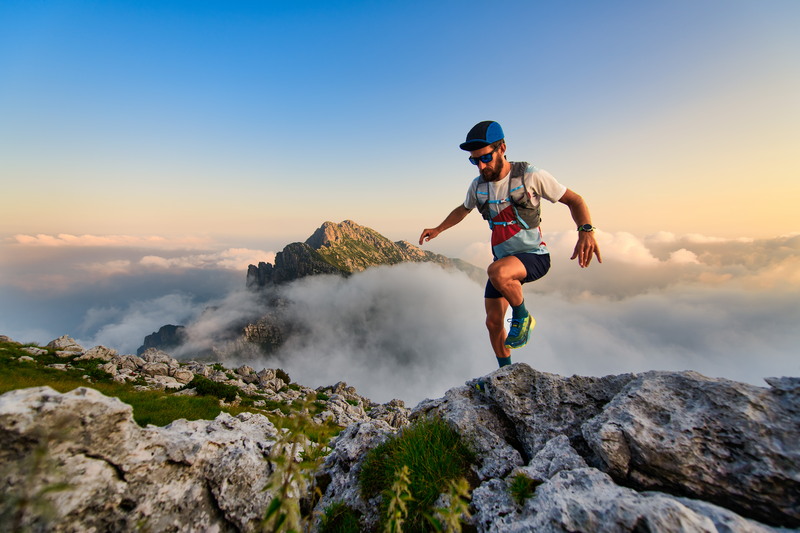
94% of researchers rate our articles as excellent or good
Learn more about the work of our research integrity team to safeguard the quality of each article we publish.
Find out more
MINI REVIEW article
Front. Energy Res. , 10 April 2024
Sec. Bioenergy and Biofuels
Volume 12 - 2024 | https://doi.org/10.3389/fenrg.2024.1382377
Achieving sustainable energy and material use mandates a critical focus on carbon recycling. The imperative for an efficient carbon cycle is paramount in sustainable energy systems and the chemical industry. Syngas, derived from waste and biomass gasification, offers a robust foundation for such recycling efforts. Various technologies, each with unique gas purity requirements, facilitate further refinement of syngas. This study provides a detailed and comparative analysis of the purity specifications necessary for both energetic and material utilization pathways.
Syngas offers a broad spectrum of applications for an efficient carbon cycle, aiming to decarbonize sectors such as energy, fuels, and chemicals by reducing dependency on fossil carbon. The primary constituents of syngas are hydrogen (H2), carbon monoxide (CO), and carbon dioxide (CO2). Various gasification technologies are employed to produce syngas. Noteworthy among these are the entrained flow reactor (EFR), fixed bed reactor (FBR), bubbling fluidized bed (BFB), circulating fluidized bed (CFB), rotary kiln (RK), and plasma reactor (PR) (Tijmensen, 2002; Molino et al., 2016). For syngas generation, sustainable carbon sources like biomass and sewage waste, or recycled fossil-based materials such as plastic waste, can be utilized. The specific feedstock determines the primary impurities and trace contaminants in syngas, which typically include particulate matter, tars (CxHy), nitrogen compounds (NH3, HCN, NOx), sulfur compounds (H2S, COS, CS2), halogens (HCl, Br, F), alkali metals (e.g., Na2CO3), and heavy metals (e.g., Pb, As).
Syngas applications can be divided broadly into two categories: material utilization, which involves converting syngas into valuable carbonaceous products like platform chemicals, and energetic utilization, which involves harnessing the chemically bound energy. This paper will detail the purity requirements for the array of processes in both the material and energetic utilization of syngas.
A myriad of research studies delves into the nature of impurities generated during the gasification of carbonaceous fuels, methodologies for removing these impurities from syngas, and the specific purity criteria required for various downstream processes in material and energy reuse. Comprehensive analyses of all impurities and their cleanup techniques are provided by Abdoulmoumine et al. (Abdoulmoumine et al., 2015), Woolcock et al. (Woolcock and Brown, 2013) and Asadullah et al. (Asadullah, 2014). The authors Rauch et al. (Rauch et al., 2014) and Litvinenko et al. (Litvinenko et al., 2018) offer detailed overviews of syngases practical applications.
However, existing studies do not collectively present an exhaustive overview of the purity requirements in the realms of material and energy utilization, particularly overlooking sub-processes such as biocatalysis and gas fermentation. To address this gap, this study categorizes the most common processes into two main groups: material utilization, and energetic utilization also called combined heat and power (CHP). An extensive literature review was conducted to ascertain the specific purity requirements for each category. Figure 1 depicts a comprehensive list of all investigated processes, categorized per the aforementioned criteria. On the left, the ratios of gas composition are displayed, while the right side illustrates the process products. For a direct comparison with syngas purity, all data is categorized and graphically compared. This includes both the highest purity requirement identified and the variance range across all surveyed literature. It should be noted that this analysis does not extend to evaluating the efficiency of these processes in terms of carbon conversion and overall efficiency.
Figure 1. Syngas utilization separated in possible pathways and their products. (d.p—depends on product, d.m—depends on microorganism).
