- State Key Laboratory of Solidification Processing, Northwestern Polytechnical University, Xi’an, China
In this study high-entropy alloys (HEAs) were devised based on a new alloy design concept, which breaks with traditional design methods for conventional alloys. As a novel alloy, HEAs have demonstrated excellent engineering properties and possible combinations of diverse properties for their unique tunable microstructures and properties. This review article explains the phase transition mechanism and mechanical properties of high-entropy alloys under the thermal-mechanical coupling effect, which is conducive to deepening the role of deformation combines annealing on the structure control and performance improvement of high-entropy alloys, giving HEAs a series of outstanding performance and engineering application prospect. To reach this goal we have explored the microstructural evolution, formation of secondary phases at high and/or intermediate temperatures and their effect on the mechanical properties of the well known AlxCoCrFeNi HEAs system, which not only has an important role in deepening the understanding of phase transition mechanism in AlxCoCrFeNi HEAs, but also has important engineering application value for promoting the application of high-entropy alloys.
Introduction
The design and development of structural materials that are suitable for extreme environments such as high temperatures, cryogenic environments, or situations that involve irradiation and corrosion, etc., are a high priority in the fields of materials science and technology. Modern technological developments in engineering, particularly in the nuclear, turbine, and aerospace industries, require new structural materials to provide higher performance than the currently available commercial alloys. Cantor et al. (2004) and Yeh et al. (2004) took the lead in adapting the traditional design methodology of alloys in 2004 and proposed the novel concept of alloy design, in which five or more elements are mixed in equiatomic or near equiatomic concentrations, such that the high configurational entropy
In the field of HEAs, solute and solvent cannot be applied in the conventional alloy and the theoretical strengthening system needs to be verified. The optimization of the mechanical properties of high-entropy alloys is thus challenging. Recently, studies have focused on overcoming the strength-ductility trade off, by introducing high-density nano-twins in the grains (Lu, 2016; Schneider et al., 2020), as processing fine grains combined with nanoscale precipitates even distribution within the grains (Zhao et al., 2020b; Guillot et al., 2020; Yu et al., 2020), controlling the lattice misfit between intermetallic nanoparticles and matrix (Miracle, 2015; He et al., 2016a; Zhang et al., 2019) and producing materials with a heterogeneous structure (Sun et al., 2018; Wu et al., 2019; Du et al., 2020). The successful preparation of eutectic high-entropy alloy (EHEA) provided a new way to optimize the phase structure of HEAs by combining the ductile phase (e.g., fcc solid-solution phase) with the hard phase (e.g., bcc solid-solution phase or intermetallics) (Lu et al., 2014; Tan et al., 2019). This structure design could be realized through a simple and effective way of thermal-mechanical processing, offering a feasible strategy for a new generation of high-strength and high-toughness HEAs. Through cold rolling and annealing processing, the size, volume fraction, and distribution of the nano-sized particles (L12-Ni3(Ti, Al), L21-(Ni, Co)2TiAl, sigma (σ) or μ intermetallic phases) formed within the fcc phase matrix of HEAs could be controlled effectively, improving strain hardening ability by interacting with dislocations in plastic deformation (He et al., 2016b; Liu et al., 2016). An excellent balance between strength and ductility was obtained in the as-cast AlCoCrFeNi2.1 EHEA (Lu et al., 2014). After extra heavily cold rolling and annealing, it showed significant improvement in tensile properties, with an ultimate tensile strength (UTS) of 1,200 MPa and elongation to failure (ef) ∼12% (Wani et al., 2016). Through cold rolling and subsequent annealing, different types of precipitates were formed within the matrix of the FeCoNiCrTi0.2 HEA, improving strength and ductility at the same time (Tong et al., 2019). It is expected that the mechanical properties of HEAs could be successfully tailored using simple thermo-mechanical processing and further extended to bulk engineer materials for industrial application.
Earlier studies have tended to focus on single-phase HEAs with equal atomic ratio. However, phase stability is easily be impacted by alloying or moderate temperature annealing, which has a further effect on mechanical properties (Zhang et al., 2017; Macdonald et al., 2019). In addition, there are often some fatal disadvantages concomitantly, in that poor fluidity and castability may cause considerable chemical inhomogeneity in single-phase HEAs (Lu et al., 2014; Lu et al., 2017). It is hard to achieve excellent balanced tensile properties, e.g., the single fcc phase HEAs are usually soft while the single bcc phase HEAs are hard and brittle (Wang et al., 2012; Guo et al., 2013; Liu et al., 2019b). Thus, researchers have increasingly kept a watchful eye on not only the single-phase HEAs but also multiphase HEAs. By altering the composition of the alloying elements, the results of Stepanov et al. (2015) showed that the volume fraction of σ phase was related to the concentration of accumulated Cr and V elements. It was reported that the addition of Ni in AlCoCrFeMo0.5Nix alloys promoted the formation of the fcc phase, and the Ni element was also found to be an effective fcc structural stable element (Juan et al., 2013). Among them, AlxCoCrFeNi HEAs have been perceived as potentially important engineering materials as the inherent crystal structure can evolve from fcc into bcc with the variation of Al concentration (Chou et al., 2009; Wang et al., 2012; Garlapati et al., 2020). It has attracted a wide range of research interest due to its excellent physical and mechanical properties (e.g., creep behavior, dynamical mechanical property, impact toughness, magnetic properties, and resistivity–temperature behavior) (Kao et al., 2011; Ma et al., 2014; Cao et al., 2016; Cieslak et al., 2018; Xia et al., 2018; Wang et al., 2019a; Zhao et al., 2020a; Wang et al., 2020).
This review reports on recent advancements in thermal-mechanical processing and its effect on microstructural evolution and phase transformation in AlxCoCrFeNi HEAs. It also correlates insights into the mechanical properties and strengthening of HEAs, especially the evolution of hardness, plasticity, and strength under tension and compression at room temperature as well as at high temperatures with the phase structure, are also correlated.
Development and Mechanical Properties of AlxCoCrFeNi HEAs
Development of AlxCoCrFeNi HEAs
In the initial stage of the HEA research field, the HEA systems containing Cu were widely exploited due to the improvement of plasticity (Cantor et al., 2004; Chen et al., 2004; Yeh et al., 2004; Wu et al., 2006; Tung et al., 2007; Sriharitha et al., 2013). However, Cu tended to segregate at grain boundary for its high enthalpy of mixing with other elements. Meanwhile, the AlxCoCrCuFeNi HEA system has been carefully studied and the variation of Al content was found to bring significant changes in microstructure and mechanical properties of AlxCoCrCuFeNi (Tong et al., 2005a; Tong et al., 2005b; Wu et al., 2006; Tung et al., 2007). The compressive properties of AlCoCrFeNi alloy without Cu were investigated, showing a combination of excellent compressive strength (∼2004 MPa) and plastic strain (∼32.7%) (Wang et al., 2008). The Cu-free AlxCoCrFeNi HEA system has subsequently received increasing attention in the last decade.
Effects of Al Addition on Microstructure of AlxCoCrFeNi HEAs
The resultant phases in all the investigated as-cast AlxCoCrFeNi HEA system (x = 0–3) were: only solid-solution structures, mainly fcc, bcc or their mixture (Kao et al., 2009; Li et al., 2009; Ma et al., 2014; Wang et al., 2014; Zuo et al., 2014; Niu et al., 2016; Xia et al., 2016; Gangireddy et al., 2018a; Gangireddy et al., 2018b; Liu et al., 2018; Zhou et al., 2018; Annasamy et al., 2019; Li et al., 2019; He et al., 2020). Alloys with low Al contents (x = 0–0.3) exhibited the simple fcc structure, as x exceeded ∼0.5, the bcc phase formed out of the fcc solid solution phase. Spinodal decomposition occurred later with an increase in Al content, leading to the formation of ordered (NiAl-type) and disordered bcc (A2) phases. Rao et al. (2016) also reported a fcc-bcc crystallographic orientation relationship between the precipitation and fcc matrix: (1) (1−10)bcc//(200)fcc and [001]bcc//[001]fcc; (2) (1−11)B2//(2−20)fcc and [011]B2//[
The mechanism of bcc phase formation in AlxCoCrFeNi has received much attention. Kao et al. (2009) investigated the microstructural evolution of as-cast, -homogenized (1,100°C/24 h), and -deformed (1,100°C/24 h + 50% CR) AlxCoCrFeNi (0 ≤ x ≤ 2) high-entropy alloys. They reported that the structure of as-cast was sequentially single fcc (x < 0.45), duplex fcc–bcc (0.45 ≤ x ≤ 0.88), and single bcc (x > 0.88). While the x intervals for the existence of duplex phase in -homogenized and -deformed AlxCoCrFeNi alloys are 0.30 ≤ x ≤ 1.17 and 0.30 ≤ x ≤ 0.875, respectively, indicating the widening of the range of two-phase regions after homogenization treatment. The Al element was found to be a bcc stabilizer in AlxCoCrFeNi alloys. Jasiewicz et al. (2015) elucidated the phase stability of AlxCoCrFeNi (x ≤ 3) HEAs based on experimental data and computational results and found that the fcc phase was more stable when x < 0.62, and the range of fcc/bcc two-phase region was 0.5 ≤ x ≤ 1.0. Ogura et al. (2017) also illustrated the effect of Al addition on phase transition in AlxCoCrFeNi alloys via first principles electronic structure calculations and an increase in Al content lowered the total energy difference between fcc and bcc.
Thermodynamic Appraisal of AlxCoCrFeNi HEAs
To accelerate the characterization of the composition-structure-property relationship of AlxCoCrFeNi HEAs, a calculation of phase diagrams (CALPHAD) approach was developed to predict the phase relationship in previous studies (Xia et al., 2016; Butler and Weaver, 2017; Rao et al., 2017; Gwalani et al., 2018; Shi et al., 2018; Komarasamy et al., 2019).
Xia et al. (2016) successfully predicted the phase diagram of the AlxCoCrFeNi (x = 0–2) alloy system through the CALPHAD approach using the PanHEA database. The experimental observations of AlxCoCrFeNi (x = 0.1, 0.75 and 1.5, respectively) were consistent with the predicted equilibrium phases diagrams. The fcc phase was stable over a wide temperature range of 645–1434 C for Al0.1CoCrFeNi alloy, whereas decomposition occurred at lower temperatures below 500 C. In addition, the predicted primary phase is the fcc phase and the B2 phase for the Al0.75CoCrFeNi alloy and Al1.5CoCrFeNi alloy, respectively. Komarasamy et al. (2019) chose the aging condition based on the pseudo-binary phase diagram using the PANDAT HEA database to develop the Ni3Al (L12-type), B2 (Al–Ni based), and Al3Ni particles to strengthen the Al0.5CoCrFeNi alloy. The existence of B2 precipitates was predicted for all heat treatment conditions except for 550°C, where L12 phases formed. The experimental phase relationship agreed well with the calculated result. To understand the phase stability and transformation pathway of Al0.3CoCrFeNi alloy under different thermal treatments, Gwalani et al. (2018) calculated the molar fraction of equilibrium phases as a function of the temperature for the alloy. Based on the calculated equilibrium phase data, the fcc-based Al0.3CoCrFeNi alloy was metastable at 620°C, and thus providing the possibility for the formation of new phases. All of these suggest that this way of calculating equilibrium phase diagrams provides useful guidance for the prediction of phases in the AlxCoCrFeNi HEAs.
Mechanical Properties of AlxCoCrFeNi HEAs
The Al content has a significant impact on the mechanical properties of the AlxCoCrFeNi HEA system. With the Al addition, the as-cast AlxCoCrFeNi alloys become much stronger, arising from the formation of bcc structures. The transition from fcc to bcc led to the hardness values varying from ∼120 to ∼570 Hv (Wang et al., 2012). The as-forged AlxCoCrFeNi alloys exhibited excellent mechanical properties at both room and cryogenic temperatures. The yield strength and tensile strength of the Al0.1CoCrFeNi alloy reached 412 and 1,042 MPa, while the yield strength and tensile strength of the Al0.3CoCrFeNi alloy were 515 and 1,010 MPa at 77 K, respectively. Different from conventional alloys, the plasticity of HEAs increased significantly with the decrease of temperature (Li and Zhang, 2016).
