- 1Research Institute for Textile and Clothing at Niederrhein University of Applied Sciences (FTB), Mönchengladbach, Germany
- 2Faculty of Textile and Clothing Technology at Niederrhein University of Applied Sciences, Mönchengladbach, Germany
The global increase of the amount of microplastics in aquatic systems is an ever-growing problem. Household laundering of synthetic textiles has been identified as one significant reason for the release of fibrous microplastics (FMP), although a high proportion of the waste water generated by the washing process is filtered by wastewater treatment plants, e.g., in Germany, before it enters the environment. The washing of garments made of synthetic materials is considered particularly and was investigated during this study. Therefore, 11 fleece garments, one mixed batch and three non-raised garments were washed several times and under different conditions in houshold washing machines. However, this study utilizing different functional polyester garments showed that mechanical raised textiles (e.g., fleece) do not generally have higher emission values than non-raised textiles, such as sports shirts and sports pants. During the washing process, the release of FMP can be influenced by different washing parameters, always aiming for a good washing result. The experiments showed, that the release of FMP into the aquatic environment can be reduced by the washing habits—especially a high washing machine load and a shortened washing time were found to be effective.
1 Introduction
The distribution of microplastics in the environment has become of general concern, as these persistent materials are now detected in all areas of the environment: in marine waters, in fresh water, in soils and also in the air (GESAMP, 2016; European Commission, 2019; Schöpel and Stamminger, 2019). The term “microplastics” defines plastic particles that are smaller than 5 mm (ISO/TR 21960:2020, 2024) and includes also synthetic fibers and fiber fragments, e.g., fragments from textiles (Cole et al., 2011; Hartmann et al., 2019). However, the majority of detected microplastics is smaller than 500 µm (Galvão et al., 2020; Cai et al., 2021). In this study, the term “fibrous microplastics” (FMP) is used for microplastics of textile origin with an aspect ratio of 1:3 or larger. FMP is released from textiles in many ways, especially during textile production if yarn spinning, fabric manufacture, dyeing and chemical or mechanical treatment are included (Liu et al., 2021; Lim et al.,2022). Different methods of mechanical treatment are used to produce raised fabrics, such as fleece. This depends on the fabric type and the desired effect. In general, the raising process can vary greatly depending on the type of raising rollers and coverings used, the ratio of pile and counter-pile, the number of raising rollers in the drum, the number of process steps and on factors such as process speed and contact pressure. This leads to various types of fabric surfaces. Besides that, household laundry is one of the major entry paths for FMPs into the environment (Browne et al., 2011; GESAMP, 2016; Mermaid Consortium, 2017; Singh et al., 2020; Periyasamy and Tehrani-Bagha, 2022). Household laundry releases synthetic fiber fragments, which enter sewage treatment plants (where these exist) via the sewer system. Most treatment methods do not completely remove FMP, so that some of them end up in the water and thus in the food chain (e.g., Mintening et al., 2017; Bruce et al., 2016). Additionally, FMP is further spread in the environment if the sewage sludge is used as fertilizer in agriculture (Bannick et al., 2018). This activated sludge is one of the measures to retain fibers or other microplastic in conventional waste water treatment plants. The introduction of FMP and the amounts released via household laundry into the environment have now been investigated in a number of studies with very different results (see for example, Galvão et al., 2020; Gavigan et al., 2020; Tiffin et al., 2021; Hazlehurst et al., 2023). Zhang et al. performed an extensive literature review and found that the FMP release varies enormously between 50.6 and 1,180 kg per 100,000 inhabitants per year depending on the washing conditions, the textiles used and the analytical methods (Zhang et al., 2021). In the aquatic environment the microplastic particles cause problems because, due to their size, they can be easily ingested by aquatic organisms (e.g., Rochman et al., 2015) and can cause acute toxic or chronic effects depending on the concentration (e.g., Cole et al., 2011).
Older studies detected a high abundance of fiber fragments from synthetic polymers, such as polyester, in the aquatic system (Browne et al.,2011; Bruce et al., 2016), while newer studies also detected the appearance of natural fibers in the aquatic system. Due to their faster degradation in comparison to synthetic fibers, natural fibers may release toxic compounds and dyes to the environment (Stanton et al., 2019, Liu et al., 2023). However, polyester degrades very slowly (Klein et al., 2018) and therefore will be abundantly present in the environment for many years. Thus, the experiments here concentrate on polyester fibers from textiles. The polyester described in the literature is usually polyethylene terephthalate (PET), often referred in the textile industry simply as “polyester” or “PES” (ISO expression for fibers made out of PET and PBT, ISO 2076:2021, Textiles—Man-made fibres—Generic names). Thus, the term “PES” is used here. PES accounts for the largest share of the world fiber production at approx. 65% of the worldwide fiber production of around 60 million tons (CIRFS, 2021). Textiles with performance for use in sports articles and so-called “outdoor articles” have experienced significant growth in volume in recent years. Consumers expect textiles for this sector to offer a high level of clothing comfort combined with functionality, such as moisture management. Here, PES is one of the most widely used fiber materials. Both, voluminous garments, such as fleece jackets and sweaters, and smooth garments, such as T-shirts and pants, are popular and worn in a variety of ways.
Household laundry is used to remove irritating substances such as fats, proteins, salts or pigments to freshen up the garments. For this purpose, textiles in private households are usually treated in drum washing machines, with water and detergents at a selected temperature and time. These four washing parameters - time, temperature, mechanical action and chemistry - are in equilibrium with each other as in Sinner’s circle (Sinner, 1960) and must be set to different levels depending on the washing task and load in order to achieve a high washing effect and to protect the items to be washed. Material abrasion through textile production and usage is removed from the textile goods in addition to the substances perceived as dirt or other contamination by the consumer. The washing parameters not only affect the washing result, but also the release of FMP from textiles (Periyasamy and Tehrani-Bagha, 2022). For example, a study by De Falco et al. shows that a prolonged washing time resulted in a slightly, but not significantly, increased fiber release (De Falco et al., 2018). Studies on the influence of washing temperature show different results. In some cases, higher temperatures (60 °C) led to a higher fiber release (De Falco et al., 2018; Yang et al., 2019; Zambrano et al., 2019), while in some cases no significant influence of washing temperature was found (Hernandez et al., 2017). The influence of mechanics during washing has been scarcely studied. Kelly et al. found that a high water level with low agitation resulted in increased fiber release (Kelly et al., 2019). A higher load of the washing machine reduces the mechanical stress on the textiles during washing and thereby the fiber release (Lant et al., 2020). The use of detergents and fabric softeners during washing is controversially discussed. In some studies, the amount of released fiber increased when washing additives were increased (Hernandez et al., 2017; Almroth et al., 2018; Zambrano et al., 2019) while in other studies, the fiber release was not significantly affected (Pirc et al., 2016; Lant et al., 2020). In December 2022 Zara Home (brand of Inditex) launched a detergent which may reduce microfiber release by up to 80% depending on the fabric type and the washing conditions (BASF 2022).
The textile parameters must not be neglected in the consideration of the fiber release from the laundry: The type of fabric (woven, knit or non-woven) and the fabric treatment during production (e.g., dyeing and finishing) play an important role (Liu et al., 2021; Periyasamy, 2023). The highest number of fiber fragments was released from softshell material, followed by fleece material and T-shirts (Sillanpää and Sainio, 2017) or vice versa (Kärkkäinen and Sillanpää, 2021). When comparing fleece fabric with plain knitted fabric, significantly more FMP per m2 of textile was released in fleece than in plain knitted fabric (Almroth et al., 2018). In a study where textile samples were cut by laser, the fleece fabric released significantly more fibers than the smooth fabric. Scissor-cutting of the samples reduced the differences between fleece and smooth material and similar amounts of FMP were released after five washes (Cai et al., 2020). In contrast, another study found no difference in the release of FMP between fleece fabric and non-raised smooth fabric (Lant et al., 2020). Investigations with different yarn structures showed that textured PES fibers were released a lot in the first wash, but the emission was significantly reduced in the fifth wash compared to flat and staple PES fibers (Palacios-Marín et al., 2022). The analyzed data shows that the amount of FMP released from textiles by household laundry is influenced by a variety of factors. The comparison of measured values from different studies is complicated due to differing laundry items, washing parameters, and especially due to different methods of FMP collection (Tiffin et al., 2021).
