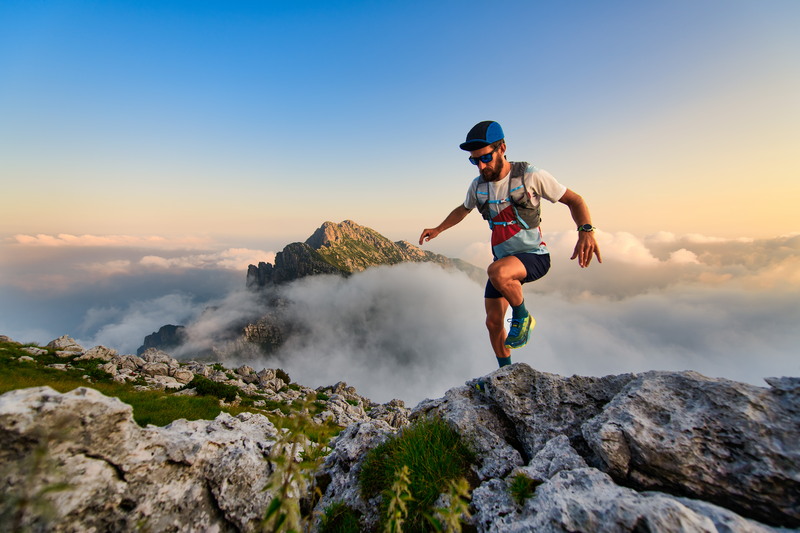
95% of researchers rate our articles as excellent or good
Learn more about the work of our research integrity team to safeguard the quality of each article we publish.
Find out more
ORIGINAL RESEARCH article
Front. Mater. , 20 April 2021
Sec. Structural Materials
Volume 8 - 2021 | https://doi.org/10.3389/fmats.2021.634336
This article is part of the Research Topic Development and Application of Bituminous Materials for Civil Infrastructures View all 20 articles
In order to understand the influence of the vibration mixing method on the performance of cement-stabilized aggregate mixture (CSAM), in this study, an unconfined compressive strength test, drying shrinkage test and the influence of gradation characteristics on compressive strength were used to systematically analyze the performance of CSAM based on vibration mixing. At the same time, the influence mechanism of vibration mixing on the interface transition zone of cement aggregate was analyzed by use of a scanning electron microscope (SEM), and the influence of the mixing method on cement dispersion uniformity was studied by the ethylene diamine tetraacetic acid (EDTA) titration method. The results show that 7 days of unconfined compressive strength and crack resistance of the CSAM with vibration mixing is better than those of the ordinary mixing, and the aggregate grade has a great influence on the compressive strength of the CSAM. Vibration mixing can improve the micro-water-cement ratio uniformity of CSAM and significantly improve the bonding condition of the interface transition zone between cement paste and aggregate, thus enhancing the structural compactness of CSAM. The dispersion uniformity of cement under the vibration mixing is better than that of ordinary mixing.
The semi-rigid base has the characteristics of high strength, excellent stability and high economical efficiency, and since the 1980s, it has therefore become the most widely used grass-roots road construction in China. However, the semi-rigid base has the disadvantage of easy cracking. At the same time, with the rapid increase in heavy load and overload vehicles, it also has poor durability and cracks. The main reason for these issues is that the semi-rigid base material is uneven and divided. Cement-stabilized aggregate mixture (CSAM) is a typical semi-rigid base material, which is a kind of heterogeneous material with low cement dosage. It is easily causes segregation, crushing, loosening and other defects in the mixing, transportation, paving and rolling stages, but improving the uniformity of the mixture can solve these defects to a certain extent. Researches on the impact of mixing methods on the mixture found that vibration mixing can make up for the defects of ordinary mixing, fully tap the potential of materials, reduce the amount of cement, enhance the strength of the mixture and reduce cracking.
