) × 100 mm (W) × 0.6 mm (T). All of the bamboo chips were evenly divided into three groups with 100 specimens in every group, namely, Group A, Group B, and the control group. The technology of LbL self-assembly with PA-PEI solution was first applied to improve the flame retardancy performance of shaving super bamboo. The PA solution was prepared by mixing PA with deionized water by magnetic stirrers (DF-101S, Shanghai Lichen Instrument Technology Co., Ltd., Shanghai, China) for 20 min to obtain a homogenized solution at room temperature. The PEI solution was prepared in the same method. Diagrammatic representation of bamboo specimens LbL self-assembly with PA-PEI is illustrated in Figure 1. Bamboo chips in Groups A and B were evenly divided into five groups and marked as A1 to A5 and B1 to B5, respectively. Before LbL self-assembled with PA-PEI, all of the bamboo chips were immersed in water at 70°C for 15 min and dried at 60 ± 1°C in a drying oven (DKN611, Yamato Scientific Co., Ltd. Tokyo, Japan) for 30 min and then at 103 ± 2°C until the constant mass is reached when two successive weights do not differ by more than 0.1%. The bamboo specimens with different solution concentrations and times of LbL self-assembly with PA-PEI are shown in Table 1. Bamboo chips in Group A1 were immersed in 5 wt% PA solution for 5 min and then dried at 60 ± 1°C until the moisture content (MC) reduced to 12%. Besides, the bamboo chips were dipped in a 5 wt% PEI solution for 5 min and dried at 60 ± 1°C for 30 min and then at 103 ± 2°C until the constant mass is reached. Bamboo specimens in Group A5 were obtained by repeating the preceding steps five times. Bamboo specimens in Group B were LbL self-assembled by immersing in the 10 wt% PA solution and 10 wt% PEI solution using the same processing step as Group A. Besides, bamboo specimens in Group B5 were immersed in the 10 wt% PA solution and 10 wt% PEI solution five times.

TABLE 1. Bamboo specimens with different solution concentrations and times of LbL self-assembly with PA-PEI.
Weight Percent Gain of Bamboo Specimens Self-Assembly With Phytic Acid-Polyethyleneimine
Weight percent gain (WPG) of bamboo specimens LbL self-assembly with PA-PEI was calculated according to Equation 1:
where M1 is the ovendry weight of bamboo samples before LbL self-assembly treatment in g and M2 is the ovendry weight of bamboo samples after LbL self-assembly treatment in g.
Fourier Transform Infrared Analysis of Bamboo Specimens Layer by Layer Self-Assembly With Phytic Acid-Polyethyleneimine
FTIR analysis of bamboo specimens before and after LbL self-assembly with PA-PEI was completed by spectroscopy (Nicolet 6700, Nicolet Co., Ltd., United States). The investigation was conducted in the 400–4,000 cm−1 frequency range (Zhang X. et al., 2019). The tested specimen for FTIR test was produced by mixing 1 mg bamboo powders (i.e., ovendry state) with a size of sieve opening ranges from 80 to 120 with 99 mg potassium bromide (KBr).
TG-DTA Analysis of Bamboo Specimens Layer by Layer Self-Assembly With Phytic Acid-Polyethyleneimine
TG-DTA analysis of bamboo specimens before and after LbL self-assembly with PA-PEI was completed by a simultaneous thermal analysis (STA 409 C, NETZSCH Company, German). Ten mg of bamboo powders was placed in an Al2O3 crucible and measured by heating from 20°C to 800°C with a heating rate of 10°C/min in the nitrogen atmosphere.
Cone Calorimeter Analysis of Bamboo Specimens Layer by Layer Self-Assembly With Phytic Acid-Polyethyleneimine
The combustion performance of bamboo specimens was measured by a cone calorimeter (Fire Testing Technology Ltd., United Kingdom) in accordance with ISO 5660-1 (Yu et al., 2016; Hou et al., 2017). All specimens with dimensions of 100 mm (L) ×100 mm (W)×6 mm (T) were hot-pressed at 100°C for 5 min through laminating shaving super bamboo specimens (100 mm (L) ×100 mm (W)×0.6 mm (T)). Prior to cone calorimeter testing, the tested specimens were conditioned to equilibrium moisture content (EMC) at a controlled environment (Temperature of 23°C; 50% relative humidity (RH)) in a high-low humidity alternating test box (EL-10KA, Espec Corporation, Hudsonville, MI, United States) until the constant mass is reached. The tested specimens were irradiated with an incident heat flux of 50 kW (Yu et al., 2016; Hou et al., 2017). All the experimental treatments were performed three times with the average values reported.
Results and Discussion
Weight Percent Gain of Bamboo Specimens Self-Assembly With Phytic Acid-Polyethyleneimine
WPG of bamboo specimens before and after LbL self-assembly is illustrated in Figure 2. A gradual increase was observed in WPG with the increasing times of LbL self-assembly as illustrated in Figure 2. A slight increase of 1.36% was obtained to A1 as compared with the untreated bamboo specimens. However, an increment of 10.88% was generated with the further increase times of LbL self-assembly to five of A5 and over seven times than that of A1. It was also noted that WPG of B1 and B5 was 3.89 and 40.08%, respectively. An obvious increase was generated compared to that of A1 (1.36%) and A5 (10.88%), indicating that the increment was caused by increasing concentration of PA-PEI solution. Therefore, it was concluded that adsorption capacities of PA and PEI were increased with the treatment by LbL self-assembly method and the increase of solution concentration.
