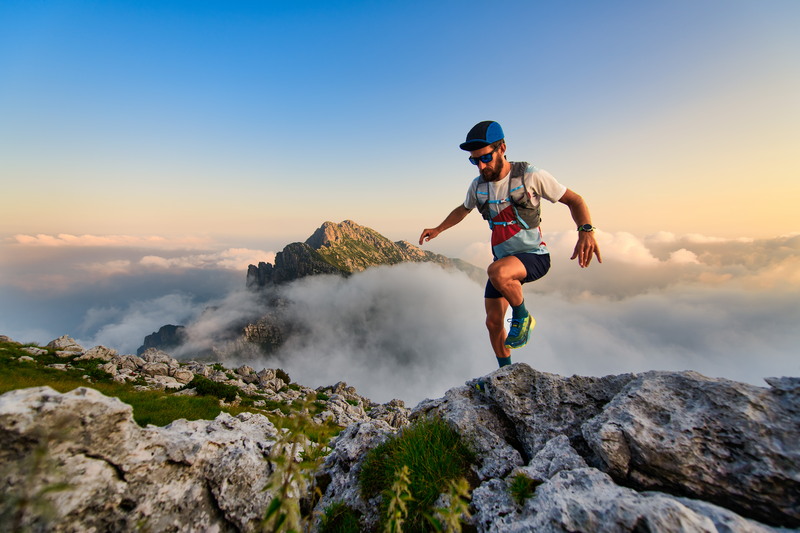
95% of researchers rate our articles as excellent or good
Learn more about the work of our research integrity team to safeguard the quality of each article we publish.
Find out more
ORIGINAL RESEARCH article
Front. Mater. , 16 March 2021
Sec. Structural Materials
Volume 8 - 2021 | https://doi.org/10.3389/fmats.2021.645612
High-temperature oxidation tests were carried out on binderless tungsten carbide (WC) with different Y2O3 contents (0, 1, 2, 3, and 4 wt.%) and on YG3 cemented carbide. Results demonstrated that the addition of Y2O3 led to a significant improvement in the high-temperature oxidation resistance of binderless tungsten carbide compared with those of YG3 cemented carbide and pure tungsten carbide. After oxidation at 800°C for 120 min, the oxidation weight gain of binderless tungsten carbide with 1 wt.% Y2O3 was 58.54 mg cm−2, corresponding to the reduction by 47.7% compared with YG3 cemented carbide. In the high temperature oxidation process, WC in the triangle grain boundary was first oxidized to Y2WO6 due to the high activity of Y2O3 which is present mainly in the WC grain boundaries. The transport of W4+ outward along the grain boundary and the diffusion of O2− inward along the grain boundary were hindered by Y2WO6 with the high ionic radius and thus the antioxidant capacity of binderless tungsten carbide was improved. Meanwhile, the adhesive ability of oxidation layer on the substrate was enhanced with the “pinning effect” of Y2WO6, which also led to the improvement of oxidation resistance. With the Y2O3 content increasing from 1 to 4 wt.%, the antioxidant properties of binderless tungsten carbide gradually declined, and the antioxidant performance of binderless tungsten carbide with 1 wt.% Y2O3 was found to be the best.
Tungsten carbides with metallic binder cobalt are widely used for cutting tools and wear applications due to their excellent mechanical properties (Kim et al., 2004; Xiao et al., 2010; Ou et al., 2012; Zhang et al., 2016; Liu et al., 2018). Although the binder cobalt greatly improves sinter ability and fracture toughness, they also weaken the hardness, wear resistance, and corrosion resistance of WC matrix, especially at high temperatures (Engqvist et al.,1999; Beste et al., 2001; Bozzini et al., 2004; Hussainova et al., 2014; Xia et al., 2016; Zhang et al., 2017; Liu et al., 2018). For applications for cutting tools, because the highest temperature at tool/chip interface may vary between 600 and 1000°C (Bhaumik et al., 1999; Majumdar et al., 2005; Sutter and Ranc, 2007), oxidation of cemented carbides will take place in dry and high speed cutting (Basu and Sarin, 1996; Voitovich et al., 1996; Campo et al., 2009; Chen et al., 2015; Chen et al., 2016), which will result in the degradation of mechanical properties and decreasing of their service lifetime. Literatures show that oxidation occur preferentially in the Co binder phase (Voitovich et al., 1996; Chen et al., 2015; Chen et al., 2016). In the work of Chen et al. (Chen et al., 2015; Chen et al., 2016), it is reported that WC-Co cemented carbides have the selective oxidation characteristic at 500°C, results shown that the oxidation of Co phase was prior to the oxidation of WC phase. The O content in Co phase increases quickly while there is no change of O content in WC phase because no oxidation takes place.