Optimizing the thermal-mechanical processing of the low-Al AlxCoCrFeNi alloys is a promising method of enhancing mechanical properties. Recent studies have indicated that the combined strength-ductility results from the complex interplay between multiple strengthening mechanisms, which are created by cold rolling and subsequent annealing (Gwalani et al., 2020). A strong Hall–Petch hardening effect with refining grains could be obtained in single-phase Al0.3CoCrFeNi alloy (Gwalani et al., 2017). Aging the alloy at 550–900°C led to the precipitation of nano-scaled B2 and/or σ intermetallic precipitates. Complex reinforcement effects resulting from fine fcc grains, intermetallic B2, and/or σ grains resulted in the unusually high strength of Al0.3CoCrFeNi HEA. Furthermore, the atomic distribution of Al-rich nano-clusters within the fcc phase brought about additional strength in the CR-550 condition (Gwalani et al., 2020). The significant changes in the phase structure and mechanical properties induced by the Al addition make this alloy system a desirable candidate material for structural materials with tunable strength.
Thermal Induced Phase Transition and Its Effect on AlxCoCrFeNi HEAs
Thermal Induced Phase Transformation
Thermodynamic Ways of Annealing
The fcc-type CoCrFeNi HEA was generally considered to be thermally stable in the as-cast condition. However, after annealing at 750°C for 800 h, composition decomposition occurred and the minor addition of Al could further shorten the duration (He et al., 2017). The annealing temperature is one of the key factors that determine phase compositions. Prolonged annealing could also promote the second phase to precipitate from the matrix or along the grain boundary. Therefore, the investigation for the phase equilibria and phase stabilities of a series of AlxCoCrFeNi HEAs is significant, since they could influence the material design for applications at an intermediate temperature and expected component lifetime.
The room and high temperature XRD (from 573 to 1,373 K) patterns of the AlxCoCrFeNi (x = 0–1.8) alloys demonstrated that crystal structure remained stable, except in Al0.9–Al1.2 alloys (Wang et al., 2014). The (Ni, Al)-rich acicular precipitates formed within the dendritic region of Al0.5, while Al0.3 remained a simple fcc phase with uniform composition after aged at 1,173 and 1,373 K for 2 h. A spinodal formed two-phase microstructure, consisting of disordered (Fe, Cr)-rich phase and ordered (Ni, Al)-rich phase, was observed in both as-cast Al0.9 and Al1.5 alloys. For the Al0.9–Al1.2 alloys, in line with the DSC analysis, the phase transition from bcc to fcc took place at 873 K and the appearance of σ phase was also observed at the temperature range of 873–1173 K, which depended on Al content. Butler and Weaver (2017) investigated the phase equilibria and phase stabilities of AlxCoCrFeNi HEAs through methodically coupling the experimental results with predictions based on CALPHAD models. The coarsening of microstructures that consist of fcc, bcc, and/or ordered B2 phases occurred in all the alloys after annealing at 1,050°C. Annealing at 700°C conduced to stabilizing the mixed structure of fcc, bcc, B2, and/or σ phases depending on the relative concentration of Al. EDS analysis showed the Al depletion and Cr enrichment in fcc and bcc phases, respectively, while the B2 phase was enriched in Al and Ni, and the σ phase was enriched in Fe and Cr, respectively. The phase prediction by modeling coincided with the experimental results in Al10Co22.5Cr22.5Fe22.5Ni22.5 and Al30Co17.5Cr17.5Fe17.5Ni17.5 HEAs but failed in Al15Co21.25Cr21.25Fe21.25Ni21.25 and Al20Co20Cr20Fe20Ni20 HEAs. The discrepancies were mainly related to destabilized components of the fcc phase at 700and 1,000°C. This indicated that CALPHAD based models were useful for predicting the phases formed in HEAs with complex components, but that the current thermodynamic database needs to be improved.
Nartu et al. (2020) investigated the effect of heat treatment on the microstructural evolution and mechanical properties of laser additively manufactured Al0.3CrFeCoNi HEA. The formation of the nano-scaled (Al, Ni)-rich clusters resulted from in-situ heat treatment during the part building and could act as the heterogeneous nucleation sites for the precipitates that form at high temperature aging. Nanometer-sized L12 or γ′ type precipitation with spherical or rod-like morphology was predominantly revealed in the grain interior after being aged at 620°C for 50 h. Larger precipitates were also found at the grain boundaries of this condition and confirmed to be Al-rich B2 and Cr-rich σ phases. Niu et al. (2017a) investigated the influence of heat treatment on the microstructure of a fcc + bcc dual-phase Al0.5CoCrFeNi alloy. The alloy changed from dendritic into spherocrystal after being heat-treated at 650°C while rod-shaped phases and elliptoid phases rich in Al–Ni were precipitated after heat treatment at 1,150°C. The Al–Ni rich nano-sized B2 phase was also found to precipitate from the interdendritic (bcc) region after heat treatment at 650°C (Niu et al., 2016). Grain coarsening occurred after heat treatment at 850°C, and the fine bcc phase emerged and distributed uniformly in the matrix, as seen in Figure 1 (Wang et al., 2017a). Another study reported the precipitation of a plate-like hexagonal closed-packed phase with high cobalt content located at the interdendritic region of the Al0.5CoCrFeNi HEA after 650°C/8 h heat-treatment (Wang et al., 2017b). Though a simple shear, the bcc phase could transform into the hcp phase, and the crystal orientation relationship between these two phases has also been to been established as [11–20]hcp || [111]bcc (000–1)hcp || (10–1)bcc. Liu et al. (2014) investigated the phase completion and stability of the AlCoCrFeNi alloy. They observed the phase transition from bcc and B2 to bcc and fcc after heat treatment at 950°C, indicating that the solid-solution phases of the as-cast alloy were unstable due to quenched-in chemical segregation. These studies suggest that the phase stability of AlxCoCrFeNi HEA should be carefully evaluated, especially at the intermediate temperature.
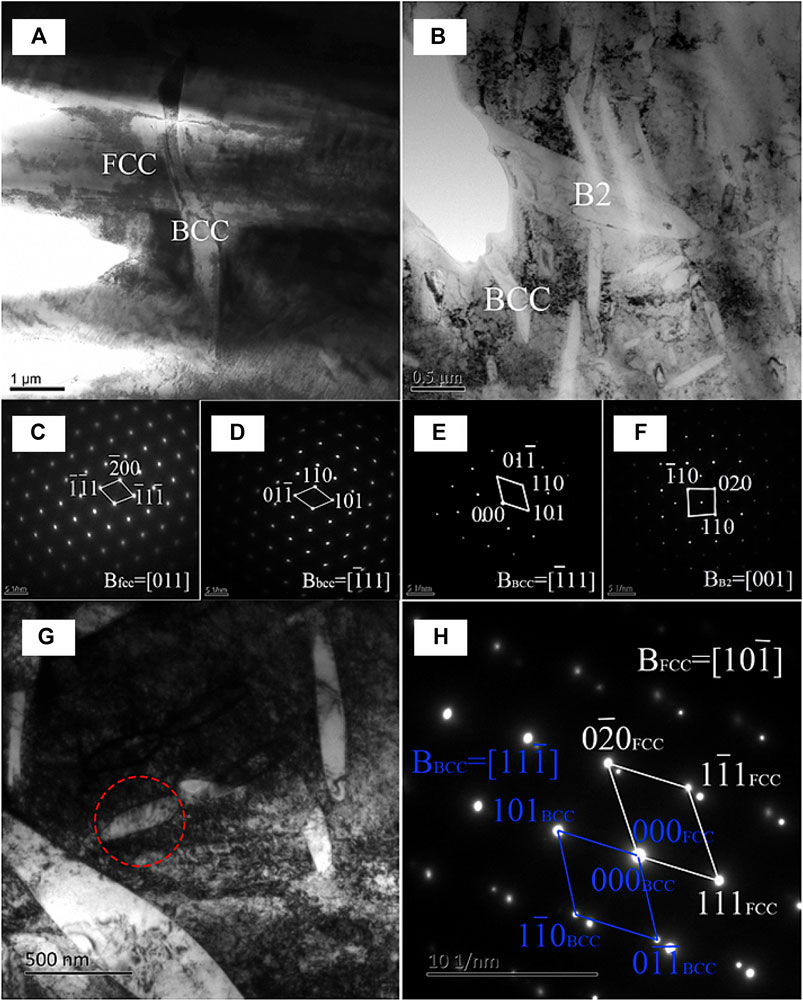
FIGURE 1. TEM bright images (A) as-cast alloy, (B,C) corresponding selected electron diffraction imagem (D,G) heat-treated alloy at 1,123 K/8 h, and (E–H) corresponding selected electron diffraction image (Wang et al., 2017a). (Reprinted from Journal of Alloys and Compounds, Vol 710, Wang et al., The FCC to BCC phase transformation kinetics in an Al0.5CoCrFeNi high entropy alloy, Pages No.148, Copyright (2017), with permission from Elsevier).
Kinetic Way of Tailoring Phases
The kinetic way is also important to the mechanism of phase evolution for HEAs. It is a way of establishing the reasonable heat treatment parameters to enhance performance. Wang et al. have inspected the phase transformation kinetics of the fcc Al0.25CoCrFeNi (Wang et al., 2018b) and fcc + bcc Al0.5CoCrFeNi (Wang et al., 2017a) HEAs during an experiment on isochronal heating by thermal dilation. The estimated activation energy and kinetic exponent were almost stable, indicating a slow and steady phase transition in an Al0.25CoCrFeNi HEA (Figure 2A). The phase transition was also a growth-controlled process without nucleation during the main transformation process, according to the decreasing trend from 1.5 to one of the determined kinetic exponent. The ordering transition from fcc to L12 occurred during the heat treatment at 650°C.
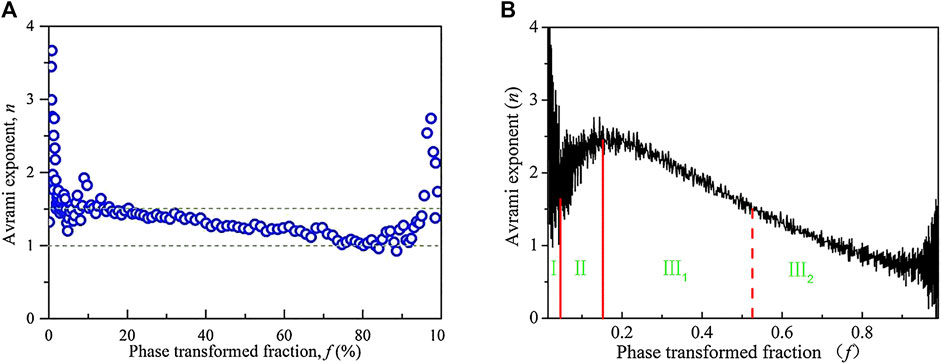
FIGURE 2. (A) The local Avrami exponent (blue circle) as a function of phase transformed fraction of Al0.25CoCrFeNi HEA (4 K/min). The green zone represents the range of n from 1 to 1.5 (Wang et al., 2018b). (B) Variation in n with the increasing volume fraction of Al0.5CoCrFeNi HEA (3 K/min). (Wang et al., 2017a).
Compared with Al0.25CoCrFeNi HEA, three stages of phase transformation were characterized in Al0.5CoCrFeNi during the continuous heating process, and the third one corresponded to the fcc-bcc phase transition. Careful research into the microstructural evolution indicated that the first two stages of phase transformation involved nanoparticle precipitation (Niu et al., 2016; Niu et al., 2017a), whereas the transition from fcc to bcc took place in the third phase transformation. The three stages of the third phase transition were divided according to the determined Avrami exponent n (Figure 2B). Note that the third stage was divided into two parts, Ⅲ1 and Ⅲ2. The decrease of n indicated a reduced nucleation rate in Ⅲ1. In Ⅲ2 the formation of bcc structure led to a decrease of the concentration of bcc forming elements at the interface, thus further lowering the nucleation rate. The activation energy for Al0.25CoCrFeNi (198 ± 1 KJ/mol) and Al0.5CoCrFeNi (144–284 KJ/mol) HEAs was quite different, mainly due to the phase transition type differences between the two alloys, for the former it was order-disorder transition while the latter was an fcc-bcc transition. The kinetics of phase transformation in HEAs requires further exploration in future studies. In particular, it would be helpful to understand more about the phase selection through kinetic phase transformation and how this relates to annealing.
Mechanical Properties and Precipitation-Strengthening in AlxCoCrFeNi HEAs
Niu et al. (2016) reported that annealing at 650°C for 0.5 to 8 h of Al0.5CoCrFeNi HEA had a significant hardening effect, exhibiting the yield strength (YS) varying between 355 and 834 MPa strongly depending on the annealing time. The excellent tensile properties of alloy heat-treated for 8 h showed a YS of ∼834 MPa with an elongation of 25%, which could be ascribed to the dispersed nano-sized B2 phase (∼70 nm). After heat treatment at 850°C, the nano-sized B2 phase with a structure of thick slat and bcc phase with a structure of thin slat was formed in the fcc matrix. After heat treatment, a good combination of strength and plasticity was obtained by increasing the ultimate tensile strength up to 1,143 MPa and an elongation of 21.5% (Wang et al., 2017a). In Al0.3CoCrFeNi HEA single crystals, only coherent particles of the γ′-phase were detected during aging 50 h at 893 K. The interaction of slip dislocations with γ′-phase particles occurred via a shearing mechanism and the contribution to the hardening from γ′-phase particles was 25–30 MPa. The absence of grain boundaries also suppressed the formation of B2-phase particles in Al0.3CoCrFeNi HEA single crystals (Kireeva et al., 2020).
