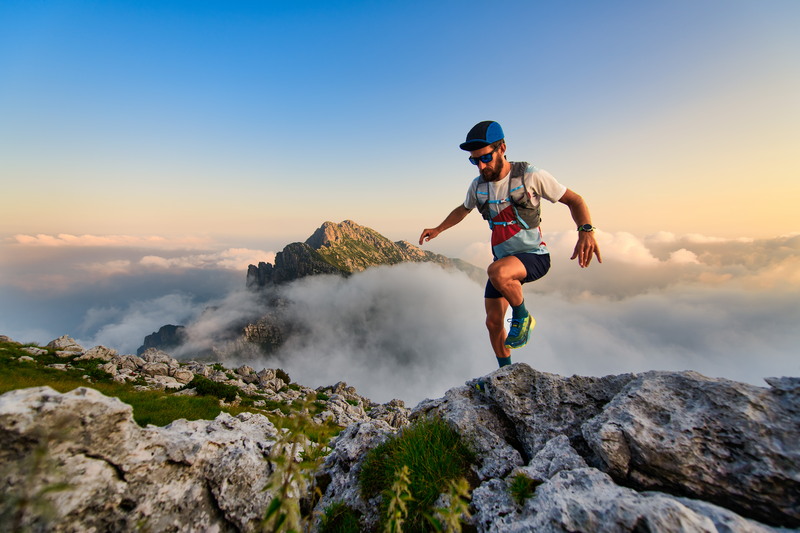
95% of researchers rate our articles as excellent or good
Learn more about the work of our research integrity team to safeguard the quality of each article we publish.
Find out more
ORIGINAL RESEARCH article
Front. Energy Res. , 20 January 2025
Sec. Electrochemical Energy Storage
Volume 12 - 2024 | https://doi.org/10.3389/fenrg.2024.1508471
This article is part of the Research Topic Advanced Electrolyte Design for Next-Generation Electrochemical Energy Storage Devices View all articles
A correction has been applied to this article in:
Corrigendum: A corporate approach to enhancing lithium-ion battery safety through flame-retardant electrolyte development
Lithium-ion batteries (LIBs) are integral to modern technology, yet their reliance on flammable liquid electrolytes poses significant safety challenges, especially in electric vehicles and large-scale energy storage systems. This paper presents the development of flame-retardant electrolytes utilizing the Define-Measure-Analyze-Design-Optimize-Verify (DMADOV) methodology to enhance both safety and performance of LIBs. The study initiates by defining the correlation between the properties of organic solvents and electrochemical stability, focusing on the overcharging risks that can induce thermal runaway. Through systematic measurement and analysis of candidate components, critical factors influencing the quality of flame-retardant electrolytes are identified. The design phase prioritizes the establishment of solid electrolyte interface (SEI) conditions for γ-butyrolactone (γ-BL), ensuring the electrolyte’s performance and stability in LIBs. The optimization phase further refines the SEI formation conditions to address performance challenges identified during initial design, incorporating related manufacturing processes. The final verification phase confirms the alignment of the flame-retardant electrolyte composition with optimized SEI conditions, establishing a viable electrolyte range for practical applications. The study demonstrates that the use of γ-BL markedly reduces the explosion risk due to overcharging. The final verification phase confirms the alignment of the flame-retardant electrolyte composition with optimized SEI conditions, establishing a viable electrolyte range for practical applications. Significantly, this study emphasizes the importance of robust SEI design in developing flame-retardant electrolytes with high-flash-point organic solvents like γ-BL, supported by validation experiments on patented technology. These advancements not only enhance the safety profile of LIBs but also demonstrate the potential for improved battery performance, paving the way for broader applications in energy storage solutions.
Li-ion batteries (LIBs) are pivotal in numerous technological fields, such as portable electronics, electric vehicles, drones, and energy storage systems, due to their high energy density, long cycle life, and low self-discharge characteristics (Neef and Thielmann, 2023). These attributes render LIBs essential for modern devices, providing power in increasingly compact forms. Consequently, LIBs remain at the forefront of research and industry, driven by the increasing demand for efficient and durable energy storage solutions (Grey and Hall, 2020). Despite their advantages, most LIBs use flammable liquid electrolytes with about 70 vol% of low-flash-point solvents such as DEC, which poses serious risks. The volatility of these electrolytes under stress can lead to failures like fires or explosions, threatening user safety and the environment (Ouyang et al., 2019). This issue is critical in applications like electric vehicles and large-scale energy systems where failure has severe consequences.
As the demand for higher performance in these technical applications continues, research must also continue to ensure the safety of high-capacity and -power LIBs. This trend is pushing the boundaries of current battery technologies, necessitating the development of more advanced and robust systems. Consequently, high-capacity LIBs are increasingly being equipped with sophisticated safety mechanisms, such as protection circuit module (PCM), current interrupt devices (CID), mechanical venting system, and so on (Li et al., 2022). While these safety systems are effective in mitigating risks, there is a constant need for innovative technologies that can provide intrinsic safety without compromising performance by increasing the cost and complexity of battery design.
