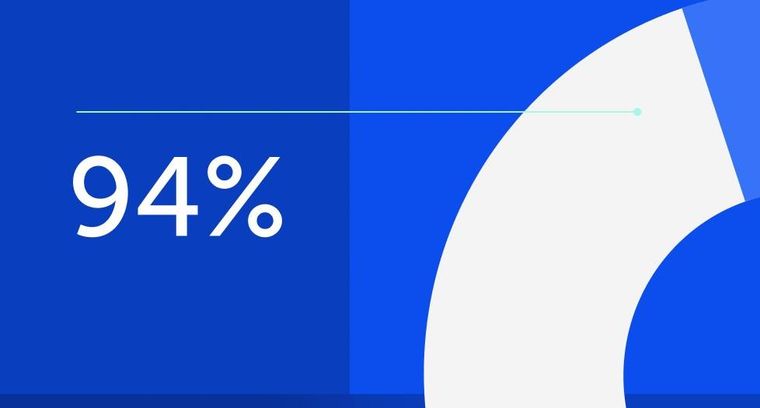
94% of researchers rate our articles as excellent or good
Learn more about the work of our research integrity team to safeguard the quality of each article we publish.
Find out more
ORIGINAL RESEARCH article
Front. Mar. Sci., 02 December 2021
Sec. Ocean Solutions
Volume 8 - 2021 | https://doi.org/10.3389/fmars.2021.761307
In response to the pervasive anthropogenic pollution of the ocean, this manuscript suggests the use of biodegradable elastomers in marine applications. The present study characterizes 25 samples of highly biodegradable polymers, obtained blending a base elastomer with natural fibers. Mechanical analysis and Scanning Electron Microscope imaging, reveal how base polymers behave differently depending on the plant fiber chosen, on the external forcing—exposure to water—and on the doses that constitute the final biocomposite. Results suggest that EcoflexTM 00-30 and EcoflexTM 00-50, mixed with potato starch, perform best mechanically, maintaining up to 70% of their maximum tensile strain. Moreover, early signs of degradation are visible on polysiloxane rubber blended with 50% vegetable fibers after 19 hours in distilled water. Analyses demonstrate that highly biodegradable elastomers are good candidates to satisfy the requirements of aquatic devices. Furthermore, the discussed materials can improve the dexterity and biodegradability of marine technology.
Nowadays reducing the carbon footprint has become a mandatory call for all the technological fields. Indeed, the Paris agreement states that signatory countries will have to take measures today in order to reach the net zero emissions goal set by 2050. Embracing this goal translates into numerous measures to change the way we produce energy, consume products and dispose of them. These measures regard industrial, domestic and scientific environments. In this study we will focus on how to reduce the carbon footprint of marine research (Net Zero Oceanographic Capability, 2021).
The boundaries of marine sciences expand through exploration and hence the need of new data (Levin et al., 2019), for this reason researchers continuously create and call for novel technology (Madin et al., 2019). In the last two decades, the scientific community investigated the realization of a sustained observational network (Garzoli et al., 2009), which encompasses innovative technology (Nassar et al., 2018; Shaikh et al., 2019; Aracri et al., 2021), increased spatial resolution of data logging platforms and integration of new autonomous systems. Despite the continuous technological evolution, some data platforms are never recovered, some fail at sea, others are destined to be lost in the water.
For instance, anchor parachutes, are routinely used to make the deployment of oceanographic moorings more gentle; highly biodegradable elastomers could already be employed to render them dissoluble in marine water. Also, biocomposites could be employed to build short term observations drifters, used to collect short term wind and current data and useful to validate coastal and lagoon models (Quattrocchi et al., 2021). Another example of sea platforms often lost at sea comes from animal based telemetry. In recent years, it increased exponentially, sustained, among other things, by reduction of manufacturing costs and miniaturization of novel devices (Harcourt et al., 2019). Marine scientists started to use marine animals tagging for data logging in the 1980s (Harcourt et al., 2019). This technique proved to be useful not only to study the behavior of marine mammals or other sea animals (Hooker and Boyd, 2003; Lear and Whitney, 2016; Treasure et al., 2017), but also to collect environmental data, such as pressure, salinity and temperature of the water (Treasure et al., 2017). Marine animal tagging is particularly handy in patches of the sea covered by ice (Treasure et al., 2017), which are out of reach for traditional measurement methods—tethered Conductivity Temperature Depth (CTD), Autonomous Underwater Vehicles (AUVs), Remote Operated Vehicles (ROVs), Gliders, Argo floats.
