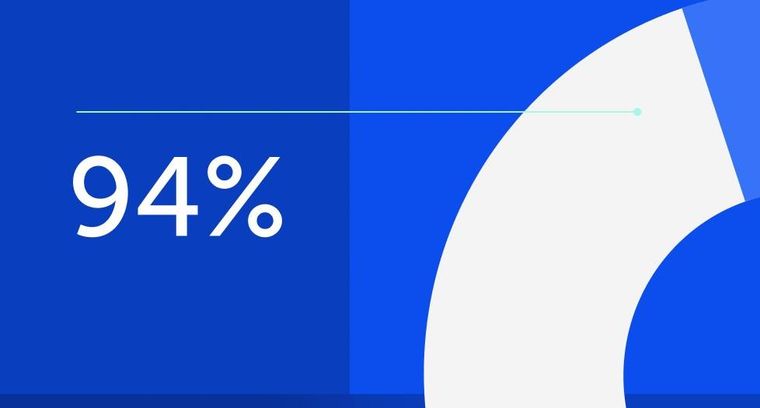
94% of researchers rate our articles as excellent or good
Learn more about the work of our research integrity team to safeguard the quality of each article we publish.
Find out more
REVIEW article
Front. Mater., 25 March 2021
Sec. Smart Materials
Volume 8 - 2021 | https://doi.org/10.3389/fmats.2021.640102
This article is part of the Research TopicSynthesis, Characterization and Applications of Magneto-Responsive Functional MaterialsView all 11 articles
Magnetorheological fluid (MRF) is a kind of smart materials with rheological behavior change by means of external magnetic field application, which has been widely adopted in many complex systems of different technical fields. In this work, the state-of-the-art MRF based devices are reviewed according to structural configurations reported from 2018 to 2020. Based on the rheological characteristic, the MRF has a variety of operational modes, such as flow mode, shear mode, squeeze mode and pinch mode, and has unique advantages in some special practical applications. With reference to these operational modes, improved engineering mechanical devices with MRF are summarized, including brakes, clutches, dampers, and mounts proposed over these 3 years. Furthermore, some new medical devices using the MRF are also investigated, such as surgical assistive devices and artificial limbs. In particular, some outstanding advances on the structural innovations and application superiority of these devices are introduced in detail. Finally, an overview of the significant issues that occur in the MRF based devices is reported, and the developing trends for the devices using the MRF are discussed.
Magnetorheological fluid (MRF), as a kind of smart materials, has been widely studied by scholars due to its controllable rheological properties in a few milliseconds (Jackson et al., 2018; Fu et al., 2020; Zheng et al., 2020). In the technical fields of vibration isolation (Rossi et al., 2018; Phu and Choi, 2019), energy absorption (Ahamed et al., 2016; Yoon J.-Y. et al., 2020), and actuation control (Hong et al., 2019; Zhang L. et al., 2019) et al., MRF has a unique advantage as the main part of the manipulation or regulation mechanism. Therefore, MRF based devices have great potential in structural optimization and innovative development and show outstanding performance in engineering (Hu et al., 2019; Yuan et al., 2019; Zhou et al., 2020) and medical fields (El Wahed, 2020).
MRF based devices are mainly based on four operational modes of MRF, including flow mode, shear mode, squeeze mode and pinch mode, which show different performance in various practical application requirements (Elsaady et al., 2020a). Using the above four operational modes, widely studied engineering mechanical devices mainly involve brake, clutch, damper, and mount etc. (Ahamed et al., 2018). Because the MRF can generate a reliable and stable magnetorheological phenomenon with fast response and strong controllability in the magnetic field environment (Juan et al., 2011), MRF based devices generally have a low failure rate and high regulating ability. However, with the change of the production environment and the improvement of application requirements, these MRF based devices have gradually exposed some defects, such as weak magnetic field (Lee et al., 2018), unstable MRF because of overheated electromagnetic coils (Wang et al., 2019b), settlement of MRF in the idle state (Bastola et al., 2019), leakage of MRF (Tu et al., 2019), and an overall large and bulky devices volume (Li J. H. et al., 2018). Therefore, in view of the various problems in practical applications, many scholars have proposed different improvements and optimization methods based on traditional structures, which has greatly enhanced the performance of the MRF based devices.
Furthermore, different from the above application types, the MRF has been further developed, and has in recent years become an important part of the haptic feedback system (Song et al., 2018b) and artificial limbs (Pandit et al., 2018) in the medical field. In the haptic feedback system based on the MRF, using the controlled rheological characteristics, a resistance environment similar to the real sense of touch is generated and transmitted to the operator, which is widely applied to the teleoperated catheter operating system (Song et al., 2018a) or intelligent haptic interface devices (Topcu et al., 2018). Moreover, in some medical auxiliary and customized devices, such as prostheses (Jing et al., 2018; Zhou and Liu, 2020), rehabilitation protection devices (Zhou et al., 2020), and skeletons (Veronneau et al., 2018), the MRF has been widely studied for advantages of adjustable stiffness and easy structure integration. Based on these specific applications, novel product structures and design methods are proposed using the MRF, which fully reflects the irreplaceable role of the smart material in many advanced technologies.
Having thus described some basic concepts and providing a broad categorization, some typical MRF based devices are investigated in engineering and medical applications from 2018 to 2020. In this work, 104 academic articles from these 3 years are used as a reference, reporting on the novel structure configurations, design purposes, and advantages of MRF based devices. Based on the above classification introduction, the proportions of different development directions are shown in Figure 1. Furthermore, some drawbacks of the MRF filled devices are also summarized. After a discussion, conclusions, and outline, prospects for the development of MRF based devices are presented.
FIGURE 1. Classification of MRF based devices with proportions according to the referred literatures.
A brake is a device with the function of making moving parts (or moving machinery) slow down, stop or maintain the stopped state, which is widely used in lifting transportation equipment, mining equipment, construction engineering equipment, and marine ship equipment. Increasing brake torque, eliminating hysteresis time, optimizing device volume and weight, and reducing energy consumption are the main directions of developing new MRF brakes (Bazargan-Lari, 2019; Zhu et al., 2019). Some MRF brakes reported from 2018 to 2020 are summarized in Table 1.
In 2018, a radial multi-pole-and-layer MRF brake with higher torque and torque density was proposed, shown in Figure 2A (Wu et al., 2018). In this design, two superposition magnetic fields are generated by inner and outer coils with 12 magnetic poles, and four media layers of MRF are located in these coils. The braking characteristics of the device are significantly improved, but the added coils increase the overall weight and energy consumption. Furthermore, an MRF brake was designed with a multi-drum architecture, shown in Figure 2B (Qin et al., 2018). The device is compact and light-weight, generating four gaps of MRF, which increases the shear area but also requires higher manufacturing accuracy. In order to enhance the braking torque, except the above structural changes, a configuration of an MRF brake with three coils on each side of the brake housing was designed, shown in Figure 2C (Nguyen et al., 2019). The device provides better braking performance than a traditional single side-coil MRF brake. However, the device is also unable to avoid the defects of being heavy, having high energy consumption, and temperature interference. Different from the above design solution, an MRF brake was proposed to avoid meaningless loss, where permanent magnets were used to attract MRF into a neighboring gap, shown in Figure 3A (Shamieh and Sedaghati, 2018). Through eliminating contact of the MRF and rotor, power loss due to the zero-field viscous torque is decreased. On the other hand, in the braking state of the device, the effective shear area of MRF is small and the braking torque is limited. Moreover, an elastomeric baffle device with MRF was proposed and applied for the electronic joystick machine shown in Figure 3B (Elliott and Buckner, 2018). The device provides controllable resistance to axial motion of the center shaft and has the advantages of reducing cost and complexity.
FIGURE 2. (A) Multi-pole-and-layer MRF brake (Wu et al., 2018). (B) Multi-drum MRF brake (Qin et al., 2018). (C) Multiple side-coil MRF brake (Nguyen et al., 2019).
