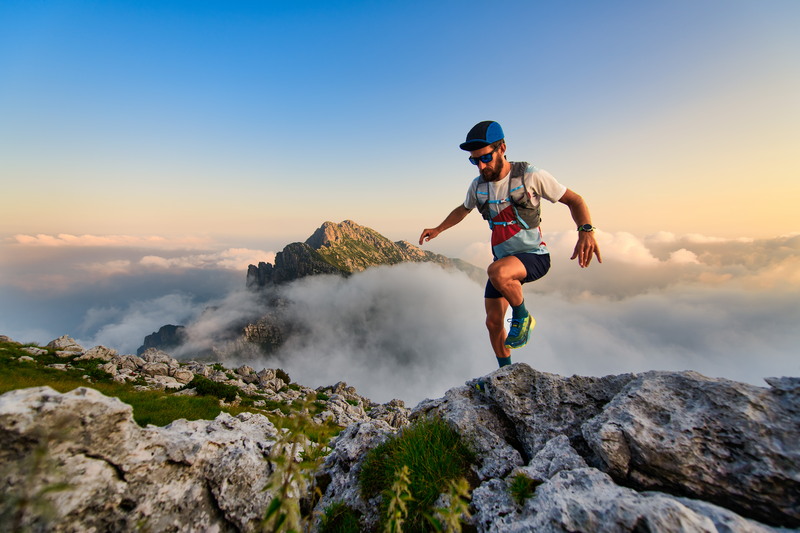
94% of researchers rate our articles as excellent or good
Learn more about the work of our research integrity team to safeguard the quality of each article we publish.
Find out more
MINI REVIEW article
Front. Mater. , 27 November 2020
Sec. Ceramics and Glass
Volume 7 - 2020 | https://doi.org/10.3389/fmats.2020.593342
This article is part of the Research Topic 2021 Retrospective: Ceramics and Glass View all 9 articles
We are living in a sensor world. Sensors are used in the house, office, car, and other areas detecting our presence by turning lights on, adjusting room temperature, detecting fires, and many other tasks. Today sensor has become a “buzz word”, without which it is hard to imagine living. They play a vital role in all sectors including housing, industry, aviation, medicine, and automobiles to name a few. Sensors can be manufactured with many types of materials. However, sensors made of ceramics have significance and have advantages when compared to those made from other materials. This mini review examines ceramic sensors and their applications in various sectors including the materials used to build them and their functioning in different areas. The paper precisely reports ceramic sensors and their applications in industry, including the medical, automotive, and aviation sectors.
Ceramics are solid materials that comprise inorganic compounds of metal or metalloids and non-metals with covalent or ionic bonds. Commonly known ceramics are brick, porcelain, and earthenware. Substances with special properties make advanced ceramics, also called fine, engineering, high performance, high tech, or technical ceramics. Traditionally ceramics are made of powder and then fabricated into a material by applying heat which exhibits strength, hardness, brittleness, and low electrical conductivity. Ceramics can be widely used almost in every application, including the fields of engineering and industry, including those used in medicine, automotive, space, and the environment. As discussed in a report by Lee and Komarneni (2005), ceramics are highly useful in corrosive environments and can be used for a long time at high temperatures without any change in their properties. Richerson and Lee (2018) compare the advantages of ceramic oxides like TiO2, Al2O3, and ZrO2 with other polymers and metals and reported that these oxides are useful for various sensor applications with special properties and advantages. This has implications for the use of ceramic materials in aviation, automobiles, medicine, and the chemical industries. Although sensors in many areas are made of ceramics, the fragility of these materials limits their application in construction materials (Okada, 2009).
A sensor is an input device that converts a physical parameter to an output in the form of an analog or digital signal. In other words, it converts a physical quantity like force, humidity, light, and converts it into an equivalent electrical output. Sensors commonly used in various applications include temperature, humidity, gas, pressure, automotive, and touch sensors etc. Technologies used by sensors include acoustic, capacitive, doppler, electromagnetic, electro-mechanical, thermistor, inductance, optic, microwave, laser, ultrasonic, peiezoelectric effect etc.
Traditional ceramics can be used in sensors where durability and toughness are a prerequisite, while advanced ceramics can be used where more emphasis is on improving the requirements of electrical, thermal, magnetic, and optical properties. Ceramics used in sensors require long durable life, high tolerance of temperature, robust nature, and should be able to undergo direct contact with liquid media. Ceramics are extensively used as temperature, humidity, pressure, oxygen, proximity, automobile, capacitive, oil level, and corrosion sensors (Critchley, 2020). Blasques et al. (2020) developed and studied the thermal and structural properties of a new ceramic nanomaterial SiO2/NPsSm2O3/C-graphite. This material is found to have samarium oxide nanoparticles whose matrix was dispersed of graphite and silica with an average pore size <4 nm. This nanomaterial was electrochemically tested by using it as an electrode material which indicated it to be promising in developing electrochemical sensors.
Synthesized powdered ceramic materials include carbides, oxides, silicates, and nitrides, which are mainly used in various forms like polycrystals, crystals, composite materials, and thin films. They show high potential in diverse areas that include industry, electronics, energy, chemicals, aviation, and automotives, etc. These materials as sensing elements have gained tremendous significance in recent years. The property of positive temperature coefficient resistance makes ceramic sensors more attractive in various applications. This makes them useful in electronic circuitry. Ceramics with this property are primary donor-doped solid solutions of barium titanate ceramics of large grain size. It is a known fact that high electric fields limit the use of piezoceramics. In such cases, traditional ceramics are preferred in environments where more stress and heat exists. Various ceramic materials with high temperature tolerance, robustness, and long durability can withstand a harsh environment and be washed, meaning they are suited to use in sensors. Materials such as alumina, zirconia, and yttria are some of the common materials used as sensing surfaces. They are widely used as temperature, pressure, oxygen, corrosion, and oil level sensors (Chiang et al., 1996). Apart from these materials many ceramic materials and composites are used as sensing materials.
Xie et al. (2018) demonstrated flexible and active shear and pressure sensors using lead zirconate titanate that measure strain, acceleration, and touch sensors that detect longitudinal, transverse, and shear loads. Perara-Mercado et al. (2018) reported a porous ceramic sensor for hydrocarbon gas leak detection. They reported the importance of porous ceramic as a material for sensors. The selection of a suitable base ceramic material and later altering pores shape, size and porosity may help in various applications. However control of permeability, low coefficient of expansion, high melting point, corrosion resistance, and tailored electronic properties are additional advantages. Recently, sensors have been used to inspect oil leakage, detect flammable gas, and hydrocarbons at high humid and low temperatures.
Su and Zhang (2017) reported carbon ceramic composite sensors. Accelerometer sensors were made from this material and BaTiO3. They deposited CNT’s on BaTiO3 substrates and reported higher sensitivity with CNT/ BaTiO3 sensors than that of BaTiO3 sensors for individual vibrating frequency. Weng et al. (2020) reported that high temperatures will degrade the electrical insulation of ceramic materials which affects the sensor characteristics. This can be overcome by adding Al2O3 to a ceramic material of YSZ thermal barrier coating which improved its insulation at high temperatures. Meng et al. (2020) developed bimodal transistor sensors by using piezoelectric ceramic substrate Lead Zirconate Titanate. Due to their large scale integration capabilities, multifunctional transistor sensors may play a key role in next-generation smart portable electronics and artificial intelligence products. Piezoelectric ceramics and their role in thermal and bimodal transistor sensors are seldom explored. Organic thermal and bimodal transistor sensors with Lead Zirconate Titanate (PZT) were developed with high sensitivity and linear response to change in temperature. Yu et al. (2020) fabricated a SiCN ceramic with an enhanced sensing distance pressure sensor. They fabricated a high-gas-tightness wireless pressure sensor with silicon carbonitride ceramic material with an increased ceramic density, and which could sense pressure from a large distance. The measurement of pressure in environments with huge temperatures (1000–1400°C), pressures (300–600 psi), and corrosive gases need to be sorted (Su et al., 2017). Authors please provide rewording (use of informal language and unclear meaning/point): “The measurement of pressure in environments with huge temperatures (1000–1400°C), pressures (300–600 psi), and corrosive gases need to be sorted” In this environment, the structure of the pressure sensor needs to be wireless and passive as these devices do not work above 600°C (Yang, 2013) and wired devices do not work in certain conditions, for example, combustion. The time sensing distance of wireless pressure sensors is also limited (Cheng et al., 2014) meaning there is a need for enhanced the sensing distance in harsh environments, increasing its life. In this context, it is important to use and develop high-gas-tightness wireless pressure sensors that are fabricated with a silicon carbonitride (SiCN) ceramic material with large sensing distance (Yu et al., 2020).
All living and non-living organisms on earth require air and water which are important for human health and in all properties of materials (Blank et al., 2016). It is important to measure water content in any environment and material for various computations. It is noteworthy that in chemical sensors, which detect the signature of particular compounds, ions in composite specimens are available on a small scale (Wolfbeis and Weidgans, 2006) and in recent years there has been increasing demand for humidity sensors (Tan et al., 2005; Liu et al., 2008; Su and Chen, 2008; Song et al., 2009; Cha et al., 2011). Humidity sensors that detect water vapor enable us to measure the amount of water in the air (Tan et al., 2005; Song et al., 2009). Yadav (2018) reviewed various types of humidity sensors and their importance in human life. Depending on the technology involved, humidity sensors are capable of providing accurate measurements of absolute humidity by mixing measurements of temperature and relative humidity (RH: the ratio of air moisture to maximum moisture at a specific temperature, while humidity is the difference between them). These sensors are categorized into thermal, capacitive, and resistive type sensors.
