- Division of Surface Electrochemistry, Koszalin University of Technology, Koszalin, Poland
The research work has been concerned on the studies and development of electrochemical polishing in the magnetic field magnetoelectropolishing (MEP) in comparison with the standard electropolishing (EP) methods performed without stirring (EP) and the process with the forced electrolyte mixing (MIX). Advanced techniques were used in the studies, to measure the effects of the surface treatment. They are as follows: scanning electron microscopy (SEM/EDS), X-ray Photoelectron Spectroscopy, Secondary Ion Mass Spectroscopy, surface roughness, and nanoindentation measurements. For the corrosion studies, the electrochemical methods were used, such as: open circuit potential OCP, potentiodynamic curves PC, and electrochemical impedance spectroscopy EIS measurements. The MEP process is advised mainly due to the opportunity to enrich the surface layer with the chromium compounds (austenitic stainless steels), or titanium compounds (CP Ti Grade 2, Nitinol). The surface layers of biomaterials after MEP process contain much lower amount of carcinogenic compounds, like chromium VI oxidation stage (Cr6+) (austenitic stainless steels) and nickel compounds (austenitic stainless steel and Nitinol) versus those ones obtained after EP and MIX treatments. It is interesting that apart from the significant modification of the surface layer obtained after MEP, also mechanical properties, such as nanohardness, modulus of elasticity, and mechanical resistance to bending and torsion, undergo considerable advantageous changes. All they make the MEP process very promising for application in many clean industries, such as medical equipment and devices, electronics, food industry, etc.
Introduction
Electrochemical polishing of materials, metals, and alloys (Hryniewicz et al., 2006, 2007, 2008a,b,c, 2009a,b,c, 2011a,b,c, 2012a,b, 2008b; Hryniewicz, 2007; Hryniewicz and Rokicki, 2007, 2008; Rokicki and Hryniewicz, 2008, 2012; Rokicki et al., 2008, 2012; Hryniewicz and Rokosz, 2009, 2010a,b, 2013a,b; Rokicki, 2009; Rokosz and Hryniewicz, 2010a,b, 2011, 2013a,b,c; Rokosz, 2011, 2012; Rokosz and Raaen, 2011; Rokosz et al., 2012a,b,c), is one of the most often used finishing operation, specifically in case of surface treatments of metallic biomaterials with complicated shapes (coronary stents, prostheses, etc.). In the metallic materials, apart from the desired minimum surface roughness and frequently a proper shine, a high corrosion resistance and the lack of carcinogenic elements in the surface layer, are also of high importance. The studies with the magnetic field involved in the process of EP started some time ago (Hryniewicz et al., 2006, 2007, 2008a,b,c, 2009a,b,c; Hryniewicz, 2007; Hryniewicz and Rokicki, 2007; Rokicki and Hryniewicz, 2008; Rokicki et al., 2008; Hryniewicz and Rokosz, 2009), with the effects being revealed and published consecutively (Hryniewicz and Rokosz, 2010a,b, 2013a,b, 2014; Rokosz and Hryniewicz, 2010a,b, 2011, 2013a,b,c; Hryniewicz et al., 2011a,b,c, 2012a,b; Rokosz, 2011, 2012; Rokosz and Raaen, 2011; Rokicki and Hryniewicz, 2012; Rokicki et al., 2012; Rokosz et al., 2012a,c). There were a number of earlier experiments done, with the magnetic field announced to use mainly to enhance coating/electrocoating processes. Important mechanical effects of the magnetic field usage have been studied for decades, to mention just a few (Bocksted and Klamecki, 2007; El Mansori and Klamecki, 2007; Zaidi et al., 2007).
The first effective use of the magnetic field to EP was announced by Rokicki, with the process named and patented as magnetoelectropolishing (MEP) (Rokicki, 2009). The study development of the MEP was consequently realized by Hryniewicz et al. (Hryniewicz et al., 2006, 2007, 2008a,b,c, 2009a,b,c, 2011a,b,c, 2012a,b, 2014; Hryniewicz, 2007; Hryniewicz and Rokicki, 2007, 2008; Rokicki and Hryniewicz, 2008, 2012; Rokicki et al., 2008, 2012; Hryniewicz and Rokosz, 2009, 2010a,b, 2013a,b, 2014; Rokosz and Hryniewicz, 2010a,b, 2011, 2013a,b,c; Rokosz, 2011, 2012; Rokosz and Raaen, 2011; Rokosz et al., 2012a,b,c, 2014). Thus the consecutive detailed studies of the effect of the magnetic field on the chemical composition, corrosion resistance of the surface layer formed under MEP, and mechanical properties, were investigated. Specifically, the research of some selected types of steels, covering measurements and analyses, was performed and presented by Rokosz (2011, 2012), and Hryniewicz et al. (Hryniewicz et al., 2006, 2007, 2008a,b,c, 2009a,b,c, 2011a,b,c, 2012a, 2014; Hryniewicz, 2007; Hryniewicz and Rokicki, 2007; Rokicki and Hryniewicz, 2008, 2012; Rokicki et al., 2008, 2012; Hryniewicz and Rokosz, 2009, 2010a,b, 2013a,b, 2014; Rokosz and Hryniewicz, 2010a,b, 2011, 2013a,b,c; Rokosz and Raaen, 2011; Rokosz et al., 2012a,b,c, 2014).
