- Georgia Institute of Technology, Atlanta, GA, United States
As robot technologies are rapidly improving, an increasing number of new ideas on utilizing robots for automated operation and maintenance tasks in nuclear power plants (NPPs) are being studied. However, due to safety concerns, researchers hardly found opportunities to test their new robot solutions on physical NPPs. In that sense, an efficient and realistic simulation environment plays a vital role in the development of automation systems for an NPP. In this paper, we propose the design of a 3D digital twin system capable of simulating NPP in real-time. This system obtains the data from a full-scope NPP simulator to reproduce the operating conditions of the plant. In addition, a scenario of a team of robots performing inspection tasks like temperature and pressure measurements will highlight its usability. This system enables development of intelligent robot swarms to deploy for inspection and maintenance purposes. It will positively impact autonomous control and operations for many types of reactors by reducing uncertainty in autonomous control and providing the tools necessary for remote intervention.
1 Introduction
One of the main applications of robots is in hazardous environments, which offsets the presence of humans. A nuclear power plant (NPP) is an imperative example of it, with its high-temperature environment and radiation. The Nuclear Regulatory Commission (NRC) 10 Code of Federal Regulations (CFR) 20 stipulates that if the full body dosage of radiation exceeds 50 mSv per year, the worker should stop working immediately to prevent detrimental effects on health NRC (2020). This requires a huge demand for manpower to operate the NPP. To curb this huge demand for manpower, the International Atomic Energy Agency (IAEA) favors the use of robots in NPPs and is investing efforts to convince all stakeholders to develop novel robots and intelligence systems for the plants (IAEA, 2018). The essential basis of robots is to avoid human exposure to hazardous environments, general maintenance, and post-accidental activities. In addition, robots can be used as teleoperated machines to handle risky activities inside the containment region. Robots are an integral part of the online maintenance facility, which can eliminate the need for plant shutdowns. Also, robots offer ubiquitous benefits of working without loss of precision and with no interruptions (Iqbal et al., 2012).
The nuclear power industry in the United States contributes significantly to non-carbon electricity generation, but it faces challenges such as strict safety regulations and aging infrastructure. As the industry seeks to scale green energy, innovators are adopting robots to reduce worker’s presence in harsh environments, boost efficiency, and cut costs. For example, Ontario Power Generation, Talen Energy, and the United Kingdom Atomic Energy Authority (UKAEA), Duke Energy’s Oconee Nuclear Station use Boston Dynamics’ Spot for remote inspections, downtime reduction, and decommissioning support Boston Dynamics (2022b) Duke Energy (2024). These applications demonstrate the feasibility of utilizing quadrupeds to improve nuclear power sector safety, efficiency, and cost-effectiveness Boston Dynamics (2022a). Robots can provide dynamic sensing with non-destructive sensors mounted, such as radiation. Additionally, if the sensor is not integrated into the I&C system and manual gauge reading is required, a robot can be useful, such as by reading pressure gauges. The industry’s future operations and decommissioning efforts will benefit from robots’ agility, autonomy, and flexibility in component inspection and maintenance. As researchers around the world are investing time and efforts to develop novel robotic systems for NPPs, they are always faced with the challenge of testing these systems given the strict regulatory policies. Therefore, there is an urgent need for an ecosystem that provides an easy and quick way to test such systems to accelerate overall development. Digital twins (DTs) are a feasible solution to this issue. This concept has evolved from the work of Michael Grieves and John Vickers on product lifecycle management (Grieves, 2023). The DT model consists of a physical product and its digital representation. Data flows from the physical system to the DT, whereas information flows from the digital system to the physical. They have helped industries increase operational efficiencies, enhance safety and reliability, reduce errors, share information faster, and make better predictions.
A DT can have several different forms, depending on the application. There are physics-driven DTs, which are based on the fundamental laws governing a system, and data-driven DTs, which use the data from the physical system as a model. In the context of nuclear power plants, there have been numerous works in the literature (Singh et al., 2022). mentions the use of DT in 13 different industries, the nuclear power plant industry being one of them. It talks about how DT can be helpful in controlling the NPPs. Additionally, it mentions a 4-year project in France run by the Électricité de France (EDF) to create DTs for nuclear reactors. In (Apte, 2021), a multidisciplinary team is also working on developing DTs for nuclear reactors (Jharko et al., 2021). has designed a digital twin as a solution for the decommissioning issue of NPPs. It also emphasizes the need to create DTs for different elements of plants with strong mathematical foundations (Vitalli and Moreira, 2023). developed a DT with a virtual modeling scheme that is realistic and has an interface for communication with a real-world environment (Wang et al., 2022). has proposed a DT system that can help in the installation of out-of-core detectors. Haptic digital twin technology for remote manipulation is discussed in (Tugal et al., 2023). It discusses the usability of such a system for post-operational clean-out and operations in contaminated environments after a disaster. Therefore, there is huge scope for DTs in NPPs. However, there is no state-of-the-art DT that bridges the gap between nuclear engineering and robotics. This research develops a novel platform that enables this link so that robots can be deployed seamlessly inside the NPPs, reducing human exposure to harsh environments, improving the overall efficiency and economics of nuclear power operations, and contributing to net zero goal.
