- 1Academic Affairs Department, Wenzhou Business College, Wenzhou City, China
- 2Institute of Scientific Research, Great Bay University, Dongguan City, China
The purpose of this study is to explore when win‒win lean practices can be combined with auditing mechanisms, specifically when adopting the combination of the two. In it, we investigate which capabilities are produced and how they build a stronger control system and produce a greater control force for supplier involvement in the development of the lean practices environment. Does the control force have a positive effect on raising resilience and further realizing the targets of sustainable supplier management? The resource-based view (RBV) is an important theoretical basis for this study. Covariance-based Structural Equation Modelling (CB-SEM) is the main method applied to analyse data from 231 Chinese manufacturers to test and verify the research questions. To test and verify the research questions with CB-SEM before, we test and measure the validity and reliability of the constructs through factor loadings, composite reliability (CR), and average variance extracted (AVE). In addition, we also verify the discriminant validity through the Fornell-Lacker criterion and Cross Loadings and test the multicollinearity. We use AMOS and SPSS 23.0 as our analysis tools. According to the test results, win‒win lean practices can increase supplier dependence on leading companies or manufacturers. It can drive supplier involvement in the formulation of a lean practice environment, expand control over suppliers, produce greater visibility, and further have a positive effect on resilience. In addition, when combined with auditing mechanisms, dependency will drive suppliers to cooperate with auditing practices and reduce their resistance, increase their involvement in the formulation of lean practice environments, further promoting resilience. In addition, dependency and auditing intervention will induce or even raise stakeholder pressure, which can usually maintain the supplier’s cooperation. Finally, dependence, positive intervention, and stakeholder pressure can be deemed strategic resources or capabilities. Based on the above, a cycle between three will be formulated and become a stronger control system, producing greater control force to continue maintaining supplier involvement. It will produce a positive effect to enhance resilience and further realize sustainable supplier management.
Introduction
Building a supply chain environment has become an important competitive strategy for coping with heavy competitive pressure. In a supply chain, effective collaboration between manufacturers and partners in related operations is critical for promoting competitiveness and increasing economic profits; however, collaboration also complicates supply chain operational processes, further leading to serious pollution emissions. Due to social expectations and pressure, manufacturers need to adopt remedies to address supply chain pollution problems.
To reduce the pollution emissions of supply chains, suppliers are critical. In fact, if suppliers purchase highly polluting raw materials and the process of manufacturing the semifinished product involves more pollution and contaminates the water and air, then when these semifinished products are used by manufacturers to produce finished products, the entire manufacturing process can induce air or water pollution. When customers receive the finished product, the use of this product may also release noxious gases because the raw material from which it is made is highly polluting. Based on the above aspects, manufacturers should think about how to control supplier purchases of raw materials and production activities to avoid raising the pollution emissions of the whole supply chain (Brandenburg and Rebs, 2015). Therefore, the development of sustainable supplier management is a necessary way to control raw material purchasing and supplier production activities.
Sustainable supplier management is clearly a critical activity, from purchasing to the process of producing semifinished products, that can be undertaken by suppliers (Govindan et al., 2015). To develop sustainable supplier management, the current research results focus on two directions. First, researchers argue that fit and cooperative suppliers are important bases. Therefore, they adopt a decision-making approach to help manufacturers select fit suppliers (Orji and Wei, 2015; Zimmer et al., 2016; Foroozesh et al., 2018). Second, researchers have tried to develop processes to improve sustainable supplier management. For example, Reuter et al. (2010) considered a firm’s dynamic ability to explore improvements in sustainable supplier management, and Wolf (2014) and Rashidi and Saen (2018) considered social pressure and environmental performance when exploring programmes to improve sustainable supplier management.
However, suppliers are independent and are, thus, not always fully compliant. It is possible that the profit motive could drive them to engage in opportunistic behaviours, indirectly purchase polluting raw materials (Appolloni et al., 2014) and adopt operational processes or production activities that involve pollutants (Chen and Ye, 2022). These opportunistic behaviours, even when there is an awareness that they are occurring, are difficult to prevent. Thus, the related pollution emissions that result from them usually become quite serious. Although the current research, including the work of Amege and Hanu (2018), still suggests that supplier selection can reduce the risk of the occurrence of opportunistic behaviour, it is still difficult to fully control suppliers. As a result, more practitioners have argued that if resilience in the existing sustainable supplier management base can be increased, then it can effectively prevent or even control the opportunistic behaviour of suppliers in purchasing and production activities, further ensuring the efficiency of sustainable supplier management.
Resilience is the ability of supply chains to prevent, respond to, and control uncertainty risks, including opportunistic behaviours (Ponomarov and Holcomb, 2009; Day, 2014). According to Eryarsoy et al. (2022), the establishment of a greater organizational structure or environment can strategically produce resources or capabilities. According to the resource-based view (RBV), these resources or capabilities can become a control force and enhance resilience (Ji et al., 2020). Based on the above, the current research results indicate that the development of a lean practice environment can produce some strategic resources and capabilities for enhancing resilience. Specifically, lean practices are used to eliminate redundant activities and maximize operational efficiency through pull production, 5S, employee involvement, and total productive maintenance (TPM; Ruiz-Benítez et al., 2018). When the lean practices environment is established, closer collaboration as an organizational strategic capability will be produced (Trujillo-Gallego et al., 2021). It can expand visibility, indirectly prevent, and even control opportunistic behaviours, thus increasing resilience (Yu and Huo, 2018; Abideen and Mohamad, 2021) and further realizing sustainable supplier management.
However, the principle of lean practices requires suppliers to be fully involved with manufacturers to build the lean environment (Chavez et al., 2013). However, whether suppliers are fully involved in the formulation of lean practice environments is critical. A large body of the literature has mainly considered the role of supplier involvement in lean practice improvement, further proving its importance in terms of lean practices and providing more valuable suggestions to improve supplier involvement (Arkader, 2001; Ugochukwu et al., 2012; Bortolotti et al., 2016; Godinho Filho et al., 2016; Yadav et al., 2019). However, over 48% of manufacturers find it difficult to require suppliers to be fully involved in the formulation of lean practice environments (Mirdad and Eseonu, 2015). Until now, supplier involvement has remained a problem and is still confusing to manufacturers as manufacturers find difficulty in requiring full supplier involvement. Sometimes, as Paranikas et al. (2015) stated, manufacturers even become minorities. If supplier involvement is hard to maintain, the establishment of a lean practice’s environment will be affected. A closer collaboration is hard to produce, which leads to the opportunistic behaviours from suppliers being hard to prevent, similar to the concept of poor resilience. Finally, the realization of sustainable supplier management is also affected. Therefore, how to address this and successfully guide all suppliers to become fully involved is still a challenge. However, there is less interest in deeply exploring how to guide suppliers to become fully involved, and manufacturers are also looking for a solution. This has become a gap in the existing study.
When we carefully analyse the experiences and annual sustainable reports of a few successful cases, such as the Taiwan Semiconductor Manufacturing Company (TSMC) and Samsung Group, which involved informal interviews with 72 middle supervisors, a solution to the above problem may emerge. We find that if manufacturers can adopt a win‒win strategy in terms of lean practices, then combined with auditing mechanisms, they will produce strategic resources and capabilities, it becomes a stronger control system and produces a control force to improve supplier involvement in the development of the lean practices environment. Finally, it increases the resilience to better prevent and control opportunistic behaviour, further control the purchasing and manufacturing process of suppliers, and realize highly efficient sustainable supplier management. As a concept of RBV, these capabilities are strategic resources because they have a positive effect on enhancing resilience. However, when adopting the combination of win‒win lean practices and auditing mechanisms, which capabilities are produced and how can these capabilities build a stronger control system and produce a greater control force for supplier involvement in the development of the lean practices environment? Does the control force have a positive effect on raising resilience and further realizing the targets of sustainable supplier management? Although some researchers, such as Scholten and Schilder (2015) and Kochan and Nowicki (2018), have noted that lean practices and auditing can be improved at the same time and can have a positive effect on the use of resilience to prevent opportunistic behaviours, it is still difficult to answer the above questions.
