- Argonne National Laboratory, Lemont, IL, United States
Hydrogen is a zero-carbon energy carrier with potential to decarbonize industrial and transportation sectors, but its life-cycle greenhouse gas (GHG) emissions depend on its energy supply chain and carbon management measures (e.g., carbon capture and storage). Global support for clean hydrogen production and use has recently intensified. In the United States, Congress passed several laws that incentivize the production and use of renewable and low-carbon hydrogen, such as the Bipartisan Infrastructure Law (BIL) in 2021 and the Inflation Reduction Act (IRA) in 2022, which provides tax credits of up to $3/kg depending on the carbon intensity of the produced hydrogen. A comprehensive life-cycle accounting of GHG emissions associated with hydrogen production is needed to determine the carbon intensity of hydrogen throughout its value chain. In the United States, Argonne’s R&D GREET® (Greenhouse Gases, Regulated emissions, and Energy use in Technologies) model has been widely used for hydrogen carbon intensity calculations. This paper describes the major hydrogen technology pathways considered in the United States and provides data sources and carbon intensity results for each of the hydrogen production and delivery pathways using consistent system boundaries and most recent technology performance and supply chain data.
1 Introduction
Hydrogen is a zero-carbon energy carrier commonly used in the production of chemicals and fuels. Depending on the energy source and technology used for hydrogen production and delivery, there can be life-cycle greenhouse gas (GHG) emissions associated with hydrogen production and use. Clean energy sources and carbon management measures (e.g., carbon capture and storage) can be deployed to provide the largest reductions in GHG emissions associated hydrogen production and use.
Interest has grown globally in the economic production of clean hydrogen to replace the current carbon-intensive hydrogen production via reforming of fossil natural gas. In particular, the United States (U.S.) Congress passed several laws that incentivize the production and use of renewable and low-carbon hydrogen. The Bipartisan Infrastructure Law (BIL) passed in 2021 provided $9.5B to incentivize the deployment of clean hydrogen hubs in various parts of the United States and the development of electrolyzer technologies. To qualify for the BIL incentives, the produced hydrogen must meet specific GHG emissions standards on a life-cycle basis. Seven hydrogen hubs were awarded in 2023 in different regions of the United States. In 2022, Congress passed the Inflation Reduction Act (IRA), which provides tax credits of up to $3/kg depending on the carbon intensity of the produced hydrogen.
Due to the impact of hydrogen carbon intensity (CI) on the end use applications of hydrogen (e.g., fuel cell vehicles, ammonia, synthetic fuels and chemicals, metal reduction, etc.), many authors have examined the CI of hydrogen produced by various methods. According to the U.S. Department of Energy, steam methane reforming (SMR) of natural gas (NG) has been one of the most common methods of hydrogen production in the United States in 2024 (U.S. DOE undated). However, the CI of hydrogen produced via SMR is high. A recent study by Henriksen et al. (2024) reported life-cycle emissions of 10.6 kgCO2e/kgH2 while Zang et al. (2024) reported 9.9 kgCO2e/kgH2 including displacement credits due to the export of excess steam produced. Sun et al. (2019) studied SMR facility level GHG emissions and determined a U.S. national average of 9.3 kgCO2e/kgH2. In a report published by the National Energy Technology Laboratory (NETL) which modeled an SMR facility, they determined that the CI of hydrogen produced to be 12.4 kgCO2e/kgH2, which can be reduced to 10.2 kgCO2e/kgH2 if the produced steam was exported (Lewis et al., 2022). Khojasteh Salkuyeh et al. (2017) determined that hydrogen produced by SMR would have emissions of 11.5 kgCO2e/kgH2, which is supported by other authors determined that the life-cycle emissions of hydrogen produced by steam methane reforming of natural gas were 11.9 kgCO2e/kgH2, including embodied emissions from capital expenditure (CapEx) (Cetinkaya et al., 2012; Spath and Mann, 2000). Other studies report slightly lower emission values of between 10.4 CO2e/kgH2 (Susmozas et al., 2013). To reduce the CI of hydrogen produced from NG SMR, carbon capture and storage (CCS) systems were implemented. This approach resulted in a sharp reduction of GHG emissions to between 3.4 and 3.6 kgCO2e/kgH2 (Khojasteh Salkuyeh et al., 2017; Henriksen et al., 2024; Zang et al., 2024; Dufour et al., 2010).
Due to the high CI of hydrogen produced from NG SMR without CCS, many hydrogen production technologies have been studied as possible alternatives. One such method is autothermal reforming (ATR) of natural gas. A literature review determined that many authors reported GHG emissions from ATR with CCS in the range of 3.3–3.7 kgCO2e/kgH2 (Henriksen et al., 2024; Zang et al., 2024), although emissions as high as 3.9 kgCO2e/kgH2 have been reported (Hajjaji et al., 2013). In the absence of CCS, ATR GHG emissions increase to between 10.8 and 11.0 kgCO2e/kgH2 (Hajjaji et al., 2013; Oni et al., 2022). Gasification of carbonaceous material such as coal or biomass is another method of hydrogen production. Authors have reported emissions from coal gasification ranging between 11.6 and 20 kgCO2e/kgH2 without CCS (Cetinkaya et al., 2012; Henriksen et al., 2024; Verma and Kumar 2015), although emissions can reach as high as 25.3 kgCO2/kgH2 if lignite is used (Burmistrz et al., 2016). With the inclusion of CCS, Henriksen et al. (2024) determined that the CI of hydrogen decreases to 3.9 kgCO2e/kgH2, while Burmistrz et al. (2016) noted GHG emissions ranging between 4.1 and 7.1 kgCO2e/kgH2. To further reduce the CI of hydrogen produced via gasification, biomass may be used in place of coal as it is a biogenic source of carbon. However, reported emissions vary widely due to differences in the carbon content of the biomass gasified (Henriksen et al., 2024; Moreno and Dufour, 2013). Susmozas et al., 2013 investigated the CI of hydrogen produced from poplar gasification and reported GHG emissions of 0.4 kgCO2e/kgH2. With CCS, this value decreases to −14.6 kgCO2e/kgH2 (Susmozas et al., 2016). In contrast, Henriksen et al. (2024) reported GHG emissions of 5.3 kgCO2e/kgH2 without CCS and −15 kgCO2e/kgH2 when CCS is included. Kalinci et al. (2012) reported emissions of 8.5 kgCO2e/kgH2 using pinewood, while Li et al. (2020) calculated GHG emissions of 5.4 kgCO2e/kgH2 for hydrogen produced using straw.
Finally, the electrolysis of water presents the possibility for low CI hydrogen production should renewable electricity, such as wind, solar, hydro, or nuclear electricity be used. Low-temperature electrolysis (LTE) is typical for proton exchange membrane (PEM) and alkaline electrolyzer technologies, while high-temperature electrolysis (HTE) is typical for solid-oxide electrolyzer cell (SOEC) technology. While nuclear high-temperature gas cooled reactors (HTGR) have supply chain upstream emissions, they can produce hydrogen with CI as low as 0.4 kgCO2e/kgH2 (Giraldi et al., 2015). Karaca et al. (2020) reported similar values of 0.4 and 0.5 kgCO2e/kgH2 for electrolysis using boiling water reactors (BWR) and pressurized water reactors (PWR), respectively. These values are also supported by Bicer and Dincer (2017), whose study indicated GHG emissions between 0.5 and 0.6 kgCO2e/kgH2 for hydrogen produced by high-temperature electrolysis and electrolysis, respectively (Bicer and Dincer, 2017).
CapEx-embodied emissions of clean electricity contribute significantly to the CI of hydrogen produced via electrolysis. Iyer et al. (2024) reported emissions as high as 2.4 kgCO2e/kgH2 for electrolysis using solar power and 0.5 kgCO2e/kgH2 when nuclear power from LWRs is used. These results are supported by Gan et al. (2024) who reported GHG emissions of 2.1, 0.6, 0.4, and 0.3 kgCO2e/kgH2 for water electrolysis using solar, wind, hydro, and nuclear power, respectively. Henriksen et al. (2024) further distinguishes between the type of electrolysis methods, noting emissions of 1.8 and 2.2 kgCO2e/kgH2 for PEM and SOEC, respectively, when wind electricity is used, which increases to 2.8 and 2.9 kgCO2e/kgH2 when solar energy is used. Palmer et al. (2021) reported a similar CI of hydrogen produced via electrolysis using solar power of 2.3 kgCO2e/kgH2. Cetinkaya et al. (2012) reported GHG emissions of 1.0 and 2.4 kgCO2e/kgH2 for hydrogen produced by using wind and solar power, respectively.