Perhaps the most appealing field for biodegradable materials is soft robotics, i.e., a field of robotics that raised significant interest among scientists in the last 20 years (Trivedi et al., 2008). Among many of the applications of soft robots there are offshore operations (Sayed et al., 2018, 2021) and ocean exploration (Aracri et al., 2021), which both entail a significant risk of losing the device performing the task. More specifically, elastomers such as EcoflexTM 00-30 are widely used in aquatic soft robotics (Giorgio-Serchi and Weymouth, 2017; Armanini et al., 2021; Bujard et al., 2021), because they have a density very close to that of water and an elasticity vaguely similar to that of living tissue. This last aspect is actually key to bio-inspiration, which often drives the design of soft robots. Examples of soft devices (Figure 1) that have been already deployed in the ocean are SoFi (Katzschmann et al., 2018), different kind of grippers, suitable for delicate sampling (Galloway et al., 2016; Phillips et al., 2018) and compliant sensory skin (Shaikh et al., 2019).
Figure 1. Real word deployment of soft systems, i.e., settings where highly biodegradable elastomers can be employed. The image shows two different designs of soft robotics grippers for delicate sampling (Galloway et al., 2016-top right- and Phillips et al., 2018 -bottom right-), compliant marine sensory skin (Nassar et al., 2018), an underwater soft fish robot (Katzschmann et al., 2018).
Beholding the pervasive pollution (Worm et al., 2017), of the world's ocean, it is inevitable to link the increasing number of deployed devices (Editorial, 2020) with the danger of aggravated contamination of the natural environment. The dilemma, arising from the contrast between the need of more oceanographic data and the need to reduce plastic pollution (Borja et al., 2020), made the research on biocomposites manufacturing (Bayer et al., 2014; Ceseracciu et al., 2015; Barron and Sparks, 2020; Lott et al., 2021) and transient electronics (Yin et al., 2014; Fu et al., 2015, 2016; Guna et al., 2016) thrive. Therefore, experimental projects contemplated bio-compatible materials for coral healing (Contardi et al., 2020), disposable soft robots (Rossiter et al., 2016, 2017) and observing platforms (Novelli et al., 2017), such as moorings (Pillsbury, 1993) and data retrieving autonomous systems (AOML Communications to Physical Oceanography, 2020), to reduce the economical and environmental cost of oceanographic cruises.
This study investigates the properties of soft biomaterials as substitutes of plastic components for devices meant to be left adrift at sea, which, with the call for increasing the deployments of autonomous platforms, is likely to grow.
The following sections describe the data and methods of our experiments to create highly biodegradable biocomposites. The article continues with the synthesis of the main results and the discussion. The conclusions derived from the experiments are at the end of the manuscript.
Biocomposite, as intended in this study, is a material resulting from the mixing of a base elastomer and a plant fiber. By creating and testing different kinds of biocomposites in the lab, we want to demonstrate that their microstructure insures a level of biodegradability higher than the base polymer used, and that their physical properties ensure a mechanical performance similar to the one of commonly used plastic in the marine environment.
To characterize the effect of natural fibers in elastomeric blends, we created samples with different ratios of vegetable powder and elastomer. We selected two base polymers widely used in soft robotics: E43 and EcoflexTM.
E43 (silicone/polysiloxane rubber) is a mono-component elastomer. EcoflexTM (Polybutylene Adipate Terephthalate- PBAT-) is a bi-component elastomer. As vegetable ingredients we used potato starch, produced by Sigma-Aldrich1 and cocoa powder. If needed, we added heptane as a solvent to help amalgamating the mixture (starch + elastomer). Some samples were created using pre-treated potato starch, i.e., dried for 2 h at 50 degrees E43PPS50, E43PPS60, E50PPS60. The final blends database is synthesized in Table 1. Blends including cocoa powder easily stick to the Petri dish; to avoid it, we used Teflon coated containers.
After curing time, we selected two samples with different base polymers, E43 and EcoflexTM 00-10 (E43PS50 and E10PS50), both blended with potato starch, 50% concentration, and we immersed them in distilled water (MilliQ) at 50°C for 19 h (obtaining E43PS50W and E10PS50W), to observe any possible degradation happening in such time span. We then measured and cataloged the microscopic and mechanical properties of the materials.
We used the most significant and integer samples to acquire SEM (Scanning Electron Microscope) images (Table 1 superscriptSEM). For SEM imaging the samples have to be prepared to rest on small place holders, covered with carbon tape, to enhance conductivity. To obtain a clean cross section, the sample needs to be placed in liquid nitrogen, then snapped and placed on the carbon tape. We also placed top and bottom sides on the carbon tape. We covered the sides of the samples on the carbon tape with silver paste to improve conductivity. We used the sputter coater to cover the samples with gold powder. The main results are reported in Figures 2–4 and discussed in the next section.
