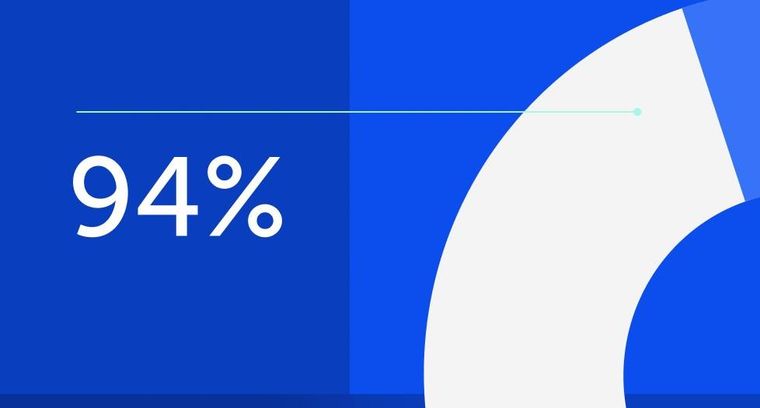
94% of researchers rate our articles as excellent or good
Learn more about the work of our research integrity team to safeguard the quality of each article we publish.
Find out more
MINI REVIEW article
Front. Mater., 13 November 2018
Sec. Semiconducting Materials and Devices
Volume 5 - 2018 | https://doi.org/10.3389/fmats.2018.00065
This article is part of the Research TopicFrontiers in Materials: Rising Stars View all 56 articles
Energy harvesting is one of the most rapidly growing of the emerging technologies. This field has arrived at the hybrid and multi-source era, where hybrid structures and novel materials are able to boost the energy conversion efficiency and/or make the harvesters capable of benefitting from multiple energy sources simultaneously. Such hybrid and multi-source energy harvesters have not frequently been reviewed in the past, potentially because of the small number of publications compared to that of their single-source and individual counterparts. However, as their number is becoming larger, it is now necessary to give sufficient and frequent reviews of developments in the field. Furthermore, an increasing number of developed energy harvesters are moving out of the laboratory into industrial markets. In practice, energy harvesters need to be integrated with energy storage and/or end users such as sensors and wireless sensor networks. Therefore, the harvester-storage and harvester-sensor integration systems also need to be reviewed frequently. This mini review includes works reported in the first half of 2018 and provides a timely update to the published review. It focuses on the above-mentioned hybrid and multi-source energy harvesters as well as on integrated harvesters, energy storage systems and end users (e.g., sensors), including CMOS (complementary metal-oxide-semiconductor) technology-based harvesters and systems.
Energy harvesting technology covers the conversion of solar/light, vibration/kinetic, wind/fluidic, magnetic, and thermal energies into electricity, via various mechanisms such as the photovoltaic, piezoelectric, electromagnetic, electrostatic, triboelectric, magnetostrictive, thermoelectric, and pyroelectric effects. Recently, a comprehensive review of energy harvesting research has been published (Bai et al., 2018). It summarizes single-source energy harvesters and focuses on hybrid and multi-source energy harvesters with novel materials and structures. In addition, the latest comprehensive reviews on piezoelectric energy harvesters, where the majority of energy harvesting research is relevant, have now been published (Uchino, 2018; Yang et al., 2018c).
This mini review focuses on hybrid and multi-source energy harvesters as well as those integrated with energy storage and/or sensors. Works reported in the first half of 2018 are included and it is recommended to be read together with the reference (Bai et al., 2018) as this review provides a timely update. Hybrid, single-source energy harvesters contains recent work on hybrid, single-source energy harvesters. Hybrid, multi-source energy harvesters involves the work on hybrid, multi-source energy harvesters. Energy harvesters integrated with energy storage and/or end users introduces the work on the integration of energy harvesters with energy storage or sensors, including CMOS (complementary metal-oxide-semiconductor) technology-based harvesters and systems. In certain situations, energy storage systems can act simultaneously as harvesters and these works are also included in Energy harvesters integrated with energy storage and/or end users. Conclusions and perspectives concludes this mini review and provides perspectives for further research.
Kinetic energy harvesters have the largest number of available energy conversion mechanisms among all the harvesters, however each has its own advantages and disadvantages. The piezoelectric effect can generate only moderate output voltage and power density with a large matched resistive load (up to the MΩ level), but has the advantage of ease of miniaturization. The triboelectric effect can provide very high output voltage, high peak power density and flexibility, and this makes triboelectric harvesters considerably attractive for wearable applications. However, the matched resistive load for the maximum output power is usually also very large (tens of MΩ). This challenges the regulator designs in interface circuits (ICs). Also, triboelectric harvesters are mostly made with polymers which cannot endure the high or low temperatures which may be generated by combustion engines/electric motors or the ambient conditions in the polar winter, respectively. Electrostatic and electrostrictive effects can also provide solutions for flexibility or miniaturization but an external voltage source is needed in most cases. The electromagnetic effect is able to offer large output power if space is not limited but, otherwise, miniaturization and low power density will be the main issues. The magnetostrictive effect requires the presence of both piezoelectric materials and permanent magnets in order to harvest kinetic energy. On the other hand, this enables structural hybridization, thus allowing multiple sources (i.e., kinetic energy and magnetic field) to be harvested simultaneously.
Because of energy losses, each of the above-mentioned effects has a limit on the harvestable kinetic energy and extractable electricity and hence a limit on the energy conversion efficiency. Therefore, the hybridization of several kinetic energy harvesting effects into the same harvester not only complements each other's disadvantages but also helps to increase the overall efficiency. Hybrid harvesters for kinetic energy are the most common single-source harvesters.