A thermal humidity sensor, also known as a hygrometer, works under the principle of detecting changes in temperature or currents. A capacitive humidity sensor measures RH with the help of a thin metal oxide strip (whose electrical capacity varies with RH ), which is placed between two electrodes. Depending on the existing humidity in the air, the two thermal sensors conduct current. One measures ambient air and the other is enclosed in dry nitrogen, and the difference between them gives humidity. These sensors are sued for weather monitoring and in commercial industries whose RH measurement ranges from zero to cent percent. They require calibration regularly, with a complex circuit, and operate over a large temperature range. The resistive humidity sensor measures the electrical impedance of atoms by using ions in salts and changes in humidity cause a change in resistance. These sensors are based on the principle that conduction in non–metallic conductors is due to their water content. They are usually made of materials with less resistance, as it varies significantly with humidity. A low resistive material is deposited on top of two electrodes in an inter-digitized pattern, increasing the area of contact which, on absorbing water, brings a change in resistivity that is then measured with a small electric circuit.
In general, the pressure exerted by air completely saturated with water is called PWS (saturation water vapor pressure) (Yeo et al., 2008) and is proportional to temperature. These sensors are developed to sense water vapor either in under saturated (with air) or under controlled conditions (without air) (Bozóki et al., 2003; Parikh et al., 2006; Tang et al., 2012). By and large, the way they work involves considering relative humidity based upon the actual water vapor/saturation water vapor pressure ratio at a given temperature. The prime quality of a good practical humidity sensor includes short response time, minimum hysteresis, less temperature dependence, its economic benefits, the fact that it resists contamination and involves easy fabrication, durability, and can be used for all types of water (Bayhan and Kavasoğlu, 2006; Islam and Saha, 2006; Majumdar and Banerji, 2009; Estella et al., 2010; Zhang et al., 2010a; Su and Lin, 2012). The main concern while designing these sensors are the limitations of the materials and reports indicate that this process involves either synthesizing new material or improving the properties of existing materials CE (N) (He et al., 2010). Since the sensing time of existing materials is higher (Oprea et al., 2009), new sensing materials like ceramics have been explored (Erol et al., 2011), including spinel oxides, metal oxides, perovskite oxides, or a combination of these compounds whose sensing ability depends on the physical and chemical properties. The sensing mechanism is governed by water adsorption on a ceramic surface and this process is supported by a distinctive ceramic structure with pores, grains, and grain boundaries (Faia et al., 2004; Bayhan and Kavasoğlu, 2006). Authors please check edit meaning. Water adsorption brings a change in the mechanical or electrical parameters of the sensing element, which is utilized by the humidity sensor (Yuk and Troczynski, 2003). The monitoring of humidity with instruments designed using ceramic sensing elements uses optical, mass sensitive, and electrochemical principles of operation.
Out of many existing humidity sensors, impedance based sensors are common. Their operation depends on the resistance, impedance, and capacitance of the sensing element, which senses the type and amount of surface adsorbate. In a resistive sensor, analytical signals change the real part of the impedance in the imaginary part of the capacitive sensors. The impedance decreases with an increase in relative humidity (RH) in a resistive sensor, whereas capacitance increases with RH in the capacitive sensor. A change in sensor dielectric constant with change in RH is the working principle behind capacitive humidity sensors (Wang et al., 2005). It has a ceramic substrate accompanied by metal electrodes or wire wound electrodes coated with humidity sensing ceramic material (Xu et al., 1998). Many sensors of this type were reported as responding to RH above 11% and below 95 % (Zhou et al., 2013), some responding to levels of 10 % (Faia and Furtado, 2013), 5 % (Edwin Suresh Raj et al., 2002) and less (Kotnala et al., 2013), or at 97 % (Su and Lin, 2012) and above (Zhao et al., 2013). Most of them operate at normal temperatures between 13o C to 35o C (Geng et al., 2012; Liang et al., 2012; Su and Lin, 2012; Su et al., 2012; Zhang et al., 2012a) even though they can operate above 100oC (Chen et al., 2009a) or between 100 and 400o C (Tischner et al., 2008; Chen et al., 2009b).
Zeolite based sensors are capable of detecting humidity (up to 600o C) with decreasing atmosphere (Neumeier et al., 2008). The majority of these sensors evaluate a change in impedance under the AC current, which avoids the polarization effect of adsorbed water. However, this requires complex signal processing circuits (Biswas et al., 2013). Some reports indicate no significant difference in measured values in DC or AC modes by using ceramic thin films (Kotnala et al., 2013) while some indicated that the AC voltage sensor exhibits lower impedance compared to DC voltage (Wang et al., 2008b).
Zirconia ceramic sensors are electrochemical devices developed primarily for the measurement of oxygen in gas mixtures. The addition of an electrode pair to the sensor coverts it into a pump-gauge device. The operation of this type of pump gauge sensor was reported by Maskell and Page (1999) and it can sense water vapor or CO2 at 0.004 and 0.02 mole fractions and above 800°C.
Sensors of optical type are more advantageous than electrical type since their operation does not get affected by neighboring electric magnetic fields (Yadav et al., 2010). It also has a fast response time, no requirement of electrical contacts which may be damaged by the substance that is to be sensed, and safety towards flammable vapors and gases (Somani, et al., 2001). These sensors generally utilize a fluorescence technique and guided wave spectroscopy. Water vapour interacts with the sensitive ceramic layer, changing optical parameters such as the refractive index (Mohan et al., 2012; Sharma and Gupta, 2013), reflectance (Jen et al., 2010; Yadav et al., 2010), photoluminescence (Zhang et al., 2011; Zhang et al., 2012b), and shifts in wavelength (Steele et al., 2006; Liu et al., 2011; Wales et al., 2013).
Mass sensitive sensors are simple in construction and operation with low weight and power consumption. These sensors operate on the principle of frequency shift (Janata, 2009) and Quartz Crystal Microphotometer is known to be the most popular mass sensor with high stability and sensitivity, that measures very small changes in mass on a nanoscale (Zhu et al., 2010; Xie et al., 2013). It consists of polished quartz disks with gold or silver electrodes fabricated on both sides and the sensor is coated with ceramic film. The change in frequency of quartz crystal is measured and this change depends on the adsorbed mass and films’ physical properties (Erol et al., 2011). Reports indicate that ZnO nanoparticle loaded QCM (Quartz Crystal Microphotometer) shows a sharp increase in resonance frequency with increasing RH and no change for empty QCM during adsorption (Erol et al., 2010; Erol et al., 2011). The sensitivity of these sensors depends on the thickness, uniformity, and size of ceramic particles (Zhu et al., 2010; Xie et al., 2013).
Sensor technology requires different materials based on the transformation of energy between input and output. The combination of existing materials may lead to more reliable and economical sensors. Because of this, sensors with ceramic materials are studied, as they exhibit high strength, hardness, durability, melting point, low electrical and thermal conductivity, and chemical inertness. Reports indicate that metal oxides are mainly suitable for sensing elements in the case of electrochemical, mass, and optical humidity sensors since they exhibit excellent practical robustness, stability (thermal and environmental), huge temperature range, mechanical strength, and low fabrication costs. Metal oxides with spinel structures are often preferred as they facilitate changes in properties, as well as their physical and chemical properties, and change with cation distribution (Vijaya et al., 2007). The majority of metal oxides function based on structural defects existing and the extent of non-stoichiometry. Compounds with spinel structure containing a high density of defects and that have a tetrahedral framework, exhibit a semiconductive nature (Kotnala et al., 2008). Similarly, perovskite oxides ABO3 (solid solution) in which A ( rare or alkaline earth metal influenced by humidity) and B (transition metal) is reported to be better than normal metal oxides (Wang et al., 2009) in which some exhibit sensitivity to humidity in temperature range equal to 300oC (Hassen et al., 2000), > 400oC (Chen et al., 2009a), 400–650oC (Chen et al., 2010), > 500oC (Chen et al., 2009b), 500–700oC (Wang and Virkar, 2004), 700oC (Zhou and Ahmad, 2008) and mainly depend on the semiconducting nature of ceramic materials (Chou et al., 2009). Apart from these materials, titanate-based materials (Zhang et al., 2008), phosphate-based materials (Zhang et al., 2011; Sheng et al., 2012), tungstate-based materials (You et al., 2012), bismuth iron molybdate (Sears, 2000; Sears 2005), some oxygen-free compounds (Zhang et al., 2012a), glass-ceramic composites (Pal and Chakravorty, 2006), zeolites (Urbiztondo et al., 2011), clay minerals (Su and Lin, 2012) are used for the development of electrochemical humidity sensors. The addition of the identified dopant to the sensing ceramic modifies the adsorption of water vapor, transport mechanism, microstructure, and water adsorption sites (Neri et al., 2001; Vilaseca et al., 2006). The selection of a proper sensing element allows the ceramic humidity sensor to improve its sensitivity, signal response, functioning, and stability.
Development of reliable sensors for measurements in industries like metal, steel, glass, paper, automobile, and power industries, where touch environment are of prime importance (Logothetis, 1991; Azad et al., 1992; Yamazoe and Miura, 1994; Viswanathan et al., 1997; Fukatsu et al., 1998). The technology of sensors has resulted in efficiency, improvement, and reduced emissions in the automobile industry. Given these advances, ceramic gas sensors are here reviewed.