Figure 2. Different levels of dispersion between the medium and the potato starch particles. Top row-E43PPS50. Middle row-E43PS50. Bottom row-E43PS50W.
Figure 3. Top row of images shows the flat surface of pure E43. The middle row shows the presence of some flaking and cracks on the flat surface of sample E43PS50. The bottom row presents the flat surface (that has been immersed in water) of sample E43PS50W with bigger and frequent flaking.
Figure 4. Sample E43PS50W. Observed cracks and caves ascribable to the degradation of the material in the water.
To prepare the 19 samples (Table 1 in bold) for tensile tests, we cut a dog-bone shaped specimen. The strain rate of the tensile test was 50 mm/min and we followed the ASTM D 882 method. The test consists in applying a controlled tensile force on every sample and register the modulus, maximum load, tensile stress at yield, tensile strain at yield, tensile stress at maximum load, the main results are graphically reported in Figure 5 and Table 2.
Figure 5. Stress-strain curves of the specimen in bold in Table 1. EcoflexTM 00-30 and EcoflexTM 00-50, 50% blends maintain most of tensile strain resistance of the pure elastomers.
E10PS70 presented sparse visible crystals homogeneously distributed in the sample. E30PS70 instead had ramified crystals. E50PS70 was very brittle with dense ramifications. E43PS70 showed little sparse crystals. E43PS60 had sparse little dot-crystals. Also E43PPS60 displayed sparse little dot-crystals, even finer than E43PS60. E43PS50 showed sparse little dot-crystals, less frequent than E43PS60, but similar in size.
The cross section of sample E43PS50W clearly displayed dispersion between potato starch particles (~34.5μm diameter) and the medium (E43), see Figure 2. Also, the samples blended with pre-dried starch had finer conglomerates, ~15.6μm diameter, of starch visible in the cross section (Figure 2). Instead E43PS50 had lumps of starch which reached ~37μm diameter with an average of ~27μm. As noted in Stasiak et al. (2013) the potato starch produced by Sigma-Aldrich should be considered “wet”; pre-drying the starch in the oven likely removed the humidity in the powder and the bigger clumps disintegrated, allowing the starch to disperse in the medium with finer lumps. The surface on the submerged side of the sample had frequent flaking (Figure 3), 2 to 7 flakes, probably due to the degradation process in water. Samples that were not left in the water (E43PS50, E43PPS50) showed less flaking, 0 to 3 flakes, on the flat surfaces (view from above) (Figure 3). The flakes in E43PS50 are 21.7μm wide, 26.9μm long. The flakes in E43PPS50 reach up to 38.1μm width, 41.5μm length. E43PS50W presents ‘cave” structures, which are 29.4μm wide and 60.1μm long, probably the result of degradation happening in the water (Figure 4). All the materials containing starch displayed several cracks on both sides probably due to evaporation processes. The width of the cracks present in the samples E43PS50 and E43PPS50 is similar, i.e., 0.7μm, sometimes 0.6μm for E43PPS50. E43PS50W instead had smaller cracks, 0.4μm wide, positioned at the base of those lumps of starch that had visible wrinkling at the attachment with the medium.
Observing the graphs emerges that E43 and EcoflexTM 00-10 are the materials most affected by the presence of plant fibers in the blend, which reduces their maximum tensile strain to 30% with respect to the pure base elastomer. In fact, in the E43 (EcoflexTM 00-10) case, the maximum tensile strain changes from 8.42 (12.77) mm to 2.68 (3.82) mm when blended with 50% potato starch powder. In the case of E43 the pre-dried potato starch did not seem to affect consistently the mechanical properties of the elastomers, i.e., with 50% concentration of starch the specimen broke slightly before the same blend with untreated potato starch. In the sample with 60% concentration of starch, the opposite happened. Instead, EcoflexTM 00-30 and EcoflexTM 00-50 showed better resistance to stress, even when blended with potato starch, which reduced their maximum tensile strain to 65–70%, with respect to the pure base elastomer. In EcoflexTM 00-30 (EcoflexTM 00-50), the maximum tensile strain changes form 11.77 (9.29) mm to 7.69 (6.55) mm when blended with 50% potato starch powder. The reduction of tensile strain for the samples containing potato starch has been observed also by Contardi et al. (2021). Their samples, created with the same technique had starch/E43 weight ratio of 60:40, similarly to our E43PS60 and E43PPS60. The biocomposites broke at 1.5 mm/mm in both studies. Moreover, their study demonstrated as 45% of the surface of the biocomposite began to degrade after 6 months at sea. Mechanical performances decrease gradually with the increase of potato starch in the blend, there is not such a dramatic loss of resistance to stress, as it happens instead in the E43 and EcoflexTM 00-10 specimens. The influence of the pre-dried potato starch on the mechanical performance of the material remains unclear. In the EcoflexTM 00-50 specimen the blend with pre-dried potato starch performed very poorly in comparison with the same blend with untreated starch (Figure 5).
