- 1Department of Energy and Technology, Swedish University of Agricultural Sciences, Uppsala, Sweden
- 2Future Water Institute, University of Cape Town, Cape Town, South Africa
- 3Civil Engineering Department, University of Cape Town, Cape Town, South Africa
- 4Built Environment and Bioeconomy, Tampere University of Applied Sciences, Tampere, Finland
This study evaluated the recovery of amorphous calcium phosphate and vivianite from industrial wastewater produced by a toothpaste manufacturing facility, where phosphorus concentrations exceed 3,000 mg L−1. The goal was to reduce the phosphorus concentration on-site to below 20 mg P L−1, so that treated wastewater can be discharged to a municipal wastewater treatment plant. In bench-scale experiments, various dosages of Ca(OH)2 (10–25 g L−1) and FeSO4·7H2O (20–60 g L−1) were evaluated to identify optimal conditions for precipitating >99% of the phosphorus. Pilot-scale experiments showed that recovery of amorphous calcium phosphate required dosing 25 g L−1 Ca(OH)2 and mixing for 60 min, whereas recovery of metavivianite required co-dosing 60 g L−1 FeSO₄·6–7H₂O and 7.2 g L−1 NaOH and mixing for 15 min. Variations in influent wastewater composition were found to significantly affect the pH as well as concentrations of residual Fe2+ and Ca2+ in the treated wastewater. Impurities present in chemicals used for precipitating phosphorus were found to influence purity of the recovered phosphate products. The chemical demand for recovering 99% of the phosphorus in the toothpaste industry wastewater was found to be significantly higher than for recovering 95% of the phosphorus in conventional municipal wastewater. This was due to a higher treatment goal and the unique composition of the wastewater, characterised by its high ionic strength and elevated concentrations of Na+ and Cl−, which potentially inhibited nucleation and crystal growth during chemical precipitation. A preliminary economic analysis indicated that recovering vivianite, with potential applications in the electronics industry, could generate significantly higher profits compared to amorphous calcium phosphate, but this depends on the product purity. Overall, this study highlights the potential for industrial wastewater to contribute to a circular phosphorus economy.
1 Introduction
Excess phosphorus in the environment is harmful, as it can cause hypoxia and eutrophication in natural water bodies (Preisner et al., 2020). However, treatment that only removes phosphorus from wastewater is not sufficient and the focus must be shifted to developing industrial-scale technologies that close the phosphorus loop, moving beyond removal to recycling (Jupp et al., 2021b). The majority of mined phosphorus is produced via the wet process (Gantner et al., 2014), which is environmentally unsustainable and results in production of 5 mt of phosphogypsum per mt of phosphoric acid, of which 88% is landfilled (Tayibi et al., 2009).
The two main technological processes available for phosphorus recovery from wastewater are chemical precipitation and enhanced biological phosphorus removal (EBPR) (Jupp et al., 2021a). Chemical precipitation involves addition of a metal (Al3+/Fe2+/Fe3+/Ca2+) salt to wastewater to precipitate metal phosphates (Kemacheevakul et al., 2011). This method is versatile and can be adapted for various industrial wastewaters, but it requires careful control of pH and chemical dosage to optimize phosphorus recovery. EBPR involves the use of microorganisms to accumulate phosphorus intracellularly and remove it during sludge treatment, but the process is primarily used for treating domestic wastewater with predictable compositions (Bunce et al., 2018). To chemically precipitate phosphorus from wastewater that contains no ammonium ions, there are three approaches. First, by dosing wastewater with Ca(OH)2 to precipitate phosphate as amorphous calcium phosphate. Second, by dosing wastewater with Fe3+ to precipitate amorphous ferric phosphate (FePO4) or Fe2+ to precipitate phosphate as metavivianite (Fe3(PO4)2.8H2O) (Wang et al., 2019). Third, by dosing alum or hydrated aluminium sulphate to coagulate and flocculate phosphorus as AlPO4, but this is mainly a phosphorus removal method rather than a phosphorus recovery method. This is because AlPO4 binds phosphorus in an insoluble form that is not readily bioavailable for plant uptake, unlike products such as struvite or vivianite, which can be effectively recycled as fertilisers. Amorphous calcium and iron phosphate can be used in agriculture as a slow-release phosphorus fertiliser (Cabeza et al., 2019). Low-purity vivianite is commonly used as fertiliser, whereas high-purity vivianite is highly sought after in the electronics industry, particularly for use in lithium-ion battery production (Rao and Varadaraju, 2015), and in the art industry as a pigment in paint (Rao and Varadaraju, 2015). Vivianite crystals can be sold for $100–500 kg−1, while as a pigment used in paint it is even more valuable, selling for as much as $700–800 kg−1 (Simbeye et al., 2023). Considering that calcium phosphate can typically only be sold for less than $1 kg−1 (Yetilmezsoy et al., 2017), recovering P as vivianite would likely be significantly more profitable. For advanced applications such as lithium-ion batteries, where lithium salts must have a purity of at least 99.5%, vivianite would similarly need to meet these high purity standards to serve as a precursor for producing lithium iron phosphate (Avdibegović et al., 2022). However, extracting high-purity vivianite from mixed precipitates produced by treating complex matrices such as domestic wastewater is challenging. In such matrices, co-precipitates such as heavy metals, alkaline earth metals, and organic compounds complicate the purification process necessary to produce industry-grade vivianite (Zhang et al., 2022).
