- 1School of Material and Mineral Resources Engineering Campus, Universiti Sains Malaysia, Nibong Tebal, Malaysia
- 2School of Chemical Science, Universiti Sains Malaysia, Minden Heights, Malaysia
- 3Department of Rubber Technology and Polymer Science, Faculty of Science and Technology, Prince of Songkla University, Songkhla, Thailand
Lignin has potential as a reinforcing filler and to become an alternative to carbon black in the rubber industry. This is because it is formed from cheaper materials with abundant annually renewable sources and has low weight, high biological efficiency, and wide ecological adaptability. The utilization of bio-filler in the rubber industry has garnered increasing attention from researchers due to increasing environmental concerns over the toxic effects of carbon black on health and the environment. This article is intended to summarize current efforts in the development of a green and sustainable rubber product. Instead of focusing on silica and alternative rubber matrix-like guayule and Russian dandelion, it looks at lignin, which also has potential as a reinforcing filler and can enable the development of competitive green rubber composites. Lignin has several special characteristics such as good mechanical, physico-chemical, biodegradability, and antioxidant properties and excellent thermal stability. However, the incorporation of lignin in a rubber matrix is not straightforward, and this needs to be overcome with certain suitable solutions because of the polarity of lignin molecules, which contributes to strong self-interactions. Consequently, chemical modification of lignin is often used to improve the dispersion of lignin in elastomers, or a compatibilizer is added to enhance interfacial adhesion between lignin and the rubber matrix. This review attempts to compile relevant knowledge about the performance of lignin-filled rubber composite using different approaches such as mixing method, surface modification, hybrid fillers, etc. This study is expected to gain significant interest from researchers globally on the subject of lignin-based rubber composites and the advancement of development in green rubber products.
Introduction
Given the many applications of rubber in industrial parts such as hoses, tires, seals, cushions, etc., it should be acknowledged that many aspects need to be considered and understood. To obtain excellent performance from rubber compounds, a reinforcing filler is needed to provide reinforcement. Specifically, in the tire technology area, reinforcement is known as the incorporation of finely divided (mineral) particles into vulcanized compounds that improve abrasion, tearing, cutting, and rupture resistance due to their stiffness and hardness (Medalia and Kraus, 1994). Tires are the most prominent rubber items, both in terms of importance and in terms of the volume of production. Most of the natural rubber, synthetic rubber, and 90% of the worldwide production of carbon black are used in the tire industry. This is due to the ability of rubber to enhance the strength of the tire. In spite of the functionalities of carbon black as the reinforcing filler, it is petrochemical and non-degradable material, and a large amount of energy is consumed in its production. Moreover, the hazardous effect of the utilization of carbon black has polluted the environment, starting from the production process, which emits carbon dioxide into the atmosphere (Attharangsan et al., 2012). It further contributes to the critical environmental situation when tires run on roads. The high rolling resistance of tires adds friction and causes engines to burn extra fuel, which leads in turn to more greenhouse gas emissions.
Indeed, the stock reduction of oil-based material and environmental issues so as the global warming phenomenon have inspired researchers to focus on the development of a green tire formulated from renewable resources (Thakur and Singha, 2010; Langan et al., 2011; Thakur et al., 2011). Recent trends in technology innovation for green tires incorporate a bio-filler to substitute carbon black. Several potential green fillers from new resources have attracted a great amount of attention from researchers, such as lignins, which are renewable, bio-degradable, inexpensive, light-weight, and abundant (Setua et al., 2000; Košíková and Gregorová, 2005; Bogoeva-Gaceva et al., 2007; Eichhorn et al., 2010; Mishra et al., 2012; Bajpai et al., 2013; Hussin et al., 2014).
Lignin is the second most abundant natural resource (Gosselink et al., 2004; Faruk et al., 2012; Kakroodi et al., 2013; Kazemi et al., 2013). It is an aromatic polymer (Lora and Glasser, 2002; Fitigau et al., 2013) that acts as a glue to hold cellulose and hemicellulose together in plants, to strengthen cell walls, and to protect plants against parasites and disease (Erdocia et al., 2014; Kakroodi et al., 2014; Lang et al., 2018). The complex structure of amorphous lignin is interestingly formed by the attachment of different functional groups such as methoxyl, phenolic, hydroxyl, and carbonyl groups. A huge amount of lignin by-product is produced by the paper and pulp industries, and about ~98% of that is usually burned to generate energy or just disposed of in landfill, hence posing a major disposal problem (Mohan and Karthikeyan, 1997; Zhang and Chuang, 2001; Kumar et al., 2009; Doherty et al., 2011; Saake and Lehnen, 2012; Laurichesse and Avérous, 2014; Lang et al., 2018). Therefore, the development of new technologies is crucial to explore the functionality of this precious by-product further, not only for use in low- and medium-value applications but in high-value applications as well (Hämäläinen et al., 2018). Many applications that have been explored by researchers, for example, as adhesive (Gosselink et al., 2004), stabilizing agents (De Paoli and Furlan, 1985), reinforcing agents (Kumaran and De, 1978; Setua et al., 2000; Benko et al., 2014), superabsorbent hydrogels, and phenolic resin (Suhas et al., 2007; Kumar et al., 2009; Hu et al., 2011).
The main goal of this review is to focus on lignin-derived compounds as bio-renewable filler as well as the performance and properties of lignin-reinforced rubber composites. The overall characteristics of lignin-filled rubber composites with different methods of modification and mixing techniques of the lignin into rubber compound, which influences the properties of the lignin-filled rubber compound, are also discussed. Lastly, upcoming trends in lignin-reinforced rubber composites will be presented as the review's conclusion.
Conventional Carbon Black in Rubber Composite
Rubber Composite
A wide variety of rubber compositions are used in the tire industry. The base elastomers that are commonly used consist of blends of natural rubber (NR), butadiene rubber (BR), styrene-butadiene rubber (SBR), ethylene-propylene-diene rubber (EPDM), and epoxidized natural rubber (ENR). Apparently, the utilization of rubber without filler does not provide good properties for any application. Therefore, filler is used to impart better properties to rubber products, with carbon black or silica used commercially. Other ingredients with different functionalities are also incorporated into rubber compounds depending on the application, i.e., softeners, vulcanizing agents, accelerators, activators, retarders, and anti-degradants. As is widely known, accelerators are used to increase the rate and density of cross-linking and are activated by an activator, while retarders are used to prevent rubber scorching and to delay the vulcanization process. Furthermore, anti-degradants are important for applications like tire production to prevent degradation by oxygen, ozone, heat, or other factors (Ignatz-Hoover et al., 2003; Datta et al., 2007).
Rubber Matrix
NR is the most common raw material used as the main component in tire manufacturing and possesses impressive characteristics such as green strength and tensile strength due to its spontaneous crystallization when exposed to strain. It is a unique biopolymer and is the best raw material for manufacturing tires for cars, trucks, and aircraft. Besides, NR is a unique material that has valuable properties that synthetic rubber lacks. Due to the rapid development of economies such as in those of China and India, the demand for NR is continuing to increase, and prices have become increasingly volatile (Beilen and Poirier, 2007; Soratana et al., 2017). Furthermore, with the spread of fungal disease harming rubber trees and the tendency of farmers to plant more profitable palm oil rather than rubber (Jawjit et al., 2010), the chances of natural rubber prices shooting up are high.
BR is the second-largest volume of synthetic rubber produced after SBR. This is commonly blended with NR in the sidewall and treads of tires. It has been found that its low glass transition temperature, Tg, results in exceptional abrasion resistance and low rolling resistance. Thus, a blend of NR/BR is the focus for tire applications incorporating ingredients such as carbon black, curatives, and a high concentration of anti-degradants to provide weather resistance (Waddell, 1998; Hamed, 2012). The addition of SBR lowers the price and imparts good wear and bonding properties, as well as good heat aging properties and abrasion resistance. It also possesses a non-crystalline and non-polar character with a low gum tensile strength of about ~2 MPa (Chakraborty et al., 2009). Atashi and Shiva (2010) focused on optimizing the failure properties of passenger car tire tread compounds with combinations of NR, SBR, and BR. They modified the curing conditions and the behavior of the rubber matrixes. Hao et al. (2001) also found that the Mooney viscosity and scorch time of hybrid rubber SBR/NR composites showed improvement when they modified the curing conditions.
Besides, the dynamic conditions of a tire, especially the sidewall, which is easily attacked by ozone, give rise to a demand for life-extension by improving ozone and thermo-oxidative resistance. Blending EPDM with NR and BR has shown good potential for ozone resistance (Sahakaro et al., 2007). This is because the EPDM phase dispersed in rubber blends provides an internal anti-ozonant to highly unsaturated rubbers since it is an ozone-resistant polymer. The modification of NR with a random distribution of epoxy groups together with a polymer backbone forms ENR (Pire et al., 2011). The existence of these epoxy groups imparts ENR with miscibility with other polymers (Narathichat et al., 2012) or active fillers (Sengloyluan et al., 2014) through reactive compatibilization as they are reacted with nucleophilic reagents (Chang et al., 2007; Nguyen et al., 2012; Zhang et al., 2012).
Carbon Black as a Common Reinforcing Filler
Carbon black is ultrafine powder manufactured by the burning of hydrocarbons in a limited supply of air (Drogin, 1968; Huang, 2002). Aggregate size and shape and the number of particles per aggregate play important roles in the determination of the structure of carbon black. Carbon black with high branching contains many prime particles that are referred to as high-structure black, with stronger attractive forces between aggregates. This means that more energy is required in the process of dispersion to break the chain. High-structure black has the tendency to produce larger aggregate grains in contact, with smaller distances between aggregate grains. This attribute is important in achieving high electrical conductivity (Huang, 2002).
For tire manufacturing, carbon black is used extensively as the reinforcing filler. Several mechanical properties of tires are reinforced such as its modulus, tear strength, and wear characteristics (Khalil et al., 2007; Yu et al., 2016a). The usage of carbon black as a reinforcing filler, which started in the twentieth century, has produced a ten-fold increase in the service life of tires. This phenomenon is due to the strong interaction formed between the surface of carbon black and the rubber matrix (Brennan et al., 1964; Leblanc, 2002; Fukahori, 2003; Hoshikawa et al., 2016). The incorporation of carbon black has an important effect not only on the mechanical properties but also on the dynamic properties of the tires (Schaefer et al., 2000; ten Brinke, 2002; Hilonga et al., 2012). Aside from solely focusing on the strength of a tire, improvements of the tire's dimensional stability, conductive filler, ultraviolet light stabilizer, colorant, and antioxidant to extend the service lifetime of rubber are also important (Huang, 2002). Since then, carbon black has continued to be used significantly in tires and also other rubber products as a reinforcing material, and up to 30% of rubber compounds involve the incorporation of carbon black (Sudin and Swamy, 2006; Siti Suhaily et al., 2013).
Eco-Toxicological Effect
Carbon black is an oil-based rubber reinforcing filler. Several types of carbon blacks are available with different characteristic properties. Incomplete combustion or thermal degradation through pyrolysis produce furnace and thermal blacks (Huang, 2002), which are mainly used in sectors such as rubber and polymer composites. The production process by the pyrolysis method using liquid or gas hydrocarbons emits carbon dioxide gas. Moreover, carbon black is harmful not only to the environment but also to humans, as it is proven to cause pulmonary inflammation through repeated inhalation in animal models (Morfeld et al., 2006). Furthermore, the millimeter size of carbon black in pellet form in industry is transformed into powder form once it is introduced into the mixer (Huang, 2002; Wang et al., 2003). The pellet form is only used for ease of transportation and handling of carbon black in the rubber industry. But then, reversion into the aggregated state may occur due to the shear forces that are applied during the mixing process, which breaks apart the agglomerates and produces particles ranging from 70 to 500 nm, potentially increasing the risk of exposure for workers (Basfar et al., 2002).
