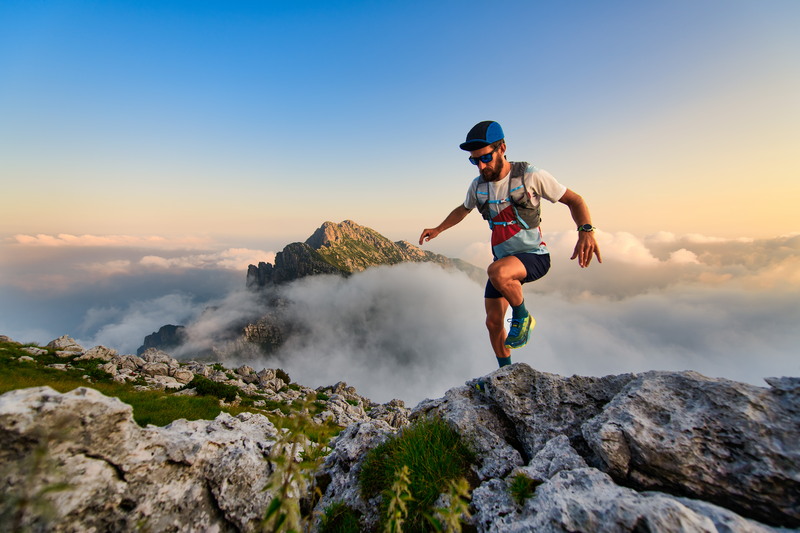
95% of researchers rate our articles as excellent or good
Learn more about the work of our research integrity team to safeguard the quality of each article we publish.
Find out more
ORIGINAL RESEARCH article
Front. Mater. , 05 April 2021
Sec. Structural Materials
Volume 8 - 2021 | https://doi.org/10.3389/fmats.2021.575802
This article is part of the Research Topic Development and Application of Bituminous Materials for Civil Infrastructures View all 20 articles
The objective of this study is to investigate the compaction characteristics of cold recycled mixtures with asphalt emulsion (CRME) using the Superpave gyratory compactor (SGC) method. Five characteristic parameters were proposed and calculated including the compaction energy index, the compaction energy index, three compaction energy indicators at different compaction stages. The influence of these parameters and material compositions were analyzed for the pavement performance. The difference between SGC and Marshall double-sided compaction/heavy compaction method was compared. The results show that the proposed parameters can better reflect the compaction characteristics of CRME, and the mixture effect with SGC of 50 gyrations was close to that with 75 blows using the Marshall compaction. The asphalt emulsion contents and compaction temperatures had a significant effect on compaction characteristics, but the effect of aggregate gradations was not significant. The appropriate asphalt emulsion and the new aggregate content can increase the capability of the CRME to resist the permanent deformation. The optimum mixing water content of CRME obtained by the SGC method was reduced by 18%, but the density increased by 3.5%, compared with the heavy compaction method. Finally, a new idea to determine the optimum emulsified asphalt content of CRME was provided through analyzing the compaction characteristic parameters.
The requirements for asphalt pavements become stricter with the increase of heavy traffics and overloading of vehicles. Severe distress is observed for the surface layer after years of serving. Therefore, thousands of semi-rigid asphalt pavements that were constructed decades ago need to be reconstructed and maintained, which will generate a large amount of reclaimed asphalt pavement (RAP). Cold recycling technology with asphalt emulsion can use almost 100% of RAP without heating, reducing pollution and waste emissions, as well as the aged asphalt mixtures deposited at landfills (Lin et al., 2017; Xiao et al., 2018; Rodríguez-Fernández et al., 2019). The environmental and economic benefits of cold recycling make it an attractive alternative for pavement conservation and rehabilitation (Turk et al., 2016).
Recently, cold recycling technology has been used in more and more road maintenance and reconstruction projects. However, there is no widely accepted design method for Cold Recycled Mixes with Asphalt Emulsion (CRME). Besides, the inconsistent compaction between lab and field discourages the wide use of such technology (Martinez-Echevarria et al., 2012). The current mixture design method (JTG/T5521-2019) for the CRME is based on the modified Marshall method without considering the horizontal shearing behavior caused by traffic loads. Moreover, the specimen density is expected to be increased as the blow number increases, and there are also some problems, including second compaction and poor test reproducibility. Numerous studies have been conducted to study the compaction characteristics of asphalt mixtures (MOC of PRC, 2019). It was claimed that the mixture that using the Superpave Gyratory Compactor (SGC) method obtained a material that has more similar properties to the materials on the field in terms of particle alignment and density (Tarefder and Ahmad, 2016). Therefore, it is necessary and meaningful to study the compaction characteristics of CRME to improve project quality and guide the construction practice.
