- 1Department of Aerospace Engineering, Universiti Putra Malaysia, Seri Kembangan, Malaysia
- 2Department of Industrial Automation, Universiti Kuala Lumpur, Kuala Lumpur, Malaysia
- 3Laboratory of Biocomposite Technology, Institute of Tropical Forestry and Forest Products (INTROP), Universiti Putra Malaysia, Seri Kembangan, Malaysia
- 4Department of Electrical and Electronics Engineering, Universiti Putra Malaysia, Seri Kembangan, Malaysia
- 5Department of Mechanical Engineering, Universiti Teknologi Petronas, Tronoh, Malaysia
The demand for composite fiber material is significantly high due to its excellent mechanical properties and its use in various industries. Recently, with the increasing awareness of environmental issues, researchers are now focusing more on eco-friendly and green materials. A biocomposite offers a good balance of strength and stiffness ratio, bending and membrane mechanical properties, balanced thermal distortion stability, reduced weight and cost, improved fatigue resistance, reduced notch sensitivity, and, comparatively, better performance than synthetic composites. Yet, due to the complex anisotropy of the composite material, the inspection and detection of inner defects become a challenge. Long-pulse thermography is one of the non-destructive evaluations (NDEs) used to detect defects in composite materials. However, very limited research has been carried out on the usage of a low-resolution infrared camera to perform defect or damage inspection on flax composite laminates. In this paper, an experimental setup of a long pulse thermography system using low-resolution infrared camera was performed on flax bio-composite to identify impact and lightning damage. The result highlights that with control parameters, a low-resolution infrared camera has the capability to capture the lightning and impact defects of flax biocomposites using the long-pulse thermography system. An image processing method is then applied to the defect to improve the quality of defect detection and reduce background noise.
Introduction
Natural fibers like jute, flax, and kenaf are resources from nature and cannot harm nature compared to synthetic fibers. Natural fibers are much cheaper than synthetic fiber, have good specific strength properties and less density, are eco-friendly (Amir et al., 2018), have good acoustic insulation (Dicker et al., 2014), are lightweight (Dittenber and Gangarao, 2012), and can be extracted using a simple process (Arockiam et al., 2018). Much research has been performed on studying the potential of natural fiber in engineering. Asim et al. (2018) discussed specifically the capability of natural fiber/biomass filler–reinforced polymer composites in aerospace applications, and Naveen et al. (2019) discussed the selection of natural fiber for hybrid Kevlar and for personal body armor application.
Flax (Linum usitatissimum), also known as common flax or linseed, is a member of the genus Linum in the family Linaceae. It is a food and fiber crop cultivated in cooler regions of the world. The main components of flax that determine the physical properties in different quantities are wax, pectin and lignin, cellulose, and hemicellulose. The percentage of each component varied according to different researchers (Yan et al., 2014). Cellulose covers an average of 62–72% of the properties of this material. Various of mechanical test and analysis have been conducted on flax fiber to evaluate and explore the strength of this material. According to Ramesh (2019), 0.4 g of single flax could produce 20,000 fibers, which makes the flax fiber one among the strongest and stiffest plant fibers. Along the axis of the flax fiber, the stiffness (E) of the flax fiber ranges from 45 to 55 GPa, and the strength is at a range of 800–1,000 MPa (Lefeuvre et al., 2014). The flax fiber has good mechanical properties and wide accessibility, and is cheap, environmentally friendly, and easily manageable (Dittenber and Gangarao, 2012; Sanjay and Siengchin, 2021). The flax fiber also shows better energy absorption compared to glass fiber at high strain rate (Kim et al., 2014), and it has lower density compared to glass fiber (Ramnath et al., 2014). Modification of flax material such as alkalization, will reduce the absorption of environmental moisture, and hybridization with other materials could improve the mechanical properties (Dhakal et al., 2013). Hence, with the advantages, the flax fiber has the potential to become a reinforcement fiber for engineering applications. However, due to their complex anisotropy of the composite material, the inspection and detection of inner defects during the operation become a challenge.
Impact and Lightning Defects in Composite Structure Material
It is crucial to understand the mechanical properties and strength of natural fibers due to the demands in many industries. The endurance of the material during their service life includes the capability to withstand impact and environmental situation such lightning also need to be analyzed. Low-velocity impact damage often begins with surface defects or internal delamination (Kroworz and Katunin, 2018). This includes matrix damage such as fiber–matrix interface damage and matrix cracking (Ravandi et al., 2017). In an application such as aircraft, small debris on the runway could cause bigger damages such as delamination or fiber and matrix breakage (Nur et al., 2017). Studies on hybridization of flax/glass has shown improve performance on absorbing impact (Barouni and Dhakal, 2019).
For outdoor applications that use composite materials such as aircraft, cars, and wind turbine body structures, the materials are highly exposed to lightning strikes. According to research by Larsson (2002), an airplane is usually struck by lightning once a year. In 7 years of data collected by Peesapati et al. (2011), it is shown that 739 wind turbines had been struck by lightning, which causes severe damages to the turbine blades and frame. Hence, studies on lightning strikes on composite materials became highly important. Studies on lightning strike assessment on composite and biocomposite wind turbines were performed using ultrasonic-guided wave and visual inspection methods (Mat Daud et al., 2018) to evaluate lightning strike defects on graphite/epoxy composite laminate (Hirano et al., 2010).