As can be seen, many LCA studies of hydrogen have been carried out over a span of multiple years, covering different system boundaries, and from the perspective of different countries. A comprehensive life-cycle accounting of GHG emissions associated with hydrogen production is needed to determine the carbon intensity of hydrogen throughout its value chain. This paper aims to provide readers with the information necessary to understand hydrogen production in the United States and the life-cycle emissions associated with it using consistent system boundaries and most recent technology performance and supply chain data. In the United States, Argonne’s R&D GREET® (Greenhouse Gases, Regulated emissions, and Energy use in Technologies) model has been widely used for hydrogen carbon intensity calculations. R&D GREET provides in-depth life-cycle simulations for a variety of energy and chemical products, including hydrogen technologies. This paper describes the major hydrogen technology pathways considered in the United States and provides data sources and carbon intensity results for each of the hydrogen production pathways.
2 Hydrogen production technology pathways
In this section, we discuss hydrogen production technologies, their necessary process inputs, and the operating conditions in R&D GREET, 2023. We also highlight important parameters that have a significant impact on the well-to-gate (WTG) CI of hydrogen production and any accompanying data sources. Detailed data for each pathway can be found in the Supplementary Material. The co-product allocation method in GREET follows the ISO 14067 protocol, with system expansion and substitution method applied where feasible, and allocation based on physical attributes (e.g., by energy or mass) is otherwise applied.
2.1 Natural gas and biogas reforming
This section discusses natural gas or biogas reforming technologies for hydrogen production. Because fugitive methane emissions from the natural gas supply chain significantly impact the CI of hydrogen, we provide a detailed discussion on upstream burdens of NG, from recovery through transmission to the hydrogen plant. Steam methane reforming has been the most common technology for hydrogen production. Because of the high CI of hydrogen produced via reforming of natural gas, CCS technology is of interest and is discussed in this section. ATR is of particular interest due to its favorable application with CCS.
2.1.1 Upstream burdens for natural gas
Upstream GHG emissions associated with the NG supply chain play a critical role in the CI of hydrogen produced via methane reforming technology pathways. Such emissions cannot be mitigated by CCS at hydrogen production facilities. Fugitive methane emissions and combustion CO2 emissions occur within activities associated with NG recovery, processing, and transportation to the hydrogen production plant.
Methane-related emissions can be measured by using bottom-up field measurements and top-down measurements from aircraft, satellites, and weather stations (Rutherford et al., 2021). The US EPA Greenhouse Gas Inventory (GHGI) uses data from bottom-up measurements. Other studies suggested that GHGI undercounts emissions (Rutherford et al., 2021; Alvarez et al., 2018). R&D GREET, 2023 implements a hybrid bottom-up and top-down approach to estimate methane emissions throughout NG supply chain (Burnham, 2023). R&D GREET uses average NG transmission pipeline distance from the field to the end-use of 680 miles, which is based on national U.S. ton-miles of natural gas freight via pipeline in 2009, as reported by The U.S. Department of Transportation’s Bureau of Transportation Statistics (BTS), special tabulation, Tables 1–50, and tons of dry natural gas production in the same year as reported by Energy Information Agency (Dunn et al., 2013). Table 1 provides the methane emissions values for various upstream processes involved in NG supply chain (Burnham, 2023).
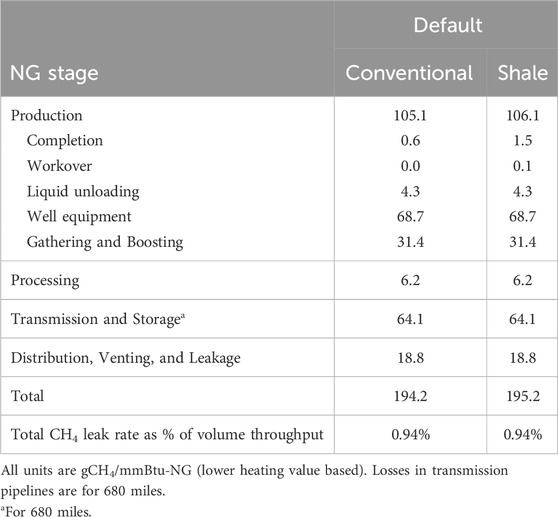
Table 1. NG upstream non-combustion methane emissions using bottom-up/top-down hybrid approach based upon Rutherford et al. (2021), Alvarez et al. (2018).
Greenhouse gas emissions associated with NG recovery include production and gathering and boosting (G&B) phases in the field. These emissions are associated with combustion of NG and diesel used for compression and other activities at production and G&B stages. The national average fuel use for NG recovery in the United States was calculated based on basin- and technology-level information from select datasets of the National Energy Technology Laboratory’s 2020 ONE Future report (Rai et al., 2021) using a weighted average of fuel consumption (NG and diesel) and NG production data for all basins. These basins are divided by recovery technology (conventional and unconventional) and locations, with different fuel use estimates. R&D GREET combines NG production and G&B into NG recovery. The fuel use data in Table 2 are provided for conventional and unconventional (shale and tight) technologies.
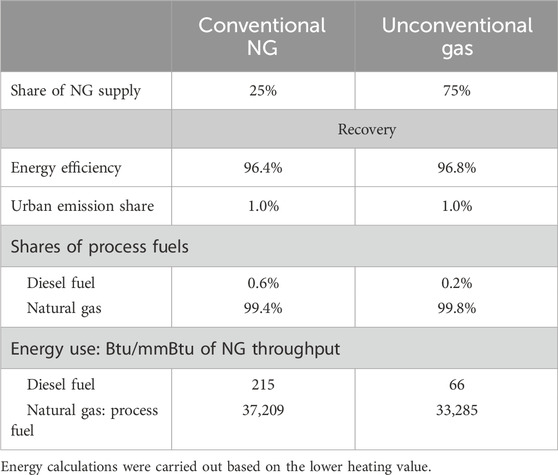
Table 2. Shares and parameters of NG recovery processes for conventional and unconventional gas in R&D GREET (2023).
2.1.2 Steam methane reforming
In a steam methane reforming plant, natural gas is reformed along with steam to produce hydrogen-rich syngas (CO + H2). The reforming reaction takes place mainly in the primary reformer; because of its endothermic nature, some natural gas along with tail gas from the downstream pressure swing adsorption (PSA) unit is combusted in the shell side of the reformer to provide the process heat, which leads to direct GHG emissions from the reformer stack. Furthermore, CO in syngas reacts with steam to produce additional hydrogen alongside CO2 via shift reaction (exothermic). Heat is recovered from the high-temperature process streams and combustion gases to preheat the feed, combustion air, and boiler feedwater; the recovered heat is used to generate steam (Kunz et al., 2018) needed for the reaction, with any surplus steam is available for export to nearby applications. Hydrogen is separated via PSA; unconverted gases (known as tail gas), including CO2, are used to provide process heat to the reformer as mentioned earlier. Details for the data used in this calculation can be found in Supplementary Table S1.
In this analysis, a displacement credit is taken for exported steam considering forgone emissions from a NG boiler that would have been used to produce the same amount of energy in the exported steam. Currently, the SMR pathway in R&D GREET is based on the ASPEN modeling from Case 1 of Lewis et al. (2022). Case 1 of Lewis et al. (2022) covers the steam methane reforming with and without CCS. NG consumption and on-site CO2 emissions per unit of produced hydrogen varies with several process optimization parameters, such as the methane slip, steam-to-carbon ratio, NG heating value, the need for byproduct steam, and the process configuration (Rajyalakshmi et al., 2012). These optimizations are made for a given plant based upon the NG price in the United States and capital expenses.
The Lewis et al. (2022) SMR study modified its SMR model to include CO2 capture from NG conversion and NG combustion [Case 2 in Lewis et al. (2022)]. After optimization, no steam was available for export (available steam is used for CO2 capture), slightly more NG was required, and 96% of the CO2 produced on-site was captured and delivered by pipeline for underground storage 62 km away in a deep saline formation.
