- 1Division of Energy Systems, Department of Management and Engineering, Linköping University, Linköping, Sweden
- 2Department of Building and Environment Engineering, University of Gävle, Gävle, Sweden
- 3Department of Industrial Management, Industrial Design and Mechanical Engineering, University of Gävle, Gävle, Sweden
In the effort to limit global warming to 1.5°C above the pre-industrial level, decarbonization of supply chains is crucial. Companies will need to reduce not only their direct and indirect emissions (scope 1 and 2) but also their indirect emissions (scope 3). In some sectors, the upstream scope 3 emissions can actually be larger than the companies’ direct emissions. Therefore, a systematic literature review was carried out to understand how previous research in the field of supply chain management (SCM) approached energy efficiency and energy management in the upstream supply chain. The results indicate that only a few studies have addressed energy efficiency within SCM, and the majority assess energy solely as total energy use, without exploring opportunities to reduce final energy use among upstream suppliers. Moreover, results show that there is a lack of standards and methods to assess suppliers’ energy use, making it difficult for suppliers, particularly small and medium-sized enterprises, to overcome barriers to implementing energy management. In conclusion, even though energy efficiency is a cost-effective means to reduce CO2 emissions, only a limited number of studies in the field of SCM have integrated energy efficiency, revealing a vast knowledge gap in this field.
1 Introduction
According to the International Energy Agency 2022, countries must double their energy efficiency improvements to 4% annually from now until 2030 to limit global warming to 1.5°C above pre-industrial levels and achieve net zero emissions by 2050 (IEA, 2023). This effort would lead to a 10% reduction in projected energy demand for 2030 compared to 2022 and will require participation from different actors in society such as policymakers, governments and industries (IEA, 2023). Previous studies have indicated that the emissions originating outside of company’s boundaries can be higher than those originating directly from their own operations (Meinrenken et al., 2020; Gopalakrishnan, 2022). The report Net-Zero Challenge: The Supply Chain Opportunity (World Economic Forum, 2021) states that the decarbonization of the supply chain will be essential for companies to achieve ambitious climate goals (World Economic Forum, 2021). Particularly, industrial companies will play an important role in this process. Companies will need to reduce not only their direct greenhouse gases (GHG) emissions (scope 1 and 2) but also the emissions from the entire supply chain (scope 3) (CDP, 2020).
So far, most of the large companies, usually focal companies in a supply chain, have concentrated on the reduction of emissions connected to their operational control (scope 1) and from purchased energy (scope 2), while the indirect emissions (scope 3) have been a challenge (Farsan et al., 2018; Giesekam et al., 2021; Stenzel and Waichman, 2023). Scope 3 includes all the activities outside the boundaries of the focal company and is divided into two parts (Figure 1): upstream emissions, which include the emissions from all activities, from material extraction to those of the focal company, and downstream emissions, which consist of all emissions from the focal companies and those of the end customer (GHG Protocol, 2011). As upstream supply chain emissions can be more than ten times larger than direct emissions, the establishment of targets to reduce upstream scope 3 emissions is becoming an essential part of business practice (CDP, 2020). Companies can drive decarbonization across the entire supply chain by using their influence to support and put pressure on suppliers. For instance, the science-based targets (SBTi) have proposed a framework to create a strategy to engage suppliers in establishing targets to reduce GHG (Farsan et al., 2018).
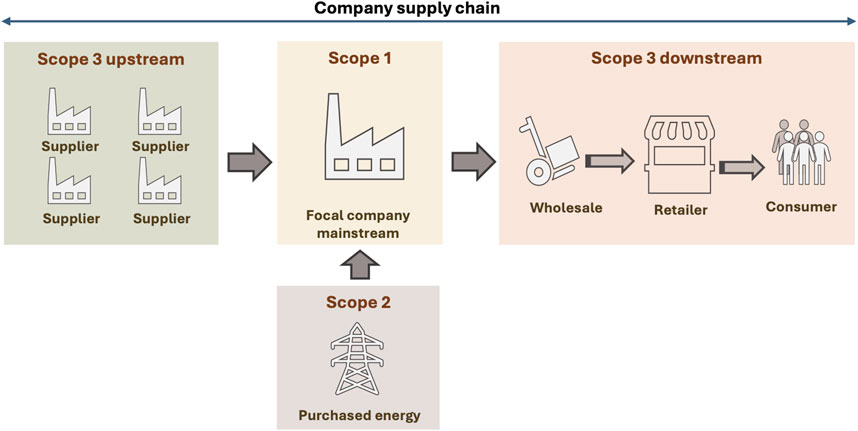
Figure 1. Emissions from a focal company perspective, based on the GHG Protocol (GHG Protocol, 2011) and how they are related to a supply chain.
Implementing energy efficiency is one of the most cost-effective ways to reduce CO2 emissions (IEA, 2022). In 2022, the industry sector was responsible for emitting 9.0 Gt of CO2, representing a quarter of the total CO2 emissions globally. It was also responsible for consuming 37% of global energy use, increasing by 4% compared to 2002 (IEA, 2023). Improving energy efficiency within industries can contribute not only to reducing the industries’ environmental impact but also to improving the companies’ profitability (Johansson and Thollander, 2018), since increased energy prices can affect the companies’ competitiveness in the market (Marchi and Zanoni, 2017; Johansson and Thollander, 2018). Marchi et al. (2018) proposed a model to support investors in evaluating how a financial collaboration between members of a supply chain can overcome the energy efficiency barriers in companies with low energy efficiency performance. A means to improve energy efficiency is through energy management (EnM). EnM is the implementation of both energy efficiency technology measures and the management of the use of these technologies, which has the potential to significantly increase the potential for energy efficiency in a company (Backlund et al., 2012b). Marchi and Zanoni (2017) carried out a literature review on how energy performance is integrated into supply chain management (SCM). Their findings showed that a limited number of studies have integrated energy efficiency into SCM, and most of them were focused on cost reduction when introducing energy efficiency into the assessment of the supply chain performance (Marchi and Zanoni, 2017). Their review contributes with knowledge about energy efficiency measures and the related decision-making processes in supply chain design and management, both upstream and downstream, with a special emphasis on downstream activities and transportation and logistics. However, there is also a need to understand the relationship between focal companies and their suppliers, and how focal companies approach energy management in their upstream supply chain.
This reveals a knowledge gap in how the implementation of energy efficiency in a supply chain can contribute to speeding up the decarbonization of the upstream supply chain and the industrial sector as a whole. To address this knowledge gap, a systematic literature review (SLR) was carried out aiming to understand how previous research in the field of supply chain management approached energy efficiency in the upstream supply chain and how energy efficiency and EnM are incorporated into the sustainability assessment of an upstream supply chain.
This review is structured as follows: Section 2 presents a theoretical framework; Section 3 presents the methodology of the SLR; Section 4 presents the findings of the SLR regarding how energy is approached in an SCM; Section 5 discusses the results; followed by Section 6, with the conclusions and limitations.
2 Theoretical framework
2.1 Supply chain and sustainability
In the literature, there are different definitions used for SCM. Giunipero and Denslow (2022) made a list with several definitions. One of the definitions, which will be used in this study, is the one from Lambert and Cooper (2000) and Giunipero and Denslow (2022). They defined SCM as the management of a network of companies across the flow of a product from material extraction to final customers (Lambert and Cooper, 2000; Giunipero and Denslow, 2022). These networks can be complex as they involve the management of the relationships between different companies (Giunipero and Denslow, 2022). Effective management of these networks is crucial to achieving competitive advantage and increasing profitability, and an important area of research focuses on identifying which members within these networks are essential for the business and for determining optimal strategies for their management (Kraljic, 1983; Lambert and Cooper, 2000; Lovell et al., 2005).
Hence, managing the performance of the entire supply chain is key for a business to succeed (Lambert and Cooper, 2000). In recent years, sustainability has become an important part of SCM. Driven by the growing pressure from environmental regulations and customer expectations, companies have increasingly integrated environmental strategies into SCM. In the literature, there are different terminologies when sustainability is incorporated into a supply chain: for instance, green supply chain management (GSCM), sustainable supply chain management (SSCM), and low carbon supply chain management (LCSCM). Recently, circular supply chain management (CSCM) has also appeared, since the attention to the end-of-life of the products has increased (Geissdoerfer et al., 2018; Cui et al., 2024).
The concept of GSCM emerged in the 1990s and gained more attention at the beginning of the 2000s as companies sought to reduce their environmental impact (Hervani et al., 2005; Srivastava, 2007). In the literature, there are different definitions of GSCM (Hervani et al., 2005; Srivastava, 2007; Gawusu et al., 2022). Srivastava (2007) defined GSCM as the integration of environmental thinking into all supply chain processes, from material selection to end-of-life product management, aiming to reach a balance between economic and environmental performance. This enables companies to maintain competitiveness in the market and meet regulatory and customer expectations (Srivastava, 2007; Gawusu et al., 2022). In the SSCM, the three dimensions of sustainability are incorporated, giving attention also to the social dimension. In LCSCM the goal is to minimize the carbon footprint in the supply chain activities (Shaharudin et al., 2019). The focus is the quantification of the carbon footprint and GHG emissions from all the supply chain activities without taking into consideration other environmental aspects (Damert et al., 2018).
