- 1Department of Environment and New Resources, SINTEF Ocean, Trondheim, Norway
- 2Department of Engineering Cybernetics, Norwegian University of Science and Technology (NTNU), Trondheim, Norway
In order to industrialize macroalgal cultivation in Norway, new automated methods and solutions for seeding, deployment and harvesting need to be developed. Today's solutions are time and resource demanding, still yielding volumes nationally in the range of 100–200 tons per year in total (not including wild harvest), while the potential is in the megaton range. Standardization of equipment and automation can be one way to upscale production. Here we present results from a design study of a module-based solution for industrial cultivation, with specific solutions for spinning of thin seedling strings onto longlines, and a robotic module for interaction with the submerged farm at deployment and harvest. A reduced-scale physical prototype of the farm concept with the robot has been built for testing of deployment and harvesting techniques. The concept has been named SPOKe: Standardized Production of Kelp.
1. Introduction
Cultivation of the oceans is required to meet demands for food, animal and fish feed, materials and energy for a growing global population. Norway, with one of the world's longest temperate and productive coastlines, can take a leading role. Norway has six times more ocean than land area, making the ocean one of Norway's greatest natural resources. It is already exploited extensively through oil and gas production and farming of Atlantic salmon, but despite having a significant economic potential (Olafsen et al., 2012), the volume of seaweed cultivation is small. Therefore, the Norwegian strategy for research and development in the marine sector has recommended further development and industrialization of seaweed cultivation and harvest (HAV 211).
Exploitation of wild seaweed resources has a long tradition in Norway (largely Laminaria hyperborea and Ascophyllum nodosum; Meland and Rebours, 2012). Early uses were as manure, feed and food, and is believed to go back to the first settlements in Norway. During the nineteenth century, export of potash increased from 1,500 to 6,000 tons, produced from 150,000 tons of seaweed (Meland and Rebours, 2012). Today, the list of potential uses range from biogas production, salmon feed, human consumption (raw, as spices and ingredients) to cosmetics and medical products. The harvested areas are subject to regulations and periodic following, and it is recognized that the growing demands of the industry can not be satisfied solely from the wild (Stévant et al., 2017). Biomass availability can also suffer great variations (Bell et al., 2015). Over-harvesting of seaweed in other countries has already shown devastating consequences 2 (Buschmann et al., 2017); all reasons to call attention to development of efficient, sustainable methods for cultivation.
Kim et al. (2017) point to several challenges for seaweed cultivation in the western world, despite significant development in the last decades. Among these are new engineering solutions, autonomous and robotic technologies and advanced sensing and monitoring techniques. Also, in their perspective article on seaweed and climate change mitigation Duarte et al. (2017) state that the current technology for seaweed aquaculture is based on simple structures and is limited to relatively sheltered waters, restricting the available area for the industry. The Norwegian coastline is vast, and comprises several temperature ranges and coastal and offshore areas, some of which are very high in nutrients (Broch et al., 2019). Macroalgae, being phototrophic organisms, naturally inhabit shallow depths. The available ocean volume for seaweed production may therefore be significantly increased if deeper waters can be utilized.
Profitability is an obvious demand if automated farms are to be realized. van den Burg et al. (2016) assessed offshore production of seaweed in the North Sea. The study found that a 300% increase in estimated revenue, all other things being equal, would be needed for the cultivation to be economically feasible. Technical innovation was suggested as one way to reduce costs. Today, seaweed farms are designed intuitively, usually for smaller scales and with manual handling in mind. Retrofitting of automation processes to such designs is hard, as the basic structure is not suitable for automation. Until now, biological concerns have been in focus for production. In order to automate, the simplest possible solutions should be sought. Standardization is a natural step following simplification, allowing for standardized equipment and cost reductions, and facilitating modularity and redundancy of production modules and equipment. In this study, a seaweed cultivation farm is designed with the focus on automation, standardized solutions and modular design, fit for offshore waters. The concept is called SPOKe: Standardized Production of Kelp. Several aspects of the concept will be discussed. An overview of some of the details are given in Figure 1.
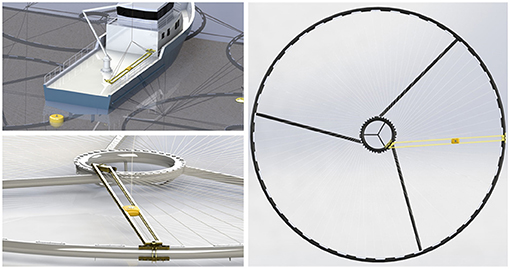
Figure 1. An overview of some of the details of the Standardized Production of Kelp (SPOKe) concept. (Top left) Service vessel launches gantry robot on to submerged modules at the seaweed farm. (Bottom left) Gantry robot attached to module, applying string. (Right) SPOKe module with tool attached. Illustrations from the VR simulation.
1.1. State of the Art
The biology and environmental interactions involved in seaweed cultivation are widely treated in the literature. However, scientific publications covering cultivation technology for seaweeds are few. Ask and Azanza (2002) reviewed cultivation status and production systems for eucheumatoid species, a group of red seaweeds, and found that “no true advance have taken place in commercial eucheumatoid farming in over a decade.” From 15 listed methods, only four were in use at the time of the study. Automation was not mentioned. In a more update review, Kim et al. (2017) pointed at the necessity for new designs and approaches to macroalgal cultivation, suitable also for offshore conditions. Buck and Buchholz (2004) presented a “ring carrier” cultivation system for open ocean macroalgal cultivation, which was shown to have high resistance to rough weather conditions and being easy to handle for farmers. However, harvesting was still done manually after towing the modules to shore and lifting by crane, or using divers. Bak et al. (2018) developed and tested an offshore long-line cultivation rig on the Faroe Islands, but focused on re-seeding and economic profitability, not automation. In fact, the developed cultivation rig was constructed using no specially designed parts, but off-the-shelf equipment designed for the fishery, aquaculture and offshore industry. The study, however, concluded with innovation being required to reduce operational costs and manpower. Titlyanov and Titlyanova (2010) presented an overview of the state of the art in global seaweed cultivation, including both intensive and extensive production methods. They reported on a variety of methods, but none of these utilize automation.