The present study is focused on performance textiles used for sports and outdoor activities made of PES. This includes raised fabrics (e.g., fleece) as well as smooth fabrics. The parameters “time” and “mechanics” (spin cycles and loading) during the washing process were carefully considered and applied to a variety of textiles. Consumer behavior and care instructions from manufacturers for sporting and outdoor goods were used as the base for the development of our method. The investigation results in a differentiated depiction of the amount of FMP released by household laundry. A reliable methodology of FMP detection based on fractional filtration, gravimetric determination of FMP release and indication of FMP in relation to the weight of goods used was developed in preliminary experiments (data not shown).
2 Materials and methods
2.1 Textile material
Different textiles from 100% polyester (PES) or polyester mixed with other materials were analyzed in this study. They were provided by project partners (F1-F11 = jackets; mixed batch t-shirt, towel, pillow case, jacket) or bought in various discounters (sports shirt 1, sports shirt 2, sports pant). These materials were used to put together washing batches, each consisting of the same product. As many individual items were combined until a specific weight was obtained. The number of items for each material varied according to the grammage and the size of the textiles. Textile properties such as mass per unit area (grammage), construction and mechanical treatment differed. Various fleece and fleece-like materials, raised on one side or on both sides, interlock material with and without filling thread and plain knitted fabric were tested. Additional to washing batches consisting of several pieces of the same garment, a mixed batch with four T-shirts, one pillowcase, one jacket and two towels was applied. The samples of the mixed batch had different grammages and textile structures, but were all made of 100% PES and had a total weight of 2 kg per batch. These textiles were provided by the Henkel Company (Germany). Grammages of the textiles were determined according to DIN EN 12127:1997-12, (2024) using a fine balance (ABJ-120-4NM, Kern and Sohn GmbH, Balingen-Frommern, Germany). The textiles were all tested in garment forms. Table 1 gives information about the garment details.
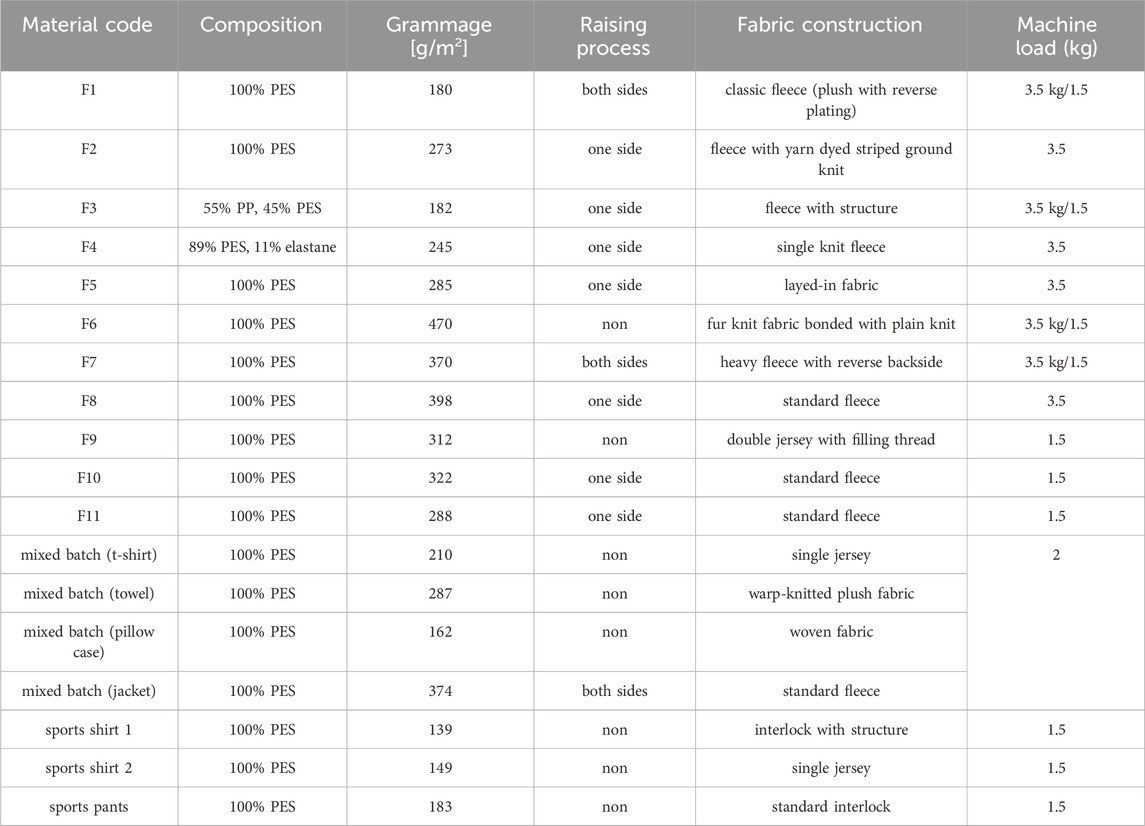
Table 1. Properties of the investigated garments and information about the machine loads applied in washing experiments (Section 2.2).
2.2 Washing and drying
The garments described in Table 1 were washed in a front loader washing machine (Miele and Cie KG, Gütersloh, Germany, model WDD031 WPS) under different conditions. The automatic water quantity control was switched off, so that all washing batches were washed with the same level of fluid. A liquid detergent (15 mL/kg textile; Persil Universal Gel, Henkel Company, Germany) was used. Additionally, textiles F6 and F7 were washed including a fabric softener (30 mL per wash load; Vernel Frischer Morgen, Henkel Company, Germany). The loading quantity of the washing machine was 3.5 (almost full drum) or 1.5 kg (half drum), resulting in a different mechanical stress on the laundry items. The mixed batch was washed as it is (2 kg). Table 2 gives an overview of the selected washing programs. All textiles were washed10 times. Additionally, textiles F1, F3 and F4 (3.5 kg) were washed 20 times. For each garment three replicates (n = 3) were tested, unless otherwise stated (see Table 3).
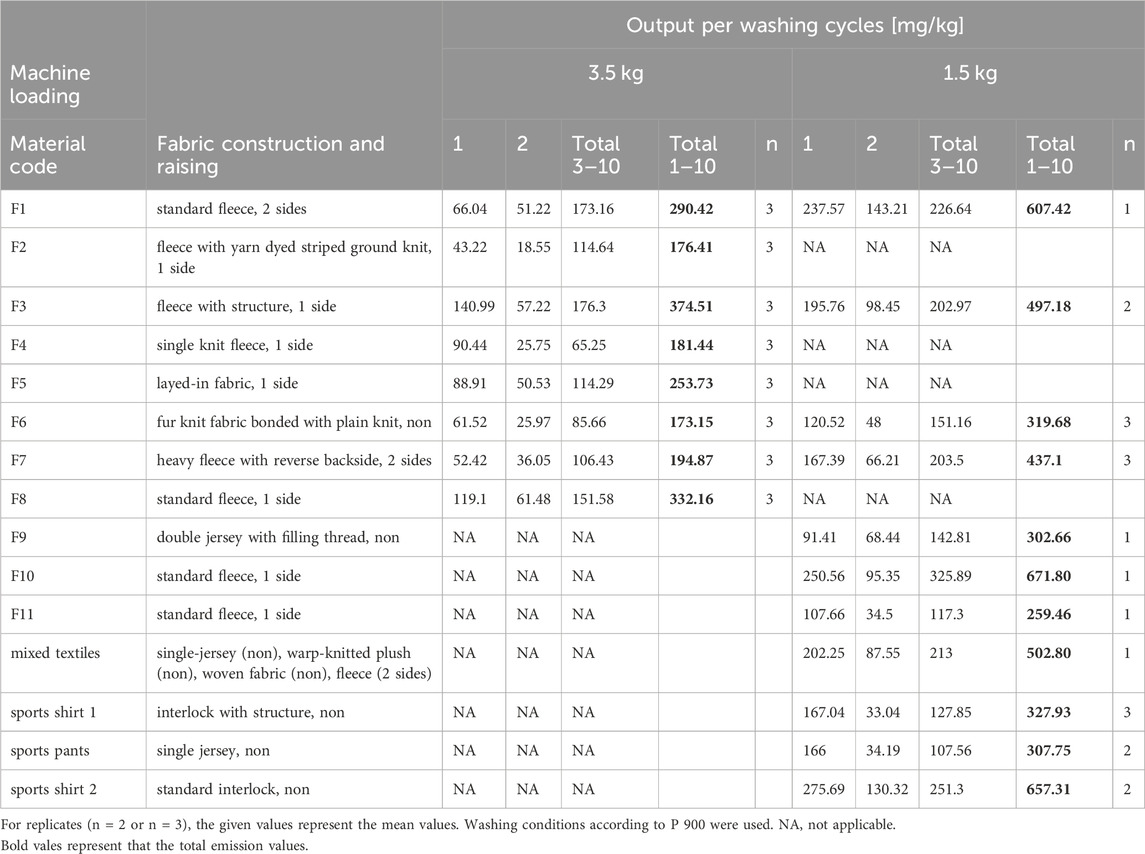
Table 3. Comparison of the FMP emission after washing from different garments and at different loading quantities.