FIGURE 3. (A) MRF brake without zero-field viscous torque (Shamieh and Sedaghati, 2018). (B) Elastomeric baffle MRF device (Elliott and Buckner, 2018).
In 2019, a micro-brake was proposed to regulate a miniature turbine generator based on MR fluid and MR grease, respectively, shown in Figure 4A (Huang et al., 2018; Dai et al., 2019). In the simple device, an electromagnetic coil fills internal space, and low permeability materials are used to maximize the magnetic field density. The brake can improve enough resistance when the turbine generator is working at high wind speeds. Similar to a compact structure, a novel hollowed multi-drum MRF brake was proposed to deal with the magnetic hysteresis, shown in Figure 4B (Qin et al., 2019). The device has a multi-drum mode, and a hollowed casing filled with actuator provides the important reference of the composite structure. But these compact structures tend to increase the MRF temperature and cause the braking torque to decrease. Then, a squeezing brake was presented to reduce the effect of temperature on MRF, shown in Figure 4C (Wang et al., 2019a). In this device, several flumes are designed to dissipate the heat of MRF and brake disc, the water-cooling method effectively improves the working time and maintains high brake torque. However, the flumes increase the size of the brake and require the addition of water circulation equipment. Furthermore, in 2020, an MRF brake under squeeze-shear mode was designed, in which a squeezing bolt was presented to produce compressive force for transmission performance, and a magnetic vane was set to ensure that a magnetic flux crosses both sides of the rotor, shown in Figure 4D (Wang and Bi, 2020). Utilizing the combined mode, the MRF device generated higher torque compared to those without compression. Moreover, an MRF brake with adaptive stiffness control was applied to a snake-like robot shown in Figure 4E (Zhang D. et al., 2020). Although this device has only the most basic brake structure, a number of MRF brakes are assembled head to tail, that is, the brake can also be regarded as an actuator. By flexibly controlling the output torque of each joint MRF brake, the twisting motion of the snake-like robot can be realized. Since the motion of each joint is different, the actuators with MRF need to be controlled, separately.
FIGURE 4. (A) Rotary micro-brake (Dai et al., 2019). (B) Multi-drum MRF brake (Qin et al., 2019). (C) High-torque squeezing MRF brake (Wang et al., 2019a). (D) MRF brake with squeeze-shear mode (Wang and Bi, 2020). (E) Snake like robot with MRF actuators (Zhang D. et al., 2020).
A clutch is a commonly used mechanism in transmission or actuation equipment and can separate or engage motion components at any time (Tian et al., 2018; Wang W. D. et al., 2019). As a special power switch, a high-quality clutch has some basic requirements such as a smooth joint, rapid and complete separation, a small sized exterior profile, good wear resistance, adequate heat dissipation capacity, is easy to operate, and is labor saving. Aiming to realize the above working performance, new clutches based on MRF have been extensively studied and have unique advantages in many engineering applications. Some MRF clutches from 2018 to 2020 are summarized in Table 2.
In 2018, an MRF clutch was presented using permanent magnets, which is covered by a steel cylinder (Fernandez et al., 2018). The steel cylinder is adjusted to move the clutch device in and out and alters the intensity of the magnetic field around MRF to vary transmitted torque. This method can quickly control the magnetic field without changing the position of permanent magnets. In 2019, an MRF transmission device was proposed for high-power applications, shown in Figure 5A (Wu et al., 2019). It can be seen from the schematic configuration that a multi-hollow transmission disc was designed, and each single disc has a plurality of magnetic conductive columns and flumes for cooling liquid. The structure design with maximum output torque of 1880 N m and slip power of 70 kW has great working performance. Because of the large working area of the cooling liquid and MRF, the sealing requirements and production costs for this device are high. Based on the coupled operation mode, a multi-disc MRF clutch was presented, two of which are fixed on the casing and shaft, shown in Figure 5B (Kikuchi et al., 2020). Utilizing the clutch, a new actuator with flexible torque control can be assembled for the haptic device. Moreover, a hydrodynamic MRF clutch shown in Figure 5C was proposed, where the centrifugal forces in the pump actuate MRF to flow through the channel placed in the magnetic valve and the cross over turbine (Olszak et al., 2019). Thus, the turbine torque is controlled by regulating excited voltage of the electromagnetic coil. On the other hand, there are higher restrictions on particle size and precipitation characteristics of MRF in this device. In addition, to address the problem of an uneven magnetic field, a wedge clearance was designed in a drum type MRF transmission device (Yang and Chen, 2019). The outer cylinder is connected with the driving shaft, and the inner cylinder with an inclined surface is connected with the driven shaft. MRF fills the wedge-shaped clearance between the inner and outer cylinders. The results show that when the wedge angle is about 1.074°, the magnetic induction intensity in the working gap has the most uniform distribution, which is conducive to a stable and accurate torque output.
FIGURE 5. (A) High-power MRF clutch (Wu et al., 2019). (B) Multi-layered disc MRF clutch and twin-driven MRF actuator (Kikuchi et al., 2020). (C) Hydrodynamic clutch with MRF (Olszak et al., 2019).
In order to maintain a stable working performance and to improve transmission torque, a hybrid model combined with MRF and shape memory alloy was proposed by Wang X. et al. (2019) and Xiong et al. (2019) shown in Figure 6A. When the temperature reaches a critical phase transition value, the electrothermal shape memory spring outputs pressure and pushes the friction disc to squeeze the active disc. The MRF device adds the squeezing working mode with a compact structure, but the operating time of this mode is limited by temperature. In 2020, with the aim to reduce chattering, an MRF clutch-brake was proposed, as shown in Figure 6B (Binyet and Chang, 2020). In this device, permanent magnets are placed in a casing that can axially slide, which allows a good shielding from the magnetic flux in the off mode. Permanent magnets are conducted to mechanically excite the device, offering simplicity and a reliable operation. However, the magnetic field gradient on the surface of permanent magnets is large and the magnetization of MRF is not uniform. In addition, MRF after magnetization and the permanent magnets are magnetically attractive, thus a large force is required to separate them. To improve durability, a magnetic screw pump was studied to promote fluid mixing within an MRF clutch, shown in Figure 6C (Pilon et al., 2020). Instead of having solid flights, the screw flights are made of 3D structures of MRF formed by the concentration of the magnetic field lines around helical grooves. From durability test results, the specific structure can increase durability by up to 42% when compared to a standard MRF based clutch.
FIGURE 6. (A) MRF and shape memory alloy combined clutch (Xiong et al., 2019). (B) MRF clutch-brake with permanent magnets (Binyet and Chang, 2020). (C) MRF clutch with grooved drum (Pilon et al., 2020).
As a new type of mechanical device, MRF dampers and mounts have the ability to provide variable damping (Xu et al., 2018b), mitigate adverse vibration (Dong et al., 2018), and recycle kinetic energy (Wang et al., 2018), and play a key role in many fields (Ha et al., 2018; Lv et al., 2020). For different engineering applications, the development of high-performance MRF dampers and mounts has always been a research hotspot, such as adjusting local structure size, optimizing internal magnetic field, and updating configuration design.