Compared to municipal wastewater, industrial wastewater can be a less complex matrix for producing high-purity vivianite. Several industries such as dairy processing, meat processing, and beverage production generate significant quantities of phosphorus-laden effluents (Mittal, 2006). The toothpaste industry, while not as prominent a contributor as agricultural industries, also faces challenges related to phosphorus in its effluents. Many toothpaste formulations include synthetic phosphate compounds due to their biocompatibility, non-toxicity, and osteoconductivty (Enax and Epple, 2018). These compounds are used in dentistry and oral care products for applications including tooth remineralisation, reduction of tooth sensitivity, cleaning, whitening, and controlling oral microbial biofilms on teeth surfaces (Chen et al., 2021). The production of these compounds results in the generation of phosphorus-containing effluent, which must be treated on-site before it can be released to the environment or conveyed to a municipal wastewater treatment plant. By recovering phosphorus as value-added products like vivianite, such industries can support a circular transition in the water sector while also potentially generating economic benefits (Zhu et al., 2023).
The aim of this study was to investigate the feasibility of recovering phosphorus as value-added products (amorphous calcium phosphate and metavivianite) from wastewater containing high phosphorus load (>4,000 mg P L−1) produced by a toothpaste manufacturing industry. Both processes were evaluated in bench-scale and pilot-scale experiments. The treatment goal was to recover more than 99% of the phosphorus and reduce the phosphorus concentration in wastewater to below 20 mg L−1. This limit is specific to the facility’s permit for discharging treated wastewater to a nearby municipal treatment plant, where it undergoes further processing to meet lower phosphorus limits typically required for environmental discharge in compliance with regulations such as the EU Urban Wastewater Treatment Directive 91/271/EEC. Overall, this study provides insights into scalable methods for producing high-purity vivianite and phosphorus recovery, supporting the transition towards more sustainable industrial practices.
2 Methodology
2.1 Industrial wastewater
Wastewater was sourced from a toothpaste manufacturing company in Uppsala, Sweden and stored at room temperature (20°C ± 2°C) until use in experiments. The wastewater contains between 4 and 7 g P L−1 as dissolved inorganic orthophosphate, in addition to high concentration of other ions (Table 1). Other forms of phosphorus, such as particulate or organic phosphorus, are not present. This makes the wastewater composition rather unique. There are few examples, if any, in literature where wastewater with similar chemistry has been treated to remove phosphorus.
2.2 Bench-scale experiments
In bench-scale experiments, technical grade Ca(OH)2 (Nordkalk SL 90, Nordkalk AB, Sweden) and analytical grade FeSO4·7H2O (Sigma-Aldrich, Germany) was used. Both calcium phosphate and vivianite precipitations were conducted using a similar approach. In each case, 200 mL of wastewater was placed in a 250 mL flask, dosed with Ca(OH)2 (between 10 g L−1 and 25 g L−1) or FeSO4.7H2O (between 20 g L−1 and 60 g L−1) and mixed over a magnetic stirrer set to 500 rpm at room temperature (20°C ± 2°C). The flasks were covered to prevent CO2 absorption and Fe2+ oxidation. The pH and electrical conductivity (EC) were monitored at 5-min intervals for 4 h. For vivianite precipitation, the pH of the wastewater was adjusted to 7.0 (±0.1) by adding 1 M KOH.
2.3 Pilot-scale experiments
In pilot-scale experiments, technical grade Ca(OH)2 (Nordkalk SL 90, Nordkalk AB, Sweden) and technical grade FeSO4.6-7H2O (Ferrogranul 20, KRONOS ecochem, Germany) was used. To evaluate the treatments at pilot-scale, two reactors in stainless steel were custom-built with a maximum holding capacity of 10 L. The reactors had a truncated cone design configuration with an opening at the top that was used to insert a propeller (R 1345, 4-bladed, Ø100 mm, 540 mm) connected to an OHS 60 digital overhead stirrer (Velp Scientifica, Italy). A second opening at the bottom of the reactor was equipped with a ball valve that was used to drain wastewater at the end of the treatment.
To start the Ca(OH)2 pilot-scale study, 9 L of wastewater was added to each reactor. The overhead stirrer was switched on and set to 350 rpm. Probes for measuring pH and EC were inserted and positioned. Then, 25 g L−1 Ca(OH)2 was added to the reactors and the treatment was performed for 60 min. Subsequently, the ball valve was opened, and the reactors were drained to collect the treated wastewater in separate containers which were covered with a lid and allowed to sit undisturbed overnight. About 250 mL of wastewater was filtered and stored in polypropylene flasks (0.5 L, VWR, Sweden) at room temperature for further analysis. To restart the treatment, the reactors were washed with deionised water, refilled with 9 L of fresh wastewater, and all previous steps were repeated. In total, 9 different batches of treatment were carried out in duplicate.
To start the ferrous sulphate pilot-scale study, 9 L of wastewater was added to each reactor. The overhead stirrer was switched on and set to 420 rpm. Probes for measuring pH and EC were inserted and positioned. Then, 60 g L−1 FeSO4.6–7H2O and 7.2 g L−1 NaOH were added to the reactors and the treatment was performed for 15 min. Subsequently, the ball valve was opened, and the reactors were drained to collect the treated wastewater in separate containers. About 250 mL of wastewater was filtered and stored in polypropylene flasks (0.5 L, VWR, Sweden) at room temperature for further analysis. For the next batch, the reactors were washed with deionised water, filled with 9 L of fresh wastewater, and all previous steps were repeated. In total, 9 batches of treatment were carried out.