The interface between a vegetable fiber and a polymer matrix is the transition zone where two materials combine mechanically, physically and/or chemically (Zhou et al., 2016). Plant fibers are naturally hydrophilic whilst polymers are hydrophobic rendering the two materials not compatible. Some of the techniques to improve the interface bonding include heat treatment to evaporate the water absorbed from the environment by the vegetable fiber, this would improve the bonding with the hydrophobic silicones. SEM images show indeed finer conglomerates, hence better blending at a microscopic level, mechanically the biocomposite E43PPS60 had an improved tensile strain (Extension) at Maximum Load [mm/mm] from 1.089 to 1.312. Cocoa powder is more hydrophobic than potato starch and contains between 8 and 26% of fat (Gibson and Newsham, 2018), rendering it hardly hydro-soluble. Therefore, the samples containing cocoa powder were amalgamated poorly and showed dense ramifications, making them hard to manipulate.
The more homogeneous and continuous is the blend the better the loads distribute across the matrix. Curves in Figure 5 are stress-strain curves of E43, EcoflexTM 00-10, ECOFLEXTM, 00-30 EcoflexTM 00-50. Elastomers often report J-shaped stress strain curves, resembling the same curves of biological material, e.g., skin, organ tissue, cartilage. This means that at a lower stress correspond to a higher elongation, but the more tensile force is exerted on the specimen the stiffer it becomes, until the rupture point. The j-shaped curves can be recognized in the pure elastomers. The stretching characteristics of the elastomeric network are not dominant in the case of the biocomposites (Ceseracciu et al., 2015). In fact the latter materials display a more linear behavior and a reduced rupture strain.
Bearing in mind the scope of our study, it is important to consider that in soft robotics, bioinspiration is an important component, hence the capability of a material to mimic the movement of an animal tissue is important to reproduce locomotion techniques, to ensure resilience and allow dexterity, for instance in the marine environment. For this reason elastomers such as E43 and EcoflexTM are often employed in soft robotics. The Young's modulus of chosen elastomers is in the same order of magnitude of the one of biological materials, i.e., 105−106 Pa (Rus and Tolley, 2015).
Another important characteristic for aquatic soft robots is buoyancy. The potato starch that we used had a moisture content equal to 18–21%. According to Stasiak et al. (2013) wet (~20% moisture content) packed potato starch has a density equal to 621 Kg/m3, dropping to 283 Kg/m3 for aerated powders. The density of EcoflexTM 00-30 (00-50, 00-10) is equal to 1091.47 Kg/m3 (1094.31 Kg/m3, 1063.12 Kg/m3)2, see Figure 6. The starch lowers the density of the resulting biocomposite, creating a bigger buoyancy margin, which would play to the advantage of a richer payload.
Figure 6. Variation of density in the elastomers depending from the percentage of starch. The more starch is in the blend the lower is the density of the resulting material. The inset shows the density of the pure elastomers vs. their shore hardness, i.e., resistance to indentation.
During the creation of the samples, it became clear that potato starch was better than cocoa powder to create highly biodegradable elastomers. The specimen that contained cocoa were very brittle and too frail to handle. Therefore, we did not include those samples in the SEM imaging or the mechanical tests.
Visually the elastomer-potato starch blends showed little crystals which increased in number and size the more percentage of the blend was constituted by starch. Eventually these crystals became ramifications, e.g., E30PS70, which indicated a very brittle sample.
At the microscopical level, dispersion between the medium and the vegetable fibers is clearly visible. Pre-drying the potato starch leads to a blend with finer conglomerates (~15.6μm instead of ~37μm diameter).
The samples that were in contact with distilled water for 19 h displayed early signs of degradation, i.e., frequent flaking (up to 7) and cracking on the flat surface (Figure 3), and cave structures (~60.1μm length) and fractures in the cross section (Figure 4). E43PS50W showed visible wrinkling at the base of the starch lump with small cracks (~0.4μm width).
Mechanical tests revealed that, among the four elastomers that we chose as basis for our experiments (E43, EcoflexTM 00-10, EcoflexTM 00-30, EcoflexTM 00-50), EcoflexTM 00-30 and EcoflexTM 00-50 best maintained the mechanical properties even when blended with 50% potato starch. The maximum tensile strain decreased to 30% in E43 and EcoflexTM 00-10, but only to 65-70% in EcoflexTM 00-30 and EcoflexTM 00-50.