In another example for AlCoCrFeNi HEA, heat treatment at 850°C caused the phase transformation of the bcc matrix to the σ phase, drastically increasing the micro-hardness of the interdendritic region. The brittle σ phase then transformed back to the bcc matrix when heat-treated at 975°C, causing the alloy to soften, with lower micro-hardness but larger elongation. Homogenization treatment was conducted at a temperature above 1,200°C, leading to an increase both in compressive strength and compressive contraction (Munitz et al., 2016). Zhao et al. (2020a) reported that with increasing temperature from 950to 1,200°C, the increased bcc phase and disappeared σ phase could improve the compressive properties of AlCoCrFeNi with both the YS and strain increased from ∼1,069 to 1,254 MPa and ∼17–∼21%, respectively. Phase distribution was found to strongly influence the initiation and propagation of the cracks. They observed that cracks could propagate and terminate in both the dendrite (Figures 3B,C,E) and interdendritic region (Figures 3A,D,F) of the two samples. Besides, cracks changed the propagation route and then terminated at grain boundaries in the interdendritic region, which consisted of bcc matrix and B2 precipitates (Figures 3A,F), rather than stopping at the fcc grain boundaries.
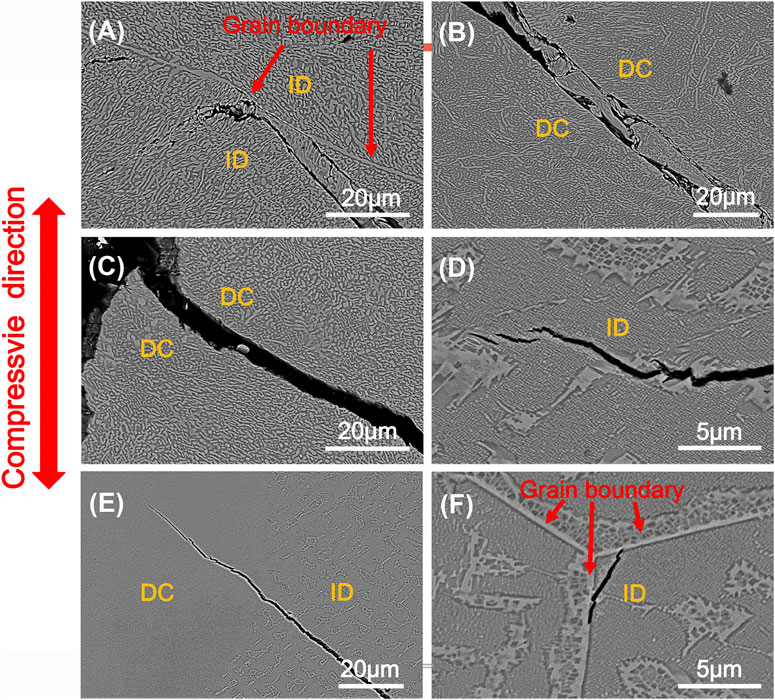
FIGURE 3. Back-scattered election images of cracks after fracture in the compressive test at different processing temperatures (A–C) 950°C, (D–F) 1,200°C (Zhao et al., 2020a). (Reprinted from Journal of Alloys and Compounds, Vol 820, Zhao et al., Effect of strong magnetic field on the microstructure and mechanical-magnetic properties of AlCoCrFeNi high-entropy alloy, Pages No.5, Copyright (2020), with permission from Elsevier).
Thermo-Mechanical Coupling Effect
Microstructure Evolution After Thermo-Mechanical Treatment
Since the effect of heat treatment on mechanical properties was limited, numerous methods including rolling, forging, tension, compression and torsion, were then adopted to strengthen the materials by inducing the plasticity of the HEAs (Yu et al., 2016;Hou et al., 2017a; Guo et al., 2018). Optimized thermal-mechanical processing by deformation and subsequent annealing could lead to the grain refinement and formation of the strengthening phase. Figure 4 exhibits the microstructures of ultrafine grains and/or nanostructured precipitates generated simply through cold deformation and annealing under different conditions (Guo et al., 2018; Gwalani et al., 2018; Shi et al., 2018; Hou et al., 2019; Wu et al., 2019; He et al., 2020). In the meantime, Wang et al. (2018c) investigated the effect of cold rolling on the fcc to bcc transformation kinetics of the Al0.5CoCrFeNi HEA and concluded that pre-deformation induced defects could facilitate the nucleation and growth process during the phase transition compared with the as-cast sample.
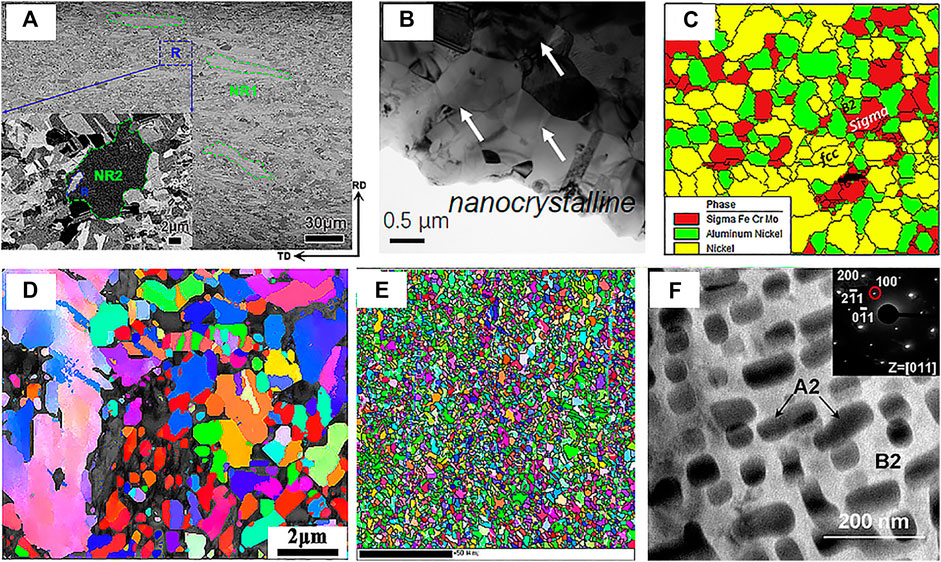
FIGURE 4. Example microstructures of AlxCoCrFeNi HEAs under different conditions (A) BSE image of the 873 K-annealed Al0.1CoCrFeNi HEA, showing the microstructure composed of three types of grains: stretched original grains, partially recrystallized grains of large size, and completely recrystallized grains of fine size (Wu et al., 2019). (B) Nanocrystalline Al0.25CoCrFeNi HEA generated by directly annealing after cold rolling (He et al., 2020). (C) Tri-phase Al0.3CoCrFeNi HEA consisting of fcc, B2 and σ phases (Gwalani et al., 2018). (D) Ultrafine-grained Al0.45CoCrFeNi HEA generated in the recrystallization area after annealing at 800°C (Hou et al., 2019). (E) Fully-recrystallized Al0.5CoCrFeNi HEA with refined grains (Guo et al., 2018). (F) Cuboidal participates with the side length ranging from 20 to 180 nm, randomly distributed in the B2 matrix of Al0.7CoCrFeNi HEA (Shi et al., 2018).
Effect of Cold Deformation and Annealing on the Microstructure
In general, thermo-mechanical processing is usually used to break and refine the coarse as-cast grains and/or second phases. However, the increase in strength was almost always along accompanied by decreased work hardenability due to the reduced dislocation storage capability of the refined structure. Therefore, a rational design of the thermo-mechanical processing is needed, to improve both strength and ductility. This section describes the effect of cold deformation and subsequent annealing on the microstructure of AlxCoCrFeNi HEAs. It reviews the recrystallization and grain growth of AlxCoCrFeNi alloys, and the effect of aging at an intermediate temperature phase structures is presented afterward.
Yang et al. (2019c) reported the gradient effect on grain size in cold-rolled and annealed Al0.1CoCrFeNi alloys. The yield strength and grain size followed the classical Hall–Petch relationship, exhibiting a grain boundary hardening efficient of 464 MPa μm1/2. Wu et al. (2019) have proposed a promising way to enhance the comprehensive mechanical properties of bulk high-entropy alloys by simple cold rolling and subsequent annealing at an intermediate temperature of 873 K. A heterogeneous structure with three types of grains was successfully generated including deformed grains, partially recrystallized grains (volume fraction of ∼37%), and fully recrystallized-equiaxed grains, with a volume fraction of ∼10, 37, and 53%, respectively, as shown in Figure 4A. The phase remained in a single fcc phase after the cold-rolled Al0.25CoCrFeNi was annealed at 1,100°C for 10 h (Hou et al., 2017b). The grain size was reduced from 230 to ∼13 μm through multiple cold rolling and annealing processes (He et al., 2020), as shown in Figure 4B. The grain size could also be adjusted in a wide range in a single fcc phase Al0.3CoCrFeNi alloy (Gwalani et al., 2017). The fcc-based Al0.3CoCrFeNi HEA was dramatically transformed to a duplex fcc- ordered B2 (Choudhuri et al., 2018b) and even a tri-phase consisting of fcc, B2, and σ phases (Figure 4C) by tuning the cold rolling and annealing at a temperature of 800°C and 620°C, respectively (Gwalani et al., 2018). The strength enhancement due to grain boundary strengthening obeyed the Hall-Petch relationship and the Hall–Petch coefficient in Al0.25 and Al0.3 alloy was ∼784 and 824 MPa μm1/2, respectively. The high Hall–Petch coefficient observed in the AlxCoCrFeNi (x = 0.1–0.3) alloy indicated that dislocation motion is more difficult in AlxCoCrFeNi (x = 0.1–0.3) HEA than conventional alloys.
Hou et al. (2019) investigated the grain growth behavior of cold-rolled Al0.45CoCrFeNi alloy after heat treatment at 700–1,100°C. Shear bands could still be retained after annealing at 800°C due to recrystallization. Ultrafine recrystallized fcc grains with an average grain size of 0.62 μm were generated, as shown in Figure 4D. The grain-growth exponent (n) is estimated to be 3.4, which was attributed to the fact that the grain corner-distributed B2 precipitation effectively hindered grain growth. The microstructure of the cold-rolling (Figure 4E) and subsequent annealing of Al0.5CoCrFeNi HEA has also been investigated (Guo et al., 2018; Yang et al., 2019a). The reported recrystallization temperature (∼0.81 Tm; Tm referring to the melting point) in the alloy was attributed to coarse as-cast grains, severe lattice distortion effect, and sluggish diffusion effect. The dispersed bcc particles at grain boundaries could effectively slow the grain growth when annealing at 1,200°C with a holding time extended to 16 h.
After cold rolling, a large number of crystal defects such as dislocations are produced in the material, which store high deformation energy. Through subsequent annealing, the stored energy could be released and the deformed structure recrystallizes to refine the grains. The ideal structures could be obtained via reasonable heat treatment, i.e., ultrafine-grain structure, or heterogeneous structure. Meanwhile, high-entropy alloys exhibited a rather high recrystallization temperature and strong resistance to grain growth during annealing, mainly due to the precipitates in the vicinity of the grain boundaries effectively suppressing the grain coarsening of the fcc matrix.
Effect of Hot Deformation and Annealing on the Microstructure
The investigation of hot deformation and dynamic recrystallization mechanisms in AlxCoCrFeNi alloys is vital, considering the current interest in employing HEAs for critical high temperature applications. Haghdadi et al. (2020b) investigated the hot-worked microstructure of an Al0.3CoCrFeNi alloy. Most deformation bands were poorly developed even at high strains due to the intrinsic resistance of the lattice to dislocation movement in HEA. The alloy softened through dynamic recrystallization, mainly occurring at the initial grain boundaries through the grain boundary migration caused by strain then followed by multiple twinning chains and the formation of micro-shear bands. Hot deformation at 1,030°C under the strain rate of 0.1 s−1 was mainly conducted through the matrix phase in Al0.6CoCrFeNi and Al0.9CoCrFeNi alloys (Haghdadi et al., 2020a). Discontinuous dynamic recrystallization (DDRX) occurred at the interphase boundary mantle regions in the fcc matrix of Al0.6CoCrFeNi alloy, along with local subgrain coalescence. With further deformation, the DDRX regions expanded and covered most of the microstructure at a strain of 1.5. While in the Al0.9CoCrFeNi alloy, the bcc matrix mainly underwent continuous dynamic recrystallization. No evidence of DDRX in the BCC phase of Al0.9CoCrFeNi was observed even at the highest strain level of 1.5.
