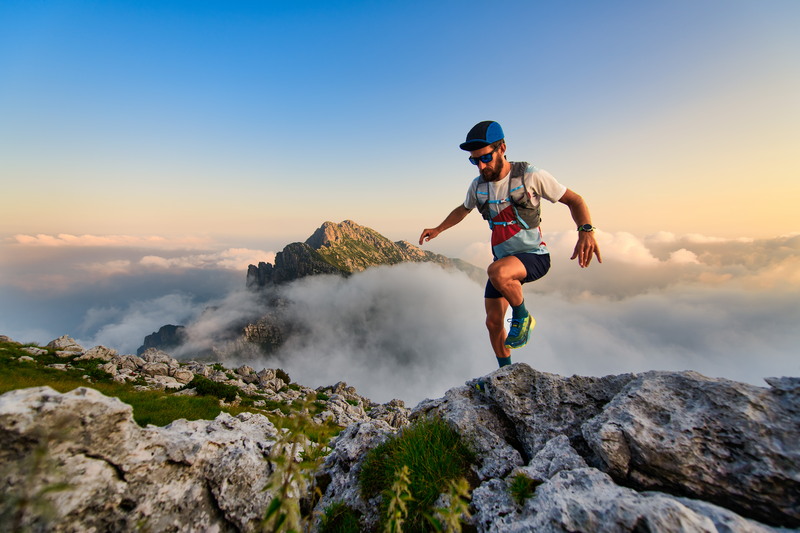
95% of researchers rate our articles as excellent or good
Learn more about the work of our research integrity team to safeguard the quality of each article we publish.
Find out more
MINI REVIEW article
Front. Mater. , 24 April 2020
Sec. Energy Materials
Volume 7 - 2020 | https://doi.org/10.3389/fmats.2020.00096
This article is part of the Research Topic Chemistry, Synthesis, and Interaction of Advanced Electrolyte Materials for High-Energy-Density Batteries View all 8 articles
Zn is an important negative electrode material in our battery industry and next-generation Zn based batteries are prospective to compete with lithium-ion batteries on cost and energy density. Corrosion is a severe challenge facing Zn electrodes, which can decrease the capacity, cyclability, and shelf life of batteries. More attention should be paid to Zn electrode corrosion in developing rechargeable and high energy density Zn batteries. In this mini review, the fundamental electrochemical behavior and corrosion of Zn electrodes in aqueous environment are retrospected. Then main strategies in recent studies to mitigate Zn electrode corrosion including electrolyte additives usage, electrode composition design and electrode morphology modification are reviewed.
Developing advanced batteries is crucial for energy storage and application in the modern society (Fan et al., 2019b; Lin et al., 2019). Zn as an anode material is inexpensive, safe, environmentally friendly, easy to recycle, and of high energy density. Due to these merits, it has been successfully used in various systems including Zn-Carbon battery, alkaline Zn-MnO2 battery, Zn-Ag battery, and primary Zn-air battery. Even after the tremendous success of lithium-ion battery (LIB) during the past decades, the Zn based batteries still keep a considerable market share in the whole battery industry and developing novel Zn batteries is a research focus (Reddy, 2010; Chao et al., 2019; Liu X. et al., 2019). Another important feature of Zn is the electrochemical reversibility in aqueous environments, making it possible to manufacture secondary Zn batteries. Investigators are trying to develop next generation rechargeable Zn based batteries such as Zn-Ni, Zn-air and Zn-ion batteries, which are promising to compete with LIB on energy density and cost in the future.
Corrosion is an important problem that influences many aspects of industry and our daily life (Zhang et al., 2017; Sun et al., 2018; Wang et al., 2019). It also affects the service life of electrodes in batteries, especially in certain conditions (Zhang, 2008). In order to enhance the energy density of Zn batteries, it is crucial to adopt Zn electrodes with high specific surface area rather than simply utilizing Zn foil or Zn plate electrodes (Parker et al., 2018; Stock et al., 2019; Zhao et al., 2019). In this case, the corrosion rate of Zn electrode would increase. This self-discharge phenomenon of Zn electrode would shorten the service life and storage life of Zn batteries (Sun et al., 2019).
