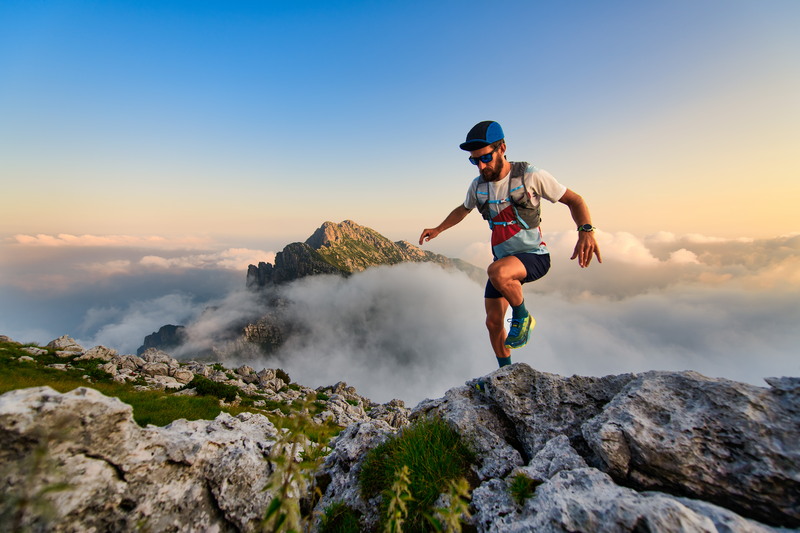
95% of researchers rate our articles as excellent or good
Learn more about the work of our research integrity team to safeguard the quality of each article we publish.
Find out more
ORIGINAL RESEARCH article
Front. Environ. Sci. , 23 September 2022
Sec. Environmental Informatics and Remote Sensing
Volume 10 - 2022 | https://doi.org/10.3389/fenvs.2022.1012057
This article is part of the Research Topic Rock Landslide Risk Assessment, Stability Analysis and Monitoring for The Development of Early Warning Systems and Reinforcement Measures View all 24 articles
Phosphogypsum is a solid waste produced in the production of wet-process phosphoric acid. The main component is calcium sulfate dihydrate, and its constant calcium activity is very low. It is a very difficult waste to handle. The slag produced in the ironmaking processes of the Jiuquan Iron and Steel Company has high activity and can be mixed with phosphogypsum to prepare backfilling cementitious materials for the backfilling of goaf (see Introduction below) to prevent its subsidence and cracking and subsequent subsidence of the land surface above the goaf. In this paper, an orthogonal test of material strength under different ratios and finenesses was carried out, and the optimal formula of phosphogypsum-based cementitious material was obtained. On this basis, SEM (Scanning Electron Microscope) and XRD (X-ray Diffraction) were used to observe the internal structure of phosphogypsum-based cementitious materials. The results show that: when the content of quicklime is 5.5%–6.0%, the content of phosphogypsum is 30%–33%, the content of NaOH is 1.5%–2.0%, the content of Glauber’s salt is 2.5%–3%, the average particle size is 15.88 μm, and grinding aids and an early strengthening agent were added, and in the case of the strengthening agent, the 3-days and 7-days strengths of the filling reached the highest values of 1.58 MPa (mean flexural strength) and 4.1 MPa, respectively. The formation of calcium silicate hydrates gel (C-S-H) and ettringite (AFt) gradually increased with age, and the structure became denser. The ettringite plays the role of interspersed support in the filling body, thereby improving the overall strength. This research provides a theoretical basis and practical reference for the treatment of goaf.
Goaf is any underground void created by human excavation or natural geological movement under the surface of the planet (Du et al., 2017). The existence of a goaf causes the safe production of a mine to encounter great safety problems (Du et al., 2021). Personnel and mechanical equipment may fall into the goaf and be injured or damaged (Sun et al., 2022). At present, the underground goaf has become an important problem restricting the development of mines and the urbanization of the upper part of the goaf (Zhang et al., 2022). With the deep mining of mines, collapse accidents are prone to occur, and buildings cannot be built affected by goafs, which brings inconvenience to people’s life and production (Li et al., 2022). A large number of stopes, chambers, and roadways left in underground mining have not been treated in time, which has brought serious hidden dangers to open-pit mining and posed a serious threat to mine staff and equipment (Du et al., 2020).The latest research shows that the stepped subsidence of the ground caused by a goaf is one of the main reasons for the instability and damage of landslides (Zhou et al., 2022). Therefore, an effective way to reduce the geological risks of any mining area is to carry out backfilling of the goaf and reduce the subsidence of the ground surface (Du et al., 2022).
Solid waste refers to solid and semi-solid waste materials produced by human beings in production, consumption, life, and other activities (Li et al., 2019). It mainly includes solid particles, garbage, slag, sludge, abandoned products, damaged utensils, defective products, animal carcasses, spoiled food, human and animal manure, etc (Huang and Lin, 2010). These solid wastes will cause great damage to the ecological environment. In the guiding opinions on the comprehensive utilization of bulk solid waste in the “14th Five-Year Plan,” it is pointed out that bulk solid waste is the core area of comprehensive utilization of resources due to its large volume and wide range, prominent environmental impact, and broad utilization prospects (Xiao et al., 2019). Promoting the comprehensive utilization of bulk solid waste is of great significance to improving resource utilization efficiency and environmental quality, and promoting a comprehensive green transformation of economic and social development (Sun et al., 2020). At present, the cumulative stockpiles of bulk solid waste total about 60 billion tons, and annual new stockpiles are nearly 3 billion tons. Among them, the utilization rates of solid wastes such as red mud, phosphogypsum, and steel slag is still low, occupying a large amount of land resources, and present large environmental safety hazards (Luo et al., 2020). It is necessary to thoroughly implement the Law of the People’s Republic of China on the Prevention and Control of Environmental Pollution by Solid Waste and other laws and regulations, to vigorously promote the reduction, resource utilization and safe disposal of bulk solid wastes at their source, strengthen the whole-chain governance, focus on solving prominent contradictions and problems, and promote the comprehensive utilization of resources to allow industry to realize new development (Szajerski et al., 2019).
