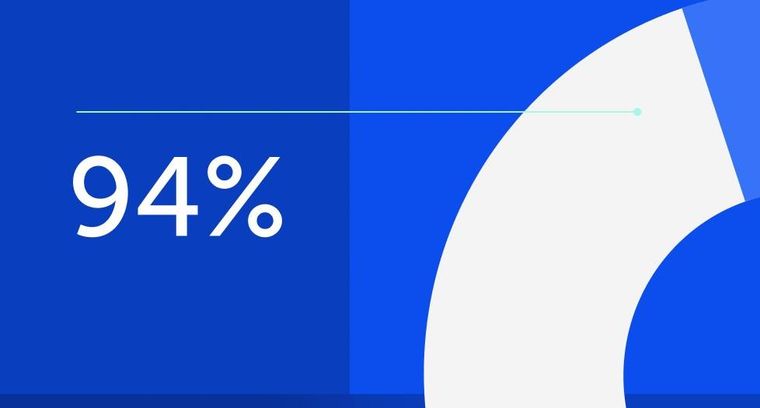
94% of researchers rate our articles as excellent or good
Learn more about the work of our research integrity team to safeguard the quality of each article we publish.
Find out more
ORIGINAL RESEARCH article
Front. Mater., 06 July 2021
Sec. Smart Materials
Volume 8 - 2021 | https://doi.org/10.3389/fmats.2021.692273
This article is part of the Research Topic2021 Retrospective: Smart MaterialsView all 11 articles
There are a lot of vibrational energies, which are low frequency, multidirectional, and broadband, in the nature. This creates difficulties for devices that aim at harvesting vibration energy. Here, we present a liquid-metal-based freestanding triboelectric generator (LM-FTG) for vibration energy harvesting. In this device, the fluidity of liquid is used to increase sensitivity to vibration for better low-frequency response and multidirectional vibration energy harvesting capability. The freestanding power generation mode is able to increase power generation stability. Experiments show that the bandwidth of LM-FTG can almost cover the entire sweep frequency range, and a 10 μF capacitor can be charged to 6.46 V at 7.5 Hz in 60 s by LM-FTG. In particular, 100 LEDs are illuminated in the low-frequency environmental experiment successfully. The proposed LM-FTG can work in low frequency with large working bandwidth, which provides an effective method for energy harvesting of low-frequency and multidirectional vibrations.
Internet of Things technology and distributed sensor networks have gradually become the development trend of society, such as wearable devices, smart home appliances, and marine monitoring buoys. They are distributed in all aspects of our lives. These devices can only be powered by distributed independent power sources, and the batteries need to be replaced one by one to ensure the reliability of the device, which will greatly increase maintenance costs (Kim et al., 2017; Yildirim et al., 2017). To convert energy from nature, such as light energy (Park et al., 2016; Kim et al., 2015; Wen et al., 2016), heat energy (Siddique et al., 2017; Sebald et al., 2009; Kim et al., 2014), vibration energy (Sang et al., 2019; Li et al., 2019; Wang et al., 2018b), and so on (Starner, 1996; Guo et al., 2016), has become an effective solution (Yu et al., 2019; Jiang et al., 2018; Pu et al., 2018). A wearable textile battery (Lee et al., 2013), charged by polymer solar cells, can effectively harvest the light energy, providing enough power to light up nine LEDs. But, this kind of energy harvester generally has a poor energy harvesting effect because of the small area of the surface and its susceptibility to the environment, such as the night and cloudy days. Although some designs that harvest heat energy to power the devices have been proposed, they are very sensitive to the temperature and humidity of the environment (Kyono et al., 2003). Vibration energy is an inherent solution to harvest the energy from nature and is not so sensitive to environmental factors such as light intensity, temperature, and humidity (Rome et al., 2005; Dai et al., 2012). Vibration occurs widely in nature, for example, in the form of human walking, ocean waves, and vibration of mechanical systems. Typically, these vibrations are low frequency, multidirectional, and broadband, which means that traditional electromagnetic energy harvesters (EMGs) are not suitable (Yang et al., 2010; Zuo et al., 2010; Miki et al., 2012).
The reason why EMG is not suitable is that EMG is based on Faraday’s law of electromagnetic induction, which means that it relates to the time derivative of the electric field (Khaligh et al., 2010; Siddique et al., 2015). So, EMG is generally suitable for high-frequency situations (above 50 Hz) (Zi et al., 2016; Zhu et al., 2019). Although many people have been working to improve the EMG’s capability to operate at low frequencies over the years, it has not been effective for vibrations below 5 Hz because of its incompatibility (Fan et al., 2018; Yildirim et al., 2017a). In addition to EMG, there are some designs that harvest vibration energy with piezoelectric energy harvesters (PEHs) (Zeng et al., 2013; Wei et al., 2013; Safaei et al., 2019; Xiujian et al., 2018). However, PEHs have a common problem: considering the low rate of open-circuit voltage, and piezoelectric modules are often used in series in order to reach the right voltage, which increases the volume of the device. Due to the limited range of the bearing capacity, piezoelectric materials require frequent replacement during usage (Saadon and Sidek, 2011; Liu et al., 2011; Jung et al., 2017).
