- 1Department of Mechanical and Manufacturing Engineering, Manipal Institute of Technology, Manipal Academy of Higher Education, Manipal, India
- 2Department of Aeronautical and Automobile Engineering, Manipal Institute of Technology, Manipal Academy of Higher Education, Manipal, India
- 3Laboratory of Biocomposite Technology (BIOCOMPOSITE), Institute of Tropical Forestry and Forest Products (INTROP), Universiti Putra Malaysia, Serdang, Malaysia
- 4Department of Aerospace Engineering, Faculty of Engineering, Universiti Putra Malaysia, Serdang, Malaysia
- 5Aerospace Malaysia Innovation Centre (944751-A), Prime Minister’s Department, MIGHT Partnership Hub, Jalan Impact, Cyberjaya, Malaysia
In this study an attempt was made to explore the possibility of substituting 3D E-glass fabric with eco-friendly basalt fabric along with the modification of resin using MWCNTs, a material system about which very limited information exists. The study involved comparing the mechanical properties of two sets of composites. The first set was comprised of 3D orthogonally woven E-glass-reinforced epoxy composites, basalt-reinforced epoxy composites, and hybrid 3D E-glass orthogonally woven/basalt-reinforced epoxy composites while the second set of composites was the same as the first but prepared with resin modified with Multi Walled Carbon Nanotubes (MWCNTs). All the composites were fabricated by hand lay-up and compression molding techniques. To modify the resin for the second set of composites, MWCNTs were dispersed into the epoxy resin with acetone as a surfactant by magnetic stirring and ultra-sonification. Mechanical tests included tensile, flexural, and low velocity impact strength which were evaluated as per standards. Scanning electron microscopy (SEM) was employed to study the fractured surfaces. Results showed that resin modification did not yield any positive results on the mechanical properties of the composites. The highest tensile (364.4 MPa) and flexural strength (345.3 MPa) was obtained for 3D E-glass composites followed by basalt composites and hybrid 3D E-glass/basalt composites while the highest impact strength of 198.42 kJ/m2 was exhibited by the hybrid 3D E-glass/basalt composites. SEM micrographs showed de-bonding between the modified matrix and fiber which was seen as one of the primary causes for relatively poor performance of the composites prepared with modified resin. Fiber breakage, matrix cracking, fiber pull-out, and delamination were the other modes of failure. Results suggest that hybridization with basalt fibers is a much safer, more cost effective, and eco-friendly option over resin modification.
Introduction
With the growing concerns of environmental issues and the depletion of limited resources due to the overuse of synthetic and environmentally harmful materials has led to the recent advancement in biodegradable materials (Girijappa et al., 2019; Neuba et al., 2020). In foresight of such perilous times, the government has taken initiatives to preserve the balance of nature by implementing policies to make the best use of natural and renewable resources (Bajwa and Bhattacharjee, 2016; Papageorgiou, 2018). To accomplish such a goal, it is necessary that the manufacturers be provided with a plethora of environmentally friendly materials to choose from as substitutes for their current choices. Researchers have been actively working toward the production of green composites by experimenting with resins and fibers obtained from nature, and by making use of naturally derived materials (Väisänen et al., 2017; Peças et al., 2018; Souza et al., 2020; Vinod et al., 2020; Yorseng et al., 2020). They have attempted to replace the conventional materials used for the matrix and reinforcement. Not only are these composites beneficial to the environment but also drastically lower the cost of raw materials and manufacturing (Santos et al., 2020). Pure green composites are produced by combining biofibers and natural resins. Such composites can be disposed of at the end of the life span without harming the environment (Ramesh et al., 2020). Even though such characteristics are necessary, the demand for durability and superior performance of their synthetic alternatives is high, making it essential to find an intermediate entity. Therefore, hybrid composites have been developed for this purpose, which infuse the best of both of the available alternatives. This has been achieved by combining natural fibers and synthetic fibers in synthetic matrices (Asim et al., 2019; Mochane et al., 2019; Ricciardi et al., 2019).
In case of natural fiber-reinforced polymer matrix composites, comparable properties can be brought about with the use of the right configuration of reinforcement and matrix. Based on its origin, natural fibers may be classified into three different categories–plant, animal, and mineral-based fibers. Some commonly used plant fibers include Flax fibers, bamboo fibers, banana fibers, Kenaf fibers, Areca fibers, Sisal fibers, Borassus fruit fibers, Grewia Serrulata bast fibers, Coconut Coir fibers, Acacia Nilotica fibers, and Jute fibers (Mohammed et al., 2015; Mahesha et al., 2017; Nayak et al., 2020b; Heckadka et al., 2020; Shenoy et al., 2020). Animal based fibers include silk obtained from butterfly larvae and spiders, and wool obtained from alpaca, angora, qiviut, and chicken feathers (Sanjay et al., 2018). One of the more popular mineral fibers is basalt, which has recently gained popularity as composite reinforcement. An optimal combination of mechanical properties can be forged by combining synthetic as well as natural fibers. This involves manipulation of the stacking sequence of fibers in the case of woven mats. Bio-based materials not only refer to natural fibers but also to polymers (George et al., 2020).
Currently, natural fiber-reinforced polymer matrix composites have been able to achieve mechanical properties on par with or sometimes even greater than glass fiber-reinforced polymer matrix composites (Shaker et al., 2020). This could be easily worked out with the help of hybridization, wherein synthetic fibers are introduced along with natural fibers, and an optimal stacking sequence is used. Hybridization can impart the positives of both the alternatives to the resultant composite. Many natural fibers such as bamboo fibers, areca fibers, Borassus fibers, and basalt fibers have been used with E-glass fibers because of their light weight, low cost, and biodegradability (Girijappa et al., 2019).
In the research conducted by Patel et al. (2020) on basalt-glass hybrid composites, they reported that a pure basalt fiber-reinforced polyester composite panel possessed the highest tensile as well as flexural strength of 333.8 MPa and 361 MPa, respectively. The all glass composite possessed the second highest flexural strength of 328 MPa and the lowest tensile strength of 191.6 MPa. The hybrid composites followed two separate stacking sequences, either with basalt fiber or glass fibers on the outer layers. Both the panels reported similar flexural strengths of 199 MPa and 204 MPa whereas the panel with glass fiber on the outer layers produced a higher tensile strength (264.6 MPa) in contrast to the panel with basalt fiber on the outer layers. Abd El-Baky et al. (2020) studied the influence of hybridization on flax fiber-reinforced epoxy composites with glass and basalt fibers. The non-hybrid glass fiber composite panel reported the highest tensile strength of 264.43 MPa, preceding the glass and basalt hybrid panel, which had a tensile strength of 225.99 MPa. This was higher than the tensile strength of the non-hybrid basalt composite panel (184.74 MPa). The non-hybrid glass fiber composite panel also reported the highest flexural and impact strength of 272.73 MPa and 261.56 kJ/mm2, respectively. The hybrid glass/basalt panel had a flexural and impact strength of 194.54 MPa and 212.41 kJ/mm2, respectively. Overall, the hybrid panel was seen to possess properties intermediary to the two extremes i.e., non-hybrid glass and basalt panels. They concluded by calling hybridization a way to achieve comparable properties at a lower cost and weight in contrast to the non-hybrid panels. Andrew and Ramesh (2015) studied the residual strength and compression after impact properties of glass-basalt hybrid composites. They subjected the non-hybrid glass and basalt panels and the hybrid glass basalt panel to a low velocity impact under an impact energy of 2.17 J. The impacted specimens were then subjected to compression tests and a comparison was drawn between the panels. They reported that the GFRP laminate possessed a maximum impact stiffness of 501.64 N/mm which was far higher than the basalt and hybrid counterparts. They concluded by saying that basalt was not an effective replacement for glass fiber laminates, especially in a configuration where basalt was used as a skin layer in a hybrid. Fiore et al. (2011) studied the influence on the mechanical properties of GFRPs by the virtue of hybridization with uniaxial basalt fiber layers. Every lamina out of six available laminas in the glass fiber-reinforced composites were subsequently replaced by basalt fibers and the effect was studied. An increment of 118% in flexural modulus was observed in the composite panel where the outer layers were of basalt (19.5 GPa). Similarly, 45% higher tensile strength than GFRP was reported in the same panel (210.3 MPa), and a 70% increase in tensile modulus (14.1 GPa) from the GFRP.