As a result, this study aims to explore the above questions. In this study, the RBV is our fundamental basis. We adopt the core idea of the RBV to deeply explore our research question. Because the RBV is a fit theoretical base to explore the production of critical resources, abilities, forces, or other factors, its purpose aligns with our research questions.
Theoretical framework
Given the research goal, the resource-based view (RBV) is an important theoretical basis from which to explore our research question. The RBV was developed in 1984 by Wernerfelt, 1984 and its basic supposition is that firms have different tangible and intangible resources or capabilities and that these resources and capabilities can provide unique opportunities for firms to maintain or even improve their competitive advantage.
According to the RBV, firms can develop their competitive advantage by creating strategic resources and/or capabilities (Barney, 1991). Specifically, resources and/or capabilities must be valuable, rare, inimitable, and nonsubstitutable. According to Barney (1991), resources can be categorized as physical capital, human capital, and organizational capital. Of course, resources can also be extended to include financial capital, technological capital, and reputational capital (Grant, 1991). These resources are possibly tangible, such as infrastructure, or intangible, such as information or knowledge sharing (Galbreath, 2005). In addition to resources, organizational capabilities are also an important factor in developing a competitive advantage. Therefore, capabilities also fall within the scope of the RBV. However, capabilities are different from resources. Organizational capabilities are defined as higher-order constructs that rely on the bundling of resources (Brandon-Jones et al., 2014). When resources are combined and utilized together, they create capabilities (Grant, 1991). A competitive advantage created by capabilities will more deeply strengthen an organization’s management and processes and is therefore more likely to be sustainable compared to a competitive advantage created purely by resources (Brush & Artz, 1999).
Based on the above aspects, recent studies have usually explored the development of competitive advantage through the lens of the RBV, and their models have often been developed with a three-level structure, including critical tangible and intangible resources, the production of organizational capabilities, and competitive advantage. If, as stated in the introduction, the control of raw material purchases and the production activities of suppliers leads to sustainability and if resilience is an organizational capability, then according to our research questions, we aim to explore why the combination of win‒win lean practices and auditing mechanisms can raise resilience and help manufacturers prevent and control the opportunistic behaviours of suppliers, which is the same approach as that taken to explore a rare resource or ability. Therefore, the application of the RBV in this study is appropriate. Some recent studies have certainly adopted the three-level theoretical framework to explore the same question. For example, Brandon-Jones et al. (2014) tried to explore the development of supply chain resilience and robustness; they assumed that supply chain connectivity and information sharing are rare resources and that these two resources can produce critical capabilities, such as visibility, and can further increase resilience and robustness. Dubey et al. (2017) explored improvements in supply chain resilience and assumed that connectivity and information sharing are rare resources that produce high visibility, thereby improving resilience. Brusset and Teller (2017) developed a three-level model to explore improvements in resilience. Organizational, informational, relational, and human resources are critical and promote external integration and flexibility, which improve resilience. Based on the above aspects, this study develops a three-level theoretical framework to explore our research question.
Literature review and theoretical framework
Combination of win‒win lean practices and auditing mechanisms
To explore our research question, we first need to introduce how a few successful real-world companies have developed a framework for combination of the win-win lean practices and auditing mechanisms. Based on the framework, we also understand how the combination develops a stronger control system and produce control force to promote supplier involvement in development of the lean practices environment. Therefore, we refer to the Corporate Social Responsibility (CSR) Report of TSMC (2020), the Sustainable Future Report of Samsung Electronics (2020), and the Supplier Responsibility Progress Report of Apple (2020). In addition, we also adopt informal interviews with 72 middle superiors from these companies. The TSMC is a global leader of the semiconductor manufacturing industry; Samsung Electronics is the world’s largest manufacturer of consumer electronics and components such as the semiconductor; and Apple is the leader in production of consumer electronics world over. Heterogeneous seems like existing in different companies using of the combination of win-win lean practices and auditing mechanisms. However, TSMC has established a long-term cooperative relationship with Apple. Therefore, they use common strategies. As for Samsung Electronics, its main competitor is TSMC in the area of electronics components for semiconductors. A healthy competition exists between the two companies, and they share mutual strategies, such as combination of win-win lean practices and auditing mechanisms. Thus, the problem of heterogeneity is nonexistent. Based on the above aspects, we further analyse and draw the following conclusions.
First, we discuss win‒win lean practices. TSMC constructed a virtual fabrication system to develop a highly transparent production process, similar to a lean practice environment. Through this system, TSMC was able to monitor production operation, control raw material inventory and demand, and eliminate any redundant activities to increase production efficiency. Most importantly, suppliers were also involved in this system, strengthening the close collaboration between TSMC and its suppliers. Samsung also adopted a digital manufacturing platform in its production process. Through this digital manufacturing platform, further lean manufacturing with suppliers could be accomplished. For Apple, because reducing costs is always an important goal, the company developed its own lean practice perspective to integrate with its suppliers and control production costs. Then, for any supplier that cooperates with lean practices, these three companies usually adopt a win‒win strategy to attract and encourage supplier involvement in the formulation of a lean practice environment. The purpose of the win‒win strategy is to reconcile the divergent interests between participants to provide parties with joint benefits as an outcome of the specific negotiation (Thomas et al., 2013), which means that companies help suppliers maintain their market share and ensure that these suppliers are making progress. Because companies help suppliers expand their order sourcing and raise their economic profits, a closer “dependence” is produced. According to Sun (2018), dependence can certainly be deemed an important strategic resource and capability. To maintain economic profits, a supplier will accept this dependence, and when this dependence is deepened, these three companies have greater control over the supply chain and can require suppliers to increase their intention to attend to the formulation of a lean practice environment. Based on the above aspects, a successful win‒win lean practice is established. In fact, win‒win lean practices have further helped these three companies grasp and understand any situation because of the associated dependence.
Second, after the dependence is produced through win‒win lean practices, these companies further implement auditing mechanisms. The auditing process can be divided into four steps. In the first step, companies develop relevant supplier management indices. For example, TSMC requires every supplier to abide by its “supplier behaviour standard”, Apple has its own comprehensive supplier measurement standard, and Samsung has developed a standard to raise supplier awareness of sustainability. These standards and indices focus on requirements for raw material purchases and low-emission production activities. These two requirements are critical for the successful improvement of sustainable supplier management. In the second step, companies measure the risk of each supplier and consult regularly with the supplier to ensure sustainable purchases of raw materials and production activities. Companies encourage suppliers to abide by these standards and requirements to reduce the relevant risk in terms of raw material purchases and production activities. In the third step, auditing is improved by training auditors to ensure that every supplier satisfies the standards and requirements. Finally, these three companies maintain continuous improvements; therefore, they must carefully monitor their suppliers. One question arises from this: why do suppliers readily accept and cooperate with the auditing process? The critical factor is their dependence on win‒win lean practices in turning a profit. As previously stated, the purpose of the win‒win strategy is to help suppliers maintain their market share and ensure that these suppliers are making progress. Therefore, when improving auditing processes, dependence will reduce suppliers’ resistance to auditing, further allowing the auditing mechanism to be a “positive intervention”. Positive intervention can also be deemed an important strategic organizational capability (Chen and Ye, 2022). If suppliers do not accept the positive intervention, then they understand that their economic profits will be affected by dependence. These interventions help these companies more deeply grasp the situations of their suppliers at any time. The above process produces a cycle between dependence and positive intervention. Thus, companies like to gain full control over suppliers. When suppliers accept auditing, and problems are pointed out during the process, suppliers understand that their economic profits will be affected. Therefore, suppliers will be strongly encouraged to maintain high involvement in the process to satisfy auditing requirements, which will improve the development of the lean practice environment, ensure that collaboration will be better, and have a positive effect on the enhancement of resilience.