Currently, researchers have different opinions on the mixture design and parameters of CRME using the SGC method. Hillgren et al. proposed to determine the design gyration number at 96% of the target density. The target density was the specimen density after 200 gyrations times (Hillgren et al., 1989). Gao et al. (2014) analyzed the parameters sensibility for the CRME using the SGC method and obtained a regression equation based on design compaction number, compaction temperature, and emulsified asphalt content. They also provided a new method to determine the optimum moisture content of the cold mixture. In terms of the compaction method, Yan observed that the specimen density of the CRME that was compacted with 50–70 blows using the Marshall method was equivalent to the specimen density that was compacted with 30–50 gyrations using the SGC method (Yan, 2006). Flores et al. (2019) developed a new design methodology for cold recycled mixtures with emulsions and a Global Performance Index was proposed to compare the formula and optimize the mixture. The conditions were investigated for the compaction of cold recycled mixtures with emulsions and 100% RAP. It was recommended to apply a compaction energy level of 100 gyrations for specimens with 100 mm diameter and 60 mm height, and an energy level of 200 gyrations for specimens with 100-mm diameter and-100 mm height (Flores et al., 2020). A research project has been conducted to adapt to the current French experimental device. It is called “PCG3,” which was devoted strictly to hot mix asphalt (HMA) characterization to allow for the compaction of cold mixes by adding the functionality of collecting extruded water due to emulsion breaking (Wendling et al., 2015). A new volumetric mix-design procedure was developed for cold in-place recycling (CIR) asphalt mixtures by utilizing the SGC method. The procedure required that the density of specimens was close to that in the field. The performance of CIR mixtures from the new mix-design procedure was evaluated by the mechanistic-empirical pavement design guide (MEPDG) models, as well as in the field testing (Lee et al., 2016). The SGC metrics were recommended to quantify workability and compactability. The curing temperature generally had a more significant influence on test results than cure time (Casillas and Braham, 2020).
The data from the SGC compaction curve was mainly used to analyze the compaction properties of the HMA. The compaction curve from SGC was divided into two stages in where the construction energy index (CEI) and traffic densification index (TDI) were defined respectively. The two indicators were used to characterize the HMA performance during the construction stage and the pavement serving stage. The test results showed that the nominal maximum aggregate size, aggregate gradation, and asphalt content of HMA had significant effects on CEI, and the TDI can accurately predict the high-temperature stability of the mixes (Dessouky et al., 2004). The compaction dissipation energy index can better evaluate the significance of each influencing factor of asphalt mixture (DelRio-Prat et al., 2011). It has been proved that the higher temperature of RAP results in better compaction of the cold mixture in the field (Kim and Lee, 2011). The CEI and the compacted curve slope of HMA have been defined based on the SGC compaction curve, and the workability and road stability of HMA were analyzed (Zhang et al., 2005). Based on the HMA compaction characteristics, the number of rollers required on-site is determined from the perspective of energy equivalence (Li et al., 2011). In summary, the researchers conducted lots of research for the HMA mixtures on the characteristics of the compaction curve based on the SGC method and defined different compaction stages and corresponding characteristic parameters, which played a good role in the construction control of the mixture. However, there are limited studies that evaluated CRME compaction properties. The analysis method used in the HMA can partly be used on the CRME. Also, there is no unified method to determine the design parameters, including the optimum emulsified asphalt content, the optimum moisture content, and the compaction temperature (Brovelli and Crispino, 2012; Kim, 2012). These problems in CRME motivated this research.
The objectives of this paper are to 1) investigate the compaction characteristics of CRME by analyzing the SGC densification curves, 2) and propose the compaction characteristic parameters that can be used to analyze the compaction characteristics of the mixture. Also, the article attempts to propose a reasonable method to determine the optimum content of emulsion and moisture for CRME and specific compaction temperature. Finally, this research may help to better understand the material properties of CRME and provide a reference idea for the design of CRME to improve the construction quality.
The RAP was obtained from an expressway maintenance project in Henan Province, China, in which the recycled asphalt content was 4.87%. In terms of the binder properties, the penetration at 25°C was 3.1 mm; the ductility at 15°C was 12.7 cm; the softening point was 61.8°C; the viscosity at 60°C was 2457 Pas, which indicated the asphalt binder was highly aged after 12 years in service.
A cationic slow-cracking fast-setting emulsifier for cold recycled asphalt mixture was used in this study, and asphalt emulsion was prepared with Zhenhai #70 petroleum asphalt using the colloidal mill in the laboratory. Tap water was utilized to prepare the asphalt emulsion and mix the cold recycled asphalt mixture. The basic properties of the asphalt emulsion are shown in Table 1.
To reduce the RAP variability, the milled RAP was divided into sizes of 0–3 , 3–5 , 5–10 , and 10–20 mm. Based on the specification requirements of JTG/T5521-2019, the gradation of CRME was designed. The design gradation of CRME included 90% RAP and 10% limestone gravel (size from 10 to 20 mm). There were also two sets of comparison gradations. One gradation included 80% RAP and 20% limestone gravel, and the other gradation was composed of 70% RAP, 20% limestone gravel, and 10% fine aggregate. Technical indicators, including crushing value, gross volume density, percentage of flat-elongated particles, and sand equivalent were measured in accordance with JTG F40 (MOC of PRC, 2004). The gradations of CRME were displayed in Figure 1.
