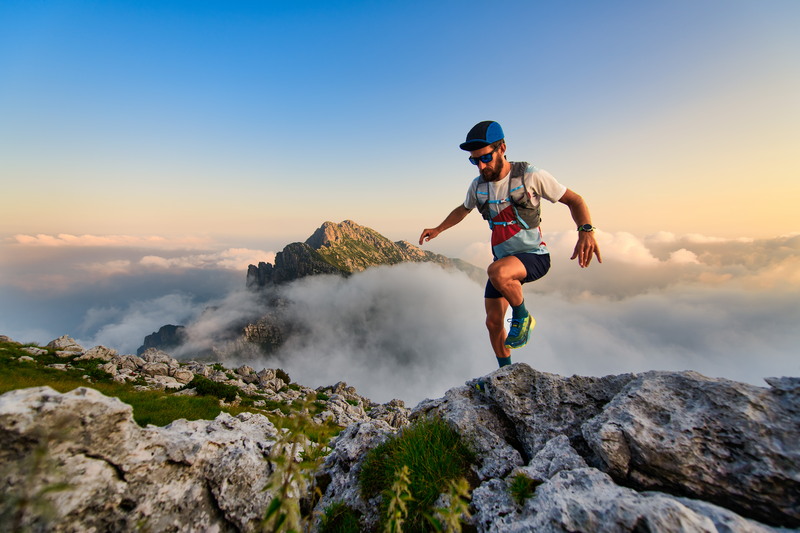
95% of researchers rate our articles as excellent or good
Learn more about the work of our research integrity team to safeguard the quality of each article we publish.
Find out more
ORIGINAL RESEARCH article
Front. Mater. , 13 January 2021
Sec. Structural Materials
Volume 7 - 2020 | https://doi.org/10.3389/fmats.2020.623864
This article is part of the Research Topic Lightweight Structural Metallic Materials View all 13 articles
A vacuum-induced multistage atomization process was adopted to fabricate the high-performance 304 stainless steel powder for 3D printing, based on the flexible control of the droplet spheroidization and solidification process. The 36.7 μm-median diameter (D50) 304 stainless steel powder with high sphericity was successfully obtained, together with particle size proportion of 45–55 μm larger than 35% and the lower oxygen and nitrogen content increment below 0.04%.
The 3D printing technique is an advanced forming process based on layer-by-layer “bottom-up” material stacking in the three-dimensional space. Compared with casting, forging, and other traditional processes, 3D printing suits for the near-net-shape forming of complex parts because it can significantly shorten the production period and save raw materials. Hence, 3D printing is regarded as a breakthrough technique in the new round of technological revolution and has been widely concerned worldwide (Jones, 2012; Preston et al., 2013).
Yang et al. prepared high-performance 316L stainless steel (σb = 755 MPa, δ = 18%) for vane wheels of high-precision planet gears using selective laser melting (SLM) (Yang et al., 2019). Khademzadeh, Tolosa, and Choi et al. found that metal powder particle size significantly affected the surface completeness and mechanical properties of 3D printing parts (Tolosa et al., 2010; Choi et al., 2012; Khademzadeh et al., 2015). Meier et al. reported that powder sphericity had an effect on the loose density, packed density, and fluidity of 3D printing parts (Meier et al., 2019). Park stated that the element purity (O, N) of 15-5ph stainless steel powder influenced the performance of 3D printing parts (Zhang et al., 2018). In terms processes (Lewandowski and Seifi, 2016; Bartolomeu et al., 2017; Ma et al., 2017; Suryawanshi et al., 2017; Fortunato et al., 2018; Kong et al., 2018), researchers believe that metal powder quality is one of the key factors influencing the forming process and the final performance of 3D printing [direct metal laser sintering (DMLS), SLM, laser-engineered net shaping (LENS), and electron beam melting (EBM)). Thus, preparation techniques of high-performance metal powder for 3D printing are of crucial importance.
In this study, contactless vacuum induction and multistage atomization flexible control were combined to improve the powder purity, particle size, and sphericity, which cannot be well tailored by the existing powder preparation processes, such as high-temperature plasma process and rotating electrode process. Finally, high-performance 304 stainless steel powder for 3D printing was successfully prepared.
The 304 stainless steel (AISI304) was selected as raw material, and a contactless induction heating and multistage atomization pressure flexible control process was used for powder preparation. During the preparation by EIGA, the quantity of 304 stainless steel powder from a single lot is 10 Kg. The process route involves as follows: 1) heating power W: 28 kW, 2) bar material feeding speed v: 0.04–0.06 mm/s, angular spin rate ω: 6 r/min; and 3) atomization stage pressure: 4.5–6–8 MPa, at an interval time of 7 s.