Currently, there are major issues associated with fossil fuel, such as global warming, increases in price, depletion, and the large dependence of carbon blacks on oil supplies, so that the world faces critical issues to ensure that it has enough energy and natural resources. With increasing prices and the demand to ensure a safe environment and healthy population, the carbon black utilized in tire manufacturing must be substituted with other eco-friendly and naturally based fillers (Ehrburger-Dolle et al., 1994; Snowdon et al., 2014). Therefore, the research community is continuing in its efforts to find the best solution to give better properties for a “green” composite. Many researchers are making efforts to develop an alternative material to substitute carbon black (Zafarmehrabian et al., 2012; Jiang et al., 2013).
Green Tire Technology
The term “green tire” refers to entirely new types of tire that are built completely from sustainable material. It is also known as an “eco-friendly” tire, which does not pose a threat to the environment. As people are giving their attention and focus toward environmental protection, the utilization of various natural biomasses is being examined to replace carbon black as a filler in NR polymer matrix to produce greener tires. Three features are considered: fuel efficiency, wet grip, and noise. These green tires employ a special type of tightly bonded rubber in the tread blocks that enhances the physical and mechanical properties in terms of abrasion resistance and more energy being retained during driving. This means that a lower rolling resistance is established, and thus less engine power is needed for rotating the tires, which results in fuel efficiency in the automobile industry. Many researchers have explored a sustainable material substitute for oil-based carbon black as the reinforcing filler to produce green tire composites (Guy et al., 2009; Hilonga et al., 2012; Hirayama and Saron, 2012; Zafarmehrabian et al., 2012; Siti Suhaily et al., 2013; Sarkawi et al., 2015).
In the early 1990s, Michelin introduced the “Green Tire” technology in the tire industry, which involved a full substitute of carbon black by silica as the reinforcing filler in passenger tire treads (Zafarmehrabian et al., 2012). However, the manufacturer faced major difficulties in the construction of the green tire due to the polar nature of silica, which is incompatible with the non-polar rubber matrix. Some researchers then discovered that organosilanes acted as an outstanding bonding material between silica and the rubber matrix (Park and Cho, 2003; Atashi and Shiva, 2010; Kaewsakul et al., 2014). Thus, silica/organosilane technology was developed to ensure that excellent performance was obtained from the green tire. This technology contributed to savings in automotive fuel, since it reduced rolling resistance by approximately 20% compared to a tire reinforced by carbon black (Hall and Moreland, 2001; Niedermeier et al., 2002; Hilonga et al., 2012; Sarkawi et al., 2015).
Other than Michelin, Goodyear and Bridgestone play a major role in tire manufacturing, as they are also investing in green technologies, specifically tire technology, and are expanding their market share in the tire industry. Based on a report published by Mathews (2018) from Tech Sci Research recently, they anticipated that domestic production of tires in the United States will be boosted by fuel-efficient tire technology, thus inducing a need to find alternative raw materials for use in tire manufacturing. Other than silica filler, another option has also been studied for replacing traditional rubber and chemical usage in the tire industry. In 2015, the company Evonik reported the development of a liquid polybutadiene that makes the silica/silane system more compatible with the rubber matrix of tires (Braum and Jacobi, 2017).
Alternative Renewable Rubber Matrix
Rubber trees (Hevea brasiliensis) are largely composed of poly (cis-1,4–isoprene) and mainly grow in vulnerable areas such as South East Asia and a small part of Africa. The demand for tires and the consumption of natural rubber are expected to increase in line with the increase in the global population and the expansion of the automobile industry. Hence, the carbon footprint is expected to become greater, contributing to global warming. Resource depletion is also a major issue. Even though the source for the synthesis of natural rubber is more than 2,000 plant species, only H. brasiliensis is used for commercial production (Mooibroek and Cornish, 2000; Cornish, 2017). Thus, alternative crops for natural rubber are important to sustain the natural rubber supply, its long-term productivity improvement, and best-in-class technology availability for natural rubber production (Cornish, 2017). A few species such as dandelions (e.g., Taraxacum brevicorniculatum) and guayule (Parthenium argentatum) are possible alternative rubber sources (Mooibroek and Cornish, 2000; Beilen and Poirier, 2007; Schmidt et al., 2010; Venkatachalam et al., 2013).
Russian Dandelion
The prospects of plants such as dandelion as an alternative natural rubber source look brighter because of its inherent natural rubber potential and its metabolic processes, which affect the rubber synthesis and became the focus of study with the aim of enhancing its annual productivity (Laibach et al., 2015). In the 1930s−1950s, Russian dandelion was cultivated as a domestic source of rubber in the Soviet Union. After World War II, it was cultivated to overcome a shortage of rubber in Europe. It is scientifically known as T. brevicorniculatum and is a member of the Asteraceae family. The plant has bright yellow flowers made of many tiny florets. Its roots contain 15 percent latex of a quality similar to that of the rubber tree, making it a viable alternative (Cheng, 1963). The latex containing the rubber and producing proteins contributes to the formation of long polyisoprene chains, which generates high elasticity, high tensile strength, and low-temperature flexibility, making it an ideal raw material for tire manufacturing (Venkatachalam et al., 2013). Dandelion also has the advantage of growing annually, unlike Hevea, which usually takes from seven to 10 years to produce latex, and this certainly helps to reduce the dependence on Hevea for rubber and makes dandelion cost-competitive as a natural rubber source. Continental have produced the first tires where the tread uses 100 percent dandelion natural rubber as a polymer. The biggest plans to manufacture consumer road tires made from dandelion-derived rubber will be realized in 5–10 years. It has been proven that durable tires produced from dandelion rubber can replace tires produced from Hevea, as its quality is comparable to that of traditional natural rubber. In some applications, dandelion rubber performs even better than traditional natural rubber; specifically, it provides good grip on wet surfaces.
Guayule
Guayule is an evergreen plant that can be found in the dry area of the south-west USA to the north of Mexico and, therefore, can be grown in environments different from natural rubber (H. brasiliensis) trees. Moreover, the rubber constituent it contains is very similar to that in natural rubber (H. brasiliensis) trees and it is able to produce a sufficient quantity of natural rubber for commercial rubber application (Benedict et al., 2008; Laibach et al., 2015). This is thus expected to become a valuable new source for tire-grade rubber in commercial applications. The cultivation of the guayule takes a shorter time than that of natural rubber trees; it takes about 3 years before the trees are ready for harvesting and processing to obtain natural rubber (Ray et al., 2005; Beilen and Poirier, 2007).
A part of Bridgestone's plan in its research is to optimize the natural rubber content in the guayule plant and evaluate its application in a broader range of tire types and rubber compounds (Ray et al., 2005; Soratana et al., 2017). In 2015, the Bridgestone group took an impressive step toward the expansion and diversification of renewable resources by producing the first tire made 100% from guayule-derived natural rubber. In order to reduce its environmental footprint, the company built similar passenger tires that use guayule natural rubber instead of natural rubber from Hevea in all of the tire's major natural rubber components, including the tread, sidewall, and bead filler (Rasutis et al., 2015; Cornish, 2017).
Lignin as an Alternative Filler for Rubber Compounds
Chemistry and Properties of Lignin
Lignin is the second most abundant renewable natural resource next to cellulose. It consists of three-dimensionally amorphous polymer chains, which play an important mechanical support role in the plant. This structure acts as a glue that holds the fibers together and a stiffening agent within the fibers (Thakur and Thakur, 2015). It imparts rigidity and impact strength to the cell walls in plants (Feldman, 2016) and protects them from harsh environmental conditions such as water, etc. (Teaca et al., 2013; Thakur and Thakur, 2015). Even though lignin is thermally stable as compared to cellulose and hemicellulose, by contrast, it is responsible for the ultraviolet (UV) biodegradation of the materials (Singha et al., 2009). The bonds between lignin and carbohydrate are covalent in nature and are composed of benzyl esters and phenyl glycol-sides (Doherty et al., 2011).
Lignin possesses a phenylpropanoid backbone along with phenolic and benzylic hydroxyl, methoxyl, and carbonyl substitutions (Gosselink et al., 2004; Jiang et al., 2013; Bahl et al., 2014a). The basic structural units of lignin are p-coumaryl alcohol (p-hydroxyphenyl, H), coniferyl alcohol (guaiacyl, G), and sinapyl alcohol (syringyl, S) (Figure 1). Lignin is generally available as a major byproduct from a number of industries such as in papermaking, ethanol production from biomass, etc., and is generally burned to recover energy-pulping chemicals or used in enzymatic or acid hydrolysis processes (Setua et al., 2000). Considerable efforts are now being made to effectively utilize waste lignin as one of the components of polymer matrices for high-performance composite applications (Watkins et al., 2014).
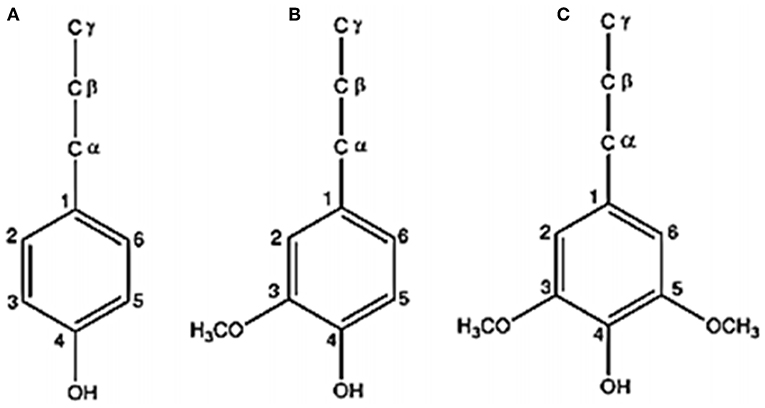
Figure 1. Major phenylpropanoid units of lignin (A) p-caumaryl alcohol (p-hydroxylphenyl), (B) coniferyl alcohol (guaiacyl), and (C) sinapyl alcohol (syringyl) (this is reproduced with permission from Budapest University of Technology and Economics, Faculty of Mechanical Engineering, Department of Polymer Engineering; Jiang et al., 2013).
Furthermore, the abundant functional groups on its surface is one of the reasons why it is widely studied as a reinforcing filler of plastics and rubber. In this context, the functional groups provide the possibility for chemical modification to ensure compatibility with an appropriate matrix polymer (Frigerio, 2014). The common linkage to form a three-dimensional network structure is β-O-4, α-O-4, β-5, 5-5, 4-O-5, β-1, and β-β bonds, which link the basic structural units of lignin (Vainio et al., 2004). Typical softwood lignin is based generally on coniferyl alcohol units and is also called G lignin (Capanema et al., 2005; Dashtban et al., 2010). It is isolated through different types of delignification processes with different sources, but their structure is very similar and highly polydisperse. Moreover, another class is hardwood lignin, which contains a mixture of G and S units. The third type of monomeric unit, based on G, S, and H units, is found in other plants such as cereals, greases, and other non-woods (Suhas et al., 2007). The p-hydroxylphenyl type aromatic rings increase the reactivity due to the free positions at three and five, and thus, a large fraction of these groups is essential for the use of lignin in foam applications. Generally, lignin isolated from different resources has been reported to have molecular masses in the range of 1,000–20,000 g/mol (Doherty et al., 2011; Thakur et al., 2014).
The chemical structure and properties of lignin vary with the plant from which it is derived, either extracted as a byproduct or extracted directly from lignocellulosic materials (Thakur et al., 2014), as well as extraction method used (Watkins et al., 2014). Lignin offers great advantages such as high abundance, light weight, cost-competitiveness, biodegradability, and environmental friendliness. In view of it being insoluble in water (hydrophobic) and stable in nature, achieving efficient transportation of water and nutrition in the cells of plant (Nordstrom et al., 2013), and having an antioxidant, antimicrobial, and biodegradable nature, along with its CO2 neutrality and reinforcing capability (Pouteau et al., 2003; Boeriu et al., 2004; Doherty et al., 2011; Bertini et al., 2012) it is an excellent alternative for the development of innovative polymer composite materials (Frigerio, 2014; Watkins et al., 2014).