Zn is applied in many aspects of the industry and our daily life. Apart from utilized as anode material, another significant application of Zn is cathodic protection for iron. Accordingly, the corrosion behavior and the electrochemistry of Zn in aqueous environment have been extensively investigated. However, the corrosion of Zn electrodes is influenced by so many factors such as Zn electrode morphology, additives, electrolyte composition, concentration, and pH value, as well as the operation conditions of the battery (Zhang, 2008; Li et al., 2019). There are still many fundamental corrosion mechanisms to be clarified. Particularly, as the advanced porous Zn electrodes and novel electrolytes increasingly being applied in the next generation rechargeable batteries (Parker et al., 2017; Liu P. et al., 2019; Stock et al., 2019), more attention should be paid to the corrosion thermodynamics and kinetics of Zn electrodes. This mini review will briefly retrospect basic aspects of Zn corrosion and then review different strategies adopted by investigators to mitigate the corrosion of Zn electrodes in rechargeable batteries.
The widely applied alkaline electrolyte in Zn batteries is 7 M KOH solution, which means the pH value is higher than 14. Sometimes neutral or acidic electrolytes are also investigated. The electrochemical thermodynamics in these systems is the basis of zinc dissolution, zinc deposition, and hydrogen evolution. According to the calculation method developed by Pourbaix (Pourbaix, 1974), the basic E-pH equilibrium diagram (Pourbaix diagram) of Zn in aqueous environment is shown in Figure 1.
Figure 1. Potential-pH equilibrium diagram for the zinc-water system at 25°C [established by considering Zn(OH)2].
In the diagram, line a and b refer to the equilibrium conditions of hydrogen evolution reaction (HER) and oxygen evolution reaction (OER) from water (the partial pressure of hydrogen or oxygen is 1 atm at 25°C). The region between line a and b is called electrochemical window of water. Line 6, 3, and 7 represent the equilibrium conditions between metallic Zn and its oxidized species. Therefore, in water or aqueous solutions Zn is thermodynamically unstable. In acidic solutions Zn2+ is stable, while in alkaline solutions HZnO2– or ZnO are stable. When the solution pH value is in the range between 8.5 and 10.5, Zn(OH)2 can cover the Zn surface, which would inhibit the dissolution of Zn.
Generally, corrosion of Zn is related to the hydrogen evolution reaction (HER), which can be expressed by the following two equations.
Acidic environments:
Alkaline environments:
It should be noted that the Pourbaix diagram applies merely to the simplest systems. If some species which can combine with Zn to form complexes or insoluble compounds are present in the Zn-aqueous system, the electrochemical equilibrium would be much more complicated (Zhang, 2008). Furthermore, Pourbaix diagram is only a thermodynamics description and in real condition the kinetics factors should be considered. For example, the equilibrium potential between Zn and its oxidation state is lower than hydrogen evolution potential. Therefore, from the perspective of thermodynamics, the hydrogen evolution reaction can always drive the oxidation of Zn in the whole pH range. But actually, the overpotential of HER on Zn electrode is high so that the hydrogen evolution rate is not that obvious (Lee, 1971).
According to the Tafel equation:
the overpotential η is co-determined by the exchange current i0 and the Tafel slope b. The low value of i0 is the cause of high HER overpotential. However, when the composition of Zn electrode or electrolyte are changed, the overpotential alter and the corrosion tendency of Zn may increase. For example, the HER overpotential of Zn electrode can significantly reduce with the presence of ZnO (Lee et al., 2006a). The morphology of Zn electrode also affects the hydrogen evolution. A more porous Zn electrode generally leads to larger specific area, which increases the exchange current and exacerbates Zn electrode corrosion (Sun et al., 2019).
