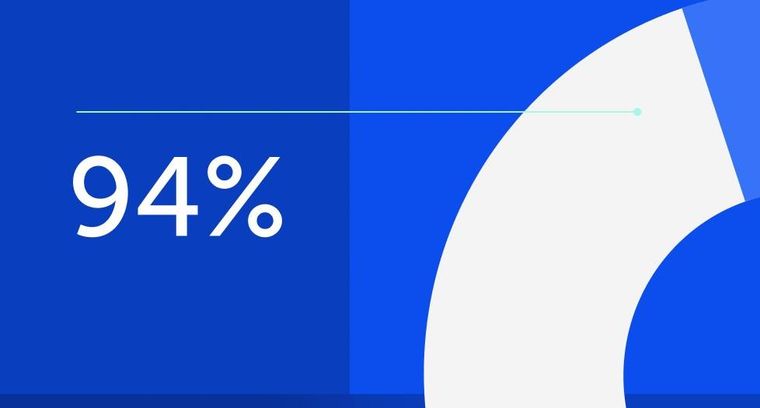
94% of researchers rate our articles as excellent or good
Learn more about the work of our research integrity team to safeguard the quality of each article we publish.
Find out more
REVIEW article
Front. Energy Res., 24 May 2024
Sec. Advanced Clean Fuel Technologies
Volume 12 - 2024 | https://doi.org/10.3389/fenrg.2024.1399033
This article is part of the Research TopicProduction Technology for Deep ReservoirsView all 37 articles
Sand production in oil wells seriously affects the production of oil and gas in oilfields. Although conventional sand-control techniques can effectively prevent sand production, it may also limit the productivity of oil wells. Fracturing and packing sand control technology changes the distribution of pressure and flow in the wellbore, while foam polymer resin diversion technology reduces the anisotropy of reservoir permeability and increases the area of oil leakage in the reservoir, both achieving the goal of sand control and increased production. The sand-free production rate is successfully increased thanks to zeta potential sand control technology, which modifies the formation’s sand potential and causes the sand to agglomerate without harming the reservoir. This article first looks into the causes of sand production in oil and gas wells before examining the fundamentals, implementation strategies, and effects of traditional sand control techniques, fracturing and filling sand control technology, foam polymer resin diversion technology, and Zeta potential sand control technology. In this article, the experience of sand control technology in actual oil field applications is summarized, explained in detail, and the future development possibilities of sand control technology are discussed.
Sand production is one of the common hazards for the oil wells in the oil field development. It is often seen in the oil and gas reservoirs dominated by unconsolidated sandstone (Kamaruddin N et al., 2021; Shunchao Z et al., 2022). If the sand production issue is not handled promptly and effectively, sand particles in the wellbore will continue to accumulate, blocking the oil flow channels, resulting in a sharp decline in the production of oil and gas wells, and potentially even forcing the premature abandonment of the well. Therefore, it is necessary to understand the causes of sand production and the mechanism of sand control in oil and gas wells, and adopt effective sand control technology to reduce the harm caused by sand production (Gomez R et al., 2022a). However, the research and application of sand control technology are facing numerous challenges. Different geological conditions of oilfields, well structures, and exploitation methods may lead to differences and complexities in sand production phenomena. Therefore, the research on sand control technology needs to comprehensively consider various factors and explore more scientific and effective solutions (Li Z et al., 2022; Trujillo et al., 2023). Common sand control technologies include mechanical sand control, chemical sand control and composite sand control, etc. However, these technologies will increase the additional resistance of fluid flow into the wellbore while sand control, thus reducing the near-wellbore permeability (Nejati H et al., 2023). Fracturing sand control can create highly conductive oil and gas seepage channels by changing the pressure distribution and flow patterns around the well (Wang and Sun, 2022). Sand control and stimulation are both effective, thus it is considered an efficient technique for reservoir development (Habib et al., 2022). Zeta potential sand control technology uses chemicals to change the potential of the sand surface and reservoir rocks, reducing the repulsive force between sand particles and gathering into clumps. Sand particles can still gather again after being dispersed without damaging the reservoir (Kalabayev et al., 2021; Parhizgar Keradeh and Tabatabaei-Nezhad, 2023; Singh et al., 2014).
Based on previous research on the causes of sand production and conventional sand control techniques, this article further delves into various application forms of fracture filling sand control technology, including Tip Screen Out (TSO), subsequent resin sand control, and fiber composite sand control techniques. Detailed introductions and analyses are provided regarding the construction tools, construction processes, and application effects of these techniques. In addition, two novel sand control technologies are introduced: foam polymer resin diversion technology and Zeta potential sand control technology. Their production effects and applications are elaborated, providing references and new insights for addressing the sand control issues in oilfields with severe sand production and fine silt. Through this investigation, it is recognized that fracture filling sand control technology and its related new techniques offer effective solutions for oilfield sand control. By thoroughly studying the construction tools, processes, and application effects of these technologies, we can provide more scientific and efficient guidance for sand control work in oilfields, thus providing strong support for sustainable oilfield production.
Sand production is a common issue in oil extraction, and its existence can reduce well output, shorten the lifespan of equipment, and impact wellbore stability (Wang J L et al., 2003; Wong G K et al., 2003). The causes of sand production are diverse, and through thorough analysis of these causes, we can more accurately identify the key factors that lead to sand production (Al Shizawi et al., 2018; Fattahpour V et al., 2020; Devalve C et al., 2021; Chandrakant A A et al., 2023). This allows us to formulate targeted sand control measures, which can not only reduce the risk of sand production but also improve the efficiency and safety of oil extraction. Therefore, through research and summary, the current main geological factors can be categorized into two major types: geological factors and production factors. Geological factors primarily involve stratum characteristics, rock physical properties, and geological structures. Geological structures such as loosely cemented sandstone layers, faults, and cracks in the stratum can all lead to sand production (Fuller et al., 2019; Minnich J.L et al., 2021). On the other hand, production factors are closely related to mining methods, production pressure differences, mining speeds, and wellbore design. Unreasonable mining methods, excessive production pressure differences, or excessively fast mining speeds can all increase the scouring force of fluids on the particles of the reservoir framework, leading to sand production (Izurieta A et al., 2020; Ayazi P et al., 2021; Hasmin et al., 2022a; Mandhari S et al., 2022).
Geological factors refer to the geological conditions in which the well is located, including the geological age of the area around the hole, particle uniformity, cementation and degree of cementation (Table 1) (Ubuara, et al., 2024; Balasandran A et al., 2021). The reasons for sand production in oil wells are not always the same, and there may be some differences in the causes of sand production among oil wells in different regions, One of the main aspects is the geological conditions of the reservoir itself, which mainly include the following aspects (Madasu and Vo., 2016; Hassan N A et al., 2020; Kueh J Z et al., 2022; Mahardhini A et al., 2021).
(1) Influence of rock physical properties: ①Reservoir bonding strength. The sand production in oil reservoir is greatly influenced by the cementation strength of the reservoir, The cementation strength of oil reservoir is affected by the type, quantity and strength of cementing materials, The forms of cementation in oil reservoirs mainly include mud cementation, carbonate cementation, and siliceous cementation, with their cementation strengths increasing in sequence; The cementation types mainly include matrix cementation, porous cementation, and contact cementation. Generally, matrix cementation is less prone to sand production due to its high strength, followed by porous cementation which may lead to minor sand production.; Contact cementation is the type most prone to sand production, Generally speaking, cementation strength is affected by the combined effect of various geological factors. When the various stresses in the formation exceed the cementation strength, sand production may occur. Sandstone oil and gas reservoirs have a larger amount of cementation, better cementation types, more uniform distribution, and an earlier geological age, resulting in stronger cementation strength and less likelihood of sand production. Conversely, if the cementation is weaker, sand production is more likely to occur. ②The influence of reservoir mineral composition. If the unstable minerals such as montmorillonite account for a relatively large proportion of the mineral composition, they will expand when exposed to water during mining, squeezing the rock particles and disturbing the cementation between them, leading to easy sand production (Peerakham C et al., 2023; Deng et al., 2023; Dwitama S et al., 2021).
(2) Impact of formation pressure: The decrease in formation pressure can weaken the destruction caused by squeezing, thereby reducing sand production in the oil reservoir (Tang C et al., 2022; Stephen Babagbemi A et al., 2023).
(3) Impact of high horizontal tectonic stress: Under normal circumstances, there is no significant difference between the two horizontal principal tectonic stresses. However, due to the decrease in porosity and increase in formation strength during the exploitation process, even small movements in the formation can lead to an increase in stress in that direction. A higher stress difference can result in wellbore failure, leading to sand production from the oil well (Aroyehun M E et al., 2018; Yeap W J et al., 2019; Zhenxiang Z et al., 2020).