Third, dependence and positive intervention will induce stakeholder pressure. The abovementioned three companies have great business and social reputations in terms of environmental sustainability improvement. Therefore, cooperative suppliers with high dependence are usually deemed high-level firms in terms of environmental sustainability, and it is easy for them to raise their image within society, government, or among other competitive and cooperative firms. However, this also poses a threat. According to stakeholder theory and the definitions stated above, it can be seen that stakeholders in the promotion process of low-carbon housing include the government, society, cooperative and competitive firms (Yang et al., 2021), and these stakeholders will produce heavy pressure. Therefore, the threat will continue to act as a type of “stakeholder pressure”. Normally, these three companies release their auditing reports every year and list their highly cooperative suppliers in terms of environmental sustainability. If the level of supplier involvement among these three companies reduces and affects the lean practice environment and can be disclosed through auditing reports, then suppliers will encounter heavy stakeholder pressure, and stakeholders will question whether lower involvement can raise pollution emissions and force these three companies to reduce or terminate their cooperation with suppliers of lower involvement levels. To avoid the above negative effects, suppliers are forced to cooperate more with these companies in the formulation of lean practice environments, which can be deemed highly involved. Additionally, such involvement has a positive effect on lean practice improvement and increasing resilience. In addition, increasing stakeholder pressure also drives suppliers to cooperate more with the requirements of companies. Their dependence increases significantly, and they may even be willing to accept auditing interventions and cooperate with auditing results to bring about change. Therefore, stakeholder pressure is a driving factor and can be deemed a strategic capability. When stakeholder pressure is produced, it will combine dependence and positive intervention and further formulate a cycle; it will become a stronger control system and continue to produce a stronger control force to improve supplier involvement in the development of the lean practice environment.
Based on the above, the combination of win‒win lean practices and auditing mechanisms will produce three strategic capabilities, including dependence, positive intervention of auditing mechanisms, and stakeholder pressure. A cycle between the three capabilities will be formulated and further become a stronger control system, which will produce a control force to promote supplier involvement in the development of the lean practices environment. According to the relationship between lean practices and resilience, the combination can maintain the efficiency of lean practices and enhance resilience, further realizing sustainable supplier management. The above concepts are shown in Figure 1.
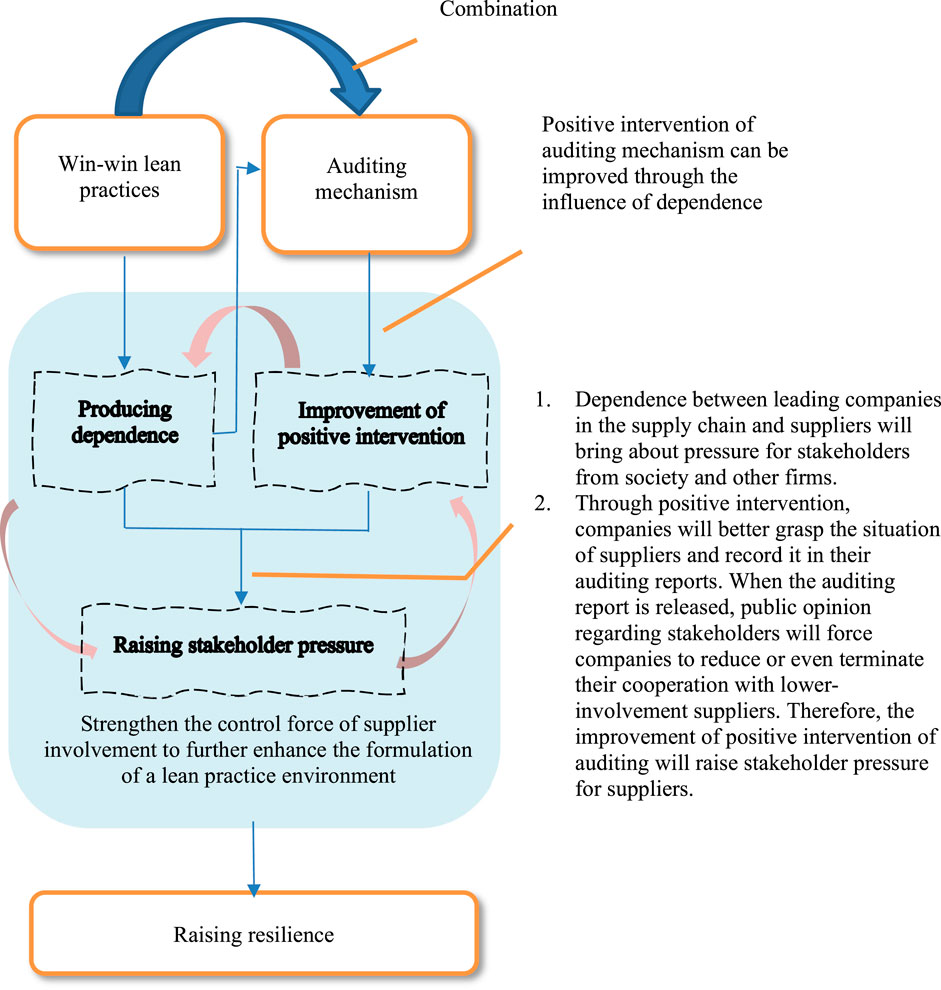
FIGURE 1. Framework and practice of the combination of win‒win lean practices and auditing mechanisms.
Based on the above discussion, we can understand that the combination of win‒win lean practices and auditing intervention can maintain supplier involvement in the development of the lean practices environment because the combination can produce three strategic resources and capabilities, including dependence, positive intervention, and stakeholder pressure. These capabilities can form a cycle, becoming a stronger control system and producing control force to improve and maintain supplier involvement in the development of the lean practices environment. According to the analysis of the three companies, it certainly enhances resilience to control and prevent the opportunistic behaviours of suppliers and further realizes sustainable supplier management. However, does the conclusion apply to different firms? Further verification is needed. Therefore, based on the above, we develop related hypotheses and establish a theoretical framework from 3.2 to 3.4 for further testing.
Relationships among dependence on win‒win lean practices, the positive intervention of auditing mechanisms, increasing stakeholder pressure, and resilience.
First, we discuss dependence. Win‒win strategies certainly have a positive effect on promoting the dependence of supplier partners (Wu et al., 2012). However, when dependence increases, does it have a positive effect on the enhancement of resilience? Although existing studies lack a clear discussion of the relationship between these two factors, a few studies, such as Scholten and Schilder (2015), Abi Ghanem et al. (2016), and Pettit et al. (2019), have addressed it. Specifically, when supplier dependence increases significantly, it reduces the barriers between manufacturers and suppliers. Manufacturers can interact deeply with suppliers and be a dominant force in requiring supplier cooperation, and resistance from suppliers is thus usually reduced. As a result, supplier involvement is improved, and the development of a lean practice environment will benefit. Due to the relationship between greater lean practices and resilience, resilience can increase and produce efficiency to help manufacturers prevent the opportunistic behaviours of suppliers. Based on the above aspects, we establish the following hypothesis:
H1a. Increasing dependence through win‒win lean practices has a positive effect on raising resilience.Second, dependence will promote the positive intervention of an auditing mechanism and further ensure supplier cooperation and involvement. Such mechanisms certainly have a positive effect on the improvement of lean practices and raising resilience to prevent opportunistic behaviour (Azadegan and Jayaram, 2018). Specifically, auditing mechanisms can be used to measure and assess supplier behaviour. Through auditing reports, a company can evaluate the risk inherent in supplier cooperation in lean practices involvement and adopt remedies to address it (Dabhilkar et al., 2016; Shishodia et al., 2019). However, auditing mechanisms are similar to interventions, and many suppliers usually resist them. When dependence is increased through win‒win lean practices, it is possible to increase the positive impact of auditing. For example, Jüttner et al. (2003), Sullivan-Taylor and Branicki (2011), and Miller and Engemann (2019) noted that dependence is an important factor in auditing practices. High levels of dependence can promote auditing and have a further positive effect on supplier involvement and the improvement of lean practices. Resilience also allows firms to prevent the opportunistic behaviours of suppliers. Most importantly, when suppliers accept auditing intervention, there appears to be a synergy between dependence and auditing intervention, similar to the effect of dependence in strengthening the relationship between supplier involvement in lean practices and resilience. Based on this, we establish the following hypotheses:
H1b. The positive intervention of auditing mechanisms has a positive effect on resilience for preventing the opportunistic behaviour of suppliers.
H1c. An increase in dependence can increase the positive impact of auditing mechanisms.
