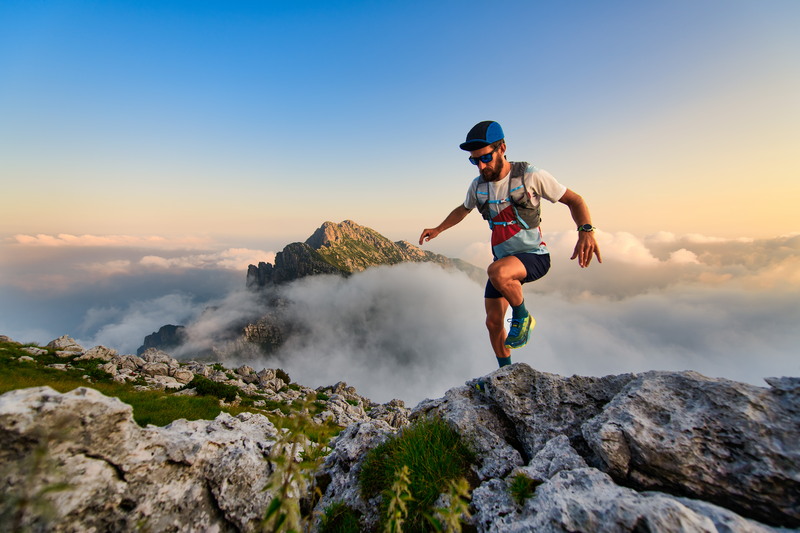
95% of researchers rate our articles as excellent or good
Learn more about the work of our research integrity team to safeguard the quality of each article we publish.
Find out more
REVIEW article
Front. Environ. Sci. , 09 July 2021
Sec. Toxicology, Pollution and the Environment
Volume 9 - 2021 | https://doi.org/10.3389/fenvs.2021.683403
This article is part of the Research Topic Plastics, Microplastics, and Nanoplastics: Management and Mitigation of Water Contamination View all 6 articles
Due to their numerous merits (such as high durability, diverse applicability, ready-availability, low-cost, reusability, and so on), the presumably inevitable use of plastics makes their waste ubiquitously dispersed in our environment, especially in the oceans. The environmental damage posed, especially to the ecosystem, initiated the need for recourse control of these environmentally refractory pollutants. In this review, the various sources, classifications, fate, and control measures of plastic wastes were appraised. Further, of the three primary techniques for resource control, pyrolysis was reviewed in-depth, showing its relevance and superiority over others. Specific case studies showed that liquid and gaseous fuels derived from pyrolyzed plastics are a waste-to-wealth system that requires optimization and intensification. Such an approach would further help rid our planet of the numerous plastic wastes while improving our economy and achieving our energy demand. One approach identified to improve the current pyrolysis technology is catalysis. Further research should devise green methods for organic catalysis, which are environmentally benign.
Globally, plastics are indispensable materials due to their diverse applicability, excellent durability, hydrophobicity, low thermal and electrical conductivity, ready availability, and relatively low production cost, leading to an incessant increase in their demand by humans (Syamsiroa et al., 2014; Khan et al., 2016). Plastics can be used in different applications such as insulations, noise reduction, sealing, and electronic components (Awasthi et al., 2017). About ≈280 million tons of plastics are produced annually, while a proportion of this quantity is recycled, adding to the amount in the subsequent year (Chanashetty and Patil, 2015). Figure 1A shows the quantity and trend of primary waste plastic generated in the last 115 years from various industries, while Figure 1B depicts the production/pollution magnitude by country.
FIGURE 1. (A) Trend of plastic waste production per industry from 1950 to 2015 (Geyer et al., 2018) (B) Magnitude of plastic production/pollution by country (McDonnell, 2015).
Due to the outright abuse of plastics and their improper waste management, vast quantities are indiscriminately discarded on bare lands, oceans, sewers, and drainages. When water flows in the sewers and drainages are blocked in the cities, flooding ensues (Alabi et al., 2019). This condition often endangers human lives and properties. Whereas, oceanic plastic pollution disrupts ocean navigation, affecting marine productivity and causing the sudden death of some vulnerable marine mammals, thereby degrading the ecosystem (Awuchi and Awuchi, 2019).
According to the World Economic Forum 2019, if plastic pollution is not curbed, it will overpopulate and outweigh the Pisces on or before 2050 (Schwab, 2019). In Figure 2, the attribution of plastic waste pollution (based on production magnitude, management flaws, and oceanic pollution) globally is provided.
FIGURE 2. Attribution of plastic waste pollution (in millions of metric tons per year) across the global (d’Ambrières, 2019).
Plastics are majorly categorized into thermoplastics and thermosetting polymers. On exposure to sufficient heat, thermoplastics repeatedly soften and melt. Expectedly, they harden to their status quo when heat is withdrawn (Manickam et al., 2015). This property makes them amenable to recycling. Popular examples of thermoplastics include polyethylene (PE), polypropylene (PP), polystyrene (PS), and polyvinyl chloride (PVC). Figure 3 depicts the classification of plastics according to their demand per sector and amount found in polymers. On the contrary, thermosets or thermosetting plastics melt and take shape once upon exposure to sufficient heat, i.e., they are not amenable for recycling after first production (Askeland, 1996; Dhinakaran et al., 2020).
FIGURE 3. Categorization of plastics based on demand per sector and polymer type (PlasticEurope, 2015).
Bottling companies, eateries, and packaging companies are the primary sources of plastics. The European Union recently moved to enact stricter restrictions on indiscriminate disposal of organic waste, emphasizing the need to recover and recycle solid wastes, especially plastics (Wasilewski, 2013).
The chemical bonds that form during the polymerization of plastics are characteristically strong, resulting in high durability (i.e., high resistance to natural degradation). The non-biodegradability of plastics makes their elimination from the ecosystem very tedious (Chanashetty and Patil, 2015). Therefore, a holistic management approach to curb the plastics pollution menace is imperative.
In this current age, humans cannot do without plastics. Even if further plastic production is banned, the residual problem accrued over the years will linger for many years to come because plastics are already dispersed in every sphere of the environment (Godfrey, 2019). Therefore, instead of a production ban on plastics, a more realistic mitigation approach is to scavenge plastics from waterways, lands, sewers, drainages, oceans, etc., and recycle them appropriately. Alternatively, converting waste plastics into liquid fuel via pyrolysis portends a plausible solution to the environmental challenges associated with the excessive use of plastics (Sharuddin et al., 2017). Since energy demand keeps rising and fossil fuel generation, which is expensive and environmentally unfriendly, remains the primary source, biofuel generation through plastic pyrolysis portends a clean and economical option for energy generation (Al-Salem et al., 2020; Erdogan, 2020; Khan et al., 2016).