Rao et al. (2017) investigated the formation of the second phase in the forged AlxCoCrFeNi (x = 0.3, 0.5, 0.7) alloys via an in-situ TEM heating study. The forged alloys mainly consisted of fcc and B2 phases (Ni, Al)-rich L12 nanoprecipitates were observed in the fcc matrix of forged Al0.5CoCrFeNi, while the Cr-rich bcc phase existed within the B2 phase. Many twins also formed within the fcc phase in all the as-forged alloys due to the low stacking fault energy (Kumar et al., 2015; Choudhuri et al., 2019), whereas high local deformation was present in the B2 region. Two types of precipitates were observed using an in-situ TEM study, a Cr-rich σ phase, and an Al-rich θ phase (an Al45Cr7 type). They also described the σ phase precipitation in detail using a thermodynamic calculation. One observation was that the σ phase could nucleate at the bcc/B2 interface, where the Cr-rich bcc phase forming in the B2 region would then decompose. The other observation was that the σ phase directly from the fcc matrix. The homogenization effect of 1,250°C heat treatment on the forged Al0.7CoCrFeNi HEA was investigated by Shi et al. (2018). A net-like A2 (disordered) phase and nano-sized spherical A2 particles were distributed in the B2 matrix in the as-forged Al0.7CoCrFeNi alloy. After being heat-treated at 1,250°C for 1,000 h, the as-equilibrated Al0.7CoCrFeN showed a morphological transformation of the A2 phase, changing from being net-like nano-particles to cuboidal participates that were randomly distributed in the B2 matrix, as shown in Figure 4F.
Research on the hot deformation of AlxCoCrFeNi high-entropy alloys is still rare. The softening mechanism within the fcc and/or bcc phases could be influenced by the varying of Al concentration. Meanwhile, the heat treatment after hot deformation at homogenization temperature was certified to have a profound influence on simplifying the microstructure and reducing the elemental segregation. Research exploring the hot deformation behavior of high entropy alloy is at a preliminary stage and further studies on the microstructure evolution and property improvement of the alloy after deformation are needed.
Precipitation at Intermediate Temperatures
Recent studies indicate that AlxCoCrFeNi HEAs display a significant age-hardening phenomenon. Precipitation at intermediate temperatures of the famous fcc-based Al0.3CoCrFeNi alloy has been reported by many researchers. An aging treatment that was used to fully-recrystallize Al0.3CoCrFeNi HEA at 550°C for 150 h and 700°C for 50 h, resulted in the formation of ordered L12 Ni3(Ti,Al)-type precipitates dispersed in the interior of the grains and B2 precipitates forming along the grain boundaries, respectively (Gwalani et al., 2017). The lath-like B2 precipitates exhibited an orientation relationship with the fcc matrix. The stable nano-scale B2 precipitates were also found along the twin boundary in close proximity to the fcc matrix (Wang et al., 2019b). A combination of both nano-scaled ordered L12 precipitates and grain boundary B2 precipitates were obtained after being aged at 620°C for 50 h (Gwalani et al., 2017).
Concurrent recrystallization and precipitation occurred after being directly aged at 550°C for 24 h and 620°C for 50 h of 90% cold-rolled Al0.3CoCrFeNi alloy and microstructures consisting of tri-phase (fcc + B2 + σ) were obtained. A dual-phase (fcc + B2) structure was produced after being aged at 900°C for 0.5 h, and only the fcc phase was detected after being aged at 1,100°C (Gwalani et al., 2020). The grain size had a significant impact on the annealing-induced phase transformation in Al0.3CrFeCoNi HEA. In the coarse-grained alloy, the fcc phase transformed to the ordered L12 phase and finally to the B2 phase with increasing temperature, while the No L12 phase formed during the annealing process of the nanocrystalline alloy (Tang et al., 2016). The grain boundaries in the nanocrystalline HEA could provide a channel for the rapid diffusion of elements to form the high-temperature stable B2 phase at a relatively low temperature, thereby inhibiting the formation of the L12 ordering.
The fcc phase remained disordered after being heat treated at 1,100 °C in cold-rolled Al0.7CoCrFeNi HEA, while the B2 to B2+bcc transformation occurred in the B2 lamellae. Subsequent low temperature annealing treatment at 580 °C for 24 h introduced nano-scaled order L12 precipitates in the fcc lamellae. B2/bcc phases were also found in the fcc + L12 region (Gwalani et al., 2019). The formation of similar conjoint B2/bcc phase during the process of annealing was also reported in Al0.5CoCrFeNi alloy, as shown in Figure 5 (Yang et al., 2020). The compositional differences are visible within the Al-Ni rich B2 regions (Figure 5A), suggesting the presence of Cr rich nano-precipitates, resulting from the coherent interfaces between the two phases and driven by the concentration profiles (Rao et al., 2017).
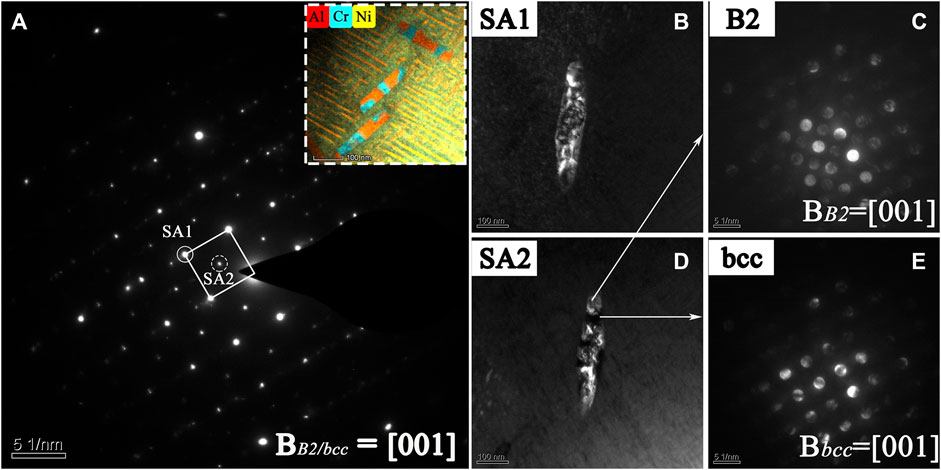
FIGURE 5. (A) the SADP image from the [001] bcc zone axis of the B2/bcc region with the image of HAADF-EDS (B,D) dark field images from the [001]B2/bcc zone axis, and (C,E) the corresponding electron diffraction patterns of the CRSA-140 Al0.5CoCrFeNi alloy (Yang et al., 2020). (Reprinted from Journal of Materials Science & Technology, Vol 72, Yang et al., Nanophase precipitation and strengthening in a dual-phase Al0.5CoCrFeNi high-entropy alloy, Pages No.6, Copyright (2021), with permission from Elsevier).
In general, the low-Al CoCrFeNi-based high-entropy alloy shows striking phase stability during annealing at an elevated temperature after cold rolling for a long time. However, intermediate temperature annealing for a long time could lead to phase decomposition and then form a dual-phase or tri-phase structure. During the thermo-mechanical processing of duplex AlxCoCrFeNi alloys, the fcc grains show slow growth during annealing for a long time, which is ascribed to the pinning effect resulting from the precipitated bcc phase in the grain boundaries. Besides, ordered phases are amenable to precipitation in fully recrystallized AlxCoCrFeNi alloys after a prolonged annealing time at an intermediated temperature. Prior deformation and subsequent annealing could substantially alter the morphology and distribution of precipitates. The dislocations introduced by pre-deformation could also act as heterogeneous nucleation sites for the secondary phase.
Mechanical Properties and Deformation Behavior
The tensile yield strength of the fcc-based Al0.25CoFeCrNi and Al0.3CoFeCrNi HEAs can be easily tuned via different thermal-mechanical processes, e.g., cold rolling and subsequent annealing (CRSA), as shown in Figure 6 (Gwalani et al., 2017; Hou et al., 2017a; Gwalani et al., 2020; He et al., 2020). Hou et al. (2017a) carried out cold rolling processing on Al0.25CoFeCrNi, resulting in a substantial strengthening of the alloy, with yield strength approaching 1,280 MPa (Figure 6A); however, this was at the expense of low ductility (ε ∼2.3%). The annealing of the deformed alloy triggered recrystallization of the alloy, introducing an effective Hall-Petch strengthening (He et al., 2020). A further increase in YS could result from the precipitation of L12, B2, and/or σ nanoparticles. A high Hall-Petch strengthening, caused by direct annealing after deformation, led to a high yield strength (∼1,060 MPa) with acceptable ductility (∼19%) (Figure 6A). The increase in YS of the fully crystallized Al0.3CoFeCrNi alloy after the precipitation of the ordered phases is shown in Figure 6B, comparing the CR-1150, CRSA-550, CRSA-620, and CRSA-700 conditions. The combination of both the L12 and B2 type precipitates within the fcc matrix leading to optimal enhancement, with strengthening contributions calculated as ∼126 MPa for the L12 precipitates, and ∼56 MPa for the B2 precipitates, respectively (Gwalani et al., 2017). The multiple strengthening effects of grain boundary strengthening, composite reinforcement effect caused by ultrafine B2 and σ grains, and precipitation strengthening by Al–Ni rich nanoclusters give the CR-550 alloy high strength (∼1,862 MPa) (Gwalani et al., 2020).

FIGURE 6. Comparison of yield strength of (A) Al0.25CoCrFeNi, and (B) Al0.3CoCrFeNi alloys under different thermal-mechanical processing conditions (Hou et al., 2017a; Gwalani et al., 2017; Gwalani et al., 2020; He et al., 2020).
Grain Boundary Strengthening
With the grain refinement in Al0.1CoCrFeNi alloy twinning in recrystallized alloys could be severely inhibited, resulting in a lower value of strain hardening rate compared to as-cast alloy (Wu et al., 2019). The average grain size at a different scale (4.7, 7.5, 15.2, 32.5, and 59.5 μm) also affected the deformation behavior of the Al0.1CoCrFeNi alloy. The alloy with fine grains revealed a good balance of strength and ductility compared to those with coarse grain size. A mixed deformation mode of dislocation slip and twinning occurred in the alloys, certified by the high density of dislocation entanglements in association with the generation of deformation twin bundles (Figures 7A–F–F). However, more active twinning behavior was observed in coarse grain alloys with wider twin thickness and smaller twin spacing compared to the fine grain alloys during tensile deformation (Figures 7G–I–I), which promoted the hardening of the alloy and postponed the necking and thus enhanced the ductility (Yang et al., 2019c).
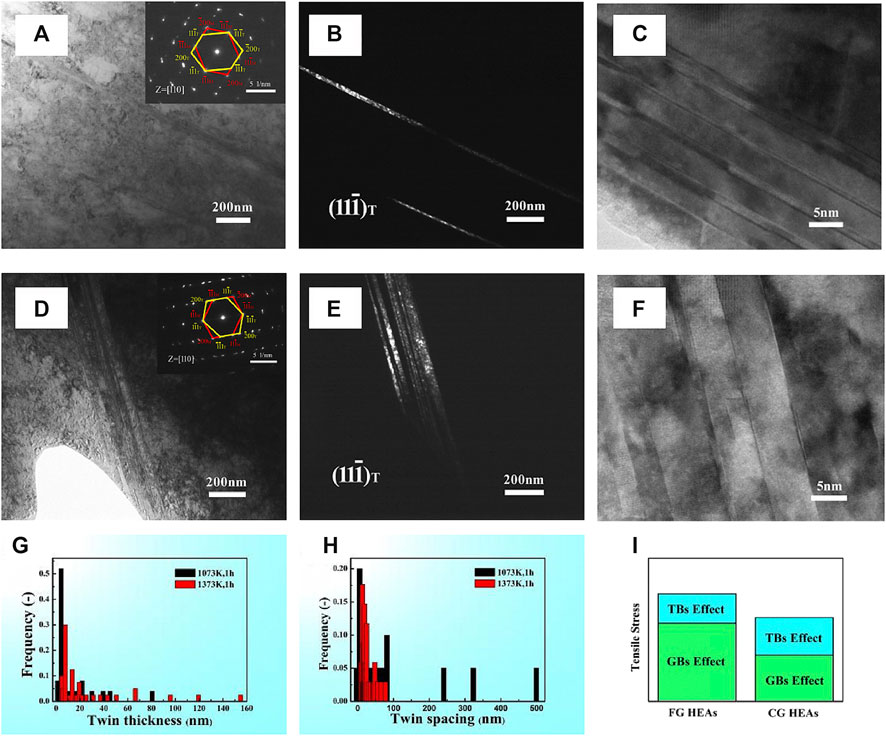
FIGURE 7. (A) Bright-field (BF) image with corresponding selected-area diffraction pattern (SADP), (B) dark-field (DF) image, and (C) high-resolution TEM (HRTEM) image of FG (∼4.7 μm) HEA, (D) BF image with corresponding SADP, (E) DF image, and (F) HRTEM image of CG (∼59.5 μm) HEA; statistics of twin thickness (G), and twin spacing (H), (I) schematic illustrations of the contribution of twin boundaries (TBs) and grain boundaries (GBs) to the tensile stress of FG and CG HEAs (Yang et al., 2019c). (Reprinted from Journal of Alloys and Compounds, Vol 795, Yang et al., Revealing the Hall-Petch relationship of Al0.1CoCrFeNi high-entropy alloy and its deformation mechanisms, Pages No.272, Copyright (2019), with permission from Elsevier).