In 2018, based on the concept of functional integration, an MRF device was proposed with controllable damping, energy recovery, and velocity self-sensing, shown in Figure 7A (Bai et al., 2018). In this device, a damping mechanism with MRF generates torque, which is then translated to a linear damping force via a ball screw. Cooperating with a permanent magnet rotor and generator stator, the ball screw converts the mechanical energy to an electrical energy for storage or directly to power electromagnetic coils. To reduce harmfulness from an overshoot to a buffered object, an MRF energy absorber, as a controllable damper, was presented and is shown in Figure 7B (Li Z. Q. et al., 2018). In the device, a structure configuration of a central drain hole is designed on the inner plate to share the drop pressure of MRF and cannot be affected by the magnetic field. However, the design forms a straight flow channel of MRF, which limits the increase of the damping force. To have a better vibration isolation effect, an MRF damper was designed by utilizing multiple electromagnetic poles integrated in the cylinder, shown in Figure 7C (Liu et al., 2018). In the MRF damper, the magnetic flux density in the annular flow channel is effectively increased compared with that of the traditional channel, and the multi-pole structure could minimize the dimension of the piston to improve the active area for a great dynamic range of the damping force. Although the device reduces the volume of the piston and MRF, it increases the size and number of coils, and does not decrease the overall weight. Furthermore, an internal bypass MRF shock absorber was proposed for vibration control of high-speed, and is shown in Figure 7D (Bai et al., 2019). The MRF device consists mainly of the inner and outer coaxially arranged cylinders and one piston. Five electromagnetic coils wound on the outer wall of the inner cylinder increase work length of the fluid gap, and the decoupling windings from the piston effectively improve the stroke of the damper. As the inner cylinder is constrained mainly by the MRF and piston, when the center of inner cylinder is shifted from the axis of the device, the movement of the piston rod may be affected, and the outer cylinder can be damaged. Moreover, to optimize the response time of the damper, an MRF damper with a permanent magnet was proposed, and is shown in Figure 7E (Lee and Choi, 2019). Using ferromagnetic and paramagnetic sidebars shaped by a rectangular column, the step input of the damping force is achieved by the structure design of the magnetization area.
FIGURE 7. (A) Power-generated MRF absorber (Bai et al., 2018). (B) MRF absorber with center drain hole (Li Z. Q. et al., 2018). (C) Outer multi-pole MRF damper (Liu et al., 2018). (D) Internal bypass MRF absorber (Bai et al., 2018). (E) MRF damper with permanent magnet (Lee et al., 2018).
In 2019, an MRF damper, shown in Figure 8A, was proposed for the lunar lander, which can absorb the impact energy from complex landing surfaces (Wang C. et al., 2019). In the device, a combined structure of master and bypass cylinders is designed, where the master cylinder is connected with the piston rod to receive the external impact; the bypass cylinder with coils adjusts the flow viscosity of MRF to change damping. Thus, the MRF in the damper has a definite flow circuit, and damping control is reliable. Furthermore, an MRF damper with a pinch mode was proposed, where a triangle-shaped nonmagnetic spacer is designed to separate the magnetic core and to generate undulating magnetic field lines, shown in Figure 8B (Lee et al., 2019). Utilizing the magnetic field circuit, a pinch mode is formed in the annular MRF damper, and the pinch effect is verified in experiments. To realize a fast response, an MRF damper was designed and is shown in Figure 8C (Yoon et al., 2019; Yoon D. S. et al., 2020). A soft magnetic composite is selected as the core material and the inner surface of the housing is machined with grooves. Through these improvements, the eddy current effect on response time is reduced in the MRF device. In addition, a bi-directional liquid spring damper with MRF was presented and is shown in Figure 8D (Maus and Gordaninejad, 2019). The device with a two-chamber design has equal or dissimilar spring rates in compression and rebound, and the spring rate can also be pre-set independently in both compression and rebound. Because of the two-chamber structure, the sealing area of MRF needs to be increased relatively. Based on the combined operation mode, MRF dampers with an inner and outer chamber damping units were presented (Deng H. X. et al., 2019; Huang et al., 2019). The inner chamber damping unit is connected to a vibrating object, while the outer is connected to a spring, and is shown in Figure 8E. Specifically, the inner unit is set as the piston rod of the outer unit, and outer coil is wound around the outer wall of the inner unit. The combined operation mode effectively expands the control range of the damping force and the stroke range of the piston rod. However, as the damping force is regulated jointly by the spring and MRF, the accurate output of the device is more complicated.
FIGURE 8. (A) MRF damper with combination structure (Wang C. et al., 2019). (B) MRF damper with pinch mode (Lee et al., 2019). (C) MRF damper with fast response (Yoon et al., 2019). (D) Bi-directional liquid spring MRF damper (Maus and Gordaninejad, 2019). (E) MRF damper with two chamber damping units (Deng H. X. et al., 2019).
In 2020, aiming to reduce the sedimentation of MRF, a damper shown in Figure 9A was designed (Huang et al., 2020). In this device, a permanent magnet is embedded in the piston to drive particles back and forth, and a conductive strip is disposed to monitor particle chains of MRF for a sedimentation amount. On the other hand, the permanent magnet also enhances the resistance of the piston during normal movement and increases the energy consumption. To realize a huge range change of the damping force, an MRF damper with a squeeze and valve mode was presented, and is shown in Figure 9B (Ruan et al., 2020). In this device, the piston has an internal channel that divides MRF into three parts. With the movement of the piston, MRF has squeeze and valve working modes at the same time. Furthermore, a bypass MRF damper was proposed with a serpentine flux valve type, and is shown in Figure 9C (Idris et al., 2020). The valve of MRF is connected to a cylinder in the same center axis but is not attached to the piston. So, the device has a larger dynamic range and is less bulky than conventional structures. Moreover, to reuse vibration energy and to simplify the structure, a self-powered MRF damper was proposed for washing machines (Bui et al., 2020). The device integrates an energy-harvesting technology, where induced power from induction coils is directly transmitted to excitation coils of the damper to generate a corresponding damping force, as shown in Figure 9D.
FIGURE 9. (A) MRF damper with self-monitoring (Huang et al., 2020). (B) MRF damper with squeeze-valve mode (Ruan et al., 2020). (C) MRF damper with serpentine flux valve (Idris et al., 2020). (D) MRF damper with self-powered (Bui et al., 2020).
In addition, some other MRF dampers, mounts, and absorbers with a vibration reduction effect have been studied and optimized in key positions to effectively improve the working performance. These MRF devices are also summarized for corresponding improved methods, as shown in Table 3.
With the development of remote surgery and robot-assisted equipment, the MRF plays an increasingly important role in the medical field. The MRF is mainly applied in two aspects—tactile feedback devices and medical wearable rehabilitation devices. The research results obtained between 2018 and 2020, are briefly summarized in Table 4.
Using MRF to simulate the feedback of different environments and to provide operators with real tactile experience are currently hot research topics. In 2018, for surgical robotic applications, a force generator module with MRF was developed to provide force-feedback information (Shokrollahi et al., 2020). The device, shown in Figure 10A, is capable of rapidly re-producing forces generated in tele-robotic bone biopsy procedures and provides a wide range of force measurements. However, it is difficult to simulate all the stress ranges only using MRF in the areas where the hardness changes greatly between bone and soft tissue. In 2019, an MRF spherical actuator with haptic feedback was proposed to the applications of joysticks (Chen D. P. et al., 2019). The actuator, shown in Figure 10B, has a special stator that replaces the traditional single coil with eight separate coils and magnetic circuits, which can achieve control of forces in different interaction directions. Furthermore, an endovascular catheterization system shown in Figure 10C was proposed, which consists of a master device and a slave device (Yin et al., 2018; Guo et al., 2019). In the slave device, the catheter moves in the blood vessel and sends real resistance obtained by the sensor to the master device. The master device uses MRF to simulate the resistance, thus giving the remote physician a realistic sense and improving the safety of surgery. This master device provides an approximate damping environment, but in a particular direction, the variation of damping is not very differentiated. Similarly, to realize a certain stiffness and damping properties of human tissue, a controllable tactile device was designed, where MRF was immersed into porous polyurethane foam and sealed by adhesive tape (Park et al., 2020). The device, shown in Figure 10D, can capture several different repulsive forces of human organs generated at an operating site in minimally invasive surgery and can improve the real tactile sensing of the remote doctor.