Besides providing introductory details about the nature and routes of plastic pollution globally, this review appraises plastic recycling and energy recovery technologies, especially via pyrolysis, to enhance a greener and sustainable environment. Also, the environmental impact of waste pollution, the recovery methods, detailed experimental results, and cost implications are reviewed.
The negative feedback from plastic pollution is mainly environmental and social (Pawar et al., 2016). Plastic debris causes esthetic problems, and it also presents a hazard to maritime activities, including fishing and tourism (Li et al., 2016). Discarded fishing nets causes ghost fishing, resulting in losses to commercial fisheries (Richardson et al., 2018). Also, marine organisms can easily colonize floating plastic debris if it persists at the sea surface long enough, thereby facilitating the transport of non-native species. However, the problems attracting most public and media attention are those resulting in ingestion and entanglement by wildlife. More than 260 marine species have been susceptible to ingestion of plastics or entanglement within plastic debris, which retard their movement needed for feeding and mating, causing various degrees of lacerations, ulcers, even death (Alabi et al., 2019).
On gaseous release, CO2 and CH4 are released when landfilled plastic wastes decompose naturally. Besides, when plastic wastes are subjected to open-burning, the released CO2 (being a greenhouse gas) traps radiant heat, contributing more to the already increasing global warming (Royer et al., 2018). Open burning of plastics and plastic products also releases pollutants hazardous pollutants, such as toxic metals, persistent organic pollutants (POPs, like dioxins, polychlorinated biphenyl, and furans), which induces respiratory disorders carcinogenic diseases if inhaled or ingested (Verma et al., 2016).
Most of the additives present in plastics are potential carcinogens and endocrine disruptors. Ingestion, skin contact, and inhalation are the main routes of exposure of humans to these additives. Table 1 lists the uses and various health effects of toxic compounds in plastic types (Pawar et al., 2016). For instance, dermatitis has been reported from skin contact with some additives present in plastics (Salles and Deschamps, 2010).
TABLE 1. Properties of toxins found in or produced by plastics (Bouchentouf, 2013; Pawar et al., 2016).
Recently, the occurrence of microplastics (MPs) has motivated researchers into a new direction of research (Smith et al., 2018). Plastics in the environment undergo photochemical, thermal, and biological degradation to form MPs (Fok et al., 2020). MPs are plastics of less than 5 mm in size (Thompson et al., 2004). Most MPs form from breaking off of large plastics (Cole et al., 2011). Also, the aging process can result in MPs release into drinking water, having similar polymer composition to the plastic used for water transportation (Mintenig et al., 2019) Because of their relatively small size, large specific surface area, and strong adsorption capacity, MPs pose more ecological risks than their bulkier counterparts by adsorbing persistent organic pollutants (POPs), toxic metals, and pathogens in the environment (Bakir et al., 2014).
MP pollution has become popular in water environmental protection research. Yet, the environmental factors influencing MPs production are not fully understood and inadequately investigated. Pollution sources, human activities, and hydrodynamic factors have been reported to influence MP accumulation and transportation in the ecosystem and the food chains (Horton et al., 2017). One of the hydrodynamic factors that affect MP sizing and dispersion is the river width; the wider the width, the faster larger MPs are transported (Warnock and Ruf, 2019). Other properties are pH, temperature, and salinity.
Horton and coworkers found that 70–80% of MPs waste in marine systems was imported by rivers. MPs from point sources include direct input from sewers, drains, and others (Horton et al., 2017). Those from non-point sources are runoff from different land-use types, having a more complicated impact on the distribution of MPs in river systems MP pollution is spatially different and strongly affected by land-use types (Jang et al., 2020).
In vitro and in vivo studies show that micro- or nano-plastics might overcome tissue barriers, thus interacting with single cells and inducing the activation of cell responses, especially effects on the immune system (Lehner et al., 2019a). Yet, the potential toxicity of MPs to the human body has not yet been extensively studied.
Humans are exposed to MPs via inhalation, ingestion, or dermal absorption (Lehner et al., 2019b). Of these, drinking water is the most prominent exposure route (Novotna et al., 2019). For example, MPs were found in all the treated water samples, having an abundance range of 338 ± 76 to 628 ± 28 MP L−1. In the effluent of a drinking water treatment plant in the Yangtze River Delta, 1–5 μm MPs were found at 930 ± 72 MP L−1 (Ren et al., 2020). In China, MPs (at 440 ± 275 MP?L−1) were found in 38 tap water samples from various cities (Tong et al., 2020). Earlier, Mason and colleagues found 93% MP concentration from 259 bottled water samples of 11 various brands (Mason et al., 2018).
Usually, MPs get into drinking water during water purification, transportation, and packaging, suggesting that plastic forms of equipment or containers are likely the entry points (Eerkes-Medrano et al., 2015). For instance, some MPs (>1 μm) were detected in bottled mineral water, at a level of 2,649 ± 2857 MP L−1 contained in a disposable PET bottle. Here, PET was the predominant MP, indicating that packaging was the likely contamination source (Schymanski et al., 2018). Elsewhere, MPs (>20 μm) were found in wastewater purification systems. The abrasion of plastic equipment during the purification or transport was opined as the MP source in the drinking water (Mintenig et al., 2019). In China, polyethylene (PE, 26.8%) and polypropylene (PP, 24.4%) were the most abundant MP polymer types observed in drinking water because PE and PP are abundant pipe material used (Tong et al., 2020).
Figure 4 depicts the potential routes by which marine microplastic pollution could hinder biological species (Enerkem, 2018; European Environmental Agency, 2019). From this illustration, we could deduce that the enormous use of plastic bottles globally is largely responsible for the current hindrances microplastics are inducing on marine lives.
FIGURE 4. Possible toxicokinetic routes for microplastic pollution on aquatic species (European Environmental Agency, 2019).
Human consumption of animals exposed to microplastics and plastic additives can be detrimental. Generally, humans are exposed through inhalation, ingestion, or dermal absorption (Lehner et al., 2019b), as drinking water has been opined as the main route (Novota et al., 2019). In particular, the microplastics abundance (MP) found in treated water ranged from 338 ± 76 to 628 ± 28 MP L−1 (Pivokonsk et al., 2018).
Despite the diverse and intense efforts devoted to curbing plastic pollution, it is still uneconomical to segregate the various plastics found in our water bodies or landfills before any further treatment. Ideally, each plastic type should be in a separate stream to ensure cleaner and efficient recycling, enabling a higher percentage of the expected outcome (Hopewell et al., 2009). An easy way out is to sort at the source, i.e., household sorting of plastic bottles after prewashing and drying. Figure 5 shows the recent and projected treatment and fate options of plastics that enter the ecosystem.