One full washing series with 10 washing and drying cycles was performed with soft water instead of normal tap water.
The washing water was collected and subsequently filtered. After each washing cycle, the washing machines were cleaned twice with the cold wash program. As a control, the resulting liquors were filtered exemplarily to measure the FMP load of the water. After five washing days, the washing machines were cleaned with a 90 °C cleaning program.
After washing, the garments were dried in a heat pump dryer (Miele and Cie KG, Gütersloh, Germany, model TDD220 WP) using the easy care program followed by a warm ventilation program.
2.3 Sample collection after washing
The entire liquor of a washing process was collected in 80 L mechanically pre-cleaned drums (Section 2.4) and filtered directly under pressure by means of a five-step filter cascade, provided by the project partner TU Dresden. Circular stainless steel filters (diameter = 130 mm; Franz Eckert GmbH, Waldkirch) with pore sizes of 1,500 μm, 500 μm, 150 μm, 50 μm and 5 µm were used. To ensure that the entire liquor was filtrated, the drum was rinsed three times with 1 L of tap water (=3 L in total) after filtration. This water was also filtrated, followed by an additional 15 L of tap water to rinse the remaining FMP from the tubing.
2.4 Cleaning procedures
Every piece of equipment used was regularly cleaned to prevent cross-contamination: the 80 L drums used to collect the washing liquor were thoroughly rinsed with tap water after each use, and left upside down for drying between uses. Additionally, they were mechanically cleaned using a brush and tap water at least once a month, or after they were not in use for longer periods.
The stainless-steel filters were cleaned after each use in a two-stage process. Loosely attached fibers were manually removed with a brush, before the whole filter was submerged in concentrated sulphuric acid (>95%, various companies) for 24–72 h to dissolve all remaining residues. The effectiveness of this cleaning process was verified using light microscopy. After cleaning, no fiber residue was detected.
The stainless-steel tube system of the filtration cascade was completely emptied by means of compressed air at the end of each filtration. Between filtrations, the whole setup was rinsed by pumping tap water through it for at least 10 min. After five washing days, mechanical cleaning of the tube system was performed to prevent biofilm formation (e.g., during non-use at the weekend) and to clean off any biofilm that had formed.
2.5 Analytics
The FMP output was quantified gravimetrically for each fraction by means of fine weighing (fine scale ALJ250-4A, Kern and Sohn GmbH, Balingen-Frommern, Germany, d = 0.1 mg) and the relative FMP output was calculated in mg/kg textile for each washing load. Mean values and a standard deviation of three replicates per condition were calculated where possible. To better understand the relative shedding in each washing load, the emissions from each washing cycle was additionally calculated as a percentage of the total emissions from all washing cycles.
Furthermore, exemplary light microscopic (Keyence VH-Z220R) analyses of the filter residues were carried out to determine the dimensions and color of the fiber residues. Light microscopy was additionally used to visualize the textile surfaces. Here, a magnification of ×20 was chosen.
The purity of the filter residues was determined at BAM (Bundesanstalt für Materialforschung, Berlin) using the TED-GC/MS method according to an internal protocol as proof of concept for F6. As a complementary method, the chemical composition of the FMP was determined by µFTIR for F1 by the chemical department of the Niederrhein University of Applied Sciences. In this method, light microscopy for morphology investigation of fibers and fragments is combined with FTIR-spectroscopy for each detected fiber/fragment. The resulting FTIR spectra were automatically compared with a standard database, to determine the most likely material for each detected fiber/fragment.
3 Results and discussion
The aim of this research was the determination of the dependency of the microplastic output from polyester textiles on household washing parameters. It was found that the strongest filter loading was observed using the 5 µm filter, indicating that the released fibers and fragments have sizes in the lower micrometer range and indeed belong to the category of “fibrous microplastics.” However, longer fibers with diameters smaller than 50 µm also meander through the coarser filters and then remain on the filter cake of the smallest filter (see Supplementary Figures S1, S2). Similar fiber lengths were detected by Hernandez et al. (40 μm–1,500 µm) (Hernandez et al., 2017) and Zambrano et al. (approx. 200–1,250 µm) (Zambrano et al., 2019).
Instrumental analysis was performed to characterize the collected material and identify possible impurities. TED-GC/MS demonstrated that just 1% of the analyzed material (F6, 100% PES) did not consist of PES, and belonged to residues of zippers and buttons, for example, (see Supplementary Figure S3). Figure 1 visualized the results of the µFTIR spectroscopy for one selected sample (F1, 100% PES) as a proof-of-concept. Figure 1A shows the filter with filtered FMP and fiber fragments - the image was taken by light microscopy. This image was simultaneously analyzed by µFTIR spectroscopy and the data was compared with relevant databases. The PES material was visualized in yellow here (Figure 1B). In Figure 1C the PES (red) and the non-PES material (black with circle) were distinguished. This data confirmed a high amount of filtered PES FMP material.
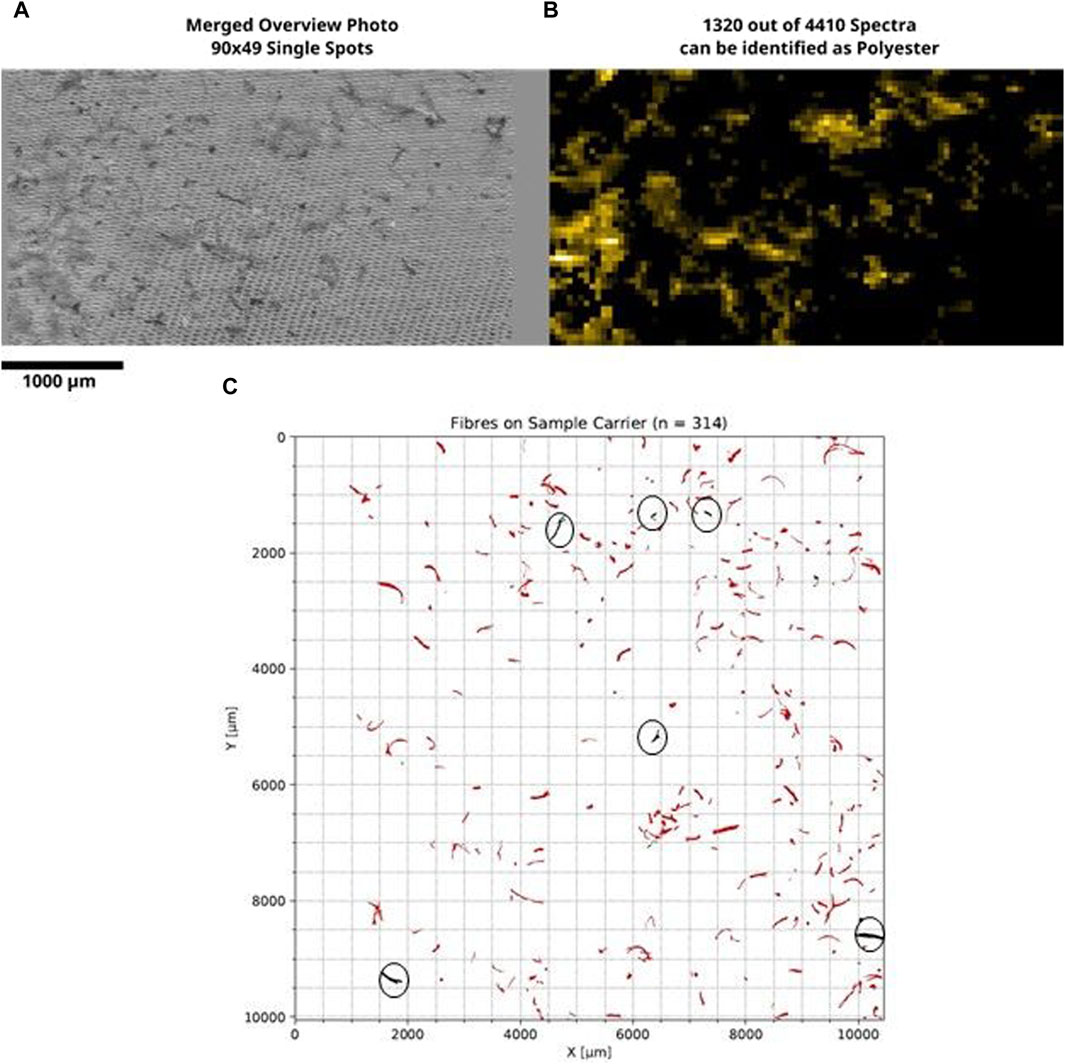
Figure 1. Analysis of the filter cakes with µFTIR: (A) Overview image of all fibers (fragments), (B) Image with a filter for polyester in yellow. (C) Foreign fibers or particles which do not consist of PES are circled. All other compounds were detected as PES.