H1d. The positive intervention of auditing mechanisms has a mediating effect on the relationship between dependence and resilience.Third, dependence and the positive intervention of auditing mechanisms may induce an increase in stakeholder pressure. In addition, although stakeholder pressure plays a critical role in environmental sustainability, the extant research lacks direct evidence to prove whether the raising of stakeholder pressure has a positive effect on supplier involvement in lean practices environmental development and further raises resilience to sustainability. However, a few works, such as Rafi-Ul-Shan et al. (2018) and Das (2018), have inferred the relationships among raising stakeholder pressure, supplier involvement in lean practices and raising resilience. This means that when stakeholder pressure increases due to related factors, it is possible to raise resilience and further control any opportunistic behaviour by suppliers that would disrupt improvement in environmental sustainability. In addition, whether increasing dependence and positive intervention in auditing mechanisms induce an increase in stakeholder pressure remains to be explored. However, we can still infer that the above situation is possible. For example, Herold (2018) indicated that dependence between companies and cooperative partners involves some activities and influences environmental sustainability. Therefore, stakeholders from communities of shared life can observe whether their activities satisfy environmental requirements (Lee, 2011). At such a time, stakeholders are a source of pressure and encourage all participants to follow the requirements of environmental sustainability. In addition, these stakeholders carry weight in terms of the improvement of environmental sustainability; therefore, they monitor to auditing reports and pressure companies to address related problems, such as lower supplier involvement leading to damage to environmental sustainability (Hyatt and Berente, 2017). With increasing stakeholder pressure, suppliers will be more cooperative and involved. Based on the above aspects, a cycle between these three capabilities is formulated and becomes a stronger control system and further produces a control force to drive supplier involvement in the development of the lean practices environment. Furthermore, this cycle has a positive effect on resilience. Based on this, we establish the following hypotheses:
H1e. Increasing dependence through win‒win lean practices can induce stakeholder pressure.
H1f. The positive intervention of auditing mechanisms can induce stakeholder pressure.
H1g. Increasing stakeholder pressure has a positive effect on raising resilience.
H1h. Stakeholder pressure has a mediating effect on the relationships among dependence, positive intervention, and resilience.
The influence of resilience on the control of raw material purchases and of production activities among suppliers.
When resilience increases significantly, it is possible to prevent the opportunistic behaviours of suppliers and further exert control over raw material purchases and related production activities. In fact, resilience promotes responsible purchases. According to Carvalho et al. (2012) and Azadegan et al. (2013), if any supplier engages in opportunistic behaviour, the entire supply chain could be affected, increasing pollution. Resilience raises awareness of the responsibility for making sustainable purchases and preventing and controlling the emergence of opportunistic behaviour in purchases (Rachid, 2017; Laasch and Gherardi, 2019). In controlling supplier production activities, if resilience leads to prevention, many researchers have also proven that resilience certainly has a positive effect on the control of the production activities of suppliers, on ensuring that these production activities abide by environmental awareness, and on avoiding high levels of pollution in operational processes. For example, Duarte and Machado (2011) and Ji et al. (2020) obtained similar results. Based on the above discussion, we establish the following hypotheses:
H2a. Increasing resilience has a positive effect on control over the raw material purchases of suppliers.
H2b. Increasing resilience has a positive effect on control over production activities, which reduces pollution.
Theoretical framework
On the basis of the above literature review and hypothesis development, this study develops the theoretical framework shown in Figure 2. In line with Figure 2, this study further tests the path relationships among increasing dependence through win‒win lean practices, the positive intervention of auditing, increasing stakeholder pressure, resilience, the control of raw material purchases, and the control of supplier production activities. Through this theoretical framework, we can try to answer our research questions.
Materials and Methods
Questionnaire, operationalization of and variables for the constructs, data collection, and sample profile.
To test our research hypotheses and further explore our theoretical framework, we utilize survey-based empirical data from Chinese manufacturers. As part of a broader research project, a cross-sectional survey instrument was first designed. In line with the theoretical framework described in Figure 2, the questionnaire encompassed six constructs. In line with related studies, we operationalized each construct and its related variables. These variables became the items in the questionnaire, as shown in Table 1.
We collected the relevant empirical data through the questionnaire. Questionnaires were sent to 373 manufacturing companies in China. We received 231 valid responses, for a response rate of 61.93%. To characterize the profile of the companies in the sample, we investigated three characteristics, namely, enterprise size, product type, and the timing implementation of lean practices and auditing mechanisms, to promote the robustness and resilience of supplier management. The characteristics of respondents, derived from the aggregated results, are shown in Table 2.
Methods
Covariance-based structural equation modelling (CB-SEM) is a convenient method for estimating path relationship models with latent variables while including mediation effects (Sadikaj et al., 2021). Xu (2021) indicated that “SEM is a multivariate statistical analysis method. It can not only test some unpredictable abstract ideas but also design parameters for the causal connection model”. SEM is a widely used research approach. According to Hair et al. (2011), if the research goal is to adopt a theory to be base and test, theory confirmation, or comparison of alternative theories, CB-SEM should be a main method. This study will adopt CB-SEM as the main approach to verify our theoretical framework and hypotheses because RBV is an important theory base in this study, which is why we adopt CB-SEM as the main method. In CB-SEM analysis, we used AMOS 23.0 as our analysis tool.
However, to test the theoretical framework and hypotheses with CB-SEM, the validity and reliability of the constructs should be tested first. The main indices used to measure constructs’ validity and reliability are factor loadings, composite reliability (CR), and average variance extracted (AVE). Regarding the factor loading, we will adopt exploratory factor analysis (EFA) to calculate it, and the SPSS 23.0 is the main tool. Regarding the requirements for the indices, the factor loadings should exceed 0.4 (Hu and Bentler, 1999), and the CR and AVE values should exceed 0.7 and 0.5, respectively (Hair et al., 2016). An exception is that if the AVE is lower than 0.5 but higher than 0.36 and the CR is above 0.7, then the results can be accepted (Fornell and Larcker, 1981).
However, to ensure the results of the constructs’ validity, in addition to the AVE results, we should verify the discriminant validity. Discriminant validity is used to measure whether each construct can be distinguished from other constructs. Existing studies usually adopt three approaches to test discriminant validity, including the Fornell-Lacker criterion, Cross Loadings, and heterotrait-monotrait ratio (HTMT). However, Roemer et al. (2021) indicated that HTMT assumes tau-equivalet measurement models, which are unlikely to hold for most empirical studies. In addition, interesting research from Afthanorhan et al. (2021) indicated that HTMT is recommended when researchers use partial least squares structural equation modelling (PLS-SEM) to verify path relationships. If researchers just use CB-SEM, the Fornell-Lacker criterion and Cross Loadings are recommended. Based on the above, because this study uses CB-SEM as the main method to verify the theoretical framework and hypotheses, we adopt the Fornell-Lacker criterion and Cross Loadings to verify discriminant validity. Regarding the requirement of the Fornell-Lacker criterion, the square root of each construct’s AVE should be greater than its correlation with other constructs (Fornell and Larcker, 1981). Regarding the Cross Loadings, the analysis results of each construct should have clear validity.
In addition, we need to test the multicollinearity for dependence, the positive intervention of auditing mechanisms, and stakeholder pressure. These three constructs are identified as critical factors, and the interaction relationships among the three factors may produce a stronger control force to improve supplier involvement in lean practices and further raise resilience. Multicollinearity refers to a situation in which more than two explanatory variables in a multiple regression model are highly linearly related. If the test results are highly linearly related, then the coefficient estimates of the multiple regression may exhibit bias, which will affect the judgement of the model and hypotheses. To measure the multicollinearity of dependence, the positive intervention of auditing mechanisms, and stakeholder pressure, variance inflation factors (VIFs) are adopted. According to Hair et al. (2011), the VIF of each construct should be lower than 5.
Finally, after verifying the constructs’ reliability and validity and testing for multicollinearity, we will verify our theoretical framework and hypotheses. After verification, the model’s goodness of fit should be measured. Three fit indices, including the comparative fit index (CFI), the goodness-of-fit index (GFI), and Tucker‒Lewis’s index (TLI), should be adopted. In addition, we also adopt the chi-square to the degree of freedom (CMIN/DF), root mean square error of approximation (RMSEA), and root mean residual (RMR). In sum, we adopt six indices to measure model fit. Regarding the requirements of CFI, GFI, and TLI, their value should be higher than 0.9 (Waqas et al., 2018). The requirements of the CMIN/DF should be lower than 2 (Browne and Cudeck, 1993); in addition, RMSEA should be lower than 0.08 (Browne and Cudeck, 1993). Finally, as to RMR requirements, according to Hu and Bentler (1999), the model is considered acceptable if the RMR is less than 0.05.