FIGURE 5. Recent and projected fate of environmental plastic waste (The Pew Charitable Trusts and SYSTEMIQ, 2018).
Mechanical recycling involves two processes: physical methods to homogenize the waste (i.e., storage, shredding, washing, and sorting) and melt processing (i.e., re-granulation and reprocessing) (Vannessa, 2007). A generalized mechanical recycling process for plastic recovery is depicted in Figure 6. The flakes are further processed by compounding into a more turgid material (Ragaert, 2019).
FIGURE 6. Mechanical recycling for plastic wastes (Ragaert, 2019).
The recyclates can effectively replace the original plastics. The process after re-melting could involve injection molding, extrusion, rotational molding, and heat pressing (Lettieri and Baeyens, 2009; Ignatyev et al., 2014).
Generally, the mechanical recycling method is only applicable to thermoplastic materials. Examples of mechanical recycling of post-consumer plastics waste include 1) collecting, cleaning, sorting, pulverizing of PP crates, followed by blending with plain polymer for molding new crates (Coulier et al., 2007), 2) collecting, washing, pulverizing, re-washing, sorting, drying, re-granulation, and converting of low-density polyethylene (LDPE) films into refuse bags (Ragaert et al., 2017), and 3) collecting, sorting, pulverizing, washing, sorting, drying, and processing PET bottles into polyester fibers, used to make diverse forms of sheets and containers (López-Fonseca et al., 2011; European Environmental Agency, 2019).
Chemical recycling occurs by chemically reducing a polymer to its original monomeric form for reprocessing (re-polymerization) into brand new plastics (Figure 7) (Andrady, 2003; Karayannidis and Achilias, 2007; Al-Salem et al., 2009; Francis, 2016; Das and Tiwari, 2018). Here, the thermal and catalytic depolymerization of long polymer chains into oligomers can either be deployed solely or used to complement mechanical recycling (Grigore, 2017). The option of reproducing the original polymer or a different kind suffices because the derived monomers, oligomers, or mixtures of other hydrocarbons are suitable feedstock materials (Olah et al., 2008; Francis, 2016).
FIGURE 7. A typical chemical recycling technique for waste plastic control (Pohjakallio et al., 2020).
For example, through microwave irradiation in the presence of (di)ethylene glycol and metal salt catalyst, PET monomerizes into the intermediate monomer bis(2-hydroxyethyl)terephthalate (BHET) (Pingale and Shukla, 2008; Achilias et al., 2010). The BHET can then be used to reproduce PET via polymerization with the release of ethylene glycol (Scheirs, 1998; Scheirs and Long, 2003).
The chemical processes for depolymerizing plastics include glycolysis, gasification, methanolysis, and pyrolysis. This review focuses on the pyrolysis route.
During the chemical recycling of PET via glycolysis, ethylene glycol molecule is incorporated into the PET chains, forming bis(hydroxyethyl) terephthalate (BHET), which is a substrate for PET synthesis and other oligomers (Colomines et al., 2005; Karayannidis and Achilias, 2007; López et al., 2011). Generally, BHET catalyzes PET glycolysis of several ionic liquids. For instance, with basic ionic liquid, 1-butyl-3-methylimidazolium hydroxyl ([Bmim]OH), it exhibits higher catalytic activity than 1-butyl-3-methylimidazolium bicarbonate ([Bmim]HCO3), 1-butyl-3-methylimidazolium chloride ([Bmim]Cl), 1-butyl-3-methylimidazolium bromide ([Bmim]Br) (Yue et al., 2011). Elsewhere, the purification of glycolysis products was catalyzed by ionic liquids, a process simpler and more efficient than the use of traditional compounds (such as metal acetate) (Wang et al., 2009).
Gasification involves partial combustion, initially developed for coal and oil industries. There are several system variations, depending on the gas used, such as pure oxygen, air, steam, oxygen-enriched air, or CO2 (Mishra et al., 2018). In turn, the temperature required depends on the fuel type, usually within 800–160°C. Gasification is beneficial for fuel gas production because one gaseous product is formed. However, the process is too energy intensive, cost-ineffective, and potentially unsafe (Sikarwar et al., 2017). The synthetic gas generated is graded based on its composition, heat capacity, and applicability. Usually, more than 73% of the waste's carbon content is converted to gas, leaving behind benign ash residue for subsequent and terminal disposal (Vannessa, 2007).
Elsewhere, a typical example of methanolysis is one whereby polyethylene terephthalate (PET) is degraded by methanol at 180–280°C and 2–4 MPa, yielding dimethyl terephthalate (DMT) and ethylene glycol (EG), among other minor by-products (Al-Sabagh et al., 2016; Geyer et al., 2016). The chemical process of PET methanolysis is presented in Figure 8.
FIGURE 8. Methanolysis of polyethylene terephthalate (Geyer et al., 2016).
As depicted in Figure 9, pyrolysis is a process when plastics are heated in the absence of oxygen till the waste plastic material decomposes into gases and oils. During pyrolysis, plastic polymers break down into small molecules (Sharuddin et al., 2017). Pyrolysis at high temperatures (>600°C) favors the production of small gas molecules, while low temperature (<400°C) produces more viscous liquids. This process is a viable route for recycling waste plastics and converts into fuels and gases and also solves the environmental problem because most of the plastic commonly contains toxic and halogen flame retardants (Maafa, 2021).
FIGURE 9. A typical pyrolytic process for plastic waste management (Ragaert et al., 2017).
Pyrolysis helps convert post-consumer waste plastic into produce valuable hydrocarbons and a unique approach for catalytic recycling of plastic waste (Awasthi et al., 2017).
Energy recovery usually refers to the recovery of the inherent energy of a material (Eriksson and Finnveden, 2017). Because most polymers oil-based materials, it is understandable that they are excellent sources of liquid fuel. The quantity of energy recoverable from a plastic when incinerated largely depends on the calorific value of the plastic. The approximated average calorific value of mixed plastic waste is 35 MJykg, superior to those of paper (16 MJykg) and organic waste (3 MJykg) (Hopewell et al., 2009). Aside from incineration, waste-derived fuel and recovery of methane from landfill are other energy recovery approaches.
Comparatively, Japan and the United States are nations on the frontline of implementing energy recovery technologies. For instance, Japan subjects about 78% of its municipal waste to energy recovery mechanisms, while Denmark and the United Kingdom only use 58 and 9%, respectively (Goodship, 2007). These wide differences among the nations can be attributed to the varying degree of acceptance of landfilling as a waste disposal option. However, with the growing cost and strict restrictions on landfilling, the prospect of energy recovery is expected to improve.