An overview of part of the Chinese seaweed industry was given by Su et al. (2017), who presented large-scale hatchery production of the seaweed Saccharina japonica in China, “including pre-treatment of parental plants, control of spore release, and control and adjustment of solar irradiance and temperature at different developmental stages of the plants as well as the nutrient supply regime over the entire course.” Zhang et al. (2017) is another Chinese paper which described a development of a mechanized harvesting machine, designed for the traditional floating raft seaweed farms.
A cultivation protocol for sugar kelp was given by Forbord et al. (2012) who described seedling production and sea cultivation of sugar kelp on long-lines, although production technology was not covered in detail. This protocol has been further developed and published as a book chapter (Forbord et al., 2018).
In the following, we give some examples of modern production systems used by commercial companies.
Seaweed Energy Solutions (SES) is based in Trondheim and at Frøya off the coast of Mid-Norway. Their production consists mainly of horizontal carrier ropes, at shallow depths. In 2017 they had a production of approximately 30 metric ton per hectare, and an average of 1 meter carrier rope per square meter (Jon Funderud, pers. comm.). SES has also developed a 3D substrate (Figure 2), but this substrate is currently not utilized. Figure 3 (left) shows one of their production sites off the coast of Mid-Norway.
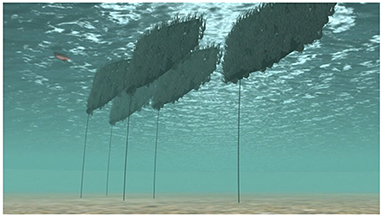
Figure 2. A patented 2D sheet, developed by Seaweed Energy Solutions for seaweed cultivation in exposed waters (image from www.theexplorer.no/solutions/industrial-scale-offshore-seaweed-cultivation/). Image reproduced with permission.
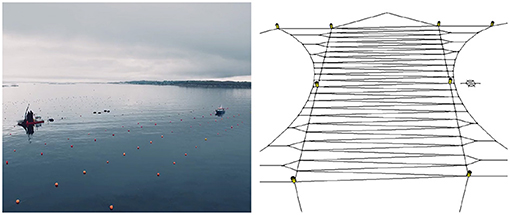
Figure 3. (Left) Seaweed Energy Solutions (SES) production site (Photo: SES). (Right) Buland 10 system used by Seaweed from Norway (image from vaerlandetfiskeredskap.no). Images are reproduced with permission.
Seaweed from Norway is a company based in Bulandet on the west coast of Norway, cultivating S. latissima and Alaria esculenta for human consumption. Seaweed from Norway has in collaboration with the company Værlandet fiskeredskap developed the cultivation system Buland 10 (Figure 3, right). This system has a cultivation area of 1 hectare and a total of 2,500 m of carrier rope. The system consists of horizontal carrier ropes in tension by an external rope rig or frame system. The system can be expanded by joining multiple modules together. This system is to our knowledge the only system commercially available, ready-made for shipment to customers.
The Norwegian project Seaweed vessel 2020 on development of a large-scale, specialized seaweed cultivation vessel has been finished in a collaboration between several industry partners. The vessel, still on the drawing board, is intended to be used in all stages of the cultivation; from installation of the farm facilities to harvesting and transport of biomass. Such a vessel makes the interaction of remote sites in offshore regions possible, and fits in the design-concept proposed in this paper.
AT-sea/SIOEN Algaesheet is a spin-off from the EU-project AT-Sea and is produced by the Belgian company SIOEN. The system consists of 10 × 3.2 m sheets connected to form a 100 m long unit3. The system has been reported to yield up to 14 kg/m2 of Saccharina latissima on winter crops on the coast of Ireland. At-Sea, now named AtSeaNova, is a Belgium-based company offering turnkey solutions for seaweed farms. In late January 2020, they introduced a product called the SeaHarvester I which mechanizes the cultivation processes of seeding, harvesting and cleaning, for both 2D substrata and long-lines. AtSeaNova also offer solutions for direct seeding for brown and green seaweeds, using an algae binder that glues the juveniles to the cultivation substrate (Kerrison et al., 2020). Solutions for direct seeding are also offered by the Dutch company Hortimare. The combination of direct seeding and automated cultivation is potentially a very potent one, and although the SPOKe concept is not restricted to specific processes, the most efficient methods available should be considered.
1.2. Objectives
The aim of this study was to investigate and propose automation concepts for industrial scale cultivation of seaweed. In order to limit the scope of the task we focused on S. latissima, as it is one of the most common species for cultivation in Norway. We also limited the scope to rope as substrate. In the following sections we outline the design criteria applied, the design choices and their rationale, and the automation techniques applied in the concept.
2. Materials and Methods
2.1. Design Criteria
We have applied five design criteria in the development of the concept:
2.1.1. Suitability for Automation
Automation is a key pre-requisite for Norway to develop large-scale macroalgal cultivation, as labor comes with higher costs compared with many other countries. To be able to utilize also off-shore areas, a robust farm design with minimal demand for on-site supervision is required. As many steps as possible in the cultivation process (deployment and harvesting especially) should be automated. Monitoring of growth and the surrounding environment is a part of an automated cultivation system; such monitoring is needed to evaluate and optimize the production, and to ensure that deployment and harvesting is initiated under the right conditions.
2.1.2. Area Efficiency
Macroalgal cultivation is area quota based in Norway. Hence, it is important to get as high a yield per hectare as possible. Area efficiency should be considered along with efficient farm interaction, with the design allowing efficient handling of the farm during deployment, daily operation and harvesting. One hectare may yield up to 220 ton biomass due to nutrient content, depending on localization (Sanderson et al., 2012). The average production today is around 7–20 ton per hectare (Broch et al., 2019), which implies that there is a potential for significantly more area effective production. A new cultivation system should be able to utilize more of the potential.
2.1.3. Light Availability
Macroalgae capture sunlight through photosynthesis to produce chemical energy. Photosynthetically active radiation (PAR; unit μmol m−2s−1) is a measure of the availability of light in the wavelength spectrum used by primary producers. The rate of photosynthesis increases with PAR irradiance, until a saturation level where further increase in irradiance will not significantly affect the growth. It has been estimated that the irradiance for maximal photosynthetic rate for S. latissima is λmin = 90 μmol m−2 s−1 (Broch et al., 2013). In the evaluation of light utilization in section 2.2.1, this value will be used as an estimate of the lower PAR limit for saturation.