3.1 Determination of the emission quantity over several washing cycles
The output quantity of FMP was analyzed over 10 washing/drying cycles (loading quantity: 1.5 kg or 3.5 kg). The laundry items were washed using the easy-care program (P 900) and then dried using a heat pump dryer after every washing cycle. The amount of FMP from the washing process was quantified. The FMP output was highest in the first washing cycle, and continued to decrease over the course of the further cycles until it asymptotically approached an output of approx. 10 mg/kg FMP. F4 reached an output of 10 mg/kg after 4 washes, F3 after 9 washes and F1 after 13 washes. The FMP output also did not increase in washes 10–20. This was exemplary tested for the textiles F1, F3 and F4 (see Figure 2).
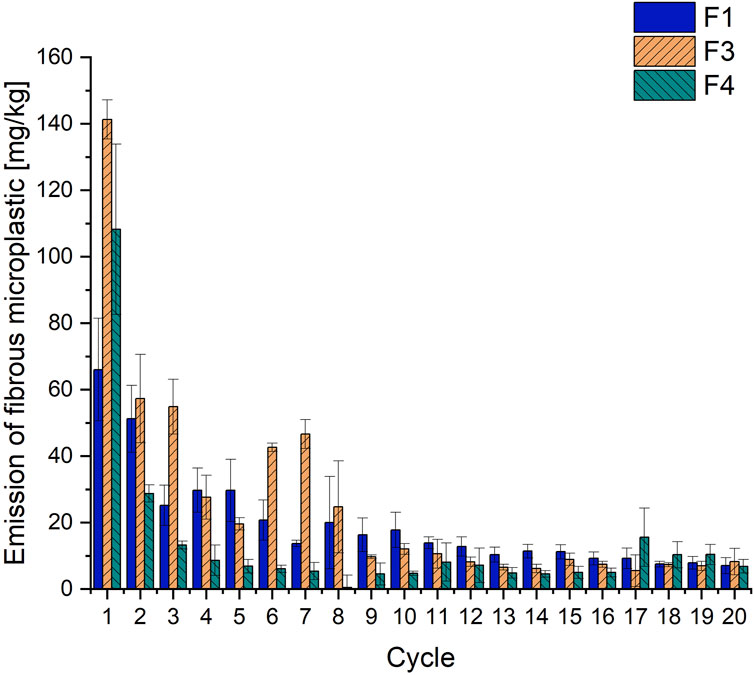
Figure 2. Illustration of the mean value of FMP emission with a standard deviation over 20 washing cycles for different garments. All garments were fleeces. n = 3; loading quantity: 3.5 kg.
These observations are in line with the results from the literature (Pirc et al., 2016; Almroth et al., 2018; Lant et al., 2020; Lim et al., 2022). The mechanical stress on the textile leads to fiber abrasion and fiber (fragment) release in each washing cycle. This happens throughout the lifetime of the textile and could be observed even after 48 washes (Lant et al., 2020).
The leveling of the emitted FMP after approx. 10 washing cycles to approx. 10 mg/kg textile is independent from the material of the textile and is true for 100% PES (F1), 55% PP + 45% PES (F3) and 89% PES + 11% elastane (F4), here. Although, polyester is the most abundant material regarding microplastics in the environment, other synthetic polymers, such as PP or polyamide were found, too (Periyasamy and Tehrani-Bagha, 2022). All these materials degrade very slowly or not at all in an aquatic environment (Klein et al., 2018).
3.2 Comparison of different garments and surface constructions
Furthermore, in addition to garments made out of pure fleece materials, the emission values were also investigated on a washing batch of different textiles (“mixed textiles”) made from 100% PES (T-shirt, pillowcase, blanket and towel) and on non-raised textiles made from 100% PES filament yarns (sports shirts and sports pants). Figure 3 shows a selection of the experimental results, comparing a fleece material (raised on both sides, F1) and an interlock material with filling thread (F9), with the mixed batch and non-raised sports shirt 1 and 2. The textiles were washed with low loadings of 1.5 kg and 2 kg (mixed textiles), respectively.
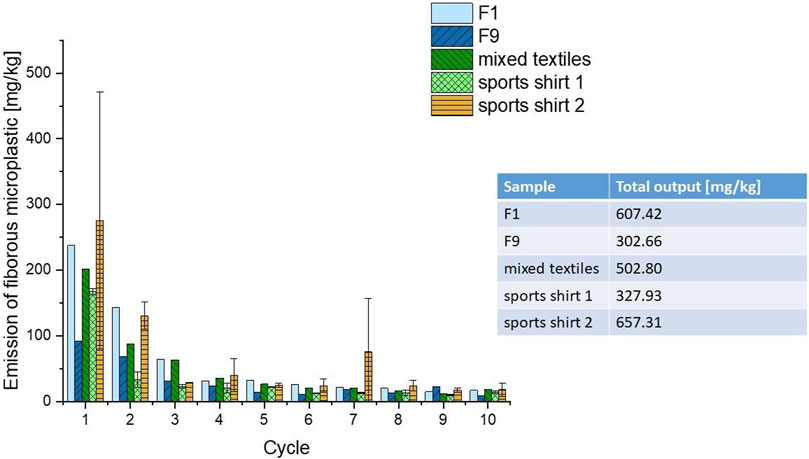
Figure 3. Comparative plot of the FMP emission [mg/kg] of different laundry items over 10 washing cycles. For F1, F9 and mixed textiles: n = 1; for sports shirts 1 and 2: n = 3, the mean values with standard deviation are presented for replicates (n = 3); loading quantities: F1, F9, sports shirts 1 and 2: 1.5 kg, mixed textiles: 2 kg. The table shows the total output of FMP, summed up from 10 washing cycles.
As seen from Figure 3, the overall emission quantities are very different. The interlock material with filling thread (F9) showed the lowest output (302.67 mg/kg in total) for the machine load of 1.5 kg. Comparing the FMP emission of the first washing cycle, the sports shirt 1 emitted a similar amount of FMP as the mixed textile batch, which also included one raised textile (jacket) and one plush fabric (towel). However, the washing batch of standard fleece garments (F1) showed a high emission (607 mg/kg) over the entire course of 10 washing cycles. This value was even topped by sports shirt 2 with a total output of 657 mg/kg. In contrast to these two textiles, the mixed textile batch showed clearly less FMP emission (503 mg/kg). The interlock garment (F9) and the sports shirt 1 released the lowest amounts of FMP (303 and 328 mg/kg) within 10 washing cycles. This comparison shows that non-raised textiles are not per se superior to fleece material and contradicts general expectations for FMP release from non-raised textiles (especially in the first wash). However, similar results were obtained by Kärkkäinen and Sillanpää (2021) and this clearly demonstrates that not just the textile construction, but also various other parameters have an influence on the FMP emission and must be considered in detail.
Figure 3 shows a drop in FMP released in the third wash. This is comparable to data from other researchers (Pirc et al., 2016; Almroth et al., 2018; Lant et al., 2020; Vassilenko et al., 2021) and indicates that washing alone is not responsible for the release of FMP. Raw material production, making-up, and further processing steps can also contribute to fiber fragmentation. If these fiber fragments are not removed from the finished goods after production and processing, they will instead be removed during the first washing cycles in the household laundry and enter the wastewater. For the production of fleece material, the circular knitted yard goods are raised on both sides and optionally sheared, so that a soft and voluminous surface is created. In the process, there is a loss of material, which, according to experience, can add up to 30%.
Table 3 compares the FMP emission for all analyzed textiles, divided in emission of the first, the second and the third to 10th washing cycles. This determination was done to review the hypothesis, that fleece material emits more FMP in the first washing cycles due to the raising process during production.
