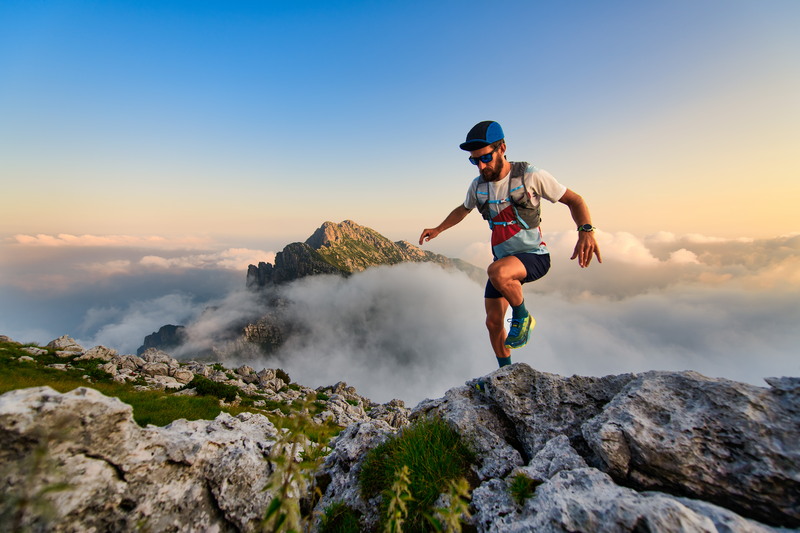
95% of researchers rate our articles as excellent or good
Learn more about the work of our research integrity team to safeguard the quality of each article we publish.
Find out more
ORIGINAL RESEARCH article
Front. Mater. , 06 November 2020
Sec. Ceramics and Glass
Volume 7 - 2020 | https://doi.org/10.3389/fmats.2020.544660
This article is part of the Research Topic Proceedings of PP1594: Topological Engineering of Ultrastrong Glasses View all 13 articles
We study the mechanical properties of nanoglass (NG) nanopillars with diameters ranging from 4.5 to 54 nm by means of molecular dynamic simulations and compare the results with those obtained for nanopillars prepared from homogeneous glasses. NG nanopillars of two different types of glasses, namely, Cu64Zr36 and Pd80Si20, were cut from samples prepared by nanoparticle consolidation. The influence of nanopillar diameter on the deformation behavior and strain localization is investigated. Moreover, cyclic loading is used to explore the origin of stress overshoots in the stress–strain curves of NGs. Finally, from the calculated properties, a deformation map for NG and homogeneous glass nanopillars is derived.
Nanoglasses (NGs) are glassy materials with microstructural features on the nanoscale, which consist of glassy grains connected by glass–glass interfaces (Ivanisenko et al., 2018). These interfaces are characterized by an excess volume (Jing et al., 1989; Şopu et al., 2009), a defective short-range order (SRO) (Ritter et al., 2011), and a different composition as compared with the glassy grains (Adjaoud and Albe, 2016; Wang et al., 2016a; Adjaoud and Albe, 2018). NGs can be synthesized by cold compaction of nanometer-sized metallic glassy particles obtained via inert gas condensation (Jing et al., 1989; Weissmüller et al., 1992; Gleiter, 2008; Fang et al., 2012; Gleiter, 2013; Gleiter et al., 2014; Gleiter, 2016; Nandam et al., 2017; Ivanisenko et al., 2018). Microcompression test revealed considerable plasticity in an Sc75Fe25 NG, while the homogeneous glass (HG) with identical composition fails in a brittle manner (Fang et al., 2012). When reducing the sample size to the nanoscale, 15% plastic strain was observed in a 400 nm Sc75Fe25 NG nanopillar using in situ tensile tests in a transmission electron microscope (Wang et al., 2015). Moreover, a systematic study of nanosized and microsized Sc75Fe25 HG and NG pillars by means of compression tests showed that both, yield strength and deformation mode, are size-dependent in HG pillars. These properties, however, are size-independent in the NG pillars (Wang et al., 2016b), which was attributed to the microstructural features present in the NG. Indeed, molecular dynamic (MD) simulations revealed that glass–glass interfaces in NGs act as nucleation sites for shear transformation zones (STZs) and prevent strain localization, which leads to the more homogeneous deformation of NGs as compared with HGs (Şopu et al., 2011; Adibi et al., 2013; Albe et al., 2013; Adibi et al., 2014; Şopu and Albe, 2015; Adjaoud and Albe, 2019; Cheng and Trelewicz, 2019b).
MD simulations were also used in the past to investigate the effect of grain size on the deformation behavior of a 50 nm Cu64Zr36 NG nanopillar (Adibi et al., 2015a; Adibi et al., 2016). In these studies, the nanopillar was prepared by cutting a cylinder from an NG produced from an HG using the Poisson–Voronoi tessellation method (Brostow et al., 1978; Finney, 1979; Tanemura et al., 1983). However, this model of an NG underestimates the volume fraction of the interfaces as compared with the NGs prepared by consolidation of nanoparticles (Adjaoud and Albe, 2018; Cheng and Trelewicz, 2019a; Cheng and Trelewicz, 2019b; Adjaoud and Albe, 2019) which is more consistent with the experiment (Fang et al., 2012; Wang et al., 2015; Wang et al., 2016b).