Fourier Transform Infrared Analysis
FTIR curves of untreated and treated bamboo specimens are presented in Figure 3. PA5 and PA10 in Figure 3B are bamboo specimens treated with 5 wt% and 10 wt% of PA solutions, respectively. That of PEI5 and PEI10 are bamboo specimens treated with 5 wt% and 10 wt% of PEI solutions, respectively. An obvious decrease in the peak intensity at 3,440 cm−1 indicated the reduction of the content of free -OH in bamboo specimens after LbL self-assembly. Actually, PA was speedily assembled to the surface of bamboo specimens through physical absorption by hydrogen bond, indicating the excellent connection between PA and bamboo specimens (Guo et al., 2019). And then, PEI was also combined with PA by hydrogen bond during the immersion of bamboo specimens in PEI solutions. Hence, PEI was assembled to the surface of bamboo specimens with PA as intermediation. This is the reason why bamboo specimens were first dipped in PA solution and then PEI solution in our study. It was also noted that the band at approximately 1,633 cm−1 of O-P-O (Zhang et al., 2014a) and P=O double bond stretching in the range of 1,200–1,260 cm−1 (Jiang et al., 2012) originated from PA clearly appear as illustrated in Figure 3. Combination between free -OH in bamboo specimens and O-P-O in PA was speedily formed with the immersing of bamboo specimens in PA solution, further leading a reduction in both the peak intensity of free -OH in bamboo specimens and O-P-O in PA. Besides, the band at 1,495 cm−1 was caused by symmetric and asymmetric bending vibration of -NH2 in PEI (Wang et al., 2014). The functional group of -NH2 in PEI was combined with P = O in PA with the immersion of bamboo specimens in PA solution. The absorption peak at 1736 cm−1 corresponding to the C = O stretching in the carboxyl (Duygu et al., 2008) of bamboo specimens was also observed. Cellulose was evidenced to exist in the bamboo specimens with the presence of the peak intensity at 1,056 cm−1 of C-O-C. A decrease in the peak intensity ratio between C-O-C and O-P-O indicated the depositing of PA on the surface of bamboo specimens. In summary, a thin film of PA-PEI was evidenced to be generated on the surface of treated bamboo specimens after LbL self-assembly with PA-PEI solution in this study.
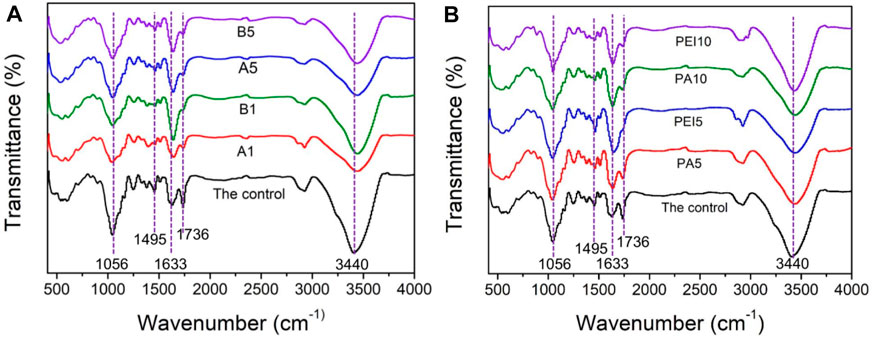
FIGURE 3. FTIR curves of bamboo specimens: (A). bamboo specimens before and after self-assembly with PA-PEI; (B). bamboo specimens before and after treatment with PA solution and PEI solution.
TG-DTA Analysis
Figure 4 shows the TG and DTG curves of bamboo specimens before and after self-assembly with PA-PEI. The maximum weight loss rate (WLRmax) and the temperature (t) to WLRmax of bamboo specimens before and after self-assembly with PA-PEI are listed in Table 2. The pyrolysis process of bamboo is mainly divided into three stages in accordance with the heat treatment temperature (Zhang Y. et al., 2020). An obvious weight loss was observed in bamboo specimens before and after self-assembly with PA-PEI in the temperature ranging from 80 to 90°C in the first stage of the pyrolysis process as shown in Figure 4B. Compared with WLRmax of the control group (4.4%/°C), the WLRmax of treated bamboo specimens was obviously increased by 86.8% (A1) and 95.9% (B1), respectively. However, the corresponding increment of WLRmax was 44.8% (A5) and 79.1% (B5) with the further increase times of self-assembly to five. Besides, t of the treated bamboo specimens was also increased by 36.1% (A1), 13.4% (B1), 20.1% (A5), and 20.0% (B5), respectively. This may be due to the evaporation of moisture in bamboo specimens in accordance with the pyrolysis process of bamboo and wood (Duygu et al., 2008; Poletto et al., 2012). Besides, overflow of trace free organic molecules for PA was also observed in the pyrolysis process of the treated bamboo specimens according to the boiling points of PA and PEI. A slight difference between bamboo specimens before and after self-assembly with PA-PEI was observed due to the evaporation of PA.

FIGURE 4. Weight curves (A) and DTG curves (B) of bamboo specimens before and after self-assembly with PA-PEI in N2 atmosphere.
As listed in Table 2, WLRmax of the treated bamboo specimens in the second stage of the pyrolysis process was decreased by 19.91% (A1), 11.17% (A5), 18.03% (B1), and 32.20% (B5) in comparison with that of the control group (19.69%/°C), respectively. Moreover, t of A1 (333.88°C) and B1 (343.46°C) were slightly decreased by 10.52 and 7.95%, respectively. The decrements of t were increased to 17.77% (A5) and 17.48% (B5) with the further increase time for LbL self-assembly with PA-PEI to five. In addition, it was found that residual mass at 800 °C was significantly increased to 126.34% (A1) and 123.10% (B1) after the first time of LbL self-assembly with PA-PEI. A significant increase in residual mass was generated with the increase of times for LbL self-assembly with PA-PEI to five, which was nearly doubled (i.e., A5: 196.33% and B5: 202.73%). This may be due to the PA-PEI thin film formed on the surface of treated bamboo specimens in the LbL assembly process with PA-PEI solutions. The thin film was thick enough to prevent bamboo specimens from thermal decomposition with the increase of concentration of PA-PEI solution and times of LbL self-assembly. Hence, a remarkable increase was found in the residual mass at 800°C of treated bamboo specimens (Shen et al., 2016).