The garments made out of different textiles emitted a large variation of FMP from 173 mg/kg (F6, machine load 3.5 kg) to 672 mg/kg (F10, machine load 1.5 kg) within ten washing cycles. The smooth surfaces of sports shirt 1 (328 mg/kg) and sports pants (308 mg/kg) seems to be advantageous against standard fleece material with two raised sides (F1, 607 mg/kg and F7, 473 mg/kg), when comparing the overall FMP output for machine loadings of 1.5 kg. In contrast, sports shirt 2 showed an amount of FMP emission (657 mg/kg) in the range of standard fleeces F1 and F10 (672 mg/kg), raised on one side. The textiles with one raised side, but not a classic fleece structure (e.g., F3 and F11), and textiles with a rough surface, which was achieved by other than raising processes (e.g., F6 and F9) emitted FMP in the range of 250 mg/kg to 400 mg/kg.
A high proportion of the overall output of FMP is released from the material in the first two washes [60 mg/kg (F2, 3.5 kg) to 405 mg/kg (sports shirt 2, 1.5 kg)]. This indicates that the fiber fragments are produced during the mechanical treatment of the knitted fabric and the garment production (cutting, making, trimming—CMT). In the case of smooth fabrics, the roughening production step is omitted. The detected fiber fragments and the high FMP release in the first two washing cycles as well as the high FMP release of sports shirt 2 can therefore be attributed to the garment production processes (CMT). It can be assumed that fiber fragments that were already produced in earlier production steps due to various mechanical influences in the yarn processing and the fabric construction (e.g., the knitting process) were already emitted in the wet finishing processes (e.g., dyeing and rinsing). In other studies, it was even observed that PES shirts released significantly more microplastics in the first washes compared to fleece goods, and that both values only converged from the fifth wash onwards (Sillanpää and Sainio, 2017). In general, it is very difficult to make reliable predictions on the estimated FMP release during washing just based on mechanical treatment or product type. The quality of processing, the dyeing processes, the pre-washing, the awareness at production site and others have a huge influence on the FMP emission in the first two washes and beyond.
Commercial textile products vary strongly in grammage, thickness and density (see Table 1), which additionally complicates a comparison. The experimental results shown here demonstrate the necessity to perform washing experiments with each textile to obtain values for FMP release. In this case a forecast without experimental work is not serious.
If these emission quantities are not evaluated according to mg/kg, but as a percentage, a surprising correlation emerges, which is shown in Figure 4: Measured against the total emission, approx. 40%–60% of the FMP are emitted from the items in the first two washing cycles. From the third cycle onwards, the emission values for all samples approach a limit value of approx. 10% of the total amount. For example, the mixed batch, as seen in Figure 3, shows a higher emission in mg/kg during the individual washing cycles, but about the same percentage output as the other samples investigated. This effect was also observed with other samples tested and can be seen in the following Table 4.
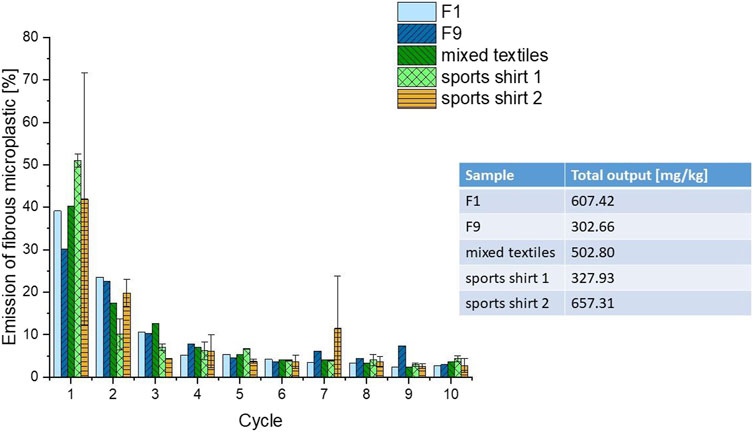
Figure 4. Comparative representation of the FMP emission [%] of different laundry items over 10 washing cycles. For F1, F9 and mixed textiles: n = 1; for sports shirts 1 and 2: n = 3, the mean values with standard deviation are presented for replicates (n = 3); loading quantities: F1, F9, sports shirt 1 and 2: 1.5 kg, mixed textiles: 2 kg.
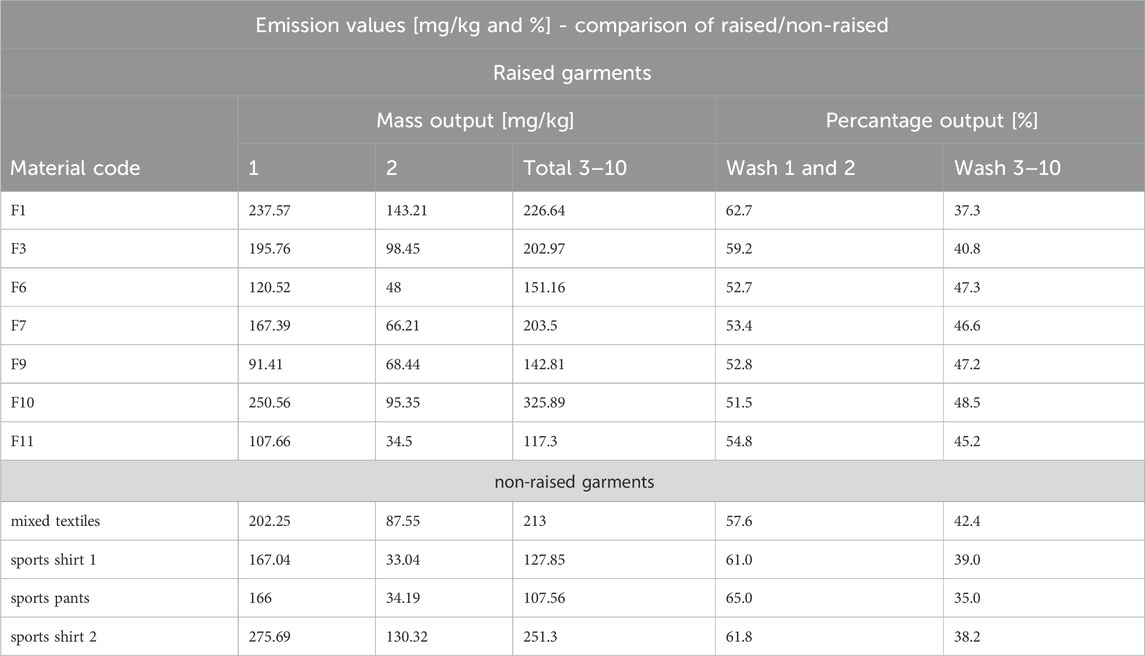
Table 4. Comparison of absolute and percentage emission values of FMP after washing from raised and non-raised garments. Washing conditions according to P 900 were used. Maschine load was 1.5 kg, respectively 2 kg (mixed textiles).
It was found that raised textiles do not necessarily release more FMP in the washing process than non-raised goods. When comparing the percentage of FMP released in the first two washes with the percentage in washes 3–10, it is even noticeable that at the beginning of the washing tests the non-raised textiles (see Table 4) tend to release more than the raised textiles.
3.3 Influence of washing parameter
In addition to the investigation of the FMP output over at least 10 washing cycles, various parameters such as the addition of fabric softener, loading quantity, type of program and spinning speed and the use of soft water, were investigated for the FMP emission. The results are summarized for selected textiles in Table 5.
3.3.1 Fabric softener
The substances added to the washing water have an influence on the washing result. In the experiments shown here, detergent was added to all washing tests, as washing without detergent is not a consumer reality. Another chemical that can be added to the washing process is fabric softener. The use of fabric softener does not normally comply with the manufacturer’s instructions for functional clothing, and it was not recommended here, as well. However, as it is quite possible that this clothing is washed with fabric softener in household laundry, the effect on the microplastic emission should be investigated. Textiles F6 and F7 were chosen for this experiment due to their differences in fabric construction (fur knit fabric bonded with plain knit vs. heavy fleece with reverse backside). The reduced stiffness of the fibres should result in less friction between the fibres, which could lead to a lower microplastic emission.