For the research on the CSAM with vibration mixing (Dong et al., 2019), analyzed the influence of vibration on the mixing process of CSAM by testing the mixing power curve of different mixing methods and carried out a comparative test of vibration mixing and ordinary mixing. The results show that the vibration mixing improves the homogeneity of CSAM, and the microstructure is uniform and dense, which leads to high compressive strength and good dry shrinkage. Zhang et al. (2018) established the equivalent relationship between the modified laboratory vibration mixing and the site vibration mixing through a series of tests. It was found that the design result of laboratory CSAM vibration mixing was better than that of site CSAM vibration mixing, and the unconfined compressive strength of CSAM was greater than that of the mixture mixed by site vibration mixing. Zhao L. J. et al. (2018) carried out the comparative test of vibration mixing and ordinary mixing, and the results showed that under the condition of vibration mixing, the influence of mixing time on the compressive strength of mixture is the greatest, followed by vibration frequency and mixing speed, and the influence of wet mixing time is the least. With the increase in mixing parameters, the compressive strength increases as well, and the coefficient of variation decreases. On the basis of reasonable mixing parameters, the vibration mixing can significantly improve the strength index of the mixture, but with the increase of cement content, the strength improvement rate of CSAM with the vibration mixing decreases.
Chen et al. (2019) analyzed the influence of different design parameters of CSAM with vibration mixing on the mechanical properties of the mixture by using gray correlation theory. The test results show that the most significant design parameter affecting the mechanical properties of CSAM is the cement dosage, followed by dry density, aggregate gradation, compactness and water content. Liang (2018) carried out a freeze-thaw test and dry shrinkage test of CSAM under vibration and ordinary mixing methods, and they found that the frost resistance and crack resistance of the specimens under vibration mixing are better. Zhang and Zhang (2016) found that the appearance of vibration mixing can improve the mixing uniformity of the mixture and ensure the engineering quality at the mixing stage. Liu and Xiong (2018) compared the unconfined compressive strength, splitting strength and dry shrinkage coefficient of CSAM produced by vibration mixing and ordinary mixing with laboratory specimens with core samples of solid engineering. The results show that the unconfined compressive strength of CSAM made by vibration mixing is higher than that of ordinary mixing, and the unconfined compressive strength of laboratory vibration mixing specimens is better than that of site vibration mixing conditions. Duan et al. (2020) prepared skeleton-dense CSAM specimens by static pressure and vibration compaction and pre-cracked at the early stage of maintenance. The development laws of the pre-splitting degree, mechanics, dry shrinkage and crack resistance of CSAM after early pre-cracking treatment under different molding methods were studied. The results indicate that the pre-splitting degree of the specimen increases first and then decreases under the action of vibration. Before reaching the maximum pre-splitting degree, the pre-splitting degree of the static pressure specimen is higher than that of the vibration specimen; however, under the same pre-splitting parameters, the self-healing performance of the vibration specimen is better than that of the static pressure specimen, and the tensile strength index of the static pressure specimen is the worst. After the pre-splitting treatment, the dry shrinkage of the vibration and static pressure specimens can be reduced by 35.8 and 35.3%, respectively. After pre cracking treatment, the crack resistance of the specimens increases by 2–3 times. Zheng et al. (2018) used a fiber tensile test, splitting tensile test and bending test to analyze the influence of the two mixing methods on the mechanical properties of reinforcement, comparing the vibration mixing and the ordinary mixing. The findings show that vibration mixing can effectively improve the fiber distribution in the concrete and increase the fiber density to effectively improve the mechanical properties of steel fiber reinforced concrete. Zhou and Li (2019) compared the difference in compaction standards, mechanical strength, shrinkage characteristics and mineral gradation decay determined by the cement stabilized recycled gravel mixture with the compaction and static pressure method. The compacted moisture content and dry shrinkage determined by the vibration test deformation and gradation decay of minerals were lower, while maximum dry density and mechanical strength were higher. Zhao K. Y. et al. (2018) used two mixing methods for preparing C60 high-strength concrete, using one-step mixing technology and three-step mixing technology to carry out comparative experiments. The study finds that under the two mixing conditions, the viscosity of concrete was significantly reduced, the fluidity and compressive strength improved, and the most suitable mixing methods and mixing processes for C60 high-strength concrete were vibration mixing and three-step mixing.
By searching the existing data, it is found that the existing research on vibration mixing mainly focuses on the impact of vibration mixing on the performance of CSAM, such as compressive strength, dry shrinkage performance, etc., which can provide a reference for the study of this paper. However, the influence of aggregate gradation on the compressive strength of mixture and the influence mechanism of vibration mixing on the interface transition zone of cement aggregate are less involved, so the influence of vibration mixing technology on the performance of CSAM is not fully evaluated. Based on the double horizontal shaft vibration mixer (DT60ZBW), as a test, this paper compared the strength and crack resistance of the mixture, the relationship between the bearing capacity of coarse aggregate and the compressive strength of the mixture under two different mixing methods of vibration mixing and ordinary mixing. Meanwhile, we analyzed the influence mechanism of CSAM with vibration mixing and its influence on cement dispersion uniformity to guide the construction of CSAM, and improving road durability has a guiding role.