The electrolyte is another pivotal factor that determines the fundamental electrochemistry of Zn electrodes. Therefore, modifying the electrolyte would effectively alter the corrosion behavior of Zn electrodes. In a few early studies, the influence of electrolyte conditions on Zn electrode corrosion has been investigated, especially in concentrated alkaline solutions. The HER rate would be increased if impurities introduce metal cations such as Cu2+, Ni2+, As3+, and Sb3+ into the electrolyte. On the contrary, the presence of Pb2+ can decrease the HER rate (Era et al., 1968). Adding some metal oxide or hydroxide (e.g., In2O3) into Zn powder gel is also beneficial to the corrosion resistance of anode material (Sato et al., 1992). Apart from inorganic inhibitors, many organic additives such as α-diphenylglyoxime, polyethylene glycol (600), tartrate, and dinonylphenol phosphate ester are also explored by investigators (Nartey et al., 1994; Moon et al., 2005; Lee et al., 2006b; Qu, 2006). The inhibition mechanism of these organic species is generally considered to be adsorption onto Zn surface. Qu et al. proposed that an effective inhibitor should cover the surface of Zn electrode when the battery was at rest and had fast desorption kinetics after applying anodic potential. In this case the negative effect on discharge performance of the Zn electrode could be minimized (Qu, 2006).
In recent years, there are some new inhibitors in traditional alkaline electrolytes for different Zn batteries reported by investigators. Xiao et al. (2018) compared benzotriazole, thiourea and sodium dodecyl benzene sulfonate and found that benzotriazole is the most effective to decrease Zn corrosion in Zn-air battery. Huang et al. (2018) studied the influence of ethylenediaminetetraacetic acid (EDTA), polysorbate 20, and tartaric acid on Zn electrode behavior in a Zn-air battery. It was found that EDTA was superior to the other two in preventing not only corrosion but also dendrite formation.
In addition to traditional alkaline electrolytes, novel aqueous or non-aqueous liquid electrolytes and solid-state electrolytes are continuously developed (Chen et al., 2019; Fan et al., 2019a). Due to the different electrochemical environment, the corrosion behavior of Zn electrode should be re-estimated. For example, Han et al. manufactured a type of salt reinforced gelatin-based solid-state electrolyte, which contained less free water compared to traditional aqueous electrolytes and showed lower corrosion tendency (Han et al., 2019). In addition, inhibitors that can be compatible to new electrolytes have also been studied. Chen and coworkers developed a mildly acidic electrolyte containing 5% fumed silica (FS) for Zn-LiMn2O4 battery (Hoang et al., 2017; Xiong et al., 2018; Mitha et al., 2019). This electrolyte reduced the dendrite growth of Zn electrode but would increase the corrosion rate. They explored several inhibitors including pyrazole, lignin and poly(ethylene glycol) in this system and optimized the corresponding concentrations. For example, the liner polarization curves of Zn electrodes revealed that the FS electrolyte increased the corrosion of Zn electrode and the addition of pyrazole largely mitigated the corrosion tendency.
Modifying the composition of Zn electrode is a commonly adopted method to control anode corrosion. A lot of heavy metal elements including Cd, In, Sn, Ti, Pb, and Bi (or their oxides) have been investigated as additives into Zn electrodes (McBreen and Gannon, 1981, 1983, 1985; Biegler et al., 1983; Sato et al., 1983; Bonnick and Dahn, 2012). Due to high HER overpotential, these elements could reduce Zn corrosion. In more recent studies, Bi is the most widely used alloying element which is also reported to be beneficial to controlling dendrite growth and shape change of Zn electrodes (Kim et al., 2015; Jo et al., 2017; Chotipanich et al., 2018; Park et al., 2018).
To reduce the cost of additives, some investigators also explored some inexpensive alloying elements. In primary Zn-air battery, Durmus et al. (2019) studied Zn alloy electrode that contained 10 wt. % Al and found it more corrosion resistant than pure Zn electrode. Lee and Ryu (2018) added different amount of Al and Si (1–3 wt.%) into Zn gel electrodes for secondary Zn-air batteries and found that 2 wt.% Al-mixed anodes were the least prone to corrosion compared to bare Zn and Si-mixed Zn electrodes.