Binderless tungsten carbide has received wide attention of scholars worldwide because of its higher hardness (Imasato et al., 1995; Tsai et al., 2010), better abrasion resistance and corrosion resistance (Engqvist et al., 1999; Beste et al., 2001; Hussainova et al., 2014; Wang et al., 2018) compared with the conventional tungsten carbide with metallic binder cobalt. To address the drawbacks such as the high sintering temperature, low density and poor fracture toughness of the binderless tungsten carbide, researchers have carried out extensive studies and proposed a variety of methods to lower the sintering temperature and improve the mechanical properties (Zheng et al., 2013; Ren et al., 2015; Kwak et al., 2016; Nino et al., 2017; Wang et al., 2018). Nevertheless, there have been few reports on the oxidation process of the binderless tungsten carbide. In our previous study (Wang et al., 2018), we found the addition of Y2O3 was of significant influence on the sintering densification and mechanical properties of binderless tungsten carbide. The hardness and fracture toughness of WC-1 wt.% Y2O3 increased by 46 and 40% compared to the pure WC. However, the effect of Y2O3 addition on high-temperature oxidation of binderless tungsten carbide is still unclear, which will affect the design and application of the binderless tungsten carbide as cutting tool materials.
The main purpose of the present work is to investigate the oxidation kinetics law of the binderless tungsten carbide with different contents of Y2O3, analyze the microstructure of the oxidation layer and discuss the oxidation mechanism of Y2O3 in binderless tungsten carbide.
The WC powder used in this research was supplied by Xiamen Golden Egret Special Alloy Co. Ltd., Xiamen, China, and the average grain size was 0.2 µm. To remove the surface oxide, WC powder was firstly pretreated with activated liquid consisting of 30 ml L−1 nitric acid (HNO3), 40 ml L−1 hydrofluoric acid (HF) and 3 g L−1 ammonium fluoride (NH4F). Then, the pretreated WC powder was used to prepare Y2O3-doped WC powder with Y2O3 contents of 1, 2, 3 and 4 wt.% by the chemical co-precipitation method. The specific process of activation pretreatment and preparation of Y2O3-doped WC powder were described in our previous study (Wang et al., 2018). The pure WC and Y2O3-doped WC were sintered with an SPS system produced by Sumitomo Coal Mining Co., Ltd. using a sintering temperature of 1600°C, sintering pressure of 45 MPa, a heating rate of 100°C/min and a holding time of 5 min. The YG3 cemented carbide used for comparative test was provided by Zhuzhou cemented carbide cutting tools co., Ltd. The compositions of the WC cemented carbides are shown in Table 1.
The oxidation weight gain test was carried out in a tube furnace. Specimens for the experiment with the dimension of about 10 mm × 10 mm × 5 mm were cut from the sintered samples. The surfaces of the specimens were ground and polished. Before the oxidation experiment, we measured the length and width of each surface of the specimens with a spiral micrometer with an accuracy of 0.01 mm, and then calculated the surface area. The specimens were placed in a tube furnace and were heated to the oxidizing temperature at a heating rate of 10°C/min, and the oxidizing temperature was held for a certain time before cooling off. Oxidizing temperatures of 600°, 700°, 750° and 800°C, and holding times of 30, 60, 90 and 120 min were used. The specimens before and after the oxidation were weighed using an analytical balance with an accuracy of 1 × 10−4g, each sample was measured five times and averaged. The fracture and surface of the oxidation layers were observed by field emission scanning electron microscopy (FE-SEM, Model: S-4800, Hitachi, Japan). The composition and phase of the oxidation products were analyzed by energy dispersive spectrometry (EDS) and X-ray diffraction (XRD, Model: D8-Advance, Germany) analysis. The electron cloud density of binderless tungsten carbide’s oxidation atom ball-and-stick model was simulated by Guassion09W software.