A triboelectric nanogenerator (TENG) uses the coupling of the triboelectric effect and the electrostatic induction effect, which determine the excellent performance of the TENG in the low-frequency range (Zhang et al., 2014; Qian et al., 2020; Hou et al., 2018; Wang S. et al., 2020; Gao et al., 2018; Wang Z. et al., 2020; Liu et al., 2020a, b). An optimized TENG-based insole designed by Wang (Hou et al., 2013) can harvest the energy of unidirectional vibration excited by contact separation between feet and insoles, which can provide enough power to light up 30 LEDs simultaneously. A self-powered backpack (Yang et al., 2013), which is
Here, we present a liquid-metal-based freestanding triboelectric generator (LM-FTG) to solve the problem of vibration energy harvesting. The power generation mode of LM-FTG is freestanding in order to ensure the stability of power generation, which avoids the situation that the liquid metal cannot contact the metal electrode to generate electricity. We show the details of the specific electricity generation process. The multidirectional harvesting capability and low-frequency adaptability are proved by intuitive experiments and theoretical analysis. In the experiments, we perform an inertial frequency-sweep experiment, which proves the multidirectional and broadband vibration harvesting capability of the device. The power experiment under inertial force constant frequency excitation further proves superiority of different working modes and the low-frequency response of LM-FTG. Through the low-frequency environmental experiment, the practicality of this device is proved.
As shown in Figure 1A, LM-FTG, which consists of an aluminum alloy threaded cylinder, two aluminum alloy threaded caps, a 3D printed material sleeve (polylactic acid), a suitable amount (the height of the liquid level is about a quarter of the height of the container) of the liquid metal (mercury, gallium, or gallium–indium), two triboelectric components, and two silicone seals, is similar in shape to a cylindrical container. In order to prevent the liquid metal from conducting with the external metal shell, which enhances the overall impact resistance, a 3D printed material sleeve is used to isolate the liquid metal from the metal shell. The silicone sealing ring is placed between the aluminum alloy threaded cap and the triboelectric component. By screwing the threaded cap tightly, the container is sealed. When LM-FTG is subjected to external excitation, the internal liquid metal collides between the surfaces of Kapton at both sides to generate electricity. The detailed information of LM-FTG is shown in Supplementary Figure S1.
FIGURE 1. Working principle of LM-FTG. (A) Schematic illustration showing the device configuration of LM-FTG; (B) step-by-step illustration showing the working principle of LM-FTG.
It is worth noting that, in the selection of the liquid metal, we put the droplets of mercury, gallium, and water on the Kapton’s surface, respectively, and observed their surface morphology. As shown in Figure 2, the droplets of mercury and gallium on the Kapton’s surface basically maintain a spherical droplet state while the water is flat on the surface. This proves not only that gallium can be easily separated from Kapton without adhesion but also that mercury has this property. However, compared to mercury, gallium is easier to oxidize in the air and forms an oxide layer that is difficult to detach on the Kapton’s surface. In response to this phenomenon, we chose mercury, which is extremely difficult to oxidize, as the liquid metal in LM-FTG.
FIGURE 2. Droplets of mercury, gallium, and water on Kapton’s surface. (A) Mercury; (B) gallium; and (C) water.
A complete cycle of the electricity generation process is shown in Figure 1B. The contact-separation movement between the liquid metal and the triboelectric components is driven by the excitation of the outer casing. First, after pouring the liquid metal into the container, the liquid metal makes contact with the Kapton surface on one side. Due to the different capabilities of the liquid metal and Kapton to absorb electrons, electrons are transferred from the liquid metal onto the Kapton’s surface, causing positive charges at the interface of the liquid metal and negative charges on the Kapton’s surface. Then, the two materials are separated by the external excitation, and a potential difference is formed between them. In order to counteract the electric field, electrons will flow from the lower surface copper electrode to the upper surface copper electrode, which forms a reverse current. As the liquid metal continues to rise, it will collide with the upper Kapton’s surface. Similar to the previous process, the liquid metal also undergoes charge transfer with the upper Kapton. Finally, during the liquid-metal drop process, due to the potential difference between the liquid metal and the upper surface, it will produce a current in the opposite direction to the previous process. Therefore, the pulse output of the entire process exhibits the characteristics of AC. In particular, this freestanding power generation mode causes the device to contact-separate the upper and lower surfaces twice in one power generation cycle, so it is equivalent to two power generations, which increases the number of power generations and improves power generation efficiency. In addition, compared with the first proposed sliding friction power generation mode, this power generation mode does not need to ensure that the internal liquid metal is always in contact with the conductor, which increases the stability of power generation.
Since the internal liquid metal can generate electricity just by impacting and shaking between Kapton at both sides, we set four working modes, which are vertical placement and vertical vibration (VV mode), vertical placement and horizontal vibration (VH mode), horizontal placement and vertical vibration (HV mode), and horizontal placement and horizontal vibration (HH mode), according to the LM-FTG’s placement and vibration direction. Figure 3 shows the liquid flow mode under different working modes. In order to prove that the vibration modes are similar to the pictures, we put the liquid metal in the transparent tube and shook the hand to simulate vibration (see Supplementary Movies S1–S4). It can be seen from the video that the liquid metal can impact surfaces of both sides regardless of the working mode under external excitation. So, the multidirectional vibration harvesting capability of LM-FTG can also be demonstrated.
FIGURE 3. Internal liquid flow. (A) Liquid flow in the VV mode; (B) liquid flow in the VH mode; (C) liquid flow in the HV mode; and (D) liquid flow in the HH mode.
