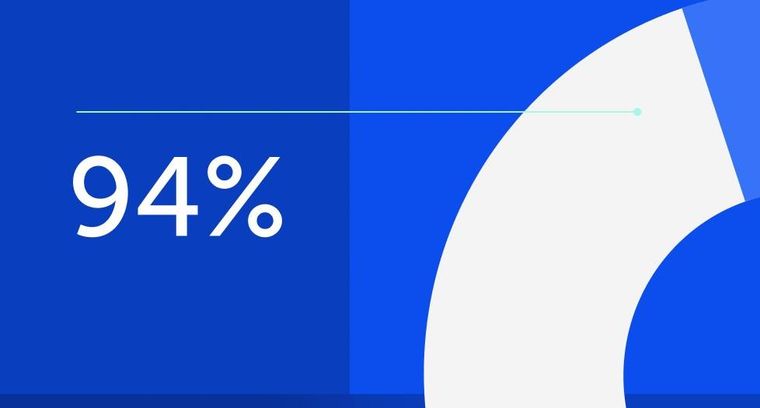
94% of researchers rate our articles as excellent or good
Learn more about the work of our research integrity team to safeguard the quality of each article we publish.
Find out more
REVIEW article
Front. Environ. Sci., 28 February 2024
Sec. Environmental Systems Engineering
Volume 12 - 2024 | https://doi.org/10.3389/fenvs.2024.1365162
This article is part of the Research TopicTextile Fiber Pollution from Source to SinkView all 6 articles
Each year, millions of tons of clothing are both produced and discarded, exerting a substantial impact on the environment and public health. Even when textile waste is disposed of in landfills, it persistently adds to pollution in the air, water, and soil. This review explores the diverse implications of textile waste, examining circular economy principles and highlighting opportunities for transforming textile waste into eco-friendly materials. This review highlights opportunities to repurpose textile waste into new products, aligning with the principles of a circular economy. The discussed materials, such as cotton, wool, polyester, nylon, and kevlar, can be utilized in various industries, including construction, non-woven, furniture, carpet, agriculture, and paper. The alternative materials presented offer excellent mechanical, thermal, and acoustic properties, providing sustainable alternatives in applications ranging from civil construction to insulation and structure reinforcement, minimizing environmental impact. Green material alternatives enhance cost-effectiveness in constructing eco-friendly buildings, reducing the need for extracting new raw materials and minimizing the carbon footprint. It is expected that research on opportunities for recovering textile waste will soon intensify, leading to the implementation of these new eco-friendly products.
In recent years, there has been a growing concern about environmental issues and high energy consumption. Ensuring the sustainability of energy resources and the environment has become one of the significant challenges of our time (Islam and Bhat, 2019). From an environmental perspective, the rapid growth in the global population, coupled with its escalating consumption rates and the growing tendency to dispose of materials in landfills as waste prematurely, poses significant obstacles to sustainability (Bergstrom and Randall, 2016).
Textile waste has a significant impact on the environment and public health, as millions of tons of clothes are produced and disposed of every year, causing a large accumulation of waste in landfills, with very negative consequences (Islam and Bhat, 2019; European Parliament, 2023). Waste management is important to minimize the consequences on the environment. The best strategies for reducing waste start with avoiding, reducing and reusing. At the end of the products’ life cycle, there are several approaches that can be followed: recycling, incineration, biodegradation and landfill (Muthu, 2020).
Circular economy aims to reduce excessive waste, promoting its use as a ‘raw material’ for the manufacture of new products. This allows economic growth to be decoupled from the negative consequences of resource depletion and environmental degradation (Neves and Marques, 2022).
The recovery and attribution of new applications to textile waste is currently possible through several reprocessing technologies, enabling its reuse within the textile industry or its utilization in emerging sectors such as construction, non-woven production industries, furniture and paper industries, automotive and agriculture (Bhatia et al., 2014).
This review article aims to delve into the multifaceted implications associated with textile waste, alongside a rigorous examination of the underlying principles governing the circular economy framework. The comprehensive elucidation of textile waste valorization constitutes a focal point of this analysis, wherein a meticulous exposition will be provided, elucidating numerous examples that highlight the transformation of waste into innovative materials. These new materials are mainly used for thermal and acoustic insulation and structural reinforcing. Incorporating thermal insulation in buildings plays a vital role in reducing energy consumption by minimizing temperature changes (Al-Homoud, 2005; Islam and Bhat, 2019). Sound insulation is also important to reduce the harmful effects of noise to which the population is constantly exposed (Islam and Bhat, 2019).
Every year, millions of tons of clothing and footwear are produced and discarded, according to the European Environment Agency, between 2000 and 2020 textile production almost doubled, from 58 million tons to 109 million tons. An increase up to 145 million tons is expected by 2030 (Islam and Bhat, 2019; European Parliament, 2023). In Europe, every year, each citizen uses about 26 kilos of textiles and discards about 11 kilos, with most of the used clothes (87%) being incinerated or landfilled (European Parliament, 2023). In the US only about 12% of clothing waste is recovered (Ütebay et al., 2019). It is estimated that every year more than 92 million tons of textile waste are produced (Niinimäki et al., 2020; Centobelli et al., 2022).
“Fast fashion” is the main culprit for this trend, because it is a business model based on offering consumers frequent novelty in the form of low-priced, trend-led product (Islam and Bhat, 2019; Muthu, 2020; Niinimäki et al., 2020). This concept probably explains the increase of clothes consumed per capita by 47% between 2000 and 2015 (Peters et al., 2021). These companies are characterized by the rapid ability to design, manufacture and distribute clothing, which allows them to respond quickly to changing trends and bring new styles to the market within weeks. This fact, alongside the low-prices associated, leads consumers to shop more frequently in order to stay up to date with the latest fashion trends (Islam and Bhat, 2019; Niinimäki et al., 2020; Bailey et al., 2022). These products are available at low prices, which is why companies often adopt measures to reduce production costs, such as using cheaper raw materials and producing in countries with lower labour costs (Bailey et al., 2022). Due to the low cost and rapid turnover of these products, consumers tend to understand fashion as disposable, buying clothes for the short term and quickly disposing of them (Islam and Bhat, 2019; Niinimäki et al., 2020). For example, some clothes are projected to be used only 10 times (McNeill and Moore, 2015). While fast fashion has gained popularity for its affordability and quick response to trends, it has also been criticized for its environmental and ethical impacts. The industry’s emphasis on low-cost production can contribute to environmental degradation, exploitation of labour in developing countries, and the generation of large amounts of textile waste (Islam and Bhat, 2019; Niinimäki et al., 2020; Bailey et al., 2022). In recent years, there has been a growing awareness and movement towards sustainable and ethical fashion practices as consumers seek alternatives to the fast fashion model (Centobelli et al., 2022).
Textile industry is the second most polluting and waste-generating sector in the world, accounting for 10% of total atmospheric carbon emissions (which corresponds to 1.7 billion tonnes of emissions) (Ütebay et al., 2019; Niinimäki et al., 2020; Baccouch et al., 2022; Centobelli et al., 2022) and 20% of global wastewater (79 billion l) annually (Islam and Bhat, 2019; Niinimäki et al., 2020; Centobelli et al., 2022; European Parliament, 2023). Furthermore, chemical treatments and dyes used in the manufacturing process are responsible for 35% of ocean pollution by microplastics (Niinimäki et al., 2020). In 2020, to produce clothes for each EU citizen around 9 m3 of water, 400 m2 of land and 391 kg of raw materials were required. For each citizen, around 270 kg of carbon was emitted, meaning that textile products consumed in the EU generated 121 million tons of greenhouse gases (European Parliament, 2023). CO2 emissions are expected to increase to nearly 2.8 billion tons until 2030 (Islam and Bhat, 2019).
The environmental impact of production varies according to the types of fibers, synthetic or natural. In Figure 1, the values of fiber production, water consumption, energy consumption and carbon dioxide emission for polyester, cotton, non-cotton cellulosic, polyamide, wool and helm are represented (Niinimäki et al., 2020). Polyester is the most used fiber in industries, representing a production of 54 million tons of fibers (Islam and Bhat, 2019; Niinimäki et al., 2020). In relation to the freshwater consumption, cotton has the highest, accounting for 1559l per kg of fiber. In textile industry, energy consumption and CO2 emissions are more increased during the initial fiber extraction, mainly synthetic fibers because they are from fossil fuels. To produce polyamide, 160 kWh are used per kg of fiber. One way to reduce CO2 emissions associated with fiber production is to replace synthetic fibers with natural fibers (e.g., wool and hemp). Wool and hemp have low carbon emissions of 17.0 and 3.1, respectively. Natural fibers (cotton, non-cotton cellulosics, wool and hemp) require less energy, but during their production they require significantly more water than synthetic fibers (polyester and polyamide).
When textile waste decomposes, several gases are released into the atmosphere, namely, methane. This powerful gas contributes significantly to greenhouse gas emissions because it absorbs the sun’s heat that radiates on the Earth’s surface and retains it in the atmosphere. This leads to an increase of Earth’s temperature, which is called global warming (Islam and Bhat, 2019). Non-renewable petroleum-based materials release gases during their decomposition, making a very harmful contribution to air, water and soil pollution (Baccouch et al., 2022).
In addition to these problems, this industry has a devastating impact on the health of local populations, animals and ecosystems where the factories are located (European Parliament, 2023).