Many European countries have adopted routine use of municipal solid waste combustors with modern energy recovery and fiue gas cleaning technologies to improve meeting the high domestic electricity demands. It is more energy efficient when the combustor is coupled with a local municipal heating system, thereby producing and supplying hot water and steam to homes and other structures where needed (Ryu and Shin, 2013). In some areas in Paris, France, residential buildings are equipped with combustors, enabling domestic waste incineration that also provides readily available and low-cost heating systems for the residents (Larané, 2000). The first ever electricity generating plant that operates solely on waste plastics as fuel was built in Japan. The plant can manage 700 tonnes of plastic wastes a day, generating enough power for 30,000 Japanese homes (Vannessa, 2007).
Al-Salem et al. (2020) pyrolyzed plastic waste in an Auger Pyrolysis Reactor at 500°C. Their research gathered that plastic waste reclamation from landfills and subsequent conversion into hydrocarbon products was efficient and commercialized, judging by the mass balance and product characterization. Further analysis confirmed that the liquid fractions shared similar properties with petrol and diesel, while the wax products were viable and could be used for coating, covering, and lubrication (Gabbar et al., 2017). Before then, Demirbas (2004) pyrolyzed conducted three plastics waste types viz. polystyrene, polyethylene, and polypropylene, retrieved from landfill. The pyrolyzed polystyrene yielded higher liquid (especially styrene, with minor quantities of naphtha, gasoline, and light gas oil). In contrast, the others were more efficient in generating gaseous fuels (mainly paraffinic hydrocarbons and olefins).
Onwudili et al. (2009) carried out Co-pyrolysis of PS and PE at 300–500°C in a closed batch reactor. Specifically, PE degraded to oil at 425°C. Beyond this temperature, the amount of fuel oil (mainly aliphatic hydrocarbons) product reduced as more char and fuel gas were produced. On the other hand, PS degraded at ≈350°C into a viscous dark-colored aromatic oil, mainly toluene and ethylbenzene, often used as raw materials in the paint industry. Thus, a closed batch system can effectively degrade LDPE and PS into high-grade liquid fuels, new industrial raw materials, and/or chemical feedstock for the petroleum refinery.
About a decade ago, Adrados et al. (2012) collected waste plastics (of various types, such as PE, PP, PS, etc.) from a local material recovery facility. They pyrolyzed the waste plastics in a non-stirred, semi-batch reactor, at a heating rate 20°C/min to 500°C, and held for 30 min. The final products consisted of 40.9 wt% of oils, 25.6 wt% gases, and 5.3 wt% of char, with 28.2 wt% of inorganic residue, derived from the non-plastic packaging materials in the waste. The oils consisted of C5–C9, C10–C13, and >C13 compounds, while the pyrogas comprised of light hydrocarbons (such as methane, ethane, ethene, and <C6 molecule), CO2, CO, and hydrogen. The char, with 29.3% carbon content, is potentially an excellent solid fuel.
Elsewhere, Chanashetty and Patil (2015) carried out pyrolysis of waste LDPE to derive liquid fuel similar to petrol or diesel. The team found that the properties of the fuel obtained were similar to those from petrol. Also obtained from the thermal cracking were some light gases, such as methane, ethane, propane, and butane.
More recently, Budsaereechai et al. (2019) pyrolyzed four waste plastic types viz. PS, PP, LDPE, and HDPE in the presence of pelletized bentonite clay as a catalyst. They reported that the oils from PS were primarily aromatics in the gasoline range (C5–C9). At the same time, PP, LDPE, and HDPE yielded aliphatic hydrocarbons with longer chains, making them suitable fuels for diesel engines.
Due to the incessant increase in the production, use, and abuse of plastics on a global scale, the rate and magnitude at which plastic wastes are generated have also increased astronomically in the past 3 decades. This scenario has led to severe environmental problems arising from the need to dispose of such huge quantities of waste daily (Miteva et al., 2016). Because plastics are non-biodegradable, eliminating them from the ecosystem is cumbersome. Their common treatment via indiscriminate burning has been indicted to contributing to greenhouse gas emissions. Thus, incineration has sufficed as a major treatment option for plastic waste in reducing greenhouse gas emissions (Oasmaa et al., 2020).
Of the three main plastic waste maintenance methods (i.e., incineration, mechanical recycling, and chemical recycling (pyrolysis)), landfilling is more responsible for severe environmental issues because of the environmental load involved (Miskolczi et al., 2009). Plastic waste disposal via landfills provides habitats for insects and rodents, causing various diseases among nearby residents (Alexandra, 2012). Because landfilling is time-consuming before noticeable results can be observed, the method has been found to induce environmental burdens, acting as stressors to the soil, aquifers and promoting air pollution in the form of odor release (Al-Salem et al., 2020).
Alternatively, the incineration of plastics produces a large amount of thermal energy, which is often accompanied by some air pollutants. When not properly operation, incinerators release carcinogens in the form of dioxin, furan, and toxic metals in the smoke, causing secondary environmental problems (Chanashetty and Patil, 2015). Based on these facts, researchers have agreed that the most prospective route for plastic waste management (i.e., control and utilization) is via pyrolysis (Miskolczi et al., 2009; Syamsiroa et al., 2014). Moreover, the oil produced from biomass pyrolysis is a “green” fuel because it is combustion contributes to lowering CO2 emissions. Overall, pyrolysis is a more efficient, economical, and cleaner plastic waste management technology (Abnisa et al., 2004).
To improve the energy recovery efficiency of plastic waste pyrolysis and shorten the recovery time, numerous catalysts (such as zeolite, silica-alumina, and fluid-cracking catalyst) have been used.
Catalytic pyrolysis of plastic waste with binder-free bentonite clay pellets was carried out by Budsaereechai et al. (2019). The clay pellets successfully ensured the production of liquid fuels with improved calorific values and lowered viscosity. Also, the study demonstrated that using the catalyst in a powdery form induced unwanted pressure drop in the catalyst column, a scenario avoided by using pellets. Also, with the pellets, the operation time was reduced to only 10 min/kg of plastic waste. Moreover, no wax was formed in this particular system.
Elsewhere, Suhartono et al. (2018) reported plastic pyrolysis using natural zeolite as a catalyst in the search for alternative fuel. The catalyst achieved the highest fuel oil yield derivation. The researchers obtained 650 ml (65% vol/w) and 550 ml (55% vol/w) of fuel oil from 1 kg of HDPE and LDPE, respectively. However, without catalysis, the respective yields were 250 ml (25% vol/w) and 300 ml.
