- 1Advanced Materials Department, Jožef Stefan Institute, Ljubljana, Slovenia
- 2Jožef Stefan International Postgraduate School, Ljubljana, Slovenia
- 3Microelectronics Research Unit, University of Oulu, Oulu, Finland
In this paper, ceramic upside-down lithium molybdate-strontium titanate (LMO-ST) composites fabricated at room temperature are described. Room temperature fabrication (RTF) is a promising alternative to the time- and energy-consuming high-temperature sintering of electroceramics, which involves mixing of the initial phases, molding with a steel dye, pressing, and drying, while in the last two phases the action of densification takes place. The LMO-ST composites are based on a high ratio of filler ST, coupled with the corresponding LMO binder. Part of the binder is admixed to the ceramic particles and additional part is added as a saturated aqueous solution, which crystallizes during pressing and drying, leading to its deposition on the surface of the filler particles. As a result, sufficient binding with 76–84% relative density was achieved. The deeper insight into the method was provided by various processing aspects and corresponding microstructural investigations. The particle size distribution, pressure, pressing time, ultrasonic treatment, drying time and processing conditions were optimized to obtain improved functional properties of the LMO-ST composites. The results of this study with relative permittivity in the range of 65–78 and dielectric loss tangent values of 0.002–0.05 can attract considerable attention for the use of LMO-ST composites in the industry of electroceramics.
Introduction
To meet the needs and expectations of the global society, it is important to develop new technologies for the production of low-loss microwave dielectric ceramics to be integrated into microelectronic components and electronic circuits as resonators, antennas, filters, and capacitors (Narang and Bahel, 2010; Sebastian et al., 2015; Sulong et al., 2016; Tuhkala et al., 2017). In addition to intrinsic material properties, the broad application value of low-loss ceramics is strongly influenced by various parameters, such as porosity, particle size, stoichiometry, purity of raw constituents and various processing conditions. From a practical point of view, materials need to be engineered to exhibit improved functional properties, along with optimized fabricating conditions that result in a reasonable cost for the final product. Until recently, the production of bulk electroceramics was mainly based on high temperature solid state sintering. The associated disadvantages of high processing temperatures in the microelectronics industry are high energy consumption and complicated post-processing and integration with other materials. In general, the quest for improved functionality of electroceramics requires an adaptation of the fabrication process. In this regard, the demand for environmentally friendly production of electronic devices is ushering in a new era of low temperature fabricated ceramic composites. Novel low temperature densification ceramic methods for compaction (Kähäri et al., 2014; Guo et al., 2016) inspired by natural geological processes and chemical weathering do not require high temperatures, unlike man-made ceramics (Bouville and Studart, 2017).
Reducing processing temperatures and energy for densification in electroceramics using the so-called cold sintering method of LMO ceramic composites has been an intensely studied field recently (Andrews et al., 2020). Strontium titanate (SrTiO3, ST) as a dielectric perovskite material continues to be the focus of intense research due to its high relative permittivity, environmental compatibility, and diverse applicability (Shende et al., 2001). ST-based ceramics are conventionally fabricated by high-temperature solid-state sintering at temperatures around 1,400–1,550°C and exhibit a relative permittivity of 240 and a dielectric loss tangent of 0.0008 (Muhamad et al., 2017) at 10 kHz. In addition, lithium molybdate (Li2MoO4, LMO) has been extensively investigated as a dielectric ceramic (Kähäri et al., 2016; Väätäjä et al., 2018), especially with respect to potential applications as patch antennas and humidity sensors (Kähäri et al., 2017). LMO is generally sintered at temperatures ranging from 500 to 620°C (Zhou et al., 2010; Kähäri et al., 2014). In terms of dielectric properties, LMO exhibits a relative permittivity of 5.1 with corresponding dielectric loss tangent values of 0.0004 at 10 GHz (Kähäri et al., 2014; Väätäjä et al., 2018). In contrast to conventional manufacturing of electronic devices, the LMO-ST ceramic composite system is based on a net-shape technology.
Room temperature fabrication (RTF) was developed by Kähäri et al. (2014), who investigated the potential of water-soluble LMO ceramic compacts by moistening with water and post-processing at room temperature and additionally at 120 and 540°C. Recently, RTF has gained a foothold in the field of ceramic composites. The method has been investigated on ceramic composites of lithium molybdate and lead zirconate titanate (LMO-PZT) (Nelo et al., 2019b) and lithium molybdate and barium strontium titanate (LMO-BST) (Nelo et al., 2019a) ceramic composites. RTF of bulk ceramic upside-down composites is based on the incorporation of a high loading of filler material with the required functional properties and corresponding binder in solid and partly in aqueous form. Maintaining the high filler content and introducing a small amount of the binder into the system reverses the usual structure of 0–3 ceramic composites, hence the term upside-down was introduced. The presence of LMO-saturated solution enables partial dissolution of the binder during pressing (Väätäjä et al., 2018), which thus aids mass transport between particles and the densification process. Consequently, solution precipitation and subsequent rearrangement of the microstructure is achieved. During pressing and drying, water evaporation and solidification take place. The binder crystallizes on the surface of the filler particles, thus physically binding them together. In this way, a lower porosity and a good packing density can be achieved. The novel and innovative technique of ceramics densification at room temperature is advantageous as the ceramics produced in this way have applicable electrical properties without the need for sintering at high temperatures, thus significantly reducing the cost of producing ceramics.
Our research presented in this paper encompasses synthesis of the upside-down composites of ST and LMO for their use in various electronic applications. In this study, the optimization of RTF parameters was investigated. In particular, the effects of powder particle size distribution, ultrasonic treatment, pressure and pressing time during sample compaction, as well as drying time and exposure to moisture were investigated to improve the densification process, including the final packing density and dielectric properties of the LMO-ST composites. In addition, the microstructure of the composites and the mechanical properties were investigated.
In line with the ongoing trends and increasing need for miniaturization of electronic devices, it is important to obtain high functionality of a material that occupies as little space as possible. High relative permittivity and low dielectric losses achieved via RTF of LMO-ST composites might play an important role in device miniaturization, such as electronic circuits for the mobile phone industry (Sebastian et al., 2015).
Materials and Methods
The LMO-ST based samples for RTF experiments were prepared in two stages. In the first stage, ST ceramics were prepared from SrCO3 and TiO2 powders in order to engineer their microstructural properties of further composites (both chemicals ≥ 99.9%, Sigma - Aldrich Co., United States). In the second stage, LMO-ST composites were prepared, and the procedure was similar in many aspects to that developed and used in other studies in the field of RTF upside-down composites (Nelo et al., 2019a, b).
For the synthesis of ST ceramics, SrCO3 powder and TiO2 powder were well-mixed in the appropriate stoichiometric ratio with the addition of ethanol as a mixing medium. The dried powder mixture was pressed into pellets and calcined at 1,100°C for 20 h. After calcination, the pellets were crushed and ground in a mortar using a pestle. Then, the calcined powder was milled using yttria-stabilized zirconia (YSZ) balls, pressed into pellets, and sintered at 1,400°C for 20 h. The two-step process was carried out in a high-temperature furnace in an air atmosphere. The sintered ST ceramics were characterized in detail according to their microstructural and dielectric properties.