According to Tuni et al. (2018), when incorporating sustainability in a supply chain, the main activities studied are the environmental performance, the selection and evaluation of suppliers, and the optimization of the supply chain design (Tuni et al., 2018). In fact, there is extensive literature focusing on the implementation and evaluation of the environmental performance of GSCM (Hervani et al., 2005; Srivastava, 2007; Olugu et al., 2011; Min and Kim, 2012; Tuni et al., 2018; Tseng et al., 2019; Gawusu et al., 2022), SSCM (Seuring and Müller, 2008; Ahi et al., 2016; Das, 2017; Dahlmann and Roehrich, 2019) and LCSM (Shaharudin et al., 2019). Likewise, a wide range of articles analyze and develop analytical models and frameworks to evaluate and assess the environmental performance of the upstream suppliers (Sinha and Anand, 2017; Tuni et al., 2018; Fallahpour et al., 2021).
Even though there are several studies that have developed different methods to evaluate the environmental performance of the suppliers, there is still a lack of standards regarding environmental key performance indicators (KPIs) adopted to measure it. In a review paper, Tuni et al. (2018) identified that there is a variation in the indicators adopted by companies when it comes to environmental performance in GSCM which makes it difficult to benchmark the suppliers’ performance over time. In these studies, Tuni et al. (2018) found that different environmental performance indicators which are related to carbon emissions and natural resources are used in frameworks: water usage, use of materials, use of recycled resources, and land use are the most frequent. KPIs related to energy are less frequent, even though, when energy is mentioned, the most common indicators used are energy use, while energy efficiency and renewable energy are less common.
2.2 Energy efficiency in industry
Even though energy efficiency measures can lead to strategic cost reductions and offer a cost-effective way to reduce GHG emissions, they are not always implemented due to various barriers (Fleiter et al., 2011; Backlund et al., 2012b; Johansson and Thollander, 2018; Thollander et al., 2020). This is called the energy efficiency gap, which is the difference between the potential for energy efficiency and what de facto is implemented (Palm and Thollander, 2010). EnM is the implementation of systematic activities and routines aiming to continuously reduce a company’s energy use and its related energy costs (Schulze et al., 2016). In EnM the deployment of new technologies is not the only way to reduce energy use. By establishing consistent routines, employees can effectively manage processes in a more structured manner that enables companies to constantly identify inefficiencies in equipment, optimize energy systems, and evaluate the technology’s performance (Backlund et al., 2012a). Thollander and Palm (2010) identified a few successful factors for the implementation of EnM (Palm and Thollander, 2010). Later, Johansson and Thollander (2018) presented the ten factors for successful in-house EnM, showing that full support from top management to implement in-house energy management activities and having a long term energy strategy, preferably with quantified goals, are the two most important factors (Johansson and Thollander, 2018).
In the last decades, several articles studied the implementation of in-house energy efficiency measures in large industrial companies (Lawrence et al., 2019; Andersson, 2020). However, small and medium-sized enterprises (SMEs), which are a significant proportion of suppliers to large industrial companies, usually do not have the resources to implement EnM in their companies (Jalo et al., 2021a). Frequently, SMEs have a lack of economic resources, time, knowledge, and awareness to implement energy efficiency (Marchi and Zanoni, 2017; Jalo et al., 2021a).
Previous research has shown that an energy management system (EnMS) can be an effective tool for implementing energy efficiency in-house in industrial companies (Johansson and Thollander, 2018; Sannö et al., 2019). The standard ISO 50001 provides a guideline for the activities that should be implemented in EnM (Schulze et al., 2016; International Standard Organization, 2018). An important first step to implementing EnM practices involves conducting an energy audit (Thollander et al., 2020), which comprises a systematic examination of a company’s energy use, aiming to identify potential measures for improvements (Johansson and Thollander, 2018). Energy audits help industries become more aware of the benefits of energy efficiency measures by quantifying energy usage and promoting knowledge about which measures can be implemented (Andrei et al., 2021). In energy audits, the energy use of different processes is evaluated to identify key areas for improvement. Establishing energy KPIs for each process, e.g., KPIs based on ISO 50006 (International Standard Organization, 2023), is crucial to understanding which process uses most energy and should be targeted for implementing energy efficiency measures (EEMs) (Johnsson et al., 2019). Several previous studies analyzed energy end use (EEU) on process levels in different industry sectors (Thollander et al., 2015; Johnsson et al., 2019). Former studies have also presented taxonomies for different manufacturing industries, which facilitates benchmarking (Andersson et al., 2018a), as in some sectors, processes may vary from plant to plant (Andersson et al., 2018a; Johnsson et al., 2019).
2.3 Energy efficiency in supply chain management
Implementing energy efficiency and energy-saving strategies in SCM is a crucial step in reducing dependency on fossil fuels and, consequently, cutting down GHG emissions (Marchi and Zanoni, 2017). Moreover, this will guarantee energy supply security by cutting energy demand in manufacturing, leading to fewer resources needed as energy sources. In supply chains in the manufacturing industry, both focal companies and suppliers can be highly energy-intensive industries. Thus, improving energy efficiency in the industrial sector is an important step in decarbonizing supply chains.
However, there is a scarcity of studies that have investigated the opportunities for implementing EEMs in supply chains. Marchi et al. (2018) developed a supply chain model that evaluates the impact of financial collaboration among a focal company and its suppliers when the focal company has access to capital and lower interest rates. The results indicate that it is more beneficial for the focal company (buyer) to invest in improving the energy efficiency of its partner (supplier) than investing in-house, because this can enhance the energy performance of the entire supply chain at a lower cost (Marchi et al., 2018).
In another review, Marchi and Zanoni (2017) categorized and reviewed literature that integrated energy performance into SCM, focusing on how the benefits introduced through energy efficiency measures are quantitatively or qualitatively approached. Their results show that most of the studies with a quantitative approach focus on the cost of the energy flow as a parameter in the performance of the supply chain. In the studies with a qualitative approach, nevertheless, energy performance is considered as an indicator in the evaluation of the performance of GSCM and SSCM, showing that energy can be an important indicator in the performance of the supply chain and the decision-making process. The results also reveal a lack of standards for how energy issues should be measured, and the potential environmental and economic effects that the implementation of energy efficiency practices could have on the entire supply chain. In these studies, all types of industries and all activities in a supply chain were included in the analysis, i.e., upstream and downstream including transportation and logistics activities (Marchi and Zanoni, 2017). However, most of the articles found by Marchi and Zanoni (2017) analyzed energy efficiency measures mainly in downstream activities, and transportation and logistics.
3 Methodology
The methodology used was an SLR based on the work of Durach et al. (2017). Durach et al. (2017) have developed a guideline for adapting a SLR methodology from medical studies to be used in the field of SCM, which has then been used in several previous review studies in this field, see, e.g., (Aloui et al., 2021; Renna, 2024). In our review, the results from the search string have shown that the sample of articles was strongly dominated by those published in the SCM field requiring the use of a methodology which was adapted specifically to be used in this field. According to Durach et al. (2017) it is important to make adaptations when using SLR in different disciplines, since every field has an idiosyncrasy and needs a different methodology in the process of paper selection and in the synthesis of the literature. Studies in the SCM field have four specific characteristics which impose challenges regarding accuracy and transparency in the construction of a review (Durach et al., 2017).
The first characteristic is the theoretical boundary, since different studies use different theoretical lenses. The second characteristic is the different units of analysis, as the entity studied in a supply chain can vary from studying only one manufacturer or supplier to a whole supply chain. The third characteristic is the variation of the source of data, since data can be collected in different ways, for instance, from one entity or a group of entities. The fourth characteristic relates to the study context, for instance, geographic location, period, culture, shareholders, and industry sector (Durach et al., 2017). The six steps proposed by this guideline were applied in this research and will be described below (Figure 2).
Step 1. Formulate the research question. This article aims to explore the intersection between SCM and energy efficiency and/or EnM. Then, the research question formulated is: How are energy efficiency and EnM incorporated in previous studies in the SCM field?
Step 2. Determine inclusion and exclusion criteria. The inclusion and exclusion criteria were defined (Table 1). In SCM studies, the unit of analysis can vary significantly, varying from upstream to downstream activities, and in the actors involved (Nguyen et al., 2022). In this study, the unit of analysis that was examined was the focal company’s management of their upstream suppliers. Articles which studied both upstream and downstream activities in supply chains were included if they focused on upstream suppliers. All papers that analyzed only the downstream activities were excluded as well as papers which focused on the transportation between suppliers and focal company, Scope 2, or digitalization. It was also determined to only include manufacturing companies (Table 1).
Step 3. Retrieve a baseline sample of articles. The online databases Scopus and Web of Science were used in the search process to identify relevant papers in the field of SCM and energy efficiency/EnM. The search string used (“green supply chain” OR “sustainable supply chain” OR “circular supply chain”) AND (“energy” OR “climate”) is based on the research aim and research questions and was searched for in article titles, abstracts, and keywords. Original articles written in English and published up until 4 April 2024, were included.