A bi-directional, piezoelectric-electromagnetic hybrid harvester built around a tube-shaped frame, combining two piezoelectric cantilevers with cuboidal magnets as tip masses, a suspended cylindrical magnet and a set of coils, has been reported (Fan et al., 2018a). The two cantilevers were attached at both ends of the tube frame. The cylindrical magnet was suspended in the tube. The coils were wound around the wall of the tube. The harvester could be excited in two directions, i.e., along the tube length and thus driving the suspended magnet to move in the tube, or perpendicular to the tube length and thus bending the cantilevers. In the former scenario, the moving magnet passes through the coil, harvesting the kinetic energy via the electromagnetic effect. It also couples with the two magnets on the cantilever tips, forcing the cantilevers to bend and thus harvesting the energy via the piezoelectric effect simultaneously. In such a working mode, the harvester could be driven at an ultra-low frequency (< 10 Hz). In a capacitor charging test, this hybrid harvester showed an efficiency increase of up to 49 and 14% compared to its electromagnetic and piezoelectric individual counterparts, respectively (Fan et al., 2018a).
Another piezoelectric-electromagnetic hybrid harvester has been designed for higher operating frequencies (60–120 Hz) (Li et al., 2018a). A piezoelectric beam was fixed at both ends, with a magnet attached at the center of the beam. A set of coils was placed under the magnet with an adjustable gap. When the beam was excited by vibration, the energy was harvested via both piezoelectric and electromagnetic effects. Although the data for efficiency calculation were not fully given, the output power of the hybrid harvester was shown to be up to 40 and 130% higher than those of its piezoelectric and electromagnetic counterparts, respectively (Li et al., 2018a). In addition, a couple of recently published patents reveal two-dimensional (or two-degree-of-freedom) piezoelectric-electromagnetic hybrid harvesters (Fan et al., 2018b,c). Such harvesters comprised a U-shaped piezoelectric cantilever or two-stage piezoelectric cantilevers, magnets, coils, springs, and other supportive structures. These harvesters, as claimed in the patent descriptions, featured compact design, high energy conversion efficiency, and low cost (Fan et al., 2018b,c).
Biomechanical energy (e.g., human body movement) is another important kinetic energy source which is attractive in the application of wearable electronics. An electromagnetic-triboelectric hybrid harvester has been designed and fabricated for the energy generated from the swinging behavior of human arms during locomotion (Maharjan et al., 2018). An ABS (acrylonitrile butadiene styrene) ring tube was fabricated by 3D printing and a 50 μm PTFE (polytetrafluoroethylene) film with a nanowire-like surface was fabricated and then attached on the inner wall of the ABS tube. Inter-digitated Al electrodes and Cu coils were wrapped around the tube and the Al and Cu layers were separated by Kapton tape. Meanwhile, an NdFeB magnetic ball was placed in the tube. Such a harvester can be worn on the wrist, thus harvesting the human arm swinging motion during walking or running. The Al electrodes and nanowire-like surface of the PTFE acted as the triboelectric harvester, whilst the magnet and Cu coils acted as the electromagnetic harvester. In a capacitor charging test this hybrid harvester showed efficiency increases of 9 and 300% at the early stage of the charging compared to its electromagnetic and triboelectric individual counterparts, respectively. At the later stage of the charging, the increases were 36 and 25%, respectively. With a 5 s charging, the harvested energy was able to power a wristwatch to operate for 410 s. This harvester could also power a heart-rate sensor and monitor real-time signals of the wearer's heart rates.
Another electromagnetic-triboelectric hybrid harvester has been created for oceanic energy harvesting (Feng et al., 2018). Figure 1A explains the structure of this harvester. Seven Al electrodes covered by PTFE were fixed on an acrylic substrate. The electrodes were made into three groups, forming a honeycomb-like three electrode structure, as marked by different colors in the figure. A magnet was suspended above the substrate via three springs while the bottom of the magnet was covered by another Al electrode, thus acting as the triboelectric harvester in cooperation with the PTFE and other electrodes. The triboelectric harvester could work in both in-plane sliding mode and vertical contact-separation mode. Seven sets of Cu coils were attached on the back of the substrate, acting as the electromagnetic harvester together with the magnet. In a capacitor charging test, the hybrid harvester achieved 54 and 150% efficiency increases compared to those of its electromagnetic and triboelectric individual counterparts (Feng et al., 2018). Table 1 summarizes the hybrid, single-source energy harvesters reviewed in this paper.
Figure 1. (A) Schematic of a honeycomb-like, three-electrode and triboelectric-electromagnetic hybrid energy harvester for ocean waves. Reproduced with permission (Feng et al., 2018). Copyright 2018, Elsevier. (B) Schematic of a hybrid harvester for vibrational and magnetic energy. Reproduced under the terms of the Creative Commons Attribution (CC BY) license (Hu et al., 2018). Copyright 2018, AIP Publishing. (C) Schematic of a triboelectric-photovoltaic hybrid energy harvester for self-powered lighting. Reproduced with permission (Cao et al., 2018). Copyright 2018, John Wiley and Sons. (D) Schematic of a thermoelectric energy harvester employing piezoelectric effect (left) and its demonstration of surface temperature mapping function (right). Reproduced with permission (Chun et al., 2018). Copyright 2018, American Chemical Society. (E) Schematic and working principle of a monolithic, solar-powered tactile sensor. Reproduced with permission (Saraf et al., 2018). Copyright 2018, John and Wiley and Sons. (F) Schematic of the Li-ion batteries working as a kinetic energy harvester simultaneously. Reproduced with permission (Schiffer and Arnold, 2018). Copyright 2017, Springer Nature.
Table 1. Summary of the hybrid energy harvesters and integrated harvester-storage/harvester-end user systems.
