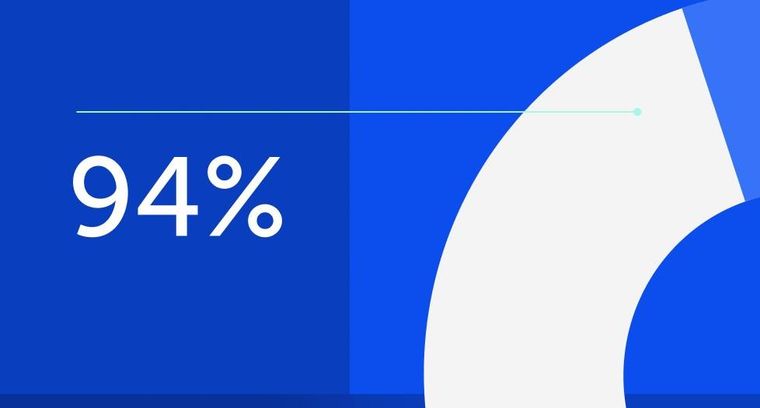
94% of researchers rate our articles as excellent or good
Learn more about the work of our research integrity team to safeguard the quality of each article we publish.
Find out more
REVIEW article
Front. Energy Res., 11 June 2024
Sec. Energy Efficiency
Volume 12 - 2024 | https://doi.org/10.3389/fenrg.2024.1424059
Sand production is one of the challenges facing the oil industry. This paper reviews the latest research advances in chemical sand control and aims to provide a reference for related researchers. Firstly, the commonly used chemical sand control materials are introduced. Second, recent advances in chemical sand control are reviewed, including materials, methods, and processes. Third, laboratory methods for sand control research are presented. Finally, the gaps and challenges of chemical sand control materials are pointed out, and possible future directions for chemical sand control methods are envisioned.
With oil and gas production, sand grains in the reservoir are dislodged by fluid flushing and transported to the wellbore, a phenomenon known as Sand production. Sand production is more severe in unconsolidated or weakly consolidated reservoirs (Ahad et al., 2020). With the development of conventional oil and gas reservoirs and the test recovery of gas hydrates, effective sand control is a key issue (Wu et al., 2021; Ding et al., 2022; Zhang et al., 2022; Luo et al., 2023; Wang et al., 2023). During the extraction of weakly consolidated reservoirs, too fast oil production rate will increase the structural stress of the reservoir rock, and the fine sand grains will be pulled out, eventually leading to a sand production problem (Zhu et al., 2017; Chen WL. et al., 2022). Sand production is a problem in many reservoirs, and oilfields spend a lot of money each year on sand control (Saghandali et al., 2022).
Sand production during oil and gas extraction can lead to many problems. Sand grain transport can lead to reduced reservoir permeability (Deng et al., 2019). Sand grain transport near the wellbore can cause a decline in oil and gas production. Sand production is also a challenge for the safe operation of the equipment (Ma et al., 2020; Bharadwaj et al., 2021; Jin et al., 2021). Sand grain can flush downhole and ground pipelines and shorten their service life. Sand grains can also damage equipment such as pumps, safety valves, and throttles, leading to problems such as perforation blockage, wellbore instability, and formation caving (Sun and Bai, 2017; Ma et al., 2020; Shen K. et al., 2023; Tananykhin et al., 2023; Yan et al., 2023). In addition, Sand production can lead to a significant loss of production time.
The causes of Sand production fall into two main categories: inappropriate stimulation measures and inappropriate production operations (Safaei et al., 2023). Pressure drilling, perforation operations, acid fracturing, and other measures in unconsolidated or weakly consolidated formations may all lead to sand production problems (Ahad et al., 2020). After drilling fluid, completion fluid, and fracturing fluid invade the reservoir, they can cause clay to expand and change the wettability of the rock. Measures such as drilling and hydraulic fracturing can alter the stress balance in the wellbore area, weaken the bonding between sand and gravel, and increase the risk of sand production in the reservoir (Saghandali et al., 2022). In addition, inappropriate production operations can also cause sand production in reservoirs. Excessive production flow increases the erosion of sand and gravel and causes significant pressure drop near the wellbore (Tabar et al., 2021). After oil and gas production, the pressure in the reservoir decreases, the stress on the sand grain increases, and the risk of reservoir rock fragmentation and Sand production increases. With the further development of sand production, the sand and cement in the wellbore area are carried out of the formation by oil and gas, increasing formation pores and exacerbating sand production (Zhu et al., 2017; Tabar et al., 2021; Saghandali et al., 2022; Song et al., 2022; Safaei et al., 2023).
There are two main types of sand control methods: mechanical and chemical (Safaei et al., 2023). Mechanical sand control is using sand control equipment to prevent sand grains from entering the wellbore from the formation. Chemical sand production uses chemical reagents to improve the bonding strength between sand grains and to avoid reservoir sand production.
In mechanical sand control methods, equipment such as slotted steel pipes, gravel filling, and screening pipes prevent sand grains from migrating from the reservoir to the wellbore (Guo et al., 2020). This method has high installation costs and may also lead to a decrease in oil and gas production. In addition, due to prolonged fluid erosion, sand control equipment has a short service life and requires frequent replacement, increasing costs. Acidizing measures can also exacerbate damage to sand control equipment (Li et al., 2018; Shen KX. et al., 2023).
In chemical sand control methods, chemical reagents are injected into the reservoir, which enhances the cementation between the sand grain and improves the mechanical properties of the reservoir (Dargi et al., 2024). However, the injected consolidation agent will reduce the porosity and permeability of the reservoir. It is difficult to improve the bonding strength without damaging the reservoir permeability (Peerakham et al., 2023). The polymers used in chemical sand control mainly include epoxy resin, furan resin, phenolic resin, and polyurethane. Epoxy resin is widely used due to its low cost, high strength, and long curing time (Tabar et al., 2021). In addition, nanofillers have excellent mechanical properties, and adding a certain amount of nanofillers to the polymer can significantly improve its performance (Mishra and Ojha, 2016). The limitation of using polymers such as resins is their high viscosity, making it difficult to inject into reservoirs. Solvents such as xylene and petroleum ether are commonly used to reduce the viscosity of polymers. However, these solvents have low flash points and are very dangerous to operate (Qin et al., 2023). Another method to reduce resin viscosity is to use water-based polymers. Waterborne polymers can dissolve in water to reduce viscosity and ensure smooth reservoir injection (Qin et al., 2023).
This article introduces the mechanism of reservoir sand production and commonly used chemical sand control materials. Secondly, the latest progress in chemical sand control was reviewed. Thirdly, the research methods for laboratory sand control were introduced. Finally, the gaps and challenges of chemical sand control methods were pointed out, and the possible future development directions were discussed.
In this section, the main polymers and nanofillers used in sand control materials were reviewed, and their properties, advantages, and disadvantages were introduced. Provide a reference for the rational selection of sand control materials.