Step 4. Apply the inclusion/exclusion criteria from step two. The first screening consists of reading titles and abstracts. If the titles and abstracts do not fit in the inclusion criteria, these articles were excluded. However, if titles, keywords, and abstracts were vague, the entire text was briefly analyzed. As the sample obtained had a variety of units of analysis, sources of data, and study context, it was decided to focus solely on how energy is approached in the papers, rather than on the supply chain characteristics. In this screening, 455 articles were excluded as they were out of the inclusion criteria. After reading the remaining 150 papers in full, 18 were selected for analysis (Figure 3). (See Supplementary Table S1A for the complete list of the included papers).
Step 5. Synthesize the articles. By applying thematic analysis, the 18 articles were inductively aggregated into thematic categories which were based solely on how energy is approached when studying upstream the supply chain. Papers were read three times to understand the similarities between them, as these papers study different units of analysis, different sources of data, and contexts. The categories answer the research question formulated in Step 1.
Step 6. Reporting the results of the SLR. The categories defined by using thematic analysis are reported and analyzed in the results section and then discussed in the discussion section.

Figure 2. Description of the steps to conduct the systematic literature review adapted from Durach et al. (2017).
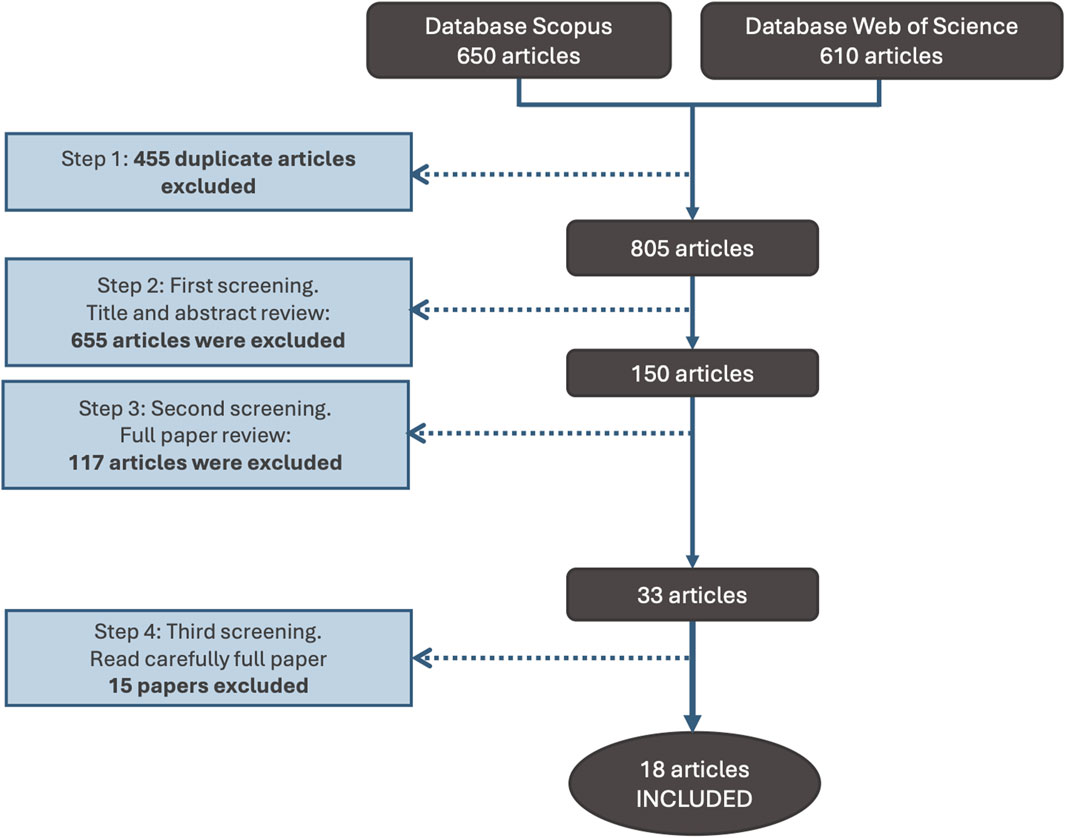
Figure 3. Steps in the process of conducting the SLR based on Durach et al. (2017) and showing the papers selected.
4 Results
Analyzing literature in the field of SCM is complex as research findings may vary depending on how data was gathered and collected (Durach et al., 2017). The articles selected in this review have used different methods, which may have influenced their findings—for example, some studies have used qualitative studies based on case studies or surveys and others have used theoretical conceptualization (e.g., frameworks or simulation models). Moreover, the articles studied different sectors in the manufacturing industry and some focused on both downstream and upstream activities, while others only studied upstream activities (Supplementary Table S2A). Despite this diversity from a SCM perspective, and from analyzing these papers from an energy perspective, the articles can be inductively classified based solely on how energy is approached in the upstream supply chain regardless of which unit or sector they are studying. The categories developed are 1) Carbon emission from energy use; 2) Total energy use; and 3) Energy management (Figure 4).
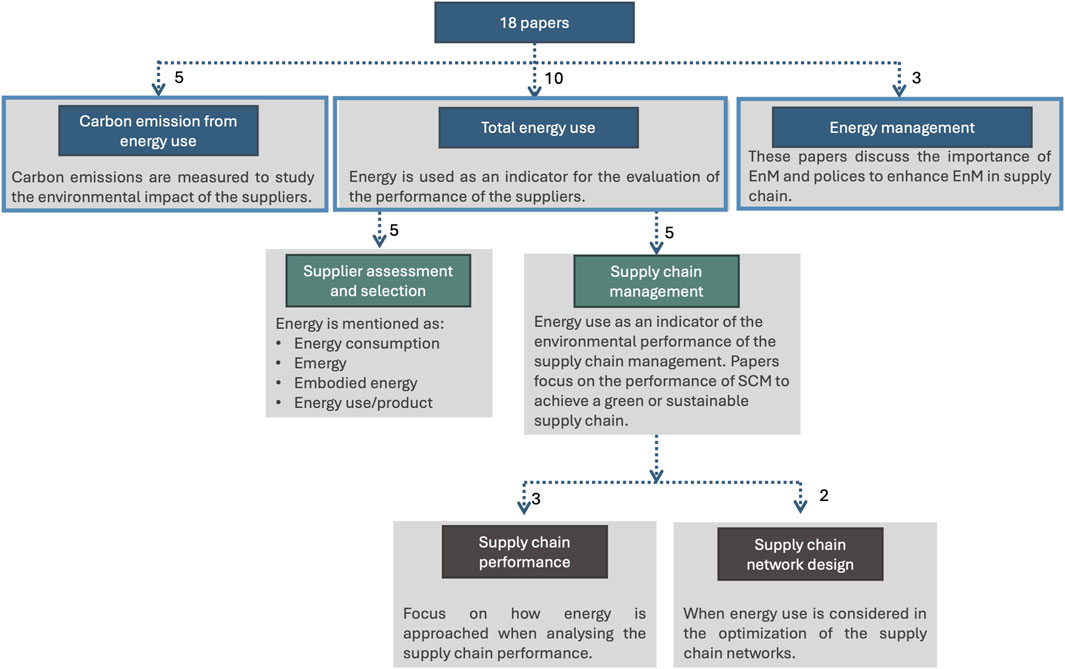
Figure 4. Categorization of the 18 selected articles. The number of papers for each category is indicated.
In summary, the results revealed that in the existing SCM literature, energy is only used as an environmental indicator. The findings for each category are described below.
4.1 Carbon emission from energy use (carbon management)
Carbon emissions are measured to analyze the environmental impact of upstream suppliers. Generally, carbon emissions, and carbon footprint are used as common indicators to evaluate the environmental impact of the supply chain. In fact, in the second screening of this review, it was observed that a vast number of studies estimate or calculate carbon emissions or the carbon footprint of supply chains (Tseng and Hung, 2014; Fallahpour et al., 2020; Maeno et al., 2022) without approaching the carbon emissions from suppliers’ energy use, or at least do not specify how energy is included in the calculation. The five articles selected for this category have studied the carbon emissions of an upstream supply chain by focusing on the emissions from energy use. In these studies, different methodologies have been used, for instance quantitative methods such as mathematical modeling (Sarkar et al., 2018), multi-region input-output (MRIO) models (Kucukvar et al., 2016), conceptual framework (Montoya-Torres et al., 2015), and qualitative methods such as interviews and document analysis (Lee and Cheong, 2011). Case studies are usually applied to the models to validate the outcomes of the methods (Lee and Cheong, 2011; Montoya-Torres et al., 2015; Sarkar et al., 2018).