In practice, a single energy source may not always be powerful and stable enough for a harvester to generate sufficient electricity for the end usage. Multi-source energy harvesting through structural hybridization or multi-functional materials addresses this issue. By employing magnetostrictive and piezoelectric materials at the same time, ambient magnetic waves dissipated from electric devices and power transmission lines can be harvested. For instance, a magneto-mechano-electric generator consisting of a highly textured Fe-Ga alloy (magnetostrictive) and a Pb(Mg1/3Nb2/3)O3-Pb(Zr,Ti)O3 (PMN-PZT) single crystal macro-fiber composite (piezoelectric) has been reported to achieve an output power density of 3.22 mW/cm3 with < 1 mT magnetic input energy. This power density was an order of magnitude higher than that using piezoelectric cantilevers to harvest kinetic energy (Annapureddy et al., 2018). A wireless sensor network for the IoT (Internet of Things) could be powered by such harvested energy for timing and sensing (pressure and temperature) functions. Although simultaneously harvesting kinetic energy via the piezoelectric effect was not realized in this work, it is definitely an option for such a hybrid structure.
A specially designed piezoelectric cantilever with magnets as tip masses has also been reported to simultaneously harvest magnetic and vibrational energy (Hu et al., 2018). Figure 1B shows the configuration. A beryllium bronze beam was fabricated with a special curve which was fixed with an Al holder and a PZT (Pb(Zr,Ti)O3) piezoelectric transducer was attached above the curve and bridged the two parts of the beam. Two magnets were embedded on both tips of the beam. The hybrid harvester was placed close to a wire emitting a magnetic field and subject to a vibration. An output power increase of up to 300% was achieved when simultaneously harvesting both energy sources compared to that of harvesting either single source (Hu et al., 2018).
Kinetic and solar energy can be considered the most pervasive and commonly co-existing ambient energy sources, where harvesting of both simultaneously can be significantly beneficial. A self-powered lantern based on a triboelectric-photovoltaic hybrid structure has been built for harvesting wind and light energy (Cao et al., 2018). Figure 1C shows the schematic of the configuration. A transparent PLA (polylactic acid) tube was connected to a central axis rod via bearings and transparent, inter-digitated ITO electrodes were coated on the inner wall of the tube. A rod coated with a layer of FEP (fluorinated ethylene propylene) film was placed on top of the ITO electrodes. A DSSC (dye-sensitized solar cell) was also mounted in the tube as shown in the figure. In addition, a SLB (soft lithium battery) and 10 LEDs (light-emitting diodes) were connected. The PLA tube rotated when driven by the wind, and the freely moving FEP rod generated friction with the ITO electrodes, thus harvesting the wind energy through the triboelectric effect. Meanwhile, solar energy was harvested by the DSSC. The harvested energy was stored in the SLB and used for lighting the LEDs. Being charged for 0.88 h, the SLB could be discharged for 4.12 h with 10 μA current (Cao et al., 2018). This performance was equivalent to 100 and 33% efficiency increases compared to those of the individual triboelectric generator and solar cell, respectively.
A lamination of Al, Si, PEDOT:PSS (poly(3,4-ethylenedioxythiophene):poly(styrenesulfonate)), Ag finger electrode and PDMS (polydimethylsiloxane) from bottom to top has been proposed to harvest solar energy and raindrops (Liu et al., 2018d). The novelty of this hybrid harvester is that the PEDOT:PSS layer acted not only as an anti-reflection layer for the Si solar cell but also as the mutual electrode for the triboelectric component (PDMS). The raindrops hit the PDMS layer and thus electricity was generated via the triboelectric effect which complemented the efficiency decrease of the solar cell on rainy days. The efficiency of the solar cell was measured to be 13.6% under a standard AM 1.5G solar spectrum and the output power density of the triboelectric component was simulated to be 1.74 mW/m2 (Liu et al., 2018d).
Apart from structural hybridization as introduced above, multi-source energy harvesters can also be realized with multi-functional materials. Details have been given in the reference (Bai et al., 2018). Recently, a PVDF (polyvinylidene fluoride)-ZnO composite has been reported (Ma et al., 2018). The composite consisting of 33 wt% ZnO nanowires and PVDF polymer helped to increase the output voltage by over 300% compared to that using PVDF only. Although ZnO has a wide band gap and cannot absorb the visible range of the solar spectrum, such a composite does provide a potential method of making multi-functional materials by replacing the ZnO filler with some narrow band gap materials. In this case the PVDF matrix can perform as a piezoelectric harvester and the filler as a photovoltaic harvester.
The pyroelectric effect is known for the energy harvesting from temperature fluctuations. A pyroelectric harvester has been reported to utilize a vortex to generate the temperature fluctuation and thus harvest wind energy via the pyroelectric effect (Raouadi and Touayar, 2018). The vortex generator was a right-angled substrate on which a PVDF film was deposited on the horizontal part. The wind flowed along the horizontal direction and when it collided with the vertical part of the substrate, a vortex and thus a temperature fluctuation was generated and applied to the PVDF film. An output power density of 2.82 μW/cm2 was obtained. The main advantage of this harvester was that it was able to capture energy even with a very weak air flow (down to 1 m/s velocity) (Raouadi and Touayar, 2018). Although the piezoelectric effect was not mentioned, PVDF is also ferroelectric and well known for its co-exhibition of piezoelectric and pyroelectric effects. Therefore, this structure could naturally become a multi-source harvester by employing the piezoelectric effect at the same time. Stronger ferroelectric materials e.g., PZT (Pb(Zr,Ti)O3), PMN-PT (Pb(Mg1/3Nb2/3)O3-PbTiO3), Mn-doped BNT-BT ((Bi0.5Na0.5)TiO3-BaTiO3), and Sr0.5Ba0.5NbO3 (Bowen et al., 2014a,b) could also replace the PVDF in order to improve the piezoelectric and pyroelectric performance.
