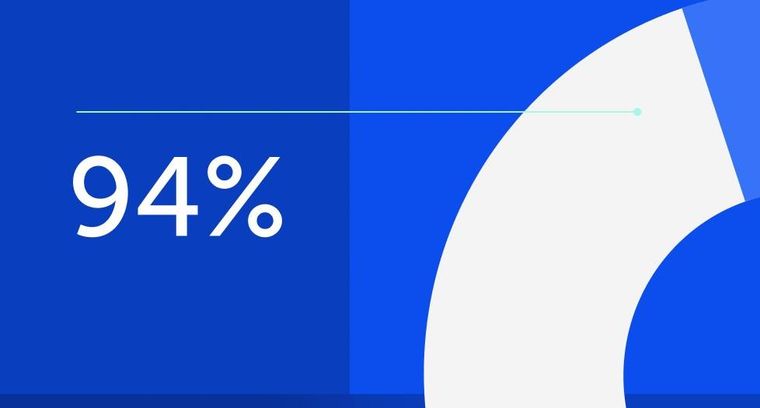
94% of researchers rate our articles as excellent or good
Learn more about the work of our research integrity team to safeguard the quality of each article we publish.
Find out more
MINI REVIEW article
Front. Mater., 27 November 2020
Sec. Structural Materials
Volume 7 - 2020 | https://doi.org/10.3389/fmats.2020.602522
This article is part of the Research TopicAdvances in Steel Manufacturing and ProcessingView all 7 articles
Dephosphorization has always been a challenging task in the steelmaking process. In the traditional studies, CaO-based steelmaking slag was usually treated as a homogeneous liquid phase to analyze the dephosphorization equilibrium between molten slag and hot metal (slag/metal). In fact, the slag shows a coexisting state of both liquid and solid at steelmaking temperature. In recent years, multi-phase slag refining has been proposed and proved to be an efficient technique to improve the utilization of solid lime and the dephosphorization efficiency in steelmaking practices. The present review focuses on hot issues for the multi-phase slag refining, including the dissolution of solid lime to the molten slag, the formation of 2CaO·SiO2 and phosphorus-rich solid solution of 2CaO·SiO2-3CaO·P2O5, as well as the phosphorus distribution ratio between the solid and liquid phases in the multi-phase slag. In addition to the discussion on thermal and kinetic factors of dephosphorization, the necessity of further research is proposed on the dissolution behavior of phosphorus-rich solid solution and phosphorus redistribution in the slag of high temperature, high basicity and high FeO in the final stage of converter steelmaking. Then, a more applicable dynamic model of dephosphorization could be expected considering the equilibrium not only between molten slag and liquid metal but also among the phases of the multi-phase slag in steelmaking process. Furthermore, the modelling work is beneficial for the fine control of the BOF process and the development of intelligent manufacturing in steelmaking industry.
Dephosphorization is always the major but challenging task in the steelmaking process. CaO-based fluxes are widely used in hot metal pretreatment process and basic oxygen steelmaking process to form dephosphorization slags, which consist of CaO-SiO2-P2O5-FetO-(MgO, MnO, Al2O3, …) systems. Dephosphorization reaction in the steelmaking process and phosphorus equilibrium between liquid iron and molten slag have been extensively studied since the 1940’s (Assis et al., 2015). On the basis of studies on the relationship between phosphorus distribution and slag composition as well as temperature, different phosphorus partition (LP) equations were obtained (Turkdogan and Pearson, 1953a; b; Healy, 1970; Gaskell, 1982; Mori, 1984; Suito and Inoue, 1984a; Bergman, 1988; Ogawa et al., 2001; Lee and Fruehan, 2005). Since the physicochemical effects of the solid-liquid coexisting phase in the slag have not been clarified yet, the slag was regarded as a homogeneous liquid phase to analyze the two-phase slag-metal equilibrium in those researches.
It is well known that tricalcium phosphate (3CaO·P2O5) is the main product of the dephosphorization reaction in the steelmaking process, as well as 2CaO·SiO2 is the main calcium silicate in the CaO-based steelmaking slag. According to the phase diagram of the CaO-SiO2-P2O5 system, a solid solution can be easily formed by 2CaO·SiO2 (C2S) and 3CaO·P2O5 (C3P) in a wide composition range at the steelmaking temperature (Fix et al., 1969). Since a large phosphorus partition ratio between the C2S-C3P solid solution and the liquid slag has been observed (Ito et al., 1982), the importance of solid phase in the slag for dephosphorization has been taken a growing attention by Japanese researchers. The concept of multi-phase slag refining was firstly proposed by Japanese researchers, and the multi-phase slag was also called multi-phase flux or meso-phase slag (Inoue and Suito, 2006a; Hamano et al., 2006). The Iron and Steel Institute of Japan (ISIJ) organized a research group on the multi-phase slag refining for dephosphorization in the steelmaking process, which consisted of 11 university professors and 10 industry researchers. Researches on this subject were conducted from year 2005 to 2009, and the results were published in Tetsu-to-Hagané as a special issue on the “Innovative Development of Refining Processes in Steelmaking by Multi-Phase Fluxes” (Tsukihashi, 2009). A new reaction model for hot metal dephosphorization was proposed by Kitamura et al.(2009), taking into account the effects of C2S solid phase and lime dissolution, as well as the interactions of the solid and liquid phases in molten slag, in addition to the reaction between hot metal and liquid slag. Finally, the MPSR (Multi-Phase Slag Refining) model for simulation of hot metal dephosphorizaiton process was developed, and applied to five steelmaking companies with good performance (Kitamura et al., 2014). Furthermore, the commercial thermodynamic software FactSage was also used for modelling of dephosphorizaiton process in BOF converter (Jung et al., 2014; Khadhraoui et al., 2018).
The present review focuses on hot issues for the multi-phase slag refining, including the lime dissolution into the molten slag, the formation of 2CaO·SiO2 and 2CaO·SiO2-3CaO·P2O5 solid solution, and the distribution ratio of phosphorus between the solid and liquid phases in the slag, as well as the modeling of dephosphorization by multi-phase slag. Moreover, the necessity of some further researches is proposed by the authors.
Phosphorus removal from liquid metal can be described by the ionic or molecular reactions, as shown in Equations (1) and (2), respectively (Drain et al., 2017).
Known from the equations, the phosphorus removal is affected by [P] activity, oxygen potential [O] and basicity (O2-). And the temperature also has a significant effect on the reaction, as given in Equation (3) (Turkdogan, 2000a).
The incorporation of liquid phosphorus pentoxide (P2O5) into the CaO and FeO containing steelmaking slags can be represented by Equation (4) or Equation (5).
The enrichment possibility Ncj of five probable structural units containing P2O5 as
Consequently, the dephosphorization reaction in the steelmaking process can be described as Equation (6) by combining Equation (2) and Equation (4), and the equilibrium constant for this reaction is given as Equation (7).