In this work, we report the results of a systematic study on the influence of nanopillar diameter on the mechanical properties of NG and HG nanopillars with various diameters by means of MD simulations. The NG nanopillars were cut from NGs prepared by nanoparticle consolidation (Adjaoud and Albe, 2018). We first investigate the influence of nanopillar diameter on the deformation behavior and strain localization. Then, we examine the effects of nanopillar diameter on Young’s modulus and yield stress of NG and HG nanopillars. We finally use the obtained mechanical properties to derive a deformation map for NG and HG nanopillars. In order to see whether the mechanical properties of NG and HG nanopillars depend on the chemical composition, all simulations were done for two different types of NGs and HGs, namely, Cu64Zr36 and Pd80Si20.
MD simulations were carried out using the LAMMPS simulation package (Plimpton, 1995).The interatomic interactions are described by the Finnis–Sinclair-modified-type potential for Cu–Zr (Mendelev et al., 2009) and the embedded atom model potential for Pd–Si (Ding et al., 2012). These potentials have been optimized to predict accurately the structure of liquid and amorphous Cu–Zr and Pd–Si alloys and were successfully applied to Cu–Zr and Pd–Si glasses (Cheng et al., 2013; An et al., 2016; Tang et al., 2018; Adjaoud and Albe, 2019).
First, Cu64Zr36 and Pd80Si20HGs were obtained by quenching a melt, which was already equilibrated at 2,000 K, to a temperature of about 50 K at a quenching rate of 0.01 K ps−1 (Ritter et al., 2011). Next, we prepared Cu64Zr36 and Pd80Si20 NGs by cold compaction of several glassy spheres with diameters ranging from 6 to 8 nm as described by Adjaoud and Albe, 2018. The resulting NGs have dimensions of about 18 nm
The NGs and HGs were replicated and relaxed in order to construct larger samples. After that, the nanopillars were prepared by cutting a cylinder followed by structural relaxation. The diameters of the nanopillars are ranging from D = 4.5–54 nm, which corresponds to 17 million atoms at maximum. The HG nanopillars have a homogeneous microstructure, while the NG nanopillars have an inhomogeneous microstructure (see Supplementary Figure S1). All nanopillars have an aspect ratio (length-to-diameter) of 2, except the nanopillars with D = 4.5 nm which have an aspect ratio of 4. The later aspect ratio is chosen in order to still keep the periodicity in the direction of the axis of the NG nanopillar.
In order to characterize the mechanical properties of NG and HG nanopillars, a series of tensile deformation simulations were performed. The uniaxial tensile load was applied along the axis of the nanopillars, which was chosen in the z-direction, with a constant strain rate of 4.107 s−1 at 50 K. The atomic scale deformation mechanisms were analyzed in terms of the local atomic von Mizes shear strain calculated with the OVITO analysis and visualization software (Stukowski, 2010).
In NG nanopillars, the glass–glass interfaces as well as the free surface can act as nucleation sites for shear events (Albe et al., 2013). Figures 1A,B present the stress–strain curves for Cu64Zr36 and Pd80Si20 NG nanopillars with an average grain size of d = 7 nm and diameters ranging from D = 4.5–54 nm. It can be seen that the maximum stress,
FIGURE 1. Tensile test of Cu64Zr36 and Pd80Si20 nanoglass (NG) and homogeneous glass (HG) nanopillars with an average grain size of d = 7 nm and diameters ranging from D = 4.5–54 nm. (A,B) Engineering stress–strain curves for NG nanopillars. (C,D) Engineering stress–strain curves for HG nanopillars. (E,F) Local von Mises shear strain at 27% total strain, showing strain localization in the NG nanopillars. (G,H) Local von Mises shear strain at 16% total strain, showing strain localization in the HG nanopillars. Engineering stress–strain curves for HG and NG bulk samples are added for reference; those for Cu64Zr36 bulk samples are taken from reference (Adjaoud and Albe, 2019).
Nanopillars with a diameter smaller than the average grain size (d = 7 nm) exhibit the highest
Figures 1C,D show the engineering stress–strain curves for the Cu64Zr36 and Pd80Si20 HG nanopillars with diameters ranging from 4.5 up to 54 nm. The Cu64Zr36 and Pd80Si20HGs are shown for comparison. It can be seen that the Cu64Zr36 HG exhibits a stress drop after the maximum stress, indicating the formation of a critical shear band (Adjaoud and Albe, 2019). The Pd80Si20 HG, in contrast, does not show a stress drop, suggesting that the Pd80Si20 HG is more ductile than the Cu64Zr36 HG. This is in agreement with the bending experiment and compression test on Pd–Si glasses (Yao et al., 2006; An et al., 2016). The nanopillars with smaller diameters, 4.5 nm for Cu64Zr36 and up to 9 nm for Pd80Si20, show strain softening upon yielding. Nanopillars with larger diameters, D
Next, we inspect the strain localization in NG nanopillars. By analyzing von Mises strains, three deformation modes can be defined: (1) pure necking, when the deformation plane is perpendicular to the deformation axis; (2) pure shear banding, when the angle between the deformation plane and the deformation axis is about 40°–60°; and (3) if a nanopillar is not long enough to allow strain localization to occur in a form of necking or shear banding, then von Mises strain distributes over the whole nanopillar which exhibits homogeneous deformation.