A recently published patent has released the design of an umbrella apparatus which managed to incorporate photovoltaic, piezoelectric, electromagnetic, and radio frequency (RF) energy harvesters into different parts of an umbrella (Lu et al., 2018). The canopy of the umbrella was replaced by a multi-layer lamination combining photovoltaic and piezoelectric energy harvesters. The lamination consisted of an inverted polymer solar cell layer (He et al., 2012), a PVDF piezoelectric layer, electrode layers, and other supportive layers. When the energy harvesting canopy was open, solar and kinetic (i.e., wind and raindrops) energy could be harvested. Meanwhile, the open canopy could spin when subjected to wind force, thus driving a miniature windmill (electromagnetic energy harvester) embedded in the shaft of the umbrella. In addition, the shaft of the umbrella could act as a monopole antenna and an RF energy harvesting circuit could be installed in the shaft in order to harvest RF energy. Furthermore, the shaft, in conjunction with a movable ferrule, contained a magnet and coils. When the canopy was closed, the umbrella could used as a cane. By striking the ferrule on the ground while walking, the magnet would be forced to move through the coils, forming another electromagnetic harvester. Apart from these energy harvesting components, the necessary DC-DC converters, switches, conductive leads and a rechargeable battery were also installed in the umbrella (Lu et al., 2018). Personal electronic devices could be charged through a port of the umbrella so that the entire umbrella became a self-powered, portable charging station. Hybrid, multi-source energy harvesters in this paper are also summarized in Table 1.
The IoT is undoubtedly where energy harvesting technology is aiming to have a significant impact. As the IoT requires an extensive number of sensors and wireless sensor networks, energy harvesters need to show their compatibility when integrated or utilized in different cases rather than only giving consideration to their output performance. As energy harvesters as individual components are becoming mature, there is an increasing number of publications demonstrating the feasibility of integrated energy harvesters with sensors or electricity consuming devices.
Piezoelectric energy harvesters have been integrated with structural health monitoring sensors for various constructions and bio-activity monitoring circuits used in implantable biomedical devices. In the former case piezoelectric patches were attached on a pipe which was undergoing forced vibrations, for the purposes of damage detection and indicators for control (Cahill et al., 2018). In the latter case, a self-powered neural activity monitor consisting of an impact-based piezoelectric harvester, a power transfer circuit, and a neural signal monitoring circuit was proposed (Kim et al., 2018). Both of them successfully demonstrated enough energy generated by the harvesters to power all the devices, as well as the feasibility and reliability of these methods.
A thermo-magneto-piezoelectric generator made with a non-linear piezoelectric cantilever, a hard magnet (Nd) and a soft magnet (Gd) has been reported (Chun et al., 2018). Figure 1D (left) shows the configuration of the harvester. The soft magnet was attached to the tip of the piezoelectric cantilever and the hard magnet was placed on the hot side. As the soft magnet was ferroelectric, it was attracted by the hard magnet but when they touched each other the temperature of the soft magnet became higher than the Curie temperature and it thus became paramagnetic (losing its permanent magnetic properties momentarily). The soft magnet was then released, driving the cantilever to oscillate and harvest the vibration energy. When the soft magnet cooled down and returned to the ferromagnetic state, a new cycle started. With this method, thermal energy (temperature gradient) was harvested via the piezoelectric effect. By applying Ag nanoparticles on the surface of the soft magnet, thermal transport was enhanced. This, together with the non-linearity of the cantilever, induced a 2200% higher output power compared to that of the linear counterpart (Chun et al., 2018). Such a harvester was used to power temperature-mapping sensors, thus monitoring the surface thermal variations, as shown in Figure 1D (right).
A self-powered chemical sensing system has been built by connecting a resistance-type gas (NO2) sensor with a contact-separate mode triboelectric harvester in series and an LED in parallel (Shen et al., 2018). The system worked as a vehicle exhaust detector, where the triboelectric harvester was driven by the motor vehicle exhaust flow, thus powering the gas sensor and giving an alarm via the LED. The system provided an independent operation regardless of the working frequency of the harvester.
An electromagnetic-triboelectric hybrid harvester-sensor integration has been reported to be able to harvest the kinetic energy of vehicular wheel rotation and act as a rotation speed and displacement sensor simultaneously (Yang et al., 2018a). With the hybrid harvesting working principle, an efficiency increase of 70–300% was achieved. The sensing data could be transmitted wirelessly, which provided a potential application for self-powered rotating mobile devices used in a remote environment (e.g., a moon car).
A floating wireless sensor node has been reported to be powered by solar and thermal energy via photovoltaic and thermoelectric harvesters, respectively. On a sunny day, the sensor node could operate self-sufficiently on the water, enabling long-range wireless communication between the sensor node and a gateway. The sensor node consumed 6.6 Wh energy per day (equivalent to 275 mW power), whilst the solar panels and thermoelectric generator could provide 349 and 18 mW power, respectively (Lee et al., 2018).
Some organic-halide perovskites, e.g., (CH3NH3)PbI3 (MAPbI3), are known for the co-existence of their ferroelectric and photovoltaic properties (Bai et al., 2018). Based on this unique feature, a self-powered tactile sensor has been fabricated using ZnO nanosheets and MAPbI3 film (Saraf et al., 2018). The schematic and working principle of the configuration is shown in Figure 1E. The MAPbI3 film was poled laterally, with the ZnO nanosheets aligned approximately perpendicular to the film. The ZnO acted as a pressure-sensitive drain. This means that when a pressure was applied, the ZnO nanosheets were forced to bend, thus increasing their interfacing area with the MAPbI3 film. Under illumination, this resulted in a higher charge collection and a pressure-sensitive modulation of the photocurrent. Such a solar-powered tactile sensor could be functional for more than 72 h after a 5 min poling process which required a 55 μW/h·cm2 energy budget (Saraf et al., 2018).
In practice, it is common to connect a solar cell with a Li-ion battery for simultaneous energy harvesting and storage. However, a monolithic photo-battery has been invented to substitute this two-component solar cell-battery combination (Ahmad et al., 2018). A highly photoactive 2D perovskite, ((C6H9C2H4NH3)2PbX4 (X = I or Br), was used for both photo-charging and Li-ion storage. The photo-battery was a lamination of glass, Al, stainless steel, metal Li, Whatman borosilicate paper soaked with LiPF6, 2D perovskite, Cu and FTO (fluorine-doped SnO2) layers, from bottom to top. The efficiency and capacity (up to 100 mAh/g) similar to that of individual photovoltaic materials and batteries, respectively, were retained.