The sintered ST pellets were crushed in an agate mortar. The resulting powder was divided by a stack of steel sieves with different mesh sizes (500, 200, 150, 63, and 40 μm; 200 mm in diameter, ISO3310 Endecotts Limited) fixed in a Sieve Shaker (Octagon 200 Sieve shaker, 230 V, 50 Hz, Endecotts Limited). Different size fractions up to 500 μm were obtained. Li2MoO4 (99+%, Alfa Aesar, Thermo Fisher Scientific, Germany) was ground with a pestle in a mortar and sieved to the size fraction below 40 μm. Besides, a saturated solution of LMO and distilled water (solubility 79.5 g/100 ml at 20°C) was also prepared as a binding liquid phase. Ceramic composites were prepared from the mixture of 6.5 wt% dry LMO and 93.5 wt% ST. The same composition was kept constant during the experimental work presented in this paper. ST fractions and the desired amount of LMO were weighed using analytical balance (AG104, Mettler Toledo) and mixed by shaking for 1 min in a 25-mL glass vial. Then, 0.2 mL of a saturated aqueous solution of LMO was added while everything was mixed together and transferred into a 10 mm diameter steel dye. After the mixture was added into the dye, ultrasonic treatment was applied to achieve higher wetting of the particles and their denser distribution. For this purpose, UP100H ultrasonic processor was used with MS1 sonotrode (100 W, 30 kHz, Hielscher Ultrasonics GmbH) set to 100% amplitude and cycle 0.1. The next step was uniaxial pressing of the LMO—ST mixture at room temperature, at a pressure varied from 60 to 1,000 MPa and a pressing time of 1–60 min (Manual Lab press, P/O/Weber, Germany). After pressing, the pellets were weighed and subjected to drying from 3 to 20 h at 110°C. Then, the pellets were weighed again and the water content and total LMO content of 9 wt% were estimated from the mass difference. The dimensions (width and height) of the pellets were measured using a caliper, from which the density of the LMO-ST composites was calculated. The schematic of the LMO-ST sample preparation is shown in Figure 1.
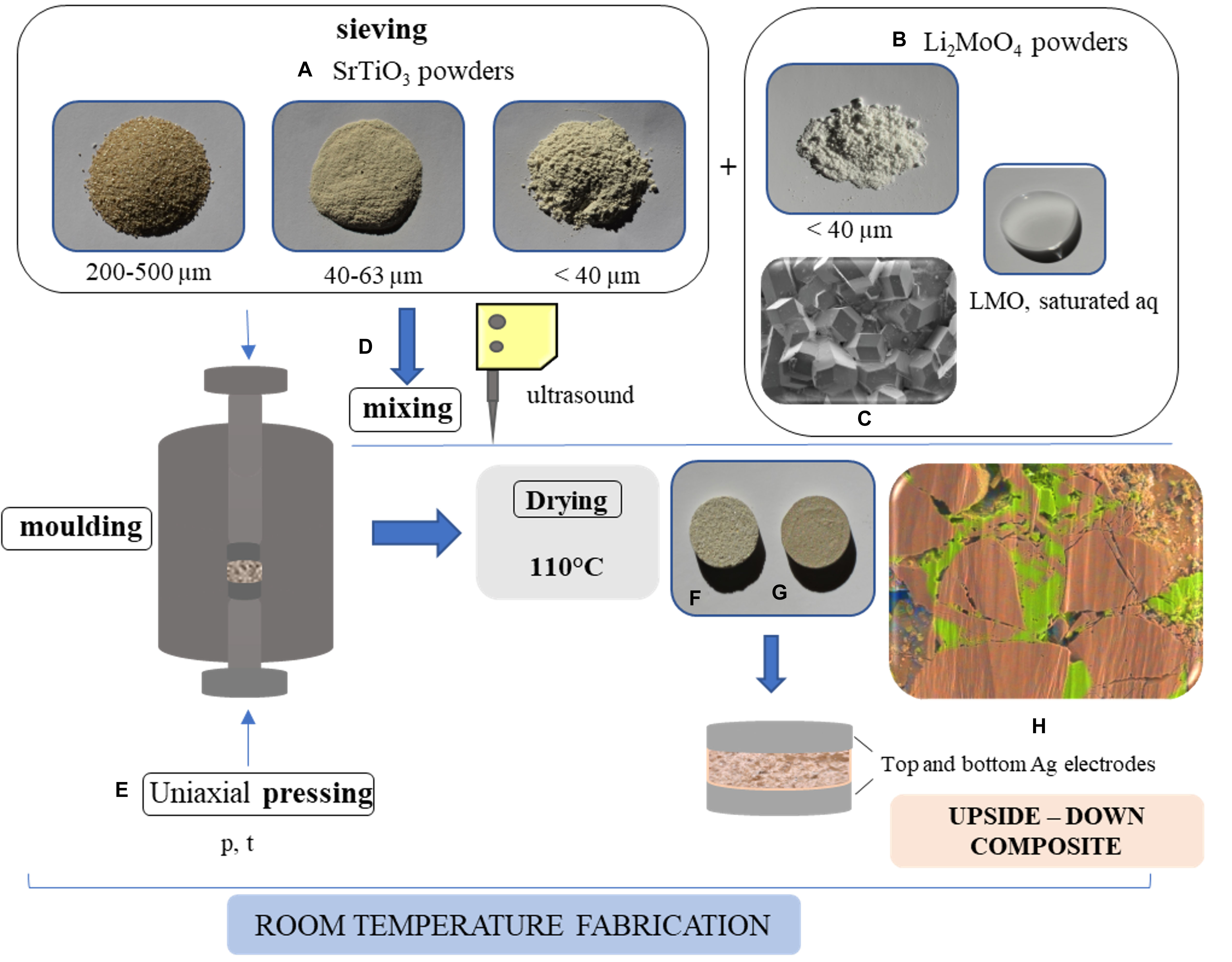
Figure 1. The experimental preparation protocol of upside-down LMO-ST composites is shown on the processing scheme. The initial components showed (A) ST sintered powder, which was subsequently sieved into three different fractions, and (B) LMO binder present in a solid phase (40 μm) as well as in saturated aqueous solution. (C) SEM micrograph of LMO crystals. (D) Mixing assisted by ultrasonic treatment. (E) Uniaxial pressure assisted densification. (F) Dried and densified pellet. (G) A densified pellet with silver electrode applied. (H) EDS mapping of the final LMO-ST composite.
A microstructural analysis was carried out using a scanning electron microscope FESEM Ultra plus (Carl Zeiss, Germany), equipped with an energy dispersive spectrometer (EDS, Inca 400, Oxford Instruments). Before SEM examination, the samples were coated with a 4–5 nm thick Pt layer with PECS (GATAN Inc.). The crystal structure of both constituents and composites was analyzed by X-ray diffraction (XRD, AXS D4 Endeavor, Bruker Instruments) at room temperature. Cross sections of the pellets for SEM/EDS analysis were prepared using an ion beam cross section polisher (IB -19530CP, Jeol). Mechanical properties, such as modulus of elasticity and compressive strength, were measured using the ASTM D695 test standard (Zwick/Roell Z030, United Kingdom). Prior to dielectric measurements, silver paste (DuPont 5064H, DuPont Microcircuits Material, United States) was applied to the top and bottom surfaces of the pellet and dried at 110°C at both sites. Relative permittivity and dielectric losses were measured using Agilent 4284A Precision LCR meter with custom sample holder after open/short circuit calibration. The setup was placed in a desiccator. All dielectric measurements were performed in the frequency range of 20 Hz–1 MHz with an amplitude of 1 V.
Results and Discussion
In the experimental work, we attempt to optimize the RTF method on LMO-ST composites. For this purpose, the influence of different processing parameters on the dielectric properties of the prepared composite samples was evaluated. The experimental results in terms of relative density and relative permittivity are presented with a corresponding error bar of 2% calculated from the accuracy of the measured sample dimensions and LCR meter. Moreover, the error value of the dielectric losses was estimated to be only 0.004% and therefore not further reported. In addition, we also investigated the temperature dependence of the relative permittivity in the temperature range from 20 to 80°C at 1 MHz. The results showed that a typical value of the temperature coefficient ranges from −0.13 to −0.15%, which agrees well with the literature data for ST ceramics (Viana et al., 1994; Muhamad et al., 2017).