Just recently, a new paper was published, concerned with the use of a magnetic field (Cheng et al., 2013) for the surface technology. Unexpectedly, the authors (Cheng et al., 2013) called the process a “magnetization technology” not mentioning about any previous works carried out in this area. However, no details have been provided in their paper (Cheng et al., 2013), apart from the use of an electromagnet of “0.35 T magnetic field intensity.” A reader is not informed, why 0.35 T, and not, e.g., 0.22 or 0.55 T, was applied in their experiment. Several our works concerned with MEP indicates 350 mT as a turning point in using the magnetic field to the process of EP and revealing the reason for assuming that magnitude (Rokosz and Hryniewicz, 2010a,b, 2013b,c; Hryniewicz et al., 2011b; Rokosz, 2012; Rokosz et al., 2012a; Hryniewicz and Rokosz, 2013b). No one of our earlier published paper in this field was cited in (Cheng et al., 2013). While the title of the paper suggests a “novel surface treatment for 316L stainless steel,” the treatment procedure of this novel technology relies on using SiC abrasive polishing with the grit size of 2000 to get ready the sample surface for the studies of semiconducting properties of the surface film obtained, corrosion resistance, etc. It is not clear if a passivation in “3.5 wt% NaCl solution” reported in their paper (Cheng et al., 2013) was performed chemically or electrochemically. Thus, if the authors (Cheng et al., 2013) in their paper inform the audience of the “magnetization technology” and then present the results on corrosion resistance, so such a statement seems to be misleading. Surface finishing technology relies on the surface treatment before the studies of the effects are investigated.
Most of our works on MEP of metals and alloys were published during recent years. For the EP experiments with the magnetic field, the electrolytes consisting with a mixture of acids H3PO4 and H2SO4 with some other additives, were used. This work is to sum up the up-to-date achievements in this field of technology. Highlights and advantages of the MEP process have been accented. A mathematical model, concerning the MEP process of stainless steels and showing fluctuations of surface effects of the magnetic field intensity B, is provided.
Design and Building the MEP Working-Measuring Set-Up
The set-up used for a standard electrochemical polishing (EP) (Figure 1), has been designed based on the Authors’ own concept (Rokosz and Hryniewicz, 2010a; Rokosz, 2012; Hryniewicz et al., 2014), and is composed with basic components (without a magnetic field). It consists of an electrochemical cell C, potentiostat A, heating system B, computer D, digital multimeter E, and serves for the EP operation and for determination of anodic polarization curves. For some EP experiments, additional mixing was introduced to the system (MIX) to compare the results obtained.
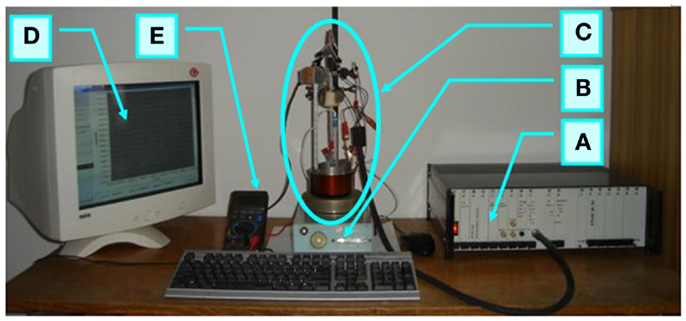
Figure 1. Set-up used for standard electrochemical polishing EP: A, potentiostat; B, heating system; C, electrochemical cell; D, computer with software; E, digital multimeter.
In Figure 2 the set-up of Figure 1 was additionally equipped with a neodymium magnet. Two forms of magnets have been used for the MEP experiments: the flat cylindrical one, as shown in Figure 2 F, and ring magnets, presented elsewhere (Hryniewicz et al., 2009a,b; Hryniewicz and Rokosz, 2010b).
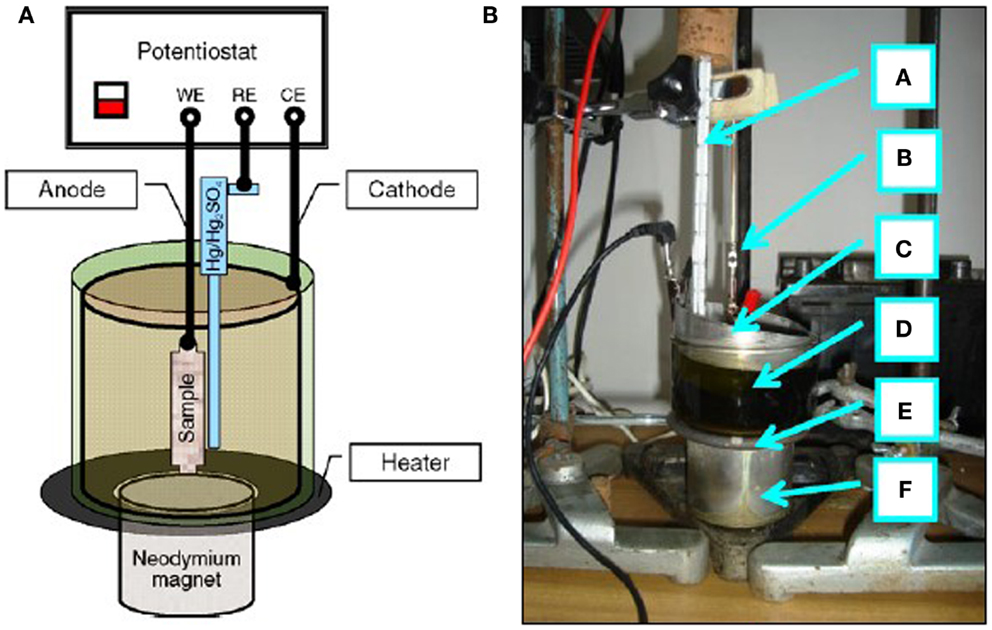
Figure 2. Set-up used for electrochemical polishing in the magnetic field MEP: (A) scheme of connections, (B) photo (a, thermometer; b, anode; c, cathode; d, electrochemical cell; e, heater; f, neodymium magnet).