Cement is an important component to improve the early-stage performance of CRME. 1% PC32.5 cement by weight of the aggregates was used in the CRME. The cement was obtained from Hebei province. Its initial setting time was 264 min, and the final setting time was 387 min. The water requirement for the normal consistency of cement paste was 26.8%.
The SGC compaction curve provides the most important information to understand the CRME compaction characteristics. As shown in Figure 2, the typical gyratory compaction curve clearly describes that the mixture density increases as the gyration level increases.
The compaction curve is a power-law function, and the fitting equation is shown in Eq. 1:
where A and b are regression parameters, N is gyration number,
The compaction curve was divided into three different intervals to reflect the characteristics of CRME at different stages. The first stage was the initial compaction stage, in which the degree of compaction rapidly increased at first. The aggregates move and contact gradually due to emulsified asphalt and water, and the increase rate of the density decreases with the gyration number increasing. The curvature radius of the compaction curve changed from large to small. There is a minimum radius of curvature that is corresponding to the initial compaction number (Nini). The second stage was a design compaction stage when the air voids content achieved the design requirement, where the gyration number was set as the design compaction number (Ndes). The third stage was an ultimate compaction stage after the CRME reached the designed air voids content. At this stage, the compaction degree was small as the gyration number increased, and the emulsions began to show instability. In this study, the maximum gyration number (Nmax) was set at 100.
The densification curve is usually used to reflect the compaction property of the mixes. As shown in Figure 3, the densification curve from Nini to Ndes is a straight line expressed with an average slope of Kid in semi-logarithmic coordinates. The calculation formula is shown in Eq. 2. A larger Kid indicates higher compaction of the mixes. The slope of Kdm is used to reflect the compaction characteristics of CRME after opening traffic, which represents the compactability from Ndes to Nmax. The average slope of the densification curve is Kdm, which can be obtained with linear regression. As shown in Eq. 3, a larger Kdm indicates a higher compactability of the mixes after open traffic as well as worse the deformation resistance.
Where
Nini = initial gyration number when the maximum curvature occurs.
Ndes = design gyration number when the design air voids content is obtained.
Nmax = maximum number of gyrations.
Although the slopes of the densification curve partly reflected the compaction characteristics of the mixes, they cannot accurately show the total compaction energy. Therefore, an energy-related index was proposed. The compaction energy index (CEI) can be calculated by measuring the area under the compaction curve between any two points, which indicated the required energy under the gyration compactor. Based on the three-stage compaction characteristics of CRME, the first stage compaction energy index (FCEI), the second stage compaction energy index (SCEI), and the third stage compaction energy index (TCEI) were proposed.
As shown in Figure 2, The FCEI was calculated by measuring the area under the compaction curve from one to Nini gyrations, which reflects the workability of the mixes. The SCEI was calculated by measuring the area under the compaction curve from Ninito Ndes gyrations, which reflects the compaction characteristics of the mixes during the paving and rolling stages. The TCEI was calculated by measuring the area under the compaction curve from Ndes to Nmax gyrations. A larger TCEI indicated a stronger deformation resistance of CRME. The approximate calculations of FCEI, SCEI, and TCEI can be seen in Eqs. 4–6.
Where
Nini = when the radius of curvature for the compaction curve is a minimum, which is an initial compaction number.
Ndes = when air void of mixes attains design requirements, which is design number.
Nmax = the maximum number of gyrations is set at 100 in this study, A and b are the regression parameters of the densification curve.
The modified Marshall method included three processes for the mix design of CRME. First, the optimum moisture content of the CRME was selected at an asphalt emulsion content of 3.5% by the maximum dry density of samples. Second, the optimum asphalt emulsion content was determined by the Indirect Tensile Strength (ITS) and dry-wet ITS ratio. The samples were prepared by the Marshall method using 75 blows on both sides at the optimum determining moisture content. The air voids content should be controlled at 8–13%. Third, the performance of CRME was evaluated by ITS and moisture damage resistance.