Although silicones are not found in nature, studies demonstrate that their degradation is harmless for the environment, yielding benign silica, water, and CO2 (Graiver et al., 2003). Polysiloxane is more sensitive to hydrolysis and abiotic degradation, whilst PBAT is subject to biodegradation and shows excellent mechanical properties (Jian et al., 2020). Also, the Executive Summary (Brandt et al., 2012) on Silicon-Chemistry Carbon Balance states that the use of silicones in Europe, USA and Japan led to a reduction of green house emissions of 54 tons of CO2. Highly biodegradable elastomers can improve the bio-compatibility of elastomers in order to reduce the carbon footprint of marine sciences. Their mechanical and physical properties well compare to those of commonly used elastomers, e.g., resilience, easy manufacturing, versatility. Nevertheless, their environmental impact can be minimized especially for devices that are likely to be lost, or are meant to be left at sea.
This manuscript shows that a 50% vegetable fiber presence in the blend led to visible degradation after 19 h in distilled water. Moreover, potato starch preserves the mechanical properties of the base elastomer better than cocoa powder, which, instead, made the samples very fragile and challenging to handle. Not all base elastomers maintain their resistance to strain when blended with vegetable fibers. Nevertheless, EcoflexTM 00-30 and EcoflexTM 00-50, 50% blends, reduced their maximum tensile strain to 70% of their capacity, making them good candidates for in-situ experiments.
Further analyses could include biodegradability assessment of a material, e.g., Biochemical Oxygen Demand (BOD Test): carried out immersing the material in water (e.g., Mediterranean Water) and measuring the Dissolved Organic Carbon (DOC) and CO2 content in the air gap in the bottle to evaluate respiration processes in the sample. Nevertheless, BOD tests can not reproduce faithfully the environmental conditions that a given instrument is going to encounter in his life at sea. These conditions are hard to recreate in a laboratory, given the lack of data in the deep sea, such as the variability rates, pressure, salinity, currents, microbiological interaction, light penetration, etc... For this reason real world studies, such as that conducted by Contardi et al. are extremely valuable.
In the real world highly biodegradable elastomers can be already employed to manufacture anchor parachutes and marine sensory skin, as well as short term observations drifters, used to tune the wind settings in coastal and lagoon models. Moreover, the lower density of highly biodegradable elastomers would leave space for a larger payload.
When the soft materials play an important role in the propulsion of a device, the change in density given by highly biodegradable materials can not be neglected. This might constitute a limitation to their use. Moreover, the lifetime of biodegradable instruments would be inevitably shorter than that of traditional observing platforms. Rendering the use of highly biodegradable elastomers more suitable for short term observations or as part of a spatially mindful deployment.
Biocomposities can already be used in traditional oceanographic platforms. However, international exchange the recent employment of soft robotics in the marine environment disclosed a whole new realm, where bio-elastomers can annihilate the footprint of marine observations.
The original contributions presented in the study are included in the article/Supplementary Material, further inquiries can be directed to the corresponding author.
SA organized the international exchange between the University of Edinburgh and the Italian Institute of Technology, designed and performed the experiments, and wrote the present manuscript. MC performed the SEM imaging and conceived the water degradation experiment. MZ performed the mechanical tests. IB organized the international exchange and instructed SA on how to make biodegradable elastomers. FG-S helped with the writing and editing of the manuscript. AS led the acquisition of the financial support for the project leading to this publication. All authors contributed to the article and approved the submitted version.
The authors acknowledge financial support from the EPSRC ORCA Hub (EP/R026173/1). SA also acknowledges the financial support from the National Research Council of Italy to fund the Short Term Mobility Program 2021 -prot. n. 49963-, which enabled, among other things, the writing of this study.
The authors declare that the research was conducted in the absence of any commercial or financial relationships that could be construed as a potential conflict of interest.
All claims expressed in this article are solely those of the authors and do not necessarily represent those of their affiliated organizations, or those of the publisher, the editors and the reviewers. Any product that may be evaluated in this article, or claim that may be made by its manufacturer, is not guaranteed or endorsed by the publisher.
We want to acknowledge the Soft Systems Research Group of the School of Engineering, University of Edinburgh for the welcoming and supporting environment. Similarly we are thankful to IIT - Istituto Italiano di Tecnologia - that welcomed the exchange with the University of Edinburgh and hosted all the experiments. We also wish to acknowledge the support of Dr. Chiara Gambardella during the application of the Short Mobility Program, which led to the writing of this manuscript. Many thanks to Mr. Filippo Castelli for the advice about interface between matrix-fiber during the reviews. We are grateful to the reviewers who dedicated their time to improve our manuscript.