2.1.3 Autothermal reforming
Autothermal reforming is similar to SMR in principle; however, the major difference is that the feed reforming and fuel combustion take place in the reformer, self-providing the heat required for the reforming reaction. An air separation unit is used to feed pure oxygen for combustion in the autothermal reformer, thus allowing for all the CO2 to be in the process side and in higher concentration (compared to SMR), thus simplifying the capture process. The hydrogen-rich syngas from the reformer is sent to shift reactors in which CO gets converted to CO2 via process feed steam, and additional hydrogen is produced. The process heat generated in the reformer and shift reactors is used for producing low-pressure steam, which is used for CCS. After CCS, pure hydrogen (99.9%) is separated via pressure swing adsorption (PSA). Tail gas from PSA is rich in hydrogen (73%) with some CO, CH4, CO2, and N2 and therefore has energy value, which is partly recycled to the CO2 capture unit with the remainder of tail gas combusted in a fired heater to heat the NG feed and generate steam needed for the reaction. The CO2 from tail gas combustion in the fired heater is small and thus is not captured, resulting in overall CO2 capture rate of 94.5%. The ATR pathway in R&D GREET uses the energy and mass balance inventory from Case 3 of Lewis et al. (2022).
2.1.4 Biogas or renewable natural gas feedstock for reforming
Reforming can also be carried out using low-CI renewable natural gas (RNG), which can assist in lowering the CI of produced hydrogen. Raw biogas can be produced from various waste streams—for example, landfill gas (LFG), or by converting wet waste into biogas via anaerobic digestion. Raw biogas is a mixture of CH4 and CO2 with water, sulfur, and other contaminants. It must be upgraded by separation and purification to become pipeline-grade RNG, which is interchangeable with fossil natural gas. We focused on RNG from LFG reforming in this paper.
Waste feedstocks are not produced intentionally and must be treated and disposed of. Thus, credits are taken for avoided emissions related to the business-as-usual treatment of waste feedstock. In the present work, we computed life-cycle emissions of LFG pathways by using a carbon neutrality approach, in which CO2 arising from biogenic carbon combustion is considered as CO2 from the air when organic materials are produced (Eggleston et al., 2006; U.S. EPA, 2010). Credits were taken for the business-as-usual practice (flaring of LFG), which causes small N2O and CH4 emissions. These credits are relatively small.
Key considerations are energy use during biogas upgrading to RNG and transportation operations, types of waste components, climate conditions, waste decay rates, collection strategy, landcover, and oxidation factors (Lee et al., 2017). Details of the RNG pathways are described in Lee et al. (2017), Lee et al. (2016a), Lee et al. (2021), as well as Lee et al. (2016b), Mintz et al. (2010), Han et al. (2011).
2.2 Water electrolysis
Hydrogen can also be produced via splitting water molecules by using an electrochemical reaction termed electrolysis process. We discuss low-temperature electrolysis via PEM and high-temperature electrolysis via SOEC. PEM electrolyzer energy efficiency was adopted from the DOE Hydrogen and Fuel Cells Program Record (U.S. DOE, 2019). Efficiency, defined as the produced hydrogen’s heating value on a lower heating value (LHV) basis divided by the total electric energy usage, was 60.1% (55.5 kWh/kgH2), representing current performance.
High-temperature electrolysis in SOECs take advantage of increased electrolysis energy efficiency with elevated temperatures. We adopted information from the DOE Hydrogen and Fuel Cells Program Record #20006 (U.S. DOE, 2020), in which steam and electricity from nuclear light water reactor (LWR) are used to power the SOEC. Near-term implementations would likely draw high-quality steam from the LWR steam manifold (Wendt and Boardman, 2022) for the thermal energy needs of SOEC. This is the same steam that would otherwise be used for electricity generation via the steam turbine. Therefore, we converted the SOEC thermal demand to an equivalent electricity by using a steam power plant net thermal efficiency of 33%. This converted value was added to the SOEC electrical power demand, resulting in a total hydrogen production efficiency of 79% (LHV basis), which equates to 42 kWh/kgH2 of equivalent electricity consumption. SOEC upstream emissions arise from the carbon intensity of the nuclear fuel cycle associated with LWR nuclear power generation, which is the default nuclear power technology in R&D GREET.
All GHG emissions associated with water electrolysis arise from upstream power generation, which are considered zero for solar, wind, and hydroelectric power (excluding equipment-embodied emissions). These scenarios are labelled LTE Renewable. PEM electrolysis with conventional LWR nuclear power has emissions related to the uranium supply chain to the nuclear reactor.
2.3 Biomass gasification
The H2A model (Mann and Steward, 2018) is used for the biomass gasification pathway in the R&D GREET. In the model, gasification char is used in a dryer to dry poplar biomass from 50 wt% to 12 wt% moisture content. The biomass is subsequently gasified in steam, and the gaseous product is passed through a steam reformer. The resulting syngas goes through low- and high-temperature shift reactors to produce a hydrogen-rich gas mixture. Hydrogen is recovered through PSA, and its tail gas is used as a fuel to provide thermal energy and power for the process. The energy efficiency of the biomass gasification process on an LHV basis is 44.2% with 2.3% of total energy coming from NG, 0.6% from grid electricity, and 97.1% from biomass.
2.4 Coal gasification
Hydrogen can be produced by gasification of coal and then reacting the generated syngas with steam. In the coal gasification process, coal is first dried with air and then fed into the gasifier along with oxygen from an air separation unit to produce syngas. In the next step, the syngas goes through a scrubber and undergoes a water gas shift reaction to produce mainly CO2 and hydrogen-rich process gas. CO2 is removed via PSA to produce pure hydrogen. If not captured, CO2 leaves through the stack. Case 4 from Lewis et al. (2022) is used for energy and mass balance inventory for coal gasification without a CCS pathway. In coal gasification with CCS, after the shift reaction, most of the CO2 is captured in a capture (Selexol) unit and then compressed and transported for sequestration. Case 5 from Lewis et al. (2022) is used for energy and mass balance inventory for coal gasification with CCS.
2.5 Byproduct hydrogen
Byproduct hydrogen is co-produced in technologies in which hydrogen is produced in small quantities relative to other products. The emissions occurring at such facilities can be allocated to various products based on mass, energy, or market value and therefore, may allow recovery of low-CI hydrogen. We cover byproduct hydrogen from chlor-alkali plants and natural gas liquid steam cracker plants in this section.
2.5.1 Chlor-alkali hydrogen
Chlor-alkali (C-A) processes produce Cl2, NaOH, and nearly pure hydrogen electrochemically via electrolysis of brine. Hydrogen can be used for process heat, sold, or vented/flared. For plants that use hydrogen for process heat, hydrogen may be otherwise sold while sourcing NG to replace the forgone energy in the sold hydrogen. The default R&D GREET chlor-alkali pathway considers that C-A hydrogen is recovered and compressed to 20 bars for export. Therefore, we treat Cl2, NaOH, and hydrogen as C-A co-products and allocate emissions among them on a mass basis. The mass yields of Cl2, NaOH, and hydrogen lead to allocation factors of 46%, 52%, and 1.3%, respectively. C-A facilities may generate other co-products, such as KOH, HCl, NaOCl, Ethylene Dichloride (EDC), and Vinyl Chloride Monomer (VCM). In such facilities, the allocation factors may vary based on the production amount of each chemical. In this work, we have accounted for an industry-weighted average production and calculated the allocation factors accordingly. Additionally, hydrogen is produced at 1.3 bar in the C-A process. For consistent comparison with hydrogen production via methane reforming and water electrolysis, we consider the additional electricity required to compress hydrogen from 1.3 bar to 20 bar and allocate the compression burden to hydrogen.
Existing C-A plants use a range of electrolysis technologies. The most common configuration uses a membrane cell, relies on grid power (no CHP), and has no electricity or steam displacement credits. We developed a fuel inventory from which emissions were computed with R&D GREET.