In this paper, the Portland cement (P.O 42.5) produced by Hunan Pingtang Nanfang Cement Co., Ltd. was used. The limestone produced in Yueyang was used as the aggregates, and the domestic tap-water was used as the mixing water. All the raw materials met the requirements of the Technical Guidelines for Construction of Highway Roadbases (hereafter Technical Guidelines).
The gradation selected in this paper is shown in Figure 1.
Combined with the actual project and related research results, the cement dosage is determined as 3, 3.5, 4, 4.5, and 5% by using the external mixing method. The optimal moisture content is obtained according to the compaction test, and the results are shown in Figure 2.
A double horizontal shaft vibrating mixer (DT60ZBW) with a nominal capacity of 60L developed by Detong vibration mixing company, Xuchang City, Henan Province, was adopted. DT60ZBW is mainly composed of a mixing driving mechanism, vibration driving mechanism, mixing cylinder, vibration exciter, synchronous device, transmission device, etc. The maximum stirring time was 55 s, the stirring speed was 55 r/min, the stirring blades were 14, and the vibration intensity was 3–5 g. Weigh the mass of aggregate, water and cement required by each test piece, add water to the weighed aggregate for 2 h, add the corresponding cement, and put it into the mixer to mix for 15 s until it is even. When the mixing motor and vibration motor are started at the same time, it is vibration mixing combined with conventional mixing; only starting the mixing motor is ordinary mixing. The equipment is shown in Figure 3.
The unconfined compressive strength test (T 0805-1994) of CSAM was carried out according to Test Methods of Materials Stabilized with Inorganic Highway Engineering JTG E51-2009 (hereinafter, Test Methods). The 7 days unconfined compressive strength was determined to evaluate its ultimate strength under the condition of no lateral pressure. Through the contrast test of different mixing methods, the influence of the mixing method on the compressive strength of CSAM is analyzed.
The maximum nominal particle size of aggregate used in this paper is 26.5 mm. According to the Bailey method, the boundary particle size of coarse and fine aggregate is calculated: 0.22 times the maximum nominal particle size of aggregate is taken as the boundary point of coarse and fine aggregate (5.83 mm). According to the principle of closest particle size of aggregate, 4.75 mm is taken as the boundary particle size of coarse and fine aggregate in which the aggregate above 4.75 mm is coarse aggregate.
The computer-controlled electronic universal testing machine was used to carry out penetration tests on coarse aggregate above 4.75 mm. A total of 12 mm was taken as the standard depth of penetration test, and the penetration load was recorded to study the skeleton bearing capacity of coarse aggregate with different aggregate gradation.
According to the Test Methods, the dry shrinkage test (T 0854-2009) of CSAM was developed. The beam type specimen with the size of 100 mm × 100 mm × 400 mm is formed by the static pressure method, and the compactness was 98%. After 6 h, the specimen is taken out by dismantling the mold and placed in the standard curing room for 7 days. When the temperature and humidity in the drying shrinkage test chamber reach 20 ± 1°C and 60 ± 5%, put the beam specimen and shrinkage meter into the drying shrinkage test chamber for drying shrinkage test, read the dial indicator at the same time every day, and record the length change of the specimen. The moisture change of the same specimen is determined by measuring the mass of the specimen, and the drying shrinkage coefficient of the specimen is calculated according to the drying shrinkage strain and water loss rate. At the end of the 29 days test period, the test pieces are put into the oven, dried to constant weight, and the standard length of the test pieces is measured. Through the contrast test of different mixing methods, the influence of mixing methods on dry shrinkage performance of CSAM is analyzed.
On the basis of the ethylene diamine tetraacetic acid (EDTA) titration method (T 0809-2009) in the Test Methods, four groups of parallel tests are carried out for each mixture (different mixing methods and cement dosage). In each parallel test, four different areas of the mixture in the mixing bin are selected to carry out the tests, and the ratio is that between the standard deviation and the average of the measured cement dosage of different parts of the mixture in the mixing bin. The coefficient of variation is obtained, and the averages of the four groups of the parallel tests are taken to evaluate the dispersion uniformity of CSAM under different mixing methods.