Phosphogypsum is one such type of solid waste (Mohammed et al., 2018). Phosphogypsum mainly comprises two kinds, gray-black and gray-white, and has a particle diameter generally of 5–50 μm and a crystal water content of 20%–25% (Liu et al., 2019; Pinto et al., 2020; Wang et al., 2020). Phosphogypsum is a solid waste produced in the production of wet-process phosphoric acid, and its component is mainly calcium sulfate dihydrate (He et al., 2012; Chen et al., 2016; Cao, 2018; Sun, 2020). The composition of phosphogypsum is relatively complex. In addition to calcium sulfate, there are incompletely decomposed phosphate rock, residual phosphoric acid, fluoride, acid-insoluble matter, organic matter, etc. Among them, the existence of fluorine and organic matter has the greatest impact on the resource utilization of phosphogypsum (He et al., 2014; Cui et al., 2021). The random discharge and accumulation of phosphogypsum has seriously damaged the ecological environment, not only polluting groundwater resources, but also causing a waste of land resources (Luo et al., 2013; Bouchhima et al., 2017).
Slag is a by-product of the blast furnace ironmaking process. In the ironmaking process, iron oxide is reduced to metallic iron at high temperatures, and impurities such as silica and alumina in iron ore react with lime to form a melt with silicate and aluminosilicate as the main components. After quenching, it becomes a loose and porous granular material, which is known as blast furnace slag, often referred to as simply slag (Hua et al., 2016). Slag is also a type of solid waste (Rosales et al., 2020). The phosphogypsum-based cementitious material prepared based on JISCO slag fully utilizes phosphogypsum and JISCO slag.
The phosphogypsum-based cementitious material prepared based on JISCO slag not only makes full use of phosphogypsum, but also saves the filling cost of Jinchuan mine filling-method mining. The filling method is to backfill these wastes into the goaf, which not only treats the waste, which reduces pollution, but also reduces the probability of surface subsidence caused by mining (Min et al., 2019; Yin et al., 2019; Zhou et al., 2020). Since mining is going on all the time, it cannot be suspended due to the need for backfilling, so the backfilled body needs to have a certain strength at an early stage to avoid taking up time. Using cement as aggregate will cost the purchase of cement and transportation, while the JISCO slag and phosphogypsum used in this paper are sourced near the Jinchuan Mine, so there are basically no transportation costs and a low total cost. It not only saves money, but also saves the cost of slag treatment and reduces the pollution to the environment. In this paper, an orthogonal test of material strength under different ratios and finenesses was carried out. According to its 3ays and 7 days early strength, the optimal formulation of phosphogypsum-based filling cementitious material was found. The hydration process of gypsum-based cementitious materials was analyzed.
Figure 1 is a schematic diagram of goaf filling.
The research results show that for the development of new cementitious materials based on slag micropowder, the strength of the cemented backfill is not only related to the properties of the backfill aggregate, mortar ratio, and slurry concentration, but also to the quality, activity, micropowder fineness, gradation, and excitation of the slag. Formulations are closely related. Therefore, tests are carried out on the strength of cemented fillings with different finenesses of cementitious materials.
In the laboratory, an ND6-4L small ball mill was used to grind the original slag micropowder of Jiugang Company for 30 min, 60 min, and 90 min, respectively, and three kinds of slag micropowder with different finenesses were obtained. After grinding for 30 , 60 , and 90 min, the average particle size was 20.00 microns, 15.88 microns, and 12.26 microns, respectively, which were 17.5%, 38.6%, and 52.8% lower than the original slag powder particle size of 24.31 microns, respectively. The content of slag with a particle size larger than 45 microns was 10.2%, 8.0%, and 3.9%, respectively.
The original slag powder, the medium-fine slag powder (ground for 60 min), and the ultra-fine slag powder (ground for 90 min) of Jiuzhou Iron and Steel Co., Ltd., Were selected to carry out the strength test of the cemented filling body of phosphogypsum-based filling cementitious materials. The test aggregate is the coarse aggregate of crushed waste rock in Longshou Mine, the test mortar ratio is 1:4, and the slurry mass concentration is 80%.
It can be seen from Table 1 that the maximum strength of the cemented backfill at 3 days is 0.70 MPa, which is 63% of the cement cementitious material. The maximum strength of the cemented backfill at 7 days is 3.80 MPa, which is 1.9 times that of the cement cementitious material. It can be seen from Table 2 that the main factor affecting the strength of the cemented backfill at 3 and 7 days is quicklime. The quicklime, NaOH, and Glauber’s salt in the optimal formula for 3 and 7 days are the same, 5.5%, 2.0%, and 3.0% respectively, but the phosphogypsum is different, being 30% for 3 days and 33% for 7 days.
It can be seen from Table 1 that the maximum strength of the cemented backfill at 3 days is 1.09 MPa, which is equivalent to 87% of the cement strength, and which is 56% higher than the original slag powder strength. At 7 days, the maximum strength of the cemented backfill is 5.84 MPa, which is equivalent to 2.5 times the strength of cement, and is 54% higher than the strength of the original slag powder.