The properties of polymer matrix composites can also be manipulated through the addition of reagents and fillers (Hemath et al., 2020). The reagents consist of coupling agents which basically help in the interfacial adhesion of two dissimilar materials, in this case the multi-walled carbon nanotubes (MWCNT) and the matrix. Fillers, on the other hand, are one kind of reinforcement which are added in a very small amount to the matrix. These can be either natural or synthetic (Dinesh et al., 2020; Setty et al., 2020). In the case of synthetic fillers, the most widely used fillers are MWCNTs, which are also known as nano fillers. The addition of a filler to the polymers can bring about a change in the properties of the matrix resulting from the filler-filler and filler-matrix connection at a nano or micro level (Korayem et al., 2014; Yang et al., 2014; Ismail et al., 2018).
Rathore et al. (2016) studied the mechanical performance of MWCNT-filled glass/epoxy composites focusing on the optimal content of the CNT required. The epoxy was modified by dispersing CNT effectively by sonication. A total of 0.1%wt of MWCNT samples reported 32.8% and 11.5% increment in flexural strength and flexural modulus. This is validated by the SEM images which show that 0.1%wt of MWCNT has the best dispersion in the polymer matrix. Venkatesan et al. (2019) studied the effect of CNT addition as a filler in epoxy composites and glass fiber-reinforced epoxy composites. They varied the percentage of CNT in the resin at 1%, 3%, and 5%, and subjected the fabricated composites to impact tests. The results reported were in support of CNT-filled glass fiber-reinforced epoxy composites which reported a heavy increase in impact strength when 1% (w/w) CNT was filled in the epoxy resin. CNT is known to form agglomerates if not dispersed properly. Chaudhary et al. (2018) performed a study on the effect of CNT on the ILSS of plain-woven glass fabric and epoxy composites. They found CNT to be decremental toward the interlaminar properties if agglomeration took place within the matrix of the composite.
From the referred literature, so far, the usage of MWCNTs in E-glass composites has had a positive effect on the mechanical properties of PMCs. Also basalt composites and basalt-based hybrid composites have shown promising results. But, limited information exists with regard to mechanical properties of hybrid 3D E-glass/basalt-reinforced epoxy composites. Also, there appears to be a knowledge gap with the use of MWCNT in such composites. Therefore, a proposal of a composite system that could leverage between the increase in properties through the addition of a synthetic, eco-friendly, cost-effective, and non-toxic filler through hybridization with a natural fiber reinforcement was seen to be necessary. This research work involves a systematic approach toward improving the properties of a 3D E-glass orthogonal fiber-reinforced epoxy composite. One method employed to achieve this was hybridization with a natural fiber using a fixed compression ratio and another method included the modification of the epoxy resin by dispersing MWCNTs using ultrasonic mixing. Subsequently, a combination of both was explored in this research in order to study the interactions of both the modification techniques. Hence, the effect of these modification techniques on the tensile strength, flexural strength, and impact strength were investigated.
Materials and Methods
Materials
For the fabrication of composites, 3D E-glass orthogonally woven fabric with an areal density of 1830 gsm procured from Fibermax Composites, Greece and plain woven basalt fabric of an areal density of 300 gsm procured from Composites Tomorrow, were used. Epoxamite slow curing resin A103 along with its designated hardener were selected for this study and were imported from Smooth-On Inc., USA. Multi Walled Carbon Nanotubes (MWCNTs) of a diameter in the range of 6–9 nm and a length in the range of 5–10 µm were supplied by ZKK Sdn. Bhd., Selangor, Malaysia.
Fabrication of Composites
Composites were fabricated by hand lay-up and compression molding techniques. The laid up composite laminates were pressed into the molding machine with a compression factor of 1.4 to achieve a target fiber volume fraction of around 50% (Nayak et al., 2020a). Pressing of laid up composite laminates helps in better consolidation, improved bonding between the constituents, and also helps in reducing the void content. For lay-up, an open mold consisting of two mild steel (MS) plates were used. The lay-up was done on one of the MS plates while the other was placed over the lay-up. The lay-up with the two MS plates were later moved to the compression molding machine where it was pressed. To achieve the required thickness, precise machined spacer blocks were placed between the two MS plates before pressing.
Six different types of composites of 300 mm × 150 mm × 4 mm were fabricated, the details of which are presented in Table 1. Of the six composites, three were fabricated with epoxy modified with 0.5% wt. MWCNTs. CNTs have a high tendency to form agglomerates, due to their high surface energy. These clumps hinder efficient stress transfer and induce micro-defects in the composite matrix (Jen and Wang, 2012). To get a better dispersion, the following method was utilized. First, MWCNTs were added to acetone in the ratio of 1:15 and mixed thoroughly using a magnetic stirrer at room temperature. The mixture was then sonicated using a sonicator probe. The process of stirring and sonication was repeated with the addition of resin. Acetone was removed from the modified epoxy by heating the mix at 70°C (Nor et al., 2019). The polymer epoxy resins used for fabrication are relatively viscous and hence possess a damping property, which can result in the attenuation of ultrasonic waves (Ma et al., 2010). This is the reason why low viscosity solvents such as water, ethanol, and acetone are used. The MWCNTs are known to have a weaker interaction with the matrices in which they are dispersed. However, the ultrasonic waves produced through sonication act as impulses, which result in the removal of agglomerates and nanoparticles from the surface of the MWCNTs. This causes an increased interaction between the polymer matrix and MWCNTs.
Figure 1 schematically shows the resin modification and fabrication of composites with modified resin. For the other three laminates, the epoxy resin was directly mixed with the hardener in the ratio of 28.4:1. During the hand lay-up, the resin was applied on the fabrics by a brush. The curing of all composites was carried out at room temperature under pressed conditions for 24 h.
Hybrid composites were fabricated by replacing one middle layer of 3D E-glass fabric by six layers of basalt fabric and thus the areal density of all the composites was maintained. Hybrid composites were fabricated with 3D E-glass fabric as skin reinforcement since the material system being studied here was for impact application and current literature suggested the use of synthetic reinforcement on the outside for such applications (Yahaya et al., 2014; Salman et al., 2016; Salman et al., 2017; Nayak et al., 2020c); hence the effect of the stack sequence on the mechanical properties was not an objective here.