FIGURE 10. (A) MRF haptic device for robotic bone biopsy (Shokrollahi et al., 2020). (B) Multi-direction MRF actuator for haptic applications (Chen D. P. et al., 2019). (C) Endovascular catheterization system with haptic feedback (Guo et al., 2019). (D) Tactile device to simulate human tissues forces (Park et al., 2020).
Moreover, MRF also has many new applications in medical rehabilitation equipment. In 2018, a prosthetic knee with a novel MRF brake was proposed, assisting humans to realize normal gait movement (Mousavi and Sayyaadi, 2018). The MRF brake, shown in Figure 11A, has a T-shaped drum with an arc form surface boundary, which can meet the requirements for flexible variation of the braking torque. To enhance the rehabilitation of the human shoulder and upper limb, a multi-freedom MRF based damper with a ball-and-socket structure was proposed (Wahed and Balkhoyor, 2018; Wahed and Wang, 2019). The new damper shown in Figure 11B can effectively simulate the motion of human joints and provides a rehabilitation training environment. Further, the device can refine the design of damping forces in different directions to realize the control of damping variation in multi-directions. Furthermore, using a drawing lithography approach, some MRF microneedles were fabricated for minimally invasive surgery, transdermal drug delivery, and smart wearable equipment (Chen Z. P. et al., 2018; Chen et al. 2019a; Chen et al., 2019b). In a gradient magnetic field, the MRF is magnetized and generates fusiform patterns, which results in different forms of microneedle arrays after heating and solidifying, as shown in Figure 10C. The MRF microneedles are cheaper and simpler to produce than traditional precision machining. With the aim to prevent paralysis and gait abnormalities affecting human ankle joints, a semi-active ankle-foot orthosis with an MRF link mechanism was designed (Oba et al., 2019). The MRF device, combined with a compression spring, can mitigate foot slap and toe drag during different phases of movement, as shown in Figure 11D. Similarly, for movement recovery, an MRF variable stiffness leg was designed to improve energy efficiency and gait stability (Christie et al., 2019b). The device, shown in Figure 11E, is housed in the lower leg section, whose output shaft is linked to the upper leg section. When the coil current is zero, the leg has a soft single spring stiffness, while huge damping torque is achieved under a large input current. Therefore, the device has a relatively wide range of damping variation. Moreover, based on the assistive technologies, a novel soft exoskeleton with MRF damper was proposed to suppress pathological tremor (Zahedi et al., 2020). The MRF damper connected with a flexible elliptic spring can assist in suppressing tremor of the wrist joint in 3 ° of freedom with varying intensity, as shown in Figure 11F. This device prevents wrist tremor with a less constrained area on the hand surface, which thus reduces the suppression effect of a small amplitude tremor.
FIGURE 11. (A) MRF damper with drum of an arc surface boundary (Mousavi and Sayyaadi, 2018). (B) Smart ball-socket actuator for upper limb rehabilitation (Wahed and Balkhoyor, 2018). (C) Magnetization-induced self-assembling process of microneedle array (Chen Z. P. et al., 2018; Chen et al. 2019a; Chen et al., 2019b). (D) MRF damper for ankle-foot orthosis (Oba et al., 2019). (E) MRF based variable stiffness leg (Christie et al., 2019b). (F) MRF soft exoskeleton (Zahedi et al., 2020).
According to different structure configurations, MRF based devices reported from 2018 to 2020 are investigated in this work, including MRF brakes, MRF clutches, MRF dampers and mounts for engineering applications, and other new devices for medical applications. In terms of the literature presented above, improvement methods are mainly concentrated in the following ways: Use of multiple coils or magnetic poles to enhance magnetic field strength; Improving the combination of braking structure and active structure to increase the effective contact area of MRF; Replacing the coil with a permanent magnet, or adjusting the size and position of the permanent magnet to improve working performance; Optimizing the magnetic circuit to improve the utilization ratio of the magnetic field; Changing the position of the magnetic field in the working process to avoid settling of MRF or reducing the zero field viscosity. There have been many successful applications that have come from these improvements, but some problems still need to be addressed. By adding coils and magnetic poles, the volume and weight of devices can be larger, which is not easy to disassemble and cost may also be increased. Furthermore, when the working area of MRF is enlarged, the wear is relatively enhanced and the working temperature is also increased, so the rheological property is decreased. By adopting a bypass or extension structure, the output range of devices is extended, but the response time and maximum output force needs to be balanced. In addition, when the MRF is applied in haptic devices, it is still limited to simulating the feedback forces that are in different directions at the same time or one direction with large variation gradient.
In light of the practical application requirements, some development directions are proposed for MRF based devices. The combination of working modes in a limited volume may play a greater role, such as shear-squeeze mode, flow-squeeze mode, etc. The cooperation of magnetic materials and coils can be further developed to increase strength, flexibility, and utilization of the magnetic field, and can reduce power consumption. In order to improve the service life of devices and the accuracy of fault diagnoses, some structure can be designed to measure the working temperature and wear condition of MRF. With the increasing torque output, the energy loss caused by zero field viscosity should be seriously considered, where an ultrasonic wave can be used to reduce zero field viscosity or can cut off the contact between MRF and the rotor to avoid unnecessary energy consumption. Aiming to improve the accuracy of haptic feedback in complex structures, MRF can be combined with other rheological materials or magnetic actuated elastic materials to design a multilayer configuration.
The application potential of MRF in different fields will be further explored. For example, according to the variable damping and stiffness characteristics of MRF, intelligent wearable devices can be used in medical treatment to prevent joint vibration; in virtual reality devices, the motion damping is changed for the wearer to increase the experience of a real environment; in the remote control of medical or other fields, real-time tactile feedback is simulated for operators to improve the sense of reality. Although these directions present many challenging problems, the need for practical applications will certainly drive current research of MRF based devices forward.
DH: Methodology, software, data curation, writing-original draft preparation. XL: Conceptualization, methodology, analysis. ZL: Resources, visualization, investigation. PF: Analysis, writing-reviewing and editing. AH-S: Resources, funding acquisition, writing-reviewing and editing. ZL: Conceptualization, writing-reviewing and editing, funding acquisition.
This work was supported in part by the Future Scientists Program of China University of Mining and Technology (2020WLKXJ025), the Postgraduate Research and Practice Innovation Program of Jiangsu Province (KYCX20_1986) and Priority Academic Program Development of Jiangsu Higher Education Institutions (PAPD).
The authors declare that the research was conducted in the absence of any commercial or financial relationships that could be construed as a potential conflict of interest.