Apart from their electrochemical properties, Li-ion intercalation materials are also mechanically active. When a stress is applied, they can exhibit a mechanical-electrochemical coupling that increases the voltage of the battery (Schiffer and Arnold, 2018). Therefore, a study into using Li-ion batteries to simultaneously harvest energy has been carried out (Schiffer and Arnold, 2018). Two 170 mAh pouch cells containing LCO (lithium cobalt oxide) and graphite electrodes were connected together as shown in Figure 1F. The green cell was compressed as the harvester and the blue one was the reference and reservoir. The efficiency of this harvester-storage integration was only 0.012%, much smaller than that of conventional kinetic energy harvesters such as piezoelectric, electromagnetic, and triboelectric systems (Bai et al., 2018). The theoretical efficiency was predicted to be 2.9%. A supercapacitor has been reported for the same purpose of simultaneously harvesting and storing energy (Yang et al., 2018b). A piece of anodic Al2O3 membrane with nanochannels was sandwiched between two layers of CNT (carbon nanotube)/Ti mesh electrodes. The electrolyte started to flow when subjected to pressure, causing the electrokinetic supercapacitor to operate in both harvesting and storage modes. The efficiency could reach 0.03–0.1% under one bar pressure or regulated external load.
As sensors (especially large sensors for the IoT) are made with CMOS technology, work focusing on the full integration of energy harvesters (and/or storage), interface circuits and sensors based on CMOS technology are also reviewed here. CMOS technology provides an approach to integrating all micro-scale components on one chip. Therefore, a number of CMOS-based power conditioning circuits (e.g., converters, rectifiers, etc.) for energy harvesting have been reported, including those allowing multiple energy sources as the input (Camarda et al., 2018; Katic et al., 2018; Li et al., 2018b; Liu et al., 2018a,b,c; Luo et al., 2018; McCullagh, 2018; Shi et al., 2018; Taghadosi et al., 2018; Wang et al., 2018; Yi et al., 2018a,b; Yoon et al., 2018).
A low-power battery-less energy harvesting system implemented in a CMOS−130 nm technology for IoT applications used a dual-mode DC-DC converter to harvest solar and kinetic energy via photovoltaic and piezoelectric transducers, respectively (Elhebeary et al., 2018). A supercapacitor was used as the storage. On-chip, there were also a programmable switch to optimize the efficiency of the system and a maximum power point tracking circuit (MPPT). This circuit realized self-starting and a peak efficiency of 90.5% (the ratio of rectified energy to harvested energy) (Elhebeary et al., 2018). Meanwhile, a triple-source hybrid circuit implemented in a CMOS−180 nm technology managed simultaneously to extract thermal energy via a thermoelectric harvester and vibration via electromagnetic and piezoelectric harvesters, and then deliver a single DC output (Ulusan et al., 2018). The system included an on-chip cross-coupled charge pump to boost the thermoelectric voltage, a low drop-out AC-DC doubler to rectify the electromagnetic output, and a combination of negative voltage converter, synchronous power extraction, DC-DC converter and external inductor for the piezoelectric signal. Tested with an electromagnetic harvester worn on the wrist of a jogger, a commercial low volume PZT-based harvester and a thermoelectric generator, the system provided up to 110 μW output power in the simultaneous multi-mode operation, equivalent to 460% of the power delivered by a stand-alone circuit (Ulusan et al., 2018).
Beside CMOS-based power conditioning circuitry, full integrations involving energy harvesters have also been reported. For instance, RF energy harvesters were integrated with a power management circuit, temperature sensor or image sensor on the same chip (Khan et al., 2018; Park et al., 2018; Saffari et al., 2018). The RF-DC converter using internal threshold voltage cancellation with an auxiliary transistor block was implemented in a CMOS−180 nm technology together with a MPPT (Khan et al., 2018). This RF harvesting system delivered nearly 11 μW output power and 39.3% power conversion efficiency with −15 dBm, 900 MHz input (Khan et al., 2018).
On the other hand, implemented in a CMOS−130 nm technology, a fully integrated RF-powered temperature sensor managed to operate non-intermittently with 1.05 μW power consumption and −16 dBm, 915 MHz input (Saffari et al., 2018). As distinct from other works, this RF harvester-temperature sensor system eliminated the power management circuit for a minimalistic design. To achieve this, a subthreshold ring oscillator was used in order to produce a highly temperature-dependent oscillation frequency, thus acting as a temperature-frequency converter. The frequency-modulated signal was then transferred to an external reader using back scattering (Saffari et al., 2018).
A multifunctional CMOS active pixel which could simultaneously complete the tasks of imaging and energy harvesting has been reported (Park et al., 2018). In contrast to conventional CMOS electron-based imaging pixels, this work adopted a hole-based imaging method, being able to self-power the image capturing function at 15 fps with the energy harvested from >60 klux illumination. The output power density of 998 pW/klux/mm2 was the highest among all counterparts of its kind (Park et al., 2018). A summary of the integrated energy harvesters introduced in this paper is given in Table 1.
Other relevant circuit designs for ultra-low power management used in energy harvesting powered IoT systems, with a special focus on multiple energy sources, have recently been reviewed (Estrada–Lopez et al., 2018).