In the electrolyte field, various approaches are being studied to develop flame-retardant or non-flammable electrolytes to reduce flammability and minimize the risk of thermal runaway (Mu et al., 2023). Approaches include liquid, gel, and solid-state formulations, each with their own advantages and challenges. Liquid electrolytes offer high ionic conductivity and low cost; however, they inherently require some flammable organic solvents that may compromise flame retardancy, thus limiting safety improvements. In contrast, solid polymer electrolytes provide excellent safety features but face a significant technical challenge: they need to enhance ionic conductivity by nearly tenfold, particularly under low-temperature conditions. Gel polymer electrolytes, considered a compromise between the characteristics of liquids and solids, aim to address the limitations of solid polymer electrolytes through the addition of liquid components (Huang C. et al., 2024; Chen et al., 2024; Li et al., 2025). From an industrial perspective, liquid flame-retardant electrolytes, in particular, the liquid flame-retardant electrolyte discussed experimentally in this paper may be the most desirable approach because it can be applied without any special changes to the production lines of LIB manufacturers. In particular, liquid flame-retardant electrolytes may be the most desirable approach for companies because they can be applied to the manufacturing processes of LIBs currently in production without significant changes. Strategies to improve the flame resistance of these liquid electrolytes include adding flame-retardant additives, using new solvents with higher flash points, and developing non-flammable ionic liquids (Wang et al., 2014). Improving the flame resistance of electrolytes can significantly reduce the risk of thermal runaway in LIBs and allow for higher energy densities, resulting in lighter and more compact battery packs. Even if flame-retardant electrolytes can improve the safety of LIBs, they must still meet consumer expectations for proper charge-discharge performance over a wide range of temperatures required for applications that require LIBs, such as smartphones, electric vehicles, and renewable energy storage (Huang Y. et al., 2024). This is essential because industries such as electric vehicles and renewable energy storage require high performance and safety.
It is no exaggeration to say that flame-retardant electrolytes have now reached a point where they are essential for LIB design, which continuously demands high capacity and high power. If a high-safety electrolyte design technology that can respond to this changing technological environment is developed, LIBs can continue to lead as a core technology in eco-friendly mobile science and technology civilization. In this paper, we summarize the electrolyte design technology that can improve the safety of LIBs by reducing the amount of linear carbonate compound with low flash point and increasing the amount of cyclic carbonate with high flash point and relatively low heat of combustion. In this process, we will find the cause of performance deterioration due to the change in electrolyte composition and solve the problem using the Six Sigma method, which is a form in which companies develop technology in the order of Define, Measure/Analyze, Design, and Optimize/Verify. This electrolyte development method is expected to be helpful for researchers who have not yet developed LIBs in companies to understand the process of developing high-safety electrolytes for LIBs.
In Definition step, the correlation between the physical properties of various organic solvents that can be used as electrolytes and the electrochemical stability of LIBs should be analyzed. In this paper, we define the process leading to explosion when an overcharge situation occurs during the use of LIBs, and use this step to find electrolyte conditions that can solve this overcharge problem.
Among the unexpected events that can occur during the operation of LIBs, overcharge is an electrochemical phenomenon that occurs inside the cell that can lead to dangerous events, including explosion. As shown in Figure 1, when the LiMO₂ electrode is overcharged to a potential outside the normal charging range, not only does the electrolyte undergo oxidative decomposition, but also the electrolyte undergoes reduction decomposition due to the excessive lithium precipitated from the graphite electrode. In addition to this electrolyte decomposition, the LiMO₂ structure decomposes due to the excessively dissociated Li+ ions, releasing oxygen, and the environment in which fire occurs inside the cell becomes more severe (Lee et al., 2023). On the other hand, if the reduction of Li+ ions proceeds excessively in the graphite electrode, lithium dendrite may form, penetrating the separator and causing a hard short (Becherer et al., 2022). Unfortunately, these electrochemical phenomena proceed as exothermic reactions, accelerating the temperature rise inside the cell, which can lead to a hard short, where the separator melts, shrinks, or tears, causing direct contact between the overcharged graphite electrode and the LiMO2 electrode. As a result, thermal runaway occurs, which can lead to a chain reaction of explosions in environments where a large number of LIBs are used in confined spaces, such as electric vehicles or renewable energy storage systems. In fact, as the supply of LIBs used for these purposes increases every year, explosion accidents due to overcharge are also increasing rapidly every year (Lai et al., 2022). Therefore, overcharge is one of the most dangerous scenarios in LIB operation, so strong safeguards are installed to mitigate the risk (Chung et al., 2009).
Figure 1. Electrochemical hazards occurring within lithium-ion batteries during overcharge and the associated temperature variations.
However, in order to design an electrolyte for LIBs, both the overall performance and safety as a battery must be considered. High-dielectric compounds promote lithium salt dissociation, while low viscosity can increase ion conductivity. Unfortunately, compounds with high dielectric constants also have high viscosity and melting points, so they must be mixed appropriately with low-dielectric solvents. Maintaining a balance of these characteristics is essential to improving the performance of LIBs. In order to be used as an electrolyte component, compounds with a wide electrochemical stability that can withstand the high charging voltage conditions of LIBs must be selected. Using compounds with high flash points and low combustion heat as electrolyte compositions can protect LIBs more safely from the risk of fire or explosion.
Table 1 lists the common solvents used in LIB electrolytes: diethyl carbonate (DEC), γ-butyrolactone (γ-BL), propylene carbonate (PC), and ethylene carbonate (EC). 1,1,2,2,3,3-Hexafluoro-1-(2,2,3,3-tetrafluoro propoxy) propane (FE) is a type of non-flammable solvent used in the patent (Yamaguchi et al., 2007). EC is notable for its high dielectric constant, aiding in effective salt dissociation, and its high boiling and flash points coupled with low heat of combustion enhance its safety, particularly during overcharging. Despite these benefits, EC’s high melting point and viscosity limit its low-temperature ionic conductivity, making it unsuitable alone for sub-ambient conditions. Therefore, EC is typically mixed with lower melting point and viscosity solvents like DEC, despite DEC’s own high-temperature performance challenges due to its low boiling point and safety risks from its low flash point and high heat of combustion. Blending EC with DEC, typically around 70 vol%, achieves stable performance at standard conditions. However, this mixture can pose safety risks under high temperature or abnormal conditions like overcharging.