Figures 1E,F show the atomic von Mises shear strain at 27% engineering strain for Cu64Zr36 and Pd80Si20 NG nanopillars. It can be seen that the 4.5 nm nanopillars deform by necking. This necking deformation mode can be explained by the large surface-to-volume fraction which leads to the nucleation of a high number of STZs at the surface of the nanopillar (Albe et al., 2013). The 9 and 18 nm NG nanopillars, where the diameter is about or twice the average grain size, exhibit nearly homogeneous deformation, confirming the weak strain softening observed in the stress–strain curves (see Figures 1A,B). When the nanopillar diameter is significantly larger than the average grain size, as in the case of the 36 and 54 nm NG nanopillars, the nanopillars deform again by necking. This is consistent with the strain softening occurring in the stress–train curves. By comparing the Cu64Zr36 and Pd80Si20 NG nanopillars, it can be seen that the deformation behavior is similar and thus does not depend on the type of the NG nanopillars. Moreover, even after deformation, the interfaces are still characterized by compositional variation (see Supplementary Figure S2).
Recent MD studies (Adjaoud and Albe, 2019; Cheng and Trelewicz, 2019b) revealed that the mechanical properties of bulk NG samples are rather independent of the grain size which was attributed to the constant volume fraction of interfaces for NGs with different grain sizes because of the varying interfaces’ width. Based on those results, one could expect that the deformation behavior of the NG nanopillars in the present study is grain-size independent as their bulk NGs counterparts. It is interesting to note that a different result was obtained for bulk NGs and NG nanopillars produced by the Poisson–Voronoi tessellation method, which exhibits a grain-size-dependent deformation behavior because the glass–glass interfaces are assumed to have a constant width of 1 nm independent of the grain size (Adibi et al., 2013; Adibi et al., 2015a).
If we compare the NG nanopillars and bulk NG samples of both glasses, we see that bulk NG samples show no strain softening and a homogeneous deformation behavior (Adjaoud and Albe, 2019; Cheng and Trelewicz, 2019b) similar to the 9 nm NG nanopillars (see Figures 1A,B).
In order to see whether the necking deformation mode, which is observed in the Cu64Zr36 and Pd80Si20 NG nanopillars, is related to the presence of glass–glass interfaces or free surface, we inspected the atomic von Mises shear strain in the HG nanopillars which is shown in Figures 1G,H at 16% engineering strain. It can be seen that, with smaller diameters, the nanopillars deform by necking, while strain localization in the nanopillars with larger diameters occurs in the form of a shear band. This is in line with previous MD simulation results (Adibi et al., 2015b). Again, because of the large surface-to-volume fraction, the 4.5 nm HG nanopillars deform by necking independent of the chemical composition, similar to the 4.5 nm NG nanopillars. Previous atomistic simulations on Cu64Zr36 HGs have shown that a sample thickness of at least 5 nm is needed for shear band formation (Cheng and Ma, 2011).
Comparing the Cu64Zr36 HG nanopillars with the Pd80Si20 HG nanopillars, we find that the stress drop is steeper and strain localization is more pronounced in the Cu64Zr36 HG nanopillars. Moreover,
Our results show that the main differences between the NG nanopillars and HG nanopillars are maximum stress
It is known that cyclic loading may significantly affect the deformation behavior of materials. Cyclic loading is usually performed in the elastic regime (Sha et al., 2015;Sha et al., 2017) or in the plastic regime (Zhu et al., 2017; Tang et al., 2018). The cyclic loading of metallic glasses in the plastic regime leads usually to the phenomenon of stress overshoot (Maaß et al., 2012).
In order to investigate the stress overshoot and the remaining plastic deformation in the NG nanopillars in more detail, we performed cyclic loading on the 18 nm Cu64Zr36 and Pd80Si20 NG nanopillars by unloading them from 15% engineering strain and then reloading them. Figures 2A,B present the corresponding stress–strain curves during the cyclic loading. In both glasses, the cyclic loading leads to a slight increase of flow stress after reloading caused by structural relaxation: the fractions of the Cu-centered icosahedra in the Cu64Zr36 NG nanopillar, including full icosahedra (index [0,12,0,0]) and disordered icosahedra (indexes [0,2,8,2] and [0,3,6,3]) and the most prominent Voronoipolyhedra Si[0,3,6,0] in the Pd80Si20 NG nanopillar, significantly increase after the first loading stage (see Figures 2C,D), which indicates that defective interfacial areas are relaxed during the initial stage of plastic deformation.
FIGURE 2. Cu64Zr36 and Pd80Si20 nanoglass (NG) and homogeneous glass (HG) nanopillars with a diameter of 18 nm under cyclic loading. (A,B) Engineering stress–strain curves for NG nanopillars. (C) Variation of Cu-centered icosahedra in the Cu64Zr36 NG nanopillars, including full icosahedra (index [0,12,0,0]) and disordered icosahedra (indexes [0,2,8,2] and [0,3,6,3]) as a function of the engineering strain. (D) Variation of the most prominent Voronoipolyhedra in the Pd80Si20 NG nanopillar, Si[0,3,6,0], as a function of the engineering strain. (E,F) Engineering stress–strain curves for HG nanopillars. (G) Variation of Cu-centered icosahedra in the Cu64Zr36 HG nanopillars as a function of the engineering strain. (H) Variation of the most prominent Voronoipolyhedra in the Pd80Si20 HG nanopillar, Si[0,3,6,0], as a function of the engineering strain. The engineering stress–strain curves for the monotonic loading of 18 nm Cu64Zr36 and Pd80Si20 NG and HG nanopillars are reproduced for reference.