According to directive 2008/98/EC of 19 November 2008 of the European Union Waste Framework Directive, the best waste management strategy is to prevent the waste (European Parliament and Council, 2008). Waste management began with the concept of 3Rs: reducing, reusing and recycling (Neves and Marques, 2022). Over the years, these concepts have evolved into 10Rs, as will be presented in section 4 (Morseletto, 2020). Reduce and reuse are some of the practices that help decrease the amount of waste. At the end of the lifespan of textile materials, there are several destinations that they can follow: recycling, incineration, biodegradation and landfill (Figure 2). (Muthu, 2020)
Reducing the consumption of textile products is a good practice, because it minimizes the amount of waste generated and uses fewer resources to produce new products. A good practice to reduce textile consumption is to opt for high-quality items that are more expensive, but perform better and, therefore, will last longer and cause less waste (Abdul-Rahman, 2014). Reuse, as the name suggests, refers to various means of extending the practical useful life of textile products, with or without prior modification, by transferring them to new owners (Sandin and Peters, 2018; Muthu, 2020). This can take two forms: primary: reuse for the same purpose; - secondary: reuse for a purpose other than that originally intended. This process can be achieved in several ways, such as collecting goods by charities, selling them in second-hand stores, donating them to loved ones, etc. In many countries, it is common to see bins collecting second-hand clothes with the intention of being distributed to people in need (Muthu, 2020). An example is Gekas Ullared’s (retail store), where its customers can since 2012 leave clothes, fabrics and toys to be donated to Human Bridge (a charitable organization). Buying second-hand clothes has also been increasing in recent years (Ekström and Salomonson, 2014). For post-consumer textiles, in environmental terms, this is the best option because it delays the disposal of the product and prevents it from being deposited in landfill before the necessary time. Furthermore, it also minimizes the production of new textile products (Muthu, 2020). The companies Lindez and Myrorna give a discount coupon if customers deliver old clothes. The objective is to increase customer awareness on the importance of giving their clothes a second chance (Ekström and Salomonson, 2014; Filho et al., 2019). In Brazil, there is a Reuse Fabric Bank that aims to extend the lifespan of clothing, fabrics and post-consumer waste from industries, allowing them to return to circulation and avoiding sending them to landfills prematurely. If one deposits the parts directly in this bank, they receive credits for each kilogram which can later be used to obtain other materials from the bank. The most common users are artisans, fashion and design students, stylists, among others (Broega et al., 2017; Filho et al., 2019). The environmental impact of reusing textiles is 70 times lower than producing new clothes. A recent study shows that it is possible to save 3 kg of CO2 for each garment reused and water use is only 0.01% of what it would be to produce a new garment (BIR, 2022). Another study demonstrated that by reusing pairs of trousers (made from 65% polyester/35% cotton) it is possible to reduce approximately 20% of natural gas and crude oil consumption, 25% of nutrient enrichment impact, 28% of acidification impact, 30% of soil toxicity and 45% of water toxicity during the production chain (Muthu, 2020).
Recycling refers to the destructuring of a discarded product after its use and subsequent processing of the resulting components for application in similar or different products. This approach is advantageous because it allows the use of resources (water and energy consumption) to be reduced, as virgin raw materials are replaced by these new materials, preventing the depletion of non-renewable resources. Recycling textile waste reduces carbon emissions in the life cycle of these products, thus reducing the greenhouse effect and, consequently, global warming and waste disposal in landfills is avoided/reduced (Muthu, 2020; Baccouch et al., 2022). Recycling can be divided into two categories: closed-loop: the recycled material returns to the same life cycle (raw material for the same product); - open-loop: the recycled material leaves its current life cycle and appears as a completely new product, with a new life cycle (Muthu, 2020; Baccouch et al., 2022). This process is generally downcycling so, in most cases, the quality of the recycled material is lower than the equivalent virgin material (Muthu, 2020). To improve the quality of the recycled product, for example, avoid mixing different fibers or using lower quality fibers, aiming for a product with a single fiber in its composition (Morley et al., 2009). Collection rates for potentially recyclable materials are still low. In Brazil, South Africa, Russia and China, collection rates are 12, 10, 11% and 20%, respectively. In more economically developed countries such as Canada, France and Italy, collection rates are 32% 40% and 43%, respectively (Filho et al., 2019). This is due to the existence of several obstacles to overcome in the recycling of textile waste (Filho et al., 2019; Muthu, 2020).Textile products are very complex, as they contain several types of materials such as metals, plastics, polymers, among others. Recycling is not always viable, due to the difficulty in separating these materials, given their different mechanical and technological properties (Marconi et al., 2018). The strength of textile fibers is also a challenge, because their strength complicates their crushing, which is necessary to convert the material back into raw material. Furthermore, there is also the presence of chemical materials and dyes that are toxic and carcinogenic, making the recycling process difficult. Consequently, this problem leads to the unavailability of recycled textile materials, due to insufficient quantities of suitable and accessible textile waste for recycling. One of the main reasons for the insufficient quantity of recyclable materials is the lack of technologies for sorting and separating textile waste for recycling. Existing technology also cannot separate dyes and other chemical contaminants from fibers. Automated sorting will improve the efficiency of the production process and increase the number of textiles suitable for recycling. In economic terms, the demand for recycled textiles is limited, because virgin raw materials have better quality and lower market prices. Recycled textile materials still have relatively high prices due to the high cost of recycling processes, plus transportation, which discourages potential investors. Economically, it is more attractive to use multiple textile fibers, as it makes the recycling process more accessible (Filho et al., 2019). The low recycling rate is also due to society’s low awareness of textile recycling. Currently, many countries prioritize the recycling of waste, such as glass, wood, paper, plastic and metal, while textile recycling is less prioritized and publicized (Anthouli et al., 2013).
Textile waste recycling has been thoroughly discussed in the literature. Dissanayake et al., conducted an extensive review on the topic and concluded that unblended cotton (50%) was the most frequently studied, followed by cotton and polyester blends (29%) (Dissanayake and Weerasinghe, 2021). The main method used for fabric waste managing was mechanical recycling, either by melt-extrusion (shredding, crushing, grinding, melting, and re-extruding into fibers, spun into yarns or directed towards non-wovens), or cutting, shredding and carding (construction and industrial sector applications) (Shen et al., 2010; El Wazna et al., 2017; Dissanayake et al., 2018; Peña-Pichardo et al., 2018). Chemical and biochemical strategies comprised 38% and 14% of the studies analyzed. Chemical methodologies follow one of two paths—either there’s depolymerization into the material’s monomer units, followed by repolymerization; or dissolution, where the waste’s constituents are separated, filtered and regenerated into fibers through the use of adequate solvents (Raj et al., 2009; Vadicherla and Saravanan, 2017). According to their findings, recycling follows mostly open-loop approaches (34%), with the construction and building sectors being the main contributors (Dissanayake and Weerasinghe, 2021).
A different approach for waste management is biodegradation, as it guarantees the effective disposal of a product and helps it complete its life cycle, without causing any impact on the environment. This process occurs through the chemical degradation of materials, which is aggravated by the action of microorganisms, namely, fungi, bacteria and algae (Leja and Lewandowicz, 2010; Muthu, 2020). The materials are converted into biomass, carbon dioxide and water. Biodegradation can be aerobic and anaerobic. If oxygen is present in the reaction medium, this is aerobic biodegradation and carbon dioxide is produced. Otherwise, it is anaerobic degradation (absence of oxygen) and methane is produced instead of carbon dioxide. The extent of biodegradation of materials depends on several factors such as ambient temperature, the amount of water available, the presence of microorganisms and chemical factors (for example, pH) (Muthu, 2020). Arshad et al. studied the degradation of fabrics (cotton, jute, hemp, linen, polyester and wool) for 3 months, under attack by microorganisms present in the soil, using two methods: in contact with the soil and in the absence of soil. When in contact with the soil, it was difficult to understand which fiber was most biodegradable because most of them are natural fibers, which are mainly made up of cellulose. In the absence of contact with the soil, jute and linen are the most biodegradable. Of the natural fibers, wool is the least biodegradable since its molecular structure and surface are very resistant, making it difficult for microorganisms to penetrate. As polyester is a synthetic material, microorganisms cannot degrade it, making it a non-biodegradable material (Arshad and Mujahid, 2011).
Textiles wastes consisting of a synthetic polymer alongside cellulose fractions pose danger to the environment and present potential towards biofuel production (Wojnowska-Baryła et al., 2022). Roughly 35%–40% of textile waste is constituted by cellulose, which can be harnessed to be used as a feedstock in the generation of products such as ethanol and biogas (Jeihanipour et al., 2010; Shen et al., 2013). Anaerobic biodegradation is often applied towards the production of biogas from textile waste (Juanga-Labayen et al., 2022), exploiting its biodegradable cotton content as a source for bioethanol biorefining and the production of biogas. (Wojnowska-Baryła et al., 2022). Examples of previous studies in which this textile waste management strategy was employed are summarized below, alongside processing conditions and main results (Table 1). Most methane-rich biogas textile sources for anaerobic digestion found consist of textile cotton wastes, mainly due to its high cellulose percentage (∼54%) (Raj et al., 2009). Studies have also described the possibility of producing methane from other textile related wastes through anaerobic digestion, such as sludges resultant from the textile dying process, posing an energetically and cost-effective alternative (Zhou et al., 2021).
TABLE 1. Biogas production from textile wastes under anaerobic degradation—adapted and modified from (Juanga-Labayen et al., 2022).
In addition to biogas, bioethanol production using textile waste as a feedstock in fermentation has been investigated, although far fewer studies have been developed (Table 2). Pre-treatments are determining in this process, notably improving ethanol yields. Cellulose feedstocks are often pre-treated in order to increase surface area and enzyme accessibility, through alterations in porosity and crystallinity. Attempts have been made using chemical treatments (alkali, organo-solvents), joint physical and chemical treatments (hydrothermal, acid pretreatments assisted by microwaves) and synergic combinations (organo-solvents, trailed by hydrothermal treatment) (Wojnowska-Baryła et al., 2022).
TABLE 2. Ethanol production from textile wastes—adapted and modified from (Wojnowska-Baryła et al., 2022).
Another approach to waste management is incineration. This involves burning waste under conditions and it has a negative impact on the environment and human health. Incineration can be carried out with or without energy recovery, with the former being preferably used, as, despite the negative impact, it also brings benefits (energy production). Incineration without energy recovery is not a desirable option (Muthu, 2020). Textile waste can be incinerated, but the incinerator often cannot accept large quantities because the long threads act as a fuse from incineration to waste storage. For this reason, industrial textiles are landfilled. However, this is decreasing with the addition of pre-treatments such as cutting and shredding (Palm, 2011).
The last and least desired option is to dispose of waste in landfills, which only generates negative effects on the environment and human health. In addition, problems such as space availability also arise, as in most countries current landfills are full (waste takes many years to decompose) and there is no more space to build new ones (Muthu, 2020). Only textile waste unsuitable for other waste management strategies can be disposed of in landfills (Rapsikevičienė et al., 2019). The Environmental Protection Agency revealed that in the United States, in 2015 around 12 million tons of clothing and footwear were discarded, of which more than 8 million tons ended up in landfills (Brewer, 2019). In Europe, only around 15%–20% of textile products are recycled. The 75%–80% was landfilled or incinerated (Sandin and Peters, 2018; Bailey et al., 2022).
Life cycle assessment is the process of evaluating or estimating the impact a product in its useful life has on the environment and human health, that is, from its production (including the extraction of raw materials) until elimination. For this estimate, emissions to air, water and soil are assessed during production, use and disposal of the product. After that, the assessed amount is related to possible environmental effects, including resource depletion, ozone depletion, global warming, among others (Asdrubali et al., 2015; Islam and Bhat, 2019).
In a linear economic system (Figure 3), raw materials are taken from the environment and converted into final products that will be disposed of at the end of their useful life. These products are often designed for a single purpose and have a short shelf life, leading to a large accumulation of waste (Sariatli, 2017; Neves and Marques, 2022). A traditional linear economy, without processes such as recycling, is not sustainable and, therefore, must be replaced by a circular system (Geisendorf and Pietrulla, 2018).
FIGURE 3. Scheme of the linear economy system and circular economy system. Adapted from (Ellen Mac Arthur Foundation, 2019).