Lignin as a Natural Alternative Source
Due to their contribution to addressing economic and environmental challenges, there has been a noticeable increasing trend in the rigorous study of bio-based composites by researchers from industry and also academia. The study includes the production of rubber composites containing lignin. Lignin is included in rubber products to enhance their properties and also lower their prices (Kumaran and De, 1978; Botros et al., 2006; Feldman, 2016). However, previous studies of lignin-filled rubbers revealed the incompatibility of polar lignin and non-polar rubber (Setua et al., 2000; Kosikova et al., 2007; Barana et al., 2016). This has generated further study of the incorporation of lignin into the rubber matrix by using various mixing methods and modifications to achieve better performance.
The published literature on lignin in the rubber industry is highlighted in Table 1. The hydrophilicity behavior of lignin causes difficulties in terms of the dispersion of lignin in the rubber matrix as well as in the properties of the end rubber product. A lot of approaches have been taken by researchers to improve the process of rubber compound preparation and enhance the flexibility of the final composites (Vieira et al., 2011). One approach to utilize lignin for rubber application is by using simple blending with a rubber matrix (Shukla et al., 1998; Setua et al., 2000; Botros et al., 2006; Barana et al., 2016). However, such rubber compounds suffered from low compatibility and poor disperse-ability. Therefore, further research applied high-temperature dynamic heat treatment (HTDHT) to improve the dispersion of lignin and enhance the properties of the composite (Jiang et al., 2015). Based on various reports, the latex co-precipitation method has achieved excellent outcomes (Ouyang et al., 2009; Asrul et al., 2013; John et al., 2014; Yu et al., 2015, 2016a,b). The process is quite complicated but is a positive approach to enhance the distribution of lignin in the rubber matrix, which results in rubber composites with better mechanical properties. In addition, surface modification using a coupling agent and compatibilizer also has a large impact on the properties of the lignin-filled rubber composite.
Mixing Technique of Lignin Into Rubber Composites
The mixing method is one of the factors that determine the properties of a rubber compound. It may produce poor quality if an unsuitable method is chosen, as this may affect not only the rheological characteristics but also the mechanical and physical properties. This is because, with an unsuitable method, the rubber material does not blend evenly or the reinforcing process may not even be initiated. The main reasons for the incorporation of lignin into rubber compounds as a substitute for an oil-based filler are economical and environmental concerns. In addition, the improvement of properties including compatibility, stabilization, reinforcement, and cost-effectiveness (Botros et al., 2006; Feldman, 2016) is also important. Several mixing methods have been explored to develop the best product properties in terms of mechanical and rheological characteristics. However, the addition of the dry powder form of lignin usually leads to severe coalescence of lignin particles and poor properties in the blends.
Conventional Milling
The used of a conventional two roll mill machine has been common in the rubber industry, especially for tire compounds, and is frequently adopted because of its availability. The properties of the compound depend highly on the skill of the operator and also the ingredients involved. Unfortunately, direct mixing of dry powder lignin into the rubber matrix shows little or almost no reinforcing effect, and the filler is considered to behave as inert (Barana et al., 2016). The reinforcing ability of lignin for rubber depends on two factors: the particle size of the lignin and the interfacial interactions between the lignin and the rubber matrix (Shukla et al., 1998; Botros et al., 2006; Jiang et al., 2015) due to the high content of hydroxyl groups in the lignin surface. The incompatibility obtained was due to a cavity forming around lignin agglomerates, resulting in poor interfacial adhesion and poor compatibility between lignin and rubber.
As an alternative, Jiang et al. (2015) prepared a rubber compound using a laboratory two roll mill in which the lignin was incorporated into ENR. Then, before the mixing process was initiated with other ingredients on the two roll mill, the rubber compounds went through a high-temperature dynamic heat treatment (HTDHT) procedure (180°C) using an internal mixer. The impact of using this method was that lignin was well-dispersed and exhibited great compatibility with ENR, forming a reactive compound. Thus, it is possible to maximize the reinforcing efficiency of lignin by this in situ dispersion and compatibilization strategy when a conventional sulfur-vulcanized system is applied. The success of this method was proven by FESEM photos, as shown in Figure 2, which clarifies the perfect lignin distribution.
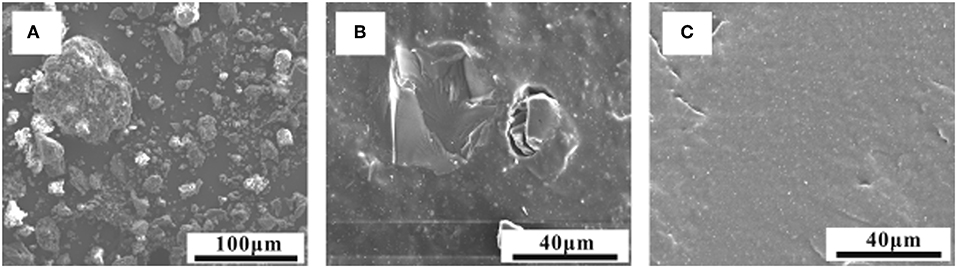
Figure 2. FESEM photos of (A) lignin powder, (B) directly mixed, and (C) heat-treated lignin/ENR composites (this is reproduced with permission from John Wiley and Sons; Jiang et al., 2015).
Latex Co-precipitation
Forming a lignin-rubber compound via latex co-precipitation is a common method used besides other conventional mixing methods to incorporate lignin into rubber latex and form a rubber masterbatch. This method enhanced reinforcement ability and improved the properties of the compound (Košíková and Gregorová, 2005; Asrul et al., 2013; Yu et al., 2015). Previous studies have illustrated that lignin can reach the reinforcement level of carbon black or silica by the co-precipitation of rubber latex and alkaline solutions of lignin (Jiang et al., 2013, 2015). Košíková and Gregorová (2005) reported that the lignin samples act as an active filler in rubber compounds. This is because a positive value of the coefficient of activity, αF, of 0.6631 was obtained and increased the reinforcing characteristic. Furthermore, latex co-precipitation method exhibited a good result, with homogenous distribution in the rubber compound and a finer particle size of lignin formed (Košíková and Gregorová, 2005; Jiang et al., 2013). This was proven by SEM photos, as shown in Figure 3. Furthermore, the flocculation and filtration of lignin/rubber co-precipitates were extremely slow. This also seriously limits the development of lignin-based rubber composites.
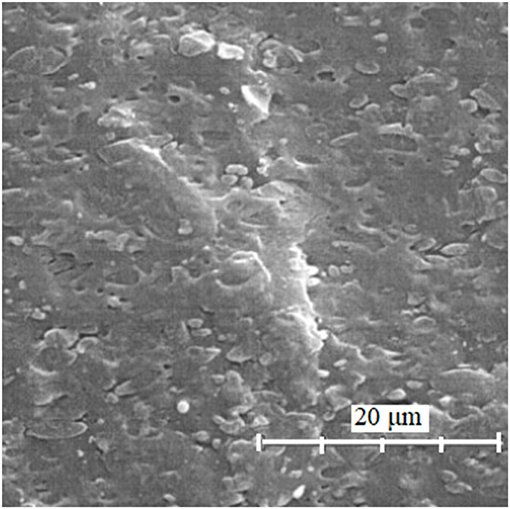
Figure 3. SEM photo of SBR compound containing 50 phr of lignin as a reinforcing filler at a magnification of x5,000 (this is reproduced with permission from John Wiley and Sons; Košíková and Gregorová, 2005).
Modification and Lignin-Based Application
The modification method is known as a method to increase the interfacial bonding strength between lignin and the rubber matrix. This is because the reinforcement effect of lignin is not as good as that of carbon black due to the poor dispersion ability of lignin in rubber and the poor interfacial adhesion between lignin and the rubber matrix. Chemical modification in rubber-based applications is generally carried out either through (1) chemical modification of the lignin surface, (2) the use of substitute chemicals or additives during mixing that contain functional groups that are capable of forming a bridge between lignin and rubber matrix, or (3) the rubber matrix being modified to achieve better compatibility and end-product properties. Researchers have tried many approaches to improve the reinforcement effect of lignin and rubber (Bahl et al., 2014a,b; Bova et al., 2016; Tran et al., 2016; Ikeda et al., 2017; Miao and Hamad, 2017) and have achieved various levels of success in enhancing the adhesion and dispersion of lignin in the rubber matrix, as has been reported in previous studies (Laurichesse and Avérous, 2014; Thakur et al., 2014).
Techniques using coupling agents and adhesion agents for improving interfacial bonding have also been reported (Bahl et al., 2014b; Wang et al., 2018). These approaches produced covalent bonds between the lignin and the rubber matrix, thus enhancing the interfacial bonding. Furthermore, the chemical modification aims to improve the compatibility between lignin filler and non-polar rubber matrices by surface modification of lignins such as with hexamethylenetetramine (Setua et al., 2000; Frigerio et al., 2014; Thakur et al., 2014; Jiang et al., 2015) and cyclohexylamine (Bahl and Jana, 2014). This treatment basically involves the reaction of lignin and formaldehyde and is reported to provide excellent abrasion resistance and enhancement of tire properties.
A recent new approach to enhancing the dispersion and compatibility of lignin in the rubber matrix was to introduce the construction of a dual crosslinking network. A dual crosslinking network consists of the covalent bonds formed between sulfur and carbon atoms in rubber and sacrificial non-covalent bonds formed among lignins and Zn2+ ions. The development of high-performance lignin-filled rubber was explored by adding Zn-based coordination bonds (Wang et al., 2018) and forming networks consisting of sulfur covalent bonds and the dynamic coordination of sacrificial bonds, as shown in Figure 4. The mechanism of sacrificial bonding provided the outstanding properties of a strong and tough rubber compound (Sun et al., 2012; Schmitt et al., 2015; Zhang et al., 2016; Wang et al., 2018).
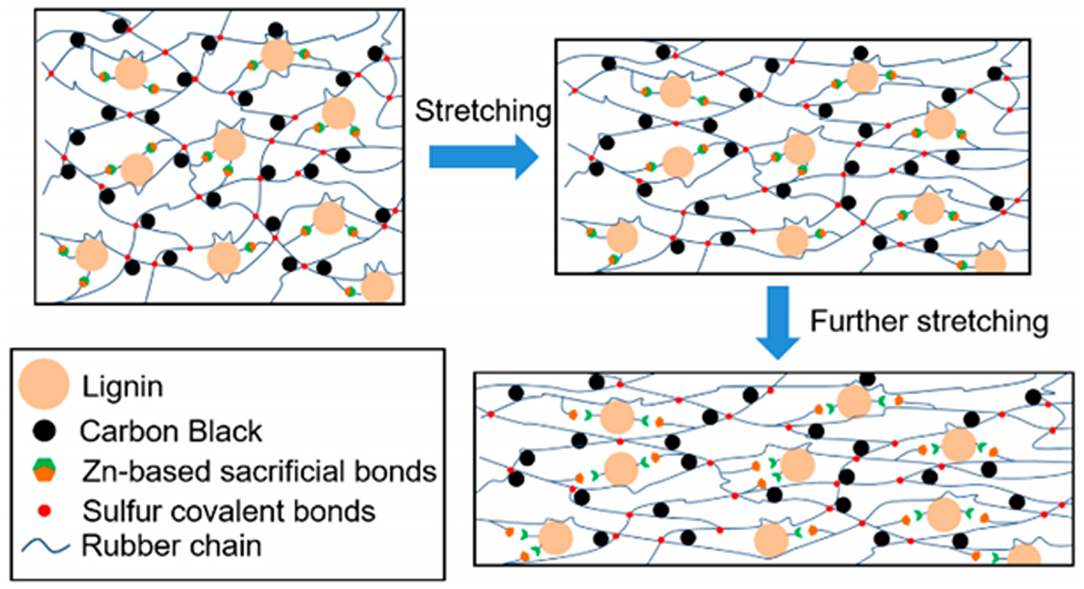
Figure 4. Schematic representation of a dual crosslinking network for lignin/carbon black/NBR composites [this is reproduced with permission from MDPI (Basels); Wang et al., 2018].
