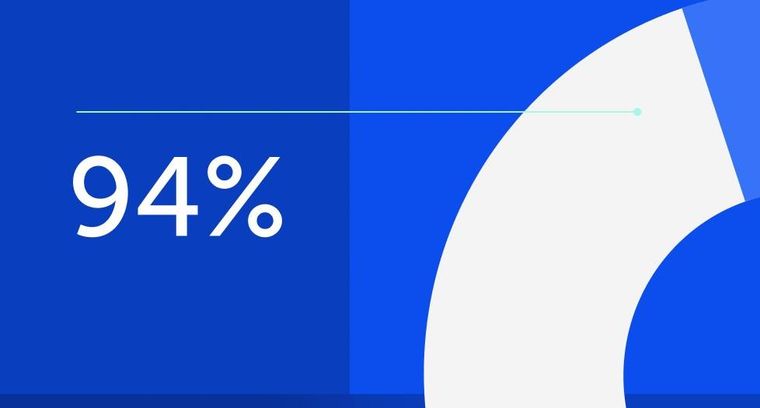
94% of researchers rate our articles as excellent or good
Learn more about the work of our research integrity team to safeguard the quality of each article we publish.
Find out more
ORIGINAL RESEARCH article
Front. Mar. Sci., 02 September 2022
Sec. Marine Biotechnology and Bioproducts
Volume 9 - 2022 | https://doi.org/10.3389/fmars.2022.948086
This article is part of the Research TopicBoosting the Potential of Algae for Biomass Production, Valorisation, and BioremediationView all 9 articles
The biorefinery concept facilitates the extraction of different constituents from seaweed, ensuring full usage of resources and generating few residues through a succession of steps. Innovative and environmentally-friendly extraction techniques, dubbed “green processing technologies,” have been developed in recent years. Using the bioprocess simulation software SuperPro Designer®, a model was developed and used to demonstrate the feasibility of two different multi-product biorefinery scenarios applying green technologies to one of the most promising species in Europe, the brown alga Saccharina latissima (sugar kelp). Analyzing the current state of the art and commercial applications, enzyme-assisted extraction was chosen as an emerging sustainable technology to simulate the production of alginate and the functional saccharides laminarin and fucoidan. These simulations were compared to an additional simulation of alginate production using the low-yield alkaline extraction technique currently used in the industry, which has been proven not feasible for the expected prices of cultivated seaweed in Europe. Complete biomass valorization is achieved by the sub-processing of the by-streams into complementary products such as biostimulants and animal feed. The valorization of up to 1.07 € per kilogram of fresh weight biomass was achieved using enzyme-assisted extraction and prioritizing laminarin and fucoidan as main products. Extraction yields and raw biomass alginate composition have the largest sensitivity effects on the profitability of biorefineries. This provides further insight into the crucial research opportunities on downstream processing and seaweed cultivation targets.
There is an increasing worldwide interest in seaweed production, as it represents a promising sustainable biomass source that could serve as feedstock for a plethora of valuable products. This has created a market opportunity for seaweed-derived products. Governmental agencies and private investors are strongly encouraging the macroalgae industry in Europe. A moderately ambitious prediction of the European productivity of seaweed reaches 4.7 million fresh weight tons per year by 2030, a 15.6-fold increase from the current 300,000 tons produced (Vincent et al., 2020).
The brown alga Saccharina latissima has gathered the most attention in Europe due to the current knowledge on production strategies, production yields, scalability, and high concentration of valuable biomolecules. The main constituent of S. latissima is alginate, a highly valuable polysaccharide that is widely used as a thickener and gelling agent in medical and food products (Rhein-Knudsen et al., 2015). Currently, the main industrial application of brown seaweed is alginate alkaline extraction, which has low yields and demands a high level of unsustainable acids and alkaline processing steps (Łabowska et al., 2019). In addition to alginate, the most important storage carbohydrates are laminarin and fucoidan, which correspond to a varying range of 5%–45% of the total dry weight and have promising bioactivity and therapeutic properties (Ale et al., 2011; Sharma et al., 2018; Cui et al., 2021). Complementary, it contains relatively high concentrations of other important components such as proteins, polyunsaturated fatty acids (PUFAs), cellulose, and minerals (among others) that can be used in different applications, such as animal feed supplements and vegetable biostimulants (Lange et al., 2020).
The previously proposed biorefineries mirror the techniques used in plant-derived biomass processing, which strongly rely on unsustainable or hazardous operations such as solvent extraction, alkaline extraction, or other harsh chemical pre-treatments (Fasahati et al., 2015; Kadam et al., 2017; Soleymani and Rosentrater, 2017). Novel sustainable technologies have emerged in the last decade and are currently a strong research topic in seaweed valorization. These promising techniques, dubbed “green technology,” include enzyme-assisted extraction, microwave-assisted extraction, ultrasound-assisted extraction, sub-critical water processing, super-critical fluid extraction, ionic liquids, and deep eutectic solvents (Postma et al., 2018; Bordoloi and Goosen, 2020).
To ensure the commercial success of the seaweed industry in Europe, the production cost of processed bulk products must be compensated with additional revenue. Furthermore, the implementation of multi-product biorefineries in which nearly 100% of the biomass can be valorized using novel green technologies would be a crucial milestone for sustainability (Jouanneu et al., 2021).
Despite their potential, few techno-economic evaluations of multiproduct biorefineries for S. latissima focusing on novel green technologies have been conducted. Among all the green technologies available, enzyme-assisted extraction (EAE) has been the most explored and thus a higher amount of data is available for techno-economic analysis. This work aims to design a macroalgae biorefinery based on EAE as a novel green technology that is economically feasible for 10% of the expected seaweed production in Europe by 2030. The bioprocess-simulation software SuperPro Designer® is used to design the process and calculate the material and energy balances. In total, two scenarios are designed, evaluated, and compared with traditional alkaline extraction methods.