In some investigations, multiple additives were simultaneously utilized. Aremu et al. (2019) added K2S and PbO into Zn-BiO electrodes. The results of electrochemical tests showed that the coexistence BiO, K2S, and PbO would restrain corrosion to the maximum level. Besides, the capacity of Zn-BiO-K2S-PbO electrode was superior to Zn-BiO, Zn-BiO-K2S, and Zn-BiO-PbO electrodes (Aremu et al., 2019). In Ni-Zn batteries, Wang et al. (2017) fabricated Zn electrodes with different amount of Al and Sb. The electrode structure was layered double hydroxides. The enhanced corrosion resistance of Zn-Al-Sb electrode was also attributed by the authors to the high HER overpotential of Sb (Wang et al., 2017). Similarly, they introduced graphic carbon nitride into Zn-Al layered double oxide electrode and also found the increased corrosion resistance (Cui et al., 2019).
As mentioned, the electrode morphology (e.g., porosity) affects the corrosion kinetics on Zn anodes. A larger specific surface area leads to a higher HER exchange current. The HER rate on Zn powder with small particle size is faster than that on Zn powder with large particle size (Zhang, 2008). However, the corrosion in a real system should consider more complex factors. In a recent study, Liu et al. prepared a series of porous Zn electrodes with different pore sizes (average values ranging from 300 μm to 8 μm as shown in Figures 2a–h). According to the polarization curves (Figure 2i), the Zn electrode with pore size of 300 μm had larger corrosion current than pure Zn electrode, which was corresponding to the phenomenon described above. But when the pore size further decreased, the corrosion potential altered to negative values and the corrosion current reduced. This opposite phenomenon was possibly attributed to the accumulation of zincate as the corrosion product in the smaller pore structure (Liu P. et al., 2019). In some earlier studies (Gregory et al., 1972; Vorkapić et al., 1974), it was also reported that the presence of Zn(OH) in alkaline electrolytes can restrain the HER rate.
Figure 2. (a–h) Electrodeposited 3D porous Zn structures with pore size ranging from 300 μm to 8 μm. (i) Liner polarization curves of pure Zn and porous Zn electrodes with different pore sizes (Liu P. et al., 2019). Copyright: 2019 Liu et al. This is an open-access article distributed under the terms of the Creative Commons Attribution License (CC BY). The use, distribution or reproduction in other forums is permitted, provided the original author(s) and the copyright owner(s) are credited and that the original publication in this journal is cited, in accordance with accepted academic practice.
Another strategy to mitigate Zn electrode corrosion is introducing coating on the Zn surface. For example, Lee et al. (2013) fabricated aluminum oxide coated Zn electrode and found it had enhanced corrosion resistance. Hu et al. (2019) rolled and tore Zn foil and Sn foil and then coated a Pb film via surface chemical reaction to prepare Zn electrode with artificial solid electrolyte interface (ASEI) in a Zn-Ni battery. The HER overpotential was enhanced on this type of Zn electrode. Besides, the dendrite growth behavior of the Zn electrode was also changed (Hu et al., 2019). Polyaniline coating (Jo et al., 2019) and carbon shell (Wei et al., 2019) were also reported to be beneficial to reduce self-discharge of Zn electrode.
With the development of more advanced, porous and high energy density Zn electrodes for rechargeable Zn batteries, more works should be performed to investigate the corrosion behavior of Zn electrodes. The following points should be the research focus in the future. (1) Utilizing electrolyte or electrode additives is a convenient method to alter the corrosion electrochemistry of Zn electrodes. It is required to develop effective and inexpensive inhibitors, especially for those novel electrolytes. (2) Acquiring inspirations from other battery systems (e.g., LIBs) and designing new 3D structure with coating or shell may be an efficient way to mitigate corrosion and at the same time deal with other challenges facing Zn electrodes such as dendrite formation and shape change. (3) The relationship between corrosion and the morphology of advanced Zn electrodes should be further clarified. To enhance the corrosion resistance of porous Zn electrodes with high energy density, it is crucial to reveal the electrochemical condition and diffusion kinetics in local environment.
LL drafted the manuscript. YS reviewed and revised the manuscript. XW, YJ, and JL provided the comments and suggestions.
This work was supported by the National Natural Science Foundation of China (Grant No. 5190146) and China Postdoctoral Science Foundation (Grant No. 2018M632016).