2.1.4. Durability/reliability
A new concept should be durable in order to withstand off-shore conditions. Experience from the salmon farming industry should be taken into account, as modern, commercial fish cages are an extensively tested technology, typically constructed in HDPE (High Density Polyethylene) polymer. HDPE has high strength, is not affected by corrosion and handles the hydrodynamic strains well. This makes it an ideal choice of material for a macroalgae cultivation system, and it may even be possible to re-use HDPE rings from the salmon farming industry.
2.1.5. Scalability
The new cultivation concept should be easily upscaled to utilize large production areas. This property is closely linked to standardization and modularity which reduces the need for site-specific farm design, and allows for redundancy. Equipment used on one unit at one location is applicable at another, and may be shared between farms and companies.
2.2. Design Choices
2.2.1. Module Shape
Two geometric module shapes of the farm are considered in detail in the following; cylindrical and frustum. Right-angled shapes are not taken into consideration. Although area efficient, these shapes have severe disadvantages when it comes to mechanical strength. A stable and predictable geometrical shape is a crucial foundation for automation of the farm. The additional tools made to connect and interact with the modules can be simplified if the modules are uniform. Circular shapes solve both these aspects; having a high mechanical strength and mechanical integrity. The circular form may be utilized in two or three dimensions; as a disc or a frustum. The frustum is constructed of two circles, axially separated with different diameters (Figure 4), and the angled area between the circles forming the cultivation area.
Both geometries render the use of a one-dimensional substrate, such as rope, in a 2D or 3D configuration for optimal light exposure possible, whilst still leaving the substrate one-dimensional for easy harvesting. The angles of the conical frustum sides can be optimized for maximum light exposure. In order to radiate the whole surface and not leave parts of it in shadow, such a solution needs to include a way of rotating the module, complicating the concept significantly. However, let us investigate if this solution has some advantages. A key element of the design concept is in both cases the ability to deploy 1D substrate, “wrap” it in a 2D form for growth, and then unwind it during harvesting to 1D.
2.2.2. Horizontal vs. Angled Cultivation Structure
One may hypothesize that a conical shaped frustum is beneficial compared to a horizontally oriented disk shaped module, since the sunlight generally acts at a significant angle onto the water surface. Furthermore, it refracts and changes its angle of attack as it travels from air to water (Snell's law—Equation 1; Figure 5). As the direct irradiation comes at an angle, a slanted surface should be able to absorb more of the light than a horizontal one. The conical frustum may be rotated with a constant speed (e.g., a few rotations per day), ensuring that all the seaweed is exposed to the same amount of sunlight per given period of time.
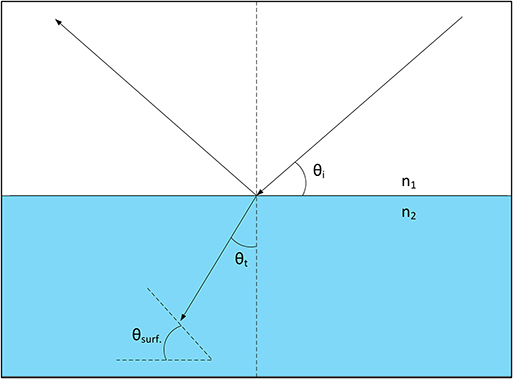
Figure 5. Illustration of angles above and below the surface as a result of reflection and refraction.
2.2.2.1. Average Sun Height
To calculate the average sun height, a MATLAB script based on a formula for declination in Kirk (1983) was used. The script returns the angle between the horizon and the sun at noon at a given date, time and latitude. In these calculations, the sun angle was obtained with a one week interval starting 21.11.2016 and ending 29.05.2017, i.e., 28 weeks in total. Trondheim was used as an example location with its latitudinal placement of 63.434. This resulted in an average sun height of θi = 12.6°.
2.2.2.2. Refraction of Sun Rays
As stated in section 2.2.2, it is assumed that Snell's law (Equation 1) of refraction applies and that both the air and the water are homogenous.
With the sun height θi calculated above and the refractive indices given in Table 1, the resulting refraction angle is θt≈47°. The resulting angles are illustrated in Figure 5.
2.2.2.3. Reflection of Light From Sea
Using the Fresnel equation and assuming that the light from the sun in unpolarized and both the water and the air is homogenous we are able to calculate the amount of light reflected away from the water surface (Vaughan, 2014). This reflection factor can then be used as a reduction factor for the PAR of the light passing through the water surface. The Fresnel equation distinguishes between s- and p-polarized light as shown in Equations (2) and (3), but by assuming that the light still is unpolarized after passing through water, we get the total reflectance, as shown in Equation (4).
Using the angles θi and θt and the refractive indices presented in Table 1, the resulting reflectance is at R ≈ 27%.
2.2.2.4. Radiation on a Conical Frustum
By using a MATLAB script based on Bird and Riordan (1984), it is possible to calculate both the direct and diffuse PAR at any given sun height. Given the angle θi, the script returned a direct and a diffuse PAR of λdir = 540 μ mol m−2 s−1 and λdif = 313 μ mol m−2 s−1, respectively. PAR onto a plane normal to the direct irradiance is then λ⊥ = λdir + λdif. By multiplying the direct PAR by the cosine of the sun angle and adding the diffuse PAR, we obtain the total PAR value for a horizontal surface as: λ∥ = cos(90°−ϕi)λdir + λdif.
When reducing the λ⊥ by the reflectivity factor we get the PAR value after reflection, . To get the PAR onto a surface below the surface angled by θsurf, we project the direct part by multiplying by the cosine of ϕt − θsurf:
For a horizontal surface, mol m−2 s−1. Figure 6 shows the PAR λ∠ as a function of plane angle θsurf. From this we see that the optimum plane angle is relative to the horizon (for a conical frustum shaped cultivation system), which gives the highest direct PAR for the given sun angle. This angle results in PAR of ~625 μ mol m−2 s−1, so the optimally angled plane, as expected, receives a higher light input than a horizontal plane. However, this is only true for the part of the plant facing toward the sun.
