- 1School of Mechanical and Electrical Engineering, Central South University, Changsha, China
- 2School of Microelectronics, Xidian University, Xi’an, China
Over millions of years of evolution, species in nature have gradually adopted bio-structures. These structures have specific mechanical, hydrodynamic, optical, and electrical properties, which provide humans with valuable abilities to design and fabricate high-performance components and devices. However, traditional fabrication technologies cannot accurately reproduce or imitate the complicated and exquisite bioinspired structures, which restrict the development and application of biomimetic study. Due to the emergence and development of 3D printing technologies, more bioinspired structures can now be designed and fabricated. Recent progress in the 3D printing of structures inspired by species in nature, such as springtails, filefish, abalone shell, conch shell, wheat awn, plant stem, and wood, are reviewed in this paper, which also discusses current challenges and potential future developments in 3D printing for bioinspired structures.
Introduction
Due to the urgent demand for components and devices with specific properties, high-performance materials and structures are currently being rapidly developed (Liu et al., 2017; Velasco-Hogan et al., 2018; Li et al., 2019a). Learning from nature, bioinspired materials and structures generally have excellent mechanical, hydrodynamic, optical, and electrical properties (Yang et al., 2018; Kong et al., 2019). From the macroscopic to the microscopic scale, some bioinspired structures are proposed and developed according to the typical characteristics and structures of animals and plants, as shown in Figure 1. This biomimicry paves the way for developing high-performance materials and structures.
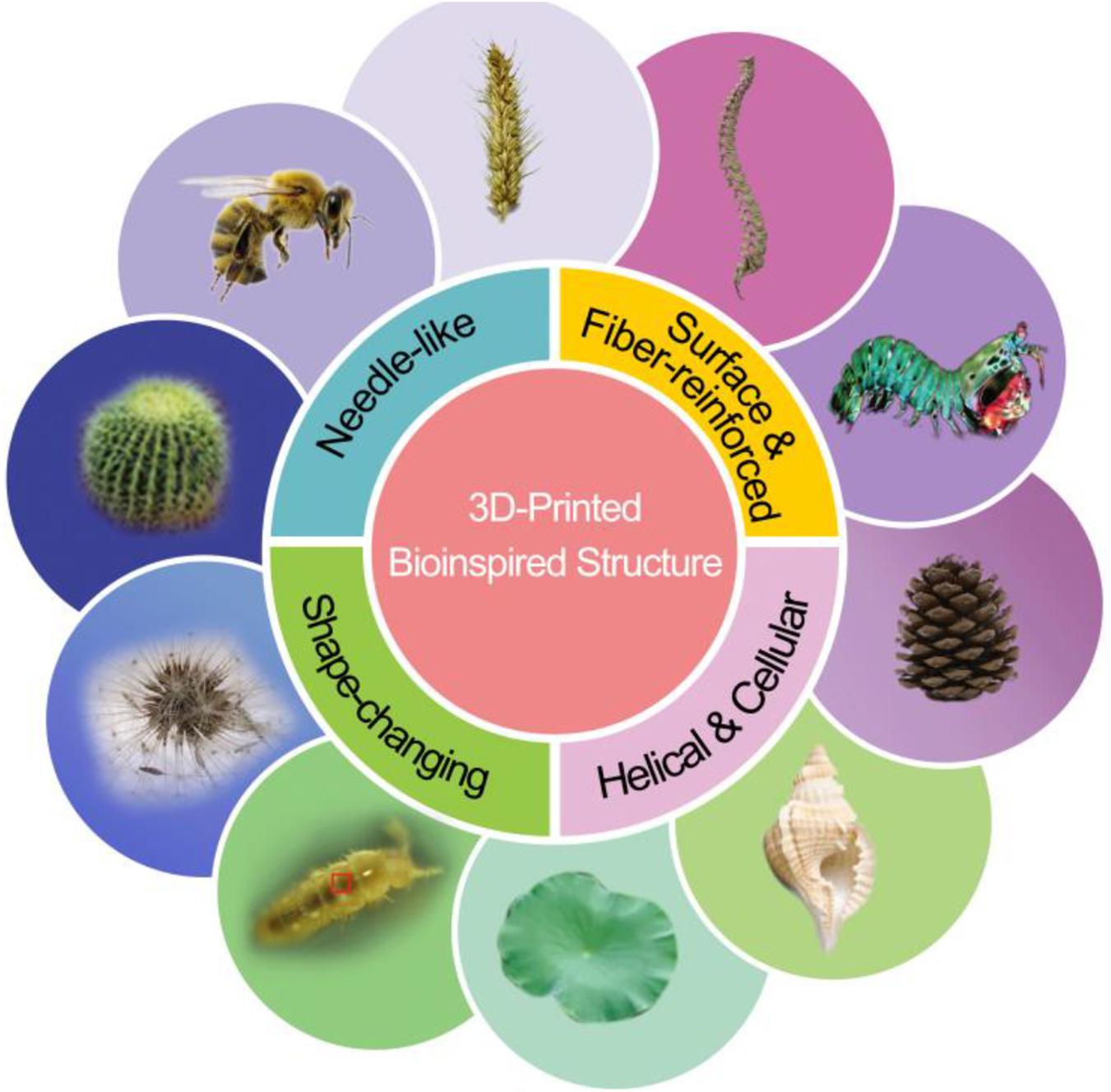
Figure 1. 3D-printed bioinspired structures including geometric (hierarchical, helical, cellular, and needle-like) and functional (surface, fiber-reinforced, and shape-changing) structures.
Generally, bioinspired structures are always complex and exquisite, but cannot be fabricated by using traditional fabrication technologies. Due to the flexibility of 3D printing technologies, it can be used to fabricate structures with arbitrary geometry (Mi et al., 2018; Saha et al., 2019; Spadaccini, 2019). 3D printing technologies include fused deposition modeling (FDM), direct ink writing (DIW), selective laser sintering (SLS), stereolithography (SLA), multijet printing (MJP), and selective laser melting (SLM) (Haleem and Javaid, 2018; Schaffner et al., 2018; Nazir et al., 2019), amongst other technologies, which have been successfully utilized to solve the fabrication challenges of bioinspired structures (Saratti et al., 2018; Du Plessis et al., 2019; Yan et al., 2020). However, there are some limitations to the 3D printing of bioinspired structures. The balance of resolution, cost, and speed for 3D printing are great challenges, and the fabrication of multiscale structures also presents a practical problem.
In this paper, we review the developments in 3D printing for bioinspired structures that have emerged in recent years, focusing largely on bioinspired geometrical and functional structures. The bioinspired geometrical structures include hierarchical, helical, cellular, and needle-like structures and bioinspired functional structures include surface, fiber-reinforced and shape-changing structures. Finally, the review explores the current challenges and potential future developments in this field.
3D Printing of Bioinspired Geometrical Structures
Various geometrical structures with excellent mechanical performance are present in a large number of species in nature. These attributes include high stiffness, strength, toughness, wear resistance, fatigue resistance, and corrosion resistance. Inspired by these geometrical structures, high-performance materials and structures can be fabricated for various applications. In this section, hierarchical, helical, cellular, and needle-like structures are reviewed.
Hierarchical and Helical Structures
A hierarchical structure can be seen everywhere in nature and provides an abundant resource for biomimicry, enabling us to develop materials and structures with reinforced mechanical properties. Using electrically assisted 3D-printing technology, Yang et al. (2019) have fabricated hierarchical structures with complex 3D shapes inspired by the microstructure of nacre, shown in Figure 2A. During the bottom-up projection-based SLA process, graphene nanoplatelets (GNs) were aligned by the electric field (433 V/cm) and acted as bricks, while the photocurable resin (MJ) with low viscosity, served as the mortar between the GNs. The 3D-printed nacre with aligned GNs (2 weight%) has a lightweight property (1.06 g/cm3) while exhibiting comparable toughness and strength to natural nacre. In Figure 2B, Kokkinis et al. (2018) developed a multimaterial 3D-printing platform to fabricate hierarchical structures inspired by mechanical gradients. Multimaterial printing can fabricate exquisite 3D objects by DIW, using two specifically designed resins that include photocurable methacrylate/acrylate monomers and oligomers. The mechanically graded elastomers achievable by a multimaterial ink system were printed into bioinspired structures to study their effect on the mechanical behavior of synthetic heterogeneous materials. The crack initiation and growth processes of graded inter-vertebral discs can be highly controlled and predicted, which highlights the potential of mechanical gradients as an effective way to tune failure and lifetime of biological and synthetic heterogeneous materials. Inspired by the microstructure of stomatopod, bone and abalone shell, the hierarchical and hybrid biomimetic structures were fabricated by rotational DIW using viscoelastic inks composed of short carbon fiber-filled epoxy resins (Jia et al., 2018), as shown in Figure 2C. The results indicate that hybrid architecture designs can be further improved in terms of flexibility, strength, and toughness and that there could be more control over the deformation field, crack initiation location, and crack propagation pattern. This implies that the hybrid design approach provides an alternative to the hierarchical design approach in improving mechanical performance. In Figure 2D, the hierarchical structures inspired by baleen were studied by using advanced multimaterial 3D-printed models (Wang et al., 2018). The simulation results show that the incorporation of the stiff “mineral” component (Model IV) leads to the largest increase in rate stiffening and strengthening.