The oxidation resistance of the WC cemented carbide was determined by measuring the weight change after the oxidation at the temperatures of 600°, 700°, 750 ° and 800°C respectively. The weight gains per unit surface area of the WC cemented carbide vs. oxidized time at different temperatures were shown in Figure 1. Figure 1A shows the weight gain of the WC cemented carbide oxidized at 600°C for 120 min. It is observed that both the binderless tungsten carbide with different contents of Y2O3 and the YG3 cemented carbide show a small weight increase during oxidation at 600°C. However, the binderless tungsten carbide specimen with 1 wt.% Y2O3 has the smallest oxidation weight gain of 0.097 mg cm−2 while the oxidation weight gain of the YG3 cemented carbide sample is 1.62 mg cm−2 for the same oxidation condition. Figures 1B–D shows the oxidation kinetics curves of different WC cemented carbide at the oxidation temperatures of 700°C, 750°C and 800°C, respectively. It can be seen from the oxidation dynamics curve that the weight gain rate of YG3 cemented carbide does not change with the increase in the oxidation time, and the antioxidant performance is poor. However, as the oxidation time increases, the oxidation weight gain of all binderless tungsten carbide specimens with different contents of Y2O3 tends to slow down and the oxidation rate gradually decreases, which demonstrates that the antioxidant capacities of binderless tungsten carbides are better than that of YG3 cemented carbide. A comparison between Figures 1A,B shows that the oxidation weight gain rate of WC cemented carbide at 700 °C increased by one to two orders of magnitude compared to that at 600°C. As can be seen from Figures 1B,C binderless tungsten carbide with 1 wt.% Y2O3 oxidation shows the smallest weight gain and thus has the best antioxidant ability. With the increase of the Y2O3 content, the oxidation weight gain of the binderless tungsten carbide increases gradually, and the antioxidant capacity decreases; nevertheless, all samples show better antioxidant capacity than that of pure WC. For the oxidation temperature of 800°C, the antioxidant capacity of WC-4 wt.% Y2O3 decreased significantly, while that of WC-1 wt.% Y2O3 remained adequate (Figure 1D). The oxidation weight gain of the YG3 cemented carbide sample oxidized at 800°C for 120 min was 111.87 mg cm−2, while that of WC-1wt.% Y2O3 was only 58.54 mg cm−2, corresponding to a decrease of 47.7% compared with the YG3 cemented carbide sample.
FIGURE 1. Oxidation weight gain of YG3 cemented carbide and binderless tungsten carbide with different contents of Y2O3 at different oxidation temperatures. (A) 600°C, 120 min. (B) 700°C. (C) 750°C. (D) 800°C.
When the high-temperature oxidation kinetics curve of the material conforms to the parabolic law, it can be expressed by the following formula (Tatarko et al., 2013):
where
According to the test data in Figure 1, square of oxidation weight gain of binderless tungsten carbide vs. time at different oxidation temperatures was drawn and basically close to a straight line (Figure 2). That means the oxidation kinetics curve of binderless tungsten carbide oxidized in the temperature range from 700° to 800°C are consistent with the parabolic law. Using Eq. 1, the values of the parabolic oxidation rate constant k were estimated from the slopes of the square of the weight gain per unit surface area plotted vs. time. The oxidative activation energy Q was calculated from the slope of the Arrhenius plot between the parabolic rate constants and the oxidation temperatures. The values of the parabolic oxidation rate constant k and the oxidative activation energy Q in the temperature range from 700° to 800°C were calculated, and the results are shown in Table 2. An examination of the data presented in Table 2 shows that the value of the parabolic oxidation rate constant k of binderless tungsten carbide with Y2O3 addition is smaller than that of pure WC for all temperatures in the 700°–800°C range, while the values of the oxidation activation energy Q are larger than those of pure WC. As the Y2O3 content increased from 1 to 4 wt.%, the value of the oxidation rate constant k gradually increased, and the activation energy Q gradually decreased. The oxidation rate constant k reflects the antioxidant performance, and oxidation is a thermal activation process, so that the oxidation activation energy Q represents the energy barrier that must be crossed during oxidation, and indicates the difficulty of oxidation. Thus, better oxidation resistance is obtained for smaller values of k and bigger values of Q. The addition of Y2O3 in the binderless tungsten carbide increases the energy needed for oxidation reaction, and improves the oxidation resistance of binderless tungsten carbide. However, with the increase in the Y2O3 content, the oxidation resistance of binderless tungsten carbide gradually declines.
FIGURE 2. Square of oxidation weight gain of binderless tungsten carbide vs. time at different oxidation temperatures. (A) 700°C; (B) 750°C; (C) 800°C.
TABLE 3. Oxidation reaction equations and corresponding change of Gibbs free energy (∆G) in WC-Y2O3 cemented carbide.