In addition, fabricating nano-lignin and performing nano-scale distribution using colloidal lignin-Poly(diallyldimethylammonium chloride) (PDADMAC) complexes (LPCs) showed an enhancement of the reinforcement ability (Jiang et al., 2013) in NR/lignin nanocomposites, as shown in Figure 5. Lignin was viewed as an anionic polyelectrolyte (colloidal) when phenolic hydroxyl and carboxylic groups were ionized. As a result, LPCs were homogeneously distributed in the NR matrix, which resulted in improved mechanical properties and thermal and thermo-oxidative stability for the NR/LPC composites. Pillai and Renneckar (2009) and Yang et al. (2005) showed, through FTIR spectra, there was interaction between lignin units and PDADMAC chains.
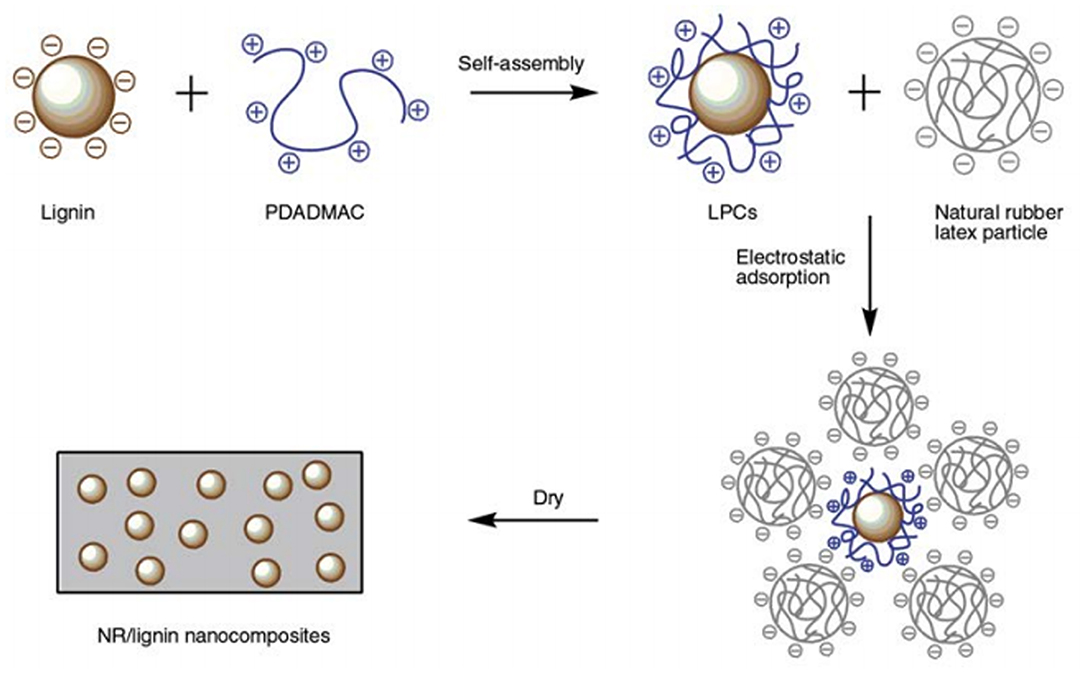
Figure 5. Schematic representation of the fabrication of nanolignin for the preparation of natural rubber (NR)/lignin nanocomposite (this is reproduced with permission from Budapest University of Technology and Economics, Faculty of Mechanical Engineering, Department of Polymer Engineering; Jiang et al., 2013).
Another method suggested is to graft polymers onto lignin using controlled radical polymerization, and this method has shown advantages (Wang et al., 2011) over modified lignin. This approach improved the surface reactivity by converting phenolic or aliphatic hydroxyl group into new functionalized groups like ketone or aldehyde, hence enhancing the reinforcement characteristic compared to the crude version (Shukla et al., 1998). However, the grafting method also has high potential for modification, since it achieves comparable results to the co-precipitation mixing method but has a shorter process time.
Furthermore, chemical modification such as acetylation of hydroxyl groups has also been reported to achieve the same improvement in terms of compatibility and dispersion in the rubber matrix (Bertini et al., 2012; Barana et al., 2016). However, the reliability of phenolic hydroxyl groups must be safeguarded, as their modification results in the inhibition of antioxidant properties (Sadeghifar and Argyropoulos, 2015). Surface modifications have provided the external surface of lignin agglomerates with a better affinity toward the rubber matrix. In addition, the interaction of sodium lignosulfonates (SLS) with carbon nanotubes was studied by Liu et al. (2007). A similar study looked at the surface functionalization of MWNTs using Kraft lignin and its use in energy storage applications (Milczarek and Nowicki, 2013).
Moreover, researchers are also paying a lot of attention to hybrid technologies with carbon black (Bahl et al., 2014a), silica (Strzemiecka et al., 2016; Yu et al., 2016a), montmorillonite (Cao et al., 2013; Jiang et al., 2014), and layered double hydroxides (LDHs) (Xiao et al., 2013). This technique mostly provides good reinforcing ability to the rubber compound. According to Bahl et al. (2014a), a hybrid filler between lignin and carbon black could lower the viscoelastic loss. Meanwhile, a lignin-montmorillonite hybrid filler was prepared by direct dehydration of the mixture of black liquor and montmorillonite and was used to reinforce acrylonitrile butadiene rubber (NBR) (Cao et al., 2013). However, this method is time-consuming and is not suitable for large-scale manufacturing. Furthermore, the modification of lignin in a rubber compound by using a hybrid method is unsatisfactory in terms of lignin dispersion and lignin–rubber interaction.
Reinforcement Studies of Lignin-Rubber Composites
The addition of reinforcing agents often changes the properties of a rubber composite. It not only improves the mechanical properties, such as toughness, but also influences the thermal properties. Many researchers have focused on different approaches, and some of them have used different accelerator systems (Kumaran and De, 1978) and different types of crosslink agents (Nando and De, 1980) to study the network structure involved in lignin-filled rubber composites in detail, hence evaluating the properties obtained.
Cure Properties
The effect of the substitution of carbon black with natural lignin has been studied in great depth by researchers. Gradual replacement of carbon black with lignin has increased the scorch and optimum cure time, tS2 and t90, respectively, and reduced the curing rate index (CRI) and the crosslink density of the lignin-filled rubber composite. The inclusion of lignin into the rubber matrix delayed the vulcanization of rubber due to the effect of radical scavenging by hindered phenol groups in lignin (Liu et al., 2013; Wang et al., 2018). Torque values were decreased by the presence of lignin, indicating worse interfacial adhesion between unmodified lignin and rubber matrix segments compared to solely carbon black (Wang et al., 2018). However, researchers reported that lignin was dispersed well in natural rubber and made the compound more scorch-resistant and improved the optimum cure time (Nando and De, 1980).
Curing behavior is also dependent on the curing system used. The distribution of different types of crosslinks is affected by the reversion time, and the inclusion of lignin showed that it actually takes part during the vulcanization process and that the mechanism is due to the thermal stability itself. Besides, the conventional vulcanization (CV) system delayed the optimum cure time, but the semi-efficient (semi-EV) and efficient vulcanization (EV) systems increased the cure rate (Nando and De, 1980; Shukla et al., 1998; Kakroodi and Sain, 2016). Nevertheless, some studies reported that the presence of lignin decreased the crosslink density and the number of polysulphidic crosslinks while maintaining the number of disulfidic and monosulfidic crosslinks (Kumaran and De, 1978; Kakroodi and Sain, 2016). They suggested that the incorporation of lignin in the rubber matrix masked some of the cross-linking sites on the rubber molecules. Normally, acidic functional groups in lignin particles should interrelate with the basic rubber components.
Mechanical Properties
In practice, the interaction of filler particles with one another does not constantly yield the expected and desired effects. Theoretically, the mechanical properties shown differently depend on the modification and formulation used, as summarized in Table 2. The properties show significant improvement compared to control samples. Hybrid fillers were reported by Wang et al. (2002) as the best way to gain the optimum balance of tire properties, particularly rolling resistance, wet traction, and wear resistance. The combination of lignin with montmorillonite (Cao et al., 2013; Jiang et al., 2014), layered double hydroxides (Xiao et al., 2013), and carbon black (Košíková and Gregorová, 2005; Xiao et al., 2013; Bahl et al., 2014a) as hybrid fillers in rubber composites resulted in higher tensile strength, thermal stability, and low rolling resistance. This was because the components of the hybrid filler worked together, with the lignin suppressing the formation of a filler network and, in return, the other fillers assisting in the dispersion of lignin in the rubber matrix. Despite this, time consumption is an issue in the preparation of these lignin-based hybrid fillers. Moreover, the organic solvent used in this process is unfavorable for industrial production (Jiang et al., 2015).
The incorporation of lignin into the rubber matrix can prevent the loss of mechanical properties that arises due to oxidative degradation. Setua et al. (2000) reported that unmodified lignin showed poor tensile strength compared to DCP-modified lignin. The tensile strength at failure of vulcanized rubber reflected the true reinforcement behavior of the hybrid filler, as the tensile strength and elongation at break were the failure properties. The result obtained by Bahl et al. (2014a) for the tensile strength of the SBR-30/LS/CB compound with an LS:CB ratio by weight of 10:90 (30 phr) was closed to that of the compound of SBR-30/CB (30 phr). However, the tensile strength dropped dramatically for the hybrid filler compound with a 20:80 LS:CB weight ratio, as shown in Figure 6. This was due to strong interaction between lignin and carbon black, which resisted the breakage of the networks and prevented dispersion by shear forces during compounding. Furthermore, the incorporation of lignin improved the Young's modulus of the rubber compounds in the whole range of deformations without compromising elongation at break (Barana et al., 2016). This was due to the protection given by lignin against degradation processes in the rubber matrix during mixing with high mechanical and thermo-oxidative stresses. However, flex crack resistance could sometimes be improved even at lower cross-link density of the rubber, and there was also an increase in crack growth resistance due to the higher percentage of disulfidic crosslinks (Kakroodi and Sain, 2016).
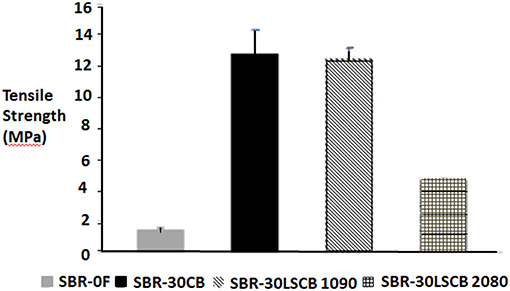
Figure 6. Tensile strength of SBR vulcanizates filled with 30 phr filler (this is reproduced with permission from Elsevier; Bahl et al., 2014a).
Thermal Properties
The thermal stability of rubber composites was investigated through thermal decomposition, as displayed in Table 3 (Jiang et al., 2013). Environmental stresses such as oxygen and heat led to undesirable chemical changes in polymers, such as loss of ductility, loss of surface quality, and changes in their molecular weights and structures (Kakroodi and Rodrigue, 2013; Kakroodi and Sain, 2016). The changes to rubber molecular weights were due to chain scission followed by cross-linking of the produced macro-radicals with unsaturated C=C double bonds. Furthermore, the formation and accumulation of small molecules such as H2, carbon monoxide, carbon dioxide, and monomers can cause cracks and crazes in the rubber. Nevertheless, the inclusion of lignin into the natural rubber compound enhanced the thermal stability. The strong interaction among lignin and NR molecular chains provided various effects like branching, surface, and size effects (Peng et al., 2007; Jiang et al., 2013).
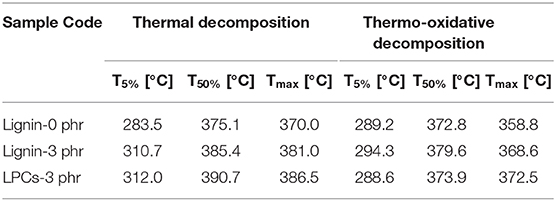
Table 3. Comparison of the thermal and thermo-oxidative decomposition for NR without lignin, NR/lignin, and NR/LPCs composites (this is reproduced with permission from Budapest University of Technology and Economics, Faculty of Mechanical Engineering, Department of Polymer Engineering; Jiang et al., 2013).