The FTS process employs catalysts for the chemical production of liquid hydrocarbons and oxygenated compounds. This process is classified into two categories: low-temperature FTS, operating at 200°C–240°C for the production of waxes and/or diesel fuel using cobalt or iron catalysts, and high-temperature FTS, at 300°C–350°C, primarily for the production of olefins and gasoline with iron catalysts (Dayton et al., 2011). FTS reactors operate under pressures ranging from 10 to 60 bar. The exothermic nature of the reaction releases chemical energy in the form of heat (Boerrigter et al., 2005). Iron catalysts, while cost-effective and more impurity-tolerant, have a limited operational lifespan of a few weeks. Cobalt catalysts, on the other hand, are more efficient in hydrogenation and boast a longer operational lifespan of several years. However, contaminants like NH3, HCN, H2S, and COS can deactivate these catalysts. The literature cites maximum tolerable concentrations ranging between 10 ppbv and 10 ppmv for NH3, and 10 ppbv to 1 ppmv for HCN. Sulfur compounds such as H2S, CS2, and COS have concentration limits set between 10 and 100 ppbv. HCl, at concentrations above 10 ppbv in syngas, can cause catalyst corrosion. The presence of alkali metals, if not kept below 10 ppbv, can lead to deposition on the catalyst structure. Similarly, tars, especially those above the dew point or exceeding 1 ppmv, are associated with catalyst deactivation. Fouling from particles like dust, soot, and ash is expected at concentrations greater than 0.26 mg Nm−3 with particle sizes exceeding 2 µm. It is important to note that all tolerable concentrations are determined based on the economic optimum associated with the estimated catalyst lifetime. (Additional literature of the limits mentioned (Abdoulmoumine et al., 2015; Boerrigter et al., 2005; E4Tech, 2009; Boerrigter, 2002; Spath and Dayton, 2003; Woolcock and Brown, 2013; Borg et al., 2011; Hamelinck et al., 2004; Hu et al., 2022; Leibold et al., 2008))
Compared to traditional refining processes, fermentation stands out as a biocatalytic conversion process. In this process, anaerobic microbes or acetogenic microorganisms utilize syngas as a carbon source to metabolize and produce various acids like acetic, butyric, and hexanoic acid, alcohols including ethanol, isopropanol, butanol, and hexanol, along with other chemicals such as 2,3-butanediol, acetone, fatty acids, and fatty alcohols (Ramachandriya et al., 2016). Prominent microbial catalysts in this domain are M. thermoacetica, B. methylotrophicum, Clostridium ljungdahlii, Clostridium autoethanogenum, Acetobacterium woodii, Clostridium carboxidivorans, and Peptostreptococcus. The fermentation processes using various microorganisms and reactor technologies are comprehensively described by Acharya et al. (Acharya et al., 2014). Some studies indicate that biocatalytic conversion is somewhat less sensitive to impurities compared to chemical catalysis. Nevertheless, impurities do influence the fermentation process, and their effect varies significantly depending on the type of microorganism involved. For instance, inorganic and hydrocarbon impurities can diminish the fermentability of the gas if the particle size is smaller than 0.025 µm. Ammonia, at very high concentrations, inhibits the alcohol dehydrogenase (ADH) enzyme, while at lower concentrations, it serves as a nitrogen source for the bacteria. Nitric oxide (NO) in excess of 40 ppmv leads to the complete inhibition of hydrogenase and ADH, thus curtailing the carbon available for product formation. Nitrite (NO2) inhibits both formate dehydrogenase (FDH) and nitrate reductase at a concentration of 1 mol m−3. Hydrogen sulfide (H2S) at levels less than 30 mol m−3 impedes Thiosulfate Sulfurtransferase (TS) and L-ascorbate oxidase (LAO), while carbonyl sulfide (COS) adversely affects carbon monoxide dehydrogenase (CODH) and sulfur dioxide (SO2) impacts Ascorbic acid oxidase (AAO). The production efficiency also declines with increasing oxygen concentrations; oxygen levels exceeding 293 ppmv inhibit the enzyme pyruvate-ferredoxin oxidoreductase hydrogenase and lead to an increase in redox potential (Munasinghe and Khanal, 2010; Xu et al., 2011; Daniell et al., 2012; Acharya et al., 2014; Sun et al., 2019). In terms of solid impurities, many studies focus on their impact on the medium, with assumptions about gas concentration being made based on the complete solubility of these impurities. Although hydrogen cyanide (HCN) is known for its high cytotoxic impact on fermentation, comprehensive data on its maximum concentration is limited. However, a successful fermentation process conducted by Rückel et al. (Rückel et al., 2022) at an HCN concentration below 1 ppmv suggests this as a feasible upper limit. It is also important to note that the yield of fermentation products is profoundly influenced by factors such as nutrient components, temperature, pressure, pH, flow conditions, and the concentration of products in the medium. (Additional literature of the limits mentioned (E4Tech, 2009; Ahmed and Lewis, 2007; Rückel et al., 2022; Acharya et al., 2014; Xu et al., 2011; Sun et al., 2019; Munasinghe and Khanal, 2010; Daniell et al., 2012; Ramachandriya et al., 2016))