Epoxy resin is a low molecular weight prepolymer containing one epoxy group (Jin et al., 2015) (Figure 1). Epoxy resin belongs to thermosetting resins, and curing agents can cure it (Capricho et al., 2020). Epoxy resin has excellent mechanical properties, heat resistance, and chemical resistance. Therefore, epoxy resin is widely used in fiber-reinforced adhesives and coating materials. However, epoxy resin has high brittleness.
A typical synthesis method for epoxy resin is to use alkaline catalysts to generate diglycidyl ether of bisphenol A (DGEBA) from bisphenol A. The performance of DGEBA (Figure 2) resin depends on the number of repeating units. The low molecular weight is usually liquid, while the high molecular weight is usually high viscosity liquid or solid.
Figure 2. Chemical structure of DGEBA (Jin et al., 2015).
Polymer methacrylate (Figure 3) has high strength, corrosion resistance, and lightweight properties. Polymethyl methacrylate belongs to thermoplastic resins, and its poor thermal stability limits its application in sand control materials. Adding nanofillers to Polymer methacrylate significantly improves its mechanical properties and thermal stability (Wang et al., 2015).
Furan resin (Figure 4) is synthesized from phenol and formaldehyde, with excellent chemical and heat resistance and compatibility with other resins (Karlinskii and Ananikov, 2023). Furan resin is widely used as an adhesive and protective coating and is an ideal sand control material (Gandini and Lacerda, 2022). However, the curing process of furan resin is complex and takes a long time. In addition, formaldehyde, one of the raw materials for preparing furan resin, is very dangerous and needs to be carefully handled during transportation, production, and storage (Rivero et al., 2014).
Phenolic resin (Figure 5) has the advantages of strong mechanical properties, good flame retardancy, stable processing performance, and low cost, and is widely used in the petroleum industry (Hirano and Asami, 2013). Phenolic resin has a high curing temperature and a long curing time (Xu et al., 2019). The phenolic hydroxyl and methylene in the molecular structure of unmodified phenolic resin are easy to oxidize. Many scholars have conducted functional modification research on the molecular structure of phenolic resin, mainly including toughness, abrasion resistance, and anti-aging (Tang et al., 2021).
Polyurethane (Figure 6) is widely used in coating materials, adhesives, and primers due to its excellent wear resistance, flexibility, and mechanical properties (Atiqah et al., 2017). The carbamate group is the basic repeating unit of polyurethane, formed by the additional polymerization of isocyanate and macromolecule containing hydroxide (Jiang et al., 2023). According to the different polyols, polyurethane can be divided into polyester polyurethane and polyether polyurethane (Krol and Krol, 2020). In recent years, due to the increasing attention paid to environmental protection issues, waterborne polyurethane has received widespread attention (Panda et al., 2018).
The resins used in sand control materials mainly include epoxy resin, polymethyl methacrylate, furan resin, phenolic resin, and polyurethane (Ahad et al., 2020). Epoxy resin has excellent mechanical properties, chemical stability, and low cost and potential applications in sand control materials. However, the viscosity of these resins is very high, making it difficult to inject into the reservoir (Safaei et al., 2023). There are currently two main methods for reducing the viscosity of resins: organic solvent dissolution and waterborne resins (Nejati et al., 2023). Organic solvents have issues such as toxicity and low flash points and should be used with caution. Waterborne resin is non-toxic and harmless and can control the viscosity of the resin within an operable range. It is a promising method for reducing resin viscosity. The summary of commonly used sand control materials is shown in Table 1.
During the development of weakly consolidated reservoirs, sand grain is inevitably dislodged and transported as reservoir pressure decreases. Sand grain transportation not only alters the mechanical properties of the reservoir but also leads to a decrease in the permeability of the wellbore area, resulting in a decrease in the production of oil and gas wells (Han et al., 2020) (Figure 7). The resin has good mechanical and chemical properties and is effective against sanding.
Figure 7. Mechanism diagram of reservoir plugging due to sand grain transportation (Han et al., 2020).
Organosilanes are effective in consolidating sand grains through hydrolysis and polycondensation reactions. Li et al. optimized an organosilane sand control process with an organosilane concentration of 3%–5%, a catalytic HCl concentration of 1%–3%, and a generation temperature lower than 100°C (Li et al., 2017). It was found that organosilanes reacted with the surface of the sand grain to form a hydrophobic film, connecting the sand grain to the substrate and achieving sand control. The consolidation mechanism and image of organosane are shown in Figure 8. Organosilanes are hydrolyzed in water to form silanol, which reacts with the hydroxyl groups on the surface of the quartz sand to form thin films. These films are hydrophobic and can connect the sand grains.
Figure 8. Organosilane sand consolidation mechanism (A), sand consolidation properties of different organosilanes (B) (Li et al., 2017).
Dargi et al. conducted sand control experiments on weakly consolidated sandstone using furan resin. They found that the reservoir permeability retention rate was above 90%, and the sand production rate was significantly reduced (Dargi et al., 2024). Zhang et al. used phenolic resin to solidify sand, and the results showed that the strength of the consolidated sand reached 5 MPa, which can meet the sand control requirements (Zhang et al., 2013). Liu et al. synthesized a chemical sand control agent, pentaerythritol phosphate melamine salt (PPMS), which is made by the reaction of pentaerythritol, phosphoric acid, and melamine (Figure 9) (Liu et al., 2016). PPMS can reduce the negative charge density on the clay surface, allowing particles to aggregate through hydrogen bonds and static charges, effectively preventing sand production.
Figure 9. PMMS synthesis mechanism diagram (Liu et al., 2016).
Liu et al. used polyurethane to solidify loose sandstone, and a polymer film wrapped and connected the sand grains (Figure 10) (Liu et al., 2018). Li et al. cemented weakly cemented sands using porous polyurethane. Compared to conventional dense resins, the pores of the porous polyurethane provide seepage channels that limit permeability reduction (Li et al., 2022). Many field applications have shown that resin injection for sand production control can effectively improve reservoir mechanical properties and reduce sand production (El-monier et al., 2013; Shang et al., 2019; Izurieta et al., 2020; Mahardhini et al., 2021; Zaitoun et al., 2022; Zhao et al., 2022; Miri et al., 2023; Peerakham et al., 2023; Stephen Babagbemi et al., 2023).
Figure 10. Polyurethane and curing agent (A), consolidated sand grain (B), schematic of polymer interaction with sand grain (C) (Liu et al., 2018).
Hydrogels are hydrophilic polymers with a 3-dimensional network structure (Guo et al., 2022; Kang et al., 2022), specifically classified into three main categories: in situ cross-linked polymer gels, preformed gels, and foam gels (Zhu et al., 2017). In the petroleum industry, hydrogels are widely used in lost circulation control, temporary plugging, water blocking, and sand control (Bai et al., 2015; Rajaee et al., 2017; Zhao and Bai, 2022). The chemical structure of commonly used polymers is shown in Figure 11.