(4) Impact of fluid properties: The viscosity of the fluid affects sand production in the oil reservoir. As the viscosity of the fluid increases, the critical flow velocity at which sand production begins to occur in the core decreases. In other words, the higher the fluid viscosity, the more likely it is to cause sand production. Additionally, the pH of the fluid also affects sand production in the oil reservoir. As the pH of the fluid increases, the critical flow velocity for sand production decreases. When the pH of the fluid reaches 14, the sand production rate can increase sharply (Malau A et al., 2017; Mahmoudi M et al., 2018; Styward B et al., 2018; Wang X, 2018).
Production and construction factors refer to the direct impact of human construction operations on sand production in the formation (Table 2) (Cavender T et al., 2003b). The influence of these factors can be reduced through appropriate control and adjustment. Production factors mainly include the following aspects.
(1) The impact of perforation. When the perforation density is high, the critical pressure for shear failure decreases after stress release, and the stress borne by the rock mass increases. This leads to the destruction of the sandstone layer structure and sand production in oil wells (Agee D M et al., 2016; Al-Arnous A B et al., 2021).
(2) The impact of fluid extraction intensity. As the production of fluid increases, the flow velocity of the liquid also increases. With the accelerated flow rate of formation fluid, the drag force on the sand particles also increases. This makes the formation tension more susceptible to damage, resulting in poor stability and a high risk of sand production. When the production pressure difference increases, high speed flow may lead to sudden sand production, and a decrease in axial flow rate may lead to instability of sand arch and increased sand production (Ranjith et al., 2014; Casares and Talavera, 2001; Denney D, 2002; Denney D, 2003; Denney D, 2006).
(3) Production dynamic pressure difference. In the middle and late stages of oil well production, the reservoir pressure decreases, the pressure borne by the rock increases, the pressure between formation pores decreases, the pressure of the overlying strata increases, and the contact stress between sand particles increases. When the pressure exceeds the compressive strength of the sandstone, the sandstone framework breaks, leading to sand production in the oil well (Guinot F et al., 2001; Heitmann N et al., 2002; Gomez R et al., 2022b).
(4) The impact of changes in water cut in an oilfield. As the oilfield is developed, the water cut of oil wells continues to rise, increasing the degree of water washing in the reservoir. Cementation materials can be dissolved and washed away by water, reducing the cementation strength of the rock. Additionally, the cohesion strength of clays in the reservoir depends on the wetting phase. When the clay encounters water, the cohesion strength drops sharply, leading to an increase in sand volume and subsequently causing sand production (Schubert et al., 1975).
Therefore, through theoretical and experimental research can determine the best construction technology and parameters, to achieve the purpose of sand control and sand control.
With the continuous innovative progress of sand control technology, a variety of sand control technology has been formed. Among them, the conventional sand control technology mainly includes mechanical sand control, chemical sand control, coking sand control and composite sand control (Nie,S et al., 2023; Ma,L et al., 2022; Prasad V et al., 2020). Mechanical sand control techniques mainly use slotted liner, wire-wound screen and gravel pack to prevent formation sand bodies from entering the well bore (Matanović et al., 2012; Rodoplu R S and Al-Mohanna K S, 2019; Rozlan M R et al., 2022). Chemical sand control is to inject chemicals into the loose formation and consolidate the formation sand body to achieve sand control. Generally, chemical sand control can be divided into three types (Safaei et al., 2023a): resin cemented formation sand, artificial well wall and other chemical solidified sand. Coke sand control technology is mainly through heating the oil layer, so that the coke substance in the oil layer solidifies on the surface of the sand body, to improve the adhesion between the sand body and the sand body, and prevent the sand body migration. The commonly used coking methods include hot air injection for sand consolidation and short-term burning of oil reservoir for sand (Martin et al., 1958; Abass H H et al., 1993; Bale A et al., 1994; Baker C et al., 1995) consolidation. Compound sand control technology is an organic combination of mechanical sand control and chemical sand control, through the establishment of a double sand barrier around the hole and on the tubing of the same oil well to achieve the purpose of sand control. The composite sand control technology can better solve the problem of the deficiency of single sand control technology, but it also has the characteristics (Carpenter, 2018; Liu H-Y. et al., 2022) of complex process and poor economy. In order to meet the need of further sand control, new sand control technologies such as fracturing pack sand control, composite perforation sand control, expandable slotted pipe and layered extruded gravel pack have been developed (Rodoplu et al., 2023; Dong et al., 2016).
Mechanical sand control is a physical sand control technique that involves inserting filling tools and sand control pipes into the wellbore, and then filling gravel outside the pipe to prevent sand ingress. In its application, there are two common forms: sand control pipe technology and improved sand control pipe technology - gravel packing technology for pipe strings. The former mainly establishes a sand barrier within the wellbore using sand control pipes, while the latter primarily relies on the compaction of gravel between the sand control pipe and the casing to block the flow of ceramsite, and also uses sand control pipes within the wellbore for sand prevention (Hurt R S and Germanovich L N, 2012; Dong, C., et al., 2016; Safaei, A., et al., 2023b).
(1) sand control pipe string technology. By installing sand control devices at the lower end of the production pump, such as multi-layer screen pipes and wire-wound screen pipes, sand particles are isolated outside the production pump, reducing the impact of sand production on the pump. The application of this technology is relatively simple and can effectively address the issue of sand production in medium-to-coarse sandstone formations. However, it has a shorter service life and does not filter fine sand and gravel effectively.
(2) Improved sand control pipe string technology. During construction, the mechanical pipe string is first inserted into the oil well. Then, gravel or ceramsite is used to fill the annular space between the mechanical pipe string and the casing, creating multiple layers of sand filter barriers. This technology can better filter fine sand and has a longer service life, but it has issues such as complex construction, high investment, and inappropriate gravel sizes that can affect oil flow capacity and production.
Mechanical sand control technology has good sand control and oil production enhancement effects, with a high success rate in applications and relatively long effective periods. However, there are also some limitations in its application. This technology may not be effective in dealing with fine sand strata and high-pressure strata, and it may also increase the difficulty of operation during later operations or well repairs due to the influence of sand control strings or gravel packing operations. Therefore, when applying this technology, it is crucial to select reasonable technical parameters, such as the size of the sand control pipe perforations and the sand control particle size. These parameters can affect the sand control effect and final production capacity. During on-site practical applications, representative sand samples should be selected for screening under allowable processing conditions to determine the sand control particle size. Based on this, the appropriate size of the sand control pipe perforations should be selected to ensure good sand control effects without affecting production capacity.
Compared to mechanical sand control, chemical sand control technology is widely used in oil and gas wells due to its advantages of simple process flow and ease of subsequent operations and treatment. Chemical sand control refers to the injection of chemical agents into the loosely consolidated formation around the wellbore to consolidate the formation sand, thus achieving the purpose of solidifying the formation. There are mainly two methods: artificial casing and artificial cementation (Safaei, A., et al., 2023a; Piemontese, M., et al., 2014; Solares et al., 2022).
(1) The artificial casing method. The artificial casing method primarily involves injecting specific chemical substances, such as cement mortar, emulsified cement, and water-mixed dry sand, into the formation. After these substances solidify, they form an artificial casing with a certain strength, which can effectively consolidate the formation while enhancing sand control effectiveness. One of the advantages of this method is that it does not leave any residual objects during application. However, repeated use of this method can affect the permeability of the formation.
(2) Artificial cementation method. The artificial cementation method primarily involves injecting specific chemical cementing agents, such as silicate or resin, into the formation near the wellbore. These chemical cementing agents react with the sand grains in the formation to form a cemented body with certain strength, firmly bonding the sand grains together and preventing them from flowing into the wellbore. The impact of this method on formation permeability is relatively minor, and it typically achieves good sand control results. However, the cost of chemical cementing agents is relatively high, and the cementation process within the formation requires time, which can affect the progress of sand control operations.
This method is relatively simple to operate and achieves good results with fine silt reservoirs. Additionally, it can effectively block water if the water cut in the oil layer is high during production. However, a significant limitation of chemical sand control methods is their short duration of effectiveness. Over time, especially after prolonged erosion, the chemical colloidal structure can be disrupted, rendering it ineffective in sand control. Therefore, chemical sand control methods are primarily utilized in the early stages of production or in high-water-cut wells, where they can effectively control sand and water. When applying chemical sand control methods, it is crucial to consider the actual sand production conditions, formation pressure, permeability, and injection-production connectivity to determine the construction plan and parameters. Precise calculation of the required sand control radius is essential to ensure the implementation of an effective sand control plan that achieves desired results.
Coking sand control primarily involves heating the oil layer to cause the crude oil to coke on the surface of sand grains. This coked thin layer bonds the sand grains together, enhancing the adhesive force on the surface of the sand grains and achieving the purpose of sand control. There are mainly two methods for this technique: sand fixation through injected hot air and short-term in-situ combustion for oil layer sand fixation (Zhu et al., 2022).
(1) Hot air injection for sand fixation. This method involves injecting hot air into the wellbore to raise the temperature of the oil layer, which prompts the coking of crude oil.
(2) Short-term in-situ combustion for oil layer sand fixation. This method directly applies short-term fire to the oil layer, rapidly coking the crude oil within it.