The authors declare that the research was conducted in the absence of any commercial or financial relationships that could be construed as a potential conflict of interest.
Aremu, E. O., Park, D.-J., and Ryu, K.-S. (2019). The effects of anode additives towards suppressing dendrite growth and hydrogen gas evolution reaction in Zn-air secondary batteries. Ionics 25, 4197–4207. doi: 10.1007/s11581-019-02973-y
Biegler, C., Deutscher, R. L., Fletcher, S., Hua, S., and Woods, R. (1983). Accelerated testing of additives in zinc plates of nickel zinc cells. J. Electrochem. Soc. 130, 2303–2309. doi: 10.1149/1.2119575
Bonnick, P., and Dahn, J. R. (2012). A simple coin cell design for testing rechargeable zinc-air or alkaline battery systems. J. Electrochem. Soc. 159, A981–A989. doi: 10.1149/2.023207jes
Chao, D., Zhou, W., Ye, C., Zhang, Q., Chen, Y., Gu, L., et al. (2019). An electrolytic Zn-MnO2 battery for high-voltage and scalable energy storage. Angew. Chem. Int. Ed. 58, 7823–7828. doi: 10.1002/anie.201904174
Chen, C.-Y., Matsumoto, K., Kubota, K., Hagiwara, R., and Xu, Q. (2019). A room-temperature molten hydrate electrolyte for rechargeable zinc–air batteries. Adv. Energy Mater. 0:1900196. doi: 10.1002/aenm.201900196
Chotipanich, J., Arpornwichanop, A., Yonezawa, T., and Kheawhom, S. (2018). Electronic and ionic conductivities enhancement of zinc anode for flexible printed zinc-air battery. Eng. J. Thail. 22, 47–57. doi: 10.4186/ej.2018.22.2.47
Cui, F., Yang, Z., Chen, L., Zeng, X., Meng, J., Jiang, Y., et al. (2019). Preparation of graphitic Carbon Nitride/Zn-Al layered double oxides composites and its electrochemical performance as an anodic material for zinc-nickel secondary batteries. J. Electrochem. Soc. 166, A2563–A2569. doi: 10.1149/2.1001912jes
Durmus, Y. E., Guerrero, S. S. M., Tempel, H., Hausen, F., Kungl, H., and Eichel, R.-A. (2019). Influence of Al alloying on the electrochemical behavior of Zn electrodes for zn-air batteries with neutral sodium chloride electrolyte. Front. Chem. 7:800. doi: 10.3389/fchem.2019.00800
Era, A., Takehara, Z., and Yoshizawa, S. (1968). Influence of impurities especially lead contained in manganese dioxide upon the self-discharge of the Leclanche dry cell. Electrochimica Acta 13, 383–396. doi: 10.1016/0013-4686(68)87010-0
Fan, X., Liu, J., Song, Z., Han, X., Deng, Y., Zhong, C., et al. (2019a). Porous nanocomposite gel polymer electrolyte with high ionic conductivity and superior electrolyte retention capability for long-cycle-life flexible zinc–air batteries. Nano Energy 56, 454–462. doi: 10.1016/j.nanoen.2018.11.057
Fan, X., Liu, X., Hu, W., Zhong, C., and Lu, J. (2019b). Advances in the development of power supplies for the internet of everything. InfoMat 1, 130–139. doi: 10.1002/inf2.12016
Gregory, D. P., Jones, P. C., and Redfearn, D. P. (1972). The corrosion of zinc anodes in aqueous alkaline electrolytes. J. Electrochem. Soc. 119, 1288–1292. doi: 10.1149/1.2403980
Han, Q., Chi, X., Liu, Y., Wang, L., Du, Y., Ren, Y., et al. (2019). An inorganic salt reinforced Zn2+-conducting solid-state electrolyte for ultra-stable Zn metal batteries. J. Mater. Chem. A 7, 22287–22295. doi: 10.1039/c9ta07218g