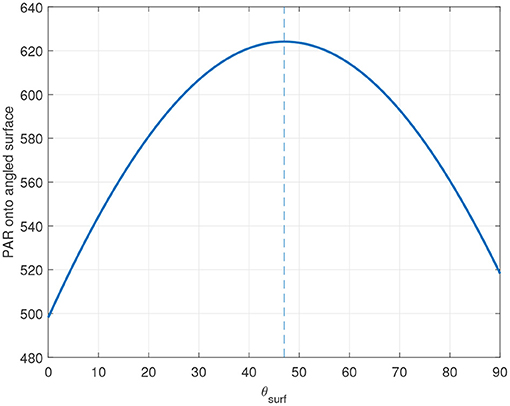
Figure 6. Average PAR (μ mol m−2 s−1) as a function of plane angle θsurf. The optimum angle is indicated by the hatched line.
Assuming that the cultivation plant rotates with a constant speed, we can estimate the average PAR, . Figure 7 illustrates the irradiance on a plane as it rotates away from the light source. The diffuse irradiance is equal through the circumference, while the amount of direct radiance decreases as the plant rotates away. To calculate this reduction of direct PAR, the reduction of the light opening is calculated for every degree of rotation and then multiplied with the direct PAR at zero rotation. The distribution of PAR as the plant rotates in the interval −90 to 90° is presented in Figure 8; for greater rotations only diffuse irradiance reaches the angled surface. Averaging over the whole circle, we get mol m−2 s−1, which is about 55% lower light exposure than that of a horizontal surface.
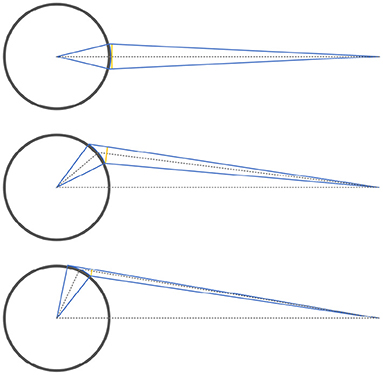
Figure 7. Illustration of area radiation on a circular plane as it rotates away from the light source. The diffuse irradiance is equal through the circumference, while the amount of direct radiance decreases as the plant rotates away. To calculate this reduction of direct radiance, the reduction of the light opening (yellow bar) is calculated for every degree of rotation and then multiplied with the direct PAR at zero rotation.
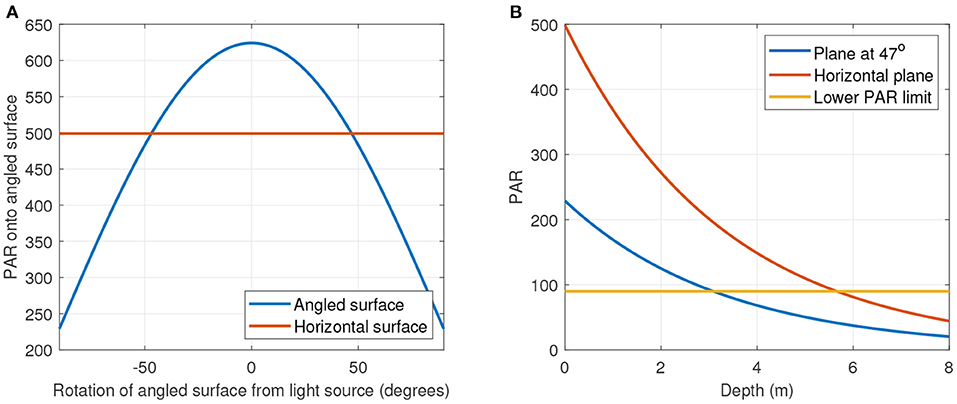
Figure 8. (A) PAR (μ mol m−2 s−1) distribution as a conical frustum plant rotates, vs. normal horizontal cultivation plant. (B) Reduction of PAR (μ mol m−2 s−1) as a function of depth, compared to the lower PAR limit for saturation.
2.2.2.5. PAR Reduction Due to Depth
Due to absorption, PAR decreases downward through the water column. To account for this, we calculate PAR along the vertical dimension as a function of chlorophyll concentration (P) and cDOM absorption (αcDOM):
where EPAR(i) and EPAR(i−1) are the PAR values at two vertical levels with the depth difference dz. The equation is based on Alver et al. (2014).
The chlorophyll concentration and cDOM absorption varies from season to season and between locations. The calculations can be repeated for any specific scenario of interest, but as a representative example, we estimate absorption using the values presented in Table 1. By applying Equation (6) to we get a distribution as shown in Figure 8 for the angled and the horizontal planes, with a lower PAR limit as described in section 2.1 shown for comparison. Over this limit, it is assumed that the photosynthetic activity is fully saturated. Under this limit, the growth of the algae can be limited.
2.2.2.6. Conclusion
Based on the above estimates, it appears that a conical frustum shape has its disadvantages when it comes to average light exposure. The conical frustum, at the optimal angle, is found to receive on average 55% lower PAR than the horizontal plane. As a result, at depths >3 m the average PAR is lower than the PAR saturation limit for a conical plant. This severely limits the size of the conical system due to the optimal cone angle θsurf = 47°. Furthermore, since the PAR for the conical frustum varies with the module's rotation, the saturation limit will in fact make the effective average PAR even lower if PAR exceeds the saturation limit when each individual plant is facing the sun. We therefore conclude that the disc shape appears superior to a conical one, considering both light utilization and structural simplicity.
2.2.3. Carrier Rope Structure
As stated in section 2.2.1, the 1D substrate is to be wrapped around the frame structure of the cultivation module. There are multiple wrapping possibilities, but the most promising are presented in Table 2. The main challenges with the different wraps is both the area optimizing and the practical aspects. For comparison, the outer frame ring has a diameter of 25 m, and for those with an inner ring that has a diameter of 3.5 m.
From Table 2, we see that a slanted outwards wrap gives the longest possible carrier rope, given a minimum spacing of 0.15 m. Tight rope spacing over prolonged distance is considered undesirable, due to possible biomass scrape off in high currents. The practical effects of carrier spacing is yet to be determined, and the numbers used in the table are estimations. The slanted outward wrap in combination with a center ring ensures that the unsupported length of each portion of the carrier rope is minimized to the radius of the structure, in comparison the carrier rope on the slanted wrap has an unsupported length equal to the diameter of the module. All wrapping patterns can utilize the circular structure as an efficient base for automated tools to move on, except for the slanted pattern. This pattern has parallel ropes within a circular frame, which makes automation more difficult since a robotic tool could easily move rotating on the outer frame, but not in parallel with the ropes. By these considerations, the slanted outward wrap seems to be the best choice.
