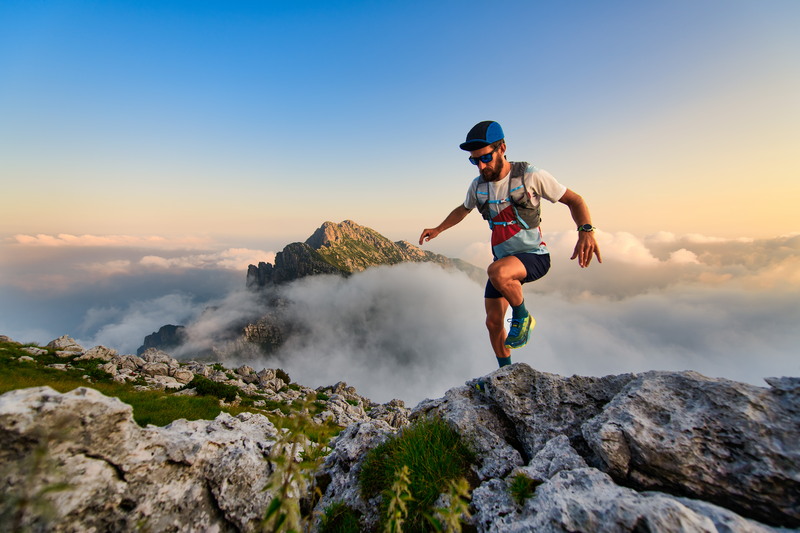
95% of researchers rate our articles as excellent or good
Learn more about the work of our research integrity team to safeguard the quality of each article we publish.
Find out more
ORIGINAL RESEARCH article
Front. Mater. , 29 November 2019
Sec. Energy Materials
Volume 6 - 2019 | https://doi.org/10.3389/fmats.2019.00309
This article is part of the Research Topic Chemistry, Synthesis, and Interaction of Advanced Electrolyte Materials for High-Energy-Density Batteries View all 8 articles
In this paper, the precursor Ni0.8Co0.1Mn0.1(OH)2 is prepared by a co-precipitation method. By mixing this material with LiOH in proportion and sintering twice under 500 and 800°C, respectively, the cathode material of LiNi0.8Co0.1Mn0.1O2 (NCM811) for lithium ion batteries (LIBs) is synthesized. To improve the performance of this NCM811 material, Al2O3, ZrO2, and LBO (Li2O-2B2O3) are, respectively, used to coat it by a wet chemical method. The effects of Al2O3, ZrO2, and LBO thin coating layers (~20–200 nm) on the morphology, structure and electrochemical property of NCM811 are studied using XRD, SEM, TEM, XPS, and electrochemical measurements. Coin LIBs are assembled with the uncoated, Al2O3-coated, ZrO2-coated, and LBO-coated NCM811 cathode materials for performance validation. The experiment results confirm that the charge-discharge specific capacity, Coulomb efficiency, water absorption stability, cycle characteristics, and resistance stability of the NCM811 cathode material can be significantly improved by coating it with LBO particularly. Therefore, the surface coating to the particles of cathode materials using LBO is expected to be an effective and practical modification method to improve the electrochemical performance of LIBs.
Electrochemical energy technologies, such as lithium-ion batteries, metal-air batteries, fuel cell, and water electrolysis, etc., have been recognized as one type of the most reliable and efficient options for clean and sustainable electricity energy storage and conversion (Khan et al., 2018; Wang et al., 2018; Zhang H. et al., 2018; Zhang L. et al., 2018). For relatively mature lithium-ion batteries (LIBs), the cathode materials play a dominating role in the performance of LIBs. In order to further increase energy densities of the devices, high-nickel NCM-based materials such as LiNixCoyMnzO2 (here x+y+z = 1 with x>y+z) family have been explored and used in LIBs. It seems that one of the most promising LIB cathode materials is LiNi0.8Co0.1Mn0.1O2 (NCM811, where x = 0.8, y = 0.1, and z = 0.1), which shows higher specific capacity than other family members (Cao et al., 2018; Li Q. et al., 2018).
In general, for high-nickel NCM-based materials, there are several shortcomings which have been identified. (1) Li+/Ni2+ mixing when Ni2+ content is increased. In high-nickel NCM-based material, part of Ni2+ may occupy the Li+ position, forming a cation mixing and then reducing the specific capacity of material. Furthermore, during the charging process, the low-valence nickel ion in the transition metal (Co, Mn) layer can migrate to the lithium layer, occupying the lithium vacancies, affecting the diffusion of Li+. The voltage stability of the material is also relatively weak, which is easy to decline rapidly (Noh et al., 2013; Li et al., 2019; Zhang et al., 2019). (2) Poor thermal stability. Studies have shown that the higher the nickel content in the ternary material, the worse the thermal stability, causing safety issue (Aurbach, 2000; Ma et al., 2019). (3) Unstable surface structure. The excessive delithiation occurs in the surface structure with charging, and the layered structure of the high-nickel NCM-based material changes to the spinel structure and the inert rock salt structure with a hicker inert NiO layer. Furthermore, the high-valent active transition metal ions on the surface layer can have side reactions with the electrolyte, causing the increase of polarization and then the decay of the capacity (Noh et al., 2006). (4) Too high surface alkali content. The nickel element in the NCM-based material is alkaline, which is easy to absorb water and CO2 when exposed to air and reacts with residual lithium in the surface layer to form LiOH and Li2CO3, which can further increase the pH value of the material and seriously affect the electrochemical performance of the NCM-based material (Bi et al., 2016). In recent years, many improvements have been carried out for high-nickel NCM-based materials of LIB cathodes, including innovating the synthesis processes, doping modification, and matching of microstructure with electrolyte. There are mainly two methods to improve the performance of high-nickel NCM-based materials. (1) Element doping for improving the cationic mixing and lattice stability, such as doping Mg, Al, Zr, and other components into materials to improve the cycling performance (Nobili et al., 2012; Min et al., 2017). (2) Coating the material particles with electrochemically inert materials to prevent or suppress the side reactions between the cathode surface and electrolyte, and improve the particles' structural stability for enhancing the cycle-life of the corresponding LIBs. The commonly used physical protective coating materials are Al2O3 (Chen et al., 2019), MgO (Yoon et al., 2012), CeO2 (Wu et al., 2019), ZrO2 (Li G. et al., 2018), Co3O4 (Hao et al., 2019), etc. The common feature of these coatings is that their metal ions have only one stable valence state with high chemical stability under the electrochemical window conditions. Of course, the coating also have some shortcomings, because as the insulators of ions and electrons, they may have a negative impact on the transport of lithium ions, thereby affecting or reducing the Coulombic efficiency, power output, and other electrochemical properties of LIBs.