Liu et al. (2019a) fabricated an ultra fine grained triplex Al0.3CoCrFeNi high-entropy alloy through cold rolling and annealing at 700°C for 36 h. The alloy exhibited an extraordinary yield strength of 900 MPa and a total plastic strain of ∼25%, as shown in Figure 8A. Grain boundary strengthening was calculated to be ∼780 MPa, and the difference between the computed and experimental value of yield strength could be attributed to the fine B2 and σ precipitates that formed at the grain interior and boundaries during annealing treatment. The formation of extensive deformation nano twins during plastic deformation gave rise to the enhanced dislocation storage ability of the fcc phase and thus led to large ductility (Figure 8B). Even though the Hall–Petch strengthening contribution of Al0.3CoCrFeNi HEA increased from ∼160 to ∼850 MPa can be attributed to the extremely fine grains, the extent of Hall-Petch strengthening could nevertheless be reduced after the precipitation of the B2 and σ phases (Gwalani et al., 2020). These results indicate that subtle control of the grain size in high-entropy alloys is a strategy of strengthening and toughening. However, the interplay of multiple strengthening mechanisms should also be taken into consideration to obtain the best performance.
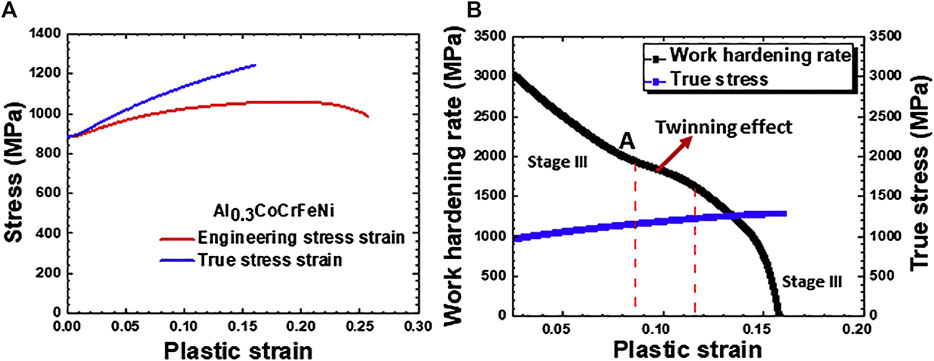
FIGURE 8. Mechanical properties of UFG Al0.3CoCrFeNi (A) Engineering stress-strain and true stress-strain curves, and (B) work hardening rate true strain curve along with true stress-strain denoting the necking criterion (Liu et al., 2019a). (Reprinted from Scripta Materialia, Vol 158, Liu et al., NFatigue behavior of ultrafine grained triplex Al0.3CoCrFeNi high entropy alloy, Pages No.118, Copyright (2019), with permission from Elsevier).
Precipitation Strengthening
The fcc phase of Al0.3CoCrFeNi alloy was transformed into an ordered B2 phase through tuning the cold rolling percentage and subsequently annealing at 800°C. The B2 grains acted as Eshelby type inclusion and could raise local stress levels during the deformation to trigger twinning (Choudhuri et al., 2018b). The yield strength of Al0.3CoCrFeNi could be enhanced from ∼260 to 490 MPa by introducing the γ′ phase and grain boundary B2 phase. γ′ precipitation led to a ∼78% enhancement in YS while B2 precipitation led to a ∼35% enhancement in YS (Gwalani et al., 2017). The boundaries of coherent nano-scaled L12 precipitate were inferred as thermal obstacles (Gangireddy et al., 2019). Introduction of the L12 precipitate effectively strengthened the dual-phase (fcc + B2) Al0.7CoCrFeNi alloy and the strengthening contribution was modeled using Orowan bowing and by-pass mechanism (Gwalani et al., 2019).
Komarasamy et al. (2019) modified the hot-rolled Al0.5CoCrFeNi alloy via high-temperature severe plastic deformation (HTSPD) and subsequent aging. The dissolution of the thermodynamically stable B2 phase during HTSPD then resulted in the precipitation of fine L12 and B2 phases as well as a thermodynamically unfavorable Al3Ni phase, showing a combination of high ultimate tensile strength (1,400 MPa) and good elongation. Both the HTSPD and aged condition alloys with hierarchical microstructural features exhibited increasing strength and sustained work hardening, which were attributed to the precipitation of the thin B2 phase and increased dislocation storage caused by the Al3Ni phase, respectively. It has been reported that the homogeneous distribution of the ordered L12 phase occurred at 650°C in fully-recrystallized Al0.5CoCrFeNi alloy and that this can strengthen the fcc matrix by inducing substantial low-misfit nanoscale interfaces that resist dislocation motion effectively (Yang et al., 2019b). Heterogeneous plastic strain could accumulate near the fcc–bcc/B2 phase boundaries in Al-rich fcc-bcc AlxCoCrFeNi HEAs. B2/bcc precipitates could prevent the formation of distinct deformation bands and their propagation in the fcc region of heat-treated Al0.5CoCrFeNi alloy during room temperature deformation. The work hardening rate of the Al0.5CoCrFeNi alloy proved to be high, and a large number of deformation twins were produced in the fcc matrix (Bonisch et al., 2018). A large number of deformation twins generated by plastic deformation in hot-forged Al0.7CoCrFeNi alloys could also be used for strengthening and toughing the alloy. However, when the volume fraction of the second phase exceeds a specific value, this could have a very obvious effect on the mechanical properties of the alloy, making it high strength but low plasticity.
In summary, it is interesting that the alloying of Al to fcc-based CoCrFeNi alloy could induce not only the transition from fcc to bcc but also fascinating phase transitions, including the ordering transition, bcc–hcp transition, and the formation of B2 and σ phases. Such phase transitions usually contribute to the substantial strengthening of the alloys. Synergy could be achieved in a variety of strengthening–toughening mechanisms through the appropriate thermal–mechanical process, which is expected to obtain the desired mechanical properties.
Deformation Behavior
Most of the fcc-based HEAs are reported to have rather low stacking fault energies (6–30 mJ/m−2), and can form extensive twins during deformation at cryogenic temperature but minimal twinning at room temperature (Otto et al., 2013; Zhang et al., 2014; Choudhuri et al., 2019; Chen et al., 2020). For example, the Al0.1CoCrFeNi alloy formed only a small fraction of nanoscale (∼2 nm thick) deformation twins under quasistatic tension at room temperature, which provided an additional plastic deformation mode and improved the work hardening of the Al0.1CoCrFeNi alloy (Choudhuri et al., 2018a). Deformation twins, as another fundamental plastic deformation mode, are relevant to internal and external factors such as crystal structure, strain rate, and temperature (Wang et al., 2018d). Severe plastic deformation could introduce higher internal stresses, which is expected to promote the emergence of deformation twins (Kumar et al., 2015; Choudhuri et al., 2018b; Chen et al., 2019). Choudhuri et al. (2019) investigated the deformation mechanisms of Al0.3CoCrFeNi HEAs. TEM observation of the deformed behavior of the coarse-grained single-phase alloy indicated that the formation of the {111} slip band and generation of the nano-twin were the predominant deformation mechanisms. The presence of the hard B2 and σ intermetallics directly promoted the strain hardening of the fcc matrix phase. Within the fcc-B2 clusters, thicker deformation twins and dislocation plasticity were the main deformation mechanisms, while within the fcc-B2-σ clusters, dislocation plasticity, nano-twinning, plus limited crack formation in and around the σ grains were the primary deformation mechanisms.
Zhang et al. (2016) explored the hot deformation behavior of Al0.5CrFeCoNi HEA in both the as-cast and homogenized conditions, where the flow stress heightened with increasing strain rate and lower temperature. Moreover, under the same deformation conditions, the flow stress in the homogenized state was higher than that in the as-cast state. The average activation energy was estimated to be ∼300 KJ/mol. Serrations in flow behavior have also been reported for a few HEAs. Zhang et al. (2018) reported that an abnormal tendency happened in the serration curves during hot compression, indicating a conversion of the deformation mechanism at elevated temperatures. A large number of parallel deformation twins formed in the Al0.3CoCrFeNi HEA after being compressed at 600°C, accounting for the continuous work-hardening phenomenon that occurred below 700°C (Figures 9A,C,D). As the temperature rose to 800°C, the escalation of dislocation mobility and SFE led to the transformation of the deformation mechanism from {111} <11–2> twinning to slip (Figure 9B). The transformation of the serration type was also reported in Al0.5CrFeCoNi HEA (Niu et al., 2017b). With increasing temperature (200–500°C) and decreasing strain rate (10−3–10–4 s−1), the serration type changed from type A to type A+ B, and finally to type B+ C. The allow became brittle, which was attributed to dynamic strain aging since solute atoms could block the dislocation movement by interacting with dislocations.
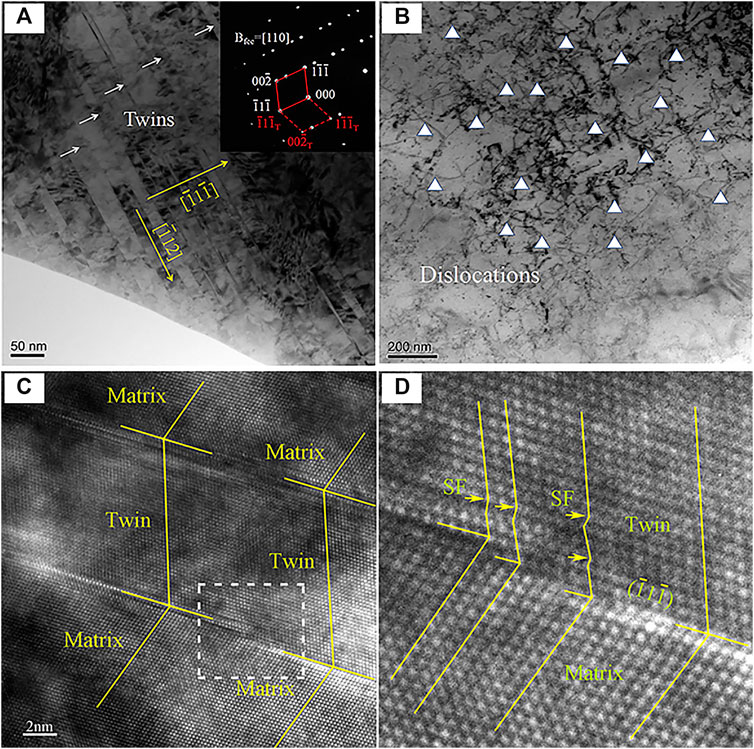
FIGURE 9. Microstructure of Al0.3CoCrFeNi HEA compressive samples (A) at 600°C, showing parallel nano-twins, (B) at 800°C, showing high density dislocations (Zhang et al., 2018). HETEM image of sample compressed at 600°C, (C) a typical deformation twin, and (D) the enlarged image of the white dashed square (Zhang et al., 2018).
Concluding Remarks
This article reviewed the effect of thermal-mechanical processes on AlxCoCrFeNi high-entropy alloys, emphasizing the correlation of the microstructure and how this corresponds to mechanical performance. There is tremendous scope to further explore HEAs with hierarchical microstructure to achieve enhanced mechanical properties. By controlling the hierarchical grain structure or precipitation of various intermetallic compounds, the complex interplay of various strengthening mechanisms within the HEA results in a large range of strength-ductility combinations. However, such cumulative strengthening effects should be further systematically quantified. In addition, the temperature has a very significant impact on the stacking fault energy. Therefore, an alloy with relatively low stacking fault energy regulates the stacking fault energy, triggering the TWIP and trip effects of alloys, which is also expected to play a guiding role in further optimization of the strength and toughness of high-entropy alloy.
Author Contributions
HY made a first draft, with substantial input, writing efforts, and discussions from JL, WW, HK, and JW.