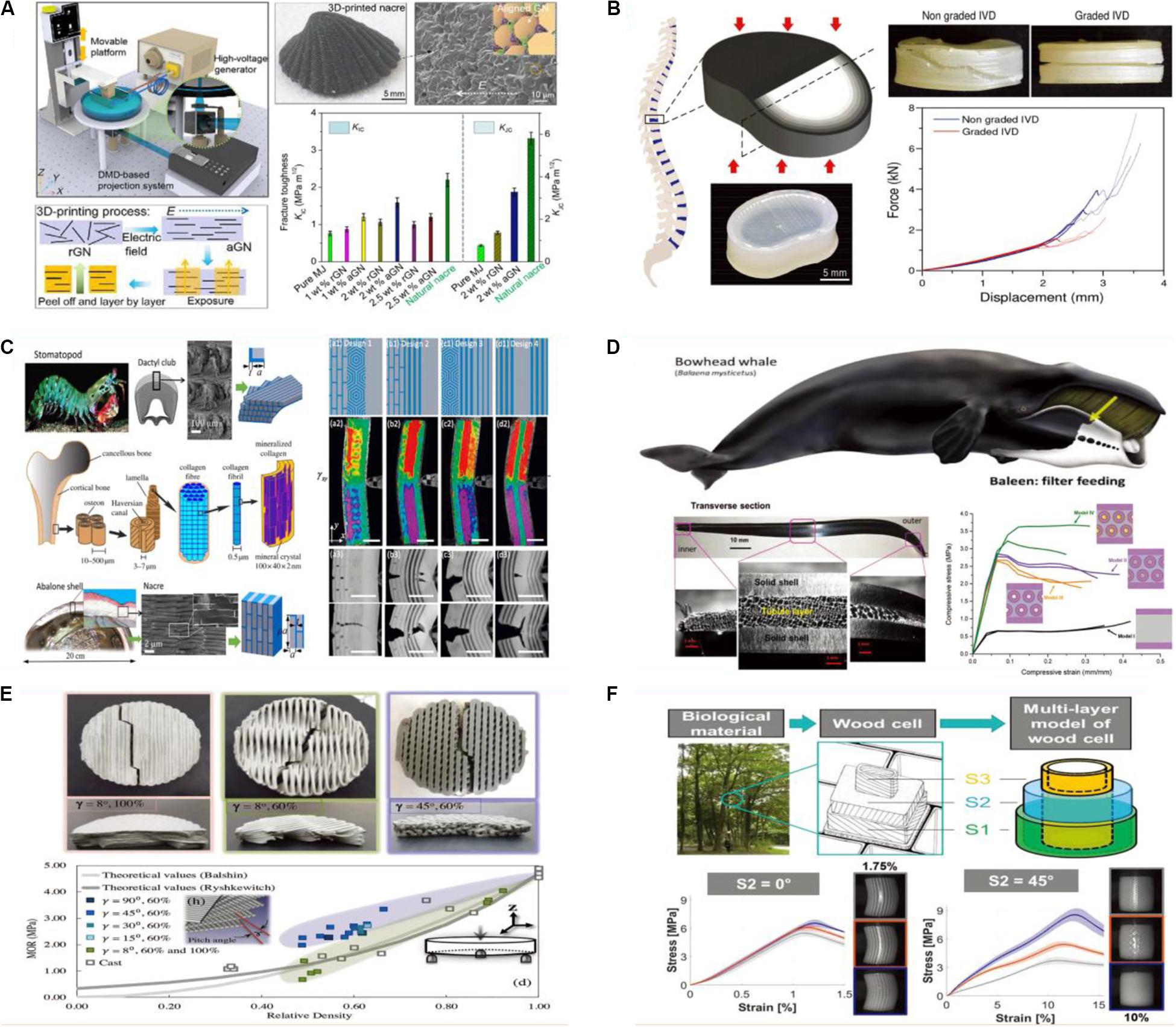
Figure 2. (A) The electrically assisted 3D printing of a nacre-inspired hierarchical structure with different mass ratios of GNs (Yang et al., 2019). Reproduced with the permission of the American Association for the Advancement of Science. (B) Graded inter-vertebral disc (IVD) and non-graded IVD, inspired by the human IVD after compression tests (Kokkinis et al., 2018). Reproduced with the permission of 2018 WILEY-VCH Verlag GmbH & Co. KGaA, Weinheim. (C) The controllable crack locations and crack patterns of hybrid biomimetic hierarchical structures, inspired by the microstructure of stomatopod, bone, and abalone shell (Jia et al., 2018). Reproduced with the permission of Elsevier Ltd. (D) Hierarchical structure models inspired by baleen (Wang et al., 2018). Reproduced with the permission of 2018 WILEY-VCH Verlag GmbH & Co. KGaA, Weinheim. (E) Cement-based material disks, based on Bouligand architectures (Moini et al., 2018). Reproduced with the permission of 2018 WILEY-VCH Verlag GmbH & Co. KGaA, Weinheim. (F) A three-layer cylindrical structure, inspired by wood (Zorzetto and Ruffoni, 2019). Reproduced with the permission of 2018 WILEY-VCH Verlag GmbH & Co. KGaA, Weinheim.
As shown in Figure 2E, based on Bouligand architectures, hardened cement paste elements with hierarchical and helical structures were fabricated by 3D printing technology (Moini et al., 2018). The damage mechanisms (including crack growth at the interfaces and interfacial microcracking) were systemically investigated, and the Bouligand architectures showed improvements of failure by more than 50%, exhibiting the controlled spread of damage without sacrificing the strength. In addition, the wood-inspired helical composites were manufactured by 3D multimaterial polyjet printing combined with computer simulations to investigate mechanical performance (Zorzetto and Ruffoni, 2019). The helicoidal biocomposites were arranged in multiple layers with different fiber orientations, and the results show that fibers with a helix angle greater than 0° allow the 3D-printed structures to effectively escape from buckling collapse by twisting. Consequently, the helicoidal biocomposites can reach a failure strain which is an order of magnitude larger (Figure 2F).
Cellular Structures
Cellular structures have high-porosity architectures that have potential applications as tough, lightweight components. Inspired by the microstructure of the grass stems of Elytrigia repens (Figure 3A), ultralight hierarchical and cellular graphene materials were fabricated by ink-based 3D printing technology (Peng et al., 2019). These compression test results show that ultralight hierarchical and cellular graphene materials can achieve ultrahigh elasticity and stability at compressive strains up to 95%, and Young’s modulus is threefold higher than conventional bulk superelastic materials with comparable geometric density. TiO2 foams with a hierarchical cellular structure have been fabricated by 3D printing technology (Arango et al., 2018). The foams were formed by trapping air bubbles in the emulsified hybrid TiO2/Ti-organic aqueous suspensions, and then directly written as planar, three-dimensional free-standing and spanning structures (Figure 3B). The curing of the foams was investigated using UV light, and the results show that the measured Brunauer–Emmett–Teller surface area for the open-cell (L75-S3-O22) foam is 46.094 cm2/g lower compared with a closed-cell (L75-S5.5-O19.5) foam with 49.556 cm2/g, which implies that the type of cellular architecture is important in specific applications, and indicates differences arising from the way light interacts with the ceramic scaffold and the methylene blue solution. Schwarzites are 3D porous solids with cellular structures, and possess unusual mechanical and electronic properties. As shown in Figure 3C, the mechanical behavior of 3D printed Schwarzites structures across different length scales have also been investigated (Sajadi et al., 2018). This study created 3D printed schwarzite structures composed of carbon and poly (lactic acid) filament with a 3 mm diameter. The deformation of a sphere- and peanut-like unit cell, exemplifies the benefits of Schwarzite structures, which have impact resistance and unique stress distribution that can be used to build high load-bearing and impact-resistant structures.