2.3. Automation
2.3.1. Automated Carrier Rope Preparation
The concept encompasses automated spinning of seeded string on carrier rope. Working, field deployable prototypes for this have been developed and tested at full-scale. A scaled prototype of the ring module and interacting gantry robot has also been realized at Department of Engineering Cybernetics, NTNU, in collaboration with SINTEF Ocean.
The string substrate needs to be prepared and pre-grown in bioreactors. The thin (1.2 mm) braided string is spun onto standardized plastic cylinders. The prepared cylinders are bathed in a culture of spores (or gametophytes) in the bioreactors for a minimum of 4 weeks. Preparation of the cylinders has been automated. This machine (Figure 9, right) is able to wind the string from reels on to two plastic cylinders in parallel. The strings attach at the bottom of each cylinder and traverse upwards using a special rotating threaded rod. At the top end of the cylinders the mechanism automatically stops, and the cylinders are removed.
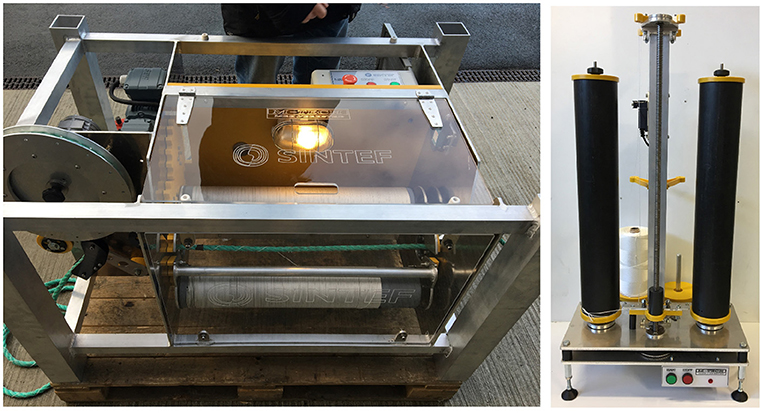
Figure 9. (Left) The rope spinner that spins seedling substrate onto carrier rope. (Right) The automatic rewinder that winds seedling substrate onto cylinders for pre-growth of seedlings.
When the growth phase on the cylinders in the bioreactor is done, they are ready for shipment from the lab to the deployment site. The cylinders need to be kept moist or submerged in seawater, in order to keep the seedlings from drying and deteriorating. At deployment time, the cylinders are installed in the rope spinner (Figure 9, left), which spins the strong onto the carrier rope as it is pulled through the machine.
2.3.2. Automated Deployment and Harvesting
The new cultivation concept is designed with deployment and harvesting in mind. To achieve automated deployment and harvesting, the idea is to use a separate, dedicated tool, deployed from a service vessel. The tool, a gantry robot, is lowered into the sea and mounts on the frame of the cultivation module, for deployment or harvesting. It utilizes the round shape of the module and is designed to slide on its circumference. While the tool is sliding on the circumference of the two main frames a “robot” moves back-and-forward deploying or removing the carrier rope. On site and ready for deployment, the seedling strings are spun onto the carrier rope using the rope spinner. Positioned on the deck of a service vessel, the prepared string is fed into the submerged gantry robot, automatically rigging the rope between the inner and outer ring of the modules. Figure 10 shows the service vessel with rope spinner, as it is deploying the gantry robot.
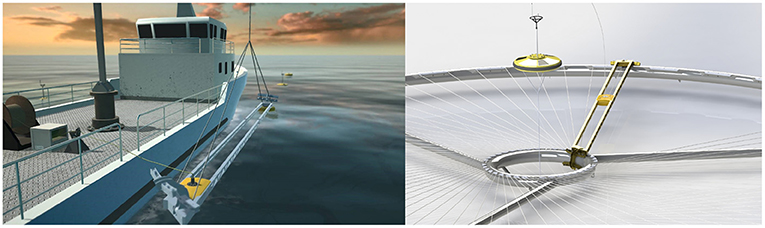
Figure 10. (Left) service vessel deploying the gantry robot, with the rope spinner on deck. (Right) Monitoring buoy fitted onto a SPOKe unit.
The gantry robot is designed only to be deployed during deployment and harvesting. To ease the mounting of the tool, it is fitted with gripping-arms at both ends, which also holds it in place during operation and provides motivity around the circumference. A centered connection point between the boom and the circular module may be used for easier deployment. Figure 11 shows a physical downscaled prototype (radius ~2 m) built for testing of deployment and harvesting techniques.
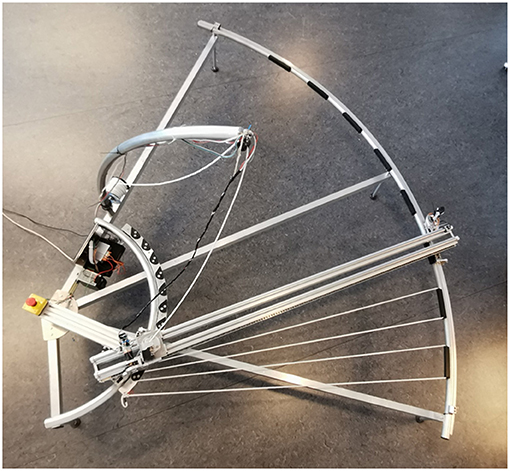
Figure 11. Prototype of a 90°sector of a SPOKe module for testing of deployment and harvesting techniques.
The gantry robot is driven around the circumference by motors at the outer end of the boom. For this system to work it is important that the system can measure its relative position on the frame at all times. This can be achieved using RFID tags, spaced around the circumference of the outer ring. Reading the tags, the gantry robot is able to decipher its location relative to the frame, and can also combine this technology with rotary encoding for position extrapolation.
2.3.3. Monitoring
The SPOKe concept includes data collection buoys for instrumentation and surveillance of the plant. Weather buoys might be used as inspiration for this; they are floating sensor carriers, often with a single mooring point, permitting easy deployment and moving. Weather buoys are also self-sustaining and are therefore able to collect and transmit data in real-time over long duration. Such features are ideal for macroalgae production. The ability to collect weather and growth data of algae can give a better understanding of the parameters governing a good biomass as well as making it easier to monitor multiple production units from a single communication central.