The chosen reaction conditions for the pilot-scale study were optimized based on preliminary tests to ensure effective phosphorus removal, while the treatment was replicated in nine batches to ensure robustness and reliability. All the pilot-scale experiments were done in duplicate. Average values along with standard deviation have been reported in figures.
2.4 Physical and chemical analyses
At the end of the bench-scale experiments, a sample of the treated wastewater was withdrawn, filtered (0.45 µm; Filtropur S, Sarstedt, Germany) and adjusted to pH 5-8 by adding 5 M H2SO4. The prepared sample was digested using a Spectroquant® Crack-Set 10 test kit (114687) and analysed for concentration of phosphate in the range 1–100 mg L−1 using a Spectroquant® test kit (100798, Merck KGaA, Germany) and a NOVA 60 A photometer (Merck KGaA, Germany).
Samples of treated wastewater collected at the end of the pilot-scale experiments were analysed for concentration of PO4-P, Ca2+, Mg2+ and Fe2+ by colorimetric methods using a Thermo Scientific™ Gallery™ discrete analyser. Ca (test kit 984361) was analysed by reaction with Arsenazo III to form a colored complex that is measured at 660 nm. Mg (test kit 984358) was analysed by reaction with xylidyl blue in alkaline conditions to form a red coloured complex that is measured at 510 nm. Fe (test kit 984706 and 984707) was analysed by reaction with with 1,10 phenanthroline in the pH range 2.5–9.0 to form a orange-red complex that is measured at 510 nm. Orthophosphate (test kit 984366 and 984368) was determined by reaction with ammonium molybdate and antimony potassium tartrate under acidic conditions. The 12-molybdophosphoric acid complex formed is subsequently reduced with ascorbic acid to form a blue heteropoly compound that is measured spectrophotometrically at 880 nm/660 nm.
The pH was measured using a pH glass electrode (Metrohm iUnitrode with Pt1000, 6.0278.300, Switzerland) connected to a 914 pH/Conductometer (2.914.0020, Metrohm, Switzerland). The electrical conductivity was measured by using a conductivity measuring cell (Metrohm, 6.0917.080, Switzerland) connected to a measuring instrument (Metrohm 914 pH/Conductometer, 2.914.0020, Switzerland).
3 Results and discussion
3.1 Removal of phosphorus in benchtop experiments
The initial benchtop experiments determined the ideal chemical dosages for calcium hydroxide and iron sulphate. Dosing the wastewater with Ca(OH)2 increased the pH at different rates (Figure 1). A Ca(OH)2 dosage of 10 g L−1 increased the pH to approximately 11.0, whereas a dosage of 25 g L−1 Ca(OH)2 resulted in supersaturation and a pH of greater than 13.0. The higher the Ca(OH)2 dose, the faster was the equilibration of pH. It took less than 60 min for the pH to equilibrate at the highest Ca(OH)2 dose. At 15 g Ca(OH)2 L−1, the results showed that the final P concentration was 0.545 g L−1 (92% P removal) (Figure 2A). Whereas, at 20 and 25 g Ca(OH)2 L−1, the experimental results showed that final P concentration was less than 0.04 g L−1. Therefore, for the subsequent experiments at pilot-scale, we chose a dose of 25 g Ca(OH)2 L-1 to account for variations in phosphorus concentration of the wastewater and variation in the calcium concentration of Ca(OH)2 used in the study.
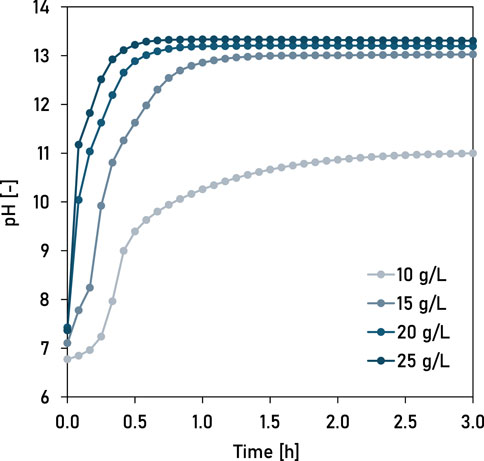
Figure 1. The experimentally observed changes in pH of wastewater when dosed with different concentrations of Ca(OH)2 at 20°C.
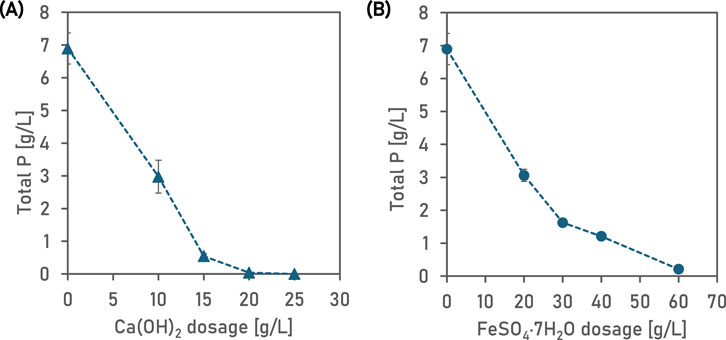
Figure 2. The total aqueous p remaining in solution for different dosages of Ca(OH)2 (A) and FeSO4·7H2O (B) Observed in bench-scale laboratory experiments 20°C. For the Fe experiments, after recording the drop in pH of wastewater due to FeSO4 addition, the pH was adjusted to 7.0 (±0.1) by adding 1 M KOH. Average values have been plotted and error bars show standard deviation of two replicates.