The correlation between the increase of flow stress and structural relaxation is also observed in the HG nanopillars (see Figures 2E–H). However, in the HG nanopillars, the stress increases only in a small region of engineering strains as compared with the NG nanopillars: after the initial stress increases, the stresses of the monotonic tensile loading and the cyclic loading merge together in the Cu64Zr36 HG nanopillar, while in the Pd80Si20 HG nanopillar, the stress of the cyclic loading is slightly lower than that of the monotonic tensile loading. Moreover, the fractions of the Cu-centered icosahedra in the Cu64Zr36 HG nanopillar and the Voronoipolyhedra Si[0,3,6,0] in the Pd80Si20 HG nanopillar for the cyclic loading remain higher than those for the monotonic tensile loading after the stress overshoot, indicating the recovery of the local order upon unloading.
These results are in agreement with recent MD simulation results which showed that a cyclic loading after the formation of a shear band in a Cu50Zr50 HG leads to structural relaxation, and consequently, a stress increase occurs in the stress–strain curve (Tang et al., 2018). Experiments and theoretical models have shown that this phenomenon depends on temperature, strain rate, and structural relaxation (Kawamura et al., 1997; Lu et al., 2003; Maaß et al., 2012; Jiang et al., 2015; Yang et al., 2019).
We, next, explore the effect of nanopillar diameter on Young’s modulus and yield strength. We obtained Young’s modulus from the slope of stress–strain curves at the small strain where the stress is proportional to the strain. We used 0.2% offset strain to calculate the yield strength. Figures 3A,B show the calculated Young’s moduli as a function of the nanopillar diameter for Cu64Zr36 and Pd80Si20 NG and HG nanopillars. The HG and NG bulk samples are shown for comparison.
FIGURE 3. Effect of size on Young’s modulus and yield strength of homogeneous glass (HG) and nanoglass (NG) nanopillars. (A,B) Young’s modulus as a function of the nanopillar diameter for Cu64Zr36 and Pd80Si20 NG and HG nanopillars. (C,D) Yield strength as a function of the nanopillar diameter for Cu64Zr36 and Pd80Si20 NG and HG nanopillars. The HG and NG bulk samples are added for comparison.
The calculated Young’s moduli for Cu64Zr36 and Pd80Si20 HGs are in agreement with the experimental data which are about 67 GPa for Cu64Zr36 (Mendelev et al., 2008) and 94 Gpa for Pd80Si20 (Mizubayashi et al., 1998). It can be seen that Young’s modulus depends slightly on the nanopillar diameter when D
In order to further investigate the difference in deformation modes between the NG and HG nanopillars, we calculated the critical stress required for SB formation (Volkert et al., 2008),
The predicted critical stress values for the homogeneous glasses (HGs) match very well with the observed deformation modes as shown in Figure4. The only exception is the Cu–Zr nanopillar with D = 9 nm. In case of the NG nanopillars, the data fall in the homogeneous regime. The only clear exceptions are the data for the nanopillars with D
FIGURE 4. Flow stress normalized by Young’s modulus and shear band energy per unit area as a function of the nanopillar diameter at 5% total strain. Red squares and red circles represent Cu64Zr36 and Pd80Si20 homogeneous glass (HG) nanopillars, respectively. Blue squares and blue circles represent Cu64Zr36 and Pd80Si20nanoglass (NG) nanopillars, respectively. Open symbols indicate the occurrence of a shear band.
The results presented above are for nanopillars with diameters up to 54 nm. This size is much smaller than that used in experiment which is about 400 nm (Wang et al., 2015). Sample preparation and mechanical testing in experiments make it difficult to prepare nanopillars with diameters below 100 nm (Shi, 2019). On the other hand, the increase of the nanopillar size in MD simulation leads to the increase of the number of atoms, and this becomes computationally expensive. Although the sample size mismatched between MD simulation and experiment, MD simulation is useful to understand experimental observations (Liontas et al., 2016). From the present MD results, one can see that, for both systems, Cu–Zr and Pd–Si, the 36 and 54 nm NG nanopillars exhibit a similar mechanical behavior. This may be attributed to the small surface-to-volume fraction which leads to the deformation to be dominated by the interfaces rather than by the surface. Indeed, a recent MD simulation study on HG nanopillars has shown that the surface stress becomes less significant when the nanopillar diameter is larger than 30 nm (Zhang et al., 2015). Thus, one could expect that NG nanopillars with diameters larger than 54 nm should show a similar mechanical behavior as the 36 and 54 nm nanopillars.
Present MD simulation results on HG nanopillars show that the transition from necking to shear banding occurs at a diameter between 10 and 20 nm. These results are in agreement with previous MD simulation results which reported that size-independent shear banding until their dimensions approach the shear-band thickness which is about 5–20 nm (Adibi et al., 2016; Liontas et al., 2016; Shi, 2019). This transition appears in experiments at a lager sample diameter, between 100 and 400 nm, as compared with MD simulations (Tian et al., 2016). This difference in the sample size on the change of the deformation mode between experiments and simulations can be related to the different processing and testing conditions (Shi, 2019).
Simulations of NG nanopillars reveal no shear banding: NG nanopillars exhibit necking or homogeneous deformation. Homogeneous deformation occurs in the 9 and 18 nm NG nanopillars, where their length is not long enough to allow strain localization to form necking. Necking deformation mode was also reported in previous MD simulations on the Cu64Zr36 NG nanopillars with a diameter of 50 nm (Adibi et al., 2015a; Adibi et al., 2016).