Large-scale methanol production is predominantly carried out through steam reforming of natural gas. The synthesis of methanol from syngas and steam typically utilizes catalysts based on copper oxide, zinc oxide, or chromium oxide, operating at pressures of 50–100 bar and temperatures between 230°C–350°C (Dayton et al., 2011). Small concentrations of CO2 can act as promoters for the primary hydrogenation reactions, which are exothermic and result in a reduction of molar volume. Catalyst deactivation often occurs due to the blockage of active sites, leading to reduced activity. The formation of inactive copper salts due to poisoning by sulfur and halogens also contributes to a decrease in surface area (Rauch et al., 2014). The literature specifies concentration limits for H2S and COS (<100 ppbv), as well as halides (<1 ppbv). The presence of alkali or other trace metals can inadvertently catalyze side reactions, such as Fischer-Tropsch synthesis (FTS) and Mixed alcohol synthesis (MAS) (E4Tech, 2009). To prevent this, concentrations should be restricted to alkali <10 ppbv and heavy metals (HM) < 0.01 ppmv. The maximum allowable concentration of nitrogen compounds is typically set at NH3 and HCN <10 ppbv and NO < 100 ppmv. (Additional literature of the limits mentioned (E4Tech, 2009; Boerrigter et al., 2005; Spath and Dayton, 2003; Woolcock and Brown, 2013))
MAS utilizes a catalytic process with catalysts similar to those used in FTS and methanol synthesis. Cu and Zn-based catalysts, when modified with alkali metals, can enhance alcohol-based reactions, leading to a product mix similar to that of bio-catalytic fermentation of syngas. The typical products include methanol, ethanol, propanol, butanol, and longer-chain alcohols. Due to the similarities of these catalysts with those used in FTS and methanol synthesis, the challenges and limitations encountered are largely comparable (Fang et al., 2009). According to adapted literature values, the maximum concentration ranges for nitrogen impurities should be below 0.01 ppmv, sulfur impurities between 0.06–100 ppmv, and HCl from 1–10 ppbv to avoid catalyst deactivation. Particle deposition can occur at concentrations greater than 0.26 mg Nm−3 with a particle size of 2 µm. Moreover, tars need to be nearly completely removed to prevent interference with the catalytic process. (Additional literature of the limits mentioned (Christensen et al., 2011; E4Tech, 2009))
BioSNG is produced through the methanation of syngases, fundamentally relying on the hydration of CO and CO2 in two separate exothermic reactions (Rönsch et al., 2016). The reactor design, along with the catalyst used, plays a crucial role in determining the conversion efficiency and selectivity of this process. Mills et al. (Mills and Steffgen, 1974) have provided a comprehensive overview of the activity and selectivity of various active metals in these catalysts, ranking them as Ru > Fe > Ni > Co > Mo for activity, and Ni > Co > Fe > Ru for selectivity. The choice of support material and promoters also significantly affects the catalyst reactivity and lifespan. Catalysts in the SNG production process are sensitive to various impurities. H2S, for instance, can lead to chemisorption on the catalytic sites, resulting in deactivation. Its concentration should be maintained within 0.one to four ppmv. COS limits are cited in the literature as being up to 8 ppmv. Tars, at concentrations below 1 mg/Nm³, can lead to physical deposition on the surface area or coke deposition on the nickel surface via the Boudouard reaction. NH3 has a maximum permissible concentration of 1 ppmv. It is noteworthy that ammonia can also be formed as a side reaction during the methanation process (Kiendl et al., 2014). (Additional literature of the limits mentioned (Kaltschmitt et al., 2016; Molino et al., 2018; E4Tech, 2009; Fendt, 2020; Kopyscinski et al., 2010; Neubert et al., 2017; Zwart et al., 2006))
Currently, the majority of hydrogen production is achieved through steam reforming of hydrocarbons, wherein the resulting syngas is further processed to extract hydrogen. This method is also applicable for syngas derived from gasification processes. The contained CO is converted into H2 and CO2 through the Water Gas Shift (WGS) reaction (Ciferno, 2002; Rauch et al., 2014; Wagemann and Tippkötter, 2019). However, information regarding the compatibility of trace substances in the catalytic WGS reaction is relatively scarce. Various catalysts are employed in WGS, including CuZn-oxide for the low-temperature shift (LTS) at 180°C–270°C, FeCr-oxide for the high-temperature shift (HTS) at 300°C–530°C (Wang et al., 2008), and Co-Mo/Al-oxide for the sour gas shift (SGS) at 230°C–500°C (Babita et al., 2011). H2S is known to negatively affect the catalysts used in LTS and HTS (Loipersböck et al., 2017), whereas SGS catalysts exhibit tolerance to high concentrations of sulfur components. Another avenue for the shift reaction and hydrogen separation involves the use of membrane reactors. For instance, a Pd-based membrane can efficiently separate a high-purity H2 stream with notable selectivity (You et al., 2018). However, the effects of typical impurities on such membranes remain largely unexplored. Abdollahi et al. have investigated key impurities like H2S and NH3, which can adversely affect the membrane (Abdollahi et al., 2010). In their study, a carbon molecular sieve (CMS) membrane and an impurity-tolerant commercial Co/Mo/Al2O3 catalyst were utilized for in situ hydrogen separation. At lower temperatures (<150°C), a decrease in permeability was observed. Literature indicates the limits for H2S range between 0.1–220 ppmv, and for HCl between 0.001–50 ppmv. It is important to note that impurities which may not affect WGS catalysis could be detrimental to downstream synthesis processes. (Additional literature of the limits mentioned (Mellor et al., 1997; Schaidle et al., 2010; Veksha et al., 2018; Dou et al., 2019))