Table 1. Comparison of physical and chemical properties of solvents examined as electrolyte components in this paper.
PC and γ-BL offer high dielectric constants, high boiling points above 200°C, and low freezing points below - 40°C, alongside high flash points and low heats of combustion, suggesting that could enhance safety and stability in formulations. However, these solvents have poor electrochemical stability in the SEI formed at the anode, limiting their use under normal cycles (An et al., 2016). Addressing this, flame-retardant electrolytes using PC and γ-BL necessitate SEI design tailored for these solvents’ specific conditions, ensuring durability and high-temperature stability, which are advanced aspects of electrolyte design for LIBs. In this paper, we verify the patented technology regarding a flame-retardant electrolyte developed by replacing flammable solvents such as DEC and DMC with γ-BL, and analyze the operating mechanism of the flame-retardant electrolyte. To this end, we newly applied an electrolyte designed with a composition similar to that proposed in the patent to a single full-cell (SFC) composed of graphite and Li(Ni0.6Co0.2Mn0.2)O2 electrode, and verified how the flame-retardant electrolyte works in LIBs.
The measurement and analysis stages are to find out what problems need to be solved for the flame-retardant solvent selected in the define stage to be applied as an electrolyte component of LIBs. In this paper, the cycle and overcharge tests were used as a process to find technical problems that need to be improved for use as a flame-retardant electrolyte.
When LIBs are subjected to overcharging, the mechanisms that can lead to ignition or explosion vary based on several factors, including the conditions of overcharging, the types of batteries (prismatic, cylindrical, pouch), the structures of active materials, and the compositions of the electrolytes. Figure 2 presents the experimental results of an overcharge and 2.0 C cycle performed on a 4.2 V pouch-type LIBs (LiCoO2-Graphite, 800 mA h), using an electrolyte composed of EC/DEC (3/7, vol%), EC/γ-BL (6/4, vol%), and EC/γ-BL/FE (5/3/2, vol%). The overcharge experiment was conducted by charging the LIBs with the protection circuit removed to 4.2 V at 1.0 C and then overcharging them at 3.0 C (Yamaguchi et al., 2007). As can be seen in the figure, the voltage rapidly increased to 5 V, and the temperature change measured by a sensor attached externally to the battery during this period was almost negligible (step 1). These results suggest that the rapid voltage rise to 5 V was primarily due to overvoltage applied to the LiCoO2 electrode, and that no electrochemical reactions occurred that could induce exothermic events such as electrolyte oxidation or reduction. In step 2, the voltage gradually increased from 5 V to 6 V over 900 s, and the pouched-LIBs expanded without a temperature increase. This phenomenon is thought to be due to electrochemical reactions such as electrolyte decomposition at the graphite or LiCoO2 electrode, and it is thought that the potential increase of the LiCoO2 electrode was suppressed by this faradaic reaction.
Figure 2. (A) 3.0 C overcharge and (B) 1.0 C cycling performed on 4.2 V pouch-type LIBs (LiCoO₂-Graphite, 800 mAh) with electrolytes consisting of EC/DEC (3/7 vol%), EC/γ-BL (6/4 vol%), and EC/γ-BL/FE (5/3/2 vol%).
After reaching 6 V, all LIBs showed a brief voltage drop and temperature increase, but the degree of temperature increase varied depending on the electrolyte condition (step 3). Once the voltage climbed back to 6 V, all LIBs exhibited a rapid surge in voltage, reaching up to 14 V (step 4). At this step, the internal temperature trends showed significant differences based on the electrolyte composition. In particular, LIBs using an electrolyte mixture of EC/DEC (3/7, vol%), which contains 70 vol% of DEC known for its low flash point and high combustion heat, exhibited relatively mild temperature increases up to step 3. However, upon entering Stage 4, the external temperature of these batteries spiked sharply, reaching as high as 400°C. Conversely, LIBs using an electrolyte mixture of EC/γ-BL (6/4, vol%) showed a stable temperature around 120°C throughout both Stage 3 and Stage 4. Additionally, LIBs featuring an electrolyte formulation of EC/γ-BL/FE (5/3/2, vol%), which included 20 vol% of a non-flammable solvent (FE), were noted to maintain a stable temperature around 60°C, indicating no further temperature increase under these conditions.
These experiments, shown in Figure 2A, were conducted using a pouch-type battery, and the following series of events could be observed under overcharge conditions. That is, the fact that the temperature increase rate was not large until reaching 130°C under the EC/DEC (3/7, vol%) condition means that the exothermic reaction due to the oxidation or reduction reaction of the electrolyte at the electrode interface due to overcharge progressed less than under the condition where γ-BL was applied, which relatively suppressed the volatilization of DEC. As a result, it is judged that the temperature inside the cell increases to over 120°C due to the cumulative exothermic reaction caused by overcharging, causing the separator to melt and shrink, and ultimately causing the temperature to rise to 400 C due to the ignition phenomenon caused by the hard short.