The process is designed using the currently available information in the literature. This scheme is then evaluated in the bioprocess simulator SuperPro Designer®, with which the material and energy balances of each unit operation are based on specific economic and processing inputs and yields.
The available feedstock is assumed to be 470,000 tons of seaweed fresh weight (FW) biomass per year, which is equivalent to 10% of the predicted production of total seaweed in Europe by 2030 (Vincent et al., 2020). Van den Burg and company stated that the selling price of seaweed for hydrocolloid extraction is 950 USD per ton of dry weight (DW) biomass. After correcting for inflation using the consumer price index, conversion to euros and assuming a dry matter content of 20% in seaweed, the selling price for fresh weight biomass is considered €123 per ton FW (van den Burg et al., 2016; Juul et al., 2021) and €1,230 per ton DW (KelpBlue, 2022).
The biorefinery factory is assumed to operate for 330 days per year in a batch-operated mode. All economic calculations are evaluated with the Euro as the currency and have a reference value of €0.87 per USD (as of October 2021).
Alginate is the most abundant polymer in brown algae, and it is considered a structural polysaccharide that is widely used in the industry for its jellying properties. The most important storage carbohydrates are mannitol, laminarin, and fucoidan; the combination of these three corresponds to a varying range of 5%–45% of the total dry weight. The biomass and polysaccharide composition were chosen during the high-harvesting season in late spring and during shallow cultivation (Sharma et al., 2018). The polysaccharide composition used for the simulations is presented in Table 1.
Alginate is composed of mannuronic acid and guluronic acid linked by a β-1,4-glycosidic bond. Their molecular ratio (M/G) is crucial for the jellying properties (and thus quality) of alginate. Due to the higher degree of rotation of guluronic acid around the glycosidic bond, the lower the M/G ratio, the higher the viscosity of the polysaccharide (Jiao et al., 2019). This proportion depends on the species and cultivation strategies, which is not within the scope of this work. Therefore the ratio of 0.77 was chosen for the simulations in accordance with previous work conducted on multicomponent separation of S. latissima (Sterner and Edlund, 2016). The total glucose concentration in the dry weight biomass is 14.08% (Sharma et al., 2018). Since cellulose and laminarin are both completely composed of glycosidic monomers and are present at varying concentrations, it is assumed that half of it is part of structural cellulose while the other half is storage laminarin.
The biomass from S. latissima was initially washed in an automatic algae washer with fresh water at ambient temperature to remove leftover impurities that could reduce the overall yield of the process and further ground. A simplified representation of this process is seen in Figure 1.
The pretreated biomass was then subjected to enzyme-assisted extraction in a stirred tank reactor with a loading of 5% DW. High dilution of the biomass must prevent extreme process viscosities because of the extracted alginate. Following previous studies on the liquefaction of brown algae using different hydrolases (Habeebullah et al., 2020), the biomass undergoes enzymatic reaction with an alcalase (with endo and exo protease activities) at a loading of 0.1% of the total dry weight for 3 h at 50°C. It is assumed from the work of Sabeena and company that 70% of the biomass components will be extracted from the biomass (Habeebullah et al., 2020).
Sterner and Edlund determined that the chelation strength of extraction media with sodium citrate in low alkaline solutions increased the extraction yield of alginate, increased its purity, and gave the optimal G:M ratio. Furthermore, immediately after the enzymatic reaction, sodium citrate will be charged to the reactor at a loading of 5% of the initial biomass dry weight, and pH will be adjusted to 9.3. Alginic acid (guluronic acid and mannuronic acid) can be converted into sodium alginate (Sterner and Edlund, 2016).
It is assumed that all the alginic acid released from the EAE will be converted into a completely soluble sodium alginate (Hernández-Carmona et al., 1998). During the extraction and the alginate solubilization, an increase in process viscosity is expected (Hernández-Carmona et al., 1999). Therefore, the power consumption of the equipment was calculated based on the empirical equations for viscous substances in a stirred tank reactor (Ameur et al., 2017), the reactor design, and the maximum viscosity of 4,000 mPa s reported by Hernandez-Carmona et al. (1999). This resulted in a specific power consumption of 2.52 kW m−3. The stream will be diluted in-line at a ratio of 1.4 MT of water per MT of extracted media to reduce the viscosity and increase the filtration yields. The diluted content will be filtered in rotatory filtration units to remove the debris and the unextracted biomass.
The permeate undergoes the well-known calcium alginate process for alginate purification. In summary, alginate is isolated via precipitation of calcium alginate and further treated with acid and sodium carbonate and dried (Mchugh et al., 2001; Hernández-Carmona et al., 2002; Jiao et al., 2019).
After the rotatory filtration, the retained debris will be further treated to obtain the biostimulant and animal feed by-products. The retentate will be subjected to a second enzymatic treatment with the same protease mixture and conditions as the previous. During this step, besides a second extraction, the soluble protein that was retained will be hydrolyzed into smaller peptides. The solids are removed and dried for animal feed, while the liquids are commercialized as biostimulants for vegetable growth. The protease is not deactivated because, for both the biostimulant and the animal feed, smaller peptides are desired as they increase the nitrogen uptake (Kocira et al., 2020; Goñi et al., 2021) and digestibility, respectively.
A second enzyme-assisted extraction biorefinery simulation of S. latissima was developed, focusing now on fucoidan and laminarin purification. In this scenario, carbohydrases, specifically alginate and hemicellulose degrading hydrolytic enzymes, are used. As a result, alginate is partially degraded during the initial extraction, reducing the viscosity of the process and therefore limiting considerably the amount of water needed (An et al., 2008). Because of this, the overall size of the equipment is also reduced since no additional water is required to dilute the main streams. Figure 2 presents a simplified flowchart for the biorefinery of laminarin and fucoidan production.
Figure 2 Simplified flowchart for laminarin and fucoidan production biorefinery using enzyme assisted extraction.