In another study, Miteva et al. (2016) performed catalytic (Al2O3-SiO2) pyrolysis on waste plastic. The researchers reported that SiO2 exhibited the most significant effect on the quality and quantity of liquid fuel produced. Another research on fuel production from municipal plastics wastes using Y-zeolite and natural zeolite as catalysts was reported (Syamsiroa et al., 2014). Here, the catalyst reduced the liquid fraction at the expense of the gaseous fraction. The authors attributed this result to the presence of impurities in the waste. When the two catalysts were later compared against each other, it was found that the natural zeolite catalyst was more efficient of the two materials. Elsewhere, zeolite catalyst has been credited with lowering the impurities' levels derived from the oil of pyrolyzed municipal plastic waste (Miskolczi et al., 2009).
Apart from using zeolite, bentonite, and silica/aluminum, spent Fluid Cracking Catalyst (FCC) has been adopted as a catalyst to improve the plastic conversion during pyrolysis (Lee et al., 2003). The efficiency of FCC was compared with that of thermal degradation (without catalyst). FCC was observed to have lowered the degradation temperature, hastened the liquid fuel product rate, and reduced the residue content than the conventional thermal degradation.
Although the environmental benefit of plastic pyrolysis has been established, there is a need to evaluate the cost of operating a plastic pyrolytic process for commercial purposes (Enerkem, 2018). In this scope, the production cost is the consumption of Liquid Petroleum Gas (LPG) for the pyrolysis of plastic waste, excluding equipment investment cost. Suhartono et al. (2018) evaluated production cost and the price of oil fuel produced per unit 2 kg of plastic waste raw. In their research, they concluded that the operational cost of pyrolysis using LPG as a thermal source was IDR 12,300/L (≈$170/L) of fuel oil, while the present market price of conventional kerosene (as at the time of their research) was IDR 13,600/L (≈$180/L).
Last year, Kulkarni and Shastri (2020) also conducted an economic analysis of waste plastic pyrolysis in Mumbai, India. In their evaluation, the factors considered include the costs of transporting sorted waste (over 40 km from the plant site), shredding, and the power required by the pyrolyzer. The ignored factors include the labor cost. The heat energy generated from the plant was used to generate the electricity needed for the operation. Considering these factors, they estimated the total expenditure as INR 8,189.8/ton (≈$112.6/ton) of plastic waste, with a total earning of INR 15,236.9/ton (≈$210/ton) of the trash. Hence, a profit of INR 7,047.1 per ton ($97/ton) was achieved.
Since the production and use of plastics cannot be halted in the foreseeable future, due to the immense benefits of plastic to the modern world, the way forward includes the following:
1. Where unavoidable, more thermoplastics, which is recyclable, should be produced for essential use, rather than thermosetting plastics, which are unrecyclable;
2. The pyrolysis option of resource recovery should be prioritized because of its inherent benefits, such as being a waste-to-wealth scheme and environmental benignity.
3. For source control, household energy recovery from plastics has exemplified in Paris, should be encouraged.
4. Where possible, governments should monetize the scavenging of plastics from the ocean and other waterways to reduce the eventual environmental cataclysm that results from flooding and endangered aquatic lives.
The author confirms being the sole contributor of this work and has approved it for publication.
The author declares that the research was conducted in the absence of any commercial or financial relationships that could be construed as a potential conflict of interest.
My immense gratitude to my exceptional and excellent research assistants, Usman Hassan and Oladimeji Afolabi, who helped gather some of the resource manuscripts used for this study.
Abnisa, F., Wan Daud, W. M. A., Arami-Niya, A., Ali, B. S., and Sahu, J. N. (2004). Recovery of Liquid Fuel from the Aqueous Phase of Pyrolysis Oil Using Catalytic Conversion. Energy & Fuels 28, 3074–3085.
Achilias, D. S., Redhwi, H. H., Siddiqui, M. N., Nikolaidis, A. K., Bikiaris, D. N., and Karayannidis, G. P. (2010). Glycolytic Depolymerization of PET Waste in a Microwave Reactor. J. Appl. Polym. Sci. 118, 3066–3073. doi:10.1002/app.32737
Adrados, A., de Marco, I., Caballero, B. M., López, A., Laresgoiti, M. F., and Torres, A. (2012). Pyrolysis of Plastic Packaging Waste: A Comparison of Plastic Residuals from Material Recovery Facilities with Simulated Plastic Waste. Waste Manag. 32, 826–832. doi:10.1016/j.wasman.2011.06.016
Al-Sabagh, A. M., Yehia, F. Z., Eshaq, G., Rabie, A. M., and ElMetwally, A. E. (2016). Greener Routes for Recycling of Polyethylene Terephthalate. Egypt. J. Pet. 25 (1), 53–64. doi:10.1016/j.ejpe.2015.03.001
Al-Salem, S. M., Lettieri, P., and Baeyens, J. (2009). Recycling and Recovery Routes of Plastic Solid Waste (PSW): A Review. Waste Manag. 29, 2625–2643. doi:10.1016/j.wasman.2009.06.004
Al-Salem, S. M., Yang, Y., Wang, J., and Leeke, G. A. (2020). Pyro-Oil and Wax Recovery from Reclaimed Plastic Waste in a Continuous Auger Pyrolysis Reactor. Energies 13 (8), 2040–2050. doi:10.3390/en13082040
Alabi, O. A>, Ologbonjaye, K. I., Awosolu, O., and Alalade, O. E. (2019). Public and Environmental Health Effects of Plastic Wastes Disposal: a Review. J. Toxicolocy Risk Assess. 5, 021.
Alexandra, L. (2012). Municipal Solid Waste: Turning a Problem into Resource. United States: World Bank, 2–4.
Askeland, D. R. (1996). Polymers. In: The Science and Engineering of Materials. Boston, MA: Springer, 488–548. doi:10.1007/978-1-4899-2895-5_15
Awasthi, A., Shivashankar, M., and Majumder, S. (2017). Plastic Solid Waste Utilization Technologies: a Review. IOP Conf. Ser. Mater. Sci. Eng. 263 (2), 022024. doi:10.1088/1757-899x/263/2/022024
Awuchi, C. G., and Awuchi, C. G. (2019). Impacts of Plastic Pollution on the Sustainability of Seafood Value Chain and Human Health. Int. J. Adv. Acad. Res. 5 (11), 46–138.
Bakir, A., Rowland, S. J., and Thompson, R. C. (2014). Enhanced Desorption of Persistent Organic Pollutants from Microplastics under Simulated Physiological Conditions. Environ. Pollut. 185, 16–23. doi:10.1016/j.envpol.2013.10.007
Bouchentouf, S. (2013). Abundance of Plastic Debris in Intertidal Surface Sediments from Arzew Gulf (Western Algeria). Am. J. Mater. Sci. 1, 28–32.