It has been reported that the peak at 320∼330°C and 373°C of bamboo material under N2 atmosphere is the degradation of hemicellulose and lignin, respectively (Brebu and Vasile, 2010; Herrera et al., 2014). Additionally, incombustible gases, such as N2, are always generated in the decomposition process of PEI in the phosphorus-nitrogen flame retardant system (PA-PEI) formed on the surface of bamboo specimens after LbL self-assembly with PA-PEI and a relatively weak contribution to the TG-DTG curve in this study. The decomposition of PA was generated in a low-temperature stage, and metaphosphoric acid was formed in this stage with PA as an acid source. Besides, binding interaction between metaphosphoric acid and the matrix occurred and further resulted in the formation of a dehydration carbon layer. Moreover, the degradation chain reaction of the matrix shifts to the formation of the carbon layer and leads to the increase in the carbon residue contents (Jeng et al., 2002; Daneluti and Matos, 2013; Cheng et al., 2016b). Therefore, the maximum degradation rate of the substrate comes earlier at a lower temperature. The same conclusion was also obtained by increasing residual mass, as shown in Figure 4A, Table 2, and the attenuation of the second peak in DTG curves illustrated in Figure 4B. It was also noted that times of LbL self-assembly with PA-PEI makes a great difference to pyrolysis process of bamboo specimens. For the bamboo specimens LbL self-assembly with PA-PEI, the following order of residual mass was found: B5>A5>B1>A1. Hence, the bamboo specimens LbL self-assembly with PA-PEI five times (A5 and B5) showed the highest residual mass.
Cone Calorimeter Analysis
Heat Release Rate and Total Heat Release
HRR (A) and THR (B) curves of bamboo specimens before and after self-assembly with PA-PEI are presented in Figure 5. As illustrated in Figure 5A, the combustion process of bamboo specimens is mainly divided into two stages. For the first stage, two HRR peaks of the untreated and treated bamboo specimens were observed. Peak HRR (PHRR) of A5 and B1 was greater than that of the control. And the time to PHRR of A5 and B1 was also slightly decreased, indicating the earlier combustion of A5 and B1. This may be due to the dehydration of wood components catalyzed by PA in a low-temperature stage, and the degradation of organic compounds was accelerated, which promoted the release of combustible volatile products (Wang et al., 2004; Gong et al., 2020). Moreover, PHRR of B5 (213.41 kW/m2) was decreased by 18.71% as compared with the control group (262.54 kW/m2). Therefore, it is evident that increasing the concentration of PA-PEI solutions and times of LbL self-assembly with PA-PEI contributes to a slight improvement in the flame retardancy of bamboo specimens in the first combustion stage of cone calorimeter analysis. This may be due to the PA-PEI thin film generated on the surface of treated bamboo specimens in the LbL assembly process with PA-PEI solutions. The PA-PEI thin film can effectively prevent bamboo specimens from combusting with the increase of concentration of PA-PEI solution and times of LbL assembly.
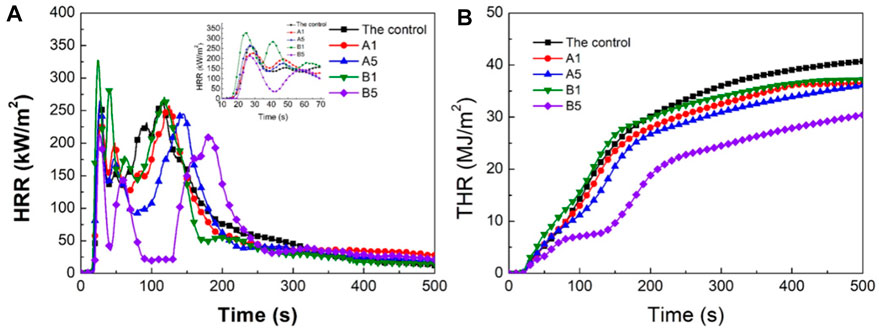
FIGURE 5. HRR (A) and THR (B) curves of bamboo specimens before and after LbL self-assembly with PA-PEI.
The PHRR in the second stage, average HRR (AHRR), PHRR, and THR of bamboo specimens are shown in Table 3. A reduction in PHRR of bamboo specimens after LbL self-assembly with PA-PEI was generated as compared to the control. The corresponding values of PHRR2 were decreased by 2.68% (A1), 11.17% (A5), and 19.57% (B5) in comparison with the control group, respectively. The time to PHRR was delayed from 115 s (the control group) to 125 s (A1), 144 s (A5), 118 s (B1), and 181 s (B5), suggesting lower flammability of the treated bamboo specimens. The reason was that the increasing concentrations of PA-PEI solution and times of LbL self-assembly with PA-PEI resulted in the generation of IFR film on the surface of bamboo specimens, which can protect the underlying bamboo matrix from sharp combustion during the cone calorimeter test. However, PHRR of B5 (213.41 kW/m2) prepared by using the IFR system with 10 wt% PA solution and 10 wt% PEI solution was greater than that of FR wood (164.80 kW/m2) prepared by using 8 wt% PA solution and 3 wt% uracil solution (Zhang L. et al., 2020).