The circular economy (CE), often termed a “closed-loop economy”, prevents the generation of excessive waste by transforming it into valuable resources for producing new goods (Figure 3). This economy model extends the useful life of products and restores and regenerates them, guided by regenerative design (Geisendorf and Pietrulla, 2018). CE’s objective is to create a sustainable development, generating a method to create economic growth without depleting resources and degrading the environment (Jørgensen and Pedersen, 2018; Morseletto, 2020; Webster, 2021; Neves and Marques, 2022). It began with the concept of reducing, reusing and recycling (known as the 3Rs), essential for the waste management process (Section 3) (Neves and Marques, 2022) It has since extended to 10 Rs: “refuse, rethink, reduce, reuse, repair, refurbish, remanufacture, repurpose, recycle and recovery” (Table 3). Rethink is part of a strategy of smarter product use and/or manufacture and it can be applied before production starts (companies) or before acquiring the products (individuals). Rethink principle encourages individuals and businesses to reconsider their consumption patterns and make more mindful choices. On the individual’s point of view, it involves questioning and reevaluating the necessity of purchases, as well as assessing product’s environmental and social impacts (Morseletto, 2020). Companies should integrate environmental considerations into the design process, like ecodesign, since the product design phase plays a crucial role on environmental impacts (Delaney et al., 2022), as this phase can be responsible for 80% of products’ sustainability performance (Riesener et al., 2023). Ecodesign is part of the rethink strategy as an approach to designing products, processes, and systems, which during the design phase considers factors such as type and quantities of resource used, energy efficiency, waste reduction, and the overall ecological footprint (Kirchherr et al., 2023; Morseletto, 2023). This process is carried out to extend the final product’s life and turns these products’ recycling less complex. Besides all environmental concerns, ecodesign also considers social and ethical needs. By integrating environmental considerations into the design process, ecodesign aims to contribute to a more sustainable and ecologically responsible future (Riesener et al., 2023). In 2005, the European Commission wrote the first directive on ecodesign for energy-using products (European Parliament, 2005), nonetheless revoked by 2009/125/EC Framework Directive (EUROPEAN PARLIAMENT et al., 2009) which includes any good that could have an impact on energy consumption during its use know as energy related products. Recently, the EU proposed regulation on ecodesign, which established a framework for ecodesign requirements for sustainable products (EUROPEAN PARLIAMENT AND COUNCIL, 2022), the main instrument to guide product design phases and life cycles with continuous improvements (Bundgaard and Huulgaard, 2023). This regulation focused on two major aspects - the importance given to substances of concern, and the establishment of a digital product passport that may introduce changes on the perspective for the textile production, helping the transition to a non-toxic circular economy. Ecodesign means the integration of environmental sustainability considerations into the characteristics of a product and the processes taking place throughout the product’s value chain (EUROPEAN PARLIAMENT et al., 2009).
TABLE 3. 10 Rs inserted in the circular economy concept (Morseletto, 2020).
The combination of all these concepts defines an economic model that, in addition to minimizing the extraction of raw materials and natural sources, transforms end-of-life materials into a resource for new materials, closing cycles in industrial ecosystems and minimizing waste (Morseletto, 2020; Neves and Marques, 2022).
However, drawbacks, such as not enough investments to introduce the CE in the sector, no internationally recognized normative institutions to regulate the sector, insufficient and ineffective public opinion on the topic have been hindering its progress (Sariatli, 2017; Jørgensen and Pedersen, 2018).
The CE is therefore beneficial and fundamental to society, leading industries into a more efficient and environmentally friendly future (Sariatli, 2017; Jørgensen and Pedersen, 2018). The execution of CE within global economy is essential to ensure human life on planet Earth in the long term (Geisendorf and Pietrulla, 2018). So, a transition from the linear economy to the CE is essential and urgent. (Sariatli, 2017).
In respect to LCA studies on textiles, Chopra et al. (2023) compiled goals reoccurring in the literature, presented below with adaptations (Table 4). According to the authors, The Higg Index allows the benchmarking of textile life cycle impacts in the sector, systematically assessing the processes involved, regarding material/energy flows, and quantifying the environmental impacts associated with developing valorization methods. Their review showed that the life cycle production phase of textiles and its use phase are the most studied, in that order; however, analyses on the impact of the end-of-life stage is yet to be developed (Chopra et al., 2023).
TABLE 4. LCA studies regarding textile producing and its environmental impact published in the recent decade. Adapted and modified from (Chopra et al., 2023).
Textile waste comes from various sources, such as household use and waste from production lines, both of which are increasing considerably. Based on sources, textile waste is classified as pre-consumer/post-industrial (PCPIW) and post-consumer waste (PCW). PCPIW refers to material discarded during the manufacturing process of textile materials (yarns, cuttings, mill ends, damaged goods, etc.), before it is used by the consumer. It is generated from natural and synthetic fibers production, spinning, weaving, knitting, dyeing, printing, finishing, designing, and cutting, wholesalers, trading companies, retailers and mass merchandise chains. Typically, PCPIW can be recovered and reused as raw material for the automotive, furniture, non-wovens and other industries. PCW refers to a product the consumer has used and that no longer serves a need, being subsequently disposed of. This waste can also be recovered and recycled, a practice that is only enacted in a low percentage of cases (Bhatia et al., 2014; Islam and Bhat, 2019; Rapsikevičienė et al., 2019; Patti et al., 2020).
Currently, resorting to several reprocessing technologies, it is already possible to recover fibers from textile waste and assign them a new application. High quality fibers can be obtained from PCPIW; however, if recovered at the end of the material’s life, they’ll present lower quality. The recovered fibers can be once again used in the textile industry or be given new applications, such as in the building, non-woven, furniture, carpet, agriculture and paper industries (Table 5). They can be spun into new yarns for the production of fabrics, knitting or non-woven fabrics, upholstery materials, biomaterial composites, insulation materials, among others (Bhatia et al., 2014).
In the literature, there are already several examples of new materials incorporating textile waste (cotton, polyester, EVA, leather, wool, etc.) such as, non-woven structures and composites, produced from PCPIW and PCW. In the sections below, several examples of both types of waste will be described, but mainly from PCPIW. Most of the new materials produced feature acoustic and/or thermal insulation capabilities. The use of efficient thermal insulation materials reduces energy consumption by minimizing heat losses and gains during the heating and cooling of the building (Al-Homoud, 2005). In domestic buildings, good thermal insulation can reduce energy consumption by around 65% (Hadded et al., 2016). Sound insulation is also key in reducing the harmful effects of noise that the population is constantly exposed to. The gradual increase in noise pollution is due to various factors such as urbanization, industrialization, increased use of vehicles, electrical and household and industrial mechanical appliances. Noise pollution is responsible for a number of negative health effects, encouraging the incorporation of insulation materials into buildings, cars, etc (Islam and Bhat, 2019)
The production of non-wovens is one of the applications for the recovered textile waste. Non-wovens consist of a backbone of dense, porous fibers, making them ideal materials for insulation (Islam and Bhat, 2019; Wazna et al., 2019). These can be produced from textile waste, either in the form of fibers or polymers, and different fibers can be used simultaneously. The use of these fibers increases price accessibility, since they replace the virgin raw material (Bhatia et al., 2014). In some cases, non-wovens can be subjected to high temperatures and pressures to produce composite materials (Islam and Bhat, 2019).
When processing a non-woven structure, one starts by transforming the loose fibers into different webs with different area densities. After the formation of the web, a connection between the fibers is necessary to increase the strength and stability of the material. There are three bonding processes available: chemical (latex or chemical reagents), thermal (airlay) and mechanical bonding (needle-punching). The selection of web formation and bonding processes depends on the type of fiber, required strength, density, thickness and the desired end-use properties of the non-wovens produced (Islam and Bhat, 2019). In chemical bonding method (Figure 4A), binders are applied to the unbonded web. These binders can be latex or chemical agents that form a colloidal system in which a high molecular weight polymer is dispersed in water. Binders can be applied using different technologies, such as impregnation in a foulard, spray bonding, by kiss roll application or via binder print. The addition of specific characteristics, such as, for example, hydrophilic/hydrophobic, flame retardant, abrasion resistant, is possible by adding binding agents or special additives. After applying the binders, different drying systems (drum, can or band dryers) are applied to evaporate the water and consolidate the web (Kamath et al., 2004). The airlay technology (Figure 4B) is based on mixing and placing fibers in layers, which are then pressed between rollers in a heated chamber. The temperature depends on the origin of the bicomponent fibers and the pressure of the desired bulk density (Zach et al., 2016; Drochytka et al., 2017). In the needle-punching technique (Figure 4C), a barbed needle is used which is driven up and down through webs of fiber. These needle actions interlock the fibers and help hold the structure together by frictional forces. This process consolidates the structure of the fibrous web without any toxic binders by interlacing the fibers. Non-woven quality is defined by needle geometry, needle density, needle mounting geometry on the needle plate and process parameters such as penetration depth and number of stitches per m2. (Maity et al., 2012; Wazna et al., 2019).
FIGURE 4. Scheme of non-woven structures production methods. (A) Chemical; (B) Airlay; (C) Needle-punching.
Below will be presented several examples of non-woven structures produced from different textile waste and by different methods (Table 6). All examples described revealed good thermal and/or acoustic and mechanic properties, to be applied in the construction, automobile industries or agriculture.
For application as thermal insulation, non-woven structures were produced from silk cocoon waste (PCPIW), by needle-punching method. The samples as they have superior thermal insulation value (0.212 m2K/W) compared to commercial product, are good options to be used as environmentally friendly and low-cost thermal insulation materials, for the automotive, furniture and clothing industries (Kumar et al., 2022). Wazna et al. prepared non-woven samples to produce insulation materials from PCPIW such as acrylic and wool, with fiber lengths from 40 to 50 mm. The technique used was needle-punching, with puncture density parameters of 90 punctures/cm2 and 300 strokes per minute. Thermal conductivity values are between 0.035 and 0.049 W/(mK), which is comparable to conventional insulation materials (Wazna et al., 2019). Gounni et al. also used shredded acrylic fibers (PCPIW) to produce thermal insulation materials for building construction, using the same technique. The thermal conductivity and air permeability are close to that of standard building materials (Gounni et al., 2018).
For acoustic insulation, Fera et al. produced several non-woven structures, from cotton selvedge waste (Figure 5), by needle-punching method. The study revealed that the sound absorption coefficient (α = 0.230–0.930) of all samples increases with the increasing frequency level (500–3,000 Hz). These samples are suitable for acoustic insulation. (Fera et al., 2022).
FIGURE 5. Cotton selvedge waste (Fera et al., 2022).