In most cases, hot metal dephosphorization slag and BOF slag consist of CaO-SiO2-FetO-P2O5, and the industrial operations are carried out in the C2S saturated region (Pahlevani et al., 2010). A solid solution of C2S with C3P can be formed at steelmaking temperature over a wide composition range (Fix et al., 1969). Lv and Wang (Lv et al., 2017) considered that the dephosphorization process could be composed of two segments as “oxidation dephosphorization” and “solid phosphorus”. Though, the “oxidation dephosphorization” indicates the reaction between liquid metal and molten slag given by Equation (6) in traditional studies, and the “solid phosphorus” may indicate the formation of phosphorus-rich solid solution C2S-C3P in the multi-phase slag.
The limit of dephosphorization reaction is determined by the phosphorus equilibrium between liquid metal and molten slag, which can be expressed in several forms, such as equilibrium constants (
Where, (%P) is the phosphorus content in molten slag, and [%P] is the phosphorus content in liquid metal.
Some representative formulas for LP calculation in CaO-SiO2-P2O5-FetO-X(X: MgO, MnO, Al2O3, …) systems are selected from literatures, as shown in Table 1.
As shown in Table 1, the influence of slag composition on LP mainly represents in three forms, i.e., component concentration, basicity and theoretical optical basicity.
Turkdogan et al. (Turkdogan and Pearson, 1953a; Turkdogan and Pearson, 1953b) considered that the FetO content in the slag has a decisive influence on the degree of steel dephosphorization, and the slag-metal reactions in steelmaking practices are far from the equilibrium states (Turkdogan, 2000b). The effect of FetO on the phosphorus partition was taken into account for all of the LP calculation formulas shown in Table 1 in different forms. Since the CaO content has a notable effect on the activity of P2O5 in the slag, it was introduced to correct the LP calculation by (Healy, 1970). In addition, the effects of MgO and MnO content on the dephosphorization equilibrium were studied by Suito and Inoue (1984b). Besides, some other LP calculation formulas were proposed using the optical basicity of the slag (Gaskell, 1982; Mori, 1984; Bergman, 1988). In the studies of Ogawa et al. (2001) and Lee and Fruehan (2005), LP was calculated using the binary or multi-basicity of the slag. There are also some other LP calculation formulas obtained in different researches (Suito and Inoue, 1995; Monaghan et al., 1998; Basu et al., 2007), but represented in the same three forms.
In the above studies, the slag was treated as a homogeneous single phase and tended to be in a state of thermodynamic equilibirum. However, since the actual slag is not a completely homogeneous liquid phase, and the industrial process is often difficult to reach the theoretical equilibrium. Therefore, it is obviously not enough to study the phosphorus equilibrium between liquid metal and molten slag. The thermodynamics and kinetics of the interactions between the solid and liquid phases in the multi-phase slag should also be considered.
The multi-phase slag refining was firstly proposed by Tsukihashi, and most of the relative researches were conducted by Japanese researchers, due to the popularization of hot metal pretreatment technology in Japan since the 1980s, the restricted use of fluorspar for environmental reasons (Ogawa and Maruoka, 2014; Sone et al., 2019). The researches mainly focus on the lime dissolution and the formation of phosphorus-condensed solid solution, as well as the phosphorus distribution between solid solution and liquid slag, and dephosphorization models including multi-phase slag interactions.
As well known, the melting temperature of CaO is over 2,500°C, which is an indispensable component for the high melting point phase in the steelmaking slag. The progress of slag-metal reactions in steelmaking process is largely influenced by the CaO content in the molten slag, and therefore by the dissolution rate of solid lime. Consequently, aiming to clarify the dissolution behavior of solid lime to the molten slag, laboratory experiments were conducted in the dynamic or static conditions.
When a lime particle dissolves into the CaO-SiO2 or CaO-SiO2-Al2O3 or CaO-SiO2-FeO melt, a layer of 2CaO·SiO2 is confirmed to be formed on the periphery of lime particle, and the increasing temperature and the addition of CaF2 or TiO2 can accelerates the dissolution rate of CaO as well as that of the 2CaO·SiO2 layer (Kimura et al., 1974; Amini et al., 2007; Deng and Du, 2012).
In another laboratory experiment of sintered CaO rod rotating in CaO-SiO2-Al2O3 or CaO-SiO2-FeO slag, the thickness of the C2S layer was obviously affected by the FeO content in the slag, and the dissolution rate of solid lime in FeO-containing slag was much greater than that in FeO-free slag (Matsushima et al., 1976; Matsushima et al., 1977; Yang et al., 2007). Meanwhile, the formation of Al2O3 or FeO rich slag layer between solid lime and the C2S layer were also observed, due to the penetration of Al2O3 and FeO into solid lime. But in these studies, the formation and dissolution of the C2S layer had not been paid enough attention, until it was found by (Yang et al., 2007) to have a significant inhibitory effect on the dissolution of lime, and the removal of the C2S layer by mechanical erosion was proved to be the main mechanism for the lime dissolution (Deng and Du, 2012). The residual stress caused by formation of C2S-C3P on the C2S surface was also considered to be one of the possible reasons for C2S peeling (Xie et al., 2016).
As reported by (Ono et al., 1983), in hot metal dephosphorization by simultaneous lime and oxygen injection, CaO starts to dissolve due to the penetration of FetO and MntO. Then, the phosphorus reacted with CaO-Fe(Mn)tO in the reaction layers, and finally fixed as CaO-SiO2-P2O5 solid solution, the process is shown in Figure 1. This inference is consistent with the results of (Hamano et al., 2006), in which a CaO-FeO layer was observed nearby the solid CaO, as well as a reaction layer of solid CaO-SiO2-P2O5 coexisting with liquid slag besides the CaO-FeO phase.
FIGURE 1. Schematic illustration of lime dissolution and dephosphorization process (Ono et al., 1983) [Figure 6 of (Ono et al., 1983), Copyright The Iron and Steel Institute of Japan].
The reaction product of hot metal dephosphorizaiton was proved to be 3CaO·P2O5 in the laboratory scale experiments, which coagulated with other SiO2-bearing particles in the slag to form a solid solution phase (Nozaki et al., 1983). The phosphorus-rich solid solution phase is confirmed to consist mainly with 2CaO·SiO2-3CaO·P2O5, or sometimes the mixture of 2CaO·SiO2-3CaO·P2O5 and 3CaO·SiO2, according to the mineralogical analysis results of the slag (Sasaki et al., 2002; Gao et al., 2012). Thermodynamically stable CaO-FeO phase was confirmed by using the chemical equilibration method, which can enhance the phosphorus condensation from liquid slag to solid solution (Gao et al., 2012).