ICEs utilize syngas as a fuel, with air typically serving as the oxidizing medium for converting it into mechanical energy and heat. Pradhan et al. provide comprehensive insights into the use of syngas in ICE processes (Pradhan et al., 2015). Existing literature specifies certain limits regarding particulates and hydrocarbons. The reviewed studies indicate that the minimum purity requirement for particles should be 50 mg Nm−3, with particle sizes ranging between 3–10 µm. Particulates like sand and ash primarily cause cohesive wear damage to moving parts. Conversely, tars can condense, leading to the clogging of process instruments and piping; thus, a maximum limit of 100 mg Nm−3 for hydrocarbons is advised. The literature, however, does not specify exact purity requirements for trace gases. Here, the concerns are twofold: corrosion and compliance with exhaust gas emission standards. Alkali elements in ashes and sulfur compounds are known to cause corrosion. A few sources suggest a maximum sulfur component concentration of <1,150 mg Nm−3 and alkali concentration of <50 mg Nm−3. Halides, which can react with installed materials causing damage, have a recommended guideline value of HCl <330 ppmv, based on limited available data. Nitrogen compounds do not pose material compatibility issues. However, the oxidation of NH3 and HCN leads to the formation of nitrogen oxides, which are regulated in exhaust emissions. Depending on the combustion quality of the ICE, an upper limit for NH3 concentration is set at <78 ppmv (Hasler and Nussbaumer, 1999; Spliethoff, 2010; Higman and van der Burgt, 2011; Kaltschmitt et al., 2016). Whitty et al. have conducted detailed studies on emissions resulting from syngas combustion (Whitty et al., 2008). (Additional literature of the limits mentioned (Baratieri et al., 2022; Martínez et al., 2012))
GTs are predominantly utilized in Gas Turbine Combined-Cycle (GTCC) systems, offering a reliable and efficient method for energy and heat conversion. Wright et al. detail the technology involved in firing syngas in GTs (Wright and Gibbons, 2007). GTs encounter challenges similar to ICEs, but with stricter purity requirements for the combustion gas. Particulates from the gasification process can damage blades and other moving parts. It is suggested that particle concentration should be maintained below 20–30 mg Nm−3, with a maximum particle size of 0.1–5 µm. While tars cannot condense in the high-temperature environment of the combustion chamber, condensing hydrocarbons can cause blockages as the process progresses. Literature indicates a maximum concentration limit of 5 mg Nm−3 for hydrocarbons, which is particularly problematic in heat exchangers and compressors. The impact of trace substances in GTs can be paralleled to those in ICEs (Baratieri et al., 2009). Examined limits for GTs include 50 ppmv for nitrogen compounds concerning emissions and ranges of 1–20 ppmv for sulfur compounds, 1–160 ppmv for HCl, and up to 0.24 mg Nm−3 for alkali metals. (Additional literature of the limits mentioned (Higman and van der Burgt, 2008; Spliethoff, 2010; Kaltschmitt et al., 2016))
SOFCs present an efficient alternative to combustion-based technologies for syngas conversion in energy and heat recovery. Operating on the principle of a galvanic cell with separate oxidation and reduction processes, SOFCs are extensively described by Radenahmad et al. (Radenahmad et al., 2022). There have been numerous studies on the degradation of fuel cells utilizing coal and biomass-derived syngas. Various material combinations can serve as anode materials, notably Ni-Yttria stabilized Zirconia (Ni-YSZ) and nickel-gadolinia doped ceria (Ni-GDC). Key issues for anode materials include carbon deposition due to hydrocarbons, and chemical degradation by sulfur components and halides. Particle sizes of 5–10 μm at concentrations exceeding 23 mg Nm−3 can clog anode pores, resulting in performance degradation. While tars are not inherently detrimental to SOFCs and can undergo reforming or oxidation, initial concentrations of 10–100 mg Nm−3 may lead to carbon deposition and catalyst deactivation. The anode is particularly susceptible to degradation from sulfur poisoning, carbon deposition, and mechanical instability. Sulfur impedes the active sites for hydrocarbon conversion and forms nickel sulfide (NiS), progressively reducing performance. Various sources suggest a maximum tolerance of 0.01–200 ppmv H2S. Chlorine compounds, particularly HCl at concentrations between 1–160 ppmv HCl, significantly diminish performance. Conversely, ammonia is potentially beneficial, dissociating into H2 and N2, with a tolerance threshold up to 5,000 ppmv. Some literature indicates that ammonia removal may not be necessary for SOFC operation. (Additional literature of the limits mentioned (Cayan et al., 2008; Hofmann et al., 2009; Laycock et al., 2011; Cayan et al., 2012; Lorente et al., 2012; Ud Din and Zainal, 2016; Marcantonio et al., 2022))
The analysis contrasts various downstream routes for material utilization, comparing alcohol production (Figure 2A), the creation of longer-chain hydrocarbons (Figure 2B), and the application in energetic applications (Figure 2C). In these figures, the solid lines represent the highest purity level required for each component as indicated in the literature, while the colored, translucent areas depict the range extending to the lowest required purity level.