Mechanical Testing of Composites
Tests for mechanical properties such as tensile and flexural strength were conducted on a Zwick Roell Universal Testing Machine (UTM) (Model:Z020). The tensile test was carried out as per ASTM D3039 (ASTM, 2017) at a constant cross head speed of 2 mm/min whereas the flexural test (3 point) was carried out as per ASTM D7264 (ASTM, 2015) at a constant cross head speed of 1 mm/min. Charpy impact tests were conducted on a Zwick Roell Pendulum impact tester (Model: HIT 50P) as per ISO 179-1 (ISO, 2010) where the specimen were subjected to an energy of 22 J. For each of the tests, five samples were used and an average was arrived at. Specimen for all the tests were prepared using a jig saw cutter.
Scanning Electron Microscopy
A Scanning Electron Microscope (SEM) (Zeiss EVO 18 Special Edition) was used to study the damaged surfaces of the tested specimens. The specimens were sputtered with gold and palladium prior to scanning. An accelerating voltage of 15 kV was employed, and the machine was operated under both variable pressure and high vacuum mode.
Results and Discussion
Tensile and Flexural Strength
The tensile strength of a composite is the maximum tensile stress it can withstand before any failure. The variation in tensile strength among various composites is presented in Figure 2. EGC composites were seen to possess the highest tensile strength of 364.4 MPa, preceding the EBC and HGB composites at 346.3 MPa and 348.3 MPa, respectively. MEG was seen to have a tensile strength of 253.8 MPa which was about 30% lower than EG. Similarly, MEB and the MHC were seen to possess tensile strengths of 44% and 37% (194.6 MPa and 218.2 MPa) lower than the EBC and HGB composites. It can be observed that the tensile strength values of the HGB and EBC are very close, i.e., 348.3 MPa and 346.3 MPa, respectively, and are closer to the tensile strength of the EGC (364.4 MPa) than pure 3D E-glass composites since, the glass fabric had been replaced by layers of basalt fabric. In addition to this, basalt fibers, as natural fibers, do not harm the environment when disposed off after its life cycle.
An overall decrement was seen in the values of tensile strength of the CNT modified epoxy composites. Sonication may have caused the long polymer chains to break into smaller chains thereby reducing the strength of the matrix (Rokita et al., 2005; Paulusse and Sijbesma, 2006). The drop in strength of the composites prepared with modified resin could be primarily attributed to the poor strength of the matrix. Probe sonication is known to damage the structure of CNTs and can be seen as a reason for the poor performance of resin modified composites (Gou et al., 2012; Huang and Terentjev, 2012). A drop in strength could also be due to the poor interfacial properties between the glass fibers, basalt fibers, and the modified matrix. A weak fiber-matrix interface results in weak interfacial adhesion leading to poor stress transfer among the constituents, causing failure phenomena such as matrix cracking, fiber de-bonding, and relative movement of fibers all resulting in premature failure of the composites (Rizal et al., 2018). The effect of a poor fiber-matrix interface was more prevalent between modified resin and basalt fibers when compared to glass fibers which explains the significant drop in tensile strength of MEB composites when compared to that of EBC composites. On the other hand, though there was a drop in tensile strength for MEG composites over EGC composites (about 30%); the drop was less when compared with the drop in tensile strength of MEB composites over EBC composites (44%) which can be attributed to the relatively higher tensile strength of the glass fibers. The improved performance of the MHC composites can again be attributed to the presence of E-glass fibers along with basalt fibers.
The flexural strengths of the composites are shown in Figure 3. The modulus of rupture, i.e., flexural strength, was used to evaluate the bending strength of the composite. EGC composites reported a maximum flexural strength of 345.3 MPa, followed by EBC and HGB. Like the tensile strength results, a detrimental trend in flexural strength was observed as well. The flexural strength decreased by about 40%, 44%, and 39% for MEG, MEB, and MHC, respectively when compared to EGC composites. It can be inferred that even though EGC was superior to all other combinations in terms of flexural strength, EBC was not too far behind in its performance. Dalinkevich et al. (2009) compared basalt fibers with E-glass and S-glass fibers and reported similar findings. This further promotes the appeal of substituting synthetic fibers with natural ones.
Figure 4 shows the lateral view of a failed flexural test specimen. Delamination was not visible in the case of EGC composites (Figure 4A) while excessive delamination was seen among the basalt plies of the HGB and MHC composites (Figures 4B,C). This delamination can be seen as the primary reason for the poor performance of composites with basalt fabric. Though delamination was not visible as seen in composites with basalt plies, the layers appeared to have lost adherence in the case of MEG composites as shown in Figure 4D. Ineffective bonding between individual laminae can cause such delamination and can be overcome by using either coupling agents or treating the basalt fabric using chemical or physical means (Dhand et al., 2015). In the case of the hybrid composites (HGB), the effect of a poor fiber-matrix interface was compounded due to the presence of a different material in the 3D E-glass fabric. As seen with the tensile properties, the addition of CNT to the epoxy did not prove to be beneficial for the flexural properties of the composite. Poor fiber matrix-fiber interfacial properties along with ineffective bonding among the basalt layers and with the glass fabric results in the dismal performance of the modified resin composites when compared to the composites fabricated with unmodified resin.
Impact Strength
Impact strength is the maximum energy that can be absorbed when the composite panel is subject to a sudden impact. It is usually measured in terms of intensity of energy absorbed (kJ/m2). Impact properties of composites are influenced by the mechanism of energy absorption and dissipation in materials. Figure 5 presents the average impact strength for each of the investigated composites. HGB was seen to have the highest impact strength of 198.42 kJ/m2 followed by EBC while EGC was reported to have the lowest strength of 118.65 kJ/m2. Despite the fact that resin modification moderately improved the strength of the E-glass composite by 19%, basalt and hybrid composites encountered a decrease of 17% and 36%, it can be concluded that the modification of resin had the lowest significance in the enhancement of energy absorption. Also, it can be observed that a change of fibers had a significant influence on the impact properties of the composites with unmodified resin while in the case of modified resin the change of fibers had the least influence on the impact properties of the composites.
Traditionally 3D E-glass composites have been known to outperform other synthetic fibers due to the presence of binder yarn (Khatkar et al., 2020).
It is believed that the impact energy is absorbed and translates into delamination of the layers (Wisnom, 2012). In the case of HGB composites, the introduction of basalt fabrics led to an increase in the number of interfaces when compared to EBC composites. Improved impact properties can be attributed to the synergistic effect of superior impact properties of 3D fabric and the efficient absorption of energy through the core of the composite comprised of basalt fabric. Poor impact properties of the composites with modified resin can be again attributed to poor fiber-matrix interfaces. The use of basalt to achieve hybridization can certainly be seen as advantageous. Where the addition of CNTs provided an improvement of 19%, hybridization achieved up to a 67% improvement from a pure glass composite, while saving the time and energy required in modifying the resin. Not only is it favorable in terms of reinforcement but it is also a safe and eco-friendly alternative.