2.5.2 Natural gas liquids steam cracking hydrogen
Natural gas liquids (NGL) are by-products of natural gas processing plants and are key feedstocks for petrochemicals production after conversion to light olefins in NGL steam cracker plants. Hydrogen is present in the process tail gas, which is used as fuel by the plant furnaces. This hydrogen can be recovered via PSA (Lee and Elgowainy, 2018). In the United States, current and planned NGL cracker plants could produce 3.5 million tonnes of hydrogen per year by 2025, especially in the U.S. Gulf Coast region (Lee and Elgowainy, 2018; Woodward, 2017).
When hydrogen is recovered from the process tail gas for export instead of being combusted with tail gas in the furnace, its energy value must be replaced (substituted) by an alternative energy source, such as NG. In this analysis, energy use and emissions for NGL cracker hydrogen arise from the furnace fuel substitution. For each kg of recovered hydrogen, 120 MJ (LHV basis) of NG fuel is substituted. The associated burdens are the upstream burdens for procuring and combusting 120 MJ of NG, plus the upstream burdens associated with the PSA electricity use for hydrogen purification. All such burdens are allocated to the sold hydrogen (Lee and Elgowainy, 2018). We assumed 0.5 kWh/kgH2 for the PSA step needed for hydrogen separation from tail gas.
3 Emerging technologies
While methane reforming and water electrolysis are established technologies and widely used methods of hydrogen production, there are several emerging technologies for hydrogen production that are at various technology readiness levels (TRLs).
3.1 Methane pyrolysis
Methane pyrolysis has been of recent interest in the United States. It decomposes methane into its constituent molecules: carbon and hydrogen. This process is usually carried out at high temperatures (above 1,000°C), though catalysts may be added to reduce the reaction temperature. The equation for this reaction is shown in Equation 1:
While typically used for carbon black production, methane pyrolysis has potential for hydrogen production. Unlike most emerging technologies, methane pyrolysis is currently applied on an industrial scale to produce carbon black and hydrogen at a facility operated by Monolith Inc. Monolith uses plasma to achieve the high temperatures needed for uncatalyzed decomposition of methane. Currently, this is the only industrial-scale methane pyrolysis facility operating in the United States; many other methane pyrolysis projects are still in the pilot- or bench-scale phases. Methane pyrolysis pathway in R&D GREET relied on operation data obtained from Monolith Inc. and can be found in the Supplementary Material (Vyawahare et al., 2023).
3.2 Partial oxidation
Partial oxidation (POx) is another emerging technology for hydrogen production that involves reacting methane with O2, partially oxidizing methane into CO and hydrogen according to Equation 2:
Unlike the endothermic steam reforming reaction used in SMR plants, POx involves an exothermic reaction, making it the faster reaction of the two (Steinberg and Cheng, 1989). Furthermore, the endothermic nature of steam reforming makes it dependent on external heating sources to maintain the appropriate reaction temperature. However, the requirement for high purity oxygen for the POx reaction increases the costs associated with this method of hydrogen production (Chaubey et al., 2013). The endothermic nature of steam reforming and exothermic nature of POx can be further exploited by combining both processes to form a new process known as ATR, discussed in Section 2.1.3. In ATR, heat produced by POx is used as a heat source for steam reforming, resulting in a reaction system that has net-zero enthalpy (Semelsberger 2009). However, due to lack of process level data for POx, we did not perform a LCA for this hydrogen production pathway.
3.3 Geologic hydrogen
Recently, there has been growing interest in extracting hydrogen that is naturally produced or externally stimulated and recovered from underground geologic formations. The two main mechanisms of hydrogen formation are serpentinization and radiolysis; the former of which involves the reduction of water to produce hydrogen, while the latter describes the production of hydrogen via the decomposition water due to exposure to ionizing radiation (Yedinak, 2022). These reservoirs potentially contain trillions of tons of untapped hydrogen reserves, which has the potential to provide hydrogen for hundreds of years (Pearce, 2024; USGS, 2023). However, factors such as high reactivity, high diffusivity, and imperfect analytical techniques have hindered hydrogen exploration efforts (Zgonnik, 2020). Currently, research is being carried out to determine the feasibility of geologic hydrogen extraction with the U.S. Department of Energy dedicating 20 million USD to the topic (ARPA-E, 2024). As this method of hydrogen production is still in its infancy, there is insufficient data available to perform a credible LCA for determining associated CI.
4 Hydrogen conditioning and delivery pathways
4.1 Hydrogen transportation and distribution
Gaseous hydrogen can be delivered from the production facility to refueling stations either by tube-trailer or pipeline. On the other hand, liquefied hydrogen can be transported via cryogenic tanker trucks to refueling stations. In R&D GREET, we assume a default transportation distance of 161 km (100 mi). In gaseous hydrogen scenarios, a bulk loading terminal is co-located at the hydrogen production site and grid electricity is required for compression. More information on hydrogen compression can be found in the Supplementary Material. In liquefied hydrogen scenarios, a liquefier is co-located at the hydrogen production site and is operated using grid electricity as well. However, the electricity source may change depending on the electricity used for hydrogen production (e.g., hydro or nuclear power).
In nuclear power scenarios for hydrogen production via water electrolysis, the gaseous hydrogen terminal and liquefier are assumed to use nuclear power, instead of the grid mix. If solar or wind power is used, grid electricity is assumed to be used to power the liquefier and the gaseous hydrogen loading terminal instead. This is due to the intermittent nature of these electricity sources, making them unsuitable for providing electricity to applications that require a steady source of electricity to function. However, as hydroelectricity is a reliable source of renewable power, we considered it as the default source of electricity to operate the liquefier and hydrogen loading terminals if it is also used to produce hydrogen.
While there is no hydrogen losses considered in the transportation and distribution (T&D) or at the hydrogen refueling station (HRS) for gaseous hydrogen, liquid hydrogen is assumed to incur some loss at each stage due to boiling off. These include a loss of 0.5% at the liquefaction plant, 0.3% at the bulk terminal, 5% of unloaded amount at refueling station, and 4 kg per day per cryopump at the HRS. More details are provided in Frank et al. (2021).
4.2 Hydrogen liquefaction
Liquefaction is an energy-intensive process. We developed the energy intensity in R&D GREET by surveying gas industry experts about existing technology (liquid nitrogen precooling and Claude cycle liquefaction). Our analysis assumes an energy intensity of 11 kWh/kgLH2, which is representative of a 20 tonnes/day liquefier built with existing technology. Since they are not yet proven, we do not consider potential future high-efficiency liquefiers that may potentially achieve 6 kWh/kgLH2 at the 50 tonnes/day scale (Cardella et al., 2017).
4.3 Hydrogen storage
Following the transportation of hydrogen to the refueling station, it must be stored while awaiting use. Hydrogen storage systems can be broadly classified into two categories: physical storage and geological storage. The most common methods of physical storage in small quantities (up to a few tons) either compress hydrogen into storage tanks or liquefy hydrogen for storage in cryogenic tanks. Storage tanks are often located at refueling stations and differ depending on whether they will store gaseous or liquid hydrogen. Gaseous hydrogen storage tanks are typically made to withstand high pressures and have a maximum pressure of ∼1,000 bar (Argonne National Laboratory, 2023), while liquid hydrogen storage tanks need to be well-insulated to maintain cryogenic conditions. In R&D GREET, compression is considered for gaseous hydrogen storage, while liquid hydrogen storage tanks are assumed to consume electricity for pumping operations.
Other methods of physical hydrogen storage have been developed. One example is chemical storage, in which hydrogen is converted to hydrides such as magnesium hydride, ammonia, or methanol (Andersson and Grönkvist, 2019). Due to the strong bonds formed in metal hydrides, they can be stored safely in high-density in ambient conditions, though high energy input is required to subsequently release the hydrogen (Bellosta von Colbe et al., 2019). On the other hand, chemical storage in the form of common chemicals such as ammonia and methanol tend to be favored over metal hydrides, due to their established nature in terms of the manufacturing technology and transportation infrastructure. Geologic hydrogen storage can store vast quantities (thousands of tons) of hydrogen in naturally occurring subsurface reservoirs, which does not require maintenance or storage vessels like physical storage. Instead, the hydrogen can be injected into developed salt caverns where impermeable salt layers act as a natural barrier to prevent hydrogen from escaping (Aftab et al., 2022). Salt caverns have already been deployed in the U.S. Gulf of Mexico region. There are no GHG emissions associated with cavern operation for hydrogen storage. There are indirect emissions associated with compression of hydrogen for storage, which is included in the compression stage.