Non-destructive evaluation (NDE) has been widely used to evaluate damage on composite material structure. Numerous methods have been suggested to detect damage for different materials either composite, hybrid, or bio composite. However, it remains as a challenge due to the anisotropy of materials where each material has difference mechanical properties. Thermography method has several advantages compared to other NDE methods, as it does not require pairs to do the inspection, a non-contact NDE and large inspection area (Brandão et al., 2016). Moreover, thermography monitoring system could be fully optimized in a manufacturing system when integrated with a robotic system (Khodayar et al., 2018). Thermography has performed as one of NDE techniques in research to detect and evaluate failure material on carbon reinforcement fiber (CFRP) to detect foreign inclusions and delamination or impact defect (Ekanayake et al., 2018; Grys, 2018; Saeed et al., 2018) or defect on bio composite material such as basalt fiber woven composites, aramid (Diharjo et al., 2013; Kalyanavalli et al., 2018) and kenaf (Bendada et al., 2013) had been done. Furthermore, Ultrasound NDE toolshave also been used to evaluate lightning damage on composite fibers and CFRP composite (Hirano et al., 2010), on Carbon Nanotube (Logakis and Skordos, 2012), and flax reinforcement fiber (Mat Daud et al., 2018). Yet only a few numbers of research had been done using thermography as the NDE tool to evaluate lightning defects. Roche et al. (2018) utilized thermography system to monitor lightning defect of carbon/epoxy composite.
Active infrared thermography (IRT) utilized an external excitation source to generate heat in the material under inspection. Several established active IRT techniques are lock-in, flash or short-pulse (PT), and long-pulse thermography (LPT). A new extension of the thermography technique, namely, pulse-compression thermography (PuCT) was introduced using a form of heating simulation code such as Barker code and Golay code in the thermography system to detect steel and composite defects. This technique has been proposed by researchers for detecting the subsurface defect on the CFRP (Ghali et al., 2011; Silipigni et al., 2017; Rani and Mulaveesala, 2020). Research shows that there is an improvement of signal-to-noise ratio (SNR) of defect detection on CFRP composites using the PuCT method. One of the limitations of PuCT is the sideslope that influences the impulse response reconstruction (Wu et al., 2019). Moreover, very little research has been carried out on the impact defect on natural composites such as the flax composite. Among IRT techniques, LPT has several advantages such as fast setup with a simple excitation source and lower cost (Pickering et al., 2013).
The resolution of an infrared camera depends on the total pixels. Resolution can be separated into low (resolution is less and equal to 160 × 120 or 19,600 pixels), medium (resolution at 320 × 240 pixels), and high resolution (640 × 480 pixels). However, most research utilized a high-resolution infrared camera for the thermography system. Table 1 shows several studies wherein materials are tested using a high-resolution camera to monitor natural and synthetic composite materials. A high-resolution infrared camera is costly especially for commercial and research applications. As an example, a FLIR camera A655sc with 320 × 240 pixels for industrial and research purposes listed in a website will cost about £19,158.00. Therefore, it is a limitation for a small and medium company to set up a thermography system as a monitoring system for composite products.
The detection quality of an infrared camera can be divided into several parameters. These parameters are as follows: excitation source (heating angle, heating duration, and power), infrared camera resolution, electromagnetic spectrum of the camera, material physical and mechanical properties (thickness, emissivity, and thermal conductivity), and surroundings (either indoors or outdoors that cause radiation received by the camera) (Kang et al., 2001; Marinetti and Cesaratto, 2012; Usamentiaga et al., 2014; Balageas et al., 2016).
Heat plays an important role in the thermography system. It is essential to have uniform heat across the surface material to capture defects. In LPT, proper heating duration is required that is enough for the temperature to propagate through the surface of the material and produce a temperature contrast between the defected and the non-defected area which could be seen clearly as the temperature starts to decay. The behavior can be captured using an infrared camera. Heating duration also relies on the thermal property of the material and the thickness of the material (Maldague, 2002). It is important to ensure optimum thermal contrast to detect defects of impact and lightning. The defect area cannot be captured if the heating duration is too low. However, if the heating duration is too long, it could damage the material and cause unwanted reflected radiation that influences the quality of the defect captured.
To set up the LPT system, several equipment are required such as a heat source, an infrared camera, and a computer to record the images. The system could be either in reflex mode or in transmission mode. Research shows that LPT provides better detection compared to several thermography techniques such as eddy current thermography for the CFRP (Pickering et al., 2013; Wang et al., 2019) and delamination defect of the basalt fiber–reinforced composite (Kalyanavalli et al., 2018).
The outcome of this experiment is to evaluate the capability of a low-resolution infrared camera to assess the impact and lightning damage or the defect of the flax composite fiber using the LPT system. Several parameters were controlled such as heating angle, heat source distance, heating duration, and using a close apparatus to improve the detection of defects.