To investigate its contribution in terms of FMP emission, the maximum recommended amount of fabric softener (30 mL) according to the manufacturer was added to the washing process. The amount of FMP release was determined gravimetrically and accumulated over 10 cycles. The use of fabric softener has no influence on the amount of FMP released into the washing process (see Table 5). In the case of F6, the output quantity into the washing process is somewhat higher (approx. 80 mg/kg; 398.51 mg/kg vs. 319.68 mg/kg). However, this effect could not be reproduced in the investigation of another material (F7), so that it can be assumed that there is no or, depending on the material, only a minor influence on the FMP release. These results are in line with the observations in the literature (Pirc et al., 2016; Lant et al., 2020), where no significant influence of detergent and fabric softener on fiber release was observed.
3.3.2 Loading quantity
The loading quantity of the washing machine influences the mechanical stress on the textiles during washing and thus the fiber release (Lant et al., 2020). For that reason, different loading quantities, namely, 3.5 kg (corresponding to a full load of the washing drum) and 1.5 kg (corresponding to a half load of the washing drum) were used in almost all the tests (see Table 1). Figure 5 shows the difference in the amount of FMP emission for three materials. As can be seen in Figure 5, the output of FMP is always higher at half of the load of the washing drum when compared to the full load of the washing drum. In the examples shown here, the lower load results in approximately a doubling of the value in the washing process. This is probably due to the mechanics in the washing process, as the falling height of the textiles is significantly higher at lower loads than at full load. On the other hand, at lower loads, the ratio of wash water to garments is higher, resulting in a better perfusion of the garments. These results correlate very good with an experimental set-up from Volgare et al., where increasing the number of polyester T-shirts (1–17) resulted in decreasing emission of FMP (401 ± 17 to 76 ± 5 mg/kg). However, the amount of washing water was automatically regulated by the washing machine depending on the washing load (Volgare et al., 2021). In contrast to that, the automatic water regulation was deactivated in the experiments presented here. For the consumer, these results lead to the recommendation to load the washing machine with a large amount of laundry to reduce the release of FMP. However, overloading the machine could have a negative impact on the washing result and should therefore be avoided (Lant et al., 2020).
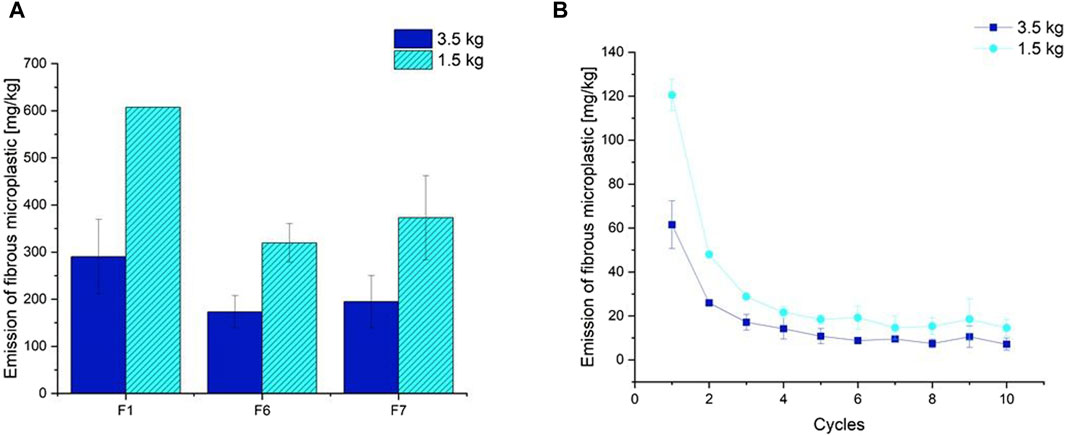
Figure 5. Representation of FMP emission rates (A) (sum 1–10) at different loading rates during household washes and (B) exemplary representation of FMP emission in the different wash cycles (F6).
3.3.3 Washing program, spin speed and hardness of the water
Other parameters investigated were the influence of the washing program (easy-care or express program), the spin speed (900 rpm vs. 1,200 rpm) and the hardness of the water used (Mönchengladbach: 8.4–14° dH (https://www.new.de/wasser/trinkwasserqualitaet) compared to soft water). Figure 6 shows the results of the comparative tests for material F7 as an example. Details of the single washing programs are shown in Table 2. As can be clearly seen from Figure 6, neither increasing the spin speed from 900 rpm (P 900) to 1,200 rpm (P1200) nor using fabric softener (S) or soft water (W) leads to an increased FMP emission compared to the control speed (P 900). The selection of the washing program, on the other hand, may show a slight influence on the emission. The use of the express program with a low wash time (E 1200; run time 30 min, wash temperature 40 °C, spin speed 1,200 rpm) shows a slightly lower value compared to the control load washed using the easy care program (P 1200, run time 1:59 h, wash temperature 40 °C, spin speed 1,200 rpm). De Falco et al. published similar results, where a reduced washing time also led to a slightly reduced release of microplastics (De Falco et al., 2018). If the output values of the 3–10 washes are compared as a percentage of the total emission (washes 1–10), the following picture emerges (see Figure 7).
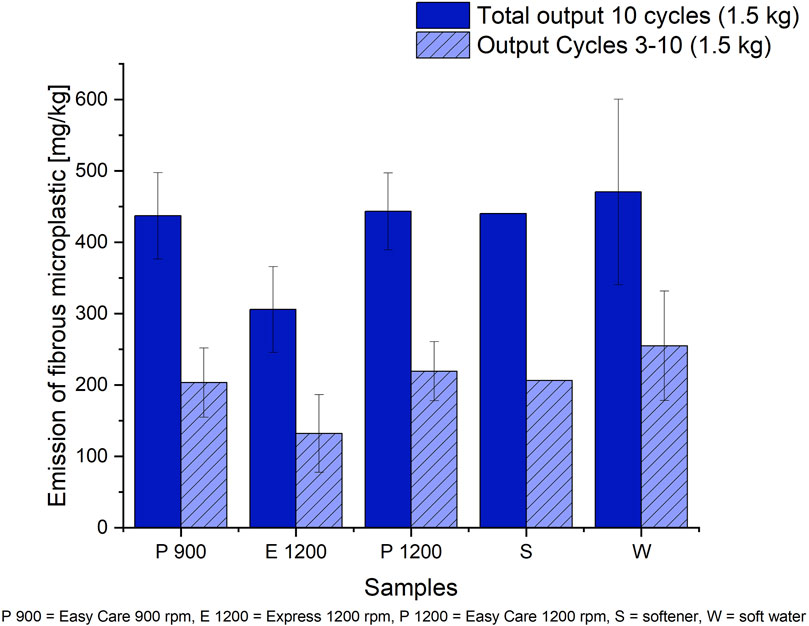
Figure 6. Comparative studies of different parameters (program, spin number, fabric softener, water hardness) on FMP emission in mg/kg for Textile F7.
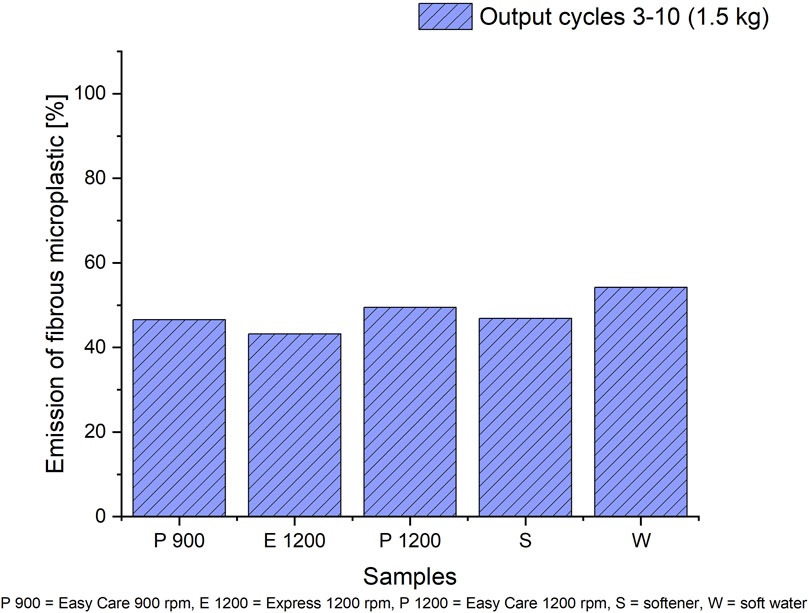
Figure 7. Comparative studies of different parameters for F7 (program, spin number, fabric softener, water hardness) on FMP emission in %.