5 Results and discussion
The WTG emission results for the hydrogen pathways in R&D GREET are provided in Figure 1. These results do not include CapEx embodied emissions associated with construction of hydrogen production facilities. Conventional SMR without CCS and NGL cracking produce hydrogen with the highest carbon intensities at 9.3 and 8.5 kgCO2e/kgH2, respectively. The high carbon intensity of hydrogen production from NGL cracking comes from replacing energy in hydrogen separated from tail gas with natural gas combustion for NGL cracking process. While the production of hydrogen via coal gasification generates high GHG emissions at 18.6 kgCO2e/kgH2, this is not a common method of hydrogen production in the United States. Coal gasification with CCS significantly reduces GHG emissions associated with hydrogen production. The other methods of hydrogen production, such as water electrolysis using clean electricity, by-product hydrogen from chlor-alkali, biomass gasification, methane pyrolysis, and SMR and ATR with CCS have significantly lower hydrogen CI as shown in Figure 1. When CCS systems are implemented or RNG is used, ATR and SMR on-site emissions can be significantly reduced.
For many hydrogen production technologies, upstream (supply chain) emissions play a significant role in the CI of produced hydrogen. Upstream emissions for feedstock and energy supply to hydrogen production technologies can be subdivided into two categories: Upstream emissions associated with electricity generation and transmission, and upstream emissions associated with feedstock and process energy acquisition. Upstream emissions associated with electricity supply are the primary driving factor of GHG emissions for electrolysis, chlor-alkali, and methane pyrolysis pathways, accounting for at least half of overall emissions in the pathway. As a result, the hydrogen CI from these pathways can be significantly reduced if clean electricity is used, thus presenting a significant decarbonization opportunity. On the other hand, upstream emissions associated with feedstock and process energy acquisition are the key drivers of GHG emissions for coal gasification with CCS, biomass gasification, SMR with CCS, SMR using LFG, and ATR with CCS, as shown in Figure 1. However, unlike upstream emissions associated with electricity supply, these emissions are harder to mitigate by hydrogen producers. This is because their supply chain often involves multiple activities that are heavily reliant on fossil fuels, such as mining for coal, recovery, processing and fugitive methane emissions for natural gas, as well as transporting these feedstocks to the hydrogen production plant.
We examined the impact of electricity CI on several hydrogen pathways in Figure 2. For this sensitivity analysis, we examined electricity from three different sources: renewable electricity, United States grid mix (440 gCO2e/kWh), and Hawaiian grid mix (870 gCO2e/kWh). SMR, NGL, and biomass gasification are the least affected by the CI of electricity due to the minor role of electricity in these processes, accounting for 0.5, 2.6, and 11% of hydrogen CI, respectively, as shown in Figure 1. As the implementation of CCS systems demand additional electricity, hydrogen production pathways that use CCS, such as SMR, ATR, and coal gasification show higher contribution of electricity supply emissions to hydrogen CI. Water electrolysis and methane pyrolysis, however, show the largest impact of electricity supply emissions on hydrogen CI. This is because of their significant electricity consumption per unit of hydrogen produced, as shown in Supplementary Table S3. As the C-A process also involves high electricity use for the electrolysis of brine solution, the CI of its products are also expected to be largely dependent on the CI of electricity supply. Hydrogen CI produced via water electrolysis is directly proportional to the CI of electricity used.
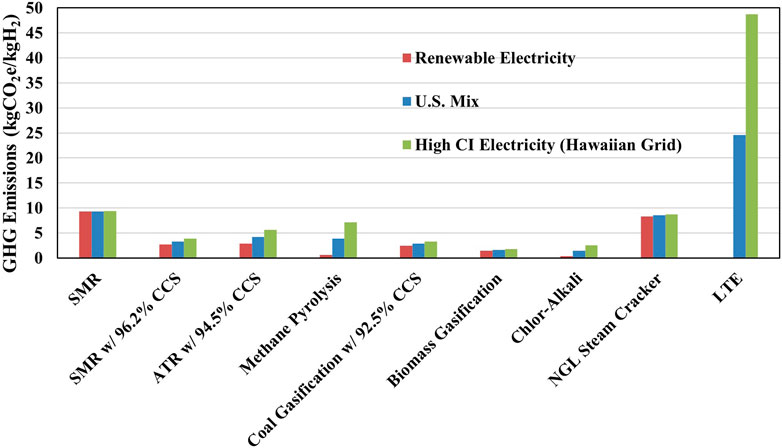
Figure 2. Effect of the carbon intensity of electricity used on the GHG emissions of hydrogen production.
We also carried out a sensitivity analysis on hydrogen production pathways that rely on natural gas. As methane is a potent GHG with a Global Warming Potential (GWP) of 29.8 (Intergovernmental Panel on Climate C, 2023), methane emissions in the NG supply chain can have a significant impact on the hydrogen CI. Sensitivity analysis was carried out using methane emission rates ranging from 0% (low) to 2% (high), with a default value of 1%. The results of this analysis are shown in Figure 3. SMR with CCS and ATR with CCS showed the greatest dependence on methane emission rate, with WTG emissions increasing by 1.2 and 1.1 kgCO2e/kgH2, respectively, at 2% methane emission rate, compared to default value. The increase in GHG emissions for SMR with CCS is higher compared to SMR, as more natural gas is required to meet the increased energy demands of the CCS. Biomass gasification was insensitive to the changed methane emission rate, as natural gas is not a primary energy source for the gasification process. While chlor-alkali and methane pyrolysis, which is sensitive to methane emissions, rely heavily on electricity, the allocation of emissions between hydrogen and other co-products reduces the sensitivity to the methane emission rate.
Figure 4 shows the gate-to-pump (GTP) emissions for each step after the hydrogen leaves the production plant up to hydrogen refueling station for hydrogen vehicle applications. These emission sources can be broken down into several steps: compressing gaseous hydrogen for delivery and storage, liquefaction, transportation to destination, and any additional compression and precooling required for dispensing or storage at HRS. Compressing hydrogen at the plant gate for tube-trailer loading or pipeline delivery is carried out next to production and thus, the electricity supply is assumed to be sourced from the regional grid around the hydrogen plant. Using U.S. grid electricity for this compression step contributes 0.8 kgCO2e/kgH2 to overall emissions for loading tube-trailers and 0.3 kgCO2e/kgH2 for pipeline delivery, constituting 63% of total GTP emissions for gaseous hydrogen transported via tube-trailers and 20% for pipelines. As the compression process for hydrogen delivery requires a dispatchable source of electricity, intermittent electricity sources such as solar PV (photovoltaic) and wind may not be suitable for this process without energy storage system to mitigate the intermittency. Thus, compression is assumed to rely on regional grid electricity, even though the facility may be using solar PV or wind electricity for hydrogen production. To reduce these emissions, other clean dispatchable electricity sources such as hydroelectricity and nuclear power can be used, as shown in Figure 4. However, this effect is less significant when hydrogen is transported through pipelines due to the higher electricity consumption at HRS. Using grid electricity, the pressurization requirements for storage at the HRS contribute 1.2 kgCO2e/kgH2 to overall emissions and represent 76% of GTP emissions for pipelines. While gaseous hydrogen delivery via pipeline is less energy and emissions intensive (80% lower) compared to tube-trailer delivery, it incurs higher GHG emissions at HRS due to the higher compression ratio at HRS. Alternatively, the gaseous hydrogen may be liquefied and subsequently transported to the HRS via cryogenic tanker truck. The liquefaction step is energy-intensive, contributing a significant 5 kgCO2e/kgH2 to GTP emissions when U.S. average grid electricity is used. These emissions can only be reduced by using a dispatchable source of clean electricity, e.g., hydro and nuclear power. For this analysis, we assumed that all hydrogen production methods used grid electricity unless otherwise specified.