Experimental Methods
Thermography Setup
The system employs a reflex thermography method setup where the sample images are captured from the same side of the heating source. The distance from the infrared camera to the sample is 30 cm. The thermal excitation source consists of two halogen lamps where both were fixed at 30° angle facing the material as shown in Figure 1. The distance between halogen lamps to the sample is 30 cm. A long pulse at a duration of 20–30 s was suggested for this experiment to produce optimum temperature contrast for the flax samples. Two halogen lamps facing the sample at an angle of 30° with rated power of 1kWwere used to produce about 2kWm−2 power density (Wang et al., 2018) for each second of the heating period. Two low-resolution cameras from different companies were selected for the system as shown in Table 2.
The experiment was conducted indoors with control parameters and in a closed apparatus or using designated boxed-shape configurations to obtain an optimum thermal contrast for the detection of impact and lightning defects using a low-resolution infrared camera. A bright color material was used as the internal background color, and an exhaust fan was used to cool down the surrounding after each experiment. All the parameters were controlled to reduce the absorption of heat from the surroundings. The camera was connected to a computer, and the data were saved in an image mode. The design of the thermography system setup is shown in Figure 2.
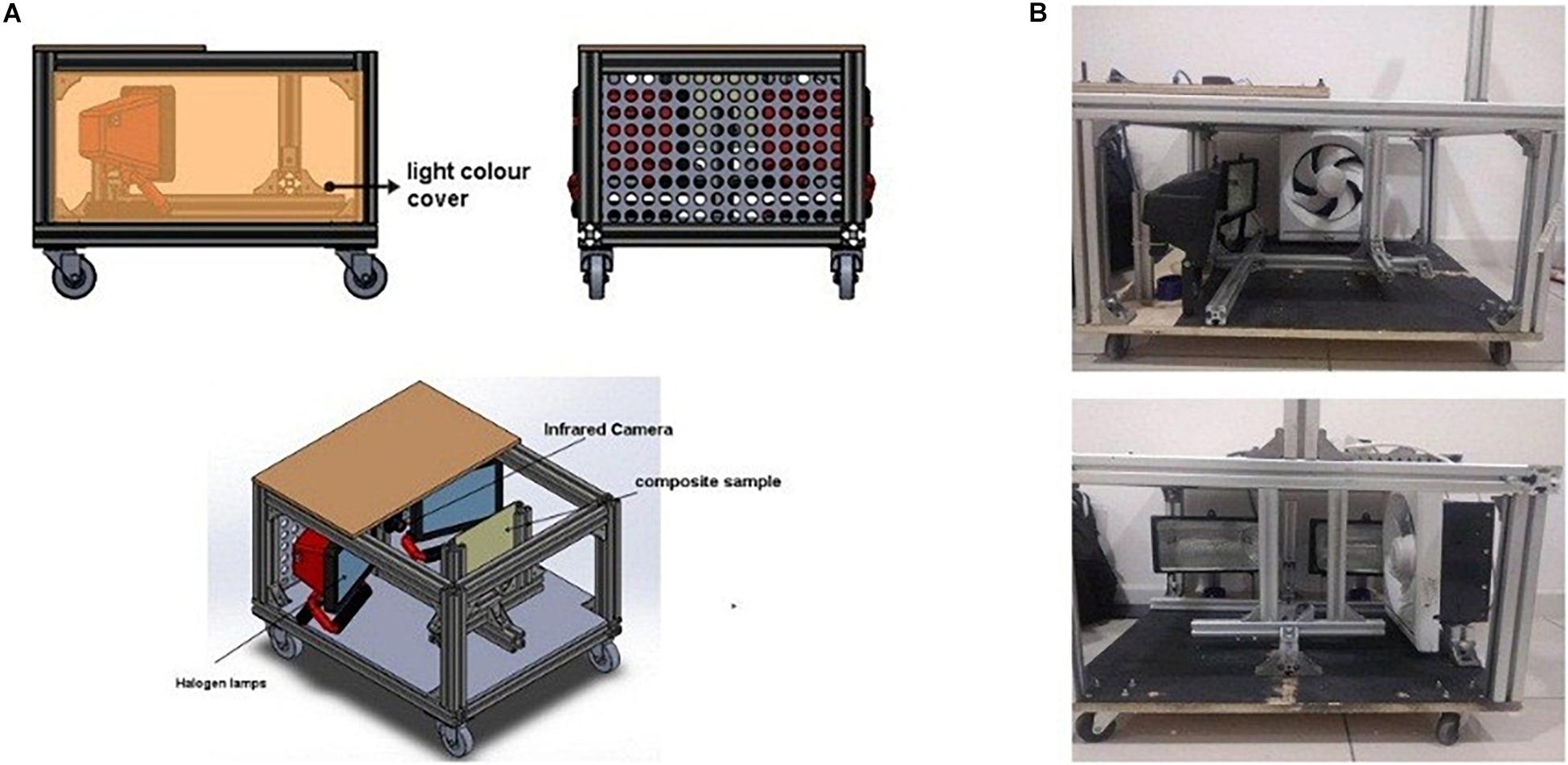
Figure 2. (A) Engineering drawing design of the thermography system in a close apparatus. (B) Rear side and front view of the apparatus.