These models can also simulate different scenarios regarding energy use by applying sensitivity analysis (Sarkar et al., 2018), which is a common method in the SCM field. For example, two studies have simulated what could happen if suppliers use more renewable energy instead of fossil fuels. Sarkar et al. (2018) showed that by increasing the use of solar energy (Photovoltaics, PV), carbon emissions and energy costs could be reduced while the total cost of production could slightly increase due to the initial investment in the PV system. In the long term, however, the cost of running the PV systems could be lower than buying electricity. Kucukvar et al. (2016) studied 16 different sectors in Turkey, revealing that, in most sectors (75% of those studied), the upstream supply chain, on average, contributes with more than 80% of the total energy use in the supply chain, whereas the contribution of downstream activities (transport, warehousing, and retail) is very low. The carbon footprint contribution follows a similar trend as the contribution to the total carbon emissions of the upstream supplier is found to be at least 80% for most manufacturing sectors, except for four sectors in which the onsite carbon emissions are higher. The results also revealed that when considering the three supply chain phases (upstream, onsite manufacturing, and downstream activities), some sectors with high energy use in the upstream phase exhibit lower upstream carbon emissions. This suggests that analyzing carbon emissions from energy use alone is not sufficient, as it may overlook sectors which have low carbon footprints but high final energy use. Furthermore, most of the frameworks and case studies used data on total energy use and carbon emissions from databases without studying the particularities of the suppliers’ processes. For instance, Kucukvar et al. (2016) used data from the World Input-Output Database (WIOD) (which is not active anymore) and Montoya-Torres et al. (2015) used total energy used in the facilities and applied the tools developed by GHG Protocol (WBCSD, 2004). Obtaining total energy use and carbon footprint based on different databases can influence the results by giving different values when calculating the total energy use or carbon footprint/emission, which hinders the comparison between different studies. Montoya-Torres et al. (2015) highlight, for example, the difficulties in obtaining data from outsourced activities in a supply chain. Moreover, Kucukvar et al. (2016) show that different sectors can have different results regarding total energy use and carbon emissions in the three supply chain phases (i.e., upstream, onsite, downstream), revealing the importance of considering the characteristics of the facilities studied.
Nevertheless, these models do not investigate what opportunities suppliers could have to implement EEMs before investing in renewables, which could be a more cost-effective way of reducing carbon emissions upstream. One reason can be that most of these models do not consider the differences in the supplier’s processes and do not study the opportunities these suppliers have in implementing in-house EEMs. Lee and Cheong (2011) studied carbon management in SCM to identify and measure the carbon footprint of the first-tier suppliers in an automobile company (Lee and Cheong, 2011). Carbon emission for each process was estimated; however, the energy carrier and energy source for each process were not specified, as the inputs for the carbon emission calculations were mainly based on the total consumption of different types of fossil fuels. Carbon management in a supply chain is a step forward to decarbonize supply chains; however, more studies are needed. Developing a carbon footprint measurement and evaluation system in the supply chain offers a track record for enhancing carbon but does not give the total picture of how companies can reduce their energy use, which will cost-effectively reduce carbon emissions. As Kucukvar et al. (2016) have shown, it might not be enough to analyze energy use by relying on only carbon emissions.
Helo et al. (2024) calculated the CO2 emissions of a product using life cycle assessment (LCA), which considers different scenarios relating to suppliers’ location. Their findings reveal that the total CO2-equivalent emissions of a product change depending on each supplier’s geographical location, even when the suppliers use the same amount of energy. This indicates that the type of energy source of each supplier, which for electricity depends upon the energy mix of each country, influences the overall CO2-equivalent emissions of a product (Helo et al., 2024).
The results of these studies indicate that it is important not only to calculate CO2 emissions in isolation, but also to explore other additional factors such as the geographical locations of suppliers and their specific conditions (e.g., energy source, company size, and turnover), as these factors significantly impact total energy use and carbon footprint.
4.2 Total energy use
Articles that belong to this category include total energy use (mostly referred to as energy consumption) as an environmental indicator in the assessment and in the selection of the suppliers (Kara and Ibbotson, 2011; Kumar et al., 2017; Tian and Sarkis, 2020; Ghosh et al., 2022a; 2022b), or in the evaluation of the environmental performance of the supply chain (Tognetti et al., 2015; Wang et al., 2016; Pinto, 2020; Soleimani et al., 2022; Althaqafi, 2023).
4.2.1 Supplier assessment and selection
In the last years, companies have been assessing the environmental work of their suppliers when selecting them or when assessing their performance. Ghosh et al. (2022a) have done a literature review which reveals that the “use of renewable energy” is not explored when modeling the implementation and evaluation of GSCM. Ghosh et al. (2022a) wrote a review which also reveals that “use of renewable energy”, and “total energy consumption” are rarely used in models for supplier selection (SS).
Most papers in this category focus mainly on developing a model for supplier assessment in order to implement a GSCM (Ghosh et al., 2022a; 2022b) or an SSCM (Kumar et al., 2017). These papers focus on defining which parameters or dimensions should be used to support focal companies in selecting and assessing the most sustainable suppliers, including energy as one of the criteria. In these articles, energy was approached with different metrics such as total energy consumption (Ghosh et al., 2022b; 2022a), energy consumption/product (Kumar et al., 2017), emergy (Tian and Sarkis, 2020) or embodied energy (Kara and Ibbotson, 2011). These parameters are typically used in models developed for supplier assessments.
In literature, the development of models to carry out the selection and assessment of suppliers is common. In recent years, the focus has been on including environmental parameters in these models to evaluate the sustainable performance of suppliers. Due to the complexity of supplier selection, it is common to use a multi-criteria decision-making (MCDM) approach, as these types of assessments include several parameters. By using MCDM, it is possible to combine different environmental parameters and weigh them, as many different alternatives can be considered and simulated (Ghosh et al., 2022a). Generally, a case study can be applied to these methods to evaluate the suitability of the models. Kumar et al. (2017) have used Fuzzy AHP and fuzzy multi-objective linear programming and applied it in a case study by examining a multinational automobile company. In this model, the three dimensions of sustainability were taken into consideration, and energy is approached as energy use per product based on average values for each company. Ghosh et al. (2022a) employed decision-making models such as COPRAS, GRA, and TOPSIS to propose a framework to evaluate suppliers’ organizations according to their environmental performance. Through the application of these methods, researchers analyzed and ranked different environmental criteria to determine their relevance in implementing GSCM and selecting sustainable suppliers. Their results show that total energy use can be an important parameter (Kumar et al., 2017; Ghosh et al., 2022b; 2022a).
Apart from MCDM, supplier assessment can also be made by using other methods. Tian and Sarkis. (2020) have used emergy accounting (EMA) as a tool to benchmark the environmental performance of three suppliers in a GSCM. They used a hypothetical example with three suppliers which manufacture water bottles to a focal company located in Shanghai. According to the authors, the strength of emergy accounting lies in its capacity to recognize nature’s contribution to economic systems, as conducting an emergy analysis enables a company to accurately identify the consumption of natural resources throughout the entire process. The disadvantage of using emergy, however, is that it can have uncertainties in the data related to materials, as it is difficult to trace all this information. Kara and Ibbotson (2011) analyzed the embodied energy using LCA software and data regarding materials and electricity generation from different data sources. Their study was a case study of an Australian roofing system company investigating different supply chain scenarios by calculating embodied energy with the aim of understanding which suppliers could produce the least emissions in the upstream supply chain. The suppliers were in different parts of the world and used different energy sources in their facilities and transportation. The results revealed that the location of the suppliers can influence the embodied energy, as each location uses different sources of electricity generation (Kara and Ibbotson, 2011).
4.2.2 Supply chain management
In this category, the articles approached energy in different supply chain processes and did not focus on calculating total energy use as the previous group had, but rather mentioned energy use as an important dimension in SCM. Some focus on the environmental performance of the supply chain (Wang et al., 2016; Pinto, 2020; Althaqafi, 2023) while others on the optimization of the supply chain network (Tognetti et al., 2015; Soleimani et al., 2022). These two groups of papers are described below.
4.2.2.1 Supply chain performance
In this category, the three articles studied the environmental performance of the supply chain. Pinto (2020) interviewed eight Portuguese companies and demonstrated that energy use stands out as a significant performance indicator when identifying the most crucial green practices, alongside water consumption, air emissions, and CO2 emissions (Pinto, 2020). Wang et al. (2016) analyzed how supply chain inefficiencies can affect energy use, concluding that, by avoiding excess inventory and overproduction, energy use can be reduced not only in the retail system but also in the production in the upstream supply chain. They emphasize the relevance of avoiding inefficiencies in the supply chain by considering energy used in both upstream and downstream activities, as it reduces the embodied energy of the product. Althaqafi (2023) developed a framework to rank the green practices in a GSCM for the manufacturing of electrical vehicles (EV), in which energy efficiency in the manufacturing process is considered an important practice to improve the performance of the GSCM in the manufacturing of EVs (Althaqafi, 2023). His study was the only one in this category that included energy efficiency as an important factor in achieving a GSCM.
4.2.2.2 Supply chain network design
Here, the two articles studied the optimization of supply chain network design, which involves two levels of decision-making. The initial level of decision concentrates on configuring the network by optimizing facility numbers and selecting optimal locations. The second level of decision optimizes the utilization of the network structure by allocating customer demand to various facilities and planning transportation strategies for each route (Yu and Solvang, 2020). A supply chain network design can study a network between different suppliers (Soleimani et al., 2022) or a network of facilities of the same company but which are located in different geographical locations (Tognetti et al., 2015). When focusing on the second level of supply chain network design, studies focus mainly on the development of models to optimize transportation between the different locations (suppliers, manufacturers, distribution centers, customers) to reduce total cost, increase responsiveness and reduce carbon emissions (Martí et al., 2015). Hence, the first screening (Step 2 in Figure 3) in this review found only two articles that included energy use at the different facilities when studying supply chain network design. Soleimani et al. (2022) and Tognetti et al. (2015) include energy use from manufacturers to develop a more sustainable supply chain network. Soleimani et al. (2022) propose to include the energy use from manufacturing as a parameter in the supply chain network design optimization models, as the use of renewable energy can improve the results and enhance sustainability in the network design. Tognetti et al. (2015) show that when optimizing the supply network, the facilities’ locations and energy mix do affect the emissions of the supply chain network design. This study emphasizes the impact of considering the energy mix employed in each facility within the supply chain design. While logistics activities such as transport and distances between suppliers or focal companies’ facilities typically exhibit the primary environmental impact, considering the energy mix used in each facility can significantly influence the environmental performance of the supply chain network design.