Figure 11. Different polymer chemical structures (Zhu et al., 2017). The chemical structure of PAM (A), HPAM (B), PAN (C), PVA (D), and PVAm (E).
Marandi et al. used polyacrylamide to prepare hydrogel for sand production in reservoirs in southern Iran (Marandi et al., 2018). The experimental results indicate that the solidified rock core can maintain good structural strength under high stress and temperatures. The CT image (Figure 12) shows that the permeability of the core injected with hydrogel is significantly reduced, indicating that the hydrogel enters deep and effectively consolidates the sand grain. After hydrogel injection, sand production is reduced by 90%, water permeability is reduced by 95 times, and oil permeability is reduced by 7.5 times. It shows that the hydrogel has good sand control performance and can effectively prevent water from flowing out. Hajipour et al. used polyacrylamide to synthesize a temporary plugging gel. The polymer can undergo a normal gelation reaction when the pressure ranges from 6.9 to 27.61 MPa (Hajipour et al., 2018). The Young’s modulus of the generated gel is 190.3 MPa with a strong network structure.
Salehi et al. conducted sand control experiments using polyacrylamide (Salehi et al., 2019). The hydrogel was injected into the core at 90°C, and the results show that the hydrogel can improve the core’s compressive strength and effectively prevent sand production. It can be seen from Figure 13A that a covalent bond links the polymer and carrier to form a three-dimensional network structure, which ensures the mechanical strength of the hydrogel. The viscosity increases as the polymer concentration increases, indicating a high crosslinking density under high-viscosity conditions (Figure 13B).
Figure 13. SEM images of hydrogel samples with different polymer concentrations (A) Hydrogel viscosity at different polymer concentrations (B) (Salehi et al., 2019).
Hydrogels have low mechanical strength, and adding nanoparticles and nanofibers to hydrogels can significantly increase their strength (Figure 14) (Dai et al., 2016). Nanofiller-hydrogel composites have promising applications. The application of nanocomposites in sand control will be introduced in the next section.
Figure 14. Principle of nanoparticle-enhanced hydrogels (Dai et al., 2016).
Pure polymers have performance deficiencies, such as low mechanical strength and poor heat resistance. Adding some nanofillers to polymers can significantly improve their properties. Commonly used nanofillers are graphene, carbon nanotubes, and silica nanoparticles.
Qin et al. added graphene oxide to polyacrylamide. The nanocomposites showed an increase in elastic modulus and a 20.71% increase in breakout pressure compared to the pure polymer (Qin et al., 2023). Hydrogen bonding between N, O, and H on graphene oxide in the nanocomposites can improve the strength of the gel (Figure 15). Yuan et al. prepared a sand consolidant using nano silica and polymer as raw materials. The sand grains consolidated with nanocomposites were structurally stable and had excellent mechanical properties (Yuan et al., 2023). The principle of sand consolidation by nanocomposites is shown in Figure 16.
Figure 15. Graphene oxide-gel interaction (A), gel cross-linking mechanism (B), graphene-gel interaction mechanism (C) (Qin et al., 2023).
Figure 16. Schematic diagram of nanocomposite interaction with sand grain (Yuan et al., 2023).
In addition, nanoparticles can form an adsorption layer to enhance the physical and chemical properties of the pore surface, which facilitates the adsorption and immobilization of fine particles on the pore surface. Nanoparticles enhance clay stability and effectively prevent particle transport (Arab and Pourafshary, 2013; Habibi et al., 2014; Mishra and Ojha, 2016; Hasannejada et al., 2017; Mansouri et al., 2019; Zhao et al., 2021; Akhter et al., 2022; Liu et al., 2022; Madadizadeh et al., 2022; Ngata et al., 2022). The properties of nanocomposites depend on the nano content and the degree of dispersion of the nanofillers in the polymer. The higher the degree of dispersion of the nanofiller in the polymer, the better the performance of the nanocomposite. Functionally modified nanoparticles have better dispersion ability in polymers.
Hot air injection is another method of sand control. The injected hot air oxidizes the crude oil in the reservoir, and the coke and resin formed between the sand grains effectively prevent sand grain transport (Safaei et al., 2023). Osman et al. consolidated the reservoir using a low-temperature oxidation method. The sand grains were 20/30 mesh, hot air at 100°C–150°C was injected into the reservoir, and the compressive strength of the consolidated sand packages ranged from 2.58 to 8.72 MPa, with permeability losses ranging from 4.5% to 22% (Osman et al., 2000). The results show that the higher the oxidation temperature, the shorter the consolidation time and the higher the compressive strength. The hot air injection method is less harmful to the reservoir permeability. The sand control technique of injecting hot air can provide sufficient compressive strength for the reservoir to withstand high fluid flow rates, and the method is less harmful to the reservoir permeability.
Aslesen conducted consolidation experiments on reservoirs using the Solder Glass method (Aslesen et al., 1981). Melt the lead oxide and silicon dioxide glass, and the material melts and decomposes into coherent crystals in the reservoir. Reservoirs cemented using this technique are unaffected by temperature and chemical attack and are flexible enough to withstand high pressures and fluid flow rates. This technique does not lead to a decrease in reservoir permeability, but it is time-consuming and expensive.
Torrest et al. performed sand consolidation experiments using electrolytic nickel, which has a short consolidation time. This method is more effective for sand consolidation and is applicable over a wider temperature range (Torrest, 1975). But this method is very complicated to operate.
Triaxial experiments are a laboratory method for studying the mechanical properties of geotechnics (Figure 17). For core samples before and after consolidation, triaxial experiments can respond to chemical reagents’ effect on the core’s mechanical properties (Bai et al., 2022). According to the stress state during the experiment, triaxial experiments are categorized into conventional triaxial experiments (stress state: σ1>σ2 = σ3>0) and true triaxial experiments (stress state: σ1>σ2>σ3>0) (Lee et al., 2013; Mishra and Janecek, 2017; Wang et al., 2022).
Figure 17. Schematic diagram of the triaxial test (Bai et al., 2022).
Poisson’s ratio is an important physical quantity in rocks. It refers to the ratio of lateral normal strain to the axial normal strain of rock under uniaxial tension or compression. Poisson’s ratio values range from 0 to 0.5, with smaller values indicating harder materials and higher values indicating softer materials (Espitia et al., 2017; Chen F. et al., 2022; Huang et al., 2023). The Poisson’s ratio calculation formula is shown in Eq. 1. Young’s modulus is a physical quantity that describes the resistance of rocks to deformation. Young’s modulus is the ratio of strain to stress generated per unit area of rock under uniaxial tension. Young’s modulus reflects the rigidity of a material, and the larger its value, the less likely the rock is to deform (Du et al., 2016; Yin et al., 2022). The calculation formula for Young’s modulus is shown in Eq. 2. The compressive strength is the limit at which a rock can withstand pressure, and its calculation formula is shown in Eq. 3.