The NG nanopillars studied in the present study are cut from an as-prepared NG. Structural relaxation due to the high compaction rate used in simulation during the preparation of the NG may change the deformation mode. Indeed, a recent study on the compression test of Pd–Si NG nanopillar with a diameter of 36 nm showed a change in the deformation mode from homogeneous deformation to shear banding when the nanopillar is cut from an annealed NG (Nandam et al., 2020). The effect of annealing on the change of the deformation mode was also reported in a recent experiment and simulation study on Zr–Ni–Al nanosized metallic glasses (Liontas et al., 2016).
We have investigated the influence of structure size on the mechanical properties of NG and HG nanopillars with 7 nm grain size and diameters ranging from 4.5 up to 54 nm by means of MD simulations. Simulations were done for two different glasses, namely, Cu64Zr36 and Pd80Si20, as representatives of metal–metal and metal–metalloid systems, respectively. Different from previous studies, the NGs were produced by consolidation rather than Voronoi tessellation and thus have a more realistic microstructure.
Our results show a clear difference in the deformation mode between NG and HG for the 36 and 54 nm nanopillars, independent of the glass type. While HG nanopillars exhibit a stress drop and strain localization developing in a shear band, NG nanopillars show ductile deformation behavior with softening at larger engineering strains and deformation by necking. The tensile ductility of about 13–15% found in our simulations is in agreement with 15% plastic strain observed for a 400 nm Sc75Fe25 NG nanopillar using in situ tensile tests in a transmission electron microscope (Wang et al., 2015). HG and NG nanopillars with D = 4.5 nm, where the pillar diameter is smaller than the average grain size d = 7 nm of the NG, deform by necking since the nucleation of STZs on the surface is dominating. In the HG nanopillars with D = 9 and 18 nm, shear banding is more obvious in Cu64Zr36 than in Pd80Si20. When reducing the NG nanopillar diameter to near or double the average grain size, strain softening appears at the larger engineering strain (>20%). Moreover, structural relaxation after a cyclic loading leads to local recovery, and the stress increases upon reloading.
We determined Young’s modulus and yield strengths from stress–strain curves of tensile deformations. We find that both properties are smaller in the NG nanopillars as compared with their homogeneous counterparts in both glasses. From Young’s modulus values and the shear band energy, the critical stress for shear band formation is estimated. We find that the predicted critical stress values are quite consistent with the observed deformation modes.
All datasets generated for this study are included in the article and Supplementary Material.
OA and KA contributed equally to the conception and design of this study; OA set up and ran the simulations, performed the analysis, and wrote the first draft of the manuscript; KA supervised the work and reviewed and edited the manuscript.
The authors acknowledge the financial support of the Deutsche Forschungsgemeinschaft (DFG) through project no. AL 578/15–2.
The authors declare that the research was conducted in the absence of any commercial or financial relationships that could be construed as a potential conflict of interest.
The authors gratefully acknowledge the Gauss Centre for Supercomputing e.V. (www.gauss-centre.eu) for funding this project by providing computing time through the John von Neumann Institute for Computing (NIC) on the GCS Supercomputer JUWELS at Jülich Supercomputing Centre (JSC). Computational time was also made available by the Lichtenberg High Performance Computer Cluster at TU Darmstadt.
The Supplementary Material for this article can be found online at: https://www.frontiersin.org/articles/10.3389/fmats.2020.544660/full#supplementary-material.
Adibi, S., Branicio, P. S., and Ballarini, R. (2016). Compromising high strength and ductility in nanoglass-metallic glass nanolaminates. RSC Adv. 6, 13548–13553. doi:10.1039/C5RA24715B
Adibi, S., Branicio, P. S., and Joshi, S. P. (2015a). Suppression of shear banding and transition to necking and homogeneous flow in nanoglass nanopillars. Sci. Rep. 5, 15611. doi:10.1038/srep15611
Adibi, S., Branicio, P. S., Liontas, R., Chen, D. Z., Greer, J. R., Srolovitz, D. J., et al. (2015b). Surface roughness imparts tensile ductility to nanoscale metallic glasses. Extreme Mech. Lett. 5, 88–95. doi:10.1016/j.eml.2015.08.004
Adibi, S., Branicio, P. S., Zhang, Y.-W., and Joshi, S. P. (2014). Composition and grain size effects on the structural and mechanical properties of CuZr nanoglasses. J. Appl. Phys. 116, 043522. doi:10.1063/1.4891450
Adibi, S., Sha, Z.-D., Branicio, P. S., Joshi, S. P., Liu, Z.-S., and Zhang, Y.-W. (2013). A transition from localized shear banding to homogeneous superplastic flow in nanoglass. Appl. Phys. Lett. 103, 211905. doi:10.1063/1.4833018
Adjaoud, O., and Albe, K. (2016). Interfaces and interphases in nanoglasses: surface segregation effects and their implications on structural properties. Acta Mater. 113, 284. doi:10.1016/j.actamat.2016.05.002
Adjaoud, O., and Albe, K. (2018). Microstructure formation of metallic nanoglasses: insights from molecular dynamics simulations. Acta Mater. 145, 322–330. doi:10.1016/j.actamat.2017.12.014
Adjaoud, O., and Albe, K. (2019). Influence of microstructural features on the plastic deformation behavior of metallic nanoglasses. Acta Mater. 168, 393–400. doi:10.1016/j.actamat.2019.02.033
Albe, K., Ritter, Y., and Şopu, D. (2013). Enhancing the plasticity of metallic glasses: shear band formation, nanocomposites and nanoglasses investigated by molecular dynamics simulations. Mech. Mater. 67, 94–103. doi:10.1016/j.mechmat.2013.06.004
An, Q., Samwer, K., Demetriou, M. D., Floyd, M. C., Duggins, D. O., Johnson, W. L., et al. (2016). How the toughness in metallic glasses depends on topological and chemical heterogeneity. Proc. Natl. Acad. Sci. U. S. A. 113, 7053–7058. doi:10.1073/pnas.1607506113
Brostow, W., Dussault, J.-P., and Fox, B. L. (1978). Construction of voronoi polyhedra. J. Comput. Phys. 29, 81–92. doi:10.1016/0021-9991(78)90110-9
Cao, A. J., Cheng, Y. Q., and Ma, E. (2009). Structural processes that initiate shear localization in metallic glass. Acta Mater. 57, 5146 – 5155.