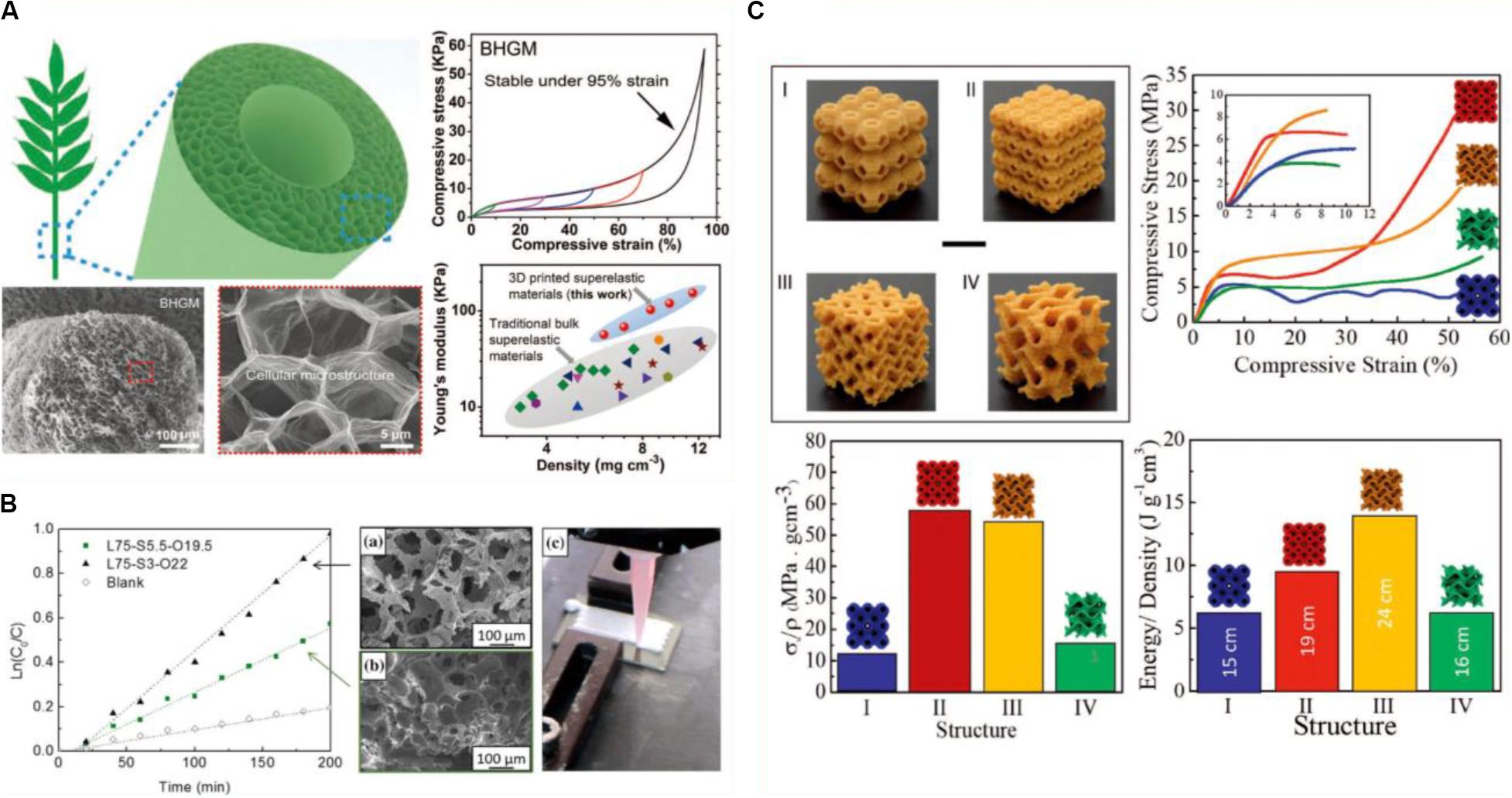
Figure 3. (A) Hierarchical and cellular graphene materials inspired by the grass stem of Elytrigia repens, via 3D printing (Peng et al., 2019). Reproduced with the permission of 2019 WILEY-VCH Verlag GmbH & Co. KGaA, Weinheim. (B) TiO2 foams with hierarchical cellular structure, fabricated by 3D printing (Arango et al., 2018). Reproduced with the permission of 2018 The Minerals, Metals & Materials Society. (C) 3D printed schwarzite structures across different length scales (Sajadi et al., 2018). Reproduced with the permission of 2017 WILEY-VCH Verlag GmbH & Co. KGaA, Weinheim.
Needle-Like Structures
Needle-like structures have typical insertion and friction characteristics and provide a source for biomimicry design that have potential applications in medicine. Bioinspired needles have been designed and fabricated by the Connex350 3D printer, to investigate the insertion performance in real tissues (Sahlabadi et al., 2017). As shown in Figure 4A, insertion tests into the bovine brain and liver were performed. The results from tests with proposed bioinspired needles show that there is a 10–25% decrease in the insertion force for insertions and a 35–45% reduction in the insertion force for insertions into the bovine liver. Surgical needles inspired by a bee sting have also been designed and 3D printed, to study insertion forces that could reduce tissue deformation (Sahlabadi and Hutapea, 2018). Needle insertion tests on tissue-mimicking polyvinyl chloride gel were performed (Figure 4B), and the results show that these bioinspired needles can decrease the insertion force by 24% and the tissue deformation by 17%. Inspired by the microstructure of wheat awn, other needle-like anisotropic polymer microactuators were manufactured by a modified magnetically assisted stereolithography 3D printing technology (Ma et al., 2019), as shown in Figure 4C. The photosensitive resins are a mixture of clear resin and flexible resin in a ratio of 3:2, and the sieved short steel fibers (SSFs) with an average aspect ratio of 168, were added into the matrix in the mass/volume ratio 2:5. The effects of these geometric parameters on the anisotropy friction generated by needle-like microactuators were systematically investigated, and the maximum frictional anisotropy achieved had a tilting angle set 60/30. This research provides an understanding of anisotropic friction for developing intelligent actuators.