Test results
Before testing our hypotheses, we test the constructs’ reliability and validity. As shown in Table 3, all the factor loadings from EFA exceed 0.4. Therefore, the factor loadings satisfy the requirement. Regarding CR, as shown in Table 3, all the CR values exceed 0.7. Regarding the AVE, the AVE values for all constructs are less than 0.5 and higher than 0.36. According to Fornell and Larcker, because the CRs of all constructs are still higher than 0.7, the test results satisfy the measurement requirements. Next, we test for discriminant validity. The analysis results of the Fornell-Lacker criterion and Cross Loadings are shown in Tables 4 and 5. Regarding the analysis results of the Fornell-Lacker criterion, we find that the square root of each construct’s AVE is certainly greater than its correlation with other constructs; in addition, according to the analysis results of the Cross Loadings, it is a clear discriminant between constructs. Based on the above, discriminant validity was achieved.
Next, we test the multicollinearity for dependence, the positive intervention of auditing mechanisms, and stakeholder pressure, the results of which are shown in Table 6. The VIF values of dependence, positive intervention of auditing mechanisms, and stakeholder pressure are 1.176, 1.374, and 1.266, respectively, all lower than 5, meeting the VIF requirement. Therefore, multicollinearity among dependence, positive intervention of auditing mechanisms, and stakeholder pressure does not exist.
Then, we use CB-SEM analysis to verify the hypotheses. Regarding the results from testing the hypotheses, the relationship between increasing dependence through win‒win lean practices and resilience is supported, β = 0.724, p < 0.01. The relationship between the positive intervention of auditing mechanisms and resilience is supported, with β = 0.918, p < 0.01. In addition, the relationship between increasing dependence through win‒win lean practices and the positive intervention of auditing mechanisms is also supported, and its β = 0.752, p < 0.01. Through the above combined results, H1a, H1b, and H1c are supported. In addition, the relationship between increasing dependence through win‒win lean practices and stakeholder pressure is supported, with β = 0.621, p < 0.01. The relationship between the positive intervention of auditing mechanisms and stakeholder pressure is supported, and its β = 0.949, p < 0.01. Finally, the relationship between stakeholder pressure and resilience is also supported, β = 0.955, p < 0.01. Based on the above, H1e, H1f, and H1 g are supported.
In addition, we need to verify H1d and H1 h because these two hypotheses concern mediating effects. According to Khan et al. (2022), bootstrapped analysis can be applied to verify the mediation test. Specifically, mediation analysis was satisfied by applying 5,000 bootstrap samples. In addition, we set a 95% confidence interval. In this study, H1d verifies the mediating effect of the positive intervention between increasing dependence through win‒win lean practices and resilience. We supposed H1d to be Model 1. H1 h is to verify the mediating effect of stakeholder pressure on increasing dependence through win‒win lean practices, positive intervention, and resilience. Therefore, the relationship between increasing dependence through win‒win lean practices, stakeholder pressure, and resilience was assumed to be Model 2-1, and the relationship between positive intervention, stakeholder pressure, and resilience was assumed to be Model 2-2. The analysis results of the above mediating effects are shown in Table 7. In Model 1, although the direct effect between increasing dependence through win‒win lean practices and resilience was not supported, the indirect effect between increasing dependence through win‒win lean practices, positive intervention, and resilience was supported. Based on the above, H1d is supported. Regarding Model 2-1, we find that the direct effect between increasing dependence through win‒win lean practices and resilience was not supported; however, the indirect effect between increasing dependence through win‒win lean practices, stakeholder pressure, and resilience was supported. Therefore, stakeholder pressure seems to be a mediator. However, when we checked for Model 2-2, direct or indirect effects between positive intervention, stakeholder pressure, and resilience were not supported. Based on the above, H1 h is not supported.
The relationship between resilience and control over raw material purchases is also supported, with β = 0.945 and p < 0.01. In addition, the relationship between resilience and control over production activities is also supported, with β = 0.904 and p < 0.01. Based on the above, H2a and H2b are supported.
Finally, in terms of measuring model fit, the CFI, GFI, TLI, CMIN/DF, RMR, and RMSEA are the main indices used. All model fit results are as follows: CFI is 0.930, GFI is 0.921, TLI is 0.916, CMIN/DF is 1.678, RMR is 0.038, RMSEA is 0.054, and these indices all satisfy the basic requirements.
Discussion
According to the test results, we have answers to our research questions. When win‒win lean practices are established and combined with auditing mechanisms, which capabilities are produced, and how can they build a stronger control system and produce greater control force? We tried to analyse a few successful cases and carefully observe and further verify them through empirical testing. Based on the above aspects, we establish answers to the research question. Actually, the formulation of the control system depends on three critical capabilities—dependence, the positive intervention of auditing mechanisms, and stakeholder pressure. Considering that these three capabilities have a positive effect and formulate a cycle as a control system to enhance resilience, they match the concept of RBV, and these three capabilities are critical factors. Based on the above, we further discuss it below.
First, through win‒win lean practices, a supplier’s economic profits will be significantly raised. However, with the increase in economic profits from leading companies or manufacturers, the supplier’s dependence will increase. To maintain economic profits, suppliers usually raise their involvement intention in terms of lean practices, which produces positive efficiency in the formulation of lean practice environments. Close involvement between leading companies or manufacturers and suppliers will be promoted, and resilience will be improved significantly. Therefore, if win‒win lean practices continue to be improved, then high dependence will maintain close involvement, lean practices will be better, and resilience will be at a level that can be well maintained. Based on the above, H1a was supported.
Second, when implementing auditing mechanisms combining them with win‒win lean practices, dependence improves closer involvement; therefore, dependence will reduce suppliers’ resistance to auditing intervention and even lead them to accept and cooperate with auditing. At this time, auditing will be deemed a positive intervention. Specifically, suppliers are not always willing to accept auditing because they view it as being similar to an intervention. However, as the level of dependence increases through win‒win lean practices, suppliers become more cooperative. Therefore, they accept the auditing process, which is why H1c was supported. Suppliers’ positive attitudes towards auditing will raise their involvement level and will lead them to be willing to cooperate with the auditing results to improve and formulate a better lean practice environment. Such a positive attitude can have a positive effect on supplier involvement in the development of the lean practices environment, and it can raise resilience. Therefore, H1b is supported. In addition, auditing will help leading companies or manufacturers grasp the situation of suppliers more deeply, and suppliers will be aware of the resistance to auditing that may reduce the cooperation level among leading companies or manufacturers and lead to economic profit losses. This is similar to the control force of leading companies or manufacturers being expanded. Based on the above, H1d was supported.
Third, the development of green and sustainable supply chain development has become an important issue today. Partners of leading companies or manufacturers in the global supply chain are also listed and continue to be the focus. These leading companies or manufacturers usually bear heavy social responsibility, especially in terms of environmental sustainability. Their partners are also focused on whether they cooperate with the related environmental policy of leading companies or manufacturers. This means that with the dependence fostered by win‒win lean practices, related stakeholders such as social and regulatory processes from government or other firms will act as a form of pressure. People from society will act to boycott; regulatory processes from the government will give a consequence or industry standard requirement in environment and pollution emissions; other firms may reduce willingness to cooperate. With increasing stakeholder pressure, these suppliers will be forced to raise their involvement level in lean practices environment development and jointly improve environmental sustainability. If not, these stakeholders may force leading companies or manufacturers to reduce or even cancel their cooperative relationships with these suppliers. In addition, auditing reports must be announced every year to disclose the improvement in company circumstances in terms of environmental sustainability. Of course, this disclosure also depends on the supplier’s cooperation scenario. If auditing reports disclose opportunistic behaviour from some suppliers, causing damage, then stakeholders will pressure leading companies or manufacturers to improve. Based on the above aspects, the interaction between dependence and the positive intervention of auditing mechanisms induces stakeholder pressure, which is why H1e and H1f were supported; it also becomes a control system and produces a stronger force to improve suppliers’ involvement in lean practices and produces a positive effect in terms of raising resilience. Based on the above, the relationships between H1e, H1f, and H1g are explained. However, our analysis results did not support H1h, but it reveals important information; that is, the formulation of the control system through three capability formulations should be based on dependence. Win‒win lean practices should be prioritized and combined with the auditing mechanism. In addition, only the combination of dependence and positive intervention can drive stakeholder pressure and form a control system to improve supplier involvement, further enhancing resilience. Alternatively, it is difficult to drive stakeholder pressure through rare positive intervention of auditing mechanisms.