In experiments dosing the wastewater with FeSO4.7H2O, it was observed that the pH dropped to between 3.0 and 4.0 at a dose of >40 g L−1, but that it could be brought back to pH 7.0 by addition of 1 M KOH. Two factors affect the choice of the operating pH. Firstly, the pH of wastewater must be adjusted by adding an alkali because dosing FeSO4 results in acidification of the solution. Thus, the higher the operating pH, the higher is the chemical demand for alkalisation. Secondly, the stoichiometric Fe:P molar ratio in metavivianite is 1.5:1. This suggests that to remove all the phosphate from wastewater as vivianite (about 7 g PO4-P L−1), the minimum FeSO4.7H2O dose required is 60.6 g L−1. If vivianite precipitation at this dose is suboptimal (e.g., at pH < 4.0), then residual Fe2+ is left in solution. On exposure to air, residual Fe2+ can oxidise to Fe3+, and the rate of oxidation is higher at a higher pH (Morgan and Lahav, 2007). Therefore, to minimise residual Fe2+ as well as Fe2+ oxidation, the operating pH must be between 6.0 and 7.0. The reason we chose a final operating pH of 7 was because this is the pH value where the maximum amount of vivianite can form with the highest purity (Supplementary Figure S1).
At 40 g FeSO4.6–7H2O L−1, the results showed that the aqueous P concentration had reduced to 1.21 g L−1 (82% P removal) (Figure 2B). Dosing 60 g FeSO4.7H2O L−1 resulted in an aqueous P concentration of 0.210 g L−1 (97% P removal). Therefore, in experiments at pilot scale, we chose a dose of 60 g FeSO4.6–7H2O L−1 to account for variations in phosphorus concentration of the wastewater, and because the FeSO4 used in the pilot study was only of technical grade (the manufacturer claims that 6-7 mol of water of crystallisation is present per mole of FeSO4).
3.2 Removal of phosphate in pilot-scale experiments
During the pilot-scale treatment with Ca(OH)2, the pH of wastewater increased to between 12.8 and 13.5 during 60 min of treatment (Figure 3A).
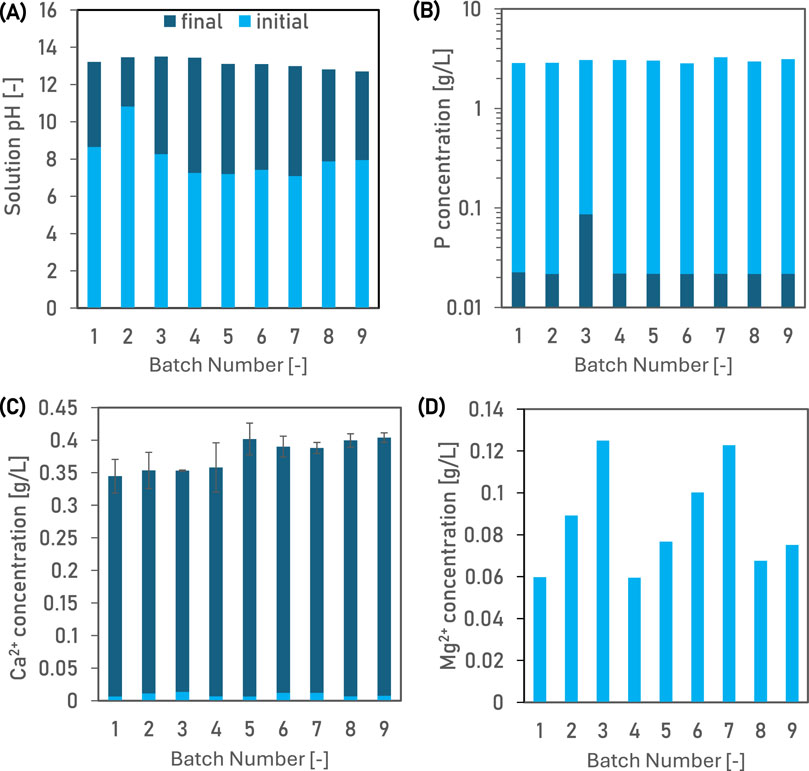
Figure 3. The solution pH (A) and concentration of phosphorus (B), calcium (C) and magnesium (D) in the nine batches of the wastewater, before and after treatment with 25 g Ca(OH)2 L−1 at 20°C in the pilot scale reactor. Average values have been plotted and error bars show standard deviation of two replicates.
The initial P concentration in the wastewater was measured to between 2.84 and 3.11 g L−1 for the 9 batches tested (Figure 3B). Following treatment with 25 g Ca(OH)2 L−1 at room temperature for 60 min, the average residual P concentration was measured to be less than 0.02 g L−1. The removal of phosphorus was >99% across all batches. The residual concentration of Ca2+ in the wastewater was measured to between 0.338 and 0.396 L−1 (Figure 3C). Reducing the Ca(OH)2 dose to 24.5 g L−1 would minimise the residual Ca2+ without affecting the removal of P. No Mg2+ was detected in the treated water (Figure 3D), which is attributed to the precipitation of Mg(OH)2 at pH values of >10.5 (Simha et al., 2022).