Figure 2. Based on state of the art limit values obtained from literature. (A) Material utilization pathways (methanol & mixed alcohol production) (B) Material utilization pathways (gas, gasoline, diesel, paraffine waxes,…) (C) Energetic utilization pathways. *Assumed ash composition from beech wood for converting from ppm to mg Nm−3 (Vassilev et al., 2013).
In alcohol production, biocatalytic processing demonstrates substantial robustness towards a wide spectrum of syngas impurities. HCN is identified as the most critical component in the biological process, with a maximum concentration threshold of 1 ppmv. Chemical catalysts used in alcohol production, however, require stringent removal of catalyst poisons like sulfur and halides, necessitating a reduction of all listed impurities below 1 ppmv consistently.
Comparatively, in the domain of energetic applications, ICEs are categorized as the most robust process. The highest purity requirements for sulfur components, halogens, nitrogen compounds, and particulate impurities in ICEs are noted to be lower than those for GTs and SOFCs. The primary challenges in ICEs involve deposition, fouling, and corrosion caused by particles, tars, halides, and alkalis. Table 1 outlines all values used in Figure 2 with the maximum requirement of the respective gas component.
Table 1. Summary of maximum limit values by process and impurity, as derived from current literature. * No literature data available.
In the changing economic environment, the utilization of carbon sources from sustainable sectors is gaining increasing importance. Within this context, a critical trade-off emerges between the benefits offered by these sources and the purity requirements they necessitate. Generally, processes aimed at generating energy and heat are considered more robust, characterized by lower purity requirements for the utilized syngas. However, the necessity for gas cleaning remains. The extent of cleaning required largely depends on the gasification technology employed and the resultant level of contamination (Dayton et al., 2011). Crucially, the intended final product plays a pivotal role in determining the selection of technology. Nonetheless, the cost and complexity associated with purification should not be overlooked, as the intricacies of the separation process can significantly impact the economic feasibility of the overall operation.
PL: Writing–original draft, Writing–review and editing. SF: Funding acquisition, Project administration, Resources, Supervision, Writing–original draft, Writing–review and editing. HS: Funding acquisition, Project administration, Resources, Supervision, Writing–original draft, Writing–review and editing.
The author(s) declare that financial support was received for the research, authorship, and/or publication of this article. This study was carried out in the framework of the projects “VERENA” (project no.: 03EE5044B) sponsored by the Federal Ministry for Economic Affairs and Climate Action (Germany) and “ReGasFerm” (project no.: 031B0677A) sponsored by the Federal Ministry of Education and Research (Germany).
The authors declare that the research was conducted in the absence of any commercial or financial relationships that could be construed as a potential conflict of interest.
All claims expressed in this article are solely those of the authors and do not necessarily represent those of their affiliated organizations, or those of the publisher, the editors and the reviewers. Any product that may be evaluated in this article, or claim that may be made by its manufacturer, is not guaranteed or endorsed by the publisher.
Abdollahi, M., Yu, J., Hwang, H. T., Liu, P. K., Ciora, R., Sahimi, M., et al. (2010). Process intensification in hydrogen production from biomass-derived syngas. Ind. Eng. Chem. Res. 49 (21), 10986–10993. doi:10.1021/ie100620e
Abdoulmoumine, N., Adhikari, S., Kulkarni, A., and Chattanathan, S. (2015). A review on biomass gasification syngas cleanup. Appl. Energy 155, 294–307. doi:10.1016/j.apenergy.2015.05.095
Acharya, B., Roy, P., and Dutta, A. (2014). Review of syngas fermentation processes for bioethanol. Biofuels 5 (5), 551–564. doi:10.1080/17597269.2014.1002996
Ahmed, A., and Lewis, R. S. (2007). Fermentation of biomass-generated synthesis gas: effects of nitric oxide. Biotechnol. Bioeng. 97 (5), 1080–1086. doi:10.1002/bit.21305
Asadullah, M. (2014). Biomass gasification gas cleaning for downstream applications: a comparative critical review. Renew. Sustain. Energy Rev. 40, 118–132. doi:10.1016/j.rser.2014.07.132
Babita, K., Sridhar, S., and Raghavan, K. V. (2011). Membrane reactors for fuel cell quality hydrogen through WGSR – review of their status, challenges and opportunities. Int. J. Hydrogen Energy 36 (11), 6671–6688. doi:10.1016/j.ijhydene.2011.02.107
Baratieri, M., Baggio, P., Bosio, B., Grigiante, M., and Longo, G. A. (2009). The use of biomass syngas in IC engines and CCGT plants: a comparative analysis. Appl. Therm. Eng. 29 (16), 3309–3318. doi:10.1016/j.applthermaleng.2009.05.003
Baratieri, M., Baggio, P., Bosio, B., Grigiante, M., and Longo, G. A. (2022). The use of biomass syngas in IC engines and CCGT plants: a comparative analysis.