The optimum moisture content of CRMEs was determined by the heavy compaction test in standard JTG E40 (MOC of PRC, 2007). The CRME was compacted in layers in the standard compaction apparatus. When the maximum particle size of CRME was 20 mm, a compaction cylinder with an inner diameter of 100 mm was used, and the compaction effort was 2687 kJ/m3. When the maximum particle size of CRME was 40 mm, a compaction cylinder with an inner diameter of 152 mm was used, and the compaction effort was 2677 kJ/m3. The wet density of compacted specimens is calculated by the compaction cylinder volume and CRME mass. The dry density was calculated as Eq. 7.
where
The ITS is a key indicator for the mix design of CRME. Two groups of specimens were prepared for the ITS tests (JTG/T5521-2019). Three replicate specimens in the first group were saturated in a water bath at 25°C for 23 h, then placed in a water bath at 15°C for 1 h before measuring wet ITS strength (ITSw). Three replicate specimens in the second group were soaked only in a water bath at 15°C for 1 h before measuring dry ITS (ITSd). The ITS test was conducted at 15°C at a loading rate of 50 mm/min. The percentage of the ITS ratio (ITSR) is calculated by Eq. 8.
where ITSR is the dry-wet ITS ratio. ITSw is wet ITS (Unit: MPa). ITSd is dry ITS (Unit: MPa).
The water damage resistance was evaluated by an indirect tensile strength ratio (TSR) test, following the JTG E20 procedure (MOC of PRC, 2011). The TSR was determined as the ratio of the tensile strength of dry specimens to the tensile strength of the conditioned specimens. The saturated specimens were conditioned at −18°C for 24 h and then submerged in the water bath at 60°C for another 24 h.
The rutting resistance was evaluated by a wheel tracking test, following a standard procedure in JTG E20-2011. The test specimen was a slab (300 × 300 × 80 mm3) prepared by a roller compactor. During the wheel tracking test, the asphalt concrete slab was loaded by a repeated solid rubber tire with a contact pressure of 0.7 MPa at a speed of 42 cycles per minute. The test took 1 h and the rutting depth was recorded. The dynamic stability (DS) was defined as the average loading cycles that achieved a 1 mm rutting depth. A higher DS value was preferable for the rutting resistance.
The low-temperature performance was evaluated via a three-point beam bending test at 10°C, following a standard procedure in JTG/E20-2011. The specimen size was 50 mm × 50 mm × 250 mm. A vertical load was applied until the beam was fractured. The flexural strength, flexural stiffness, and fracture strain were obtained.
The compaction of CRME should not only simulate the compaction on the field but also ensure consistency between laboratory compaction and on-site construction. It was important to determine the gyration number, which affected the property of CRME. If the design gyration number was too low, the designed properties of CRME cannot be achieved. If the design gyration number was too high, the construction quality may not be able to meet the design requirements. It was observed that lots of asphalt emulsions were pressed out from the CRME at an extremely high gyration number, which cannot reflect the design performance of the mixture.
The CRME was prepared as cylinder specimens with a height of 63.5 mm and a diameter of 100 mm. The asphalt emulsion content and mixed water content was 3.5 and 2.8% by weight of aggregates, respectively. The gradation of G90 was used. The prepared specimens were aged for about 24 h at 25°C and then were cured rapidly in an air-circulating oven at 40°C for 72 h. A compaction curve is shown in Figure 4.
As shown in Figure 4, the relationship between the air voids content of the specimen and the gyration number can be fitted as a power-law function. By calculating the derivative of the regression curve equation, the slope of any point on the compaction curve can be calculated, which reflected the compaction rate at certain gyration numbers. As the gyration number increased, the compactibility gradually decreased and finally tended to be 0.
When the gyration number was between 0 and 10 gyrations, the air voids content of the specimen changed sharply and the difference is about 8%. From 10 to 30 gyrations, the air voids content of the specimen slowly decreased, with a decrease of 4.7%. From 30 to 50 gyrations, the air voids content decreased by 2.1%. From 50 to 75 gyrations, the air voids content slightly decreased by 1.6%. It was observed that some emulsions were squeezed out from the mixture after 50 gyrations, as is shown in Figure 5. When the gyration number was about or more than 75 gyrations, a large number of emulsions were squeezed out from the bottom of the mold, which affected the performance of the mixes. It was required in the specification JTG/T5521-2019 that the air voids content of CRME should in the range of 8–13%, and the ideal air voids content of the CRME is typically controlled at about 11 ± 1%. Based on that, the preliminary design gyration number was set at 50.
To further understand the impact of gyration number on the CRME, the volume parameter changes of the CRME for four different emulsion contents (3.0, 3.5, 4.0, and 4.5%) with G90 gradation and three different RAP proportions (70, 80, and 90%) in the same asphalt emulsion content (4.0%) were studied. The optimum water content for the CRME, including the water in asphalt emulsion, in the virgin aggregate and the RAP, and mixing water, was determined at the maximum dry density. Therefore, when the asphalt emulsion content changes, the mixing of water content changes accordingly. In this article, since the aggregates are all dried, the influence of gradation changes on the mixing water is not considered. The specimens were compacted at 100 gyrations and the air voids contents at different gyrations were calculated. The results are summarized in Figure 6.
FIGURE 6. The air voids content of the CRME for different emulsified asphalt contents and gradation changes with the gyration number.