In order to prove that the liquid metal can better respond to external low-frequency vibration, we develop the fluid field equations for one of the working modes and estimate the relationship between the liquid free surface wave height and the frequency of external excitation. As shown in Figure 4A, we assume that LM-FTG works in the VH mode and set up an inertial frame and a moving coordinate system. The height of the liquid surface is represented by h, and the radius of the circular surface of the cylindrical container is represented by R.
FIGURE 4. (A) Cylindrical tank under sinusoidal lateral excitation. (B) Relationship between maximum wave height
Assuming the container is laterally excited in the x-axis direction,
where A and ω are the excitation amplitude and frequency, respectively. Since the analysis can be simplified if the fluid equations are linearized for small displacements, the linearized fluid field equations take the form
The dynamic and kinematic free surface conditions in Eq. 4 and Eq. 5 can be combined into
A typical solution of Eq. 2 subject to conditions in Eq. 3 is
where
where
Substituting Eq. 8 into Eq. 7, Eq. 7 can be rewritten as
The total potential function is the sum of the fluid perturbed function
Substituting Eq. 10 into condition Eq. 4 gives the surface wave height
The maximum wave height occurs at
We set the amplitude A = 0.001 m and substitute the relevant parameters of LM-FTG into the expression (R = 0.015 m and h = 0.015 m) to obtain the maximum wave height of the liquid surface
In order to explore the performance and characteristics of LM-FTG, we conducted two major experiments based on the experimental environment. The first part is an experiment conducted on a vibrating table, mainly to explore the material properties and multidirectional vibration harvesting capability of LM-FTG. The experimental results also play a guiding role in the subsequent experiments. This part of the experimental system mainly consists of a vibration table (Sushi DC-1000–15) and its controller (RC-3000), a digital multimeter (ZLG DMM6001), a computer, and a resistance box (see Supplementary Figure S2).
The second part of the experiment is a low-frequency environmental experiment, which proves the practicality of this device.
For the experiment on the vibration table, it is mainly divided into three parts, namely, basic output experiment, frequency-sweep experiment, and power experiment. Firstly, the basic output experiment is used to measure the internal resistance of the material, and then, a frequency-sweep test is used to not only investigate the influence of the working modes on the test data but also verify broadband output. The final power experiment explores the continuous discharge capability of LM-FTG at low frequencies and further verifies the effects of different working modes, which plays a guiding role in the low-frequency environmental experiment.
In order to measure the maximum output power and power density of LM-FTG in the frequency-sweep experiment, the basic output of LM-FTG needs to be determined to infer the internal resistance. The output voltage, output current (Figure 5A), and power of LM-FTG (Figure 5B) is measured at constant frequency (10 Hz) and peak-to-peak value (15 mm) excitation. We sequentially change the resistance of the resistance box to measure the output voltage and current of LM-FTG. Then, the optimum resistance of the generator is determined by obtaining the maximum output power. Through the experimental results and drawing, it can be found that the maximum output power is obtained when the resistance is 8 M
FIGURE 5. Basic output of the material. (A) Output voltage and output current of Kapton under different resistance values. (B) The power of Kapton at different resistance values.
According to the analysis of the theoretical part, the working modes of LM-FTG have an impact on its power generation capability. Two fixed LM-FTG’s bases are fixed on the vibration table, and the vertical and horizontal vibration tables are used to test LM-FTG. In order to explore the power generation capability and working bandwidth of each mode, we perform an inertial-force frequency-sweep experiment in four working modes (see Supplementary Figure S3). Figure 6 shows the frequency-domain performance results of LM-FTG under an excitation in which the peak-to-peak value is 13 mm and the frequency f sweep is from 3 to 18 Hz at a frequency rise rate of 0.05 Hz/s.
FIGURE 6. Results of the inertial-force frequency-sweep test under 13 mm peak-to-peak excitation at 3–18 Hz sweep frequency: (A) Output voltage and current of LM-FTG in the VV mode. (B) Output voltage and current of LM-FTG in the VH mode. (C) Output voltage and current of LM-FTG in the HV mode. (D) Output voltage and current of LM-FTG in the HH mode.
It can be seen from Figure 6A that when LM-FTG is in the VV mode, the output of LM-FTG always shows an upward trend after 6.2 Hz (the effective frequency bands, which are the colored areas, are defined as the frequency bands, where the output voltage exceeds 10 V), and the peak output voltage and current can reach 252 V and 25.2 μA, respectively. However, in the case of the VH mode (Figure 6B), LM-FTG has a small output after 16.2 Hz, and the peak output can only reach 15 V and 0.2 μA, which is not ideal. Figures 6C,D show the situation of horizontal placement. It can be seen from Figure 6C that, for the vertical vibration, LM-FTG starts to show an obvious output after 5.2 Hz. Although the peak output can only reach 58 V and 5.8 μA, the output is relatively stable, which covers the entire frequency band after 5.2 Hz. In particular, in the case of horizontal vibration, the output, which is shown in Figure 6D, achieves a full-band coverage of 3–18 Hz, and the peak output can reach 181 V and 1.8 μA. Based on the abovementioned data, it can be seen that, in the case of vertical placement, although the maximum peak output in the four modes can be achieved in vertical vibration and the frequency band width is great, the response to the horizontal vibration is poor, which hardly has output and is difficult to meet the energy harvesting of multidirectional vibrations. When placed horizontally, although the peak output does not shine in the two vibration directions, it has a wide frequency band and even achieves full-band coverage under horizontal vibration, which is more in line with the requirements of vibration energy harvesting. It is worth noting that LM-FTG has a good effect in both VV and HH modes. The reason is that the vibration direction in these two modes is kept parallel to the tank body, which can ensure that the liquid metal is better contacted and separated from the Kapton on both sides.