Hoang, T. K. A., Doan, T. N. L., Cho, J. H., Su, J. Y. J., Lee, C., Lu, C., et al. (2017). Sustainable Gel Electrolyte Containing Pyrazole as Corrosion Inhibitor and Dendrite Suppressor for Aqueous Zn/LiMn2O4 Battery. Chemsuschem 10, 2816–2822. doi: 10.1002/cssc.201700441
Hu, J., Ding, J., Du, Z., Duan, H., and Yang, S. (2019). Zinc anode with artificial solid electrolyte interface for dendrite-free Ni-Zn secondary battery. J. Colloid Interface Sci. 555, 174–179. doi: 10.1016/j.jcis.2019.07.088
Huang, M.-C., Huang, S.-H., Chiu, S.-C., Hsueh, K.-L., Chang, W.-S., Yang, C.-C., et al. (2018). Improved electrochemical performance of Zn-air secondary batteries via novel organic additives. J. Chin. Chem. Soc. 65, 1239–1244. doi: 10.1002/jccs.201700445
Jo, Y. N., Prasanna, K., Kang, S. H., Ilango, P. R., Kim, H. S., Eom, S. W., et al. (2017). The effects of mechanical alloying on the self-discharge and corrosion behavior in Zn-air batteries. J. Ind. Eng. Chem. 53, 247–252. doi: 10.1016/j.jiec.2017.04.032
Jo, Y. N., Santhoshkumar, P., Prasanna, K., Vediappan, K., and Lee, C. W. (2019). Improving self-discharge and anti-corrosion performance of Zn-air batteries using conductive polymer-coated Zn active materials. J. Ind. Eng. Chem. 76, 396–402. doi: 10.1016/j.jiec.2019.04.005
Kim, H. S., Jo, Y. N., Lee, W. J., Kim, K. J., and Lee, C. W. (2015). Coating on Zinc surface to improve the electrochemical behavior of Zinc Anodes for Zinc-Air fuel cells. Electroanalysis 27, 517–523. doi: 10.1002/elan.201400457
Lee, C. W., Eom, S. W., Sathiyanarayanan, K., and Yun, M. S. (2006a). Preliminary comparative studies of zinc and zinc oxide electrodes on corrosion reaction and reversible reaction for zinc/air fuel cells. Electrochim. Acta 52, 1588–1591. doi: 10.1016/j.electacta.2006.02.063
Lee, C. W., Sathiyanarayanan, K., Eom, S. W., Kim, H. S., and Yun, M. S. (2006b). Novel electrochemical behavior of zinc anodes in zinc/air batteries in the presence of additives. J. Power Sources 159, 1474–1477. doi: 10.1016/j.jpowsour.2005.11.074
Lee, S.-M., Kim, Y.-J., Eom, S.-W., Choi, N.-S., Kim, K.-W., and Cho, S.-B. (2013). Improvement in self-discharge of Zn anode by applying surface modification for Zn-air batteries with high energy density. J. Power Sources 227, 177–184. doi: 10.1016/j.jpowsour.2012.11.046
Lee, T. S. (1971). Hydrogen Over potential on Pure Metals in Alkaline Solution. J. Electrochem. Soc. 118, 1278–1282. doi: 10.1149/1.2408305
Lee, Y.-S., and Ryu, K.-S. (2018). Effects of aluminum and silicon as additive materials for the Zinc Anode in Zn-Air Batteries. J. Korean Electrochem. Soc. 21, 12–20. doi: 10.5229/JKES.2018.21.1.12
Li, M., Liu, B., Fan, X., Liu, X., Liu, J., Ding, J., et al. (2019). Long-shelf-life polymer electrolyte based on tetraethylammonium hydroxide for flexible Zinc–air batteries. ACS Appl. Mater. Interf. 11, 28909–28917. doi: 10.1021/acsami.9b09086
Lin, X., Sun, Q., Davis, K. D., Li, R., and Sun, X. (2019). The application of carbon materials in nonaqueous Na-O2 batteries. Carbon Energy 1, 141–164. doi: 10.1002/cey2.15
Liu, P., Ling, X., Zhong, C., Deng, Y., Han, X., and Hu, W. (2019). Porous Zinc anode design for Zn-air chemistry. Front. Chem. 7:656. doi: 10.3389/fchem.2019.00656
Liu, X., Yuan, Y., Liu, J., Liu, B., Chen, X., Ding, J., et al. (2019). Utilizing solar energy to improve the oxygen evolution reaction kinetics in zinc-air battery. Nat. Commun. 10:4767. doi: 10.1038/s41467-019-12627-2