Ahamed, R., Choi, S.-B., and Ferdaus, M. M. (2018). A state of art on magneto-rheological materials and their potential applications. J. Intell. Mater. Syst. Struct. 29 (10), 2051–2095. doi:10.1177/1045389X18754350
Ahamed, R., Ferdaus, M. M., and Li, Y. (2016). Advancement in energy harvesting magneto-rheological fluid damper: a review. Korea Aust. Rheol. J. 28 (4), 355–379. doi:10.1007/s13367-016-0035-2
Bai, X.-X., Zhong, W.-M., Zou, Q., Zhu, A.-D., and Sun, J. (2018). Principle, design and validation of a power-generated magnetorheological energy absorber with velocity self-sensing capability. Smart Mater. Struct. 27 (7), 1–43. doi:10.1088/1361-665X/aac7ef
Bai, X. X., Shen, S., Wereley, N. M., and Wang, D. H. (2019). Controllability of magnetorheological shock absorber: I. Insights, modeling and simulation. Smart Mater. Struct. 28 (1), 1–44. doi:10.1088/1361-665X/aaf072
Bastola, A. K., Ang, E., Paudel, M., and Li, L. (2019). Soft hybrid magnetorheological elastomer: gap bridging between MR fluid and MR elastomer. Colloids Surf. A Physicochem. Eng. Asp. 583, 1–35. doi:10.1016/j.colsurfa.2019.123975
Bazargan-Lari, Y. (2019). Design and shape optimization of MR brakes using Nelder-Mead optimization algorithm. Mech. Ind. 20 (6), 1–9. doi:10.1051/meca/2019017
Binyet, E. M., and Chang, J.-Y. (2020). Magnetohydrodynamics modelling of a permanent magnets activated MRF clutch-brake. Microsyst. Technol. 26 (11), 3451–3457. doi:10.1007/s00542-020-04910-w
Bui, Q.-D., Nguyen, Q. H., Nguyen, T. T., and Mai, D.-D. (2020). Development of a magnetorheological damper with self-powered ability for washing machines. Appl. Sci. 10 (12), 1–22. doi:10.3390/app10124099
Chen, B., Huang, D., Li, C., and Chen, C. (2019). Design and modeling for 2D plate type MR damper. Front. Mater. 6, 1–28. doi:10.3389/fmats.2019.00028
Chen, C., Chan, Y. S., Zou, L., and Liao, W.-H. (2018). Self-powered magnetorheological dampers for motorcycle suspensions. Proc. Inst. Mech. Eng. D J. Automob. Eng. 232 (7), 921–935. doi:10.1177/0954407017723761
Chen, D. P., Song, A. G., Tian, L., Ouyang, Q. Q., and Xiong, P. W. (2019). Development of a multidirectional controlled small-scale spherical MR actuator for haptic applications. IEEE/ASME Trans. Mechatron. 24 (4), 1597–1607. doi:10.1109/TMECH.2019.2916099
Chen, Z. P., Ren, L., Li, J. Y., Yao, L. B., and Chen, Y. (2018). Rapid fabrication of microneedles using magnetorheological drawing lithography. Acta Biomater. 65, 283–291. doi:10.1016/j.actbio.2017.10.030
Chen, Z. P., Ye, R., Lee, W., Ji, D. W., Zhang, Y. X., and Yang, Y. L. (2019a). Magnetization‐induced self‐assembling of bendable microneedle arrays for triboelectric nanogenerators. Adv. Electron. Mater. 5 (5), 1–9. doi:10.1002/aelm.201800785
Chen, Z. P., Ye, R., Yang, J. B., Lin, Y. Y., Lee, W. H., and Li, J. W. (2019b). Rapidly fabricated microneedle arrays using magnetorheological drawing lithography for transdermal drug delivery. ACS Biomater. Sci. Eng. 5 (10), 5506–5513. doi:10.1021/acsbiomaterials.9b00919
Cheng, M., Chen, Z. B., and Xing, J. W. (2018). Design, analysis, and experimental evaluation of a magnetorheological damper with meandering magnetic circuit. IEEE Trans. Magn. 54 (5), 1–10. doi:10.1109/TMAG.2018.2797090
Christie, M. D., Sun, S., Deng, L., Ning, D. H., Du, H., Zhang, S. W., et al. (2019a). A variable resonance magnetorheological-fluid-based pendulum tuned mass damper for seismic vibration suppression. Mech. Syst. Signal Process. 116, 530–544. doi:10.1016/j.ymssp.2018.07.007
Christie, M. D., Sun, S., Ning, D. H., Du, H., Zhang, S. W., and Li, W. H. (2019b). A highly stiffness-adjustable robot leg for enhancing locomotive performance. Mech. Syst. Signal Process. 126, 458–468. doi:10.1016/j.ymssp.2019.02.043
Dai, J., Chang, H., Zhao, R., Huang, J., and Li, K. Q. (2019). Investigation of the relationship among the microstructure, rheological properties of MR grease and the speed reduction performance of a rotary micro-brake. Mech. Syst. Signal Process. 116, 741–750. doi:10.1016/j.ymssp.2018.07.004
Deng, H. X., Deng, J. L., Yue, R., and Han, G. H. (2019). Design and verification of a seat suspension with variable stiffness and damping. Smart Mater. Struct. 28 (6), 1–11. doi:10.1088/1361-665X/ab18d4
Deng, H. X., Han, G. H., Zhang, J., and Wang, M. X. (2018). Development of a non-piston MR suspension rod for variable mass systems. Smart Mater. Struct. 27 (6), 1–10. doi:10.1088/1361-665X/aabc2b
Deng, L., Sun, S. S., Christie, M. D., and Yang, J. (2019). Experimental testing and modelling of a rotary variable stiffness and damping shock absorber using magnetorheological technology. J. Intell. Mater. Syst. Struct. 30 (10), 1453–1465. doi:10.1177/1045389X19835955
Desai, R. M., Jamadar, M. E. H., Kumar, H., Joladarashi, S., and Sekaran, S. C. R. (2019). Design and experimental characterization of a twin-tube MR damper for a passenger van. J. Braz. Soc. Mech. Sci. Eng. 41 (8), 1–12. doi:10.1007/s40430-019-1833-5
Dong, X. M., Liu, W. Q., An, G. P., Zhou, Y. Q., and Yu, J. Q. (2018). A novel rotary magnetorheological flexible joint with variable stiffness and damping. Smart Mater. Struct. 27 (10), 1–25. doi:10.1088/1361-665X/aae00e
El Wahed, A. K. (2020). A novel hydraulic actuation system utilizing magnetorheological fluids for single-port laparoscopic surgery applications. Materials 13 (6), 1–13. doi:10.3390/ma13061380
Elliott, C. M., and Buckner, G. D. (2018). Design optimization of a novel elastomeric baffle magnetorheological fluid device. J. Intell. Mater. Syst. Struct. 29 (19), 3774–3791. doi:10.1177/1045389X18799211
Elsaady, W., Oyadiji, S. O., and Nasser, A. (2020a). A review on multi-physics numerical modelling in different applications of magnetorheological fluids. J. Intell. Mater. Syst. Struct. 31 (16), 1855–1897. doi:10.1177/1045389X20935632
Elsaady, W., Oyadiji, S. O., and Nasser, A. (2020b). Magnetic circuit analysis and fluid flow modeling of an MR damper with enhanced magnetic characteristics. IEEE Trans. Magn. 56 (9), 1–20. doi:10.1109/TMAG.2020.3011669
Fernandez, M. A., Chang, J.-Y., and Huang, C.-Y. (2018). Development of a passive magnetorheological fluid clutch with field-blocking mechanism. IEEE Trans. Magn. 54 (11), 1–5. doi:10.1109/TMAG.2018.2834389
Fu, Y., Yao, J. J., Zhao, H. H., Zhao, G., Wan, Z. S., and Guo, R. Z. (2020). A muscle-like magnetorheological actuator based on bidisperse magnetic particles enhanced flexible alginate-gelatin sponges. Smart Mater. Struct. 29 (1), 1–13. doi:10.1088/1361-665X/ab515f
Guo, S. X., Song, Y., Yin, X. C., Zhang, L. S., Tamiya, T., and Hirata, H. (2019). A novel robot-assisted endovascular catheterization system with haptic force feedback. IEEE Trans. Robot. 35 (3), 685–696. doi:10.1109/TRO.2019.2896763
Ha, Q., Royel, S., and Balaguer, C. (2018). Low-energy structures embedded with smart dampers. Energy Build. 177, 375–384. doi:10.1016/j.enbuild.2018.08.016