Two-component composites consist of functional ST ceramics and LMO binding phase. Preliminary characterization of the as-prepared ST ceramic revealed that calcination and sintering resulted in a very dense ceramic with a high relative density of over 98% and an average grain size of 1.5 μm (Figure 2). The conventionally sintered ST, used as filler, exhibits relative permittivity of 296 and dielectric losses of 0.0015 at 1 MHz. Figure 3 shows the XRD patterns of the representative LMO-ST composite sample and both initial components. The pattern of the composite sample exhibits the characteristic XRD reflections of ST (ICDD No. 35-0734) and LMO (ICDD No. 12-0763), confirming that the components do not react. The intensity of reflections that belong to the LMO phase is weak compared to ST reflections due to the low LMO phase content of about 9 wt%. Nevertheless, the most intense LMO reflections are clearly seen at 2Θ values of 20o, 21.1o, 24.9o, 26.8o, and 27.6o.
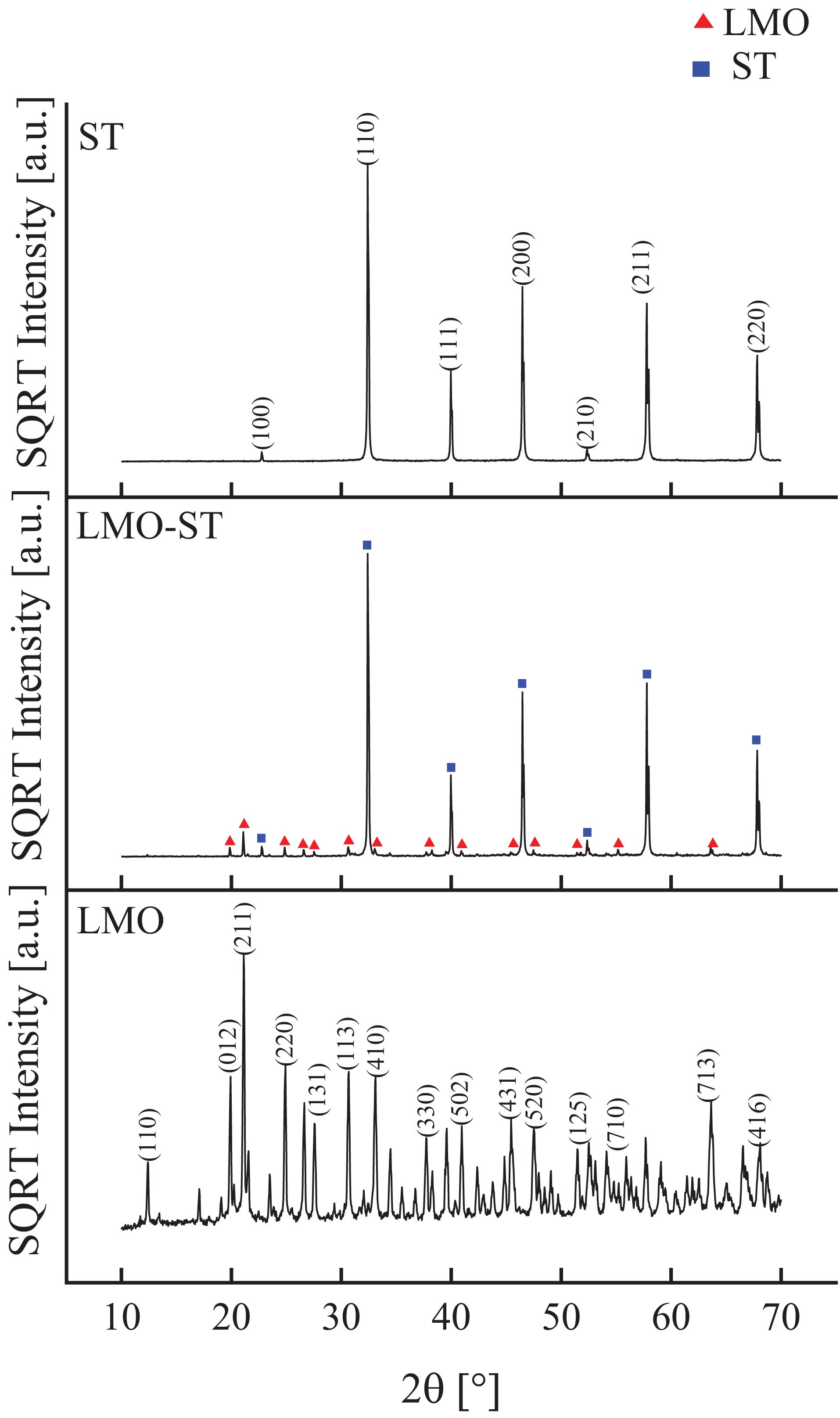
Figure 3. X-ray diffraction patterns of LMO-ST composite, ST sintered at 1,400°C and commercial LMO.
The microstructures of the prepared composites are shown in Figure 4. SEM micrographs, supplemented by EDS mapping, show a typical 0–3 composite microstructure in which LMO is an isolated phase and the ST constituent forms a continuous phase. In Figures 4A–C, the green colored regions are associated with LMO, while the orange colored regions belong to the ST particles. The LMO phase is homogeneously distributed among the larger ST particles (Figure 4A). Moreover, Figures 4A–C show that the samples have significant residual porosity, which is consistent with the results of the density measurements. The LMO phase incorporates smaller ST particles and fills the voids between larger ST particles. The contact between the LMO phase and the ST particles is predominantly tight, yet loose contact can be observed at certain interfaces. Prepared cross sections showed a typical curtaining pattern on the surface as a result of ion beam treatment by the cross section polisher (Figures 4A–C).
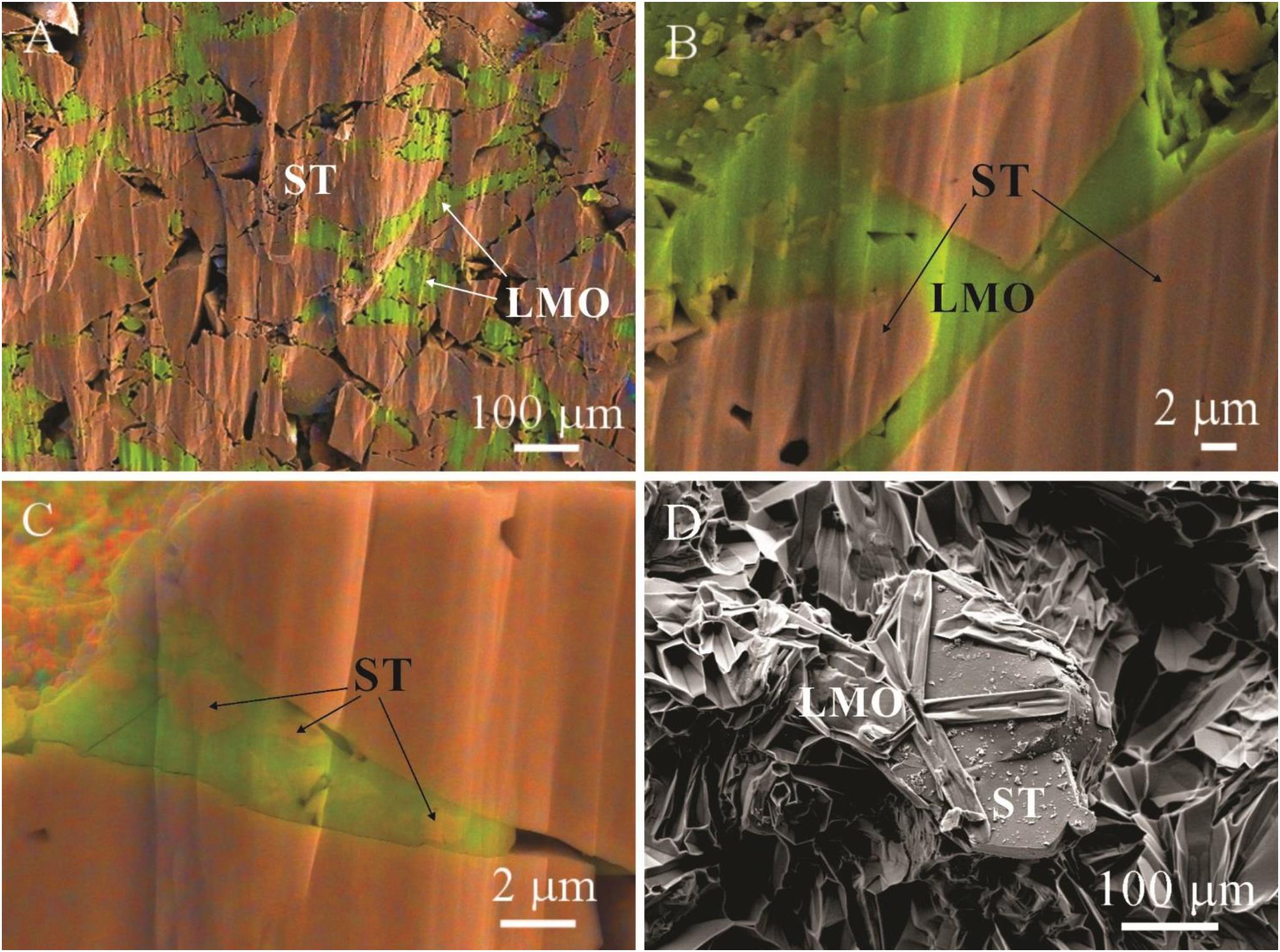
Figure 4. EDS mappings of the cross section (A–C). (B,C) Expanded view of the LMO-ST contact showing good adhesion and bonding of LMO (green color) on the surface of larger and smaller ST particles (orange color). (D) SEM micrograph of the surface of the prepared samples.