Scanning Electron Microscopy
Figure 6 shows the images of the tensile specimens of EGC, MEG, MEB, HCB, and MHC. Figure 6A shows the fractured surface of the EGC specimen. The structure of the 3D fabric is seen clearly with fibers in both directions with warp and weft standing out distinctly. The fibers appear broken, bent, and disoriented indicating that the fiber bundles snapped due to the tensile loading. Matrix cracking is also seen toward the bottom right of the image. Fiber pull-out due to the tensile load is also seen which appear as dark tiny holes among the fiber bundles. Figure 6B shows the fractured surface of the HGB specimen. It can be noted that the basalt fibers are of a comparatively smaller diameter than the E-glass fibers, hence a clear distinction can be drawn between the two in the picture. Similar to EGC in Figure 6A, here also the fibers can be seen to have undergone fiber snapping, as the fibers are visible out of plane. In the direction normal to the viewing plane, there are multiple dark spots visible, indicating fiber pull-out. Phenomena such as fiber bending can also be seen. Delamination can be seen which is highly visible in the central portion of the failed surface, where the basalt fibers are dominant indicating a weak interfacial bonding. This validates delamination as an important cause for the lesser tensile strength of EBC (346.3 MPa) than EGC, which had a tensile strength of 364.4 MPa. Also, delamination is comparatively less in EGC than EBC. Figure 6C presents the micrograph of MEG’s fractured surface. Extensive delamination is seen which validates the reason for the 30% drop in tensile strength (253.8 MPa) in comparison to EGC (364.4 MPa).
Figure 6D shows the micrograph of the failed MEB specimen. Disorientation among the basalt fibers is similar to what is seen in Figure 6B, giving an indication that the basalt fibers experienced a higher amount of relative sliding between the fibers. This relative movement could be due to poor interfacial properties between the CNT-modified matrix and basalt fibers in general, resulting in the de-bonding of the basalt fibers and the modified matrix, hence causing higher slippage. Failure mechanisms like fiber splitting and delamination is also visible. This delamination can be seen as a common factor in cases where basalt fibers are used, namely the already discussed HGB and MEB. Moreover debris of the matrix can also be seen giving an indication of a brittle failure of the matrix. The micrograph of the failed tensile MHC specimen is shown in Figure 6E. As seen in the earlier SEM micrographs, fiber snapping is visible in the case of basalt fibers. The degree of disorientation in the case of basalt fibers is relatively higher in comparison to the E-glass strands. Since the central portion of the hybrid laminate, either fabricated with modified epoxy or pure epoxy, is only basalt fiber, there is a fairly visible amount of delamination, which is similar to Figures 6B,D. This further confirms that the dominant failure mechanism in the case of composite panels wherein basalt fibers are used is delamination. Though fiber pull-out is visible, when compared to the basalt fibers, glass fibers appear to have held themselves together with minimal snapping of the individual fibers.
Figure 7 illustrates the SEM micrographs of the fractured impact specimens. A clear distinction between the warp and weft directional fibers can be seen in Figure 7A. The presence of orthogonal binder in the z-direction holds the fibers in place, hence a sort of clean fractured surface is observed. In the case of impact loading, the binder yarn promotes crack branching and deviation from the center plane (Dahale et al., 2019). As the impact wave propagates along the z-direction, the impact energy is dissipated amongst the fiber layers. Therefore, delamination is unlikely to occur amongst E-glass fiber laminates so long as the binder yarn can provide out-of-plane damage resistance. As observed, little to no delamination is present amongst the fabric layers. However, multiple sites of fiber pull-out are present which are perceived as tiny dark holes on the surface of the laminate. A few loose, snapped fibers can be seen as well. The snapping of fibers is a common characteristic of fractured impact specimens. The number of snapped fibers is greater and can be clearly seen in Figure 7B which is the SEM micrograph of the MEG composite, indicating poor stress transfer between the matrix and reinforcement phase. Nonetheless, delamination occurs in the laminate. A greater extent of damage is observed in the MEG impact specimen with regard to that of EGC. This provides evidence to support the fact that MEG specimens can absorb a higher amount of energy, which is in coherence with the results seen in Figure 5. In Figure 7C (EBC composite) the fractured surface appears to be disoriented to a much higher degree when compared to the E-glass composites (EGC). With impact loading, the wave is propagated through the composite, and for the composite to be successful, the impact energy should be dissipated through it. The energy is absorbed and is translated into relative displacement and the damage of fibers. The extent of damage is evident from the micrograph. Broken fibers, snapping of fibers, and delamination between the layers is also visible. To maintain the areal density, eighteen plies of basalt fabric were used to fabricate the composite; this results in an increased number of interfaces. The interfacial bonding is overcome due to the absorption of impact energy and results in delamination. The absence of binder yarn as well, promotes delamination between the layers. This explains the improved performance of the EBC composites over EGC composites.
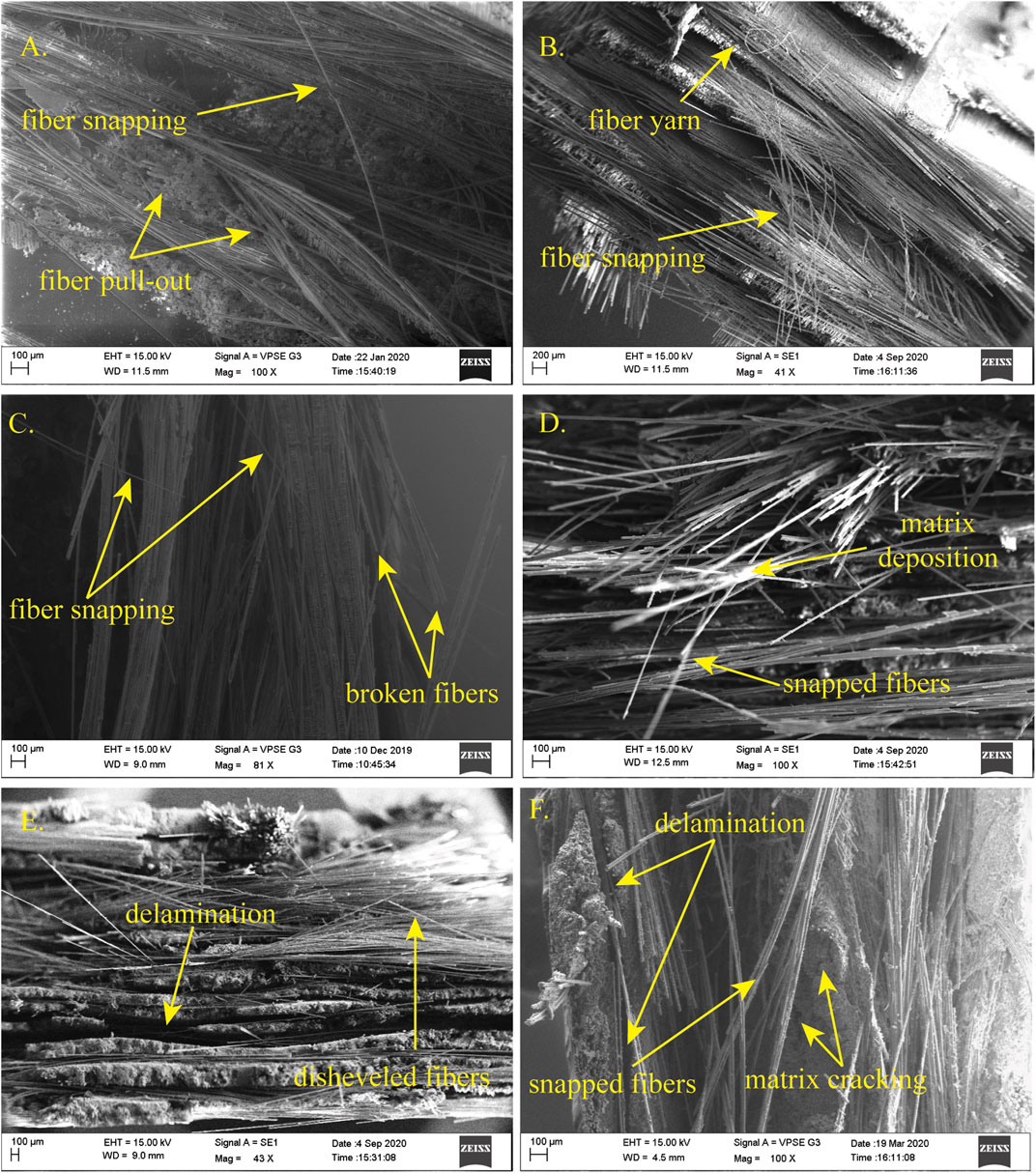
FIGURE 7. SEM micrographs for impact specimens. (A) EGC, (B) MEG, (C) EBC, (D) MEB, (E) HGB, (F) MHC.