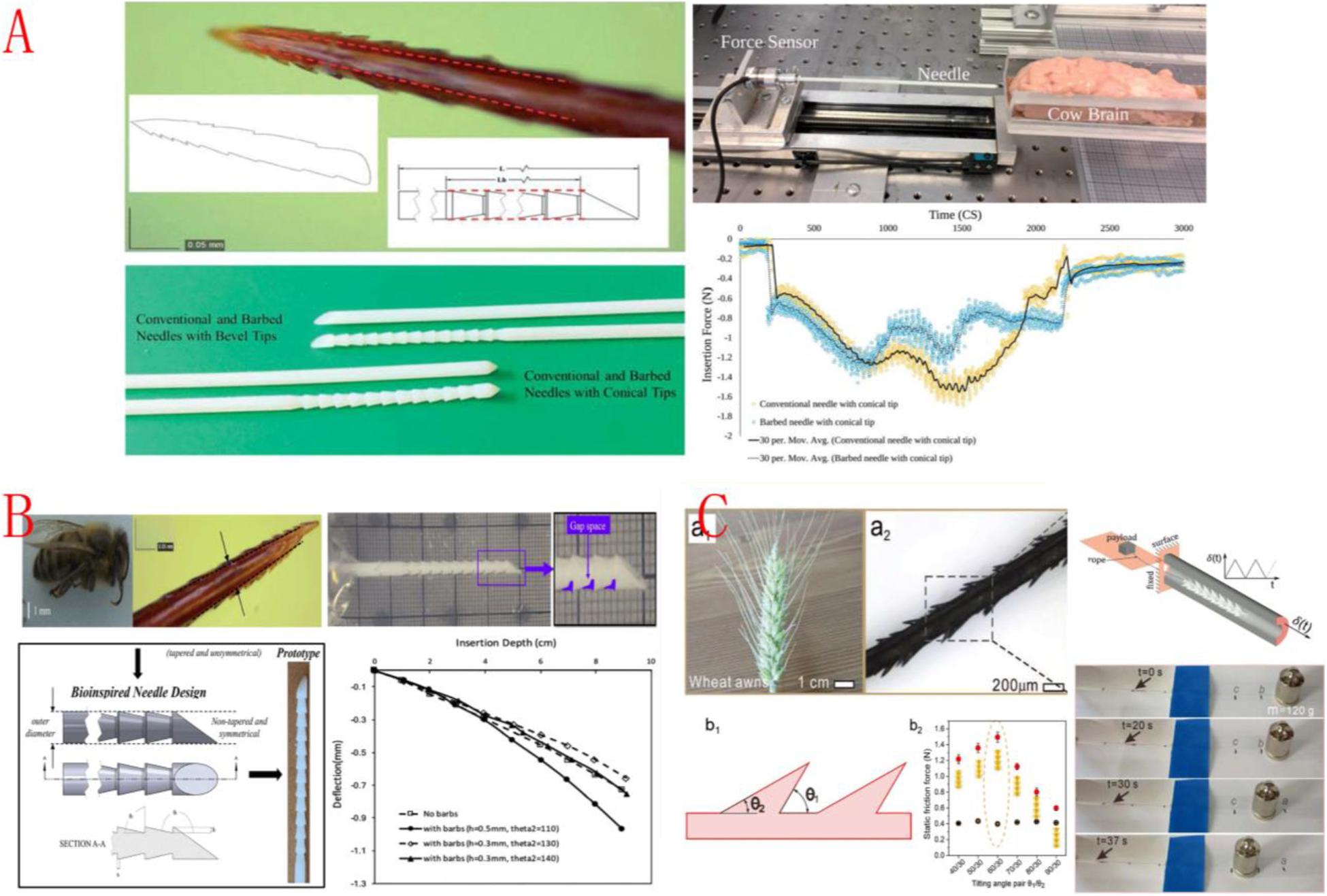
Figure 4. (A) 3D bioinspired needles with specially designed barbs for decreasing insertion force (Sahlabadi et al., 2017). Reproduced with the permission of the Society of Medical Innovation and Technology, 2017. (B) Stinger needles, inspired by honeybee for decreasing tissue damage (Sahlabadi et al., 2017). Reproduced with the permission of 2018 by ASME. (C) 3D printed needle-like anisotropic polymer microactuators, inspired by the microstructure of wheat awn (Ma et al., 2019). Reproduced with the permission of 2018 WILEY-VCH Verlag GmbH & Co. KGaA, Weinheim.
3D Printing of Bioinspired Functional Structures
Apart from the excellent mechanical properties of many geometrical structures in nature, species with typical functional structures have interesting properties such as liquid super-repellent, super-wettability, shape memory, and shape-changing. These have potential applications in the design and fabrication of high-performance structures. Examples of functional surface, finer-reinforced, and shape-changing structures are reviewed in this section.
Surface Structures
Various surface structures in nature possess typical properties, such as super-repellent abilities and friction. Inspired by Folsomia candida, triply re-entrant structures that possess super-repellence to water and various organic liquids, were fabricated via the newly developed direct laser writing technology: a two-photon polymerization based 3D printing technology (Liu et al., 2018) shown in Figure 5A. Anti-penetration and the anti-adhesion behaviors can be controlled through the precise adjustment of the diameter of the cover, and the center-to-center distance between the microstructures. These microstructures are fabricated on substrates to ensure electrical conductivity and directional liquid flow, with potential applications in electronic devices, high-throughput biological sensors, and optical displays. Mimicking the hook-like features of the filefish skin surface (Figure 5B), friction anisotropic surfaces with oriented micro-/nanostructures were fabricated by Polydimethylsiloxane (SYLGARD 184) with Young’s modulus of ∼2 MPa, using a digital light processing 3D printing technology (Ji et al., 2018). A systematic investigation of the friction behavior embedded samples with hook-like spines into a flexible supporting layer with different thicknesses, densities, and abilities to bend. The anisotropy of the friction force of the different 3D printed engineering surfaces led to directional driving performance under external stretch or vibration, which has potential applications in directional actuation, intelligent sensors, and particular tribological systems. Li et al. (2019b) developed a low-cost 3D printing technology (multiscale SLA) to print a macroscale object with microscale surface structures inspired by shark skin and lotus leaf, as shown in Figure 5C. The optical filter can modify laser spot size for lasers with different wavelengths to achieve a maximum resolution of 37 μm, which has the potential to serve as a powerful tool that can bring bioinspired structures into real-life applications.
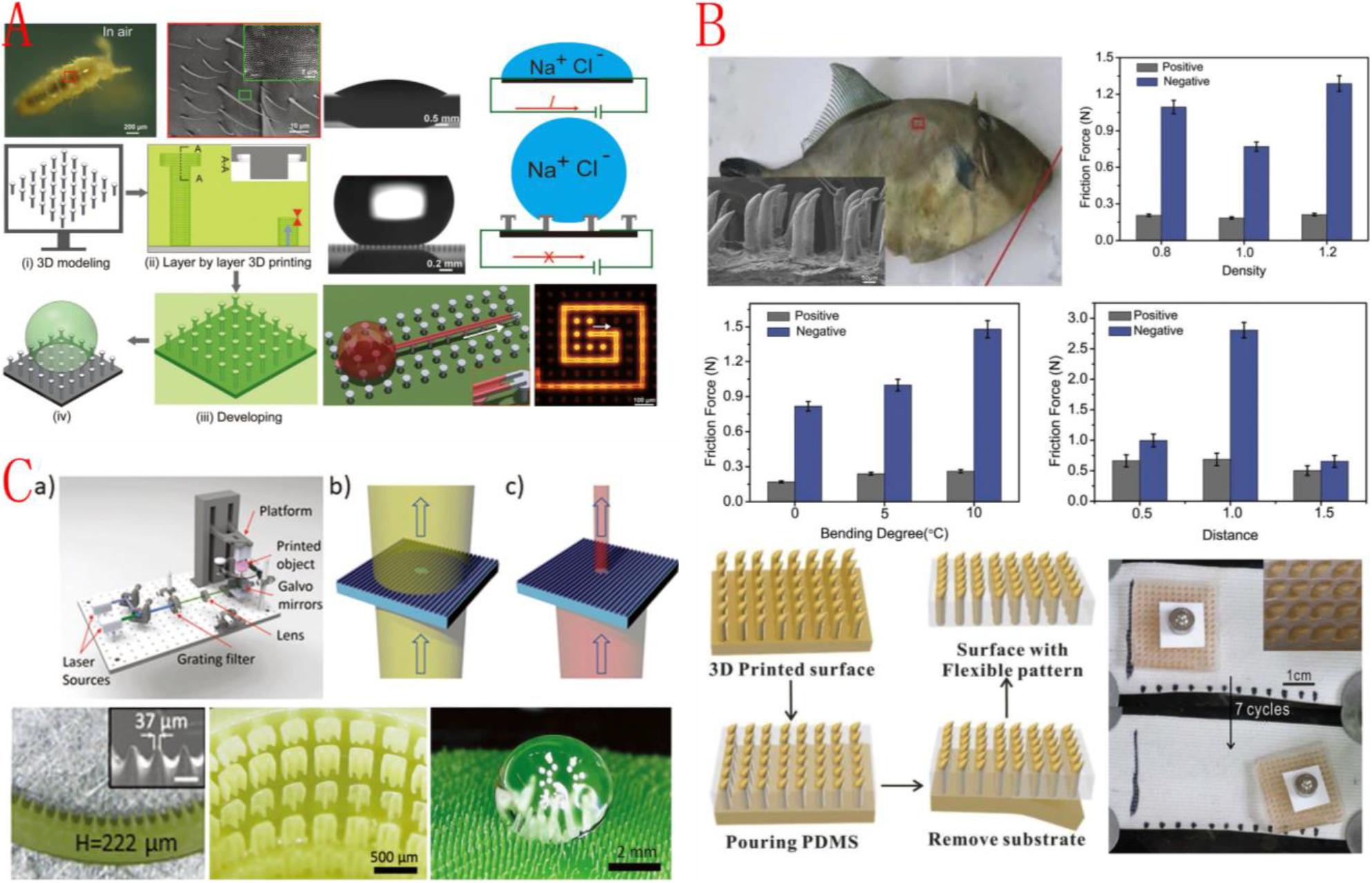
Figure 5. (A) Triply re-entrant structures inspired by Folsomia candida, fabricated via two-photon polymerization based 3D printing technology (Liu et al., 2018). Reproduced with the permission of 2018 WILEY-VCH Verlag GmbH & Co. KGaA, Weinheim. (B) 3D printed friction anisotropic surfaces, inspired by the surface structures of the Filefish skin (Ji et al., 2018). Reproduced with the permission of 2018 Elsevier Ltd. (C) Low-cost multiscale stereolithography technology, used to print a macroscale object with microscale surface structures, inspired by shark skins and lotus leaf (Li et al., 2019b). Reproduced with the permission of 2019 WILEY-VCH Verlag GmbH & Co. KGaA, Weinheim.