Coking sand control technology can effectively meet sand control requirements to a certain extent. However, its application is relatively complex, requiring precise control of thermal energy to ensure the effectiveness of coking. Additionally, this technique can have an impact on formation permeability, potentially causing damage to the reservoir. Furthermore, its cost is relatively high. Therefore, in the application process, it is necessary to comprehensively consider formation conditions, engineering requirements, and economic factors. Enhanced on-site monitoring and evaluation should be conducted to ensure the safety and effectiveness of the coking operation.
Several conventional sand control technologies each have their own applicable conditions, advantages, and disadvantages. They have been widely used in the field and have achieved good sand control effects. The applicable conditions and application effects are shown in Tables 3, 4 (Mayorga Cespeded et al., 2020; Bai et al., 2021).
As can be seen from the tables, several sand control technologies each have their own applicable conditions and effects. While they have proven effective in field applications, to achieve even better sand control results, it is advisable to utilize comprehensive sand control techniques in practical applications. By combining the advantages of various conventional sand control methods and developing comprehensive sand control plans tailored to the specific conditions of the reservoir and the specific sand control requirements on site, the effectiveness and stability of the technological application can be improved. For instance, the utilization of chemical sand control and coking sand control techniques can further enhance sand control effects and extend their validity period. Meanwhile, in practical applications, it is necessary to comprehensively consider reservoir conditions, sand control requirements, and economic benefits to select appropriate sand control techniques. Real-time monitoring and data collection should be conducted to more accurately evaluate the effectiveness of sand control and make timely adjustments and optimizations.
With the wide application of fracturing technology, sand return of proppant after pressure has become a new problem for sand control. At the same time, some domestic oil and gas reservoirs with serious sand production and difficulty in sand control have been gradually put into development (Junstate et al., 2008; Ma et al., 2020). However, conventional sand control technology is faced with problems (Yushi et al., 2021a) such as poor effect of fine silt prevention, damage to the reservoir, aging or failure. Therefore, frac pack sand control technology, which has the advantages of both stimulation and sand control, has become an important solution. In recent years, Zeta potential sand control technology has become a new development direction of sand control technology by changing the formation sand potential to make it aggregate, effectively improve the sand production without damaging the reservoir.
Fracturing pack sand control technology has the advantages of increasing production and sand control. As shown in Figure 1, post-fracturing fractures can effectively change the pressure distribution pattern and flow pattern around the well, It can be clearly seen from the figure that the high-pressure zone near the wellbore has been expanded after fracturing. The reduction of the pressure gradient can reduce the cost of displacement energy, thereby increasing the area of low pressure around the well and decontaminating some of the near-wellbore areas, This allows oil and gas that was originally difficult to reach the wellbore to flow smoothly. In addition, the flow pattern in the fracture zone changed from radial to bilinear flow, reducing the production pressure differential and flow pressure gradient, thereby reducing the ability of fluid to scour and carry sand. This action mitigated or avoided the failure (Yang et al., 2005; Katende et al., 2023; Liu Y-X. et al., 2022; Merzoug et al., 2023) of the reservoir rock framework.
Figure 1. Wellbore pressure in an unfractured well (left) and a fractured sand control well (right).
End sand removal fracturing sand control is a fracturing process in which the reasonable design of construction parameters makes the sand plug form at the end (surrounding) of the fracture when the predetermined length is reached, and the sand carrying liquid is continued to be pumped into the fracture. The fracture length no longer increases, but the width keeps increasing, and the fracture conductivity is greatly improved. Generally, there are two different pumping phases, as shown in Figure 2. In the first stage, the fracturing vehicle creates the fracture under high pressure. When the hydraulic fracture length and height reach the expected value, the low sand ratio and high displacement of mortar are pumped into the fracture end to de-sand, and then the fracture extension is terminated. In the second stage, after the end is de-sanded, the sand carrying fluid is pumped to increase the fracture width and finally improve the fracture conductivity (Yushi et al., 2021b).
The tip screening out process is gradually formed on the basis of hydraulic fracturing technology, which artificially controls the fracture propagation and greatly increases the width of the fracture to achieve the purpose of both increasing production and sand control (Desroches and Thiercelin, 1993; Ortega L et al., 1996; Morita N et al., 1998). In unconsolidated sandstone reservoirs with high permeability, increasing fracture conductivity is more beneficial to increase production than increasing fracture length. The percolation belt with high permeability can make the radial flow direction of fluid oil quasi-linear flow change, which can effectively reduce the production pressure difference, reduce the seepage resistance of crude oil, improve the flow conditions of oil and gas, so as to achieve the purpose of increasing production and sand control (Fan et al., 2001).
Naranjo-Agudelo A J. (Naranjo-Agudelo A J, 2021). carried out the design and simulation of the end sand removal fracturing and filling construction of Lao 168 block of Laohekou Oilfield, optimized the pumping procedure, and carried out the field implementation. Among them, the average oil production of 12 Wells using the end sand removal fracturing technology is 12.82t/d, and the average pre-pressure productivity is only 3.6t/d.
Sand control in unconsolidated sandstone reservoirs can be solved by end-de-sanding technology, and the sand carrying performance of fracturing fluid should be considered in the implementation. By increasing the viscosity of the fracturing fluid, it can effectively improve the sand carrying performance and expand the fracture width. In the end de-sand fracturing, it is advisable to use stage sand addition to ensure the sand control effect (Singh and Sharma, 2023).
Follow-up resin sand control fracturing is a technical measure with better sand control effect developed on the basis of end sand removal fracturing. In the later stage of fracturing, resin is sprayed on the proppant to form resin sand, and then the resin sand is pumped into the formation as proppant. By controlling the viscosity, displacement and sand ratio of the fracturing fluid, the resin sand is sealed in the way of end sand removal, which softens and solidifies in the formation fracture, thus for mining an artificial well wall with multistage separation and filtration around the well. To achieve sand (Junstate et al., 2008; Katende et al., 2023; Liu et al., 2023; Hasmin et al., 2022b) retention (Figure 3).
Dong C et al. (Dong C et al., 2016) determined the optimal curing time and the compatibility of resin sand and fracturing fluid in the experiment. The accumulated oil increase of 25 Wells was 2865t, and the average daily oil increase of a single well was 2.8t. Wong G K et al. (Wong G K et al., 2003) obtained the economic combination of 4:1 quartz sand followed by resin sand in the experiment, which was successfully applied to Mazhuang oilfield, with a cumulative oil increase of 4002t and an average daily oil increase of 5.47t per well, which was 3t higher than the average daily oil production per well in the block. Tarek M. (Tarek and Leung, 2024). optimized the sand control and fracturing technology of tailing resin sand in Daqing Sazhong and Sanan oilfields, adjusted the proportion of sand added in fracturing and the amount of resin sand, and made the strength of production liquid increase from 4.44t/(dm) in 2004 to 7.01t/(dm) in 2005, which increased by 2.57t/(dm).
In frac sand control operations, the addition of fibers to the proppant strengthens the proppant in the fracture, reduces the chance of backflow, and helps prevent the formation of fine silt. In 2005, Zhou et al. (Zhou et al., 2006). Proposed fiber composite sand control technology. The general idea includes six aspects: “solution, stability, consolidation, prevention, protection and enhancement”. In the specific construction process, firstly, stimulation measures are adopted to “de-damage” the near-well reservoir, and then treatment fluid containing soft fiber is injected to “stabilize” sand. The fibers are then combined with the resin coating to form a three-dimensional mesh composite structure that “solidifies” the sand. The end de-sanding and fiber-composite technology work together to “prevent” the sand and then inject the well washing fluid that “protects” the reservoir. Finally, the end desanding technique is used to press open short and wide fractures in the reservoir to increase the conductivity of the fractures, thus achieving the purpose of “increasing” production.
The fiber composite sand control technology uses both soft and hard fibers. The positive branch chain of soft fiber will expand when it meets water, absorb fine silt, form fine silt combination, improve the critical velocity, and realize the role of soft fiber “sand stabilization”; The hard fiber colludes with each other to form a three-dimensional network structure through its bending, curling and spiral crossing characteristics, forming a filter layer that can bind the sand (see Figure 4), preventing the fine silt combination from entering the wellbore and realizing the role of “sand retention".
In Shibu 3–10 well, fiber composite, clean fracturing fluid and end sand removal are used to form a supporting fiber composite screen-less sand control technology, which has achieved good application effect. Before sand control, the daily gas output is 1.53 × 104 m3, and sand production is serious. After fiber composite sand control operation, the production system of the well remains unchanged, with daily gas of 3.10 × 104 m3 and no sand production (Zhou et al., 2006). Junstate, X (Junstate X et al., 2020) applied fiber composite sand control technology to achieve significant results in Cao104 block. Compared with conventional mechanical sand control technology, the cycle increased oil by 5,051.1t, the average water cut decreased by 2.3%, the average oil-gas ratio increased by 0.38, and the output input ratio reached 4.6.