By analyzing the reaction interface of the solid CaO and the CaO-SiO2-FeO-P2O5 slag at 1,573 and 1,673 K, the formation of the CaO-FeO layer and the P-rich solid solutions were determined (Hamano et al., 2006), and the reaction mechanism of solid CaO and the molten slag was clarified as follows (Saito et al., 2009).
(1) The solid CaO dissolves into the molten slag and the solid phase of 2CaO·SiO2 is formed in the melt, then a reaction zone with solid and liquid phases coexisting appears between the bulk slag and the solid CaO (Figure 2A).
(2) With the continuous generation of 2CaO·SiO2 in the melt, the concentration of CaO and SiO2 decreases and FeO increases. Owing to the activity gradient of FeO, Fe2+ diffuses from FeO rich zone to both solid CaO and bulk slag, and CaO-FeO layer is formed adjacent to solid CaO (Figure 2B).
(3) Ca2+ diffuses to the bulk slag through the CaO-FeO layer, owing to the activity gradient of Ca2+. By repeating this process, the CaO-FeO phase grows, and the dissolution of CaO proceeds (Figure 2C).
(4) The P2O5 in the liquid phase reacts quickly with the 2CaO·SiO2, and the phosphorus rich phase of 2CaO·SiO2-3CaO·P2O5 solid solution is formed (Figure 2D).
(5) With the P2O5 diffusing from the molten slag to the reaction interface and reaction with 2CaO·SiO2 continuously, the phosphorus is further condensed as 2CaO·SiO2-3CaO·P2O5 solid solution with high P2O5 content (Figure 2E).
FIGURE 2. Reaction mechanism of solid CaO and CaO-SiO2-FeO-P2O5 slag (Saito et al., 2009). [Figure 10 of (Saito et al., 2009), Copyright The Iron and Steel Institute of Japan].
Because the transfer rate of phosphorous from molten slag to a 2CaO·SiO2 particle is significantly fast, the particle changes into C2S-C3P solid solution in less than 5 s (Inoue and Suito, 2006b). Thus, the formations of C2S and C2S-C3P solid solution can be considered to be simultaneously, as shown in Figure 2.
In order to obtain the dissolution rate of CaO into molten slags (Matsushima et al., 1976; Matsushima et al., 1977), measured the diameter of sintered CaO rod in CaO-SiO2-Al2O3 and CaO-SiO2-FeO slags using a rotating rod test (Figure 3A). Assuming the mass transfer in the slag is the rate-determining step, the dissolution rate can be obtained by Equation (9).
Where, k is the mass transfer coefficient of CaO in the slag (m/s), (%CaO)i and (%CaO)b are the content of CaO in the interface and in bulk slag, respectively.
Where, u and v are the relative velocity (m/s) and kinematic viscosity (m2/s), respectively. d is the diameter of the rod (m), and D is the diffusion coefficient of CaO in the slag (m2/s).
FIGURE 3. Experimental apparatus to measure the dissolution rate of CaO by (A) (Matsushima et al., 1977) [ Figure 1 of (Matsushima et al., 1977), Copyright The Iron and Steel Institute of Japan] and (B) (Deng et al., 2012) [Figure 9 of (Deng et al., 2012), Copyright WILEY-VCH].
The dissolution rates of solid CaO in CaO-SiO2-FetO slags at hot-metal temperatures with different additives of X (X: CaF2, CaCl2, Al2O3 and B2O3) were studied by using the same method (Hamano et al., 2004). It was considered to be well controlled by the mass transfer in the bulk slag, and increases with FetO concentration and decreases with basicity of the slag. Since the enhancement factors of each additives were obtained by laboratory experiments, the comprehensive dissolution rate of CaO to CaO-SiO2-FetO-X slag can be expressed by Equation (11). The comparison on the effect of different of additives on raising the dissolution rate was CaF2 > CaCl2 > B2O3 > Al2O3.
Where,
On the other hand, Du. Sichen and his group (Deng and Du, 2012; Deng et al., 2012) proposed a different method, with the experimental facility as shown in Figure 3B. In this method, the molten slag was stirred instead of rotating the solid CaO, and a lime cube was used instead of sintered CaO rod. The forced convection around the lime cube was considered to be much greater, and about half of the lime could be dissolved within 6 min, that was more consistent with the industrial operation. The dissolution rate of the CaO cube was represented by Equation (12).
Where,
FIGURE 4. Dissolution behavior of cube lime with various densities by (Deng and Du, 2012) [Figure 1 of (Deng et al., 2012), Copyright Springer].
The dissolution rates of various limes including the industrial quick lime were measured by (Maruoka et al., 2013) in the molten slag stirred by gas bubbling. In this study, it increased with the gas flowrate, but was not strongly influenced by the density of lime, when the C2S layer formed and covered the lime surface. It is considered to be the most realistic method to simulate the actual situation in steelmaking process (Kitamura, 2017).
Consequently, the lime dissolution can be expressed by Equation (13) in gas stirring situation (Maruoka et al., 2013) or by Equation (14) in rod rotation situation (Matsushima et al., 1977; Umakoshi et al., 1984)
Where,
Based on the above studies, the dissolution rate of lime and the mass content of CaO in molten slag can be obtained, as well as the remained mass of undissolved solid CaO. Then, the extent of dephosphorization can be concluded, by considering the phosphorus equilibrium between the metal and the slag with known compositions.
Although the dephosphorization reaction have been widely studied, it is still an ongoing topic due to the continuous desire of higher efficiency for dephosphorization and lime utilization in steelmaking process.
The dephosphorization reaction in a solid and liquid coexistence slag is greatly influenced by the solid phase that precipitates in the slag. The higher efficiency of dephosphorization can be observed in the C2S crystallizing range, owing to the concentration of phosphorus in the solid phase (Sasaki et al., 2002). It was revealed that P2O5 can be condensed easily in the solid solution with a high distribution ratio, which was up to tens or even higher than one hundred, as shown in Table 2.
TABLE 2. Studies on the distribution ratio of P2O5 between solid solution and liquid phase in multi-phase slag
In the study of (Ito et al., 1982), about 80% of the phosphorus transported from the molten slags to the precipitated solid C2S, when the molten slag was cool down to the liquidus temperature and showed a state of liquid and solid coexisting. The equilibrium distribution ratio (
Since the mechanisms of lime dissolution and the phosphorus enrichment in the multi-phase slag have been clarified, prediction of the phosphorus content in steel by establishing a more accurate dephosphorization model could be expected, considering the reactions of multi-phase slag refining.
The dephosphorization reaction occurs under non-equilibrium conditions, due to the large difference in oxygen potentials between the metal and the slag phases, and the oxygen potential at the metal-slag interface has crucial influence on the reaction rate (Kitamura, 2014). The oxygen potentials of the two phases and their interface were calculated using a computational thermodynamics method (Miyamoto et al., 2009), as shown in Figure 5.