Few studies have researched the EAE of brown algae by focusing on fucoidan and laminarin rather than alginate. The extraction conditions and yields were obtained from the work of Nguyen and colleagues. During the EAE, an enzymatic mixture of cellulase and alginate was added at a rate of 4% (w/w) of biomass solids for 3 h. The extraction results from the hydrolysis of the structural polysaccharides cellulose and alginate, thus reducing the overall viscosity and releasing the lower molecular weight polysaccharides and peptides (Nguyen et al., 2020). A yield of 30% fucoidan release was reported by Nguyen. For this simulation, this same percentage is assumed as the overall extraction efficiency.
After the precipitation of leftover alginate, the aqueous filtrate is then subjected to different filtration and dialysis operations to concentrate the stream and separate fucoidan from laminarin. Fucoidan has a varying molecular weight between 200 and 500 kDa (Nguyen et al., 2020; Wang et al., 2021), while laminarin is considerably smaller, ranging from 3 to 10 kDa (Graiff et al., 2016; Wang et al., 2021).
An initial ultra-diafiltration step is used to wash and concentrate fucoidan and laminarin using a MWCO of 5 kDa at a flux of 30 L m–2 h−1, which is within the range of industrial ultrafiltration capacities (Harrison et al., 2015). Afterwards, the filtration strategy followed for the simulation is based on the work reported by Sterner and Gröndahl. In short, the washed retentate will be ultrafiltered at a MWCO of 50 kDa. The permeated laminarin is concentrated at a MWCO of 5 kDa (Sterner and Gröndahl, 2021). The overall retention yields vary among different studies, therefore it will be assumed to be 80%. Further research must be conducted to obtain a better understanding of the retention yields of ultrafiltration of S. latissima-derived polysaccharides. To give a better insight into the importance of research on this matter, the effect on the profitability of these yields will be validated in the sensitivity analysis. A final spray drying step polishes the product for sale.
For the by-product processing, the recovered precipitated alginate is mixed with the debris left from rotatory filtration and processed into a biostimulant and feed as described previously. In this scenario, the two sub-products have higher alginate concentrations.
Depreciation will be calculated using the straight-line method, meaning that the deductible depreciation per year will be equal to 10% of the Direct-Fixed Capital Costs (DFC). Following the construction, a 4-month startup period is considered. The salvage value of the equipment will be omitted as it is not intended to be sold. According to Dutch legislation, the disposal cost is equivalent to €13.07 per ton of waste that goes to landfill or is incinerated.
To reduce the uncertainty level of the simulations, no debts or loan interests will be considered to reduce the uncertainty level of the simulations. These parameters are unique for every company and can be easily adapted in a CAPEX/OPEX project of a stakeholder using the outcome of this work. The tax will be 25%, as it is stipulated by Dutch law for companies with incomes above €245,000 (Netherlands, 2022). No running royalties are considered, as R/D is already included, and no patent is assumed to be bought. Also, there will be no advertising or selling expenses.
Working capital is calculated based on three months of operating expenses (labor, raw materials, utilities, waste treatment, etc.). The startup period will account for 5% of the DFC. The DFC is calculated according to a modified version of the average value for enzymatic processes proposed by Heinzle (Heinzle et al., 2007). The installation cost was established individually for every unit operation and varied from 40% to 60% of the equipment cost. Table 2 summarizes the economic multipliers for the biorefinery simulation.
Table 2 Economic multipliers (Lang factors) for direct fixed cost estimation based on equipment purchase cost.
In comparison with Heinzle, the instrumentation costs are assumed to be the maximum value for the established range, as a highly automated plant is expected.
The equipment costs were calculated by combining the scale up and inflation index costs, as summarized in Equation (1).
Where the new equipment cost (Cost2) is calculated from a reference cost (Cost1) taken through direct contact with equipment providers or from different databases on the internet (Peters et al., 2002; Matche.com, 2014). The scale up was calculated at a factor of 0.6, which is common for blending tanks. Finally, the Chemical Engineering Plant Cost Index (I2 and I1) is used to fix for inflation if the reference was made in previous years (Harrison et al., 2015).
The operational costs consider the cost of materials, labor, consumables, laboratory QC&QA, waste treatment/disposal, utilities and facility dependent. Although there are multiple studies addressing the logistic, transportation, and R&D costs of the upcoming seaweed industry, due to a lack of concrete results and the fact that these costs are usually absorbed by the production cost of the seaweed biomass, these parameters won’t be considered in the biorefinery simulations (Vincent et al., 2020).
The labor-hours per hour (the real time that an operator will be operating an equipment during an hour of processing) of every equipment will be determined individually for every equipment unit. The total labor cost will be the sum of the yearly labor hour demand multiplied by the labor cost rate. The total labor cost for an operator will be determined by the average labor cost of the Netherlands, equal to 36.8 € h−1 (Eurostat, 2020), multiplied by a lumped factor of 1.18 (which includes labor benefits, administrative costs of labor, etc.), which results in a lumped rate of 43.42 € hr−1. Laboratory quality control will be assumed to be 15% of the total labor cost. The material, consumables, and waste treatment costs are going to be individually addressed based on material balances and equipment specifications. As for utilities, the power cost is assumed to be 0.102 € kW-h−1 (Global Petrol Prices, 2021), while the cost for steam production is assumed at 10 € ton−1.
The facility-dependent costs include the depreciation of the biorefinery and the administrative costs. The maintenance will be stated individually for each major equipment while the depreciation costs are calculated according to Equation (2). Insurance, local taxes, and factory expenses are considered as 1%, 2%, and 5% of DFC, respectively.
To fully understand the additional value that the biorefinery adds to the seaweed, the price of the feedstock will not be considered during the simulations and the operational cost discussion of the biorefinery. Nonetheless, it will be considered once again during the unitary profit calculations.