In the version for moderate current densities (up to 50–100 A/dm2) the set-up consisted with: a potentiostat ATLAS 98, cylindrical austenitic stainless steel cathode of the area of more than 100 times greater than that of the tested sample-anode, which was placed inside the cathode (the anode–cathode distance was about 45 mm), Hg/Hg2SO4 MSE reference electrode, heater, thermometer, and a neodymium magnet, whereas for the circuit of high-density currents of up to 1000 A/dm2, a stabilized power supply RNG-3010 was used with a rectifier unit Telzas PDN 24-48-(60)/30(25) (Rokicki and Hryniewicz, 2008; Hryniewicz and Rokosz, 2009).
Polarization Characteristics for the MEP versus EP and MIX Treatments
The anodic polarization curves of austenitic AISI 316L stainless steel and ferritic AISI 430 steel for the MEP as well as EP and MIX operations were given in (Hryniewicz and Rokosz, 2010a; Rokosz, 2012). For the austenitic stainless steel as a paramagnetic material, the magnetic field influences mainly the ferromagnetic iron compounds. Following that way, the intensive dissolution of the ferromagnetic compounds of the 316L SS surface layer to electrolyte is observed (Rokosz, 2012). In the case of ferritic stainless steel (ferromagnetic material) an immediate magnetization of the structure results in slowing the dissolution of the ferrous compounds to the electrolyte solution. In conclusion, the MEP process is not advised for ferromagnetic materials. The main advantages of using the magnetic field in EP are visible in Figure 3. The plateau current density of anodic polarization curves obtained in the MEP process is much above of that one obtained for the EP process.
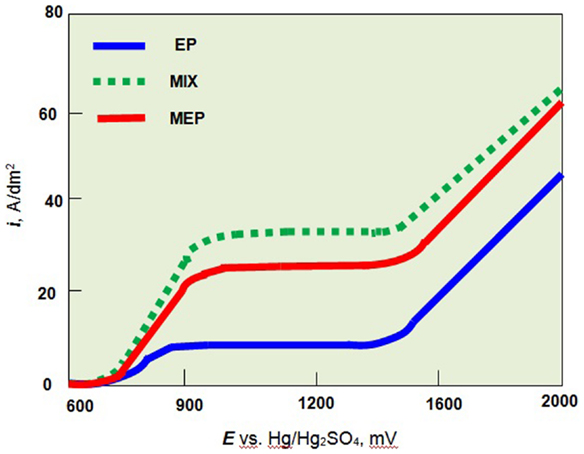
Figure 3. Anodic polarization curves of austenitic stainless steel (AISI 316L SS) in H2SO4:H3PO4 = 2:3 solution at temperature 60°C without stirring (EP), with stirring (MIX), and in the magnetic field (MEP).
Chemical Composition of Surface Layers
The studies of chemical composition of surface layers created after electrochemical polishing EP, MIX, and MEP for non-alloyed/carbon steel as well as ferritic and austenitic stainless steels, as performed by X-ray Photoelectron Spectroscopy (XPS) and electrochemical measurements, were carried out and presented in numerous Authors’ works (Hryniewicz et al., 2008b, 2009c, 2011a,c, 2012b; Hryniewicz and Rokosz, 2010b, 2013b, 2014; Rokosz and Hryniewicz, 2010b, 2013a,b,c; Rokosz, 2011; Rokosz and Raaen, 2011; Rokosz et al., 2012a,b, 2014). The results of the studies have shown that the treatment time for unalloyed steel was much higher than that applied to ferritic or austenitic stainless steels for each of the treatments: EP, MIX, and MEP. It was found that type of the electrochemical treatment (EP, MIX, and MEP) considerably influences the chemical composition of the surface layer formed on the anode. In the case of ferromagnetic steels, like unalloyed and chromium ferritic steels, the highest enrichment of the surface layer/film with chromium compounds was obtained after electrochemical polishing without stirring (EP) (Rokosz, 2012). For the paramagnetic steel, which is the austenitic stainless steel, the highest enrichment of chromium and molybdenum in the surface layer was obtained after electrochemical polishing in a magnetic field MEP 200 (Figure 4). The notations in Figure 4, EP50, MIX50, MEP50, and MEP200 refer to the anodic current density 50, and 200 A/dm2, respectively. The coefficient (Cr + 3.3Mo)/Fe is the most characteristic index proving of the effect of the magnetic field on the enrichment of surface film formed after MEP in chromium and molybdenum compounds. One may easily notice the most advantageous effect of MEP200 (Figure 4).