Budsaereechai, S., Hunt, A. J., and Ngernyen, Y. (2019). Catalytic Pyrolysis of Plastic Waste for the Production of Liquid Fuels for Engines. RSC Adv. 9, 5844–5857. doi:10.1039/c8ra10058f
Chanashetty, V. B., and Patil, B. (2015). Fuel from Plastic Waste. Int. J. Emerging Tech. 6 (2), 121–128.
Cole, M., Lindeque, P., Halsband, C., and Galloway, T. S. (2011). Microplastics as Contaminants in the marine Environment: A Review. Mar. Pollut. Bull. 62 (12), 2588–2597. doi:10.1016/j.marpolbul.2011.09.025
Colomines, G., Robin, J. J., and Tersac, G. (2005). Study of the Glycolysis of PET by Oligoesters. Polymer 46, 3230–3247. doi:10.1016/j.polymer.2005.02.047
Coulier, L., Orbons, H. G. M., and Rijk, R. (2007). Analytical Protocol to Study the Food Safety of (Multiple-)recycled High-Density Polyethylene (HDPE) and Polypropylene (PP) Crates: Influence of Recycling on the Migration and Formation of Degradation Products. Polym. Degrad. Stab. 92 (11), 2016–2025. doi:10.1016/j.polymdegradstab.2007.07.022
d’Ambrières, W. (2019). Plastics Recycling Worldwide: Current Overview and Desirable Changes. Field Actions Sci. Rep. 19, 12–21.
Das, P., and Tiwari, P. (2018). Valorization of Packaging Plastic Waste by Slow Pyrolysis. Resour. Conservation Recycling 128, 69–77. doi:10.1016/j.resconrec.2017.09.025
Demirbas, A. (2004). Pyrolysis of Municipal Plastic Wastes for Recovery of Gasoline-Range Hydrocarbons. J. Anal. Appl. Pyrolysis 72, 97–102. doi:10.1016/j.jaap.2004.03.001
Dhinakaran, V., Surendar, K. V., Hasunfur Riyaz, M. S., and Ravichandran, M. (2020). Review on Study of Thermosetting and Thermoplastic Materials in the Automated Fiber Placement Process. Mater. Today Proc. 27 (2), 812–815. doi:10.1016/j.matpr.2019.12.355
Eerkes-Medrano, D., Thompson, R. C., and Aldridge, D. C. (2015). Microplastics in Freshwater Systems: A Review of the Emerging Threats, Identification of Knowledge Gaps and Prioritisation of Research Needs. Water Res. 75, 63–82. doi:10.1016/j.watres.2015.02.012
Enerkem (2018). Partners Agree on Initial Funding to Kick off Waste-To-Chemistry Project in Rotterdam. URL https://enerkem.com/newsroom/releases/?communique_id=122566.
Erdogan, S. (2020). Recycling of Waste Plastics into Pyrolytic Fuels and Their Use in IC Engines. London: IntechOpen, 1–23.
Eriksson, O., and Finnveden, G. (2017). Energy Recovery from Waste Incineration-The Importance of Technology Data and System Boundaries on CO2 Emissions. Energies 10 (4), 539. doi:10.3390/en10040539
European Environmental Agency (2019). Resource Efficiency and Waste. Available: https://www.eea.europa.eu/themes/waste/intro (Accessed May 14, 2019).
Fok, L., Lam, T. W. L., Li, H.-X., and Xu, X.-R. (2020). A Meta-Analysis of Methodologies Adopted by Microplastic Studies in China. Sci. Total Environ. 718, 135371. doi:10.1016/j.scitotenv.2019.135371
Francis, R. (2016). Recycling of Polymers: Methods,Characterizationand Applications. Ind. Eng. Chem. Res., 40. Hoboken, NJ, USA: John Wiley & Sons, 4749–4756.
Gabbar, H., Aboughaly, M., and Stoute, C. A. (2017). DC Thermal Plasma Design and Utilization for the Low Density Polyethylene to Diesel Oil Pyrolysis Reaction. Energies 10, 784. DC thermal plasma design and utilization for the low density polyethylene to diesel oil pyrolysis reaction Energies. doi:10.3390/en10060784
Geyer, B., Lorenz, G., and Kandelbauer, A. (2016). Recycling of Poly(ethylene Terephthalate) - A Review Focusing on Chemical Methods. Express Polym. Lett. 10 (7), 559–586. doi:10.3144/expresspolymlett.2016.53
Geyer, R., Jambeck, R., and Law, K. (2018). Production, Use and Fate of All Plastics Ever Made, Supranote 20; European Commission, Communication from the Commission to the European Parliament, the Council, the European Economic and Social Committee and the Committee of the Regions: A European Strategy for Plastics in a Circular Economy. :Jan. 16, 2018:28:FIN# https://eur-lex.europa.eu/legal-content/EN/TXT/?qid=1516265440535&uri=COM.
Godfrey, L. (2019). Waste Plastic, the Challenge Facing Developing Countries-Ban it, Change it, Collect it?. Recycling 4, 3. doi:10.3390/recycling4010003
Grigore, M. (2017). Methods of Recycling, Properties and Applications of Recycled Thermoplastic Polymers. Recycling 2, 24. doi:10.3390/recycling2040024
Hopewell, J., Dvorak, R., and Kosior, E. (2009). Plastics Recycling: Challenges and Opportunities. Phil. Trans. R. Soc. B 364 (1526), 2115–2126. doi:10.1098/rstb.2008.0311
Horton, A. A., Walton, A., Spurgeon, D. J., Lahive, E., and Svendsen, C. (2017). Microplastics in Freshwater and Terrestrial Environments: Evaluating the Current Understanding to Identify the Knowledge Gaps and Future Research Priorities. Sci. Total Environ. 586, 127–141. doi:10.1016/j.scitotenv.2017.01.190
Ignatyev, I. A., Thielemans, W., and Vander Beke, B. (2014). Recycling of Polymers: A Review. ChemSusChem. 7 (6), 1579–1593. doi:10.1002/cssc.201300898
Jang, M., Shim, W. J., Cho, Y., Han, G. M., Song, Y. K., and Hong, S. H. (2020). A Close Relationship between Microplastic Contamination and Coastal Area Use Pattern. Water Res. 171, 115400. doi:10.1016/j.watres.2019.115400
Karayannidis, G. P., and Achilias, D. S. (2007). Chemical Recycling of Poly(ethylene Terephthalate). Macromol. Mater. Eng. 292, 128–146. doi:10.1002/mame.200600341
Khan, M. Z., Sultana, M., Al-Mamun, M. R., and Hasan, M. R. (2016). Pyrolytic Waste Plastic Oil and its Diesel Blend: Fuel Characterization. J. Environ. Public Health 2016, 7869080. doi:10.1155/2016/7869080
Kulkarni, S., and Shastri, Y. (2020). Economic Analysis and Life Cycle Assessment of Pyrolysis of Plastic Waste in Mumbai, India in Sustainable Waste Management: Policies and Case Studies, 1, 454–463.