4.3 Energy management
Despite previous research showing that EnM is a cost-effective means to reduce energy use and GHG emissions, EnM is rarely approached when studying sustainability in a supply chain. The results of this review revealed that by reading 150 full papers in Step 3 (Figure 3), only three articles mentioned EnM when studying upstream supply chains. These articles use different methodologies, such as theoretical discussion (de Sousa Jabbour et al., 2017) or qualitative methods by using interviews (Kumar et al., 2022; Kunkel et al., 2022). Even though these articles studied different activities in a supply chain, all of them highlighted the opportunities of including EnM in SCM.
For instance, Kumar et al. (2022) have defined a list of sustainable supply chain indicators to identify the appropriate indicators which can effectively be correlated with the sustainable development goals (SDGs). By reviewing extended literature and by asking consumers and companies in the automotive industry, EnM appeared as the fourth most relevant indicator together with alternative energy sources, which were in seventh place. De Sousa Jabbour et al. (2017) proposed the use of ISO 50001 to complement ISO14001 to improve not only the environmental performance of the supply chain but also the energy performance, as both standards contribute to the reduction of carbon emissions and the demand for natural resources. Kunkel et al. (2022) studied the role of digitalization in the implementation of SSCC (sustainable supply chain collaboration). By studying electronic manufacturing suppliers, the results show that, in this sector, few companies use digitalization to collect real data on energy efficiency, despite recognizing the advantages of using digitalization. These advantages include simplifying and facilitating the communication between focal companies and suppliers, helping the management of energy use by detecting savings potential in suppliers’ plants, measuring processes through sensors, calculating product carbon footprint along the chain, and facilitating the collection of data for energy audits.
5 Discussion and recommendations
Decarbonizing supply chains is crucial to meeting climate goals (CDP, 2020), and energy efficiency will play an important role in this process. Therefore, studying how to reduce emissions by implementing EEMs in supply chains within the manufacturing industry can be crucial for reducing scope 3 emissions. The findings of this SLR reveal that few studies in the SCM field approach energy efficiency when assessing the environmental performance of supply chain activities and upstream suppliers in the industrial sector. Moreover, regardless of how the studies approach sustainability, i.e., GSCM, SSCM, LCSCM, most of the articles that take energy into account consider it as one of the environmental indicators, while energy efficiency and emissions from energy sources are rarely considered in the environmental assessments. Moreover, total energy use serves as input data in the studies, which consider energy to be a significant aspect of the environmental performance of the supply chain. However, companies need to have information on energy use at a process level to identify potential areas of improvement (Andersson et al., 2021) which could overcome the energy efficiency gap described in the theoretical framework. Moreover, approaching energy based only on the total energy use will fail to significantly contribute to the development of an effective strategy for increasing energy efficiency in supply chains and at the same time reduce scope 3 upstream emissions. Particularly, in the industrial sector, companies require a deep analysis of the energy use in individual processes to identify potential EEMs. This is crucial due to the substantial heterogeneity observed in industrial processes, being especially pronounced in SMEs (Andersson et al., 2018b), which can have very specialized processes. Therefore, the development of taxonomies in different manufacturing industries can be important to enable the establishment of KPIs for the individual processes (Andersson et al., 2018a).
The results of this review study also indicate that most of the articles analyzed green supply chains, which emphasize sustainability from both environmental and economic perspectives. Few articles (Kumar et al., 2017; 2022) have studied upstream sustainable supply chains from a social perspective. Kunkel et al. (2022) and Sarkar et al. (2018) studied sustainable supply chains but did not investigate the social perspective further. According to Kumar et al. (2022), companies tend to concentrate on the environmental perspective, as they are driven by environmental policies, while the social perspective receives less attention, as it can be less economically beneficial. This result is in line with a review by Marchi and Zanoni (2017) which indicates that a limited number of studies have integrated energy efficiency in the supply chain management activities and most of them were focused on cost reduction.
Another important result is that when it comes to environmental indicators, some articles in the literature have developed different methods to evaluate the environmental performance of the suppliers (Hervani et al., 2005; Fallahpour et al., 2020; 2021), nevertheless, there is still a lack of standards regarding the environmental parameters and indicators adopted to measure it. The same occurs with energy KPIs, as the articles have used different approaches and methods to assess the energy use of the upstream suppliers and the environmental performance of the supply chain. It aligns with the findings of the review paper by Tuni et al. (2018), which highlights the variability in indicators used by companies to assess the environmental performance of a green supply chain. The findings of this review paper also indicate that most studies focus on the development of frameworks and models which were applied in a case study. However, no studies were found that investigate which current methods companies adopt to assess their upstream suppliers.
Thus, one key conclusion is that standards, energy KPIs, and general approaches to and methods of supply chain EnM need to be explored and developed. Considering that most of the large companies’ suppliers are SMEs (Szczepański, 2021), there is a great opportunity to reduce scope 3 GHG emissions by developing standards that support these upstream suppliers in overcoming the barriers to implementing EEMs, for instance, lack of time, resources and knowledge as identified in previous studies (Jalo et al., 2021a). This will not only reduce the upstream scope 3 emissions from large companies but also increase the profitability of both suppliers and focal companies. Moreover, it will serve focal companies in their effort for increased resilience and reduced risks, as their suppliers, if they become more energy efficient, will be better equipped to handle increased energy prices and grid-related challenges. For example, Mishra et al.’s (2023) study analyzed the adoption of renewable energy technologies in sustainable, closed-loop supply chains as a way to reduce and mitigate the risk of energy interruption in a supply chain (Mishra et al., 2023).
By correlating the findings from this review with the previous knowledge in the field of EnM, the evaluation of the energy performance of the supply chain, and more specifically the performance of the upstream suppliers, could be integrated into the in-house energy management of large companies. Given that EnM can be a means to implement EEMs, Figure 5 presents a conceptual framework of a possible intersection between the implementation of in-house EnM (scope 1 and 2 of the focal company) and the establishment of energy KPIs to be included in the environmental assessment of upstream suppliers in a supply chain (scope 3 of the focal company), which will improve the overall environmental performance of the entire supply chain. Schulze et al. (2016) have identified five components with the respective activities needed to implement an in-house EnM. In this framework, the first step is to carry out an energy audit in order to measure the current energy use in each process and define energy KPIs. Here we suggest that the energy KPIs defined in the in-house EnM could be applied in the evaluation of the energy performance of the upstream supply chain. Thus, more specific energy KPIs, e.g., KPIs defined by ISO 50.006 (International Standard Organization, 2023), could be included in the assessment of an upstream supply chain. Subsequently, in the strategy/planning phase for in-house EnM, when the focal company defines in-house energy policy and energy targets, energy targets for the assessment of their suppliers should also be included. Hence, the evaluation of suppliers’ energy performance can be incorporated as a part of the focal company’s energy strategy, which will consequently contribute to the reduction of scope 3 upstream emission.
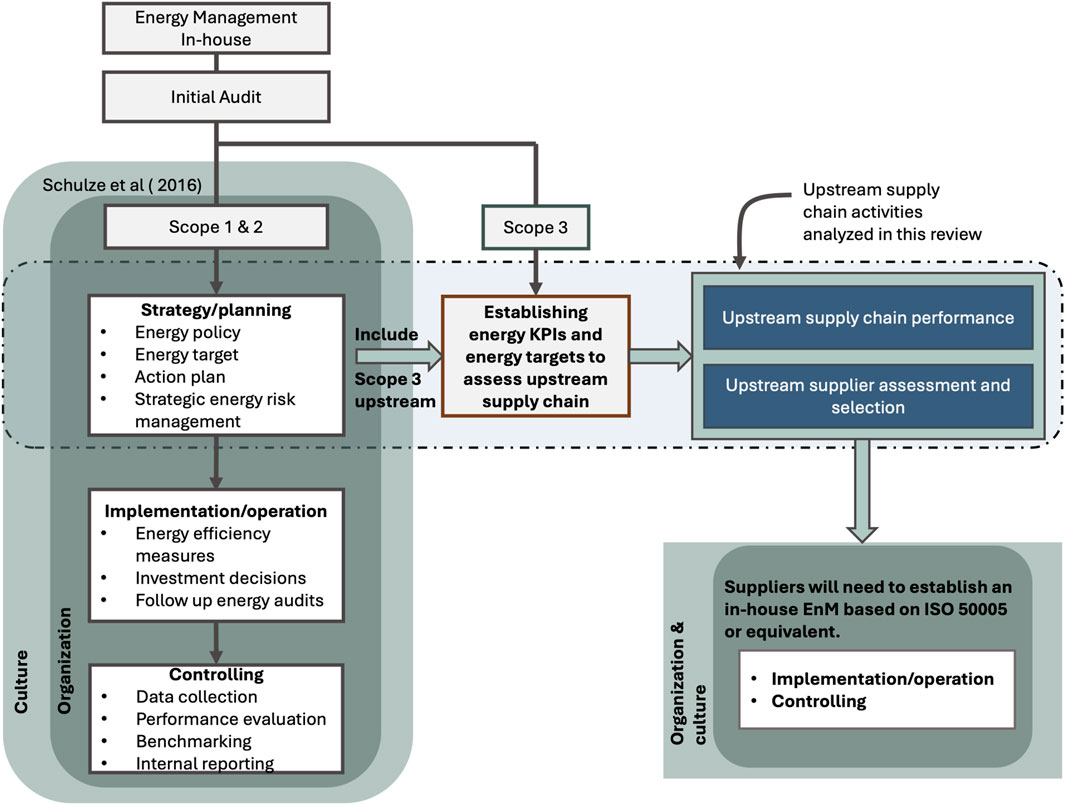
Figure 5. The intersection between in-house EnM and upstream supply chain assessment. The in-house EnM framework developed by Schulze et al. (2016) can be used to include scope 3 in the focal company strategic decision (scope 1 and 2) to reduce energy use and emissions in the upstream scope 3.