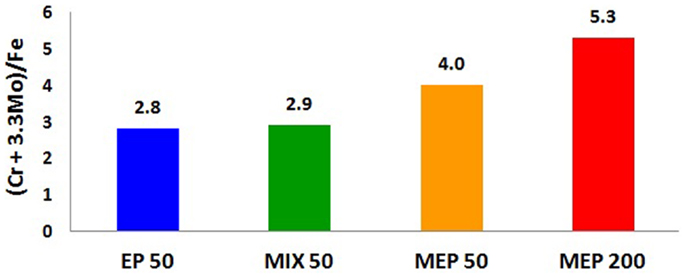
Figure 4. XPS study results: changes in surface film composition of austenitic AISI 316L stainless steel after different electropolishing treatments: EP50, the process without stirring; MIX50, the process with a moderate electrolyte mixing; MEP50, magnetoelectropolishing at 50 A/dm2; MEP200, magnetoelectropolishing at 200 A/dm2.
A considerable change in the surface layer composition was also observed in other metals and non-ferrous alloys (Hryniewicz et al., 2006, 2007, 2008c, 2009a,c, 2011a; Hryniewicz, 2007; Hryniewicz and Rokicki, 2007, 2008; Hryniewicz and Rokosz, 2009, 2013a). The collective results of the surface layer composition study performed on Nitinol endodontic files are given in Figure 5. While after a standard EP the total titanium contents against total nickel contents increased about 3.5 times so after a MEP this ratio increased to about 6.5.
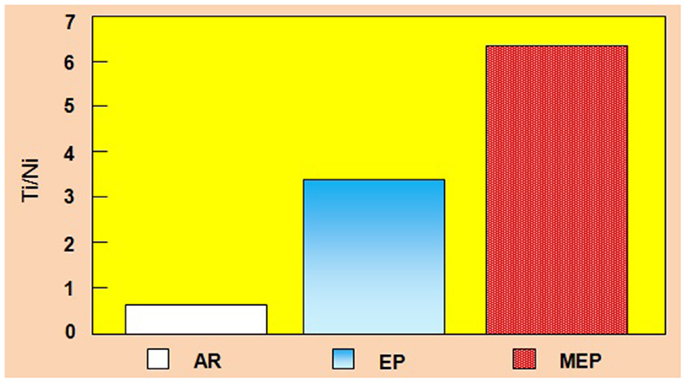
Figure 5. Total Ti/Ni ratio contents comparison of NiTi endodontic files on surface: AR, as received (bulk/matrix data), EP, after a standard electropolishing, and MEP, after magnetoelectropolishing.
Pitting Corrosion Effect
Many corrosion studies were performed concerning the effect of MEP (Hryniewicz, 2007; Hryniewicz and Rokicki, 2007; Hryniewicz et al., 2007, 2008a,c, 2009a,b,c, 2011a; Hryniewicz and Rokosz, 2009, 2014; Rokosz and Hryniewicz, 2010a, 2011, 2013c; Rokosz, 2012; Rokosz et al., 2012a). In this work the mathematical model, which describes the change of pitting corrosion potential (Rokosz, 2012) versus induction of the magnetic field B and the anodic current density i, was developed. An example of the Authors’ mathematical model presenting Epit = f(B, i) with the designated confidence intervals at the significance level α = 0.05, satisfying the adequacy of the mathematical model to the real object (test F – lack of fit), is shown below:
and
It should be noted that during the MEP of a paramagnetic material, the self-arisen automatic mixing of electrolyte around the workpiece is observed. With increasing of the magnetic field induction, a compensation of the effects of mixing solution (Lorentz force) by the “pure” magnetic field is realized. With further growth of the magnetic field intensity, the increasing amount of dia- and paramagnetic compounds is observed in the surface layer. In the case of austenitic steels, the amount of chromium compounds is rising in relation to the amount of iron compounds. This effect is detected in the form of increasing the corrosion resistance of the surface layer (Hryniewicz et al., 2008a; Rokosz and Hryniewicz, 2010a; Rokosz, 2012).
Mechanical Changes after MEP
Bending Tests
Mechanical bending tests were performed on Nitinol samples to reveal the effect of MEP on the results. For this purpose, a 2-mm NiTi wire was cut into pieces of about 40 mm long and a 180° bending was done in accordance to the standard (Polish Standard, 1975; Hryniewicz and Rokicki, 2008). Results of the studies, performed on nine samples (three times three samples each time), are given in Figure 6. For comparison, the test results performed on as-received samples is displayed. One can easily notice a distinct difference in the results obtained on Nitinol samples after MEP in comparison with those ones obtained after EP.