Larané, A. (2000). French Use Household Waste for Heating and Resource Recovery. Environ. Sci. Eng. Mag.. https://esemag.com/archives/french-use-household-waste-for-heating-and-resource-recovery.
Lee, K.-H., Jeon, S.-G., Kim, K.-H., Noh, N.-S., Shin, D.-H., Park, J., et al. (2003). Thermal and Catalytic Degradation of Waste High-Density Polyethylene (HDPE) Using Spent FCC Catalyst. Korean J. Chem. Eng. 20 (4), 693–697. doi:10.1007/bf02706909
Lehner, R., Wohlleben, W., Septiadi, D., Landsiedel, R., Petri-Fink, A., and Rothen-Rutishauser, B. (2019a). A Novel 3D Intestine Barrier Model to Study the Immune Response upon Exposure to Microplastics. Arch. Toxicol. 94 (7), 2463–2479.
Lehner, R., Weder, C., Petri-Fink, A., and Rothen-Rutishauser, B. (2019b). Emergence of Nanoplastic in the Environment and Possible Impact on Human Health. Environ. Sci. Technol. 53 (4), 1748–1765. doi:10.1021/acs.est.8b05512
Lettieri, P., and Baeyens, J. (2009). Recycling and Recovery Routes of Plastic Solid Waste ( PSW ): A Review. Waste Manag. 29 (10), 2625–2643.
Li, W. C., Tse, H. F., and Fok, L. (2016). Plastic Waste in the marine Environment: a Review of Sources, Occurrence and Effects. Sci. Total Environ. 566-567, 333–349. doi:10.1016/j.scitotenv.2016.05.084
López, A., De Marco, I., Caballero, B. M., Laresgoiti, M. F., and Adrados, A. (2011). Dechlorination of Fuels in Pyrolysis of PVC Containing Plastic Wastes Fuel Process. Technol. 92 (2), 253–260. doi:10.1016/j.fuproc.2010.05.008
López-Fonseca, R., Duque-Ingunza, I., de Rivas, B., Flores-Giraldo, L., and Gutiérrez-Ortiz, J. I. (20082011). Kinetics of Catalytic Glycolysis of PET Wastes with Sodium Carbonate. Chem. Eng. J. 168, 312–320.doi:10.1016/j.cej.2011.01.031
Maafa, I. (2021). Pyrolysis of Polystyrene Waste: a Review. Polymers 13, 225. doi:10.3390/polym13020225
Manickam, R., Benin, A., and Retnam, S. J. (2015). Comparative Study of Tensile Properties on Thermoplastic and Thermosetting Polymer Composites. Int. J. Appl. Eng. Res. 10 (11), 10109.
Mason, S. A., Welch, V. G., and Neratko, J. (2018). Synthetic Polymer Contamination in Bottled Water. Front. Chem. 6, 407. doi:10.3389/fchem.2018.00407
McDonnell, T. I. M. (2015). There’s a Horrifying Amount of Plastic in the Ocean This Chart Shows Who’s to Blame. https://www.motherjones.com/environment/2015/02/ocean-plastic-waste-china/.
Mintenig, S. M., Löder, M. G. J., Primpke, S., and Gerdts, G. (2019). Low Numbers of Microplastics Detected in Drinking Water from Ground Water Sources. Sci. Total Environ. 648, 631–635. doi:10.1016/j.scitotenv.2018.08.178
Mishra, A., Gautam, S., and Sharma, T. (2018). Effect of Operating Parameters on Coal Gasification. Int. J. Coal Sci. Technol. 5, 113–125. doi:10.1007/s40789-018-0196-3
Miskolczi, N., Angyal, A., Bartha, L., and Valkai, I. (2009). Fuels by Pyrolysis of Waste Plastics from Agricultural and Packaging Sectors in a Pilot Scale Reactor. Fuel Process. Tech. 90, 1032–1040. doi:10.1016/j.fuproc.2009.04.019
Miteva, K., Aleksovski, S., and Bogoeva-Gaceva, G. (2016). Catalytic Pyrolysis of Waste Plastic into Liquid Fuel. Zas Mat. 57 (4), 600–604. doi:10.5937/zasmat1604600m
Novotna, K., Cermakova, L., Pivokonska, L., Cajthaml, T., and Pivokonsky, M. (2019). Microplastics in Drinking Water Treatment - Current Knowledge and Research Needs. Sci. Total Environ. 667, 730–740. doi:10.1016/j.scitotenv.2019.02.431
Oasmaa, A., Qureshi, M. S., Pihkola, H., Deviatkin, I., and Mannila, J. (2020). Pyrolysis of Plastic Waste: Opportunities and Challenges. J. Anal. Appl. Pyrolysis 152, 104804.
Olah, G. A., Goeppert, A., and Prakash, G. K. S. (2008). Chemical Recycling of Carbon Dioxide to Methanol and Dimethyl Ether: From Greenhouse Gas to Renewable, Environmentally Carbon Neutral Fuels and Synthetic Hydrocarbons. J. Org. Chem. 74, 487–498. doi:10.1021/jo801260f
Onwudili, J. A., Insura, N., and Williams, P. T. (2009). Composition of Products from the Pyrolysis of Polyethylene and Polystyrene in a Closed Batch Reactor: Effects of Temperature and Residence Time. J. Anal. Appl. Pyrolysis 86, 293–303. doi:10.1016/j.jaap.2009.07.008
Pawar, P. R., Shirgaonkar., S., and Patil, R. B. (2016). Plastic marine Debris: Sources, Distribution and Impacts on Coastal and Ocean Biodiversity. PENCIL Publ. Biol. Sci. 3 (1), 40–54.
Pingale, N., and Shukla, S. R. (2008). Microwave Assisted Ecofriendly Recycling of Poly (Ethylene Terephthalate) Bottle Waste. Eur. Polym. J. 44 (12), 4151–4156.
Pivokonsk, M., Cermokova, L., Novotna, K., and Peer, P. (2018). Occurrence of Microplastics in Raw and Treated Drinking Water. Sci. Total Environ. 643, 1644–1651.
PlasticEurope (2015). Plastics: The FACT 2014/2015: An Analysis of European Plastics Production, Demand, and Waste Data. Belgium: PlasticsEurope Brussels.