Due to the novelty of industrial processing of seaweed in Europe, cashflow analysis would represent unrealistic scenarios with high degrees of uncertainty. Furthermore, the economic assessment of the simulations will be determined by the added value of the seaweed as feedstock. To get to this value, several costs (referenced to kg of fresh weight feedstock) are defined and described from Equation (3) to Equation (6). To appropriately analyze the bottlenecks in the process, the Partial Unitary Production Cost is used, in which all the operating costs per year, excluding the purchase price of seaweed, are divided by the total feedstock used. Furthermore, the Total Unitary Production Cost includes the cost of seaweed. Similarly, the unitary revenue is the yearly revenue divided by the raw material used. Finally, the Total Unitary Profit is the difference between the Total Unitary Revenue and the Total Unitary Production Costs.
Unitary profit calculation based on the total feedstock available in the simulations not only gives more insight into the actual feasibility of seaweed bioprocessing, but it also homogenizes all the simulations made in this study (as the initial feedstock is constant) and further opens an opportunity for proper comparison.
Complementary to the unitary profit, important economic parameters needed to assess the profitability and attractiveness of an investment are calculated. Gross margin represents the rational amount of the revenues that are actual profit and will be calculated according to Equation (7). Return of investment (ROI) is the percentual value of the annual net profit compared to the total investment of the biorefinery, as described by Equation (8). Finally, the payback time is the number of years that it will take to receive an equal amount of profit as the initial investment, or in other words, the inverse of the ROI (Equation (9)).
To determine the revenue, the market selling prices had to be determined and can be seen in Table 3. The selling price for alginate, laminarin, and fucoidan strongly depends on different factors, such as purity and chemical composition (the mannuronic acid: guluronic acid in alginate). The prices used for this simulation were taken from direct communication with seaweed producing companies and are within the ranges reviewed by Zhang and Thomsen (2019).
To pinpoint the factors with more impact over the unitary profit of each process, a sensibility analysis is performed to every simulation. At least six parameters of each process are separately modified from the initial simulation and assessed at ±20% variability while keeping every other aspect of the process constant. The relative effect of each parameter is calculated and defined as the change in the profit in comparison to the original (Equation (10)).
The relative effect is then used to calculate the elasticity factor (at 20% variation) of the parameter. The elasticity represents the effect of the variation compared to the change in the parameter and is calculated according to Equation (11).
The process has an annual operating time of 330 days. The total batch time for this recipe is 26 h. The first step, algae washing, is time-limited and lasts 8.5 h. Therefore, to increase the overall equipment usability, a cycle time of 8.5 h was established. A new batch will start exactly after the previous batch finishes the first step, working semi-continuously. Furthermore, 929 batches per year are performed. With a biomass loading of 505 MT per batch, a total amount of 470,526 MT is processed every year, equivalent to 10% of the expected seaweed production by 2030.
The simulation predicts that 16,210 MT of alginate with a purity of 69.50% will be produced on a yearly basis. The overall alginate yield is 70%, which directly corresponds to the enzymatic extraction efficiency. The precipitation and solubilization strategy of calcium chloride processing of alginate is a well-known process optimized to reduce alginate loss (Hernández-Carmona et al., 1999). Furthermore, the initial extraction and solubilization of alginate is the limitation and key point for optimization.
The permeated aqueous stream after the calcium alginate precipitate recovery through screen filtration can be further processed into nutritional or pharmaceutical compounds. The stream contains 1.8 MT, 4.5 MT, and 4.63 MT of fucoidan, laminarin, and protein per batch, respectively. The debris that is treated with protease hydrolysis results in 28 MT batch−1 of animal feed and 113,044 MT of vegetable biostimulant with a high concentration of laminarin and fucoidan. Figure 3 presents the material balance of the raw feedstock composition.
Figure 3 Sankey diagram for the raw material mass flow throughout the alginate biorefinery of S. latissima.
The total capital investment was equal to €314,781,000. This is around 2.2 times the total plant direct costs, which is €141,682,000. The reactors for EAE represent most of the equipment costs at 33.25%. This is followed by the number of storage reception tanks required for the implementation of semi-continuous processing at 18.17%. The principal drawback of this process is the high working volumes derived from the need to dilute the streams to reduce the viscosity of the process and increase the recovery yields. This is instantly reflected in the increasing cost of the processing tanks when working in a batch mode. The equipment specifically required for the processing of biostimulants and feed is equivalent to 27% of the total equipment cost.
The total annual operating costs (excluding seaweed) are €95,815,683, of which 25.68% are CAPEX while 74.32% are OPEX. As appreciated in Figure 4, raw materials represent 41% of the total operating costs, which leads considerably over the utilities, which account for only 16% of the total costs. This is in accordance with different techno-economic assessments of biorefinery of seaweed using EAE, where the materials are the limiting factor of the process (Charoensiddhi et al., 2018).
Figure 4 Operational cost distribution (%) of alginate biorefinery and laminarin and fucoidan biorefinery of S. latissima. € is Euro, % is percentage.
The partial unitary operating cost is 0.204 € kgFW−1. By adding the purchase cost for fresh weight seaweed (0.123 € kgFW−1), the total unitary production cost is 0.327 € kgFW−1. The cost of seaweed represented 37.61% of the total cost. Surprisingly, enzyme costs only represent 1.68% of the total bulk materials. This is due to the high yield of 70% and low enzyme costs (Rao et al., 2010). Protease is a commonly used enzyme in industry, and a plethora of research has been conducted to reduce its production costs.
The parameters evaluated in a sensibility analysis for S. latissima biorefineries were chosen due to their obvious effect on the process. The parameters along with the change in profit and the elasticity coefficient can be found in Figure 5. It was expected that the alginate composition had a major effect over the profitability; it was proven that with a more concentrated feedstock, the profit rises because the productivity increases considerably more than the operational costs. Alginate composition had a positive elasticity coefficient of 3.1, which means that the effect on the profitability was three times greater than the change in alginate concentration.
Figure 5 Tornado diagram of sensibility analysis for alginate production with S. latissima with change in profit as a function of ±20% variation in each parameter and, labeled the elasticity coefficient for each evaluated parameter.