During pilot-scale treatment with FeSO4, the wastewater pH could be increased above 6 (except for batch 7) by co-dosing the raw wastewater with FeSO4.6-7H2O and NaOH (Figure 4A). Following treatment with 60 g FeSO4.6-7H2O L−1 at room temperature for 15 min, the P concentration in the 9 batches of wastewater ranged from 0.021 to 0.022 g L−1 (Figure 4B). Fe was not detected in the raw wastewater. Residual Fe2+ in the treated wastewater was 1.7 ± 0.9 g L−1 and varied significantly between batches (Figure 4C). The most likely reasons for this are two-fold. Firstly, FeSO4 was overdosed in relation to P concentration of the raw wastewater. In bench-scale lab experiments, the P concentration of the raw wastewater was 6.895 g L−1 and the FeSO4.7H2O dose required was estimated to be 60 g L−1. However, in pilot-scale experiments, the P concentration of the raw wastewater was lower, less than 3.11 g L−1. Therefore, the Fe:P molar ratio was much higher (2.2–2.4), depending on whether six or 7 mol of water of crystallisation was present per mole of FeSO4. Secondly, on exposure to air, the residual Fe2+ oxidised to Fe3+ which precipitated as iron(III) hydroxide, due to its low solubility in water. Reddish-brown solids, characteristic of iron hydroxide, were observed as co-precipitates that formed a thin layer on top the predominant precipitate, deep blue vivianite. As this study only measured Fe2+ concentration in untreated and treated wastewater, the extent of Fe2+ oxidation cannot be estimated but was likely high in batches 2, 3 and 6. The Mg concentration in wastewater increased from an initial concentration of 0.09 g L−1 to between 0.636 and 0.904 g L−1 after treatment (Figure 4D). According to the manufacturer (KRONOS ecochem, Germany), the FeSO4 (trade name Ferrogranul 20) used in the study typically contains 0.7% Mg, 0.3% Ca, 0.04% Mn and 0.6% insoluble impurities. Given these values, 0.42 g Mg L−1 was added to the wastewater, which initially contained 0.09 g Mg L−1, explaining the observed increase in magnesium concentration. However, the 0.6% insoluble impurities present a problem for the vivianite produced by dosing wastewater with Ferrogranul 20, as they are likely to co-precipitate with the vivianite in the pH range of 4.0–8.0. According to our thermodynamic simulations, Mn and Ca initially present in Ferrogranul 20 would also co-precipitate with metavivianite as Mn3(PO4)2 and Ca5(OH) (PO4)3, respectively. Altogether, these impurities would constitute an estimated 2.4% of the precipitate mass, resulting in a theoretical vivianite purity of 97.6% at a pH of 7 (Supplementary Figure S2). For applications such as lithium-ion batteries that use vivianite as a precursor, this level of impurity is unacceptable, since they can impact the battery’s energy storage capacity, lifetime and safety (He et al., 2021).
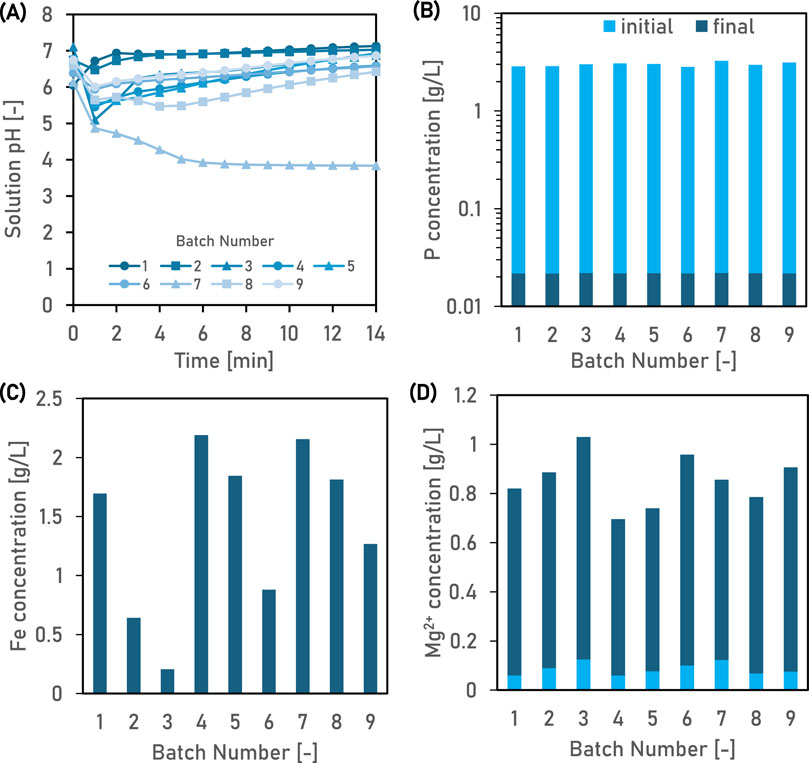
Figure 4. The solution pH (A) and concentration of PO4-P (B), Fe2+ (C) and Mg2+ (D) in the nine batches of the wastewater, before and after treatment with 60 g FeSO4.6-7H2O L−1 and 7.2 g L−1 NaOH at 20°C in the pilot-scale reactor.