McBreen, J., and Gannon, E. (1981). The electrochemistry of metal oxide additives in pasted zinc electrodes. Electrochim. Acta 26, 1439–1446. doi: 10.1016/0013-4686(81)90015-3
McBreen, J., and Gannon, E. (1983). The effect of additives on current distribution in pasted Zinc Electrodes. J. Electrochem. Soc. 130, 1980–1982. doi: 10.1149/1.2119488
McBreen, J., and Gannon, E. (1985). Bismuth oxide as an additive in pasted zinc electrodes. J. Power Sources 15, 169–177. doi: 10.1016/0378-7753(85)80070-7
Mitha, A., Mi, H., Dong, W., Cho, I. S., Ly, J., Yoo, S., et al. (2019). Thixotropic gel electrolyte containing poly(ethylene glycol) with high zinc ion concentration for the secondary aqueous Zn/LiMn2O4 battery. J. Electroanal. Chem. 836, 1–6. doi: 10.1016/j.jelechem.2019.01.014
Moon, K., Lee, M., Kim, K., and Park, K. (2005). The effect of additives on the corrosion resistance of Zn electrode in alkaline battery system. Met. Mater. Int. 11, 221–226. doi: 10.1007/BF03027446
Nartey, V. K., Binder, L., and Kordesch, K. (1994). Identification of organic corrosion inhibitors suitable for use in rechargeable alkaline zinc batteries. J. Power Sources 52, 217–222. doi: 10.1016/0378-7753(94)02010-8
Park, D.-J., Aremu, E. O., and Ryu, K.-S. (2018). Bismuth oxide as an excellent anode additive for inhibiting dendrite formation in zinc-air secondary batteries. Appl. Surf. Sci. 456, 507–514. doi: 10.1016/j.apsusc.2018.06.079
Parker, J. F., Chervin, C. N., Pala, I. R., Machler, M., Burz, M. F., Long, J. W., et al. (2017). Rechargeable nickel–3D zinc batteries: an energy-dense, safer alternative to lithium-ion. Science 356, 415–418. doi: 10.1126/science.aak9991
Parker, J. F., Ko, J. S., Rolison, D. R., and Long, J. W. (2018). Translating materials-level performance into device-relevant metrics for Zinc-Based batteries. Joule 2, 2519–2527. doi: 10.1016/j.joule.2018.11.007
Pourbaix, M. (1974). Atlas of Electrochemical Equilibria in Aqueous Solutions. Available online at: http://gen.lib.rus.ec/book/index.php?md5=4d2ba03aaacf7bdaff81ec3632e69806 (accessed December 26, 2019).
Qu, D. (2006). Behavior of Dinonylphenol Phosphate Ester and its influence on the oxidation of a Zn anode in alkaline solution. J. Power Sources 162, 706–712. doi: 10.1016/j.jpowsour.2006.04.150
Sato, Y., Kanda, M., Niki, H., Ueno, M., Murata, K., Shirogami, T., et al. (1983). Long life sealed nickel-zinc cell using a new separator. J. Power Sources 9, 147–159. doi: 10.1016/0378-7753(83)80029-9
Sato, Y., Takahashi, M., Asakura, H., Yoshida, T., Tada, K., Kobayakawa, K., et al. (1992). Gas evolution behavior of Zn alloy powder in KOH solution. J. Power Sources 38, 317–325. doi: 10.1016/0378-7753(92)80121-Q
Stock, D., Dongmo, S., Janek, J., and Schröder, D. (2019). Benchmarking anode concepts: the future of electrically rechargeable Zinc–Air batteries. ACS Energy Lett. 4, 1287–1300. doi: 10.1021/acsenergylett.9b00510
Sun, Y., Liu, X., Jiang, Y., Li, J., Ding, J., Hu, W., et al. (2019). Recent advances and challenges in divalent and multivalent metal electrodes for metal–air batteries. J. Mater. Chem. A 7, 18183–18208. doi: 10.1039/C9TA05094A
Sun, Y., Wang, J., Jiang, Y., and Li, J. (2018). A comparative study on potentiodynamic and potentiostatic critical pitting temperature of austenitic stainless steels. Mater. Corros. 69, 44–52. doi: 10.1002/maco.201709641