THR curves of bamboo specimens before and after LbL self-assembly with PA-PEI are presented in Figure 5B. It was noted that the THR of the treated bamboo specimens was decreased with the increase in the concentration of PA-PEI solution and times of LbL self-assembly. For the bamboo specimens LbL self-assembly with PA-PEI, the following order of THR was found: A1>A5>B1>B5 (Table 3). A small decrement of 8.76% (from 41.67 MJ/m2 to 38.02 MJ/m2) occurred in the THR of bamboo specimens (A5) self-assembly with the IFR system with 5 wt% PA solution and 5 wt% PEI solution with increase times of LbL self-assembly to five in comparison with the control. Moreover, THR of bamboo specimens (B5) self-assembly with the IFR system with 10 wt% PA solution and 10 wt% PEI solution five times the LbL self-assembly reduced by 22.30% (from 41.67 MJ/m2 to 32.38 MJ/m2). It indicated that both improvement in PA-PEI solution and times of LbL self-assembly can help to improve the flame retardancy of bamboo specimens. It was also noted that THR of B5 (32.38 MJ/m2) prepared by using the IFR system with 10 wt% PA solution and 10 wt% PEI solution was greater than that of FR wood (16.90 MJ/m2) prepared by using 8 wt% PA solution and 3 wt% uracil solution (Zhang Y. et al., 2020).
Time to Ignition and Fire Performance Index
Time to ignition (TTI) is the continuous ignition time required from the surface of the tested materials to be ignited under the preset heat radiation power. Fire performance index (FPI) is the ratio of the TTI of the tested material to the PHRR. FPI is calculated according to the following formula: FPI (s/(kW.m−2)) = TTI/PHRR, which is usually used to evaluate the potential flashover hazard of the material in a fire (Petrella, 1994; Xu et al., 2013; Yu et al., 2016; Hou et al., 2017). Besides, the flashover time of the tested material is an important basis for the design of fire escape time. The larger the FPI, the later the material flashover time.
Figure 6 plots TTI and FPI of bamboo specimens before and after LbL self-assembly with PA-PEI. It indicated that the concentration of PA-PEI solution and times of LbL self-assembly had a limited effect on TTI of bamboo specimens. Additionally, TTI of bamboo specimens was slightly increased from 12 to 13 s with the increasing times of LbL self-assembly to five, with the IFR system with 10 wt% PA solution and 10 wt% PEI solution. However, FPI of B5 was increased by 35.56% (from 0.045 s/(kW/m2) to 0.061 s/(kW/m2)) in comparison to the control. Actually, both increase in TTI and decrease in PHRR contribute to the increase of FPI, further leading to improved fire resistance of bamboo specimens LbL self-assembly with PA-PEI (Hou et al., 2019).
Mass Loss Rate and Residual Mass
MLR in initial 360 s and residual mass of bamboo specimens before and after LbL self-assembly with PA-PEI are presented in Figure 7. As shown in Figure 7A, MLR of the treated bamboo specimens was decreased with the increase in PA-PEI solution and times for LbL self-assembly with PA-PEI. For the bamboo specimens LbL self-assembly with PA-PEI, the following order of MLR in initial 180 s was found: B1>A1>A5>B5. That of MLR of A1, A5, and B1 was almost the same from 180 to 360 s as presented in Figure 7A. Residual mass of A1 (1.54%) and B1 (1.07%) decreased more considerably than that of the control group (2.90%) as illustrated in Figure 7B. Besides, residual mass of A5 (8.07%) was 178.28% greater and B5 (16.84%) was 480.69% greater than the control group (2.90%), respectively. It indicated that the IFR system with PA-PEI solution can exert a flame retardant action at the flaming combustion stage to fix the carbon source, thereby producing more carbon residue (i.e., Residual mass). Additionally, the PA-PEI thin film formed on the surface of the treated bamboo specimens in LbL assembly process can effectively protect bamboo specimens from combusting with increasing times of LbL self-assembly. Similar results were obtained from TG and DTG analysis, as shown in Figure 4.
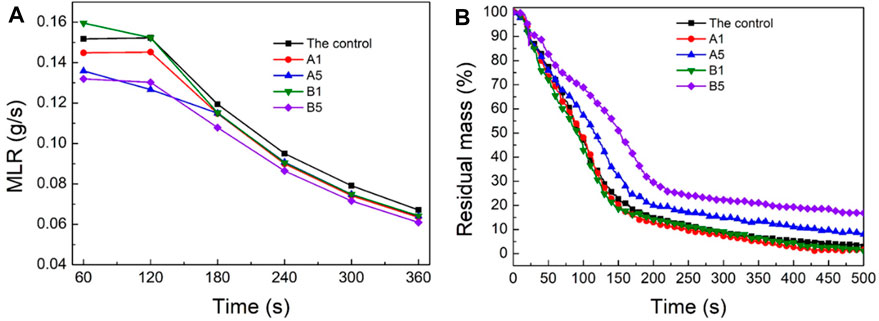
FIGURE 7. MLR (A) in initial 360 s and residual mass (B) of bamboo specimens before and after LbL self-assembly with PA-PEI.
Effective Heat of Combustion, CO Yield, and CO2 Yield
Figure 8 illustrates the EHC of bamboo specimens before and after LbL self-assembly with PA-PEI in initial 360 s, and the detailed data for the EHC of the bamboo specimens before and after LbL self-assembly with PA-PEI are listed in Table 4. As shown in Figure 8, the EHC of the treated bamboo specimens was decreased with increasing PA-PEI concentrations and times of LbL self-assembly. Average EHC and peak EHC of bamboo specimens after LbL self-assembly with PA-PEI (i.e., A1, A5, and B1) were slightly decreased by less than 10% as shown in Table 4. Besides, average EHC and peak EHC of bamboo specimens after LbL self-assembly with PA-PEI were decreased by 18.90% (B5: 11.84 MJ/kg) with increasing times of LbL self-assembly to five at the IFR system with 10 wt% PA solution and 10 wt% PEI solution in comparison with the control group (14.60 MJ/kg). In addition, the time to peak EHC of the treated bamboo specimens was remarkably prolonged and more than doubled to compare with the control group (Table 4), indicating that the IFR system with 10 wt% PA solution and 10 wt% PEI solution plays a significant role in limiting the production of flammable volatile products.