This paper proposes a novel design of a DT aimed at making the robot deployment process efficient. Unlike traditional twins, which consist of a physical system coupled with a digital counterpart, this DT has two digital systems coupled together. One of the digital systems is physics-driven; it is a full-scope high-fidelity Generic Pressurized Water Reactor (GPWR) simulator developed by Western Services Corporation (WSC, 1995) that simulates the operation of a NPP based on fundamental laws. Another system is data-driven, which obtains the sensor data and forms a 3D environment where robotic systems are deployed. This is developed using NVIDIA Omniverse (NVIDIA, 2023g) integrated with an open-source middleware robotics suite called Robot Operating System (ROS). It contains software libraries and tools that help you build the application Open Robotics, 2021. In this research, the ROS Noetic Ninjemys is used Open Robotics (2020). The main goal of this DT is to train and operate robots in a simulated environment so that the deployment of robots in such complex environments is smooth and efficient. The (Yadav et al., 2021) presents the following three conditions for a system to qualify as a nuclear DT.
• The system must exist in digital form and can be managed, processed, and executed on a digital device.
• The system must be capable of updating dynamically and in real-time to represent the physical phenomenon and should maintain state concurrency.
• The system should be related to an NPP life-cycle activity.
The DT proposed in this paper satisfies all three conditions if the physics-driven system is considered a physical entity. This is valid for the domain of nuclear power plants since it is difficult to obtain sensor and actuator data in real-time from an actual nuclear power plant given the strict regulatory protocols. Therefore, the GPWR simulator can be considered analogous to a real generic NPP, consisting of all sub-systems and simulating operations under different scenarios. The rest of the paper is organized as follows: Section 2 discusses the methodology and system architecture; Section 3 uses case studies to demonstrate the impact of the system; Section 4 discusses the potential uses and restrictions of the DT; Section 5 presents the conclusion.
2 Materials and methods
2.1 Data projection from nuclear power plant to 3D simulation environment
To build an NPP digital twin in 3D simulation, it is needed to project the NPP sensor data into the 3D simulation environment. However, it is usually restricted to obtaining real data from the physical NPP because of the strict security regulations. Therefore, a high-fidelity full-scope GPWR simulator is utilized to obtain the NPP data (WSC, 1995). A script-based method of extracting GPWR data is required to quickly deliver its sensor data to the 3D environment. Although GPWR primarily uses a graphical user interface (GUI), it also offers a data communication protocol with dynamic data exchange (DDE) (Microsoft Corporation, 2020). The GPWR data is extracted in real-time by utilizing the DDE protocol with Python three in the Win32 environment in this research.
When requesting a particular sensor variable through the DDE protocol, the value of the corresponding sensor can be obtained, with the variable serving as the key identifier. Only one value for one key can be extracted for each request. Therefore, in order to extract multiple sensor data points, it is necessary to define all sensor variables and request the values of each sensor. In the digital twin environment presented in this paper, target sensors are predetermined and stored as a configuration file. Only the data from those sensors is extracted through DDE, which enhances the memory management efficiency of the overall system.
The sensor data extracted through DDE is delivered to the machine, which contains the 3D environment, through the transmission control protocol (TCP) (Postel, 1981). The 3D environment works as a TCP server, and the client collects and transfers sensor data to the server. TCP needs the three-way handshake just once at the beginning of the connection, so it is a proper method for building a data stream pipeline. In order to transfer data in key-value form through the byte stream, the characters to split the key-value set are required. We used the “:” between key and value as a separator, and the “|” between the current key-value set and the next key-value set as a separator. The following is an example of representing N key-value sets as a byte stream.
The robot simulation is one of the main applications of this digital twin environment. Therefore, the sensor data delivered to the 3D environment through the TCP socket is published in the ROS (Open Robotics, 2020) topic. We defined the custom ROS message format for delivering GPWR sensor data. Using the predefined separator, the key and value are distinguished and parsed in the form of a custom ROS message. Table 1 represents the custom ROS message, which includes the timestamp when data is transferred, the number of total key-value sets, key variables, and sensor values for each key.
2.2 Sensor model
Once data from the GPWR simulator is received in the digital twin environment, it is modeled based on a control logic to represent various operating modes of the sensor. The sensors are modeled with four operating conditions based on the NRC guidelines on performance indications, which are as follows: NRC (2023)
1) Green: Healthy sensor with performance within expected performance level.