3.3 Practical implications
According to Statistics Sweden (2020), 300 L p−1 d−1 of mixed wastewater containing 5 mg P L−1 is produced in Sweden, and according to the toothpaste manufacturer, 600 L d−1 industrial wastewater is produced. Therefore, the wastewater from the toothpaste manufacturing industry evaluated in this study contains the same amount of phosphorus as that produced by an urban neighbourhood of 2,800 people in Sweden and highlights the importance of managing industrial sources of phosphorus pollution in urban areas. The two approaches we evaluated in this study offer different benefits and challenges in practice. From an operational perspective, precipitating amorphous calcium phosphate is relatively easier because only one chemical [i.e., Ca(OH)₂] needs to be dosed to provide the necessary calcium ions while also increasing the pH for maximum phosphorus removal. However, fixing the Ca(OH)2 dosage and having a varying wastewater composition can result in overdosing with calcium, as observed in our pilot-scale experiments. Moreover, the formation of amorphous calcium phosphate required 60 min of mixing for more than 99% of the phosphate to be removed. In contrast, vivianite precipitation is faster (<15 min) but requires dosing both an iron salt and a base to adjust the pH to be in the optimal range for maximising vivianite formation. This affects the operating cost and complexity of the process. To precipitate calcium phosphate, we estimate $3.23 m⁻³ would be required assuming Ca(OH)2 costs $132 ton−1. To precipitate vivianite, we estimate $8.49 m⁻³ would be required assuming NaOH costs $362 ton−1 and FeSO4.7H2O costs $80 ton−1 (Supplementary Table S1). However, the selling price of calcium phosphate and vivianite can differ substantially depending on the purity of the product. The selling price of calcium phosphate is around $1,180 per ton, while for the purest vivianite, the price can be up to $10,700 per ton. For the wastewater evaluated in the current study, it is estimated that 16.1 kg m−3 of calcium phosphate or 24.1 kg m−3 of vivianite could be produced, resulting in an income of $19 m-3 for calcium phosphate and $258 m−3 for vivianite (Supplementary Table S1).
The post-processing separation of solid calcium phosphate could be achieved using settling and filtration, while vivianite could be collected using magnetic separation (Wijdeveld et al., 2022). The calcium phosphate product is likely to be less pure if excess calcium hydroxide is added, creating a saturated solution due to the low solubility of calcium hydroxide. Additionally, co-precipitation with magnesium hydroxide would occur at operating pH values of >10 (Simha et al., 2022). In the case of vivianite, co-precipitation mainly occurs due to impurities present in Ferrongranul 20. These impurities could be removed during the magnetic separation of vivianite (Wijdeveld et al., 2022) or by using purer Fe(II) salts during treatment.
Both the calcium hydroxide and iron sulphate dosing resulted in more than 99% phosphorus removal in the pilot experiments. On average 6.42 kg Ca kg−1 P was required for calcium phosphate precipitation, and 8.05 kg Fe kg-1 p was required for vivianite precipitation. The chemical demand for treating toothpaste manufacturing wastewater is significantly higher than conventional municipal wastewater treatment works, which typically require 0.83 kg Fe/kg P and contain 4–8 mg P L−1 (Prot et al., 2020). This can be attributed to the unique composition of the industrial wastewater which includes high amounts of other ions, such as up to 10 g Na+ L−1 and 6 g Cl− L−1 (Table 1), although our thermodynamic modelling did not indicate that these ions significantly affected the solubility of calcium or iron salts beyond what was expected from the co-precipitation of magnesium and other metals (Supplementary Figure S2). High ionic strength and salinity can inhibit nucleation, and crystal growth during chemical phosphate precipitation (Srivastava et al., 2021). Additionally, our study had a much higher phosphorus removal goal (99%) compared to the targets typically set for municipal wastewater treatment plants [95% removal in Sweden according to (Statistics Sweden Kommunala avloppsreningsverk, 2020)], along with a much higher initial phosphorus concentration in the influent wastewater. The chemical dosage required for phosphorus removal in wastewater treatment does not scale linearly as the removal target increases from 95% to 99% (Solon et al., 2017). As the concentration of phosphorus in wastewater decreases, achieving further removal becomes increasingly challenging due to the non-linear kinetics of chemical phosphate precipitation (Lu et al., 2024). Changes in wastewater chemistry and the reduced availability of phosphate ions slow down reaction rates and reduce precipitation efficiency (Lu et al., 2024).
Overall, the findings from this study have significant practical implications for managing phosphorus in industrial wastewaters. Upscaling the chemical phosphate precipitation process from bench-scale to pilot-scale demonstrated that achieving over 99% on-site removal requires careful optimization of reaction conditions and chemical dosages, including consideration of impurities that chemicals used in wastewater treatment could contribute to precipitated phosphate products. Recovering phosphorus as value-added products such as vivianite offer industries an alternative approach to comply with discharge regulations while creating additional economic benefits. However, as shown in this study, such value addition will require more complex wastewater treatment processes. The market for circular phosphorus and its derivates is already established and is expected to grow significantly in the future, driven by increasing demand in sectors such as agriculture, electronics, and energy storage (Mew et al., 2018).
4 Conclusion
This study demonstrated the feasibility of recovering phosphorus from high-load industrial wastewater from a toothpaste manufacturer as amorphous calcium phosphate and vivianite through bench-scale and pilot-scale experiments. The optimal dose of Ca(OH)2 and FeSO4.6-7H2O required for phosphate precipitation, as well as the operating conditions that maximised the removal of phosphate while minimising the residual concentration of unwanted ions such as Mg, Ca, and Fe were determined. Overall, the following optimal treatments were identified:
Amorphous Calcium Phosphate: A dosage of 24.5 g Ca(OH)₂ L−1 of wastewater effectively maximises apatite formation while minimising residual Ca2⁺ concentrations. Post-treatment, pH adjustment is necessary due to the increase in pH to over 12.5.