For thermal and acoustic insulation applications, Patnaik et al. developed non-wovens from wool and polyester of PCPIW, using the needle-punching technique. The composition of the non-wovens varied in the percentage of wool and polyester, number of layers and thickness. To increase fire retardancy and moisture resistance properties, a mixture of di-ammonium phosphate and sodium tetraborate (5% by weight) and silicon (1% by weight) was also added. The values obtained for thermal conductivity and sound absorption coefficient are between 0.030 and 0.038 W/mk and 0.340–0.580 (at 1,000–2000 Hz), respectively (Patnaik et al., 2015). Cai et al. also used wool fibers PCPIW (28 µm of diameter) to produced non-wovens, mixing them with virgin wool fibers in a 1:1 ratio, applying the needle-punching method. The acoustic and thermal resistance properties were superior to those of commercial materials, deeming them a great choice for the automobile industry (Cai et al., 2021). Using polyester PCPIW, Trajkovic et al. also produced thermal and acoustic insulation structures. Four types of polyesters were used (Figure 6), differing in the type of waste cut, amount of fiber, recycled/virgin and mixed with lycra and/or cotton. The waste was wrapped in a 100% PP non-woven to form the insulation frame. The measured values for thermal conductivity (0.052 and 0.060 W/mK) of the samples are similar to commercial thermal insulation materials. After performing the acoustic tests, the authors found that, regardless of the structural characteristics of the fabric from which the samples were made or the method of preparing the clippings, in terms of human perception, the differences in sound absorption were not significant (Trajković et al., 2016).
FIGURE 6. Samples of the 4 types of polyesters used to produce the final structures. (Trajković et al., 2016).
Selvedges (PCPIW) can also be used to produce non-wovens. Bogale et al. used cotton and polyester selvedges, using the chemical method, produced several non-woven structures. These samples have thermal and acoustic properties identical to conventional materials (Bogale et al., 2023).
Resorting to the airlay method for web formation, Zach et al. also produced thermal and acoustic insulation materials from PCW such as polyester fibers, linen and recycled cotton. The average thermal conductivity and absorption coefficients of materials were 0.036–0.050 W/mk and 0.350 to 0.60, respectively (Zach et al., 2016). Sakthivel et al. also manufactured non-woven structures from cotton and polyester PCPIW, separated and mixed. To aid in the process, polyvinylacetate (PVA) was used as a binder. The samples produced demonstrated good thermal (λ = 0.120–0.130 W/mK) and acoustic (α = 0.150–0.360) properties (Sakthivel et al., 2020). Using the same method and polyester fibers (PCPIW), Drochytka et al. produced insulating material incorporating residues of the polyvinyl chloride (PVC) matrix in the form of granules (Drochytka et al., 2017). The panels produced in the three aforementioned studies showed similar properties to commercial insulation panels used in civil construction, thus contributing to ecological construction (Zach et al., 2016; Drochytka et al., 2017; Sakthivel et al., 2020).
Geotextiles can also be produced using textile waste. Leon et al. produced non-wovens from knitted articles of polyacrylonitrile (PCW) and polyester (PCPIW) wastes, using PP as matrix. The study confirmed that it is possible to apply these geotextiles in the circular textile industry in Romania (Leon et al., 2016). Abidi et al. also developed non-wovens from waste cotton (PCPIW and PCW), for application in agriculture. This study aims to replace the plastic films that are usually used for agricultural mulching. The results revealed good resistance to accelerated climatic conditions and insignificant degradation. In addition, the thickness of the samples can also combine soil moisture retention with good soil heating properties. The samples developed appear to be a promising alternative to be applied in agriculture (Abidi et al., 2021).
More and more industries are looking for alternative materials for their products and all of these examples can be used.
Textile wastes can likewise be used to produce composites by applying heat and pressure. Textile waste can first be converted into non-wovens or be used directly as is. In the production of composites, various mixtures and layers of fibers can be applied, and it is also common to use polymers as blinders (Islam and Bhat, 2019).
Processes for producing composites from textile waste will be described below, using various techniques such as compression molding (CM), vacuum infusion (VI) and thermoforming (TF) (Kutz, 2011; Spasojevic, 2019; Greene, 2021; Dumont et al., 2023). CM (Figure 7A) is a very simple technique for processing polymer composite materials, which can have thermosetting, thermoplastic or fibrous materials as matrices. This method involves pressing/compressing a load of deformable material between two-halves of a heated mold and its subsequent transformation into a molded part, after cooling. The equipment typically involves a large tonnage press and heated dyes. Often, the equipment is connected to a water source, which allows the material to heat up, but mainly allows the part to cool down faster, reducing the equipment’s usage time. This process is attractive because it is easily automated and can be used to produce very complex geometries without any waste (Greene, 2021; Dumont et al., 2023). VI method (Figure 7B) uses the force of a vacuum to remove air from the reinforcing material, so that the resin can subsequently infiltrate better. First, the mold is coated with gel and the material is placed under the mold and covered with a perforated release film. Vacuum is applied to compact the material, without applying resin. The resin is infused only after complete vacuum. This method is advantageous because the mechanical properties of the composites are superior (Spasojevic, 2019). TF process (Figure 7C) once again uses heat and pressure to transform a flat mold (reinforced or unreinforced) into a desired three-dimensional shape. The process involves heating a sheet (monomaterial, coextrusion or laminate) of uniform thickness, which is stretched over a mold to form a rigid or semi-rigid shape. The disadvantage of this method is that there is waste of material, which has to be trimmed after the article is molded (Kutz, 2011).
FIGURE 7. Scheme of composites production methods. (A) Compression molding; (B) Vacuum infusion; (C) Thermoforming.
Below will be described several examples of composites produced from textile waste, mainly from PCPIW. In Table 7, there is a summary of all the studies presented, which were ordered according to their properties.
There are several composites incorporated with textile waste with good mechanical properties, for application, for example, in civil construction. Meng et al. produced composites from denim fabric waste (PCPIW) and epoxy resin. First, non-wovens are produced from the waste, using the needle-punching method. Then, epoxy resin was used as a binding agent and, by VI method, the final composite was produced (Meng et al., 2020). In another study, composites structures were produced from denim trim scrap combined with PP. By CM, different composites were produced, in sandwich and multilayer structures. In general, the mechanical properties decreased and this is due to the fabric’s stiffness being lower than that of the PP matrix, so instead of reinforcing the material, it weakens it. On the other hand, the tensile test showed little or no plastic deformation in the invoice area, meaning that the fabric inhibits the plastic deformation of the matrix which, in itself, is only capable of doing so if subjected to heavy loads. Compared to traditional composites, the stiffness of these new composites is lower, but they have greater resistance than composites. More studies are still needed to understand the possible application of these composites in the development of new products (Gómez et al., 2016).
Mishra et al. also studied the incorporation of cotton (PCPIW textile) waste into composites, using PP as a matrix. The method used was CM and several samples were made with different proportions of materials. The study of the mechanical properties of green composites revealed that textile waste can be safely used as a reinforcing structure in the manufacture of composites (Mishra et al., 2014). In another study, composites were also produced, by VI method, from cotton and jute (PCPIW) wastes, using polyester resin as the matrix. These materials have good mechanical properties and are a good option to reduce costs and solve the problem of waste disposal (Karahan et al., 2018). In addition, Ailenei et al. produced panels (Figure 8) from PCPIW and PCW PP films, by TF method. The objective of the study was to improve mechanical properties and replace traditional wood-based oriented strand boards. The results obtained showed that the new composite materials developed are an efficient solution and the mechanical properties are significantly higher than the traditional material (Ailenei et al., 2021).
FIGURE 8. Composite panel incorporating with waste: (A) pre-and (B) post-the technological TF process (Ailenei et al., 2021).
One of the most common applications for composites is acoustic insulation. Barbanera et al. produced composites out of leather waste from PCPIW using PVA as a blinder for building insulation. The molds were cold compacted and under pressure in a hydraulic press. A reduction coefficient of 0.200 and 0.460 and transmission loss values of 25–42 dB and 25–33 dB were obtained, respectively. These results are in the same order of magnitude as other insulation panels used, revealing their potential in insulation applications (Barbanera et al., 2020). Utilizing textile fabrics waste and CM method, Juciene et al. produced acoustic panels with threads disassembled from fabrics and leftovers in a square shape, employing corn starch as a binder in a ratio 1:1. The acoustic properties showed results similar to commercial panels for application in civil construction (Juciene et al., 2022).
Stemming from cotton and polyester textile (PCPIW), Dissanayake et al. produced insulation materials, selecting natural rubber as the bonding agent. Samples were produced by the CM technique under heat and varying analyzing temperatures and panel thickness. Samples’ NRC values ranged in between 0.500 and 0.700 (Dissanayake et al., 2021). Also using cotton and polyester textile (PCPIW), del Rey et al. also developed acoustic panels, by the same method. These panels differed in type and amount of binder used (pure polyester or phenolic resins) and density and thickness of the samples (del Rey et al., 2015). In these two studies, the acoustic properties were comparable to those of commercialized products (del Rey et al., 2015; Dissanayake et al., 2021). Baccouch et al. used cotton, polyester (PCW) and cotton/polyester non-woven waste mixed with epoxy resin to produce panels destined for automobile or construction applications. The epoxy resin was injected inside the non-woven structures, using the VI method, without the use of compatibilizers. Mechanical and acoustic tests deemed the composites appropriate for the intended applications (Baccouch et al., 2022). Textile waste (polyamide and polyacrylic) from PCPIW when mixed with polyurethane (PU) foam also forms composites that can be used for acoustic insulation (α = 0.000–0.880 and NRC = 0.280–0.600). The composite materials obtained have better sound absorption properties compared to rigid PU foam (Tiuc et al., 2016).
Composites incorporated with waste also have good thermal properties. Dissanayake et al. produced thermal insulation panels from nylon fibers (PCPIW) mixed with spandex and PU in different amounts, proving the usage of CM as a technique is also adequate. The best thermal conductivity value (0.095 W/mK) was shown for a composition of 60% nylon mixed with spandex and 40% ground PU. This panel has similar properties to commercially purchased products (Dissanayake et al., 2018). Wool fiber waste (PCPIW) can also be used to produce composites, by CM, with good thermal insulation properties (λ = 0.034–0.039 W/mK). Hassanin et al. mixed wool waste with Tetra Pak® waste in different proportions, using glass fibers and jute fibers as binders (Hassanin et al., 2018). Valverde et al. used polyester and PU from PCPIW to produce new thermal insulation panels employing the TF method. The thermal conductivity of the panels obtained ranged between 0.041 and 0.053 W/mK, similarly to other commercial insulating materials (Valverde et al., 2013).