A ceramic gas sensor uses transitions in metal oxide (ZnO, TiO2, and SnO2) as its base material. The principle behind these oxides is to detect gases like CO, H2, NOx, CH4, and CO2, etc. with variation in electrical conductivity. Selective CO sensors are used in combustion applications. A selective CO sensor was designed by CISM with PN junction having Anatase (N-type), doped with CuO and La2O3, and Rutile (P-type) with base material titania. A combination of Anatase and Rutile in proper ratio works as a selective CO sensor. Zhou et al. (2018) reported that a Ni-doped SnO2 nanoparticles-based CO gas sensor exhibited better gas response than pure SnO2 and Zn doped SnO2 based gas sensors through response and recovery times. Jaouali et al. (2017) investigated the oxygen sensing properties of lanthanum orthoferrite (LaFeO3) ceramic and indicated good response to oxygen at mild temperatures (300–450°C) with high stability in a humid environment and excellent selectivity to oxygen over other interfering gases such as CO, NO2, CO2, H2, and ethanol. Rizi et al. (2019) investigated for SnO2/Ag2O ceramic nanocomposite (CNP) to sense H2 gas in place of the ceramic semiconductors being used for applications in gas sensing industries and inferred that CNP annealed at 300°C had the highest response to H2 gas. NOx can be detected with YSZ (Yttria Stabilized Zirconia) sensors with metal oxide electrodes (Miura et al., 1996). But this sensor requires reference gas, limiting its application in automotive exhausts of variable oxygen environments. Perovskite oxides like calcium zirconate (CaZrO3) can be used for the sensing of hydrocarbons (Chiang et al., 1998). However, hydrocarbon detection in the presence of CO can create some problems. Commercial YSZ oxygen sensors work with air as a reference electrode. Air reference sensors are unsuitable if oxygen needs to be monitored at different locations. In this context, CISM developed an oxygen sensor with a Ni/NiO reference electrode. Chowdhury et al. (2001) reported that the usage of an Al2O3 isolation tube makes the sensor strong, with stable performance. Nevertheless, it suffers from long-term stability because of grain growth and the sintering of the inner electrode. Therefore we need a solid reference system that does not sinter at operating temperature.
It is a known fact that incomplete combustion of carbon fuels produces dangerous carbon monoxide gas. Hence it is of prime importance to detect this gas for the safety of human life in various circumstances (Kong et al., 2000). Zhu et al. (2019) reported that the sensing of CO by Pd-SnO2 composite nanoceramics at room temperature. They summarized the CO sensing capabilities of Pd-SnO2 by comparing samples with a difference in Pd contents at different temperatures. Observations indicate no sensitivity to CO at room temperature for Pd content ≤2 wt% and good sensitivity reported for samples heated to very high temperatures ≥1000°C and 2 wt% Pd (Figure 1A).
Alcoholic compounds like ethanol, methanol, and propanol are volatile and inflammable and people might be exposed to them due to industrial emissions. Authors please provide rewording for: “Alcoholic compounds like ethanol, methanol, and propanol are volatile and inflammable whose exposure may be due to industrial emissions. At certain levels liver, skin, brain, and respiratory problems can occur. Employees working in industry can suffer from eye and skin and stomach irritation when exposed to excess ethanol. However, methanol and ethanol production is a must for the pharmaceutical industry. Hence detection of these vapors at a low concentration level is necessary to save human life. In this context, a sensor with high accuracy that is capable of detecting these vapors is reported by Anjum et al. (2018). They reported a graphite doped Hydroxyapatite (GHAp) nanoceramic for detecting these vapors at low temperatures. They synthesized substrate materials for vapor sensing. They reported that GHAp sensor material can detect all vapors separately, even when they are present collectively in ambient air, with rapid recovery and response time in comparison to host materials. Reports indicate that vapor sensing occurs at a lower concentration of 50 ppm. The sensing ability of synthesized HAp for detecting CO and CO2 is reported (Zhang et al., 2017b) while limited sensitivity in the detection of room temperature ethanol and methanol with concentrations as low as 100 ppm of alcoholic vapors was reported by Khairnar et al. (2015). Huixia et al. (2015) reported that the sensing mechanism of the substrate is based on adsorption and desorption of the target gas molecule.
Figure 1B shows the sensing mechanism of synthesized HAp substrate.
Many researchers have reported work related to gas sensors and ceramic materials, which are used in designing and fabricating these sensors. A H2 gas sensor was reported with SnO2 (Wang et al., 2008a; Shen et al., 2015; Kadhim and Hassan, 2017), Co-SnO2 nanofibers (Liu et al., 2010), Pt-SnO2 thin film (Shahabuddin et al., 2017), Pd-SnO2 (Van Duy et al., 2015), Al-SnO2 nanofibers (Xu et al., 2011), ZnO/SnO2 composite (Mondal et al., 2014), SnO2/CNT (Yang et al., 2010), AuSnO2 nanoparticles (Wang et al., 2017), Eu-SnO2 nanoparticles (Singh et al., 2017), Pd-SnO2/MoS2 composite (Zhang et al., 2017a), Pd-SnO2 nanofibers (Zhang et al., 2010b), Co-SnO2 nanoparticles (Lavanya et al., 2017), and NOx gas by using NiCr2O4 (Miura et al., 1996; Zhuiykov et al., 2001), ZnCr2O4 (Zhuiykov et al., 2002; Miura et al., 2004; Zhuiykov and Miura, 2005), Tin-doped indium (ITO) (Li et al., 2005), ZnO (Miura et al., 2004; West et al., 2005), Cr2O3 (Miura et al., 1996; Martin et al., 2003; Szabo and Dutta, 2004), CO and NO2 sensors with CuO nanowire (Kim et al., 2008), NH3 with Zeolite H-ZSM5 (Moos et al., 2002), CO2 and NO2 with ß alumina (Billi et al., 2002).
The continuous development of sensors combined with net connectivity has made automobiles more safe and reliable. Reports indicate that worldwide, nearly sixty-five million cars were sold in 2017 alone, with an expected increase by five percent every year (Mohankumar et al., 2019). As discussed by Carmo et al. (2010) global sensor markets are expected to expand by 10% over the next five years. The demand for automobile sensors is increasing as they enable manufacturers to make driving more comfortable, safe, and meet the requirements connected with the environmental impact of cars (Bécsi et al., 2017). The prime features of automotive sensing technology include design towards the integration of signals, mechanical flexibility, and environmental safety (Kuutti et al., 2018). The automotive sensors that are available today relate to multiple functions, including mass airflow, pressure, air cleaner temperature, crankshaft position, coolant level, oxygen, oil temperature, transmission temperature, transmission input speed, vehicle speed, coolant temperature, pressure feedback, transmission output speed, methanol fuel, brake fluid level, ABS wheel speed which measures torque, position, exhaust, fuel efficiency and engine oil quality, etc.
Temperature sensors play a significant role in automobile applications that include silicon chips, thermistors, and resistive temperature detector (RTD) (Park et al., 2015). Thermistor sensors depend on the characteristics of ceramic oxide composite materials, the resistance of which varies with temperature (Blaschke et al., 2006). The production cost of the RTD sensor is high compared to others. These sensors generally consist of an Al2O3 substrate, platinum metal resistor, and a glass plate (Kato et al., 1996). Consideration of sensitivity, range of operation, accuracy, durability, and response time are of importance while manufacturing temperature sensors.
The application of pressure sensors in automobiles includes pressure measurement in the fuel tank, fuel injection, oil tank, and brake fluid, etc. (Beker et al., 2018; Borole et al., 2018; Je et al., 2016). Both the ignition and fuel control require pressure measurement (Guardiola et al., 2019). In cars, the inlet manifold pressure sensor in petrol engines, and the inlet and exhaust manifold pressure sensor in diesel engines, are important pressure sensors that work based on potentiometric, inductive, capacitive, and piezoelectric techniques. Silicon diaphragm with silicon strain gauges or capacitive deflection sensing is commonly used pressure sensors.
Chen and Mehregany (2008) demonstrated a silicon carbide capacitive surface micromachined pressure sensor that can measure static pressures. Gas sensors are used in automobiles to measure the concentration of O2 in exhaust gases (Ritter et al., 2018). When an oxygen sensor is installed in the emission control system to measure the levels of toxic exhaust gases, which can also be controlled. These sensors measure exhaust gases like CO, NO, and H2 (Javed et al., 2018). This sensor is also called a lambda sensor and it measures residual O2 concentration in the exhaust and helps to maintain combustible air-fuel mixture in the right composition. SnO2, TiO2, and ZrO2 are currently used for manufacturing lambda sensors. Out of these, the electrically heated ZrO2 sensor works on the principle of change in voltage or current, while the SnO2 and TiO2 sensors work based on semiconductor technology.
In 2017 Lavanya et al. (2017) have developed a hydrogen leak conductometric sensor based on transition metal ion-doped SnO2 for automotive applications. These sensors are potentially convenient in hydrogen-based fuel cars in the future. Zirconia is a prominent sensor material and acts as a high-temperature oxygen conductor on appropriate doping with Ca2+ or Y3+. When the exterior and interior of an A zirconia tube are exposed to a hot atmosphere and air, it will prevent leakage between the two environments. Porous platinum electrodes on two surfaces of the zirconia electrolyte generate a potential equal to the difference of oxygen between the outer atmosphere and interior air. Figure 1H shows a zirconia oxygen sensor, which is equipped in any automobile. It mainly controls the A/F ratio uses a feedback circuit, which is necessary for protecting the catalytic converter elements from too low or too high A/F ratios.