Vivianite: A dosage of 45 g FeSO₄·7H₂O L−1 of wastewater maximizes vivianite formation while minimizing residual Fe2⁺ concentrations. For optimal results, the raw wastewater pH must be adjusted with an alkali before treatment, but no further pH adjustment is required post-treatment. To achieve high purity vivianite recovery, it is essential to use chemicals of higher purity than those employed in this study for wastewater treatment.
Both the treatments resulted in 99% recovery of phosphorus, reducing the residual phosphorus concentration in the toothpaste manufacturing wastewater to below 20 mg L−1. Future research could focus on enhancing the yield and purity of the recovered phosphate products, optimizing process kinetics and post-processing techniques, conducting a detailed economic analysis, and addressing regulatory compliance challenges of treating industrial wastewater in decentralized treatment settings.
Data availability statement
The original contributions presented in the study are included in the article/Supplementary Material, further inquiries can be directed to the corresponding author.
Author contributions
DR: Conceptualization, Formal Analysis, Investigation, Methodology, Software, Visualization, Writing–original draft, Writing–review and editing. JJ: Data curation, Formal Analysis, Investigation, Methodology, Writing–original draft, Writing–review and editing. BV: Conceptualization, Funding acquisition, Methodology, Project administration, Resources, Writing–review and editing. PS: Conceptualization, Formal Analysis, Funding acquisition, Investigation, Methodology, Project administration, Resources, Supervision, Writing–original draft, Writing–review and editing.
Funding
The author(s) declare that financial support was received for the research, authorship, and/or publication of this article. This study was partially supported by funding from a private company. PS and DR was supported by a grant from Familjen Kamprads stiftelse for the project Urine Diversion 3.0 (Grant number 20230107). DR was also supported by internal funding from the University of Cape Town and the August T Larsson Guest Researcher Programme at the Swedish University of Agricultural Sciences.
Conflict of interest
The authors declare that the research was conducted in the absence of any commercial or financial relationships that could be construed as a potential conflict of interest.
The author(s) declared that they were an editorial board member of Frontiers, at the time of submission. This had no impact on the peer review process and the final decision.
Publisher’s note
All claims expressed in this article are solely those of the authors and do not necessarily represent those of their affiliated organizations, or those of the publisher, the editors and the reviewers. Any product that may be evaluated in this article, or claim that may be made by its manufacturer, is not guaranteed or endorsed by the publisher.
Supplementary material
The Supplementary Material for this article can be found online at: https://www.frontiersin.org/articles/10.3389/fenvs.2024.1491220/full#supplementary-material
References
Avdibegović, D., Nguyen, V. T., and Binnemans, K. (2022). One-step Solvometallurgical process for purification of lithium chloride to battery grade. J. Sustain. Metallurgy 8 (2), 893–899. doi:10.1007/s40831-022-00540-w
Bunce, J. T., Ndam, E., Ofiteru, I. D., Moore, A., and Graham, D. W. (2018). A review of phosphorus removal technologies and their applicability to small-scale domestic wastewater treatment systems. Front. Environ. Sci. 6. doi:10.3389/fenvs.2018.00008
Cabeza, R. A., Steingrobe, B., and Claassen, N. (2019). Phosphorus fractionation in soils fertilized with recycled phosphorus products. J. Soil Sci. Plant Nutr. 19 (3), 611–619. doi:10.1007/s42729-019-00061-8
Chen, L., Al-Bayatee, S., Khurshid, Z., Shavandi, A., Brunton, P., and Ratnayake, J. (2021). Hydroxyapatite in oral care products-A review. Mater. (Basel) 14 (17), 4865. doi:10.3390/ma14174865
Enax, J., and Epple, M. (2018). Synthetic hydroxyapatite as a biomimetic oral care agent. Oral health and Prev. Dent. 16 (1), 7–19. doi:10.3290/j.ohpd.a39690
He, J., Li, X., Wang, F., Jing, M., and Ciu, J. (2021). Determination of elemental impurities in lithium iron phosphate using ICP-OES. Thermo Fisher Scientific.