To fulfill the focal company request regarding energy KPIs, suppliers need to carry out an energy audit to be able to measure their energy use and report the energy KPIs established by focal companies. This will require an energy audit program for industrial SMEs (Thollander et al., 2014), which can follow the standard ISO 50005 (International Standard Organization, 2022). In this case, the focal company will need to support the suppliers which are SMEs, as previous research has indicated that SMEs can face obstacles in implementing energy measures in their facilities (Johansson et al., 2019; Jalo et al., 2021b; 2021a).
Thus, the focal companies will need to take action to reduce the energy use of their suppliers to reduce their upstream scope 3 emissions. Allocating responsibility for scope 3 emissions to large companies incentivizes them to collaborate with their supply chain partners to identify opportunities for reducing emissions from the entire supply chain (Gopalakrishnan, 2022). Moreover, scope 3 for the focal company is the equivalent of scope 1 for the suppliers, indicating that both companies have the responsibility to cooperate to decarbonize the supply chain. However, previous studies pointed out that focal companies have been facing constraints in receiving emissions information from their suppliers, such as a lack of access and transparency of data from suppliers and a lack of standards for how suppliers report their GHG emissions (Stenzel and Waichman, 2023). This may highlight the importance of building trust and commitment in a buyer–supplier relationship, so suppliers become open to sharing their information.
6 Conclusion and future research
This study provides an overview of how previous studies in the field of SCM approached energy efficiency and EnM when studying upstream supply chains. By conducting an SLR, 18 articles were identified that address energy when studying an upstream supply chain in the manufacturing sector. In the first screening, a wide range of studies focused on carbon emission in the supply chain. Even though carbon emissions are a common indicator in the evaluation of the environmental performance of different activities in a supply chain, few studies have approached the emissions from an energy use perspective. This is a drawback because energy use is the root cause of these emissions and therefore has a significant impact on reducing a company’s carbon emissions.
The scope of this paper is primarily the upstream supply chain in the global manufacturing sector, focusing on how energy is included in SCM, excluding logistic activities such as transport and raw material extraction. Therefore, the result of this review contributes to category 1 in scope 3. It may be argued that, from a supply chain perspective, articles should not be compared as they study different units and different industrial sectors located in different countries, etc. Nonetheless, the focus of this study is to explore how energy efficiency or EnM has been incorporated in previous studies in upstream supply chains, regardless of the industrial sector, country, or company size. Hence, one important area of future research and development could be to study specific industrial sectors, as the characteristics of each sector should be considered. Furthermore, most of the articles investigate only the performance of the first-tier suppliers. In that sense, a broader perspective is needed in the future in which the second-tier and third-tier suppliers are also included to decarbonize the entire upstream supply chain.
Furthermore, the results revealed that studies on SCM focus on manufacturing industry outside Europe, while most of the papers studying EnM focus on Europe. This calls for a global standard that can be applied jointly in different countries. However, more research is called for that investigates the particularities of each country, as they can have different conditions, environmental legislations, and different accessibility of energy supply.
Moreover, despite this study’s limitations, the findings bring to light a significant gap in the existing scientific literature regarding the contribution of the implementation of energy efficiency in the suppliers’ facilities to globally decarbonize upstream supply chains. The contribution of this study can have important implications for practitioners as it highlights the challenge regarding reducing energy use, which will also reduce the demand for natural resources and emissions in scope 3 upstream. Furthermore, it became clear that focal companies will need to take action beyond their facilities to decarbonize the entire supply chain by using their influence to support suppliers and define methods to evaluate and support their suppliers.
Thus, this study can be a first step forward in understanding the challenges and opportunities of including energy efficiency in supply chains. Further research is suggested to speed up the decarbonization of the upstream supply chain, such as:
- Investigate possible strategies to develop the relationship between focal companies and suppliers to include cooperation regarding energy efficiency implementation.
- More studies involving case studies, including energy KPIs to be used, standards, etc. are needed to investigate how energy efficiency strategies could be implemented in an upstream supply chain network and how focal companies and suppliers can work together to reduce energy use and scope 3 emissions.
- The development of a framework that can be used to implement and evaluate EnM in upstream supply chains in which focal companies support their suppliers in the process. In this way, knowledge from the EnM field can be applied in the SCM field.
Author contributions
BX: Conceptualization, Formal Analysis, Investigation, Methodology, Visualization, Writing–original draft, Writing–review and editing. PT: Conceptualization, Funding acquisition, Supervision, Writing–review and editing. PH: Conceptualization, Supervision, Writing–review and editing. MJ: Conceptualization, Funding acquisition, Project administration, Supervision, Writing–review and editing.
Funding
The author(s) declare that financial support was received for the research, authorship, and/or publication of this article. The study has been carried out under the Energy4Supply project financed by the European Commission within the Clean Energy Transition sub-programme of the LIFE Programme and the project Sustainability Assurance of Supply Chains financed by the Swedish Energy Agency project number 52744-1.
Conflict of interest
The authors declare that the research was conducted in the absence of any commercial or financial relationships that could be construed as a potential conflict of interest.
Publisher’s note
All claims expressed in this article are solely those of the authors and do not necessarily represent those of their affiliated organizations, or those of the publisher, the editors and the reviewers. Any product that may be evaluated in this article, or claim that may be made by its manufacturer, is not guaranteed or endorsed by the publisher.
Supplementary material
The Supplementary Material for this article can be found online at: https://www.frontiersin.org/articles/10.3389/fenrg.2024.1425795/full#supplementary-material
References
Ahi, P., Jaber, M. Y., and Searcy, C. (2016). A comprehensive multidimensional framework for assessing the performance of sustainable supply chains. Appl. Math. Model 40, 10153–10166. doi:10.1016/J.APM.2016.07.001
Aloui, A., Hamani, N., Derrouiche, R., and Delahoche, L. (2021). Systematic literature review on collaborative sustainable transportation: overview, analysis and perspectives. Transp. Res. Interdiscip. Perspect. 9, 100291. doi:10.1016/j.trip.2020.100291
Althaqafi, T. (2023). Cultivating sustainable supply chain Practises in electric vehicle manufacturing: a MCDM approach to assessing GSCM performance. World Electr. Veh. J. 14, 290. doi:10.3390/wevj14100290
Andersson, E. (2020) Enabling industrial energy benchmarking Process-level energy end-use, key performance indicators, and efficiency potential. Linköping: Linköping University.
Andersson, E., Arfwidsson, O., and Thollander, P. (2018a). Benchmarking energy performance of industrial small and medium-sized enterprises using an energy efficiency index: results based on an energy audit policy program. J. Clean. Prod. 182, 883–895. doi:10.1016/j.jclepro.2018.02.027
Andersson, E., Dernegård, H., Wallén, M., and Thollander, P. (2021). Decarbonization of industry: implementation of energy performance indicators for successful energy management practices in kraft pulp mills. Energy Rep. 7, 1808–1817. doi:10.1016/j.egyr.2021.03.009
Andersson, E., Karlsson, M., Thollander, P., and Paramonova, S. (2018b). Energy end-use and efficiency potentials among Swedish industrial small and medium-sized enterprises – a dataset analysis from the national energy audit program. Renew. Sustain. Energy Rev. 93, 165–177. doi:10.1016/j.rser.2018.05.037
Andrei, M., Thollander, P., Pierre, I., Gindroz, B., and Rohdin, P. (2021). Decarbonization of industry: Guidelines towards a harmonized energy efficiency policy program impact evaluation methodology. Energy Rep. 7, 1385–1395. doi:10.1016/j.egyr.2021.02.067
Backlund, S., Broberg, S., Ottosson, M., and Thollander, P. (2012a). “Energy efficiency potentials and energy management practices in Swedish firms,” in Summer Study on energy efficiency in industry (eceee 2012) (Arnhem, Netherlands: European Council for an Energy Efficient Economy), 11–14.
Backlund, S., Thollander, P., Palm, J., and Ottosson, M. (2012b). Extending the energy efficiency gap. Energy Policy 51, 392–396. doi:10.1016/j.enpol.2012.08.042
CDP (2020). Transparency to transformation: a chain reaction - CDP global supply chain report 2020. Available at: https://www.cdp.net/en/research/global-reports/transparency-to-transformation (Accessed February 27, 2024).