An 80-mesh screen was used for the 304 stainless steel powder. The morphology of powder was observed using a Gemini SEM 300 field-emission scanning electron microscope (SEM). Particle size and distribution were determined using a BETTERSIZE 2000 laser particle analyzer. The physical properties of powder were assessed through a BT1001 universal property analyzer. Elemental composition was analyzed by a chemical analytical method (ICP).
The scientific essence for preparation of metal powder for 3D printing is a continuous process of droplet spheroidization and solidified coupling of metal materials. Figure 1 shows the SEM images of 304 stainless steel powder prepared from a vacuum induction single-stage atomization process (8 MPa). It can be found that the large atomization pressure endowed the metal drops with large flying linear velocity, so the droplets were prone to ruleless collision and intensified breakage during atomization. Moreover, the surface of metal drops experienced very fast overcooling and solidification, leading to the ruleless and fast droplet solidification. Hence, the powder particles in this process were evenly distributed, and the median diameter D50 was determined as approximately 41.7 μm (Figure 2), but ellipsoidal or irregular powder was easily observed, so the entire powder sphericity was relatively low (Figure 1A).
FIGURE 1. Morphology of powder prepared from 304 stainless steel single-stage atomization process (atomization pressure: 8 MPa).
To address the above problem, we fully considered the spheroidization control of metal droplets to ensure the appropriate overcooling of metal droplets during solidification, and designed a multistage atomization flexible process (atomization pressure: 4.5–6–8 MPa, time interval: 7 s), based on the nozzle structure and the physical properties of 304 stainless steel (density and droplet fluidity). Figure 3 shows the SEM images of the powder, and the corresponding particle size was displayed in Figure 2.
FIGURE 3. Morphology of 304 stainless steel powder prepared from multistage atomization (atomization pressure: 4.5–6–8 MPa, interval 7 s).
At the initial stage of the multistage atomization process, as the pressure was approximately 4.5–6 MPa, the initial movement velocity of metal droplets and the gas flow of ring-like nozzle were flexibly controlled, and the motion path of metal droplets in the airflow field was distributed in order, which decreased the probability of ruleless collision of metal droplets. As the atomization pressure rose to 8 MPa, the droplets were rapidly solidified, and printed the nucleation and growth, causing the formation of smaller-size powder particles (Figure 3).
In addition, the distribution profile of peak particle diameter was left-shifted, indicating the present multistage atomization can increase the proportion of fine powder, and the final median diameter D50 was decreased to 36.7 μm (Figure 2). The overall sphericity of the powder was fine, and part of the powder slightly grew up (Figure 3A). Furthermore, these power particles were characterized by high surface quality, without fracture, convex, adhesion, or other defects (Figure 3B).
Table 1 lists the compositional analysis and physical properties of the present 304 stainless steel powder. The contactless vacuum induction multistage atomization process can effectively decrease the increment of O and N concentrations and can significantly improve the elemental purity during powder preparation. Moreover, the overall physical properties of the powder changed slightly and can meet the requirement for exclusive use in 3D printing.
TABLE 1. Chemical composition and physical properties of 304 stainless steel powder prepared from different atomization processes.
Thus, high-performance 304 stainless steel powder exclusive for 3D printing was successfully prepared, and the particle size proportion of 45–55 μm can reach approximately 40%. Through the multistage atomization process, the O and N elemental composition and overall physical properties—sphericity and particle size of 3D printing power—were flexibly controlled. Importantly, this process can also be used for preparation of other brands of stainless steels, such as 316L, or other metal material powder with similar density.
The high-performance 304 stainless steel metal powder exclusive for 3D printing was prepared by a vacuum induction multistage atomization process, which can improve the powder composition, overall physical properties, sphericity, and particle size by means of flexible control of multistage atomization pressure.
The original contributions presented in the study are included in the articlemanuscript/Supplementary Material, and further inquiries can be directed to the corresponding author.
XJ, LC, and GZ conceived of and designed the experiments; CT and XJ carried out the experiments; LC, JL, and XZ analyzed the data; XJ and XC wrote the manuscript.
This study was funded by the Liaoning Provincial Department of Finance (No. LQGD2017024), the National Natural Science Foundation (No. 51805335), and Liaoning Provincial Natural Science Foundation projects (No. 20180550998).
The authors declare that the research was conducted in the absence of any commercial or financial relationships that could be construed as a potential conflict of interest.
Thanks to the members of the research team.