The S-3000N produced by Hitachi company of Japan was used to scan the specimens prepared by different mixing methods. The scanning area is divided into cement matrix, aggregate surface and aggregate cement interface to evaluate the effect of different agitation methods on cement particle distribution and gel structure, pore saturation of aggregate surface and cracking of mixture.
The mechanism of the experimental scheme is seen in Table 1.
By changing the mixing method, cement dosage and aggregate gradation, the unconfined compressive strength of CSAM was tested. According to the test results of four parallel groups, the average value and the results are shown in Figure 4.
Figure 4. 7 days Unconfined compressive strength of cement-stabilized aggregate mixture (CSAM) with different mixing methods.
The 7-day unconfined compressive strength of CSAM with vibration mixing is better than that of CSAM with ordinary mixing. It is because vibration can break up the water film wrapped on the outer surface of the cement mass, and increase the dispersion and hydration of cement particles in the mixture. On the other hand, vibration mixing can improve the movement speed of aggregate and the collision frequency between aggregate particles, which is conducive to the coating of cement and aggregate particles, so as to enhance the bond between cement and aggregate, and enhance the strength of the interface transition zone (Feng and Wang, 2009; Zhao et al., 2015; Wang et al., 2020).
The 7-day unconfined compressive strength of the C-B-3-1 mixture is higher than that of the C-B-1-1 mixture under the two mixing methods. The C-B-3-1 mixture belongs to the skeleton dense structure, and the degree of intercalation between aggregates is more obvious. While the C-B-1-1 mixture belongs to the suspension dense structure, the degree of intercalation of aggregates is insufficient, and the compressive strength is mainly provided by the bonding of cement hydration products (Wang, 2017), resulting in the above results at the same cement dosage.
The 7-day unconfined compressive strength of the C-B-3-1 and C-B-1-1 mixture increased linearly with the cement dosage under the two mixing methods, and the correlation coefficients were all over 0.97 (Table 2), indicating a good correlation. This is due to the increase of cement dosage, which shows that the effective cement particles participating in hydration reaction in the mixture increase, and the content of viscous hydrated calcium silicate increases, which further improves the strength of the interface transition zone; on the macro level, the compressive strength of the mixture increases (Han and Li, 2016).
Table 2. Linear regression coefficient between 7 days unconfined compressive strength and cement dosage with a different mixing method.
Four kinds of aggregate gradation are selected: C-B-3-1, C-B-3-2, C-B-3-3, and C-B-3-4. In order to eliminate the influence of cement dosage difference on the compressive strength of the mixture, the cement dosage was set at 4%. The 7-day unconfined compressive strength results of four kinds of coarse aggregate penetration are tested and their corresponding mixtures under different mixing methods are shown in Figure 5.
Figure 5. The relationship between penetration load of coarse aggregate and compressive strength of CSAM.
There is a good linear relationship between the penetration load of coarse aggregate and the 7-day unconfined compressive strength of CSAM. The correlation coefficient between the penetration load of coarse aggregate and the compressive strength of CSAM with ordinary mixing is 0.8417, and that of CSAM with vibrating mixing is 0.7835. Due to the increase of penetration load of coarse aggregate and the increase of aggregate resistance to deformation under external force, resulting in the increase of compressive strength of CSAM.
The drying shrinkage test results of C-B-3-1 and C-B-1-1 mixtures with ordinary mixing and vibration mixing are shown in Figures 6, 7.
Figure 6. Cumulative dry shrinkage of two mixtures under different mixing methods. (A) C-B-3-1 and (B) C-B-1-1.
The cumulative water loss rate and the cumulative dry shrinkage both show the law of gentle in the initial stage and rapid increase in the later stage. When the cumulative water loss rate is the same, the common mixing mixture has a greater cumulative dry shrinkage.
Under the same cement dosage, the dry shrinkage performance of the CSAM with vibration mixing is better than that of the ordinary mixing. The vibration mixing ensures the water and cement in the CSAM are more evenly distributed, and the bonding part is denser and uniform; meanwhile, the strength is improved, the crack resistance is enhanced, and the corresponding dry shrinkage coefficient is reduced. After the mixture is evenly mixed, the large pores decrease, and the small pores increase; this enhances the water holding capacity, reduces the cracking caused by water evaporation and reduces the drying shrinkage coefficient accordingly. The hydration products are evenly distributed among the aggregate pores, making the mixture specimen more uniform and dense, improving its overall coordination deformation ability and thus reducing the overall dry shrinkage strain (Bai, 2013).