In addition to the above lithium-free metal oxides used as coating materials for cathode materials, some researchers have employed lithium-containing Li2ZrO3 (Dong et al., 2015), Li3PO4 (Song et al., 2011), Li2O-2B2O3 (LBO) (Chan et al., 2005; Lim et al., 2014; Song et al., 2019) to coat cathode materials. These lithium-containing compounds, in particular, conductive LBO can maintain stable electrochemical properties at high oxidation potential. LBO coating has shown a good ionic conductivity, which makes the coated cathode materials more conducive to lithium ions, thus leading to better electrochemical properties. It has been reported in the literature that the surface coatings of LBO glass on LiNi0.5Mn1.5O4 (Lim et al., 2014), LiNi0.5Co0.2Mn0.3O2 (Song et al., 2019), and LiMn2O4 (Chan et al., 2005) cathodes can make remarkable improvements in charge-discharge behavior, cycle-life and other electrochemical properties. The influence of coating on the electrochemical properties of cathode materials is shown in Table 1. However, there are a few of researches reporting about the coating of LBO on LiNi0.8Co0.1Mn0.1O2 (NCM811) cathode material.
In this work, NCM811 cathode material is prepared by a co-precipitation method. In order to improve the electrochemical properties, several materials such as Al2O3, ZrO2, and LBO are used, respectively, to coat NCM811 for LIB cathode materials. The microstructures and morphologies of the coated NCM811 materials are characterized by X-ray diffraction (XRD), scanning electron microscopy (SEM), transmission electron microscope (TEM) and X-ray photoelectron spectroscopy (XPS). The coated NCM811 materials as the cathodes are assembled in coin LIBs for performance validation. The effects of different coatings on the electrochemical properties of NCM811 are studied by testing the charge/discharge curves and Coulomb efficiencies, cycle performance and DC resistances of the corresponding coin LIBs.
According to a molar ratio of 8:1:1 (Ni: Co: Mn metal ions), nickel sulfate (NiSO4·6H2O), cobalt sulfate (CoSO4·7H2O), manganese sulfate (MnSO4·2H2O) were, respectively, weighed and added into deionized water and stirred evenly, and a mixed solution with a total concentration of metal ions of 0.5 mol/L was prepared. The mixed solution was placed in the reactor, and 1 mol/L NaOH solution as the precipitator and 0.5 mol/L ammonia solution as the complexing buffer were added continuously. The whole reaction process was carried out in a N2 atmosphere for insulating air. The pH value of the mixed solution was controlled from 10.5 to 11.5, and the temperature of reactor was controlled at 55°C under a continuously stirring for 24 h. The obtained precipitates were filtered and washed with deionized water after 4 h of static aging, and then dried in a vacuum drying chamber at 95°C for 24 h to obtain the gray-brown precursor Ni0.8Co0.1Mn0.1(OH)2. LiOH·H2O and this precursor were weighed according to the molar ratio of 1.04:1. The weighted mixture was then grinded evenly, calcined at 500°C for 4 h and cooled for 1 h in a muffle furnace. Then the black LiNi0.8Co0.1Mn0.1O2 (NCM811) powder was obtained by continuous calcination in a tube furnace protected by oxygen gas at 85°C for 16 h.
For Al2O3 coating, Al(NO3)3·9H2O was weighed for forming a solution of with 0.05 ml/L of Al3+. Then a total concentration of 1 mol/L Al(NO3)3·9H2O and CO(NH2)2 with a molar ratio of 1: 1.15 was prepared. The pure phase NCM811 was weighed in a beaker with a proper amount of deionized water added to disperse it into a uniform solution by ultrasound. Then, according to the amount of coated Al2O3 of 1,000 ppm (Weight proportion of the coated substance calculated based on the content of substance Al2O3), the quantitative solution of Al(NO3)3·9H2O was slowly added into NCM811 dispersion solution, and stirred for 1 h. The suspension of NCM811 deposited by Al(OH)3 was obtained by heating at 85°C in a water bath for 4 h under a rapid stirring. The obtained mixture was filtrated and washed with deionized water, then dried in a vacuum drying box at 100°C for 24 h. Then a heat treatment at 500°C was carried out for 4 h. Finally, the NCM811 coated with Al2O3 was obtained by naturally cooling, grinding and calcinating in a muffle furnace at 800°C for 8 h in air atmosphere.