Complementary, the selling price of alginate and an elasticity coefficient of 2.1. The change in profit is almost proportional to the change in the cost of the seaweed feedstock and biostimulant, both with elasticity coefficients near 1. The change in the selling price of animal feed and the cost of enzymes is not significant over the profit of the biorefinery. The latter might be surprising in the first instance, but nevertheless, the buying price and high yields considered for this simulation are very optimistic.
The operating characteristics are the same as in the previous simulation (recalling that 505 MT of biomass is processed per batch for 929 batches per year). The tank used for the enzyme-assisted extraction is clearly a limitation of the process due to its high operating time (17.5 h). In the simulation, it is assumed that the washing and grinding of the biomass along with the reception of the biomass by the tank for EAE occur in parallel. This, although it seems like a time-saving strategy, is a drawback to the process. If the biomass were to be stored in a different (cheaper) tank, there would not be the necessity to stagger a complementary bioreactor. Further optimization is required.
The biorefinery produces 1,193 MT and 2,592.52 MT of fucoidan and laminarin per year, respectively. This quantity is considerably lower than the biostimulant (171,134 MT per year) and animal feed (44,915 MT per year). Nevertheless the high selling prices compensate for the limited production. Figure 6 describes the mass flow of the raw materials into their respective products. The final purity for laminarin and fucoidan is 65% and 67%, respectively.
Figure 6 Sankey diagram for the raw material mass flow throughout the laminarin biorefinery of S. latissima.
A notorious difference between this process and that one described in Simulation 2 is that the biostimulant and animal feed has higher amounts of alginic acid compared to Simulation 1.
The total investment for the biorefinery that prioritizes Fucoidan and Laminarin as main products is are M€ 561.3; that is 78% more compared to the alginate processing plant. When prioritizing the production of low molecular weight saccharides, ultrafiltration techniques for purification and concentration of compounds at different molecular weights are required. Complementary ultra-diafiltration is needed to remove salts and contaminants.
Furthermore, it is expected that filtering represents most of the equipment cost. The total cost for ultrafiltration is equal to 49% of the total equipment costs, of which 33% is due to the diafiltration units used to wash laminarin and fucoidan prior to their respective purifications. Although filtration is a sustainable and effective processing alternative, the high implementation could limit the profitability of the process.
When targeting fucoidan and laminarin, it is necessary to include an enzymatic cocktail with carbohydrases that degrade alginate. This reduces the processing viscosity, increases the filtration yields, and limits the amount of water needed for dilution. Nevertheless, this enzymatic cocktail is not as common as alkaline proteases, which in turn increases the purchasing price considerably. This is revealed in Figure 4, where 73.38% of the operational costs relate to raw materials, of which 51.2% represent the cost of the enzymes. The total operational costs were M€ 301.1, which represent 0.642 € kgFW−1.
For laminarin and fucoidan production, the elasticity effect of the evaluated parameters did not impact alginate production. These parameters, along with the change in profit and the elasticity coefficients, can be found in Figure 7.
Figure 7 Tornado diagram of sensibility analysis for laminarin production with S. latissima with change in profit as a function of ±20% variation in each parameter and, labeled the elasticity coefficient for each evaluated parameter.
EAE efficiency has the greatest impact on profitability, with a positive elasticity coefficient of 1.5 (less than half as the alginate composition was for Simulation 2). Next are the alginate composition and the filtration efficiency. In this scenario, a higher alginate percentage represents a diminution in the quantity of fucoidan and laminarin, thus having a negative effect.
The selling prices of laminarin and fucoidan have an equal effect on the profitability of the biorefinery. The cost of the enzymes has a moderate elasticity coefficient of 0.47, despite representing 60% of the partial operating costs.
The executive summary for all simulations is presented in Table 4, including an additional simulation on traditional alkaline alginate extraction based on the yields described by the works of Hernandez-Carmona and company (Hernández-Carmona et al., 1998; Hernández-Carmona et al., 1999; Mchugh et al., 2001; Hernández-Carmona et al., 2002). The complete simulation can be seen in the supplementary material; in brief, biomass is pre-treated using formalin and HCl, followed by an alkaline extraction using sodium carbonate. The extracted alginate was further purified as described in simulation 1.
Table 4 Executive summary for two biorefinery scenarios of S. latissima, with alginate as main product and with laminarin and fucoidan as main products.
Simulation 2 (laminarin production from S. latissima) had the highest unitary gross profit with €1.07 of profit per kg of seaweed, while Simulation 1 (alginate from S. latissima) had €0.125 per kg of fresh weight. The traditional alkaline extraction has a negative profit margin due to the cost of seaweed and the low extraction yields.
Simulation 2 requires 1.78 times more capital investment than Scenario 1. Similarly, the operational costs of laminarin production are the highest due to the high cost of the enzymatic cocktail (composed of cellulase and alginase) in comparison with the cheaper protease used for Simulation 1. Despite this, laminarin and fucoidan from Simulation 3 have the highest unitary selling cost of all the products used in this work. Furthermore, the total revenues for Simulation 3 are nearly four times bigger.
Under the current conditions, alginate production from S. latissima is the least profitable scenario, with 0.12 € kgFW−1. It has the lowest revenues and unitary profit. Both the operational and investment drawbacks of the process are a result of the operational viscosity. Some efforts have been made to overcome this situation, such as cyclic alginate extraction using ion-absorbing resin (Sterner et al., 2017).
One of the main drawbacks to designing a seaweed biorefinery is that its bromatological composition and availability may change drastically from season to season (Sharma et al., 2018; Mohy El-Din, 2019; Suresh Kumar et al., 2021), thus representing a risk to the profitability. Optimal late-spring harvesting conditions were chosen for this simulation. Nonetheless, sensitivity analysis confirmed that small variations in biomass composition may have a meaningful impact on profit. This is in accordance with the constraints and challenges of seaweed biorefinery presented in the Biorefinery Manual from the GENIALG project. (Jouanneu et al., 2021). This is an issue specifically for Simulation 2, where fucoidan and laminarin production represent 90% of the total revenues but only 7% of the dry matter biomass composition.