Han, C., Kim, B.-G., Kang, B.-H., and Choi, S.-B. (2019). Effects of magnetic core parameters on landing stability and efficiency of magnetorheological damper-based landing gear system. J. Intell. Mater. Syst. Struct. 31 (2), 198–208. doi:10.1177/1045389X19862639
Hong, S.-W., Yoon, J.-Y., Kim, S.-H., Lee, S.-K., Kim, Y.-R., Park, Y.-J., et al. (2019). 3D-Printed soft structure of polyurethane and magnetorheological fluid: a proof-of-concept investigation of its stiffness tunability. Micromachines 10 (10), 1–9. doi:10.3390/mi10100655
Hu, G., Zhang, J., Zhong, F., and Yu, L. (2019). Performance evaluation of an improved radial magnetorheological valve and its application in the valve controlled cylinder system. Smart Mater. Struct. 28 (4), 1–18. doi:10.1088/1361-665X/ab0b4f
Huang, H., Chen, C., Zhang, Z. C., Zheng, J. N., Li, Y. Z., and Chen, S. M. (2020). Design and experiment of a new structure of MR damper for improving and self-monitoring the sedimentation stability of MR fluid. Smart Mater. Struct. 29 (7), 1–22. doi:10.1088/1361-665X/ab8839
Huang, H., Sun, S. S., Chen, S. M., and Li, W. H. (2019). Numerical and experimental studies on a new variable stiffness and damping magnetorheological fluid damper. J. Intell. Mater. Syst. Struct. 30 (11), 1639–1652. doi:10.1177/1045389X19844003
Huang, J., Dai, J., Zhao, R., Chang, H., and Xie, S. (2018). Investigation on current excitation of magnetorheological-fluid-based microbrake for microturbine generator. AIAA J. 56 (10), 4039–4048. doi:10.2514/1.J056948
Idris, M. H., Imaduddin, F., Mazlan, S. A., and Choi, S. B. (2020). A concentric design of a bypass magnetorheological fluid damper with a serpentine flux valve. Actuators 9 (1), 1–21. doi:10.3390/act9010016
Jackson, J. A., Messner, M. C., and Dudukovic, N. A. (2018). Field responsive mechanical metamaterials. Sci. Adv. 4 (12), 1–9. doi:10.1126/sciadv.aau6419
Jing, Z. J., Sun, S. S., and Ouyang, Y. M. (2018). Design and modeling analysis of a changeable stiffness robotic leg working with magnetorheological technology. J. Intell. Mater. Syst. Struct. 29 (19), 3725–3736. doi:10.1177/1045389X18798958
Juan, D. V., Daniel, J. K., and Roque, H. A. (2011). Magnetorheological fluids a review. Soft Matter 7, 3701–3710. doi:10.1088/1361-665X/ab515f
Kang, B.-H., Yoon, J.-Y., Kim, G.-W., and Choi, S.-B. (2020). Landing efficiency control of a six-degree-of-freedom aircraft model with magnetorheological dampers: part 1-modeling. J. Intell. Mater. Syst. Struct., 1045389X2094257. doi:10.1177/1045389X20942578
Kikuchi, T., Abe, I., Nagata, T., Yamaguchi, A., and Takano, T. (2020). Twin-driven actuator with multi-layered disc magnetorheological fluid clutches for haptics. J. Intell. Mater. Syst. Struct., 1045389X2094395. doi:10.1177/1045389X20943958
Kim, B. G., Yoon, D. S., Kim, G. W., Choi, S. B., and Tan, A. S. (2020). Design of a novel magnetorheological damper adaptable to low and high stroke velocity of vehicle suspension system. Appl. Sci. 10 (16), 1–17. doi:10.3390/app10165586
Lee, T.-H., Kang, B.-H., and Choi, S.-B. (2019). A quasi-static model for the pinch mode analysis of a magnetorheological fluid flow with an experimental validation. Mech. Syst. Signal Process. 134, 1–16. doi:10.1088/1361-665X/ab515f10.1016/j.ymssp.2019.106308
Lee, T. H., and Choi, S. B. (2019). On the response time of a new permanent magnet based magnetorheological damper experimental investigation. Smart Mater. Struct. 28 (1), 1–31. doi:10.1088/1361-665X/aaf0dc
Lee, T. H., Han, C., and Choi, S. B. (2018). Design and damping force characterization of a new magnetorheological damper activated by permanent magnet flux dispersion. Smart Mater. Struct. 27 (1), 1–13. doi:10.1088/1361-665X/aa9ad6
Li, J. H., Liu, Z. H., and Liu, Z. (2018). Electromechanical characteristics and numerical simulation of a new smaller magnetorheological fluid damper. Mech. Res. Commun. 92, 81–86. doi:10.1016/j.mechrescom.2018.07.010
Li, Z. Q., Liao, C. R., Fu, B. Y., Jian, X. C., and Shou, M. J. (2018). Study of radial flow mode magnetorheological energy absorber with center drain hole. Smart Mater. Struct. 27 (10), 1–16. doi:10.1088/1361-665X/aad932
Liu, S. G., Feng, L. F., Zhao, D., and Huang, H. (2018). The development of an outer multi-pole magneto-rheological damper with high dynamic range of damping force. Smart Mater. Struct. 27 (11), 1–27. doi:10.1088/1361-665X/aae004
Lv, H., Zhang, S., Sun, Q., Chen, R., and Zhang, W. J. (2020). The dynamic models, control strategies and applications for magnetorheological damping systems: a systematic review. J. Vib. Eng. Technol. 9, 131–147. doi:10.1007/s42417-020-00215-4
Maus, N., and Gordaninejad, F. (2019). A Bi-directional, liquid-spring-magnetorheological-fluid-damper system. Front. Mater. 6, 1–11. doi:10.3389/fmats.2019.00006
Mousavi, S. H., and Sayyaadi, H. (2018). Optimization and testing of a new prototype hybrid MR brake with arc form surface as a prosthetic knee. IEEE/ASME Trans. Mechatron. 23 (3), 1204–1214. doi:10.1109/TMECH.2018.2820065
Nguyen, N. D., Thang, L. D., Hiep, L. D., and Nguyen, Q. H. (2019). Development of a new magnetorheological fluid–based brake with multiple coils placed on the side housings. J. Intell. Mater. Syst. Struct. 30 (5), 734–748. doi:10.1177/1045389X18818385
Ning, D. H., Sun, S. S., Yu, J. Q., and Zheng, M. Y. (2019). A rotary variable admittance device and its application in vehicle seat suspension vibration control. J. Franklin Inst. 356 (14), 7873–7895. doi:10.1016/j.jfranklin.2019.04.015
Oba, T., Kadone, H., Hassan, M., and Suzuki, K. (2019). Robotic ankle-foot orthosis with a variable viscosity link using MR fluid. IEEE/ASME Trans. Mechatron. 24 (2), 495–504. doi:10.1109/TMECH.2019.2894406
Oh, J.-S., and Choi, S.-B. (2019). Ride quality control of a full vehicle suspension system featuring magnetorheological dampers with multiple orifice holes. Front. Mater. 6, 1–10. doi:10.3389/fmats.2019.00008
Olszak, A., Osowski, K., Kesy, Z., and Kesy, A. (2019). Investigation of hydrodynamic clutch with a magnetorheological fluid. J. Intell. Mater. Syst. Struct. 30 (1), 155–168. doi:10.1177/1045389X18803463
Ouyang, Q., Hu, H., Qian, C., Zhang, G., Wang, J., and Zheng, J. (2019). Investigation of the influence of magnetic field distribution on the magnetorheological absorber with individually controllable coils. IEEE Trans. Magn. 55 (8), 1–13. doi:10.1109/TMAG.2019.2907515
Pandit, S., Godiyal, A. K., and Vimal, A. K. (2018). An affordable insole-sensor-based trans-femoral prosthesis for normal gait. Sensors 18 (3), 1–18. doi:10.3390/s18030706
Park, Y.-J., Yoon, J.-Y., Kang, B.-H., Kim, G.-W., and Choi, S.-B. (2020). A tactile device generating repulsive forces of various human tissues fabricated from magnetic-responsive fluid in porous polyurethane. Materials 13 (5), 1–14. doi:10.3390/ma13051062