It can be seen from Table 2 that the strength activator of the medium-fine phosphogypsum-based cementitious material changed from the quicklime of the original phosphogypsum-based cementitious material to phosphogypsum at 3 days, and the quicklime in the optimal formula changed from the original 5.5%–6.5%, phosphogypsum changed from 30% to 36%, NaOH changed from 2.0% to 2.5%, and thenardite changed from 3.0% to 2.5%. At 7 days, the strength activator of the medium-fine phosphogypsum-based cementitious material changed from the quicklime of the original phosphogypsum-based cementitious material to NaOH, and the quicklime phosphogypsum in the optimal formula changed from the original 33%–30%, while the others remained unchanged.
It can be seen from Table 1 that the maximum strength of the cemented backfill at 3 days is 1.26 MPa, which is equivalent to 89% of the cement strength, 80% higher than the original slag powder strength, and 15% higher than the medium and fine slag powder strength. At 7 days, the maximum strength of the cemented backfill is 6.65 MPa, which is 2.1 times that of cement, 58% higher than that of undisturbed slag powder, and 2% higher than that of medium and fine slag powder.
It can be seen from Table 2 that the strength activator of the ultra-fine phosphogypsum-based cementitious material changed from the phosphogypsum of the medium-fine phosphogypsum-based cementitious material to NaOH at 3 days, and the optimal formula was from the quicklime of the medium-fineness, which changed from 6.5% to 5.5%, and thenardite 2.5% became 3.0%. At 7 days, the strength activator of ultra-fine phosphogypsum-based cementitious material is the same as that of medium-fine phosphogypsum-based cementitious material. The optimal formula changes from 30% of phosphogypsum in medium-fineness to 33%, 2.0% of NaOH changes to 1.5%, and 3.0% of Glauber’s salt changes to 2.5%.
Comprehensive analysis was carried out on the 3-days and 7-days data obtained from the above three different fineness phosphogypsum-based cementitious materials cemented backfill strength tests. From this the following conclusions are drawn:
(1) It can be seen from Figure 2 that the strength of the cemented filling body of phosphogypsum-based cementitious material decreases linearly with the increase of the average particle size of the powder at 3 days.
(2) It can be seen that the average particle size of the filling body is 12.26 μm when the strength is the highest, that is, the ultra-fine slag powder. However, when the average particle size is 15.88 μm, that is, the medium-fine slag powder, the strength of the backfill at 3 days is only 13.5% lower than that of the ultra-fine slag powder. Therefore, increasing the grinding time of the slag powder will not only increase the cost, but also have little effect on the increase of strength. Therefore, the average particle size of the slag powder is 15.88 μm, that is, the medium and fine slag powder, is best. Therefore, the average particle size of slag micropowder is less than 16 μm, and the content of slag micropowder +45 μm is less than 8%, corresponding to a 3-days average strength of 0.81 MPa and 7-days average strength of 4.67 MPa.
FIGURE 2. The relationship between the strength of the filling body and the average particle size of the powder.
It can be seen from the above test that the strength at 3 days still cannot meet the requirements of Jinchuan Mine for cementitious materials, and adding appropriate additives will be a good choice. To this end, orthogonal experiments will be carried out for different admixtures, and appropriate admixtures will be selected to improve the strength of phosphogypsum-based cementitious materials.
A grinding aid is used to make the grinding fineness finer when the ball mill is grinding, thereby improving the mechanical properties of the cementitious material. In order to choose the grinding aid more suitable for JISCO slag, three grinding aids, SA115, SA117, and SA119, provided by Beijing Yuanxin Tongxin Technology Co., Ltd., were used to carry out the orthogonal test of the strength of phosphogypsum-based cementitious materials.
According to the filling system and process parameters of Longshou Mine in the Jinchuan Mine, the aggregate is a coarse aggregate of waste rock, a cement-sand ratio of 1:4, and a slurry concentration of 80%. According to the strength test of cemented backfill with different fineness cementitious materials, the fineness of phosphogypsum cementitious material is determined as medium fineness, with 6% quicklime, 34% phosphogypsum, and 60% slag powder. Since mirabilite excitation and NaOH alkali excitation may have compound effects with grinding aids, orthogonal tests of four factors and three levels of grinding aid product, grinding aid addition, and thenardite and NaOH were carried out.
It can be seen from Table 3 that the maximum compressive strength at 3 days is 1.21 MPa, while the maximum strength of the medium-fine phosphogypsum-based cementitious material is 1.26 MPa. It can be seen that only adding grinding aids has little effect on the strength of the filling. Among them, the SA117 grinding aid had the best effect on strength at 3 days.
Since the addition of grinding aids has little effect on phosphogypsum-based cementitious materials, an experiment on the effects of early strength agents on phosphogypsum-based cementitious materials was carried out. The aggregate, mortar ratio, and slurry concentration tested were the same as in the above test. According to the test results of the above 3 days, SA117 was used as the grinding aid, and the dosage was 0.05%. The compound early-strength activator was designed by a three-level orthogonal design of Glauber’s salt, NaOH, and NaCl.
It can be seen from Table 4 that the maximum strength of the filling body is 1.82 MPa at 3 days, and the maximum strength of the filling body is 5.59 MPa at 7 days. The composite early strength agent can significantly improve the strength of the filling body. The average strength of the filling body was 1.58 MPa at 3 days, and the average strength of the filling body at 7 days was 4.1 MPa.