Under the same dosage and mixing mode, the dry shrinkage performance of the C-B-3-1 mixture is better than that of the C-B-1-1 mixture. This is because the C-B-3-1 mixture belongs to the skeleton dense structure, and the C-B-1-1 belongs to the suspended dense structure. In the dense skeleton mixture, the coarse aggregate forms a skeleton, which contains fine aggregate and cement. Therefore, the volume change can occur inside the coarse aggregate, which will weaken the overall volume change of the mixture (Xue, 2016).
Vibration mixing can improve the crack resistance of the mixture by reducing the cement dosage. The dry shrinkage coefficient of the CSAM of 3% of the cement in vibration mixing is smaller than that of the ordinary mixing. According to the strength test results, the unconfined compressive strength of the mixture with 3% cement and 3.5% of the cement for 7days meets the specification requirements. This shows that the cracking problem of mixture can be reduced significantly when the cement content is reduced and when the base strength is guaranteed under the same grading condition.
According to the EDTA titration method in the test procedures, the cement dosage of fresh CSAM in the mixing bin under different mixing methods was tested. The cement dispersion uniformity of the C-B-3-1 and C-B-1-1 mixtures with vibration mixing is better than that of ordinary mixing. Figure 8 shows that the variation coefficient of cement dose of vibration mixing is basically smaller than that of ordinary mixing. The average variation coefficient of cement dosage with the 3 and 3.5% C-B-3-1 mixtures under ordinary mixing is 1.4 and 1.7% higher than that of vibration mixing, respectively. The average coefficient of cement dosage with the 3.5 and 4% C-B-1-1 mixtures under vibration mixing decreased by 3.9 and 3.5%, respectively, compared with the ordinary mixing. It should be that the high-frequency vibration wave emitted by the vibration source at the mixing shaft will disperse the agglomerated cement particles evenly in the mixture to improve the overall uniformity of the mixture.
Figure 8. Coefficient of variation of CSAM under different mixing methods. (A) C-B-3-1 and (B) C-B-1-1.
The C-B-1-1, C-B-1-2, and C-B-1-3 mixtures with 4.0% cement dosages at a curing age of 28 days under different mixing methods were cut into samples of 5 mm by a precision cutting machine and polished by sandpaper from coarse to fine to obtain a smooth plane to be measured and sealed for preservation. The interface transition zone was found by an electron microscope at 100 times magnification, and then the cracks and cement hydration products were observed at 1,000 times magnification. The scanning area was divided into cement matrix, aggregate surface, aggregate and cement interface. During scanning, the more comprehensive and typical areas were taken as far as possible to make one picture include three expected contents. The scanning results are shown in Figures 9–11.
Figure 9. Scanning electron microscope (SEM) picture of C-B-1-3 (1000×). (A) C-B-1-3 with ordinary mixing and (B) C-B-1-3 with vibration mixing.
Figure 10. Scanning electron microscope picture of C-B-1-1 (1000×). (A) C-B-1-1 with ordinary mixing and (B) C-B-1-1 with vibration mixing.
Figure 11. Scanning electron microscope picture of C-B-1-2 (1000×). (A) C-B-1-2 with ordinary mixing and (B) C-B-1-2 with vibration mixing.
In Figure 9A, the cement matrix is similar to the cluster formed by spherical particles, and there are some small pores and gullies between the cement particles. This indicates that although cement hydration has reached a certain degree, there may be hydrated particles inside the spherical particles. In Figure 9B, the particles of cement hydration products in the cement matrix are more delicate, and some are even flocculent and evenly distributed. The results show that the hydration of cement in CSAM is more sufficient under vibration mixing. Cement and free water become loose under high-frequency vibration with vibration mixing, which means the cement comes into contact with free water more fully, there is less cement agglomeration, and cement hydration products are distributed more evenly and widely.