Fiber-Reinforced Structures
Fiber is a crucial element in bioinspired composite materials. Fiber-reinforced materials and structures have excellent mechanical performance. The slurry-based SLA 3D printing technique, shown in Figure 6A, is based on a shear-induced fiber orientation process that was developed to fabricate fiber-reinforced structures (Ren et al., 2019a). This investigated the influence of relative factors on fiber orientation, fabricating fiber-reinforced line, sinusoidal, and zigzag structures to study their mechanical properties. The results showed that the bioinspired zigzag designs and bioinspired sinusoidal-architected designs have a relative higher impact energy, and Young’s modulus compared to other patterns with the same fiber aspect ratio and fiber volume fraction. Additionally, Ren et al. (2019b) fabricated structural gradient shape memory composites with fibers inspired by the microstructure of wheat awn and softwood branches via modified magnetically assisted SLA 3D printing technology, shown in Figure 6B. This investigated the underlying formation mechanism of gradient shape memory properties for bioinspired composites with fibers, indicating the potential of fabricating soft actuators with gradient and continuous locomotion. Inspired by natural composites with complex fiber arrangements within continuous matrices, a rotational 3D printing method was developed to spatially control the orientation of short fibers in polymer matrices, including brittle and flexible epoxy resins (Raney et al., 2018). As shown in Figure 6C, by varying the nozzle rotation speed relative to the printing speed, the fiber-reinforced composites with programmable strain distribution and failure as well as enhanced damage tolerance, can be fabricated. The fiber-reinforced composites printed with rotation are able to withstand much higher puncture forces before catastrophic failure, compared with those printed without rotation.
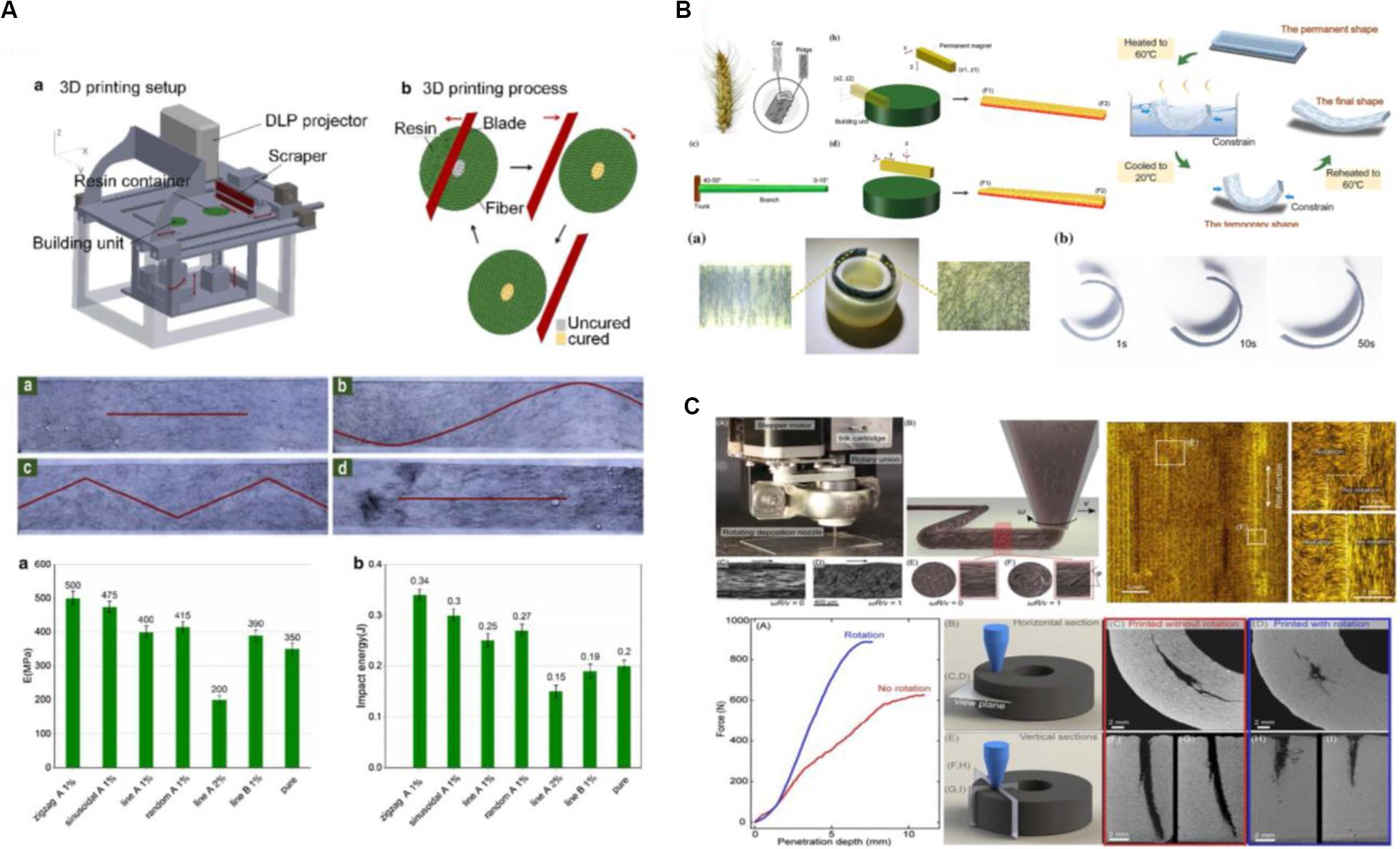
Figure 6. (A) Fiber-reinforced composites, fabricated by a slurry-based stereolithography 3D printing technique (Ren et al., 2019a). Reproduced with the permission of the Korean Society for Precision Engineering 2019. (B) Structural gradient shape memory composites with fibers inspired by the microstructure of wheat awn and softwood branches (Ren et al., 2019b). Reproduced with the permission of Springer Science + Business Media, LLC, part of Springer Nature 2019. (C) Fiber-reinforced composites fabricated by a rotational 3D printing method (Raney et al., 2018). Reproduced with the permission of PNAS.
Shape-Changing Structures
Many species in nature can change their shapes in response to external stimuli such as heat, moisture, light, and electricity. Various bioinspired shape-changing materials and structures have been proposed and developed. As shown in Figure 7A, the temperature-responsive linear hydrogel was used to fabricate bioinspired shape-changing structures via DIW technology (Arslan et al., 2018). These shape-changing structures can realize programmed motions, such as twisting, bending, and other complex motions, which show the potential to fabricate soft devices. The bioinspired shape-changing structures were fabricated by DIW technology using the composites of an active thermally responsive swelling gel and a passive thermally non-responsive gel (Liu et al., 2019a). By changing the environmental temperature, a variety of shape changes including uniaxial elongation, radial expansion, bending, and gripping can be realized by the fabricated structures, seen in Figure 7B. Similarly, inspired by the swelling and elastic properties of cacti and euphorbias, a shape-changing tube structure was designed and 3D printed using soft swellable poly N-isopropylacrylamide and stiff non-swellable polyacrylamide (Liu et al., 2019b), pictured in Figure 7C. The shape of the tube structure was also affected by the environmental temperature. In Figure 7D, digital light 4D printing technology was adopted to fabricate the bioinspired 3D shape-changing structures, which uses temperature-responsive hydrogels with locally programmable degrees and rates of swelling and shrinking (Nojoomi et al., 2018). These fabricated 3D shape-changing structures can achieve programmable morphologies and motions, which potentially pave the way for designing and fabricating soft engineering systems, for use in soft robots, actuators, and artificial muscles.