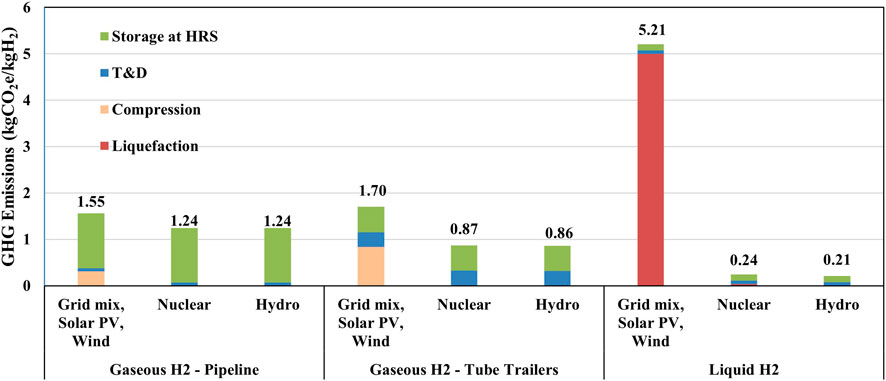
Figure 4. Gate-to-Pump emissions for gaseous and liquid hydrogen. 100 mi of transportation distance is assumed.
While we did not include CapEx embodied emissions in the aforementioned analysis, our previous work on embodied emissions clearly showed that it has a significant impact on the CI of hydrogen produced via electrolysis using renewable energy (Gan et al., 2023; Gan et al., 2024). Therefore, it is important to understand the impact of embodied emissions on the CI of hydrogen produced from various technologies.
In Figure 5, we included embodied emissions coming from the feedstock and electricity inputs, such as the construction of coal mines and farming equipment, as well as the GHG emissions from the construction of hydrogen production facilities and electrolyzers (Iyer et al., 2024). In addition, we assumed that the emissions from SMR facility construction would be similar for ATR, methane pyrolysis, and gasification. However, these emissions are small and do not have a significant impact on the CI of hydrogen. Figure 5 shows the impact of CapEx embodied emissions on the CI of hydrogen produced via a variety of technology pathways, such as SMR, ATR, coal and biomass gasification, and water electrolysis. We observed that the CapEx embodied emissions for SMR, ATR, coal gasification, and methane pyrolysis comprise between 0.7% and 6% of total life cycle GHG emissions associated with hydrogen production. Embodied emissions have a large impact on hydrogen CI from biomass gasification, mainly due to the farming equipment. They also have large impact on the hydrogen CI from water electrolysis using renewable electricity, contributing approximately 2 kgCO2e/kgH2 for solar power.
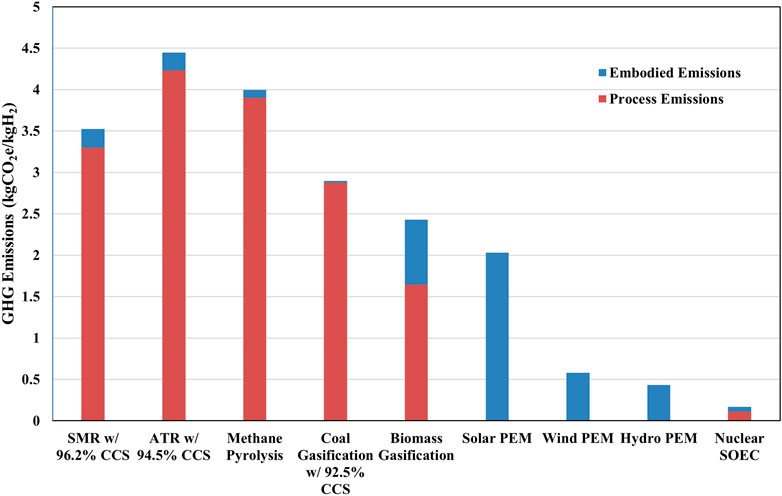
Figure 5. CI of hydrogen produced from various production technologies including CapEx embodied emissions.
6 Conclusion
This paper examines the CI of hydrogen produced via a variety of conventional and emerging technologies, as well as its packaging (compression and liquefaction), delivery and storage in the United States. The feedstock and energy supply chain upstream GHG emissions play a significant role in the CI of hydrogen production and thus using biogenic feedstock (e.g., biogas) and/or clean electricity (e.g., renewable or nuclear power), a low CI hydrogen production can be achieved. As clean electricity is currently the simplest approach of the two, many hydrogen producers may consider water electrolysis or other emerging technologies such as plasma pyrolysis of methane, both of which consume large amounts of electricity per unit of hydrogen produced. Also, onsite emissions can be mitigated via carbon management technologies such as CCS. Hydrogen packaging and delivery also contribute significant GHG emissions due to the high electricity requirement for hydrogen compression and liquefaction. Finally, embodied emissions can have a significant impact on the CI of hydrogen produced and cannot be ignored in some cases. Overall, mitigating feedstock supply chain GHG emissions (e.g., CH4 emissions in the NG supply chain), utilizing cleaner energy supply (e.g., clean electricity for water electrolysis and methane pyrolysis, and RNG for SMR and ATR), implementing carbon management strategies (e.g., CCS), and using clean electricity for hydrogen compression and liquefaction can substantially reduce the life cycle carbon footprint of hydrogen supplied to various end use applications.
Data availability statement
The datasets presented in this study can be found in online repositories. The names of the repository/repositories and accession number(s) can be found below: https://greet.anl.gov/.
Author contributions
AE: Conceptualization, Funding acquisition, Project administration, Resources, Supervision, Writing–review and editing. PV: Formal Analysis, Investigation, Methodology, Validation, Writing–original draft, Writing–review and editing. CN: Data curation, Formal Analysis, Investigation, Validation, Writing–original draft, Writing–review and editing. EF: Conceptualization, Writing–review and editing, Data curation, Investigation. AdB: Conceptualization, Writing–review and editing, Validation. AnB: Conceptualization, Writing–review and editing. PS: Conceptualization, Writing–review and editing. HC: Conceptualization, Writing–review and editing. UL: Conceptualization, Writing–review and editing. KR: Writing–review and editing, Conceptualization. MW: Supervision, Writing–review and editing.
Funding
The author(s) declare that financial support was received for the research, authorship, and/or publication of this article. Argonne National Laboratory’s work was supported by the U.S. Department of Energy, Office Energy Efficiency and Renewable Energy, Hydrogen and Fuel Cell Technologies Office under contract DE-AC02-06CH11357.
Conflict of interest
The authors declare that the research was conducted in the absence of any commercial or financial relationships that could be construed as a potential conflict of interest.
Publisher’s note
All claims expressed in this article are solely those of the authors and do not necessarily represent those of their affiliated organizations, or those of the publisher, the editors and the reviewers. Any product that may be evaluated in this article, or claim that may be made by its manufacturer, is not guaranteed or endorsed by the publisher.
Supplementary material
The Supplementary Material for this article can be found online at: https://www.frontiersin.org/articles/10.3389/fenrg.2024.1473383/full#supplementary-material
References
Aftab, A., Hassanpouryouzband, A., Xie, Q., Machuca, L. L., and Sarmadivaleh, M. (2022). Toward a fundamental understanding of geological hydrogen storage. Industrial and Eng. Chem. Res. 61 (9), 3233–3253. doi:10.1021/acs.iecr.1c04380
Alvarez, R. A., Zavala-Araiza, D., Lyon, D. R., Allen, D. T., Barkley, Z. R., Brandt, A. R., et al. (2018). Assessment of methane emissions from the U.S. oil and gas supply chain. Science 361 (6398), 186–188. doi:10.1126/science.aar7204
Andersson, J., and Grönkvist, S. (2019). Large-scale storage of hydrogen. Int. J. Hydrogen Energy 44 (23), 11901–11919. doi:10.1016/j.ijhydene.2019.03.063
Argonne National Laboratory (2023). Hydrogen delivery scenario analysis model (HDSAM), United States. Available at: https://hdsam.es.anl.gov/index.php?content=hdsam.
ARPA-E (2024). U.S. Department of energy announces $20 million to 16 projects spearheading exploration of geologic hydrogen. Available at: https://arpa-e.energy.gov/news-and-media/press-releases/us-department-energy-announces-20-million-16-projects-spearheading (Accessed 2024).