2) White: Healthy sensor but performance outside an expected range of nominal utility performance.
3) Yellow: Healthy Sensor but reduction in safety margins.
4) Red: Unhealthy sensor.
A data processing module is designed that takes the input sensor data from the GPWR and uses sensor threshold data to model the sensors inside the 3D environment. Figure 1 shows the sensor modeled in different operating modes.
2.3 System architecture
The core software used to model it is NVIDIA Isaac Sim (NVIDIA, 2023f). The central entity is called the NVIDIA Omniverse, (NVIDIA, 2023g), which encompasses Isaac Sim with various other applications and services using which one can build complex large-scale digital twin systems. To develop a 3D model of the environment and the robots, the universal Scene Description (USD) (USD, 2021) format is used, which was developed by Pixar. It is extensible, powerful, and a diverse tool due to its features like complex property inheritance, instancing, layering, and lazy loading. The simulation engine used is called NVIDA Physx (NVIDIA, 2023h), which supports a plethora of devices ranging from smartphones to high-end GPU’s. Using the power capabilities of Isaac Sim, it was possible to create such a complex simulation environment.
In Section 2.1, we have observed the process by which data from GPWR is transmitted to a computer for the purpose of creating a digital twin. In order to use the data inside the simulator, there is a need to connect the Omniverse and ROS applications. As seen in Figure 2, Isaac ROS Bridge is responsible for making this connection. It is an extension of Omniverse that provides a common set of components to exchange published or received data (NVIDIA, 2023j). Internally, this app runs a custom build of ROS Noetic (Open Robotics, 2020) and connects it with Omniverse Framework and Python3.
2.4 Improved collaboration
The developed DT components were packaged as an Omniverse extension. Omniverse extensions are the core building blocks of Omniverse Kit-based Apps (NVIDIA, 2023e). The developed extension provides two benefits. First, it lowers the huddles for the new collaborators to get started with. To promote collaboration between users and developers, it is important to make the developed DT accessible to those who are new to the related tools. The developed Omniverse extensions provide user-friendly graphical interfaces to configure and run the simulations in the way users intended, instead of touching the source codes or using command-line interfaces, which require users to go through documentation and put their time into learning the new tool.
Secondly, it allows the developers to deploy the application easily. The Omniverse extension is a ready-to-deploy package that does not require additional configuration in different environments. The only thing users need to do is download the package and open it at Isaac Sim to load all the required setups that other developers have built. Developers can avoid spending much unnecessary communication or effort to align their environment to run the same package so that they can focus more on contributing to each other to improve the package.
Figure 3 shows the Omniverse extension developed by the authors. The “Information” section displays how the users should operate the DT and the results of the operations. “Connection with GPWR” allows users to install and run the ROS package for communication with the GPWR simulator. The “Load Environment” section allows users to load different world configurations with different numbers of robot agents and prepare geographical graphs, which are required for LTL multi-agent task assignment simulation, from the given world map loaded. Finally, the “LTL Task” section simulates the LTL multi-agent task assignment simulation, which will be discussed in the later part of this article.
The physics-driven digital twin can simulate different malfunctions or failure modes of a nuclear power plant. The data-driven digital twin can simulate this in a 3D environment because it is linked to a physics-driven system through the DDE protocol. The data-driven system can simulate different robots and test their operation under various conditions. Consequently, this results in the expedited and simplified deployment of robots. It also offers robotics researchers a practical platform to develop and test their algorithms. The system’s extension features facilitate the smooth and easy installation of this digital twin.
3 Results
3.1 Case-I: Robot planning and scheduling
The developed digital twin was tested with a multi-agent task assignment simulation using a preference based linear temporal logic (LTL) algorithm developed in a previous work (Hesu et al., 2023). This algorithm is based on LTL planning for multiple robots (Schillinger et al., 2018a; b) and extended to consider the preference of given tasks in addition to the costs of the tasks so that robots can prioritize measurements, which can improve system diagnosis the most efficiently. This algorithm gets the list of tasks to be accomplished and the preferences of the tasks, along with the information of the agents, as inputs. Then it generates how the tasks are distributed and in which order they should be carried out by each agent, considering not only the cost of the tasks but also their preferences. This logic has been developed to find the best strategy to deploy multiple robots to collect multiple data points from different locations of the target facility to increase the diagnosis accuracy within the shortest time.