Furthermore, the hindered complex phenolic hydroxyls of lignin acted to improve and stabilize the reaction during thermal testing, which was initiated by oxygen and its radical types (Pouteau et al., 2003; Barana et al., 2016) as shown in Figure 7. Different types of lignin have different concentrations of phenolic hydroxyls that contribute to the stability of the polymer. Sometimes, the modification of lignin showed lower thermal stability as compared to unmodified lignin (Jiang et al., 2013). This might be due to the interaction within phenolic radical cations, as this would weaken the ability of phenolic hydroxyls to scavenge free radicals in lignin. Besides, lignin has been used to improve thermal properties, since it acts as a flame retardant and has good thermal insulating properties (Xing et al., 2013). In addition, the lignin gives protection to the rubber matrix against degradation processes during mixing at high mechanical and thermo-oxidative stresses.
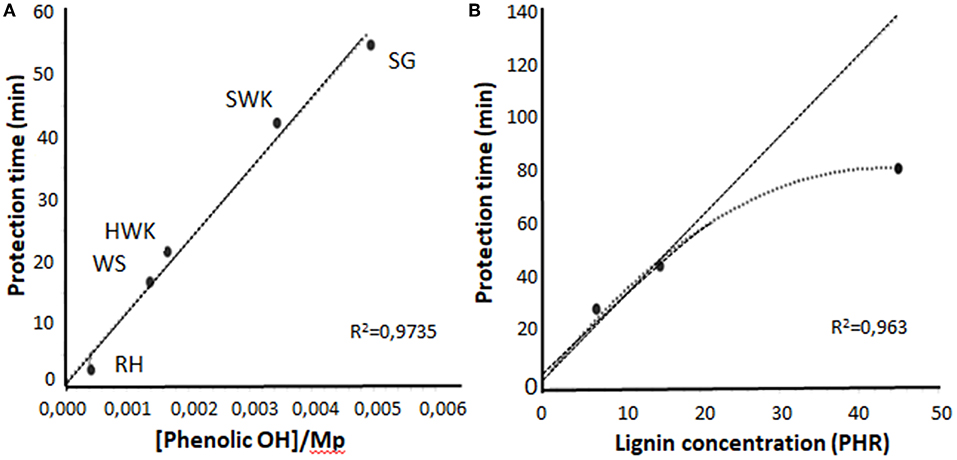
Figure 7. Influence of the concentration of phenolic hydroxyls of different types of lignin (A) and SWK lignin concentration (B) on the protection time (OIT) (this reprinted with permission from Barana et al., 2016; Copyright (2016) American Chemical Society).
Dynamic Mechanical Properties (DMA)
The dynamic mechanical behavior of a rubber compound is generally characterized using DMA testing and analysis. The storage modulus (E') and loss tangent (tan δ) against temperature have been analyzed to observe the influence of Kraft lignin on the thermomechanical properties of natural rubber composites. The storage modulus showed a positive correlation with the elastic modulus of rubber composites and was proportionate to the crosslink density (Geethamma et al., 2005; Cao et al., 2013; Yu et al., 2015). Meanwhile, the loss tangent is related to the energy dissipation as heat (Jiang et al., 2015). According to Datta and Parcheta (2017), the incorporation of Kraft lignin in natural rubber composites leads to a decrease in the stiffness and an increase in the damping capacity of the natural rubber matrix. The value of the storage modulus strongly decreased in the temperature range between −60 and −20°C, which is related to the glass transition temperature, Tg, of the natural rubber matrix; this can be observed from the midpoint of the decreasing part of the curve approaching Tg. This is closely associated with the relaxation of the natural rubber chains. The cooperative motion of macromolecules induces the dissipation of energy at a temperature of the maximum tan δ. After −25°C, the curve characteristics are related to the remaining crystalline regions melting in the macromolecule chains from the natural rubber matrix.
However, Robertson and Rackaitis (2011) mentioned that the increment in storage modulus implied the characteristic of materials with higher stiffness, which should be associated with the addition of rigid lignin particles, enhancement of filler–rubber interactions, and the reinforcing nature of lignin on rubber materials. Increasing the lignin content in rubber composites shifted its tan δ peaks to higher temperatures and continually increased the Tg taken at the maximum value of tan δ peaks. This phenomenon can be clearly seen in case of the utilization of lignin in ENR rubber, in which the molecules of ENR are covalently bonded to lignin particles during the mixing process in the presence of high temperature. The bonds strongly restrict the mobility of the chain segments of ENR. Besides, the tan δ peak height significantly decreases with increasing lignin content. As reported earlier, the increase in the Tg of nanoparticle-filled polymer composite was generally <10°C, which indicates the uniform dispersion of lignin and changes in the network structure of lignin/ENR composites (Jiang et al., 2015).
Oil/Solvent Resistance Properties
Less attention has been given to the topic of oil resistance characteristics. However, the hydrophilic properties of lignin will give advantages to the rubber compound, improving its oil resistance characteristics (Asrul et al., 2013), and will have a good influence on the natural rubber compound, as it has low oil and solvent resistance. The degree of absorption also depends on the type of oil used. The presence of lignin, even in a small amount, in the rubber significantly reduced the adsorption level of a rubber compound, as reported by Asrul et al. (2013). This indicated the formation of chain entanglement from secondary bonding between lignin and rubber molecules (Figure 8), affecting the mass changes of the lignin-filled rubber sample. These characteristics impacted the properties of the rubber compound, which reduced the stiffness and strength of the compound as well as giving it poor chemical resistance and low dimensional stability. However, the opposite effect has been seen with a modified lignin-filled rubber compound, which had better swelling resistance, even higher than carbon black-filled rubber. This was highlighted by Setua et al. (2000), who showed that surface treatment increased the polarity of the lignin.
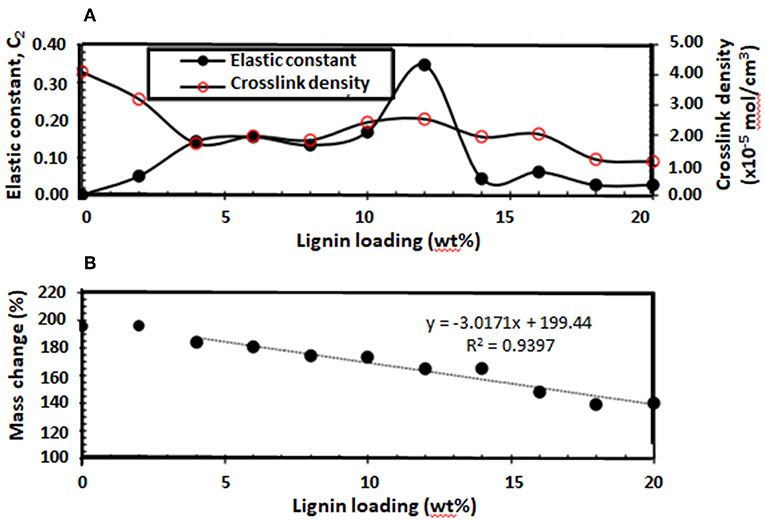
Figure 8. Effect of lignin loadings on the (A) crosslink density and elastic constant, C2, and (B) percentage mass change (this is reproduced with permission from Asrul et al., 2013).
Future Perspectives
Lignin has unique properties and has attracted many researchers to explore and determine its potential applications in a variety of industries. The delignification processes of lignin are well-documented, and many of its main properties have been reported. However, more studies are required on product commercialization and manufacturing processes for composites based on lignin. The main reason for this paper is to cause scientists and researchers to look at the potential of lignin as a reinforcing filler in the rubber industry as a substitute for carbon black due to the depletion of oil stock and the harm the latter brings to the environment. Many studies in recent years have focused on the utilization of lignin in synthetic rubber and less so in natural rubber. Incorporating a lignin particle into an unsaturated chain rubber matrix may have a toughening effect. Numerous experiments have been performed since the 1940s to determine which mixing methods contribute good composite properties. Until now, simple and efficient ways to formulate lignin/rubber composites with excellent interfacial interaction and dispersion quality are yet to be found. However, we have here compiled and compared the best modification and mixing methods for lignin as a reinforcing filler or an additive to rubber compounds; this can now be used for future studies. The appropriate method will play an important role in providing optimized properties, especially for green tire applications.
Author Contributions
NO, MH, KS, and NH contributed to the conception and revision of the manuscript. The manuscript was mainly written by NM and was edited by NO.
Funding
The authors thank the Fundamental Research Grant Scheme (203.PBAHAN.6071350) and MyPhD for a scholarship (NM) and the Ministry of Higher Education (MoHE), Malaysia and Universiti Sains Malaysia (USM) Bridging Grant (304.PKIMIA.6316041) for financial support.
Conflict of Interest
The authors declare that the research was conducted in the absence of any commercial or financial relationships that could be construed as a potential conflict of interest.
Acknowledgments
The authors would like to express their gratitude to the School of Materials and Mineral Resources Engineering (SMMRE), Universiti Sains Malaysia (USM), Prince of Songkhla University, Pattani Campus (PSU), Ministry of High Education (MoHE) of Malaysia for the MyPhD scholarship, and the Postgraduate Research Attachment (PGRA) Fund, Institute of Postgraduate Studies, USM.
References
Agarwal, K., Prasad, M., Sharma, R. B., and Setua, D. K. (2014). Novel bio-degradable lignin reinforced NBR composites. Int. J. Energy Eng. 4, 47–62.
Asrul, M., Othman, M., Zakaria, M., and Fauzi, M. S. (2013). Lignin filled unvulcanisednatural rubber latex: effectsof lignin on oil resistance, tensile strength and morphology of rubber films. Int. J. Eng. Sci. Invent. 2, 38–43.
Atashi, H., and Shiva, M. (2010). Formulation for passenger tread tire compound based on styrene butadiene rubber/cis-butadiene rubber/natural rubber blend and semi-dispersible silica/carbon black filler system. Asian J. Chem. 22, 7519–7530.
Attharangsan, S., Ismail, H., Bakar, M. A., and Ismail, J. (2012). Carbon black (CB)/rice husk powder (RHP) hybrid filler-filled natural rubber composites: Effect of CB/RHP ratio on property of the composites. Polym. Plast. Technol. Eng. 51, 655–662. doi: 10.1080/03602559.2012.662256
Bahl, K., and Jana, S. C. (2014). Surface modification of lignosulfonates for reinforcement of styrene-butadiene rubber compounds. J. Appl. Polym. Sci. 131, 1–9. doi: 10.1002/app.40123
Bahl, K., Miyoshi, T., and Jana, S. C. (2014a). Hybrid fillers of lignin and carbon black for lowering of viscoelastic loss in rubber compounds. Polymer 55, 3825–3835. doi: 10.1016/j.polymer.2014.06.061
Bahl, K., Swanson, N., Pugh, C., and Jana, S. C. (2014b). Polybutadiene-g-polypentafluorostyrene as a coupling agent for lignin-filled rubber compounds. Polymer 55, 6754–6763. doi: 10.1016/j.polymer.2014.11.008
Bajpai, P. K., Meena, D., Vatsa, S., and Singh, I. (2013). Tensile behavior of nettle fiber composites exposed to various environments. J. Nat. Fibers 10, 244–256. doi: 10.1080/15440478.2013.791912
Barana, D., Ali, S. D., Salanti, A., Orlandi, M., Castellani, L., Hanel, T., et al. (2016). Influence of lignin features on thermal stability and mechanical properties of natural rubber compounds. ACS Sustain. Chem. Eng. 4, 5258–5267. doi: 10.1021/acssuschemeng.6b00774
Basfar, A. A., Abdel-Aziz, M. M., and Mofti, S. (2002). Influence of different curing systems on the physico-mechanical properties and stability of SBR and NR rubbers. Radiat. Phys. Chem. 63, 81–87. doi: 10.1016/S0969-806X(01)00486-8
Beilen, J. B., and Van Poirier, Y. (2007). Guayule and russian dandelion as alternative sources of natural rubber. Crit. Rev. Biotechnol. 27, 217–231. doi: 10.1080/07388550701775927
Benedict, C. R., Greer, P. J., and Foster, M. A. (2008). The physiological and biochemical responses of guayule to the low temperature of the Chihuahuan Desert in the biosynthesis of rubber. Ind. Crops Prod. 27, 225–235. doi: 10.1016/j.indcrop.2007.09.003
Benko, D. A., Hahn, B. R., Cohen, M. P., Dirk, S. M., and Cicotte, K. N. (2014). Functionalized lignin, Rubber Containing Functionalized Lignin and Products Containing Such Rubber Composition. United States Patent No. 8664305B2, 6–12.