The Supplementary Material for this article can be found online at: https://www.frontiersin.org/articles/10.3389/fmars.2021.761307/full#supplementary-material
1. ^https://www.sigmaaldrich.com/IT/en/sds/sial/s4251
2. ^https://www.smooth-on.com/tb/files/ECOFLEX_SERIES_TB.pdf
AOML Communications to Physical Oceanography (2020). Pods away! New Autonomous Data Pods Will Provide Low-Cost, Reliable Data Retrieval. NOAA Blog.
Aracri, S., Giorgio-Serchi, F., Suaria, G., Sayed, M. E., Nemitz, M. P., Mahon, S., et al. (2021). Soft robots for ocean exploration and offshore operations: a perspective. Soft Robot. 1–15. doi: 10.1089/soro.2020.0011
Armanini, C., Farman, M., Calisti, M., Giorgio-Serchi, F., Stefanini, C., and Renda, F. (2021). “Flagellate underwater robotics at macroscale: design, modeling, and characterization,” in IEEE Transactions on Robotics, 1–17.
Barron, A., and Sparks, T. D. (2020). Commercial marine-degradable polymers for flexible packaging. iScience 23, 101353. doi: 10.1016/j.isci.2020.101353
Bayer, I. S., Guzman-Puyol, S., Heredia-Guerrero, J. A., Ceseracciu, L., Pignatelli, F., Ruffilli, R., et al. (2014). Direct transformation of edible vegetable waste into bioplastics. Am. Chem. Soc. Macromol. 47, 5135–5143. doi: 10.1021/ma5008557
Borja, A., Andersen, J. H., Arvanitidis, C. D., Basset, A., Buhl-Mortensen, L., Carvalho, S., et al. (2020). Past and future grand challenges in marine ecosystem ecology. Front. Mar. Sci. 7:362. doi: 10.3389/fmars.2020.00362
Brandt, B., Bernd, E., Pilz, H., Hadzhiyska, D., and Seizov, P. (2012). Executive Summary. Silicon-Chemistry Carbon Balance. An Assessment of Greenhouse Gas Emissions and Reductions. Technical report.
Bujard, T., Giorgio-Serchi, F., and Weymouth, G. D. (2021). A resonant squid-inspired robot unlocks biological propulsive efficiency. Sci. Robot. 6:eabd2971. doi: 10.1126/scirobotics.abd2971
Ceseracciu, L., Heredia-Guerrero, J. A., Dante, S., Athanassiou, A., and Bayer, I. S. (2015). Robust and biodegradable elastomers based on corn starch and polydimethylsiloxane (PDMS). Am. Chem. Soc. Appl. Mater. Interfaces 7, 3742–3753. doi: 10.1021/am508515z
Contardi, M., Montano, S., Galli, P., Mazzon, G., Mah'd Moh'd Ayyoub, A., Seveso, D., et al. (2021). Marine fouling characteristics of biocomposites in a coral reef ecosystem. Adv. Sustain. Syst. 5, 2100089. doi: 10.1002/adsu.202100089
Contardi, M., Montano, S., Liguori, G., Heredia-Guerrero, J. A., Galli, P., Athanassiou, A., et al. (2020). Treatment of coral wounds by combining an antiseptic bilayer film and an injectable antioxidant biopolymer. Sci. Rep. 10, 988. doi: 10.1038/s41598-020-57980-1
Fu, K., Liu, Z., Yao, Y., Wang, Z., Zhao, B., Luo, W., et al. (2015). Transient rechargeable batteries triggered by cascade reactions. Nano Lett. 15, 4664–4671. doi: 10.1021/acs.nanolett.5b01451
Fu, K. K., Wang, Z., Dai, J., Carter, M., and Hu, L. (2016). Transient electronics: materials and devices. Chem. Mater. 28, 3527–3539. doi: 10.1021/acs.chemmater.5b04931
Galloway, K. C., Becker, K. P., Phillips, B., Kirby, J., Licht, S., Tchernov, D., et al. (2016). Soft robotic grippers for biological sampling on deep reefs. Soft Robot. 3, 23–33. doi: 10.1089/soro.2015.0019
Garzoli, S. L., Boebel, O., Bryden, H., Fine, R. A., Fukasawa, M., Gladyshev, S., et al. (2009). “Progressing towards global sustained deep ocean observations,” in Proceedings of OceanObs'09: Sustained Ocean Observations and Information for Society, Vol. 2, eds J. Hall, D, Harrison, and D. Stammer (Venice: European Space Agency WPP-306).