Where µ is the Poisson’s ratio; Δσ1 is the axial stress increment; Δσ3 is the lateral stress increment; Δε3 is the lateral strain increment; Δε1 is the axial strain increment; E is the Young’s modulus; CS is the compressive strength; P is the pressure; A is the cross-sectional area.
In sand consolidation experiments, it is important to characterize the pore-throat structure of the samples. This section describes the main laboratory methods for pore throat structure characterization and their advantages and disadvantages.
Scanning electron microscopy (SEM) and X-ray computed tomography (CT) are the main imaging methods. SEM utilizes a focused beam of electrons to scan the sample’s surface, producing an image of the sample (Figure 18A). Interactions between electrons and atoms in the sample will generate signals containing information about the surface topography (e.g., pore size and distribution) and sample components. Energy dispersive spectroscopy (EDS) and cathodoluminescence (CL) can analyze the material composition of a sample (Lai et al., 2018). CT works on the principle that the radiation attenuates as it passes through the sample (Figure 18B), and the attenuation rate is related to the composition and density of the sample. The X-rays carrying information about the sample’s internal structure will be converted into visible, electrical, and digital signals sequentially. Pore characters such as pore morphology, type, distribution, connectivity, and heterogeneity can be extracted from them (Liu et al., 2023).
Figure 18. SEM working principle and SEM image (A), CT working principle and CT image (B) (Lai et al., 2018; Qian et al., 2022; Liu et al., 2023).
SEM has limited resolution and detection area and can only reflect the pore information within the visual area (generally 4∼7 nm). CT is a non-destructive imaging technique that obtains two-dimensional images of internal rock sections and reconstructs the three-dimensional distribution of pore throat structures.
Fluid intrusion methods include mercury intrusion porosimetry (MIP), gas adsorption, fluid intrusion porosimetry (FIP), and spontaneous imbibition (SI) (Gao and Hu, 2016; Zhao et al., 2020; Sharifigaliuk et al., 2021).
MIP utilizes non-wetting mercury high-pressure intrusion (Figure 19) to enter the pore throat space of the sample by overcoming capillary forces (preferentially occupying the pore throat space connected by a large throat). The pore throat size and volume distribution were determined based on the columnar pore morphology model and the Washburn equation by recording the pressed mercury pressure and volume at each equilibrium point (Wang et al., 2019). Gas adsorption measures equilibrium adsorption capacity at low temperatures to obtain the adsorption isotherm (equilibrium adsorption capacity vs relative pressure). The pore structure can be obtained by measuring and analyzing the adsorption isotherms of different adsorption models (Chen et al., 2015). FIP measures the porosity of low-permeability samples (bulk, regular, or irregular samples) by directly measuring the volume and particle density of the sample. Fluid can invade porous structures and occupy the pore space of vacuum pumping. The saturated fluid mass can be obtained from the difference in weight of the sample before and after saturating the fluid, while the volume can be obtained according to Archimedes’ principle (Kuila et al., 2014).
Figure 19. MIP working principle (A), MIP treatment results (B), low pressure gas adsorption isotherms (C), FIP treatment results (D) (Chen et al., 2015; Lai et al., 2018; Qian et al., 2022).
SI is a method of describing pore wettability and connectivity, in which a wetting fluid replaces a non-wetting fluid along a direction parallel or perpendicular to the laminae during the measurement process (Lai et al., 2018). The MIP experimental procedure requires great care because mercury is toxic. In gas adsorption methods, the sample particle size greatly influences the measurement results. In FIP testing, prolonged immersion of samples may result in the dissolution of soluble minerals and swelling of clays. The detection ranges of various pore characterization methods are shown in Figure 20.
Figure 20. Detection range of various pore characterization methods (Chen et al., 2024).
Sand production can lead to problems such as reduced reservoir permeability and equipment damage. Chemical sand control methods can improve reservoir stability and effectively prevent Sand production. This paper reviews chemical sand control methods based on chemical sand control materials, methods, and theoretical and applied characterization, respectively.
Several chemical sand control strategies have prevented sand grain production and transport. There are generally four mechanisms of action for chemical sand control methods: the coating of sand control materials on the surface of formation rocks and sand grains, the reaction of sand control materials with formation rocks and sand grains, the injection of nanoparticles to enhance the interaction between the sand grains, and thermal methods. In the coating method, the sand control material does not react with the reservoir, and there are prospects for utilizing advanced sand control materials (nanocomposites) for sand control.
The polymers often used in chemical grit control are epoxy, polyurethane, furan, and phenolic resins, and the nanofillers used are graphene, carbon nanotubes, and silica nanoparticles. Pure polymers are highly viscous, difficult to inject into reservoirs, and prone to generating toxic substances during the preparation and use of these polymeric materials. In the context of green environmental protection, using waterborne polymeric materials is a promising chemical sand control method. In addition, adding nanofillers to polymer materials can improve their mechanical strength, chemical stability, and thermal stability.
It is important to conduct sand control experiments in the laboratory, and triaxial experiments can respond to information such as Young’s modulus, Poisson’s ratio, and compressive strength before and after core consolidation. Non-destructive methods such as CT, SEM are recommended among the pore throat structure characterization methods.
Despite advances in chemical sand control methods, gaps and challenges remain. 1. Nanofillers are poorly dispersed in polymers and even agglomerate in preparing nanocomposites. The dispersing ability of nanofillers in polymers should be improved in the future. 2. Laboratory physical experiments ignore many practical situations, such as the effects of high temperatures and highly corrosive environments on sand control materials. 3. The effect of sand control materials on reservoir wettability and permeability should be further studied, for example, the effect of polymers on the wettability and permeability of different reservoirs. 4. The strength of waterborne polymeric needs to be further improved. The low viscosity of the water-based polymer material makes it easy to inject into the reservoir, but the low viscosity leads to its low cross-linking density and low strength.
ZX: Writing–original draft. KS: Writing–original draft. JZ: Writing–review and editing. QH: Writing–review and editing. PL: Writing–review and editing. JD: Writing–review and editing. JW: Writing–review and editing.
The author(s) declare that financial support was received for the research, authorship, and/or publication of this article. This work was supported by the National Key R&D Program of China (2023YFC2811005).
Author JW was employed by Chengdu Synergy Oilfield Technology Service Co., Ltd.
The remaining authors declare that the research was conducted in the absence of any commercial or financial relationships that could be construed as a potential conflict of interest.
All claims expressed in this article are solely those of the authors and do not necessarily represent those of their affiliated organizations, or those of the publisher, the editors and the reviewers. Any product that may be evaluated in this article, or claim that may be made by its manufacturer, is not guaranteed or endorsed by the publisher.