Bertini, F., Canetti, M., Cacciamani, A., Elegir, G., Orlandi, M., and Zoia, L. (2012). Effect of ligno-derivatives on thermal properties and degradation behavior of poly(3-hydroxybutyrate)-based biocomposites. Polym. Degrad. Stab. 97, 1979–1987. doi: 10.1016/j.polymdegradstab.2012.03.009
Boeriu, C. G., Bravo, D., Gosselink, R. J. A., and Van Dam, J. E. G. (2004). Characterisation of structure-dependent functional properties of lignin with infrared spectroscopy. Industr. Crops Products 20, 205–218. doi: 10.1016/j.indcrop.2004.04.022
Bogoeva-Gaceva, G., Avella, M., Malinconico, M., Buzarovska, A., Grozdanov, A., Gentile, G., et al. (2007). Natural fiber eco-composites. Polym. Compos. 28, 98–107. doi: 10.1002/pc.20270
Botros, S. H., Eid, M. A. M., and Nageeb, Z. A. (2006). Thermal stability and dielectric relaxation of natural rubber/soda lignin and natural rubber/thiolignin composites. J. Appl. Polym. Sci. 99, 2504–2511. doi: 10.1002/app.22865
Bova, T., Tran, C. D., Balakshin, M. Y., Chen, J., Capanema, E. A., and Naskar, A. K. (2016). An approach towards tailoring interfacial structures and properties of multiphase renewable thermoplastics from lignin–nitrile rubber. Electron. Suppl. Mater. Green Chem. 18, 5423–5437. doi: 10.1039/C6GC01067A
Braum, M. V., and Jacobi, M. A. M. (2017). Silica grafted with epoxidized liquid polybutadienes: its behavior as filler for tire tread compounds. Rubber Chem. Technol. 90, 173–194. doi: 10.5254/rct.16.83760
Brennan, J. J., Jermyn, T. E., and Boonstra, B. B. (1964). Carbon black–polymer interaction: a measure of reinforcement. J. Appl. Polym. Sci. 8, 2687–2706. doi: 10.1002/app.1964.070080615
Cao, Z., Liao, Z., Wang, X., Su, S., Feng, J., and Zhu, J. (2013). Preparation and properties of NBR composites filled with a novel black liquor – montmorillonite complex. J. Appl. Polym. Sci. 127, 3725–3730. doi: 10.1002/app.37984
Capanema, E. A., Balakshin, M. Y., and Kadla, J. F. (2005). Quantitative characterization of a hardwood milled wood lignin by nuclear magnetic resonance spectroscopy. J. Agric. Food Chem. 53, 9639–9649. doi: 10.1021/jf0515330
Chakraborty, S., Sengupta, R., Dasgupta, S., Mukhopadhyay, R., Bandyopadhyay, S., Joshi, M., et al. (2009). Synthesis and characterization of styrene butadiene rubber-bentonite clay nanocomposites. Polym. Eng. Sci. 49, 1279–1290. doi: 10.1002/pen.21367
Chang, Y.-W., Mishra, J. K., Cheong, J.-H., and Kim, D.-K. (2007). Thermomechanical properties and shape memory effect of epoxidized natural rubber crosslinked by 3-amino-1,2,4-triazole. Polym. Int. 56, 694–698. doi: 10.1002/pi.2203
Cheng, T.-H. (1963). Utilization of wild plants in communist China. Econ. Bot. 19, 3–15. doi: 10.1007/BF02971180
Cornish, K. (2017). Alternative natural rubber crops: why should we care? Technol. Innov. 18, 245–256. doi: 10.21300/18.4.2017.245
Dashtban, M., Schraft, H., Syed, T. A., and Qin, W. (2010). Fungal biodegradation and enzymatic modification of lignin. Int. J. Biochem. Mol. Biol. 1, 36–50.
Datta, J., and Parcheta, P. (2017). A comparative study on selective properties of Kraft lignin–natural rubber composites containing different plasticizers. Iran. Polym. J. 26, 453–466. doi: 10.1007/s13726-017-0534-0
Datta, J., Parcheta, P., and Surówka, J. (2017). Softwood-lignin/natural rubber composites containing novel plasticizing agent: preparation and characterization. Ind. Crops Prod. 95, 675–685. doi: 10.1016/j.indcrop.2016.11.036
Datta, R. N., Huntink, N. M., Datta, S., and Talma, A. G. (2007). Rubber vulcanizates degradation and stabilization. Rubber Chem. Technol. 80, 436–480. doi: 10.5254/1.3548174
De Paoli, M.-A., and Furlan, L. T. (1985). Sugar cane bagasse-lignin as photo-stabilizer for butadiene rubber. Polym. Degrad. Stab. 11, 327–337. doi: 10.1016/0141-3910(85)90036-9
Doherty, W. O. S., Mousavioun, P., and Fellows, C. M. (2011). Value-adding to cellulosic ethanol: lignin polymers. Ind. Crops Prod. 33, 259–276. doi: 10.1016/j.indcrop.2010.10.022
Drogin, I. (1968). Carbon black. J. Air Pollut. Control Assoc. 18, 216–228. doi: 10.1080/00022470.1968.10469118
Ehrburger-Dolle, F., Lahaye, J., and Misono, S. (1994). Percolation in carbon black powders. Carbon N. Y. 32, 1363–1368. doi: 10.1016/0008-6223(94)90123-6
Eichhorn, S. J., Dufresne, A., Aranguren, M., Marcovich, N. E., Capadona, J. R., Rowan, S. J., et al. (2010). Review: current international research into cellulose nanofibres and nanocomposites. J. Mater. Sci. 45, 1–33. doi: 10.1007/s10853-009-3874-0
Erdocia, X., Prado, R., Corcuera, M. Á., and Labidi, J. (2014). Influence of reaction conditions on lignin hydrothermal treatment. Front. Energy Res. 2:13. doi: 10.3389/fenrg.2014.00013
Faruk, O., Bledzki, A. K., Fink, H. P., and Sain, M. (2012). Biocomposites reinforced with natural fibers: 2000-2010. Prog. Polym. Sci. 37, 1552–1596. doi: 10.1016/j.progpolymsci.2012.04.003
Feldman, D. (2016). Lignin nanocomposites. J. Macromol. Sci. Part A Pure Appl. Chem. 53, 382–387. doi: 10.1080/10601325.2016.1166006
Fitigau, I. F., Peter, F., and Boeriu, C. G. (2013). Oxidative polymerization of lignins by laccase in water-acetone mixture. Acta Biochim. Pol. 60, 817–822. doi: 10.18388/abp.2013_2065
Frigerio, P. (2014). Biopolymers in Elastomers: Lignins as Biofiller for Tyre Compound. Ph.D. thesis, University of Milano Bicacco, Italy.
Frigerio, P., Zoia, L., Orlandi, M., Hanel, T., and Castellani, L. (2014). Application of sulphur-free lignins as a filler for elastomers: effect of hexamethylenetetramine treatment. BioResources 9, 1387–1400. doi: 10.15376/biores.9.1.1387-1400
Fukahori, Y. (2003). The mechanics and mechanism of the carbon black reinforcement of elastomers. Rubber Chem. Technol. 76, 548–566. doi: 10.5254/1.3547760
Geethamma, V. G., Kalaprasad, G., Groeninckx, G., and Thomas, S. (2005). Dynamic mechanical behavior of short coir fiber reinforced natural rubber composites. Compos. Part A Appl. Sci. Manuf. 36, 1499–1506. doi: 10.1016/j.compositesa.2005.03.004
Gosselink, R. J. A., Abächerli, A., Semke, H., Malherbe, R., Käuper, P., Nadif, A., et al. (2004). Analytical protocols for characterisation of sulphur-free lignin. Ind. Crops Prod. 19, 271–281. doi: 10.1016/j.indcrop.2003.10.008
Gregorová, A., Košíková, B., and Moravčík, R. (2006). Stabilization effect of lignin in natural rubber. Polym. Degrad. Stab. 91, 229–233. doi: 10.1016/j.polymdegradstab.2005.05.009
Guy, L., Daudey, S., Cochet, P., and Bomal, Y. (2009). New insights in the dynamic properties of precipitated silica filled rubber using a new high surface silica. Raw Mater. Appl. 62, 383–391.
Hall, D. E., and Moreland, J. C. (2001). Fundamentals of rolling resistance. Rubber Chem. Technol. 74, 525–539. doi: 10.5254/1.3547650
Hämäläinen, V., Grönroos, T., Suonp,ää, A., Heikkil,ä, M. W., Romein, B., Ihalainen, P., et al. (2018). Enzymatic processes to unlock the lignin value. Front. Bioeng. Biotechnol. 6:20. doi: 10.3389/fbioe.2018.00020
Hamed, G. R. (2012). “Materials and compounds,” in Engineering with Rubber, 11–36. doi: 10.3139/9783446428713.002
Hao, P. T., Ismail, H., and Hashim, A. S. (2001). Study of two types of styrene butadiene rubber in tire tread compounds. Polymer Test. 20, 539–544. doi: 10.1016/S0142-9418(00)00073-8
Hilonga, A., Kim, J., Sarawade, P. B., Quang, D. V., Shao, G. N., Elineema, G., et al. (2012). Synthesis of mesoporous silica with superior properties suitable for green tire. J. Ind. Eng. Chem. 18, 1841–1844. doi: 10.1016/j.jiec.2012.04.015
Hirayama, D., and Saron, C. (2012). Chemical modifications in styrene-butadiene rubber after microwave devulcanization. Ind. Eng. Chem. Res. 51, 3975–3980. doi: 10.1021/ie202077g
Hoshikawa, Y., An, B., Kashihara, S., Ishii, T., Ando, M., Fujisawa, S., et al. (2016). Analysis of the interaction between rubber polymer and carbon black surfaces by efficient removal of physisorbed polymer from carbon-rubber composites. Carbon N. Y. 99, 148–156. doi: 10.1016/j.carbon.2015.12.003
Hu, L., Pan, H., Zhou, Y., and Zhang, M. (2011). Methods to improve lignin's reactivity as a phenol substitute and as replacement for other phenolic. Bioresources 6, 3515–3525. doi: 10.15376/biores.6.3.3515-3525
Huang, J. C. (2002). Carbon black filled conducting polymers and polymer blends. Adv. Polym. Technol. 21, 299–313. doi: 10.1002/adv.10025
Hussin, M. H., Rahim, A. A., Mohamad Ibrahim, M. N., Perrin, D., Yemloul, M., and Brosse, N. (2014). Impact of catalytic oil palm fronds (OPF) pulping on organosolv lignin properties. Polym. Degrad. Stab. 109, 33–39. doi: 10.1016/j.polymdegradstab.2014.06.016
Ignatz-Hoover, F., To, B. H., Datta, R. N., De Hoog, A. J., Huntink, N. M., and Talma, A. G. (2003). Chemical additives migration in rubber. Rubber Chem. Technol. 76, 747–768. doi: 10.5254/1.3547765
Ikeda, Y., Junkong, P., Yokohama, H., Kitano, R., Phakkeeree, T., Kato, A., et al. (2017). Reinforcing biofiller “Lignin” for high performance green natural rubber nanocomposites. RSC Adv. 7, 5222–5231. doi: 10.1039/C6RA26359C
Jagadale, S. C., Chavan, R. P., Rajkumar, K., Shinde, D. N., and Patil, C. L. (2016). Lignin as a plasticizer in nitrile rubber, it's effect on properties. Int. J. Res. Eng. Appl. Sci. 6, 78–84.