However, in cases where γ-BL, which has a similar heat of combustion to DEC but a flash point of 99°C, was used, the voltage increased to 6 V, and the temperature rose to 120°C, leading only to cell swelling without progressing to thermal runaway due to hard short. This outcome suggests that the significantly lower heat of combustion of γ-BL compared to DEC prevented the melting of the polyethylene (PE) separator, which has a melting temperature of 134°C, thus not allowing for the occurrence of hard short. On the other hand, when a non-flammable FE solvent was applied, it was observed that the temperature did not exceed 60°C. This result suggests that the pouch expanded and ruptured during overcharge up to 6 V because the boiling point of FE is 93°C, which is considerably lower than that of γ-BL or EC, and finally reached a stable state without further temperature increase.
Figure 2B illustrates the 1.0 C cycle performance of a pouch-type full cell with flame-retardant components, γ-BL and FE. It is observed that the lifespan performance significantly deteriorates from the initial cycles when a flame-retardant electrolyte was applied. When the lifespan performance declines sharply from the outset following a change in electrolyte composition, it is highly likely that the SEI formed at the interface of graphite electrode during initial charging is in an unstable state, or alternatively, that the ionic conductivity of the electrolyte has decreased due to compositional changes. Analysis of the ionic conductivity of these compositions revealed that when γ-BL was used instead of DEC, the ionic conductivity increased by 3 mS/cm. Meanwhile, as can be confirmed in Supplementary Figure S1B; Figure 3B, a notable difference was observed in the electrolyte decomposition behavior related to SEI formation during the initial charge process. Ultimately, it is concluded that the degradation of the cycle performance of LIBs using γ-BL is due to the instability of the SEI formed at the graphite electrode interface.
Figure 3. (A) Initial charge-discharge curves of LIBs composed of Graphite and Li(Ni₀.₆Co₀.₂Mn₀.₂)O₂ electrodes using four different electrolytes designed in Table 2, and (B) dQ/dV analysis of their charge curves.
In the composition of 1.0 M LiPF6 in EC/DEC (3/7, vol%), SEI is known to be formed by the decomposition of EC-solvated supramolecular structure,
According to the research results on the SEI structure formed at the graphite interface of LIBs, it is analyzed that the inorganic layer and organic layer are formed mixedly with a thickness of several tens of nm by the reduction of the electrolyte components distributed at the electrode interface (Peled and Menkin, 2017). Among the organic solvents currently used as electrolyte components of LIBs, FEC is a substance that can be reduced before EC if it does not cause a special behavior due to the solvation structure with lithium salt in the electrolyte because fluorine, which has high electronegativity, is substituted for EC (Wang et al., 2018). Therefore, FEC can be a candidate substance worth sufficiently verifying as a SEI modification composition formed in a flame-retardant electrolyte of γ-BL composition. Meanwhile, the electrochemical decomposition behavior of the electrolyte for forming SEI can be changed depending on the conditions of use of the electrolyte salt. That is, when LiBF4, which has a higher ionic bonding strength than LiPF6, was added to 1.0 M LiPF6 of EC/DEC (3/7, vol%), the reduction-decomposition voltage of the electrolyte gradually shifted to a higher potential, as shown in Supplementary Figure S2B. Since both the electrolyte salt and the components of the electrolyte are involved in SEI formation, appropriate combinations of two or more electrolyte salts can facilitate the development of an SEI suitable for flame-retardant electrolytes (Takeuchi et al., 2009). Another experimental result showed that the addition of salts having larger electronic spatial extents (ESE) than
In Design step, the SEI design conditions necessary for applying γ-BL as a flame-retardant electrolyte component are found from the meaningful experimental results performed in the Measurement and Analysis. In this paper, the SEI forming sources designed in Table 3 were applied to a 4.45 V single full cell composed of graphite and Li(Ni0.6Co0.2Mn0.2)O2 electrodes, and the effects of the differences in SEI formation components on the overall performance of the LIBs were compared and analyzed with the related patents.
In order for γ-BL to properly implement its effect as a flame-retardant electrolyte component, a systematic analysis of the electrochemical effect of the SEI formed by FEC and LiBF4 is necessary, as confirmed in the Measure and Analyze step. Table 2 is an experimental plan designed to find the SEI conditions suitable for the electrolyte conditions of 1.0 M LiPF6 in EC/DEC/γ-BL (3/2/5, vol%). The electrolyte components used in the verification experiments were supplied as follows. The main components of the liquid electrolyte, such as LiPF6, LiBF4, EC, and DEC, were purchased from ENCHEM Co., a Korean electrolyte manufacturer, and the new electrolyte components, γ-BL and FEC, were purchased from DAEJUNG Co., Korea and Thermo Fisher Scientific Co., United States, respectively. Also, the charging voltage was set to 4.45 V, and the capacity varied depending on the electrolyte composition, with the relevant data presented in Figure 3. Additionally, the detailed specifications of the electrode and separator can be found in Supplementary Table S4. In order to pursue both convenience and reproducibility of the experiment, the concentration of LiPF6, the main electrolyte salt, was changed from 1.3 mol/L to 1.0 mol/L, the concentration of FEC from 5 wt% to 3 wt%, and the concentration of LiBF4 from 0.03 mol/L to 3 wt% in the composition suggested in the related patent (Yamaguchi et al., 2009). However, there was no significant change in the logical flow of the experimental results.
Table 2. Experimental design for SEI formation compatible with flame-retardant electrolytes using γ-BL, based on the patent.