COY and CO2Y of bamboo specimens before and after self-assembly with PA-PEI in the initial 360 s are presented in Figure 9. It was found that the COY was increased with the increase in the concentration of PA-PEI solution and the times of LbL self-assembly with PA-PEI, and the following order of COY in the initial 360 s was found: B5>A5>B1>A1. The reason was that the thin film of PA-PEI formed on the surface of the treated bamboo specimens was thick enough to prevent bamboo specimens from combusting with the increase of concentration of PA-PEI solution and times of LbL self-assembly (Jiang et al., 2012). Hence, a remarkable increase in the COY of the treated bamboo specimens was obtained and increased with the delay of combustion time. However, the following order of CO2Y in the initial 360 s was found: B1>A1>B5>A5. The incomplete combustion of the treated bamboo specimens led to a reduction in the CO2Y during the cone calorimeter test.
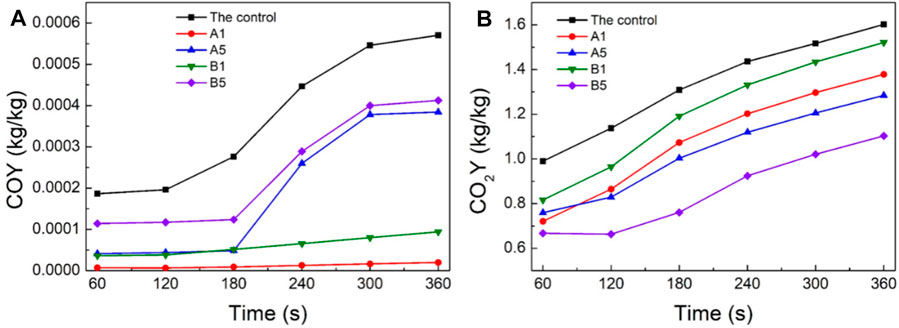
FIGURE 9. COY (A) and CO2Y (B) of bamboo specimens before and after LbL self-assembly with PA-PEI in initial 360 s.
Average COY and CO2Y of bamboo specimens before and after self-assembly with PA-PEI are shown in Figure 10. The average COY of the treated bamboo specimens was increased with the increase in the times of LbL self-assembly with PA-PEI, and the following order of average COY was found: B5>A5>A1>B1. The average COY of the treated bamboo specimens was decreased by 50.28% (A1), 72.02% (B1), 21.93% (A5), and 17.77% (B5) as compared with the control, respectively. By contrast, the average CO2Y of bamboo specimens after self-assembly with PA-PEI (i.e., A1, A5, and B5) was slightly decreased by less than 20%. B5 showed a decrease of 16.88% in average CO2Y (B5: 1.364 kg/kg) compared to the control group (1.641 kg/kg). It indicated that the IFR system with PA-PEI played an obvious inhibiting effect on the combustion of bamboo materials during the cone calorimeter test (Nguyen et al., 2013). It is well known that bamboo is mainly composed of cellulose, lignin, and hemicellulose, and it will crack to produce small-molecule combustible substances under combustion conditions. Thereby, CO and CO2 are expected to be generated after the combustion of bamboo (Jakab et al., 1995; Bassilakis et al., 2001). Both increase in average COY and decrease in CO2Y of the treated bamboo specimens were caused by the imperfect combustion of bamboo specimens LbL self-assembly with PA-PEI. The thin film of PA-PEI formed on the surface of the treated bamboo specimens was thick enough to prevent bamboo specimens from combusting with the increase of concentration of PA-PEI solution and times of LbL self-assembly (Nguyen et al., 2013).
Combined with the analysis of EHC shown in Figure 8 and Table 4, an obvious fixation effect of the IFR system with PA-PEI solution on the C element was obtained in the combustion process of bamboo materials. Additionally, the PA-PEI thin film formed on the surface of treated bamboo specimens in the LbL assembly process was thick enough to protect bamboo specimens from thermal decomposition and sharp combustion, leading to the increase in amount of residual mass (Figure 7B) and decrease in EHC (Figure 8) during the cone calorimeter test. Similar results were obtained from the TG-DTG analysis of bamboo specimens after self-assembly with PA-PEI. The formation of a protective char layer during the cone calorimeter measurement acts as a barrier, reduces the HRR and the yield of CO2, and further increases residual mass, indicating that a well-integrated flame retardant performance was obtained to the bamboo specimens treated with the IFR solution of 10 wt% PA and 10 wt% PEI five times the LbL self-assembly with PA-PEI.
Conclusions
The PA-PEI-based fire-retardant layer was coated on the surface of shaving super bamboo specimens by an LbL self-assembly technology to improve the flame retardancy of bamboo materials in this study. The effects of PA-PEI solution and times of LbL self-assembly with PA-PEI on the flame retardancy of bamboo specimens were systematically investigated. The LbL self-assembly with PA-PEI promoted the generation of a residual char layer with excellent stability. In addition, a higher solution concentration of PA-PEI and more times of LbL self-assembly made the specimens exhibit smaller HRR and lower yield of CO and CO2, but greater residual mass and FPI values. For bamboo specimens self-assembly with 10 wt% PA solution and 10 wt% PEI solution five times, PHRR and THR were reduced by 19.36 and 22.30%, respectively, compared to the control group. In addition, the FPI and residual mass of the bamboo specimens self-assembly with 10 wt% PA solution and 10 wt% PEI solution 5 times were increased by 35.56 and 480.70% in comparison with the control group, respectively. This work contributes to a better understanding of the effects of LbL self-assembly with PA-PEI on the flame retardancy of bamboo specimens, thus providing a useful approach for the value-added utilization of bamboo materials.
Data Availability Statement
The original contribution presented in the study are included in the article/supplementary material; further inquiries can be directed to the corresponding authors.