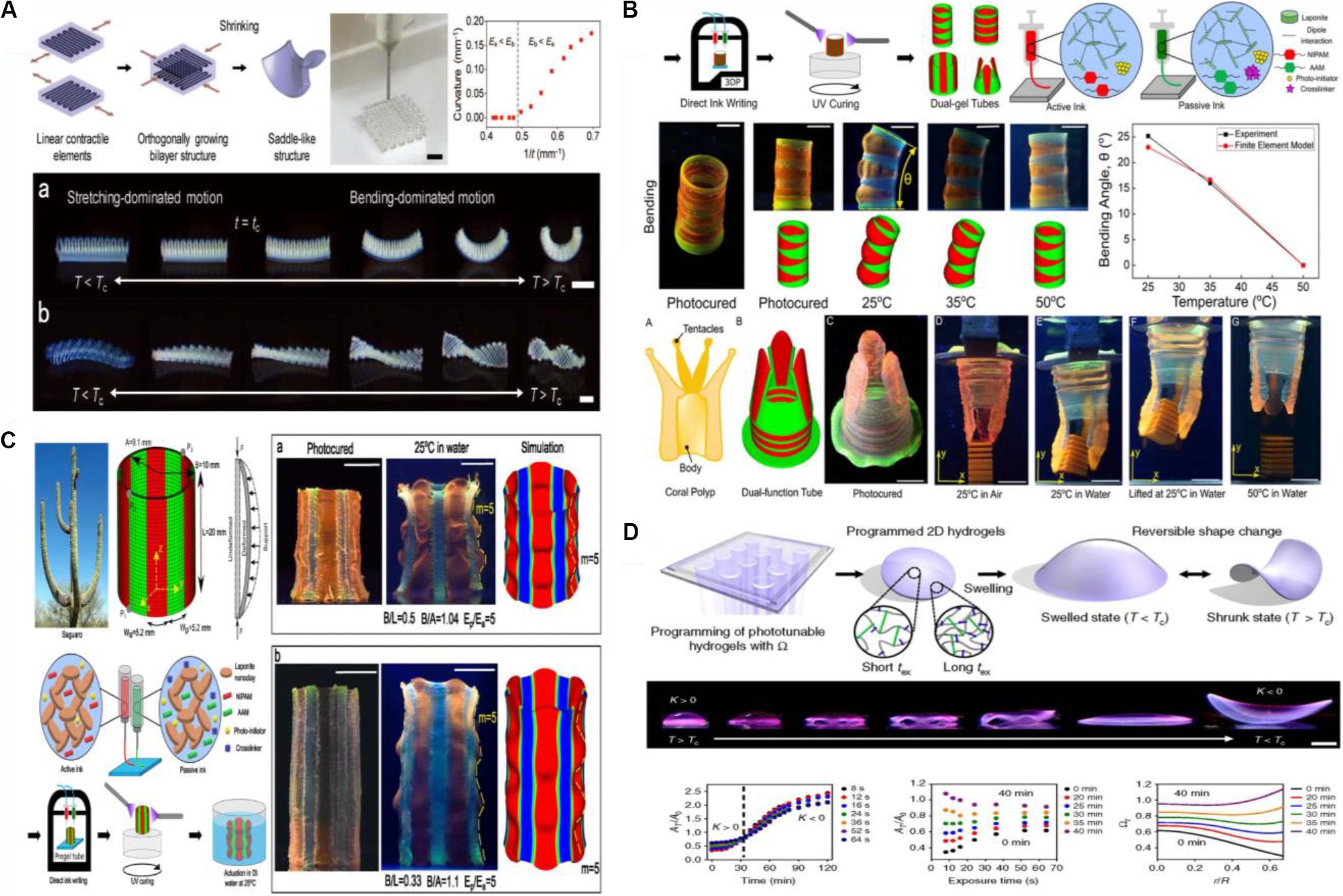
Figure 7. Heat-induced shape-changing structures fabricated by 3D printing technology. (A) Bioinspired shape-changing structures fabricated by temperature-responsive linear hydrogel (Arslan et al., 2018). Reproduced with the permission of WILEY-VCH Verlag GmbH & Co. KGaA, Weinheim. (B,C) Bioinspired shape-changing tube structures fabricated by soft swellable poly N-isopropylacrylamide and stiff non-swellable polyacrylamide (Liu et al., 2019a,b). Reproduced with the permission of the American Chemical Society, 2019 Elsevier Ltd. (D) Bioinspired 3D shape-changing structures with programmable morphologies and motions (Nojoomi et al., 2018). Reproduced with the permission of Nature Communications.
Except for heat-induced deformable structures, other bioinspired shape-changing structures, shown in Figure 8A. these structures were inspired by multilamellar fiber architecture and the functional principles of an elephant trunk. The soft actuators were fabricated by the multimaterial DIW process using pneumatic silicones (Schaffner et al., 2018). The surface of bioinspired actuators was decorated with reinforcing stripes at a well-defined lead angle, which can be altered to achieve elongation, contraction, or twisting motions. In addition, soft somatosensitive actuators with multiple conductive features were fabricated by embedded DIW technology (Truby et al., 2017). As shown in Figure 8B, this embedded DIW enables the seamless integration of multiple ionically conductive and fluidic features within elastomeric matrices to produce actuators with the bioinspired sensing and actuation capabilities that can potentially be applied in soft robotic, wearable, and haptic devices. A novel bioinspired joint system, consisting of dissimilar materials with high strength and high strain elements, was fabricated by using directly extruding and writing technologies (Hamidi and Tadesse, 2018). The joint consists of continuous metal fibers and reinforced thermoplastic parts that resemble bones and soft elastomer to mimic soft tissues (Figure 8C), with high mechanical strength and elasticity. Similarly, inspired by the natural structure of the musculoskeletal system, a twisted and coiled artificial muscle was designed and fabricated by 3D printing technology (Wu et al., 2018), as shown in Figure 8D. The artificial muscle is made by twisting a nylon 6 fishing line precursor fiber and wrapping a very thin resistance wire around it, meaning it has remarkable tensile and bending motions. This has great potential in the development of soft robots. The magnetism-induced shape-changing structures were 3D printed using the cellularized anisotropic hybrid hydrogel which is fabricated through a mild and biocompatible process driven by multiple external stimuli, including magnetic field, temperature, and light (Tognato et al., 2019). As shown in Figure 8E, the 3D-printed starfish soft robot can realize swimming and wrapping motions under the guidance of magnetic fields. Inspired by the moisture induced deformation of the pine cone, the electrically driven paper-based bilayer actuator is fabricated by a simple and scalable screen-printing method (Hu et al., 2019), as shown in Figure 8F. In the paper-based actuator, the polymer and silver nanoparticles are the deformation active units and energy conversion components, respectively. Paper-based actuators can construct various bioinspired motions, which provide new perspectives on multifunctional smart robots and biomimetic devices.