Phu, D. X., and Choi, S.-B. (2019). Magnetorheological fluid based devices reported in 2013-2018: mini-review and comment on structural configurations. Front. Mater. 6, 19. doi:10.3389/fmats.2019.00019
Pilon, R., Landry-Blais, A., and Gillet, B. (2020). A magnetic screw pump for magnetorheological clutch durability enhancement. J. Intell. Mater. Syst. Struct. 31 (7), 945–955. doi:10.1177/1045389X20906474
Qiang, L. S., Wang, J. S., Chen, C., and Wang, F. F. (2019). Design and analysis of magnetorheological fluid dampers based on ultrasonic effects. China Mech. Eng. 30 (14), 1658–1672. doi:10.3969/j.issn.1004-132X.2019.014.004
Qin, H. H., Song, A. G., and Mo, Y. T. (2019). A hybrid actuator with hollowed multi-drum magnetorheological brake and direct-current micromotor for hysteresis compensation. J. Intell. Mater. Syst. Struct. 30 (7), 1031–1042. doi:10.1177/1045389X19828473
Qin, H., Song, A., Zeng, X., and Hu, S. (2018). Design and evaluation of a small-scale multi-drum magnetorheological brake. J. Intell. Mater. Syst. Struct. 29 (12), 2607–2618. doi:10.1177/1045389X18770878
Rossi, A., Orsini, F., Scorza, A., Botta, F., Belfiore, N., and Sciuto, S. (2018). A review on parametric dynamic models of magnetorheological dampers and their characterization methods. Actuators 7 (2), 1–21. doi:10.3390/act7020016
Ruan, X. H., Xuan, S. H., Zhao, J., Bian, H. T., and Gong, X. L. (2020). Mechanical performance of a novel magnetorheological fluid damper based on squeeze-valve bi-mode of MRF. Smart Mater. Struct. 29 (5), 1–42. doi:10.1088/1361-665X/ab7e34
Sassi, S., Sassi, A., Cherif, K., and Tarlochan, F. (2018). Magnetorheological damper with external excitation for more efficient control of vehicles' dynamics. J. Intell. Mater. Syst. Struct. 29 (14), 2919–2932. doi:10.1177/1045389X18781038
Shamieh, H., and Sedaghati, R. (2018). Development, optimization, and control of a novel magnetorheological brake with no zero-field viscous torque for automotive applications. J. Intell. Mater. Syst. Struct. 29 (16), 3199–3213. doi:10.1177/1045389X18758186
Shokrollahi, E., Goldenberg, A. A., Drake, J. M., Eastwood, K. W., and Kang, M. (2020). Application of a nonlinear Hammerstein-Wiener estimator in the development and control of a magnetorheological fluid haptic device for robotic bone biopsy. Actuators 7 (4), 1–22. doi:10.3390/act7040083
Song, Y., Guo, S. X., and Yin, X. C. (2018a). Design and performance evaluation of a haptic interface based on MR fluids for endovascular tele-surgery. Microsyst. Technol. 24 (2), 909–918. doi:10.1007/s00542-017-3404-y
Song, Y., Guo, S. X., and Yin, X. C. (2018b). Performance evaluation of a robot-assisted catheter operating system with haptic feedback. Biomed. Microdevices 20 (2), 50. doi:10.1007/s10544-018-0294-4
Tian, S. L., Chen, X. A., He, Y., Chen, T. C., and Li, P. M. (2018). A dynamic loading system for high-speed motorized spindle with magnetorheological fluid. J. Intell. Mater. Syst. Struct. 29 (13), 2754–2765. doi:10.1177/1045389X18778369
Topcu, O., Tascioglu, Y., and Konukseven, E. I. (2018). Modeling and experimental evaluation of a rotary peristaltic magnetorheological fluid device with low off-state torque for haptic interfaces. J. Braz. Soc. Mech. Sci. 40 (1), 1–9. doi:10.1007/s40430-017-0930-6
Tu, J. W., Li, Z., and Zhang, J. R. (2019). Development, test, and mechanical model of the leak-proof magnetorheological damper. Front. Mater. 6, 1–13. doi:10.3389/fmats.2019.00118
Urkucu, T., and Keles, O. (2018). Magneto-rheological engine mount design and experimental characterization. J. Mech. Sci. Technol. 32 (11), 5171–5178. doi:10.1007/s12206-018-1015-y
Veronneau, C., Bigue, J. P. L., Lussier-Desbiens, A., and Plante, J. S. (2018). A high-bandwidth back-drivable hydrostatic power distribution system for exoskeletons based on magnetorheological clutches. IEEE. Robot. Autom. Lett. 3 (3), 2592–2599. doi:10.1109/LRA.2018.2812910
Wahed, A. K. E., and Balkhoyor, L. B. (2018). The performance of a smart ball-and-socket actuator applied to upper limb rehabilitation. J. Intell. Mater. Syst. Struct. 29 (13), 2811–2822. doi:10.1177/1045389X18780349
Wahed, A. K. E., and Wang, H. C. (2019). Performance evaluation of a magnetorheological fluid damper using numerical and theoretical methods with experimental validation. Front. Mater. 6, 1–9. doi:10.3389/fmats.2019.00027
Wang, C., Nie, H., Chen, J., and Lee, H. P. (2019). The design and dynamic analysis of a lunar lander with semi-active control. Acta Astronaut. 157, 145–156. doi:10.1016/j.actaastro.2018.12.037
Wang, H. Y., and Bi, C. (2020). Study of a magnetorheological brake under compression-shear mode. Smart Mater. Struct. 29 (1), 1–17. doi:10.1088/1361-665X/ab5162
Wang, N. N., Liu, X. H., and Grzegora, K. (2019a). Effect of temperature on the transmission characteristics of high-torque magnetorheological brakes. Smart Mater. Struct. 28 (1), 1–20. doi:10.1088/1361-665X/ab134c
Wang, N. N., Liu, X. H., and Zhang, X. H. (2019b). Squeeze-strengthening effect of silicone oil-based magnetorheological fluid with nanometer Fe3O4 addition in high-torque magnetorheological brakes. J. Nanosci. Nanotechnol. 19 (5), 2633–2639. doi:10.1166/jnn.2019.15895
Wang, W. D., Sun, T. S., and Yuan, X. Q. (2019). Design and analysis of variable flexible actuator for human-robot interaction. J. Northwest. Polytechn. Univ. 37 (2), 242–248. doi:10.1051/jnwpu/20193720242
Wang, X., Huang, J., and Xie, Y. (2019). Research on conical magnetorheological and shape memory alloy composite transmission performance. J. Mech. Transm. 43 (8), 36–40. doi:10.16578/j.issn.1004.2539.2019.08.007
Wang, Z. H., Chen, Z. Q., Gao, H., and Wang, H. (2018). Development of a self-powered magnetorheological damper system for cable vibration control. Appl. Sci. 8 (1), 118. doi:10.3390/app8010118
Wei, M., Rui, X., Zhu, W., Yang, F., Gu, L., and Zhu, H. (2020). Design, modelling and testing of a novel high-torque magnetorheological damper. Smart Mater. Struct. 29 (2), 1–13. doi:10.1088/1361-665X/ab6436
Wu, J., Li, H., Jiang, X., and Yao, J. (2018). Design, simulation and testing of a novel radial multi-pole multi-layer magnetorheological brake. Smart Mater. Struct. 27 (2), 1–12. doi:10.1088/1361-665X/aaa58a
Wu, X. F., Huang, C. H., Tian, Z. Z., and Ji, J. J. (2019). Development of a novel magnetorheological fluids transmission device for high-power applications. Smart Mater. Struct. 28 (5), 1–13. doi:10.1088/1361-665X/ab0eaf
Xin, D. K., Nie, S. L., Ji, H., and Yin, F. L. (2018). Characteristics, optimal design, and performance analyses of MRF damper. Shock Vib. 2018, 6454932. doi:10.1155/2018/6454932
Xiong, Y., Huang, J., and Shu, R. Z. (2019). Combined transmission performance of magnetorheological and electrothermal shape memory alloy. China Mechanical Engineering. Available at: http://kns.cnki.net/kcms/detail/42.1294.TH.20201013.1440.009.html.