Moreover, SEM micrographs of the surface of as-prepared pellets demonstrate that after the densification process, LMO is concentrated at the bottom and top of the pellet. This behavior can be attributed to the pressing phase, where the liquid LMO-rich phase is pressed out at the top and bottom of the steel dye. When the pellets are subjected to drying as post-processing, evaporation of water and extensive crystallization of LMO occur in this area. As a result, we obtain a surface as seen in the micrograph in Figure 4D.
Mechanical characterization of the LMO-ST composites was performed to inspect the stability of the final composite. The results show a compressive strength of 0.69 MPa at 2% strain deformation and a compressive modulus of elasticity of 554 MPa. Room temperature fabricated pellets consisting of different fractions of pure ST powder mixed with water were not stable, which is another indication of the indispensable role of the LMO binder.
The Effect of Particle Size Distribution on Dielectric Properties of LMO-ST Composites
As a first step to investigate different processing parameters in RTF of LMO-ST composites, the effects of particle size and the ratio of different fractions were studied. One of the important physical parameters of as-prepared composites is the packing density, which is desired to be as high as possible as reported in previous works (Kähäri et al., 2015). The packing density is strongly related to the ratio of larger to smaller particles and their volume fractions. As reported, it tends to become lower when the ratio of larger to smaller particles decreases. The packing mechanism can be predicted by the Furnas model in such a way that smaller particles fill the interstices between larger packed particles, resulting in lower porosity (Zheng et al., 1995).
To test the effect of particle size distribution on dielectric properties, the size of ST particles was varied. The size of the LMO particles was constantly ranging below 40 μm. The average value of relative permittivity was taken from a series of three samples prepared under the same experimental conditions and is presented in Table 1. For RTF of LMO-ST composites, the following processing conditions were constantly set: 0.5 min of ultrasonic treatment, 5 min of pressing at 250 MPa, 20 h of drying.

Table 1. The effect of ST particle size fractions on the relative density and dielectric properties of LMO-ST composites fabricated at RT and measured at 1 MHz.
A wide particle size distribution contributes positively to higher relative density values (Nelo et al., 2019b). The use of smaller particles (mixture 1) resulted in the lowest relative density of 76 ± 2%, while higher relative density values of 81 ± 2% and 84 ± 2% were obtained with LMO-ST mixtures 2 and 3, respectively, consisting of larger particles. Following the idea of the influence of particle size distribution on the maximum packing density of randomly dispersed spheres, the initial particle size distribution was changed from single to triple modal (d1, 1/7 of d1, 1/49 of d1) and mixed in the ratio of fractions 75/14/11. Theoretically, in this way a maximum packing density of 95% can be achieved (Shenoy, 1999). LMO-ST mixtures 4 and 5 implemented this idea with a resulting relative density of 83–84 ± 2%.
In terms of dielectric properties, the ceramic prepared from smaller particles (mixture 1) exhibits the lowest relative permittivity of 46 ± 1 with the corresponding dielectric loss tangent of 0.005. This could be due to the higher porosity in the case of sample mixture 1. According to our results, pellets of larger particles (mixture 3) have a relative permittivity of 70 ± 1 and dielectric losses of 0.002, compared to sample mixture 2, where a lower relative permittivity of 65 ± 1 and dielectric losses of 0.003 were achieved.
Thus, the relative permittivity of LMO-ST composites improves with increasing size of the initial particles. Generally, by increasing the relative permittivity of the samples, their dielectric losses are also increased. Compared to mixture 2, mixture 4 shows a slightly improved relative permittivity of 67 ± 1. Similarly, mixture 5 outperforms mixture 3 by having a relative permittivity of 73 ± 1, which corresponds to increased dielectric losses of 0.005. According to these results, the LMO-ST mixture 5 was selected as the one with an optimal particle size distribution and thus used in further experiments.
The Effect of Ultrasonic Treatment on Dielectric Properties of LMO-ST Composites
After initial experiments on the effects of particle size distribution on packing density and dielectric properties, ultrasonic treatment was used to investigate another processing parameter. If particles are not well-mixed, agglomerated and undispersed zones of a compound can form, negatively affecting the binding process. As previously reported, ultrasonic irradiation in liquid-solid systems provides more uniform mixing (Thompson and Doraiswamy, 2000) and improves the crystallization process of the LMO binder on the ST filler particles. In addition, the ultrasonic field causes bubbles to collapse near the particle surface, thus increasing mass transfer. In the absence of sufficient mass transfer, high supersaturation subsequently occurs, leading to aggregation of the LMO (Li et al., 2006).
LMO-ST samples were prepared from mixture 5, which consisted of ST particles 40 μm, 40–63, μm and 200–500 μm and were subjected to ultrasonic treatment using the ultrasonic processor. For RTF of LMO-ST composites, the following operating conditions were constantly set: 5 min of pressing at 250 MPa and 20 h of drying. The ultrasonic duration was varied between 0, 0.5, 1, 2, and 5 min. As a result, a constant relative density of 83 ± 2% was obtained from the dimensions of the samples. Furthermore, the measured relative permittivity and dielectric losses are shown in Figure 5, from which it can be seen that the duration of ultrasonic treatment of the initial mixture affects the dielectric properties of the LMO-ST composites. The highest measured relative permittivity was obtained after the composite system was treated with ultrasound for 5 min, while the lowest dielectric losses were obtained after 0.5 min. As shown, the relative permittivity increases up to 10% with increasing duration of ultrasonic treatment, which doubles the dielectric losses. From a practical point of view, our goal was to facilitate the fabrication process, so the ultrasonic treatment was set to a constant 0.5 min in further experiments.