Funding
This work was supported by the Natural Science Foundation of China (51774240 and 51571161), a fund from the State Key Laboratory of Solidification Processing in NWPU (2019-TS-04), the seed Foundation of Innovation and Creation for Graduate Students in Northwestern Polytechnical University (CX2020007), the Innovation Capability Support Program of Shaanxi (2020KJXX-073), the Natural Science Foundation of Chongqing (cstc2020jcyj-msxmX0976), and received Fundamental Research Funds for the Central Universities.
Conflict of Interest
The authors declare that the research was conducted in the absence of any commercial or financial relationships that could be construed as a potential conflict of interest.
References
Annasamy, M., Haghdadi, N., Taylor, A., Hodgson, P., and Fabijanic, D. (2019). Dynamic recrystallization behaviour of AlxCoCrFeNi high entropy alloys during high-temperature plane strain compression. Mater. Sci. Eng. A. 745, 90–106. doi:10.1016/j.msea.2018.12.102
Bonisch, M., Wu, Y., and Sehitoglu, H. (2018). Twinning-induced strain hardening in dual-phase FeCoCrNiAl0.5 at room and cryogenic temperature. Sci. Rep. 8, 10663. doi:10.1038/s41598-018-28784-1
Butler, T. M., and Weaver, M. L. (2017). Investigation of the phase stabilities in AlNiCoCrFe high entropy alloys. J. Alloys Compd. 691, 119–129. doi:10.1016/j.jallcom.2016.08.121
Cantor, B., Chang, I. T. H., Knight, P., and Vincent, A. J. B. (2004). Microstructural development in equiatomic multicomponent alloys. Mater. Sci. Eng. A. 375–377, 213–218
Cao, T., Shang, J., Zhao, J., Cheng, C., Wang, R., and Wang, H. (2016). The influence of Al elements on the structure and the creep behavior of AlxCoCrFeNi high entropy alloys. Mater. Lett. 164, 344–347. doi:10.1016/j.matlet.2015.11.016
Chen, G., Li, L. T., Qiao, J. W., Jiao, Z. M., Ma, S. G., Ng, F. L., et al. (2019). Gradient hierarchical grain structures of Al0.1CoCrFeNi high-entropy alloys through dynamic torsion. Mater. Lett. 238, 163–166. doi:10.1016/j.matlet.2018.11.176
Chen, S., Aitken, Z. H., Wu, Z., Yu, Z., Banerjee, R., and Zhang, Y. W. (2020). Hall-Petch and inverse Hall-Petch relations in high-entropy CoNiFeAlxCu1-x alloys. Mater. Sci. Eng. A. 773. doi:10.1016/j.msea.2019.138873
Chen, T. K., Shun, T. T., Yeh, J. W., and Wong, M. S. (2004). Nanostructured nitride films of multi-element high-entropy alloys by reactive DC sputtering. Surf. Coating. Technol. 188-189, 193–200. doi:10.1016/j.surfcoat.2004.08.023
Chou, H. P., Chang, Y. S., Chen, S. K., and Yeh, J. W. (2009). Microstructure, thermophysical and electrical properties in AlxCoCrFeNi (0 ≤ x ≤ 2) high-entropy alloys. Mater. Sci. Eng. B. 163, 184–189. doi:10.1016/j.mseb.2009.05.024
Choudhuri, D., Gwalani, B., Gorsse, S., Komarasamy, M., Mantri, S. A., Srinivasan, S. G., et al. (2019). Enhancing strength and strain hardenability via deformation twinning in fcc-based high entropy alloys reinforced with intermetallic compounds. Acta Mater. 165, 420–430. doi:10.1016/j.actamat.2018.12.010
Choudhuri, D., Komarasamy, M., Ageh, V., and Mishra, R. S. (2018a). Investigation of plastic deformation modes in Al0.1CoCrFeNi high entropy alloy. Mater. Chem. Phys. 217, 308–314. doi:10.1016/j.matchemphys.2018.05.050
Choudhuri, D., Shukla, S., Green, W. B., Gwalani, B., Ageh, V., Banerjee, R., et al. (2018b). Crystallographically degenerate B2 precipitation in a plastically deformed fcc-based complex concentrated alloy. Mater. Res. Lett. 6, 171–177. doi:10.1080/21663831.2018.1426649
Cieslak, J., Tobola, J., Berent, K., and Marciszko, M. (2018). Phase composition of AlxFeNiCrCo high entropy alloys prepared by sintering and arc-melting methods. J. Alloys Compd. 740, 264–272. doi:10.1016/j.jallcom.2017.12.333
Du, X. H., Li, W. P., Chang, H. T., Yang, T., Duan, G. S., Wu, B. L., et al. (2020). Dual heterogeneous structures lead to ultrahigh strength and uniform ductility in a Co-Cr-Ni medium-entropy alloy. Nat. Commun. 11, 2390. doi:10.1038/s41467-020-16085-z
Gangireddy, S., Gwalani, B., and Mishra, R. S. (2018a). Grain size dependence of strain rate sensitivity in a single phase FCC high entropy alloy Al0. 3CoCrFeNi. Mater. Sci. Eng. A. 736, 344–348. doi:10.1016/j.msea.2018.09.009
Gangireddy, S., Gwalani, B., Soni, V., Banerjee, R., and Mishra, R. S. (2019). Contrasting mechanical behavior in precipitation hardenable AlxCoCrFeNi high entropy alloy microstructures: single phase FCC vs. dual phase FCC–BCC. Mater. Sci. Eng. A. 739, 158–166. doi:10.1016/j.msea.2018.10.021
Gangireddy, S., Kaimiao, L., Gwalani, B., and Mishra, R. (2018b). Microstructural dependence of strain rate sensitivity in thermomechanically processed Al0.1CoCrFeNi high entropy alloy. Mater. Sci. Eng. A. 727, 148–159. doi:10.1016/j.msea.2018.04.108
Gao, X., Lu, Y., Liu, J., Wang, J., Wang, T., and Zhao, Y. (2019). Extraordinary ductility and strain hardening of Cr26Mn20Fe20Co20Ni14 TWIP high-entropy alloy by cooperative planar slipping and twinning. Materialia. 8, 21–78. doi:10.1016/j.mtla.2019.100485
Garlapati, M. M., Vaidya, M., Karati, A., Mishra, S., Bhattacharya, R., and Murty, B. S. (2020). Influence of Al content on thermal stability of nanocrystalline AlxCoCrFeNi high entropy alloys at low and intermediate temperatures. Adv. Powder Technol. 7, 33–68. doi:10.1016/j.apt.2020.02.032
George, E. P., Curtin, W. A., and Tasan, C. C. (2020). High entropy alloys: a focused review of mechanical properties and deformation mechanisms. Acta Mater. 188, 435–474. doi:10.1016/j.actamat.2019.12.015
Gorsse, S., Miracle, D. B., and Senkov, O. N. (2017). Mapping the world of complex concentrated alloys. Acta Mater. 135, 177–187. doi:10.1016/j.actamat.2017.06.027
Guillot, I., Tyrman, M., Perrière, L., Couzinié, J. P. P., Lilensten, L., Prima, F., et al. (2020). Ultrafine-grained two-phase high-entropy alloy microstructures obtained via recrystallization: mechanical properties. Front. Mater. 8, 221–288. doi:10.3389/fmats.2020.00125
Guo, S., Ng, C., and Liu, C. T. (2013). Anomalous solidification microstructures in Co-free AlxCrCuFeNi2 high-entropy alloys. J. Alloys Compd. 557, 77–81. doi:10.1016/j.jallcom.2013.01.007
Guo, T., Li, J., Wang, J., Wang, W. Y., Liu, Y., Luo, X., et al. (2018). Microstructure and properties of bulk Al0.5CoCrFeNi high-entropy alloy by cold rolling and subsequent annealing. Mater. Sci. Eng. A. 729, 141–148. doi:10.1016/j.msea.2018.05.054
Guo, T., Li, J., Wang, J., Wang, Y., Kou, H., and Niu, S. (2017). Liquid-phase separation in undercooled CoCrCuFeNi high entropy alloy. Intermetallics. 86, 110–115. doi:10.1016/j.intermet.2017.03.021
Gwalani, B., Choudhuri, D., Liu, K., Lloyd, J. T., Mishra, R. S., and Banerjee, R. (2020). Interplay between single phase solid solution strengthening and multi-phase strengthening in the same high entropy alloy. Mater. Sci. Eng. A. 771, 437–515. doi:10.1016/j.msea.2019.138620
Gwalani, B., Gangireddy, S., Zheng, Y., Soni, V., Mishra, R. S., and Banerjee, R. (2019). Influence of ordered L12 precipitation on strain-rate dependent mechanical behavior in a eutectic high entropy alloy. Sci. Rep. 9, 6371. doi:10.1038/s41598-019-42870-y
Gwalani, B., Gorsse, S., Choudhuri, D., Styles, M., Zheng, Y., Mishra, R. S., et al. (2018). Modifying transformation pathways in high entropy alloys or complex concentrated alloys via thermo-mechanical processing. Acta Mater. 153, 169–185. doi:10.1016/j.actamat.2018.05.009
Gwalani, B., Soni, V., Lee, M., Mantri, S. A., Ren, Y., and Banerjee, R. (2017). Optimizing the coupled effects of Hall–Petch and precipitation strengthening in a Al0.3CoCrFeNi high entropy alloy. Mater. Des. 121, 254–260. doi:10.1016/j.matdes.2017.02.072
Haghdadi, N., Primig, S., Annasamy, M., Cizek, P., Hodgson, P. D., and Fabijanic, D. M. (2020a). Dynamic recrystallization in AlxCoCrFeNi duplex high entropy alloys. J. Alloys Compd. 830, 115–233. doi:10.1016/j.jallcom.2020.154720
Haghdadi, N., Primig, S., Annasamy, M., Cizek, P., Hodgson, P. D., and Fabijanic, D. M. (2020b). On the hot-worked microstructure of a face-centered cubic Al0.3CoCrFeNi high entropy alloy. Scripta Mater. 178, 144–149. doi:10.1016/j.scriptamat.2019.11.022
He, F., Wang, Z., Wu, Q., Li, J., Wang, J., and Liu, C. T. (2017). Phase separation of metastable CoCrFeNi high entropy alloy at intermediate temperatures. Scripta Mater. 126, 15–19. doi:10.1016/j.scriptamat.2016.08.008
He, J. Y., Wang, H., Huang, H. L., Xu, X. D., Chen, M. W., Wu, Y., et al. (2016a). A precipitation-hardened high-entropy alloy with outstanding tensile properties. Acta Mater. 102, 187–196. doi:10.1016/j.actamat.2015.08.076
He, J. Y., Wang, H., Wu, Y., Liu, X. J., Mao, H. H., Nieh, T. G., et al. (2016b). Precipitation behavior and its effects on tensile properties of FeCoNiCr high-entropy alloys. Intermetallics. 79, 41–52. doi:10.1016/j.intermet.2016.09.005
He, Y., Yang, H., Zhao, C., Zhang, Y., Pan, X., Li, J., et al. (2020). Enhancing mechanical properties of Al0.25CoCrFeNi high-entropy alloy via cold rolling and subsequent annealing. J. Alloys Compd. 830, 23–45. doi:10.1016/j.jallcom.2020.154645
Hou, J., Shi, X., Qiao, J., Zhang, Y., Liaw, P. K., and Wu, Y. (2019). Ultrafine-grained dual phase Al0.45CoCrFeNi high-entropy alloys. Mater. Des. 180, 107910. doi:10.1016/j.matdes.2019.107910
Hou, J., Zhang, M., Ma, S., Liaw, P. K., Zhang, Y., and Qiao, J. (2017a). Strengthening in Al0.25CoCrFeNi high-entropy alloys by cold rolling. Mater. Sci. Eng. A. 707, 593–601. doi:10.1016/j.msea.2017.09.089
Hou, J., Zhang, M., Yang, H., and Qiao, J. (2017b). Deformation behavior of Al0.25CoCrFeNi high-entropy alloy after recrystallization. Metals. 7, 12–23. doi:10.3390/met7040111
Jasiewicz, K., Cieslak, J., Kaprzyk, S., and Tobola, J. (2015). Relative crystal stability of AlxFeNiCrCo high entropy alloys from XRD analysis and formation energy calculation. J. Alloys Compd. 648, 307–312. doi:10.1016/j.jallcom.2015.06.260