Material Preparation
The reinforcement used in this study was flax (EU), construction 0°, Fiber TEX 106. Three types of flax samples were used for this study where each was exposed to impact and lightning. These samples consist of flax with an embedded wire, flax without an embedded wire mesh, and flax with a copper outer-ply wire mesh that acts as a lightning shield (refer to Figure 3). A black tape was applied to the surface of the sample to improve emissivity. These samples were approximately 100 mm by 100 mm in size and had 1–3 mm of thickness together with epoxy resin. The matrix used was epoxy resin brand EpoxAmite 100 (Smooth-on) and cured with Hardener brand 102 Medium (Smooth-on), which was supplied by Castmech Technologies, Malaysia. The curing time for the resin is 12 h at room temperature. The fabrication processes involved in this research is the vacuum bagging process. The process flow for the vacuum infusion process is illustrated below in Figure 4.
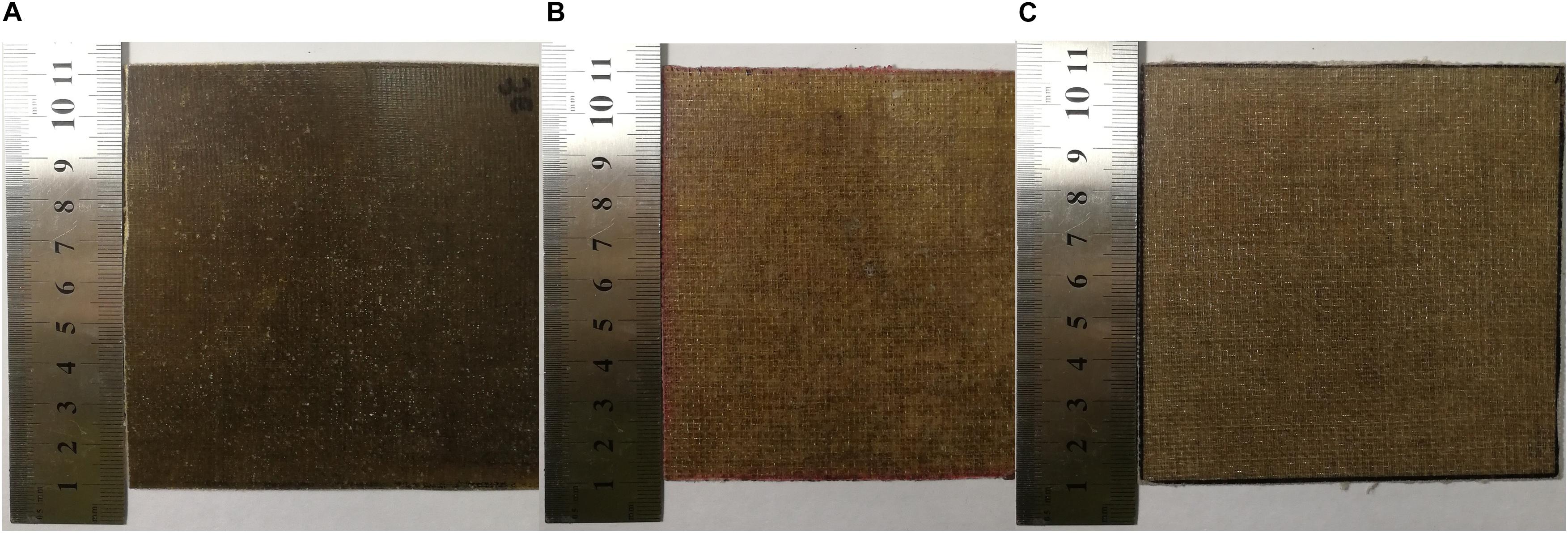
Figure 3. Testing samples; (A) flax composite, (B) flax with an embedded wire mesh, and (C) flax with an outer-ply wire mesh.
In the vacuum infusion process, the working area for flax plate fabrication was first cleaned using acetone. Afterward, the working area was waxed in a three-layer process to give better surface roughness to the flax plate. The ratio between the flax and epoxy resin is 30:70, following the ratio used by Yousif et al. (2012). The resin was prepared in an epoxy to hardener ratio of 100 g:28.4 g as recommended by the manufacturer. The flax layer, flax thickness, macro-fiber composite (MFC) bonding techniques, and mold were dependent on the experiments conducted. The peel plies were as a released layer between the flow mesh and the vacuum bag. The flow mesh assisted the resin to flow smoothly through the flax. The pressure inside the working area was tested after being covered up with a vacuum bag and a sealant. The resin compound was prepared according to the proposed ratio. Immediately after the resin mixture was stirred, the vacuum machine was switched on, and the vacuum compartment inside the vacuum bag sucked the resin inside and saturated the flax. The resin flow was observed, and the vacuum pump was switched off after the part was fully saturated. The part was left at room temperature for 12 h for the curing process. Then, the vacuum bag, peel plies, and mesh were carefully removed. The part was then taken out and cut to the required dimension.
For lightning defects, samples were taken from a lightning strike experiment that used a high-voltage (HV) electrode impulse generated by the Marx Impulse Generator. In this experiment, four stages were enough to produce a breakdown on the fiber where the lightning strike was increased for every 10 kV starting from 50 KV, if there was no breakdown. The illustration of the experimental setup for the lightning defect is shown in Figure 5. The diameter of flax burnt and breakage area cause by lightning is from 4 mm to 7 mm located at the center of samples is shown in Figure 6. A 5 J impacted sample of flax without an embedded wire mesh sample only using IM1-C impact test systems was used in the study. The impact test is performed using a drop-weight tool with a hemispherical striker tip with a diameter of 16 mm.