Ahad, N. A., Jami, M., and Tyson, S. (2020). A review of experimental studies on sand screen selection for unconsolidated sandstone reservoirs. J. Petroleum Explor. Prod. Technol. 10 (4), 1675–1688. doi:10.1007/s13202-019-00826-y
Akhter, F., Rao, A. A., Abbasi, M. N., Wahocho, S. A., Mallah, M. A., Anees-ur-Rehman, H., et al. (2022). A comprehensive review of synthesis, applications and future prospects for silica nanoparticles (SNPs). Silicon 14 (14), 8295–8310. doi:10.1007/s12633-021-01611-5
Arab, D., and Pourafshary, P. (2013). Nanoparticles-assisted surface charge modification of the porous medium to treat colloidal particles migration induced by low salinity water flooding. Colloids Surfaces a-Physicochemical Eng. Aspects 436, 803–814. doi:10.1016/j.colsurfa.2013.08.022
Aslesen, K. S., Short, C. J., and Terwilliger, P. L. (1981). “A new method for sand control and well stimulation in unconsolidated dirty sands,” in proceedings of the SPE Annual Technical Conference and Exhibition, F, San Antonio, Texas, October, 1981. doi:10.2523/10172-ms
Atiqah, A., Mastura, M. T., Ali, B. A. A., Jawaid, M., and Sapuan, S. (2017). A review on polyurethane and its polymer composites. Curr. Org. Synth. 14 (2), 233–248. doi:10.2174/1570179413666160831124749
Bai, B., Zhou, J., and Yin, M. (2015). A comprehensive review of polyacrylamide polymer gels for conformance control. Petroleum Explor. Dev. 42 (4), 525–532. doi:10.1016/s1876-3804(15)30045-8
Bai, J., Diao, Y., Jia, C., Liu, C., Zhang, M., and Wang, C. (2022). A review of advances in triaxial tests: instruments, test techniques and prospects. KSCE J. Civ. Eng. 26 (8), 3325–3341. doi:10.1007/s12205-022-1345-1
Bharadwaj, R., Kumar, M., Harsh, S., and Mishra, D. (2021). “Evaluation of latest technological advances in sand control completions: a case study,” in Proceedings of the SPE 2021 Symposium Compilation, F, Virtual, November, 2021. doi:10.2118/208447-ms
Capricho, J. C., Fox, B., and Hameed, N. (2020). Multifunctionality in epoxy resins. Polym. Rev. 60 (1), 1–41. doi:10.1080/15583724.2019.1650063
Chen, H. L., Ji, B. X., Wei, B., Meng, Z., Li, Y., Lu, J., et al. (2024). Experimental simulation of enhanced oil recovery on shale rocks using gas injection from material to Characterization: challenges and solutions. Fuel 356, 129588. doi:10.1016/j.fuel.2023.129588
Chen, W. L., Grabowski, R. C., and Goel, S. (2022a). Clay swelling: role of cations in stabilizing/destabilizing mechanisms. Acs Omega 7 (4), 3185–3191. doi:10.1021/acsomega.1c04384
Chen, Y. Y., Wei, L., Mastalerz, M., and Schimmelmann, A. (2015). The effect of analytical particle size on gas adsorption porosimetry of shale. Int. J. Coal Geol. 138, 103–112. doi:10.1016/j.coal.2014.12.012
Chen, F., Wang, X. B., Du, Y. H., and Tang, C. A. (2022b). Numerical experiment research on failure characteristics of anchored rock with negative Poisson's ratio bolt. Front. Earth Sci. 10, 899755. doi:10.3389/feart.2022.899755
Dai, C., Chen, W., You, Q., Wang, H., Yang, Z., He, L., et al. (2016). A novel strengthened dispersed particle gel for enhanced oil recovery application. J. Industrial Eng. Chem. 41, 175–182. doi:10.1016/j.jiec.2016.07.024
Dargi, M., Khamehchi, E., and Ghallath, F. (2024). Sandstone chemical consolidation and wettability improvement using furan polymer-based nanofluid. Sci. Rep. 14 (1), 5248. doi:10.1038/s41598-024-56007-3
Deng, F., Li, X., He, L., and Feng, Y. (2019). Experimental evaluation of metal foam for sand control. J. Petroleum Sci. Eng. 176, 1152–1160. doi:10.1016/j.petrol.2019.01.087
Ding, J., Cheng, Y., and Yan, C. (2022). Research on sand control effect and micro-plugging mechanism of sand control medium in the development of natural gas hydrate reservoir. J. Petroleum Sci. Eng. 215, 110703. doi:10.1016/j.petrol.2022.110703
Du, S. H., Shi, Y. M., Guan, P., and Zhang, Y. (2016). New inspiration on effective development of tight reservoir in secondary exploitation by using rock mechanics method. Energy Explor. Exploitation 34 (1), 3–18. doi:10.1177/0144598715623661
El-Monier, I. A., Nasr-El-Din, H. A., Harper, T. L., and Rosen, R. (2013). A new environmentally friendly clay stabilizer. Spe Prod. Operations 28 (2), 145–153. doi:10.2118/136061-pa
Espitia, J. M., Caicedo, B., and Vallejo, L. (2017). Effect of suction and stress on Poisson's ratio of argillaceous rocks. Geotech. Lett. 7 (1), 53–59. doi:10.1680/jgele.16.00138
Gandini, A., and Lacerda, T. M. (2022). Furan polymers: state of the art and perspectives. Macromol. Mater. Eng. 307 (6), 2100902. doi:10.1002/mame.202100902
Gao, Z. Y., and Hu, Q. H. (2016). Wettability of Mississippian Barnett Shale samples at different depths: investigations from directional spontaneous imbibition. Aapg Bull. 100 (1), 101–114. doi:10.1306/09141514095
Guo, Y. J., Nouri, A., and Nejadi, S. (2020). Effect of slot width and density on slotted liner performance in SAGD operations. Energies 13 (1), 268. doi:10.3390/en13010268
Guo, H., Ge, J., Wu, Q., He, Z., Wang, W., and Cao, G. (2022). Syneresis behavior of polymer gels aged in different brines from gelants. Gels 8 (3), 166. doi:10.3390/gels8030166
Habibi, A., Ahmadi, M., Pourafshary, P., and Ayatollahi, S. (2014). Fines migration control in sandstone formation by improving silica surface zeta potential using a nanoparticle coating process. Energy Sources Part a-Recovery Util. Environ. Eff. 36 (21), 2376–2382. doi:10.1080/15567036.2011.569836
Hajipour, A., Salehi, M. B., Sefti, M. V., and Heidari, A. (2018). Experimental study of polyacrylamide gel in close-in well operation. Polym. Adv. Technol. 29 (4), 1278–1286. doi:10.1002/pat.4239
Han, G., Kwon, T.-H., Lee, J. Y., and Jung, J. (2020). Fines migration and pore clogging induced by single- and two-phase fluid flows in porous media: from the perspectives of particle detachment and particle-level forces. Geomechanics Energy Environ. 23, 100131. doi:10.1016/j.gete.2019.100131
Hasannejada, R., Pourafshary, P., Vatani, A., and Sameni, A. (2017). Application of silica nanofluid to control initiation of fines migration. Petroleum Explor. Dev. 44 (5), 850–859. doi:10.1016/s1876-3804(17)30096-4