Figure 3 presents the surface morphologies of the oxidation layer of binderless tungsten carbide with different Y2O3 contents and of YG3 cemented carbide that are oxidized at 800°C for 60 min. Figure 3A,B show that there are many pores uniformly distributed on the surface of the oxidation layer of pure tungsten carbide and the grains are loose. However, the addition of Y2O3 in binderless tungsten carbide greatly improves the compactness of the surface of the oxidation layer (Figures 3C–J); in particular, when the Y2O3 content is 1 wt.%, the surface of the oxidation layer is the densest, and hardly any pores are observed (Figures 3C,D). As the Y2O3 content increases, the grain size in the oxidation layer and the number of the pores increase gradually (Figures 3E–J). Figures 3K,L present the surface morphology of the oxidation layer of YG3 cemented carbide. The grain size varies greatly, and the space between the grains is relatively loose. The outer grains have regular multilateral shapes, while the inner grain is almost spherical (Figures 3K,L). The elemental composition of the oxidation surface of binderless tungsten carbide was analyzed via EDS. Due to the low Y2O3 content, only O and W elements were detected, whereas Y was not detected. Figure 4 shows the results of the EDS analysis of the micro zones 1 and 2 of YG3 cemented carbide shown in Figure 3L. Zone 1 in Figure 3L has high Co element content (Figure 4A) while zone 2 only contains elements O and W with no Co (Figure 4B). Further XRD analysis was performed on the oxidation surface of YG3 cemented carbide as shown in Figure 5A. The WO3 and CoWO4 phases were detected on the surface of the oxidation layer of YG3 cemented carbide. According to the EDS and XRD results, the regular polygonal grain on the surface of the oxidation layer of YG3 is CoWO4 and the almost spherical small grain is WO3. Figure 5B shows the XRD results for the binderless tungsten carbide, which indicates that WO3 is the major phase and that Y2WO6 is a secondary phase in the tungsten carbide with Y2O3.
FIGURE 3. Surface morphology of the oxidation layer of binderless tungsten carbide with different Y2O3 contents and YG3 cemented carbide oxidized at 800°C for 60 min (A,B) WC; (C,D) WC-1 wt.% Y2O3; (E,F) WC-2 wt.% Y2O3; (G,H) WC-3 wt.% Y2O3; (I,J) WC-4 wt.% Y2O3(K,L) YG3.
FIGURE 4. EDS analysis results of micro zones 1 (A) and 2 (B) of YG3 shown in Figure 2L.
FIGURE 5. XRD patterns of the surface of oxidation layer of YG3 cemented carbide (A) and binderless tungsten carbide with different Y2O3 contents (B).
Figure 6 displays the cross-section morphologies of different cemented carbide oxidized at 600°C for 30 min. It can be seen that YG3 has the thickest oxidation layer close to 10 μm, while pure WC is about 7 μm, and WC-1 wt.% Y2O3 has the thinnest oxidation layer with the thickness of less than 5 μm. In YG3 and pure WC samples (seen from Figures 6A,B), the interface between the oxidation layer and the substrate is not firm, and the peeling of the oxidation layer can be seen. However, the oxidation films of cemented carbides with Y2O3 are well combined with the substrate (seen from Figures 6C,D). When the content of Y2O3 increases from 2 to 4 wt.%, the thickness of the oxidation layer doesn’t change much, ranging from 6 to 6.5 μm, and some micro cracks are distributed in the oxidation films (seen from the arrows in Figures 6D–F).
FIGURE 6. Cross-section morphology of the different WC cemented carbides oxidized at 873 K for 30 min. (A) YG3; (B) pure WC; (C) WC-1 wt.% Y2O3; (D) WC-2 wt.% Y2O3; (E) WC-3 wt.% Y2O3; (F) WC-4 wt.% Y2O3.
The above results indicate that the antioxidant performance of binderless tungsten carbide with 1 wt.% Y2O3 was found to be the best. To further observe the oxidation process of binderless tungsten carbide doped with Y2O3, the WC-1 wt.% Y2O3 fresh fracture was placed in a tube furnace, heated to the test temperature at a heating rate of 10°C/min, and then cooled after holding for 30 minat the test temperature. The test temperatures were 300°, 350°, 400°, 500° and 600°C. The fracture morphologies were observed by scanning electron microscopy. Figure 7 shows the fracture morphologies of WC-1 wt.% Y2O3 oxidized at different temperatures. No oxidation phenomenon was observed at room temperature (Figure 7A) and at 300°C (Figure 7B). When the oxidation temperature was 350°C, partial oxidation occurs in the triangular area between the WC grains (indicated by the arrows in Figure 7C). With the further increase of the temperature from 400° to 600°C, the oxidation products gradually covered the entire section, and the oxidation products structure was dense (seen from Figures 7D–F).
FIGURE 7. SEM images of the fracture surface of WC-1wt.% Y2O3 oxidized at different temperatures. (A) original; (B) 300°C; (C) 350°C; (D) 400°C; (E) 500°C; (F) 600°C.