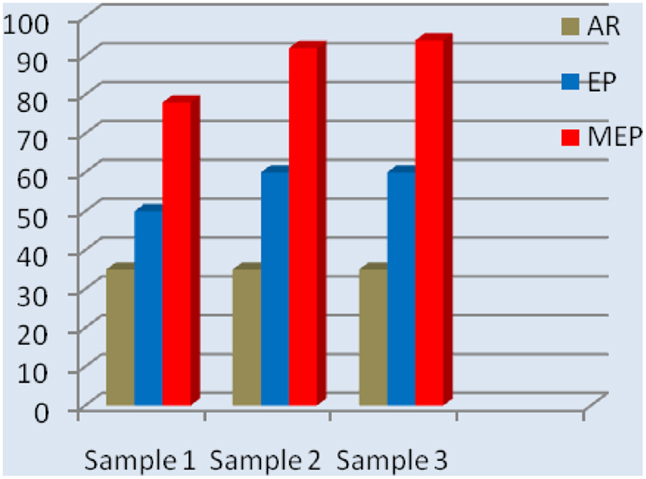
Figure 6. Relative results of bending tests performed on Nitinol wire samples after EP and MEP; AR as received.
Changes in Nanohardness and Reduced Young’s Modulus after MEP
A significant effect of the magnetic field inductance on nanohardness and reduced Young’s modulus of the surface layer formed after the MEP versus EP, was demonstrated (Hryniewicz et al., 2009c, 2013; Rokosz et al., 2012c). A nanoindentation technique was used for that purpose to two biomaterials: CP titanium Grade 2 (Hryniewicz et al., 2009a, 2011a) and stainless steel AISI 316L (Hryniewicz et al., 2008a,b, 2009b, 2011c; Hryniewicz and Rokosz, 2010b, 2013b; Rokosz and Hryniewicz, 2010a, 2013c; Rokosz, 2012; Rokosz et al., 2012a) to reveal this effect, with some of the results presented in Figure 7. The notations presented on horizontal axis in Figure 7 refer to the sample surfaces treated mechanically (MP) using abrasive polishing with SiC paper up to the grit size 1000, a standard EP, and treated by MEP.
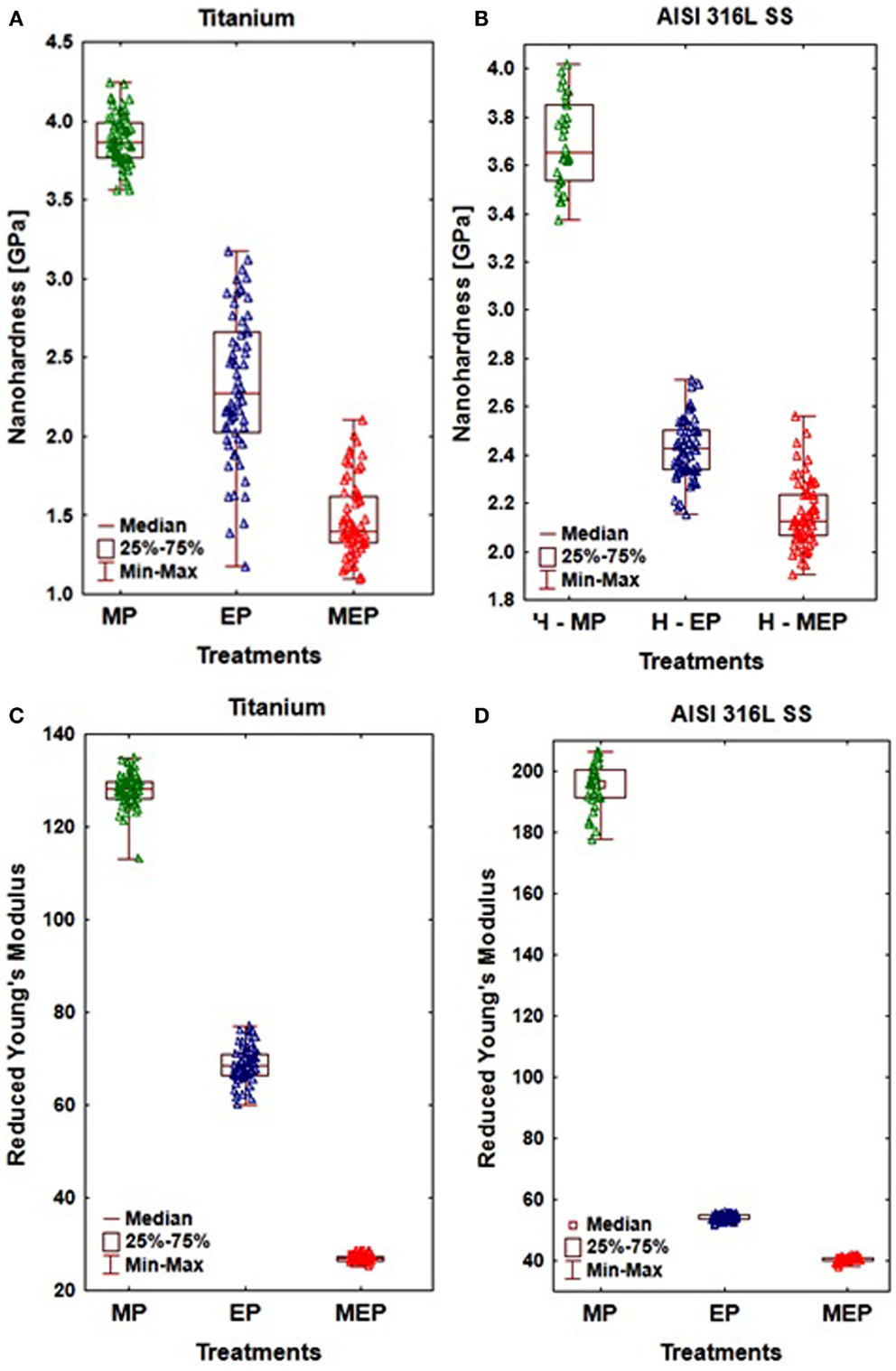
Figure 7. The results of nanoindentation obtained on CP Ti Grade 2 (A,C), and AISI 316L SS (B,D) showing: (A,B) nanohardness, (C,D) reduced Young’s modulus.