Jawjit, W., Kroeze, C., and Rattanapan, S. (2010). Greenhouse gas emissions from rubber industry in Thailand. J. Clean. Prod. 18, 403–411. doi: 10.1016/j.jclepro.2009.12.003
Jiang, C., He, H., Jiang, H., Ma, L., and Jia, D. M. (2013). Nano-lignin filled natural rubber composites: preparation and characterization. Express Polym. Lett. 7, 480–493. doi: 10.3144/expresspolymlett.2013.44
Jiang, C., He, H., Yao, X., Yu, P., Zhou, L., and Jia, D. (2015). In situ dispersion and compatibilization of lignin/epoxidized natural rubber composites: Reactivity, morphology and property. J. Appl. Polym. Sci. 132, 1–10. doi: 10.1002/app.42044
Jiang, C., He, H., Yu, P., Wang, D. K., Zhou, L., and Jia, D. M. (2014). Plane-interface-induced lignin-based nanosheets and its reinforcing effect on styrene-butadiene rubber. Express Polym. Lett. 8, 619–634. doi: 10.3144/expresspolymlett.2014.66
John, S., Issac, J. M., and Alex, R. (2014). Mechanical properties of natural rubber composites reinforced with lignin from Caryota fibre. Int. J. Emerg. Technol. Adv. Eng. 4, 567–570.
Kaewsakul, B. W., Sahakaro, K., and Dierkes, W. K. (2014). “Flocculation kinetics and filler-rubber interaction in silica-reinforced natural rubber compounds,” in Presented at the Fall 186th Technical Meeting of Rubber Division (Nashville, TN: ACS, 1–20.
Kakroodi, A. R., Cheng, S., Sain, M., and Asiri, A. (2014). Mechanical, thermal, and morphological properties of nanocomposites based on polyvinyl alcohol and cellulose nanofiber from Aloe vera rind. J. Nanomater. 2014:903498. doi: 10.1155/2014/903498
Kakroodi, A. R., Kazemi, Y., and Rodrigue, D. (2013). Mechanical, rheological, morphological and water absorption properties of maleated polyethylene/hemp composites: effect of ground tire rubber addition. Compos. Part B Eng. 51, 337–344. doi: 10.1016/j.compositesb.2013.03.032
Kakroodi, A. R., and Rodrigue, D. (2013). Degradation behavior of maleated polyethylene/ground tire rubber thermoplastic elastomers with and without stabilizers. Polym. Degrad. Stab. 98, 2184–2192. doi: 10.1016/j.polymdegradstab.2013.08.017
Kakroodi, A. R., and Sain, M. (2016). “Lignin-reinforced rubber composites,” in Lignin in Polymer Composites, eds O. Faruk and M. Sain (Waltham, MA: Mathew Deans), 195–206. doi: 10.1002/marc.201900059
Kazemi, Y., Cloutier, A., and Rodrigue, D. (2013). Mechanical and morphological properties of wood plastic composites based on municipal plastic waste. Polym. Compos. 34, 487–493. doi: 10.1002/pc.22442
Khalil, H. P. S. A., Noriman, N. Z., Ahmad, M. N., Ratnam, M. M., and Fuaad, N. A. N. (2007). Polyester composites filled carbon black and activated carbon from bamboo (gigantochloa scortechinii): physical and mechanical properties. J. Reinf. Plast. Compos. 26, 305–320. doi: 10.1177/0731684407065066
Košíková, B., and Gregorová, A. (2005). Sulfur-free lignin as reinforcing component of styrene-butadiene rubber. J. Appl. Polym. Sci. 97, 924–929. doi: 10.1002/app.21448
Kosikova, B., Gregorova, A., Osvald, A., and Krajcovicova, J. (2007). Role of lignin filler in stabilization of natural rubber-based composites. J. Appl. Polym. Sci. 103, 1226–1231. doi: 10.1002/app.24530
Kumar, M. N. S., Mohanty, A. K., Erickson, L., and Misra, M. (2009). Lignin and its applications with polymers. J. Biobased Mater. Bioenergy 3, 1–24. doi: 10.1166/jbmb.2009.1001
Kumaran, M. G., and De, S. K. (1978). Utilization of lignins in rubber compounding. J. Appl. Polym. Sci. 22, 1885–1893. doi: 10.1002/app.1978.070220711
Laibach, N., Hillebrand, A., Twyman, R. M., Prufer, D., and Gronover, C. S. (2015). Identification of a Taraxacum brevicorniculatum rubber elongation factor protein that is localized on rubber particles and promotes rubber biosynthesis. Plant J. 82, 609–620. doi: 10.1111/tpj.12836
Lang, J. M., Shrestha, U. M., and Dadmun, M. (2018). The effect of plant source on the properties of lignin-based polyurethanes. Front. Energy Res. 6:4. doi: 10.3389/fenrg.2018.00004
Langan, P., Gnanakaran, S., Rector, K. D., Pawley, N., Fox, D. T., Cho, D. W., et al. (2011). Exploring new strategies for cellulosic biofuels production. Energy Environ. Sci. 4, 3820–3833. doi: 10.1039/c1ee01268a
Laurichesse, S., and Avérous, L. (2014). Chemical modification of lignins: towards biobased polymers. Prog. Polym. Sci. 39, 1266–1290. doi: 10.1016/j.progpolymsci.2013.11.004
Leblanc, J. L. (2002). Rubber-filler interactions and rheological properties in filled compounds. Prog. Polym. Sci. 27, 627–687. doi: 10.1016/S0079-6700(01)00040-5
Liu, J., Liu, H., Deng, L., Liao, B., and Guo, Q. (2013). Improving aging resistance and mechanical properties of waterborne polyurethanes modified by lignin amines. J. Appl. Polym. Sci. 130, 1736–1742. doi: 10.1002/app.39267
Liu, Y., Gao, L., and Sun, J. (2007). Noncovalent functionalization of carbon nanotubes with sodium lignosulfonate and subsequent quantum dot decoration. J. Phys. Chem. C 111, 1223–1229. doi: 10.1021/jp066018z
Lora, J. H., and Glasser, W. G. (2002). Recent industrial applications of lignin: a sustainable alternative to nonrenewable materials. J. Polym. Environ. 10, 39–48. doi: 10.1023/A:1021070006895
Mathews, K. (2018). Fuel Efficient Green Tyre Technology to Roll the Tyre Industry in United States. Press Release, Tech Sci Research, New York, NY.
Medalia, A. I., and Kraus, G. (1994). “Reinforcement of elastomers by particulate fillers,” in Science and Technology of Rubber (Newton, MA: Academic Press), 387–418. doi: 10.1016/B978-0-08-051667-7.50013-5
Miao, C., and Hamad, W. Y. (2017). Controlling lignin particle size for polymer blend applications. J. Appl. Polym. Sci. 134, 1–10. doi: 10.1002/app.44669
Milczarek, G., and Nowicki, M. (2013). Carbon nanotubes/kraft lignin composite: characterization and charge storage properties. Mater. Res. Bull. 48, 4032–4038. doi: 10.1016/j.materresbull.2013.06.022
Mishra, S., Usha Rani, G., and Sen, G. (2012). Microwave initiated synthesis and application of polyacrylic acid grafted carboxymethyl cellulose. Carbohydr. Polym. 87, 2255–2262. doi: 10.1016/j.carbpol.2011.10.057
Mohan, S. V., and Karthikeyan, J. (1997). Removal of lignin and tannin colour from aqueous solution by adsorption onto activated charcoal. J. Environ. Pollut. 97, 183–187. doi: 10.1016/s0269-7491(97)00025-0
Mooibroek, H., and Cornish, K. (2000). Alternative sources of natural rubber. Appl. Microbiol. Biotechnol. 53, 355–65. doi: 10.1007/s002530051627
Morfeld, P., Büchte, S. F., Wellmann, J., McCunney, R. J., and Piekarski, C. (2006). Lung cancer mortality and carbon black exposure: Cox regression analysis of a cohort from a German carbon black production plant. J. Occup. Environ. Med. 48, 1230–1241. doi: 10.1097/01.jom.0000215282.23531.b9
Nando, G. B., and De, S. K. (1980). Effect of lignin on the network structure and properties of natural rubber mixes vulcanized by conventional, semiefficient and efficient vulcanization systems. J. Appl. Polym. Sci. 25, 1249–1252. doi: 10.1002/app.1980.070250625
Narathichat, M., Kummerlowe, C., Vennemann, N., Sahakaro, K., and Nakason, C. (2012). Influence of epoxide level and reactive blending on properties of epoxidized natural rubber and nylon-12 blends. Adv. Polym. Technol. 31, 118–129. doi: 10.1002/adv.20243
Nguyen, T. H., Tangboriboonrat, P., Rattanasom, N., Petchsuk, A., Opaprakasit, M., Thammawong, C., et al. (2012). Polylactic acid/ethylene glycol triblock copolymer as novel crosslinker for epoxidized natural rubber. J. Appl. Polym. Sci. 124, 164–174. doi: 10.1002/app.35088
Niedermeier, W., Frohlich, J., and Lugisland, H. D. (2002). Reinforcement mechanism in the rubber matrix by active fillers. Raw Mater. Appl. 55, 356–366.
Nordstrom, Y., Norberg, I., Sjoholm, E., and Drougge, R. (2013). A new softening agent for melt spinning of softwood kraft lignin. J. Appl. Polym. Sci. 129, 1274–1279. doi: 10.1002/app.38795
Ouyang, X., Ke, L., Qiu, X., Guo, Y., and Pang, Y. (2009). Sulfonation of alkali lignin and its potential use in dispersant for cement. J. Dispers. Sci. Technol. 30, 1–6. doi: 10.1080/01932690802473560
Park, S., and Cho, K. (2003). Filler – elastomer interactions : influence of silane coupling agent on crosslink density and thermal stability of silica / rubber composites. J. Colloid Interface Sci. 267, 86–91. doi: 10.1016/s0021-9797(03)00132-2
Peng, Z., Kong, L. X., Li, S. D., Chen, Y., and Huang, M. F. (2007). Self-assembled natural rubber/silica nanocomposites: its preparation and characterization. Compos. Sci. Technol. 67, 3130–3139. doi: 10.1016/j.compscitech.2007.04.016
Pillai, K. V., and Renneckar, S. (2009). Cation-π interactions as a mechanism in technical lignin adsorption to cationic surfaces. Biomacromolecules 10, 798–804. doi: 10.1021/bm801284y
Pire, M., Norvez, S., Iliopoulos, I., Le Rossignol, B., and Leibler, L. (2011). Imidazole-promoted acceleration of crosslinking in epoxidized natural rubber/dicarboxylic acid blends. Polymer 52, 5243–5249. doi: 10.1016/j.polymer.2011.09.032
Pouteau, C., Dole, P., Cathala, B., Averous, L., and Boquillon, N. (2003). Antioxidant properties of lignin in polypropylene. Polym. Degrad. Stab. 81, 9–18. doi: 10.1016/S0141-3910(03)00057-0
Rasutis, D., Soratana, K., McMahan, C., and Landis, A. E. (2015). A sustainability review of domestic rubber from the guayule plant. Ind. Crops Prod. 70, 383–394. doi: 10.1016/j.indcrop.2015.03.042
Ray, D. T., Coffelt, T. A., and Dierig, D. A. (2005). Breeding guayule for commercial production. Ind. Crops Prod. 22, 15–25. doi: 10.1016/j.indcrop.2004.06.005
Robertson, C. G., and Rackaitis, M. (2011). Further consideration of viscoelastic two glass transition behavior of nanoparticle-filled polymers. Macromolecules 44, 1177–1181. doi: 10.1021/ma102631h
Saake, B., and Lehnen, R. (2012). Lignin. Ullmann's Encycl. Ind. Chem. 21, 21–36. doi: 10.1002/14356007.a15_305.pub3
Sadeghifar, H., and Argyropoulos, D. S. (2015). Correlations of the antioxidant properties of softwood kraft lignin fractions with the thermal stability of its blends with polyethylene. ACS Sustain. Chem. Eng. 3, 349–356. doi: 10.1021/sc500756n
Sahakaro, K., Naskar, N., Datta, R. N., and Noordermeer, J. W. M. (2007). Blending of NR/BR/EPDM by reactive processing for tire sidewall applications. 1. preparation, cure characteristics and mechanical properties. J. Appl. Polym. Sci. 103, 2538–2546. doi: 10.1002/app.25088
Sarkawi, S. S., Dierkes, W. K., and Noordermeer, J. W. M. (2015). Morphology of silica-reinforced natural rubber: the effect of silane coupling agent. Rubber Chem. Technol. 88, 359–372. doi: 10.5254/rct.15.86936
Schaefer, D. W., Rieker, T., Agamalian, M., Lin, J. S., Fischer, D., Sukumaran, S., et al. (2000). Multilevel multilevel structure structure of of reinforcing reinforcing silica and carbon silica and carbon. J. Appl. Crystallogr. 33, 587–591. doi: 10.1107/S0021889800001199
Schmidt, T., Lenders, M., Hillebrand, A., Van Deenen, N., Munt, O., Reichelt, R., et al. (2010). Characterization of rubber particles and rubber chain elongation in Taraxacum koksaghyz. BMC Biochem. 11:11. doi: 10.1186/1471-2091-11-11
Schmitt, C. N. Z., Politi, Y., Reinecke, A., and Harrington, M. J. (2015). Role of sacrificial protein-metal bond exchange in mussel byssal thread self-healing. Biomacromolecules 16, 2852–2861. doi: 10.1021/acs.biomac.5b00803
Sengloyluan, K., Sahakaro, K., Dierkes, W. K., and Noordermeer, J. W. M. (2014). Silica-reinforced tire tread compounds compatibilized by using epoxidized natural rubber. Eur. Polym. J. 51, 69–79. doi: 10.1016/j.eurpolymj.2013.12.010
Setua, D. K., Shukla, M. K., Nigam, V., Singh, H., and Mathur, G. N. (2000). Lignin-reinforced rubber composites. Polym. Compos. 21, 988–995. doi: 10.1002/pc.10252
Shukla, M. K., Nigam, V., Singh, H., Setua, D. K., and Mathur, G. N. (1998). “Lignin reinforced rubber composites,” in Proceedings of Composite Materials (Jamshedpur), 233–245.