As seen in Figure 6, the air voids content of all specimens sharply decreased as the compaction number increased from 0 to 10 gyrations, and the maximum decrease was about 10%. From 10 to 30 gyrations, the change of air voids content began to slow down, with a reduction of 4.9%. From 30 to 50 gyrations, the compaction difficulty further increased, since the air voids content reduced by 2.3%. After 50 gyrations, there is a little effect on the volumetric parameters of the mixes, as compaction increased. Similarly, it was found that some emulsions began to be squeezed out with more than 50 gyrations. Considering the changing trend in air voids content and specification requirements, it was feasible to determine the design gyration number at 50.
As shown in Figure 6, it can be found when the emulsified asphalt content changed from 3.0 to 3.5% at 50 gyrations, the air voids content decreased by 8.1%, and the emulsified asphalt content changed from 3.5 to 4.0%. At the same time, the air voids content decreased by 7.9%. But when the emulsified asphalt content changed from 4.0% to 4.5, the air voids content decreased only by 2.6%. The results show that the emulsified asphalt of 4% by weight of aggregates is an obvious point for the change of volumetric parameters. When the emulsified asphalt content is less than 4.0%, the air voids content decreases significantly. When the emulsified asphalt content is greater than 4.0%, the change of air voids content is small, which indicates that emulsified asphalt content has an important effect on compaction, but the impact becomes smaller and smaller. As the gyration number increased, the compactness of the CRME for different proportions of RAP increase. However, the effect of aggregate gradation on the air voids content was very small. In summary, the content of asphalt emulsion had a higher effect on compactness than the gradation.
Based on the data in Figure 6, the regression parameters of the compaction curve for different materials are shown in Table 2. To analyze the effect of aggregate gradation, the compaction parameters for the three different aggregate gradations were calculated by the defined compaction parameters and the regression equation. The calculation results are shown in Table 3.
As seen in Table 3, in terms of compaction energy, the more new materials were added, the higher FCEI value was during the initial compaction stage. It indicated that a larger proportion of new materials resulted in worse workability of CRME. In the design compaction stage, the higher the proportion of new materials, the higher the SCEI value was, which indicated the compactibility difficulty of CRME as more new materials were added. In the third compaction stage, the larger the proportion of new materials is, the greater the compaction energy required, which indicates CRME needs a stronger ability to resist deformation. In terms of the average slope, the more the new materials are added, the larger Kid and Kdm are. It indicates the fewer new materials there is, the faster the compaction rate of the design compaction stage and the ultimate compaction stage. As the new material increased, the internal friction angle of CRME increases, which indicated the proper addition of the new materials to cold recycled mixes was helpful to resist deformation. Therefore, G90 is chosen as the optimal design gradation in this paper.
In order to analyze the effect of the asphalt emulsion content, the compaction parameters for different emulsions content were calculated. The calculation results are shown in Table 4.
As observed from Table 4, the FCEI, SCEI, TCEI, Kid, and Kdm of CRME increased as the emulsified asphalt content increased from 3 to 3.5%. That is because the mixes are at the condition of optimum moisture content, the asphalt emulsion content increase, and the added water decreases accordingly, which may increase the viscosity of the mixes and the compaction energy. It was observed that there were minimum values of compaction energy index and curve slope at the emulsified asphalt content of 4.0%, which indicated better workability during the initial compaction stage and design compaction stage, and a lower compaction rate in the third stage. Besides, it should be noted that the Kdm of different materials was close to 0, which indicated that the compactness of the CRME hardly changed after 50 gyrations. Therefore, the optimum content of emulsified asphalt was determined to be about 4.0% by weight of aggregates (G90) using 50 gyrations.
Compared with the HMA, the compactibility of the CRME is more susceptible to construction temperatures. Nevertheless, most institutions often ignore the effect of temperature when designing CRME. It is, therefore, necessary to study the effect of compaction temperature on the CRME. In the lab, raw materials were first prepared with RAP, new aggregates, emulsified asphalt, and mixing water, which were placed in incubators at 5, 25, and 45°C, respectively. The materials were evenly mixed after the temperature has been maintained for about 6 h. Then the mixes were also placed in the incubator at mixing temperature for 2 h before compaction. The specimens were compacted for 50 gyrations using SGC. Figure 7 shows the effect of compaction temperature on the bulk density and the air voids content. The effect of compaction temperature on ITS value is displayed in Figure 8.
Figure 7 shows that as the compaction temperature increased, the bulk density of the specimen increased. As a contrast, the air voids content of the specimen significantly decreased as the compaction temperature increased. As the compaction temperature increased from 5 to 25°C, the bulk density of the specimen increased by about 7%, while the air voids content of the specimen decreased by about 6.1%. As the compaction temperature increased from 25 to 45°C, the bulk density increased by about 7%, while the air voids content decreased by about 13%. It exhibited that a higher compaction temperature can significantly improve the compactness of CRME.