For ZrO2 coating, an appropriate amount of NCM811 material was weighted and put into a beaker with deionized water, stirring for 1 h. Then, citric acid (C6H8O7·H2O) and zirconium acetate (Zr(CH3COO)4) with a molar ratio of 1:1 were dissolved in the deionized water. The sum molar concentration of these two compounds in solution was 0.1 mol/L. According to the designed weight content of 1,000 ppm ZrO2 in NCM811 (calculated based on the content of substance ZrO2), the mixed citric acid and zirconium acetate solution are slowly added to NCM811 suspension. The beaker was then heated in water at 55°C with stirring for 8 h to form a solution. This solution was then evaporated until a gel was obtained. This gel was then dried in a vacuum drying chamber at 100°C for 24 h to obtain a solid sample. After grinded, the product was heat treated at 500°C for 4 h. Finally, the product of NCM811 coated with ZrO2 was obtained by calcining it in a muffle furnace at 800°C for 8 h in air atmosphere.
For LBO coating, LiOH·H2O and manganic acid (H3BO3) were added to alcohol at a molar ratio of 1:2. The above substances were completely dissolved after being heated in a water bath at 85°C for 4 h. After dissolution, the prepared uncoated NCM811 powder was added, and the quantity of the added NCM811 was controlled according to coated 1,000 ppm of LBO (calculated based on the content of substance LBO). The formed mixture was stirred until the alcohol was evaporated completely to form a solid sample. Then the solid sample was calcined in a muffle furnace at 500°C for 4 h in oxygen atmosphere, and the heating rate of the muffle furnace was 5°C/min. Then NCM811 with Li2O-2B2O3 (LBO) coating was obtained by natural cooling, grinding and calcination at 800°C for 8 h in a muffle furnace under air atmosphere.
In this paper, NCM811 without any coating is represented by A, and the samples of NCM811 coated with 1,000 ppm of Al2O3, ZrO2, and LBO are represented by B, C, and D, respectively. The preparation routes for samples of NCM811 coated by Al2O3, ZrO2, and LBO are shown in Figure 1.
Figure 1. Schematic diagrams of the preparation processes of the materials of NCM811 coated by Al2O3, ZrO2, and LBO.
The crystal structures of the samples were analyzed by X-ray diffractometer (XRD) (D/max-250, made in Japan) with the Kα radiation of copper target obtained with a wavelength of 0.153 nm, a tube voltage of 40 kV, a tube current of 250 mA, a diffraction angle scanning range of 10–80° and a scanning speed of 8°/min. The morphologies of the samples were observed by FEI Quanta-200 (manufactured in the Netherlands) field emission scanning electron microscopy (FE-SEM) with a voltage of 5 kV. The morphologies of the samples were also analyzed by JFM-2100 transmission electron microscopy (TEM) (Japan Electronics Production). X-ray photoelectron spectroscopy (XPS) was carried out on an Escalab 250xi X-ray photoelectron spectrometer.
In a typical fabrication of LIBs, NCM811, or a coated NCM811 sample, conductive carbon black (Super-P) and polyvinylidene fluoride was weighed at a mass ratio of 90:5:5 and placed in an agate mortar. After it was grinded and mixed uniformly, an appropriate amount of polypyrrolidone (NMP) was added and grinded for 2 h until the slurry was reached to a flow state. The slurry was then evenly coated on a 12 μm thick aluminum foil to form an electrode sheet. In order to remove the NMP solvent, the electrode sheet was placed in a vacuum oven and dried at 120°C for 12 h. Then the dried electrode was punched and cut into a 14 mm disc. After weighed, this disc electrode (serves as the cathode) was placed in the vacuum drying box at 60°C for 8 h, and then removed and placed in the glove box protected by argon. The prepared cathode sheet, separators (produced by Shenzhen Xing-yuan Material Co., Ltd., 16 μm thick), negative lithium foil (lithium sheet with diameter of 15 mm and thickness of 0.3 mm), electrolyte (model RT, produced by Guangzhou Tianci High-tech New Materials Co., Ltd.) were assembled into a R2032 coin LIB. All coin LIBs made from NCM811 and the coated NCM811 by Al2O3, ZrO2, and LBO were assembled in an argon glove box with oxygen and hydrogen peroxide content <1 ppm.
For water adsorption testing, the tested cathodes of NCM811 and NCM811 coated by Al2O3, ZrO2, and LBO were placed in a humidity of 10% RH and stored in an ambient temperature of 25°C. The total storage time was 72 h, and the water contents of the electrodes were measured at an 8 h interval. The moisture values of the electrodes were measured by a moisture tester (CA200/VA200, Mitsubishi Chemical Company, Japan). The temperature of the tester was controlled at 170°C.
The measurements of electrochemical performance of the coin LIBs were carried out using an electrochemical testing system (Land CT2001A, Wuhan land electronic Co., Ltd.). The current densities of the first charge and discharge are both 18 mA/g (0.1C). In the charge-discharge cycling tests of coin LIBs, the charging current density was 90 mA/g (0.5C) and the discharging current was 180 mA/g (1C), respectively. The tested voltage range was 2.8–4.3 V (vs.Li/Li+), and the static time between the charging and discharging processes was 30 min. All the tests were carried out at 25°C. DC resistance tests followed the instruction of HPPC test method in a Freedom Car Battery Testing Manual (Belt, 2010). This work used 0.5C current to charge coin batteries to different SOC states (100% SOC), and then used a charge current of 1C and charging time of 10 s to obtain DC resistances of the coin LIBs at 100% SOC states.