Fiber composite sand control technology is suitable for gas Wellswith gas cap, bottom water and interzone water (Upchurch, 1999). By adding nano SiO2 to the resin, Klimentos T. (Klimentos T, 2003). improved the mechanical properties of the fiber complex. The strength and compressive strength of the modified resin coated sand control body increased by 36.55% and 63.86%, respectively, and the strength of the fiber complex increased by 26.12%. The application of nano composite materials provides a certain development idea for fiber composite sand control technology.
The integrated fracturing sand control technology uses a single string (Figure 5) to complete the two purposes of fracturing and sand control, which is a stimulation sand control technology. The sand control screen assembly is lowered into the target zone, the formation is fractured, and after fracturing the formation, multistage sand barriers are formed in the screen sheath annulus, perforated hole, near wellbore, and deep formation through high displacement, high sand ratio, and high sand volume extrusion. This technology not only shortens the construction period and reduces the operating cost, but also effectively protects the short and wide fractures formed after the end of the sand removal fracturing to ensure sand control effect (Flores Perez and Shkred, 2020; Yan et al., 2023).
The fluid flow in the fractured formation presents a bilinear flow mode, which reduces the production pressure difference and oil flow resistance, and impedes sand migration to the bottom hole zone. High conductivity fractures and short and wide fractures formed after fracturing and packing break through the near-wellbore contamination zone to achieve better stimulation, reduce the chance of rock skeleton destruction, and reduce the scouring and carrying capacity of production fluids on sand (Figure 6).
The process involves running the bridge packer in the designed position as required. After setting the packer with a pressure, the sealing plug matching the bottom hollow bridge packer is connected to a wire-wound screen, a signalizer, and an integrated fracturing sand control suspension tool. After gradually pressing and stabilizing the pressure for 3min, after the integrated sand control suspension tool is set, pressing to 1820 MPa to open the formation fracturing channel; −The fracturing truck crew is used to carry out fracturing filling operation on the stratum according to the designed parameters and procedures, and the end sand removal is formed by controlling the construction parameters and procedures. Reverse release, and open the circulating filling channel to carry out the circulating filling of the screen sleeve annulus; Pull out the release string and complete the well.
The production layer of well 36-Skew five in Qinghe oil area is the fourth member of Shahejie Formation, with a well interval of 981.4986 m. The oil layer is shallow buried, has high viscosity of crude oil, small median sand size and high mud content, and the oil layer is seriously polluted before production. −Before using the integrated technology of fracturing sand control, the maximum daily output of fluid is 3.2m3/d and oil is 1.6t/d. After the measures, the daily output of fluid is 12.4m3/d and oil are 8.5t/d. The total production of the entire block was higher, demonstrating the effectiveness of the technology.
The unconsolidated sandstone layer is thin and multi-interbedded, and the reservoir is heterogeneous. As a result, it is necessary to use different zonal frac techniques, optimize the design of the process string, use fracturing sand control tools and zonal packers, and optimize the multi-zonal perforation process.
The integrated string (Figure 7) of upper layer acidizing and lower layer fracturing sand control enables inter-interval isolation, sand control and acidizing of formation fracturing, and is left in the wellbore after construction. The inner string is paired with the packer between the setting sections of the outer string. After release, the inner and outer strings are separated to achieve sand control and acidification for fracturing. After construction, the releasing string is removed to reduce the number of operations (Figure 8).
Figure 8. Schematic diagram of the overall design of the upper acidizing and lower fracturing integrated pipe string.
To meet the need for sand control in oil production, new sand control technologies have been rapidly developed based on conventional sand control and fracture filling sand control techniques, such as foam polymer resin diversion technology and Zeta potential sand control technology. Foam polymer resin diversion technology mainly involves injecting foam agents into the formation to form a stable foam structure, followed by introducing polymer resins to evenly distribute and solidify them within the foam, thereby effectively sealing the formation sand grains. On the other hand, Zeta potential sand control technology primarily relies on colloidal chemistry principles and surface phenomenology theory. By adjusting the Zeta potential of particles in the formation, it changes the interaction forces between particles, preventing the aggregation and flow of sand grains, thus achieving sand control. Both of these new sand control technologies have their unique characteristics and can meet the need for sand control in oil production to a certain extent, exhibiting great potential for development.
Srinath et al. (2016) proposed a new type of foam polymer resin shunt system based on chemical sand control. The shunt system coupled the characteristics of foam increasing viscosity and improving dispersion degree. After the shunt system is injected into the formation, it enters the high permeability layer with the liquid flow, and the bubbles flow through the pore throat to produce the Jamin effect, which makes the shunt system turn to the low permeability layer in the formation and uniformly cover the whole reservoir. Therefore, the shunt system can solidify a large range of formation sand under formation conditions, reduce the longitudinal anisotropy of reservoir permeability, increase the drainage area of the reservoir, and achieve the purpose of sand control and production increase. The experimental comparison of three shunt systems (foam, polymer resin and foam polymer resin) shows that the foam polymer resin system can recover 70%–75% permeability and maintain good production capacity after consolidation of sandstone.
The shunt system requires precise control of foam and polymer concentration, temperature, pressure and injection rate to ensure shunt effect and resin curing time. Reservoir heterogeneity, degree of fracture development, pore structure, and fluid properties also need to be considered.
Alfredo et al. (Rawlings, 1958; Upchurch, 1999; Tahirov T et al., 2014) injected Zeta potential changing system (ZPAS) into the formation to change the charge distribution on the surface of sand grains, starting from the control of Zeta potential between liquid and solid surfaces. By making the Zeta potential of the sandstone matrix within the range of +3 to -5mV, the electrostatic repulsion between sand particles and between sand particles and between sand particles and reservoir rocks is reduced, which encourages sand particles to aggregate into large clumps (Figure 9) and move closer to reservoir rocks, thus reducing sand migration (Kalabayev et al., 2021). Sand grains can move relative to each other without losing their ionic attraction and can re-aggregate when the stress in the reservoir changes. The injected chemical ZAPS does not affect formation wettability or permeability, only changes the surface charge of the solid particles and does not react with other chemicals or minerals in the formation, thereby increasing maximum sand-free production and reducing permeability loss.
Kalabayev et al. (2021) perform an experimental sand control operation at the Lam oil field in the South Rihedez Sea, Turkmenistan. After this treatment, the target well experienced a long-term improvement in both the production index and the sand-free flow rate, without damage to the wellbore or reservoir. The technology is not limited by wellbore geometry and can adapt to changing reservoir conditions. In practice, to ensure stability and performance, the system was manufactured using standard mixing equipment, and laboratory testing was performed to optimize the chemical formulation and determine the optimal injection rate.
Based on the study of conventional sand control techniques, this research conducted a comprehensive investigation and summary of fracturing sand control techniques and currently emerging sand control technologies. It was found that while existing sand control techniques can effectively address sand production issues in oilfield development to a certain extent, they also pose numerous problems and challenges (Table 5) (Shaffee et al., 2019; Wildhack et al., 2012).
Currently, the main issues with conventional sand control technologies include poor formation adaptability, limited effectiveness duration, unsatisfactory implementation results, high cost investment, and complex operation processes. Mechanical sand control techniques are typically suitable for coarser sand layers with higher permeability, but their performance is not ideal for fine-grained sand reservoirs. Additionally, equipment such as screens requires regular replacement and maintenance to prevent failure due to sand clogging. Chemical sand control techniques have a shorter duration of effectiveness under long-term erosion, necessitating regular maintenance and updates. The application of chemical agents also incurs relatively high costs and can potentially damage the reservoir formation, reducing its permeability. Similarly, coking sand control techniques can only temporarily address sand production issues and may affect formation conditions and crude oil properties. Precise control of thermal energy is required during its application, making the operation process relatively complex. This article focuses on the research of fracturing sand control technology, which can effectively increase the production capacity of oil wells while achieving good sand control effects. However, its application also poses the issue of complex operation techniques. During the implementation of fracturing and filling, it is necessary to correctly select the size and type of sand filling based on the actual situation, thus requiring high technical proficiency and specialized equipment. Similarly, although new sand control technologies generally have good performance and are environmentally friendly and flexible, they also have issues such as complex operation techniques and high development costs (Gomez et al., 2022a).
Currently, the issues with sand control technology are mainly reflected in its effectiveness, cost, environmental adaptability, and operational difficulty. Therefore, the principles and directions for the implementation of sand control technology in the future will be deepened and innovated based on the challenges and shortcomings of current technology, as well as the new demands of oilfield development.
(1) Principle innovation: Future sand control technology will place greater emphasis on innovation in principles. For instance, the use of special materials for the temperature-tolerant coated sand control process can create artificial well walls with high strength and good permeability, addressing the issues of existing technologies that impact the formation and reduce permeability, thus achieving sand control. For problems such as casing deformation in the oil layer and difficulties encountered during sand washing, the “plugging” process can be used to improve the efficiency and effectiveness of mechanical sand control technology.