Recalling from the sensitivity analysis on alginate production, there are several external factors that could be optimized to increase the profitability of the process, such as the alginate composition of the feedstock and the market value of higher quality alginate. Complementary, the enzymatic extraction conditions should also be further optimized and scaled to pilot testing levels. From all the main products evaluated, alginate is the most promising in terms of current market and applications, so it should not be ignored. On the contrary, more research (both in cultivation and processing technology) should be done in the upcoming years.
As previously detailed, the presented scenarios are based on referential data and assumptions. Processing parameters, conditions, yields, and prices have been cautiously chosen from the vast amount of literature and coupled into this work in order to provide insights into the profitability of seaweed processing and valorization under the current state-of-the-art. In a fast-growing industry with a plethora of stakeholders, this analysis is imperative to lead the way into a more profitable direction and accelerate the industrial establishment of seaweed processing.
Furthermore, the production of techno-economic evaluations of seaweed processing is highly encouraged. To reduce the level of uncertainty, future experimentation on seaweed valorization should report detailed yields, processing conditions, and mass balances. To complement, pilot scale testing would be highly beneficial as it could provide a more accurate representation of the industrial setting.
Two biorefinery simulations for the brown seaweed S. latissima using EAE were evaluated with positive results. Under the expected price of European cultivated seaweed, classic non-circular alkaline alginate extraction is not feasible.
The two most important parameters are the biomass composition and the EAE efficiency, which directly represent the amount of raw product available for processing. The selling price of alginate also has a reasonable elasticity effect on the profit.
In every scenario, the raw material expenses represent the higher operational costs. For biorefineries with EAE using proteases (a commonly used enzyme in the industry with lower costs), raw materials represent 40% of the total operational costs. As for the EAE biorefineries using more specific and expensive carbohydrate degrading enzymes, the raw material costs increase up to 72%.
At a purchasing cost of €0.123 per kg of fresh weight, it is tentatively possible to make a profitable biorefinery. Nevertheless, efforts on reducing the production costs of cultivated seaweed need to continue to reduce its percentage cost on biorefinery processing.
Complete valorization of the biomass is needed to increase profitability. Biostimulant is a promising product that can be easily commercialized. Animal feed is used as a low-income valorization of the remaining protein, although the revenues are negligible and only worth reducing waste treatment costs. Further protein isolation/purification may increase the value of this remnant protein.
However, EAE is a very plausible and promising green extraction method for the valorization of seaweed. Nevertheless, thorough and pinpointed research is still needed. Optimized enzymatic cocktails are required to increase the overall profitability of any seaweed biorefinery using this technology. Complementary, membrane separation, purification, and concentration of seaweed-derived polysaccharides are not widely researched. Due to the promising results in this paper, in-depth experimentation on this topic is imperative.
The information used for this work was mostly taken from lab-scale experiments at an overall technology readiness level of development. Seaweed biorefinery is promising, although more research is still needed, both at bench and pilot scale, to increase the processing yields and incorporate new information into more technoeconomic evaluations with a lower grade of uncertainty.
The original contributions presented in the study are included in the article/Supplementary Material. Further inquiries can be directed to the corresponding author.
JAHB, first authorship. He is the main contributor of this work. His contribution was on the acquisition of data, analysis, and interpretation, and drafting the article. GO is the SuperPro Designer expert. He is involved in the analysis and interpretation of data related to cost analysis, process modeling and interpretation, critical revision of the article. IB and ME contributed to the analysis of data and final approval of the article. AK was involved in the conception and design of the study, or acquisition of data, analysis, and interpretation of data, revising the article critically and give the final approval of the version to be submitted. RW was the Bioprocess Engineering Group Chair and was involved in revising the article critically and gave the final approval of the version to be submitted. All authors contributed to the article and approved the submitted version.
This study was supported by the Bioprocess Engineering Department of Wageningen University and research
This study is a result of many conversations with Kelp Blue and Algaia who are working on the processing of brown seaweed. We are very thankful for their input.
The authors declare that the research was conducted in the absence of any commercial or financial relationships that could be construed as a potential conflict of interest.
All claims expressed in this article are solely those of the authors and do not necessarily represent those of their affiliated organizations, or those of the publisher, the editors and the reviewers. Any product that may be evaluated in this article, or claim that may be made by its manufacturer, is not guaranteed or endorsed by the publisher.
The Supplementary Material for this article can be found online at: https://www.frontiersin.org/articles/10.3389/fmars.2022.948086/full#supplementary-material
Ale M. T., Mikkelsen J. D., Meyer A. S. (2011). Important determinants for fucoidan bioactivity: A critical review of structure-function relations and extraction methods for fucose-containing sulfated polysaccharides from brown seaweeds. Mar. Drugs 9 (10), 2106–2130. doi: 10.3390/MD9102106
Ameur H., Kamla Y., Sahel D. (2017). Data on the agitation of a viscous Newtonian fluid by radial impellers in a cylindrical tank. Data Brief 15, 752–756. doi: 10.1016/j.dib.2017.10.035
An Q., Zhang G., Wu H., Zhang Z., Gong W., Liu Y., et al. (2008). Production and partial properties of alginase from newly isolated flavobacterium sp. LXA. Process Biochem. 43 (8), 842–847. doi: 10.1016/j.procbio.2008.04.001
Bordoloi A., Goosen N. (2020). Green and integrated processing approaches for the recovery of high-value compounds from brown seaweeds. Adv. Botanical Res. 95, 369–413. doi: 10.1016/BS.ABR.2019.11.011
Charoensiddhi S., Lorbeer A. J., Franco C. M. M., Su P., Conlon M. A., Zhang W. (2018). Process and economic feasibility for the production of functional food from the brown alga ecklonia radiata. Algal Res. 29, 80–91. doi: 10.1016/J.ALGAL.2017.11.022
Cui Y., Zhu L., Li Y., Jiang S., Sun Q., Xie E., et al. (2021). ‘Structure of a laminarin-type β-(1→3)-glucan from brown algae sargassum henslowianum and its potential on regulating gut microbiota’. Carbohydr. Polymers 255, 117389. doi: 10.1016/j.carbpol.2020.117389
Eurostat (2020) Labour cost levels by NACE rev. 2 activity. Available at: https://ec.europa.eu/eurostat/databrowser/view/LC_LCI_LEV/bookmark/table?lang=en&bookmarkId=ef436941-7280-45dc-9145-e2f48ef775b4 (Accessed 8 October 2021).