Recent works on hybrid single-source and multi-source energy harvesters have been reviewed. Although the number of investigations is not large, recent works on harvester-sensor and harvester-storage integrations, including those energy stores operating simultaneously as harvesters, have also been reviewed. As individual energy harvesters become mature, hybridization of different energy harvesting mechanisms is one of the directions of future research. The hybridization is not only limited to the configurations combining different energy conversion mechanisms via complex structures. Multi-source energy harvesting with a single-piece of multi-functional material, either composite or novel monolithic material, should particularly receive attention. Research on such a topic is relatively lacking. However, some organic-halide perovskites (e.g., (CH3NH3)PbI3) (Rakita et al., 2017) and narrow band gap photo-ferroelectric thin-films (e.g., BFCO (Bi2FeCrO6)) (Nechache et al., 2015) and ceramics (e.g., KBNNO ((K,Ba)(Ni,Nb)O3−δ), KNBNNO ((K,Na,Ba)(Ni,Nb)O3−δ)) (Bai et al., 2017a,b), have been proved to have both visible-range photovoltaic effect and recognizable/strong ferroelectricity. Novel multi-source energy harvesters can be developed based on such materials, where photovoltaic, piezoelectric, and pyroelectric effects can be exhibited simultaneously to harvest solar, kinetic and thermal energy with only one material. In addition, in order better to support industrial applications, more self-powered sensing systems or self-charging energy stores need to be developed. The feasibility of these devices will be significantly improved when employing hybrid or multi-source energy harvesters to increase their efficiency.
All authors listed have made a substantial, direct and intellectual contribution to the work, and approved it for publication.
The authors declare that the research was conducted in the absence of any commercial or financial relationships that could be construed as a potential conflict of interest.
JJ acknowledges the funding of the Academy of Finland (project numbers 267573 and 298409).
Ahmad, S., George, C., Beesley, D. J., Baumberg, J. J., and De Volder, M. (2018). Photo–rechargeable organo–halide perovskite batteries. Nano Lett. 18, 1856–1862. doi: 10.1021/acs.nanolett.7b05153
Annapureddy, V., Na, S., Hwang, G., Kang, M. G., Sriramdas, R., Palneedi, H., et al. (2018). Exceeding milli–watt powering magneto–mechano–electric generator for standalone–powered electronics. Energy Environ. Sci. 11, 818–829. doi: 10.1039/C7EE03429F
Bai, Y., Jantunen, H., and Juuti, J. (2018). Energy harvesting research: the road from single source to multisource. Adv. Mater. 30:1707271. doi: 10.1002/adma.201707271
Bai, Y., Siponkoski, T., Perantie, J., Jantunen, H., and Juuti, J. (2017a). Ferroelectric, pyroelectric, and piezoelectric properties of a photovoltaic perovskite oxide. Appl. Phys. Lett. 110:063903. doi: 10.1063/1.4974735
Bai, Y., Tofel, P., Palosaari, J., Jantunen, H., and Juuti, J. (2017b). A game changer: a multifunctional perovskite exhibiting giant ferroelectricity and narrow bandgap with potential application in a truly monolithic multienergy harvester or sensor. Adv. Mater. 29:1700767. doi: 10.1002/adma.201700767
Bowen, C. R., Kim, H. A., Weaver, P. M., and Dunn, S. (2014a). Piezoelectric and ferroelectric materials and structures for energy harvesting applications. Energy Environ. Sci. 7, 25–44. doi: 10.1039/C3EE42454E
Bowen, C. R., Taylor, J., LeBoulbar, E., Zabek, D., Chauhan, A., and Vaish, R. (2014b). Pyroelectric materials and devices for energy harvesting applications. Energy Environ. Sci. 7, 3836–3856. doi: 10.1039/C4EE01759E
Cahill, P., Pakrashi, V., Sun, P., Mathewson, A., and Nagarajaiah, S. (2018). Energy harvesting techniques for health monitoring and indicators for control of a damaged pipe structure. Smart. Struct. Syst. 21, 287–303. doi: 10.12989/sss.2018.21.3.000
Camarda, A., Tartagni, M., and Romani, A. (2018). A−8 mV/+15 mV double polarity piezoelectric transformer–based step–up oscillator for energy harvesting applications. IEEE Trans. Circuits Syst. I Regul. Papers 65, 1454–1467. doi: 10.1109/TCSI.2017.2741779
Cao, R., Wang, J., Xing, Y., Song, W., Li, N., Zhao, S., et al. (2018). A self–powered lantern based on a triboelectric–photovoltaic hybrid nanogenerator. Adv. Mater. Technol. 3:1700371. doi: 10.1002/admt.201700371
Chun, J., Kishore, R. A., Kumar, P., Kang, M., Kang, H. B., Sanghadasa, M., et al. (2018). Self–powered temperature–mapping sensors based on thermo–magneto–electric generator. ACS Appl. Mater. Interfaces 10, 10796–10803. doi: 10.1021/acsami.7b17686
Elhebeary, M. R., Ibrahim, M. A. A., Aboudina, M. M., and Mohieldin, A. N. (2018). Dual–source self–start high–efficiency microscale smart energy harvesting system for IoT. IEEE Trans. Ind. Electron. 65, 342–351. doi: 10.1109/TIE.2017.2714119
Estrada–Lopez, J. J., Abuellil, A., Zeng, Z., and Sanchez–Sinencio, E. (2018). Multiple input energy harvesting systems for autonomous IoT end–nodes. J. Low Power Electron. Appl. 8:6. doi: 10.3390/jlpea8010006
Fan, K., Liu, S., Liu, H., Zhu, Y., Wang, W., and Zhang, D. (2018a). Scavenging energy from ultra–low frequency mechanical excitations through a bi–directional hybrid energy harvester. Appl. Energy 216, 8–20. doi: 10.1016/j.apenergy.2018.02.086
Fan, K., Ren, H., Zhu, Y., Wang, W., and Zhang, D. (2018b). “Two–degree–of–freedom piezoelectric electromagnetic hybrid energy harvester,” Patent No CN107733284(A) (Xi'an).
Fan, K., Zhu, Y., Wang, W., and Zhang, D. (2018c). “Two–dimensional piezoelectric electromagnetic hybrid energy harvester,” Patent No CN107834902(A) (Xi'an).