10.1016/j.actamat.2009.07.016CrossRef Full Text | Google Scholar
Chen, C. Q., Pei, Y. T., and De Hosson, J. T. M. (2010). Effects of size on the mechanical response of metallic glasses investigated through in situ TEM bending and compression experiments. Acta Mater. 58, 189–200. doi:10.1016/j.actamat.2009.08.070
Cheng, B., and Trelewicz, J. R. (2019a). Controlling interface structure in nanoglasses produced through hydrostatic compression of amorphous nanoparticles. Phys. Rev. Materials. 3, 035602. doi:10.1103/PhysRevMaterials.3.035602
Cheng, B., and Trelewicz, J. R. (2019b). Interfacial plasticity governs strain delocalization in metallic nanoglasses. J. Mater. Res. 34, 2325–2336. doi:10.1557/jmr.2019.101
Cheng, Y. Q., Ding, J., and Ma, E. (2013). Local Topologyvs.Atomic-level stresses as a measure of disorder: correlating structural indicators for metallic glasses. Mater. Res. Lett. 1, 3–12. doi:10.1080/21663831.2012.722759
Cheng, Y. Q., and Ma, E. (2011). Intrinsic shear strength of metallic glass. Acta Mater. 59, 1800–1807.
10.1016/j.actamat.2010.11.046CrossRef Full Text | Google Scholar
Ding, J., Cheng, Y.-Q., Sheng, H., and Ma, E. (2012). Short-range structural signature of excess specific heat and fragility of metallic-glass-forming supercooled liquids. Phys. Rev. B 85, 060201. doi:0.1103/PhysRevB.85.060201
Dubach, A., Raghavan, R., Loffler, J., Michler, J., and Ramamurty, U. (2009). Micropillar compression studies on a bulk metallic glass in different structural states. Scripta Mater. 60, 567–570. doi:10.1016/j.scriptamat.2008.12.013
Fang, J. X., Vainio, U., Puff, W., Würschum, R., Wang, X. L., Wang, D., et al. (2012). Atomic structure and structural stability of Sc75Fe25 nanoglasses. Nano Lett. 12, 458–463. doi:10.1021/nl2038216
Finney, J. L.. (1979). A procedure for the construction of voronoi polyhedra. J. Comput. Phys. 32, 137–143.
10.1016/0021-9991(79)90146-3CrossRef Full Text | Google Scholar
Gleiter, H. (2008). Our thoughts are ours, their ends none of our own: are there ways to synthesize materials beyond the limitations of today? Acta Mater. 56, 5875–5893. doi:10.1016/j.actamat.2008.08.028
Gleiter, H. (2013). Nanoglasses: a new kind of noncrystalline materials. Beilstein J. Nanotechnol. 4, 517–533. doi:10.3762/bjnano.4.61
Gleiter, H. (2016). Nanoglasses: a new kind of noncrystalline material and the way to an age of new technologies?. Small 12, 2225–2233. doi:10.1002/smll.201500899
Gleiter, H., Schimmel, T., and Hahn, H. (2014). Nanostructured solids - from nano-glasses to quantum transistors. Nano Today. 9, 17–68. doi:10.1016/j.nantod.2014.02.008
Ivanisenko, Y., Kübel, C., Nandam, S. H., Wang, C., Mu, X., Adjaoud, O., et al. (2018). Structure and properties of nanoglasses. Adv. Eng. Mater. 20, 1800404. doi:10.1002/adem.201800404
Jiang, M. Q., Wilde, G., and Dai, L. H. (2015). Origin of stress overshoot in amorphous solids. Mech. Mater. 81, 72–83.
10.1016/j.mechmat.2014.10.002CrossRef Full Text | Google Scholar
Jing, J., Krämer, A., Birringer, R., Gleiter, H., and Gonser, U. (1989). Modified atomic structure in a Pd‐Fe‐Si nanoglass. J. Non-Cryst. Solids. 113, 167–170. doi:10.1016/0022-3093(89)90007-0
Kawamura, Y., Shibata, T., Inoue, A., and Masumoto, T. (1997). Stress overshoot in stress-strain curves of Zr65Al10Ni10Cu15 metallic glass. Appl. Phys. Lett. 71, 779–781. doi:10.1063/1.119643
Li, F. C., Wang, T. Y., He, Q. F., Sun, B. A., Guo, C. Y., Feng, T., et al. (2018). Micromechanical mechanism of yielding in dual nano-phase metallic glass. Scripta Mater. 154, 186–191. doi:10.1016/j.scriptamat.2018.05.050
Liontas, R., Jafary-Zadeh, M., Zeng, Q., Zhang, Y.-W., Mao, W. L., and Greer, J. R. (2016). Substantial tensile ductility in sputtered Zr-Ni-Al nano-sized metallic glass. Acta Mater. 118, 270–285. doi:10.1016/j.actamat.2016.07.050
Liu, C., Roddatis, V., Kenesei, P., and Maaß, R. (2017). Shear-band thickness and shear-band cavities in a zr-based metallic glass. Acta Mater. 140, 206–216.