On examining Figure 7D, which is the SEM micrograph of the MEB composite, similar characteristics of fiber pull-out, delamination, and fiber snapping as of EBC are seen. The disheveled fibers project outward resulting in a disorganized fracture surface for MEB which made it difficult to notice the failure features. It should be noted that certain protruding fibers have clumps of the CNT-infused matrix coated around them, while other fiber strands appear to have a clean skin. The inference one can deduct from this is that there may have been a problem of wetting with the fibers. The basalt fibers may not have adhered well with the modified resin which led to the reduction in performance of the MEB composites.
In Figure 7E, the 3D E-glass fabric at the bottom surface appears to have remained intact, however due to a possible split in the binder yarn the glass fabric at the top surface may have unfolded when the impact load was applied. The interaction between the glass and basalt fabrics had an important role to play in determining the impact strength of the composite. Characteristics such as fiber pull-out, delamination, and fiber snapping are shown with the arrows. Delamination is the feature most prominent between the core basalt fabric layers. Examining the impact strength results and the SEM micrographs, it can be inferred that, as the impact wave propagated within the composite, the dissipated energy was largely absorbed by the basalt layers that provided a sort of cushioning effect to the composite. Figure 7F presents the micrograph of the fractured surface of the MHC composites. Delamination among the layers of glass fabric can be seen. It should be noted that the direction of impact was from left to right of the specimen in the image. Thus it is clear that the immediate effect of the impact load caused layers to delaminate. Propagation of the impact wave caused the fibers to snap which otherwise were all held by the binder yarn. In addition to delamination and snapping of fibers, cracking of the matrix is also visible.
Figure 8 shows magnified views of the tensile specimens of EBC, MEB, EGC, and MEG and explains the interaction between the matrix and the fibers. The cross section of basalt fibers in pure epoxy can be seen in Figure 8A. The matrix seems to be very well bonded with the fiber strand, indicating a good compatibility between the epoxy matrix and the basalt fabric. This explains the comparable strengths of the basalt fiber-reinforced composite EBC. Visibly, the matrix has remained intact for the most part, except for a few bits surrounding the fiber strand, this shows that the matrix in itself retained its properties and the fiber-matrix interaction also did not seem to have a negative effect on the properties of EBC.
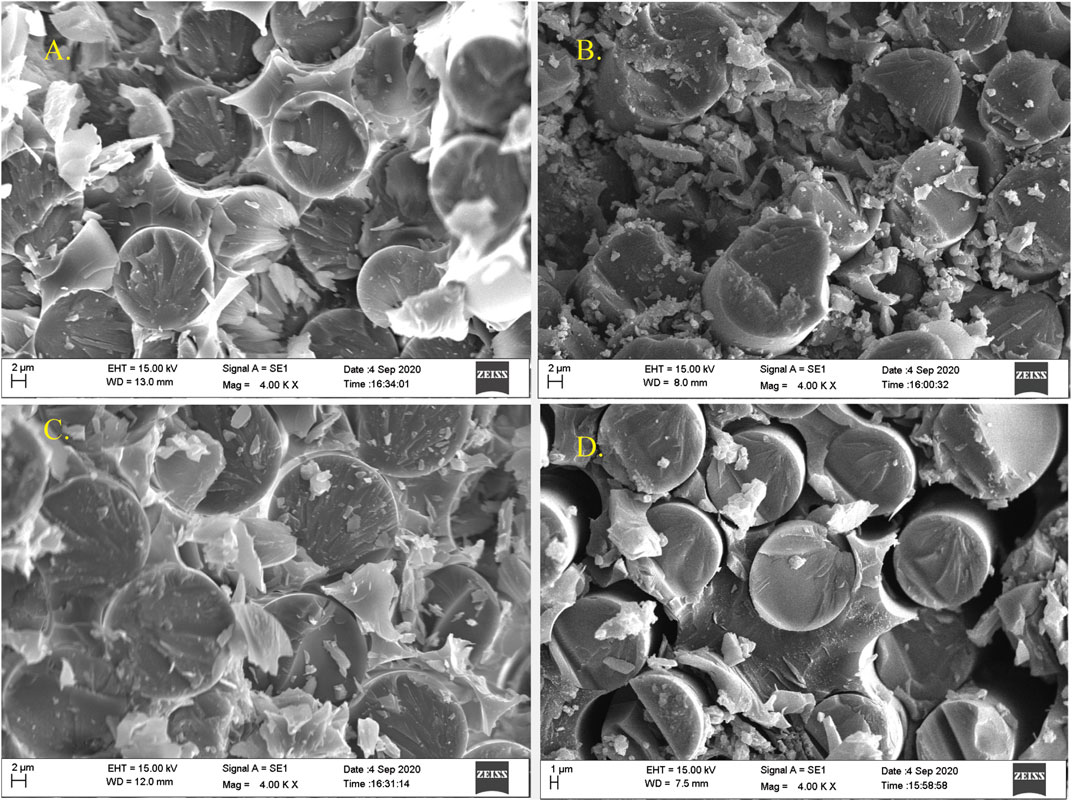
FIGURE 8. SEM micrographs showing the interaction between the resin and the fibers. (A) EBC, (B) MEB, (C) EGC, (D) MEG.
From Figure 8B, which is the SEM micrograph of the failed tensile MEB specimen, one can observe a significant amount of chips of the matrix surrounding the fiber strands. It appears that the inclusion of MWCNTs in the epoxy matrix has caused it to become brittle, possibly due to breakage of long polymer chains as a result of sonication. Although the spread of the matrix seems to be uniform in the composite, there are visibly dark areas surrounding the fiber strands, which indicate fiber matrix de-bonding, which is mostly concealed by the broken pieces of the brittle modified epoxy matrix. This de-bonding can be largely attributed to poor interfacial properties between the basalt fiber and MWCNT-modified epoxy. This is in contrast to the case of Figure 8A, wherein epoxy bonded very well with the basalt fibers, indicating that MWCNT-modified resin led to the deterioration of the fiber matrix interfacial properties.