(2) Integration and comprehensive sand control: Flexibly adjusting sand control strategies based on different geological conditions and operating environments, and developing towards integration and comprehensive sand control. For instance, shifting from single-well measures to comprehensive management, establishing a four-level management system, developing three specific processes (parameter control, wellbore sand removal, and formation sand control), establishing an integrated work approach for oil and water wells, and ultimately forming a comprehensive sand control system.
(3) Intelligence and automation: Installing sensors and monitoring systems can enable real-time monitoring of sand production in oil wells, and automatically adjust sand control measures based on actual conditions. For example, in the case of fracturing and filling sand control technology, automation technology can be used to intelligently control the fracturing and sand control process, reducing operational difficulty and improving application effectiveness.
(4) Environmental protection and sustainability: Future sand control technology will place greater emphasis on environmental protection and sustainability. For example, in chemical sand control technology, the use of chemical reagents can cause damage to the oil reservoir, thus requiring the further development of chemical reagents that have low impact on the formation and the environment.
It can be predicted that the application prospects of sand control technology are very broad and hopeful. With the continuous increase in global energy demand and the expansion of the scale and depth of oilfield development, the demand for sand control technology, as one of the key technologies to ensure the safe production of oilfields, will also continue to increase. Continuous innovation and improvement of sand control technology will more effectively improve the sand control effect and provide strong support for the sustainable development of oilfields. Secondly, the increase in environmental awareness and the popularization of the concept of sustainable development have made the environmental impact of oilfield development increasingly concerned. Sand control technology, as a technology that can reduce sand production from oil wells and protect formation stability, meets the requirements of environmental protection and sustainable development. Therefore, in the future, sand control technology will play a greater role in environmental protection and sustainable development, promoting the coordinated development of oilfield development and environmental protection. Furthermore, with the advancement of technology and the increasing difficulty of oilfield development, the requirements for sand control technology are also getting higher and higher. In the future, sand control technology will pay more attention to the development of high efficiency, intelligence, and environmental protection. For example, through the use of advanced technologies such as artificial intelligence and big data, precise prediction and optimized adjustment of sand control measures can be achieved; through the research and development of new environmentally friendly materials and technologies, the impact of the sand control process on the environment can be reduced; and through the integration of multiple sand control technologies, comprehensive sand control solutions can be formed to improve sand control effects and economic benefits. In addition, with the strengthening of international cooperation and the development of globalization trends, international exchanges and cooperation in sand control technology will become more frequent and deeper.
Based on extensive research and analysis, this paper comprehensively summarizes two major factors leading to sand production in oil wells. This phenomenon poses significant challenges to the safe and efficient production of oilfields. To address these challenges, this paper focuses on studying three kinds of fracturing sand control techniques based on the examination of various conventional sand control technologies, and introduces two new sand control techniques. It also analyzes and summarizes their technical principles as well as the issues encountered in field applications. On this basis, it further looks into the future development direction and application prospects of sand control technology. The aim is to provide safer, more efficient, and more cost-effective sand control solutions for oilfield development, thereby promoting the sustainable development of oilfields.
1) The reasons for sand production in oil Wells include geological factors and construction factors. Geological factors, including the geological age of the area around the hole, particle uniformity, cementation and degree of cementation, are indirect factors. Construction factors can reduce sand production by artificially controlling and adjusting construction process methods and parameters.
2) The conventional sand control technology includes mechanical sand control, chemical and control, coking sand control and composite sand control technology. These technologies prevent or reduce sand production through different principles and can meet the production requirements for sand control to a certain extent. However, they all have their own limitations and need to be selected based on specific application scenarios and requirements.
3) With the increasing demand for sand control technology, fracturing and packing sand control technology has unique technical advantages and huge application potential because of its characteristics of increasing production and sand control. The stimulation and sand control principle of fracturing pack sand control technology is to change the pressure distribution pattern and seepage mode around the well. At present, four kinds of fracturing packing sand control technologies, namely, end sand removal, follow-up resin sand, fiber composite sand control and fracture sand control integration, are the development direction of fracturing sand control technology.
4) With the advancement of technology and the deepening of engineering practices, conventional sand control techniques have also been continuously developed and improved. For instance, some novel sand control technologies, such as foam polymer resin diversion technology and Zeta potential sand control technology, have undergone rapid development. Foam polymer resin diverting technology uses foam to temporarily block and turn, and promotes resin to uniformly cover and consolidate sand particles, improve certain permeability of the reservoir and increase the drainage area of the reservoir. Zeta potential sand control technology changes the charge distribution of sand particles by injecting ZPAS, reduces Zeta potential to reduce electrostatic repulsion force, sand aggregates and reduces migration, and increases sand free production.
XH: Conceptualization, Investigation, Writing–original draft. ZP: Writing–review and editing. LR: Writing–review and editing. LZ: Writing–review and editing. XL: Writing–review and editing. YW: Writing–review and editing. PL: Supervision, Writing–review and editing.
The author(s) declare that financial support was received for the research, authorship, and/or publication of this article. This research was funded by the Scientific Research and Technology Development Project of the China National Petroleum Corporation (2021DQ0105-02) (Standardization research of Chinese, English, and Russian paraphrases or common terms in the oil and gas industry—Phase I) and the National Natural Science Foundation of China (42202292). The funder was not involved in the study design, collection, analysis, interpretation of data, the writing of this article, or the decision to submit it for publication.
Author XH, LR, LZ, and XL were employed by PetroChina Research Institute of Petroleum Exploration & Development. Author LR was employed by China National Oil and Gas Exploration and Development Company Ltd.
The remaining authors declare that the research was conducted in the absence of any commercial or financial relationships that could be construed as a potential conflict of interest.
All claims expressed in this article are solely those of the authors and do not necessarily represent those of their affiliated organizations, or those of the publisher, the editors and the reviewers. Any product that may be evaluated in this article, or claim that may be made by its manufacturer, is not guaranteed or endorsed by the publisher.
Abass, H. H., Wilson, J. M., Venditto, J. J., and Voss, R. E. (1993). “Stimulating weak formations using new hydraulic fracturing and sand control approaches,” in SPE Production Operations Symposium, Oklahoma City, Oklahoma, March, 1993.
Agee, D. M., Sutherland, A., Syifaai, A., Malik, B. Z., Tsangueu, B., Emmanuel, I., et al. (2016). “Sand control from a supply vessel: mobile fracturing fleet saves rig time in subsea completions,” in Offshore Technology Conference Asia, Kuala Lumpur, Malaysia, March, 2016.
Al-Arnous, A. B., Al-Bensad, Z., Ahmed, D., Bin, Md, Noor, M. N., Batita, N., et al. (2021). “Successful intervention of coiled tubing rugged tool with real-time telemetry system in Saudi arabia first multistage fracturing completion with sand control system,” in SPE Annual Technical Conference and Exhibition, Dubai, UAE, September, 2021.
Al Shizawi, W., Al Zadjali, R., Mahajan, S., and Bellmann, L. (2018). “Sand production assessment and sand control selection for steam flood in South Oman,” in SPE International Heavy Oil Conference and Exhibition, Kuwait City, Kuwait, December, 2018.
Aroyehun, M. E., Oko, F. N., Onyeanusi, O., Oguntade, T., Kabara, A., and Dimkpa, B. (2018). “Comparative study of sand control methods in selected Niger-delta sand stone reservoirs,” in SPE Nigeria Annual International Conference and Exhibition, Lagos, Nigeria, August, 2018.
Ayazi, P., Peregoy, N., Monreal, G., and Zamora, F. (2021). “Screening friction reducer performance using zeta potential,” in SPE International Conference on Oilfield Chemistry, The Woodlands, Texas, USA, December, 2021.
Bai, J., Zhou, Y., Wu, H., Zhao, S., Shang, B., and Fang, T. (2021). “Experimental study on type and accuracy optimization of sand control in sand-producing heavy oil well,” in SPE Eastern Europe Subsurface Conference, Kyiv, Ukraine, November, 2021.
Baker, C., Peach, S., and Brkich, N. (1995). “Justification for fracturing medium to high permeability formations in sand control environments,” in Annual Technical Meeting, Calgary, Alberta, June, 1995.
Balasandran, A., Ramirez, C., Mohan, R., Bela, S. M., Riyanto, L., Samuel, O. B., et al. (2021). “Malaysia's first successful implementation of sand consolidation technology as a primary sand control method executed during the drilling phase: success story and lessons learned,” in SPE/IATMI Asia Pacific Oil and Gas Conference and Exhibition, Virtual, October, 2021.
Bale, A., Owren, K., and Smith, M. B. (1994). Propped fracturing as a tool for sand control and reservoir management. SPE Prod. Facil. 9 (01), 19–28. doi:10.2118/24992-pa
Carpenter, C. (2018). Hybrid sand-consolidation fluid offers versatility in treatment of shallow reservoirs. J. Petroleum Technol. 70 (10), 71–72. doi:10.2118/1018-0071-jpt
Casares, M. A., and Talavera, J. F. (2001). “Hydraulic fracturing as A sand control method: experimental work on the VBR-24 well, vibora field, Bolivia,” in SPE Latin American and Caribbean Petroleum Engineering Conference, Buenos Aires, Argentina, March, 2001.