The nanoindentation study results given in Figure 7, referred to the sample surfaces of CP titanium Grade 2 after MP, EP, and MEP treatments, were presented in (Hryniewicz et al., 2013). The following results (at α = 0.05) were obtained on Ti after: MP (nHV = 3.88 ± 0.16 GPa, Er = 127.97 ± 3.58 GPa); EP (nHV = 2.31 ± 0.46 GPa, Er = 68.56 ± 3.87 GPa); and MEP (nHV = 1.47 ± 0.24 GPa, Er = 26.94 ± 0.67 GPa). They indicate considerable and advantageous changes of the materials studied.
Conclusion
In this work, the Authors highlighted the main features of MEP process. The extensive studies carried out on EP of ferromagnetic materials (metals and alloys) show that the best electrochemical surface treatment is a standard electrochemical polishing EP. For paramagnetic materials, like austenitic steels, titanium, Nitinol, the MEP process is advised mainly due to the opportunity to enrich the surface layer with the chromium (austenitic steel) or titanium (Nitinol) compounds. Another conclusion of the studies is, that the surface layers of biomaterials after MEP process contain much lower amounts of carcinogenic compounds like chromium VI oxidation stage (Cr6+) (austenitic stainless steel) and nickel compounds (austenitic stainless steel and Nitinol) versus those ones remained after EP and MIX treatments. It was noted that after MEP of 316L SS in the surface layer there were detected 3–5% chromium compounds (Cr6+) and 0.07–0.08% nickel compounds, while after the EP and MIX, 6–11% Cr6+ and 0.19–0.28% nickel compounds, respectively (Hryniewicz and Rokosz, 2010a). One more fact is also important, that the MEP set-up upgrading will not increase significantly the cost of the enterprise. The level of safety for the MEP process is comparable with that one referred to EP.
It may be noted that the electrochemical polishing in the magnetic field (MEP) should be advised mainly for non-ferromagnetic parts, like tantalum, titanium and its alloys, and austenitic or duplex stainless steel alloys. Ferromagnetic steels in a strong magnetic field rapidly magnetize up, so their interaction with the source of the magnetic field is extremely large and rather unsafe. That situation is usually improbable in the case of MEP of austenitic stainless steels, titanium, and/or Nitinol, which are paramagnetic materials.
Conflict of Interest Statement
The authors declare that the research was conducted in the absence of any commercial or financial relationships that could be construed as a potential conflict of interest.
References
Bocksted, J., and Klamecki, B. E. (2007). Effects of pulsed magnetic field on thrust bearing washer hardness. Wear 262, 1086–1096. doi:10.1016/j.wear.2006.11.007
Cheng, X. Q., Dong, C. F., Li, X. G., and Li, W. D. (2013). Technical note: novel surface treatment for 316L stainless steel using magnetisation technology. Mater. Res. Innov. 17, 557–560. doi:10.1179/1433075X13Y.0000000101
El Mansori, M., and Klamecki, B. E. (2007). Magnetic field effects in machining processes and on manufactured part mechanical characteristics. J. Manuf. Sci. Eng. 128, 136–145. doi:10.1115/1.2113007
Hryniewicz, T. (2007). Introduction to Surface Finishing of Metallic Biomaterials (in Polish). Koszalin: Editorial Office of Politechnika Koszalinska, 155 p.
Hryniewicz, T., and Rokicki, R. (2007). “On the surface modification of stainless steels,” in Proceedings of the 15th International Conference on Composites/Nano-Engineering, ICCE-15, ed. D. Hui (Haikou: ICCE), 345–346.
Hryniewicz, T., and Rokicki, R. (2008). “Improved surface properties of nitinol after magnetoelectropolishing,” in Proceedings of 16th Annual International Conference on Composites/Nano-Engineering, ICCE-16, ed. D. Hui (Kunming: ICCE), 87–88.
Hryniewicz, T., Rokicki, R., and Rokosz, K. (2006). Magnetoelectropolishing process improves characteristics of finished metal surfaces. Met. Finish. 104, 26–33. doi:10.1016/S0026-0576(06)80361-2
Hryniewicz, T., Rokicki, R., and Rokosz, K. (2007). Magnetoelectropolishing for metal surface modification. Trans. Inst. Met. Finish. 85, 325–332. doi:10.1179/174591907X246537
Hryniewicz, T., Rokicki, R., and Rokosz, K. (2008a). Corrosion characteristics of medical grade AISI 316L stainless steel surface after electropolishing in a magnetic field. Corrosion 64, 660–665.