Figure 8 shows that the ITSd, ITSw, and ITSR of the specimens increase significantly as the compaction temperature of CRME increases, especially when the compaction temperature of CRME increases from 5 to 25°C. At the compaction temperature of 5°C, the ITSd, ITSw, and ITSR were relatively low, which did not meet the requirements of JTG/T5521-2019. As the compaction temperature increased from 5 to 25°C, ITSd, ITSw, and ITSR increased by 15, 41, and 22%, respectively. As the compaction temperature increased from 25 to 45°C, and the ITSd, ITSw, and ITSR increased by 7, 13, and 5%, respectively. Based on the difference in ITS values at three compaction temperatures, the CRME specimens that were compacted at 25°C can obtain a good performance in terms of ITS and water stability. This can be attributed to the lower viscosity of asphalt at a higher compaction temperature. Since emulsion residue and recycled asphalt had lower viscosities when compacting at higher temperatures, the uniformity of wrapped aggregate increased, and more structural asphalt improved the tensile properties of cold recycled mixes. Besides, the viscosity of emulsified asphalt becomes smaller at higher temperatures, which was more likely for the internal movement of aggregates during the compaction process.
To further study the CRME compaction characteristics, the SGC method and modified Marshall methods were compared and analyzed at the compaction temperature of 25°C. Specimens were all in the same size, 63.5 mm in height and 100 mm in diameter. Five compaction modes and four emulsion contents were used. The specimens were compacted at four different gyrations (30, 50, 75, and 100) using the SGC method and at 75 blows using the Marshall method, separately. In addition, the four emulsion contents included 3.0, 3.5, 4.0, and 4.5% by weight of the aggregates. The air voids content and ITSd are shown in Figure 9 and Figure 10, respectively.
In Figure 9, the air voids content of the specimen decreases as the compact increases. When the gyratory number increased from 30 to 50 gyrations, the air voids content of the specimen decreased by more than 2.3%, while the ITSd increased by more than 0.15 MPa (Figure 10). The decrease of air voids content and the increase of ITSd slowed down after 50 gyrations. From 50 to 75 gyrations, the air voids content of the specimen decreased by 1.6%, and the ITSd increased by 0.08 MPa, which indicated that the effect of compaction after 50 gyrations on air voids content and ITS was insignificant. Base on that, it was also reasonable that CRME can be compacted for 50 gyrations using the SGC method.
In terms of air voids content and the ITSd value, the specimens with 75 blows using the modified Marshall method was equivalent to the specimens with around 45 gyrations using the SGC method. It was beneficial to establish the correspondence between the gyrations using the SGC method and the blows using the modified Marshall method in JTG/T5521-2019.
From the changing trend of ITSd with the content of emulsified asphalt, there was a maximum value of ITSd using SGC of 50 gyrations at the emulsified asphalt content of 4%, which the maximum ITSd is determined to be 0.85 MPa, and the specimen air voids content can be controlled at about 11.5%. The results indicated that the air voids content and strength well meet the specification (JTG/T5521-2019) requirements of the air voids content of 8–13%, and the strength greater than 0.4 MPa. At the same time, it was proved that it was reasonable and feasible to determine the optimum emulsified asphalt content by analyzing the compaction characteristic parameters.
To determine the optimum moisture content required for CRME, two sets of tests, including T1 (the optimum moisture content test using the heavy compaction method in JTG/E40-2007) and T2 (the optimum moisture content using the SGC) were analyzed and compared. The test results are shown in Figure 11.
In Figure 11, the maximum dry density of CRME is 2.035 g/cm3 from the T1 test, and the corresponding optimum mixing water of CRME is determined to be about 3.4%. As a contrast, the maximum dry density of CRME is 2.108 g/cm3 from the T2 test, and the corresponding optimum mixing water of CRME is determined to be about 2.8%, which the optimum moisture content is 4.053% by weight of aggregates. It was found that the optimum mixing water of CRME obtained by the SGC method was 0.6% smaller than that of the heavy compaction method, and the maximum dry density of CRME obtained by the SGC method was 3.6% higher than that of the heavy compaction method.
The results showed that the SGC method obtained a greater dry density than the heavy compaction method at the same mixing water content, which indicates the SGC method may more helpful for the CRME compaction. In practice, the optimum mixing water of CRME determined by the heavy compaction method was larger than on-site construction, which will cause a higher air voids content and additional costs. Therefore, it was recommended that the optimum moisture content of CRME should be determined using the SGC method.
To understand the relationship between moisture content and ITS, five groups of test specimens were compacted at 50 gyrations using the SGC method. The test results are shown in Figure 12.
It was observed that the maximum ITSd was about 0.75 MPa at 2.6% water content and the maximum ITSw was about 0.69 MPa at 2.7% water content, which meets the requirements of JTG/T 5521-2019. When the specimen ITS was at the maximum value, The CRME achieved almost the same optimum water content. Therefore, the results indicated that the density and strength of CRME had a positive correlation.