Image Processing
Without good data processing on the image captured, the image retrieved from the experiment is considered less valuable. Therefore, researchers applied image preprocessing to filter noise and enhance the defected area of the sample (Usamentiaga et al., 2014). Moreover, using a low-resolution camera, the image captured is less sharp or blur. Simple image processing methods are proposed to enhance the image and automatically detect the defect using MATLAB software. The process starts from improving the intensity of the image using imadjust function and filtering it using a median filter before the Canny edge detection algorithm is applied to the sample image to detect the edge of the defected area. Next, a morphological operation is necessary to clear small noise. Finally, the image is converted to binary image data where only a two-state output result will appear as bit 1 for the defected area and bit 1 as the non-defected area. The process flow of image processing is presented in Figure 7.
Results and Discussion
Defect Identification
Based on visual inspection, the lightning defects can be identified with the color changes on the sample surface. The lightning defect in the sample surface area is darker, and the surface texture is rougher compared to other areas. This is because of the lightning burnt area and breakage of the samples. The thermogram output images for lightning defects captured by the FLIR Lepton camera and the thermoIMAGER TIM 200 infrared cameras are shown in Figure 8.
FLIR Lepton camera and thermoIMAGER TIM 200 infrared cameras are capable of capturing lightning defects on flax-reinforced fiber sample, flax with and without a wire mesh, and flax with outer-ply samples under controlled parameters. Fiber breakage created by the lightning causes a temperature difference between defect and non-defect areas. Furthermore, a rougher surface on the sample caused by lightning produced a color difference for defect and non-defect areas.
For the impact defect sample, the thermoIMAGER TIM 200 is capable of detecting all two-impact defects points. The FLIR Lepton camera only captured a single point of the impact defect. Images for impact defects of the flax fiber captured by both cameras are presented in Figure 9. With several control and setup parameters, it is shown that a low-resolution infrared camera has the capability to be an NDE tool to detect low-impact defects, and the results are aligned with research that utilized medium- and high-resolution infrared cameras using pulse thermography to detect natural composite such as basalt fiber composite, jute, jute/hemp hybrid laminate (Zhang et al., 2018), and carbon fiber composite (Usamentiaga et al., 2013). However, in this experiment, several unknown areas, which are categorized as noise, are also captured using the thermoIMAGER TIM 200. This is the disadvantage of the pulse thermography technique where it received radiation from many factors such as the object, the surroundings, and the reflected object. Therefore, additional data processing is required such as image processing to improve blurred image and eliminate noise for low-resolution infrared cameras.
Figure 10 shows the temperature profile on the surface area of impact defect and lightning defect samples taken from the thermoIMAGER TIM 200 camera. The response can be divided into heating and cooling time. The heating duration captured in the experiment is between 20 and 30 s. The maximum temperature on the surface of all samples was from 40.3 to 45°C. A time delay during the cooling duration was observed along the time axis. This is because of the heat trapped inside the defective area which will be released slowly during the cooling time response. The cooling duration slope is much slower compared to the cooling duration for the impact defect on the flax fiber mat conducted by Prakash and Maharana (2017). This could be because of the different thickness of the material being used. There is a slight difference in the maximum temperature for the impact compared with the lightning defect where the maximum temperature for the impact defect is 40.3°C, and the value is lower than the lightning defect with maximum temperature. Figure 11 shows a sample result of flax lightning defect detection image processing flow using Canny edge detection algorithm. It is clearly shown that noise could be eliminated during the image processing process and the defect is detected.
Detection Accuracy Using the Confusion Matrix
The defects captured from both infrared cameras were checked visually, and the accuracy is analyzed using the confusion matrix. The analyses have been used for the classification of the material defect and to detect the defect on the material surface (Fang et al., 2020). For detection of the defect, it can be divided into true positive (TP) where it shows that the actual defect is detected as a defect; true negative (TN) where the actual defect is wrongly detected as noise or background; false positive (FP) where the actual noise is wrongly detected as a defect; and false negative (FN) where the actual noise is detected as noise. The equation is as follows:
The results are shown in Tables 3, 4. From the results, it is shown that both cameras are capable of detecting all impact and lightning defects. However, FLIR Lepton is capable of detecting all the defects. Nevertheless, the test is carried out on a few samples only.
Conclusion
In this experiment, the performance of thermographic NDT using long-pulse excitation for damage detection of the flax composite has been studied using two different models of low-resolution infrared cameras. The experiment was carried out indoors, under controlled environment with designated box-shaped configurations. Parameters such as heating duration, distance of the sample to the camera, and a heat source were determined at optimum as much as possible for better thermal contrast and to reduce noise. Generally, both low-resolution infrared cameras are capable of being used as a monitoring system for the flax biocomposite fiber to detect lightning and impact defects.
Data Availability Statement
The raw data supporting the conclusions of this article will be made available by the authors, without undue reservation.
Author Contributions
MA, FM, MS, MNA, and MM contributed to the work on composite materials fabrication and damage analysis. MH and MA contributed to thermography setup. IH contributed to the work of image processing. All authors contributed equally in completing this manuscript.