Hirano, K., and Asami, M. (2013). Phenolic resins-100 years of progress and their future. React. Funct. Polym. 73 (2), 256–269. doi:10.1016/j.reactfunctpolym.2012.07.003
Huang, X. L., Xu, L., Zhao, T. Y., Lu, S., Sun, Z., and Ding, D. (2023). Characterization of the negative Poisson's ratio effect of the thermal-damaged crystalline rock by the grain-based model. Int. J. Rock Mech. Min. Sci. 170, 105553. doi:10.1016/j.ijrmms.2023.105553
Izurieta, A., Serrano, F., Andrade, P., Burgos, A., Rodriguez, R., and Jaramillo, J. (2020). “Chemical sand consolidation as an effective alternative to conventional sand control methods in Ecuador,” in Proceedings of the Abu Dhabi International Petroleum Exhibition and Conference, F, Abu Dhabi, UAE, November, 2020. doi:10.2118/203069-ms
Jiang, R. J., Zheng, X. Y., Zhu, S. S., Li, W., Zhang, H., Liu, Z., et al. (2023). Recent advances in functional polyurethane chemistry: from structural design to applications. Chemistryselect 8 (11), e202204132. doi:10.1002/slct.202204132
Jin, F.-L., Li, X., and Park, S.-J. (2015). Synthesis and application of epoxy resins: a review. J. Industrial Eng. Chem. 29, 1–11. doi:10.1016/j.jiec.2015.03.026
Jin, Y., Li, Y., Wu, N., and Yang, D. (2021). Characterization of sand production for clayey-silt sediments conditioned to openhole gravel-packing: experimental observations. Spe J. 26 (6), 3591–3608. doi:10.2118/206708-pa
Kang, B., Lang, Q., Tu, J., Bu, J., Ren, J., Lyu, B., et al. (2022). Preparation and properties of double network hydrogel with high compressive strength. Polymers 14 (5), 966. doi:10.3390/polym14050966
Karlinskii, B. Y., and Ananikov, V. P. P. (2023). Recent advances in the development of green furan ring-containing polymeric materials based on renewable plant biomass. Chem. Soc. Rev. 52 (2), 836–862. doi:10.1039/d2cs00773h
Krol, P., and Krol, B. (2020). Structures, properties and applications of the polyurethane ionomers. J. Mater. Sci. 55 (1), 73–87. doi:10.1007/s10853-019-03958-y
Kuila, U., Mccarty, D. K., Derkowski, A., Fischer, T. B., and Prasad, M. (2014). Total porosity measurement in gas shales by the water immersion porosimetry (WIP) method. Fuel 117, 1115–1129. doi:10.1016/j.fuel.2013.09.073
Lai, J., Wang, G. W., Wang, Z. Y., Chen, J., Pang, X., Wang, S., et al. (2018). A review on pore structure characterization in tight sandstones. Earth-Science Rev. 177, 436–457. doi:10.1016/j.earscirev.2017.12.003
Lee, S. J., Choo, Y. W., Lee, J. W., and Sagong, M. (2013). Young's modulus of coarse granular materials via cyclic large triaxial tests: effect of parallel grading and loading pattern. Geotechnical Test. J. 36 (3), 429–441. doi:10.1520/gtj20120064
Li, X. R., Feng, Y. C., and Gray, K. E. (2018). A hydro-mechanical sand erosion model for sand production simulation. J. Petroleum Sci. Eng. 166, 208–224. doi:10.1016/j.petrol.2018.03.042
Liu, D., Zhong, X., Shi, X., Qi, Y., Zhu, T., Shao, M., et al. (2016). Pentaerythritol phosphate melamine salt, A new aggregating reagent for oilfield chemical sand control: preparation, properties, and mechanism. Energy and Fuels 30 (3), 2503–2513. doi:10.1021/acs.energyfuels.5b02648
Liu, J., Bai, Y., Song, Z., Lu, Y., Qian, W., and Kanungo, D. (2018). Evaluation of strength properties of sand modified with organic polymers. Polymers 10 (3), 287. doi:10.3390/polym10030287
Liu, Q., Sun, M. D., Sun, X. D., Liu, B., Ostadhassan, M., Huang, W., et al. (2023). Pore network characterization of shale reservoirs through state-of-the-art X-ray computed tomography: a review. Gas Sci. Eng. 113, 204967. doi:10.1016/j.jgsce.2023.204967
Liu, Y., She, Y., Zhang, F., Feng, Q., Li, X., Dong, H., et al. (2022). Mechanism of nano-depressurization and injection-augmenting Technology and its application in China’s oilfields: recent advances and perspectives. Energy and Fuels 36 (18), 10751–10765. doi:10.1021/acs.energyfuels.2c01970
Li, W., Chang, F. F., Eichmann, S. L., and Liang, F. (2022). Tailored highly porous, templated polyurethane for sand consolidation. J. Appl. Polym. Sci. 139 (17), e52045. doi:10.1002/app.52045
Li, X., Zhang, G., Ge, J., Qi, N., Jiang, P., Liao, K., et al. (2017). Organosilane film for sand migration control based on in-situ hydrolysis and polycondensation effects. J. Petroleum Sci. Eng. 158, 660–671. doi:10.1016/j.petrol.2017.08.013
Luo, T., Liu, S., and Ott, W. K. (2023). A new process to develop marine natural gas hydrate with thermal stimulation and high-efficiency sand control. Petroleum Sci. Technol., 1–18. doi:10.1080/10916466.2023.2217837
Ma, C., Deng, J., Dong, X., Sun, D., Feng, Z., Luo, C., et al. (2020). A new laboratory protocol to study the plugging and sand control performance of sand control screens. J. Petroleum Sci. Eng. 184, 106548. doi:10.1016/j.petrol.2019.106548
Madadizadeh, A., Sadeghein, A., and Riahi, S. (2022). The use of nanotechnology to prevent and mitigate fine migration: a comprehensive review. Rev. Chem. Eng. 38 (1), 1–16. doi:10.1515/revce-2019-0055
Mahardhini, A., Yudis, P., Abidiy, I., Bawono, Y., and Pradityo, R. (2021). “Successful case of resin-based chemical sand consolidation as a remedial sand control treatment,” in Proceedings of the Abu Dhabi International Petroleum Exhibition and Conference, F, Abu Dhabi, UAE, November, 2020. doi:10.2118/207942-ms
Mansouri, M., Nakhaee, A., and Pourafshary, P. (2019). Effect of SiO2 nanoparticles on fines stabilization during low salinity water flooding in sandstones. J. Petroleum Sci. Eng. 174, 637–648. doi:10.1016/j.petrol.2018.11.066
Marandi, S. Z., Salehi, M. B., and Moghadam, A. M. (2018). Sand control: experimental performance of polyacrylamide hydrogels. J. Petroleum Sci. Eng. 170, 430–439. doi:10.1016/j.petrol.2018.06.074
Miri, R., Salimi, M., Stewart, S., Bermudez Gonzalez, J. M., Mazo Suárez, C., and Nouri, A. (2023). Sand control screen selection for cased dual-annulus gas offshore wells based on scaled laboratory tests. Can. J. Chem. Eng. 102, 1957–1969. doi:10.1002/cjce.25159
Mishra, D. A., and Janecek, I. (2017). “Laboratory triaxial testing - from historical outlooks to technical aspects,” in proceedings of the ISRM European Rock Mechanics Symposium (EUROCK), Ostrava, CZECH REPUBLIC, June, 2017.