Fasahati P., Woo H. C., Liu J. J. (2015). Industrial-scale bioethanol production from brown algae: Effects of pretreatment processes on plant economics. Appl. Energy 139, 175–187. doi: 10.1016/J.APENERGY.2014.11.032
Global Petrol Prices. (2021). Netherlands Fuel prices, electricity prices, natural gas prices. Available at: https://www.globalpetrolprices.com/Netherlands/.
Goñi O., Łangowski Ł., Feeney E., Quille P., O'Connel S. (2021). Reducing nitrogen input in barley crops while maintaining yields using an engineered biostimulant derived from ascophyllum nodosum to enhance nitrogen use efficiency. Front. Plant Sci. 12. doi: 10.3389/fpls.2021.664682
Graiff A., Ruth W., Kragl U., Karsten U. (2016). Chemical characterization and quantification of the brown algal storage compound laminarin — A new methodological approach. J. Appl. Phycol. 28, 533–543. doi: 10.1007/s10811-015-0563-z
Habeebullah S. F. K., Alagarsamy S., Sattari Z., Al-Haddad S., Karsten U., Fakhraldeen S., Al-Ghunaim S., et al. (2020). Enzyme-assisted extraction of bioactive compounds from brown seaweeds and characterization. J. Appl. Phycol. 32 (1), 615–629. doi: 10.1007/s10811-019-01906-6
Harrison R. G., Todd P. W., Rudge S. R., Petrides D. P. (2015). Bioseparations science and engineering (New York: Bioseparations Science and Engineering). doi: 10.1093/oso/9780195391817.001.0001
Heinzle E., Biwer A. P., Cooney C. L. (2007). Development of sustainable bioprocesses: Modeling and assessment (Development of Sustainable Bioprocesses: Modeling and Assessment). doi: 10.1002/9780470058916
Hernández-Carmona G., McHugh D., Arvizu-Higuera D., Rodríguez-Montesinos Y. (1998). Pilot plant scale extraction of alginate from macrocystis pyrifera. 1. effect of pre-extraction treatments on yield and quality of alginate. J. Appl. Phycol 10 (6), 507–513. doi: 10.1023/A:1008004311876
Hernández-Carmona G., McHugh D., Arvizu-Higuera D., Rodríguez-Montesinos Y. (2002). Pilot plant scale extraction of alginates from macrocystis pyrifera 4. conversion of alginic acid to sodium alginate, drying and milling. J. Appl. Phycol 14 (6), 445–451. doi: 10.1023/A:1022372807813
Hernández-Carmona G., McHugh D. J., López-Gutiérrez F. (1999). Pilot plant scale extraction of alginates from macrocystis pyrifera. 2. studies on extraction conditions and methods of separating the alkaline-insoluble residue. J. Appl. Phycol 11 (6), 493–502. doi: 10.1023/A:1008114709681
Jiao W., Chen W., Mei Y., Yun Y., Wang B., Zhong Q., et al. (2019). Effects of molecular weight and guluronic Acid/Mannuronic acid ratio on the rheological behavior and stabilizing property of sodium alginate. Molecules 24 (23), 4374. doi: 10.3390/molecules24234374
Jouanneu D., Hanbidge A., Cascella K., Potin P. (2021). Biorefinery manual: Benefits and sustainability of seaweed biorefinery. Zenodo doi: 10.5281/zenodo.5046385
Juul L., Danielsen M., Nebel C., Steinhagen S., Bruhn A., Jensen S., et al. (2021). ‘Ulva fenestrata protein – comparison of three extraction methods with respect to protein yield and protein quality’. Algal Res. 60, 102496. doi: 10.1016/J.ALGAL.2021.102496
Kadam S. U., Álvarez C., Tiwari B. K., O'Donnell C. P. (2017). Extraction and characterization of protein from Irish brown seaweed ascophyllum nodosum. Food Res. Int. 99, 1021–1027. doi: 10.1016/J.FOODRES.2016.07.018
Kocira S., Szparaga A., Hara P., Treder K., Findura P., Bartoš P., et al. (2020). Biochemical and economical effect of application biostimulants containing seaweed extracts and amino acids as an element of agroecological management of bean cultivation. Sci. Rep. 10 (1), 17759. doi: 10.1038/s41598-020-74959-0
Łabowska M. B., Michalak I., Detyna J. (2019). Methods of extraction, physicochemical properties of alginates and their applications in biomedical field - a review. Open Chem. 17 (1), 738–762. doi: 10.1515/chem-20191-0077
Lange L., Bak U., Hansen S., Gregersen O., Harmsen P., Karlsson E., et al. (2020). ‘Opportunities for seaweed biorefinery’, in Dolores Torres M., Kraan S., Dominguez H. (eds) Sustainable Seaweed Technologies 1st edn. Amsterdam: Elsevier. pp. 3–31. doi: 10.1016/B978-0-12-817943-7.00001-9
Matche.com (2014) Matches. Available at: http://www.matche.com/equipcost/Reactor.html.