FIGURE 5. Relationship between oxygen potential and slag basicity (Miyamoto et al., 2009). [Figure 10 of (Miyamoto et al., 2009), Copyright The Iron and Steel Institute of Japan].
Therefore, the dephosphorization model should be established based on reaction kinetics as well as thermodynamic data. A representative model is the competitive reaction model, which was proposed by (Ohguchi et al., 1984). Based on this competitive reaction model, a computer program with the name of MACSIM was developed for the simulation of hot metal dephosphorization process in industrial scale (Kitamura et al., 1991). However, since the slag is treated as a homogeneous liquid phase in the conventional models, there is a limit for its application to the multi-phase slag refining. Since more researches on multi-phase slag refining for dephosphorization were conducted, some advanced dephosphorization models that taken into account the solid phase in the slag were proposed. In 2008, a model considering the effect of solid phase in slag and the dissolution of lime has been presented (Kitamura et al., 2008). Then, a complete computer program of Multi-Phase Slag Refining (MPSR) model with a user interface and generalized parameters was developed (Kitamura et al., 2014). The basic structure of the MPSR model is shown in Figure 6. The model employed a multi-scale model, including macro-scale model and meso-scale model. All the phases and reactions considered in the MPSR model are shown in Figure 7.
FIGURE 6. Basic structure of the Multi-Phase Slag Refining (MPSR) model (Kitamura et al., 2014). [Figure 1 of (Kitamura et al., 2014), Copyright The Iron and Steel Institute of Japan].
FIGURE 7. |Phases and reactions considered in the MPSR model (Kitamura et al., 2014). [Figure 2 of (Kitamura et al., 2014), Copyright The Iron and Steel Institute of Japan].
The MPSR model involves the followings:
(1) Chemical reactions between the liquid slag and the hot metal.
(2) Flux dissolution and scrap melting.
(3) Fraction of the solid phase and distribution of phosphorus in the multi-phase slag.
(4) Direct decarburization, FeO formation, and post combustion.
(5) Heat balance calculation.
Based on the MPSR model, a computer program was developed with a user interface and parameter setting window, as shown in Figure 8. This program has been applied to Sumitomo Metals, Nippon Steel, Kobe Steel and JFE, it is easy to use and enables the user to apply it to industrial on-line control as well as process simulation.
FIGURE 8. User interface and parameter setting window of the MPSR model (Kitamura et al., 2014) [Figures 4 and 5 of (Kitamura et al., 2014), Copyright The Iron and Steel Institute of Japan].
The program has been applied to laboratory furnaces and industrial top-bottom blown converter with some generalized thermodynamic parameters and specialized kinetic parameters in different operational conditions, and its availability was validated since the simulation results agreed well with the operational results, as shown in Figure 9 (Kitamura et al., 2014).
FIGURE 9. Simulation results of the MPSR model for (A) laboratory furnace with FeO feeding all at once and bottom stirring but no oxygen blown; (B) laboratory furnace with FeO feeding all at once, bottom stirring and oxygen top blown; (C) laboratory furnace with bottom stirring and oxygen top blown, but no FeO addition; (D) laboratory furnace with FeO feeding in batches, bottom stirring and oxygen top blown; (E) Industrial converter with FeO feeding all at once, bottom stirring and oxygen top blown(Kitamura et al., 2014) [Figures 7 to 11 of (Kitamura et al., 2014), Copyright The Iron and Steel Institute of Japan].
Since the MPSR model is only applicable for the hot metal pretreatment process and the early stage of BOF process, limited in the cases of low temperature and low basicity, another reaction model was developed for simulation of the entire BOF process based on the Effective Equilibrium Reaction Zone Model by using FactSage software (Jung et al., 2014; Van Ende and Jung, 2018). In this model, the BOF process was divided into several reaction zones, in which kinetics were taken into account by varying the effective volumes of these reaction zones, and a thermodynamic database for P2O5-containing slag was used to calculate the equilibrium of phases and chemical reactions. The calculation results of this model are shown in Figure 10, with input conditions taken from a 200-ton industrial converter reported by (Cicutti et al., 2002). The amount of C2S-C3P solid solution phase and other phases in the multi-phase slag were calculated, as well as the compositions of the liquid slag and the metal bath.
FIGURE 10. Calculation results of (A) phases in the multi-phase slag and (B) compositions of the liquid slag and (C) validations of compositions in the metal bath (Jung et al., 2014; Van Ende and Jung, 2018) [Figure 8 of (Jung et al., 2014), Copyright The Omnipress; Figure 3.9 of (Van Ende and Jung, 2018), Copyright Springer International Publishing].
On the other hand, the researchers from SMS group and GTT company (Khadhraoui et al., 2018; Khadhraoui et al., 2019) proposed a new approach to establish a dephosphorization model, by coupling a new thermodynamic database developed for industrial steelmaking slag to FactSage for the phase equilibrium calculation, and the phorsphorus distribution (
The simulation results of both MPSR model and Jung model seem to be in good agreement with industrial experiments, but there is still a potential for improvement in accuracy, while the validation of the SMS model was not mentioned in the literature. For all of these dephosphorization models with consideration of multi-phase slag refining, the influence of solid phases, especially the C2S-C3P solid solution, from both thermodynamic and kinetic perspectives, has been considered. Gibbs free energy calculations were conducted for phase equilibrium and chemical reactions in these models with generalized thermodynamic parameters, but it is not easy to determine the specialized kinetic parameters in different operational conditions, so different kinetic methods were introduced to the three models. Besides, there are some common limitations for the exiting models, due to the lack of thermodynamic and kinetic details of multi-phase slag reactions in the final stage of BOF process.
Before the concept of Multi-phase Refining being proposed, the dephosphorization slag was usually perceived as a homogeneous liquid phase in steelmaking process, including hot metal pretreatment and converter steelmaking. A lot of laboratory or industrial experiments have been conducted to clarify the mechanism of phosphorus removal from liquid metal to molten slag, in which the temperature and the composition of the slag are significantly related to the phosphorus distribution ratio. According to the principle of metallurgical thermodynamics, the temperature has an obvious effect on the equilibrium constant k in the dephosphorization reaction between the slag and hot metal, and the contents of each oxide in the slag has influence on the oxygen potential and the activity of components in the slag, thereby further affecting the distribution of phosphorus between the slag and hot metal. Although the solid-liquid coexistence state of actual steelmaking slag and its influence on dephosphorization were neglected in previous studies, most conclusions of the above studies are not inconsistent with studies on multiphase slag refining, but can be elaborated from different perspectives.