Juan, C. C., Hsu, C. Y., Tsai, C. W., Wang, W. R., Sheu, T. S., Yeh, J. W., et al. (2013). On microstructure and mechanical performance of AlCoCrFeMo0.5Nix high-entropy alloys. Intermetallics. 32, 401–407. doi:10.1016/j.intermet.2012.09.008
Kao, Y. F., Chen, S. K., Chen, T. J., Chu, P. C., Yeh, J. W., and Lin, S. J. (2011). Electrical, magnetic, and Hall properties of AlxCoCrFeNi high-entropy alloys. J. Alloys Compd. 509, 1607–1614. doi:10.1016/j.jallcom.2010.10.210
Kao, Y. F., Chen, T. J., Chen, S. K., and Yeh, J. W. (2009). Microstructure and mechanical property of as-cast, -homogenized, and -deformed AlxCoCrFeNi (0≤x≤2) high-entropy alloys. J. Alloys Compd. 488, 57–64. doi:10.1016/j.jallcom.2009.08.090
Kireeva, I. V., Chumlyakov, Y. I., Pobedennaya, Z. V., and Vyrodova, A. V. (2020). Effect of γ′-phase particles on the orientation and temperature dependence of the mechanical behaviour of Al0.3CoCrFeNi high-entropy alloy single crystals. Mater. Sci. Eng. A. 772. doi:10.1016/j.msea.2019.138772
Komarasamy, M., Wang, T., Liu, K., Reza-Nieto, L., and Mishra, R. S. (2019). Hierarchical multi-phase microstructural architecture for exceptional strength-ductility combination in a complex concentrated alloy via high-temperature severe plastic deformation. Scripta Mater. 162, 38–43. doi:10.1016/j.scriptamat.2018.10.033
Kumar, N., Ying, Q., Nie, X., Mishra, R. S., Tang, Z., Liaw, P. K., et al. (2015). High strain-rate compressive deformation behavior of the Al0.1CrFeCoNi high entropy alloy. Mater. Des. 86, 598–602. doi:10.1016/j.matdes.2015.07.161
Li, C., Li, J. C., Zhao, M., and Jiang, Q. (2009). Effect of alloying elements on microstructure and properties of multiprincipal elements high-entropy alloys. J. Alloys Compd. 475, 752–757. doi:10.1016/j.jallcom.2008.07.124
Li, D., and Zhang, Y. (2016). The ultrahigh charpy impact toughness of forged AlxCoCrFeNi high entropy alloys at room and cryogenic temperatures. Intermetallics. 70, 24–28. doi:10.1016/j.intermet.2015.11.002
Li, J., Jia, W., Wang, J., Kou, H., Zhang, D., and Beaugnon, E. (2016). Enhanced mechanical properties of a CoCrFeNi high entropy alloy by supercooling method. Mater. Des. 95, 183–187. doi:10.1016/j.matdes.2016.01.112
Li, Q., Zhang, T. W., Qiao, J. W., Ma, S. G., Zhao, D., Lu, P., et al. (2019). Mechanical properties and deformatiikon behavior of dual-phase Al0.6CoCrFeNi high-entropy alloys with heterogeneous structure at room and cryogenic temperatures. J. Alloys Compd. 95, 152663. doi:10.1016/j.jallcom.2019.152663
Liu, G., Liu, L., Liu, X., Wang, Z., Han, Z., Zhang, G., et al. (2018). Microstructure and mechanical properties of Al0.7CoCrFeNi high-entropy-alloy prepared by directional solidification. Intermetallics. 93, 93–100. doi:10.1016/j.intermet.2017.11.019
Liu, K., Komarasamy, M., Gwalani, B., Shukla, S., and Mishra, R. S. (2019a). Fatigue behavior of ultrafine grained triplex Al0.3CoCrFeNi high entropy alloy. Scripta Mater. 158, 116–120. doi:10.1016/j.scriptamat.2018.08.048
Liu, W. H., Lu, Z. P., He, J. Y., Luan, J. H., Wang, Z. J., Liu, B., et al. (2016). Ductile CoCrFeNiMox high entropy alloys strengthened by hard intermetallic phases. Acta Mater. 116, 332–342 doi:10.1016/j.actamat.2016.06.063
Liu, W. H., Wu, Y., He, J. Y., Zhang, Y., Liu, C. T., and Lu, Z. P. (2014). The phase competition and stability of high-entropy alloys. J. Occup. Med. 66, 1973–1983. doi:10.1016/j.actamat.2016.06.063
Liu, Y. Y., Chen, Z., Shi, J. C., Wang, Z. Y., and Zhang, J. Y. (2019b). The effect of Al content on microstructures and comprehensive properties in AlxCoCrCuFeNi high entropy alloys. Vacuum. 161, 143–149. doi:10.1016/j.vacuum.2018.12.009
Lu, K. (2016). Stabilizing nanostructures in metals using grain and twin boundary architectures. Nature Reviews Materials. 1, 16019. doi:10.1038/natrevmats.2016.19
Lu, Y., Dong, Y., Guo, S., Jiang, L., Kang, H., Wang, T., et al. (2014). A promising new class of high-temperature alloys: eutectic high-entropy alloys. Sci. Rep. 4, 33–79. doi:10.1038/srep06200
Lu, Y., Gao, X., Dong, Y., Wang, T., Chen, H. L., Maob, H., et al. (2018). Preparing bulk ultrafine-microstructure high-entropy alloys via direct solidification. Nanoscale. 10, 1912–1919. doi:10.1039/C7NR07281C
Lu, Y., Gao, X., Jiang, L., Chen, Z., Wang, T., Jie, J., et al. (2017). Directly cast bulk eutectic and near-eutectic high entropy alloys with balanced strength and ductility in a wide temperature range. Acta Mater. 124, 143–150. doi:10.1016/j.actamat.2016.11.016
Ma, S. G., Liaw, P. K., Gao, M. C., Qiao, J. W., Wang, Z. H., and Zhang, Y. (2014). Damping behavior of AlxCoCrFeNi high-entropy alloys by a dynamic mechanical analyzer. J. Alloys Compd. 604, 331–339. doi:10.1016/j.jallcom.2014.03.050
Macdonald, B. E., Fu, Z., Wang, X., Li, Z., Chen, W., Zhou, Y., et al. (2019). Influence of phase decomposition on mechanical behavior of an equiatomic CoCuFeMnNi high entropy alloy. Acta Mater. 181, 25–35. doi:10.1016/j.actamat.2019.09.030
Miracle, D. B. (2015). Critical Assessment 14: high entropy alloys and their development as structural materials. Mater. Sci. Technol. 31, 1142–1147. doi:10.1179/1743284714y.0000000749
Munitz, A., Salhov, S., Hayun, S., and Frage, N. (2016). Heat treatment impacts the micro-structure and mechanical properties of AlCoCrFeNi high entropy alloy. J. Alloys Compd. 683, 221–230. doi:10.1016/j.jallcom.2016.05.034
Nartu, M. S. K. K. Y., Alam, T., Dasari, S., Mantri, S. A., Gorsse, S., Siller, H., et al. (2020). Enhanced tensile yield strength in laser additively manufactured Al0.3CoCrFeNi high entropy alloy. Materialia. 9, 329–447. doi:10.1016/j.mtla.2019.100522
Niu, S., Kou, H., Guo, T., Zhang, Y., Wang, J., and Li, J. (2016). Strengthening of nanoprecipitations in an annealed Al0.5CoCrFeNi high entropy alloy. Mater. Sci. Eng. A. 671, 82–86. doi:10.1016/j.msea.2016.06.040
Niu, S., Kou, H., Zhang, Y., Wang, J., and Li, J. (2017b). The characteristics of serration in Al0.5CoCrFeNi high entropy alloy. Mater. Sci. Eng. A. 702, 96–103. doi:10.1016/j.msea.2017.05.075
Niu, S. Z., Kou, H. C., Wang, J., and Li, J. S. (2017a). Improved tensile properties of Al0.5CoCrFeNi high-entropy alloy by tailoring microstructures. Rare Metals. 12, 69–119. doi:10.1007/s12598-016-0860-y
Ogura, M., Fukushima, T., Zeller, R., and Dederichs, P. H. (2017). Structure of the high-entropy alloy AlCrFeCoNi: fcc versus bcc. J. Alloys Compd. 715, 454–459. doi:10.1016/j.jallcom.2017.04.318
Otto, F., Yang, Y., Bei, H., and George, E. P. (2013). Relative effects of enthalpy and entropy on the phase stability of equiatomic high-entropy alloys. Acta Mater. 61, 2628–2638. doi:10.1016/j.actamat.2013.01.042
Rao, J. C., Diao, H. Y., Ocelík, V., Vainchtein, D., Zhang, C., Kuo, C., et al. (2017). Secondary phases in AlxCoCrFeNi high-entropy alloys: an in-situ TEM heating study and thermodynamic appraisal. Acta Mater. 131, 206–220. doi:10.1016/j.actamat.2017.03.066
Rao, J. C., Ocelík, V., Vainchtein, D., Tang, Z., Liaw, P. K., and De Hosson, J. T. M. (2016). The fcc-bcc crystallographic orientation relationship in AlxCoCrFeNi high-entropy alloys. Mater. Lett. 176, 29–32. doi:10.1016/j.matlet.2016.04.086
Schneider, M., George, E. P., Manescau, T. J., Záležák, T., Hunfeld, J., Dlouhý, A., et al. (2020). Analysis of strengthening due to grain boundaries and annealing twin boundaries in the CrCoNi medium-entropy alloy. Int. J. Plast. 124, 155–169. doi:10.1016/j.ijplas.2019.08.009
Senkov, O. N., Miller, J. D., Miracle, D. B., and Woodward, C. (2015). Accelerated exploration of multi-principal element alloys with solid solution phases. Nat. Commun. 6, 6529. doi:10.1038/ncomms7529
Shi, Y., Collins, L., Feng, R., Zhang, C., Balke, N., Liaw, P. K., et al. (2018). Homogenization of AlxCoCrFeNi high-entropy alloys with improved corrosion resistance. Corrosion Sci. 133, 120–131. doi:10.1016/j.corsci.2018.01.030
Sriharitha, R., Murty, B. S., and Kottada, R. S. (2013). Phase formation in mechanically alloyed AlxCoCrCuFeNi (x = 0.45, 1, 2.5, 5 mol) high entropy alloys. Intermetallics. 32, 119–126. doi:10.1016/j.intermet.2012.08.015
Stepanov, N. D., Shaysultanov, D. G., Salishchev, G. A., Tikhonovsky, M. A., Oleynik, E. E., Tortika, A. S., et al. (2015). Effect of V content on microstructure and mechanical properties of the CoCrFeMnNiVx high entropy alloys. J. Alloys Compd. 628, 170–185. doi:10.1016/j.jallcom.2014.12.157
Sun, S. J., Tian, Y. Z., An, X. H., Lin, H. R., Wang, J. W., and Zhang, Z. F. (2018). Ultrahigh cryogenic strength and exceptional ductility in ultrafine-grained CoCrFeMnNi high-entropy alloy with fully recrystallized structure. Mater. Today Nano. 4, 46–53. doi:10.1016/j.mtnano.2018.12.002
Tan, Y., Li, J., Tang, Z., Wang, J., and Kou, H. (2018a). Design of high-entropy alloys with a single solid-solution phase: average properties vs. their variances. J. Alloys Compd. 742, 430–441. doi:10.1016/j.jallcom.2018.01.252
Tan, Y., Li, J., Wang, J., Kolbe, M., and Kou, H. (2018b). Microstructure characterization of CoCrFeNiMnPd eutectic high-entropy alloys. J. Alloys Compd. 731, 600–611. doi:10.1016/j.jallcom.2017.09.057
Tan, Y., Li, J., Wang, J., and Kou, H. (2019). Effect of Mn addition on the microstructures and mechanical properties of CoCrFeNiPd high entropy alloy. Entropy. 21, 153–241. doi:10.3390/e21030288
Tan, Y., Li, J., Wang, J., and Kou, H. (2017). Seaweed eutectic-dendritic solidification pattern in a CoCrFeNiMnPd eutectic high-entropy alloy. Intermetallics. 85, 74–79. doi:10.1016/j.intermet.2017.02.004
Tang, Q., Huang, Y., Cheng, H., Liao, X., Langdon, T. G., and Dai, P. (2016). The effect of grain size on the annealing-induced phase transformation in an Al0.3CoCrFeNi high entropy alloy. Mater. Des. 105, 381–385. doi:10.1016/j.matdes.2016.05.079
Tong, C. J., Chen, M. R., Yeh, J. W., Lin, S. J., Chen, S. K., Shun, T. T., et al. (2005a). Mechanical performance of the AlxCoCrCuFeNi high-entropy alloy system with multiprincipal elements. Metall. Mater. Trans. 36, 1263–1271. doi:10.1007/s11661-005-0218-9