Boerrigter, H. Green diesel from biomass via fischer-tropsch synthesis: new insights in gas cleaning and process design. Pyrolysis and gasification of biomass and waste, expert meeting,; 2002, .
Boerrigter, H., and Rauch, R. (2005). “Review of applications of gases from biomass gasification. “Syngas production and utilisation”,” in The handbook biomass gasification. Editor H. A. M. Knoef (China: published by the Biomass Technology Group BTG), 2005.
Borg, Ø., Hammer, N., Enger, B. C., Myrstad, R., Lindvåg, O. A., Eri, S., et al. (2011). Effect of biomass-derived synthesis gas impurity elements on cobalt Fischer–Tropsch catalyst performance including in situ sulphur and nitrogen addition. J. Catal. 279 (1), 163–173. doi:10.1016/j.jcat.2011.01.015
Cayan, F. N., Pakalapati, S. R., Celik, I., Xu, C., and Zondlo, J. (2012). A degradation model for solid oxide fuel cell anodes due to impurities in coal syngas: Part I theory and validation. Fuel Cells 12 (3), 464–473. doi:10.1002/fuce.201100027
Cayan, F. N., Zhi, M., Pakalapati, S. R., Celik, I., Wu, N., and Gemmen, R. (2008). Effects of coal syngas impurities on anodes of solid oxide fuel cells. J. Power Sources 185 (2), 595–602. doi:10.1016/j.jpowsour.2008.06.058
Christensen, J. M., Jensen, P. A., and Jensen, A. D. (2011). Effects of feed composition and feed impurities in the catalytic conversion of syngas to higher alcohols over alkali-promoted cobalt–molybdenum sulfide. Ind. Eng. Chem. Res. 50 (13), 7949–7963. doi:10.1021/ie200235e
Daniell, J., Köpke, M., and Simpson, S. (2012). Commercial biomass syngas fermentation. Energies 5 (12), 5372–5417. doi:10.3390/en5125372
Dayton, D. C., Turk, B., and Gupta, R. (2011). “Syngas cleanup, conditioning, and utilization,” in Thermochemical processing of biomass. Editor R. C. Brown (Chichester, UK: John Wiley & Sons, Ltd), 78–123.
Dou, X., Veksha, A., Chan, W. P., Oh, W., Liang, Y. N., Teoh, F., et al. (2019). Poisoning effects of H2S and HCl on the naphthalene steam reforming and water-gas shift activities of Ni and Fe catalysts. Fuel 241, 1008–1018. doi:10.1016/j.fuel.2018.12.119
E4Tech (2009). Review of Technologies for Gasification of Biomass and Wastes A project funded by DECC, project managed by NNFCC and conducted by E4Tech. NNFCC Proj. 09/008.
Fang, K., Li, D., Lin, M., Xiang, M., Wei, W., and Sun, Y. (2009). A short review of heterogeneous catalytic process for mixed alcohols synthesis via syngas. Catal. Today 147 (2), 133–138. doi:10.1016/j.cattod.2009.01.038
Fendt, S. (2020). Experimental investigation of a combined biomass-to-gas/power-to-gas concept for the production of synthetic natural gas (SNG). Dr. Hut. (Energietechnik) ISBN: 978-3-8439-4395-6.
Hamelinck, C., Faaij, A., Denuil, H., and Boerringter, H. (2004). Production of FT transportation fuels from biomass; technical options, process analysis and optimisation, and development potential. Energy 29 (11), 1743–1771. doi:10.1016/j.energy.2004.01.002
Hasler, P., and Nussbaumer, T. (1999). Gas cleaning for IC engine applications from fixed bed biomass gasification. Biomass Bioenergy 16 (6), 385–395. doi:10.1016/s0961-9534(99)00018-5
Higman, C., and van der Burgt, M. (2008).Gasification. Estados Unidos: Gulf Professional Pub./Elsevier Science.
Hofmann, P., Panopoulos, K. D., Aravind, P. V., Siedlecki, M., Schweiger, A., Karl, J., et al. (2009). Operation of solid oxide fuel cell on biomass product gas with tar levels >10 g Nm−3. Int. J. Hydrogen Energy 34 (22), 9203–9212. doi:10.1016/j.ijhydene.2009.07.040
Hu, J., Yu, F., and Lu, Y. (2022). Application of fischer–tropsch synthesis in biomass to liquid conversion.
M. Kaltschmitt, H. Hartmann, and H. Hofbauer (2016). “Energie aus Biomasse. 3,” Aktualisierte Aufl (Berlin, Heidelberg: Springer Berlin Heidelberg: Springer Vieweg).