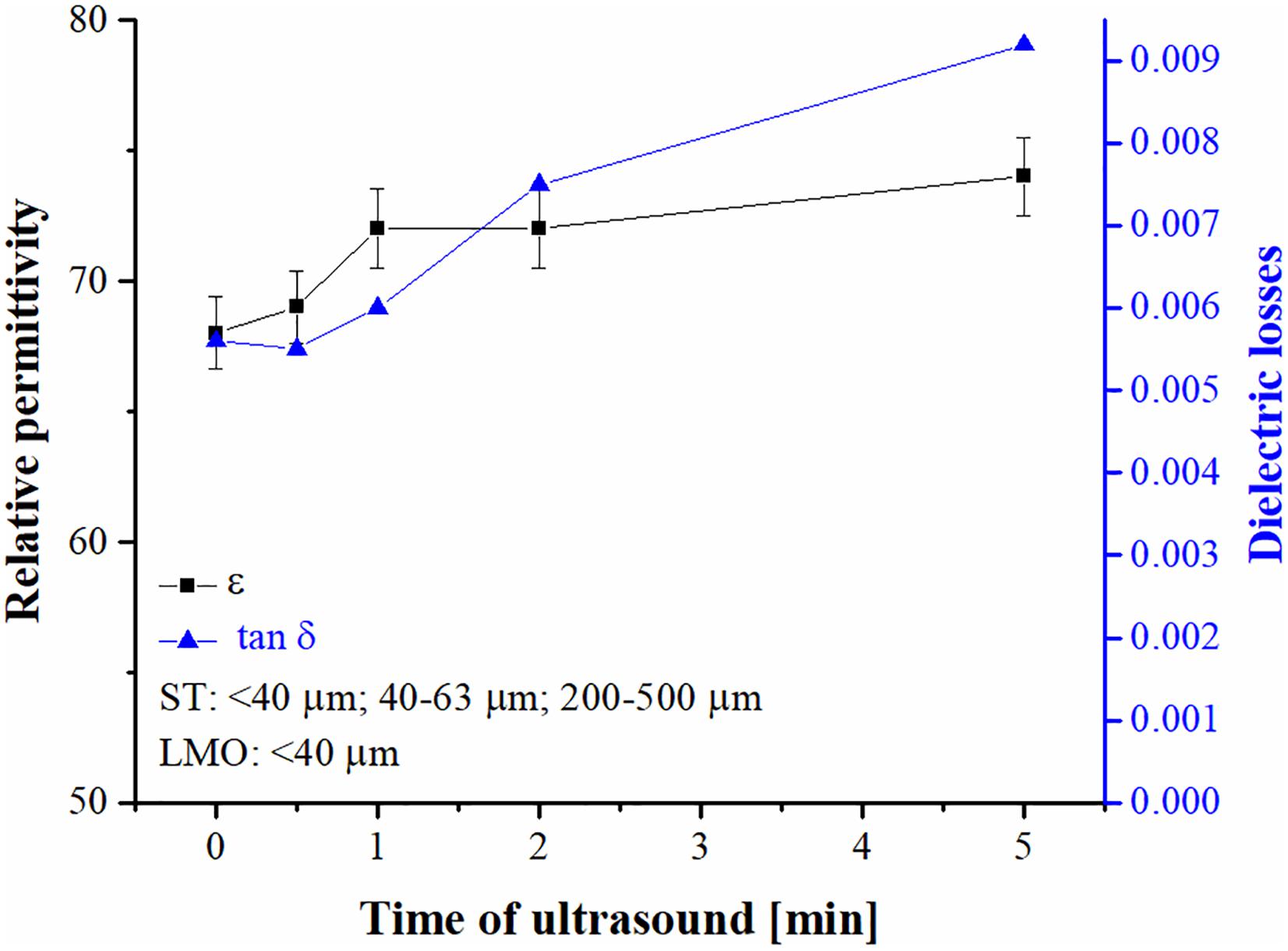
Figure 5. The effect of ultrasound duration on the dielectric properties of LMO-ST composites fabricated at RT.
The Effect of Humidity on Dielectric Properties of LMO-ST Composites
During the preliminary experimental work, we observed strong variations in dielectric properties from batch to batch. Therefore, the experimental focus was placed on the effect of ambient humidity on the dielectric properties of LMO-ST composites. As reported in previous work on dielectric ceramics, dielectric losses are strongly influenced by the operating environment and humidity (Sebastian et al., 2015). For LMO-ST composites, this could be attributed to a slight hygroscopicity of Li2MoO4 (Kähäri et al., 2017). Accordingly, optimization of the measurement setup was necessary. Dielectric measurements were performed in a desiccator to create humidity controlled conditions. During the RTF of LMO-ST composites, the following operating conditions were constantly set: 0.5 min of ultrasonic treatment, 5 min of pressing at 250 MPa, and 20 h of drying. As shown in Figure 6A, water adsorption on LMO-ST composites exposed to 100% relative humidity increases steadily with time. Figure 6B shows the effect of ambient humidity on the dielectric properties of the samples. One set of the samples was exposed to ambient conditions of approximately 60% relative humidity and the other set was placed in a desiccator immediately after drying. The results of both sets show a significant difference in the relative permittivity and dielectric losses. For example, the relative permittivity under moisture-free conditions ranges from 68 ± 1 to 74 ± 2, compared to values of relative permittivity values reaching up to 102 ± 2 under ambient conditions. In addition, dielectric losses were increased from 0.005 to 0.147 for the same change. From these results, it can be concluded that the ambient humidity has an immense effect on the dielectric properties of the LMO-ST composites. Consequently, the pellets should be stored in a desiccator at constant low humidity or impregnated with silicone electronic coating (Kähäri et al., 2017).
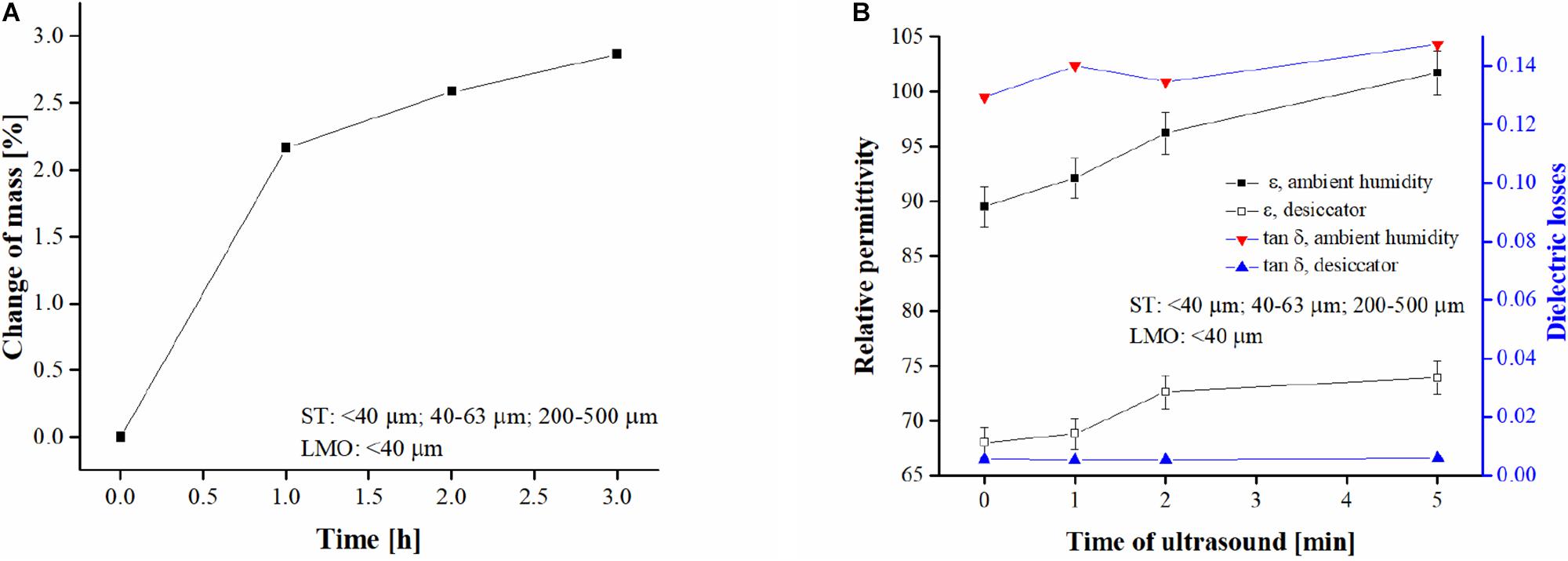
Figure 6. LMO-ST composites exposed to different conditions. (A) LMO-ST samples were exposed to 100% humidity, and the change in mass over time was observed. (B) Comparison of εr and tan δ values measured in ambient humidity (60% RH) and desiccator as a function of varied time of ultrasonic treatment.