Figure 8C shows a highly magnified micrograph of the failed surface of the EGC tensile specimen. The enclosure of the fiber strands by the matrix in this case is also very much similar to that in Figure 8A. This again implies a good bonding between the E-glass fibers and the epoxy matrix as the resin is comparatively well behaved in the presence of a long polymer chain. From the micrograph, it appears that the degree of this enclosure of the fibers by the matrix in the case of EGC is even higher than EBC. This explains the higher tensile strength of EGC (364.4 MPa) compared to that of EBC (346.3 MPa). To support this, there is also no visible fiber-matrix de-bonding, instead a uniform amount of matrix surrounding each fiber strand is observed.
Figure 8D shows the surface of the failed MEG tensile specimen. Though the matrix spread around the fibers appears to be uniform, there is a very high degree of fiber matrix de-bonding visible. The degree of de-bonding is quite high when compared with those shown in Figures 8A–C again emphasizing the poor fiber-matrix interface with modified resin. CNT dispersed in the resin is also seen and does not appear to be distributed uniformly. A higher magnification SEM micrograph (Figure 9) taken from the area between the fibers seen in Figure 8D confirms the non-uniform dispersion of the CNTs in the matrix. The clustering of CNTs in the cavity formed due to fiber pull-out is also seen. The resin used in this work is a slow curing resin and has a relatively low viscosity. This allows for gravity segregation of the CNTs, resulting in the deposition of CNT on the fiber surface and the formation of clusters within the resin system as seen in Figure 9. The formation of clusters leads to non-uniform stress transfer while the deposition of CNT on the surface of the fibers results in ineffective bonding at the fiber-matrix interface. This also can be seen as one of the reasons for the poor performance of the composites prepared with modified epoxy.
Conclusion
Three-dimensional orthogonally woven E-glass fabric reinforced epoxy composites, basalt plain woven reinforced epoxy composites, and hybrid epoxy composites with 3D E-glass and basalt fabric were fabricated. Another set of similar composites were fabricated with epoxy resin modified with MWCNTs. Mechanical properties that included tensile, flexural, and impact strengths of all the composites were determined and compared. Results indicated that the tensile strength of the three composites with epoxy resin were almost on par with each other, the highest tensile strength (364.4 MPa) was observed for 3D E-glass epoxy composites. Flexural strength was the highest for 3D E-glass epoxy composites at 345.3 MPa. Basalt composites and 3D E-glass/basalt hybrid composites reported reduced flexural strength. The highest impact strength was observed to be for 3D E-glass/basalt hybrid composites which was 198.42 kJ/m2. Epoxy modification had a negative influence over the mechanical properties of the composites. Relatively poor bonding among the basalt layers was seen as the major reason for the reduced strength of basalt and hybrid composites while the expending of energy in the delamination of successive basalt layers with better performance of 3D fabric owing to its non-crimp nature and the presence of binder yarn were seen as the primary reason for improved performance of the 3D E-glass/basalt hybrid composite. A poor fiber-matrix interface due to resin modification was seen as the reason for the overall poor performance of the composites fabricated with modified resin. Delamination, fiber breakage, snapping of fibers, and fiber-matrix de-bonding were some of the major modes of failure as seen from SEM micrographs. From the results, it can be concluded that 3D E-glass/basalt hybrid composites which are comparatively less expensive, more environmentally friendly, and have reduced health hazards show promise and have the potential to be used as a material system for applications such as automotive interiors and bumpers, and moderately loaded household and office application like doors, window panes, and partitions.
Data Availability Statement
The original contributions presented in the study are included in the article/Supplementary Material, further inquiries can be directed to the corresponding authors.
Author Contributions
SN: Conceptualization, methodology, formal analysis, writing–original draft, and investigation. SB: Supervision, formal analysis, and writing–review and editing. MS: Writing–review and editing. CK: Project administration. AS: Resources and investigation. SP: Resources and investigation. SS: Writing–review and editing.
Funding
Universiti Putra Malaysia, Geran Putra Berimpak (GPB-9668200).
Conflict of Interest
The authors declare that the research was conducted in the absence of any commercial or financial relationships that could be construed as a potential conflict of interest.
Acknowledgments
The authors would like to thank Universiti Putra Malaysia for the financial support through the Geran Putra Berimpak (GPB-9668200). The authors would like to thank the Department of Mechanical and Manufacturing Engineering, Manipal Academy of Higher Education, Manipal, Karnataka, India, the Department of Aeronautical and Automobile Engineering, Manipal Academy of Higher Education, Manipal, Karnataka, India, the Department of Aerospace Engineering, Faculty of Engineering, Universiti Putra Malaysia, and the Laboratory of Biocomposite Technology, Institute of Tropical Forestry and Forest Product (INTROP), Universiti Putra Malaysia (HICOE) for their close collaboration in this research.
References
Abd El-Baky, M. A., Attia, M. A., Abdelhaleem, M. M., and Hassan, M. A. (2020). Flax/basalt/E-glass fibers reinforced epoxy composites with enhanced mechanical properties. J. Nat. Fibers 229, 1–15. doi:10.1080/15440478.2020.1775750
Andrew, J., and Ramesh, C. (2015). Residual strength and damage characterization of unidirectional glass–basalt hybrid/epoxy CAI laminates. Arab. J. Sci. Eng. 40, 1695–1705. doi:10.1007/s13369-015-1651-8
Asim, M., Jawaid, M., Paridah, M. T., Saba, N., Nasir, M., and Shahroze, R. M. (2019). Dynamic and thermo-mechanical properties of hybridized kenaf/PALF reinforced phenolic composites. Polym. Compos. 40, 3814–3822. doi:10.1002/pc.25240
ASTM D3039/D3039M-17. (2017). Standard test method for tensile properties of polymer matrix composite materials. West Conshohocken, PA: ASTM International. www.astm.org.
ASTM D7264/D7264M-15. (2015). Standard test method for flexural properties of polymer matrix composite materials. West Conshohocken, PA: ASTM International. www.astm.org.