Based on the above research results, the CRME specimens were compacted for 50 gyrations at 25°C using the SGC method. The specimens used 4% emulsified asphalt and 2.6% mixing water (by weight of the aggregates). Technical performance was tested in the lab. As shown in Table 5, the test results can meet all the technical requirements of JTG/T5521-2019. The results suggested that the SGC method provides better overall performance, and can better meet the requirements of field application.
The compaction characteristics of CRME were studied in this paper. The main influencing factors, including aggregate gradation, the content of asphalt emulsion and moisture, the compaction temperature, and the compaction method were discussed. Based on the analysis of the results, the obtained conclusions can be summarized as follows:
(1) Five compaction characteristic parameters are proposed and derived. As a result, a new idea by analyzing the compaction characteristic parameters is used to determine the optimum emulsified asphalt content of the CRME. It is beneficial that appropriately increasing emulsion content and adding new aggregate in the mixture for deformation resistance under traffic loads.
(2) The asphalt emulsion content and compaction temperature have a significant effect on the compaction characteristics of the CRME, and the aggregate gradation has an insignificant effect. It is suggested to pave the CRME at the atmosphere temperature, which is higher than 25°C, to improve the road performance of the CRME.
(3) Compared with the heavy compaction method, the optimum mixing water content obtained by the SGC method is reduced by 18%, but the density is increased by 3.5%. This process avoids the problems of small compactness and high engineering cost caused by excess moisture.
(4) The gyratory method can be effectively applied to the CRME mixture design and it is a more realistic compaction method, which is close to the situation at the worksite. The mixture with 50 gyrations is close to that with 75 blows using the modified Marshall method and the mixture can achieve a high density and strength.
The raw data supporting the conclusions of this article will be made available by the authors, without undue reservation.
DW and HY conceived of this project and revised this artile. DW, JY, and SH drafted the article. JL, MX, and SC provided technical support for this project.
This work is supported by the National Key Research and Development Program of China (2018YFE0120200) and the National Natural Science Foundation of China (51878623).
The authors declare that the research was conducted in the absence of any commercial or financial relationships that could be construed as a potential conflict of interest.
Brovelli, C., and Crispino, M. (2012). Investigation into cold recycled materials: influence of rejuvenant, mix design procedure and effects of temperature on compaction. Constru. Build. Mater. 37 (12), 507–511. doi:10.1016/j.conbuildmat.2012.07.070
Casillas, S., and Braham, A. (2020). Quantifying effects of laboratory curing conditions on workability, compactability, and cohesion gain of cold in-place recycling. Road Mater. and Pavement Des. (4), 1–23. doi:10.1080/14680629.2020.1753101
DelRio-Prat, M., Vega-Zamanillo, A., Castro-Fresno, D., and Calzada-Perez, M. (2011). Energy consumption during compaction with a gyratory intensive compactor tester. Estimation models. Constru. Build. Mater. 25 (2), 979–986. doi:10.1016/j.conbuildmat.2010.06.083
Dessouky, S., Masad, E., and Bayomy, F. (2004). Prediction of hot mix asphalt stability using the superpave gyratory compactor. J. Mater. Civil Eng. 16 (6), 578–587. doi:10.1061/(asce)0899-1561(2004)16:6(578)
Flores, G., Gallego, J., Miranda, L., and Marcobal, J. (2020). Cold asphalt mix with emulsion and 100% rap: compaction energy and influence of emulsion and cement content. Constr. Build. Mater. 250 (7), 118804. doi:10.1016/j.conbuildmat.2020.118804
Flores, G., Gallego, J., Miranda, L., and Marcobal, J. (2019). Design methodology for in situ cold recycled mixtures with emulsion and 100% rap. Constr. Build. Mater. 216 (5), 496–505. doi:10.1016/j.conbuildmat.2019.05.042
Gao, L., Ni, F., Charmot, S., and Luo, H. (2014). Influence on compaction of cold recycled mixes with emulsions using the superpave gyratory compaction. J. Mater. Civil Eng. 26 (11), 1–8. doi:10.1061/(asce)mt.1943-5533.0000987
Hillgren, G., Svenson, A., and Wallin, T. (1989). “Asphalt Institute Manual series No 14,” in In-plant cold recycling and cold mix in Sweden-developments in laboratory testing. 3rd Edition.