Mishra, S., and Ojha, K. (2016). Nanoparticleinducedchemicalsystemforconsolidatinglooselybound sand formationsinoil fields. J. Petroleum Sci. Eng. 147, 15–23. doi:10.1016/j.petrol.2016.05.005
Nejati, H., Khamehchi, E., Derakhshan, A. A., and Shad, S. (2023). Synthesis and optimization of a Novel epoxy-based nanofluid for sand consolidation in oil wells. Geoenergy Sci. Eng. 230, 212217. doi:10.1016/j.geoen.2023.212217
Ngata, M. R., Yang, B., Aminu, M. D., Iddphonce, R., Omari, A., Shaame, M., et al. (2022). Review of developments in nanotechnology application for formation damage control. Energy and Fuels 36 (1), 80–97. doi:10.1021/acs.energyfuels.1c03223
Osman, E. A., Aggour, M. A., and Abu-Khamsin, S. A. (2000). In-situ sand consolidation by low-temperature oxidation. SPE Prod. Facil. 15 (01), 42–49. doi:10.2118/60843-pa
Panda, S. S., Panda, B. P., Nayak, S. K., and Mohanty, S. (2018). A review on waterborne thermosetting polyurethane coatings based on Castor oil: synthesis, characterization, and application. Polymer-Plastics Technol. Eng. 57 (6), 500–522. doi:10.1080/03602559.2016.1275681
Peerakham, C., Haripogepornkul, N., Putthaworapoom, N., Direkmahamongkol, S., Thanasutives, P., Zin Ko Ko, T., et al. (2023). “Chemical sand consolidation and through-tubing gravel pack, the effective alternative sand control methods in zawtika field,” in Proceedings of the International Petroleum Technology Conference, Bangkok, Thailand, March, 2023. doi:10.2523/iptc-23097-ea
Qian, Y. J., Gao, P., Fang, X. L., Sun, F., Cai, Y., and Zhou, Y. (2022). Microstructure characterization techniques for shale reservoirs: a review. Front. Earth Sci. 10, 930474. doi:10.3389/feart.2022.930474
Qin, D., Gao, W., Zhang, S., Cui, X., Chen, H., Yang, P., et al. (2023). In situ composite of graphene oxide in polyacrylamide to enhance strength of hydrogel with polyethyleneimine as crosslinker. Geoenergy Sci. Eng. 231, 212304. doi:10.1016/j.geoen.2023.212304
Rajaee, S., Salehi, M. B., Moghadam, A. M., Vafaie Sefti, M., and Mohammadi, S. (2017). Nanocomposite hydrogels adsorption: experimental investigation and performance on sandstone core. J. Petroleum Sci. Eng. 159, 934–941. doi:10.1016/j.petrol.2017.08.034
Rivero, G., Fasce, L. A., Ceré, S. M., and Manfredi, L. (2014). Furan resins as replacement of phenolic protective coatings: structural, mechanical and functional characterization. Prog. Org. Coatings 77 (1), 247–256. doi:10.1016/j.porgcoat.2013.09.015
Safaei, A., Ase, M., Ahmadi, M., Pourshamsi, T., Baloochestanzadeh, S., Khalilnezhad, A., et al. (2023). Chemical treatment for sand production control: a review of materials, methods, and field operations. Petroleum Sci. 20 (3), 1640–1658. doi:10.1016/j.petsci.2023.02.013
Saghandali, F., Baghban Salehi, M., Hosseinzadehsemnani, R., Moghanloo, R. G., and Taghikhani, V. (2022). A review on chemical sand production control techniques in oil reservoirs. Energy and Fuels 36 (10), 5185–5208. doi:10.1021/acs.energyfuels.2c00700
Salehi, M. B., Moghadam, A. M., and Marandi, S. Z. (2019). Polyacrylamide hydrogel application in sand control with compressive strength testing. Petroleum Sci. 16 (1), 94–104. doi:10.1007/s12182-018-0255-9
Shang, X., Bai, Y., Wang, Z., Wang, Q., and Dong, C. (2019). A novel chemical-consolidation sand control composition: foam amino resin system. E-Polymers 19 (1), 1–8. doi:10.1515/epoly-2019-0001
Sharifigaliuk, H., Mahmood, S. M., Rezaee, R., and Saeedi, A. (2021). Conventional methods for wettability determination of shales: a comprehensive review of challenges, lessons learned, and way forward. Mar. Petroleum Geol. 133, 105288. doi:10.1016/j.marpetgeo.2021.105288
Shen, K. X., An, Y. K. R., Xu, Z. Q., Wu, X., Zhang, P., Zhang, Y., et al. (2023a). Numerical simulation on coupling behaviors of sand production and mechanical response during NGH exploitation by depressurization from the argillaceous reservoir. Energy and Fuels 38 (1), 245–257. doi:10.1021/acs.energyfuels.3c03368
Shen, K., An, Y., Xu, Z., Wu, X., Zhang, P., Zhang, Y., et al. (2023b). Numerical simulation on coupling behaviors of sand production and mechanical response during NGH exploitation by depressurization from the argillaceous reservoir. Energy and Fuels 38 (1), 245–257. doi:10.1021/acs.energyfuels.3c03368
Song, J. Z., Fu, J. H., Xiong, Y. M., Pang, W., He, Y., Liu, L., et al. (2022). State-of-the-art brief review on sanding problem of offshore natural gas hydrates sediments. Energy Sci. Eng. 10 (1), 253–273. doi:10.1002/ese3.1006
Stephen Babagbemi, A., Mofunlewi, S., and Williams, C. (2023). “Remedial sand control using chemical sand consolidation, A field experience,” in proceedings of the SPE Nigeria Annual International Conference and Exhibition, F, Houston, Texas, USA, May, 2023. doi:10.2118/217108-ms
Sun, X., and Bai, B. (2017). Comprehensive review of water shutoff methods for horizontal wells. Petroleum Explor. Dev. 44 (6), 1022–1029. doi:10.1016/s1876-3804(17)30115-5
Tabar, M. A., Bagherzadeh, H., Shahrabadi, A., and Dahim, S. (2021). A comprehensive research in chemical consolidator/stabilizer agents on sand production control. J. Petroleum Explor. Prod. Technol. 11 (12), 4305–4324. doi:10.1007/s13202-021-01303-1
Tananykhin, D., Grigorev, M., Simonova, E., Korolev, M., Stecyuk, I., and Farrakhov, L. (2023). Effect of wire design (profile) on sand retention parameters of wire-wrapped screens for conventional production: prepack sand retention testing results. Energies 16 (5), 2438. doi:10.3390/en16052438
Tang, K. H., Zhang, A. L., Ge, T. J., Liu, X., Tang, X., and Li, Y. (2021). Research progress on modification of phenolic resin. Mater. Today Commun. 26, 101879. doi:10.1016/j.mtcomm.2020.101879