Funding
This work was supported by the Universiti Putra Malaysia.
Conflict of Interest
The authors declare that the research was conducted in the absence of any commercial or financial relationships that could be construed as a potential conflict of interest.
Acknowledgments
We wish to acknowledge the gratitude of the Universiti Putra Malaysia for providing the research grant and to Drs. Mohd Zaki Umar, Ilham Mukriz Zainal Abidin, and Siti Madiha Muhammad Amir from the Malaysian Nuclear Agency for equipment support throughout this research work.
References
Amir, S. M. M., Sultan, M. T. H., Jawaid, M., Ariffin, A. H., Mohd, S., Salleh, K. A. M., et al. (2018). “Nondestructive testing method for Kevlar and natural fiber and their hybrid composites,” in Durability and Life Prediction in Biocomposites, Fibre-Reinforced Composites and Hybrid Composites, eds M. Jawaid, M. Thariq, and N. Saba (U. K.: Woodhead Publishing), 367–388. doi: 10.1016/B978-0-08-102290-0.00016-7
Arockiam, N. J., Jawaid, M., and Saba, N. (2018). “Sustainable bio composites for aircraft components,” in Sustainable Composites for Aerospace Applications, eds M. Jawaid and M. Thariq (U. K.: Woodhead Publishing), 109–123. doi: 10.1016/B978-0-08-102131-6.00006-2
Asim, M., Saba, N., Jawaid, M., and Nasir, M. (2018). “Potential of natural fiber/biomassfiller-reinforced polymercomposites in aerospaceapplications,” in Sustainable Composites for Aerospace Applications, eds M. Jawaid and M. Thariq (U. K.: Woodhead Publishing).
Balageas, D., Maldague, X., Burleigh, D., Vavilov, V. P., Oswald-Tranta, B., Roche, J. M., et al. (2016). Thermal (IR) and Other NDT Techniques for Improved Material Inspection. J. Nondestr. Eval. 35, 1–17. doi: 10.1007/s10921-015-0331-7
Barouni, A. K., and Dhakal, H. N. (2019). Damage investigation and assessment due to low-velocity impact on flax/glass hybrid composite plates. Compos. Struct. 226:111224. doi: 10.1016/j.compstruct.2019.111224
Bendada, A., Sfarra, S., Genest, M., Paoletti, D., Rott, S., Talmy, E., et al. (2013). How to reveal subsurface defects in Kevlar® composite materials after an impact loading using infrared vision and optical NDT techniques? Eng. Fract. Mech. 108, 195–208. doi: 10.1016/j.engfracmech.2013.02.030
Brandão, P., Infante, V., Deus, A. M., and Gholizadeh, S. (2016). Thermo-mechanical modeling of a high pressure turbine blade of an airplane gas turbine engine A review of non-destructive testing methods of composite materials. Procedia Struct. Integr. 1, 50–57. doi: 10.1016/j.prostr.2016.02.008
Dhakal, H. N., Zhang, Z. Y., Guthrie, R., MacMullen, J., and Bennett, N. (2013). Development of flax/carbon fibre hybrid composites for enhanced properties. Carbohydr. Polym. 96, 1–8.
Dicker, M. P. M., Duckworth, P. F., Baker, A. B., Francois, G., Hazzard, M. K., and Weaver, P. M. (2014). Green composites: a review of material attributes and complementary applications. Compos. Part A Appl. Sci. Manuf. 56, 280–289.
Diharjo, K., Hastuti, S., Triyasmoko, A., Sumarsono, A. G., Putera, D. P., Riyadi, F., et al. (2013). “The application of kenaf fiber reinforced polypropylene composite with clay particles for the interior panel of electrical vehicle,” in Proceedings of the 2013 Joint International Conference on Rural Information and Communication Technology and Electric-Vehicle Technology, RICT and ICEV-T 2013, (U. S. A.: IEEE), doi: 10.1109/rICT-ICeVT.2013.6741532
Dittenber, D. B., and Gangarao, H. V. S. (2012). Critical review of recent publications on use of natural composites in infrastructure. Compos. Part A Appl. Sci. Manuf. 43, 1419–1429. doi: 10.1016/j.compositesa.2011.11.019
Ekanayake, S., Gurram, S., and Schmitt, R. H. (2018). Depth determination of defects in CFRP-structures using lock-in thermography. Compos. Part B Eng. 147, 128–134. doi: 10.1016/j.compositesb.2018.04.032
Fang, X., Luo, Q., Zhou, B., Li, C., and Tian, L. (2020). Research Progress of Automated Visual Surface Defect Detection for Industrial Metal Planar Materials. Sensors 20:5136.