Bajwa, D. S., and Bhattacharjee, S. (2016). Current progress, trends and challenges in the application of biofiber composites by automotive industry. J. Nat. Fibers 13, 660–669. doi:10.1080/15440478.2015.1102790
Chaudhary, S. K., Singh, K. K., and Venugopal, R. (2018). Effect of using carbon nanotubes on ILSS of glass fiber-reinforced polymer laminates. Trans. Indian Inst. Met. 71, 3029–3036. doi:10.1007/s12666-018-1404-y
Dahale, M., Neale, G., Lupicini, R., Cascone, L., McGarrigle, C., Kelly, J., et al. (2019). Effect of weave parameters on the mechanical properties of 3D woven glass composites. Compos. Struct. 223, 110947. doi:10.1016/j.compstruct.2019.110947
Dalinkevich, A. A., Gumargalieva, K. Z., Marakhovsky, S. S., and Soukhanov, A. V. (2009). Modern basalt fibrous materials and basalt fiber-based polymeric composites. J. Nat. Fibers 6, 248–271. doi:10.1080/15440470903123173
Dhand, V., Mittal, G., Rhee, K. Y., Park, S. J., and Hui, D. (2015). A short review on basalt fiber reinforced polymer composites. Compos. B Eng. 73, 166–180. doi:10.1016/j.compositesb.2014.12.011
Dinesh, S., Kumaran, P., Mohanamurugan, S., Vijay, R., Singaravelu, D. L., Vinod, A., et al. (2020). Influence of wood dust fillers on the mechanical, thermal, water absorption and biodegradation characteristics of jute fiber epoxy composites. J. Polym. Res. 27, 175. doi:10.1007/s10965-019-1975-2
Fiore, V., Di Bella, G., and Valenza, A. (2011). Glass-basalt/epoxy hybrid composites for marine applications. Mater. Des. 32, 2091–2099. doi:10.1016/j.matdes.2010.11.043
George, A., Sanjay, M. R., Sriusk, R., Parameswaranpillai, J., and Siengchin, S. (2020). A comprehensive review on chemical properties and applications of biopolymers and their composites. Int. J. Biol. Macromol. 154, 329–338. doi:10.1016/j.ijbiomac.2020.03.120
Girijappa, T. Y. G., Mavinkere Rangappa, S., Parameswaranpillai, J., and Siengchin, S. (2019). Natural fibers as sustainable and renewable resource for development of eco-friendly composites: a comprehensive review. Front. Mater. 6, 1–14. doi:10.3389/fmats.2019.00226
Gou, J., Zhuge, J., and Liang, F. (2012). “Processing of polymer nanocomposites” in Manufacturing Techniques for polymer Matrix composites (PMCs). (New York: Woodhead Publishing), 95–119.
Hemath, M., Mavinkere Rangappa, S., Kushvaha, V., Dhakal, H. N., and Siengchin, S. (2020). A comprehensive review on mechanical, electromagnetic radiation shielding, and thermal conductivity of fibers/inorganic fillers reinforced hybrid polymer composites. Polym. Compos. 41, 3940–3965. doi:10.1002/pc.25703
Huang, Y. Y., and Terentjev, E. M. (2012). Dispersion of carbon nanotubes: mixing, sonication, stabilization, and composite properties. Polymers 4, 275–295. doi:10.3390/polym4010275
Ismail, K. I., Sultan, M. T. H., Shah, A. U. M., Mazlan, N., and Ariffin, A. H. (2018). Tensile properties of hybrid biocomposite reinforced epoxy modified with Carbon Nanotube (CNT). BioResources 13, 1787–1800. doi:10.15376/biores.13.1.1787-1800
ISO 179-1:2010 (2010). Plastics—determination of Charpy impact properties—part 1: non-instrumented impact test.
Jen, Y. M., and Wang, Y. C. (2012). Stress concentration effect on the fatigue properties of carbon nanotube/epoxy composites. Compos. B Eng. 43, 1687–1694. doi:10.1016/j.compositesb.2012.01.036
Khatkar, V., Vijayalakshmi, A. G. S., Manjunath, R. N., Olhan, S., and Behera, B. K. (2020). Experimental investigation into the mechanical behavior of textile composites with various fiber reinforcement architectures. Mech. Compos. Mater. 56, 367–378. doi:10.1007/s11029-020-09888-0
Korayem, A. H., Barati, M. R., Simon, G. P., Zhao, X. L., and Duan, W. H. (2014). Reinforcing brittle and ductile epoxy matrices using carbon nanotubes masterbatch. Compos. Part A Appl. Sci. Manuf. 61, 126–133. doi:10.1016/j.compositesa.2014.02.016
Ma, P. C., Siddiqui, N. A., Marom, G., and Kim, J. K. (2010). Dispersion and functionalization of carbon nanotubes for polymer-based nanocomposites: a review. Compos. Part A Appl. Sci. Manuf. 41, 1345–1367. doi:10.1016/j.compositesa.2010.07.003
Mahesha, G. T., Satish, S. B., Kini, M. V., and Subrahmanya, B. K. (2017). Mechanical characterization and water ageing behavior studies of Grewia Serrulata bast fiber reinforced thermoset composites. J. Nat. Fibers 14, 788–800. doi:10.1080/15440478.2017.1279103
Mochane, M. J., Mokhena, T. C., Mokhothu, T. H., Mtibe, A., Sadiku, E. R., Ray, S. S., et al. (2019). Recent progress on natural fiber hybrid composites for advanced applications: a review. Express Polym. Lett. 13, 159–198. doi:10.3144/expresspolymlett.2019.15
Mohammed, L., Ansari, M. N. M., Pua, G., Jawaid, M., and Islam, M. S. (2015). A review on natural fiber reinforced polymer composite and its applications. Int. J. Polym. Sci. 24, 3–9. doi:10.1155/2015/243947
Nayak, S. Y., Satish, S. B., Sultan, M. T. H., Kini, C. R., Rajath Shenoy, K., Samant, R., et al. (2020a). Influence of fabric orientation and compression factor on the mechanical properties of 3D E-glass reinforced epoxy composites. J. Mater. Res. Technol. 9, 8517–8527. doi:10.1016/j.jmrt.2020.05.111
Nayak, S. Y., Sultan, M. T. H., Shenoy, S. B., Kini, C. R., Samant, R., Shah, A. U. M., et al. (2020b). Potential of natural fibers in composites for ballistic applications–A review. J. Nat. Fibers 178, 1–11. doi:10.1080/15440478.2020.1787919
Nayak, S. Y., Shenoy, B. S., Sultan, M. T. B. H., Kini, C. R., Shenoy, K. R., Acharya, A., et al. (2020c). Influence of stacking sequence on the mechanical properties of 3D E-glass/bamboo non-woven hybrid epoxy composites. Mater. Today Proc. 16, 385. doi:10.1016/j.matpr.2020.07.385
Neuba, L. D. M., Pereira, F., and Ribeiro, M. P. (2020). Properties of novel epoxy composites reinforced with Cyperus malaccensis sedge fiber. Polymers 12, 1776.
Nor, A. F. M., Sultan, M. T. H., Jawaid, M., Azmi, A. M. R., and Shah, A. U. M. (2019). Analysing impact properties of CNT filled bamboo/glass hybrid nanocomposites through drop-weight impact testing, UWPI and compression-after-impact behaviour. Compos. B Eng. 168, 166–174. doi:10.1016/j.compositesb.2018.12.061
Papageorgiou, G. Z. (2018). Thinking green: sustainable polymers from renewable resources. Polymers 10, 952. doi:10.3390/polym10090952
Patel, N., Patel, K., Chaudhary, V., and Gohil, P. (2020). Investigations on drilling of hybrid basalt/glass polyester composites. Aust. J. Mech. Eng. 64, 1–10. doi:10.1080/14484846.2020.1784560
Paulusse, J. M. J., and Sijbesma, Rint. P. (2006). Ultrasound in polymer chemistry: revival of an established technique. J. Polym. Sci. Polym. Chem. 44, 5445–5453. doi:10.1002/pola.21646
Peças, P., Carvalho, H., Salman, H., and Leite, M. (2018). Natural fibre composites and their applications: a review. J. Compos. Sci. 2, 66. doi:10.3390/jcs2040066
Ramesh, M., Deepa, C., Kumar, L. R., Sanjay, M. R., and Siengchin, S. (2020). Life-cycle and environmental impact assessments on processing of plant fibres and its bio-composites: a critical review. J. Ind. Textil. 21, 1528. doi:10.1177/1528083720924730
Rathore, D. K., Prusty, R. K., Kumar, D. S., and Ray, B. C. (2016). Mechanical performance of CNT-filled glass fiber/epoxy composite in in-situ elevated temperature environments emphasizing the role of CNT content. Compos. Part A Appl. Sci. Manuf. 84, 364–376. doi:10.1016/j.compositesa.2016.02.020
Ricciardi, M. R., Papa, I., Lopresto, V., Langella, A., and Antonucci, V. (2019). Effect of hybridization on the impact properties of flax/basalt epoxy composites: influence of the stacking sequence. Compos. Struct. 214, 476–485. doi:10.1016/j.compstruct.2019.01.087
Rizal, S., Ikramullah, D. A., Thalib, S., Huzni, S., and Abdul Khalil, H. P. S. (2018). Interfacial compatibility evaluation on the fiber treatment in the Typha fiber reinforced epoxy composites and their effect on the chemical and mechanical properties. Polymers 10, 1316. doi:10.3390/polym10121316
Rokita, B., Czechowska-Biskup, R., Ulanski, P., and Rosiak, J. M. (2005). Modification of polymers by ultrasound treatment in aqueous solution. E-polymers 15, 1–12. doi:10.1515/epoly.2005.5.1.261
Salman, S. D., Leman, Z., Sultan, M. T., Ishak, M. R., and Cardona, F. (2016). Ballistic impact resistance of plain woven. BioResources 11, 7282–7295.