The Effect of Drying on Dielectric Properties of LMO-ST Composites
Drying as a post-processing step was performed in addition to RTF at 110°C to accelerate evaporation and ensure complete removal of residual water. During the RTF of LMO-ST composites, the following operating conditions were constantly set: 0.5 min of ultrasonic treatment and 5 min of pressing at 250 MPa. To optimize the duration of drying, the LMO-ST composites were prepared at room temperature and dried for 3, 6, 10, and 20 h, followed by immediate measurement of the weight and dimensions of the pellets. The measured relative density of 83 ± 2% was constant for all samples and thus independent of the variations in drying time. A constant mass was reached after 3 h, as shown in Figure 7A. This result indicates that the drying time could be optimized to 3 h, which is beneficial in terms of time and energy consumption for the RTF process. As reported in the study (Nelo et al., 2019b) and further verified during our experimental work, the same effect is obtained when the ceramic is dried in a desiccator for longer than 48 h. Nevertheless, accompanying dielectric measurements showed that shorter drying can have a detrimental effect on the relative permittivity. The dielectric properties of samples dried for 3, 6, 10, and 20 h are shown in Figure 7B. Although the weight of the pellets remains constant, the relative permittivity was found to increase slightly with increasing drying time. The slight increase in relative permittivity presumably emerges from the higher crystallinity of the LMO binding phase and consequently a lower porosity, both of which are achieved with increasing drying time.
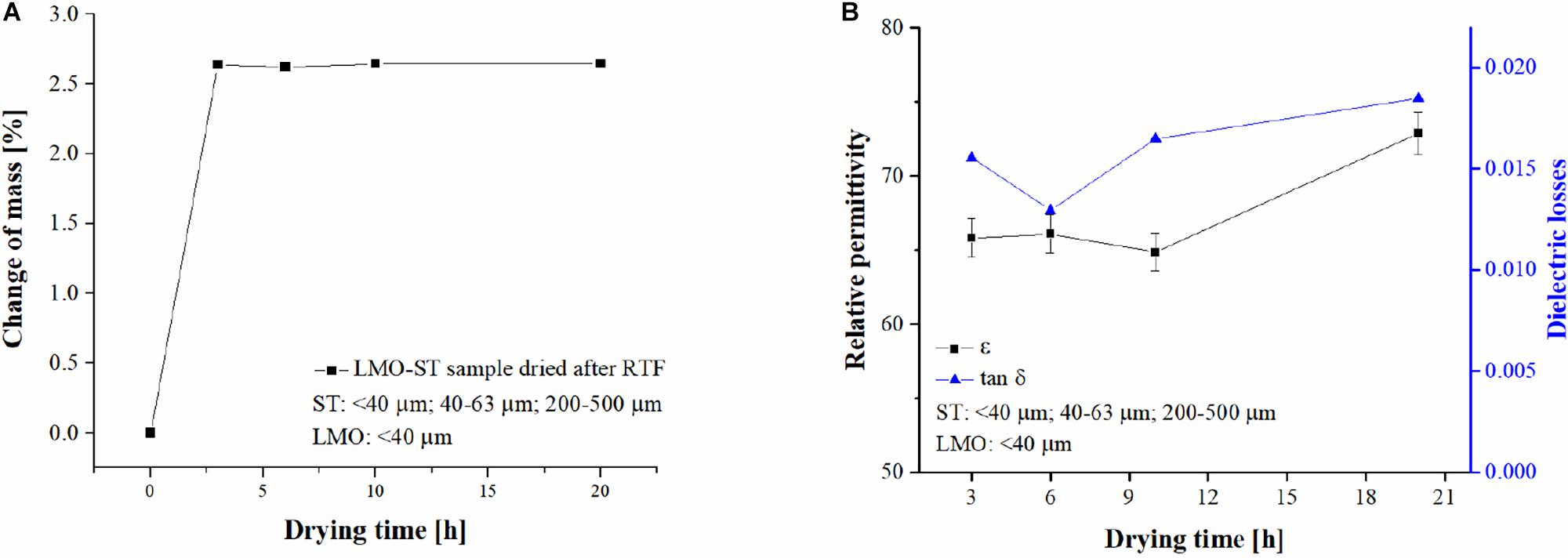
Figure 7. (A) Mass of LMO-ST composite changing over drying time. (B) Relative permittivity and dielectric losses as a function of drying time.
The Effect of Pressure and Pressing Time on Dielectric Properties of LMO-ST Composites
The main driving force of consolidation and densification during RTF of LMO-ST composites is the difference in chemical potential of the LMO solution and the pressure. During this processing step, LMO in the aqueous phase enables the rearrangement and subsequent binding of the particles (Nelo et al., 2019a). In addition, the frictional properties and wetting play an important role in reducing the voids between the ST particles during pressing (Shenoy, 1999). With the aim to inspect and optimize the RTF process, the pressure was varied from 10 to 60, 130, 250, 380, 500, and 1,000 MPa during the compaction of LMO-ST composites. During RTF, the following operating conditions were constantly set: 0.5 min of ultrasonic treatment, 5 min of pressing, and 20 h of drying. As expected and further shown in Figure 8A, higher pressure contributes to the higher relative density of the LMO-ST composites, ranging from 82 ± 2% to 87 ± 2%.
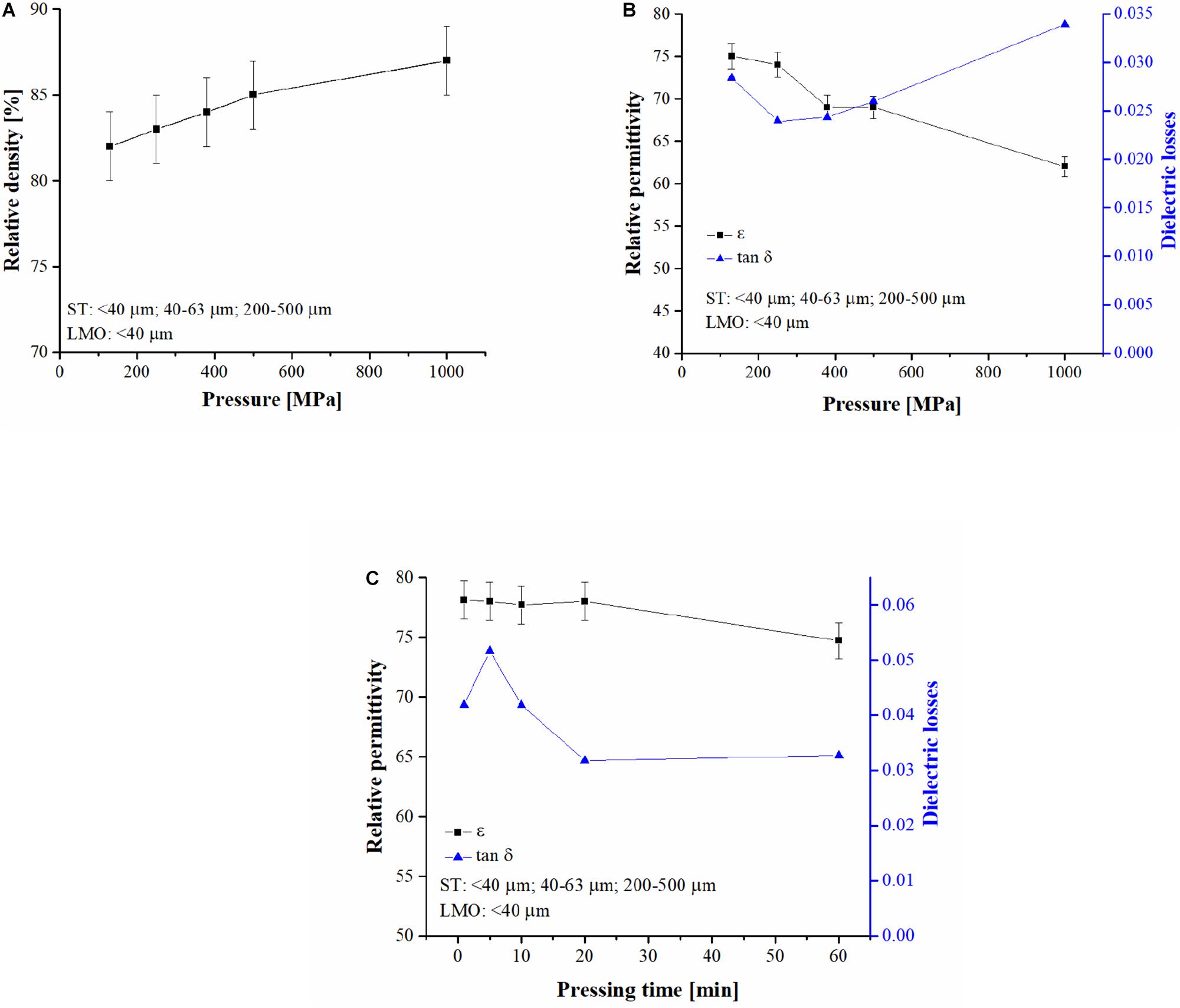
Figure 8. (A) The effect of pressure on relative density of LMO-ST composites. (B) The effect of pressure on relative permittivity and dielectric losses of LMO-ST composites. (C) The effect of pressing time on relative permittivity and dielectric losses of the LMO-ST composites.