Some authors studied both the thermal and acoustic properties of the composites they produced. Using CM method, based on textile waste (PCPIW) and industrial wastepaper, Ricciardi et al. produced composites, applicable in civil construction. Glue was used as a binding agent. Thermal behavior is similar to other commercially available composites, with k-values between 0.034 and 0.039 W/mK. The noise reduction coefficient (NRC) of these samples varies in the 0.230–0.380 range (Ricciardi et al., 2014). From recycled Kevlar fibers, nylon, polyester and PP (PCPIW), Lin et al. also produced composites. Before compression, these fibers were transformed into non-wovens. The study of the acoustic properties led to the conclusion that, in this case, the passage of the non-woven through the CM decreases the absorption coefficient throughout the studied frequency. This has to do with the fact that hot pressing decreases the spacing between the fibers and increases the rigidity of the composite. Once again, the thermal properties of the samples were in line with conventional materials (λ = 0.026 a 0.046 W/mK) (Lin et al., 2016). Rubino et al. used copolyester/polyester as binder for the production of non-wovens from wool waste (by airlay method). These non-wovens were later converted into composites by CM. The materials have good thermal (λ = 0.044–0.057 W/(m/K)) and acoustic properties (α = 0.700–1.000) for sustainable application in civil construction (Rubino et al., 2021).
A new application for these composites can also be addictive manufacturing. Haque et al. proposed a waste wool (PCPIW)/PCL composite filaments for 3D printing, maintaining cleaner manufacturing principle as a sustainable low-energy consuming method. First, waste wool/PCL pellets were produced using a twin-screw extruder. From these pellets, a desktop extruder was used to produce the 3D printing filaments. The results suggest that the tensile properties (yield strength, modulus and elongation at break) are comparable to the innate properties of PCL. As such, these filaments can be used to print various products, such as toys, household items, containers for medicine or packaging and industrial tools (Haque et al., 2023).
All these studies demonstrated the great potential that exists in incorporating textile waste into composites.
In addition to non-woven and composite structures, there are other applications that can be given to textile waste. In Table 8, other opportunities for valorization of PCPIW are described, which can be applied in cement matrices, agriculture, energy production, enzyme production and packaging (Rajput et al., 2012; Hu et al., 2018; Nunes et al., 2018; Abdallah et al., 2019; Sadrolodabaee et al., 2021b; 2021a; Rizal et al., 2021).
In the building industry, it is also possible to combine PCPIW with cement matrices. Rajput et al. studied combinations of cotton and paper waste and cement to develop bricks to be used in the building industry. The tests showed that the addition of 1%–5% of cotton and 10% of a mixture of cement, cotton and paper, increased the compressive strength compared to conventional clay bricks (Rajput et al., 2012). Sadrolodabaee et al. studied the incorporation of textile waste as internal reinforcement agents for cementitious matrices to increase ductility and cracking control. First, they produced polyester, cotton and linen non-wovens, by needle-punching technique. Mortar (a mixture of water and cement) was then added to these structures. This mixture was aspirated and compressed in order to form the final mold. These composites showed good results in terms of tenacity and post-cracking stress capacity, thus confirming the viability of using textile waste as internal reinforcement agents (Sadrolodabaee et al., 2021b; 2021a).
In agriculture, the incorporation of waste is also advantageous. The addition of wool waste (PCPIW) to the soil during the cultivation of maize and sunflower increases the nitrogen content in the soil, replacing the use of fertilizers (Abdallah et al., 2019).
Energy production is another opportunity for sustainable valorization of textile waste. Nunes et al. took cotton PCPIW and compressed it into briquettes to produce thermal energy. The briquettes were able to heat a boiler that produced 2 tons of steam per hour at 10 bar. Compared to wood briquettes, this alternative showed a lower cost (Nunes et al., 2018).
Textile wastes can also be used as nourishment for enzyme production due to its low cost. Cotton and polyester wastes (PCPIW) in several ratios were used in the fermentation process of Aspergillus niger CKB, under a nitrogen atmosphere, to obtain cellulase enzyme. In addition to obtaining cellulase, a partial recovery of glucose from cotton was also possible (Hu et al., 2018).
In a different approach, Rizal et al. used textile waste to extract cellulose nanofibrils. From cotton fabrics waste, it was possible to extract cellulose through alkaline hydrolysis. This cellulose was used to reinforce biodegradable composites of polylactic acid and chitosan. The filament was produced using an extruder. The mechanical properties increased due to the presence of cellulose. The wettability properties of the biocomposite showed its hydrophobic nature. Therefore, this biocomposite is a great choice for packaging application, as these materials must be mechanically resistant and water repellent (Rizal et al., 2021).
In this chapter, numerous examples of recovery opportunities that can be made from textile waste were described. These alternative materials are advantageous because they are low-cost, environmentally friendly and also help to reduce the amount of textile waste on the planet and minimize the carbon footprint during the waste disposal process.
This literature review introduces various innovative materials, including non-wovens and composites, which incorporate textile waste. These materials exhibit mechanical, thermal, and acoustic properties that rival or surpass those of conventionally employed materials in similar applications.
In general, there is a tendency for textile waste to be used as thermal/acoustic insulating materials. Regarding thermal properties, all non-woven (=0.012–0.049 W/mK) and composite (λ = 0.026–0.062 W/mK) structures presented have acceptable thermal conductivity values for application as thermal insulation materials. Within non-woven structures, it is worth highlighting the sample produced by Sakthivel et al. (Sakthivel et al., 2020), from polyester and recycled cotton, as they present the best thermal conductivity values (λ = 0.120–0.130 W/mK). Within the composites, the structure produced from recycled Kevlar showed the best thermal conductivity, 0.026 W/mK (Lin et al., 2016). In general, composites have higher thermal conductivity values than non-woven structures. This happens because non-woven structures are more porous, that is, they have more air spaces inside, preventing air movement and loss through radiation (Song, 2009).
Regarding acoustic properties, the absorption coefficient values are between 0.100–1.000 and 0.000–1.000 for non-woven and composite structures, respectively. Within the non-woven structures, samples from (Drochytka et al., 2017; Fera et al., 2022), made from polyester and recycled cotton, show the best results, recording a maximum absorption coefficient of 0.990. For composite structures, the sample made with recycled wool from Rubino et al. presents the best absorption coefficient values, 0.700–1.000 (Rubino et al., 2021).
Other alternatives to using waste as insulation are beginning to be studied, such as, for example, the introduction into cement matrices, fertilizers, production of enzymes, etc. The use as fertilizers and in the production of enzymes is due to the fact that some types of textile waste are organic and biodegradable materials.
All the examples described in this review are in line with the concept of circular economy, as textile waste is transformed into new products with added value. This prevents the excessive generation of waste and its accumulation in landfills, which are harmful to the environment and public health. Furthermore, by incorporating these wastes into the production of new products, the need for virgin raw materials is also reduced. Despite the advantages that these new materials present, there are also some disadvantages, such as the use of glues and resins as binders, which are harmful. It is also necessary to carry out studies on the cost of producing materials on a large scale, as companies tend to buy the cheapest materials.
In the future, it is expected that companies will begin to adopt these sustainable practices and that manufacturing techniques for these new green materials will become increasingly accessible. Due to the growing interest of companies in environmental sustainability, the application of these materials is also expected to increase, particularly in civil and automotive industries. It is also expected that studies on the incorporation of textile waste in applications for agriculture and 3D printing filaments will increase.
These new materials contribute to cost-benefit, to the reduction of textile waste, to the reduction of the use of virgin raw materials, among others. In short, it is expected that these alternative materials will help minimize the carbon footprint and the harmful consequences that the planet has suffered.
In this review paper, an extensive overview on disposal and recovery of textile waste has been compiled. Millions of tons of clothing are produced and disposed of every year, causing immeasurable consequences to the environment and human health. For this reason, the concept of circular economy has emerged, according to which no excess waste is generated as it becomes a starting point for the production of new materials. There is not yet an innovative universal solution for textile waste management, but reduce, reuse and recycling practices have already positive and significantly impacted air, water and soil pollution. Recovered textile waste can be used to manufacture non-wovens, composites or cementitious matrices, new materials that can be employed as thermal and acoustic insulation, upholstery materials, biomaterial composites, among others. Based on these literature findings, recovery of textile waste and its use to produce new materials is essential. The low costs of new materials, the decrease in raw material extraction and the reduction of environmental impact justify the active implementation of the circular economy concept in this sector. It is urgent and essential to develop new materials from existing waste for the preservation of the environment and the continuation of human life on planet Earth. In the near future, there is an anticipation that research into opportunities for reclaiming textile waste will grow, marking the exponential growth of the implementation of these novel eco-friendly products.
DA: Writing–original draft. MB: Writing–original draft. RF: Supervision, Writing–review and editing. DF: Writing–original draft, Writing–review and editing.
The author(s) declare financial support was received for the research, authorship, and/or publication of this article. The authors acknowledge the financial support from integrated project BioShoes4all—Textile Bioeconomy (Investment TC-C12-I01, Sustainable Bioeconomy), promoted by the Recovery and Resilience Plan (RRP), Next-Generation EU, for the period 2023–2026. The authors are also thankful to project UID/CTM/00264/2023 of 2C2T—Centro de Ciência e Tecnologia Têxtil, funded by National Founds through FCT/MCTES- Fundação para a Ciência and DF is thankful to CEECIND/02803/2017, founded by National Founds through FCT/MCTES.
The authors declare that the research was conducted in the absence of any commercial or financial relationships that could be construed as a potential conflict of interest.
All claims expressed in this article are solely those of the authors and do not necessarily represent those of their affiliated organizations, or those of the publisher, the editors and the reviewers. Any product that may be evaluated in this article, or claim that may be made by its manufacturer, is not guaranteed or endorsed by the publisher.
PCPIW, Pre-consumer/post-industrial, PCW, Post-consumer waste, CM, Compression molding, VI, Vacuum infusion, TF, thermoforming.
Abdallah, A., Ugolini, F., Baronti, S., Maienza, A., Ungaro, F., and Camilli, F. (2019). Assessment of two sheep wool residues from textile industry as organic fertilizer in sunflower and maize cultivation. Springer-Verlag 19, 793–807. doi:10.1007/s42729-019-00079-y
Abdul-Rahman, F. (2014). Reduce, reuse, recycle: alternatives for waste management. United States: NM State University.
Abidi, H., Rana, S., Chaouch, W., Azouz, B., Aissa, I. B., Hassen, M. B., et al. (2021). Accelerated weathering of textile waste nonwovens used as sustainable agricultural mulching. J. Industrial Text. 50, 1079–1110. doi:10.1177/1528083719855326
Ailenei, E. C., Ionesi, S. D., Dulgheriu, I., Loghin, M. C., Isopescu, D. N., Maxineasa, S. G., et al. (2021). New waste-based composite material for construction applications. Materials 14, 6079. doi:10.3390/ma14206079
Al-Homoud, Dr. M. S. (2005). Performance characteristics and practical applications of common building thermal insulation materials. Build. Environ. 40, 353–366. doi:10.1016/j.buildenv.2004.05.013
Amicarelli, V., Bux, C., Spinelli, M. P., and Lagioia, G. (2022). Life cycle assessment to tackle the take-make-waste paradigm in the textiles production. Waste Manag. 151, 10–27. doi:10.1016/j.wasman.2022.07.032
Anthouli, A., Aravossis, K., Charitopoulou, R., Tot, B., and Vujic, G. (2013). Opportunities & barriers of recycling in balkan countries: the cases of Greece and Serbia. Caliteia: HSWMA & SeSWA.