The strength formation process of the new early-strength cementitious material is the hydration process of the new cementitious material, which is a very complex physical and chemical change process. In recent years, a lot of research has been done on the hydration mechanism of slag cementitious materials. It is generally believed that water-quenched slag is a potentially active vitreous structure. This vitreous body contains a high crystallinity energy, but the hydration speed in pure water is very high. Add water slowly, because the water-quenched slag will form a dense and indeterminate acidic film on the particle surface after contact with water. The main purpose of the hydration of water-quenched slag is to destroy the acidity of the glassy surface of the water-quenched slag under the excitation of the activator, causing the protective film to disperse, dissolve, and hydrate the water-quenched slag glass body. This is the reason why the water-quenched slag has no activity at normal temperature of pure water, but can have higher gelling performance under the excitation of alkaline solution, so it is necessary to add an activator for excitation, which is indispensable.
It can be seen from the above experiments that the optimal formula for preparing phosphogypsum-based cementitious materials based on JISCO slag is: quicklime 5.5%–6.0%, phosphogypsum 30%–33%, NaOH 1.5%–2.0%, and Glauber’s salt 2.5%–3%. Water-quenched slag, also known as slag or iron slag, is the solid waste discharged during the ironmaking process, and its main chemical composition is CaO accounts for 37.78%, SiO2 accounts for 37.55%, Al2O3 accounts for 11.06%, and MgO accounts for 7.65%. Jiugang slag is the main component of our phosphogypsum-based filling cementitious material, and also the main material of the hydration reaction.
Phosphogypsum is an industrial by-product of the wet process production of phosphoric acid in phosphorus chemical enterprises. The main component of phosphogypsum is calcium sulfate dihydrate (CaSO4·2H2O). Phosphogypsum also contains many other impurities. The chemical composition of phosphogypsum discharged from Jinchang Wengfu Chemical Plant is: 49% CaSO4, 29% CaO, 2% MgO, and 2% P2O5. Phosphogypsum participates in the hydration reaction of the new cementitious material and acts as an activator.
The main component of quicklime is calcium oxide (CaO). Quicklime participates in the hydration reaction of the new cementitious material and acts as an activator. Glauber’s salt, also known as sodium sulfate, mirabilite, horse’s tooth salt, sodium nitrate, or pot salt, has the chemical composition of sodium sulfate decahydrate (Na2SO4·10H2O). Glauber’s salt participates in the hydration reaction of the new cementitious material and acts as an early-strength agent. NaOH, sodium hydroxide, commonly known as caustic soda, is easily soluble in water and forms an alkaline solution. NaOH participates in the hydration reaction of the new gelling material and acts as an early-strength agent.
First of all, the alkaline solution formed by calcium oxide (CaO) in the slurry when it meets water creates favorable conditions for the dispersion and dissolution of the water-quenched slag glassy body. Calcium oxide (CaO) reacts with water to form calcium hydroxide Ca(OH)2, which produces a large amount of Ca2+ ions and OH− ions in the slurry. The reaction method is as follows:
The Ca2+ ions and OH− ions in the slurry enter the protective film on the surface of the water-quenched slag, and the surface of the slag will form a layer of alkaline film solution containing Ca2+ ions and OH− ions. The concentration of OH− ions in the slurry is very large, and it is easier than water molecules to enter the internal cavities of the slag glassy network structure, thereby promoting the dispersion, dissolution, and hydration of the water-quenched slag. The hydration process of the water-quenched slag is firstly the pozzolanic reaction of active SiO2, Al2O3, and Ca(OH)2 in the water-quenched slag, resulting in the formation of calcium silicate hydrates gel (C-S-H) and calcium aluminate hydrates gel (C-A-H), respectively, which reacts as follows:
With the continuous supply of water in the slurry, the pozzolanic reaction continues until the slag is fully hydrated.
Since the filling material contains a large amount of phosphogypsum (CaSO4·2H2O), the phosphogypsum can act as a sulfate activator, and calcium sulfate reacts with the formed calcium aluminate hydrates gel (C-A-H) to generate calcium sulfoaluminate hydrates (3CaO·Al2O3·3CaSO4·32H2O), namely ettringite (AFt, or alumina, ferric oxide, tri-sulfate), and has the following chemical reaction formula:
Due to the formation of ettringite, the calcium aluminate hydrate, the main hydration product of slag hydration, is consumed, the moisture in the slurry is absorbed, and the hydration and hardening process of the slag is accelerated. In conclusion, the main products of the hydration reaction are calcium silicate hydrates gel (C-S-H) and ettringite (AFt).
During the hydration process in the early alkaline environment, the active silicon dioxide (SiO2) and aluminum oxide (Al2O3) in the water-quenched slag were continuously dissolved from the glassy body and participated in the hydration reaction, resulting in the formation of calcium silicate hydrates condensate gel (C-S-H) and calcium aluminate hydrates gel (C-A-H). These reactions, as well as the reaction between calcium oxide and water, absorbed a large amount of free water, and the resulting gel components, the micropowder, and aggregate bonded together, which provided the early strength, but the whole system was weak during this period. There are also a large number of voids, and the large number of voids and the fragile substances on the surface reduce the strength of the filling body, so the strength is not high. With the gradual increase of reaction products and the action of sulfates such as phosphogypsum, as the calcium aluminate hydrates gel (C-A-H) continuously reacts with CaSO4·2H2O to form hydraulic ettringite (CaO·Al2O3·3CaSO4·32H2O, AFt), the hydration products gradually increase, the quantity of free water gradually decreases, the ettringite and calcium silicate hydrates gel are intertwined to fill the voids, and the slurry hardens, the structure of the filling body is gradually more dense, and the strength of the filling body increases. In later stages, with the passage of time, the strength will increase steadily and slowly, and the structure will become denser and denser, which will further improve the compactness and mechanical strength of the filling body, so that it can reach a higher strength and form a filling with higher strength and a hardened body.