The power density of LM-FTG can be calculated according to the formula
FIGURE 7. Power density of the frequency-sweep test under 13 mm peak-to-peak excitation at 3–18 Hz sweep frequency. (A) Power density of LM-FTG in the VV mode. (B) Power density of LM-FTG in the VH mode. (C) Power density of LM-FTG in the HV mode. (D) Power density of LM-FTG in the HH mode.
In order to explore the impact of different amplitudes on LM-FTG, we performed sweep experiments on LM-FTG with the peak-to-peak values of 9 and 16 mm (see Supplementary Figure S6). Although the output voltage and current are proportional to the amplitude in some working modes, there is not much difference in the working frequency band and output of LM-FTG under these three amplitude conditions.
In order to verify LM-FTGs ability of vibration harvesting at low frequency and further prove the conclusion about the influence of working modes on harvesting capability, we performed the power experiment using the capacitor to charge in four modes like the frequency-sweep experiment. The vibration amplitude of the vibration table is set to 13 mm and the excitation frequencies applied are 6, 6.5, 7, and 7.5 Hz. The output of LM-FTG is connected to a 10 μF electrolytic capacitor to charge it, and the capacitor voltage is measured by a digital multimeter.
It can be seen from Figure 8B that, in the vertical placement, the output power of LM-FTG is very low when excited by the horizontal direction. Within 60 s, the voltage of the capacitor is below 0.4 V. Figure 8A shows the results when the vibration direction is vertical. The output power of LM-FTG is not ideal at 6 Hz, and the capacitor is only charged to 1.05 V. As the frequency gradually increases to 6.5, 7, and 7.5 Hz, the voltage of the capacitor suddenly increases to 4.68, 5.90, and 6.36 V. In the horizontal placement, the voltage of the capacitor reaches 1.89, 2.43, 2.89, and 3.02 V within 60 s at the excitation frequencies of 6, 6.5, 7, and 7.5 Hz when excited in the vertical direction. When excited by the vertical direction, the output voltage increases to 2.22, 3.50, 5.14, and 6.46 V. At horizontal placement, not only the device shows great harvesting capability for both directions of vibration but also the harvesting of low-frequency vibration energy is better than the vertical placement. In general, similar to the conclusion of the sweep-frequency experiment, LM-FTG has a good effect when the vibration direction is parallel to the tank body.
FIGURE 8. Voltage of the 10 μF capacitor charged by LM-FTG. (A) Low-frequency response of LM-FTG in the VV mode. (B) Low-frequency response of LM-FTG in the VH mode. (C) Low-frequency response of LM-FTG in the HV mode. (D) Low-frequency response of LM-FTG in the HH mode.
Since the walking vibration not only has the characteristics of low frequency, multidirection, and broadband but also is very common, we use the walking experiment to prove the practicality of LM-FTG. In the frequency-sweep experiment, the influence of the placement on the harvesting capability is verified. Here, in order to verify the impact of the placement in practice, we tied two identical LM-FTGs to the two calves in two ways (Figure 9) and conducted the walking experiment. In particular, for verifying the effect of walking speed on the LM-FTG’s harvesting capability, we measure the output voltage of LM-FTG and the acceleration of walking (see Supplementary Figure S4) at speeds of 0.8, 1.2, 2 ,and 4 m/s.
FIGURE 9. (A) LM-FTG in horizontal placement.(B) LM-FTG in vertical placement. (C) Output voltage of LM-FTG in horizontal placement. (D) Output voltage of LM-FTG in vertical placement.
Figure 9C shows the output voltage of LM-FTG under horizontal placement. It can be seen intuitively that the output voltage of LM-FTG increases with the increase in walking speed, which is an obvious proportional relationship. As shown in Figure 7C, the peak output voltage of LM-FTG is only 48 V at a walking speed of 0.8 m/s, while the peak output voltages of 1.2, 2, and 4 m/s reach 71, 82, and 169 V, respectively. The huge impact of walking speed on the open circuit voltage was verified. However, compared with the output voltage of LM-FTG in the vertical mode shown in Figure 9D, it can be seen that the difference of the output voltages is not obvious at the four walking speeds, and the peak output voltages do not exceed 50 V at most. The conclusions drawn in the frequency-sweep experiment are verified in practice.
In order to investigate the vibration frequency of walking, we measure the acceleration (see Supplementary Figure S3) of walking at the speed of 0.8 and 4 m/s. Figure 10A shows the spectrograms obtained by Fourier transform of the measured acceleration data at walking speeds of 0.8 and 4 m/s. As can be seen from Figure 10A, at a walking speed of 0.8 m/s, most of the frequency components are concentrated around 2.4 and 5 Hz. In this case where the effective band is defined as a band having an amplitude of 0.4 or more, the vibration frequency ranges from 0 to 20.82 Hz. This proves that the general walking vibration frequency band is wide and mainly concentrated in the low-frequency range. Figure 10B shows the spectrum at a walking speed of 4 m/s. Most of the frequency components are also concentrated below 5 Hz, but the frequency range can range from 0 to 32.03 Hz. By comparison, it can be seen that most of the frequency components are concentrated below 5 Hz, but the increase in speed increases the bandwidth. In summary, it can be shown that the vibration frequency of walking is mostly concentrated in 0–3 Hz, and the power generation experiment under actual walking can prove the LM-FTG’s harvesting capability in this frequency band.