Selected units can be fitted with a data collection buoy, centrally positioned in the middle of a module. The buoy can house sensors collecting environmental data, relevant for seaweed growth. The buoy could be fitted with batteries and solar panels, making it self-sustainable and able to relay information back to shore in real-time. This monitoring platform has a great potential for a variety of monitoring parameters like air temperature, water temperature at different depths, wind direction and velocity, water current direction and velocity, PAR measurement at surface and at different depths, spectral light measurements, wave height and period, mooring tension forces, and conductivity. Macroalgae biomass and growth rate can be estimated based on light measurements at different depths, possibly in combination with other measurements.
3. Results and Discussion
3.1. Suitability for Automation
The SPOKe module is designed with automated deployment and harvesting as one of the primary concerns. The module design allows for a portable gantry robot (Figures 1, 10) to be moved between modules, automatically deploying cultivation rope prepared using the rope spinner (Figure 9) or harvesting seaweed as the rope is detached from the module. The practical design and operation of a gantry robot has been considered in a master's thesis (Eggesvik, 2019). In the study, a downscaled prototype was developed (Figure 11), including one quadrant of the circular module with inner and outer cleats for fastening the cultivation rope. A gantry robot was implemented as a separate system that could be mounted on the ring structure, with the rail traveling along the inner and outer rings of the structure. A control system was implemented for positioning of the gantry robot, using encoders to keep track of the robot's position. The study found that the design worked well, allowing the robot to be easily positioned on the module. Some limits of the downscaled study were pointed out, such as smaller rope tension compared to a full-scale system, different materials used in the prototype, and that the prototype tests could not be done underwater.
3.2. Area Efficiency
Based on the estimated length of cultivation rope on each SPOKe module (Table 2) and the effective footprint of the module, a comparison with regard to area efficiency can be made with cultivation concepts that are in use today (Table 3)5. From this comparison, it is clear that the SPOKe concept has a large potential yield. Some of the assumptions that may limit the production efficiency is the close proximity of the substrate ropes at the inner circle of the module. It is unsure if macroalgae are able to grow in such close proximity as described in Table 2, or whether this will lead to loss of biomass due to mechanical friction. This is one of the questions that must be answered before we know the full production potential of this concept. A small farm of 6 units of the SPOKe concept has an actual cultivation area of 0.54 ha.
3.3. Light Availability
Light availability is an important condition when choosing the shape of the SPOKe module. The flat circular shape was found to be the most efficient with regards to light utilization. According to the light estimates used in the design process, the flat cultivation disc should be exposed to sufficient PAR down to ~5.5 m at a sun angle of 12.6°.
The irradiance for maximal photosynthetic rate for S. latissima (λmin = 90 μmol m−2 s−1) is an estimation (Broch et al., 2013). The number of details at play in the real world far exceed what is manageable in assessments like this. The problems has to be simplified, and the estimation serves as a decent basis for the further evaluations.
The calculations of potential light exposure properties for the two module shapes (circle and frustum) are under the assumption of ideal light and weather conditions (perfectly calm water surface and a cloudless sky), which will not represent the average conditions for a given production cycle. The average sun angle was found based on a the latitude of Trondheim (63.43°), and the actual value will differ based on each site's location. It should be noted that the average sun angle cannot be used to estimate average seaweed growth, as the effect of light on growth is highly nonlinear. Rather, the average sun angle is used to represent a typical value that will be seen at a production site. Furthermore, it is assumed that the angle of attack of the direct sunlight changes according to Snell's law due to refraction when passing through the water surface. In reality, wave movement will cause some dispersal of the light's angular distribution.
The light estimates in this work focus on the cultivation module itself; the actual irradiance experienced by the seaweed will depend on their density, size and self-shadowing. Due to this and the highly variable conditions that will be seen at an actual site, these calculations must be considered rough estimates useful mainly for comparing different concepts and geometries. In further work, the light availability over time should be estimated more precisely using variable sun angles and a light propagation model such as Alver et al. (2014).
3.4. Durability/Reliability
Mooring has yet to be designed and was not a part of this study. In the salmon industry, extensive knowledge of mooring techniques for comparable structures like sea cages exist, and may be used as a starting point for the SPOKe concept. The question is not trivial, however, if rough sea conditions and a minimal footprint is the target: If the modules are allowed to sway in the currents, deviating from the horizontal plane, the distance between the modules may have to be increased, thus reducing the area efficiency. Based on numerical simulation tools for salmon cage farms, SINTEF Ocean are developing a tool for structural design of kelp farms that will be applied on the SPOKe concept before any tests at sea are run with a full scale prototype.
3.5. Scalability
Like the sea cages known in the salmon farming industry, a large-scale seaweed farm must make use of modules, enabling easy replacement, interaction and to lower the costs. The use of identical or standard modules also makes scaling easier. Designed carefully, a farm could be monitored with only a fraction of monitoring buoys compared to the number of growth modules, hence increasing the utilization of potentially costly sensing equipment. Anchoring must be dimensioned for the number of modules and the local weather conditions, but the solutions for interconnections between modules stay the same.
3.6. Costs
The technology development necessary to realize the SPOKe concept as proposed here will represent a major cost. A detailed cost analysis was not a part of this study, since module costs depend on implementation choices that are not known at this stage. As known from other industries, e.g., renewable solar PV (photovoltaic) and wind power technologies with its broad variety of technological solutions in demanding environment, the innovations have had a high initial cost, decreasing with standardization and scaling of production. IRENA5 forecasted in 2016 the investment cost reduction from 2015 to 2025 to reach 57% on solar PV technology, and 15% on offshore wind (global weighted average data; Taylor et al., 2016). The comparison is interesting as an example, although renewable energy technologies may see a higher demand than offshore seaweed production. The cost reductions are driven by increasing economies of scale, more competitive supply chains and technology improvements raising capacity factors and reducing installation costs. The amount of reduction is hard to predict for offshore seaweed, but many of the working mechanisms are similar. As the general opinion of the world has given sources of renewable energy increased attention, the same may happen to western seaweed production. One new incentive has also arrived; the demand for CCS: Carbon capture and storage. Using the produced biomass from offshore seaweed plants might find a future application as captured carbon to counteract global CO2-emissions, if an efficient solution for storing could be developed.
All aspects of the concept could not be covered in this study, and several have only been touched upon briefly. Anchoring, for example, is essential, especially offshore where the anchoring needs to be designed for greater depths and extreme weather and waves. The costs of anchoring are not considered in detail, but may call for large farms in order to increase cost efficiency.