DOE 1 is a reference electrolyte composed only of EC, DEC, and LiPF6, which are commonly used as electrolyte components for LIBs. DOE 2 is a composition that applied 50 vol% γ-BL as a flame-retardant component instead of DEC in DOE 1. As analyzed in the Measure and Analyze steps, it is a composition that satisfies the overcharge performance of LIBs but needs improvement in cycle performance. DOE 3 is a composition that used FEC as an electrolyte additive, which can be reduced more easily to form SEI than EC or γ-BL, which are the main components of flame-retardant electrolytes. Finally, DOE 4 incorporates LiBF4, another main component deeply involved in SEI formation, into DOE 3 to analyze the correlation between the difference in SEI formation mechanism at the graphite electrode interface and the performance implementation as a flame-retardant electrolyte.
Figure 3 shows the initial charge-discharge performance and dQ/dV analysis for the charge curves of the LIBs composed of Graphite-Li(Ni0.6Co0.2Mn0.2)O2 not only did swelling occur under compositions designed in Table 2. This is a common interpretation method used to analyze the difference in SEI formation process during the charge process depending on the electrolyte composition. These experimental results are very similar to the experimental results of the related patent data presented in Supplementary Figure S1. That is, the experimental results show electrochemical behaviors that are almost similar to the SEI patterns formed in LIBs composed of Graphite-LiCoO2, which means that there is no great difficulty in conducting electrochemical supplementary experiments using the new battery system. Additionally, this dQ/dV data is reinforced by the EIS data shown in Figure 4, providing further insights into SEI characteristics. In the case of DOE 1, the decomposition peak of EC solvated system,
Figure 4. (A) EIS spectra of LIBs with Graphite and Li(Ni₀.₆Co₀.₂Mn₀.₂) electrodes using four electrolytes listed in Table 2, and (B) magnified view of Rb and Rf regions.
Table 3 shows the results of experiments related to the compositions of DOE 1 ∼ 4 extracted from USP 7491471B2, comparing and analyzing the overall performance of LIBs. The parts highlighted in red are areas requiring improvement under each electrolyte condition. When examining the battery performances according to each designed electrolyte, DOE 1 (corresponding to No. 1) with 70 vol% DEC applied showed the best result in terms of battery performance at room temperature (2.0 C discharge, 1.0 C cycle). However, not only did swelling occur under the 90°C protection condition, but all cells were judged unsuitable for explosion even when evaluated under the charging state, which is a mild overcharge experimental condition. DOE 2 (corresponding to No. 2) incorporating 50 vol% γ-BL for flame retardancy showed a slight advantage only in the overcharge test compared to No. 1, but failed to demonstrate adequate performance as a LIB overall. Considering this result and the clear difference in the dQ/dV data in DOE 1, it can be inferred that the reduction of only γ-BL, which is first reduced at the graphite electrode interface to form an electron-passive layer in the composition of DOE 2, is an undesirable electrochemical behavior for LIBs.
Table 3. Comparative analysis of overall performances of LIBs related to which the compositions of DOE 1 ∼ 4, summarized from the related patent (Yamaguchi et al., 2009).
In DOE 3 (corresponding to No. 3), where the SEI of the γ-BL-based electrolyte was modified with FEC, room-temperature performance was similar to that of the reference electrolyte, No. 1. However, despite the application of high-boiling-point γ-BL, it performed worse than No.1 in high-temperature storage tests. To analyze the cause of this, the experimental results in Table 2 limited to the high-temperature storage performance were analyzed. As a result, it was found that the improved stability at high temperature was more affected by the suitability of the SEI design for the γ-BL composition than by the use of the high-boiling-point γ-BL. Specifically, in the electrolyte composition of No. 1, the high-temperature storage performance of No. 2, which reduced the low boiling point DEC from 70 vol% to 20 vol% and applied 50 vol% γ-BL, was actually deteriorated. This suggests that the difference is likely due to the difference of high-temperature durability of the SEI formed by EC and γ-BL. Furthermore, the high-temperature performance of electrolyte compositions with FEC, as reported in experimental results (Example 6 in Supplementary Table S3), showed that No.3 was the most vulnerable in the 90°C storage test. Considering that the boiling point of FEC is 212°C, it is evident that the thermal durability of the SEI formed by FEC is low. Many papers have reported experimental results that the thermal characteristics of the electrolyte applied with FEC are poor (Cho et al., 2010). However, since the positive electrode used in this experiment is 4.2 V LiCoO2, and FEC was added less than 3% as an SEI forming agent, it is judged that the reason why the conditions of DOE 3 are weak in high-temperature characteristics is due to the weak thermal stability of SEI rather than the oxidation of FEC. The weakness at high temperatures caused by FEC was almost perfectly suppressed by the addition of a small amount of LiBF4, which prevented the batteries from swelling during high-temperature storage. It can be inferred that this is due to the improved durability of the SEI modified by LiBF4 at 90°C.
In overcharge performance of Table 3, the use of high flashpoint γ-BL improved performance compared to No. 1, but similar to No. 2, its effectiveness diminished under harsh conditions like overcharge from a discharged state. Finally, DOE 4 (corresponding to No. 4), where the SEI in the flame-retardant γ-BL-based composition was modified with FEC and LiBF4, showed only capacity reduction at the end of the cycle performance. It experienced almost no swelling or capacity loss under high-temperature storage conditions, and remarkably, achieved 100% safety without ignition even during the severe overcharge test even from a discharged state.
To analyze such differences in the thermal behavior of SEI, the discharged state cells were disassembled in a dry room to separate the graphite electrodes, and electrolytic components such as electrolyte salt, EC, and γ-BL were extracted by immersing them in DEC for more than 12 h. Afterwards, the thermal behavior of the SEI components was analyzed through a differential scanning calorimetry (DSC) analysis of the graphite electrodes dried under reduced pressure.