The dielectric properties of LMO-ST composites as a function of pressure are shown in Figure 8B. Pressing at 10 and 60 MPa was unsuccessful, resulting in fracture of the samples, which were thus not characterized in terms of dielectric properties. The higher pressure relative permittivity decreases in the range from 75 ± 2 to 62 ± 1, associated with higher dielectric losses. This could be attributed to the cracks of the large ST particles under higher pressure, leading to higher reflection of electric field and consequently poorer dielectric properties. Our assumption was confirmed by SEM/EDS analyzes of the samples pressed at 130 MPa and 1,000 MPa (Figures 9A,B). However, almost no cracks were observed on the cross-sectional area of the pellet pressed at 130 MPa. As a result, 250 MPa was found to be the most optimal pressure for RTF, at which both high relative permittivity and low dielectric losses were achieved. Thus, a lower pressure for composite processing is advantageous from a fabrication point of view.
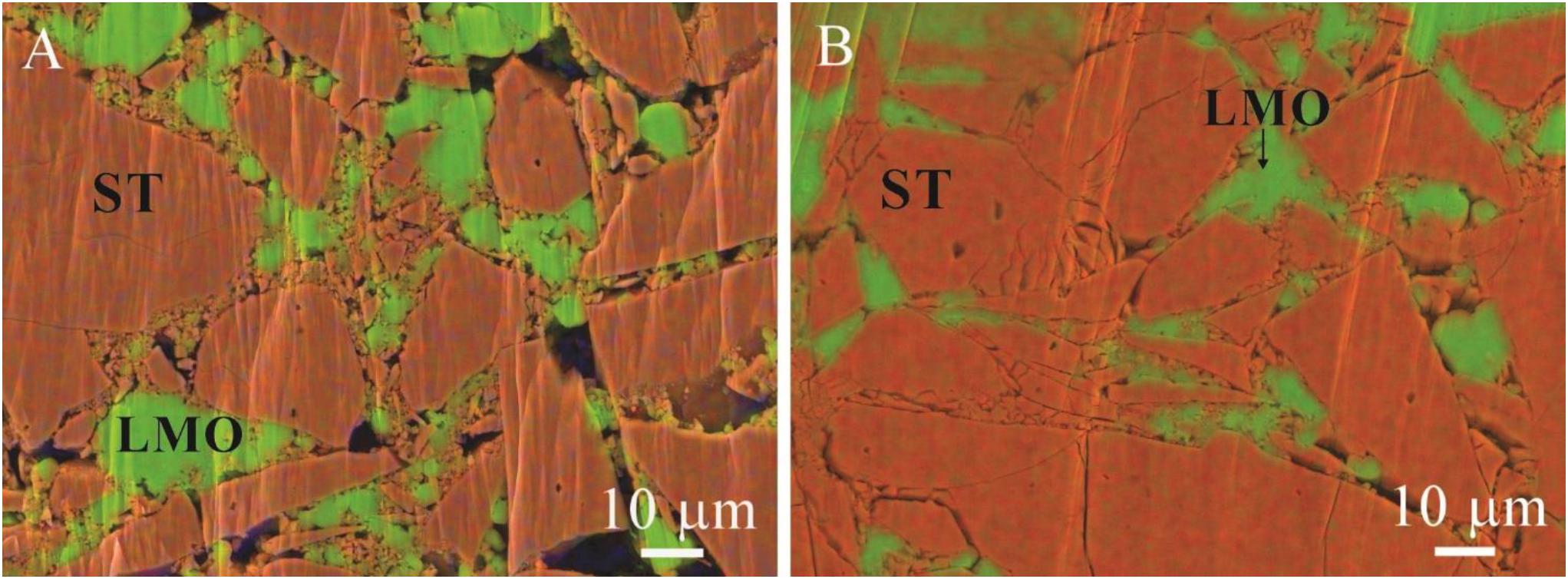
Figure 9. SEM micrographs of the LMO-ST composite pressed (A) at 130 MPa and (B) at 1,000 MPa. Green color represents LMO phase, while orange color corresponds to ST.
Another parameter related to the compaction phase at room temperature is the pressing time. The functional properties of fabricated LMO-ST composites were investigated by varying the pressing time in the range of 1, 5, 10, 20, and 60 min at a constant pressure of 250 MPa. The measured relative density was constant 84 ± 2% for all samples and was thus independent of the pressing time. To increase the interaction of the ST filler particles with the LMO binder, a small variation of the relative permittivity with the pressing time was observed, as shown in Figure 8C. While the dielectric losses increase slightly from 0.042 to 0.052 in the first 5 min, they decrease to 0.020 in the rest of the process. According to the results, we could not confirm any beneficial effect of extended time of pressing phase in the RTF process. Therefore, the final optimal pressing time was thus set to 5 min.
Conclusion
The optimization of the RTF process for LMO-ST composites is described in this paper. More precisely, the influence of various processing parameters on the final dielectric performance of LMO-ST composites has been investigated. The obtained data are demonstrated in the above figures as a function of each of the varied processing parameters. The important dielectric properties such as relative permittivity and dielectric losses were determined at 1 MHz and varied in the range of 46 ± 1–78 ± 2 and from 0.002 to 0.05, respectively. These results show that dense LMO-ST ceramic composites with excellent dielectric properties were obtained without additional sintering step at high temperatures. The high content of ST filler contributes to an increased relative permittivity, while the LMO binder in solid and aqueous phase facilitates densification during pressing, resulting in a higher packing density of 84 ± 2%. From the SEM/EDS analysis of the composites, it was confirmed that the LMO is homogeneously distributed between the ST particles, which physically binds them together and reduces the overall porosity of the composites. An improvement in the dielectric properties of the LMO-ST composites was achieved by selecting the larger ST particles (200–500 μm), which were combined with smaller ST fractions below 63 μm. Moreover, ultrasonic treatment as a processing step is shown to have a positive effect in terms of dielectric losses of the upside-down LMO-ST composites. However, the important influence of ambient humidity on the dielectric properties has been confirmed, so a careful control of the operating conditions is inevitable. Moreover, dielectric measurements must be performed in a moisture-free atmosphere. As a drying step of the RTF was studied, a constant mass was obtained after 3 h. Moreover, a shorter drying time has only a minor effect on the dielectric properties. As expected, increasing pressure contributes to a higher relative density of the LMO-ST composites, together with a lower relative permittivity. However, the dielectric properties decrease with increasing pressure, probably due to the cracks generated by the strong mechanical stress. Therefore, 0.5 min of ultrasonic treatment, 5 min of pressing at 250 MPa and a drying time of 3–6 h are the optimal processing parameters proposed in this study. The presented results show that the RTF of upside-down ceramics paves the way for a novel processing of electroceramics without significant degradation of their functionality and enables further integration possibilities in various electronic devices.