Salman, S. D., Leman, Z., Sultan, M. T. H., Ishak, M. R., and Cardona, F. (2017). Effect of kenaf fibers on trauma penetration depth and ballistic impact resistance for laminated composites. Textil. Res. J. 87, 2051–2065. doi:10.1177/0040517516663155
Sanjay, M. R., Siengchin, S., Parameswaranpillai, J., Jawaid, M., Pruncu, C. I., and Khan, A. (2018). A comprehensive review of techniques for natural fibers as reinforcement in composites: preparation, processing and characterization. Carbohydr. Polym. 207, 108–121. doi:10.1016/j.carbpol.2018.11.083
Santos, F., Garcia, C., Oliveira, M. S., Fabio, L., Nascimento, C., and Monteiro, S. N. (2020). Composites with natural fibers and conventional materials applied in a hard armor: a comparison. Polymers 12, 1920.
Setty, S. N. V. K., Govardhan, G., Mavinkere Rangappa, S., and Siengchin, S. (2020). Raw and chemically treated bio-waste filled (Limonia acidissima shell powder) vinyl ester composites: physical, mechanical, moisture absorption properties, and microstructure analysis. J. Vinyl Addit. Technol. 21, 787. doi:10.1002/vnl.21787
Shaker, K., Nawab, Y., and Jabbar, M. (2020). “Bio-composites: eco-friendly substitute of glass fiber composites”, in Handbook of nanomaterials and nanocomposites for energy and environmental applications. (Cham: Springer), 1–25. doi:10.1007/978-3-030-11155-7_108-1
Shenoy Heckadka, S., Nayak, S. Y., Kamath, C. R., Adarsh, S. P., and Samant, R. (2020). Characterization of a novel polyalthia Longifolia mid-rib fibers as a potential reinforcement for polymer composites. J. Nat. Fibers 881–13. doi:10.1080/15440478.2020.1798847
Shenoy, H. S., Pai Ballambat, R., Kini Manjeshwar, V., Kumar, M., Hegde, P., and Kamath, A. (2020). Influence of stack sequence on the mechanical characteristics of hybrid composites analyzed using cone beam computed tomography and scanning electron microscopy. Polym. Compos. 24, 774. doi:10.1002/pc.25774
Souza, A. T., Pereira, F., Neuba, L. D. M., Clay, A., Rangel, A., and Azevedo, G. D. (2020). Caranan fiber from mauritiella armata palm tree as novel reinforcement for epoxy composites. Polymers 12, 2037.
Väisänen, T., Das, O., and Tomppo, L. (2017). A review on new bio-based constituents for natural fiber-polymer composites. J. Clean. Prod. 149, 582–596. doi:10.1016/j.jclepro.2017.02.132
Venkatesan, M., Palani Kumar, K., and Rajendra Boopathy, S. (2019). Analysis of toughness in multi-walled carbon nano tubes for resin and resin glass fiber composites. Mater. Today Proc. 16, 367–373. doi:10.1016/j.matpr.2019.05.103
Vinod, A., Siengchin, S., and Parameswaranpillai, J. (2020). Renewable and sustainable biobased materials: an assessment on biofibers, biofilms, biopolymers and biocomposites. J. Clean. Prod. 120, 978. doi:10.1016/j.jclepro.2020.120978
Wisnom, M. R. (2012). The role of delamination in failure of fibre-reinforced composites. Philos. Trans. R. Soc. A Math. Phys. Eng. Sci. 370, 1850–1870. doi:10.1098/rsta.2011.0441
Yahaya, R., Sapuan, S. M., Jawaid, M., Leman, Z., and Zainudin, E. S. (2014). Quasi-static penetration and ballistic properties of kenaf-aramid hybrid composites. Mater. Des. 63, 775–782. doi:10.1016/j.matdes.2014.07.010
Yang, J., Xiao, J., and Zeng, J. (2014). Matrix modification with silane coupling agent for carbon fiber reinforced epoxy composites. Fibers Polym. 14, 759–766. doi:10.1007/s12221-013-0759-2
Yorseng, K., Rangappa, S. M., Pulikkalparambil, H., Siengchin, S., and Parameswaranpillai, J. (2020). Accelerated weathering studies of kenaf/sisal fiber fabric reinforced fully biobased hybrid bioepoxy composites for semi-structural applications: morphology, thermo-mechanical, water absorption behavior and surface hydrophobicity. Construct. Build. Mater. 235, 117464. doi:10.1016/j.conbuildmat.2019.117464
Keywords: 3D E-glass composite, basalt epoxy composites, hybrid composites, CNT fillers, sonication, mechanical properties, scanning electron microscopy
Citation: Nayak SY, Shenoy S, Hameed Sultan MT, Kini CR, Seth A, Prabhu S and Safri SNA (2021) Effect of CNT-Based Resin Modification on the Mechanical Properties of Polymer Composites. Front. Mater. 7:609010. doi: 10.3389/fmats.2020.609010
Received: 22 September 2020; Accepted: 21 December 2020;
Published: 29 January 2021.
Edited by:
Rhys Jones, Monash University, AustraliaReviewed by:
Fabrizio Sarasini, Sapienza University of Rome, ItalySanjay Mavinkere Rangappa, King Mongkut’s University of Technology North Bangkok, Thailand
Copyright © 2021 Nayak, Shenoy, Hameed Sultan, Kini, Seth, Prabhu and Safri. This is an open-access article distributed under the terms of the Creative Commons Attribution License (CC BY). The use, distribution or reproduction in other forums is permitted, provided the original author(s) and the copyright owner(s) are credited and that the original publication in this journal is cited, in accordance with accepted academic practice. No use, distribution or reproduction is permitted which does not comply with these terms.
*Correspondence: Satish Shenoy, c2F0aXNoLnNoZW5veUBtYW5pcGFsLmVkdQ==; Mohamed Thariq Hameed Sultan, dGhhcmlxQHVwbS5lZHUubXk=