Singha, A. S., Thakur, V. K., Mehta, I. K., Shama, A., Khanna, A. J., Rana, R. K., et al. (2009). Surface-modified hibiscus sabdariffa fibers : physicochemical, thermal, and morphological properties evaluation. Int. J. Polym. Anal. Charact. 14, 695–711. doi: 10.1080/10236660903325518
Siti Suhaily, S., Abdul Khalil, H. P. S., Wan Nadirah, W. O., and Jawaid, M. (2013). “Bamboo based biocomposites material, design and applications,” in Materials Science - Advanced Topics, 489–517. doi: 10.5772/56057
Snowdon, M. R., Mohanty, A. K., and Misra, M. (2014). A study of carbonized lignin as an alternative to carbon black. ACS Sustain. Chem. Eng. 2, 1257–1263. doi: 10.1021/sc500086v
Soratana, K., Rasutis, D., Azarabadi, H., Eranki, P. L., and Landis, A. E. (2017). Guayule as an alternative source of natural rubber: a comparative life cycle assessment with Hevea and synthetic rubber. J. Clean. Prod. 159, 271–280. doi: 10.1016/j.jclepro.2017.05.070
Strzemiecka, B., Klapiszewski, L., Jamrozik, A., Szalaty, T. J., Matykiewicz, D., Sterzynski, T., et al. (2016). Physicochemical characterization of functional lignin-silica hybrid fillers for potential application in abrasive tools. Materials. 9:E517. doi: 10.3390/ma9070517
Sudin, R., and Swamy, N. (2006). Bamboo and wood fibre cement composites for sustainable infrastructure regeneration. J. Mater. Sci. 41, 6917–6924. doi: 10.1007/s10853-006-0224-3
Suhas, Carrott, P. J. M., and Ribeiro Carrott, M. M. (2007). Lignin – from natural adsorbent to activated carbon : a review. Bioresour. Technol. 98, 2301–2312. doi: 10.1016/j.biortech.2006.08.008
Sun, J.-Y., Zhao, X., Illeperuma, W. R. K., Chaudhuri, O., Oh, K. H., Mooney, D. J., et al. (2012). Highly stretchable and tough hydrogels. Nature 489, 133–136. doi: 10.1038/nature11409
Teaca, C.-A., Rosu, D., Bodirlau, R., and Rosu, L. (2013). Structural changes in wood under artificial UV light irradiation determined by FTIR spectroscopy and color measurements – a brief review. Bioresources 8, 1478–1507. doi: 10.15376/biores.8.1.1478-1507
ten Brinke, A. (2002). Silica Reinforced Tyre Rubbers. Ph.D. thesis, University of Twente, Netherlands.
Thakur, V. K., and Singha, A. S. (2010). KPS-initiated graft copolymerization onto modified cellulosic biofibers. Int. J. Polym. Anal. Charact. 15, 471–485. doi: 10.1080/1023666X.2010.510294
Thakur, V. K., Singha, A. S., and Misra, B. N. (2011). Graft copolymerization of methyl methacrylate onto cellulosic biofibers. J. Appl. Polym. Sci. 122, 532–544. doi: 10.1002/app.34094
Thakur, V. K., and Thakur, M. K. (2015). Recent advances in green hydrogels from lignin: a review. Int. J. Biol. Macromol. 72, 834–847. doi: 10.1016/j.ijbiomac.2014.09.044
Thakur, V. K., Thakur, M. K., Raghavan, P., and Kessler, M. R. (2014). Progress in green polymer composites from lignin for multifunctional applications: a review. ACS Sustainable Chem. Eng. 2:5. doi: 10.1021/sc500087z
Tran, C. D., Chen, J., Keum, J. K., and Naskar, A. K. (2016). A new class of renewable thermoplastics with extraordinary performance from nanostructured lignin-elastomers. Adv. Funct. Mater. 26, 2677–2685. doi: 10.1002/adfm.201504990
Vainio, U., Maximova, N., Hortling, B., Laine, J., Stenius, P., Simola, L. K., et al. (2004). Morphology of dry lignins and size and shape of dissolved kraft lignin particles by X-ray scattering. Langmuir 20, 9736–9744. doi: 10.1021/la048407v
Venkatachalam, P., Geetha, N., Sangeetha, P., and Thulaseedharan, A. (2013). Natural rubber producing plants: an overview. Afr J. Biotechnol. 12, 1297–1310. doi: 10.5897/AJBX12.016
Vieira, M. G. A., Da Silva, M. A., Dos Santos, L. O., and Beppu, M. M. (2011). Natural-based plasticizers and biopolymer films: a review. Eur. Polym. J. 47, 254–263. doi: 10.1016/j.eurpolymj.2010.12.011
Waddell, W. H. (1998). Tire black sidewall surface discoloration and non-staining technology: a review. Rubber Chem. Technol. 71, 590–618. doi: 10.5254/1.3538493
Wang, H., Liu, W., Huang, J., Yang, D., and Qiu, X. (2018). Bioinspired engineering towards tailoring advanced lignin/rubber elastomers. Polymers 10:1033. doi: 10.3390/polym10091033
Wang, J., Yao, K., Korich, A. L., Li, S., Ma, S., Ploehn, H. J., et al. (2011). Combining renewable gum rosin and lignin: towards hydrophobic polymer composites by controlled polymerization. J. Polym. Sci. Part A Polym. Chem. 49, 3728–3738. doi: 10.1002/pola.24809
Wang, M.-J., Grey, C. A., Reznek, S. A., Mahmud, K., and Kutsovsky, Y. (2003). Carbon black. Kirk-Othmer Encycl. Chem. Technol. 4, 761–803. doi: 10.1002/0471238961.0301180204011414.a01.pub2
Wang, M.-J., Kutsovsky, Y., Zhang, P., Murphy, L. J., Laube, S., and Mahmud, K. (2002). New generation carbon-silica dual phase filler part I. Characterization and application to passenger tire. Rubber Chem. Technol. 75, 247–263. doi: 10.5254/1.3544975
Watkins, D., Nuruddin, M., Hosur, M., Tcherbi-Narteh, A., and Jeelani, S. (2014). Extraction and characterization of lignin from different biomass resources. J. Mater. Res. Technol. 4, 26–32. doi: 10.1016/j.jmrt.2014.10.009
Xiao, S., Feng, J., Zhu, J., Wang, X., Yi, C., and Su, S. (2013). Preparation and characterization of lignin-layered double hydroxide/styrene-butadiene rubber composites. J. Appl. Polym. Sci. 130, 1308–1312. doi: 10.1002/app.39311
Xing, W., Yuan, H., Zhang, P., Yang, H., Song, L., and Hu, Y. (2013). Functionalized lignin for halogen-free flame retardant rigid polyurethane foam: preparation, thermal stability, fire performance and mechanical properties. J. Polym. Res. 20:234. doi: 10.1007/s10965-013-0234-1
Xu, G., Yan, G., and Zhang, J. (2015). Lignin as coupling agent in EPDM rubber: thermal and mechanical properties. Polym. Bull. 72, 2389–2398. doi: 10.1007/s00289-015-1411-7
Yang, D. Q., Rochelte, J. F., and Sacher, E. (2005). Spectroscopic evidence for π-π interaction between poly(diallyl dimethylammonium) chloride and multiwalled carbon nanotubes. J. Phys. Chem. B 109, 4481–4484. doi: 10.1021/jp044511+
Yu, P., He, H., Jia, Y., Tian, S., Chen, J., Jia, D., et al. (2016a). A comprehensive study on lignin as a green alternative of silica in natural rubber composites. Polym. Test. 54, 176–185. doi: 10.1016/j.polymertesting.2016.07.014
Yu, P., He, H., Jiang, C., Jia, Y., Wang, D., Yao, X., et al. (2016b). Enhanced oil resistance and mechanical properties of nitrile butadiene rubber/lignin composites modified by epoxy resin. J. Appl. Polym. Sci. 133, 1–10. doi: 10.1002/app.42922
Yu, P., He, H., Jiang, C., Wang, D., Jia, Y., Zhou, L., et al. (2015). Reinforcing styrene butadiene rubber with lignin-novolac epoxy resin networks. Express Polym. Lett. 9, 36–48. doi: 10.3144/expresspolymlett.2015.5
Zafarmehrabian, R., Gangali, S. T., Ghoreishy, M. H. R., and Davallu, M. (2012). The effects of silica/carbon black ratio on the dynamic properties of the tread compounds in truck tires. J. Chem. 9, 1102–1112. doi: 10.1155/2012/571957
Zhang, H. J., Sun, T. L., Zhang, A. K., Ikura, Y., Nakajima, T., Nonoyama, T., et al. (2016). Tough physical double-network hydrogels based on amphiphilic triblock copolymers. Adv. Mater. 28, 4884–4890. doi: 10.1002/adma.201600466
Zhang, P., Huang, G., Qu, L., Nie, Y., and Weng, G. (2012). Study on the self-crosslinking behavior based on polychloroprene rubber and epoxidized natural rubber. J. Appl. Polym. Sci. 125, 1084–1090. doi: 10.1002/app.34508
Keywords: lignin, alternative carbon black, chemical modification, mixing technique, rubber-lignin properties
Citation: Mohamad Aini NA, Othman N, Hussin MH, Sahakaro K and Hayeemasae N (2020) Lignin as Alternative Reinforcing Filler in the Rubber Industry: A Review. Front. Mater. 6:329. doi: 10.3389/fmats.2019.00329
Received: 15 July 2019; Accepted: 03 December 2019;
Published: 08 January 2020.
Edited by:
Yu Dong, Curtin University, AustraliaReviewed by:
Johnny De Nardi Martins, Federal University of Santa Catarina, BrazilDongyan Liu, Chinese Academy of Sciences, China
Copyright © 2020 Mohamad Aini, Othman, Hussin, Sahakaro and Hayeemasae. This is an open-access article distributed under the terms of the Creative Commons Attribution License (CC BY). The use, distribution or reproduction in other forums is permitted, provided the original author(s) and the copyright owner(s) are credited and that the original publication in this journal is cited, in accordance with accepted academic practice. No use, distribution or reproduction is permitted which does not comply with these terms.
*Correspondence: Nadras Othman, c3JuYWRyYXNAdXNtLm15