Gibson, M., and Newsham, P. (2018). “Chapter 17-chocolate/cacao,” in Food Science and the Culinary Arts, eds M. Gibson and P. Newsham (Barcelona: Academic Press), 341–352.
Giorgio-Serchi, F., and Weymouth, G. D. (2017). “Underwater soft robotics, the benefit of body-shape variations in aquatic propulsion,” in Soft Robotics: Trends, Applications and Challenges, eds C. Laschi, J, Rossiter, F, Iida, M, Cianchetti, and L. Margheri (Cham: Springer International Publishing), 37–46.
Graiver, D., Farminer, K. W., and Narayan, R. (2003). A review of the fate and effects of silicones in the environment. J. Polym. Environ. 11, 129–136. doi: 10.1023/A:1026056129717
Guna, V. K., Murugesan, G., Basavarajaiah, B. H., Ilangovan, M., Olivera Sharon Krishna, V., and Reddy, N. (2016). Plant-based completely biodegradable printed circuit boards. IEEE Trans. Electron Devices 63, 4893–4898. doi: 10.1109/TED.2016.2619983
Harcourt, R., Sequeira, A. M., Zhang, X., Roquet, F., Komatsu, K., Heupel, M., et al. (2019). Animal-borne telemetry: an integral component of the ocean observing toolkit. Front. Mar. Sci. 6:326. doi: 10.3389/fmars.2019.00326
Hooker, S. K., and Boyd, I. L. (2003). Salinity sensors on seals: use of marine predators to carry ctd data loggers. Deep Sea Res. I Oceanogr. Res. Pap. 50, 927–939. doi: 10.1016/S0967-0637(03)00055-4
Jian, J., Xiangbin, Z., and Xianbo, H. (2020). An overview on synthesis, properties and applications of poly(butylene-adipate-co-terephthalate)–PBAT. Adv. Indust. Eng. Poly. Res. 3, 19–26. doi: 10.1016/j.aiepr.2020.01.001
Katzschmann, R. K., DelPreto, J., MacCurdy, R., and Rus, D. (2018). Exploration of underwater life with an acoustically controlled soft robotic fish. Sci. Robot. 3:eaar3449. doi: 10.1126/scirobotics.aar3449
Lear, K. O., and Whitney, N. M. (2016). Bringing data to the surface: recovering data loggers for large sample sizes from marine vertebrates. Anim. Biotelemetry 4, 1–10. doi: 10.1186/s40317-016-0105-8
Levin, L. A., Bett, B. J., Gates, A. R., Heimbach, P., Howe, B. M., Janssen, F., et al. (2019). Global observing needs in the deep ocean. Front. Mar. Sci. 6:241. doi: 10.3389/fmars.2019.00241
Lott, C., Eich, A., Makarow, D., Unger, B., van Eekert, M., Schuman, E., et al. (2021). Half-life of biodegradable plastics in the marine environment depends on material, habitat, and climate zone. Front. Mar. Sci. 8:426. doi: 10.3389/fmars.2021.662074
Madin, E. M. P., Darling, E. S., and Hardt, M. J. (2019). Emerging technologies and coral reef conservation: opportunities, challenges, and moving forward. Front. Mar. Sci. 6:727. doi: 10.3389/fmars.2019.00727
Nassar, J. M., Khan, S. M., Velling, S. J., Diaz-Gaxiola, A., Shaikh, S. F., Geraldi, N. R., et al. (2018). Compliant lightweight non-invasive standalone “Marine Skin” tagging system. npj Flexible Electron. 2, 13. doi: 10.1038/s41528-018-0025-1
Net Zero Oceanographic Capability (2021). NZOC Workshop Work Package 1. In Future Science Need. Available online at: https://projects.noc.ac.uk/nzoc/work-packages/wp1-future-science-need (accessed January 1, 2021).
Novelli, G., Guigand, C. M., Cousin, C., Ryan, E. H., Laxague, N., athan, J. M., et al. (2017). A biodegradable surface drifter for ocean sampling on a massive scale. J. Atmos. Oceanic Technol. 34, 2509–2532. doi: 10.1175/JTECH-D-17-0055.1
Phillips, B. T., Becker, K. P., Kurumaya, S., Galloway, K. C., Whittredge, G., Vogt, D. M., et al. (2018). A dexterous, glove-based teleoperable low-power soft robotic arm for delicate deep-sea biological exploration. Sci. Rep. 8:14779. doi: 10.1038/s41598-018-33138-y
Quattrocchi, G., Simeone, S., Pes, A., Sorgente, R., Ribotti, A., and Cucco, A. (2021). An operational numerical system for oil stranding risk assessment in a high-density vessel traffic area. Front. Mar. Sci. 8:133. doi: 10.3389/fmars.2021.585396
Rossiter, J., Winfield, J., and Ieropoulos, I. (2016). Here today, gone tomorrow: biodegradable soft robots. Electroactive Poly. Actuators Devices (Livorno), 9798:97981S. doi: 10.1117/12.2220611
Rossiter, J., Winfield, J., and Ieropoulos, I. (2017). “Eating, drinking, living, dying and decaying soft robots,” in Soft Robotics: Trends, Applications and Challenges, Biosystems and Biorobotics Book Series, Vol. 17, eds C. Laschi, J. Rossiter, F, Iida, M, Cianchetti, and L. Margheri (Springer International Publishing), 95–101.