Jupp, A. R., Beijer, S., Narain, G. C., Schipper, W., and Slootweg, J. C. (2021a). Phosphorus recovery and recycling–closing the loop. Chem. Soc. Rev. 50 (1), 87–101. doi:10.1039/d0cs01150a
Jupp, A. R., Beijer, S., Narain, G. C., Schipper, W., and Slootweg, J. C. (2021b). Phosphorus recovery and recycling - closing the loop. Chem. Soc. Rev. 50 (1), 87–101. doi:10.1039/d0cs01150a
Kemacheevakul, P., Polprasert, C., and Shimizu, Y. (2011). Phosphorus recovery from human urine and anaerobically treated wastewater through pH adjustment and chemical precipitation. Environ. Technol. 32 (7), 693–698. doi:10.1080/09593330.2010.510537
Lu, X., Huang, S., Liu, H., Yang, F., Zhang, T., and Wan, X. (2024). Research on intelligent chemical dosing system for phosphorus removal in wastewater treatment plants. Water 16 (11), 1623. doi:10.3390/w16111623
Mew, M., Steiner, G., and Geissler, B. (2018). Phosphorus supply chain—scientific, technical, and economic foundations: a transdisciplinary orientation. Sustainability 10 (4), 1087. doi:10.3390/su10041087
Mittal, G. S. (2006). Treatment of wastewater from abattoirs before land application--a review. Bioresour. Technol. 97 (9), 1119–1135. doi:10.1016/j.biortech.2004.11.021
Morgan, B., and Lahav, O. (2007). The effect of pH on the kinetics of spontaneous Fe (II) oxidation by O2 in aqueous solution–basic principles and a simple heuristic description. Chemosphere 68 (11), 2080–2084. doi:10.1016/j.chemosphere.2007.02.015
Preisner, M., Neverova-Dziopak, E., and Kowalewski, Z. (2020). Analysis of eutrophication potential of municipal wastewater. Water Sci. Technol. 81 (9), 1994–2003. doi:10.2166/wst.2020.254
Prot, T., Wijdeveld, W., Eshun, L. E., Dugulan, A. I., Goubitz, K., Korving, L., et al. (2020). Full-scale increased iron dosage to stimulate the formation of vivianite and its recovery from digested sewage sludge. Water Res. 182, 115911. doi:10.1016/j.watres.2020.115911
Rao, S. R., and Varadaraju, U. (2015). Hydrothermal synthesis of LiFePO 4 nanorods composed of nanoparticles from vivianite precursor and its electrochemical performance for lithium ion battery applications. Bull. Mater. Sci. 38 (5), 1385–1388. doi:10.1007/s12034-015-1025-6
Simbeye, C., Courtney, C., Simha, P., Fischer, N., and Randall, D. G. (2023). Human urine: a novel source of phosphorus for vivianite production. Sci. Total Environ. 892, 164517. doi:10.1016/j.scitotenv.2023.164517
Simha, P., Deb, C., Randall, D., and Vinnerås, B. (2022). Thermodynamics and kinetics of pH-dependent dissolution of sparingly soluble alkaline earth hydroxides in source-separated human urine collected in decentralised sanitation systems. Front. Front. Environ. Sci. 10, 889119. doi:10.3389/fenvs.2022.889119
Solon, K., Flores-Alsina, X., Kazadi Mbamba, C., Ikumi, D., Volcke, E. I. P., Vaneeckhaute, C., et al. (2017). Plant-wide modelling of phosphorus transformations in wastewater treatment systems: impacts of control and operational strategies. Water Res. 113, 97–110. doi:10.1016/j.watres.2017.02.007
Srivastava, A., Parida, V. K., Majumder, A., Gupta, B., and Gupta, A. K. (2021). Treatment of saline wastewater using physicochemical, biological, and hybrid processes: insights into inhibition mechanisms, treatment efficiencies and performance enhancement. J. Environ. Chem. Eng. 9 (4), 105775. doi:10.1016/j.jece.2021.105775
Statistics Sweden (2020). Kommunala avloppsreningsverk: In- och utgående mängder och reningsgrad efter fördelningsvariabel och substans. Vartannat år, 2014–2020. https://www.statistikdatabasen.scb.se/pxweb/sv/ssd/START__MI__MI0106/MI0106T07/
Tayibi, H., Choura, M., López, F. A., Alguacil, F. J., and López-Delgado, A. (2009). Environmental impact and management of phosphogypsum. J. Environ. Manag. 90 (8), 2377–2386. doi:10.1016/j.jenvman.2009.03.007
Wang, R., Wilfert, P., Dugulan, I., Goubitz, K., Korving, L., Witkamp, G.-J., et al. (2019). Fe(III) reduction and vivianite formation in activated sludge. Sep. Purif. Technol. 220, 126–135. doi:10.1016/j.seppur.2019.03.024
Wijdeveld, W. K., Prot, T., Sudintas, G., Kuntke, P., Korving, L., and van Loosdrecht, M. C. M. (2022). Pilot-scale magnetic recovery of vivianite from digested sewage sludge. Water Res. 212, 118131. doi:10.1016/j.watres.2022.118131
Yetilmezsoy, K., Ilhan, F., Kocak, E., and Akbin, H. M. (2017). Feasibility of struvite recovery process for fertilizer industry: a study of financial and economic analysis. J. Clean. Prod. 152, 88–102. doi:10.1016/j.jclepro.2017.03.106
Zhang, J., Chen, Z., Liu, Y., Wei, W., and Ni, B.-J. (2022). Phosphorus recovery from wastewater and sewage sludge as vivianite. J. Clean. Prod. 370, 133439. doi:10.1016/j.jclepro.2022.133439
Keywords: chemical precipitation, crystallisation, nutrient recycling, resource recovery, industrial effluent, waste valorisation
Citation: Randall DG, Jalava J, Vinnerås B and Simha P (2024) Phosphorus recovery as vivianite and amorphous calcium phosphate from high-load industrial wastewater. Front. Environ. Sci. 12:1491220. doi: 10.3389/fenvs.2024.1491220
Received: 04 September 2024; Accepted: 23 October 2024;
Published: 07 November 2024.
Edited by:
Maria Elisa Magri, Federal University of Santa Catarina, BrazilReviewed by:
Kangning Xu, Beijing Forestry University, ChinaSarvajith, King Abdullah University of Science and Technology, Saudi Arabia
Copyright © 2024 Randall, Jalava, Vinnerås and Simha. This is an open-access article distributed under the terms of the Creative Commons Attribution License (CC BY). The use, distribution or reproduction in other forums is permitted, provided the original author(s) and the copyright owner(s) are credited and that the original publication in this journal is cited, in accordance with accepted academic practice. No use, distribution or reproduction is permitted which does not comply with these terms.
*Correspondence: Prithvi Simha, cHJpdGh2aS5zaW1oYUBzbHUuc2U=, cHJpdGh2aS5zaW1oYUBtZXNwb20uZXU=