Bartolomeu, F., Buciumeanu, M., Pinto, E., Alves, N., Carvalho, O., Silva, F. S., et al. (2017). 316L stainless steel mechanical and tribological behavior-A comparison between selective laser melting, hot pressing and conventional casting. Addit. Manuf. 16, 81–89. doi:10.1016/j.addma.2017.05.007
Choi, S., Sohn, I., and Lee, H. (2012). Femtosecond laser-induced line structuring on mold stainless steel STAVAX with various scanning speeds and two polarization configurations. Int. J. Precis. Eng. Manuf. 13, 845–854. doi:10.1007/s12541-012-0110-7
Fortunato, A., Lulaj, A., Melkote, S., Liverani, E., Ascari, A., and Umbrello, D. (2018). Milling of maraging steel components produced by selective laser melting. Int. J. Adv. Manuf. Technol. 94, 1895–1902. doi:10.1007/s00170-017-0922-9
Jones, N. (2012). Science in three dimensions: the print revolution. Nature. 487, 22–23. doi:10.1038/487022a
Khademzadeh, S., Parvin, N., and Bariani, P. F. (2015). Production of NiTi alloy by direct metal deposition of mechanically alloyed powder mixtures. Int. J. Precis. Eng. Manuf. 16, 2333–2338. doi:10.1007/s12541-015-0300-1
Kong, D., Ni, X., Dong, C., Lei, X., Zhang, L., Man, C., et al. (2018). Bio-functional and anti-corrosive 3D printing 316L stainless steel fabricated by selective laser melting. Mater. Des. 152, 88–101. doi:10.1016/j.matdes.2018.04.058
Lewandowski, J. J., and Seifi, M. (2016). Metal additive manufacturing: a review of mechanical properties. Annu. Rev. Mater. Res. 46, 151–186. doi:10.1146/annurev-matsci-070115-032024
Ma, M., Wang, Z., and Zeng, X. (2017). A comparison on metallurgical behaviors of 316L stainless steel by selective laser melting and laser cladding deposition. Mater. Sci. Eng. 685, 265–273. doi:10.1016/j.msea.2016.12.112
Meier, C., Weissbach, R., Weinberg, J., Wall, W. A., and Hart, A. J. (2019). Modeling and characterization of cohesion in fine metal powders with a focus on additive manufacturing process simulations. Powder Technol. 343, 855–866. doi:10.1016/j.powtec.2018.11.072
Preston, Z., Nickels, L., and Capus, J. (2013). 3D printing of plastic and titanium parts for racing bicycles. Met. Powder Rep. 68, 30–32. doi:10.1016/S0026-0657(13)70172-3
Suryawanshi, J., Prashanth, K. G., and Ramamurty, U. (2017). Mechanical behavior of selective laser melted 316L stainless steel. Mater. Sci. Eng. 696, 113–121. doi:10.1016/j.msea.2017.04.058
Tolosa, I., Garciandia, F., Zubiri, F., Zapirain, F., and Esnaola, A. (2010). Study of mechanical properties of AISI 316 stainless steel processed by “selective laser melting”, following different manufacturing strategies. Int. J. Adv. Manuf. Technol. 51, 639–647. doi:10.1007/s00170-010-2631-5
Yang, X., Liu, Y., Ye, J., Wang, R., Zhou, T-C., and Mao, B-Y. (2019). Enhanced mechanical properties and formability of 316L stainless steel materials 3D-printed using selective laser melting. Intl. J. Min Met Mater. 26, 1396–1404. doi:10.1007/s12613-019-1837-2
Keywords: metals and alloys, powder technology, multi-stage atomization, particle size distribution, sphericity
Citation: Jiang X, Che X, Tian C, Zhu X, Zhou G, Chen L and Li J (2021) Preparation of 304 Stainless Steel Powder for 3D Printing by Vacuum-Induced Multistage Atomization. Front. Mater. 7:623864. doi: 10.3389/fmats.2020.623864
Received: 30 October 2020; Accepted: 30 November 2020;
Published: 13 January 2021.
Edited by:
Minghui Cai, Northeastern University, ChinaReviewed by:
Ye Tian, Beijing Institute of Aeronautical Materials (BIAM), ChinaCopyright © 2021 Jiang, Che, Tian, Zhu, Zhou, Chen and Li. This is an open-access article distributed under the terms of the Creative Commons Attribution License (CC BY). The use, distribution or reproduction in other forums is permitted, provided the original author(s) and the copyright owner(s) are credited and that the original publication in this journal is cited, in accordance with accepted academic practice. No use, distribution or reproduction is permitted which does not comply with these terms.
*Correspondence: Xin Che, eGlhb3hpbjIwMDQwNjhAMTYzLmNvbQ==
Disclaimer: All claims expressed in this article are solely those of the authors and do not necessarily represent those of their affiliated organizations, or those of the publisher, the editors and the reviewers. Any product that may be evaluated in this article or claim that may be made by its manufacturer is not guaranteed or endorsed by the publisher.
Research integrity at Frontiers
Learn more about the work of our research integrity team to safeguard the quality of each article we publish.