10.1016/j.actamat.2017.08.032CrossRef Full Text | Google Scholar
Liu, Z., Li, R., Wang, G., Wu, S., Lu, X., and Zhang, T. (2011). Quasi phase transition model of shear bands in metallic glasses. Acta Mater. 59, 7416–7424.
10.1016/j.actamat.2011.08.002CrossRef Full Text | Google Scholar
Lu, J., Ravichandran, G., and Johnson, W. L. (2003). Deformation behavior of the Zr41.2Ti13.8Cu12.5Ni10Be22.5 bulk metallic glass over a wide range of strain-rates and temperatures. Acta Mater. 51, 3429–3443.
10.1016/S1359-6454(03)00164-2CrossRef Full Text | Google Scholar
Maaß, R., Klaumünzer, D., Villard, G., Derlet, P. M., and Löffler, J. F. (2012). Shear-band arrest and stress overshoots during inhomogeneous flow in a metallic glass. Appl. Phys. Lett. 100, 071904. doi:10.1063/1.3684871
Mendelev, M. I., Kramer, M. J., Ott, R. T., Sordelet, D. J., Yagodin, D., and Popel, P. (2009). Development of suitable interatomic potentials for simulation of liquid and amorphous Cu-Zr alloys. Phil. Mag. 89, 967–987. doi:10.1080/14786430902832773
Mendelev, M. I., Ott, R. T., Heggen, M., Feuerebacher, M., Kramer, M. J., and Sordelet, D. J. (2008). Deformation behavior of an amorphous Cu64.5Zr35.5 alloy: a combined computer simulation and experimental study. J. Appl. Phys. 104, 123532. doi:10.1063/1.3043587
Mizubayashi, H., Okamoto, T., Koyama, K., and Horiuchi, M. (1998). Dynamic anelastic response of amorphous alloys suggesting collective motions of many atoms. Acta Mater. 46, 1257–1264.
10.1016/S1359-6454(97)00283-8CrossRef Full Text | Google Scholar
Murali, P., Zhang, Y. W., and Gao, H. J. (2012). On the characteristic length scales associated with plastic deformation in metallic glasses. Appl. Phys. Lett. 100, 201901. doi:10.1063/1.4717744
Nandam, S. H., Adjaoud, O., Schwaiger, R., Ivanisenko, Y., Chellali, M. R., Wang, D., et al. (2020). Influence of topological structure and chemical segregation on the thermal and mechanical properties of Pd-Si nanoglasses. Acta Mater. 193, 252–260. doi:10.1016/j.actamat.2020.03.021
Nandam, S. H., Ivanisenko, Y., Schwaiger, R., Śniadecki, Z., Mu, X., Wang, D., et al. (2017). Cu-Zr nanoglasses: atomic structure, thermal stability and indentation properties. Acta Mater. 136, 181–189. doi:10.1016/j.actamat.2017.07.001
Plimpton, S. (1995). Fast parallel algorithms for short-range molecular dynamics. J. Comput. Phys. 117, 1–19.
Ritter, Y., and Albe, K. (2012). Chemical and topological order in shear bands of Cu64Zr36 and Cu36Zr64 glasses. J. Appl. Phys. 111, 103527. doi:10.1063/1.4717748
Ritter, Y., Şopu, D., Gleiter, H., and Albe, K. (2011). Structure, stability and mechanical properties of internal interfaces in Cu64Zr36 nanoglasses studied by MD simulations. Acta Mater. 59, 6588–6593. doi:10.1016/j.actamat.2011.07.013
Şopu, D., and Albe, K. (2015). Influence of grain size and composition, topology and excess free volume on the deformation behavior of Cu–Zr nanoglasses. Beilstein J. Nanotechnol. 6, 537–545. doi:10.3762/bjnano.6.56
Şopu, D., Albe, K., Ritter, Y., and Gleiter, H. (2009). From nanoglasses to bulk massive glasses. Appl. Phys. Lett. 94, 191911. doi:10.1063/1.3130209
Şopu, D., Ritter, Y., Gleiter, H., and Albe, K. (2011). Deformation behavior of bulk and nanostructured metallic glasses studied via molecular dynamics simulations. Phys. Rev. B 83, 100202. doi:10.1103/PhysRevB.83.100202
Sha, Z., Wong, W. H., Pei, Q., Branicio, P. S., Liu, Z., Wang, T., et al. (2017). Atomistic origin of size effects in fatigue behavior of metallic glasses. J. Mech. Phys. Solid. 104, 84–95. doi:10.1016/j.jmps.2017.04.005
Sha, Z. D., Qu, S. X., Liu, Z. S., Wang, T. J., and Gao, H. (2015). Cyclic deformation in metallic glasses. Nano Lett. 15, 7010–7015. doi:10.1021/acs.nanolett.5b03045
Shao, Y., Yao, K., Li, M., and Liu, X. (2013). Two-zone heterogeneous structure within shear bands of a bulk metallic glass. Appl. Phys. Lett. 103, 171901. doi:10.1063/1.4826117
Shi, Y. (2019). Size-dependent mechanical responses of metallic glasses. Int. Mater. Rev. 64, 163–180. doi:10.1080/09506608.2018.1476079