Figure 2 Shows the XRD spectra of uncoated and differently coated NCM811 materials. It can be seen that the pure phased and differently coated NCM811 materials have good a hexagonal α-NaFeO2 layered structure and a R-3m space point group. The main peaks in the XRD spectra of the coated materials are identical, which indicates that the coated materials do not change the layered structure. In addition, the peaks of 006/102 and 108/110 can be observed from XRD spectra, indicating that the pure NCM811 and the coated NCM811 samples both have a good crystallinity and an ordered layered structure (Li et al., 2014). No characteristic peaks of the coated materials of Al2O3, ZrO2, and LBO can be found in the XRD spectra of the coated NCM811 materials. There were no obvious differences in the location and intensity of the diffraction peaks between pure phase material and the coated materials, and no new diffraction peaks can be observed. These can be explained by that the coated material layer does not change the original lattice structure of the bulk material, and that the coated materials of Al2O3, ZrO2, and LBO are amorphous, and only adhere to the surface of the bulk materials as the coating layers.
Figure 2. XRD patterns of NCM811 Samples (A-uncoated, B-Coated by Al2O3, C-Coated by ZrO2, D-Coated by LBO).
From the SEM images shown in Figure 3, it can be seen that the appearances of uncoated and the coated NCM811 samples are basically similar, and they are spheroids bound by the secondary solid particles. The particle size range of the secondary sphere is 3–16 um.
Figure 4 shows the TEM images of NCM811 and the coated NCM811 samples. Figure 4A is a NCM811 sample without any coating. The surface of the uncoated material is smooth and there is no coating layer that can be observed. Figure 4B is a TEM image of the NCM811 coated with Al2O3. The surface of NCM811 has a coating layer with a thickness of 20–80 nm. Figure 4C is a TEM image of the NCM811 coated with ZrO2. The thickness of the coating layer is 20–120 nm. Figure 4D is a TEM image of the NCM811 coated with LBO. The coating layer is 50–200 nm thick. For the layered cathode material, the coating layer can reduce the undesired reaction between cathode material and electrolyte and suppress lattice distortion caused by the dissolution of transition metal ions into electrolyte during charging (Zuo et al., 2017). It is expected when NCM811 is coated by a layer, the cathode could be protected, benifiting batttery performance.
Figure 4. TEM images of NCM811 samples (A-uncoated, B-Coated by Al2O3, C-Coated by ZrO2, D-Coated by LBO).
In order to further confirm the composition of NCM811 and NCM811 coated by Al2O3, ZrO2, and LBO, the prepared samples were characterized by XPS, as shown in Figure 5. The characteristic binding energies of Co2p3/2, Mn2P3/2, and Ni2P3/2 can be seen from Figures 5A–C, which are 780.04, 641.99, and 854.69 eV, indicating that the valence states of Co, Ni and Mn are +2, +3, and +4, respectively (Tan et al., 2015). The characteristic peak of 73.8 eV can be found only for NCM811 coated with Al2O3 (Sample B) (Figure 5D), which corresponds to the characteristic binding energy of Al2p3/2 of Al2O3 (Wen et al., 2018). The XPS spectrum of Zr3d include two peaks: Zr3d5/2 (181.75 ev) and Zr3d3/2 (184.25 ev), which are in good agreement with the values in literature (Huang et al., 2009). Boron can only be detected on sample of NCM 811 coated with LBO, as shown in Figure 5F. The characteristic binding energy of B1S is 191.83 eV. This is consistent with the binding energy of LBO (Li2O-2B2O3) in literature (Wang et al., 2015). XPS results show that Al2O3, ZrO2, and LBO have been successfully coated on the surface of MCM811, respectively.
From Figure 6 and Table 2 above, it can be seen that the first charge specific capacity of coin LIB made of the uncoated NCM811 sample (A) is 229.2 mAh/g, the first discharge specific capacity is 201.7 mAh/g and the first charge-discharge Coulomb efficiency is 88.00%, respectively. The first charge specific capacity of coin LIB made of the NCM811 coated by Al2O3 (B) is 226.3 mAh/g and the first discharge specific capacity is 199.2 mAh/g. The first charge-discharge Coulomb efficiency is 88.02%. These data indicate that the first charge-discharge specific capacity of NCM811 is negatively affected by Al2O3 coating, but the first charge-discharge Coulomb efficiency is slightly increased. For the coin LIB made of NCM811 coated with ZrO2 (C), the first charge specific capacity is 225.7 mAh/g, the first discharge specific capacity was 198.7 mAh/g, and the first charge-discharge Coulomb efficiency was 88.04%, respectively. The first charge and discharge capacities of NCM811 coated with ZrO2 is slightly lower than that of NCM811 without any coating, but the first charge and discharge Coulomb efficiency is increased slightly, which is consistent with that of Al2O3 coating. The first charge specific capacity of coin LIB made of NCM811 coated with LBO (D) is 230.0 mAh/g, the first discharge specific capacity is 204.3 mAh/g, and the first charge-discharge efficiency is 88.83%, respectively. These results are higher than those of both coated by Al2O3 and ZrO2. It is presumed that this may be due to the lack of electrochemical activity of both Al2O3 and ZrO2 coating, which may hinder the insertion/removal of some Li+ ions, resulting in a slight decrease in the specific capacities of charge/discharge. However, the surface interface structure of NCM811 can be stabilized by Al2O3 or ZrO2 coating layer, and the reaction between the electrode material and the electrolyte can be restrained to some extent. As a result, the Coulomb efficiencies of charge/discharge are improved. In addition to the advantages of normal surface coatinging layer, LBO as a fast ionic conductor has a good ionic conductivity and certain electrochemical activity when it is coated on the surface of NCM811. It is conducive to the transport of lithium ions during charging and discharging. This is an important reason why LBO coating layer has a better electrochemical performance than Al2O3 and ZrO2 coatings. The first charge capacity, discharge capacity and Coulomb efficiency of NCM811 coated with LBO (D) are slightly higher than those of NCM811 without any coating, and also better than those of NCM811 coated with Al2O3 and ZrO2.