In Figure 10A, there are a large number of small pores in the joint of aggregate and cement and cement matrix under ordinary mixing. In Figure 10B, there is an obvious crack in the interface transition zone of CSAM with vibration mixing, but the transition areas at other positions are in close contact, which shows that the probability and degree of internal defects in vibration mixing are lower than in ordinary mixing, and the effect of vibration mixing is better. This is due to the insufficient contact between the cement and free water in the mixture with ordinary mixing, and the free water wrapped in the dry cement cannot contact with the cement inside the matrix, resulting in insufficient hydration degree of cement, voids in the transition zone and agglomeration in the cement matrix. In Figure 11A, there is an obvious boundary between the interface transition zone of aggregate and cement, meanwhile, there are obvious gaps between the aggregates. In Figure 11B, the cement matrix and aggregate in the interface transition zone of CSAM with vibration mixing are closely combined with the aggregate, and there are small gullies on the surface, but no obvious cracks and pores are found. This illustrates that the internal structure of vibration is more compact than that of ordinary mixing.
This can be attributed to the fact that the aggregate and cement particles in the CSAM are close to each other under vibration, the gap between particles is reduced, and the contact between particles and free water is enhanced, which makes the cement hydration more sufficient and the overall structure more compact.
In this paper, the compressive strength and dry shrinkage of cement are prepared by vibration mixing and ordinary mixing, the relationship between the bearing capacity of coarse aggregate and compressive strength of mixture is compared, and the influence of vibration mixing on the interface transition zone of cement aggregate is analyzed. The main conclusions are as follows:
(1) The 7-day unconfined compressive strength of CSAM with vibration mixing is better than that of CSAM with ordinary mixing, and the enhancement rate of mixture strength by vibration mixing shows a decreasing trend with the increase of cement dosage. The 7-day unconfined compressive strength of the C-B-3-1 mixture is higher than that of the C-B-1-1 mixture with ordinary mixing, and the strength difference presents an upward trend with the increase of cement dosage.
(2) Under the same cement dosage, the dry shrinkage performance of CSMA with vibration mixing is better than that of ordinary mixing. The cumulative water loss rate of two kinds of aggregate gradation changes little with the mixing method, while the cumulative dry shrinkage increases with the increase of water loss rate. Under the same cement dosage and mixing method, the dry shrinkage performance of the C-B-3-1 mixture is better than that of the C-B-1-1 mixture.
(3) Vibration mixing can significantly improve the bonding condition of the interface transition zone between cement paste and aggregate. The cement matrix and aggregate in the interface transition zone are closely combined, and there are small gullies on the surface, but no obvious cracks and pores are found.
The datasets presented in this study can be found in online repositories. The names of the repository/repositories and accession number(s) can be found in the article/supplementary material.
All authors listed have made a substantial, direct, and intellectual contribution to the work and approved it for publication.
This research was financially supported by the National Natural Science Foundation of China (Grant Nos. 51878075 and 52008045), Guangxi Natural Science Foundation (2018GXNSFAA294146), Open Fund of Hunan International Scientific and Technological Innovation Cooperation Base of Advanced Construction and Maintenance Technology of Highway (Changsha University of Science and Technology, kfj190801), The Natural Science Foundation of Hunan Province (2020JJ5595), Guangxi Major Science and Technology Project (Gui Ke AA18242032, AB19245019, and AB17292035), and Scientific Research Project of Hunan Education Department (19C0067).
JX was employed by the company Guangxi Transportation Science and Technology Group Co., Ltd., Nanning, China.
The remaining authors declare that the research was conducted in the absence of any commercial or financial relationships that could be construed as a potential conflict of interest.
Bai, X. (2013). Research on Anti-cracking Ability Evaluation of Cement Stabilized Crushed Stone Base. dissertation/master’s thesis, Chongqing Jiaotong University, Chongqing, CQ.
Chen, K., Liang, S., Zhang, H. T., and Yang, H. S. (2019). Analyses on the influence of parameters vibration-stirred water-stabilized crushed stone on mechanical properties of based on grey correlation analysis method. Sci. Technol. Eng. 19, 321–324.
Dong, W., Xie, S. Y., Zhao, L. J., and Feng, Z. X. (2019). Influence of vibration on mixing process of cement stabilized macadam and its performance. China J. Highway Transp. 32, 181–190.
Duan, K. R., Gao, Y. L., Zhou, W. J., Pei, G. P., and He, B. (2020). Mechanical properties of pre-cracked cement-stabilized crushed stone molded by dynamic and static methods. Mater. Rep. 34, 10068–10075.