The λ (lambda) sensor is an exhaust gas oxygen sensor that plays an important role in the automobile industry. It is used in vehicles to measure and control the ratio of air versus fuel in the gases that are released from the exhaust. This reduces engine emissions and acts as a three-way catalytic converter. This results in a decrease in air pollution which is very important for the surrounding environment. The principle behind the lambda sensor is the Nernst principle. This sensor is highly stable and can perform for a long period (Xu et al., 1998). A lambda sensor is installed at a certain point, in such a way that the temperature required for the efficient functioning of the sensor is provided for the complete operating range of the engine (Pelino et al., 1998). The voltage of the sensor as well as the resistance (internal) depends on temperature. The desired closed-loop control can be set, in an unheated sensor at a temperature above 350°C and in a heated sensor above 150°C, enabling the engine to function efficiently (Matsuguchi et al., 1998).
Sensors that measure temperature and stress along with other sensors on the turbine blade are a prerequisite in aeroengines. Integrated high-performance turbine engine technology (IHPTET) has been implemented by the USA, due to the advantages of these materials. Embedding a group of thin-film sensors on the turbine blade is required to achieve aeroengine intelligence. Conventional sensors are not suitable because of their large size and weight. Small sensors can be arranged easily in any part of the aircraft engine, improving the performance and reliability of the engine. To fabricate a high temperature sensor on the surface of the turbine blade, an insulation layer needs to be added to the surface. At the same time, the electrical insulation of the ceramic material is less reliable at temperatures above 500°C (Wrbanek et al., 2001), affecting the sensor characteristics. Earlier work on high temperature insulation layers have reported the use of an Al2O3 thin film, which is deposited on metals, enhancing the capabilities of temperature insulation (Duan et al., 2017), but this thin film is removed when the temperature cycling test is finished, because of the thermal stress mismatch between the ceramic thin film and the metal (Sheng et al., 2013) giving rise to unrepeatable results not required for sensors. Another way of making an insulation layer is through TBC (Thermal Barrier Coating) technology that attaches a lower thermal conductive ceramic material to the surface of a turbine blade (Jouanny et al., 2013). In this context.
Weng et al. (2020) reported on the use of ceramic material, modifying a YSZ thermal barrier coating (TBC) formulation by adding a certain amount of Al2O3 to improve insulation at high temperatures. This study undertook micro processing on the surface of the TBC, fabrication of platinum point thermocouples, and the thermal resistor on the TBC surface and studied high temperature electrical insulation properties of the modified TBC. The results of this study indicated that electrical insulation can be improved by several orders of magnitude by adding Al2O3, meaning a reliable thin film sensor can be built on top of the TBC surface, which can be coated on turbine blade metals.
Body contact is usually used to monitor a person's medical information, such as their heart and respiratory rate, but this can usually only be monitored while sleeping, which limits its applicability. Peng et al. (2019) have reported a sleep biosignal detection system that uses low-cost piezoelectric ceramic sensors. They deployed 18 piezoelectric ceramic sensors under a mattress to capture pressure data from which respiration and heartbeat sensitivity is selected by the proposed channel-selection algorithm. Yang et al. (2020) have reported a very interesting pressure sensor with modified piezoelectric materials. Piezoelectric pressure sensors are already investigated in wearable electronics while traditional organic or inorganic composite piezoelectric films exhibit difficulty related to defects masking the performance of pressure sensors. Barium titanate modified with polydopamine was blended with polyvinylidene fluoride, forming a uniform composite, and a piezoelectric pressure sensor was fabricated. This modification technique reduces hole defects between the two components. As a result, the 17 wt % PDA@BTO/PVDF sensor exhibited a fast response of 61 ms and a remarkable piezoelectric output voltage of 9.3 V, which showed obvious improvement as compared to the pristine PVDF and BTO/PVDF composite counterparts. In addition, as an energy supplier, the sensor could produce a maximum power of 0.122 W/cm2 even with a high load resistance of 70 M. This pressure sensor was sensitive to various human motions, showing great potential in the applications of wearable electronics.
Even though piezoelectric ceramics are widely used in pressure sensors, their potential in thermal and tactile bimodal transistor sensors is rarely explored. Meng et al. (2020) demonstrated organic thermal and tactile bimodal transistor sensors, with a simple structure and fabrication technology that are based on a piezoelectric ceramic substrate, Lead Zirconate Titanate (PZT). These sensors show high sensitivity and linear response to temperature changes between 20 and 60°C with a sensitive response towards the tapping of the device surface. These sensors may be very useful in practical applications related to human interactive devices like e-skin and smart tactile sensing systems.
Porous ceramic sensors use porous ceramic material as the base material whose porosity, size, and shape can be changed. These materials have control over melting point, superficial area, corrosion, wear resistance, low expansion coefficient, permeability, etc. Sensors that inspect oil leaks, detect flammable gas, or undertake hydrocarbon gas detection are in demand. Due to their intrinsic physicochemical properties, porous ceramics play a vital role in satisfying the various needs of sensing devices, and results in the field of atmospheric sensors are consistent. Reports indicate that the most common porous materials consist of 31% SnO2(tin oxide), 23% In2O3(indium oxide), and 18%ZnO(zinc oxide), which can sense hydrocarbon gases such as LPG, CH4, H2, NO2, C2H6O, CH3OH, (CH3)2O, H2S, CO, C7H8, etc. (Perara-Mercado et al., 2018).
In recent years there has been an emphasis on the design and improvement of ceramic sensors in various sectors, some of which have been reviewed in this paper. This review has largely explored sensors that monitor humidity and gas, those used in the medicine and automobile industries. Resistive and capacitive humidity sensors are inexpensive and consume less power, operating in a large range of humidity, however, they have temperature dependence and cross sensitivity towards some chemical species. Optical sensors are more advantageous than electrical sensors as they do not interfere with electric or magnetic fields (meaning they are safe in the case of flammable gases) and have a fast response time. Mass sensors are simple in construction and operation, consuming low power. Reports indicated that the development of ceramic gas sensors can be been challenging, particularly in terms of their application in industry, which can have harsh environments.
All authors contributed to the article and approved the submitted version.
The authors declare that the research was conducted in the absence of any commercial or financial relationships that could be construed as a potential conflict of interest.
Anjum, S. R., Narwade, V. N., Bogle, K. A., and Khairnar, R. S. (2018). Graphite doped Hydroxyapatite nanoceramic. Selective alcohol Sensor,14, 98–105. doi:10.1016/j.nanoso.2018.01.010
Azad, A. M., Akbar, S. A., Mhaisalkar, S. G., Birkefeld, L. D., and Goto, K. S. (1992). Solid‐State gas sensors: a review. J. Electrochem. Soc., 139, 3690–3704. doi:10.1149/1.2069145
Bayhan, M., and Kavasoğlu, N. (2006). A study on the humidity sensing properties of ZnCr2O4-K2CrO4 ionic conductive ceramic sensor. Sensor. Actuator. B Chem. 117, 261–265. doi:10.1016/j.snb.2005.11.053
Bécsi, T., Aradi, S., Fehér, Á., and Gáldi, G. (2017). Autonomous vehicle function experiments with low-cost environment sensors. Transp. Res. Proc. 27, 333–340. doi:10.1016/j.trpro.2017.12.143
Beker, L., Maralani, A., Lin, L., and Pisano, A. P. (2018). Modeling, fabrication, and characterization of SiC concentrically matched differential capacitance output pressure sensors. Sensor Actuator Phys. 273, 293–302. doi:10.1016/j.sna.2018.02.027
Billi, E., Viricelle, J.-P., Montanaro, L., and Pijolat, C. (2002). Development of a protected gas sensor for exhaust automotive applications. IEEE Sensors J. 2, 342–348. doi:10.1109/jsen.2002.804530
Biswas, P., Kundu, S., Banerji, P., and Bhunia, S. (2013). Super rapid response of humidity sensor based on MOCVD grown ZnO nanotips array. Sens. Actuators, B 178, 331–338. doi:10.1016/j.snb.2012.12.116
Blank, T. A., Eksperiandova, L. P., and Belikov, K. N. (2016). Recent trends of ceramic humidity sensors development: a review. Sensor. Actuator. B Chem. 228, 416–442. doi:10.1016/j.snb.2016.01.015
Blaschke, M., Tille, T., Robertson, P., Mair, S., Weimar, U., and Ulmer, H. (2006). MEMS gas-sensor array for monitoring the perceived car-cabin air quality. IEEE Sensors J. 6, 1298–1308. doi:10.1109/jsen.2006.881399
Blasques, R. V., Pereira, M. A. A., Mendes, A. M. R. V., Filho, N. E. M., Gomes, W. C., Arenas, L. T., et al. (2020). Synthesis and characterization of a new ceramic nanomaterial SiO2/ NPsSm2O3/C-graphite for the development of electrochemical sensors. Mater. Chem. Phys. 243, 122255. 10.1016/j.matchemphys.2019.122255
Borole, U. P., Subramaniam, S., Kulkarni, I. R., Saravanan, P., Barshilia, H. C., and Chowdhury, P. (2018). Highly sensitive giant magnetoresistance (GMR) based ultra low differential pressure sensor. Sens. Actuat. A 280, 125–131. doi:10.1016/j.sna.2018.07.022
Bozóki, Z., Szakall, M., Mohacsi, A., Szabo, G., and Bor, Z. (2003). Diode laser based photoacoustic humidity sensors. Sens. Actuators, B 91, 219–226. doi:10.1016/s0925-4005(03)00120-5
Carmo, J. P., Mendes, P. M., Couto, C., and Correia, J. H. (2010). A 2.4-GHz CMOS short-range wireless-sensor-network interface for automotive applications. IEEE Trans. Ind. Electron. 57, 1764–1771. doi:10.1109/tie.2009.2032207
Cha, S., Gil Choi, M., Rim Jeon, H., and Chang, S.-K. (2011). Negative solvatochromism of merocyanine dyes: application as water content probes for organic solvents. Sens. Actuators, B 157, 14–18. doi:10.1016/j.snb.2011.03.020
Chen, L., and Mehregany, M. (2008). A silicon carbide capacitive pressure sensor for in-cylinder pressure measurement. Sensor Actuator Phys. 145-146, 2–8. doi:10.1016/j.sna.2007.09.015
Chen, X., Rieth, L., Miller, M. S., and Solzbacher, F. (2009a). High temperature humidity sensors based on sputtered Y-doped BaZrO3 thin films. Sens. Actuators, B 137, 578–585. doi:10.1016/j.snb.2009.01.024
Chen, X., Rieth, L., Miller, M. S., and Solzbacher, F. (2009b). Pulsed laser deposited Y-doped BaZrO3 thin films for high temperature humidity sensors. Sens. Actuators, B 142, 166–174. doi:10.1016/j.snb.2009.07.041
Chen, X., Rieth, L., Miller, M. S., and Solzbacher, F. (2010). Comparison of Y-doped BaZrO3 thin films for high temperature humidity sensors by RF sputtering and pulsed laser deposition. Sens. Actuators B Chemical 148, 173--180. doi:10.1016/j.snb.2009.07.041
Cheng, H., Shao, G., Ebadi, S., Ren, X., Harris, K., Liu, J., et al. (2014). Evanescent-mode-resonator-based and antenna-integrated wireless passive pressure sensors for harsh-environment applications. Sensor Actuator Phys. 220, 22–33. doi:10.1016/j.sna.2014.09.010
Chiang, Y.-M., Birnie, D. P., and David Kingery, W. (1996). Physical ceramics: principles for ceramic science and engineering, Hoboken, NJ: Wiley.