Kiendl, I., Klemm, M., Clemens, A., and Herrman, A. (2014). Dilute gas methanation of synthesis gas from biomass gasification. Fuel 123, 211–217. doi:10.1016/j.fuel.2014.01.036
Kopyscinski, J., Schildhauer, T. J., and Biollaz, S. M. (2010). Production of synthetic natural gas (SNG) from coal and dry biomass – a technology review from 1950 to 2009. Fuel 89 (8), 1763–1783. doi:10.1016/j.fuel.2010.01.027
Laycock, C. J., Staniforth, J. Z., and Ormerod, R. M. (2011). Biogas as a fuel for solid oxide fuel cells and synthesis gas production: effects of ceria-doping and hydrogen sulfide on the performance of nickel-based anode materials. Dalton Trans. 40 (20), 5494–5504. doi:10.1039/c0dt01373k
Leibold, H., Hornung, A., and Seifert, H. (2008). HTHP syngas cleaning concept of two stage biomass gasification for FT synthesis. Powder Technol. 180 (1-2), 265–270. doi:10.1016/j.powtec.2007.05.012
Litvinenko, V., and Meyer, B. (2018). “Syngas utilization technologies,” in Syngas production: status and potential for implementation in Russian industry. Editors V. Litvinenko, and B. Meyer (Cham: Springer International Publishing), 23–46.
Loipersböck, J., Lenzi, M., Rauch, R., and Hofbauer, H. (2017). Hydrogen production from biomass: the behavior of impurities over a CO shift unit and a biodiesel scrubber used as a gas treatment stage. Korean J. Chem. Eng. 34 (8), 2198–2203. doi:10.1007/s11814-017-0130-1
Lorente, E., Millan, M., and Brandon, N. P. (2012). Use of gasification syngas in SOFC: impact of real tar on anode materials. Int. J. Hydrogen Energy 37 (8), 7271–7278. doi:10.1016/j.ijhydene.2011.11.047
Marcantonio, V., Del Zotto, L., Ouweltjes, J. P., and Bocci, E. (2022). Main issues of the impact of tar, H2S, HCl and alkali metal from biomass-gasification derived syngas on the SOFC anode and the related gas cleaning technologies for feeding a SOFC system: a review. Int. J. Hydrogen Energy 47 (1), 517–539. doi:10.1016/j.ijhydene.2021.10.023
Martínez, J. D., Mahkamov, K., Andrade, R. V., and Silva Lora, E. E. (2012). Syngas production in downdraft biomass gasifiers and its application using internal combustion engines. Renew. Energy 38 (1), 1–9. doi:10.1016/j.renene.2011.07.035
Mellor, J. R., Copperthwaite, R. G., and Coville, N. J. (1997). The selective influence of sulfur on the performance of novel cobalt-based water-gas shift catalysts. Appl. Catal. A General 164 (1-2), 69–79. doi:10.1016/s0926-860x(97)00158-0
Mills, G. A., and Steffgen, F. W. (1974). Catalytic methanation. Catal. Rev. 8 (1), 159–210. doi:10.1080/01614947408071860
Molino, A., Chianese, S., and Musmarra, D. (2016). Biomass gasification technology: the state of the art overview. J. Energy Chem. 25 (1), 10–25. doi:10.1016/j.jechem.2015.11.005
Molino, A., Larocca, V., Chianese, S., and Musmarra, D. (2018). Biofuels production by biomass gasification: a review. Energies 11 (4), 811. doi:10.3390/en11040811
Munasinghe, P. C., and Khanal, S. K. (2010). Biomass-derived syngas fermentation into biofuels: opportunities and challenges. Bioresour. Technol. 101 (13), 5013–5022. doi:10.1016/j.biortech.2009.12.098
Neubert, M., Treiber, P., Krier, C., Hackel, M., Hellriegel, T., Dillig, M., et al. (2017). Influence of hydrocarbons and thiophene on catalytic fixed bed methanation. Fuel 207, 253–261. doi:10.1016/j.fuel.2017.06.067
Pradhan, A., Baredar, P., and Kumar, A. (2015). Syngas as an alternative fuel used in internal combustion engines: a review. J. Pure Appl. Sci. Technol. 5, 51–66. ISSN: 2249-9970.
Radenahmad, N., Azad, A. T., Saghir, M., Taweekun, J., Bakar, M. S., Reza, M. S., et al. (2022). A review on biomass derived syngas for SOFC based combined heat and power application.
Ramachandriya, K. D., Kundiyana, D. K., Sharma, A. M., Kumar, A., Atiyeh, H. K., Huhnke, R. L., et al. (2016). Critical factors affecting the integration of biomass gasification and syngas fermentation technology. AIMS Bioeng. 3 (2), 188–210. doi:10.3934/bioeng.2016.2.188
Rauch, R., Hrbek, J., and Hofbauer, H. (2014). Biomass gasification for synthesis gas production and applications of the syngas. WIREs Energy Environ. 3 (4), 343–362. doi:10.1002/wene.97
Rönsch, S., Schneider, J., Matthischke, S., Schlüter, M., Götz, M., Lefebvre, J., et al. (2016). Review on methanation – from fundamentals to current projects. Fuel 166, 276–296. doi:10.1016/j.fuel.2015.10.111
Rückel, A., Oppelt, A., Leuter, P., Johne, P., Fendt, S., and Weuster-Botz, D. (2022). Conversion of syngas from entrained flow gasification of biogenic residues with Clostridium carboxidivorans and Clostridium autoethanogenum. Fermentation 8 (9), 465. doi:10.3390/fermentation8090465
Schaidle, J. A., Lausche, A. C., and Thompson, L. T. (2010). Effects of sulfur on Mo2C and Pt/Mo2C catalysts: water gas shift reaction. J. Catal. 272 (2), 235–245. doi:10.1016/j.jcat.2010.04.004
Spath, P. L., and Dayton, D. C. (2003). Preliminary screening - technical and economic assessment of synthesis gas to fuels and chemicals with emphasis on the potential for biomass-derived syngas. NREL/TP-510-34929.