Feng, L., Liu, G., Guo, H., Tang, Q., Pu, X., Chen, J., et al. (2018). Hybridized nanogenerator based on honeycomb–like three electrodes for efficient ocean wave energy harvesting. Nano Energy 47, 217–223. doi: 10.1016/j.nanoen.2018.02.042
He, Z., Zhong, C., Su, S., Xu, M., Wu, H., and Cao, Y. (2012). Enhanced power–conversion efficiency in polymer solar cells using an inverted device structure. Nat. Photonics 6, 591–595. doi: 10.1038/nphoton.2012.190
Hu, Z., Qiu, J., Wang, X., Gao, Y., Liu, X., Chang, Q., et al. (2018). An integrated multi-source energy harvester based on vibration and magnetic field energy. AIP Adv. 8:056623. doi: 10.1063/1.5006614
Katic, J., Rodriguez, S., and Rusu, A. (2018). A high–efficiency energy harvesting interface for implanted biofuel cell and thermal harvesters. IEEE Trans. Power Electr. 33, 4125–4134. doi: 10.1109/TPEL.2017.2712668
Khan, D., Abbasizadeh, H., Kim, S., Khan, Z. H. N., Shah, S. A. A., Pu, Y. G., et al. (2018). A design of ambient RF energy harvester with sensitivity of−21 dBm and power efficiency of a 39.3% using internal threshold voltage compensation. Energies 11:1258. doi: 10.3390/en11051258
Kim, S., Ju, S., and Ji, C. (2018). Impact–based piezoelectric energy harvester as a power source for a neural activity monitoring circuit. Int. J. Grid Distrib. Comput. 11, 51–62. doi: 10.14257/ijgdc.2018.11.3.05
Lee, W., Schubert, M. J. W., Ooi, B., and Ho, S. J. (2018). Multi-source energy harvesting and storage for floating wireless sensor network nodes with long range communication capability. IEEE Trans. Ind. Appl. 54, 2606–2615. doi: 10.1109/TIA.2018.2799158
Li, P., Gao, S., and Cong, B. (2018a). Theoretical modeling, simulation and experimental study of hybrid piezoelectric and electromagnetic energy harvester. AIP Adv. 8, 035017. doi: 10.1063/1.5018836
Li, Y., Tang, Z., Zhu, Z., and Yang, Y. (2018b). A novel MPPT circuit with 99.1% tracking accuracy for energy harvesting. Analog Integr. Cir. Signal Proc. 94, 105–115. doi: 10.1007/s10470–017–1079–z
Liu, J., Li, Q., Liu, X., Li, Z., Liu, Y., Lin, Z., et al. (2018a). Picowatt 0.5 V supply with 3 ppm/degrees C CMOS voltage reference for energy harvesting system. IEICE Electr. Exp. 15:20180372. doi: 10.1587/elex.15.20180372
Liu, L., Pang, Y., Liao, X., Zhu, Z., and Yang, Y. (2018b). A power–enhanced active rectifier with offset–controlled comparator for self–powered PEH systems. J. Circuits Syst. Comput. 27:1850079. doi: 10.1142/S0218126618500792
Liu, L., Pang, Y., Yuan, W., Zhu, Z., and Yang, Y. (2018c). A self–powered piezoelectric energy harvesting interface circuit with efficiency–enhanced P–SSHI rectifier. J. Semiconduct. 394:045002. doi: 10.1088/1674–4926/39/4/045002
Liu, Y., Sun, N., Liu, J., Wen, Z., Sun, X., Lee, S., et al. (2018d). Integrating a silicon solar cell with a triboelectric nanogenerator via a mutual electrode for harvesting energy from sunlight and raindrops. ACS Nano 12, 2893–2899. doi: 10.1021/acsnano.8b00416
Lu, R. P., Ramirez, A. D., and Pascoguin, B. M. L. (2018). Multi-source energy harvesting device. Patent No US20180069405A1: United States of America as represented by Secretary of the Navy (San Diego, CA).
Luo, Z., Zeng, L., Lau, B., Lian, Y., and Heng, C. (2018). A Sub−10 mV power converter with fully integrated self–start, MPPT, and ZCS control for thermoelectric energy harvesting. IEEE Trans. Circuits Syst. I Regul. Papers 65, 1744–1757. doi: 10.1109/TCSI.2017.2757505
Ma, J., Zhang, Q., Lin, K., Zhou, L., and Ni, Z. (2018). Piezoelectric and optoelectronic properties of electrospinning hybrid PVDF and ZnO nanofibers. Mater. Res. Exp. 5:035057. doi: 10.1088/2053–1591/aab747
Maharjan, P., Toyabur, R. M., and Park, J. Y. (2018). A human locomotion inspired hybrid nanogenerator for wrist–wearable electronic device and sensor applications. Nano Energy 46, 383–395. doi: 10.1016/j.nanoen.2018.02.033
McCullagh, J. (2018). An active diode full–wave charge pump for low acceleration infrastructure–based non–periodic vibration energy harvesting. IEEE Trans. Circuits Syst. I Regul. Papers 65, 1758–1770. doi: 10.1109/TCSI.2017.2764878
Nechache, R., Harnagea, C., Li, S., Cardenas, L., Huang, W., Chakrabartty, J., et al. (2015). Bandgap tuning of multiferroic oxide solar cells. Nat. Photonics 9, 61–67. doi: 10.1038/nphoton.2014.255
Park, S., Lee, K., Song, H., and Yoon, E. (2018). Simultaneous imaging and energy harvesting in CMOS image sensor pixels. IEEE Electron Device Lett. 39, 532–535. doi: 10.1109/LED.2018.2811342
Rakita, Y., Bar–Elli, O., Meirzadeh, E., Kaslasi, H., Peleg, Y., Hodes, G., et al. (2017). Tetragonal CH3NH3PbI3 is ferroelectric. Proc. Natl. Acad. Sci. U. S. A. 114, E5504–E5512. doi: 10.1073/pnas.1702429114
Raouadi, M. H., and Touayar, O. (2018). Harvesting wind energy with pyroelectric nanogenerator PNG using the vortex generator mechanism. Sens. Actuator A Phys. 273, 42–48. doi: 10.1016/j.sna.2018.02.009