Chiang, Y., Wang, C. C., and Akbar, S. A. (1998). Calcium zirconate for the monitoring of hydrocarbons. Sensor. Actuator. B Chem. 46, 208–212. doi:10.1016/s0925-4005(98)00114-2
Chou, K.-S., Lee, T.-K., and Liu, F.-J. (1999). Sensing mechanism of a porous ceramic as humidity sensor. Sensor. Actuator. B Chem. 56, 106–111. doi:10.1016/s0925-4005(99)00187-2
Chowdhury, A. K., Akbar, S. A, Kapileswar, S, and Schorr, R. J. (2001). A rugged oxygen gas sensor with solid reference electrode for temperature applications. J. Electrochem. Soc. 148, (G91--G94). doi:10.1149/1.1343105
Critchley, L. (2020). Liam Critchley, 2020 Applications and characteristics of sensors made from ceramics. AZoM.
Duan, L., Gao, J., Wang, R., Hu, M., Su, J., Cheng, Q., et al. (2017). Simulation analysis of temperature distribution of thermal barrier coatings on aeroengine blades, J. Shanghai Jiaot. Univ. 51, (8),915–920. doi:10.16183/j.cnki.jsjtu.2017.08.004
Edwin Suresh Raj, A. M., Mallika, C., Swaminathan, K., Sreedharan, O. M., and Nagaraja, K. S. (2002). Zinc(II) oxide-zinc(II) molybdate composite humidity sensor. Sensor. Actuator. B Chem. 81, 229–236. doi:10.1016/s0925-4005(01)00957-1
Erol, A., Okur, S., Comba, B., Mermer, Ö., and Arıkan, M. Ç. (2010). Humidity sensing properties of ZnO nanoparticles synthesized by sol-gel process. Sensor. Actuator. B Chem. 145, 174–180. doi:10.1016/j.snb.2009.11.051
Erol, A., Okur, S., Yağmurcukardeş, N., and Arokan, M. Ç. (2011). Humidity-sensing properties of a ZnO nanowire film as measured with a QCM. Sens. Actuators, B 152, 115–120. doi:10.1016/j.snb.2010.09.005
Estella, J., de Vicente, P., Echeverría, J. C., and Garrido, J. J. (2010). A fibre-optic humidity sensor based on a porous silica xerogel film as the sensing element. Sensor. Actuator. B Chem. 149, 122–128. doi:10.1016/j.snb.2010.06.012
Faia, P. M., and Furtado, C. S. (2013). Effect of composition on electrical response to humidity of TiO2:ZnO sensors investigated by impedance spectroscopy. Sens. Actuators, B 181, 720–729. doi:10.1016/j.snb.2013.02.027
Faia, P. M., Furtado, C. S., and Ferreira, A. J. (2004). Humidity sensing properties of a thick-film titania prepared by a slow spinning process. Sens. Actuators, B 101, 183–190. doi:10.1016/j.snb.2004.02.050
Fraga, M. A., Pessoa, R. S., Maciel, H. S., and Massi, M. (2011). “Recent developments on silicon carbide thin films for piezoresistive sensors applications,” in Silicon carbide-materials, processing and applications in electronic devices, Editor M., Hall (London, UK: InTech).
Fukatsu, N., Kurita, N, Kiode, K., and Ohashi, T. (1998). Hydrogen sensor for molten metals usable up to 1500 K. Solid State Ionics 113–115, 219–227. doi:10.1016/s0167-2738(98)00375-0
Geng, W., Yuan, Q., Jiang, X., Tu, J., Duan, L., Gu, J., et al. (2012). Humidity sensing mechanism of mesoporous MgO/KCl-SiO2 composites analyzed by complex impedance spectra and bode diagrams. Sens. Actuators, B 174, 513– 520. doi:10.1016/j.snb.2012.08.057
Guardiola, C., Pla, B., Bares, P., and Stefanopoulou, A. (2019). Cylinder charge composition observation based on in-cylinder pressure measurement. Measurement 131, 559–568. doi:10.1016/j.measurement.2018.08.024
Hassen, M. A., Clarke, A. G., Swetnam, M. A., Kumar, R. V., and Fray, D. J. (2000). High temperature humidity monitoring using doped strontium cerate sensors. Sens. Actuators, B 69, 138–143.
He, T., Zhang, T., Zheng, W., Wang, R., Liu, X., Xia, Y., et al. (2010). Humidity sensing properties of BaTiO3 nanofiber prepared via electrospinning. Sens. Actuators, B, 146, 98–102.
Huixia, L., Yong, L., Yanni, T., Lanlan, L., Qing, Z., Kun, L., and Hanchun, T. (2015). Room temperature gas sensing properties of tubular Hydroxyapatite. New J. Chem. 39, 3865–3874. doi:10.1039/c4nj02352h
Islam, T., and Saha, H. (2006). Hysteresis compensation of a porous silicon relative Humidity sensor using ANN technique. Sens. Actuators, B 114, 334–343. doi:10.1016/j.snb.2005.05.022
Janata, J. (2009). Principles of chemical sensors. 2nd ed., Berlin, Germany: Springer Science & Business Media, 340.
Jaouali, I., Hamrouni, H., Moussa, N., Faouzi Nsib, M., Angel Centeno, M., Bonavita, A., et al. (2017). LaFeO3ceramics as selective oxygen sensors at mild temperature. Ceramics Int. 44, 4183–4189. doi:10.1016/j.ceramint.2017.11.221
Javed, U., Ramaiyan, K. P., Kreller, C. R., Brosha, E. L., Mukundan, R., and Morozov, A. V. (2018). Using sensor arrays to decode NOx/NH3/C3H8 gas mixtures for automotive exhaust monitoring. Sens. Actuat. B 264, 110–118. doi:10.1016/j.snb.2018.02.069
Je, C. H., Lee, S. Q., and Yang, W. S. (2016). High sensitivity surface micromachined absolute pressure sensor. Procedia Engineering 168, 725–728. doi:10.1016/j.proeng.2016.11.261
Jen, Y.-J., Lin, M.-J., and Chao, J.-H. (2010). Single dielectric columnar thin film as a humidity sensor. Sens. Actuators, B 149, 67–70. doi:10.1016/j.snb.2010.06.029
Jouanny, I., Palisaitis, J., and Ngo, C. (2013). In situ transmission electron microscopy studies of the kinetics of Pt-Mo alloy diffusion in ZrB 2 thin films. Appl. Phys. Lett. 103 (12), 1–11. doi:10.1063/1.4820581
Kadhim, I. H., and Hassan, H. A. (2017). Hydrogen gas sensing based on SnO2 nanostructure prepared by sol-gel spin coating method. J Elec Materi 46, 1419–1426. doi:10.1007/s11664-016-5166-1
Kato, N., Ikoma, N., and Nishikawa, S. (1996). Exhaust gas temperature sensor for OBD-II catalyst monitoring, SAE International, SAE Technical Paper.
Khairnar, R. S., Kokol, V., and Anjum, S. R. (2015). Development of Hydroxyapatite nanoceramic for methanol and ethanol sensor. Int. J. Pure Appl. Res. Eng. Tech. 3(8), 379–386.