Cavender, T., Roane, T. O., and Restarick, H. L. (2003b). “Interfacing fracturing and sand control completion strategies into multilateral technology; considerations and solutions,” in SPE Asia Pacific Oil and Gas Conference and Exhibition, Jakarta, Indonesia, September, 2003.
Chandrakant, A. A., Muhammad Yusof, A., M Zin, Z., Rosland, E. A., Balgobin, A. S., Li Ren, C., et al. (2023). “Performance of bonded bead sand screen as remedial sand control in highly erosive environment,” in SPE/IATMI Asia Pacific Oil and Gas Conference and Exhibition, Jakarta, Indonesia, October, 2023.
Deng, F.-C., Gui, F.-L., Fan, B.-T., Wen, L., Chen, S.-H., Gong, N., et al. (2023). Study on the clogging mechanism of punching screen in sand control by the punching structure parameters. Petroleum Sci. 21, 609–620. doi:10.1016/j.petsci.2023.08.017
Denney, D. (2002). Hydraulic fracturing for sand control in high gas rate screenless completions. J. Petroleum Technol. 54 (03), 45–46. doi:10.2118/0302-0045-jpt
Denney, D. (2003). Interfacing fracturing and sand-control strategies into multilateral technology. J. Petroleum Technol. 55 (07), 58–59. doi:10.2118/0703-0058-jpt
Denney, D. (2006). Fracturing for sand control: screenless completions in the yegua formation. J. Petroleum Technol. 58 (03), 56–57. doi:10.2118/0306-0056-jpt
Desroches, J., and Thiercelin, M. (1993). Modelling the propagation and closure of micro-hydraulic fractures. Int. J. Rock Mech. Min. Sci. Geomechanics Abstr. 30 (7), 1231–1234. doi:10.1016/0148-9062(93)90100-r
Devalve, C., Kao, G., Morgan, S., and Wu, S. (2021). “From wellbore breakout to sand production prediction: an integrated sand control completion design methodology and case study,” in SPE Annual Technical Conference and Exhibition, Dubai, UAE, September, 2021.
Dong, C., Zhang, Q., Gao, K., Yang, K., Feng, X., and Zhou, C. (2016). Screen sand retaining precision optimization experiment and a new empirical design model. Petroleum Explor. Dev. 43, 1082–1088. doi:10.1016/s1876-3804(16)30126-4
Dwitama, S., Rachman, R., Rizky, R.-a. M., Abidiy, I., Dharma, E., Pradityo, R., et al. (2021). “Big entrance hole perforation as new alternative approach to optimize thru-tubing sand control technique while maintaining reservoir deliverability for tunu gas reservoir in unconsolidated sand formation,” in SPE/IATMI Asia Pacific Oil and Gas Conference and Exhibition, Virtual, October, 2021.
Fan, Y., White, D. E., Aimar, A., and Satyagraha, M. T. (2001). Frac/pack modeling for high-permeability viscous oil reservoirs of the duri field, Indonesia. SPE Prod. Facil. 16 (03), 189–196. doi:10.2118/72995-pa
Fattahpour, V., Roostaei, M., Mahmoudi, M., Soroush, M., Hosseini, S. A., and Anderson, M. (2020). “Standalone sand control evaluation: developing a large-scale high temperature sand retention test apparatus,” in SPE Canada Heavy Oil Conference, Virtual, September, 2020.
Flores Perez, J. C., and Shkred, V. Y. R. U. (2020) Sand control screens for hydraulic fracture and method. US 10822918.
Fuller, M., Palisch, T., and Fischer, C. (2019). “Sieve distribution vs sand retention: the impact of mono-sieved gravel on sand control,” in SPE Annual Technical Conference and Exhibition, Calgary, Alberta, Canada, September, 2019.
Gomez, R., Khan, P., and Stolboushkin, E. (2022a). “Novel multi-stage fracturing sand control technology to improve completion efficiency,” in Early Production and Reduce Well Cost. International Petroleum Technology Conference, Riyadh, Saudi Arabia, February, 2022.
Gomez, R., Khan, P., and Stolboushkin, E. (2022b). “Novel multi-stage fracturing sand control technology to improve completion efficiency, early production and reduce well cost,” in International Petroleum Technology Conference, Riyadh, Saudi Arabia, February, 2022.
Guinot, F., Zhao, J., James, S., and Emmanuel, D. H. (2001). “Screenless completions: the development, application and field validation of a simplified model for improved reliability of fracturing for sand control treatments,” in SPE European Formation Damage Conference, The Hague, Netherlands, May, 2001.
Habibi, A., Fensky, C. E., Fattahpour, V., Roostaei, M., Mahmoudi, M., Zeng, H., et al. (2022). The role of fouling materials strength on unplugging sand control devices using an electrohydraulic stimulation technique. J. Petroleum Sci. Eng. 208, 109689. doi:10.1016/j.petrol.2021.109689
Hasmin, M. a. N., M Jeffry, S. J., Tusimin, F., Cheol, H. R., Anand, S., Zeidan, A., et al. (2022a). “Application of resin sand consolidation as primary sand control: case study of a new development well in offshore sarawak,” in ADIPEC, Abu Dhabi, UAE, October, 2022.
Hasmin, M. a. N., M Jeffry, S. J., Tusimin, F., Cheol, H. R., Anand, S., Zeidan, A., et al. (2022b). “Application of resin sand consolidation as primary sand control: case study of a new development well in offshore sarawak,” in ADIPEC, Abu Dhabi, UAE, October, 2022.
Hassan, N. A., Yeap, W. J., Singh, R., and Nik Khansani, N. Z. (2020). “Performance review of chemical sand consolidation and agglomeration for maximum potential as downhole sand control: an operator’s experience,” in SPE Asia Pacific Oil and Gas Conference and Exhibition, Virtual, November, 2020.
Heitmann, N., Pitoni, E., Ripa, G., and England, K. (2002). “Fiber-Enhanced visco-elastic surfactant fracturing enables cost-effective screenless sand control,” in European Petroleum Conference, Aberdeen, United Kingdom, October, 2002.
Hurt, R. S., and Germanovich, L. N. (2012). “Parameters controlling hydraulic fracturing and fracture tip-dominated leakoff in unconsolidated sands,” in SPE Annual Technical Conference and Exhibition, San Antonio, Texas, USA, October, 2012.
Izurieta, A., Serrano, F., Andrade, P., Burgos, A., Rodriguez, R., and Jaramillo, J. (2020). “Chemical sand consolidation as an effective alternative to conventional sand control methods in Ecuador,” in Abu Dhabi International Petroleum Exhibition and Conference, Abu Dhabi, UAE, November, 2020.
Junstate, X., Geology, G. R., Jianchun, G., and Jinzhou, Z. (2008). New progress in technology of controlling proppant flowback. Fault-Block Oil Gas Field.
Kalabayev, R., Sukhova, E., Rovshenov, G., Gurbanov, G., Gil, J., and Kontarev, R. (2021). “Novel sand conglomeration treatment prevents sand production and enhances well productivity: offshore caspian case study,” in SPE Middle East Oil and Gas Show and Conference, November, 2021.
Kamaruddin, N., A Karim, N., Hasmin, M. a. N., Bela, S. M., Riyanto, L., Samuel, O. B., et al. (2021). “Malaysia's first successful implementation of sand consolidation technology as a primary sand control method executed during the drilling phase: success story and lessons learned,” in SPE/IATMI Asia Pacific Oil and Gas Conference and Exhibition, Virtual, October, 2021.
Katende, A., Allen, C., Rutqvist, J., Nakagawa, S., and Radonjic, M. (2023). Experimental and numerical investigation of proppant embedment and conductivity reduction within a fracture in the Caney Shale, Southern Oklahoma, USA. Fuel 341, 127571. doi:10.1016/j.fuel.2023.127571
Klimentos, T. (2003). “Nmr applications in Petroleum related rock-mechanics: sand control, hydraulic fracturing, wellbore stability,” in SPWLA 44th Annual Logging Symposium, Galveston, Texas, June, 2003.
Kueh, J. Z., Tan, K. L., Dev, D., Thamilarasu, M. R., Abd Wahab, S., Riyanto, L., et al. (2022). “Sand consolidation treatment: durability in an alternative primary sand control method for a marginal reservoir,”, Riyadh, Saudi Arabia, February, 2022.
Li, Z., Song, H., Balhoff, M. T., and Espinoza, D. N. (2022). “Fracture opening patterns in granular media subjected to injection of non-Newtonian fluids,” in 56th U.S. Rock Mechanics/Geomechanics Symposium, Santa Fe, New Mexico, USA, June, 2022.