The oxidation process is controlled by the interfacial reaction rate and the rate of the diffusion of the substances involved in the reaction through the oxidation layer. The oxidation rate curve of YG3 cemented carbide essentially increased linearly and the oxidation rate did not change with the thickening of the oxidation layer. The oxidation process of YG3 cemented carbide was controlled by the interface reaction and the oxidation resistance was poor. This is mainly because the oxidation products of YG3 cemented carbide are WO3 and CoWO4 with different grain sizes that give rise to a loose oxidation layer with cracks and faults and are not favourable for antioxidant protection. By contrast, the curve of the oxidation weight gain of binderless tungsten carbide conforms to the parabolic law, and the oxidation rate decreases with the increase of oxidation time. The oxidation reaction is mainly controlled by diffusion and the oxidation layer has good protective properties.
The binderless tungsten carbide doped with Y2O3 has good oxidation resistance, we suggest as follows:
(1) Oxidation product Y2WO6 distributed at the triangle grain boundaries prevents the inward diffusion of O2− and the outward diffusion of W4+.
Figure 8 displays the SEM surface morphology (Figure 8A) and elemental analysis (Figures 8B,C) of WC-4wt.% Y2O3. It can be seen that element yttrium is mainly distributed at the WC triangle grain boundaries indicated by the arrows in Figure 8A. Combined with the XRD pattern of WC-4wt.% Y2O3 (Figure 9), the element yttrium exists in the form of Y2O3 phase. The ionic radius of Y3+ (0.090 nm) is much larger than that of W4+ (0.066 nm), and therefore, it is difficult for Y2O3 to form a solid solution with WC, so that Y2O3 is present mainly in the WC grain boundaries, which is consistent with the results in literature (Liu et al., 2015; Jin et al., 2017; He et al., 2018). Oxidation reaction equations and corresponding change of Gibbs free energy (∆G) in WC-Y2O3 cemented carbide are shown in Table 2. Figure 10 shows the ∆G−T relation curves of each reaction according to Table 2. It can be seen from Figure 10 that the Gibbs free energy of WC oxidation reaction with Y2O3 or not increases with the increase of temperature, but greatly reduced while with Y2O3, which means the greater thermodynamic trend. Therefore, in the high temperature oxidation process, WC in the triangle grain boundary was first oxidized to Y2WO6. When the compact WO3 oxidation layer was formed with the bare WC, the growt.h of the oxidation layer is mainly determined by W4+ and O2− diffusion velocities along the grain boundary. The presence of the Y2WO6 with the high ionic radius, the transport of W4+ outward along the grain boundary and the diffusion of O2− inward along the grain boundary were hindered and thus the antioxidant capacity of binderless tungsten carbide was improved by the addition of Y2O3.
(1) The excellent adhesion between the oxidation layer and the substrate surface is enhanced with the “pinning effect” of Y2WO6.
FIGURE 8. SEM surface morphology (A) and elemental analysis of WC-4wt.% Y2O3(B,C). (B) The distribution of yttrium in Panel (A); (C) EDS analysis result of micro zone A in Figure. a.
FIGURE 10. The change in Gibbs free energy (∆G) for the oxidation of component in WC-Y2O3 cemented carbide.
Figure 11 shows the oxidation layer/substrate atom ball-and-stick model (Zhong et al., 2015; Zhong et al.,2019) of pure WC and WC-Y2O3 cemented carbide, and the simulation calculation diagram of electron cloud density of frontier molecular orbits (HOMO and LUMO) of the two models calculated based on Guassion09W software. As can be seen from the atomic model in Figure 11A, WO3 oxidation layer is formed after pure WC oxidized. Electron cloud density simulation diagram in Figure 11B shows that there is no enrichment of electron cloud between atoms 4C and 1W in HOMO and LUMO frontier molecular orbits, which proves that the adhesion between WO3 oxidation layer and WC substrate is poor and WO3 oxidation layer is easy to fall off. In the atomic model doped with Y2O3 in Figure 11C, Y2O3 and WO3 are easy to oxidize to form a more stable Y2WO6 phase (seen from Figure 10). Since Y (electronegativity: 1.22) is the least electronegative atom than W (electronegativity: 2.36) and C (electronegativity: 2.55) atoms, part of the charge of Y atom will be transferred to atoms W-C, a certain degree of electron cloud enrichment can be clearly seen between atoms 4C and 1W in HOMO and LUMO frontier molecular orbits in Figure 11D, improving the adhesion between the Y2WO6 oxidation layer and WC substrate. The excellent adhesion between the oxidation layer and the substrate surface is enhanced with the “pinning effect” of Y2WO6 (Pint, 1996; Sun et al., 2016; Yu et al., 2017), which also leads to the improvement of the oxidation resistance. However, with the increase in the Y2O3 content, the local enrichment of Y2O3 results in the local rapid oxidation of tungsten carbide and overflows a large amount of CO and CO2 gases. A large outflow of gases resulted in the presence of defects such as pores or cracks (seen from Figures 3, 6), which promotes oxidation rate and reduces the antioxidant capacity of binderless tungsten carbide. The oxidation resistance of binderless tungsten carbide with 1 wt.%Y2O3 is the best among the samples with different content of Y2O3.