With a restricted use of fluorite resources and a large-scale application of hot metal pretreatment technology, the coexistence of solid and liquid phases in the slag and the effect on the dephosphorization have been paid more attention. On the one hand, efforts were made to improve the “oxidation dephosphorization” of Equation (6) by increasing the activity of CaO in the liquid slag, which mainly includes two strategies, i.e., looking for some alternatives similar to CaF2 (such as TiO2, Na2O, Al2O3, B2O3, etc.) or exploring some other methods used to accelerate lime dissolution (such as strengthening stirring, increasing FeO content, etc.). On the other hand, as an important part in the multiphase slag refining, the enrichment of “solid phosphorus” tends to be promoted by controlling the composition and temperature of the slag in a optimal range, thereby increasing the precipitation of the phosphorus-rich solid solution phase and the distribution ratio of phosphorus between the solid solution and the liquid slag. From the perspective of traditional research, increasing FeO content can facilitate the dephosphorization by promoting the dephosphorization reaction (Equation 6) which occurs at the slag-metal interface; and from the perspective of multi-phase slag refining, it can be explained that the formation of CaO-FeO phase promotes the transfer of P2O5 from the liquid slag to the solid phase, thereby forming more P-rich solid solution and increasing the solid-liquid phosphorus distribution ratio (
The dissolution behavior of lime into the molten slag has always been the focus of research, which needs to be studied from both the thermodynamics and kinetics perspectives. The existence of the C2S layer and its crucial role on lime dissolution is undoubted, but there are still different views on the decisive step. In the study on lime dissolution mechanism, the mass transfer from bulk slag to slag-C2S interface or the mechanical peeling of the C2S layer on the lime surface were regarded as the determining step, respectively (Matsushima et al., 1976; Matsushima et al., 1977; Yang et al., 2007; Deng and Du, 2012). In fact, based on the previous studies, the decomposition of the C2S layer should be treated as a comprehensive consequence of chemical reaction and mechanical erosion. Since the reactant oxides (such as SiO2, FeO and MnO, etc.) transfer from the bulk slag to the interface of the dense C2S layer and the bulk slag , chemical reactions occur at the interface which is subsequently transformed into a low melting point phase. At the same time, some special oxides (such as FeO and MnO, etc.) penetrate the reaction interface and enter into the inside of dense C2S layer or even the solid CaO layer, making the dense C2S layer loose. Following this, the loose C2S phase is broken and peeled off by gas stirring or other mechanical scouring, thereby promoting the dissolution of lime.
In traditional researches, the equilibrium constant k of the dephosphorization reaction (between hot metal and liquid slag) is generally obtained through thermodynamic experiments, then the phosphorus distribution ratio between the slag and hot metal can be calculated. In addition, the empirical formula of the phosphorus distribution ratio (
Since hot metal dephosphorization pretreatment process and dual slag BOF process have been fully applied in Japan (Ogawa and Maruoka, 2014; Kitamura et al., 2018; Sone et al., 2019), most of the researches on multi-phase slag have been carried out aiming at the process conditions of low temperature and low basicity in the hot metal pretreatment or the early stage of BOF process. In such cases, the temperature of the dephosphorization slag is usually below 1,450°C, and the basicity is less than 2.0. Moreover, due to a high carbon content in the hot metal, the FeO content in the slag is significantly lower than that in the final stage of BOF process with low carbon concentration. As shown in Table 2, many experimental studies have been conducted on the phase equilibrium and phosphorus distribution in the multi-phase slag at the temperature below 1,560°C. However, there is a lack of thermodynamic equilibrium data at the temperatures above 1,600°C, as well as the kinetic data for dissolution rate of solid solution.
Although a few literatures reported the studies on the dissolution of C2S and C2S-C3P solid solution in molten slag at 1,300–1,400°C (Yang et al., 2010; Kobayashi and Sadamoto, 2017), but their dissolution behaviors in the final stage of BOF process with a high temperature and high basicity condition have rarely studied. For the BOF process, the endpoint temperature of molten steel and slag reaches up to 1,600–1700°C, and the basicity of the slag is higher than 3.0, meanwhile the FeO content is extremely high due to low carbon content in the metal bath. Although the statistical relation between the phosphorus distribution ratio and its influential factors has been studied in the final stage conditions of BOF (Wang et al., 2014), but the dephosphorizaiton mechanism in the final stage has not been clarified yet. The dissolution of the solid solution phase and the redistribution of P in the final slag should not be neglected (Lv et al., 2017), because the phosphorus-enrichment contribution ratio of C2S solid solution is strongly affected by the basicity and FeO content (Xie et al., 2018). Meanwhile, the liquid-solid coexisting state of the molten slag would change significantly in the final stage of BOF process. Especially for the BOF process using the single slag method, the influence is very large, because the dephosphorization slags produced in the early stage are in large amount and left in the furnace to the end of the process. Therefore, a further study should be performed to clarify the dissolution mechanism of the phosphorus-rich phase solid solution in the slag and the redistribution of phosphorus in the solid and liquid phases, which is beneficial to develop a more applicable dynamic model for the phosphorus prediction of the entire BOF process, considering the multi-phase slag reactions in the final stage conditions. For modelling the entire dephosphorization process, it is necessary to consider the influence of solid phases in the multi-phase slag from both thermodynamic and kinetic perspectives, and more details still need to be further clarified through laboratory experiments. Furthermore, the modelling work is beneficial for the fine control of the BOF process and the development of intelligent manufacturing in steelmaking industry.
Molten slag in steelmaking process is usually regarded as a homogeneous liquid phase in traditional researches, which focus on increasing the slagging rate of the flux by adding co-solvents (such as CaF2, Na2O…) or improving the FeO content, so as to promote the balance of dephosphorization between liquid slag and hot metal. On the other hand, the main concerns for multi-phase slag refining are the physical and chemical properties of solid-liquid coexisting phases, and the formation and dissolution behaviors of phosphorus-rich phase solid solution, as well as the phosphorus distribution ratio between solid and liquid phases in the slag. Thus, dephosphorization reaction models established in terms of above studies can show great advantage over the previous ones. The main conclusions are shown as follows:
Since the molten slag in actual steelmaking process shows a coexisting state of both liquid and solid phases, the concept of multi-phase slag refining has been proposed and proved to be an effective way to improve the utilization of solid lime flux and the efficiency of dephosphorization in steelmaking practices. Multi-phase slag refining is not in opposition to the traditional researches, but gives more details about the reactions between the liquid slag and solid phases, and the importance of solid phases on dephosphorization is clarified.
The 2CaO·SiO2 layer on the surface of the lime particles plays a crucial role on lime dissolution. The decomposition of the C2S layer is considered as the limiting factor for the dissolution of lime in the molten slag, including a comprehensive effect of chemical reaction and mechanical peeling; the dissolution rate of lime can be improved by adding co-solvents or strengthening stirring.