Feng, Z. X., and Wang, W. Z. (2009). Reinforcement methods of concrete interfacial bond strength. J. Chang’ Univ. 29, 91–94.
Han, H. M., and Li, J. (2016). Experimental study on strength properties of cement stabilized aggregate base. Road Mach. Constr. Mech. 33, 41–45.
Liang, S. (2018). Application Research of Vibratory Mixing Technology in Cement-stabilized Graded Aggregate. dissertation/master’s thesis, Northeast Forestry University, Harbin, HLJ.
Liu, Q., and Xiong, Y. (2018). Pavement performance of cement stabilized macadam through vibrating mixing. Road Mach. Constr. Mech. 35, 74–77.
Wang, J. W. (2017). Research on Expansion Cracking of Asphalt Pavement by Cement Stabilized Macadam Base. dissertation/master’s thesis, Chang’ an University, Xi’an, SX.
Wang, Y. L., Zhang, J. B., Wang, X. T., and Zhang, Z. (2020). Laboratory investigation on the performance of cement stabilized recycled aggregate with the vibration mixing process. Math. Probl. Eng. 2020, 1–11. doi: 10.1155/2020/6625370
Xue, S. Q. (2016). Vibratory Mixing Mechanism and Experimental Study on Improving the Cement Stabilized Macadam Performance. dissertation/master’s thesis, Chang’ an University, Xi’an, SX.
Zhang, H. T., Liang, S., Yang, H. S., and Yu, L. Z. (2018). Study on performance of cement-stabilized crushed stone based on indoor vibration mix. China J. Highway Transp. 31, 58–65.
Zhang, Z. X., and Zhang, L. Q. (2016). Application of vibratory mixing technology in construction of cement-stabilized base course. Road Mach. Constr. Mech. 33, 31–36.
Zhao, K. Y., Zhao, L. J., Liu, S. S., and Hou, J. R. (2018). Effect of three-step mixing technology based on vibratory mixing on properties of high-strength concrete. IOP Conf. Ser. Mater. Sci. Eng. 542:1. doi: 10.1088/1757-899X/542/1/012003
Zhao, L. J., Jiang, W. Z., Hou, J. R., Feng, Z. X., and Xue, S. Q. (2018). Influence of mixing methods on performance of compressive strength for cement stabilized macadam mixture. China J. Highway Transp. 31, 151–158.
Zhao, W., Wang, B., Zhao, L. J., and Feng, Z. X. (2015). Improving concrete strength based on the mixing process. J. Chang’ Univ. 35, 148–153.
Zheng, Y. X., Wu, X. L., He, G. X., Shang, Q., Xu, J., and Sun, Y. (2018). Mechanical properties of steel fiber-reinforced concrete by vibratory mixing technology. Adv. Civil Eng. 2018:9025715. doi: 10.1155/2018/9025715
Keywords: cement-stabilized aggregate mixture, compressive strength, dry shrinkage, influence mechanism, vibration mixing
Citation: Li P, Wei D, Zhang D, Xiong J and Xu S (2021) Study on the Properties and Mechanisms of a Cement-Stabilized Aggregate Mixture With Vibration Mixing. Front. Mater. 8:634336. doi: 10.3389/fmats.2021.634336
Received: 27 November 2020; Accepted: 16 March 2021;
Published: 20 April 2021.
Edited by:
Hui Yao, Beijing University of Technology, ChinaReviewed by:
Yue Li, Beijing University of Technology, ChinaCopyright © 2021 Li, Wei, Zhang, Xiong and Xu. This is an open-access article distributed under the terms of the Creative Commons Attribution License (CC BY). The use, distribution or reproduction in other forums is permitted, provided the original author(s) and the copyright owner(s) are credited and that the original publication in this journal is cited, in accordance with accepted academic practice. No use, distribution or reproduction is permitted which does not comply with these terms.
*Correspondence: Dongmei Zhang, ZG16aGFuZ0Bjc3VzdC5lZHUuY24=
Disclaimer: All claims expressed in this article are solely those of the authors and do not necessarily represent those of their affiliated organizations, or those of the publisher, the editors and the reviewers. Any product that may be evaluated in this article or claim that may be made by its manufacturer is not guaranteed or endorsed by the publisher.
Research integrity at Frontiers
Learn more about the work of our research integrity team to safeguard the quality of each article we publish.