Arshad, K., and Mujahid, M. (2011). Biodegradation of textile materials. Boras: The Swedish School of Textiles, University of Boras.
Asdrubali, F., D’Alessandro, F., and Schiavoni, S. (2015). A review of unconventional sustainable building insulation materials. Sustain. Mater. Technol. 4, 1–17. doi:10.1016/j.susmat.2015.05.002
Baccouch, W., Ghith, A., Yalcin-Enis, I., Sezgin, H., Miled, W., Legrand, X., et al. (2022). Investigation of the mechanical, thermal, and acoustical behaviors of cotton, polyester, and cotton/polyester nonwoven wastes reinforced epoxy composites. J. Industrial Text. 51, 876–899. doi:10.1177/1528083720901864
Bailey, K., Basu, A., and Sharma, S. (2022). The environmental impacts of fast fashion on water quality: a systematic review. Water 14, 1073. doi:10.3390/w14071073
Barbanera, M., Belloni, E., Buratti, C., Calabrò, G., Marconi, M., Merli, F., et al. (2020). Recycled leather cutting waste-based boards: thermal, acoustic, hygrothermal and ignitability properties. J. Material Cycles Waste Manag. 22, 1339–1351. doi:10.1007/s10163-020-01024-3
Baydar, G., Ciliz, N., and Mammadov, A. (2015). Life cycle assessment of cotton textile products in Turkey. Resour. Conservation Recycl. 104, 213–223. doi:10.1016/j.resconrec.2015.08.007
Bergstrom, J. C., and Randall, A. (2016). Resource Economics: an economic approach to natural resource and environmental policy. 4th ed. Northampton, MA: Edward Elgar Publishing.
Bertram, R. F., and Chi, T. (2018). A study of companies’ business responses to fashion e-commerce’s environmental impact. Int. J. Fash. Des. Technol. Educ. 11, 254–264. doi:10.1080/17543266.2017.1406541
Bhalla, K., Kumar, T., and Rangaswamy, J. (2018). An integrated rural development model based on comprehensive life-cycle assessment (LCA) of khadi -handloom industry in rural India. Procedia CIRP 69, 493–498. doi:10.1016/j.procir.2017.11.072
Bhatia, D., Sharma, A., and Malhotra, U. (2014). Review article recycled fibers: an overview. Int. J. Fiber Text. Res. 4, 77–82.
Bianco, I., Gerboni, R., Picerno, G., and Blengini, G. A. (2022). Life cycle assessment (LCA) of MWool® recycled wool fibers. Resources 11, 41. doi:10.3390/resources11050041
BIR (2022). Annual report 2022. Belgium: bureau of international recycling. Available at: https://www.bir.org/.
Bogale, M., Sakthivel, S., Senthil Kumar, S., and Senthil Kumar, B. (2023). Sound absorbing and thermal insulating properties of recycled cotton/polyester selvedge waste chemical bonded nonwovens. J. Text. Inst. 114, 134–141. doi:10.1080/00405000.2021.2024377
Braun, G., Som, C., Schmutz, M., and Hischier, R. (2021). Environmental consequences of closing the textile loop—life cycle assessment of a circular polyester jacket. Appl. Sci. 11, 2964. doi:10.3390/app11072964
Brewer, M. K. (2019). Slow fashion in a fast fashion world: promoting sustainability and responsibility. Laws 8, 24. doi:10.3390/laws8040024
Broega, A. C., Jordão, C., and Martins, S. B. (2017). Textile sustainability: reuse of clean waste from the textile and apparel industry. IOP Conf. Ser. Mater. Sci. Eng. 254, 192006. doi:10.1088/1757-899X/254/19/192006
Bundgaard, A. M., and Huulgaard, R. D. (2023). The role of standards in support of material efficiency requirements under the Ecodesign Directive. J. Clean. Prod. 385, 135599. doi:10.1016/j.jclepro.2022.135599
Cai, Z., Al Faruque, M. A., Kiziltas, A., Mielewski, D., and Naebe, M. (2021). Sustainable lightweight insulation materials from textile-based waste for the automobile industry. Materials 14, 1241. doi:10.3390/ma14051241
Centobelli, P., Abbate, S., Nadeem, S. P., and Garza-Reyes, J. A. (2022). Slowing the fast fashion industry: an all-round perspective. Curr. Opin. Green Sustain. Chem. 38, 100684. doi:10.1016/j.cogsc.2022.100684
Chandrashekhar, B., Mishra, M. S., Sharma, K., and Dubey, S. (2011). Bio-ethanol production from textile cotton waste via dilute acid hydrolysis and fermentation by Saccharomyces cerevisiae. J. Ecobiotechnology 3.
Chopra, S. S., Dong, L., Kaur, G., Len, C., and Ki Lin, C. S. (2023). Sustainable process design for circular fashion: advances in sustainable chemistry for textile waste valorisation. Curr. Opin. Green Sustain. Chem. 39, 100747. doi:10.1016/j.cogsc.2022.100747
Dahlbo, H., Aalto, K., Eskelinen, H., and Salmenperä, H. (2017). Increasing textile circulation—consequences and requirements. Sustain. Prod. Consum. 9, 44–57. doi:10.1016/j.spc.2016.06.005
Delaney, E., Liu, W., Zhu, Z., Xu, Y., and Dai, J. S. (2022). The investigation of environmental sustainability within product design: a critical review. Des. Sci. 8, e15. doi:10.1017/dsj.2022.11
del Rey, R., Berto, L., Alba, J., and Arenas, J. P. (2015). Acoustic characterization of recycled textile materials used as core elements in noise barriers. noise Cont. engng J. 63, 439–447. doi:10.3397/1/376339
Dissanayake, D. G. K., and Weerasinghe, D. U. (2021). Fabric waste recycling: a systematic review of methods, applications, and challenges. Mater Circ. Econ. 3, 24. doi:10.1007/s42824-021-00042-2
Dissanayake, D. G. K., Weerasinghe, D. U., Thebuwanage, L. M., and Bandara, U. A. A. N. (2021). An environmentally friendly sound insulation material from post-industrial textile waste and natural rubber. J. Build. Eng. 33, 101606. doi:10.1016/j.jobe.2020.101606
Dissanayake, D. G. K., Weerasinghe, D. U., Wijesinghe, K. A. P., and Kalpage, K. M. D. M. P. (2018). Developing a compression moulded thermal insulation panel using postindustrial textile waste. Waste Manag. 79, 356–361. doi:10.1016/j.wasman.2018.08.001
Drochytka, R., Dvorakova, M., and Hodna, J. (2017). Performance evaluation and research of alternative thermal insulation based on waste polyester fibers. Procedia Eng. 195, 236–243. doi:10.1016/j.proeng.2017.04.549
Dumont, P., Martoia, F., and Orgéas, L. (2023). “11 - compression moulding,” in Design and manufacture of structural composites, 273–300.
Ekström, K. M., and Salomonson, N. (2014). Reuse and recycling of clothing and textiles—a network approach. J. Macromarketing 34, 383–399. doi:10.1177/0276146714529658
Ellen Mac Arthur Foundation (2019). Circular economy diagram. Available at: https://www.ellenmacarthurfoundation.org/(Accessed January 28, 2024).
El Wazna, M., El Fatihi, M., El Bouari, A., and Cherkaoui, O. (2017). Thermo physical characterization of sustainable insulation materials made from textile waste. J. Build. Eng. 12, 196–201. doi:10.1016/j.jobe.2017.06.008
Esteve-Turrillas, F. A., and De La Guardia, M. (2017). Environmental impact of Recover cotton in textile industry. Resour. Conservation Recycl. 116, 107–115. doi:10.1016/j.resconrec.2016.09.034
European Parliament (2005). Council of the European Union DIRECTIVE 2005/32/EC OF THE EUROPEAN PARLIAMENT AND OF THE COUNCIL of 6 July 2005 establishing a framework for the setting of ecodesign requirements for energy-using products. Off. J. Eur. Union 191, 29–58.
European Parliament (2023). The impact of textile production and waste on the environment (infographics). Available at: https://www.europarl.europa.eu/news/en/headlines/society/20201208STO93327/the-impact-of-textile-production-and-waste-on-the-environment-infographics.
European Parliament and Council (2008). Directive 2008/98/EC of 19 November 2008 on waste and repealing certain directives. Official J. Eur. Union 312, 3–30.
EUROPEAN PARLIAMENT AND COUNCIL (2022). Proposal for a REGULATION OF THE EUROPEAN PARLIAMENT AND OF THE COUNCIL establishing a framework for setting ecodesign requirements for sustainable products and repealing Directive 2009/125/EC. Brussels: Official Journal of the European Union.
EUROPEAN PARLIAMENT, COUNCIL OF THE, EUROPEAN UNION, and COUNCIL OF THE (2009). DIRECTIVE 2009/125/EC OF THE EUROPEAN PARLIAMENT AND OF THE COUNCIL of 21 October 2009 establishing a framework for the setting of ecodesign requirements for energy-related products (recast). Official J. Eur. Union 256, 10–35.
Fera, T., Zeleke, Y., and Girmay, Y. (2022). Development of non-woven from recycled fabric selvedge wastes for functional sound absorption. Int. J. Sustain. Eng. 15, 136–143. doi:10.1080/19397038.2022.2092230
Fidan, F. Ş., Aydoğan, E. K., and Uzal, N. (2021). An integrated life cycle assessment approach for denim fabric production using recycled cotton fibers and combined heat and power plant. J. Clean. Prod. 287, 125439. doi:10.1016/j.jclepro.2020.125439
Filho, W., Ellams, D., Han, S., Tyler, D., Boiten, V. J., Paço, A., et al. (2019). A review of the socio-economic advantages of textile recycling. J. Clean. Prod. 218, 10–20. doi:10.1016/j.jclepro.2019.01.210
Geisendorf, S., and Pietrulla, F. (2018). The circular economy and circular economic concepts-a literature analysis and redefinition. Thunderbird Int. Bus. Rev. 60, 771–782. doi:10.1002/tie.21924
Gholamzad, E., Karimi, K., and Masoomi, M. (2014). Effective conversion of waste polyester–cotton textile to ethanol and recovery of polyester by alkaline pretreatment. Chem. Eng. J. 253, 40–45. doi:10.1016/j.cej.2014.04.109
Gómez, J. F., González Madariaga, F. J., Rosa Sierra, L. A., and León Morán, R. M. (2016). “Scrap denim-PP composites as a material for new product design,” in Libro de Actas - systems & design: beyond processes and thinking (IFDP - SD2016) (Valencia: Universitat Politècnica València). doi:10.4995/IFDP.2016.3360
Gounni, A., El Wazna, M., El Alami, M., El Bouari, A., Cherkaoui, O., Mabouk, M. T., et al. (2018). Thermal performance evaluation of textile waste as an alternative solution for heat transfer reduction in buildings. J. Sol. Energy Eng. 140, 021004. doi:10.1115/1.4038786
Greene, J. (2021). “16 - compression molding,” in Automotive plastics and composites (United States: Elsevier), 265–278.