Because the solubility of the alkali Ca(OH)2 is small, the OH− concentration in the solution is low, so the hydration rate of the slag is very slow. After adding NaOH, the concentration of OH− in the solution is greatly increased, which not only accelerates the dissolution of slag and the depolymerization of ion groups, but also accelerates the hydration of slag, so a large amount of ettringite (AFt) and calcium aluminate hydrates gel (C-A-H) improves the early strength of the new gelling material and shortens the setting time. Because the phosphogypsum (CaSO4·2H2O) in the filling material dissolves slowly in water, it affects the hydration of the CaSO4 and C-A-H gel in the early stage of hydration, and the formation of ettringite is minor at first, which makes the early strength of the filling body low. After adding Glauber’s salt (Na2SO4·10H2O), the Glauber’s salt will quickly dissolve in water and react with calcium hydroxide as follows:
The addition of Glauber’s salt increases the concentration of CaSO4 and OH− in the slurry, which provides conditions for the formation of ettringite, accelerates the hydration of slag, and increases the quantity of ettringite in the early stages. Therefore, with the new type of cementitious material, the early strength is improved and the setting time is shortened.
(1) Technical parameters of the instrument. The scanning electron microscope used was a scanning electron microscope produced by Beijing Zhongke Instrument Technology Development Co., Ltd., model KYKY-2800B; the resolution is 4.5 nm (tungsten wire cathode); the magnification is 15×-250000×; the electron gun is a forked tungsten wire Cathode; accelerating voltage range 0–30 kV; lens system is a three-stage electromagnetic lens. The purpose is to observe the microstructure and appearance of samples at different ages, and to make semi-quantitative energy spectrum analysis of characteristic substances by electron probes.
(2) The working principle of the instrument. The focused electron beam (5 nm) strikes the surface of the sample, and the surface of the sample is scanned point by point under the action of the deflection coil to excite different secondary signals. The detector collects these signals and converts them into optical signals, and then passes them through the amplifier. The processing is enlarged to a picture tube to form a three-dimensional dynamic image.
(3) Preparation of test pieces. In order to prevent unnecessary interference to the SEM image caused by the addition of aggregates, a pure slurry without aggregates was selected in this test to analyze the test blocks. We prepared a certain concentration of slurry, poured the slurry into a 7.07 × 7.07× 7.07 cm triple test mold, and put it into a constant temperature and humidity curing box (20 ± 1°C, humidity not lower than 90%) for curing. With a hammer, we knocked open the test block of the filling that has been cured to the specified age, retained a small piece from the middle, and immerse it in anhydrous ethanol to stop the hydration reaction, then took it out for surface carbon spray treatment, and then sent it to professionals for SEM test analysis.
First, the new type of cementitious material is made into a pure slurry with a concentration of 78%, then poured into the test block mold, and put into a curing box with constant temperature and humidity for curing. SEM observation. Figure 3 shows the SEM pictures of the pure pulp test block after curing for 3, 7, and 28 days, respectively.
FIGURE 3. SEM image of new cementitious material. (A) SEM image of hydration 3d pure slurry test block. (B) SEM image of hydration 7d pure slurry test block. (C) SEM image of hydration 28d pure slurry test block.
In the SEM image of the new cementitious material, the crystals of calcium sulfate dihydrate (CaSO4·2H2O) are thin and short columns with uniform crystal size, and the ettringite crystals are needle-shaped. It can be seen from Figure 3 that there are unreacted slag particles, dihydrate phosphogypsum crystals, and ettringite, C-S-H gel generated by the hydration reaction in the filling body, and C-S-H gel covers the slag particles, dihydrate phosphogypsum crystals, and the surface of the ettringite, the filling body takes the ettringite crystals and wollenite as a skeleton to form a strong structure, and the strength of the filling body mainly comes from this formed structure.
After 3 days of hydration, the filling of the cementitious material has produced a large amount of hydration products, and some acicular (needle-like) substances have grown radially, so that the filling cementitious material has a relatively good early strength. However, its shape is still relatively coarse, the amount of ettringite generated is relatively small, and it is not separated from other generated substances and original substances, that is, the development of ettringite is not very good at this time, and the crystal size is small, which offers less support. At the same time, a small amount of amorphous C-S-H gel can be seen on the surface of the slag.
After 7 days of hydration, the hydration has been very deep, resulting in a large quantity of dense amorphous C-S-H gel; the number and size of acicular ettringite crystals has further increased, and cross-filled in larger pores to form a relatively tight network At the same time, it can be seen that the needle-like crystals of ettringite are relatively short, that is, the formation process of ettringite is still in progress; the co-growth and combination of ettringite, the amorphous C-S-H gel that makes up the gelling material, and the hydration products have gradually intertwined, and the structure is much denser than that of at 3 days, so that the strength is also greatly improved compared to that of 3 days.
After 28 days of hydration, the filling cementitious material undergoes a large degree of hydration reaction. At this time, the ettringite is more fully developed, and the crystals are more slender. They grow and overlap each other in the filling sample, and grow alternately with the amorphous C-S-H gel. The final formed C-S-H gel and the slender and coarse ettringite crystals are intertwined and have filled in the pores of the filling body, intertwined into a dense internal structure, and no obvious gap can be seen. The compressive strength of the filling body test block at this time is already high.