Xu, L.-H., Xie, X.-S., and Li, Z.-X. (2018a). A self-centering brace with superior energy dissipation capability: development and experimental study. Smart Mater. Struct. 27 (9), 1–23. doi:10.1088/1361-665X/aad5b0
Xu, L.-H., Xie, X.-S., and Li, Z.-X. (2018b). Development and experimental study of a self-centering variable damping energy dissipation brace. Eng. Struct. 160, 270–280. doi:10.1016/j.engstruct.2018.01.051
Yang, B., Sun, S., Deng, L., Jin, T., Li, W., and Li, H. (2019). Vibration control of a tunnel boring machine using adaptive magnetorheological damper. Smart Mater. Struct. 28 (11), 1–14. doi:10.1088/1361-665X/ab41a4
Yang, J., and Chen, S. (2019). Design of a drum type wedge clearance magnetorheological transmission device. Mach. Tool Hydraul. 47 (15), 105–110. doi:10.3969/j.issn.1001-3881.2019.15.022
Yin, X., Guo, S., and Song, Y. (2018). Magnetorheological fluids actuated haptic-based teleoperated catheter operating system. Micromachines 9 (9), 1–20. doi:10.3390/mi9090465
Yoon, D.-S., Park, Y.-J., and Choi, S.-B. (2019). An eddy current effect on the response time of a magnetorheological damper: analysis and experimental validation. Mech. Syst. Signal Process. 127, 136–158. doi:10.1016/j.ymssp.2019.02.058
Yoon, D. S., Kim, G. W., and Choi, S. B. (2020). Response time of magnetorheological dampers to current inputs in a semi-active suspension system modeling, control and sensitivity analysis. Mech. Syst. Signal Process. 146, 1–21. doi:10.1016/j.ymssp.2020.106999
Yoon, J.-Y., Hong, S.-W., Park, Y.-J., Kim, S.-H., Kim, G.-W., and Choi, S.-B. (2020). Tunable Young's moduli of soft composites fabricated from magnetorheological materials containing microsized iron particles. Materials 13 (15), 1–16. doi:10.3390/ma13153378
Yuan, X. J., Tian, T. Y., and Ling, H. T. (2019). A review on structural development of magnetorheological fluid damper. Shock Vib. 2019, 1–34. doi:10.1155/2019/1498962
Zahedi, A., Zhang, B., Yi, A., and Zhang, D. (2020). A soft exoskeleton for tremor suppression equipped with flexible semiactive actuator. Soft Robot. 1–16. doi:10.1089/soro.2019.0194
Zareie, S., Alam, M. S., Seethaler, R. J., and Zabihollah, A. (2019). Effect of shape memory alloy-magnetorheological fluid-based structural control system on the marine structure using nonlinear time-history analysis. Appl. Ocean Res. 91, 1–9. doi:10.1016/j.apor.2019.05.021
Zareie, S., Alam, M. S., Seethaler, R. J., and Zabihollah, A. (2020). Stability control of a novel frame integrated with an SMA-MRF control system for marine structural applications based on the frequency analysis. Appl. Ocean Res. 97, 1–9. doi:10.1016/j.apor.2020.102091
Zareie, S., and Zabihollah, A. (2020). A semi-active SMA-MRF structural stability element for seismic control in marine structures. Appl. Ocean Res. 100, 1–9. doi:10.1016/j.apor.2020.102161
Zhang, D., Yuan, H., and Cao, Z. C. (2020). Environmental adaptive control of a snake-like robot with variable stiffness actuators. IEEE/CAA J. Autom. Sinica 7 (3), 745–751. doi:10.1109/JAS.2020.1003144
Zhang, J. L., Lu, S. B., and Yu, Y. W. (2019). Design optimization and experiment of a disc-type MR device considering the centrifugal effect and plug flow region. Smart Mater. Struct. 28 (8), 1–14. doi:10.1088/1361-665X/ab2b4c
Zhang, L., Wang, W., Shi, Y., Chu, Y., and Ming, X. (2019). A new variable stiffness actuator and its control method. Ind. Robot Int. J Robot. Res. Appl. 46, 553–560. doi:10.1108/IR-05-2018-0107
Zhang, X. J., Yang, Y., Sun, S. L., He, G. J., and Li, Z. H. (2020). Methodology on a novel magnetorheological valve controlled damper synthesis design. Smart Mater. Struct. 29 (4), 1–11. doi:10.1088/1361-665X/ab72e9
Zhao, D., Zhao, J. B., Zhao, Z. H., Liu, Y., Liu, S. G., and Wang, S. H. (2020). Design and experimental study of the porous foam metal magnetorheological fluid damper based on built-in multi-pole magnetic core. J. Intell. Mater. Syst. Struct. 31 (5), 687–703. doi:10.1177/1045389X19898249
Zheng, J., Chen, S., Wu, R., and Chen, C. (2020). The induced field of magnetized wall on the static normal force of magnetorheological fluids. J. Magn. Magn. Mater. 504, 1–8. doi:10.1016/j.jmmm.2020.166652
Zhong, W.-M., Zhu, A.-D., Bai, X.-X. F., Wereley, N. M., and Zhang, N. (2020). Integrated shock absorber with both tunable inertance and damping. Front. Mater. 7, 1–14. doi:10.3389/fmats.2020.00204
Zhou, H., Zhao, W., Zhang, H., Wang, Y., Wu, X., and Sun, Z. (2020). Magnetorheological seal: a review. J. Appl. Electromagn. Mech. 62 (2), 763–786. doi:10.3233/JAE-190082
Zhou, Y., and Liu, L. (2020). “A multifunctional ankle foot orthosis utilizing a magnetorheological actuator,” in 2nd international conference on advanced nanomaterials and nanodevices, Shanghai, China, October 23–25, 2019 (IOP Conference Series-Materials Science and Engineering). doi:10.1088/1757-899X/813/1/012001
Zhu, S. X., and Geng, F. (2018). The structure design of a new magnetorhelogical brake. Hydraul. Pneum. Seals 9, 83–88. doi:10.1088/1361-665X/ab515f
Keywords: magnetorheological fluid, magnetorheological fluid-based devices, structural configuration, magnetorheological fluid brakes, magnetorheological fluid clutch, magnetorheological fluid damper, magnetorheological medical devices
Citation: Hua D, Liu X, Li Z, Fracz P, Hnydiuk-Stefan A and Li Z (2021) A Review on Structural Configurations of Magnetorheological Fluid Based Devices Reported in 2018–2020. Front. Mater. 8:640102. doi: 10.3389/fmats.2021.640102
Received: 10 December 2020; Accepted: 19 January 2021;
Published: 25 March 2021.
Edited by:
Yancheng Li, University of Technology Sydney, AustraliaReviewed by:
Phu Xuan Do, Vietnamese-German University, VietnamCopyright © 2021 Hua, Liu, Li, Fracz, Hnydiuk-Stefan and Li. This is an open-access article distributed under the terms of the Creative Commons Attribution License (CC BY). The use, distribution or reproduction in other forums is permitted, provided the original author(s) and the copyright owner(s) are credited and that the original publication in this journal is cited, in accordance with accepted academic practice. No use, distribution or reproduction is permitted which does not comply with these terms.
*Correspondence: Xinhua Liu, bGl1eGluaHVhQGN1bXQuZWR1LmNu; Zhixiong Li, emhpeGlvbmcubGlAeW9uc2VpLmFjLmty
Disclaimer: All claims expressed in this article are solely those of the authors and do not necessarily represent those of their affiliated organizations, or those of the publisher, the editors and the reviewers. Any product that may be evaluated in this article or claim that may be made by its manufacturer is not guaranteed or endorsed by the publisher.
Research integrity at Frontiers
Learn more about the work of our research integrity team to safeguard the quality of each article we publish.