In order to more intuitively demonstrate the power generation capability of LM-FTG, we wanted to light up LEDs with LM-FTG in actual walking. According to the previous experiments, we attached LM-FTG to the calf under the horizontal mode and it successfully lit up 100 series-connected LEDs (see Supplementary Movie S5).
In order to harvest vibration energy which is low frequency, multidirectional, and broadband, a triboelectric generator, which bases on the liquid metal and freestanding power generation mode, has been proposed. The device utilizes the fluidity of the liquid to more efficiently harvest low-frequency and multidirectional vibrations. Also, the freestanding power generation mode is used to decrease the structural complexity and ensure the stability of power generation. The frequency-sweep experiment shows that the difference of the working modes has a great influence on the power generation capability. The multidirectional vibration can be harvested and the working frequency band of LM-FTG is wide. In addition, the peak output can reach up to 252 V and 25.2 μA, and a 10 μF capacitor can be charged to 6.46 V at 7.5 Hz in 60 s by LM-FTG. In the low-frequency environmental experiment, the peak output voltage of LM-FTG under the horizontal mode with 4 m/s of the walking speed can reach 169 V and it can light up 100 LEDs in walking.
In addition, although the experiment was only carried out under the condition of wearing, the device can also be used in more fields. As shown in Figure 11, LM-FTG can be placed in the marine buoy to harvest wave energy from ocean waves or placed in the car suspension to harvest the vibrational energy of the car. So, we believe that LM-FTG not only provides a welcome boost for the development of a vibration energy harvester but also has a broader application prospect.
The raw data supporting the conclusions of this article will be made available by the authors, without undue reservation.
HD, ZZ, and CJ conceived and designed the manuscript. JY, SZ, MM, and XZ revised it. All authors contributed to the article and approved the submitted version.
The authors appreciate the support of the National Natural Science Foundation of China (Grant Nos. 11872167, 51675156, 51775164, and 51705122) and Natural Science Foundation of Anhui 281 Province (No. 1908085J15).
The authors declare that the research was conducted in the absence of any commercial or financial relationships that could be construed as a potential conflict of interest.
The Supplementary Material for this article can be found online at: https://www.frontiersin.org/articles/10.3389/fmats.2021.692273/full#supplementary-material
Chen, J., Guo, H., Zheng, J., Huang, Y., Liu, G., Hu, C., et al. (2016). Self-Powered Triboelectric Micro Liquid/Gas Flow Sensor for Microfluidics. ACS Nano 10, 8104–8112. doi:10.1021/acsnano.6b04440
Dai, D., Liu, J., and Zhou, Y. (2012). Harvesting Biomechanical Energy in the Walking by Shoe Based on Liquid Metal Magnetohydrodynamics. Front. Energ. 6, 112–121. doi:10.1007/s11708-012-0186-x
Deng, H., Du, Y., Wang, Z., Ye, J., Zhang, J., Ma, M., et al. (2019a). Poly-stable Energy Harvesting Based on Synergetic Multistable Vibration. Commun. Phys. 2, 10. doi:10.1038/s42005-019-0117-9
Deng, H., Ye, J., Du, Y., Zhang, J., Ma, M., and Zhong, X. (2019b). Bistable Broadband Hybrid Generator for Ultralow-Frequency Rectilinear Motion. Nano Energy 65, 103973. doi:10.1016/j.nanoen.2019.103973
Fan, K., Liu, S., Liu, H., Zhu, Y., Wang, W., and Zhang, D. (2018). Scavenging Energy from Ultra-low Frequency Mechanical Excitations through a Bi-directional Hybrid Energy Harvester. Appl. Energ. 216, 8–20. doi:10.1016/j.apenergy.2018.02.086
Gao, H., Minh, P. T., Wang, H., Minko, S., Locklin, J., Nguyen, T., et al. (2018). High-performance Flexible Yarn for Wearable Piezoelectric Nanogenerators. Smart Mater. Struct. 27, 095018. doi:10.1088/1361-665X/aad718
Guo, H., Yeh, M.-H., Lai, Y.-C., Zi, Y., Wu, C., Wen, Z., et al. (2016). All-in-one Shape-Adaptive Self-Charging Power Package for Wearable Electronics. ACS Nano 10, 10580–10588. doi:10.1021/acsnano.6b06621
Harne, R. L., and Wang, K. W. (2013). A Review of the Recent Research on Vibration Energy Harvesting via Bistable Systems. Smart Mater. Struct. 22, 023001. doi:10.1088/0964-1726/22/2/023001