For all parameters investigated, similar amounts of FMP (40%–50% of the total emission) were released in percentage terms in washes 3–10. Figure 8 shows the percentage emission values per wash cycle of F7. It is clear that already more than 50% of the total emission takes place in the first two washes. This observation is relatively independent of the washing conditions, as shown in Table 6 below. Palacios-Marín et al. investigated different textiles from different PES yarn types. They noticed similar effects with a significant decrease of the emitted fiber mass after the first wash and comparative emissions after three or four washing cycles. However, a real comparison with the data analyzed here, is not possible, as Palacios-Marín et al. performed a maximum of five washing cycles (Palacios-Marín et al., 2022). The emission of about 50% FMP within the first two washes of a total amount of 10 washes is relatively independent of the washing parameters (see Table 6). A breakdown of the emission quantity of the first two washes for the different textiles in Table 4 shows a similar tendency. Here, values between 51% and 62% are obtained, with the higher values being predominantly obtained for smooth, non-raised fabrics. These results clearly show that the amount of FMP released is not solely dependent on the construction of the textile and that fleece materials do not necessarily have the highest emission values. In addition, the data shows that a relatively good prediction can be made of how much FMP will be washed out of a textile if only the first two washes are considered. For the future, this offers the possibility to determine the emission quantities of textiles by only a few (for example, 3–5) washes and to extrapolate them to 10 washes. In this way, the number of washing cycles required to compare and evaluate textiles can be reduced, saving resources.
4 Conclusion
In this study, 18 different garment types made of 100% PES or from PES in mixture with other synthetic materials were subjected to different washing programs and the effect on the release of FMP was investigated. The amount of FMP release varied greatly depending on the textiles. Smooth textiles did not shed fewer FMP than mechanically treated fleece articles. Predictions of the FMP release on basis of material parameters and mechanical treatment are very difficult. The consumer can reduce FMP release by using full loads of the washing drum and short washing programs. Approx. 50% of the FMP released over a 10 washing cycles is released within the first two cycles. This is independent of the washing conditions and textile parameters. The results show that the extrapolation of the amounts of FMP released within the first two washes can be used to calculate the approximately released amount of FMP within ten washes and save time and resources in washing experiments. Additionally, this result leads to the conclusion that neither the washing parameters nor the textile parameters (e.g., construction and finishing) are solely responsible for the release of FMPs from synthetic textiles. These results show possible solutions to reduce the uncontrolled FMP emission into aquatic systems: First of all, the textile manufacturing processes must become less destructive and abrasive and second the textiles and garments need to be cleaned prior to distribution. This concept of post-cleaning must be carried out in such a way that FMP is not emitted on the production sites without a FMP hold back in effluents or exhaust air. Overall, it is difficult to compare the results with those from the literature, as tests are carried out under different conditions (selected textiles, washing program, detergents, etc.). The evaluation methods and calculation of the output quantity also differ considerably from each other in some cases, but in many cases lead to similar results.
Data availability statement
The raw data supporting the conclusion of this article will be made available by the authors, without undue reservation.
Author contributions
KK: Writing–original draft, Visualization. SaK: Conceptualization, Writing–original draft, Investigation, Methodology, Visualization. SB: Conceptualization, Investigation, Methodology, Writing–review and editing. JM: Conceptualization, Investigation, Methodology, Writing–review and editing. KR: Investigation, Writing–review and editing. EB: Conceptualization, Funding acquisition, Supervision, Writing–review and editing. MR: Conceptualization, Funding acquisition, Supervision, Writing–review and editing.
Funding
The author(s) declare financial support was received for the research, authorship, and/or publication of this article. The experiments were carried out within the framework of the joint project “TextileMission,” which was funded by the German Federal Ministry of Education and Research (BMBF, grant no. 13NKE010B), Germany.
Acknowledgments
The authors would like to thank all partners involved in the project, as well as the associated partners. The authors also would like to thank Malin Obermann for her support in textile analytics and Michael Stark for valuable hints and discussion. An overview of the partners and the results of the joint project can be found at https://textilemission.bsi-sport.de/partner/
Conflict of interest
The authors declare that the research was conducted in the absence of any commercial or financial relationships that could be construed as a potential conflict of interest.
Publisher’s note
All claims expressed in this article are solely those of the authors and do not necessarily represent those of their affiliated organizations, or those of the publisher, the editors and the reviewers. Any product that may be evaluated in this article, or claim that may be made by its manufacturer, is not guaranteed or endorsed by the publisher.
Supplementary material
The Supplementary Material for this article can be found online at: https://www.frontiersin.org/articles/10.3389/fenvs.2024.1330922/full#supplementary-material
References
Almroth, B. M. C., Åström, L., Roslund, S., Petersson, H., Johansson, M., and Persson, N.-K. (2018). Quantifying shedding of synthetic fibers from textiles; a source of microplastics released into the environment. Environ. Sci. Pollut. Res. 25, 1191–1199. doi:10.1007/s11356-017-0528-7
Bannick, C.-G., Brandt, S., Bernicke, M., Dienemann, C., Gast, M., Hofmeier, M., et al. (2018). Klärschlammentsorgung in der Bundesrepublik Deutschland. Umweltbundesamt; Fachgebiete III 2.4 – abfalltechnik, Abfalltechniktransfer und III 2.5 – Überwachungsverfahren, Abwasserentsorgung 2018, BASF (2022), Detergent reduces microfiber release during washing. TextileTechnology, Dec. 5th 2022, Available at: https://www.textiletechnology.net/technology/news/basfinditex-detergent (Accessed October 5, 2023).
Browne, M. A., Crump, P., Niven, S. J., Teuten, E. L., Tonkin, A., Galloway, T., et al. (2011). Accumulation of microplastic on shorelines woldwide: sources and sinks. Environ. Sci. Technol. 45, 9175–9179. doi:10.1021/es201811s
Bruce, N., Hartline, N., Karba, S., Ruff, B., Sonar, S., and Holden, P. (2016). Microfiber pollution and the apparel industry. University of California Santa Barbara, Bren School of Environmental Science and Management. Available at: http://brenmicroplastics.weebly.com/uploads/5/1/7/0/51702815/bren-patagonia_final_report.pdf) (Accessed August 19, 2016).
Cai, Y., Mitrano, D. M., Hufenus, R., and Nowack, B. (2021). Formation of fiber fragments during abrasion of polyester textiles. Environ. Sci. Technol. 55, 8001–8009. doi:10.1021/acs.est.1c00650
Cai, Y., Yang, T., Mitrano, D. M., Heuberger, M., Hufenus, R., and Nowack, B. (2020). Systematic study of microplastic fiber release from 12 different polyester textiles during washing. Environ. Sci. Technol. 54, 4847–4855. doi:10.1021/acs.est.9b07395
CIRFS (2021). European man made fibres association. Available at: https://www.cirfs.org/statistics/key-statistics/world-production-fibre (visited September 28, 2023).
Cole, M., Lindeque, P., Halsband, C., and Galloway, T. S. (2011). Microplastics as contaminants in the marine environment: a review. Mar. Pollut. Bull. 62 (12), 2588–2597. doi:10.1016/j.marpolbul.2011.09.025
De Falco, F., Gullo, M. P., Gentile, G., Di Pace, E., Cocca, M., Gelabert, L., et al. (2018). Evaluation of microplastic release caused by textile washing processes of synthetic fabrics. Environ. Pollut. 236, 916–925. doi:10.1016/j.envpol.2017.10.057
DIN EN 12127:1997-12 (2024). Textile Flächengebilde – bestimmung der flächenbezogenen Masse unter Verwendung kleiner Proben.
European Commission (2019). European commission, directorate-general for research and innovation, environmental and health risks of microplastic pollution. Luxembourg: Publications Office. https://data.europa.eu/doi/10.2777/54199.
Galvão, A., Aleixo, M., De Pablo, H., Lopes, C., and Raimundo, J. (2020). Microplastics in wastewater: microfiber emissions from common household laundry. Environ. Sci. Pollut. Res. 27, 26643–26649. doi:10.1007/s11356-020-08765-6
Gavigan, J., Kefela, T., Macadam-Somer, I., Suhl, S., and Geyer, R. (2020). Synthetic microfiber emissions to land rival those to waterbodies and are growing. PLoSONE 15 (9), e0237839. doi:10.1371/journal.pone.0237839
GESAMP (2016). “Sources, fate and effects of microplastics in the marine environment: part two of a global assessment,” in IMO/FAO/UNESCO-IOC/UNIDO/WMO/IAEA/UN/UNEP/UNDP joint group of experts on the scientific aspects of marine environmental protection. Editors Kershaw, P. J., and Rochman, C. M. Rep. Stud. GESAMP No. 93.