Liu, H.-Y., Li, H.-W., Zhu, Y.-B., Yu, J., Sun, T., Liu, W., et al. (2022a) Research and application of mechanical sand control pipe string for lateral drilling. Singapore: Springer Nature Singapore, 3979–3989.
Liu, K., Zhu, W., and Pan, B. (2023). Laboratory evaluation on oil-soluble resin as selective water shut-off agent in water control fracturing for low-permeability hydrocarbon reservoirs with bottom aquifer. Geoenergy Sci. Eng. 225, 211672. doi:10.1016/j.geoen.2023.211672
Liu, Y.-X., Zhou, H.-Y., Guo, J.-C., Zhang, Q., and Chen, C. (2022b). Controlling factors of fracture aperture reduction based on experimental study using proppant pack apparent Young's modulus. J. Petroleum Sci. Eng. 208, 109506. doi:10.1016/j.petrol.2021.109506
Ma, C., Deng, J., Dong, X., Sun, D., Feng, Z., Luo, C., et al. (2020). A new laboratory protocol to study the plugging and sand control performance of sand control screens. J. Petroleum Sci. Eng. 184, 106548. doi:10.1016/j.petrol.2019.106548
Ma, L., Dong, J., Wang, J., Zhang, Y., Li, G., and Li, J. (2022). “Sand production prediction of depleted-reservoir underground gas storage – an experimental study,” in 56th U.S. Rock Mechanics/Geomechanics Symposium, Santa Fe, New Mexico, USA, June, 2022.
Madasu, S., and Vo, L. (2016). “An effective foamed polymer resin diverter system for sand control,” in International Petroleum Technology Conference, Bangkok, Thailand, November, 2016.
Mahardhini, A., Yudis, P., Abidiy, I., Bawono, Y., and Pradityo, R. (2021). “Successful case of resin-based chemical sand consolidation as a remedial sand control treatment,” in Abu Dhabi International Petroleum Exhibition and Conference, Abu Dhabi, UAE, November, 2021.
Mahmoudi, M., Roostaei, M., Fattahpour, V., Uzcatequi, A., Cyre, J., Sutton, C., et al. (2018). “Standalone sand control failure: the role of wellbore and near wellbore hydro-thermo-chemical phenomenon on the plugging and the flow performance impairments of the standalone sand screen,” in SPE Thermal Well Integrity and Design Symposium, Banff, Alberta, Canada, November, 2018.
Malau, A., Sutarto, B., Ghozali, F., Istono, N., and Sukotrihadiyono, T. (2017). “Integrated sand control technique utilization of thru tubing sand screen and wellhead de-Sander technology,” in Abu Dhabi International Petroleum Exhibition and Conference, Abu Dhabi, UAE, November, 2017.
Mandhari, S., Al-Amri, N., Riyami, S., Busaidi, I., Saadi, F., Kayumov, R., et al. (2022). “Unlocking oil potential in mature oil fields using sand agglomeration technology and eliminating artificial lift pre-mature failures,” in ADIPEC, Abu Dhabi, UAE, October, 2022.
Martin, W. L., Alexander, J. D., and Dew, J. N. (1958). Process variables of in situ combustion. Trans. AIME 213 (01), 28–35. doi:10.2118/914-g
Matanovic, D., Cikes, M., and Moslavac, B. (2012) Sand control in well construction and operation. Berlin, Germany: Springer.
Mayorga Cespedes, E. A., Roostaei, M., Uzcátegui, A. A., Soroush, M., Izadi, H., Hosseini, S. A., et al. (2020). “Sand control optimization for rubiales field: trade-off between sand control, flow performance and mechanical integrity,” in SPE Latin American and Caribbean Petroleum Engineering Conference, Virtual, July, 2017.
Merzoug, A., Pandey, V., Rasouli, V., Damjanac, B., and Pu, H. (2023). Comparison of lattice and pseudo 3D numerical simulation of tip screen out operation. Petroleum 9 (3), 454–467. doi:10.1016/j.petlm.2023.03.004
Minnich, J. L., Biggs, T. J., and Rhoades, A. M. (2021) Polymer foam articles and methods of making polymer foams:US202117333254P. US11225561B2.
Morita, N., Burton, R. C., and Davis, E. (1998). Fracturing, frac packing, and formation failure control: can screenless completions prevent sand production? SPE Drill. Complet. 13 (03), 157–162. doi:10.2118/51187-pa
Naranjo-Agudelo, A. J. (2021). “A new methodology for selecting sand control or sand management as strategy in wells with sand production potential,” in ISRM 9th International Symposium on Geomechanics, Virtual, May, 2021.
Nejati, H., Khamehchi, E., Derakhshan, A. A., and Shad, S. (2023). Synthesis and optimization of a Novel epoxy-based nanofluid for sand consolidation in oil wells. Geoenergy Sci. Eng. 230, 212217. doi:10.1016/j.geoen.2023.212217
Nie, S., Li, H., Hu, Z., Wen, M., Gao, S., Zhang, H., et al. (2023). A review of the research status and development prospects for gravel packing sand control in horizontal wells. Geoenergy Sci. Eng. 229, 212152. doi:10.1016/j.geoen.2023.212152
Ortega, L., Brito, L., and Ben-Naceur, K. (1996). “Hydraulic fracturing for control of sand production and asphaltene deposition in deep hot wells,” in SPE Annual Technical Conference and Exhibition, Denver, Colorado, October, 1996.
Parhizgar Keradeh, M., and Tabatabaei-Nezhad, S. A. (2023). Investigation of the effect of diethylene triamine pentaacetic acid chelating agent as an enhanced oil recovery fluid on wettability alteration of sandstone rocks. Petroleum Explor. Dev. 50 (3), 675–687. doi:10.1016/s1876-3804(23)60419-7
Peerakham, C., Haripogepornkul, N., Putthaworapoom, N., Direkmahamongkol, S., Thanasutives, P., Zin Ko Ko, T., et al. (2023). “Chemical sand consolidation and through-tubing gravel pack, the effective alternative sand control methods in zawtika field,” in International Petroleum Technology Conference, Bangkok, Thailand, March, 2023.
Piemontese, M., Colombo, M., Ripa, G., Dario, P., Singh, P., and Murphy, J. (2014). “Successful placement of an advancing sand and fines control chemical as a remedial sand control, using subsea flow lines from an FPSO,” in SPE Deepwater Drilling and Completions Conference, Galveston, Texas, USA, September, 2014.
Prasad, V., Sultan, H., Al-Rumaidh, A., Fateh, A., Altarif, N., Yudin, A., et al. (2020). “Advanced combination of proppant fracturing and sand control completion system unlocks gas potential of unconsolidated jauf formation in Bahrain,” in Abu Dhabi International Petroleum Exhibition and Conference, Abu Dhabi, UAE, November, 2020.
Ranjith, P. G., Perera, M. S. A., Perera, W. K. G., Choi, S. K., and Yasar, E. (2014). Sand production during the extrusion of hydrocarbons from geological formations: a review. J. Petroleum Sci. Eng. 124, 72–82. doi:10.1016/j.petrol.2014.10.017
Rawlings, H. E. (1958). Use of hydraulic fracturing equipment for formation sand control. J. Petroleum Technol. 10 (05), 29–32. doi:10.2118/950-g
Rodoplu, R. S., and Al-Mohanna, K. S. (2019). “Planning, design and optimization of CT intervention for the first successful multistage fracturing completion with sand control system in the region,” in Abu Dhabi International Petroleum Exhibition and Conference, Abu Dhabi, UAE, November, 2019.
Rodoplu, R. S., Brohi, I. G., Al-Mohanna, K. S., and Qahtani, A. A. (2023). “A new multistage fracturing completion approach for sanding formations,” in First Application in the Region. International Petroleum Technology Conference, Bangkok, Thailand, March, 2023.
Rozlan, M. R., Salleh, N. I., Magna Bela, S., Misron, M. a. P., and Kumar, S. (2022). “Single trip multizonal resin sand consolidation and fracturing, A novel technique in sand and fines control,” in ADIPEC, Abu Dhabi, UAE, October, 2022.
Safaei, A., Asefi, M., Ahmadi, M., Pourshamsi, T., Baloochestanzadeh, S., Khalilnezhad, A., et al. (2023a). Chemical treatment for sand production control: a review of materials, methods, and field operations. Petroleum Sci. 20 (3), 1640–1658. doi:10.1016/j.petsci.2023.02.013
Safaei, A., Asefi, M., Ahmadi, M., Pourshamsi, T., Baloochestanzadeh, S., Khalilnezhad, A., et al. (2023b). Chemical treatment for sand production control: a review of materials, methods, and field operations. Petroleum Sci. 20 (3), 1640–1658. doi:10.1016/j.petsci.2023.02.013
Schubert, H., Herrmann, W., and Rumpf, H. (1975). Deformation behaviour of agglomerates under tensile stress. Powder Technol. 11 (2), 121–131. doi:10.1016/0032-5910(75)80037-4
Shaffee, S. N., Luckham, P. F., Matar, O. K., Karnik, A., and Zamberi, M. S. (2019). Numerical investigation of sand-screen performance in the presence of adhesive effects for enhanced sand control. SPE J. 24 (05), 2195–2208. doi:10.2118/195686-pa
Shunchao, Z., Yugang, Z., Huaxiao, W., Baobing, S., Tao, F., Huaxing, C., et al. (2022). “Research and application of integrated technology of chemical sand control and stratified water injection in offshore oilfields injection well,” in 56th U.S. Rock Mechanics/Geomechanics Symposium, Bangkok, Thailand, August, 2022.