Figure 6. First charge-discharge curves of the coin LIBs composed of NCM811 and NCM811 coated with different materials (A-uncoated, B-Coated by Al2O3, C-Coated by ZrO2, D-Coated by LBO).
Table 2. First charge and discharge capacities and Coulomb efficiencies of the coin LIB with NCM811 and NCM811 coated by Al2O3, ZrO2, and LBO.
From Figure 7 and Table 3, it can be seen that the water values of the electrode made of NCM811 (A) without any coating rises from 215.1 ppm to 670.2 ppm when it is stored at room temperature for 72 h at a relative humidity of 10% RH. It can be found that the water contents of the uncoated, Al2O3, ZrO2, and LBO-coated NCM811 electrodes are increased by 455.1, 274.5, 312.0, and 255.1 ppm after 72 h of storage, respectively. The water absorption of all the coated NCM811 cathodes during storage is less than that of the uncoated one. The lower water content in the cathode is beneficial to both the better discharge capacity and Coulomb efficiency of LIB (Li et al., 2016). The NCM811 cathode coated with LBO has the smallest moisture increment and has the best storage stability.
Figure 7. Water value curves of NCM811 cathodes preserved at 25°C and 10% RH (A-uncoated, B-coated by Al2O3, C-coated by ZrO2, D-coated by LBO).
Table 3. Water values of NCM811 and the NCM coated with Al2O3, ZrO2 and LBO, stored at 25°C in 10% RH humidity environment.
From Figure 8, it can be seen that after 100 cycles, the LIB capacity retentions of pure NCM811, NCM811 coated by Al2O3, ZrO2, and LBO are decreased to 98.89, 99.61, 99.66, and 99.78% of the initial capacity, respectively, demonstrating that the coated NCM811 cathode materials can give better capacity retentions. In Comparison of the data of capacity retention rate after 100 charge/discharge cycles in Figure 8 with the data in the literature listed in Table 1, it can be found that the cathode material in this work shows a higher capacity retention rate after the same number of cycles, thus demonstrating a better cycle performance. Compared with Al2O3-coated and ZrO2-coated NCM811 materials, NCM811 coated with LBO has a better cycling performance. The improved electrochemical performances of the coated samples are attributed to the protective function of the coating layer. The improved cycling performance of the coated cathode materials is attributed to the reduced electrolyte decomposition reactions and the alleviation of the impedance (see Figure 9) due to the existence of coating layers (Wang et al., 2013). The existence of coating layer is also conducive to preventing the excessive expansion of the active material particles, thus making the structure of the electrode stable and conducive to the stability of the charging and discharging processes (Zhou et al., 2019).
Figure 8. Capacity retention as a function of cycle number of the LIBs composed of NCM811 and NCM811 coated by different materials (A-uncoated, B-coated by Al2O3, C-coated by ZrO2, D-coated by LBO).
Figure 9. DC resistance data of the coin LIBs consisting of NCM811 and NCM811 coated with different materials during charge/discharge cycling (A-uncoated, B-coated by Al2O3, C-coated by ZrO2, D-coated by LBO).
Internal resistance of a battery is an importance parameter that can have a significant effect on its electrochemical performance such as cycling and power characteristics. Different cathode materials can give different internal resistances, leading to different electrochemical performances of the batteries (Shao et al., 2010). From Figure 9, it can be seen that the initial DC internal resistances of the coin LIBs composed of uncoated NCM811 (A) is 62.4 mΩ, and the resistance increases to 92.3 mΩ after 100 cycles. The initial DC internal resistance of the coin LIBs made of NCM811 coated with Al2O3 (B) is 63.6 mΩ, and the resistance value increases to 86.6 mΩ after 100 cycles. The initial DC resistance of the coin LIB made of NCM811 coated with ZrO2 (C) is 66.2 mΩ, which increases to 89.1 mΩ after 100 cycles. The initial DC resistance of the coin LIB made of NCM811 coated with LBO (D) is 64.9 mΩ, which increases to 82.5 mΩ after 100 cycles. Although the initial DC resistances of the coated NCM811 materials are slightly higher than that of uncoated one, the increasing trends of the resistances are slower than that of uncoated one. These slow increases can be beneficial to the stability of the electrochemical performance during the cycling. In comparison, NCM811 coated with LBO has the best resistance stability. Compared with Al2O3 and ZrO2 coating materials without electrochemical activity, LBO coating with NCM811 has obvious electrochemical performance advantages. LBO is a fast ionic conductor, which not only makes NCM811 higher capacity, but also the LBO coating is conducive to the migration and transfer of lithium ions between the electrode interfaces, reducing the irreversible loss of lithium ions in the process of charging and discharging, so that the lithium-ion battery has a better capacity retention and a smaller resistance increase in the process of cycling.