FIGURE 11. Simplified oxidation layer/substrate atomic ball-and-stick models of and their electron cloud density simulation diagram. (A) WO3/WC; (B) frontier molecular orbits of model (A); (C) Y2WO6/WC; (D) frontier molecular orbits of model (C).
The effects of Y2O3 addition on high temperature oxidation of binderless tungsten carbide were investigated. The conclusions are as follows: The addition of Y2O3 to the binderless tungsten carbide decreased the oxidization rate constant k and increased the oxidation activation energy Q, which means that the antioxidant property of binderless tungsten carbide was greatly improved with the addition of Y2O3. Meanwhile, the adhesion between the oxidation layer and the substrate surface is enhanced with the addition of Y2O3. With the Y2O3 content increasing from 1 to 4 wt.%, the antioxidant properties of binderless tungsten carbide gradually declined but were still better for all cases than those of pure tungsten carbide and YG3 cemented carbide. After oxidation at 800°C for 120 min, the oxidation weight gain of YG3 cemented carbide was 111.87 mg cm−2, while that of WC-1 wt.% Y2O3 was only 58.54 mg cm−2, corresponding to the reduction by 47.7% compared to YG3 cemented carbide.
The original contributions presented in the study are included in the article/Supplementary Material, further inquiries can be directed to the corresponding authors
JW has made substantial contributions to the data collection and writing of this work. DZ and LZ have made significant contributions to the framework design. ZT, WL and XZ were involved in the data analysis and discussions. XL and YW have helped with the data testing. All authors listed have made a substantial, direct, and intellectual contributions to the work, and approved it for publication.
This research was supported by the National Nature Science Foundation of China, grant number 21671145; Funding of Jiangsu Innovation Program for Graduate Education, grant number KYLX_0228; and Zhejiang Provincial Key Laboratory for Cutting Tools, grant number ZD201610.
Author XL was employed by the company Zhejiang Crystal-Optech Co. LTD.
The remaining authors declare that the research was conducted in the absence of any commercial or financial relationships that could be construed as a potential conflict of interest.
Basu, S. N., and Sarin, V. K. (1996). Oxidation behavior of WC–Co. Mater. Sci. Eng. A. 209, 206–212. doi:10.1016/0921-5093(95)10145-4
Beste, U., Hammerström, L., Engqvist, H., Rimlinger, S., and Jacobsona, S. (2001). Particle erosion of cemented carbides with low Co content. Wear 250, 809–817. doi:10.1016/S0043-1648(01)00735-9
Bhaumik, S. K., Balasubramaniam, R., Upadhyaya, G. S., and Vaidya, M. L. (1999). Oxidation behaviour of hard and binder phase modified WC–10 Co cemented carbides. J. Mater. Sci. Lett. 11, 1457–1459. doi:10.1007/BF00729663
Bozzini, B., Gaudenzi, G. P. D., Fanigliulo, A., and Mele, C. (2004). Electrochemical oxidation of WC in acidic sulphate solution. Corros. Sci. 46, 453–469. doi:10.1016/S0010-938X(03)00146-X
Campo, L. D., Pérez-Sáez, R. B., González-Fernández, L., and Tello, M. J. (2009). Kinetic sinversion in isothermal oxidation of uncoated WC-based carbides between 450 and 800°C. Corros. Sci. 51, 707–712. doi:10.1016/j.corsci.2008.12.022
Chen, L., Yi, D. Q., Wang, B., Liu, H. Q., Wu, C. P., Huang, X., et al. (2015). The selective oxidation behaviour of WC-Co cemented carbides during the early oxidation stage. Corros. Sci. 94, 1–5. doi:10.1016/j.corsci.2015.02.033
Chen, L., Yi, D., Wang, B., Liu, H. Q., and Wu, C. P. (2016). Mechanism of the early stages of oxidation of WC-Co cemented carbides. Corros. Sci. 103, 75–87. doi:10.1016/j.corsci.2015.11.007
Engqvist, H., Axén, N., and Hogmark, S. (1999). Tribological properties of a binderless carbide. Wear 232, 157–162. doi:10.1016/S0043-1648(99)00140-4