The above aspects can be considered in terms of the RBV. The combination of win‒win lean practices and auditing mechanisms raises dependence, improves the positive intervention of auditing mechanisms, and induces stakeholder pressure. When these three strategic capabilities become a cycle, similar to a control system, they promote the control force to suppliers, drive supplier involvement in the formulation of lean practice environments, and create a greater resilience to control suppliers’ opportunistic behaviour. This allows them to further realize targets of sustainable supplier management, verifying the results of H2a and H2b. Therefore, we can answer our second research question: Does the control force have a positive effect on increasing resilience? According to the test results, the control force absolutely has an effect on increasing resilience. The question is why? Specifically, raising dependence is a critical factor; it creates a greater economic profit for the supplier, but it is similar to trapping. When the dependence level is higher, leading companies or manufacturers will hold greater control force. Combined with an auditing mechanism and inducing stakeholder pressure, this situation will form a perfect trap. If a supplier wants to leave, then it will face serious damage to its economic profits. Therefore, our research results provide important insight. That is, these leading companies or manufacturers play a critical role in improving environmental sustainability. They need to bear social responsibility, expand their influence and raise control force to their partners, including suppliers.
Conclusion
This study used the RBV to explore and explain our research questions. According to observations of a few successful cases and test results, we explain how to build a stronger control system and produce greater control force through a combination of win‒win lean practices and auditing mechanisms. We explain why the control force is working to drive supplier involvement in the formulation of lean practice environments and further raise resilience, leading companies or manufacturers of supply chains to realize the targets of sustainable supplier management.
Regarding the academic implications of this study, although too many current studies have provided different viewpoints and suggestions regarding the issue of resilience, this study uses a different viewpoint based on observations from real cases to explore the research questions in combination with the RBV; therefore, our study generates some interesting academic implications. First, only a few studies have addressed the concept of win‒win lean practices in conference papers. However, the few existing papers on this topic do not explore and discuss how the concept can be applied to sustainable supplier management. In addition, the concept has been applied gradually in the industrial field. However, what is lacking is a deep exploration of how it produces a control force to drive supplier involvement in lean practices and further promote resilience to ensure the realization of sustainable supplier management targets. Therefore, this study expands the literature through research questions and verification results. Second, this study also explains why the implementation of auditing mechanisms in combination with win‒win lean practices can build a control system and produce a control force to drive supplier involvement in lean practices and environmental development, promote resilience to prevent opportunistic behaviour, control supplier behaviour related to raw material purchases and production activities, further reduce pollution emissions throughout the whole supply chain, and achieve the ideal level of sustainable supplier management. Our research results provide new and different theoretical suggestions. In terms of practical implications, the research idea behind this study is to observe real cases; when we prove the importance of win‒win lean practices through empirical testing, there is an important implication: controlling suppliers through deeper dependence is not simply about cooperation or satisfying requirements. If dependence can be deepened through win‒win lean practice improvement, then it will reduce barriers to the improvement of the green supply chain and to sustainable management of suppliers. Deeper dependence can even increase the positive impact caused by implementing relevant supplier management approaches such as auditing mechanisms. Through the interaction between dependence and the positive intervention of auditing mechanisms, stakeholder pressure is induced. When the control system is formulated and produces a control force, resilience must increase and exert a greater influence on suppliers to prevent or even avoid the occurrence of opportunistic behaviour, further fostering green behaviour.
Although our research results provide many valuable suggestions, there are a few limitations. First, how to effectively improve win‒win lean practices to deepen supplier dependence has not been explored. In addition, the research results clarify why the combination of win‒win lean practices and auditing mechanisms is synergistic in forming resilience; however, a method for designing an effective audit process is lacking. Finally, we lack an exploration and measurement of competitive and market performance when sustainable supplier management is realized through resilience enhancement based on the results of our analysis. Based on the above research limitations, future research can address these two limitations in greater depth.
Data availability statement
The original contributions presented in the study are included in the article/Supplementary Materials, further inquiries can be directed to the corresponding author.
Ethics statement
Ethics review and approval/written informed consent was not required as per local legislation and institutional requirements.
Author contributions
P-KC conceived the study and were responsible for the design and development of the data analysis. ZQ was responsible for literature review and data collection. Authors were responsible for data interpretation and wrote the draft of the article.
Funding
This work was supported by the National Natural Science Foundation of China grant numbers 71872131 and Starting Research Fund of Great Bay University under grant YJKY220020.
Conflict of interest
The authors declare that the research was conducted in the absence of any commercial or financial relationships that could be construed as a potential conflict of interest.
Publisher’s note
All claims expressed in this article are solely those of the authors and do not necessarily represent those of their affiliated organizations, or those of the publisher, the editors and the reviewers. Any product that may be evaluated in this article, or claim that may be made by its manufacturer, is not guaranteed or endorsed by the publisher.
References
Abi Ghanem, D., Mander, S., and Gough, C. (2016). I think we need to get a better generator”: Household resilience to disruption to power supply during storm events. Energy Policy 92, 171–180. doi:10.1016/j.enpol.2016.02.003
Abideen, A. Z., and Mohamad, F. B. (2021). Advancements in industrial supply chain through lean implementation-a review. Int. J. Logist. Syst. Manag. 38 (1), 45–64. doi:10.1504/IJLSM.2021.112426
Afthanorhan, A., Ghazali, P. L., and Rashid, N. (2021). Discriminant validity: A comparison of CBSEM and consistent PLS using Fornell & larcker and HTMT approaches. J. Phys. Conf. Ser. 1874, 012085. doi:10.1088/1742-6596/1874/1/012085
Amege, H., and Hanu, C. (2018). Sustainable management of existing suppliers: A perspective of selected firms in Ghana. Res. Logist. Prod. 8. doi:10.21008/j.2083-4950.2018.8.4.2
Apple (2020). The 2020 supplier responsibility report. AvaliableAt: https://www.apple.com/supplier-responsibility/pdf/Apple_SR_2020_Progress_Report.pdf (Accessed July 15, 2021).
Appolloni, A., Sun, H., Jia, F., and Li, X. (2014). Green procurement in the private sector: A state of the art review between 1996 and 2013. J. Clean. Prod. 85, 122–133. doi:10.1016/j.jclepro.2014.08.106
Arkader, R. (2001). The perspective of suppliers on lean supply in a developing country context. Integr. Manuf. Syst. 12 (2), 87–93. doi:10.1108/09576060110384280
Azadegan, A., and Jayaram, J. (2018). “Resiliency in supply chain systems: A triadic framework using family resilience model,” in Supply chain risk management (Singapore: Springer), 269–288.
Azadegan, A., Patel, P. C., Zangoueinezhad, A., and Linderman, K. (2013). The effect of environmental complexity and environmental dynamism on lean practices. J. Operations Manag. 31 (4), 193–212. doi:10.1016/j.jom.2013.03.002
Bag, S., Gupta, S., Kumar, S., and Sivarajah, U. (2020). Role of technological dimensions of green supply chain management practices on firm performance. J. Enterp. Inf. Manag. 34 (1), 1–27. doi:10.1108/JEIM-10-2019-0324
Barney, J. (1991). Firm resources and sustained competitive advantage. J. Manag. 17 (1), 99–120. doi:10.1177/014920639101700108
Bortolotti, T., Romano, P., Martínez-Jurado, P. J., and Moyano-Fuentes, J. (2016). Towards a theory for lean implementation in supply networks. Int. J. Prod. Econ. 175, 182–196. doi:10.1016/j.ijpe.2016.02.020
Brandenburg, M., and Rebs, T. (2015). Sustainable supply chain management: A modeling perspective. Ann. Oper. Res. 229 (1), 213–252. doi:10.1007/s10479-015-1853-1
Brandon‐Jones, E., Squire, B., Autry, C. W., and Petersen, K. J. (2014). A contingent resource‐based perspective of supply chain resilience and robustness. J. Supply Chain Manag. 50 (3), 55–73. doi:10.1111/jscm.12050
Browne, M. W., and Cudeck, R. (1993). “Alternative ways of assessing model fit,” in Testing structural equation models. Editors K. A. Bollen, and J. S. Long (Newbury Park, CA: Sage), 136–162.