Singh, A., and Sharma, T. (2023). Implications of sand mobilization on stability and rheological properties of carbon dioxide foam and its transport mechanism in unconsolidated sandstone. Energy 263, 125772. doi:10.1016/j.energy.2022.125772
Singh, P., Ludanova, N., and Van Petegem, R. (2014). “Advancing chemical sand and fines control using zeta potential altering chemistry by using advanced fluid placement techniques,” in SPE International Symposium and Exhibition on Formation Damage Control, Lafayette, Louisiana, USA, February, 2014.
Solares, J. R., Bartko, K. M., and Habbtar, A. H. (2002). “Pushing the envelope: successful hydraulic fracturing for sand control strategy in high gas rate screenless completions in the jauf reservoir, Saudi arabia,” in International Symposium and Exhibition on Formation Damage Control, Lafayette, Louisiana, February, 2002.
Stephen Babagbemi, A., Mofunlewi, S., and Williams, C. (2023). “Remedial sand control using chemical sand consolidation, A field experience,” in SPE Nigeria Annual International Conference and Exhibition, Lagos, Nigeria, July, 2023.
Styward, B., Wijaya, R., Manalu, D., Wahyudhi, F., Setiawan, T., Dading, A. M., et al. (2018). “Sand conglomeration trial as an alternative to sand control: case study from mahakam delta, Indonesia,” in SPE Asia Pacific Oil and Gas Conference and Exhibition. 2018, Brisbane, Australia, October, 2018.
Tahirov, T., Allam, R., Mason, J., Twynam, A., Tanilir, B., Sweeney, K., et al. (2014). “Design and successful field execution of sand control completions in naturally fractured reservoirs,” in SPE International Symposium and Exhibition on Formation Damage Control, Lafayette, Louisiana, USA, February, 2014.
Tang, C., Ye, L., Yeap, W. J., Zulkifli, M. Z., Bt, M., Jeffry, S. J., et al. (2022). “Holistic performance review of through-tubing sand screen as remedial sand control: best practices and lesson learnt from past installations in offshore east Malaysia oil fields,” in ADIPEC, Abu Dhabi, UAE, October, 2022.
Tarek, M., and Leung, J. (2024). “Novel resin coated sand placement design guidelines for controlling proppant flowback post slickwater hydraulic fracturing treatments,” in SPE Hydraulic Fracturing Technology Conference and Exhibition, The Woodlands, Texas, USA, February, 2024.
Trujillo, E. J. T., Santin, Y., Ukoha, O., Caldarelli, R., Maier, R., Kiss, A., et al. (2023). “Internally catalyzed aqueous-based emulsion of curable epoxy resin sand consolidation treatment extends economical production in Austria's mature oil and gas fields,” in SPE Reservoir Characterisation and Simulation Conference and Exhibition, Abu Dhabi, UAE, January, 2023.
Ubuara, D. O., Olayinka, Y. A., Emujakporue, G. O., and Soronnadi-Ononiwu, G. C. (2024). Evaluation of formation susceptibility and sand production potential in an offshore field, Niger Delta Basin, Nigeria. Energy Geosci. 5 (1), 100213. doi:10.1016/j.engeos.2023.100213
Upchurch, E. R. (1999). “Near-wellbore halo effect resulting from tip screenout fracturing: its direct measurement and implication for sand control,” in SPE Annual Technical Conference and Exhibition, Houston, Texas, October, 1999.
Wang, J. L., Ren, G., Aitken, S., and Yuan, M. (2003). “An alternative wellbore stabilisation and sand control technology – application of expandable sand control system in ulti-lateral wells,” in SPE Asia Pacific Oil and Gas Conference and Exhibition, Jakarta, Indonesia, September, 2003.
Wang, X. (2018). Technology focus: sand management and sand control (october 2018). J. Petroleum Technol. 70 (10), 70. doi:10.2118/1018-0070-jpt
Wang, Y., and Sun, L. (2022). “Research and application of fracturing sand control technology optimization,” in Medium and low permeability heavy oil reservoirs. Editor J. e. Lin (Singapore: Springer Nature Singapore), 471–483.
Wildhack, S., Lesniak, C., Müssig, S., Strahammer, F., and Leitner, M. (2012). “Ceramic sand screens for sand control in unconsolidated reservoirs: application and sand retention capabilities in the maturing oil field, gaiselberg, Austria,” in SPE Annual Technical Conference and Exhibition, San Antonio, Texas, USA, October, 2012.
Wong, G. K., Fair, P. S., Bland, K. F., and Sherwood, R. S. (2003). “Balancing act: gulf of Mexico sand control completions, peak rate versus risk of sand control failure,” in SPE Annual Technical Conference and Exhibition, Denver, Colorado, October, 2003.
Yan, W., Li, F., Leng, G., Wang, H., Ma, Z., Yun, B., et al. (2023). Sand control screen erosion-failure prediction method in weakly consolidated sandstone reservoir. Geoenergy Sci. Eng. 224, 211616. doi:10.1016/j.geoen.2023.211616
Yang, S., Jiang, L., Liu, C., and Deng, Z. (2005). Surface simulation and sand proof effect test on composite perforation sand control technique. 14: 64–66+78.
Yeap, W. J., Idris, K. N., Sidek, S., Cheol, H. R., Kamat, D., Tang, C., et al. (2019). “Remedial sand control in mature fields: lessons learned from thru-tubing ceramic sand screen application in offshore east Malaysia,” in SPE/IATMI Asia Pacific Oil and Gas Conference and Exhibition, Bali, Indonesia, October, 2019.
Yushi, Z., Shi, S., Zhang, S., Yu, T., Tian, G., Ma, X., et al. (2021a). Experimental modeling of sanding fracturing and conductivity of propped fractures in conglomerate: a case study of tight conglomerate of Mahu sag in Junggar Basin, NW China. Petroleum Explor. Dev. 48, 1383–1392. doi:10.1016/s1876-3804(21)60294-x
Yushi, Z., Shi, S., Zhang, S., Yu, T., Tian, G., Ma, X., et al. (2021b). Experimental modeling of sanding fracturing and conductivity of propped fractures in conglomerate: a case study of tight conglomerate of Mahu sag in Junggar Basin, NW China. Petroleum Explor. Dev. 48, 1383–1392. doi:10.1016/s1876-3804(21)60294-x
Zhenxiang, Z., Yang, J., Zhang, Y., Wang, E., Meng, W., Qu, X., et al. (2020). “Prediction of sand production and optimization of sand control methods in the production test process of deep water gas wells,” in 54th U.S. Rock Mechanics/Geomechanics Symposium, June, 2020.
Zhou, F., Zong, Y., Liu, Y., Yang, X., Xiong, C., Zhang, S., et al. (2006). “Application and study of fine-silty sand control technique using fiber-complex high-pressure pack in sebei gas reservoir,” in SPE International Symposium and Exhibition on Formation Damage Control, Lafayette, Louisiana, USA, February, 2006.
Keywords: sand production, sand control technology, fracturing pack sand control technology, foamed polymer resin diverter technology, zeta potential sand control technology
Citation: He X, Pang Z, Ren L, Zhao L, Lu X, Wang Y and Liu P (2024) A critical review on analysis of sand producing and sand-control technologies for oil well in oilfields. Front. Energy Res. 12:1399033. doi: 10.3389/fenrg.2024.1399033
Received: 11 March 2024; Accepted: 29 April 2024;
Published: 24 May 2024.
Edited by:
Jiehao Wang, Chevron, United StatesReviewed by:
Hongyang Chu, University of Science and Technology Beijing, ChinaCopyright © 2024 He, Pang, Ren, Zhao, Lu, Wang and Liu. This is an open-access article distributed under the terms of the Creative Commons Attribution License (CC BY). The use, distribution or reproduction in other forums is permitted, provided the original author(s) and the copyright owner(s) are credited and that the original publication in this journal is cited, in accordance with accepted academic practice. No use, distribution or reproduction is permitted which does not comply with these terms.
*Correspondence: Pengcheng Liu, bHBjQGN1Z2IuZWR1LmNu
Disclaimer: All claims expressed in this article are solely those of the authors and do not necessarily represent those of their affiliated organizations, or those of the publisher, the editors and the reviewers. Any product that may be evaluated in this article or claim that may be made by its manufacturer is not guaranteed or endorsed by the publisher.
Research integrity at Frontiers
Learn more about the work of our research integrity team to safeguard the quality of each article we publish.