Hou, T.-C., Yang, Y., Zhang, H., Chen, J., Chen, L.-J., and Lin Wang, Z. (2013). Triboelectric Nanogenerator Built inside Shoe Insole for Harvesting Walking Energy. Nano Energy 2, 856–862. doi:10.1016/j.nanoen.2013.03.001
Hou, X., Zhu, J., Qian, J., Niu, X., He, J., Mu, J., et al. (2018). Stretchable Triboelectric Textile Composed of Wavy Conductive-Cloth PET and Patterned Stretchable Electrode for Harvesting Multivariant Human Motion Energy. ACS Appl. Mater. Inter. 10, 43661–43668. doi:10.1021/acsami.8b16267
Jiang, Q., Wu, C., Wang, Z., Wang, A. C., He, J.-H., Wang, Z. L., et al. (2018). MXene Electrochemical Microsupercapacitor Integrated with Triboelectric Nanogenerator as a Wearable Self-Charging Power Unit. Nano Energy 45, 266–272. doi:10.1016/j.nanoen.2018.01.004
Jung, I., Shin, Y.-H., Kim, S., Choi, J.-y., and Kang, C.-Y. (2017). Flexible Piezoelectric Polymer-Based Energy Harvesting System for Roadway Applications. Appl. Energ. 197, 222–229. doi:10.1016/j.apenergy.2017.04.020
Khaligh, A., Peng Zeng, P., and Cong Zheng, C. (2010). Kinetic Energy Harvesting Using Piezoelectric and Electromagnetic Technologies-State of the Art. IEEE Trans. Ind. Electron. 57, 850–860. doi:10.1109/TIE.2009.2024652
Kim, B. J., Kim, D. H., Lee, Y.-Y., Shin, H.-W., Han, G. S., Hong, J. S., et al. (2015). Highly Efficient and Bending Durable Perovskite Solar Cells: toward a Wearable Power Source. Energy Environ. Sci. 8, 916–921. doi:10.1039/c4ee02441a
Kim, J., Kumar, R., Bandodkar, A. J., and Wang, J. (2017). Advanced Materials for Printed Wearable Electrochemical Devices: a Review. Adv. Electron. Mater. 3, 1600260. doi:10.1002/aelm.201600260
Kim, S. J., We, J. H., and Cho, B. J. (2014). A Wearable Thermoelectric Generator Fabricated on a Glass Fabric. Energ. Environ. Sci. 7, 1959–1965. doi:10.1039/c4ee00242c
Kyono, T., Suzuki, R. O., and Ono, K. (2003). Conversion of Unused Heat Energy to Electricity by Means of Thermoelectric Generation in Condenser. IEEE Trans. Energ. Convers. 18, 330–334. doi:10.1109/TEC.2003.811721
Lee, Y.-H., Kim, J.-S., Noh, J., Lee, I., Kim, H. J., Choi, S., et al. (2013). Wearable Textile Battery Rechargeable by Solar Energy. Nano Lett. 13, 5753–5761. doi:10.1021/nl403860k
Li, Y., Shen, W., and Zhu, H. (2019). Vibration Mitigation of Stay Cables Using Electromagnetic Inertial Mass Dampers: Full-Scale experiment and Analysis. Eng. Structures 200, 109693. doi:10.1016/j.engstruct.2019.109693
Lin, Z.-H., Cheng, G., Lin, L., Lee, S., and Wang, Z. L. (2013). Water-solid Surface Contact Electrification and its Use for Harvesting Liquid-Wave Energy. Angew. Chem. 125, 12777–12781. doi:10.1002/ange.201307249
Liu, H., Tay, C. J., Quan, C., Kobayashi, T., and Lee, C. (2011). Piezoelectric MEMS Energy Harvester for Low-Frequency Vibrations with Wideband Operation Range and Steadily Increased Output Power. J. Microelectromech. Syst. 20, 1131–1142. doi:10.1109/JMEMS.2011.2162488
Liu, W., Wang, Z., Wang, G., Zeng, Q., He, W., Liu, L., et al. (2020a). Switched-capacitor-convertors Based on Fractal Design for Output Power Management of Triboelectric Nanogenerator. Nat. Commun. 11, 1883. doi:10.1038/s41467-020-15373-y
Liu, Y., Liu, W., Wang, Z., He, W., Tang, Q., Xi, Y., et al. (2020b). Quantifying Contact Status and the Air-Breakdown Model of Charge-Excitation Triboelectric Nanogenerators to Maximize Charge Density. Nat. Commun. 11, 1599. doi:10.1038/s41467-020-15368-9
Miki, S., Fujita, T., Kotoge, T., Jiang, Y. G., Uehara, M., Kanda, K., Higuchi, K., and Maenaka, K. (2012). “Electromagnetic Energy Harvester by Using Buried NdFeB,” in 2012 IEEE 25th International Conference on Micro Electro Mechanical Systems (MEMS), 1221–1224. doi:10.1109/memsys.2012.6170409
Park, M., Kim, J.-Y., Son, H. J., Lee, C.-H., Jang, S. S., and Ko, M. J. (2016). Low-temperature Solution-Processed Li-Doped SnO2 as an Effective Electron Transporting Layer for High-Performance Flexible and Wearable Perovskite Solar Cells. Nano Energy 26, 208–215. doi:10.1016/j.nanoen.2016.04.060
Pu, X., Hu, W., and Wang, Z. L. (2018). Toward Wearable Self-Charging Power Systems: the Integration of Energy-Harvesting and Storage Devices. Small 14, 1702817. doi:10.1002/smll.201702817