He, W., Tan, D. Q., Kuang, H., Li, Y. L., Yang, X., and Zhu, H. B. (2018). Effect of yttrium barrier on the preparation of precursor powders of WC-Co cemented carbide and properties of sintered bulk. J. Alloys Compd. 742, 702–711. doi:10.1016/j.jallcom.2018.01.379
Hussainova, I., Antonov, M., Voltsihhin, N., and Kübarsepp, J. (2014). Wear behavior of Co-free hardmetals doped by zirconia and produced by conventional PM and SPS routines. Wear 312, 83–90. doi:10.1016/j.wear.2014.01.014
Imasato, S., Tokumoto, K., Kitada, T., and Sakaguchi, S. (1995). Properties of ultra-fine grain binderless cemented carbide ‘RCCFN’. Int. J. Refract. Met. Hard Mater. 13, 305–312. doi:10.1016/0263-4368(95)92676-B
Jin, H., Shi, Z. Q., Li, X. D., Li, Y. F., Xia, H. Y., Xu, Z., et al. (2017). Effect of rare earth oxides on the microstructure and properties of mullite/hBN composites. Ceram. Int. 43, 3356–3362. doi:10.1016/j.ceramint.2016.11.179
Kim, H. C., Oh, D. Y., and Shon, I. J. (2004). Synthesis of WC and dense WC-x vol.% Co hard materials by high-frequency induction heated combustion method. Int. J. Refract. Met. Hard Mater. 22, 41–49. doi:10.1016/j.ijrmhm.2003.12.002
Kwak, B. W., Song, J. H., Kim, B. S., and Shon, I. J. (2016). Mechanical properties and rapid sintering of nanostructured WC and WC-TiAl3 hard materials by the pulsed current activated heating. Int. J. Refract. Met. Hard Mater. 54, 244–250. doi:10.1016/j.ijrmhm.2015.08.003
Liu, K., Wang, Z. H., Yin, Z. B., Cao, L. Y., and Yuan, J. T. (2018). Effect of Co content on microstructure and mechanical properties of ultrafine grained WC-Co cemented carbide sintered by spark plasma sintering. Ceram. Int. 44, 18711–18718. doi:10.1016/j.ceramint.2018.07.100
Liu, Y., Li, X. F., Zhou, J. H., Fu, K., Wei, W., Du, M., et al. (2015). Effects of Y2O3 addition on microstructures and mechanical properties of WC-Co functionally graded cemented carbides. Int. J. Refract. Met. Hard Mater. 50, 53–58. doi:10.1016/j.ijrmhm.2014.11.004
Majumdar, P., Jayaramachandran, R., and Ganesan, S. (2005). Finite element analysis of temperature rise in metal cutting processes. Appl. Therm. Eng. 25, 2152–2168. doi:10.1016/j.applthermaleng.2005.01.006
Nino, A., Nakaibayashi, Y., Sugiyama, S., and Taimatsu, H. (2017). Effect of Mo2C addition on the microstructures and mechanical properties of WC-SiC ceramics. Int. J. Refract. Met. Hard Mater. 64, 35–39. doi:10.1016/j.ijrmhm.2016.12.018
Ou, X. Q., Xiao, D. H., Shen, T. T., Song, M., and He, Y. H. (2012). Characterization and preparation of ultra-fine grained WC-Co alloys with minor La-additions. Int. J. Refract. Met. Hard Mater. 31, 266–273. doi:10.1016/j.ijrmhm.2011.12.011
Pint, B. A. (1996). Experimental observations in support of the dynamic-segregation theory to explain the reactive-element effect. Oxid. Met. 45, 1–37. doi:10.1007/BF01046818
Ren, X. Y., Peng, Z. J., Wang, C. B., Fu, Z. Q., Qi, L. H., and Miao, H. Z. (2015). Effect of ZrC nano-powder addition on the microstructure and mechanical properties of binderless tungsten carbide fabricated by spark plasma sintering. Int. J. Refract. Met. Hard Mater. 48, 398–407. doi:10.1016/j.ijrmhm.2014.10.013
Sun, D. J., Liang, C. Y., Shang, J. L., Song, Y. R., Li, W. Z., Liang, T. Q., et al. (2016). Effect of Y2O3 contents on oxidation resistance at 1150°C and mechanical properties at room temperature of ODS Ni-20Cr-5Al alloy. Appl. Surf. Sci. 385, 587–596. doi:10.1016/j.apsusc.2016.05.143
Sutter, G., and Ranc, N. (2007). Temperature fields in a chip during high-speed orthogonal cutting-An experimental investigation. Int. J. Mach. Tools Manu. 47, 1507–1517. doi:10.1016/j.ijmachtools.2006.11.012
Tatarko, P., Kašiarová, M., Dusza, J., and Šajgalík, P. (2013). Influence of rare-earth oxide additives on the oxidation resistance of Si3N4 -SiC nanocomposites. J. Eur. Ceram. Soc. 33, 2259–2268. doi:10.1016/j.jeurceramsoc.2013.01.008