Bellosta von Colbe, J., Ares, J.-R., Barale, J., Baricco, M., Buckley, C., Capurso, G., et al. (2019). Application of hydrides in hydrogen storage and compression: achievements, outlook and perspectives. Int. J. Hydrogen Energy 44 (15), 7780–7808. doi:10.1016/j.ijhydene.2019.01.104
Bicer, Y., and Dincer, I. (2017). Life cycle assessment of nuclear-based hydrogen and ammonia production options: a comparative evaluation. Int. J. Hydrogen Energy 42 (33), 21559–21570. doi:10.1016/j.ijhydene.2017.02.002
Burmistrz, P., Chmielniak, T., Czepirski, L., and Gazda-Grzywacz, M. (2016). Carbon footprint of the hydrogen production process utilizing subbituminous coal and lignite gasification. J. Clean. Prod. 139, 858–865. doi:10.1016/j.jclepro.2016.08.112
Burnham, A. (2023). Updated natural gas pathways in GREET 2023. Available at: https://greet.anl.gov/publication-update_ng_2023 (Accessed 2024).
Cardella, U., Decker, L., and Klein, H. (2017). Roadmap to economically viable hydrogen liquefaction. Int. J. Hydrogen Energy 42 (19), 13329–13338. doi:10.1016/j.ijhydene.2017.01.068
Cetinkaya, E., Dincer, I., and Naterer, G. F. (2012). Life cycle assessment of various hydrogen production methods. Int. J. Hydrogen Energy 37 (3), 2071–2080. doi:10.1016/j.ijhydene.2011.10.064
Chaubey, R., Sahu, S., James, O. O., and Maity, S. (2013). A review on development of industrial processes and emerging techniques for production of hydrogen from renewable and sustainable sources. Renew. Sustain. Energy Rev. 23, 443–462. doi:10.1016/j.rser.2013.02.019
Dufour, J., Gálvez, J. L., Serrano, D. P., Moreno, J., and Martínez, G. (2010). Life cycle assessment of hydrogen production by methane decomposition using carbonaceous catalysts. Int. J. Hydrogen Energy 35 (3), 1205–1212. doi:10.1016/j.ijhydene.2009.11.093
Dunn, J. B., Elgowainy, A., Vyas, A., Lu, P., Han, J., Wang, M., et al. (2013). Update to transportation parameters in GREET. Lemont, IL: Argonne National Laboratory. Available at: https://greet.es.anl.gov/publication-tansportation-distribution-13.
Eggleston, H. S., Miwa, K., Srivastava, N., and Tanabe, K. E. (2006). 2006 IPCC guidelines for national greenhouse gas inventories — a primer, Prepared by the national greenhouse gas inventories programme; intergovernmental panel on climate change (IPCC), IGES, Japan, 2008. Renew. Fuel Stand. Program (RFS2) Regul. Impact Anal. Available at: https://www.ipcc.ch/report/2006-ipcc-guidelines-for-national-greenhouse-gas-inventories/.
Frank, E. D., Elgowainy, A., Reddi, K., and Bafana, A. (2021). Life-cycle analysis of greenhouse gas emissions from hydrogen delivery: a cost-guided analysis. Int. J. Hydrogen Energy 46 (43), 22670–22683. doi:10.1016/j.ijhydene.2021.04.078
Gan, Y., Elgowainy, A., Lu, Z., Kelly, J., Wang, M., Boardman, R., et al. (2023). Greenhouse gas emissions embodied in the U.S. solar photovoltaic supply chain. Environ. Res. Lett. 18 (10), 104012. doi:10.1088/1748-9326/acf50d
Gan, Y., Ng, C., Elgowainy, A., and Marcinkoski, J. (2024). Considering embodied greenhouse emissions of nuclear and renewable power plants for electrolytic hydrogen and its use for synthetic ammonia, methanol, Fischer−Tropsch fuel production. Environ. Sci. Technol. doi:10.1021/acs.est.3c06769
Giraldi, M. R., François, J.-L., and Martin-del-Campo, C. (2015). Life cycle assessment of hydrogen production from a high temperature electrolysis process coupled to a high temperature gas nuclear reactor. Int. J. Hydrogen Energy 40 (10), 4019–4033. doi:10.1016/j.ijhydene.2015.01.093
Hajjaji, N., Pons, M.-N., Renaudin, V., and Houas, A. (2013). Comparative life cycle assessment of eight alternatives for hydrogen production from renewable and fossil feedstock. J. Clean. Prod. 44, 177–189. doi:10.1016/j.jclepro.2012.11.043
Han, J., Mintz, M., and Wang, M. (2011). Waste-to-wheel analysis of anaerobic-digestion-based renewable natural gas pathways with the GREET model. United States: Argonne National Lab. doi:10.2172/1036091
Henriksen, M. S., Matthews, H. S., White, J., Walsh, L., Grol, E., Jamieson, M., et al. (2024). Tradeoffs in life cycle water use and greenhouse gas emissions of hydrogen production pathways. Int. J. Hydrogen Energy 49, 1221–1234. doi:10.1016/j.ijhydene.2023.08.079
Intergovernmental Panel on Climate, C (2023). Climate change 2021 – the physical science basis: working group I contribution to the sixth assessment report. Cambridge: Cambridge University Press. doi:10.1017/9781009157896
Iyer, R., Prosser, J., Kelly, J., James, B., and Elgowainy, A. (2024). Life-cycle analysis of hydrogen production from water electrolyzers. Int. J. Hydrogen Energy 81, 1467–1478. doi:10.1016/j.ijhydene.2024.06.355
Kalinci, Y., Hepbasli, A., and Dincer, I. (2012). Life cycle assessment of hydrogen production from biomass gasification systems. Int. J. Hydrogen Energy 37 (19), 14026–14039. doi:10.1016/j.ijhydene.2012.06.015
Karaca, A. E., Dincer, I., and Gu, J. (2020). Life cycle assessment study on nuclear based sustainable hydrogen production options. Int. J. Hydrogen Energy 45 (41), 22148–22159. doi:10.1016/j.ijhydene.2020.06.030
Khojasteh Salkuyeh, Y., Saville, B. A., and MacLean, H. L. (2017). Techno-economic analysis and life cycle assessment of hydrogen production from natural gas using current and emerging technologies. Int. J. Hydrogen Energy 42 (30), 18894–18909. doi:10.1016/j.ijhydene.2017.05.219
Kunz, R. G., Hefele, D. C., Jordan, R. L., and Lash, F. W. (2018). Use of SCR in a hydrogen plant integrated with a stationary gas turbine - case study: the port arthur steam-methane reformer. Charlotte: Cormetech, Inc. Available at: https://www.cormetech.com/wp-content/uploads/2018/05/70093-kunz-Port-Arthur.pdf (Accessed December 23, 2021).
Lee, D.-Y., and Elgowainy, A. (2018). By-product hydrogen from steam cracking of natural gas liquids (NGLs): potential for large-scale hydrogen fuel production, life-cycle air emissions reduction, and economic benefit. Int. J. Hydrogen Energy 43 (43), 20143–20160. doi:10.1016/j.ijhydene.2018.09.039
Lee, U., Bhatt, A., Hawkins, T. R., Tao, L., Benavides, P. T., and Wang, M. (2021). Life cycle analysis of renewable natural gas and lactic acid production from waste feedstocks. J. Clean. Prod. 311, 127653. doi:10.1016/j.jclepro.2021.127653
Lee, U., Han, J., Urgun Demirtas, M., Wang, M., and Tao, L. (2016a). Lifecycle analysis of renewable natural gas and hydrocarbon fuels from wastewater treatment plants’ sludge. United States: Argonne National Lab. doi:10.2172/1327830
Lee, U., Han, J., and Wang, M. (2016b). Well-to-Wheels analysis of compressed natural gas and ethanol from municipal solid waste. United States. doi:10.2172/1334188
Lee, U., Han, J., and Wang, M. (2017). Evaluation of landfill gas emissions from municipal solid waste landfills for the life-cycle analysis of waste-to-energy pathways. J. Clean. Prod. 166, 335–342. doi:10.1016/j.jclepro.2017.08.016
Lewis, E., McNaul, S., Jamieson, M., Henriksen, M., Matthews, H. S., Walsh, L., et al. (2022). Comparison of commercial state-of-the-art, fossil-based hydrogen production technologies. United States: National Energy Technology Laboratory. doi:10.2172/1862910
Li, G., Cui, P., Wang, Y., Liu, Z., Zhu, Z., and Yang, S. (2020). Life cycle energy consumption and GHG emissions of biomass-to-hydrogen process in comparison with coal-to-hydrogen process. Energy 191, 116588. doi:10.1016/j.energy.2019.116588
Mann, M. K., and Steward, D. M. (2018). Current central hydrogen from biomass via gasification and catalytic steam reforming. Golden, CO: National Renewable Energy Laboratory. Available at: https://www.nrel.gov/hydrogen/assets/docs/current-central-biomass-gasification-v3-2018.xlsm.