Qian, J., He, J., Qian, S., Zhang, J., Niu, X., Fan, X., et al. (2020). A Nonmetallic Stretchable Nylon‐Modified High Performance Triboelectric Nanogenerator for Energy Harvesting. Adv. Funct. Mater. 30, 1907414. doi:10.1002/adfm.201907414
Rome, L. C., Flynn, L., Goldman, E. M., and Yoo, T. D. (2005). Generating Electricity while Walking with Loads. Science 309, 1725–1728. doi:10.1126/science.1111063
Saadon, S., and Sidek, O. (2011). A Review of Vibration-Based MEMS Piezoelectric Energy Harvesters. Energ. Convers. Manage. 52, 500–504. doi:10.1016/j.enconman.2010.07.024
Safaei, M., Sodano, H. A., and Anton, S. R. (2019). A Review of Energy Harvesting Using Piezoelectric Materials: State-Of-The-Art a Decade Later (2008-2018). Smart Mater. Struct. 28, 113001. doi:10.1088/1361-665X/ab36e4
Sang, M., Wang, S., Liu, S., Liu, M., Bai, L., Jiang, W., et al. (2019). A Hydrophobic, Self-Powered, Electromagnetic Shielding PVDF-Based Wearable Device for Human Body Monitoring and protection. ACS Appl. Mater. Inter. 11, 47340–47349. doi:10.1021/acsami.9b16120
Sebald, G., Guyomar, D., and Agbossou, A. (2009). On Thermoelectric and Pyroelectric Energy Harvesting. Smart Mater. Struct. 18, 125006. doi:10.1088/0964-1726/18/12/125006
Siddique, A. R. M., Mahmud, S., and Heyst, B. V. (2015). A Comprehensive Review on Vibration Based Micro Power Generators Using Electromagnetic and Piezoelectric Transducer Mechanisms. Energ. Convers. Manage. 106, 728–747. doi:10.1016/j.enconman.2015.09.071
Siddique, A. R. M., Mahmud, S., and Heyst, B. V. (2017). A Review of the State of the Science on Wearable Thermoelectric Power Generators (TEGs) and Their Existing Challenges. Renew. Sustain. Energ. Rev. 73, 730–744. doi:10.1016/j.rser.2017.01.177
Starner, T. (1996). Human-powered Wearable Computing. IBM Syst. J. 35, 618–629. doi:10.1147/sj.353.0618
Tang, W., Jiang, T., Fan, F. R., Yu, A. F., Zhang, C., Cao, X., et al. (2015). Liquid-metal Electrode for High-Performance Triboelectric Nanogenerator at an Instantaneous Energy Conversion Efficiency of 70.6%. Adv. Funct. Mater. 25, 3718–3725. doi:10.1002/adfm.201501331
Wang, S., Ding, L., Fan, X., Jiang, W., and Gong, X. (2018a). A Liquid Metal-Based Triboelectric Nanogenerator as Stretchable Electronics for Safeguarding and Self-Powered Mechanosensing. Nano Energy 53, 863–870. doi:10.1016/j.nanoen.2018.09.035
Wang, S., Gong, L., Shang, Z., Ding, L., Yin, G., Jiang, W., et al. (2018b). Novel Safeguarding Tactile E-Skins for Monitoring Human Motion Based on SST/PDMS-AgNW-PET Hybrid Structures. Adv. Funct. Mater. 28, 1707538. doi:10.1002/adfm.201707538
Wang, S., Yuan, F., Liu, S., Zhou, J., Xuan, S., Wang, Y., et al. (2020). A Smart Triboelectric Nanogenerator with Tunable Rheological and Electrical Performance for Self-Powered Multi-Sensors. J. Mater. Chem. C 8, 3715–3723. doi:10.1039/C9TC05969E
Wang, Z., Liu, W., Hu, J., He, W., Yang, H., Ling, C., et al. (2020). Two Voltages in Contact-Separation Triboelectric Nanogenerator: From Asymmetry to Symmetry for Maximum Output. NANO ENERGY 69, 104452. doi:10.1016/j.nanoen.2020.104452
Wei, S., Hu, H., and He, S. (2013). Modeling and Experimental Investigation of an Impact-Driven Piezoelectric Energy Harvester from Human Motion. Smart Mater. Struct. 22, 105020. doi:10.1088/0964-1726/22/10/105020
Wen, Z., Yeh, M.-H., Guo, H., Wang, J., Zi, Y., Xu, W., et al. (2016). Self-powered Textile for Wearable Electronics by Hybridizing Fiber-Shaped Nanogenerators, Solar Cells, and Supercapacitors. Sci. Adv. 2, e1600097. doi:10.1126/sciadv.1600097
Xie, J., Li, F., Kuang, S., Yang, H., Li, X., Tang, S., et al. (2020). Modeling and Motion Control of a Liquid Metal Droplet in a Fluidic Channel. Ieee/asme Trans. Mechatron. 25, 942–950. doi:10.1109/TMECH.2020.2964387
Xiujian, C., Jie, Z., Shuo, Q., Xushi, N., Jichao, Q., Xiaojuan, H., et al. (2018). All-in-one Filler-Elastomer-Based High-Performance Stretchable Piezoelectric Nanogenerator for Kinetic Energy Harvesting and Self-Powered Motion Monitoring. Nano Energy 53, 550. doi:10.1016/j.nanoen.2018.09.006