Hryniewicz, T., Rokosz, K., and Rokicki, R. (2008b). Electrochemical and XPS studies of AISI 316L stainless steel after electropolishing in a magnetic field. Corros. Sci. 50, 2676–2681. doi:10.1016/j.corsci.2008.06.048
Hryniewicz, T., Rokicki, R., and Rokosz, K. (2008c). Co-Cr alloy corrosion behaviour after electropolishing and “magnetoelectropolishing” treatments. Mater. Lett. 62, 3073–3076. doi:10.1016/j.matlet.2008.01.130
Hryniewicz, T., Rokicki, R., and Rokosz, K. (2009a). Corrosion and surface characterization of titanium biomaterial after magnetoelectropolishing. Surf. Coat. Technol. 23, 1508–1515. doi:10.1016/j.surfcoat.2008.11.028
Hryniewicz, T., Rokosz, K., and Filippi, M. (2009b). Biomaterial studies on AISI 316L stainless steel after magnetoelectropolishing. Materials 2, 129–145. doi:10.3390/ma2010129
Hryniewicz, T., Rokosz, K., and Rokicki, R. (2009c). “Surface investigation of NiTi rotary endodontic instruments after magnetoelectropolishing,” in MRS Proceedings, Biomaterials (XVIII International Materials Research Congress, 9. Biomaterials) (Cancun: IMRC), 17–28.
Hryniewicz, T., Rokicki, R., and Rokosz, K. (2011a). “Magnetoelectropolished titanium biomaterial”, Chapter 11, in Biomaterials Science and Engineering, ed. R. Pignatello (Rijeka, Croatia: InTech), 227–248.
Hryniewicz, T., Konarski, P., Rokosz, K., and Rokicki, R. (2011b). SIMS analysis of hydrogen content in near surface layers of AISI 316L SS after electrolytic polishing under different conditions. Surf. Coat. Technol. 205, 4228–4236. doi:10.1016/j.surfcoat.2011.03.024
Hryniewicz, T., Rokosz, K., and Micheli, V. (2011c). Auger/AES surface film measurements on AISI 316L biomaterial after magnetoelectropolishing. PAK 57, 609–614.
Hryniewicz, T., and Rokosz, K. (2009). On the wear inspection and endurance recovery of nitinol endodontic files. PAK 55, 247–250.
Hryniewicz, T., and Rokosz, K. (2010a). Polarization characteristics of magnetoelectropolishing stainless steels. Mater. Chem. Phys. 122, 169–174. doi:10.1016/j.matchemphys.2010.02.055
Hryniewicz, T., and Rokosz, K. (2010b). Analysis of XPS results of AISI 316L SS electropolished and magnetoelectropolished at varying conditions. Surf. Coat. Technol. 296, 2583–2592. doi:10.1016/j.surfcoat.2010.02.005
Hryniewicz, T., and Rokosz, K. (2013a). Corrigendum to “SEM/EDX and XPS studies of niobium after electropolishing” by T. Hryniewicz, K. Rokosz, H.R. Zschommler Sandim [Appl. Surf. Sci., yyy (2012) xxx]. Appl. Surf. Sci. 265, 931–934. doi:10.1016/j.apsusc.2012.11.104
Hryniewicz, T., and Rokosz, K. (2013b). Significant improvement of AISI 316L SS biomaterial surface after magnetoelectropolishing MEP: XPS measurements. PAK 59, 1308–1312.
Hryniewicz, T., and Rokosz, K. (2014). Corrosion resistance of magnetoelectropolished AISI 316L SS biomaterial. Anti-Corros. Methods Mater. 61, 57–64. doi:10.1108/ACMM-03-2013-1249
Hryniewicz, T., Rokosz, K., and Rokicki, R. (2014). Magnetic fields for electropolishing improvement: materials and systems. Int. Lett. Chem. Phys. Astron. 4, 98–108.
Hryniewicz, T., Rokosz, K., Valicek, J., and Rokicki, R. (2012a). Effect of magnetoelectropolishing on nanohardness and Young’s modulus of titanium biomaterial. Mater. Lett. 83, 69–72. doi:10.1016/j.matlet.2012.06.010
Hryniewicz, T., Rokosz, K., and Zschommler-Sandim, H. R. (2012b). SEM/EDX and XPS studies of niobium after electropolishing. Appl. Surf. Sci. 263, 357–361. doi:10.1016/j.apsusc.2012.09.060
Hryniewicz, T., Rokosz, K., Valicek, J., Rokicki, R., Harnicarova, M., and Vyležik, M. (2013). Measurements of nanohardness and elasticity modulus of titanium after magnetoelectropolishing. PAK 59, 676–679.
Polish Standard. (1975). PN-75/M-80002: Technological testing of wires and rods. Bending test (in Polish), Warsaw.
Rokicki, R. (2009). Apparatus and Method for Enhancing Electropolishing Utilizing Magnetic Fields. US Patent. Washington, DC.