Hadded, A., Benltoufa, S., Fayala, F., and Jemni, A. (2016). Thermo physical characterisation of recycled textile materials used for building insulating. J. Build. Eng. 5, 34–40. doi:10.1016/j.jobe.2015.10.007
Haque, A. N. M. A., Naebe, M., Mielewski, D., and Kiziltas, A. (2023). Waste wool/polycaprolactone filament towards sustainable use in 3D printing. J. Clean. Prod. 386, 135781. doi:10.1016/j.jclepro.2022.135781
Hasanzadeh, E., Mirmohamadsadeghi, S., and Karimi, K. (2018). Enhancing energy production from waste textile by hydrolysis of synthetic parts. Fuel 218, 41–48. doi:10.1016/j.fuel.2018.01.035
Hassanin, A. H., Candan, Z., Demirkir, C., and Hamouda, T. (2018). Thermal insulation properties of hybrid textile reinforced biocomposites from food packaging waste. J. Industrial Text. 47, 1024–1037. doi:10.1177/1528083716657820
Hu, Y., Du, C., Pensupa, N., and Lin, C. S. K. (2018). Optimisation of fungal cellulase production from textile waste using experimental design. Process Saf. Environ. Prot. 118, 133–142. doi:10.1016/j.psep.2018.06.009
Isci, A., and Demirer, G. N. (2007). Biogas production potential from cotton wastes. Renew. Energy 32, 750–757. doi:10.1016/j.renene.2006.03.018
Islam, S., and Bhat, G. (2019). Environmentally-friendly thermal and acoustic insulation materials from recycled textiles. J. Environ. Manag. 251, 109536. doi:10.1016/j.jenvman.2019.109536
Ismail, Z. Z., and Talib, A. R. (2016). Recycled medical cotton industry waste as a source of biogas recovery. J. Clean. Prod. 112, 4413–4418. doi:10.1016/j.jclepro.2015.06.069
Jeihanipour, A., Karimi, K., Niklasson, C., and Taherzadeh, M. J. (2010). A novel process for ethanol or biogas production from cellulose in blended-fibers waste textiles. Waste Manag. 30, 2504–2509. doi:10.1016/j.wasman.2010.06.026
Jørgensen, S., and Pedersen, L. J. T. (2018). RESTART sustainable business model innovation. Cham: Springer International Publishing. doi:10.1007/978-3-319-91971-3
Juanga-Labayen, J., Yanac, K., and Yuan, Q. (2021). Effect of substrate-to-inoculum ratio on anaerobic digestion of treated and untreated cotton textile waste. Int. J. Environ. Sci. Technol. 18, 287–296. doi:10.1007/s13762-020-02831-9
Juanga-Labayen, J. P., Labayen, I. V., and Yuan, Q. (2022). A review on textile recycling practices and challenges. Textiles 2, 174–188. doi:10.3390/textiles2010010
Juciene, M., Dobilaitė, V., Albrektas, D., and Bliūdžius, R. (2022). Investigation and evaluation of the performance of interior finishing panels made from denim textile waste. Text. Res. J. 92, 4666–4677. doi:10.1177/00405175221109636
Kutz, M. (2011). “19 - thermoforming,” in Applied plastics engineering handbook (United States: Elsevier), 333–358.
Kabir, M. M., Forgács, G., and Sárvári Horváth, I. (2013). Enhanced methane production from wool textile residues by thermal and enzymatic pretreatment. Process Biochem. 48, 575–580. doi:10.1016/j.procbio.2013.02.029
Kabir, M. M., Taherzadeh, M. J., and Sárvári Horváth, I. (2015). Dry anaerobic digestion of lignocellulosic and protein residues. Biofuel Res. J. 2, 309–316. doi:10.18331/BRJ2015.2.4.5
Karahan, M., Masood, Z., Nawab, Y., and Karahan, N. (2018). “Development and characterization of hybrid green composites from textile waste,” in Advances in ergonomics of manufacturing: managing the enterprise of the future advances in intelligent systems and computing. Editor S Trzcielinski (Cham: Springer International Publishing), 37–49. doi:10.1007/978-3-319-60474-9_4
Kirchherr, J., Yang, N.-H. N., Schulze-Spüntrup, F., Heerink, M. J., and Hartley, K. (2023). Conceptualizing the circular economy (revisited): an analysis of 221 definitions. Resour. Conservation Recycl. 194, 107001. doi:10.1016/j.resconrec.2023.107001
Kumar, M., Periasamy, S., Vinoth, V., and Thilagavathi, G. (2022). Development of needle punched nonwovens from natural fiber waste for thermal insulation application. J. Nat. Fibers 19, 9580–9588. doi:10.1080/15440478.2021.1990175
Kumar, P., Samuchiwal, S., and Malik, A. (2020). Anaerobic digestion of textile industries wastes for biogas production. Biomass Conv. bioref. 10, 715–724. doi:10.1007/s13399-020-00601-8
Kuzmanova, E., Zhelev, N., and Akunna, J. C. (2018). Effect of liquid nitrogen pre-treatment on various types of wool waste fibres for biogas production. Heliyon 4, e00619. doi:10.1016/j.heliyon.2018.e00619
Laitala, K., Klepp, I., and Henry, B. (2018). Does use matter? Comparison of environmental impacts of clothing based on fiber type. Sustainability 10, 2524. doi:10.3390/su10072524
Leja, K., and Lewandowicz, G. (2010). Polymers biodegradation and biodegradable polymers – a review.
Leon, A. L., Potop, G. L., Hristian, L., and Manea, L. R. (2016). Efficient technical solution for recycling textile materials by manufacturing nonwoven geotextiles. IOP Conf. Ser. Mater. Sci. Eng. 145, 022022. doi:10.1088/1757-899X/145/2/022022
Lin, J.-H., Li, T.-T., and Lou, C.-W. (2016). Puncture-resisting, sound-absorbing and thermal-insulating properties of polypropylene-selvages reinforced composite nonwovens. J. Industrial Text. 45, 1477–1489. doi:10.1177/1528083714562088
Liu, Y., Huang, H., Zhu, L., Zhang, C., Ren, F., and Liu, Z. (2020). Could the recycled yarns substitute for the virgin cotton yarns: a comparative LCA. Int. J. Life Cycle Assess. 25, 2050–2062. doi:10.1007/s11367-020-01815-8
Maity, S., Singha, K., Gon, D. P., Paul, P., and Singha, M. (2012). A review on jute nonwovens: manufacturing, properties and applications. Int. J. Text. Sci 1, 36–43. doi:10.5923/j.textile.20120105.02
Marconi, M., Landi, D., Meo, I., and Germani, M. (2018). Reuse of tires textile fibers in plastic compounds: is this scenario environmentally sustainable? Procedia CIRP 69, 944–949. doi:10.1016/j.procir.2017.11.074
McNeill, L., and Moore, R. (2015). Sustainable fashion consumption and the fast fashion conundrum: fashionable consumers and attitudes to sustainability in clothing choice. Int. J. Consum. Stud. 39, 212–222. doi:10.1111/ijcs.12169
Meng, X., Fan, W., Ma, Y., Wei, T., Dou, H., Yang, X., et al. (2020). Recycling of denim fabric wastes into high-performance composites using the needle-punching nonwoven fabrication route. Text. Res. J. 90, 695–709. doi:10.1177/0040517519870317
Mishra, R., Behera, B., and Militky, J. (2014). Recycling of textile waste into green composites: performance characterization. Polym. Compos. 35, 1960–1967. doi:10.1002/pc.22855
Morley, M. J., Bartlett, C., and McGill, I. (2009). Maximising reuse and recycling of UK clothing and textiles: a report to the department for environment, Food and rural affairs. United Kingdom: Oakdene Hollins Ltd.
Morseletto, P. (2020). Targets for a circular economy. Resour. Conservation Recycl. 153, 104553. doi:10.1016/j.resconrec.2019.104553
Morseletto, P. (2023). Sometimes linear, sometimes circular: States of the economy and transitions to the future. J. Clean. Prod. 390, 136138. doi:10.1016/j.jclepro.2023.136138
Muthu, S. S. (2020). “End-of-life management of textile products,” in Assessing the environmental impact of textiles and the clothing supply chain (Elsevier), 143–160. doi:10.1016/B978-0-12-819783-7.00008-9
Neves, S. A., and Marques, A. C. (2022). Drivers and barriers in the transition from a linear economy to a circular economy. J. Clean. Prod. 341, 130865. doi:10.1016/j.jclepro.2022.130865
Niinimäki, K., Peters, G., Dahlbo, H., Perry, P., Rissanen, T., and Gwilt, A. (2020). The environmental price of fast fashion. Nat. Rev. Earth Environ. 1, 189–200. doi:10.1038/s43017-020-0039-9
Nikolić, S., Lazić, V., Veljović, Đ., and Mojović, L. (2017). Production of bioethanol from pre-treated cotton fabrics and waste cotton materials. Carbohydr. Polym. 164, 136–144. doi:10.1016/j.carbpol.2017.01.090
Nunes, L. J. R., Godina, R., Matias, J. C. O., and Catalão, J. P. S. (2018). Economic and environmental benefits of using textile waste for the production of thermal energy. J. Clean. Prod. 171, 1353–1360. doi:10.1016/j.jclepro.2017.10.154
Palm, D. (2011). Improved waste management of textiles. Göteborg: Swedish Environmental Research Institute.