(1) Technical parameters of the instrument. The X-ray diffractometer used is a D8 ADVANCE, the maximum output power is ≥ 2.2 kW; the Cu target is used as the radiation source; the scanning angle range is 2θ = −−110–168°; the maximum positioning speed is ≥ 1,500°/min; the light pipe power is 2.2 kW; Long fine focal spot 0.4 × 12 mm; Maximum tube pressure 60 kV; Maximum tube flow 80 mA.
(2) The working principle of the instrument. Using the X-ray diffraction wave, when it is projected onto the sample, a discontinuous diffraction pattern will be generated due to the relative position of the single atom and its scattering ability. The diffraction pattern of a substance can be characterized by its angular position, symmetry relationship, and Bragg reflection intensity, and the phase and structure of the crystal can be analyzed by using the diffraction data.
(3) Preparation of test pieces. In order to prevent the unnecessary interference of the addition of aggregates to the XRD spectrum analysis process, a pure slurry without aggregates was used in this experiment, and test blocks were made for analysis. The filling cementitious material was made into pure slurry of a certain ratio and concentration, and a test block was made. The test block was cured in a standard curing box. After curing to a specified age, the test block was taken out, and the carbonized layer on the surface of the test block was removed. It was immediately soaked in pure ethanol for 24 h to stop the hydration reaction of the test block. The test block was taken out and dried, and then subjected to XRD diffraction analysis.
According to the optimal ratio of phosphogypsum-based new cementitious materials (5.5%–6.0% quicklime, 30%–33% phosphogypsum, 1.5%–2.0% NaOH, and 2.5%–3% mirabilite), the production concentration is a 78% slurry, poured into a module, and then put into a curing box for curing. After curing to the corresponding age, we stopped the hydration and made samples, and then conducted XRD diffraction analysis.
The XRD diffractometer model used in this experiment was a D8 ADVANCE. Test conditions: 2-Theta angle range (scanning range) is 20°–80°; scanning speed is 1°/min; scanning mode is continuous scanning. The XRD patterns of hydration at 3, 7, and 28 days are shown in Figure 4.
(1) It can be seen from the XRD analysis diagram of hydration 3 days in Figure 4 that the three strong peaks of the XRD pattern are expressed as CaSO4·2H2O, the main component of phosphogypsum, indicating that after the hydration reaction has been carried out for 3 days, the amount of phosphogypsum involved in the hydration reaction was a bit less. From the intensity of the diffraction peaks, it can be seen that CaSO4·2H2O is the main component of the cementitious material, and while ettringite is also formed after the hydration reaction, the intensity of its diffraction peaks is low, and the proportion of components in the filling is relatively small. The formation of ettringite still provides support for the early strength.
(2) It can be seen from the XRD analysis diagram of hydration 7 days in Figure 4 that the intensity of the diffraction peak of ettringite has greatly increased compared with that of 3 days, while the intensity of the corresponding diffraction peak of CaSO4·2H2O has weakened. The progress of the hydration reaction is as has been described above. The ettringite occupies a large amount in the filling body, which greatly improves the strength of the filling body at 7 days.
(3) It can be seen from the XRD analysis diagram of 28 days hydration in Figure 4 that when the hydration reaction is carried out for 28 days, the state of the diffraction peak is basically opposite to that of the diffraction peak at 3 days. At this time, the three strong peaks of the XRD pattern are ettringite, that is, that now ettringite accounts for most of the filling body.
(4) It can be seen from the comparison in Figure 4 that as the hydration time continues to increase, the diffraction peak of phosphogypsum (CaSO4·2H2O) in the filling body is constantly weakening, which indicates that the content of phosphogypsum in the cementitious material is constantly decreasing, which provides a strong proof for the participation of phosphogypsum in the hydration reaction.
(5) After the hsydration reaction for 3 days, Ca6Al2(SO4)3(OH)12·26H2O (ettringite AFt) is formed, and the formation of ettringite is the main reason for the high early strength of the filling cementitious material. From the XRD patterns of 3, 7, and 28 days, it can be seen that the diffraction peak intensity of hydration product ettringite is continuously increasing, and the increasing hydration product ettringite provides a strong support for the later higher strength of the filling cementitious material.
(6) According to the dispersion peak in Figure 4, it can be seen that with the increase of hydration reaction time, the dispersion peak gradually weakens, but it increases at 28 days. It shows that with the increase of hydration reaction time, the hydration process of the slag is accelerating, and the content of slag is decreasing. The enhancement of the 28 days dispersion peak indicates that a large quantity of amorphous C-S-H gel appeared in the hydration product at this time, which led to the appearance of dispersion peaks in the XRD pattern.
(7) The main hydration products of the filling cementitious material are ettringite and amorphous C-S-H gel, which provide the main support for the strength of the cementitious material.
FIGURE 4. XRD patterns of hydration 3, 7, and 28 days. (A) XRD analysis of 3d sample, (B) XRD analysis of 7d sample, (C) XRD analysis of 28d sample
In order to eliminate the serious risks posed by the goaf, the orthogonal test of the backfill strength of three different slag fine powders and two different admixtures for the preparation of phosphogypsum-based cementitious materials from Jiugang slag was carried out. The optimal formulation of the new cementitious material, and then based on this, the hydration reaction mechanism was studied by SEM and XRD. We have concluded as follows:
(1) A new type of backfilling cementitious material prepared from phosphogysum and JISCO slag was developed, and its formula is 5.5%–6.0% quicklime, 30%–33% phosphogypsum, 1.5%–2.0% NaOH and 2.5%–3% mirabilite, and the average particle size is 15.88 um. Compared with the traditional use of cement as filling material, not only the cost is greatly reduced, but also the accumulation and discharge of wastes such as phosphogypsum and slag are solved.