Mchugh D. J., Hernández-Carmona G., Luz Arvizu-Higuera D., Rodríguez-Montesinos Y. (2001). Pilot plant scale extraction of alginates from macrocystis pyrifera 3. precipitation, bleaching and conversion of calcium alginate to alginic acid. J. Appl. Phycol 13 (6), 471–479. doi: 10.1023/A:1012532706235
Mohy El-Din S. M. (2019). Temporal variation in chemical composition of ulva lactuca and corallina mediterranea. Int. J. Environ. Sci. Technol. 16 (10), 5783–5796. doi: 10.1007/s13762-018-2128-6
Netherlands, G. of the (2022) Taxation and bussiness. Available at: https://www.government.nl/topics/taxation-and-businesses/corporation-tax.
Nguyen T. T., Mikkelsen M., Nguyen Tran V., Dieu Trang V., Rhein-Knudsen N., Holck J., et al. (2020). Enzyme-assisted fucoidan extraction from brown macroalgae fucus distichus subsp. evanescens and Saccharina latissima. Mar. Drugs 18 (6), 296. doi: 10.3390/md18060296
Peters M., Timmerhaus K., West R. (2002) McGrawHill, equipment cost for plant design and economics for chemical engineers - 5th edition. Available at: http://www.mhhe.com/engcs/chemical/peters/data/.
Postma P. R., Cerezo-Chinarro O., Akkerman R., Olivieri G., Wijffels R., Brandenburg W., et al. (2018). Biorefinery of the macroalgae ulva lactuca: extraction of proteins and carbohydrates by mild disintegration. J. Appl. Phycol 30 (2), 1281–1293. doi: 10.1007/s10811-017-1319-8
Rao R. R., Vimudha M., Kamini N., Gowthaman M., Chandrasekran B., Saravanan P. (2010). Alkaline protease production from brevibacterium luteolum (MTCC 5982) under solid-state fermentation and its application for sulfide-free unhairing of cowhides. Appl. Biochem. Biotechnol. 182, 511–528. doi: 10.1007/s12010-016-2341-z
Rhein-Knudsen N., Ale M. T., Meyer A. S. (2015). Seaweed hydrocolloid production: An update on enzyme assisted extraction and modification technologies. Mar. Drugs 13 (6), 3340–3359. doi: 10.3390/MD13063340
Seaweed for Europe (2020). Hidden champion of the ocean: Seaweed as growth engine for a sustainable European future. Bonn: Seaweed for Europe
Sharma S., Neves L., Funderud J., Mydland L., Øverland M., Horn S. (2018). Seasonal and depth variations in the chemical composition of cultivated Saccharina latissima. Algal Res. 32, 107–112. doi: 10.1016/j.algal.2018.03.012
Soleymani M., Rosentrater K. A. (2017). Techno-economic analysis of biofuel production from macroalgae (Seaweed). Bioengineering 4 (4), 92. doi: 10.3390/bioengineering4040092
Sterner M., Edlund U. (2016). Multicomponent fractionation of Saccharina latissima brown algae using chelating salt solutions. J. Appl. Phycol 28 (4), 2561–2574. doi: 10.1007/s10811-015-0785-0
Sterner M., Ribeiro M., Gröndahl F., Edlund U. (2017). Cyclic fractionation process for Saccharina latissima using aqueous chelator and ion exchange resin. J. Appl. Phycol 29 (6), 3175–3189. doi: 10.1007/s10811-017-1176-5
Sterner M., Gröndahl F. (2021). Extraction of laminarin from Saccharina latissima seaweed using cross-flow filtration. J. Appl. Phycol 33 (3), 1825–1844. doi: 10.1007/s10811-021-02398-z
Suresh Kumar K., Kumari S. K., Singh K., Kushwaha P. (2021). ‘Influence of seasonal variation on chemical composition and nutritional profiles of macro‐ and microalgae’, in recent advances in micro- and macroalgal processing: Food and health perspectives. 1st edn. John Wiley & Sons Ltd.
van den Burg S. W. K., van Duijn A., Bartelings H., van Krimpen M., Poelman M. (2016). The economic feasibility of seaweed production in the north Sea. Aquaculture Economics Manage. 20 (3), 235–252. doi: 10.1080/13657305.2016.1177859
Vincent A., Stanley A., Ring J. (2020). Hidden champion of the ocean: Seaweed as growth engine for a sustainable European future.
Wang S. H., Huang C., Chen C., Chang C., Huang C., Dong C., et al. (2021). Isolation and purification of brown algae fucoidan from sargassum siliquosum and the analysis of anti-lipogenesis activity. Biochem. Eng. J. 165, 107798. doi: 10.1016/j.bej.2020.107798
Keywords: seaweed, biorefinery, enzyme assisted extraction, techno-economics, multiproduct
Citation: Herrera Barragán JA, Olivieri G, Boboescu I, Eppink M, Wijffels R and Kazbar A (2022) Enzyme assisted extraction for seaweed multiproduct biorefinery: A techno-economic analysis. Front. Mar. Sci. 9:948086. doi: 10.3389/fmars.2022.948086
Received: 19 May 2022; Accepted: 08 August 2022;
Published: 02 September 2022.
Edited by:
Elena Ficara, Politecnico di Milano, ItalyReviewed by:
Wei Zhang, Marine Bioproducts Cooperative Research Centre, AustraliaCopyright © 2022 Herrera Barragán, Olivieri, Boboescu, Eppink, Wijffels and Kazbar. This is an open-access article distributed under the terms of the Creative Commons Attribution License (CC BY). The use, distribution or reproduction in other forums is permitted, provided the original author(s) and the copyright owner(s) are credited and that the original publication in this journal is cited, in accordance with accepted academic practice. No use, distribution or reproduction is permitted which does not comply with these terms.
*Correspondence: Antoinette Kazbar, QW50b2luZXR0ZS5rYXpiYXJAd3VyLm5s
†These authors share last authorship
Disclaimer: All claims expressed in this article are solely those of the authors and do not necessarily represent those of their affiliated organizations, or those of the publisher, the editors and the reviewers. Any product that may be evaluated in this article or claim that may be made by its manufacturer is not guaranteed or endorsed by the publisher.
Research integrity at Frontiers
Learn more about the work of our research integrity team to safeguard the quality of each article we publish.