Kim, Y.-S., Hwang, I.-S., Kim, S.-J., Lee, C.-Y., and Lee, J.-H. (2008). CuO nanowire gas sensors for air quality control in automotive cabin. Sens. Actuat. B 135, 298–303. doi:10.1016/j.snb.2008.08.026
Kong, J., Franklin, N. R., Zhou, C. W., Chapline, M. G., Peng, S., Cho, K. J., et al. (2000). Nanotube molecular wires as chemical sensors. Science 287, 622–625. doi:10.1126/science.287.5453.622
Kotnala, R. K., Shah, J., Singh, B., Kishan, H., Singh, S., Dhawan, S. K., et al. (2008). Humidity response of Li-substituted magnesium ferrite. Sens. Actuators, B 129, 909–914. doi:10.1016/j.snb.2007.10.002
Kotnala, R. K., Shah, J., and Gupta, R. (2013). Colossal humido resistance in ceria added magnesium ferrite thin film by pulsed laser deposition. Sens. Actuators, B 181, 402–409. doi:10.1016/j.snb.2013.02.020
Kuutti, S., Fallah, S., Katsaros, K., Dianati, M., Mccullough, F., and Mouzakitis, A. (2018). A survey of the state-of-the-art localization techniques and their potentials for autonomous vehicle applications. IEEE Internet Things J. 5, 829–846. doi:10.1109/jiot.2018.2812300
Lavanya, N., Sekar, C., Fazio, E., Neri, F., Leonardi, S. G., and Neri, G. (2017). Development of a selective hydrogen leak sensor based on chemically doped SnO2 for automotive applications. Int. J. Hydrogen Energy 42, 10645–10655. doi:10.1016/j.ijhydene.2017.03.027
Lee, B., and Komarneni, S. (2005). Chemical processing of ceramics, Second ed., Boca Raton: CRC Press.
Li, X., Xiong, W., and Kale, G. M. (2005). Novel nanosized ITO electrode for mixed potential gas sensor. Electrochem. Solid-State Lett. 8, H27–H30. doi:10.1149/1.1854778
Liang, Q., Xu, H., Zhao, J., and Gao, S. (2012). Micro humidity sensors based on ZnO-In2O3 thin films with high performances. Sens. Actuators, B 165, 76–81. doi:10.1016/j.snb.2012.02.019
Liu, L., Guo, C., Li, S., Wang, L., Dong, Q., and Li, W. (2010). Improved H2 sensing properties of Co-doped SnO2 nanofibers. Sensor. Actuator. B Chem. 150, 806–810. doi:10.1016/j.snb.2010.07.022
Liu, Y. J., Shi, J., Zhang, F., Liang, H., Xu, J., and Lakhtakia, A. (2011). High- speed optical humidity sensors based on chiral sculptured thin films. Sens. Actuators, B 156, 593–598. doi:10.1016/j.snb.2011.02.003
Logothetis, E. M. (1991). “Automotive oxygen sensors.” in: Chemical sensor technology, Editor N., Yamazoe (Amsterdam, Netherlands: Elsevier) , Vol. 3, 89–104.
Majumdar, S., and Banerji, P. (2009). Moisture sensitivity of p-ZnO/n-Si heterostructure. Sens. Actuators, B 140, 134–138. doi:10.1016/j.snb.2009.03.053
Martin, L. P., Pham, A. Q., and Glass, R. S. (2003). Effect of Cr2O3 electrode morphology on the nitric oxide response of a stabilized zirconia sensor. Sens.Actuat. B 96, 53–60.
Maskell, W. C., and Page, J. A. (1999). Detection of water vapour or carbon dioxide using a zirconia pumpgauge sensor. Sens. Actuators, B 57, 99–107. doi:10.1016/s0925-4005(99)00139-2
Matsuguchi, M., Umeda, S., Sadaoka, Y., and Sakai, Y. (1998). Characterization of polymers for a capacitive-type humidity sensor based on water sorption behavior. Sensor. Actuator. B Chem. 49, 179–185. doi:10.1016/s0925-4005(98)00117-8
Meng, Z., Zhang, H., Zhu, M., Wei, X., Cao, J., Murtaza, I., et al. (2020). Lead Zirconate Titanate (a piezoelectric ceramic)-based thermal and tactile bimodal organic transistor sensors. Org. Electron. 80, 105673. doi:10.1016/j.orgel.2020.105673
Miura, N., Kurosawa, H., Hasei, M., Lu, G., and Yamazoe, N. (1996). Stabilized zirconia-based sensor using oxide electrode for detection of NOx in high-temperature combustion-exhausts. Solid State Ionics. 86-88,1069–1073. doi:10.1016/0167-2738(96)00252-4
Miura, N., Nakatou, M., and Zhuiykov, S. (2004). Development of NOx sensing devices based on YSZ and oxide electrode aiming for monitoring car exhausts. Ceram. Int. 30, 1135–1139. doi:10.1016/j.ceramint.2003.12.014
Mohan, P., Shinta, R., Fujiwara, J., Takahashi, H., Mott, D., and Matsumura, Y. (2012). Boehmite nanorod/gold nanoparticle nanocomposite film for an easy-to- Use optical humidity sensor. Sens. Actuators, B 168, 429–435. doi:10.1016/j.snb.2012.04.055
Mohankumar, P., Ajayan, J., Yasodharan, R., Devendran, P., and Sambasivam, R. (2019). A review of micromachined sensors for automotive applications. Measurement 140(40), 305–322. doi:10.1016/j.measurement.2019.03.064
Mondal, B., Basumatari, B., Das, J., Roychaudhury, C., Saha, H., and Mukherjee, N. (2014). ZnO-SnO2 based composite type gas sensor for selective hydrogen sensing. Sensor. Actuator. B Chem. 194, 389–396. doi:10.1016/j.snb.2013.12.093
Moos, R., Müller, R., Plog, C., Knezevic, A., Leye, H., and Irion, E. (2002). Selective ammonia exhaust gas sensor for automotive applications. Sens. Actuat. B 83, 181–189. doi:10.1016/s0925-4005(01)01038-3
Neri, G., Bonavita, A., Galvagno, S., Pace, C., Patanè, S., and Arena, A. (2001). Humidity sensing properties of Li-iron oxide based thin films. Sensor. Actuator. B Chem. 73, 89–94. doi:10.1016/s0925-4005(00)00679-1
Neumeier, S., Echterhof, T., Bölling, R., Pfeifer, H., and Simon, U. (2008). Zeolite based trace humidity sensor for high temperature applications in hydrogen atmosphere. Sens. Actuators, B 134, 171–174. doi:10.1016/j.snb.2008.04.022
Okada, A. (2009). Ceramic technologies for automotive industry: current status and perspectives. Mater. Sci. Eng., B 161, 182–187. doi:10.1016/j.mseb.2008.11.017
Oprea, A., Bârsan, N., and Weimar, U. (2009). Work function changes in gas sensitive materials: fundamentals and applications. Sensor. Actuator. B Chem. 142, 470–493. doi:10.1016/j.snb.2009.06.043
Pal, B. N., and Chakravorty, D. (2006). Humidity sensing by composites of glass ceramics containing silver nanoparticles and their conduction mechanism. Sensor. Actuator. B Chem. 114, 1043–1051. doi:10.1016/j.snb.2005.07.065
Parikh, K., Cattanach, K., Rao, R., Suh, D.-S., Wu, A., and Manohar, S. K. (2006). Flexible vapour sensors using single walled carbon nanotubes, Sensor. Actuator. B Chem. 113, 55–63. doi:10.1016/j.snb.2005.02.021
Park, P., Ruffieux, D., and Makinwa, K. A. A. (2015). A thermistor-based temperature sensor for a real-time clock with. IEEE J. Solid-State Circ. 50, 1571–1580. doi:10.1109/jssc.2015.2417806
Pelino, M., Cantalini, C., Sun, H.-T., and Faccio, M. (1998). Silica effect on α-Fe2O3 humidity sensor1Presented at the 2nd East Asia conference on chemical sensors, Xi'an, P.R. China, 1995.1. Sensor. Actuator. B Chem. 46, 186–193. doi:10.1016/s0925-4005(98)00113-0
Peng, M., Ding, Z., Wang, L., and Cheng, X. (2019). Detection of Sleep Biosignals Using an Intelligent Mattress based on Piezoelectric Ceramic Sensors. Sensors 19 (18), 3843. doi:10.3390/s19183843
Perara-Mercado, Y. A., Castruita-de Leon, G., and Polanco Piñerez, G. (2018). Chapter 4“Porous ceramic sensors: hydrocarbon gas leaks,”in Recent advances in porous ceramics, (London, UK: InTech) Chap. 4.
Richerson, D. W., and Lee, W. E. (2018). Modern ceramic engineering: properties, processing, and use in design, fourth ed., (Boca Raton, CRC Press).
Ritter, T., Hagen, G., Lattus, J., and Moos, R. (2018). Solid state mixed-potential sensors as direct conversion sensors for automotive catalysts. Sens. Actuat. B 255, 3025–3032. doi:10.1016/j.snb.2017.09.126
Rizi, V. S., Sharifianjazi, F., Jafarikhorami, H., Parvin, N., Fard, L. S., Irani, M., et al. (2019). Sol–gel derived SnO2/Ag2O ceramic nanocomposite for H2 gas sensing applications. Mater. Res. Express, 6(11), 1150g2. doi:10.1088/2053-1591/ab511e
Sears, W. M. (2000). The effect of oxygen stoichiometry on the humidity sensing characteristics of bismuth iron molybdate. Sens. Actuators, B 67, 161–172. doi:10.1016/s0925-4005(00)00395-6
Sears, W. M. (2005). The effect of DC polarization on the humidity sensing characteristics of bismuth iron molybdate. Sens. Actuators, B 107, 623–631. doi:10.1016/j.snb.2004.11.029
Shahabuddin, M., Umar, A., Tomar, M., and Gupta, V. (2017). Custom designed metal anchored SnO2 sensor for H2 detection. Int. J. Hydrogen Energy 42, 4597–4609. doi:10.1016/j.ijhydene.2016.12.054
Sharma, A. K., and Gupta, A. (2013). Design of a plasmonic optical sensor probe for humidity-monitoring. Sensor. Actuator. B Chem. 188, 867–871. doi:10.1016/j.snb.2013.08.002
Shen, Y., Wang, W., Fan, A., Wei, D., Liu, W., Han, C., et al. (2015). Highly sensitive hydrogen sensors based on SnO2 nanomaterials with different morphologies,Int. J. Hydrogen Energy 40, 15773–15779. doi:10.1016/j.ijhydene.2015.09.077
Sheng, M., Gu, L., Kontic, R., Zhou, Y., Zheng, K., Chen, G., et al. (2012). Humidity sensing properties of bismuth phosphates. Sensor. Actuator. B Chem. 166-167, 642–649. doi:10.1016/j.snb.2012.03.030
Sheng, C., Yu, Y., Yu, Y., Mi, L., Tang, G.-C., Song, L.-X., et al. (2013). Microstructure and thermal characterization of multilayer insulation materials based on silica aerogels. J. Inorg. Mater. 28(7), 790–794.