(2) The strength of this new type of cementitious material is 1.58 MPa at 3 days and 4.1 MPa at 7 days, when adding proper amount of grinding aid and early strength agent. It can play a supporting role in the goaf timely, prevent collapse of the goaf, and significantly reduce the risk of geological disasters such as subsidence and landslide in the goaf.
(3) Through the observation and analysis of hydration mechanism of phosphogypsum based filling cementitious materials, it is found that with the increase of age, the amount of hydrated calcium silicate gel (C-S-H) and Ettringite (AFT) is increasing, and the structure is gradually dense. The hydrated calcium silicate gel plays a role of filling adhesion in the filling body, and Ettringite plays a role of interspersed support in the filling body. It provides reference value for the development and deepening of follow-up scientific research.
The original contributions presented in the study are included in the article/Supplementary Material, further inquiries can be directed to the corresponding author.
XY (Associate Professor) and YJ (Postgraduate) designed the research plan, accomplished its processes, and wrote the manuscript. CY (Professor), XH (Associate Professor), YJ (Associate Professor), and LX (Associate Professor) reviewed the manuscript.
Key scientific research project of colleges and universities in Henan Province in 2022: Research on remote monitoring and early warning technology of filling pipeline transportation system in nonferrous metal mines (22A130005). The 61st batch of high-level talents scientific research start-up project of North China University of Water Resources and Electric Power (201803002).
The authors declare that the research was conducted in the absence of any commercial or financial relationships that could be construed as a potential conflict of interest.
All claims expressed in this article are solely those of the authors and do not necessarily represent those of their affiliated organizations, or those of the publisher, the editors and the reviewers. Any product that may be evaluated in this article, or claim that may be made by its manufacturer, is not guaranteed or endorsed by the publisher.
Bouchhima, L., Rouis, M. J., and Choura, M. (2017). A study of compaction pressure influence on properties of phosphogypsum-based bricks. Rev. Romana Mater. Rom. J. Mater. 47 (4), 476–483.
Cao, B. (2018). Study on factors affecting the strength of phosphogypsum-based composite cementitious materials. New Build. Mater. 45 (03), 23–26. doi:10.3969/j.issn.1001-702X
Chen, W., Tang, Y., Tian, J., Li, B., and Fan, J. (2016). Preparation and properties of polyaluminum modified phosphogypsum-based supersulfur slag cementitious materials. J. Wuhan Univ. Technol. 38 (02), 1–6.
Cui, X. W., Di, Y. Q., Wang, C. L., Wang, Y. B., Zhang, S. H., Zhai, Y. X., et al. (2021). Preparation and performance of vanadium tailings-reservoir sedimentphosphogypsum-based foamed concretevol. Math. PROBLEMS Eng., 1–11. doi:10.1155/2021/8468063
Du, Y., Xie, M., Jiang, Y., Li, B., and Chicas, S. (2017). Experimental rock stability assessment using the frozen–thawing test. Rock Mech. Rock Eng. 50, 1049–1053. doi:10.1007/s00603-016-1138-2
Du, Y., Xie, M., and Jia, J. (2020). Stepped settlement: A possible mechanism for translational landslides. Catena 187, 104365. doi:10.1016/j.catena.2019.104365
Du, Y., Xie, M., Jiang, U., Chen, C., Jia, B., Huo, L., et al. (2021). Review on the formation mechanism and early warning of rock collapse. Metal. Mine 535 (01), 106–119. doi:10.5040/9781782259206.ch-016
Du, Y., Li, H., Chicas, S. D., and Huo, L. (2022). Progress and perspectives of geotechnical anchor bolts on slope engineering in China. Front. Environ. Sci. 10, 928064. doi:10.3389/fenvs.2022.928064
He, Y., Hua, S., Yao, X., Zhu, H., and Zhang, L. (2012). Preparation and properties of phosphogypsum-slag-based cementitious materials. Inorg. Salt Ind. 44 (10), 21–23. doi:10.3969/j.issn.1006-4990.2012.10.006
He, H., Dong, F. Q., He, P., and Xu, L. (2014). Effect of glycerol on the preparation of phosphogypsum-based CaSO4·0.5H2O whiskers. J. Mat. Sci. 49, 1957–1963. doi:10.1007/s10853-013-7825-4
Hua, S. D., Wang, K. J., and Yao, X. (2016). Developing high performance phosphogypsum-based cementitious materials for oil-well cementing through a step-by-step optimization method. Cem. Concr. Compos. 72, 299–308. doi:10.1016/j.cemconcomp.2016.05.017
Huang, Y., and Lin, Z. (2010). Effect of sodium hydroxide on the properties of phosphogypsum based cement. J. Wuhan Univ. Technol. Mater. Sci. Ed 25 (2), 342–345. doi:10.1007/s11595-010-3342-7
Li, X., Zhou, S., Zhou, Y., Min, C., Cao, Z., Du, J., et al. (2019). Durability evaluation of phosphogypsum-based cemented backfill through drying-wetting cycles. MINERALS 9, 321. doi:10.3390/min9050321
Li, B., Zhang, G., Wang, G., and Qiao, J. (2022). Damage evolution of frozen-thawed granite based on high-resolution computed tomographic scanning. Front. Earth Sci. (Lausanne). 10, 912356. doi:10.3389/feart.2022.912356