Yang, B., Lee, C., Wei, L. K., and Lim, S.-P. (2010). Hybrid Energy Harvester Based on Piezoelectric and Electromagnetic Mechanisms. J. Micro/nanolith. MEMS MOEMS 9, 023002. doi:10.1117/1.3373516
Yang, W., Chen, J., Zhu, G., Yang, J., Bai, P., Su, Y., et al. (2013). Harvesting Energy from the Natural Vibration of Human Walking. ACS Nano 7, 11317–11324. doi:10.1021/nn405175z
Yang, Y., Sun, N., Wen, Z., Cheng, P., Zheng, H., Shao, H., et al. (2018). Liquid-Metal-Based Super-stretchable and Structure-Designable Triboelectric Nanogenerator for Wearable Electronics. ACS Nano 12, 2027–2034. doi:10.1021/acsnano.8b00147
Yildirim, T., Ghayesh, M. H., Li, W., and Alici, G. (2017a). A Nonlinearly Broadband Tuneable Energy Harvester. J. Dynamic Syst. Meas. Control. 139, 011008. doi:10.1115/1.4034321
Yildirim, T., Ghayesh, M. H., Li, W., and Alici, G. (2017). A Review on Performance Enhancement Techniques for Ambient Vibration Energy Harvesters. Renew. Sustain. Energ. Rev. 71, 435–449. doi:10.1016/j.rser.2016.12.073
Yildirim, T., Ghayesh, M. H., Searle, T., Li, W., and Alici, G. (2017b). A Parametrically Broadband Nonlinear Energy Harvester. J. Energ. Resour. Tech. 139, 011008. doi:10.1115/1.4034514
Yu, L., Yi, Y., Yao, T., Song, Y., Chen, Y., Li, Q., et al. (2019). All VN-Graphene Architecture Derived Self-Powered Wearable Sensors for Ultrasensitive Health Monitoring. Nano Res. 12, 331–338. doi:10.1007/s12274-018-2219-1
Zeng, W., Tao, X.-M., Chen, S., Shang, S., Chan, H. L. W., and Choy, S. H. (2013). Highly Durable All-Fiber Nanogenerator for Mechanical Energy Harvesting. Energ. Environ. Sci. 6, 2631–2638. doi:10.1039/c3ee41063c
Zhang, C., Tang, W., Han, C., Fan, F., and Wang, Z. L. (2014). Theoretical Comparison, Equivalent Transformation, and Conjunction Operations of Electromagnetic Induction Generator and Triboelectric Nanogenerator for Harvesting Mechanical Energy. Adv. Mater. 26, 3580–3591. doi:10.1002/adma.201400207
Zhang, J., Yan, S., Yuan, D., Alici, G., Nguyen, N.-T., Ebrahimi Warkiani, M., et al. (2016). Fundamentals and Applications of Inertial Microfluidics: a Review. Lab. Chip 16, 10–34. doi:10.1039/C5LC01159K
Zheng, L., Lin, Z.-H., Cheng, G., Wu, W., Wen, X., Lee, S., et al. (2014). Silicon-based Hybrid Cell for Harvesting Solar Energy and Raindrop Electrostatic Energy. Nano Energy 9, 291–300. doi:10.1016/j.nanoen.2014.07.024
Zhu, H., Li, Y., Shen, W., and Zhu, S. (2019). Mechanical and Energy-Harvesting Model for Electromagnetic Inertial Mass Dampers. Mech. Syst. Signal Process. 120, 203–220. doi:10.1016/j.ymssp.2018.10.023
Zi, Y., Guo, H., Wen, Z., Yeh, M.-H., Hu, C., and Wang, Z. L. (2016). Harvesting Low-Frequency (. ACS Nano 10, 4797–4805. doi:10.1021/acsnano.6b01569
Keywords: vibration energy harvesting, liquid-metal-based, freestanding, low-frequency, multidirectional, broadband
Citation: Deng H, Zhao Z, Jiao C, Ye J, Zhao S, Ma M and Zhong X (2021) A Liquid-Metal-Based Freestanding Triboelectric Generator for Low-Frequency and Multidirectional Vibration. Front. Mater. 8:692273. doi: 10.3389/fmats.2021.692273
Received: 08 April 2021; Accepted: 07 June 2021;
Published: 06 July 2021.
Edited by:
Miao Yu, Chongqing University, ChinaReviewed by:
Yancheng Li, University of Technology Sydney, AustraliaCopyright © 2021 Deng, Zhao, Jiao, Ye, Zhao, Ma and Zhong. This is an open-access article distributed under the terms of the Creative Commons Attribution License (CC BY). The use, distribution or reproduction in other forums is permitted, provided the original author(s) and the copyright owner(s) are credited and that the original publication in this journal is cited, in accordance with accepted academic practice. No use, distribution or reproduction is permitted which does not comply with these terms.
*Correspondence: Huaxia Deng, aHhkZW5nQGhmdXQuZWR1LmNu
Disclaimer: All claims expressed in this article are solely those of the authors and do not necessarily represent those of their affiliated organizations, or those of the publisher, the editors and the reviewers. Any product that may be evaluated in this article or claim that may be made by its manufacturer is not guaranteed or endorsed by the publisher.
Research integrity at Frontiers
Learn more about the work of our research integrity team to safeguard the quality of each article we publish.