Pohjakallio, M., Vuorinen, T., and Oasmaa, A. (2020). Chemical Routes for Recycling-Dissolving, Catalytic, and Thermochemical Technologies. Plast. Waste Recycling Chapter 13, 359–384. doi:10.1016/b978-0-12-817880-5.00013-x
Ragaert, K., Delva, L., and Van Geem, K. (2017). Mechanical and Chemical Recycling of Solid Plastic Waste. Waste Manag. 69, 24–58. doi:10.1016/j.wasman.2017.07.044
Ragaert, K. (2019). Mechanical Recycling for Dummies. https://ubuntoo.com/blogs/mechanical-recycling-for-dummies.
Ren, H., Tröger, R., Ahrens, L., Wiberg, K., and Yin, D. (2020). Screening of Organic Micropollutants in Raw and Drinking Water in the Yangtze River Delta, China. Environ. Sci. Europe 32 (67), 1–12.
Richardson, K., Gunn, R., Wilcox, C., and Hardesty, B. D. (2018). Understanding Causes of Gear Loss Provides a Sound Basis for Fisheries Management. Mar. Pol. 96, 278–284. doi:10.1016/j.marpol.2018.02.021
Royer, S. J., Ferron, S., Wilson, S. T., and Karl, D. M. (2018). Production of Methane and Ethylene from Plastic in the Environment. PLoS ONE 18 (8), e0200574.
Ryu, C., and Shin, D. (2013). Combined Heat and Power from Municipal Solid Waste: Current Status and Issues in South Korea. Energies 6, 45–57.
Salles, J. C., and Deschamps, F. J. (2010). Allergic Contact Dermatitis Due to a PVC Table Cover. Occup. Med. 60 (8), 662–664. doi:10.1093/occmed/kqq137
Scheirs, J., and Long, T. E. (2003). Modern Polyesters: Chemistry and Technology of Polyesters and Copolyester. England: John Wiley & Sons.
Scheirs, J. (1998). Polymer Recycling: Science, Tecnology and Application. New York: John Wiley & Sons.
Schwab, K. (2019). The Global Competitiveness Report: World Economic Forum. http://www3.weforum.org/docs/WEF_TheGlobalCompetitivenessReport2019.pdf.
Schymanski, D., Goldbeck, C., Humpf, H.-U., and Fürst, P. (2018). Analysis of Microplastics in Water by Micro-raman Spectroscopy: Release of Plastic Particles from Different Packaging into mineral Water. Water Res. 129, 154–162. doi:10.1016/j.watres.2017.11.011
Sharuddin, S. D. A., Abnisa, F., Daud, W. M. A. W., and Aroua, M. K. (2017). Pyrolysis of Plastic Waste for Liquid Fuel Production as Prospective Energy Resource. IOP Conf. Ser. Mater. Sci. Eng. 334, 012001.
Sikarwar, V. S., Zhao, M., Fennell, P. S., Shah, N., and Anthony, E. J. (2017). Progress in Biofuel Production from Gasification. Prog. Energ. Combustion Sci. 61, 189–248. doi:10.1016/j.pecs.2017.04.001
Smith, M., Love, D. C., Rochman, C. M., and Neff, R. A. (2018). Microplastics in Seafood and the Implications for Human Health. Curr. Envir Health Rpt 5 (3), 375–386. doi:10.1007/s40572-018-0206-z
Suhartono, K. P., Romli, A., Aulia, I. M., and Yanuar, M. E. (2018). Fuel Oil from Municipal Plastic Waste through Pyrolysis with and without Natural Zeolite as Catalysts. E3S Web of Conferences 73 (01021). doi:10.1051/e3sconf/20187301021
Syamsiro, M., Saptoadi, H., Norsujianto, T., Noviasri, P., Cheng, S., Alimuddin, Z., et al. (2014). Fuel Oil Production from Municipal Plastic Wastes in Sequential Pyrolysis and Catalytic Reforming Reactors. Energ. Proced. 47, 180–188. doi:10.1016/j.egypro.2014.01.212
The Pew Charitable TrustsSYSTEMIQ (2018). Breaking the Plastic Wave: A Comprehensive Assessment of Pathways towards Stopping Ocean Plastic Pollution.
Thompson, R. C., Olsen, Y., Mitchell, R. P., Davis, A., Rowland, S. J., John, A. W. G., et al. (2004). Lost at Sea: where Is All the Plastic?. Science 304, 838. doi:10.1126/science.1094559
Tong, H., Jiang, Q., Hu, X., and Zhong, X. (2020). Occurrence and Identification of Microplastics in Tap Water from China. Chemosphere 252, 126493. doi:10.1016/j.chemosphere.2020.126493
Verma, R., Vinoda, K. S., Papireddy, M., and Gowda, A. N. S. (2016). Toxic Pollutants from Plastic Waste- A Review. Proced. Environ. Sci. 35, 701–708. doi:10.1016/j.proenv.2016.07.069
Wang, H., Liu, Y., Li, Z., Zhang, X., Zhang, S., and Zhang, Y. (2009). Glycolysis of Poly(ethylene Terephthalate) Catalyzed by Ionic Liquids. Eur. Polym. J. 45, 1535–1544. doi:10.1016/j.eurpolymj.2009.01.025
Warnock, A., and Ruf, C. (2019). Response to Variations in River Flowrate by a Spaceborne GNSS-R River Width Estimator. Remote Sensing 11 (20), 2450. doi:10.3390/rs11202450
Keywords: recycling, pyrolysis, energy recovery, oil and gas, ocean plastic
Citation: Adelodun AA (2021) Plastic Recovery and Utilization: From Ocean Pollution to Green Economy. Front. Environ. Sci. 9:683403. doi: 10.3389/fenvs.2021.683403
Received: 14 April 2021; Accepted: 29 June 2021;
Published: 09 July 2021.
Edited by:
Joginder Singh, Lovely Professional University, IndiaReviewed by:
Arunkumar Subramanian, Thanthai Hans Roever College, IndiaCopyright © 2021 Adelodun. This is an open-access article distributed under the terms of the Creative Commons Attribution License (CC BY). The use, distribution or reproduction in other forums is permitted, provided the original author(s) and the copyright owner(s) are credited and that the original publication in this journal is cited, in accordance with accepted academic practice. No use, distribution or reproduction is permitted which does not comply with these terms.
*Correspondence: Adedeji A. Adelodun, YWFhZGVsb2R1bkBmdXRhLmVkdS5uZw==
†ORCID: Adedeji A. Adelodun, orcid.org/0000-0002-8344-4154
Disclaimer: All claims expressed in this article are solely those of the authors and do not necessarily represent those of their affiliated organizations, or those of the publisher, the editors and the reviewers. Any product that may be evaluated in this article or claim that may be made by its manufacturer is not guaranteed or endorsed by the publisher.
Research integrity at Frontiers
Learn more about the work of our research integrity team to safeguard the quality of each article we publish.