Besides the technical aspects highlighted in this study, there are several necessary scientific investments to be made in research on biological and ecological effects (Harley et al., 2012; Ji et al., 2016; Krueger-Hadfield et al., 2017). Also, research on the genetic diversity of some of the most commonly cultivated species is yet to be completed (Valero et al., 2017). There are environmental risks to be considered along with an increase in seaweed cultivation, and these should be addressed along with an expansion of the industry (Campbell et al., 2019). The potential environmental impacts of large-scale kelp cultures in European coastal and offshore waters have not been properly quantified, but Chinese seaweed aquaculture, more than half of the global total, extracts significant amounts of nutrients from the coastal zone (Xiao et al., 2017). A recent simulation study suggests that relatively dense and extensive kelp cultures in enclosed bay systems may substantially reduce the pelagic primary production (Aldridge et al., 2021). One would expect offshore yields, and hence the nutrient extraction to be higher (Broch et al., 2019), but so would the nutrient availability, both due to higher concentrations and greater fluxes. Large-scale kelp aquaculture may thus mitigate coastal eutrophication, but also possibly compete with phytoplankton production in some situations. Although it is not possible to quantify these costs and benefits, it is important that they are communicated clearly and openly to stakeholders and the public.
4. Conclusions
We have developed a new concept for seaweed farming, suggesting a disc structure based on light utilization, mechanical durability and suitability for automation. The concept is developed with automation in mind, and we suggest a gantry robot for deployment, harvesting and interaction with the modules. The gantry robot has been demonstrated as a prototype. The concept encompasses automation equipment for preparation and deployment of the substrate, and a monitoring buoy. In theory, a small farm of 6 units of the SPOKe concept has an actual cultivation area of 0.54 ha, with an estimated production potential of/at 50 tons seaweed.
Data Availability Statement
The original contributions presented in the study are included in the article/supplementary material, further inquiries can be directed to the corresponding author/s.
Author Contributions
TS, MOA, OJB, and ESB conceived and developed the concept. ESB worked on the concept in a summer job at SINTEF Ocean. TS and MOA planned the paper. AH initiated and supervised the work. All authors contributed to the writing of the paper.
Funding
The research reported in this paper was supported by the Research Council of Norway grant 254883 (Macrosea) and the EU-funded project Genialg (H2020-BG-2016-1).
Conflict of Interest
The authors declare that the research was conducted in the absence of any commercial or financial relationships that could be construed as a potential conflict of interest.
Footnotes
1. ^https://www.forskningsradet.no/siteassets/publikasjoner/1253983223753.pdf
2. ^See https://atseanova.com/products-services/ for pictures and more information.
3. ^WGS84, decimal form.
4. ^Note that the numbers used in this comparison are estimations, some are reported, others theoretical. The table should merely be used as a theoretical comparison, as the results are not verified.
5. ^International Renewable Energy Agency.
References
Aldridge, J., Mooney, K., Dabrowski, T., and Capuzzo, E. (2021). Modelling effects of seaweed aquaculture on phytoplankton and mussel production. Application to Strangford lough (Northern Ireland). Aquaculture 536:736400. doi: 10.1016/j.aquaculture.2021.736400
Alver, M. O., Hancke, K., Sakshaug, E., and Slagstad, D. (2014). A spectrally-resolved light propagation model for aquatic systems: steps toward. J. Mar. Syst. 130, 134–146. doi: 10.1016/j.jmarsys.2012.03.007
Ask, E. I., and Azanza, R. V. (2002). Advances in cultivation technology of commercial eucheumatoid species: a review with suggestions for future research. Aquaculture 206, 257–277. doi: 10.1016/S0044-8486(01)00724-4
Bak, U. G., Mols-Mortensen, A., and Gregersen, O. (2018). Production method and cost of commercial-scale offshore cultivation of kelp in the Faroe Islands using multiple partial harvesting. Algal Res. 33, 36–47. doi: 10.1016/j.algal.2018.05.001
Bell, T., Cavanaugh, K., Reed, D., and Siegel, D. (2015). Geographical variability in the controls of giant kelp biomass dynamics. J. Biogeogr. 42, 2010–2021. doi: 10.1111/jbi.12550
Bird, R. E., and Riordan, C. (1984). Simple Solar Spectral Model for Direct and Diffuse Irradiance in Horizontal and Tilted Planes at the Earth's Surface for Cloudless Atmospheres. Golden, CO: Solar Energy Research Institute. doi: 10.2172/5986936
Broch, O. J., Alver, M. O., Bekkby, T., Gundersen, H., Forbord, S., Handå, A., et al. (2019). Kelp cultivation potential in coastal and offshore regions of Norway. Front. Mar. Sci. 5:529. doi: 10.3389/fmars.2018.00529
Broch, O. J., Ellingsen, I. H., Forbord, S., Wang, X., Volent, Z., Alver, M. O., et al. (2013). Modelling the cultivation and bioremediation potential of the kelp Saccharina latissima in close proximity to an exposed salmon farm in Norway. Aquac. Environ. Interact. 4, 187–206. doi: 10.3354/aei00080
Buck, B. H., and Buchholz, C. M. (2004). The offshore-ring: a new system design for the open ocean aquaculture of macroalgae. J. Appl. Phycol. 16, 355–368. doi: 10.1023/B:JAPH.0000047947.96231.ea
Buschmann, A. H., Camus, C., Infante, J., Neori, A., Israel, A., Hernández-González, M. C., et al. (2017). Seaweed production: overview of the global state of exploitation, farming and emerging research activity. Eur. J. Phycol. 391–406. doi: 10.1080/09670262.2017.1365175
Campbell, I., Macleod, A., Sahlmann, C., Neves, L., Funderud, J., Øverland, M., et al. (2019). The environmental risks associated with the development of seaweed farming in Europe - prioritizing key knowledge gaps. Front. Mar. Sci. doi: 10.3389/fmars.2019.00107
Duarte, C. M., Wu, J., Xiao, X., Bruhn, A., and Krause-Jensen, D. (2017). Can seaweed farming play a role in climate change mitigation and adaptation? Front. Mar. Sci. 4:100. doi: 10.3389/fmars.2017.00100
Eggesvik, A. T. (2019). Robot for automatisk utsetting og høsting av tare (Master's thesis). Norwegian University of Science and Technology, Trondheim, Norway.