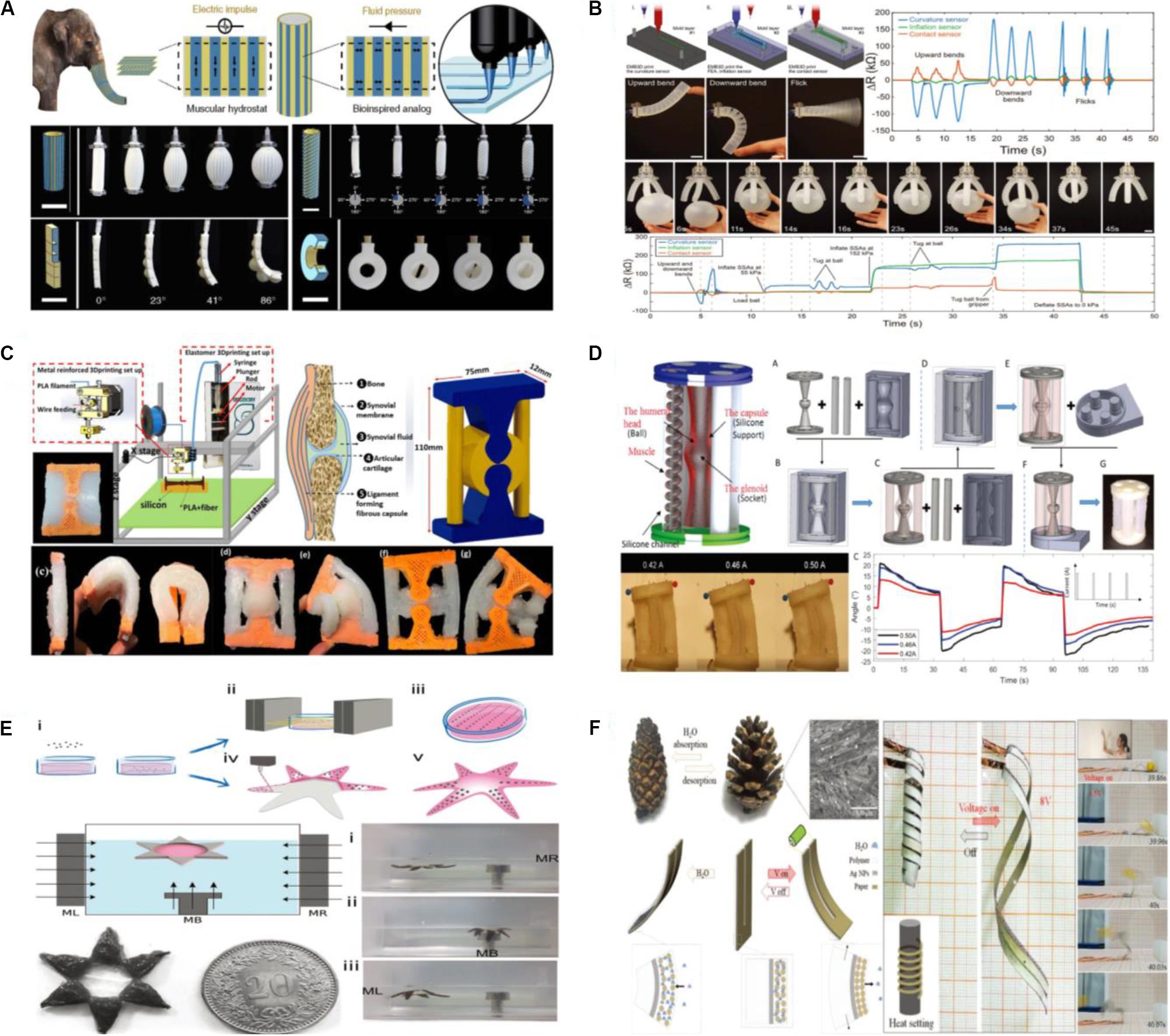
Figure 8. (A) Soft actuators inspired by multilamellar fiber architecture and functional principle of the elephant trunk (Schaffner et al., 2018). Reproduced with the permission of Nature Communications. (B) Soft somatosensitive actuators with multiple conductive features fabricated by embedded 3D printing technology (Truby et al., 2017). Reproduced with the permission of 2018 WILEY-VCH Verlag GmbH & Co. KGaA, Weinheim. (C,D) Bioinspired joint system and musculoskeletal system (Hamidi and Tadesse, 2018; Wu et al., 2018). Reproduced with the permission of 208 Elsevier Ltd, 2018 WILEY-VCH Verlag GmbH & Co. KGaA, Weinheim. (E) Magnetism-induced shape-changing structures (Tognato et al., 2019). Reproduced with the permission of 2018 WILEY-VCH Verlag GmbH & Co. KGaA, Weinheim. (F) Electrically driven paper-based bilayer actuator (Hu et al., 2019). Reproduced with the permission of 2019 WILEY-VCH Verlag GmbH & Co. KGaA, Weinheim.
Summary
Over millions of years of evolution, nature has evolved structures with relatively optimal properties. These provide researchers with valuable and useful inspiration along with tried-and-tested methods for developing high-performance materials and structures. Although traditional manufacturing technologies cannot be used to fabricate these complex structures, 3D printing can fabricate structures with arbitrary geometry. Combining biomimicry with 3D printing technology, materials, and structures with reinforced physical properties have been fabricated for various engineering applications, some of which have been explored in this paper, which has reviewed recent developments in bioinspired 3D printing.
Outlook
Although some high-performance bioinspired materials and structures have been successfully fabricated by 3D printing, there are still many unaddressed challenges and limits to the applications of biomimicry. For example, the tradeoff between high resolution, low cost, and high speed. This is due to the fact that increasing the resolution of bioinspired structures also increases cost whilst decreasing the manufacturing speed. The fabrication of multiscale structures from the nanoscale to macroscale is a challenge as to the best of our best knowledge, no methods for this type of fabrication currently exist. Additionally, bioinspired structures with multimaterial or composite materials have typical properties and functions, and it is difficult to anticipate the effects of using different interface materials. The process of clarifying the synthesis mechanisms of different materials is another challenge in fabricating high-performance bioinspired materials and structures.
Considering these challenges, it is anticipated that future developments in bioinspired 3D printing will focus on multimaterial, multiscale, multifunctional, high-efficiency, and low-cost fabrication. For multimaterial fabrication, the synthesis mechanism of different materials will be investigated and clarified to guide 3D printing. In terms of multiscale fabrication, novel 3D printing technology will be proposed to realize continuous fabrication from nanoscale to macroscale. Bioinspired materials and structures with multifunctional properties, including reinforced mechanical, electrical, electromagnetic, optical, chemical properties, will be the research hotspots. In addition, developing high-efficiency and low-cost fabrication technologies will be an effective way to accelerate the development and application of biomimetic 3D printing technology.
Author Contributions
All authors conceived the structure, wrote and reviewed the manuscript.
Funding
Supported by Innovation-Driven Project of Central South University (No. 2020CX004).
Conflict of Interest
The authors declare that the research was conducted in the absence of any commercial or financial relationships that could be construed as a potential conflict of interest.
Acknowledgments
We gratefully appreciate the assistance of Dr. Chunlong Fei, who provided valuable discussion.
References
Arango, T. M. A., Morris, N. J., and Sierros, K. A. (2018). Direct writing and controlling of hierarchical functional metal-oxides: bio-inspired multiphase processing, 3D printing and hierarchical cellular structuring. JOM 70, 1823–1829. doi: 10.1007/s11837-018-3002-1
Arslan, H., Nojoomi, A., Jeon, J., and Yum, K. (2018). 3D printing of anisotropic hydrogels with bioinspired motion. Adv. Sci. 6. doi: 10.1002/advs.201800703
Du Plessis, A., Broeckhoven, C., Yadroitsava, I., Yadroitsev, I., Hands, C. H., Kunju, R., et al. (2019). Beautiful and functional: a review of biomimetic design in additive manufacturing. Addit. Manufact. 27, 408–427. doi: 10.1016/j.addma.2019.03.033
Haleem, A., and Javaid, M. (2018). Additive manufacturing applications in industry 4.0: a review. J. Ind. Integr. Manag. 8, 3–8. doi: 10.1142/S2424862219300011
Hamidi, A., and Tadesse, Y. (2018). Single step 3D printing of bioinspired structures via metal reinforced thermoplastic and highly stretchable elastomer. Compos. Struct. 210, 250–261. doi: 10.1016/j.compstruct.2018.11.019
Hu, Y., Xu, A., Liu, J., Yang, L., Chang, L., Huang, M., et al. (2019). Multifunctional soft actuators based on anisotropic paper/polymer bilayer toward bioinspired applications. Adv. Mater. Technol. 4:1800674. doi: 10.1002/admt.201800674
Ji, Z., Yan, C., Ma, S., Gorb, S., Jia, X., Yu, B., et al. (2018). 3D printing of bioinspired topographically oriented surfaces with frictional anisotropy for directional driving. Tribol. Int. 132, 99–107. doi: 10.1016/j.triboint.2018.12.010
Jia, Z., Yu, Y., Hou, S., and Wang, L. (2018). Biomimetic architected materials with improved dynamic performance. J. Mech. Phys. Solid 125, 178–197. doi: 10.1016/j.jmps.2018.12.015
Kokkinis, D., Bouville, F., and Studart, A. R. (2018). 3D Printing of Materials with Tunable Failure via Bioinspired Mechanical Gradients. Adv. Mater. 30:e1705808. doi: 10.1002/adma.201705808
Kong, T., Luo, G., Zhao, Y., and Liu, Z. (2019). Bioinspired superwettability micro/nanoarchitectures: fabrications and applications. Adv. Funct. Mater. 29:1808012. doi: 10.1002/adfm.201808012
Li, Q., Zhang, J., Li, Q., Li, G., Tian, X., Luo, Z., et al. (2019a). Review of printed electrodes for flexible devices. Front. Mater. 5:77. doi: 10.3389/fmats.2018.00077
Li, Y., Mao, H., Hu, P., Hermes, M., Lim, H., Yoon, J., et al. (2019b). Bioinspired functional surfaces enabled by multiscale stereolithography. Adv. Mater. Technol. 4:1800638. doi: 10.1002/admt.201800638
Liu, H. L., Li, M., Zhu, M., Huang, Y., Tang, Z., Pei, Z., et al. (2017). Towards wearable electronic devices: a quasi-solid-state aqueous lithium-ion battery with outstanding stability, flexibility, safety and breathability. Nano Energy 44, 164–173. doi: 10.1016/j.nanoen.2017.12.006