Patnaik, A., Mvubu, M., Muniyasamy, S., Botha, A., and Anandjiwala, R. D. (2015). Thermal and sound insulation materials from waste wool and recycled polyester fibers and their biodegradation studies. Energy Build. 92, 161–169. doi:10.1016/j.enbuild.2015.01.056
Patti, A., Cicala, G., and Acierno, D. (2020). Eco-sustainability of the textile production: waste recovery and current recycling in the composites world. Polymers 13, 134. doi:10.3390/polym13010134
Peña-Pichardo, P., Martínez-Barrera, G., Martínez-López, M., Ureña-Núñez, F., and Dos Reis, J. M. L. (2018). Recovery of cotton fibers from waste Blue-Jeans and its use in polyester concrete. Constr. Build. Mater. 177, 409–416. doi:10.1016/j.conbuildmat.2018.05.137
Peters, G., Li, M., and Lenzen, M. (2021). The need to decelerate fast fashion in a hot climate - a global sustainability perspective on the garment industry. J. Clean. Prod. 295, 126390. doi:10.1016/j.jclepro.2021.126390
Pourzahedi, L., Vance, M. E., and Eckelman, M. J. (2017). Life cycle assessment and release studies for 15 nanosilver-enabled consumer products: investigating hotspots and patterns of contribution. Environ. Sci. 51 (12), 7148–7158. doi:10.1021/acs.est.6b05923
Raj, C., Arul, S., Sendilvelan, S., and Saravanan, C. (2009). Bio gas from textile cotton waste - an alternate fuel for diesel engines. Open Waste Manag. J. 2, 1–5. doi:10.2174/1876400201002010001
Rajput, D., Bhagade, S. S., Raut, S. P., Ralegaonkar, R. V., and Mandavgane, S. A. (2012). Reuse of cotton and recycle paper mill waste as building material. Constr. Build. Mater. 34, 470–475. doi:10.1016/j.conbuildmat.2012.02.035
Ramamoorthy, N. K., Ravi, S., and Sahadevan, R. (2018). Production of bio-ethanol from an innovative mixture of surgical waste cotton and waste card board after ammonia pre-treatment. Energy Sources, Part A Recovery, Util. Environ. Eff. 40, 2451–2457. doi:10.1080/15567036.2018.1502843
Rapsikevičienė, J., Gurauskienė, I., and Jučienė, A. (2019). Model of industrial textile waste management. EREM 75, 43–55. doi:10.5755/j01.erem.75.1.21703
Ricciardi, P., Belloni, E., and Cotana, F. (2014). Innovative panels with recycled materials: thermal and acoustic performance and Life Cycle Assessment. Appl. Energy 134, 150–162. doi:10.1016/j.apenergy.2014.07.112
Riesener, M., Kuhn, M., Hellwig, F., Ays, J., and Schuh, G. (2023). Design for circularity – identification of fields of action for ecodesign for the circular economy. Procedia CIRP 116, 137–142. doi:10.1016/j.procir.2023.02.024
Rizal, S., Olaiya, F. G., Saharudin, N. I., Abdullah, C. K., Olaiya, N. G., Mohamad Haafiz, M. K., et al. (2021). Isolation of textile waste cellulose nanofibrillated fibre reinforced in polylactic acid-chitin biodegradable composite for green packaging application. Polymers 13, 325. doi:10.3390/polym13030325
Rubino, C., Bonet Aracil, M., Liuzzi, S., Stefanizzi, P., and Martellotta, F. (2021). Wool waste used as sustainable nonwoven for building applications. J. Clean. Prod. 278, 123905. doi:10.1016/j.jclepro.2020.123905
Sadrolodabaee, P., Claramunt, J., Ardanuy, M., and De La Fuente, A. (2021a). A textile waste fiber-reinforced cement composite: comparison between short random fiber and textile reinforcement. Materials 14, 3742. doi:10.3390/ma14133742
Sadrolodabaee, P., Claramunt, J., Ardanuy, M., and Fuente, A. D. L. (2021b). Characterization of a textile waste nonwoven fabric reinforced cement composite for non-structural building components. Constr. Build. Mater. 276, 122179. doi:10.1016/j.conbuildmat.2020.122179
Safartalab, K., Dadashian, F., and Vahabzadeh, F. (2014). Fed batch enzymatic hydrolysis of cotton and viscose waste fibers to produce ethanol. ujc 2, 11–15. doi:10.13189/ujc.2014.020103
Sakthivel, S., Senthil Kumar, S., Mekonnen, S., and Solomon, E. (2020). Thermal and sound insulation properties of recycled cotton/polyester chemical bonded nonwovens. J. Eng. Fibers Fabr. 15, 155892502096881. doi:10.1177/1558925020968819
Sandin, G., and Peters, G. M. (2018). Environmental impact of textile reuse and recycling – a review. J. Clean. Prod. 184, 353–365. doi:10.1016/j.jclepro.2018.02.266
Sariatli, F. (2017). Linear economy versus circular economy: a comparative and analyzer study for optimization of economy for sustainability. Visegrad J. Bioeconomy Sustain. Dev. 6, 31–34. doi:10.1515/vjbsd-2017-0005
Shen, F., Xiao, W., Lin, L., Yang, G., Zhang, Y., and Deng, S. (2013). Enzymatic saccharification coupling with polyester recovery from cotton-based waste textiles by phosphoric acid pretreatment. Bioresour. Technol. 130, 248–255. doi:10.1016/j.biortech.2012.12.025
Shen, L., Worrell, E., and Patel, M. K. (2010). Open-loop recycling: a LCA case study of PET bottle-to-fibre recycling. Resour. Conservation Recycl. 55, 34–52. doi:10.1016/j.resconrec.2010.06.014
Sołowski, G., Konkol, I., and Cenian, A. (2020). Methane and hydrogen production from cotton waste by dark fermentation under anaerobic and micro-aerobic conditions. Biomass Bioenergy 138, 105576. doi:10.1016/j.biombioe.2020.105576
Song, G. (2009). Thermal insulation properties of textiles and clothing. Text. Cold Weather Appar. 2009, 19–32. doi:10.1533/9781845697174.1.19
Spasojevic, P. (2019). “15.10.2.3 Vacuum infusion processing,” in Unsaturated polyester resins (Elsevier), 367–406.
Subramanian, K., Chopra, S. S., Cakin, E., Li, X., and Lin, C. S. K. (2020). Environmental life cycle assessment of textile bio-recycling – valorizing cotton-polyester textile waste to pet fiber and glucose syrup. Resour. Conservation Recycl. 161, 104989. doi:10.1016/j.resconrec.2020.104989
Tiuc, A.-E., Vermeşan, H., Gabor, T., and Vasile, O. (2016). Improved sound absorption properties of polyurethane foam mixed with textile waste. Energy Procedia 85, 559–565. doi:10.1016/j.egypro.2015.12.245
Trajković, D., Jordeva, S., Tomovska, E., and Zafirova, K. (2016). Polyester apparel cutting waste as insulation material. J. Text. Inst., 1–8. doi:10.1080/00405000.2016.1237335
Ütebay, B., Çelik, P., and Çay, A. (2019). Effects of cotton textile waste properties on recycled fibre quality. J. Clean. Prod. 222, 29–35. doi:10.1016/j.jclepro.2019.03.033
Vadicherla, T., and Saravanan, D. (2017). Thermal comfort properties of single Jersey fabrics made from recycled polyester and cotton blended yarns. India: INDIAN J. FIBRE TEXT. RES.
Valverde, I. C., Castilla, L. H., Nuñez, D. F., Rodriguez-Senín, E., and De La Mano Ferreira, R. (2013). Development of new insulation panels based on textile recycled fibers. Waste Biomass Valor 4, 139–146. doi:10.1007/s12649-012-9124-8
Van Der Velden, N. M., Patel, M. K., and Vogtländer, J. G. (2014). LCA benchmarking study on textiles made of cotton, polyester, nylon, acryl, or elastane. Int. J. Life Cycle Assess. 19, 331–356. doi:10.1007/s11367-013-0626-9
Varadharajan, V., Aravinth, S., Santhosh, C., Nithya, M., and Sathya, K. (2014). Bioethanol production from cotton waste using cellulase extracted from Fusarium species. Int. J. ChemTech Res. 6, 4061–4069.
Wazna, M. E., Gounni, A., Bouari, A. E., Alami, M. E., and Cherkaoui, O. (2019). Development, characterization and thermal performance of insulating nonwoven fabrics made from textile waste. J. Industrial Text. 48, 1167–1183. doi:10.1177/1528083718757526
Webster, K. (2021). A circular economy is about the economy. Circ. Econ. Sust. 1, 115–126. doi:10.1007/s43615-021-00034-z
Wiedemann, S. G., Clarke, S. J., Nguyen, Q. V., Cheah, Z. X., and Simmons, A. T. (2023). Strategies to reduce environmental impacts from textiles: extending clothing wear life compared to fibre displacement assessed using consequential LCA. Resour. Conservation Recycl. 198, 107119. doi:10.1016/j.resconrec.2023.107119
Wiedemann, S. G., Yan, M.-J., Henry, B. K., and Murphy, C. M. (2016). Resource use and greenhouse gas emissions from three wool production regions in Australia. J. Clean. Prod. 122, 121–132. doi:10.1016/j.jclepro.2016.02.025
Wojnowska-Baryła, I., Bernat, K., and Zaborowska, M. (2022). Strategies of recovery and organic recycling used in textile waste management. IJERPH 19, 5859. doi:10.3390/ijerph19105859
Yasin, S., and Sun, D. (2019). Propelling textile waste to ascend the ladder of sustainability: EOL study on probing environmental parity in technical textiles. J. Clean. Prod. 233, 1451–1464. doi:10.1016/j.jclepro.2019.06.009
Zach, J., Hroudová, J., and Korjenic, A. (2016). Environmentally efficient thermal and acoustic insulation based on natural and waste fibers: environmentally efficient insulations based on natural and waste fibers. J. Chem. Technol. Biotechnol. 91, 2156–2161. doi:10.1002/jctb.4940
Keywords: circular economy, composite, non-woven, recycling, textile waste
Citation: Alves DI, Barreiros M, Fangueiro R and Ferreira DP (2024) Valorization of textile waste: non-woven structures and composites. Front. Environ. Sci. 12:1365162. doi: 10.3389/fenvs.2024.1365162
Received: 04 January 2024; Accepted: 15 February 2024;
Published: 28 February 2024.
Edited by:
Thomas Stanton, Loughborough University, United KingdomReviewed by:
Alana James, Northumbria University, United KingdomCopyright © 2024 Alves, Barreiros, Fangueiro and Ferreira. This is an open-access article distributed under the terms of the Creative Commons Attribution License (CC BY). The use, distribution or reproduction in other forums is permitted, provided the original author(s) and the copyright owner(s) are credited and that the original publication in this journal is cited, in accordance with accepted academic practice. No use, distribution or reproduction is permitted which does not comply with these terms.
*Correspondence: Diana P. Ferreira, ZGlhbmEuZmVycmVpcmFAZGV0LnVtaW5oby5wdA==
Disclaimer: All claims expressed in this article are solely those of the authors and do not necessarily represent those of their affiliated organizations, or those of the publisher, the editors and the reviewers. Any product that may be evaluated in this article or claim that may be made by its manufacturer is not guaranteed or endorsed by the publisher.
Research integrity at Frontiers
Learn more about the work of our research integrity team to safeguard the quality of each article we publish.