Data Availability Statement
The original contributions presented in the study are included in the article/supplementary material, further inquiries can be directed to the corresponding author/s.
Author Contributions
NK, MS, SŠ, MN, and HJ agreed about the research content. HJ and MN demonstrated experimental method and all the knowledge and details to NK. MN and HJ developed the LMO-ST composition and initial processing conditions. NK, MS, HJ, MN, and SŠ conceived the idea and course of the experiments, discussed and confirmed the findings. NK and SŠ synthesized the initial strontium titanate. NK conducted the RTF sample preparation and characterization, along with the optimization of processing parameters. SŠ operated the scanning electron microscope, provided the imaging of the composite samples, and conducted the XRD characterization of samples. NK, SŠ, MS, MN, and HJ analyzed the dielectric measurements, SEM micrographs, and other results supporting the findings of the study. All authors reviewed the manuscript.
Funding
NK, SŠ, and MS would like to acknowledge funding from Slovenian Research Agency (PR-09775 and P2-0091).
Conflict of Interest
The authors declare that the research was conducted in the absence of any commercial or financial relationships that could be construed as a potential conflict of interest.
Acknowledgments
We appreciatively acknowledge David Fabjan for the dielectric measurements, Tina Radošević for SEM imaging, and Janez Bernard for the measurements of mechanical properties of the samples.
References
Andrews, J., Button, D., and Reaney, I. M. (2020). Advances in cold sintering: improving energy consumption and unlocking new potential in component manufacturing. Johnson Matthey Technol. Rev. 64, 219–232. doi: 10.1595/205651320x15814150061554
Bouville, F., and Studart, A. R. (2017). Geologically-inspired strong bulk ceramics made with water at room temperature. Nat. Commun. 8:14655.
Guo, J., Guo, H., Baker, A. L., Lanagan, M. T., Kupp, E. R., Messing, G. L., et al. (2016). Cold sintering: a paradigm shift for processing and integration of ceramics. Angew. Chem. 128, 11629–11633. doi: 10.1002/ange.201605443
Kähäri, H., Ramachandran, P., Juuti, J., and Jantunen, H. (2017). Room-temperature-densified Li2MoO4 ceramic patch antenna and the effect of humidity. Int. J. Appl. Ceram. Technol. 14, 50–55. doi: 10.1111/ijac.12615
Kähäri, H., Teirikangas, M., Juuti, J., and Jantunen, H. (2014). Dielectric properties of lithium molybdate ceramic fabricated at room temperature. J. Am. Ceram. Soc. 97, 3378–3379. doi: 10.1111/jace.13277
Kähäri, H., Teirikangas, M., Juuti, J., and Jantunen, H. (2015). Improvements and modifications to room-temperature fabrication method for dielectric Li 2 MoO 4 ceramics. J. Am. Ceram. Soc. 98, 687–689. doi: 10.1111/jace.13471
Kähäri, H., Teirikangas, M., Juuti, J., and Jantunen, H. (2016). Room-temperature fabrication of microwave dielectric Li2MoO4–TiO2 composite ceramics. Ceram. Int. 42, 11442–11446. doi: 10.1016/j.ceramint.2016.04.081
Li, H., Li, H., Guo, Z., and Liu, Y. (2006). The application of power ultrasound to reaction crystallization. Ultrason. Sonochem. 13, 359–363. doi: 10.1016/j.ultsonch.2006.01.002
Muhamad, N. F., Osman, R. A. M., Idris, M. S., and Yasin, M. N. M. (2017). “Physical and electrical properties of SrTiO3 and SrZrO3,” in Proceedings of the EPJ Web of Conferences, Vol. 162, (Les Ulis: EDP Sciences), 1052.
Narang, S. B., and Bahel, S. (2010). Low loss dielectric ceramics for microwave applications: a review. J. Ceram. Process. Res. 11, 316–321.
Nelo, M., Peräntie, J., Siponkoski, T., Juuti, J., and Jantunen, H. (2019a). Upside-down composites: electroceramics without sintering. Appl. Mater. Today 15, 83–86. doi: 10.1016/j.apmt.2018.12.021
Nelo, M., Siponkoski, T., Kähäri, H., Kordas, K., Juuti, J., and Jantunen, H. (2019b). Upside – down composites: fabricating piezoceramics at room temperature. J. Eur. Ceram. Soc. 39, 3301–3306. doi: 10.1016/j.jeurceramsoc.2019.04.052
Sebastian, M., Ubic, R., and Jantunen, H. (2015). Low-loss dielectric ceramic materials and their properties. Int. Mater. Rev. 60, 392–412. doi: 10.1179/1743280415y.0000000007
Shende, R. V., Krueger, D. S., Rossetti, G. A., and Lombardo, S. J. (2001). Strontium zirconate and strontium titanate ceramics for high-voltage applications: synthesis, processing, and dielectric properties. J. Am. Ceram. Soc. 84, 1648–1650. doi: 10.1111/j.1151-2916.2001.tb00893.x
Shenoy, A. V. (ed.). (1999). “Steady shear viscous properties,” in Rheology of Filled Polymer Systems, (Dordrecht: Springer), 243–311. doi: 10.1007/978-94-015-9213-0_6
Sulong, T. A. T., Osman, R. A. M., and Idris, M. S. (2016). “Trends of microwave dielectric materials for antenna application,” in Proceedings of the AIP Conference, Vol. 1756, (Melville, NY: AIP Publishing LLC), 70003.
Thompson, L. H., and Doraiswamy, L. K. (2000). The rate enhancing effect of ultrasound by inducing supersaturation in a solid–liquid system. Chem. Eng. Sci. 55, 3085–3090. doi: 10.1016/S0009-2509(99)00481-9
Tuhkala, M., Teirikangas, M., and Juuti, J. (2017). “Modeling of microwave dielectric properties of composites,” in Microwave Materials and Applications 2V Set, eds M. T. Sebastian, H. Jantunen, and R. Ubic (Chichester: John Wiley & Sons, Ltd), 53–80. doi: 10.1002/9781119208549.ch2
Väätäjä, M., Kähäri, H., Ohenoja, K., Sobocinski, M., Juuti, J., and Jantunen, H. (2018). 3D printed dielectric ceramic without a sintering stage. Sci. Rep. 8:15955.
Viana, R., Lunkenheimer, P., Hemberger, J., Böhmer, R., and Loidl, A. (1994). Dielectric spectroscopy in SrTiO3. Phys. Rev. B 50, 601–604. doi: 10.1103/PhysRevB.50.601
Zheng, J., Carlson, W. B., and Reed, J. S. (1995). The packing density of binary powder mixtures. J. Eur. Ceram. Soc. 15, 479–483. doi: 10.1016/0955-2219(95)00001-b
Keywords: strontium titanate, lithium molybdate, upside-down composites, electroceramics, room temperature fabrication, dielectric properties, processing parameters
Citation: Kuzmić N, Škapin SD, Nelo M, Jantunen H and Spreitzer M (2021) Dielectric Properties of Upside-Down SrTiO3/Li2MoO4 Composites Fabricated at Room Temperature. Front. Mater. 8:669421. doi: 10.3389/fmats.2021.669421
Received: 18 February 2021; Accepted: 30 March 2021;
Published: 22 April 2021.
Edited by:
Mailadil Thomas Sebastian, University of Oulu, FinlandCopyright © 2021 Kuzmić, Škapin, Nelo, Jantunen and Spreitzer. This is an open-access article distributed under the terms of the Creative Commons Attribution License (CC BY). The use, distribution or reproduction in other forums is permitted, provided the original author(s) and the copyright owner(s) are credited and that the original publication in this journal is cited, in accordance with accepted academic practice. No use, distribution or reproduction is permitted which does not comply with these terms.
*Correspondence: Srečo Davor Škapin, c3JlY28uc2thcGluQGlqcy5zaQ==