In this paper, the precursor Ni0.8Co0.1Mn0.1(OH)2 is prepared by a co-precipitation method. Using this precursor, a cathode material of LiNi0.8Co0.1Mn0.1O2 (NCM811) for lithium ion battery (LIB) is synthesized by mixing Ni0.8Co0.1Mn0.1(OH)2 and LiOH and sintering twice. Al2O3, ZrO2, and LBO are used to coat on NCM811 to form the coated cathode materials by a wet chemical method. The effects of Al2O3, ZrO2, and LBO coatings on the morphologies, structures, compositions, and electrochemical properties of NCM811 are studied by both the physical characterization and electrochemical measurements. XRD results show that the coating layers do not change the original lattice structure of bulk NCM811. The materials of NCM811 without any coating and coated with Al2O3, ZrO2, and LBO all have a good hexagonal α-NaFeO2 layered structure. The results of SEM, TEM, and XPS show that the prepared NCM811 with particle sizes of 3–16 μm can be successfully coated by Al2O3, ZrO2, and LBO with the coating-layers thicknesses of 20–200 nm.
To validate the effects of coating layers on the material properties, coin LIBs are assembled with the uncoated NCM811, Al2O3-coated, ZrO2-coated, and LBO-coated NCM811 materials as the cathodes. Experiment results show that although the first charge-discharge specific capacities of NCM811 coated with Al2O3 and ZrO2 are slightly smaller than those of uncoated NCM811, their Coulomb efficiencies of the first charge-discharge are increased after the coating. However, the first charge capacity (230.0 mAh/g), the first discharge capacity (204.3 mAh/g) and coulomb efficiency (88.83%) of NCM811 coated with LBO show the higher performance than those of uncoated one.
Regarding the water adsorption, the cathodes made of materials of pure NCM811, coated with Al2O3, ZrO2, and LBO, respectively, are stored at room temperature with 10% RH humidity for 72 h, and the changes of water contents of the cathodes during storage are measured, and the results show that the water contents of the uncoated NCM811, Al2O3, ZrO2, and LBO-coated NCM811 cathodes are increased by 455.1, 274.5, 312.0, and 255.1 ppm, respectively. The water absorption performances of the coated NCM811 cathodes during storage are better than that of the uncoated NCM811 one. The NCM811 cathode coated with LBO has the smallest moisture increment, suggesting that it has the best storage stability.
For studying cycling performances, the capacity retentions of the pure NCM811, coated with Al2O3, ZrO2, and LBO based LIBs are tested to be 99.50, 99.77, 99.84, and 99.91% of the initial capacities after 50 charge/discharge cycles, and the corresponding cathode resistances are increased by 19.6, 14.0, 13.6, and 12.2 mΩ, respectively. These results demonstrate that the cycle performance and resistance stability of the NCM811 material can be significantly improved by the coating. The cycle performance and resistance stability of NCM811 coated with LBO are better than those of NCM811 coated with Al2O3 and ZrO2.
Based on the experiment observation and data analysis, it can be concluded that the charge-discharge specific capacity, Coulomb efficiency, water absorption stability, cycle characteristics and resistance stability of the NCM811 cathode material can be significantly improved by coating it using LBO particularly. Considering that the amount of coating material is small, the coating process is relatively simple, and the improved electrochemical performance of NCM811, the cost would not be increases significantly. So in conclusion, the surface coating to the particles of cathode materials using LBO is an effective and practical modification method to improve the electrochemical performance of LIBs. In future study of the coating modification of NCM811, the performance stability at high temperature and the performance at long cycle should be further improved.
The datasets generated for this study are available on request to the corresponding author.
HZ designed experiments, carried out experiments, and analyzed experimental results. JX analyzed experimental results. JZ designed experiments, carried out experiments, and wrote the manuscript.
The authors declare that the research was conducted in the absence of any commercial or financial relationships that could be construed as a potential conflict of interest.
We gratefully acknowledge the support from Ph.D. Program of Shanghai University, the financial supports from the National Key Research and Development Program of China (2017YFB0102200; 2017YFB0102900) and the Shanghai Pujiang Program (17PJD016).
Aurbach, D. (2000). Review of selected electrode-solution interactions which determine the performance of Li and Li ion batteries. J. Power Sources 89, 206–218. doi: 10.1016/S0378-7753(00)00431-6
Belt, J. R. (2010). Battery Test Manual for Plug-In Hybrid Electric Vehicles. Fuel Cells. U.S. Department of Energy Office of Scientific and Technical Information.