As shown in Figure 5, the graphite electrode that was immersed in the electrolyte and dried without charging and discharging did not show any endothermic behavior in the range of 100°C–150°C, whereas different endothermic peaks were observed under the four experimental conditions (Jung, 2008). In addition, these endothermic peaks showed distinct differences in temperature and shape of the endothermic peaks observed under each condition, as in the dQ/dV behavior observed in Figure 3B. These results suggest that these endothermic peaks are due to thermal behaviors related to SEI melting (Cao et al., 2013).
Figure 5. DSC comparison of graphite electrodes (A) before and (B) after storing LIBs at 90°C for 4 h in discharged state. Using 800 mAh LIBs composed of LiCoO2 and Graphite (Jung, 2008).
First, let’s look at the results analyzed before storing at 90°C. The endothermic behavior of SEI formed by γ-BL (No. 2 corresponding to DOE 2) was analyzed in a non-sharp form over a wider temperature range, unlike under EC or FEC conditions. More interesting is the comparison of the endothermic energy required for SEI melting. It was found that SEI formed by EC (DOE 1) and γ-BL (DOE 2) required 15 kJ/g, while SEI formed by FEC (DOE 3 and DOE 4) required only 7–8 kJ/g. This difference in endothermic energy is not due to the difference in the thermal stability of SEI, but rather to the difference in the chemical or physical structure, thickness, and base of the materials composing SEI, so it can be judged to be due to the difference in the SEI formation process.
Meanwhile, the DSC analysis conducted after 4 h of storage at 90°C yielded even more intriguing findings. Primarily, it was noted that the melting form of the SEI, except for that formed by FEC + LiBF4 (No. 4 corresponding to DOE 4), was significantly altered after the 90°C storage. Additionally, the change in exothermic energy after high-temperature storage was analyzed as follows: 15 kJ/g to 142 kJ/g (9.5 times, No. 1), 15 kJ/g to 93 kJ/g (6.2 times, No. 2), 7 kJ/g to unmeasurable (No. 3), and 8 kJ/g to 55 kJ/g (6.9 times, No. 4). The increase in calorific value after high-temperature storage is attributed to the accumulation of additional reduction decomposition products of the electrolyte due to SEI melting during the storage period. Particularly, as could be somewhat inferred from the 90°C storage experiments, the SEI formed under No. 3 with FEC was found to have very weak high-temperature properties. The melting pattern of the SEI formed under No. 4 conditions showed almost no deformation even after high-temperature storage, indicating superior high-temperature durability compared to other conditions.
The experimental results from this Design step reveal that merely increasing the boiling and flash points of the electrolyte does not suffice as a technology to ensure the safety of batteries under conditions such as high-temperature storage or overcharging. By constructing an SEI with enhanced durability while maintaining elevated boiling and flash points of the electrolyte, it was possible not only to suppress the swelling of the battery at high temperatures but also to keep the battery safe under extreme overcharging conditions. These results imply that in order to design a flame-retardant electrolyte, it is necessary to consider not only the high-temperature safety and salt resistance of the electrolyte components, but also the design of an SEI that is durable even under harsh conditions. However, as summarized in Table 3, the condition of No. 4 (corresponding to DOE 4) still has issues to be resolved in the 1.0 C cycle performance, which was not a problem in No. 1 (DOE 1). To solve this issue, a more detailed electrolyte design is required to form an optimal SEI for the flame-retardant electrolyte containing γ-BL.
In this stage, the electrolyte composition confirmed in the design stage should be applied to the pilot line-level manufacturing process to find and optimize items that may be problematic under mass production conditions. In this process, more effort should be put into improving the manufacturing process rather than researching electrolyte composition or material development. This paper briefly describes the process performed to solve the cycle performance problem that remained an insufficient part in the development of flame-retardant electrolyte using γ-BL.
In order to optimize the cycle performance of LIBs using γ-BL-based flame-retardant electrolytes, it is necessary to analyze and optimize the effects of each process that can affect SEI formation in the battery manufacturing process. In other words, the optimal conditions for the mixing process of FEC and LiBF4 for the flame-retardant electrolyte applied with γ-BL, which has a different dielectric constant from DEC, the impregnation process of the flame-retardant electrolyte into the coating electrode such as graphite or LiMO2, and the initial charging process that affects the electrochemical reaction of the impregnated electrolyte component should be pursued through joint research with process researchers. An experimental plan is needed to determine the optimal contents of FEC and LiBF4, which are SEI-forming electrolyte additives, after applying the electrolyte composition EC/γ-BL/DEC (3/5/2, vol%) tested in the design stage to the selected process conditions. Figure 6A is a partial example of an experimental plan designed for SEI optimization required for the DOE 4 conditions selected as the γ-BL-based flame retardant electrolyte conditions. As a result, as confirmed in the main effect analysis summarized in Figures 6B, C, applying 3.0 wt% FEC and 0.15 wt% LiBF4 was interpreted as being advantageous for the cycle life. On the other hand, it was analyzed that applying an FEC content of less than 3.0 wt% was a more effective composition for evaluating high-temperature storage performance.
Figure 6. (A) Experimental plan for designing SEI suitable for γ-BL-based flame retardant electrolyte and analysis of main effects of electrolyte additives, (B) FEC and (C) LiBF4, affecting cycle life.