Cui, L., Wu, H., Lang, X., and Li, Y. (2024). Exploring circular supply chain practices from a dual perspective: using a hybrid method under uncertainty. Int. J. Logist. Res. Appl. 27, 59–82. doi:10.1080/13675567.2021.1983527
Dahlmann, F., and Roehrich, J. K. (2019). Sustainable supply chain management and partner engagement to manage climate change information. Bus. Strategy Environ. 28, 1632–1647. doi:10.1002/bse.2392
Damert, M., Feng, Y., Zhu, Q., and Baumgartner, R. J. (2018). Motivating low-carbon initiatives among suppliers: the role of risk and opportunity perception. Resour. Conserv. Recycl 136, 276–286. doi:10.1016/J.RESCONREC.2018.05.002
Das, D. (2017). Development and validation of a scale for measuring Sustainable Supply Chain Management practices and performance. J. Clean. Prod. 164, 1344–1362. doi:10.1016/j.jclepro.2017.07.006
de Sousa Jabbour, A. B. L., Verdério Júnior, S. A., Jabbour, C. J. C., Leal Filho, W., Campos, L. S., and De Castro, R. (2017). Toward greener supply chains: is there a role for the new ISO 50001 approach to energy and carbon management? Energy Effic. 10, 777–785. doi:10.1007/s12053-016-9478-z
Durach, C. F., Kembro, J., and Wieland, A. (2017). A new Paradigm for systematic literature reviews in supply chain management. J. Supply Chain Manag. 53, 67–85. doi:10.1111/jscm.12145
Fallahpour, A., Wong, K. Y., Rajoo, S., Fathollahi-Fard, A. M., Antucheviciene, J., and Nayeri, S. (2021). An integrated approach for a sustainable supplier selection based on Industry 4.0 concept. Environ. Sci. Pollut. Res. doi:10.1007/s11356-021-17445-y
Fallahpour, A., Wong, K. Y., Rajoo, S., and Mardani, A. (2020). An integrated fuzzy carbon management-based model for suppliers’ performance evaluation and selection in green supply chain management. Int. J. Fuzzy Syst. 22, 712–723. doi:10.1007/s40815-019-00759-y
Farsan, A., Chang, A., Kerkhof, A., Cserna, B., Yan, C., Rangel Villasana, F., et al. (2018) Value chain in the value chain: Best practices in scope 3 greenhouse gas management. Available at: https://sciencebasedtargets.org/resources/files/SBT_Value_Chain_Report-1.pdf (Accessed June 10, 2024).
Fleiter, T., Worrell, E., and Eichhammer, W. (2011). Barriers to energy efficiency in industrial bottom-up energy demand models - a review. Renew. Sustain. Energy Rev. 15, 3099–3111. doi:10.1016/j.rser.2011.03.025
Gawusu, S., Zhang, X., Jamatutu, S. A., Ahmed, A., Amadu, A. A., and Djam Miensah, E. (2022). The dynamics of green supply chain management within the framework of renewable energy. Int. J. Energy Res. 46, 684–711. doi:10.1002/er.7278
Geissdoerfer, M., Morioka, S. N., de Carvalho, M. M., and Evans, S. (2018). Business models and supply chains for the circular economy. J. Clean. Prod. 190, 712–721. doi:10.1016/j.jclepro.2018.04.159
GHG-Protocol (2011). Corporate Value Chain (Scope 3) Accounting and Reporting Standard. World Resources Institute and World Business Council For Sustainable Development.
Ghosh, S., Mandal, M. C., and Ray, A. (2022a). Green supply chain management framework for supplier selection: an integrated multi-criteria decision-making approach. Int. J. Manag. Sci. Eng. Manag. 17, 205–219. doi:10.1080/17509653.2021.1997661
Ghosh, S., Mandal, M. C., and Ray, A. (2022b). Strategic sourcing model for green supply chain management: an insight into automobile manufacturing units in India. Benchmarking 29, 3097–3132. doi:10.1108/BIJ-06-2021-0333
Giesekam, J., Norman, J., Garvey, A., and Betts-Davies, S. (2021). Science-based targets: on target? Sustain. Switz. 13, 1657–1720. doi:10.3390/su13041657
Giunipero, C., and Denslow, L. (2022) Handbook of research methods for supply chain management. Cheltenham, UK: Edward Elgar Publishing, 24–44. doi:10.4337/9781788975865.00008
Gopalakrishnan, S. (2022). The why and how of assigning responsibility for supply chain emissions. Nat. Clim. Chang. 12, 1075–1077. doi:10.1038/s41558-022-01543-x
Helo, P., Mayanti, B., Bejarano, R., and Sundman, C. (2024). Sustainable supply chains – managing environmental impact data on product platforms. Int. J. Prod. Econ. 270, 109160. doi:10.1016/j.ijpe.2024.109160
Hervani, A. A., Helms, M. M., and Sarkis, J. (2005). Performance measurement for green supply chain management. Benchmarking 12, 330–353. doi:10.1108/14635770510609015
IEA (2023). What does doubling global progress on energy efficiency entail? Paris. Available at: https://www.iea.org/reports/energy-efficiency-2023/what-does-doubling-global-progress-on-energy-efficiency-entail (Accessed March 10, 2024).
International Energy Agency, I. (2022). Energy efficiency 2022. Energy Effic. doi:10.1787/679f39bd-en
International Standard Organization (2018) Energy management systems – Requirements with guidance for use ISO 50001.
International Standard Organization (2022) Energy management systems - Guidelines for a phased implementation. ISO 50005:2021).
International Standard Organization (2023) Energy management systems — evaluating energy performance using energy performance indicators and energy baselines ISO 50006. Switzerland.
Jalo, N., Johansson, I., Andrei, M., Nehler, T., and Thollander, P. (2021a). Barriers to and drivers of energy management in Swedish smes. Energies (Basel) 14, 6925. doi:10.3390/en14216925
Jalo, N., Johansson, I., Kanchiralla, F. M., and Thollander, P. (2021b). Do energy efficiency networks help reduce barriers to energy efficiency? -A case study of a regional Swedish policy program for industrial SMEs. Renew. Sustain. Energy Rev. 151, 111579. doi:10.1016/j.rser.2021.111579
Johansson, I., Mardan, N., Cornelis, E., Kimura, O., and Thollander, P. (2019). Designing policies and programmes for improved energy efficiency in industrial SMEs. Energies (Basel) 12, 1338. doi:10.3390/en12071338
Johansson, M. T., and Thollander, P. (2018). A review of barriers to and driving forces for improved energy efficiency in Swedish industry– Recommendations for successful in-house energy management. Renew. Sustain. Energy Rev. 82, 618–628. doi:10.1016/j.rser.2017.09.052
Johnsson, S., Andersson, E., Thollander, P., and Karlsson, M. (2019). Energy savings and greenhouse gas mitigation potential in the Swedish wood industry. Energy 187, 115919. doi:10.1016/j.energy.2019.115919
Kara, S., and Ibbotson, S. (2011). Embodied energy of manufacturing supply chains. CIRP J. Manuf. Sci. Technol. 4, 317–323. doi:10.1016/j.cirpj.2011.03.006
Kucukvar, M., Cansev, B., Egilmez, G., Onat, N. C., and Samadi, H. (2016). Energy-climate-manufacturing nexus: new insights from the regional and global supply chains of manufacturing industries. Appl. Energy 184, 889–904. doi:10.1016/j.apenergy.2016.03.068
Kumar, A., Shrivastav, S., Adlakha, A., and Vishwakarma, N. K. (2022). Appropriation of sustainability priorities to gain strategic advantage in a supply chain. Int. J. Prod. Perform. Manag. 71, 125–155. doi:10.1108/IJPPM-06-2020-0298
Kumar, D., Rahman, Z., and Chan, F. T. S. (2017). A fuzzy AHP and fuzzy multi-objective linear programming model for order allocation in a sustainable supply chain: a case study. Int. J. Comput. Integr. Manuf. 30, 535–551. doi:10.1080/0951192X.2016.1145813
Kunkel, S., Matthess, M., Xue, B., and Beier, G. (2022). Industry 4.0 in sustainable supply chain collaboration: insights from an interview study with international buying firms and Chinese suppliers in the electronics industry. Resour. Conserv. Recycl 182, 106274. doi:10.1016/j.resconrec.2022.106274
Lambert, D. M., and Cooper, M. C. (2000) Issues in supply chain management. Available at: http://www.CLM1.org.