Tsai, K. M., Hsieh, C. Y., and Lu, H. H. (2010). Sintering of binderless tungsten carbide. Ceram. Int. 36, 689–692. doi:10.1016/j.ceramint.2009.10.017
Voitovich, V. B., Sverdel, V. V., Voitovich, R. F., and Golovko, E. I. (1996). Oxidation of WC-Co, WC-Ni and WC-Co-Ni hard metals in the temperature range 500–800°C. Int. J. Refract. Met. Hard Mater. 14, 289–295. doi:10.1016/0263-4368(96)00009-1
Wang, J. F., Zuo, D. W., Zhu, L., Li, W. W., Tu, Z. B., and Dai, S. (2018). Effects and influence of Y2O3 addition on the microstructure and mechanical properties of binderless tungsten carbide fabricated by spark plasma sintering. Int. J. Refract. Met. Hard Mater. 71, 167–174. doi:10.1016/j.ijrmhm.2017.11.016
Xia, X., Li, X. Q., Li, J. M., and Zheng, D. H. (2016). Microstructure and characterization of WC-2.8 wt.% Al2O3-6.8 wt.% ZrO2 composites produced by spark plasma sintering. Ceram. Int. 42, 14182–14188. doi:10.1016/j.ceramint.2016.06.044
Xiao, D. H., He, Y. H., Song, M., Lin, N., and Zhang, R. F. (2010). Y2O3-and NbC-doped ultrafine WC-10Co alloys by low pressure sintering. Int. J. Refract. Met. Hard Mater. 28, 407–411. doi:10.1016/j.ijrmhm.2009.12.008
Yu, H., Ukai, S., Hayashi, S., and Oono, N. H. (2017). Effect of Cr and Y2O3 on the oxidation behavior of Co-based oxide dispersion strengthened superalloys at 900°C. Corros. Sci. 127, 147–156. doi:10.1016/j.corsci.2017.08.013
Zhang, L., Chen, Y., Zhang, H. D., Tang, W., and Zhou, L. (2017). Corrosion and strength degradation behaviors of binderless WC material and WC-Co hardmetal in alkaline solution: a comparative investigation. Int. J. Refract. Met. Hard Mater. 68, 1–8. doi:10.1016/j.ijrmhm.2017.06.003
Zhang, Q. L., To, S., Zhao, Q. L., Guo, B., and Wu, M. T. (2016). Effects of binder addition on the surface generation mechanism of WC/Co during high spindle speed grinding (HSSG). Int. J. Refract. Met. Hard Mater. 59, 32–39. doi:10.1016/j.ijrmhm.2016.05.005
Zheng, D. H., Li, X. Q., Li, Y. Y., Qu, S. G., and Yang, C. (2013). ZrO2 (3Y) toughened WC composites prepared by spark plasma sintering. J. Alloys Compd. 572, 62–67. doi:10.1016/j.jallcom.2013.03.259
Zhong, A., Chen, D., and Li, L. (2015). Revisiting the beryllium bonding interactions from energetic and wavefunction perspectives. Chem. Phys. Lett. 633, 265–272. doi:10.1016/j.cplett.2015.06.007
Keywords: high-temperature oxidation, Y2O3, binderless, tungsten carbide, oxidation kinetics
Citation: Wang J, Zuo D, Zhu L, Tu Z, Lin X, Wu Y, Li W and Zhang X (2021) Effect of Y2O3 Addition on High-Temperature Oxidation of Binderless Tungsten Carbide. Front. Mater. 8:645612. doi: 10.3389/fmats.2021.645612
Received: 23 December 2020; Accepted: 05 February 2021;
Published: 16 March 2021.
Edited by:
Antonio Caggiano, Darmstadt University of Technology, GermanyReviewed by:
Haibin Wang, Beijing University of Technology, ChinaCopyright © 2021 Wang, Zuo, Zhu, Tu, Lin, Wu, Li and Zhang. This is an open-access article distributed under the terms of the Creative Commons Attribution License (CC BY). The use, distribution or reproduction in other forums is permitted, provided the original author(s) and the copyright owner(s) are credited and that the original publication in this journal is cited, in accordance with accepted academic practice. No use, distribution or reproduction is permitted which does not comply with these terms.
*Correspondence: Dunwen Zuo, aW1pdDUwNUBudWFhLmVkdS5jbg==; Liu Zhu, emh1bGl1QHR6Yy5lZHUuY24=
Disclaimer: All claims expressed in this article are solely those of the authors and do not necessarily represent those of their affiliated organizations, or those of the publisher, the editors and the reviewers. Any product that may be evaluated in this article or claim that may be made by its manufacturer is not guaranteed or endorsed by the publisher.
Research integrity at Frontiers
Learn more about the work of our research integrity team to safeguard the quality of each article we publish.