Ghali, V. S., Panda, S. S. B., and Mulaveesala, R. (2011). Barker coded thermal wave imaging for defect detection in carbon fbre-reinforced plastics. Insight Non-Destructive Test. Condition Monitor. 53, 621–624. doi: 10.1784/insi.2011.53.11.621
Grys, S. (2018). Determining the dimension of subsurface defects by active infrared thermography – Experimental research. J. Sens. Sens. Syst. 7, 153–160. doi: 10.5194/jsss-7-153-2018
Hirano, Y., Katsumata, S., Iwahori, Y., and Todoroki, A. (2010). Artificial lightning testing on graphite/epoxy composite laminate. Compos. Part A Appl. Sci. Manuf. 41, 1461–1470. doi: 10.1016/j.compositesa.2010.06.008
Kalyanavalli, V., Ramadhas, T. K. A., and Sastikumar, D. (2018). Long pulse thermography investigations of basalt fiber reinforced composite. NDT E Int. 100, 84–91. doi: 10.1016/j.ndteint.2018.08.007
Kang, M. K., Lee, W. I., and Hahn, H. T. (2001). Analysis of vacuum bag resin transfer molding process. Composites Part A Appl. Sci. Manuf. 32, 1553–1560. doi: 10.1016/S1359-835X(01)00012-4
Khodayar, F., Lopez, F., Ibarra-Castanedo, C., and Maldague, X. (2018). Parameter Optimization of Robotize Line Scan Thermography for CFRP Composite Inspection. J. Nondestr. Eval. 37, 1–9. doi: 10.1007/s10921-017-0459-8
Kim, G., Kim, G., Park, J., Kim, D., and Cho, B. (2014). Application of infrared lock-in thermography for the quantitative evaluation of bruises on pears. Infrared Phys. Technol. 63, 133–139.
Kroworz, A., and Katunin, A. (2018). Non-Destructive Testing of Structures Using Optical and Other Methods A Review. Struct. Durability Health Monitor. 12, 1–17. doi: 10.3970/sdhm.2018.012.001
Larsson, A. (2002). The interaction between a lightning flash and an aircraft in flight. C. R. Phys. 3, 1423–1444. doi: 10.1016/S1631-0705(02)01410-X
Lefeuvre, A., Bourmaud, A., Morvan, C., and Baley, C. (2014). Elementary flax fibre tensile properties: correlation between stress-strain behaviour and fibre composition. Ind. Crops Prod. 52, 762–769. doi: 10.1016/j.indcrop.2013.11.043
Logakis, E., and Skordos, A. A. (2012). “Lightning strike performance of carbon nanotube loaded aerospace composites,” in Proceedings of the 15th European Conference on Composite Materials, (Venice: European Conference on Composite Materials, ECCM), 24–28.
Maldague, X. P. V. (2002). Introduction to NDT by active infrared thermography. Mater. Eval. 60, 1060–1073.
Manes, A., Nunes, S., Jiménez, A., Amico, S., and Giglio, M. (2018). Comparison of non-destructive techniques for impact damage area assessment in aramid/epoxy composites. Proceedings 2:437. doi: 10.3390/icem18-05320
Marinetti, S., and Cesaratto, P. G. (2012). Emissivity estimation for accurate quantitative thermography. NDT E Int. 51, 127–134. doi: 10.1016/j.ndteint.2012.06.001
Mat Daud, S. Z., Mustapha, F., and Adzis, Z. (2018). Lightning strike evaluation on composite and biocomposite vertical-axis wind turbine blade using structural health monitoring approach. J. Int. Mat. Syst. Struct. 29, 3444–3455. doi: 10.1177/1045389X17754259
Naveen, J., Jawaid, M., Zainudin, E. S., Sultan, M. T. H., and Yahaya, R. (2019). Evaluation of ballistic performance of hybrid Kevlar® /Cocos nucifera sheath reinforced epoxy composites. J. Text. Inst. 110, 1179–1189. doi: 10.1080/00405000.2018.1548801
Nur, S., Safri, A., Thariq, M., Sultan, H., Jawaid, M., and Jayakrishna, K. (2017). Impact behaviour of hybrid composites for structural applications: a review. Compos. Part B Eng. 133, 112–121. doi: 10.1016/j.compositesb.2017.09.008
Peesapati, V., Cotton, I., Sorensen, T., Krogh, T., and Kokkinos, N. (2011). Lightning protection of wind turbines - a comparison of measured data with required protection levels. IET Renew. Power Gener. 5, 48–57. doi: 10.1049/iet-rpg.2008.0107
Pickering, S. G., Chatterjee, K., Almond, D. P., and Tuli, S. (2013). LED optical excitation for the long pulse and lock-in thermographic techniques. NDT E Int. 58, 72–77. doi: 10.1016/j.ndteint.2013.04.009
Prakash, R. V., and Maharana, M. (2017). Damage detection using infrared thermography in a carbon-flax fiber hybrid composite. Procedia Struct. Integr. 7, 283–290.
Ramesh, M. (2019). Flax (Linum usitatissimum L.) fibre reinforced polymer composite materials: a review on preparation, properties and prospects. Prog. Mat. Sci. 102, 109–166. doi: 10.1016/j.pmatsci.2018.12.004
Ramnath, B. V., Elanchezhian, C., Nirmal, P. V., Kumar, G. P., Kumar, V. S., Karthick, S., et al. (2014). Experimental investigation of mechanical behavior of jute-flax based glass fiber reinforced composite. Fibers Polym. 15, 1251–1262.