Through this process, the optimized SEI composition for the flame-retardant electrolyte with γ-BL applied was fixed, and conversely, the performance of the designed SEI was verified by applying the electrolyte components EC, γ-BL, and DEC under the conditions as shown in Figure 7A. That is, the liquid components of the electrolyte were designed in the ranges of 30–15 vol% EC, 55–15 vol% DEC, and 30–70 vol% γ-BL, respectively, and the SEI forming components were designed by fixing the conditions of 3.0 wt% FEC and 0.1 wt% LiBF4 determined by the main effect analysis. As a result, as can be confirmed from the related patent data, it was shown that the discharge capacity was uniformly evaluated at 0.2 C, 0.5 C, 1.0 C, and 2.0 C conditions regardless of the composition ratio of the liquid components of the electrolyte. Even in the 90°C 4-hour storage test, which showed the largest deviation at the design stage, less than 1% expansion was observed in all compositions. The charge-discharge performance measured after the storage test also showed a recovery capacity of more than 95%. In addition, as verified in Figure 7B, the cycle performance, which remained an unresolved issue in DOE 4, was stable for more than 400 cycles in all compositions.
Figure 7. (A) Experimental plan for various ratios of electrolyte components under optimized SEI condition in Figure 6 and (B) comparison of their 1.0 C cycle performance.
This study successfully developed a flame-retardant electrolyte for LIBs using the DMADOV methodology, focusing on enhancing safety and performance critical for electric vehicles and renewable energy storage systems. The key findings of this research are as follows:
Selection of Organic Solvent: The γ-BL solvent was identified as an effective choice, significantly reducing flammability risks compared to conventional electrolytes and improving electrochemical stability. The importance of suitable solvent selection was emphasized for enhancing electrolyte safety.
SEI Formation Mechanism: The study explored the SEI formation mechanisms using FEC and LiBF4 as SEI-forming agents. This research highlighted the critical role of SEI formation in improving ion conductivity and overall battery efficiency.
Thermal Stability: Testing under overcharging scenarios demonstrated that the optimized γ-BL-based electrolyte exhibited enhanced thermal stability, significantly increasing safety during battery operation.
Performance Metrics: The developed flame-retardant electrolyte showed overall performance improvements compared to conventional electrolytes, indicating its potential for further applications in high-performance electrolyte formulations.
In conclusion, this research provides substantial evidence for the applicability of γ-BL-based flame-retardant electrolytes in enhancing the safety and performance of LIBs, offering valuable insights for future developments in high-performance electrolyte designs.
The original contributions presented in the study are included in the article/Supplementary Material, further inquiries can be directed to the corresponding author.
BL: Data curation, Formal Analysis, Writing–original draft. CJ: Conceptualization, Formal Analysis, Investigation, Project administration, Resources, Supervision, Validation, Writing–original draft, Writing–review and editing.
The author(s) declare that financial support was received for the research, authorship, and/or publication of this article. This work was supported by the 2024 Research Fund of the University of Seoul.
The authors declare that the research was conducted in the absence of any commercial or financial relationships that could be construed as a potential conflict of interest.
The author(s) declare that no Generative AI was used in the creation of this manuscript.
All claims expressed in this article are solely those of the authors and do not necessarily represent those of their affiliated organizations, or those of the publisher, the editors and the reviewers. Any product that may be evaluated in this article, or claim that may be made by its manufacturer, is not guaranteed or endorsed by the publisher.
The Supplementary Material for this article can be found online at: https://www.frontiersin.org/articles/10.3389/fenrg.2024.1508471/full#supplementary-material
An, S. J., Li, J., Daniel, C., Mohanty, D., Nagpure, S., and Wood, I. I. I. D. L. (2016). The state of understanding of the lithium-ion-battery graphite solid electrolyte interphase (SEI) and its relationship to formation cycling. Carbon 105, 52–76. doi:10.1016/j.carbon.2016.04.008
Becherer, J., Kramer, D., and Monig, R. (2022). The growth mechanism of lithium dendrites and its coupling to mechanical stress. J. Mater. Chem. A 10, 5530–5539. doi:10.1039/d1ta10920k
Cao, X., Li, Y., Li, X., Zheng, J., Gao, J., Gao, Y., et al. (2013). Novel phosphamide additive to improve thermal stability of solid electrolyte interphase on graphite anode in lithium-ion batteries. ACS Appl. Mater. Interfaces. 5, 11494–11497. doi:10.1021/am4024884
Chen, S., Wang, Y., Li, Z., Feng, Y., and Feng, W. (2024). A grafted flame-retardant gel polymer electrolyte stabilizing lithium metal for high-safety lithium metal batteries. J. Mater. Chem. A 12, 28296–28306. doi:10.1039/d4ta04343j
Cho, I., Kim, S., Shin, S., and Choi, N. (2010). Effect of SEI on capacity losses of spinel lithium manganese oxide/graphite batteries stored at 60°C. Electrochem. Solid-State Lett. 13 (11), A168–A172. doi:10.1149/1.3481711