Author Contributions
PL, YJ, and JH executed the experiment and wrote the manuscript. YY conceived and designed the study and experiment plan. LM and WC revised the manuscript. XR and XZ analyzed the experimental results.
Funding
The work was financially supported by the National Natural Science Foundation of China (Grant No. 31800473) and the Natural Science Foundation of Zhejiang province (Grant No. LY17C160007).
Conflict of Interest
PL was employed by the company Zhonghang Monitoring and Testing Technology Research Institute Co., Ltd.
The remaining authors declare that the research was conducted in the absence of any commercial or financial relationships that could be construed as a potential conflict of interest.
Publisher’s Note
All claims expressed in this article are solely those of the authors and do not necessarily represent those of their affiliated organizations, or those of the publisher, the editors and the reviewers. Any product that may be evaluated in this article, or claim that may be made by its manufacturer, is not guaranteed or endorsed by the publisher.
References
Bassilakis, R., Carangelo, R., and Wójtowicz, M. (2001). TG-FTIR Analysis of Biomass Pyrolysis. Fuel 80 (4), 1765–1786. doi:10.1016/S0016-2361(01)00061-8
Brebu, M., and Vasile, C. (2010). Thermal Degradation of Lignin-A Review. Cell. Chem. Technol. 44 (9), 353–363. doi:10.1007/s10086-010-1118-1
Cheng, X.-W., Guan, J.-P., Tang, R.-C., and Liu, K.-Q. (2016a). Phytic Acid as a Bio-Based Phosphorus Flame Retardant for Poly(lactic Acid) Nonwoven Fabric. J. Clean. Prod. 124, 114–119. doi:10.1016/j.jclepro.2016.02.113
Cheng, X.-W., Guan, J.-P., Chen, G., Yang, X.-H., and Tang, R.-C. (2016b). Adsorption and Flame Retardant Properties of Bio-Based Phytic Acid on Wool Fabric. Polymers 8 (4), 122. doi:10.3390/polym8040122
Cheng, X.-W., Guan, J.-P., Kiekens, P., Yang, X.-H., and Tang, R.-C. (2019). Preparation and Evaluation of an Eco-Friendly, Reactive, and Phytic Acid-Based Flame Retardant for Wool. Reactive Funct. Polym. 134, 58–66. doi:10.1016/j.reactfunctpolym.2018.11.006
Daneluti, A. L. M., and Matos, J. d. R. (2013). Study of thermal Behavior of Phytic Acid. Braz. J. Pharm. Sci. 49, 275–283. doi:10.1590/S1984-82502013000200009
Dusková, D., Marounek, M., and Brezina, P. (2001). Determination of Phytic Acid in Feeds and Faeces of Pigs and Poultry by Capillary Isotachophoresis. J. Sci. Food Agr. 81 (1), 36–41. doi:10.1002/1097-0010(20010101)81:13.0.CO;2-A
Duygu, K., Sandor, P., and Yaman, B. (2008). Effect of thermal Treatment on the Chemical Composition and Mechanical Properties of Birch and aspen. Bioresources 3 (2), 517–537. doi:10.1016/S0016-7037(00)00094-2
Fang, F., Ran, S., Fang, Z., Song, P., and Wang, H. (2019). Improved Flame Resistance and Thermo-Mechanical Properties of Epoxy Resin Nanocomposites from Functionalized Graphene Oxide via Self-Assembly in Water. Compos. B. Eng. 165, 406–416. doi:10.1016/j.compositesb.2019.01.086
Fang, F., Song, P., Ran, S., Guo, Z., Wang, H., and Fang, Z. (2018). A Facile Way to Prepare Phosphorus-Nitrogen-Functionalized Graphene Oxide for Enhancing the Flame Retardancy of Epoxy Resin. Composites Commun. 10, 97–102. doi:10.1016/j.coco.2018.08.001
Gong, W., Fan, M., Luo, J., Liang, J., and Meng, X. (2020). Effect of Nickel Phytate on Flame Retardancy of Intumescent Flame Retardant Polylactic Acid. Polym. Adv. Technol. 32 (4), 1548–1559. doi:10.1002/pat.5190
Guo, W., Kalali, E. N., Wang, X., Xing, W., Zhang, P., Song, L., et al. (2019). Processing Bulk Natural Bamboo into a strong and Flame-Retardant Composite Material. Ind. Crops Prod. 138, 111478. doi:10.1016/j.indcrop.2019.111478
He, W., Song, P., Yu, B., Fang, Z., and Wang, H. (2020). Flame Retardant Polymeric Nanocomposites through the Combination of Nanomaterials and Conventional Flame Retardants. Prog. Mater. Sci. 114, 100687. doi:10.1016/j.pmatsci.2020.100687
Herrera, R., Erdocia, X., Llano-Ponte, R., and Labidi, J. (2014). Characterization of Hydrothermally Treated wood in Relation to Changes on its Chemical Composition and Physical Properties. J. Anal. Appl. Pyrolysis 107, 256–266. doi:10.1016/j.jaap.2014.03.010
Hou, J., Cai, Z., and Lu, K. (2017). Cone Calorimeter Evaluation of Reinforced Hybrid wood-aluminum Composites. J. Fire Sci. 35 (2), 118–131. doi:10.1177/0734904116683717
Huo, S., Liu, Z., Li, C., Wang, X., Cai, H., and Wang, J. (2019). Synthesis of a Phosphaphenanthrene/benzimidazole-Based Curing Agent and its Application in Flame-Retardant Epoxy Resin. Polym. Degrad. Stab. 163, 100–109. doi:10.1016/j.polymdegradstab.2019.03.003