Vorkapić, L. Ž, Dražić, D. M., and Despić, A. R. (1974). Corrosion of pure and amalgamated Zinc in concentrated Alkali hydroxide solutions. J. Electrochem. Soc. 121, 1385–1392. doi: 10.1149/1.2401695
Wang, F., Chen, G., Zhang, N., Liu, X., and Ma, R. (2019). Engineering of carbon and other protective coating layers for stabilizing silicon anode materials. Carbon Energy 1, 219–245. doi: 10.1002/cey2.24
Wang, L., Liu, Y., Chen, X., Qin, H., and Yang, Z. (2017). Zinc aluminum antimony hydrotalcite as anode materials for Ni-Zn Secondary batteries. J. Electrochem. Soc. 164, A3692–A3698. doi: 10.1149/2.0831714jes
Wei, H., Hu, X., Zhang, X., Yu, Z., Zhou, T., Liu, Y., et al. (2019). Zn@C core-shell nanocomposite for rechargeable Aqueous Zn//MnO2 batteries with long lifetime. Energy Technol. 7:1800912. doi: 10.1002/ente.201800912
Xiao, Y., Shi, J., Zhao, F., Zhang, Z., and He, W. (2018). Effects of electrolyte additives on the properties of zinc-bismuth electrodes in Zinc-Air batteries. J. Electrochem. Soc. 165, A47–A54. doi: 10.1149/2.0251802jes
Xiong, W., Yang, D., Hoang, T. K. A., Ahmed, M., Zhi, J., Qiu, X., et al. (2018). Controlling the sustainability and shape change of the zinc anode in rechargeable aqueous Zn/LiMn2O4 battery. Energy Storage Mater. 15, 131–138. doi: 10.1016/j.ensm.2018.03.023
Zhang, X. G. (2008). Corrosion and Electrochemistry of Zinc (in Chinese). Berlin: Springer Science & Business Media.
Zhang, Z., Zhao, H., Zhang, H., Hu, J., and Jin, J. (2017). Microstructure evolution and pitting corrosion behavior of UNS S32750 super duplex stainless steel welds after short-time heat treatment. Corros. Sci. 121, 22–31. doi: 10.1016/j.corsci.2017.02.006
Keywords: corrosion, Zn electrode, Zn-air battery, Ni-Zn battery, hydrogen evolution reaction, corrosion inhibitor, electrolyte
Citation: Lei L, Sun Y, Wang X, Jiang Y and Li J (2020) Strategies to Enhance Corrosion Resistance of Zn Electrodes for Next Generation Batteries. Front. Mater. 7:96. doi: 10.3389/fmats.2020.00096
Received: 06 February 2020; Accepted: 30 March 2020;
Published: 24 April 2020.
Edited by:
Cheng Zhong, Tianjin University, ChinaReviewed by:
MouCheng Li, Shanghai University, ChinaCopyright © 2020 Lei, Sun, Wang, Jiang and Li. This is an open-access article distributed under the terms of the Creative Commons Attribution License (CC BY). The use, distribution or reproduction in other forums is permitted, provided the original author(s) and the copyright owner(s) are credited and that the original publication in this journal is cited, in accordance with accepted academic practice. No use, distribution or reproduction is permitted which does not comply with these terms.
*Correspondence: Yangting Sun, c3VueWFuZ3RpbmdAZnVkYW4uZWR1LmNu
Disclaimer: All claims expressed in this article are solely those of the authors and do not necessarily represent those of their affiliated organizations, or those of the publisher, the editors and the reviewers. Any product that may be evaluated in this article or claim that may be made by its manufacturer is not guaranteed or endorsed by the publisher.
Research integrity at Frontiers
Learn more about the work of our research integrity team to safeguard the quality of each article we publish.