Saffari, P., Basaligheh, A., Sieben, V. J., and Moez, K. (2018). An RF–powered wireless temperature sensor for harsh environment monitoring with non–intermittent operation. IEEE Trans. Circuits Syst. I Regul. Papers 655, 1529–1542. doi: 10.1109/TCSI.2017.2758327
Saraf, R., Pu, L., and Maheshwari, V. (2018). A light harvesting, self–powered monolith tactile sensor based on electric field induced effects in MAPbI perovskite. Adv. Mater. 30:1705778. doi: 10.1002/adma.201705778
Schiffer, Z. J., and Arnold, C. B. (2018). Characterization and model of piezoelectrochemical energy harvesting using lithium ion batteries. Exp. Mech. 58, 605–611. doi: 10.1007/s11340–017–0291–1
Shen, Q., Xie, X., Peng, M., Sun, N., Shao, H., Zheng, H., et al. (2018). Self–powered vehicle emission testing system based on coupling of triboelectric and chemoresistive effects. Adv. Funct. Mater. 28:1703420. doi: 10.1002/adfm.201703420
Shi, G., Xia, Y., Wang, X., Qian, L., Ye, Y., and Li, Q. (2018). An efficient self–powered piezoelectric energy harvesting CMOS interface circuit based on synchronous charge extraction technique. IEEE Trans. Circuits Syst. I Regul. Papers 65, 804–817. doi: 10.1109/TCSI.2017.2731795
Taghadosi, M., Albasha, L., Quadir, N. A., Rahama, Y. A., and Qaddoumi, N. (2018). High efficiency energy harvesters in 65nm CMOS process for autonomous IoT sensor applications. IEEE Access 6, 2397–2409. doi: 10.1109/ACCESS.2017.2783045
Uchino, K. (2018). Piezoelectric energy harvesting systems–essentials to successful developments. Energy Technol. 6, 829–848. doi: 10.1002/ente.201700785
Ulusan, H., Chamanian, S., Pathirana, W. P. M. R., Zorlu, O., Muhtaroglu, A., and Kulah, H. (2018). A triple hybrid micropower generator with simultaneous multi–mode energy harvesting. Smart Mater. Struct. 27:014002. doi: 10.1088/1361–665X/aa8a09
Wang, S., Ke, Y., Huang, P., and Hsieh, P. (2018). Electromagnetic energy harvester interface design for wearable applications. IEEE Trans. Circuits Syst. Ii Exp. Briefs 65, 667–671. doi: 10.1109/TCSII.2018.2820158
Yang, H., Liu, W., Xi, Y., Lai, M., Guo, H., Liu, G., et al. (2018a). Rolling friction contact–separation mode hybrid triboelectric nanogenerator for mechanical energy harvesting and self–powered multifunctional sensors. Nano Energy 47, 539–546. doi: 10.1016/j.nanoen.2018.03.028
Yang, P., Qu, X., Liu, K., Duan, J., Li, J., Chen, Q., et al. (2018b). Electrokinetic supercapacitor for simultaneous harvesting and storage of mechanical energy. ACS Appl. Mater. Interfaces 10, 8010–8015. doi: 10.1021/acsami.7b18640
Yang, Z., Zhou, S., Zu, J., and Inman, D. (2018c). High–performance piezoelectric energy harvesters and their applications. Joule 2, 642–697. doi: 10.1016/j.joule.2018.03.011
Yi, H., Yin, J., Mak, P., and Martins, R. P. (2018a). A 0.032–mm 0.15–V three–stage charge–pump scheme using a differential bootstrapped ring–VCO for energy–harvesting applications. IEEE Trans. Circuits Syst. Ii Exp. Briefs 65, 146–150. doi: 10.1109/TCSII.2017.2676159
Yi, H., Yu, W., Mak, P., Yin, J., and Martins, R. P. (2018b). A 0.18–V 382–mu W bluetooth low–energy receiver front–end with 1.33–nW sleep power for energy–harvesting applications in 28–nm CMOS. IEEE J Solid State Circuits 53, 1618–1627. doi: 10.1109/JSSC.2018.2815987
Keywords: energy harvesting, hybrid, multi-source, integration, energy storage, piezoelectric, triboelectric, photovoltaic
Citation: Bai Y, Jantunen H and Juuti J (2018) Hybrid, Multi-Source, and Integrated Energy Harvesters. Front. Mater. 5:65. doi: 10.3389/fmats.2018.00065
Received: 10 July 2018; Accepted: 23 October 2018;
Published: 13 November 2018.
Edited by:
Michael P. M. Jank, Fraunhofer Institut für Integrierte Systeme und Bauelementetechnologie IISB, GermanyReviewed by:
Romana Schirhagl, University Medical Center Groningen, NetherlandsCopyright © 2018 Bai, Jantunen and Juuti. This is an open-access article distributed under the terms of the Creative Commons Attribution License (CC BY). The use, distribution or reproduction in other forums is permitted, provided the original author(s) and the copyright owner(s) are credited and that the original publication in this journal is cited, in accordance with accepted academic practice. No use, distribution or reproduction is permitted which does not comply with these terms.
*Correspondence: Yang Bai, eWFuZy5iYWlAb3VsdS5maQ==
Disclaimer: All claims expressed in this article are solely those of the authors and do not necessarily represent those of their affiliated organizations, or those of the publisher, the editors and the reviewers. Any product that may be evaluated in this article or claim that may be made by its manufacturer is not guaranteed or endorsed by the publisher.
Research integrity at Frontiers
Learn more about the work of our research integrity team to safeguard the quality of each article we publish.