Huo, S., Song, P., Yu, B., Ran, S., Chevali, V. S., Liu, L., et al. (2021). Phosphorus-containing Flame Retardant Epoxy Thermosets: Recent Advances and Future Perspectives. Prog. Polym. Sci. 114, 101366. doi:10.1016/j.progpolymsci.2021.101366
Jakab, E., Faix, O., Till, F., and Székely, T. (1995). Thermogravimetry/mass Spectrometry Study of Six Lignins within the Scope of an International Round Robin Test. J. Anal. Appl. Pyrolysis 35 (2), 167–179. doi:10.1016/0165-2370(95)00907-7
Jeng, R.-J., Shau, S.-M., Lin, J.-J., Su, W.-C., and Chiu, Y.-S. (2002). Flame Retardant Epoxy Polymers Based on All Phosphorus-Containing Components. Eur. Polym. J. 38 (4), 683–693. doi:10.1016/S0014-3057(01)00246-4
Jiang, G., Qiao, J., and Hong, F. (2012). Application of Phosphoric Acid and Phytic Acid-Doped Bacterial Cellulose as Novel Proton-Conducting Membranes to PEMFC. Int. J. Hydrogen Energ. 37 (11), 9182–9192. doi:10.1016/j.ijhydene.2012.02.195
Jin, X., Gu, X., Chen, C., Tang, W., Li, H., Liu, X., et al. (2017). The Fire Performance of Polylactic Acid Containing a Novel Intumescent Flame Retardant and Intercalated Layered Double Hydroxides. J. Mater. Sci. 52 (20), 12235–12250. doi:10.1007/s10853-017-1354-5
Jo, S., Jeong, H., Bae, S. R., and Jeon, S. (2008). Modified Platinum Electrode with Phytic Acid and Single-Walled Carbon Nanotube: Application to the Selective Determination of Dopamine in the Presence of Ascorbic and Uric Acids. Microchem. J. 88 (1), 1–6. doi:10.1016/j.microc.2007.08.005
Laachachi, A., Ball, V., Apaydin, K., Toniazzo, V., and Ruch, D. (2011). Diffusion of Polyphosphates into (Poly(allylamine)-montmorillonite) Multilayer Films: Flame Retardant-Intumescent Films with Improved Oxygen Barrier. Langmuir 27 (22), 13879–13887. doi:10.1021/la203252q
Laufer, G., Kirkland, C., Morgan, A. B., and Grunlan, J. C. (2012). Intumescent Multilayer Nanocoating, Made with Renewable Polyelectrolytes, for Flame-Retardant Cotton. Biomacromolecules 13 (9), 2843–2848. doi:10.1021/bm300873b
Liu, C., Zhang, T., Luo, Y., Wang, Y., Li, J., Ye, T., et al. (2021). Multifunctional Polyurethane Sponge Coatings with Excellent Flame Retardant, Antibacterial, Compressible, and Recyclable Properties. Compos. B. Eng. 215, 108785. doi:10.1016/j.compositesb.2021.108785
Liu, L., Huang, G., Song, P., Yu, Y., and Fu, S. (2016). Converting Industrial Alkali Lignin to Biobased Functional Additives for Improving Fire Behavior and Smoke Suppression of Polybutylene Succinate. ACS Sustain. Chem. Eng. 4 (9), 4732–4742. doi:10.1021/acssuschemeng.6b00955
Nguyen, T.-M., Chang, S., Condon, B., Slopek, R., Graves, E., and Yoshioka-Tarver, M. (2013). Structural Effect of Phosphoramidate Derivatives on the thermal and Flame Retardant Behaviors of Treated Cotton Cellulose. Ind. Eng. Chem. Res. 52 (13), 4715–4724. doi:10.1021/ie400180f
Petrella, R. V. (1994). The Assessment of Full-Scale Fire Hazards from Cone Calorimeter Data. J. Fire Sci. 12 (1), 14–43. doi:10.1177/073490419401200102
Poletto, M., Zattera, A. J., Forte, M. M. C., and Santana, R. M. C. (2012). Thermal Decomposition of wood: Influence of wood Components and Cellulose Crystallite Size. Bioresour. Techn. 109, 148–153. doi:10.1016/j.biortech.2011.11.122
Pope, I., Hidalgo, J. P., Osorio, A., Maluk, C., and Torero, J. L. (2019). Thermal Behaviour of Laminated Bamboo Structures under Fire Conditions. Fire Mater. 45 (3), 321–330. doi:10.1002/fam.2791
Ran, S., Fang, F., Guo, Z., Song, P., Cai, Y., Fang, Z., et al. (2019). Synthesis of Decorated Graphene with P, N-Containing Compounds and its Flame Retardancy and Smoke Suppression Effects on Polylactic Acid. Compos. B. Eng. 170, 41–50. doi:10.1016/j.compositesb.2019.04.037
Scurlock, J. M. O., Dayton, D. C., and Hames, B. (2000). Bamboo: an Overlooked Biomass Resource? Biomass Bioenergy 19 (4), 229–244. doi:10.1016/S0961-9534(00)00038-6
Shen, Y., Gong, W., Zheng, B., Meng, X., and Gao, L. (2016). Synergistic Effect of Ni-Based Bimetallic Catalyst with Intumescent Flame Retardant on Flame Retardancy and thermal Stability of Polypropylene. Polym. Degrad. Stab. 129, 114–124. doi:10.1016/j.polymdegradstab.2016.04.006
Wang, P.-J., Liao, D.-J., Hu, X.-P., Pan, N., Li, W.-X., Wang, D.-Y., et al. (2019). Facile Fabrication of Biobased P N C-Containing Nano-Layered Hybrid: Preparation, Growth Mechanism and its Efficient Fire Retardancy in Epoxy. Polym. Degrad. Stab. 159, 153–162. doi:10.1016/j.polymdegradstab.2018.11.024
Wang, Q., Li, J., and Winandy, J. (2004). Chemical Mechanism of Fire Retardance of Boric Acid on wood. Wood. Sci. Technol. 38 (5), 375–389. doi:10.1007/s00226-004-0246-4