Forbord, S., Skjermo, J., Arff, J., Handå, A., Reitan, K. I., Bjerregaard, R., et al. (2012). Development of Saccharina latissima (phaeophyceae) kelp hatcheries with year-round production of zoospores and juvenile sporophytes on culture ropes for kelp aquaculture. J. Appl. Phycol. 24, 393–399. doi: 10.1007/s10811-011-9784-y
Forbord, S., Steinhovden, K., Rød, K., Handå, A., and Skjermo, J. (2018). Cultivation Protocol for Saccharina latissima, Protocols for Macroalgae Research. Boca Raton, FL: CRC Press; Taylor & Francis Group. doi: 10.1201/b21460-2
Harley, C., Anderson, K., Demes, K., Jorve, J., Kordas, R., Coyle, T., et al. (2012). Effects of climate change on global seaweed communities. J. Phycol. 48, 1064–1078. doi: 10.1111/j.1529-8817.2012.01224.x
Ji, Y., Xu, Z., Zou, D., and Gao, K. (2016). Ecophysiological responses of marine macroalgae to climate change factors. J. Appl. Phycol. 28, 2953–2967. doi: 10.1007/s10811-016-0840-5
Kerrison, P. D., Innes, M., MacLeod, A., McCormick, E., Elbourne, P. D., Stanley, M. S., et al. (2020). Comparing the effectiveness of twine- and binder-seeding in the laminariales species Alaria esculenta and Saccharina latissima. J. Appl. Phycol. 32, 2173–2181. doi: 10.1007/s10811-020-02069-5
Kim, J. K., Yarish, C., Hwang, E. K., Park, M., and Kim, Y. (2017). Seaweed aquaculture: cultivation technologies, challenges and its ecosystem services. Algae 32, 1–13. doi: 10.4490/algae.2017.32.3.3
Kirk, J. T. (1983). Light and Photosynthesis in Aquatic Ecosystems. Cambridge: Cambridge University Press.
Krueger-Hadfield, S., Kollars, N., Strand, A., Byers, J., Shainker, S., Terada, R., et al. (2017). Genetic identification of source and likely vector of a widespread marine invader. Ecol. Evol. 7, 4432–4447. doi: 10.1002/ece3.3001
Meland, M., and Rebours, C. (2012). Short description of the Norwegian seaweed industry. Bioforsk Fokus 7, 275–277.
Olafsen, T., Winther, U., Olsen, Y., and Skjermo, J. (2012). Value Creation Based on Productive Seas in 2050. (In Norwegian: Verdiskapning Basert på Produktive hav i 2050). Det Kongelige Norske Videnskabers Selskab (DKNVS); Norges Tekniske Vitenskapsakademi (NTVA).
Sanderson, J. C., Dring, M. J., Davidson, K., and Kelly, M. S. (2012). Culture, yield and bioremediation of Palmaria palmata (Linnaeus) Weber and Mohr and Saccharina latissima (Linnaeus) C. E. Lane, C. Mayes, Druehl and G. W. Saudners adjacent to fish farm cages in northwest Scotland. Aquaculture 128–135. doi: 10.1016/j.aquaculture.2012.03.019
Stévant, P., Rebours, C., and Chapman, A. (2017). Seaweed aquaculture in Norway: recent industrial developments and future perspectives. Aquac. Int. 25, 1373–1390. doi: 10.1007/s10499-017-0120-7
Su, L., Pang, S. J., Shan, T. F., and Li, X. (2017). Large-scale hatchery of the kelp Saccharina japonica: a case study experience at lvshun in northern china. J. Appl. Phycol. 29, 3003–3013. doi: 10.1007/s10811-017-1154-y
Taylor, M., Ralon, P., and Ilas, A. (2016). The Power to Change: Solar and Wind Cost Reduction Potential to 2025. International Renewable Energy Agency (IRENA).
Titlyanov, E. A., and Titlyanova, T. V. (2010). Seaweed cultivation: methods and problems. Russian J. Mar. Biol. 36, 227–242. doi: 10.1134/S1063074010040012
Valero, M., Guillemin, M.-L., Destombe, C., Jacquemin, B., Gachon, C., Badis, Y., et al. (2017). Perspectives on domestication research for sustainable seaweed aquaculture. Perspect. Phycol. 4, 33–46. doi: 10.1127/pip/2017/0066
van den Burg, S. W. K., van Duijn, A. P., Bartelings, H., van Krimpen, M. M., and Poelman, M. (2016). The economic feasibility of seaweed production in the North Sea. Aquac. Econ. Manage. 20, 235–252. doi: 10.1080/13657305.2016.1177859
Vaughan, M. (2014). Dr Martin Vaughan: lectures PY3101: Optics. Available online at: http://www.physics.ucc.ie/mvaughan/lecturing/PY3101/Optics.pdf
Xiao, X., Agusti, S., Lin, F., Li, K., Pan, Y., Yu, Y., et al. (2017). Nutrient removal from Chinese coastal waters by large-scale seaweed aquaculture. Sci. Rep. 7, 1–6. doi: 10.1038/srep46613
Keywords: aquaculture, seaweed, harvest, deployment, automation, industrialization, production concept
Citation: Solvang T, Bale ES, Broch OJ, Handå A and Alver MO (2021) Automation Concepts for Industrial-Scale Production of Seaweed. Front. Mar. Sci. 8:613093. doi: 10.3389/fmars.2021.613093
Received: 01 October 2020; Accepted: 29 March 2021;
Published: 26 April 2021.
Edited by:
Liping Liu, Shanghai Ocean University, ChinaReviewed by:
Nor Azman Kasan, University of Malaysia Terengganu, MalaysiaAlan T. Critchley, Cape Breton University, Canada
Copyright © 2021 Solvang, Bale, Broch, Handå and Alver. This is an open-access article distributed under the terms of the Creative Commons Attribution License (CC BY). The use, distribution or reproduction in other forums is permitted, provided the original author(s) and the copyright owner(s) are credited and that the original publication in this journal is cited, in accordance with accepted academic practice. No use, distribution or reproduction is permitted which does not comply with these terms.
*Correspondence: Morten Omholt Alver, bW9ydGVuLmFsdmVyQG50bnUubm8=
†Present address: Emil Scott Bale, Norconsult AS, Trondheim, Norway