Owing to the lime dissolution and increasing of temperature and FeO content in the molten slag, the solid-liquid coexisting state of the slag will change significantly. Further researches should be conducted on the dissolution of the phosphorus-rich phase solid solution (2CaO·SiO2-3CaO·P2O5) in the final stage of BOF process with high temperature, high FeO content and high basicity, as well as the redistribution of phosphorus between the solid and liquid phases in the final slag.
For modelling of the dephosphorization process, it is necessary to consider the influence of solid phases in the multi-phase slag from both thermodynamic and kinetic perspectives. Some simulation models have been developed and the results agreed well with the industrial experiments, but there is still a potential for improvement in accuracy. However, it is still necessary to develop a more applicable dynamic dephosphorization simulation model for the entire BOF process, containing more thermodynamic and kinetic details of the multi-phase slag reactions in the final stage conditions.
All authors contributed to the analysis and writing of the manuscript, and approved it for publication.
This work was supported by the National Natural Science Foundation of China (Grant No.5197041150) and Jiangxi Provincial Department of Science and Technology (Grant No.20171ACE50020).
Author XF was employed by the company Xinyu Iron and Steel Group Co. Ltd., which was one of the participants of the research project supported by Jiangxi Provincial Department of Science and Technology (Grant No.20171ACE50020).
The remaining authors declare that the research was conducted in the absence of any commercial or financial relationships that could be construed as a potential conflict of interest.
The authors also would like to give our thanks to Prof. Guohua Zhang (University of Science and Technology Beijing) and Dr. Jiangshan Zhang (University of Science and Technology Beijing) and Mr. Jianping Yang (University of Science and Technology Beijing) for their inspiring discussion on this work.
Amini, S., Brungs, M., and Ostrovski, O. (2007). Dissolution of dense lime in molten slags under static conditions. ISIJ Int. 47, 32–37 doi:10.2355/isijinternational.47.32
Assis, A. N., Tayeb, M. A., Sridhar, S., and Fruehan, R. J. (2015). Phosphorus equilibrium between liquid iron and CaO-SiO2-MgO-Al2O3-FeO-P2O5 slag Part 1: literature Review,Methodology,and BOF slags. Metall. Mater. Trans. B. 46, 2255–2263 doi:10.1007/s11663-015-0408-9
Basu, S., Lahiri, A. K., and Seetharaman, S. (2007). Phosphorus partition between liquid steel and CaO-SiO2-FeOx-P2O5-MgO slag containing 15 to 25 pct FeO. Metall. Mater. Trans. B. 38, 623–630 doi:10.1007/s11663-007-9063-0
Bergman, A. (1988). Representation of phosphorus and vanadium equilibria between liquid iron and complex steelmaking type slags. Transactions ISIJ. 28, 945–951 doi:10.2355/isijinternational1966.28.945
Cicutti, C., Valdez, M., Pérez, T., Donayo, R., and Petroni, J. (2002). Analysis of slag foaming during the operation of an industrial converter. Lat. Am. Appl. Res. 32, 237–240
Deng, T., and Du, S. (2012). Study of lime dissolution under forced convection. Metall. Mater. Trans. B. 43, 578–586 doi:10.1007/s11663-011-9629-8
Deng, T., Glaser, B., and Sichen, D. (2012). Experimental design for the mechanism study of lime dissolution in liquid slag. Steel Res. Int. 83, 259–268 doi:10.1002/srin.201100258
Drain, P. B., Monaghan, B. J., Zhang, G., Longbottom, R. J., Chapman, M. W., and Chew, S. J. (2017). A review of phosphorus partition relations for use in basic oxygen steelmaking. Ironmak. Steelmak. 44, 721–731 doi:10.1080/03019233.2017.1386456
Du, C., Lv, N., Su, C., Liu, W., Yang, J., and Wang, H. (2019). Distribution of P2O5 between solid solution and liquid phase in dephosphorization slag of CaO-SiO2-FeO-P2O5-Na2O system. J. Iron Steel Res. Int. 26, 1162–1170 doi:10.1007/s42243-018-00224-4
Fix, W., Heymann, H., and Heinke, R. (1969). Subsolidus relations in the system 2CaO·SiO2-3CaO·P2O5. J. Am. Ceram. Soc. 52, 346–347 doi:10.1111/j.1151-2916.1969.tb11948.x
Gao, X., Matsuura, H., Miyata, M., and Tsukihashi, F. (2013). Phase equilibrium for the CaO-SiO2-FeO-5mass%P2O5-5mass%Al2O3 system for dephosphorization of hot metal pretreatment. ISIJ Int. 53, 1381–1385 doi:10.2355/isijinternational.53.1381
Gao, X., Matsuura, H., Sohn, I., Wang, W., Min, D. J., and Tsukihashi, F. (2012). Phase relationship of CaO-SiO2-FeO-5 mass pct P2O5 system with low oxygen partial pressure at 1673 K (1400°C). Metall. Mater. Trans. B. 43, 694–702 doi:10.1007/s11663-012-9651-5
Gaskell, D. R. (1982). On the correlation between the distribution of phosphorus between slag and metal and the theoretical optical basicity of the slag. Transactions ISIJ. 22, 997–1000 doi:10.2355/isijinternational1966.22.997
Hamano, T., Fukagai, S., and Tsukihashi, F. (2006). Reaction mechanism between solid CaO and FeOx-CaO-SiO2-P2O5 slag at 1573 K. ISIJ Int. 46, 490–495 doi:10.2355/isijinternational.46.490
Hamano, T., Horibe, M., and Ito, K. (2004). The dissolution rate of solid lime into molten slag used for hot-metal dephosphorization. ISIJ Int. 44, 263–267 doi:10.2355/isijinternational.44.263
Inoue, R., and Suito, H. (2006a). Mechanism of dephosphorization with CaO-SiO2-FetO slags containing mesoscopic scale 2CaO·SiO2 particles. ISIJ Int. 46, 188–194 doi:10.2355/isijinternational.46.188
Inoue, R., and Suito, H. (2006b). Phosphorous partition between 2CaO·SiO2 particles and CaO-SiO2-FetO slags. ISIJ Int. 46, 174–179 doi:10.2355/isijinternational.46.174
Ito, K., and Sano, N. (1983). Phosphorus distribution between CaO-containing slag and carbon-saturated iron at hot metal temperatures. Tetsu-to-Hagané. 69, 1747–1754 doi:10.2355/tetsutohagane1955.69.15_1747