Singh, G., Kohli, N., and Singh, R. C. (2017). Preparation and characterization of Eu-doped SnO2 nanostructures for hydrogen gas sensing. J. Mater. Sci. Mater. Electron. 28, 2257–2266. doi:10.1007/s10854-016-5796-3
Somani, P. R., Viswanath, A. K., Aiyer, R. C., and Radhakrishnan, S. (2001). Charge transfer complexforming dyes incorporated in solid polymer electrolyte for optical humidity sensing. Sens. Actuators, B 80, 141–148. doi:10.1016/s0925-4005(01)00907-8
Song, X., Qi, Q., Zhang, T., and Wang, C. (2009). A humidity sensor based on KCl-doped SnO2 nanofibers. Sens. Actuators, B 138, 368–373. doi:10.1016/j.snb.2009.02.027
Steele, J. J., van Popta, A. C., Hawkeye, M. M., Sit, J. C., and Brett, M. J. (2006). Nanostructured gradient index optical filter for high-speed humidity sensing. Sensor. Actuator. B Chem. 120, 213–219. doi:10.1016/j.snb.2006.02.003
Su, P.-G., and Chen, C.-Y. (2008). Humidity sensing and electrical properties of Na- and K-montmorillonite, Sens. Actuators, B 129, 380–385. doi:10.1016/j.snb.2007.08.032
Su, P.-G., and Lin, P.-H. (2012). Electrical and humidity sensing properties of K+-nano- mica film. Sens. Actuators, B 161, 838–844. doi:10.1016/j.snb.2011.11.043
Su, C. H., and Zhang, Z. M. (2017). Sensors made of carbon ceramic composite materials. Mater. Lett. 197, 90–93. doi:10.1016/j.matlet.2017.03.147
Su, M., Wang, J., Du, H., Yao, P., Zheng, Y., and Li, X. (2012). Characterization and humidity sensitivity of electrospun ZrO2:TiO2 hetero-nanofibers with double jets. Sensor. Actuator. B Chem. 161, 1038–1045. doi:10.1016/j.snb.2011.12.005
Su, S., Lu, F., Wu, G., Wu, D., Tan, Q., Dong, H., et al. (2017). Slot antenna integrated re-entrant resonator based wireless pressure sensor for high-temperature applications. Sensors 17, 1963–1977. doi:10.3390/s17091963
Szabo, N., and Dutta, P. K. (2004). Correlation of sensing behavior of mixed potential sensors with chemical and electrochemical properties of electrodes. Solid State Ionics. 171, 183–190. doi:10.1016/j.ssi.2004.04.019
Tan, K. M., Tjin, S. C., Chan, C. C., Mohanty, L., and Tay, C. M. (2005). High relative humidity sensing using gelatin-coated long period grating. Proc. SPIE 5855, 375–378. doi:10.1117/12.623607
Tang, J., Skotadis, E., Stathopoulos, S., Roussi, V., Tsouti, V. D., and Tsoukalas, D. (2012). PHEMA functionalization of gold nanoparticles for vapor sensing: chemi-resistance, chemi-capacitance and chemi-impedance. Sens. Actuators, B 169, 129–136. doi:10.1016/j.snb.2011.03.001
Tille, T. (2010). Automotive requirements for sensors using air quality gas sensors as an example. Proc. Eng. 5, 5–8. doi:10.1016/j.proeng.2010.09.034
Tischner, A., Maier, T., Stepper, C., and Köck, A. (2008). Ultrathin SnO2 gas sensors fabricated by spray pyrolysis for the detection of humidity and carbon monoxide. Sensor. Actuator. B Chem. 134, 796–802. doi:10.1016/j.snb.2008.06.032
Urbiztondo, M., Pellejero, I., Rodriguez, A., Pina, M. P., and Santamaria, J. (2011). Zeolite-coated interdigital capacitors for humidity sensing. Sensor. Actuator. B Chem. 157, 450–459. doi:10.1016/j.snb.2011.04.089
Van Duy, N., Toan, T. H., Hoa, N. D., and Van Hieu, N. (2015). Effects of gamma irradiation on hydrogen gas-sensing characteristics of Pd-SnO2 thin film sensors. Int. J. Hydrogen Energy 40, 12572–12580. doi:10.1016/j.ijhydene.2015.07.070
Vijaya, J. J., Kennedy, L. J., Sekaran, G., Jeyaraj, B., and Nagaraja, K. S. (2007). Effect of Sr addition on the humidity sensing properties of CoAl2O4 composites. Sensor. Actuator. B Chem. 123, 211–217. doi:10.1016/j.snb.2006.08.011
Vilaseca, M., Yagüe, C., Coronas, J., and Santamaria, J. (2006). Development of QCM sensors modified by AlPO4-18 films. Sensor. Actuator. B Chem. 117, 143–150. doi:10.1016/j.snb.2005.11.013
Viswanathan, S., Reddy, R. G., and Malas, J. C. (1997). Sensors and modeling in materials processing techniques and applications. Warrendale, PA:Minerals, Metals and Materials Society.
Wales, D. J., Parker, R. M., Gates, J. C., Grossel, M. C., and Smith, P. G. R. (2013). An investigation into relative humidity measurement using an aluminosilicate sol-gel thin film as the active layer in an integrated optical Bragg grating refractometer. Sensor. Actuator. B Chem. 188, 857–866. doi:10.1016/j.snb.2013.07.089
Wang, W., and Virkar, A. V. (2004). A conductimetric humidity sensor based on proton conducting perovskite oxides. Sens. Actuators, B 98, 282–290. doi:10.1016/j.snb.2003.10.035
Wang, B., Zhu, L. F., Yang, Y. H., Xu, N. S., and Yang, G. W. (2008a). Fabrication of a SnO2 Nanowire gas sensor and sensor performance for hydrogen. J. Phys. Chem. C 112, 6643–6647. doi:10.1021/jp8003147
Wang, J., Wang, X.-h., and Wang, X.-d. (2005). Study on dielectric properties of humidity sensing nanometer materials. Sensor. Actuator. B Chem. 108, 445–449. doi:10.1016/j.snb.2004.11.089
Wang, L., Li, D., Wang, R., He, Y., Qi, Q., Wang, Y, et al. (2008b). Study on humidity sensing property based on Li-doped mesoporous silica MCM-41. Sensor. Actuator. B Chem. 133, 622–627. doi:10.1016/j.snb.2008.03.028
Wang, R., He, Y., Zhang, T., Wang, Z., Zheng, X., Niu, L., et al. (2009). DC and AC analysis of humidity sensitive properties based on K+ doped nanocrystalline LaCo0.3Fe0.7O3. Sens. Actuators, B 136, 536–540. doi:10.1016/j.snb.2008.12.002
Wang, Y., Zhao, Z., Sun, Y., Li, P., Ji, J., and Chen, Y. (2017). Fabrication and gas sensing properties of Au-loaded SnO2 composite nanoparticles for highly sensitive hydrogen detection. Sens. Actuat. B 240, 664–673. doi:10.1016/j.snb.2016.09.024
Weng, H., Duan, F. L., Ji, Z., Chen, X., Yang, Z., Zhang, Y., et al. (2020). Electrical insulation improvements of ceramic coating for high temperature sensors embedded on aeroengine turbine blade. Ceram. Int. 46, 3600–3605. doi:10.1016/j.ceramint.2019.10.078
West, D. L., Montgomery, F. C., and Armstrong, T. R. (2005). "NO-selective" NOx sensing elements for combustion exhausts. Sensor. Actuator. B Chem. 111-112, 84–90. doi:10.1016/j.snb.2005.06.043
Wolfbeis, O. S., and Weidgans, B. M. (2006). “Fiber optic chemical sensors and biosensors: a view back,” in Optical chemical sensors, NATO science series II: mathematics, physics and chemistry. Editors F., Baldini, A. N., Chester, J., Homola, and S., Martellucci (Amsterdam, Netherlands:Springer), Chap. 2, 16–44.