Bi, Y., Wang, T., Liu, M., Du, R., Yang, W. C., Liu, Z., et al. (2016). Stability of Li2CO3 in cathode of lithium ion battery and its influence on electrochemical performance. RSC Adv. 6, 19233–19237. doi: 10.1039/C6RA00648E
Cao, Y., Qi, X., Hu, K., Wang, Y., Gan, Z., Li, Y., et al. (2018). Comductive polymers encapsulatin to enhance electrochemical performance of Ni-Rich cathode material for Li-ion batteries. ACS Appl. Mater. Interfaces 10, 18270–18280. doi: 10.1021/acsami.8b02396
Chan, H. W., Duh, H. W., and Sheen, S. R. (2005). Surface treatment of the lithium boron oxide coated LiMn2O4 cathode material in Li-ion battery. Key Eng. Mat. 280–283, 671–676. doi: 10.4028/www.scientific.net/KEM.280-283.671
Chen, Y., Wang, X., Zhang, J., Chen, B., Xu, J., Zhang, S., et al. (2019). Zhang, Al2O3-coated Li1.2Mn0.54Ni0.13Co0.13O2 nanotubes as cathode materials for high-performance lithium ion batteries. RSC Adv. 9, 2172–2179. doi: 10.1039/C8RA09428D
Dong, Y., Zhao, Y., Duan, H., and Huang, J. (2015). Electrochemical performance and lithium-ion insertion/extraction studies of the novel Li3ZrO3, anode materials. Electrochim. Acta 161, 219–225. doi: 10.1016/j.electacta.2015.01.220
Hao, Z., Xu, X., Wang, H., Liu, J., and Yan, H. (2019). In situ growth of Co3O4 coating layer derived from MOFs on LiNi0.8Co0.15Al0.05O2 cathode materials. Ionics 25, 2469–2476. doi: 10.1007/s11581-018-2726-9
Huang, Y., Chen, J., Ni, J., Zhou, H., and Zhang, X. (2009). A modified ZrO2-coating process to improve electrochemical performance of LiNi1/3Co1/3Mn1/3O2. J. Power Sources 188, 538–545. doi: 10.1016/j.jpowsour.2008.12.037
Khan, M. A., Zhao, H., Zou, W., Chen, Z., Cao, W., Fang, J., et al. (2018). Recent progresses in electro-catalysts for water electrolysis. Electro. Ener. Rev. 1, 483–530. doi: 10.1007/s41918-018-0014-z
Li, D. C., Muta, T., Zhang, L. O., Yoshio, M., and Noguchi, H. (2014). Effect of synthesis method on the electrochemical performance of LiNi1/3Co1/3Mn1/3O2. J. Power Sources 132, 150–155. doi: 10.1016/j.jpowsour.2004.01.016
Li, G., Chen, X., Liu, Y., and Wang, W. (2018). One-time sintering process to synthesize ZrO2-coated LiMn2O4 materials for lithium-ion batteries. RCS Adv. 8, 16753–16761. doi: 10.1039/C8RA01421C
Li, J., Daniel, C., An, S. J., and Wood, D. (2016). Evaluation residual moisture in lithium-ion battery electrodes and its effect on electrode performance. MRS Adv. 15, 1029–1035. doi: 10.1557/adv.2016.6
Li, Q., Dang, R., Chen, M., Lee, Y., Hu, Z., and Xiao, X. (2018). Synthesis method for long cycle lithium-ion cathode material: nickel-rich core-shell LiNi0.8Co0.1Mn0.1O2. ACS Appl. Mater. Interfaces. 10, 17580–17860. doi: 10.1021/acsami.8b02000
Li, T., Yuan, X.-Z., Zhang, L., Song, D., Shi, K., and Bock, C. (2019). Degradation mechanisms and mitigation strategies of nickel-rich NMC-based lithium-ion batteries. Electro. Ener. Rev. doi: 10.1007/s41918-019-00053-3. [Epub ahead of print].
Lim, S. N., Ahn, W., Yeon, S. H., and Park, S. B. (2014). Enhanced elevated-temperature performance of Li(Ni0.8Co0.15Al0.05)O2 electrode coated with Li2O-2B2O3 glass. Electrochim. Acta 136, 1–9. doi: 10.1016/j.electacta.2014.05.056
Ma, F., Wu, Y., Wei, G., Qiu, S., and Qu, J. (2019). Enhanced electrochemical performance of LiNi0.8Co0.1Mn0.1O2 cathode via wet-chemical coating of MgO. J. Solid State Elect. 23, 2213–2224. doi: 10.1007/s10008-019-04308-3
Min, K., Seo, S. W., Song, Y. Y., Lee, H. S., and Cho, E. (2017). A first-principles study of the preventive effects of Al and Mg doping on the degradation in LiNi0.8Co0.1Mn0.1O2 cathode materials. Phys. Chem. Chem. Phys. 19, 1762–1769. doi: 10.1039/C6CP06270A
Nobili, F., Croce, F., Tossici, R., Mechini, I., Reale, P., and Marassi, R. (2012). Sol-gel synthesis and electrochemical characterization of Mg-/Zr-doped LiCoO2 cathodes for Li-ion batteries. J. Power Sources 197, 276–284. doi: 10.1016/j.jpowsour.2011.09.053
Noh, H. J., Youn, S., Yoon, C. S., and Sun, Y. K. (2013). Comparison of the structural and electrochemical properties of layered Li[NixCoyMnz]O2 (x=1/3, 0.5, 0.6, 0.7, 0.8 and 0.85) cathode materials for lithium-ion batteries. J. Power Sources 233, 121–130. doi: 10.1016/j.jpowsour.2013.01.063
Noh, M., Lee, Y., and Cho, J. (2006). Water adsorption and storage characteristics of optimized LiCoO2 and LiNi1/3Co1/3Mn1/3O2 composite cathode materials for Li-ion cells. J. Electrochem. Soc. 153, A935–A940. doi: 10.1149/1.2186041
Shao, S., Wu, F., Yang, L., Gao, L., and Burke, A. F. (2010). A measurement method for determination of dc internal resistance of batteries and supercapacitors. Electrochem. Commun. 12, 242–245. doi: 10.1016/j.elecom.2009.12.004
Song, H. G., Kim, J. Y., Kim, K. T., and Park, Y. J. (2011). Enhanced electrochemical properties of Li(Ni0.4Co0.3Mn0.3)O2 cathode by surface modification using Li3PO4-based materials. J. Power Sources 196, 6847–6855. doi: 10.1016/j.jpowsour.2010.09.027