Torrest, R. S. (1975). Electroless nickel sand consolidation: laboratory studies of cementation and calculated effect on well productivity. Soc. Petroleum Eng. J. 15 (03), 203–208. doi:10.2118/4964-pa
Wang, F. Y., Yang, K., You, J. X., and Lei, X. (2019). Analysis of pore size distribution and fractal dimension in tight sandstone with mercury intrusion porosimetry. Results Phys. 13, 102283. doi:10.1016/j.rinp.2019.102283
Wang, G., Feng, X. T., Yang, C. X., Han, Q., and Kong, R. (2022). Experimental study of the mechanical characteristics of jinping marble under multi-stage true triaxial compression testing. Rock Mech. Rock Eng. 55 (2), 953–966. doi:10.1007/s00603-021-02704-8
Wang, Y., Chen, T., and Yan, C. (2015). Reinforced performances of polymethyl methacrylate/silica fume composite spherical particles used as ultra-lightweight proppants. J. Reinf. Plastics Compos. 34 (8), 672–683. doi:10.1177/0731684415577236
Wang, Y., Long, F.-Q., Li, X.-S., Xu, Y. T., and Kou, X. (2023). Experimental study of sand migration under distinct sand control methods during gas hydrate decomposition by depressurization. Energy and Fuels 37 (17), 12966–12979. doi:10.1021/acs.energyfuels.3c01934
Wu, N., Li, Y., Chen, Q., Liu, C., Jin, Y., Tan, M., et al. (2021). Sand production management during marine natural gas hydrate exploitation: review and an innovative solution. Energy and Fuels 35 (6), 4617–4632. doi:10.1021/acs.energyfuels.0c03822
Xu, Y. R., Guo, L. F., Zhang, H. N., Zhai, H., and Ren, H. (2019). Research status, industrial application demand and prospects of phenolic resin. Rsc Adv. 9 (50), 28924–28935. doi:10.1039/c9ra06487g
Yan, W., Li, F., Leng, G., Wang, H., Ma, Z., Yun, B., et al. (2023). Sand control screen erosion-failure prediction method in weakly consolidated sandstone reservoir. Geoenergy Sci. Eng. 224, 211616. doi:10.1016/j.geoen.2023.211616
Yin, Y. C., Liu, G. Y., Zhao, T. B., Ma, Q., Wang, L., and Zhang, Y. (2022). Inversion method of the Young's modulus field and Poisson's ratio field for rock and its test application. . Mater. 15 (15), 5463. doi:10.3390/ma15155463
Yuan, J., Pei, Z., Yang, S., Yu, H., Hu, X., and Liu, H. (2023). Preparation and characterization of an eco-friendly sand-fixing agent utilizing nanosilica/polymer composites. J. Appl. Polym. Sci. 140 (18). doi:10.1002/app.53804
Zaitoun, A., Salehi, N., Bouillot, J., Hernando, L., Wijaya, B. R., Reynold, W., et al. (2022). “Mitigating sand production by polymer injection in Indonesian offshore field,” in proceedings of the SPE Asia Pacific Oil and Gas Conference and Exhibition, F, Adelaide, Australia, October, 2022. doi:10.2118/210731-ms
Zhang, F., Ouyang, J., Ma, X., and Feng, X. (2013). A new phenolic resin for sand control in wells. Chem. Technol. Fuels Oils 49 (5), 425–429. doi:10.1007/s10553-013-0465-1
Zhang, Y., Wang, W., Zhang, P., Li, G., Tian, S., Lu, J., et al. (2022). A solution to sand production from natural gas hydrate deposits with radial wells: combined gravel packing and sand screen. J. Mar. Sci. Eng. 10 (1), 71. doi:10.3390/jmse10010071
Zhao, J. H., Hu, Q. H., Liu, K. Y., Jin, Z., Dultz, S., Kaufmann, J., et al. (2020). Pore connectivity characterization of shale using integrated wood's metal impregnation, microscopy, tomography, tracer mapping and porosimetry. Fuel 259, 116248. doi:10.1016/j.fuel.2019.116248
Zhao, S., Zhou, Y., Bai, J., Baobing, S., Tao, F., Huaxing, C., et al. (2022). “Research and application of integrated Technology of chemical sand control and stratified water injection in offshore oilfields injection well,” in Proceedings of the IADC/SPE Asia Pacific Drilling Technology Conference and Exhibition, F, Bangkok, Thailand, August, 2022. doi:10.56952/arma-2022-0598
Zhao, X., Qiu, Z., Gao, J., Ren, X., Li, J., and Huang, W. (2021). Mechanism and effect of nanoparticles on controlling fines migration in unconsolidated sandstone formations. Spe J. 26 (6), 3819–3831. doi:10.2118/204474-pa
Zhao, Y., and Bai, B. (2022). Experimental study of transport behavior of swellable microgel particles in superpermeable channels for conformance control. Spe J. 27 (1), 790–805. doi:10.2118/208576-pa
Keywords: sand production, polymer, unconsolidated reservoir, pore structure, nanocomposite
Citation: Xu Z, Shen K, Zhou J, Huang Q, Liu P, Du J and Wu J (2024) Chemical sand production control: a review of materials, methods and characterization. Front. Energy Res. 12:1424059. doi: 10.3389/fenrg.2024.1424059
Received: 27 April 2024; Accepted: 22 May 2024;
Published: 11 June 2024.
Edited by:
Melike E Bildirici, Yıldız Technical University, TürkiyeReviewed by:
Mingwei Zhao, China University of Petroleum, ChinaCopyright © 2024 Xu, Shen, Zhou, Huang, Liu, Du and Wu. This is an open-access article distributed under the terms of the Creative Commons Attribution License (CC BY). The use, distribution or reproduction in other forums is permitted, provided the original author(s) and the copyright owner(s) are credited and that the original publication in this journal is cited, in accordance with accepted academic practice. No use, distribution or reproduction is permitted which does not comply with these terms.
*Correspondence: Kaixiang Shen, c2t4dkAxNjMuY29t
Disclaimer: All claims expressed in this article are solely those of the authors and do not necessarily represent those of their affiliated organizations, or those of the publisher, the editors and the reviewers. Any product that may be evaluated in this article or claim that may be made by its manufacturer is not guaranteed or endorsed by the publisher.
Research integrity at Frontiers
Learn more about the work of our research integrity team to safeguard the quality of each article we publish.