Brush, T. H., and Artz, K. W. (1999). Toward a contingent resource‐based theory: The impact of information asymmetry on the value of capabilities in veterinary medicine. Strateg. Manage. J. 20 (3), 223–250. doi:10.1002/(SICI)1097-0266(199903)20:3<223:AID-SMJ14>3.0.CO;2-M
Brusset, X., and Teller, C. (2017). Supply chain capabilities, risks, and resilience. Int. J. Prod. Econ. 184, 59–68. doi:10.1016/j.ijpe.2016.09.008
Carvalho, H., Maleki, M., and Cruz-Machado, V. (2012). The links between supply chain disturbances and resilience strategies. Int. J. Agile Syst. Manag. 5 (3), 203–234. doi:10.1504/IJASM.2012.047653
Chavez, R., Gimenez, C., Fynes, B., Wiengarten, F., and Yu, W. (2013). Internal lean practices and operational performance: The contingency perspective of industry clockspeed. Int. J. Oper. Prod. Manage. 33 (5), 562–588. doi:10.1108/01443571311322724
Chen, P. K., and Ye, Y. (2022). Influence of creating an oligopoly through government intervention to improve partner collaboration intentions in the context of green supply chains. Environ. Sci. Pollut. Res. 29 (5), 6433–6448. doi:10.1007/s11356-021-16064-x
Chuah, P., Wong, W. P., Ramayah, T., and Jantan, M. (2010). Organizational context, supplier management practices and supplier performance: A case study of a multinational company in Malaysia. J. Enterp. Inf. Manag. 23 (6), 724–758. doi:10.1108/17410391011088619
Dabhilkar, M., Birkie, S. E., and Kaulio, M. (2016). Supply-side resilience as practice bundles: A critical incident study. Int. J. Oper. Prod. Manage. 36 (8), 948–970. doi:10.1108/IJOPM-12-2014-0614
Das, K. (2018). Integrating resilience in a supply chain planning model. Int. J. Qual. Reliab. 35, 570–595.
Day, J. M. (2014). Fostering emergent resilience: The complex adaptive supply network of disaster relief. Int. J. Prod. Res. 52 (7), 1970–1988. doi:10.1080/00207543.2013.787496
Duarte, S., and Machado, V. C. (2011). Manufacturing paradigms in supply chain management. Int. J. Manag. Sci. Eng. Manag. 6 (5), 328–342. doi:10.1080/17509653.2011.10671181
Dubey, R., Gunasekaran, A., Childe, S. J., Papadopoulos, T., Blome, C., and Luo, Z. (2017). Antecedents of resilient supply chains: An empirical study. IEEE Trans. Eng. Manage. 66 (1), 8–19. doi:10.1109/TEM.2017.2723042
Eryarsoy, E., Torgalöz, A. Ö., Acar, M. F., and Zaim, S. (2022). A resource-based perspective of the interplay between organizational learning and supply chain resilience. Int. J. Phys. Distrib. Logist. Manag. ahead-of-print. doi:10.1108/IJPDLM-07-2021-0299
Fornell, C., and Larcker, D. F. (1981). Evaluating structural equation models with unobservable variables and measurement error. J. Mark. Res. 18 (1), 39–50. doi:10.1177/002224378101800104
Foroozesh, N., Tavakkoli-Moghaddam, R., and Mousavi, S. M. (2018). Sustainable-supplier selection for manufacturing services: A failure mode and effects analysis model based on interval-valued fuzzy group decision-making. Int. J. Adv. Manuf. Technol. 95 (9), 3609–3629. doi:10.1007/s00170-017-1308-8
Galbreath, J. (2005). Which resources matter the most to firm success? An exploratory study of resource-based theory. Technovation 25 (9), 979–987. doi:10.1016/j.technovation.2004.02.008
Godinho Filho, M., Ganga, G. M. D., and Gunasekaran, A. (2016). Lean manufacturing in Brazilian small and medium enterprises: Implementation and effect on performance. Int. J. Prod. Res. 54 (24), 7523–7545. doi:10.1080/00207543.2016.1201606
González-Benito, J., and González-Benito, Ó. (2006). The role of stakeholder pressure and managerial values in the implementation of environmental logistics practices. Int. J. Prod. Res. 44 (7), 1353–1373. doi:10.1080/00207540500435199
Govindan, K., Jafarian, A., and Nourbakhsh, V. (2015). Bi-objective integrating sustainable order allocation and sustainable supply chain network strategic design with stochastic demand using a novel robust hybrid multi-objective metaheuristic. Comput. Oper. Res. 62, 112–130. doi:10.1016/j.cor.2014.12.014
Grant, R. M. (1991). The resource-based theory of competitive advantage: Implications for strategy formulation. Calif. Manage. Rev. 33 (3), 114–135. doi:10.2307/41166664
Hair, J. F., Hult, G. T. M., Ringle, C., and Sarstedt, M. (2016). A primer on partial least squares structural equation modeling (PLS-SEM). Newbury Park: Sage publications.
Hair, J. F., Ringle, C. M., and Sarstedt, M. (2011). PLS-SEM: Indeed a silver bullet. J. Mark. Theory Pract. 19 (2), 139–152. doi:10.2753/MTP1069-6679190202
Herold, D. M. (2018). Demystifying the link between institutional theory and stakeholder theory in sustainability reporting. Econ. Manag. Sustain. 3 (2), 6–19. doi:10.14254/jems.2018.3-2.1
Hu, L. T., and Bentler, P. M. (1999). Cutoff criteria for fit indexes in covariance structure analysis: Conventional criteria versus new alternatives. Struct. Equ. Model. A Multidiscip. J. 6 (1), 1–55. doi:10.1080/10705519909540118
Hyatt, D. G., and Berente, N. (2017). Substantive or symbolic environmental strategies? Effects of external and internal normative stakeholder pressures. Bus. Strategy Environ. 26 (8), 1212–1234. doi:10.1002/bse.1979
Ji, L., Yuan, C., Feng, T., and Wang, C. (2020). Achieving the environmental profits of green supplier integration: The roles of supply chain resilience and knowledge combination. Sustain. Dev. 28 (4), 978–989. doi:10.1002/sd.2050
Jüttner, U., Peck, H., and Christopher, M. (2003). Supply chain risk management: Outlining an agenda for future research. Int. J. Logist. Res. Appl. 6 (4), 197–210. doi:10.1080/13675560310001627016
Khan, S. A. R., Waqas, M., Honggang, X., Ahmad, N., and Yu, Z. (2022). Adoption of innovative strategies to mitigate supply chain disruption: COVID-19 pandemic. Oper. Manag. Res. 1–19. doi:10.1007/s12063-021-00222-y
Kochan, C. G., and Nowicki, D. R. (2018). Supply chain resilience: A systematic literature review and typological framework. Int. J. Phys. Distrib. Logist. Manag. 48 (8), 842–865. doi:10.1108/IJPDLM-02-2017-0099
Laasch, O., and Gherardi, S. (2019). “Delineating and reconnecting responsible management, learning, and education (rmle): A research agenda through a social practices lens,” in Academy of management annual meeting (Boston: Academy of Management).
Lee, M. D. P. (2011). Configuration of external influences: The combined effects of institutions and stakeholders on corporate social responsibility strategies. J. Bus. Ethics 102 (2), 281–298. doi:10.1007/s10551-011-0814-0
Lo, S. M., and Shiah, Y. A. (2016). Associating the motivation with the practices of firms going green: The moderator role of environmental uncertainty. Supply Chain Manag. 21 (4), 485–498. doi:10.1108/SCM-05-2015-0184
Miller, H. E., and Engemann, K. J. (2019). “Resilience and sustainability in supply chains,” in Revisiting supply chain risk (Cham: Springer), 251–263.