Song, L., Li, X., Xiao, Z., Li, L., Gao, Z., and Zhu, H. (2019). Effect of Zr doping and Li2O-2B2O3 layer on the structural electrochemical properties of LiNi0.5Co0.2Mn0.3O2 cathode material: experiments and first-principle calculations. Ionics 25, 2017–2026. doi: 10.1007/s11581-018-2636-x
Tan, S., Wang, L., Bian, L., Xu, J., Ren, W., Hu, P., et al. (2015). Highly enhanced low temperature discharge capacity of LiNi1/3Co1/3Mn1/3O2 with lithium boron oxide glass modification. J. Power Sources 277, 139–146. doi: 10.1016/j.jpowsour.2014.11.149
Wang, D., Li, X., Wang, Z., Guo, H., Zheng, X., Xu, Y., et al. (2015). Multifunctional Li2O-2B2O3 coating for enhancing high voltage electrochemical performance and thermal stability of layered structured LiNi0.5Co0.2Mn0.3O2 cathode materials for lithium ion batteries. Electrochim. Acta 174, 1225–1233. doi: 10.1016/j.electacta.2015.06.111
Wang, Y. J., Fang, B., Zhang, D., Li, A., Wiikinson, D. P., Iganszak, A., et al. (2018). A review of carbon-composited materials as air-electrode bifunctional electrocatalysts for metal–air batteries. Electro. Ener. Rev. 1, 1–34. doi: 10.1007/s41918-018-0002-3
Wang, Z., Liu, E., Guo, L., Shi, C., He, C., Li, J., et al. (2013). Cycle performance improvement of Li-rich layered cathode material Li[Li0.2Mn0.54Ni0.13Co0.13]O2 by ZrO2 coating. Surf. Coat Tech. 235, 570–576. doi: 10.1016/j.surfcoat.2013.08.026
Wen, X., Liang, K., Tian, L., Shi, K., and Zheng, J. (2018). Al2O3 coating on Li1.256Ni0.198Co0.082Mn0.689O2.25 with spinal-structure interface layer for superior performance Lithium ion batteries. Electrochim. Acta 260, 549–556. doi: 10.1016/j.electacta.2017.12.120
Wu, J., Han, C., Wu, H., Liu, H., Zhang, Y., and Lu, C. (2019). Nano coating of Ce-tannic acid metal-organic coordination complex: surface modification of layered Li0.12Mn0.6Ni0.2O2 by CeO2 coating for lithium-ion batteries. Ionics 25, 3031–3040. doi: 10.1007/s11581-018-2823-9
Yoon, W. S., Nam, K. W., Jiang, D., Chuang, K. Y., Hanson, J., Chen, J. M., et al. (2012). Structural study of coating effect on the thermal stability of charged MgO-coated LiNi0.8Co0.2O2 cathodes investigated by in situ XRD. J. Power Sources 217, 128–134. doi: 10.1016/j.jpowsour.2012.05.028
Zhang, H., Zhao, H., Khan, M. A., Xu, J., Zhang, L., and Zhang, J. (2018). Recent progress in advanced electrode materials, separators and electrolytes for lithium batteries. J. Mater. Chem. 42, 20564–20620. doi: 10.1039/C8TA05336G
Zhang, K., Li, B., Zuo, Y., Song, J., Shang, H., Ning, F., et al. (2019). Voltage decay in layered Li-rich Mn-based cathode materials. Electro. Ener. Rev. doi: 10.1007/s41918-019-00049-z. [Epub ahead of print].
Zhang, L., Wilkinson, D. P., Liu, Y., and Zhang, J. (2018). Progress in nanostructured (Fe or Co)/N/C non-noble metal electrocatalysts for fuel cell oxygen reduction reaction. Electrochim. Acta 262, 326–336. doi: 10.1016/j.electacta.2018.01.046
Zhou, H. M., Zhu, Y. H., Sun, W. J., and Liu, Z. Z. (2019). Electrochemical performance of Al2O3 pre-coated spinel LiMn2O4. Rare Met. 38, 128–135. doi: 10.1007/s12598-014-0418-9
Keywords: LiNi0.8Co0.1Mn0.1O2, coating, cathode materials, lithium-ion batteries, electrochemical performance
Citation: Zhang H, Xu J and Zhang J (2019) Surface-Coated LiNi0.8Co0.1Mn0.1O2 (NCM811) Cathode Materials by Al2O3, ZrO2, and Li2O-2B2O3 Thin-Layers for Improving the Performance of Lithium Ion Batteries. Front. Mater. 6:309. doi: 10.3389/fmats.2019.00309
Received: 12 October 2019; Accepted: 15 November 2019;
Published: 29 November 2019.
Edited by:
Shuhui Sun, Institut National de la Recherche Scientifique (INRS), CanadaReviewed by:
Yongliang Li, Shenzhen University, ChinaCopyright © 2019 Zhang, Xu and Zhang. This is an open-access article distributed under the terms of the Creative Commons Attribution License (CC BY). The use, distribution or reproduction in other forums is permitted, provided the original author(s) and the copyright owner(s) are credited and that the original publication in this journal is cited, in accordance with accepted academic practice. No use, distribution or reproduction is permitted which does not comply with these terms.
*Correspondence: Jiujun Zhang, aml1anVuLnpoYW5nQGkuc2h1LmVkdS5jbg==
Disclaimer: All claims expressed in this article are solely those of the authors and do not necessarily represent those of their affiliated organizations, or those of the publisher, the editors and the reviewers. Any product that may be evaluated in this article or claim that may be made by its manufacturer is not guaranteed or endorsed by the publisher.
Research integrity at Frontiers
Learn more about the work of our research integrity team to safeguard the quality of each article we publish.