Rokicki, R., Haider, W., and Hryniewicz, T. (2012). Influence of sodium hypochlorite treatment of electropolished and magnetoelectropolished nitinol surfaces on adhesion and proliferation of MC3T3 pre-osteoblast cells. J. Mater. Sci. Mater. Med. 23, 2127–2139. doi:10.1007/s10856-012-4696-1
Rokicki, R., and Hryniewicz, T. (2008). Nitinol™ surface finishing by magnetoelectropolishing. Trans. Inst. Met. Finish. 86, 280–285. doi:10.1179/174591908X345040
Rokicki, R., and Hryniewicz, T. (2012). Enhanced oxidation-dissolution theory of electropolishing. Trans. Inst. Met. Finish. 90, 188–196. doi:10.1179/0020296712Z.00000000031
Rokicki, R., Hryniewicz, T., and Rokosz, K. (2008). Modifying metallic implants with magnetoelectropolishing, (invited paper). Med. Device Diagn. Ind. 30, 102–111.
Rokosz, K. (2011). Pomiar XPS składu chemicznego warstwy wierzchniej powstałej na stali austenitycznej AISI 316L SS po elektrochemicznym polerowaniu w polu magnetycznym (XPS measurement of chemical composition of surface layer formed on austenitic AISI 316L SS after electrochemical polishing in magnetic field) (in Polish). PAK 57, 563–567.
Rokosz, K. (2012). Electrochemical Polishing of Steels in a Magnetic Field (in Polish). Koszalin: Editorial Office of Politechnika Koszalinska, 211.
Rokosz, K., and Hryniewicz, T. (2010a). Pitting corrosion resistance of AISI 316L SS in Ringer’s solution after magnetoelectrochemical polishing. Corrosion 66, 035004-035004-11. doi:10.5006/1.3360910
Rokosz, K., and Hryniewicz, T. (2010b). Investigation of selected surface properties of AISI 316L SS after magnetoelectropolishing. Mater. Chem. Phys. 123, 47–55. doi:10.1016/j.matchemphys.2010.03.060
Rokosz, K., and Hryniewicz, T. (2011). Effect of magnetic field on the pitting corrosion of austenitic steel type AISI 304. Ochrona przed Korozja 54, 487–491.
Rokosz, K., and Hryniewicz, T. (2013a). XPS measurements of LDX 2101 duplex steel surface after magnetoelectropolishing. Int. J. Mater. Res. 104, 1223–1232. doi:10.3139/146.110984
Rokosz, K., and Hryniewicz, T. (2013b). Cr/Fe ratio by XPS spectra of magnetoelectropolished AISI 316L SS using linear, Shirley and Tougaard method of background subtraction. Adv. Mater. Sci. 13, 11–20.
Rokosz, K., and Hryniewicz, T. (2013c). Magnetoelectropolishing: modern and effective method of AISI 316L SS surface finishing. PAK 59, 1304–1307.
Rokosz, K., Hryniewicz, T., and Raaen, S. (2012a). Characterization of passive film formed on AISI 316L stainless steel after magnetoelectropolishing in a broad range of polarization parameters. Steel Res. Int. 83, 910–918. doi:10.1002/srin.201200046
Rokosz, K., Hryniewicz, T., and Raaen, S. (2012b). XPS measurements of 4H13 martensitic steel after electropolishing operation with electrolyte stirring. PAK 58, 545–548.
Rokosz, K., Hryniewicz, T., Valicek, J., Harnicarova, M., and Vyležik, M. (2012c). Nanoindentation measurements of AISI 316L biomaterial samples after annual immersion in Ringer’s solution followed by electrochemical polishing in a magnetic field. PAK 58, 460–463.
Rokosz, K., Hryniewicz, T., and Raaen, S. (2014). Cr/Fe ratio by XPS spectra of magnetoelectropolished AISI 316L SS fitted by Gaussian-Lorentzian shape lines. Technical Gazette 21, 4.
Rokosz, K., and Raaen, S. (2011). Badania XPS stali martenzytycznej 4H13 po elektrochemicznym polerowaniu (XPS measurements of martensitic stainless steel 4H13 after the electrochemical polishing) (in Polish). Autobusy Technika Eksploatacja Systemy Transportowe 5, 1–10.
Keywords: magnetoelectropolishing, biomaterials, surface layer composition, corrosion resistance, mechanical properties
Citation: Hryniewicz T and Rokosz K (2014) Highlights of magnetoelectropolishing. Front. Mater. 1:3. doi: 10.3389/fmats.2014.00003
Received: 27 January 2014; Accepted: 03 April 2014;
Published online: 05 May 2014.
Edited by:
Pedro De Lima-Neto, Universidade Federal do Ceará, BrazilReviewed by:
Artur Jesus Motheo, University of Sao Paulo, BrazilPedro De Lima-Neto, Universidade Federal do Ceará, Brazil
Copyright: © 2014 Hryniewicz and Rokosz. This is an open-access article distributed under the terms of the Creative Commons Attribution License (CC BY). The use, distribution or reproduction in other forums is permitted, provided the original author(s) or licensor are credited and that the original publication in this journal is cited, in accordance with accepted academic practice. No use, distribution or reproduction is permitted which does not comply with these terms.
*Correspondence: Tadeusz Hryniewicz and Krzysztof Rokosz, Division of Surface Electrochemistry, Koszalin University of Technology, Raclawicka 15-17, Koszalin PL 75-620, Poland e-mail: tadeusz.hryniewicz@tu.koszalin.pl; rokosz@tu.koszalin.pl