Kim, Y. (2012). Performance evaluation of cold in place recycling mixtures using emulsified asphalt based on dynamic modulus, flow number, flow time, and raveling loss. KSCE J. Civil Eng. 16 (4), 586–593. doi:10.1007/s12205-012-1376-0
Kim, Y., and Lee, H. (2011). Influence of reclaimed asphalt pavement temperature on mix design process of cold in-place recycling using foamed asphalt. J. Mater. Civil Eng. 23 (7), 961–968. doi:10.1061/(asce)mt.1943-5533.0000274
Lee, K., Brayton, T., Mueller, M., and Singh, A. (2016). Rational mix-design procedure for cold in-place recycling asphalt mixtures and performance prediction. J. Mater. Civil Eng. 28 (6), 04016008. doi:10.1061/(ASCE)MT.1943-5533.0001492
Li, H., Gao, Y., and Yu, W. (2011). Compaction characteristics of hot mixed asphalt and number of roller passes. J. Southeast Univ. 41 (01), 186–189. doi:10.3969/j.issn.1001-0505.2011.01.036
Lin, J., Hong, J., and Xiao, Y. (2017). Dynamic characteristics of 100% cold recycled asphalt mixture using asphalt emulsion and cement. J. Clean. Prod. 156, 337–344. doi:10.1016/j.jclepro.2017.04.065
Martinez-Echevarria, M., Miro Recasens, R., Rubio Gamez, M., and Ondina, A. (2012). In-laboratory compaction procedure for cold recycled mixes with bituminous emulsions. Constr. Build. Mater. 36 (6), 918–924. doi:10.1016/j.conbuildmat.2012.06.040
MOC of PRC (2011). “Standard test method of bitumen and bituminous mixtures for highway engineering (JTG E20-2011),” in Ministry of Communications of the people’s Republic of China (Beijing: China Communications Press).
MOC of PRC (2004). “Technical specification for construction of highway asphalt pavements (JTG F40-2004),” in Ministry of Communications of the people’s Republic of China (Beijing: China Communications Press).
MOC of PRC (2019). “Technical specifications for highway asphalt pavement recycling (JTG T5521-2019),” in Ministry of Communications of the people’s Republic of China (Beijing: China Communications Press).
MOC of PRC (2007). “Test methods of soils for highway engineering (JTG E40-2007),” in Ministry of Communications of the people’s Republic of China (Beijing: China Communications Press).
Rodríguez-Fernández, I., Lastra-González, P., Indacoechea-Vega, I., and Castro-Fresno, D. (2019). Recyclability potential of asphalt mixes containing reclaimed asphalt pavement and industrial by-products. Constr. Build. Mater. 195, 148–155. doi:10.1016/j.conbuildmat.2018.11.069
Tarefder, R., and Ahmad, M. (2016). Effect of compaction procedure on air void structure of asphalt concrete. Measurement 90, 151–157. doi:10.1016/j.measurement.2016.04.054
Turk, J., Pranjić, A., Mladenovič, A., Cotič, Z., and Jurjavčič, P. (2016). Environmental comparison of two alternative road pavement rehabilitation techniques: cold-in-place-recycling versus traditional reconstruction. J. Clean. Prod. 121, 45–55. doi:10.1016/j.jclepro.2016.02.040
Wendling, L., Gaudefroy, V., Gaschet, J., Ollier, S., and Gallier, S. (2015). Evaluation of the compactability of bituminous emulsion mixes: experimental device and methodology. Constr. Build. Mater. 17 (1), 71–80. doi:10.1080/10298436.2014.925553
Xiao, F., Yao, S., Wang, J., and Amirkhanian, S. (2018). A literature review on cold recycling technology of asphalt pavement. Constr. Build. Mater. 180, 579–604. doi:10.1016/j.conbuildmat.2018.06.006
Yan, J. (2006). Asphalt pavement cold recycling design method and performance evaluation. Master thesis. Chongqing (China): Southeast University.
Keywords: pavement engineering, cold recycled mixture with asphalt emulsion, gyratory compaction, compaction characteristic parameters, compaction temperatures
Citation: Wang D, Yao H, Yue J, Hu S, Liu J, Xu M and Chen S (2021) Compaction Characteristics of Cold Recycled Mixtures with Asphalt Emulsion and Their Influencing Factors. Front. Mater. 8:575802. doi: 10.3389/fmats.2021.575802
Received: 24 June 2020; Accepted: 19 January 2021;
Published: 05 April 2021.
Edited by:
Yu-Fei Wu, RMIT University, AustraliaReviewed by:
Xiaoming Huang, Southeast University, ChinaCopyright © 2021 Wang, Yao, Yue, Hu, Liu, Xu and Chen. This is an open-access article distributed under the terms of the Creative Commons Attribution License (CC BY). The use, distribution or reproduction in other forums is permitted, provided the original author(s) and the copyright owner(s) are credited and that the original publication in this journal is cited, in accordance with accepted academic practice. No use, distribution or reproduction is permitted which does not comply with these terms.
*Correspondence: Hui Yao, aHVpeWFvQG10dS5lZHU=
Disclaimer: All claims expressed in this article are solely those of the authors and do not necessarily represent those of their affiliated organizations, or those of the publisher, the editors and the reviewers. Any product that may be evaluated in this article or claim that may be made by its manufacturer is not guaranteed or endorsed by the publisher.
Research integrity at Frontiers
Learn more about the work of our research integrity team to safeguard the quality of each article we publish.