Rus, D., and Tolley, M. T. (2015). Design, fabrication and control of soft robots. Nature 521, 467–475. doi: 10.1038/nature14543
Sayed, M. E., Nemitz, M. P., Aracri, S., McConnell, A. C., McKenzie, R. M., and Stokes, A. A. (2018). The limpet: a ros-enabled multi-sensing platform for the orca hub. Sensors 18:3487. doi: 10.3390/s18103487
Sayed, M. E., Roberts, J. O., McKenzie, R. M., Aracri, S., Buchoux, A., and Stokes, A. A. (2021). Limpet ii: a modular, untethered soft robot. Soft Robot. 8, 319–339. doi: 10.1089/soro.2019.0161
Shaikh, S. F., Mazo-Mantilla, H. F., Qaiser, N., Khan, S. M., Nassar, J. M., Geraldi, N. R., et al. (2019). Noninvasive featherlight wearable compliant “marine skin”: standalone multisensory system for deep-sea environmental monitoring. Small 15, 1804385. doi: 10.1002/smll.201804385
Stasiak, M., Molenda, M., Opaliki, I., and Baszczak, W. (2013). Mechanical properties of native maize, wheat, and potato starches. Czech J. Food Sci. 31, 347–354. doi: 10.17221/348/2012-CJFS
Treasure, A., Roquet, F., Ansorge, I., Bester, M., Boehme, L., Bornemann, H., et al. (2017). Marine mammals exploring the oceans pole to pole: a review of the MEOP consortium. Oceanography 30, 132–138. doi: 10.5670/oceanog.2017.234
Trivedi, D., Rahn, C. D., Kier, W. M., and Walker, I. D. (2008). Soft robotics: biological inspiration, state of the art, and future research. Appl. Bionics Biomech. 5, 99–117. doi: 10.1155/2008/520417
Worm, B., Lotze, H. K., Jubinville, I., Wilcox, C., and Jambeck, J. (2017). Plastic as a persistent marine pollutant. Annu. Rev. Environ. Resour. 42, 1–26. doi: 10.1146/annurev-environ-102016-060700
Yin, L., Huang, X., Xu, H., Zhang, Y., Lam, J., Cheng, J., et al. (2014). Materials, designs, and operational characteristics for fully biodegradable primary batteries. Adv. Mater. 26, 3879–3884. doi: 10.1002/adma.201306304
Keywords: bioplastic, elastomers, marine observation network, sustainable marine science, soft robots, natural fiber-reinforced composites, biocomposites
Citation: Aracri S, Contardi M, Bayer IS, Zahid M, Giorgio-Serchi F and Stokes AA (2021) Propaedeutic Study of Biocomposites Obtained With Natural Fibers for Oceanographic Observing Platforms. Front. Mar. Sci. 8:761307. doi: 10.3389/fmars.2021.761307
Received: 19 August 2021; Accepted: 10 November 2021;
Published: 02 December 2021.
Edited by:
Wei-Bo Chen, National Science and Technology Center for Disaster Reduction (NCDR), TaiwanReviewed by:
Andri Andriyana, University of Malaya, MalaysiaCopyright © 2021 Aracri, Contardi, Bayer, Zahid, Giorgio-Serchi and Stokes. This is an open-access article distributed under the terms of the Creative Commons Attribution License (CC BY). The use, distribution or reproduction in other forums is permitted, provided the original author(s) and the copyright owner(s) are credited and that the original publication in this journal is cited, in accordance with accepted academic practice. No use, distribution or reproduction is permitted which does not comply with these terms.
*Correspondence: Simona Aracri, c2ltb25hLmFyYWNyaUBjbnIuaXQ=
Disclaimer: All claims expressed in this article are solely those of the authors and do not necessarily represent those of their affiliated organizations, or those of the publisher, the editors and the reviewers. Any product that may be evaluated in this article or claim that may be made by its manufacturer is not guaranteed or endorsed by the publisher.
Research integrity at Frontiers
Learn more about the work of our research integrity team to safeguard the quality of each article we publish.