Hartmann, N. B., Hüffer, T., Thompson, R. C., Hassellöv, M., Verschoor, A., Daugaard, A. E., et al. (2019). Are we speaking the same language? Recommendations for a definition and categorization framework for plastic debris. Environ. Sci. Technol. 53, 1039–1047. doi:10.1021/acs.est.8b05297
Hazlehurst, A., Tiffin, L., Sumner, M., and Taylor, M. (2023). Quantification of microfibre release from textiles during domestic laundering. Environ. Sci. Pollut. Res. 30, 43932–43949. doi:10.1007/s11356-023-25246-8
Hernandez, E., Nowack, B., and Mitrano, D. M. (2017). Polyester textiles as a source of microplastics from households: a mechanistic study to understand microfiber release during washing. Environ. Sci. Technol. 51, 7036–7046. doi:10.1021/acs.est.7b01750
ISO/TR 21960:2020. (2024) ISO/TR 21960:2020: plastics — environmental aspects — state of knowledge and methodologies.
Kärkkäinen, N., and Silanpää, M. (2021). Quantification of different microplastic fibres discharged from textiles in machine wash and tumble drying. Environ. Sci. Pollut. Res. 28, 16253–16263. doi:10.1007/s11356-020-11988-2
Kelly, M. R., Lant, N. J., Kurr, M., and Burgess, J. G. (2019). Importance of water-volume on the release of microplastic fibers from laundry. Release Microplastic Fibers Laund. Environ. Sci. Technol. 53, 11735–11744. doi:10.1021/acs.est.9b03022
Klein, S., Dimzon, J. K., Eubeler, J., and Knepper, T. P. (2018). “Analysis, occurrence, and degradation of microplastics in the aqueous environment,” in Freshwater microplastics – emerging environmental contaminants? The handbook of environmental science. Editors M. Wagner, and S. Lambert (Cham, Switzerland: Springer Open), 58, 69–84.
Lant, N. J., Hayward, A. S., Peththawadu, M. M. D., Sheridan, K. J., and Dean, J. R. (2020). Microfiber release from real soiled consumer laundry and the impact of fabric care products and washing conditions. PLoSONE 15 (6), e0233332. doi:10.1371/journal.pone.0233332
Lim, J., Choi, J., Won, A., Kim, M., Kim, S., and Yun, C. (2022). Cause of microfibers found in the domestic washing process of clothing; focusing on the manufacturing, wearing, and washing processes. Fash. Text. 9, 24. doi:10.1186/s40691-022-00306-8
Liu, J., Liang, J., Ding, J., Zhang, G., Zeng, X., Yang, Q., et al. (2021). Microfiber pollution: an ongoing major environmental issue related to the sustainable development of textile and clothing industry. Environ. Dev. Sustain. 23, 11240–11256. doi:10.1007/s10668-020-01173-3
Mermaid Consortium, (2017). Microfiber release from clothes after washing: hard facts, figures and promising solutions. Position Paper May 2017
Mintening, S. M., Int-Veen, I., Löder, M. G. J., Primpke, S., and Gerdts, G. (2017). Identification of microplastic in effluents of waste water treatment plants using focal plane array-based micro-Fourier-transform infrared imaging. Water Res. 108, 365–372. doi:10.1016/j.watres.2016.11.015
Palacios-Marín, A. V., Jabbar, A., and Tausif, M. (2022). Fragmented fiber pollution from common textile materials and structures during laundry. Text. Res. J. 92 (13–14), 2265–2275. doi:10.1177/00405175221090971
Periyasamy, A. P. (2023). Environmentally friendly approach to the reduction of microplastics during DomesticWashing: prospects for machine vision in microplastics reduction. Toxics 11, 575. doi:10.3390/toxics11070575
Periyasamy, A. P., and Tehrani-Bagha, A. (2022). A review on microplastic emission from textile materials and its reduction techniques. Polym. Degrad. Stab. 199, 109901. doi:10.1016/j.polymdegradstab.2022.109901
Pirc, U., Vidmar, U., Mozer, A., and Kržan, A. (2016). Emissions of microplastic fibers from microfiber fleece during domestic washing. Environ. Sci. Pollut. Res. 23, 22206–22211. doi:10.1007/s11356-016-7703-0
Rochman, C. M., Tahir, A., Williams, S. L., Baxa, D. V., Lam, R., Miller, J. T., et al. (2015). Anthropogenic debris in seafood: plastic debris and fibers from textiles in fish and bivalves sold for human consumption. Sci. Rep. 5, 14340. doi:10.1038/srep14340
Schöpel, B., and Stamminger, R. (2019). A comprehensive literature study on microfibres from washing machines. Tenside Surf. Det. 56 (2), 94–104. doi:10.3139/113.110610
Sillanpää, M., and Sainio, P. (2017). Release of polyester and cotton fibers from textiles in machine washings. Environ. Sci. Pollut. Res. 24, 19313–19321. doi:10.1007/s11356-017-9621-1
Singh, R. P., Mishra, S., and Das, A. P. (2020). Synthetic microfibers: pollution toxicity and remediation. Chemosphere 257, 127199. doi:10.1016/j.chemosphere.2020.127199
Sinner, H. (1960). Ueber das Waschen mit Haushaltwaschmaschinen: in welchem Umfange erleichtern Haushaltwaschmachinen und-geraete dasWaesche waschen im Haushalt? Hamburg: Haus und Heim-Verlag.
Stanton, T., Johnson, M., Nathanail, P., MacNaughtan, W., and Gomes, R. L. (2019). Freshwater and airborne textile fibre populations are dominated by ‘natural’, not microplastic, fibres. Sci. total Environ. 666, 377–389. doi:10.1016/j.scitotenv.2019.02.278
Tiffin, L., Hazlehurst, A., Sumner, M., and Taylor, M. (2021). Reliable quantification of microplastic release from the domestic laundry of textile fabrics. J. Text. Inst. 113 (4), 558–566. doi:10.1080/00405000.2021.1892305
Vassilenko, E., Watkins, M., Chastain, S., Mertens, J., Posacka, A. M., Patankar Ross, P. S., et al. (2021). Domestic laundry and microfiber pollution: exploring fiber shedding from consumer apparel textiles. PLOS ONE, 7, e0250346. doi:10.1371/journal.pone.0250346
Volgare, M., De Falco, F., Avolio, R., Castaldo, R., Maria Emanuela Errico, M. E., Gentile, G., et al. (2021). Washing load influences the microplastic release from polyester fabrics by affecting wettability and mechanical stress. Sci. Rep. 11, 19479. doi:10.1038/s41598-021-98836-6
Yang, L., Qiao, F., Lei, K., Li, H., Kang, Y., Cui, S., et al. (2019). Microfiber release from different fabrics during washing. Environ. Pollut. 249, 136–143. doi:10.1016/j.envpol.2019.03.011
Zambrano, M. C., Pawlak, J. J., Daystar, J., Ankeny, M., Cheng, J. J., and Venditti, R. A. (2019). Microfibers generated from the laundering of cotton, rayon and polyester based fabrics and their aquatic biodegradation. Mar. Pollut. Bull. 142, 394–407. doi:10.1016/j.marpolbul.2019.02.062
Keywords: polyester, textiles, fleece, fibrous microplastics, household laundry
Citation: Klinkhammer K, Kolbe S, Brandt S, Meyer J, Ratovo K, Bendt E and Rabe M (2024) Release of fibrous microplastics from functional polyester garments through household washing. Front. Environ. Sci. 12:1330922. doi: 10.3389/fenvs.2024.1330922
Received: 31 October 2023; Accepted: 05 March 2024;
Published: 26 April 2024.
Edited by:
Thomas Stanton, Loughborough University, United KingdomReviewed by:
Alice Hazlehurst, University of Leeds, United KingdomLisa M. Erdle, Five Gyres Institute, United States
Copyright © 2024 Klinkhammer, Kolbe, Brandt, Meyer, Ratovo, Bendt and Rabe. This is an open-access article distributed under the terms of the Creative Commons Attribution License (CC BY). The use, distribution or reproduction in other forums is permitted, provided the original author(s) and the copyright owner(s) are credited and that the original publication in this journal is cited, in accordance with accepted academic practice. No use, distribution or reproduction is permitted which does not comply with these terms.
*Correspondence: Maike Rabe, bWFpa2UucmFiZUBocy1uaWVkZXJyaGVpbi5kZQ==
†These authors have contributed equally to this work and share first authorship