Rani, A., and Mulaveesala, R. (2020). Depth resolved pulse compression favourable frequency modulated thermal wave imaging for quantitative characterization of glass fibre reinforced polymer. Infrared Phys. Technol. 110:103441. doi: 10.1016/j.infrared.2020.103441
Ravandi, M., Teo, W. S., Tran, L. Q. N., Yong, M. S., and Tay, T. E. (2017). Low velocity impact performance of stitched flax/epoxy composite laminates. Compos. Part B Eng. 117, 89–100. doi: 10.1016/j.compositesb.2017.02.003
Rizzo, F., Pinto, F., and Meo, M. (2019). Development of multifunctional hybrid metal/carbon composite structures. Compos. Struct. 222:110907. doi: 10.1016/j.compstruct.2019.110907
Roche, J.-M., Passilly, F., Beauch, P., Zaepffel, C., Sousa Martins, R., and Balageas, D. (2018). IR thermography for lightning-strike damage monitoring in composite materials. 14th Quantitative InfraRed Thermography Conference. (Germany: QIRT), 23–26. doi: 10.21611/qirt.2018.092
Saeed, N., Omar, M. A., Abdulrahman, Y., Salem, S., Mayyas, A., and Omar, M. A. (2018). IR Thermographic Analysis of 3D Printed CFRP Reference Samples with Back-Drilled and Embedded Defects. J. Nondestr. Eval. 37, 3–10.
Sanjay, M. R., and Siengchin, S. (2021). Editorial corner – a personal view exploring the applicability of natural fibers for the development of biocomposites. Express Polym. Lett. 15:193. doi: 10.3144/expresspolymlett.2021.17
Silipigni, G., Burrascano, P., Hutchins, D. A., Laureti, S., Petrucci, R., Senni, L., et al. (2017). Optimization of the pulse-compression technique applied to the infrared thermography nondestructive evaluation. NDT E Int. 87, 100–110. doi: 10.1016/j.ndteint.2017.01.011
Usamentiaga, R., Venegas, P., Guerediaga, J., Vega, L., and López, I. (2013). Feature extraction and analysis for automatic Automatic detection of impact damage in carbon fiber composites using active thermography. Infrared Phys. Technol. 58, 36–46. doi: 10.1016/j.infrared.2013.01.004
Usamentiaga, R., Venegas, P., Guerediaga, J., Vega, L., Molleda, J., and Bulnes, F. G. (2014). Infrared thermography for temperature measurement and non-destructive testing. Sensors 14, 12305–12348. doi: 10.3390/s140712305
Wang, Z., Tian, G. Y., Meo, M., and Ciampa, F. (2018). Image processing based quantitative damage evaluation in composites with long pulse thermography. NDT E Int. 99, 93–104. doi: 10.1016/j.ndteint.2018.07.004
Wang, Z., Zhu, J., Tian, G., and Ciampa, F. (2019). NDT and E International Comparative analysis of eddy current pulsed thermography and long pulse thermography for damage detection in metals and composites. NDT E Int. 107:102155. doi: 10.1016/j.ndteint.2019.102155
Wu, S., Gao, B., Yang, Y., Zhu, Y., Burrascano, P., Laureti, S., et al. (2019). Halogen optical referred pulse-compression thermography for defect detection of CFRP. Infrared Phys. Technol. 102:103006. doi: 10.1016/j.infrared.2019.103006
Yan, L., Chouw, N., and Jayaraman, K. (2014). Flax fibre and its composites - A review. Compos. Part B Eng. 56, 296–317. doi: 10.1016/j.compositesb.2013.08.014
Yousif, B. F., Shalwan, A., Chin, C. W., and Ming, K. C. (2012). Flexural properties of treated and untreated kenaf/epoxy composites. Mat. Design 40, 378–385.
Keywords: flax biocomposite, impact and lightning damage, infrared thermography, NDE technique, non-destructive evaluation, long-pulse thermography
Citation: Anwar M, Mustapha F, Sultan MTH, Halin IA, Abdullah MN, Hassim MI and Mustapha M (2021) Damage Identification on Impact and Lightning Damage of Flax Composite Laminates (Linum usitatissimum) Using Long-Pulse Thermography of a Low-Resolution Infrared Camera. Front. Mater. 8:618461. doi: 10.3389/fmats.2021.618461
Received: 17 October 2020; Accepted: 12 April 2021;
Published: 20 May 2021.
Edited by:
Alfonso Maffezzoli, University of Salento, ItalyReviewed by:
Ravibabu Mulaveesala, Indian Institute of Technology Ropar, IndiaSanjay Mavinkere Rangappa, King Mongkut’s University of Technology North Bangkok, Thailand
Copyright © 2021 Anwar, Mustapha, Sultan, Halin, Abdullah, Hassim and Mustapha. This is an open-access article distributed under the terms of the Creative Commons Attribution License (CC BY). The use, distribution or reproduction in other forums is permitted, provided the original author(s) and the copyright owner(s) are credited and that the original publication in this journal is cited, in accordance with accepted academic practice. No use, distribution or reproduction is permitted which does not comply with these terms.
*Correspondence: Faizal Mustapha, ZmFpemFsbXNAdXBtLmVkdS5teQ==; Murniwati Anwar, Z3M1MTIyMEBzdHVkZW50LnVwbS5lZHUubXk=; Mazli Mustapha, bWF6bGkubXVzdGFwaGFAdXRwLmVkdS5teQ==