Liu, J., Erol, O., Pantula, A., Liu, W., Jiang, Z., Kobayashi, K., et al. (2019a). Dual-Gel 4D Printing of Bioinspired Tubes. ACS Appl. Mater. Interfaces 11, 8492–8498. doi: 10.1021/acsami.8b17218
Liu, J., Liu, W., Pantula, A., Wang, Z., Gracias, D. H., and Nguyen, T. D. (2019b). Periodic buckling of soft 3D printed bioinspired tubes. Extreme Mech. Lett. 30:100514. doi: 10.1016/j.eml.2019.100514
Liu, X., Gu, H., Wang, M., Du, X., Gao, B., Elbaz, A., et al. (2018). 3D printing of bioinspired liquid superrepellent structures. Adv. Mater. 30:1800103. doi: 10.1002/adma.201800103
Ma, S., Scaraggi, M., Yan, C., Wang, X., Gorb, S. N., Dini, D., et al. (2019). Bioinspired 3D printed locomotion devices based on anisotropic friction. Small 15:1970005. doi: 10.1002/smll.201802931
Mi, S., Du, Z., Xu, Y., and Sun, W. (2018). The crossing and integration between microfluidic technology and 3D printing for organ-on-chips. J. Mater. Chem. B 6, 6191–6206. doi: 10.1039/c8tb01661e
Moini, M., Olek, J., Youngblood, J. P., Magee, B., and Zavattieri, P. D. (2018). Additive manufacturing and performance of architectured cement-based materials. Adv. Mater. 30, e1802123. doi: 10.1002/adma.201802123
Nazir, A., Abate, K. M., Kumar, A., and Jeng, J.-Y. (2019). A state-of-the-art review on types, design, optimization, and additive manufacturing of cellular structures. Int. J. Adv. Manuf. Technol. 104, 3489–3510. doi: 10.1007/s00170-019-04085-3
Nojoomi, A., Arslan, H., Lee, K., and Yum, K. (2018). Bioinspired 3D structures with programmable morphologies and motions. Nat. Commun. 9:3705. doi: 10.1038/s41467-018-05569-8
Peng, M., Wen, Z., Xie, L., Cheng, J., Jia, Z., Shi, D., et al. (2019). 3D printing of ultralight biomimetic hierarchical graphene materials with exceptional stiffness and resilience. Adv. Mater. 31:e1902930. doi: 10.1002/adma.201902930
Raney, J. R., Compton, B. G., Mueller, J., Ober, T. J., Shea, K., and Lewis, J. A. (2018). Rotational 3D printing of damage-tolerant composites with programmable mechanics. Proc. Natl. Acad. Sci. U.S.A. 115, 1198–1203. doi: 10.1073/pnas.1715157115
Ren, L., Li, B., Song, Z., Liu, Q., Ren, L., and Zhou, X. (2019a). 3D printing of bioinspired structural materials with fibers induced by doctor blading process. Int. J. Precis. Eng. Manuf. Green Technol. 6, 89–99. doi: 10.1007/s40684-019-00030-7
Ren, L., Li, B., Song, Z., Liu, Q., Ren, L., and Zhou, X. (2019b). 3D printing of structural gradient soft actuators by variation of bioinspired architectures. J. Mater. Sci. 54, 6542–6551. doi: 10.1007/s10853-019-03344-8
Saha, S. K., Wang, D., Nguyen, V. H., Chang, Y., Oakdale, J. S., and Chen, S.-C. (2019). Scalable submicrometer additive manufacturing. Science 366, 105–109. doi: 10.1126/science.aax8760
Sahlabadi, M., and Hutapea, P. (2018). Tissue deformation and insertion force of bee-stinger inspired surgical needles. J. Med. Devices 12:034501. doi: 10.1115/1.4040637
Sahlabadi, M., Khodaei, S., Jezler, K., and Hutapea, P. (2017). Insertion mechanics of bioinspired needles into soft tissues. Minim. Invasive Ther. Allied Technol. 27, 284–291. doi: 10.1080/13645706.2017.1418753
Sajadi, S. M., Owuor, P. S., Schara, S., Woellner, C. F., Rodrigues, V., Vajtai, R., et al. (2018). Multiscale geometric design principles applied to 3D printed schwarzites. Adv. Mater. 30:1704820. doi: 10.1002/adma.201704820
Saratti, C. M., Rocca, G. T., and Krejci, I. (2018). The potential of three-dimensional printing technologies to unlock the development of new “bio-inspired” dental materials: an overview and research roadmap. J. Prosthodont. Res. 63, 131–139. doi: 10.1016/j.jpor.2018.10.005
Schaffner, M., Faber, J. A., Pianegonda, L., Ruhs, P. A., Coulter, F., and Studart, A. R. (2018). 3D printing of robotic soft actuators with programmable bioinspired architectures. Nat. Commun. 9:878. doi: 10.1038/s41467-018-03216-w
Spadaccini, C. M. (2019). Additive manufacturing and processing of architected materials. MRS Bulletin 44, 782–788. doi: 10.1557/mrs.2019.234
Tognato, R., Armiento, A. R., Bonfrate, V., Levato, R., Malda, J., Alini, M., et al. (2019). A stimuli-responsive nanocomposite for 3D anisotropic cell-guidance and magnetic soft robotics. Adv. Funct. Mater. 29:1804647. doi: 10.1002/adfm.201804647
Truby, R. L., Wehner, M., Grosskopf, A. K., Vogt, D. M., Uzel, S. G. M., Wood, R. J., et al. (2017). Soft somatosensitive actuators via embedded 3D printing. Adv. Mater. 30:e1706383. doi: 10.1002/adma.201706383
Velasco-Hogan, A., Xu, J., and Meyers, M. A. (2018). Additive manufacturing as a method to design and optimize bioinspired structures. Adv. Mater. 30:e1800940. doi: 10.1002/adma.201800940
Wang, B., Sullivan, T. N., Pissarenko, A., Zaheri, A., Espinosa, H. D., and Meyers, M. A. (2018). Lessons from the Ocean: Whale baleen fracture resistance. Adv. Mater. 31:1804574. doi: 10.1002/adma.201804574
Wu, L., Chauhan, I., and Tadesse, Y. (2018). A novel soft actuator for the musculoskeletal system. Adv. Mater. Technol. 3:1700359. doi: 10.1002/admt.201700359
Yan, C., Jiang, P., Jia, X., and Wang, X. (2020). 3D printing of bioinspired textured surfaces with superamphiphobicity. Nanoscale 12, 2924–2938. doi: 10.1039/c9nr09620e
Yang, Y., Li, X., Chu, M., Sun, H., Jin, J., Yu, K., et al. (2019). Electrically assisted 3D printing of nacre-inspired structures with self-sensing capability. Sic. Adv. 5:eaau9490.
Yang, Y., Song, X., Li, X., Chen, Z., Zhou, C., Zhou, Q., et al. (2018). Recent progress in biomimetic additive manufacturing technology: from materials to functional structures. Adv. Mater. 30:e1706539. doi: 10.1002/adma.201706539
Keywords: 3D printing, bioinspired structures, hierarchical structures, cellular structures, fiber-reinforced structures, shape-changing structures
Citation: Wang D, Chen D and Chen Z (2020) Recent Progress in 3D Printing of Bioinspired Structures. Front. Mater. 7:286. doi: 10.3389/fmats.2020.00286
Received: 28 January 2020; Accepted: 29 July 2020;
Published: 06 November 2020.
Edited by:
Yang Yang, San Diego State University, United StatesReviewed by:
Leire Ruiz Rubio, University of the Basque Country, SpainKalappa Prashantha, Adichunchanagiri University, India
Copyright © 2020 Wang, Chen and Chen. This is an open-access article distributed under the terms of the Creative Commons Attribution License (CC BY). The use, distribution or reproduction in other forums is permitted, provided the original author(s) and the copyright owner(s) are credited and that the original publication in this journal is cited, in accordance with accepted academic practice. No use, distribution or reproduction is permitted which does not comply with these terms.
*Correspondence: Zeyu Chen, emV5dWNoZW5AY3N1LmVkdS5jbg==
†These authors have contributed equally to this work