Ito, K., Yanagisawa, M., and Sano, N. (1982). Phosphorus distribution between solid 2CaO·SiO2 and molten CaO-SiO2-FeO-Fe2O3 slags. Tetsu-to-Hagané. 68, 342–344 doi:10.2355/tetsutohagane1955.68.2_342
Jung, I. H., Hudon, P., Van Ende, M. A., and Kim, W. Y. (2014). “Thermodynamic database for P2O5-containing slags and its application to the dephosphorization process”, in: AISTech 2014 proceedings. (Indianapolis, IN, USA: Omnipress)
Khadhraoui, S., Hack, K., Jantzen, T., and Odenthal, H. (2019). Study of the state of industrial P2O5-containing slags relevant to steelmaking Processes based on a new thermodynamic database developed for CaO-FeOx-P2O5-SiO2-MnO-MgO-Al2O3 slags - Part I: ternary and lower order systems. Steel Res. Int. 90, 1900085 doi:10.1002/srin.201900085
Khadhraoui, S., Odenthal, H., Das, S., Schlautmann, M., Hack, K., Glaser, B., et al. (2018). A new approach for modelling and control of dephosphorization in BOF converter. La metallurgia italiana., 5–16. http://www.aimnet.it/la_metallurgia_italiana/2018/novembre_dicembre/khadhraoui.pdf
Kimura, H., Yanagase, T., Noguchi, F., and Ueda, Y. (1974). Studies on the mechanism of CaO dissolution into slag melts. Journal of the Japan Institute of Metals and Materials. 38, 226–232 doi:10.2320/jinstmet1952.38.3_226
Kitamura, S.. (2014). “Analysis of steelmaking reactions by coupled reaction model”, in: Proceedings of the extraction and processing division symposium on pyrometallurgy in honor of david G.C. Robertson. (San Diego, California, USA: Springer International Publishing)
Kitamura, S.. (2017). Dissolution behavior of lime into steelmaking slag. ISIJ Int. 57, 1670–1676 doi:10.2355/isijinternational.ISIJINT-2017-109
Kitamura, S., Ito, K., Pahlevani, F., and Mori, M. (2014). Development of simulation model for hot metal dephosphorization process. Tetsu-to-Hagané. 100, 491–499 doi:10.2355/tetsutohagane.100.491
Kitamura, S., Kitamura, T., Aida, E., Sakomura, R., Kaneko, T., and Nuibe, T. (1991). Development of analysis and control method for hot metal dephosphorization process by computer simulation. ISIJ Int. 31, 1329–1335 doi:10.2355/isijinternational.31.1329
Kitamura, S., Miyamoto, K., Shibata, H., Maruoka, N., and Matsuo, M. (2009). Analysis of dephosphorization reaction using a simulation model of hot metal dephosphorization by multiphase slag. ISIJ Int. 49, 1333–1339 doi:10.2355/isijinternational.49.1333
Kitamura, S., Naito, K., and Okuyama, G. (2018). History and latest trends in converter practice for steelmaking in Japan. Miner. Process. Extr. Metall. (IMM Trans. Sect. C). 128, 34–45 doi:10.1080/25726641.2018.1504661
Kitamura, S. Y., Shibata, H., and Maruoka, N. (2008). Kinetic model of hot metal dephosphorization by liquid and solid coexisting slags. Steel Res. Int. 79, 586–590 doi:10.2374/SRI08SP003-79-2008-586
Kobayashi, Y., and Sadamoto, T. (2017). Rate of 2CaO·SiO2 dissolution into molten CaO–FeO–SiO2 slag saturated with solid iron. ISIJ Int. 57, 1703–1709 doi:10.2355/isijinternational.ISIJINT-2017-328
Lee, C. M., and Fruehan, R. J. (2005). Phosphorus equilibrium between hot metal and slag. Ironmak. Steelmak. 32, 503–508 doi:10.1179/174328105X48142
Li, J., Zhang, M., Guo, M., and Yang, X. (2014). Enrichment mechanism of phosphate in CaO-SiO2-FeO-Fe2O3-P2O5 steelmaking slags. Metall. Mater. Trans. B. 45, 1666–1682 doi:10.1007/s11663-014-0085-0
Lv, Y., Wang, X., Qin, D., and Wang, H. (2017). Enrichment and influencing factors of phosphorus in slag of converter steelmaking. Iron and Steel. 52, 29–37 doi:10.13228/j.boyuan.issn0449-749x.20170084
Maruoka, N., Ishikawa, A., Shibata, H., and Kitamura, S. (2013). Dissolution rate of various limes into steelmaking slag. High Temp. Mat. Pr.-Isr. 32, 15–24 doi:10.1515/htmp-2012-0049
Matsushima, M., Yadoomaru, S., Mori, K., and Kawai, Y. (1977). A fundamental study on the dissolution rate of solid lime into liquid slag. Transactions ISIJ. 17, 442–449 doi:10.2355/isijinternational1966.17.442
Matsushima, M., Yadoomaru, S., Mori, K., and Kawai, Y. (1976). Fundamental study on the dissolution rate of CaO into liquid slag. Tetsu-to-Hagané. 62, 182–190 doi:10.2355/tetsutohagane1955.62.2_182
Miyamoto, K., Naito, K., Kitagawa, I., and Matsuo, M. (2009). Estimation of oxygen potential at slag/metal interface and effect of initial slag condition on hot metal dephosphorization. Tetsu-to-Hagané. 95, 199–206 doi:10.2355/tetsutohagane.95.199
Monaghan, B. J., Pomfret, R. J., and Coley, K. S. (1998). Kinetics of dephosphorization of carbon-saturated iron using an oxidizing slag. Metall. Mater. Trans. B. 29, 111–118 doi:10.1007/s11663-998-0013-2
Mori, T. (1984). On the phosphorus distribution between slag and metal. Transactions ISIJ. 25, 761–771 doi:10.1515/htmp-2012-0049
Nozaki, T., Takeuchi, S., Haida, O., Emi, T., Morishita, H., and Sudo, F. (1983). Mechanism of hot metal dephosphorization by injecting lime base fluxes with oxygen into bottom blown converter. Transactions ISIJ. 23, 513–521 doi:10.2355/isijinternational1966.23.513
Ogawa, Y., and Maruoka, N. (2014). Progress of hot metal treatment technology and future outlook. Tetsu-to-Hagané. 100, 434–444 doi:10.2355/tetsutohagane.100.434
Ogawa, Y., Yano, M., Kitanura, S., and Hirata, H. (2001). Development of the continuous dephosphorization and decarburization process using BOF. Tetsu-to-Hagané. 87, 21–28 doi:10.2355/tetsutohagane1955.87.1_21
Ohguchi, S., Robertson, D., Deo, B., Grieveson, P., and Jeffes, J. H. (1984). Simultaneous dephosphorization and desulphurization of molten pig iron. Ironmak. Steelmak. 11, 202–213
Ono, H., Masui, T., and Mori, H. (1983). Dephosphorization kinetics of hot metal by lime injection with oxygen gas. Tetsu-to-Hagané. 69, 1763–1770 doi:10.2355/tetsutohagane1955.69.15_1763
Pahlevani, F., Kitamura, S., Shibata, H., and Maruoka, N. (2010). Distribution of P2O5 between solid solution of 2CaO·SiO2-3CaO·P2O5 and liquid phase. ISIJ Int. 50, 822–829 doi:10.2355/isijinternational.50.822