Chung, Y. S., Yoo, S. H., and Kim, C. K. (2009). Enhancement of meltdown temperature of the polyethylene lithium-ion battery separator via surface coating with polymers having high thermal resistance. Ind. Eng. Chem. Res. 48 (9), 4346–4351. doi:10.1021/ie900096z
Grey, C. P., and Hall, D. S. (2020). Prospects for lithium-ion batteries and beyond—a 2030 vision. Nat. Commun. 11, 6279. doi:10.1038/s41467-020-19991-4
Huang, C., Li, L., Yang, P., and Chen, J. (2024a). Tris(2,2,2-trifluoroethyl) phosphite (TTFP) as a flame-retardant co-solvent to improve the safety and electrochemical performances of lithium-ion batteries. New J. Chem. 48, 17978–17989. doi:10.1039/d4nj03428g
Huang, Y., Cao, B., Geng, Z., and Li, H. (2024b). Advanced electrolytes for rechargeable lithium metal batteries with high safety and cycling stability. Acc. Mater. Res. 5, 184–193. doi:10.1021/accountsmr.3c00232
Jung, C. (2008). Electrochemical absorption effect of BF4 anion salt on SEI layer formation. Solid State Ionics 179, 1717–1720. doi:10.1016/j.ssi.2008.03.026
Lai, X., Yao, J., Jin, C., Feng, X., Wang, H., Xu, C., et al. (2022). A review of lithium-ion battery failure hazards: test standards, accident analysis, and safety suggestions. Batteries 8, 248. doi:10.3390/batteries8110248
Lee, D. H., Gong, M., Lee, E., and Seo, D. H. (2023). Oxygen redox in LiNiO2 cathodes. Joule 7, 1408–1411. doi:10.1016/j.joule.2023.06.023
Li, M., Zhao, N., Wang, C., Zou, Y., Chen, X., and Mei, Y. (2025). Improving thermal stability and electrochemical performance of polymer solid electrolyte membranes with a novel TiO2@PA-APP composite additive. Colloids Surfaces A Physicochem. Eng. Aspects 705, 135640. doi:10.1016/j.colsurfa.2024.135640
Li, W., Crompton, K. R., and Ostanek, J. K. (2022). Comparison of current interrupt device and vent design for 18650 format lithium-ion battery caps: new findings. J. Energy Storage 46, 103841. doi:10.1016/j.est.2021.103841
Mu, X., Ding, H., Wu, Y., Hu, H., and Yu, B. (2023). Nonflammable liquid electrolytes for safe lithium batteries. Small Struct. 4, 2300179. doi:10.1002/sstr.202300179
Neef, C., and Thielmann, A. (2023). Lithium-ion battery roadmap – industrialization perspectives toward 2030, chap. 2 applications and requirements. Karlsruhe: Fraunhofer Institute for Systems and Innovation Research ISI. doi:10.24406/publica-2153
Ouyang, D., Chen, M., Huang, Q., Weng, J., Wang, Z., and Wang, J. (2019). A review on the thermal hazards of the lithium-ion battery and the corresponding countermeasures. Appl. Sci. 9, 2483. doi:10.3390/app9122483
Peled, E., and Menkin, S. (2017). Review—SEI: past, present and future. J. Electrochem. Soc. 164 (7), A1703–A1719. doi:10.1149/2.1441707jes
Takeuchi, M., Kameda, Y., Umebayashi, Y., Ogawa, S., Sonoda, T., Ishiguro, S. I., et al. (2009). Ion–ion interactions of LiPF6 and LiBF4 in propylene carbonate solutions. J. Mol. Liq. 148, 99–108. doi:10.1016/j.molliq.2009.07.003
Wang, A., Kadam, S., Li, H., Shi, S., and Qi, Y. (2018). Review on modeling of the anode solid electrolyte interphase (SEI) for lithium-ion batteries. npj Comput. Mater. 4, 15. doi:10.1038/s41524-018-0064-0
Wang, J. L., Lin, F. J., Jia, H., Yang, J., Monroe, C. W., and NuLi, Y. (2014). Toward a safe lithium-sulfur battery with a flame-inhibiting electrolyte and a sulfur-based composite cathode. Angewantedte Chemie-International Ed., 53 10099–10104. doi:10.1002/anie.202405157
Xu, F., Lee, C. H., Koo, C. M., and Jung, C. (2014). Effect of electronic spatial extents (ESE) of ions on overpotential of lithium ion capacitors. Electrochimica Acta 115, 234–238. doi:10.1016/j.electacta.2013.10.175
Yamaguchi, T., Shimizu, R., Chung, H., Jung, C., Noh, H., Song, E., et al. (2009). Electrolyte for lithium secondary battery and lithium secondary battery comprising same, US patent No. 7491471 B2
Keywords: frame-retardant electrolyte, butyrolactone, SEI, FEC, LIB
Citation: Lee B and Jung C (2025) A corporate approach to enhancing lithium-ion battery safety through flame-retardant electrolyte development. Front. Energy Res. 12:1508471. doi: 10.3389/fenrg.2024.1508471
Received: 09 October 2024; Accepted: 29 November 2024;
Published: 20 January 2025.
Edited by:
Zhong Ma, University of Shanghai for Science and Technology, ChinaReviewed by:
Guillermo González, University of Chile, ChileCopyright © 2025 Lee and Jung. This is an open-access article distributed under the terms of the Creative Commons Attribution License (CC BY). The use, distribution or reproduction in other forums is permitted, provided the original author(s) and the copyright owner(s) are credited and that the original publication in this journal is cited, in accordance with accepted academic practice. No use, distribution or reproduction is permitted which does not comply with these terms.
*Correspondence: Cheolsoo Jung, Y3NqdW5nQHVvcy5hYy5rcg==
Disclaimer: All claims expressed in this article are solely those of the authors and do not necessarily represent those of their affiliated organizations, or those of the publisher, the editors and the reviewers. Any product that may be evaluated in this article or claim that may be made by its manufacturer is not guaranteed or endorsed by the publisher.
Research integrity at Frontiers
Learn more about the work of our research integrity team to safeguard the quality of each article we publish.