Mintz, M., Han, J., Wang, M., Saricks, C., and Energy, S. (2010). Well-to-Wheels analysis of landfill gas-based pathways and their addition to the GREET model. United States: Argonne National Laboratory. doi:10.2172/982696
Moreno, J., and Dufour, J. (2013). Life cycle assessment of hydrogen production from biomass gasification. Evaluation of different Spanish feedstocks. Int. J. Hydrogen Energy 38 (18), 7616–7622. doi:10.1016/j.ijhydene.2012.11.076
Oni, A. O., Anaya, K., Giwa, T., Di Lullo, G., and Kumar, A. (2022). Comparative assessment of blue hydrogen from steam methane reforming, autothermal reforming, and natural gas decomposition technologies for natural gas-producing regions. Energy Convers. Manag. 254, 115245. doi:10.1016/j.enconman.2022.115245
Palmer, G., Roberts, A., Hoadley, A., Dargaville, R., and Honnery, D. Life-cycle greenhouse gas emissions and net energy assessment of large-scale hydrogen production via electrolysis and solar PV. Energy and Environ. Sci. 2021, 14 (10), 5113–5131. doi:10.1039/D1EE01288F
Pearce, F. (2024). Natural hydrogen: a potential clean energy source beneath our feet. Available at: https://e360.yale.edu/features/natural-geologic-hydrogen-climate-change.
Rai, S., Littlefield, J., Roman-White, S., Zaimes, G. G., Cooney, G., and Skone, T. J. (2021). Industry partnerships and their role in reducing natural gas supply chain greenhouse gas emissions – phase 2; United States. doi:10.2172/1765004
R&D GREET (2023). Greenhouse gases, regulated emissions, and energy use in technologies model® (2023 excel); United States. Lemont, IL: Argonne National Laboratory (ANL). Available at: https://www.osti.gov/doecode/biblio/113174.
Rajyalakshmi, S., Patwardhan, K., and Balaramakrishna, P. V. (2012). Optimised hydrogen production by steam reforming: part I. Pet. Technol. Q. 17 (1), 105–109. Available at: https://www.digitalrefining.com/article/1000339/optimised-hydrogen-production-by-steam-reforming-part-i.
Rutherford, J. S., Sherwin, E. D., Ravikumar, A. P., Heath, G. A., Englander, J., Cooley, D., et al. (2021). Closing the methane gap in US oil and natural gas production emissions inventories. Nat. Commun. 12 (1), 4715. doi:10.1038/s41467-021-25017-4
Semelsberger, T. A. (2009). “FUELS – HYDROGEN STORAGE | chemical carriers,” in Encyclopedia of electrochemical power sources. Editor J. Garche (Elsevier), 504–518. doi:10.1016/B978-044452745-5.00331-2
Spath, P. L., and Mann, M. K. (2000). Life cycle assessment of hydrogen production via natural gas steam reforming. United States: National Renewable Energy Lab. doi:10.2172/764485
Steinberg, M., and Cheng, H. C. (1989). Modern and prospective technologies for hydrogen production from fossil fuels. Int. J. Hydrogen Energy 14 (11), 797–820. doi:10.1016/0360-3199(89)90018-9
Sun, P., Young, B., Elgowainy, A., Lu, Z., Wang, M., Morelli, B., et al. (2019). Criteria air pollutants and greenhouse gas emissions fromHydrogen production in U.S. Steam methane reforming facilities. Environ. Sci. Technol. 53 (1), 7103–7113. doi:10.1021/acs.est.8b06197
Susmozas, A., Iribarren, D., and Dufour, J. (2013). Life-cycle performance of indirect biomass gasification as a green alternative to steam methane reforming for hydrogen production. Int. J. Hydrogen Energy 38 (24), 9961–9972. doi:10.1016/j.ijhydene.2013.06.012
Susmozas, A., Iribarren, D., Zapp, P., Linβen, J., and Dufour, J. (2016). Life-cycle performance of hydrogen production via indirect biomass gasification with CO2 capture. Int. J. Hydrogen Energy 41 (42), 19484–19491. doi:10.1016/j.ijhydene.2016.02.053
U.S. DOE (2019). Hydrogen production cost from PEM electrolysis. Available at: https://www.hydrogen.energy.gov/pdfs/19009_h2_production_cost_pem_electrolysis_2019.pdf (Accessed February 24, 2022).
U.S. DOE. (2020). Hydrogen production cost from high temperature electrolysis. Available at: https://www.hydrogen.energy.gov/pdfs/20006-production-cost-high-temperature-electrolysis.pdf. (Accessed February 24, 2022).
U.S DOE (undated). Hydrogen Resources. Available at: https://www.energy.gov/eere/fuelcells/hydrogen-resources (Accessed 2024).
USGS (2023). The potential for geologic hydrogen for next-generation energy. Available at: https://www.usgs.gov/news/featured-story/potential-geologic-hydrogen-next-generation-energy (Accessed 2024).
Verma, A., and Kumar, A. (2015). Life cycle assessment of hydrogen production from underground coal gasification. Appl. Energy 147, 556–568. doi:10.1016/j.apenergy.2015.03.009
Vyawahare, P., Ng, C., and Elgowainy, A. (2023). Hydrogen production from methane pyrolysis. Available at: https://greet.anl.gov/publication-methane_pyrolysis.
Wendt, D., and Boardman, R. (2022). Personal communication. Idaho Falls, ID: Idaho National Laboratory.
Woodward, S. (2017). “NGLs supply overall production outlook,” in Platts 7th annual NGLs conference and 5th annual petrochemical seminar (Houston, Texas), 10–31.
Yedinak, E. M. (2022). The curious case of geologic hydrogen: assessing its potential as a near-term clean energy source. Joule 6 (3), 503–508. doi:10.1016/j.joule.2022.01.005
Zang, G., Graham, E. J., and Mallapragada, D. (2024). H2 production through natural gas reforming and carbon capture: a techno-economic and life cycle analysis comparison. Int. J. Hydrogen Energy 49, 1288–1303. doi:10.1016/j.ijhydene.2023.09.230
Keywords: hydrogen production, life-cycle analysis, GHG emissions, carbon intensity, inflation reduction act, United States
Citation: Elgowainy A, Vyawahare P, Ng C, Frank ED, Bafana A, Burnham A, Sun P, Cai H, Lee U, Reddi K and Wang M (2024) Environmental life-cycle analysis of hydrogen technology pathways in the United States. Front. Energy Res. 12:1473383. doi: 10.3389/fenrg.2024.1473383
Received: 30 July 2024; Accepted: 26 September 2024;
Published: 15 October 2024.
Edited by:
Tianyi Sun, Environmental Defense Fund, United StatesReviewed by:
Timothy A. Barckholtz, ExxonMobil Technology and Engineering, United StatesHan Chen, Cambrex Corporation, United States
Copyright © 2024 Elgowainy, Vyawahare, Ng, Frank, Bafana, Burnham, Sun, Cai, Lee, Reddi and Wang. This is an open-access article distributed under the terms of the Creative Commons Attribution License (CC BY). The use, distribution or reproduction in other forums is permitted, provided the original author(s) and the copyright owner(s) are credited and that the original publication in this journal is cited, in accordance with accepted academic practice. No use, distribution or reproduction is permitted which does not comply with these terms.
*Correspondence: Amgad Elgowainy, YWVsZ293YWlueUBhbmwuZ292; Pradeep Vyawahare, cHZ5YXdhaGFyZUBhbmwuZ292; Clarence Ng, Y2xhcmVuY2VqaG5nQGdtYWlsLmNvbQ==