Wrbanek, J., Fralick, G., and Martin, L. (2001). A thin film multifunction sensor for harsh environments. doi:10.2514/6.2001-3315
Xie, J., Wang, H., Lin, Y., Zhou, Y., and Wu, Y. (2013). Highly sensitive humidity sensor based on quartz crystal microbalance coated with ZnO colloid spheres. Sensor. Actuator. B Chem. 177, 1083–1088. doi:10.1016/j.snb.2012.12.033
Xie, M., Zhang, Y., Kraśny, M. J., Bowen, C., Khanbareh, H., and Gathercole, N. (2018). Flexible and active self-powered pressure, shear sensors based on freeze casting ceramic-polymer composites. Energy Environ. Sci., 11, 2919. doi:10.1039/c8ee01551a
Xu, C.-N., Miyazaki, K., and Watanabe, T. (1998). Humidity sensors using manganese oxides. Sensor. Actuator. B Chem. 46, 87–96. doi:10.1016/s0925-4005(97)00330-4
Xu, X., Sun, J., Zhang, H., Wang, Z., Dong, B., and Jiang, T. (2011). Effects of Al doping on SnO2 nanofibers in hydrogen sensor. Sens. Actuat. B 160, 858–863. doi:10.1016/j.snb.2011.08.072
Yadav, A. (2018). Classification and applications of humidity sensors: a review. Int. J. Res. Appl. Sci. Eng. Technol. 6 (4), 3686–3699. doi:10.22214/ijraset.2018.4616
Yadav, B. C., Yadav, R. C., and Dwivedi, P. K. (2010). Sol-gel processed (Mg-Zn-Ti) oxide nanocomposite film deposited on prism base as an opto-electronic humidity sensor. Sensor. Actuator. B Chem. 148, 413–419. doi:10.1016/j.snb.2010.05.046
Yamazoe, N., and Miura, N. (1994). Environmental gas sensing. Sensors and Actutators B: Chemical 20 (2), 95–102. doi:10.1016/0925-4005(93)01183-5
Yang, J. (2013). A harsh environment wireless pressure sensing solution utilizing high temperature electronics. Sensors 13, 2719–2734. doi:10.3390/s130302719
Yang, M., Kim, D.-H., Kim, W.-S., Kang, T. J., Lee, B. Y., Hong, S., et al. (2010). H2sensing characteristics of SnO2coated single wall carbon nanotube network sensors. Nanotechnology 21, 215501. doi:10.1088/0957-4484/21/21/215501
Yang, Y., Pan, H., Xie, G., Jiang, Y., Chen, C., Su, Y., et al. (2020). Flexible piezoelectric pressure sensor based on polydopamine- modified BaTiO3/PVDF composite film for human motion monitoring, Sensor Actuator Phys., 301, 111789. doi:10.1016/j.sna.2019.111789
Yeo, T. L., Sun, T., and Grattan, K. T. V. (2008). Fibre-optic sensor technologies for humidity and moisture measurement. Sens. Actuators, A 144, 280–295. doi:10.1016/j.sna.2008.01.017
You, L., Cao, Y., Sun, Y. F., Sun, P., Zhang, T., Du, Y., and Lu, G. Y. (2012). Humidity sensing properties of nanocrystalline ZnWO4 with porous structures. Sensor. Actuator. B Chem. 161, 799–804. doi:10.1016/j.snb.2011.11.035
Yu, Y., Dou, W., Xu, J., and Lv, X. (2020). Fabrication of high gas-tightness SiCN ceramic via PIP process for increasing sensing distance of pressure sensor. Ceram. Int. 46, 2155–2162. doi:10.1016/j.ceramint.2019.09.199
Yuk, J., and Troczynski, T. (2003). Sol-gel BaTiO3 thin film for humidity sensors. Sensor. Actuator. B Chem. 94, 290–293. doi:10.1016/s0925-4005(03)00371-x
Zhang, D., Sun, Y. E., Jiang, C., and Zhang, Y. (2017a). Room temperature hydrogen gas sensor based on palladium decorated tin oxide/molybdenum disulfide ternary hybrid via hydrothermal route. Sensor. Actuator. B Chem. 242, 15–24. doi:10.1016/j.snb.2016.11.005
Zhang, H., Li, Z., Liu, L., Xu, X., Wang, Z., Wang, W., et al. (2010b). Enhancement of hydrogen monitoring properties based on Pd-SnO2 composite nanofibers. Sensor. Actuator. B Chem. 147, 111–115. doi:10.1016/j.snb.2010.01.056
Zhang, J., Wang, Y., and Zheng, W. (2017b). Development of a novel electrochemical sensor for determination of matrine in Sophora flavescent. Molecules 22 (575), 1–10. doi:10.3390/molecules22040575
Zhang, W., Chen, L., Yang, Z., and Peng, J. (2011). An optical humidity sensor based on Li3PO4 hollow nanospheres. Sens. Actuators, B 155, 226–231. doi:10.1016/j.snb.2010.11.052
Zhang, W., Feng, C., and Yang, Z. (2012a). An inward replacement/etching route to controllable fabrication of zinc sulfide nanotube arrays for humidity sensing. Sens. Actuators, B 165, 62–67. doi:10.1016/j.snb.2012.02.013
Zhang, Y., Chen, Y., Zhang, Y., Cheng, X., Feng, C., and Chen, L. (2012b). A novel humidity sensor based on NaTaO3 nanocrystalline. Sens. Actuators, B 174, 485–489. doi:10.1016/j.snb.2012.08.050
Zhang, Y., Fu, W., Yang, H., Li, M., Li, Y., and Zhao, W. (2008). A novel humidity sensor based on Na2Ti3O7 nanowires with rapid response-recovery. Sens. Actuators, B 135, 317–321. doi:10.1016/j.snb.2008.08.042
Zhang, Y., Zheng, X., Zhang, T., Gong, L., Dai, S., and Chen, Y. (2010a). Humidity sensing properties of the sensor based on Bi0.5K0.5TiO3 powder, Sens. Actuators B 147, 180–184. doi:10.1016/j.snb.2010.03.045
Zhao, J., Liu, Y., Li, X., Lu, G., You, L., Liang, X., et al. (2013). Highly sensitive humidity sensor based on high surface area mesoporous LaFeO3 prepared by a nanocasting route. Sensor. Actuator. B Chem. 181, 802–809. doi:10.1016/j.snb.2013.02.077
Zhou, M., and Ahmad, A. (2008). Sol-gel processing of In-doped CaZrO3 solid electrolyte and the impedimetric sensing characteristics of humidity and hydrogen. Sensor. Actuator. B Chem. 129, 285–291. doi:10.1016/j.snb.2007.08.022
Zhou, Q., Chen, W., Xu, L., Kumar, R., Gui, Y., Zhao, Z., et al. (2018). Highly sensitive carbon monoxide (CO) gas sensors based on Ni and Zn doped SnO2 nanomaterials. Ceram. Int. 44(4), 4392–4399. doi:10.1016/j.ceramint.2017.12.038
Zhou, Y., Wang, H., Sheng, M., Zhang, Q., Zhao, Z., Lin, Y., et al. (2013). Environmentally friendly room temperature synthesis and humidity sensing applications of nanostructured Bi2O2CO3, 2013. Sens. Actuators, B 188 1312–1318. doi:10.1016/j.snb.2013.08.041
Zhu, S., Liu, Y., Wu, G., Fei, L., Zhang, S., Hu, Y., et al. (2019). Mechanism study on extraordinary room-temperature CO sensing capabilities of Pd-SnO2 composite nanoceramics. Sensor. Actuator. B Chem. 285, 49–55. 10.1016/j.snb.2019.01.027
Zhuiykov, S., and Miura, N. (2005). “Solid-state electrochemical gas sensors for emission control,” in Materials for energy conversion devices, (Amsterdam, Netherlands: Elsevier), 303–335.
Zhuiykov, S., Ono, T., Yamazoe, N., and Miura, N. (2002). High-temperature NOx sensors using zirconia solid electrolyte and zinc-family oxide sensing electrode. Solid State Ion. 152,801–807. doi:10.1016/s0167-2738(02)00331-4
Zhu, Y., Yuan, H., Xu, J., Xu, P., and Pan, Q. (2010). Highly stable and sensitive humidity sensors based on quartz crystal microbalance coated with hexagonal lamelliform monodisperse mesoporous silica SBA-15 thin film. Sens. Actuators, B 144, 164–169. doi:10.1016/j.snb.2009.10.053
Keywords: ceramics, ceramic sensors, industrial, medical, electronic, automotive and aviation sensors
Citation: Krishna Prasad NV, Venkata Prasad K, Ramesh S, Phanidhar SV, Venkata Ratnam K, Janardhan S, Manjunatha H, Sarma MSSRKN and Srinivas K (2020) Ceramic Sensors: A mini-review of their applications. Front. Mater. 7:593342. doi: 10.3389/fmats.2020.593342
Received: 10 August 2020; Accepted: 05 October 2020;
Published: 27 November 2020.
Edited by:
Ravinder Dachepalli, Osmania University, IndiaReviewed by:
Rajender Boddula, National Center for Nanoscience and Technology (CAS), ChinaCopyright © 2020 Krishna Prasad, Venkata Prasad, Ramesh, Phanidhar, Ratnam, Janardhan, Manjunatha, Sarma and Srinivas. This is an open-access article distributed under the terms of the Creative Commons Attribution License (CC BY). The use, distribution or reproduction in other forums is permitted, provided the original author(s) and the copyright owner(s) are credited and that the original publication in this journal is cited, in accordance with accepted academic practice. No use, distribution or reproduction is permitted which does not comply with these terms.
*Correspondence: N. V. Krishna Prasad, ZHJudmtwcmFzYWRAZ21haWwuY29t
Disclaimer: All claims expressed in this article are solely those of the authors and do not necessarily represent those of their affiliated organizations, or those of the publisher, the editors and the reviewers. Any product that may be evaluated in this article or claim that may be made by its manufacturer is not guaranteed or endorsed by the publisher.
Research integrity at Frontiers
Learn more about the work of our research integrity team to safeguard the quality of each article we publish.