Lawrence, A., Nehler, T., Andersson, E., Karlsson, M., and Thollander, P. (2019). Drivers, barriers and success factors for energy management in the Swedish pulp and paper industry. J. Clean. Prod. 223, 67–82. doi:10.1016/j.jclepro.2019.03.143
Lee, K. H., and Cheong, I. M. (2011). Measuring a carbon footprint and environmental practice: the case of Hyundai Motors Co. (HMC). Industrial Manag. Data Syst. 111, 961–978. doi:10.1108/02635571111144991
Lovell, A., Saw, R., and Stimson, J. (2005). Product value-density: managing diversity through supply chain segmentation. Int. J. Logist. Manag. 16, 142–158. doi:10.1108/09574090510617394
Maeno, K., Tokito, S., and Kagawa, S. (2022). CO2 mitigation through global supply chain restructuring. Energy Econ. 105, 105768. doi:10.1016/j.eneco.2021.105768
Marchi, B., and Zanoni, S. (2017). Supply chain management for improved energy efficiency: review and opportunities. Energies (Basel) 10, 1618. doi:10.3390/EN10101618
Marchi, B., Zanoni, S., Ferretti, I., and Zavanella, L. E. (2018). Stimulating investments in energy efficiency through supply chain integration. Energies (Basel) 11, 858. doi:10.3390/en11040858
Martí, J. M. C., Tancrez, J. S., and Seifert, R. W. (2015). Carbon footprint and responsiveness trade-offs in supply chain network design. Int. J. Prod. Econ. 166, 129–142. doi:10.1016/j.ijpe.2015.04.016
Meinrenken, C. J., Chen, D., Esparza, R. A., Iyer, V., Paridis, S. P., Prasad, A., et al. (2020). Carbon emissions embodied in product value chains and the role of Life Cycle Assessment in curbing them. Sci. Rep. 10, 6184. doi:10.1038/s41598-020-62030-x
Min, H., and Kim, I. (2012). Green supply chain research: Past, present, and future. Logist. Res. 4, 39–47. doi:10.1007/s12159-012-0071-3
Mishra, R., Raut, R. D., Kumar, M., Naik, B. K. R., and Luthra, S. (2023). Renewable energy technology adoption in building a sustainable circular supply chain and managing renewable energy-related risk. Ann. Oper. Res. doi:10.1007/s10479-023-05476-2
Montoya-Torres, J. R., Gutierrez-Franco, E., and Blanco, E. E. (2015). Conceptual framework for measuring carbon footprint in supply chains. Prod. Plan. Control 26, 265–279. doi:10.1080/09537287.2014.894215
Nguyen, G., Kumar, V., and Soares, A. (2022) Handbook of research methods for supply chain management. Cheltenham, UK: Edward Elgar Publishing, 45–70. doi:10.4337/9781788975865.00009
Olugu, E. U., Wong, K. Y., and Shaharoun, A. M. (2011). Development of key performance measures for the automobile green supply chain. Resour. Conserv. Recycl 55, 567–579. doi:10.1016/J.RESCONREC.2010.06.003
Palm, J., and Thollander, P. (2010). An interdisciplinary perspective on industrial energy efficiency. Appl. Energy 87, 3255–3261. doi:10.1016/j.apenergy.2010.04.019
Pinto, L. (2020). Green supply chain practices and company performance in Portuguese manufacturing sector. Bus. Strategy Environ. 29, 1832–1849. doi:10.1002/BSE.2471
Renna, P. (2024). A review of Game theory models to support production planning, Scheduling, Cloud manufacturing and sustainable production systems. Des. (Basel) 8, 26. doi:10.3390/designs8020026
Sannö, A., Johansson, M. T., Thollander, P., Wollin, J., and Sjögren, B. (2019). Approaching sustainable energy management operations in a multinational industrial corporation. Sustain. Switz. 11, 754. doi:10.3390/su11030754
Sarkar, B., Omair, M., and Choi, S. B. (2018). A multi-objective optimization of energy, economic, and carbon emission in a production model under sustainable supply chain management. Appl. Sci. Switz. 8, 1744. doi:10.3390/app8101744
Schulze, M., Nehler, H., Ottosson, M., and Thollander, P. (2016). Energy management in industry - a systematic review of previous findings and an integrative conceptual framework. J. Clean. Prod. 112, 3692–3708. doi:10.1016/j.jclepro.2015.06.060
Seuring, S., and Müller, M. (2008). From a literature review to a conceptual framework for sustainable supply chain management. J. Clean. Prod. 16, 1699–1710. doi:10.1016/j.jclepro.2008.04.020
Shaharudin, M. S., Fernando, Y., Chiappetta Jabbour, C. J., Sroufe, R., and Jasmi, M. F. A. (2019). Past, present, and future low carbon supply chain management: a content review using social network analysis. J. Clean. Prod. 218, 629–643. doi:10.1016/j.jclepro.2019.02.016
Sinha, A. K., and Anand, A. (2017). Towards fuzzy preference relationship based on decision making approach to access the performance of suppliers in environmental conscious manufacturing domain. Comput. Ind. Eng. 105, 39–54. doi:10.1016/J.CIE.2016.12.033
Soleimani, H., Chhetri, P., Fathollahi-Fard, A. M., Mirzapour Al-e-Hashem, S. M. J., and Shahparvari, S. (2022). Sustainable closed-loop supply chain with energy efficiency: Lagrangian relaxation, reformulations and heuristics. Ann. Oper. Res. 318, 531–556. doi:10.1007/s10479-022-04661-z
Srivastava, S. K. (2007). Green supply-chain management: a state-of-the-art literature review. Int. J. Manag. Rev. 9, 53–80. doi:10.1111/j.1468-2370.2007.00202.x
Stenzel, A., and Waichman, I. (2023). Supply-chain data sharing for scope 3 emissions. npj Clim. Action 2, 7. doi:10.1038/s44168-023-00032-x
Szczepański, M. (2021) EPRS | European Parliamentary research Service. Available at: https://www.europarl.europa.eu/RegData/etudes/BRIE/2021/698815/EPRS_BRI(2021)698815_EN.pdf (Accessed August 14, 2023).
Thollander, P., Paramonova, S., Cornelis, E., Kimura, O., Trianni, A., Karlsson, M., et al. (2015). International study on energy end-use data among industrial SMEs (small and medium-sized enterprises) and energy end-use efficiency improvement opportunities. J. Clean. Prod. 104, 282–296. doi:10.1016/j.jclepro.2015.04.073
Thollander, P., Rohdin, P., Rosenqvist, J., Karlsson, M., and Wollin, J. (2020) Introduction to industrial energy efficiency: energy auditing, energy management, and policy issues. doi:10.1016/C2018-0-01452-8
Thollander, P., Zubizarreta Jiménez, R., Morales, I., Kimura, O., Cornelis, E., Karlsson, M., et al. (2014) Energy end-use policies and programs towards industrial SMEs-the case of Japan, Belgium, Spain and Sweden.
Tian, X., and Sarkis, J. (2020). Expanding green supply chain performance measurement through emergy accounting and analysis. Int. J. Prod. Econ. 225, 107576. doi:10.1016/j.ijpe.2019.107576
Tognetti, A., Grosse-Ruyken, P. T., and Wagner, S. M. (2015). Green supply chain network optimization and the trade-off between environmental and economic objectives. Int. J. Prod. Econ. 170, 385–392. doi:10.1016/j.ijpe.2015.05.012
Tseng, M. L., Islam, M. S., Karia, N., Fauzi, F. A., and Afrin, S. (2019). A literature review on green supply chain management: Trends and future challenges. Resour. Conserv. Recycl 141, 145–162. doi:10.1016/j.resconrec.2018.10.009
Tseng, S. C., and Hung, S. W. (2014). A strategic decision-making model considering the social costs of carbon dioxide emissions for sustainable supply chain management. J. Environ. Manage 133, 315–322. doi:10.1016/j.jenvman.2013.11.023
Tuni, A., Rentizelas, A., and Duffy, A. (2018). Environmental performance measurement for green supply chains: a systematic analysis and review of quantitative methods. Int. J. Phys. Distribution Logist. Manag. 48, 765–793. doi:10.1108/IJPDLM-02-2017-0062
Wang, X., Cai, H., and Florig, H. K. (2016). Energy-saving implications from supply chain improvement: an exploratory study on China’s consumer goods retail system. Energy Policy 95, 411–420. doi:10.1016/j.enpol.2016.04.044
World Economic Forum (2021). Net-Zero Challenge: the supply chain opportunity - insight report. Cologny/Geneva. Available at: https://www3.weforum.org/docs/WEF_Net_Zero_Challenge_The_Supply_Chain_Opportunity_2021.pdf (Accessed January 8, 2024).
Keywords: energy management, energy efficiency, green supply chain, sustainable supply chain, scope 3, decarbonization
Citation: Xavier BM, Thollander P, Hilletofth P and Johansson M (2024) Exploring energy management integration into upstream supply chains: a systematic literature review. Front. Energy Res. 12:1425795. doi: 10.3389/fenrg.2024.1425795
Received: 30 April 2024; Accepted: 30 May 2024;
Published: 19 June 2024.
Edited by:
Melike E. Bildirici, Yıldız Technical University, TürkiyeReviewed by:
Tahsin Bakirtas, Sakarya University, TürkiyeLeonor Patricia Güereca, Universidad Nacional Autonoma de Mexico, Mexico
Copyright © 2024 Xavier, Thollander, Hilletofth and Johansson. This is an open-access article distributed under the terms of the Creative Commons Attribution License (CC BY). The use, distribution or reproduction in other forums is permitted, provided the original author(s) and the copyright owner(s) are credited and that the original publication in this journal is cited, in accordance with accepted academic practice. No use, distribution or reproduction is permitted which does not comply with these terms.
*Correspondence: Bruna Maria Xavier, bWFyaWEueGF2aWVyQGxpdS5zZQ==