Mirdad, W. K., and Eseonu, C. I. (2015). A conceptual map of the lean nomenclature: Comparing expert classification to the lean literature. Eng. Manag. J. 27 (4), 188–202. doi:10.1080/10429247.2015.1082068
Orji, I. J., and Wei, S. (2015). An innovative integration of fuzzy-logic and systems dynamics in sustainable supplier selection: A case on manufacturing industry. Comput. Ind. Eng. 88, 1–12. doi:10.1016/j.cie.2015.06.019
Pakdeechoho, N., and Sukhotu, V. (2018). Sustainable supply chain collaboration: Incentives in emerging economies. J. Manuf. Technol. Manag. 29 (2), 273–294. doi:10.1108/JMTM-05-2017-0081
Paranikas, P., Whiteford, G. P., Tevelson, B., and Belz, D. (2015). How to negotiate with powerful suppliers. Harv. Bus. Rev. 93 (7), 90–96.
Pettit, T. J., Croxton, K. L., and Fiksel, J. (2019). The evolution of resilience in supply chain management: A retrospective on ensuring supply chain resilience. J. Bus. Logist. 40 (1), 56–65. doi:10.1111/jbl.12202
Ponomarov, S. Y., and Holcomb, M. C. (2009). Understanding the concept of supply chain resilience. Int. J. Logist. Manag. 20 (1), 124–143. doi:10.1108/09574090910954873
Rachid, B. (2017). “Supply chain improvement in larg (lean, agile, resilient, green) context: A risk management approach,” in 2017 6th IEEE International Conference on Advanced Logistics and Transport (ICALT), Bali, Indonesia, 24-27 July 2017 (IEEE), 212–220.
Rafi-Ul-Shan, P. M., Grant, D. B., Perry, P., and Ahmed, S. (2018). Relationship between sustainability and risk management in fashion supply chains. Int. J. Retail Distrib. Manag. 46 (5), 466–486. doi:10.1108/IJRDM-04-2017-0092
Rashidi, K., and Saen, R. F. (2018). Incorporating dynamic concept into gradual efficiency: Improving suppliers in sustainable supplier development. J. Clean. Prod. 202, 226–243. doi:10.1016/j.jclepro.2018.08.092
Reuter, C., Foerstl, K. A. I., Hartmann, E. V. I., and Blome, C. (2010). Sustainable global supplier management: The role of dynamic capabilities in achieving competitive advantage. J. Supply Chain Manag. 46 (2), 45–63. doi:10.1111/j.1745-493X.2010.03189.x
Roemer, E., Schuberth, F., and Henseler, J. (2021). HTMT2–an improved criterion for assessing discriminant validity in structural equation modeling. Ind. Manag. Data Syst. 121 (12), 2637–2650. doi:10.1108/IMDS-02-2021-0082
Ruiz-Benítez, R., López, C., and Real, J. C. (2018). The lean and resilient management of the supply chain and its impact on performance. Int. J. Prod. Econ. 203, 190–202. doi:10.1016/j.ijpe.2018.06.009
Sadikaj, G., Wright, A. G., Dunkley, D. M., Zuroff, D. C., and Moskowitz, D. S. (2021). “Multilevel structural equation modeling for intensive longitudinal data: A practical guide for personality researchers,” in The handbook of personality dynamics and processes. Editor J. Rauthmann (San Diego: Elsevier Science Publishing), 855–885.
Samsung Electronics (2020). Sustainability report 2020. AvaliableAt: https://images.samsung.com/is/content/samsung/assets/global/our-values/resource/Samsung_Electronics_Nordic_AB_2020_Sustainability_report_ENG.pdf (Accessed July 15, 2021).
Scholten, K., and Schilder, S. (2015). The role of collaboration in supply chain resilience. Supply Chain Manag. 20 (4), 471–484. doi:10.1108/SCM-11-2014-0386
Shishodia, A., Verma, P., and Dixit, V. (2019). Supplier evaluation for resilient project driven supply chain. Comput. Ind. Eng. 129, 465–478. doi:10.1016/j.cie.2019.02.006
Sullivan-Taylor, B., and Branicki, L. (2011). Creating resilient SMEs: Why one size might not fit all. Int. J. Prod. Res. 49 (18), 5565–5579. doi:10.1080/00207543.2011.563837
Taiwan Semiconductor Manufacturering Company (2020). CSR reports. AvaliableAt: https://esg.tsmc.com/download/file/2020-csr-report/english/pdf/e-all.pdf (Accessed July 15, 2021).
Thomas, S. P., Thomas, R. W., Manrodt, K. B., and Rutner, S. M. (2013). An experimental test of negotiation strategy effects on knowledge sharing intentions in buyer–supplier relationships. J. Supply Chain Manag. 49 (2), 96–113. doi:10.1111/jscm.12004
Trujillo-Gallego, M., Sarache, W., and Sellitto, M. A. (2021). Identification of practices that facilitate manufacturing companies’ environmental collaboration and their influence on sustainable production. Sustain. Prod. Consum. 27, 1372–1391. doi:10.1016/j.spc.2021.03.009
Ugochukwu, P., Engström, J., and Langstrand, J. (2012). Lean in the supply chain: A literature review. Manag. Prod. Eng. Rev. 3, 87–96. doi:10.2478/v10270-012-0037-6
Waqas, M., Dong, Q. L., Ahmad, N., Zhu, Y., and Nadeem, M. (2018). Understanding acceptability towards sustainable transportation behavior, A case study of China. Sustainability 10 (10), 3686. doi:10.3390/su10103686
Wernerfelt, B. (1984). A resource‐based view of the firm. Strateg. Manag. J. 5 (2), 171–180. doi:10.1002/smj.4250050207
Wolf, J. (2014). The relationship between sustainable supply chain management, stakeholder pressure and corporate sustainability performance. J. Bus. Ethics 119 (3), 317–328. doi:10.1007/s10551-012-1603-0
Wu, M. Y., Weng, Y. C., and Huang, I. C. (2012). A study of supply chain partnerships based on the commitment‐trust theory. Asia Pac. J. Mark. Logist. 24 (4), 690–707. doi:10.1108/13555851211259098
Xu, X. (2021). Analysis of influencing factors of teaching effect based on structural equation model. Complexity 2021, 6618445. doi:10.1155/2021/6618445
Yadav, V., Jain, R., Mittal, M. L., Panwar, A., and Lyons, A. (2019). The impact of lean practices on the operational performance of SMEs in India. Ind. Manage. Data Syst. 119 (2), 317–330. doi:10.1108/IMDS-02-2018-0088
Yang, L., Du, P., Liao, H., and Zhang, H. (2021). Stakeholder behavior analysis of low-carbon housing promotion IOP conference series: Earth and environmental science. IOP Conf. Ser. Earth Environ. Sci. 821 (1), 012012. doi:10.1088/1755-1315/821/1/012012
Yu, Y., and Huo, B. (2018). Supply chain quality integration: Relational antecedents and operational consequences. Supply Chain Manag. 23 (3), 188–206. doi:10.1108/SCM-08-2017-0280
Keywords: sustainable supplier management, resilience, win-win lean practices, audits, resource-based view
Citation: Qin Z and Chen P-K (2022) Enhancing the resilience of sustainable supplier management through the combination of win‒win lean practices and auditing mechanisms—An analysis from the resource-based view. Front. Environ. Sci. 10:962008. doi: 10.3389/fenvs.2022.962008
Received: 05 June 2022; Accepted: 09 August 2022;
Published: 31 August 2022.
Edited by:
Larisa Ivascu, Politehnica University of Timișoara, RomaniaReviewed by:
Shankar S. Mantha, Veermata Jijabai Technological Institute, IndiaMaria Gianni, University of Macedonia, Greece
Copyright © 2022 Qin and Chen. This is an open-access article distributed under the terms of the Creative Commons Attribution License (CC BY). The use, distribution or reproduction in other forums is permitted, provided the original author(s) and the copyright owner(s) are credited and that the original publication in this journal is cited, in accordance with accepted academic practice. No use, distribution or reproduction is permitted which does not comply with these terms.
*Correspondence: Ping-Kuo Chen, YTExMDQxMDBAbXMyMy5oaW5ldC5uZXQ=