Liu, S. H., Wang, L., and Yu, B. Y. (2019). Effect of modified phosphogypsum on the hydration properties of the phosphogypsum-based supersulfated cement. Constr. Build. Mater. 214, 9–16. doi:10.1016/j.conbuildmat.2019.04.052
Luo, H., Zhu, H. P., Zi, J. M., and Lu, Y. F. (2013). Application research on anti-cracking agent for semi-rigid base. J. Test. Eval. 41, 103905. doi:10.1520/JTE103905
Luo, S., Fu, R., Sun, D., Xie, L., Zhou, Y., and Zhao, Y. (2020). Review on the effect of admixtures on water resistance and strength of phosphogypsum-based composite cementitious materials. Inorg. Salt Ind. 52 (11), 6–11. doi:10.11962/1006-4990.2020-0029
Min, C. D., Li, X. B., He, S. Y., Zhou, S. T., Zhou, S., Yang, S., et al. (2019). Effect of mixing time on the properties of phosphogypsum-based cemented backfill. Constr. Build. Mater. 210, 564–573. doi:10.1016/j.conbuildmat.2019.03.187
Mohammed, F., Biswas, W. K., Yao, H. M., and Tade, M. (2018). Sustainability assessment of symbiotic processes for the reuse of phosphogypsum. J. Clean. Prod. 188, 497–507. doi:10.1016/j.jclepro.2018.03.309
Pinto, S., Angulski da Luz, C., Munhoz, G., and Medeiros-Junior, R. (2020). Durability of phosphogypsum-based supersulfated cement mortar against external attack by sodium and magnesium sulfate. Cem. concerte Res. 136, 106172. doi:10.1016/j.cemconres.2020.106172
Rosales, J., Perez, S. M., Cabrera, M., Gázquezd, M. J., Bolivar, J. P., Brito, J., et al. (2020). Treated phosphogypsum as an alternative set regulator and mineral addition in cement production. J. Clean. Prod. 244, 118752. doi:10.1016/j.jclepro.2019.118752
Sun, T., Hu, T., Wang, G. M., Shui, Z., Ge, K., Dai, Q., et al. (2020). Influence of clinker and SCMs on soluble chemicals and expansion of phosphogypsum-based cementitious materials. J. Test. Eval. 48, 20190127. doi:10.1520/JTE20190127
Sun, M., Liang, H., Zhu, Y., Gao, X., Liu, H., and Zhu, Z. (2022). Deformation and failure mode analysis of the tunnel structure based on the tunnel-related landslides cases. Front. Earth Sci. (Lausanne). 10, 906884. doi:10.3389/feart.2022.906884
Sun, X. (2020). Properties of calcined phosphogypsum-slag-alkaline activator cementitious materials [D]. Zhengzhou, China: Zhengzhou University. doi:10.27466/d.cnki.gzzdu.2020.002056
Szajerski, P., Bogobowicz, A., Bem, H., and Gasiorowski, A. (2019). Quantitative evaluation and leaching behavior of cobalt immobilized in sulfur polymer concrete composites based on lignite fly ash, slag and phosphogypsum. J. Clean. Prod. 222, 90–102. doi:10.1016/j.jclepro.2019.03.010
Wang, Q., Cui, Y., and Xue, J. F. (2020). Study on the improvement of the waterproof and mechanical properties of hemihydrate phosphogypsum-based foam insulation materials. Constr. Build. Mater. 230, 117014. doi:10.1016/j.conbuildmat.2019.117014
Xiao, W., Yao, X., and Zhang, F. Y. (2019). Recycling of oily sludge as a roadbed material utilizing phosphogypsum-based cementitious materials. Adv. Civ. Eng. 2019, 1–10. doi:10.1155/2019/6280715
Yin, T. B., Yang, R. S., Du, J., and Shi, Y. (2019). Effects of acid and phosphate on arsenic solidification in a phosphogypsum-based cement backfill process. RSC Adv. 9, 28095–28101. doi:10.1039/c9ra04624k
Zhang, L., Niu, F., Liu, M., Ju, X., Wang, Z., Wang, J., et al. (2022). Fracture characteristics and anisotropic strength criterion of bedded sandstone. Front. Earth Sci. (Lausanne). 10, 879332. doi:10.3389/feart.2022.879332
Zhou, S. T., Li, X. B., Zhou, Y. N., Min, C. D., and Shi, Y. (2020). Effect of phosphorus on the properties of phosphogypsum-based cemented backfill. J. Hazard. Mater. 399, 122993. doi:10.1016/j.jhazmat.2020.122993
Keywords: goaf, phosphogypsum, solid waste, hydration mechanism, compressive strength
Citation: Yang X, Jia Y, Yang C, He X, Jia Y and Xu L (2022) Research on formulation optimization and hydration mechanism of phosphogypsum-based filling cementitious materials. Front. Environ. Sci. 10:1012057. doi: 10.3389/fenvs.2022.1012057
Received: 05 August 2022; Accepted: 05 September 2022;
Published: 23 September 2022.
Edited by:
Yan Du, University of Science and Technology Beijing, ChinaCopyright © 2022 Yang, Jia, Yang, He, Jia and Xu. This is an open-access article distributed under the terms of the Creative Commons Attribution License (CC BY). The use, distribution or reproduction in other forums is permitted, provided the original author(s) and the copyright owner(s) are credited and that the original publication in this journal is cited, in accordance with accepted academic practice. No use, distribution or reproduction is permitted which does not comply with these terms.
*Correspondence: Chen Yang, eWFuZ2NoZW5AbmN3dS5lZHUuY24=
Disclaimer: All claims expressed in this article are solely those of the authors and do not necessarily represent those of their affiliated organizations, or those of the publisher, the editors and the reviewers. Any product that may be evaluated in this article or claim that may be made by its manufacturer is not guaranteed or endorsed by the publisher.
Research integrity at Frontiers
Learn more about the work of our research integrity team to safeguard the quality of each article we publish.