Wang, W., Xiao, J., Wei, X., Ding, J., Wang, X., and Song, C. (2014). Development of a New clay Supported Polyethylenimine Composite for CO2 Capture. Appl. Energ. 113 (6), 334–341. doi:10.1016/j.apenergy.2013.03.090
Wang, X., Romero, M. Q., Zhang, X.-Q., Wang, R., and Wang, D.-Y. (2015). Intumescent Multilayer Hybrid Coating for Flame Retardant Cotton Fabrics Based on Layer-By-Layer Assembly and Sol-Gel Process. RSC Adv. 5 (5), 10647–10655. doi:10.1039/c4ra14943b
Wang, Y., Ding, X., Chen, X., Chen, Z., Zheng, K., Chen, L., et al. (2017). Layer-by-layer Self-Assembly Photocatalytic Nanocoating on Cotton Fabrics as Easily Recycled Photocatalyst for Degrading Gas and Liquid Pollutants. Cellulose 24 (10), 4569–4580. doi:10.1007/s10570-017-1445-0
Xiong, Z., Zhang, Y., Du, X., Song, P., and Fang, Z. (2019). Green and Scalable Fabrication of Core-Shell Biobased Flame Retardants for Reducing Flammability of Polylactic Acid. ACS Sustain. Chem. Eng. 7 (9), 8954–8963. doi:10.1021/acssuschemeng.9b01016
Xu, Q., Jin, C., Zachar, M., and Majlingova, A. (2013). Test Flammability of PVC Wall Panel with Cone Calorimetry. Proced. Eng. 62, 754–759. doi:10.1016/j.proeng.2013.08.122
Ye, C. H., Zheng, Y. F., Wang, S. Q., Xi, T. F., and Li, Y. D. (2012). In Vitro corrosion and Biocompatibility Study of Phytic Acid Modified WE43 Magnesium alloy. Appl. Surf. Sci. 258 (8), 3420–3427. doi:10.1016/j.apsusc.2011.11.087
Yu, Y., Hou, J., Dong, Z., Wang, C., Lu, F., and Song, P. (2016). Evaluating the Flammability Performance of Portland Cement-Bonded Particleboards with Different Cement-wood Ratios Using a Cone Calorimeter. J. Fire Sci. 34 (3), 199–211. doi:10.1177/0734904116630758
Zeng, X., Lin, J., Cai, W., Lu, Q., Fu, S., Li, J., et al. (2021). Fabrication of Superhydrophilic PVDF Membranes by One-step Modification with Eco-Friendly Phytic Acid and Polyethyleneimine Complex for Oil-In-Water Emulsions Separation. Chemosphere 264 (1), 128395. doi:10.1016/j.chemosphere.2020.128395
Zhang, L., Yi, D., Hao, J., and Gao, M. (2020). One‐step Treated wood by Using Natural Source Phytic Acid and Uracil for Enhanced Mechanical Properties and Flame Retardancy. Polym. Adv. Technol. 32, 1176–1186. doi:10.1002/pat.5165
Zhang, T., Yan, H., Shen, L., Fang, Z., Zhang, X., Wang, J., et al. (2014a). A Phosphorus-, Nitrogen- and Carbon-Containing Polyelectrolyte Complex: Preparation, Characterization and its Flame Retardant Performance on Polypropylene. RSC Adv. 4, 48285–48292. doi:10.1039/c4ra09243k
Zhang, T., Yan, H., Shen, L., Fang, Z., Zhang, X., Wang, J., et al. (2014b). Chitosan/Phytic Acid Polyelectrolyte Complex: A green and Renewable Intumescent Flame Retardant System for Ethylene-Vinyl Acetate Copolymer. Ind. Eng. Chem. Res. 53 (49), 19199–19207. doi:10.1021/ie503421f
Zhang, X., Zhou, Z., Zhu, Y., Dai, J., Yu, Y., and Song, P. (2019). High-pressure Steam: A Facile Strategy for the Scalable Fabrication of Flattened Bamboo Biomass. Ind. Crops Prod. 129, 97–104. doi:10.1016/j.indcrop.2018.11.061
Zhang, Y., Zhang, X., Yu, Y., Che, W., Zhang, X., and Hou, J. (2020). Evaluating the Comprehensive Influences of Heat Treatment and Polydimethylsiloxane on Integrated Performance of Bamboo Timber. RSC Adv. 10 (71), 43438–43446. doi:10.1039/d0ra08713k
Keywords: shaving super bamboo, phytic acid (PA), polyethyleneimine (PEI), self-assembly, flame retardancy
Citation: Lin P, Jiang Y, Ru X, Che W, Zhang X, Ma L, Hou J and Yu Y (2021) Evaluating the Flame Retardancy of Shaving Super Bamboo Layer by Layer Self-Assembly With Phytic Acid-Polyethyleneimine. Front. Mater. 8:697732. doi: 10.3389/fmats.2021.697732
Received: 20 April 2021; Accepted: 21 June 2021;
Published: 16 August 2021.
Edited by:
Yan Zhang, Zhejiang University, ChinaReviewed by:
Weizhao Hu, University of Science and Technology of China, ChinaSeyed Mohsen Seraji, University of Southern Queensland, Australia
Hongqiang Yan, Zhejiang University, China
Copyright © 2021 Lin, Jiang, Ru, Che, Zhang, Ma, Hou and Yu. This is an open-access article distributed under the terms of the Creative Commons Attribution License (CC BY). The use, distribution or reproduction in other forums is permitted, provided the original author(s) and the copyright owner(s) are credited and that the original publication in this journal is cited, in accordance with accepted academic practice. No use, distribution or reproduction is permitted which does not comply with these terms.
*Correspondence: Junfeng Hou, aG91anVuZmVuZ0B6YWZ1LmVkdS5jbg==; Youming Yu, eXV5b3VtaW5nQHphZnUuZWR1LmNu