Tong, C. J., Chen, Y. L., Yeh, J. W., Lin, S. J., Chen, S. K., Shun, T. T., et al. (2005b). Microstructure characterization of AlxCoCrCuFeNi high-entropy alloy system with multiprincipal elements. Metall. Mater. Trans. 36, 881–893. doi:10.1007/s11661-005-0283-0
Tong, Y., Chen, D., Han, B., Wang, J., Feng, R., Yang, T., et al. (2019). Outstanding tensile properties of a precipitation-strengthened FeCoNiCrTi0.2 high-entropy alloy at room and cryogenic temperatures. Acta Mater. 165, 228–240. doi:10.1016/j.actamat.2018.11.049
Troparevsky, M. C., Morris, J. R., Kent, P. R. C., Lupini, A. R., and Stocks, G. M. (2015). Criteria for predicting the formation of single-phase high-entropy alloys. Phys. Rev. X. 5, 114. doi:10.1103/PhysRevX.5.011041
Tung, C. C., Yeh, J. W., Shun, T. T., Chen, S. K., Huang, Y. S., and Chen, H. C. (2007). On the elemental effect of AlCoCrCuFeNi high-entropy alloy system. Mater. Lett. 61, 1–5. doi:10.1016/j.matlet.2006.03.140
Wang, C., Li, X., Li, Z., Wang, Q., Zheng, Y., Ma, Y., et al. (2020). The resistivity–temperature behavior of AlxCoCrFeNi high-entropy alloy films. Thin Solid Films. 700. doi:10.1016/j.tsf.2020.137895
Wang, J., Li, J., Wang, J., Bu, F., Kou, H., Li, C., et al. (2018a). Effect of solidification on microstructure and properties of FeCoNi(AlSi)0.2 high-entropy alloy under strong static magnetic field. Entropy. 20, 773–779. doi:10.3390/e20040275
Wang, J., Niu, S., Guo, T., Kou, H., and Li, J. (2017a). The FCC to BCC phase transformation kinetics in an Al0.5CoCrFeNi high entropy alloy. J. Alloys Compd. 710, 144–150. doi:10.1016/j.jallcom.2017.03.249
Wang, J., Wei, C., Yang, H., Guo, T., Xu, T., and Li, J. (2018b). Phase transformation kinetics of a FCC Al0.25CoCrFeNi high-entropy alloy during isochronal heating. Metals. 8, 283–289. doi:10.3390/met8121015
Wang, J., Yang, H., Guo, T., Wang, J., Wang, W. Y., and Li, J. (2018c). Effect of cold rolling on the phase transformation kinetics of an Al0.5CoCrFeNi high-entropy alloy. Entropy. 20, 63–95. doi:10.3390/e20120917
Wang, J., Zhang, Y., Niu, S. Z., Wang, W. Y., Kou, H. C., Li, J. S., et al. (2017b). Formation of a hexagonal closed-packed phase in Al0.5CoCrFeNi high entropy alloy. MRS Communications. 7, 879–884. doi:10.1557/mrc.2017.109
Wang, J., Zhang, Y., Xiao, H., Li, L., Kou, H., and Li, J. (2019a). A novel strategy for enhancing mechanical performance of Al0.5CoCrFeNi high-entropy alloy via high magnetic field. Mater. Lett. 240, 250–252. doi:10.1016/j.matlet.2018.12.127
Wang, L., Qiao, J. W., Ma, S. G., Jiao, Z. M., Zhang, T. W., Chen, G., et al. (2018d). Mechanical response and deformation behavior of Al0.6CoCrFeNi high-entropy alloys upon dynamic loading. Mater. Sci. Eng. A. 727, 208–213. doi:10.1016/j.msea.2018.05.001
Wang, W. R., Wang, W. L., Wang, S. C., Tsai, Y. C., Lai, C. H., and Yeh, J. W. (2012). Effects of Al addition on the microstructure and mechanical property of AlxCoCrFeNi high-entropy alloys. Intermetallics. 26, 44–51. doi:10.1016/j.intermet.2012.03.005
Wang, W. R., Wang, W. L., and Yeh, J. W. (2014). Phases, microstructure and mechanical properties of AlxCoCrFeNi high-entropy alloys at elevated temperatures. J. Alloys Compd. 589, 143–152. doi:10.1016/j.jallcom.2013.11.084
Wang, W. Y., Wang, J., Lin, D., Zou, C., Wu, Y., Hu, Y., et al. (2017c). Revealing the microstates of body-centered-cubic (BCC) equiatomic high entropy alloys. J. Phase Equilibria Diffus. 38, 404–415. doi:10.1007/s11669-017-0565-4
Wang, X., Zhou, W., Liu, P., Song, S., and Reddy, K. M. (2019b). Atomic scale structural characterization of B2 phase precipitated along FCC twin boundary in a CoCrFeNiAl0.3 high entropy alloy. Scripta Mater. 162, 161–165. doi:10.1016/j.scriptamat.2018.11.016
Wang, Y. P., Li, B. S., Ren, M. X., Yang, C., and Fu, H. Z. (2008). Microstructure and compressive properties of AlCrFeCoNi high entropy alloy. Mater. Sci. Eng. A. 491, 154–158. doi:10.1016/j.msea.2008.01.064
Wani, I. S., Bhattacharjee, T., Sheikh, S., Lu, Y. P., Chatterjee, S., Bhattacharjee, P. P., et al. (2016). Ultrafine-grained AlCoCrFeNi2.1 eutectic high-entropy alloy. Materials Research Letters. 4, 174–179. doi:10.1080/21663831.2016.1160451
Wu, J. M., Lin, S. J., Yeh, J. W., Chen, S. K., Huang, Y. S., and Chen, H. C. (2006). Adhesive wear behavior of AlxCoCrCuFeNi high-entropy alloys as a function of aluminum content. Wear. 261, 513–519. doi:10.1016/j.wear.2005.12.008
Wu, S. W., Wang, G., Wang, Q., Jia, Y. D., Yi, J., Zhai, Q. J., et al. (2019). Enhancement of strength-ductility trade-off in a high-entropy alloy through a heterogeneous structure. Acta Mater. 165, 444–458. doi:10.1016/j.actamat.2018.12.012
Xia, S., Gao, M. C., Yang, T., Liaw, P. K., and Zhang, Y. (2016). Phase stability and microstructures of high entropy alloys ion irradiated to high doses. J. Nucl. Mater. 480, 100–108. doi:10.1016/j.jnucmat.2016.08.017
Xia, S. Q., Gao, M. C., and Zhang, Y. (2018). Abnormal temperature dependence of impact toughness in AlxCoCrFeNi system high entropy alloys. Mater. Chem. Phys. 210, 213–221. doi:10.1016/j.jnucmat.2016.08.017
Yang, H., Li, J., Guo, T., Wang, W. Y., Kou, H., and Wang, J. (2019b). Fully recrystallized Al0.5CoCrFeNi high-entropy alloy strengthened by nanoscale precipitates. Met. Mater. Int. 25, 1145–1150. doi:10.1007/s12540-019-00284-5
Yang, H., Li, J., Pan, X., Wang, W. Y., Kou, H., and Wang, J. (2020). Nanophase precipitation and strengthening in a dual-phase Al0.5CoCrFeNi high-entropy alloy. J. Mater. Sci. Technol. 72, 1–7. doi:10.1016/j.jmst.2020.02.069
Yang, H. X., Li, J. S., Guo, T., Wang, W. Y., Kou, H. C., and Wang, J. (2019a). Evolution of microstructure and hardness in a dual-phase Al0.5CoCrFeNi high-entropy alloy with different grain sizes. Rare Metals. 39, 156–161. doi:10.1007/s12598-019-01320-4
Yang, J., Qiao, J. W., Ma, S. G., Wu, G. Y., Zhao, D., and Wang, Z. H. (2019c). Revealing the Hall-Petch relationship of Al0.1CoCrFeNi high-entropy alloy and its deformation mechanisms. J. Alloys Compd. 795, 269–274. doi:10.1016/j.jallcom.2019.04.333
Yeh, J. W., Chen, S. K., Lin, S. J., Gan, J. Y., Chin, T. S., Shun, T. T., et al. (2004). Nanostructured high-entropy alloys with multiple principal elements: novel alloy design concepts and outcomes. Adv. Eng. Mater. 6, 299–303. doi:10.1002/adem.200300567
Yu, H., Fang, W., Chang, R., Bai, X., Zhang, X., Liu, B., et al. (2020). Effects of annealing temperature and cooling medium on the microstructure and mechanical properties of a novel dual phase high entropy alloy. Mater. Char. 163. doi:10.1016/j.matchar.2020.110291
Yu, P. F., Cheng, H., Zhang, L. J., Zhang, H., Jing, Q., Ma, M. Z., et al. (2016). Effects of high pressure torsion on microstructures and properties of an Al0.1CoCrFeNi high-entropy alloy. Mater. Sci. Eng. A. 655, 283–291. doi:10.1016/j.msea.2015.12.085
Yuan, Y., Wu, Y., Tong, X., Zhang, H., Wang, H., Liu, X. J., et al. (2017). Rare-earth high-entropy alloys with giant magnetocaloric effect. Acta Mater. 125, 481–489. doi:10.1016/j.actamat.2016.12.021
Zhang, F., Wu, Y., Lou, H., Zeng, Z., Prakapenka, V. B., Greenberg, E., et al. (2017). Polymorphism in a high-entropy alloy. Nat. Commun. 8, 15687. doi:10.1038/ncomms15687
Zhang, L. J., Guo, K., Tang, H., Zhang, M. D., Fan, J. T., Cui, P., et al. (2019). The microstructure and mechanical properties of novel Al–Cr–Fe–Mn–Ni high-entropy alloys with trimodal distributions of coherent B2 precipitates. Mater. Sci. Eng. A. 757, 160–171. doi:10.1016/j.msea.2019.04.10
Zhang, Y., Li, J., Wang, J., Niu, S., and Kou, H. (2016). Hot deformation behavior of as-cast and homogenized Al0.5CoCrFeNi high entropy alloys. Metals. 6, 124–131. doi:10.3390/met6110277
Zhang, Y., Li, J., Wang, J., Wang, W. Y., Kou, H., and Beaugnon, E. (2018). Temperature dependent deformation mechanisms of Al0.3CoCrFeNi high-entropy alloy, starting from serrated flow behavior. J. Alloys Compd. 757, 39–43. doi:10.1016/j.jallcom.2018.04.305
Zhang, Y., Zuo, T. T., Tang, Z., Gao, M. C., Dahmen, K. A., Liaw, P. K., et al. (2014). Microstructures and properties of high-entropy alloys. Prog. Mater. Sci. 61, 1–93. doi:10.1016/j.pmatsci.2013.10.001
Zhao, C., Li, J., He, Y., Wang, J., Wang, W. Y., Kou, H., et al. (2020a). Effect of strong magnetic field on the microstructure and mechanical-magnetic properties of AlCoCrFeNi high-entropy alloy. J. Alloys Compd. 820, 425–489. doi:10.1016/j.jallcom.2019.153407
Zhao, Y. L., Yang, T., Li, Y. R., Fan, L., Han, B., Jiao, Z. B., et al. (2020b). Superior high-temperature properties and deformation-induced planar faults in a novel L12-strengthened high-entropy alloy. Acta Mater. 188, 517–527. doi:10.1016/j.actamat.2020.02.028
Zhou, S. C., Zhang, P., Xue, Y. F., Wang, F. C., Wang, L., Cao, T. Q., et al. (2018). Microstructure evolution of Al0.6CoCrFeNi high entropy alloy powder prepared by high pressure gas atomization. Trans. Nonferrous Metals Soc. China. 28, 939–945. doi:10.1016/s1003-6326(18)64728-4
Keywords: high-entropy alloy, thermal–mechanical processing, microstructure, strengthen, mechanical property
Citation: Li J, Yang H, Wang WY, Kou H and Wang J (2021) Thermal–Mechanical Processing and Strengthen in AlxCoCrFeNi High-Entropy Alloys. Front. Mater. 7:585602. doi: 10.3389/fmats.2020.585602
Received: 21 July 2020; Accepted: 02 December 2020;
Published: 18 January 2021.
Edited by:
Lai-Chang Zhang, Edith Cowan University, AustraliaReviewed by:
Songqin Xia, University of Science and Technology Beijing, ChinaYiping Lu, Dalian University of Technology, China
Copyright © 2021 Li, Yang, Wang, Kou and Wang. This is an open-access article distributed under the terms of the Creative Commons Attribution License (CC BY). The use, distribution or reproduction in other forums is permitted, provided the original author(s) and the copyright owner(s) are credited and that the original publication in this journal is cited, in accordance with accepted academic practice. No use, distribution or reproduction is permitted which does not comply with these terms.
*Correspondence: Jinshan Li, bGpzaEBud3B1LmVkdS5jbg==; Jun Wang, bndwdXdqQG53cHUuZWR1LmNu