Spliethoff, H. (2010). Power generation from solid fuels. Berlin, Heidelberg: Springer Berlin Heidelberg. (Power Systems).
Sun, X., Atiyeh, H. K., Huhnke, R. L., and Tanner, R. S. (2019). Syngas fermentation process development for production of biofuels and chemicals: a review. Bioresour. Technol. Rep. 7, 100279. doi:10.1016/j.biteb.2019.100279
Tijmensen, M. (2002). Exploration of the possibilities for production of Fischer Tropsch liquids and power via biomass gasification. Biomass Bioenergy 23 (2), 129–152. doi:10.1016/s0961-9534(02)00037-5
Ud Din, Z., and Zainal, Z. A. (2016). Biomass integrated gasification–SOFC systems: technology overview. Renew. Sustain. Energy Rev. 53, 1356–1376. doi:10.1016/j.rser.2015.09.013
Vassilev, S. V., Baxter, D., Andersen, L. K., and Vassileva, C. G. (2013). An overview of the composition and application of biomass ash. Part 1. Phase–mineral and chemical composition and classification. Fuel 105, 40–76. doi:10.1016/j.fuel.2012.09.041
Veksha, A., Giannis, A., Oh, W., Chang, V. W., Lisak, G., and Lim, T. (2018). Catalytic activities and resistance to HCl poisoning of Ni-based catalysts during steam reforming of naphthalene. Appl. Catal. A General 557, 25–38. doi:10.1016/j.apcata.2018.03.005
Wagemann, K., and Tippkötter, N. (2019). Biorefineries, 166. Cham: Springer International Publishing.
Wang, L., Weller, C. L., Jones, D. D., and Hanna, M. A. (2008). Contemporary issues in thermal gasification of biomass and its application to electricity and fuel production. Biomass Bioenergy 32 (7), 573–581. doi:10.1016/j.biombioe.2007.12.007
Whitty, K. J., Zhang, H. R., and Eddings, E. G. (2008). Emissions from syngas combustion. Combust. Sci. Technol. 180 (6), 1117–1136. doi:10.1080/00102200801963326
Woolcock, P. J., and Brown, R. C. (2013). A review of cleaning technologies for biomass-derived syngas. Biomass Bioenergy 52, 54–84. doi:10.1016/j.biombioe.2013.02.036
Wright, I., and Gibbons, T. (2007). Recent developments in gas turbine materials and technology and their implications for syngas firing. Int. J. Hydrogen Energy 32 (16), 3610–3621. doi:10.1016/j.ijhydene.2006.08.049
Xu, D., Tree, D. R., and Lewis, R. S. (2011). The effects of syngas impurities on syngas fermentation to liquid fuels. Biomass Bioenergy 35 (7), 2690–2696. doi:10.1016/j.biombioe.2011.03.005
You, S., Ok, Y. S., Tsang, D. C., Kwon, E. E., and Wang, C. (2018). Towards practical application of gasification: a critical review from syngas and biochar perspectives. Crit. Rev. Environ. Sci. Technol. 48 (22-24), 1165–1213. doi:10.1080/10643389.2018.1518860
Keywords: syngas, utilization and requirements, impurity limits, gasification, energy and material pathways
Citation: Leuter P, Fendt S and Spliethoff H (2024) Requirements on synthesis gas from gasification for material and energy utilization: a mini review. Front. Energy Res. 12:1382377. doi: 10.3389/fenrg.2024.1382377
Received: 05 February 2024; Accepted: 26 March 2024;
Published: 10 April 2024.
Edited by:
Jean-Henry Ferrasse, Aix-Marseille Université, FranceReviewed by:
Fabrizio Scala, University of Naples Federico II, ItalyCopyright © 2024 Leuter, Fendt and Spliethoff. This is an open-access article distributed under the terms of the Creative Commons Attribution License (CC BY). The use, distribution or reproduction in other forums is permitted, provided the original author(s) and the copyright owner(s) are credited and that the original publication in this journal is cited, in accordance with accepted academic practice. No use, distribution or reproduction is permitted which does not comply with these terms.
*Correspondence: Philipp Leuter, cGhpbGlwcC5sZXV0ZXJAdHVtLmRl
Disclaimer: All claims expressed in this article are solely those of the authors and do not necessarily represent those of their affiliated organizations, or those of the publisher, the editors and the reviewers. Any product that may be evaluated in this article or claim that may be made by its manufacturer is not guaranteed or endorsed by the publisher.
Research integrity at Frontiers
Learn more about the work of our research integrity team to safeguard the quality of each article we publish.