Stukowski, A. (2010). Visualization and analysis of atomistic simulation data with OVITO-the Open Visualization Tool. Model. Simulat. Mater. Sci. Eng. 18, 015012. doi:10.1088/0965-0393/18/1/015012
Tanemura, M., Ogawa, T., and Ogita, N. (1983). A new algorithm for three-dimensional voronoi tessellation. J. Comput. Phys. 51, 191–207. doi:10.1016/0021-9991(83)90087-6
Tang, C., Laws, K., and Ferry, M. (2018). Atomistic origin of stress overshoots and serrations in a cuzr metallic glass. Materialia 1, 121–127. doi:10.1016/j.mtla.2018.04.005
Tian, L., Wang, X.-L., and Shan, Z.-W. (2016). Mechanical behavior of micronanoscaled metallic glasses. Mater. Res. Lett. 4, 63–74. doi:10.1080/21663831.2015.1124298
Volkert, C. A., Donohue, A., and Spaepen, F. (2008). Effect of sample size on deformation in amorphous metals. J. Appl. Phys. 103, 083539. doi:10.1063/1.2884584
Wang, C., Wang, D., Mu, X., Goel, S., Feng, T., Ivanisenko, Y., et al. (2016a). Surface segregation of primary glassy nanoparticles of Fe90Sc10 nanoglass. Mater. Lett. 181, 248–252. doi:10.1016/j.matlet.2016.05.189
Wang, X., Jiang, F., Hahn, H., Li, J., Gleiter, H., Sun, J., et al. (2016b). Sample size effects on strength and deformation mechanism of Sc75Fe25 nanoglass and metallic glass. Scripta Mater. 116, 95–99. doi:10.1016/j.scriptamat.2016.01.036
Wang, X. L., Jiang, F., Hahn, H., Li, J., Gleiter, H., Sun, J., et al. (2015). Plasticity of a scandium-based nanoglass. Scripta Mater. 98, 40–43. doi:10.1016/j.scriptamat.2014.11.010
Weissmüller, J., Birringer, R., and Gleiter, H. (1992). Nanostructured crystalline and amorphous solids. Kemi 77-78, 161–170. doi:10.4028/www.scientific.net/kem.77-78.161
Yang, Z.-Y., Wang, Y.-J., and Dai, L.-H. (2019). Susceptibility of shear banding to chemical short-range order in metallic glasses. Scripta Mater. 162, 141–145.
10.1016/j.scriptamat.2018.11.001CrossRef Full Text | Google Scholar
Yao, K. F., Ruan, F., Yang, Y. Q., and Chen, N. (2006). Superductile bulk metallic glass. Appl. Phys. Lett. 88, 122106. doi:10.1063/1.2187516
Zhang, Q., Li, Q.-K., and Li, M. (2015). Internal stress and its effect on mechanical strength of metallic glass nanowires. Acta Mater. 91, 174–182. doi:10.1016/j.actamat.2015.03.029
Zhang, Y., and Greer, A. L. (2006). Thickness of shear bands in metallic glasses. Appl. Phys. Lett. 89, 071907. doi:10.1063/1.2336598
Zhong, C., Zhang, H., Cao, Q. P., Wang, X. D., Zhang, D. X., and Jiang, J. Z. (2015). The size-dependent non-localized deformation in a metallic alloy. Scripta Mater. 101, 48–51. doi:10.1016/j.scriptamat.2015.01.015
Keywords: metallic glass, nanoglass, glass–glass interfaces, nanopillar, mechanical properties, molecular dynamics
Citation: Adjaoud O and Albe K (2020) Mechanical Properties of Glassy Nanopillars: A Comparative, Computational Study of Size Effects in Nanoglasses and Homogeneous Bulk Glasses. Front. Mater. 7:544660. doi: 10.3389/fmats.2020.544660
Received: 21 March 2020; Accepted: 22 September 2020;
Published: 06 November 2020.
Edited by:
Lothar Wondraczek, Friedrich Schiller University Jena, GermanyReviewed by:
Saurabh Kapoor, SterliteTechnologies Ltd., IndiaCopyright © 2020 Adjaoud and Albe. This is an open-access article distributed under the terms of the Creative Commons Attribution License (CC BY). The use, distribution or reproduction in other forums is permitted, provided the original author(s) and the copyright owner(s) are credited and that the original publication in this journal is cited, in accordance with accepted academic practice. No use, distribution or reproduction is permitted which does not comply with these terms.
*Correspondence: Omar Adjaoud, YWRqYW91ZEBtbS50dS1kYXJtc3RhZHQuZGU=
Disclaimer: All claims expressed in this article are solely those of the authors and do not necessarily represent those of their affiliated organizations, or those of the publisher, the editors and the reviewers. Any product that may be evaluated in this article or claim that may be made by its manufacturer is not guaranteed or endorsed by the publisher.
Research integrity at Frontiers
Learn more about the work of our research integrity team to safeguard the quality of each article we publish.