Saito, R., Matsuura, H., Nakase, K., Yang, X., and Tsukihashi, F. (2009). Microscopic formation mechanisms of P2O5-containing phase at the interface between solid CaO and molten slag. Tetsu-to-Hagané. 95, 258–267 doi:10.2355/tetsutohagane.95.258
Sasaki, N., Naito, K., Demoto, Y., and Kitamura, S. (2002). Effect of initial [Si] content on the lime efficiency on the dephosphorization. Tetsu-to-Hagané. 88, 300–305 doi:10.2355/tetsutohagane1955.88.6_30
Shimauchi, K., Kitamura, S., and Shibata, H. (2009). Distribution of P2O5 between solid dicalcium silicate and liquid phases in CaO-SiO2-Fe2O3 system. ISIJ Int. 49, 505–511 doi:10.2355/isijinternational.49.505
Sone, H., Kato, Y., and Kumakura, S. (2019). Progress and future prospect of the steelmaking technology. Nippon Steel Technical Report 414, 3–14. https://www.nipponsteel.com/tech/report/pdf/414-03.pdf
Suito, H., and Inoue, R. (2006). Behavior of phosphorous transfer from CaO-FetO-P2O5(-SiO2) slag to CaO particles. ISIJ Int. 46, 180–187 doi:10.2355/isijinternational.46.180
Suito, H., and Inoue, R. (1984a). Effects of Na2O and BaO additions on phosphorus distribution between CaO-MgO-FetO-SiO2-Slags and liquid iron. Transactions ISIJ. 24, 47–53 doi:10.2355/isijinternational1966.24.47
Suito, H., and Inoue, R. (1984b). Phosphorus distribution between MgO-saturated CaO-FetO-SiO2-P2O5-MnO slags and liquid iron. Transactions ISIJ. 24, 40–46 doi:10.2355/isijinternational1966.24.40
Suito, H., and Inoue, R. (1995). Thermodynamic assessment of hot metal and steel dephosphorization with MnO-containing BOF slags. ISIJ Int. 35, 258–265 doi:10.2355/isijinternational.35.258
Tsukihashi, F. (2009). Preface to the special issue "innovative development of refining Processes in steelmaking by multi phase fluxes". Tetsu-to-Hagané. 95, 187 doi:10.2355/tetsutohagane.95.187
Turkdogan, E. T. (2000a). Assessment of P2O5 activity coefficients in molten slags. ISIJ Int. 40, 964–970 doi:10.2355/isijinternational.40.964
Turkdogan, E. T., and Pearson, J. (1953a). Activities of constituents of iron and steelmaking slags, Part I - iron oxide. J. Iron Steel Inst. 173, 217–223
Turkdogan, E. T., and Pearson, J. (1953b). Activities of constituents of iron and steelmaking slags, Part II - manganous oxide and Part III phosphorus pentoxide. J. Iron Steel Inst. 175, 393–401
Turkdogan, E. T. (2000b). Slag composition variations causing variations in steel dephosphorisation and desulphurisation in oxygen steelmaking. ISIJ Int. 40, 827–832 doi:10.2355/isijinternational.40.827
Umakoshi, M., Mori, K., and Kawai, Y. (1984). Dissolution rate of burnt dolomite in molten FetO-CaO-SiO2 slags. Transactions ISIJ. 24, 532–539 doi:10.2355/isijinternational1966.24.532
Van Ende, M., and Jung, I. (2018). “Applications of thermodynamic database to the kinetic steelmaking process simulations,” in Computational materials system design., eds. Shin, D., and Saal, J.. (Cham: Springer International Publishing), 47–66
Wang, Z., Xie, F., Wang, B., Liu, Q., Lu, X., Hu, L., et al. (2014). The control and prediction of end-point phosphorus content during BOF steelmaking process. Steel Res. Int. 85, 599–606 doi:10.1002/srin.201300194
Xie, S., Wang, W., Huang, D., Li, H., and Du, Y. (2018). Clarification of the dissolution of solid CaO and the phosphorus‐enrichment capability of calcium silicates in the multiphase slag based on the ion and molecule coexistence theory. Steel Res. Int. 89, 1700317 doi:10.1002/srin.201700317
Xie, S., Wang, W., Liu, Y., and Matsuura, H. (2014). Effect of Na2O and B2O3 on the distribution of P2O5 between solid solution and liquid phases slag. ISIJ Int. 54, 766–773 doi:10.2355/isijinternational.54.766
Xie, S., Wang, W., Luo, Z., and Huang, D. (2016). Mass transfer behavior of phosphorus from the liquid slag phase to solid 2CaO center dot SiO2 in the multiphase dephosphorization slag. Metall. Mater. Trans. B. 47, 1583–1593 doi:10.1007/s11663-016-0622-0
Yang, J., Kuwabara, M., Asano, T., Chuma, A., and Du, J. (2007). Effect of lime particle size on melting behavior of lime-containing flux. ISIJ Int. 47, 1401–1408 doi:10.2355/isijinternational.47.1401
Keywords: steelmaking dephosphorization, multi-phase slag, lime dissolution, phosphorus-rich solid solution, distribution ratio of phosphorus
Citation: Lin W, Jiao S, Zhou K, Sun J, Feng X and Liu Q (2020) A Review of Multi-phase Slag Refining for Dephosphorization in the Steelmaking Process. Front. Mater. 7:602522. doi: 10.3389/fmats.2020.602522
Received: 03 September 2020; Accepted: 27 October 2020;
Published: 27 November 2020.
Edited by:
Lai-Chang Zhang, Edith Cowan University, AustraliaReviewed by:
Neven Ukrainczyk, Darmstadt University of Technology, GermanyCopyright © 2020 Lin, Jiao, Zhou, Sun, Feng and Liu. This is an open-access article distributed under the terms of the Creative Commons Attribution License (CC BY). The use, distribution or reproduction in other forums is permitted, provided the original author(s) and the copyright owner(s) are credited and that the original publication in this journal is cited, in accordance with accepted academic practice. No use, distribution or reproduction is permitted which does not comply with these terms.
*Correspondence: Qing Liu, cWxpdUB1c3RiLmVkdS5jbg==
Disclaimer: All claims expressed in this article are solely those of the authors and do not necessarily represent those of their affiliated organizations, or those of the publisher, the editors and the reviewers. Any product that may be evaluated in this article or claim that may be made by its manufacturer is not guaranteed or endorsed by the publisher.
Research integrity at Frontiers
Learn more about the work of our research integrity team to safeguard the quality of each article we publish.