The preference-based LTL algorithm mentioned above requires two important inputs: first, the transition system definition, which is a connectivity graph with nodes representing the various locations defined inside the environment; and second, the map of the environment. The development of these two parameters is a laborious process. However, using this digital twin, it was possible to streamline this process and create an automation pipeline as shown in Figure 4, which makes the deployment of these algorithms in a new environment seamless. This automation pipeline consists of two main components: the Dynamic Control Interface (NVIDIA, 2023c) and the Occupancy Map Generation (NVIDIA, 2023i). The dynamic control interface helps to obtain the position of sensors inside the environment, using which an algorithm is implemented to create a graph. Occupancy Map Generation is used to create an entire map of the environment without using techniques like simultaneous localization and mapping (SLAM). Combining these two components accelerates the deployment of the LTL-based algorithm, making it efficient. Figure 5 shows a demo of LTL planning using three simulated agents. RVIZ is a tool widely used in the robotics industry for prototyping and debugging robotic systems. The RVIZ plot indicates that the digital twin can be easily connected to a ROS-based platform. This will help robotic researchers to test their algorithms seamlessly.
3.2 Case-II: Seamless robotic integration
One of the main advantages of this digital twin system is that it offers a variety of robots, ranging from wheeled to quadruped robots. This will help users easily simulate various test scenarios. It also enables you to create custom robots and then import them into the environment.
This is essential to the LTL planning algorithm mentioned above. It helps to simulate both homogeneous teams (every robot has the same capabilities) and heterogeneous teams (every robot has varied capabilities). Additionally, this will assist us in comprehending the various classifications of robotics necessary within the facility, predicated on their respective capabilities. Figure 6 shows two different team formations: the first team is homogeneous and consists of the NVIDIA Carterv1 (NVIDIA, 2023a) robot, and the second team is heterogeneous, consisting of the Carterv2 (NVIDIA, 2023b), the Smart Transport Robot (Fraunhofer Institute for Material Flow and Logistics IML, 2020), and Unitree A1 robots (NVIDIA, 2023k). These robots are directly available in the Isaac Sim environment.
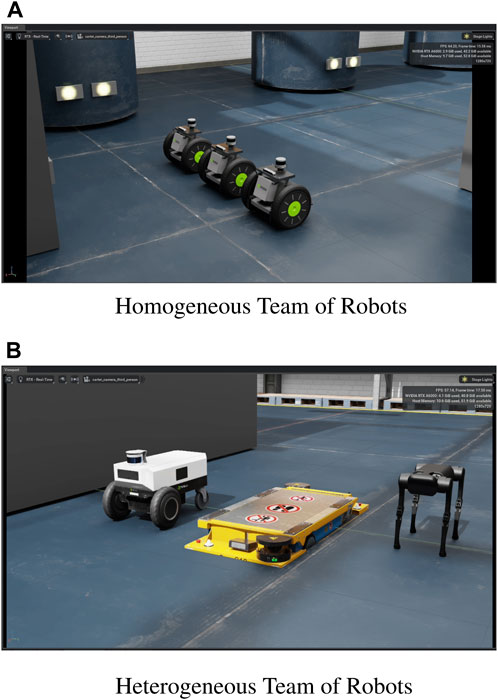
Figure 6. Different types of robot teams. (A) illustrates a homogeneous team of robots, while (B) illustrates a heterogeneous team of robots.
In addition, it is also possible to import custom-made robots. We can leverage the URDF importer, which helps convert a URDF (universal Robot Description Format) into USD format seamlessly. Figure 7 shows how a URDF of CHAMP robot (MIT, 2023) could be imported into the environment. However, to fully realize the functionality of this robot, it has to be connected with the navigation stacks in ROS by developing logic, which is out of scope for this research.
4 Discussion
This paper presents a proof-of-concept for a novel digital twin system developed using two different components: a physics-driven system that simulates the operations of NPP and a data-driven system used to simulate robots in the plant. This system can be extended to various user-specific applications like radiation monitoring, handling hazardous materials, and developing planning and scheduling algorithms like the LTL algorithm mentioned above. To make the above application work, though, a two-way pipeline needs to be built between the GPWR and the digital twin. This will help send feedback from the robot to the physics-driven system, closing the loop. In addition, one of the major roadblocks to developing in a realistic 3D environment is the time required to develop 3D models for every subsystem and component in the facility. With the advent of artificial intelligence (AI), it has been possible to leverage generative AI models to develop 3D models. The AI Room Generator Extension (NVIDIA, 2023d) is an example that used ChatGPT (OpenAI, 2023) with DeepSearch to create components of a warehouse. This example can be extrapolated to create models of nuclear power plants. This extension uses Deepsearch, which uses the Enterprise Edition of the Omniverse system and a nucleus server. We attempted to use this extension without this capability to generate a rough layout of nuclear power plants. The various subsystems were rendered as gray solid blocks, as shown in Figure 8, with the correct sub-systems named according to the prompt. This can be extended to develop a realistic model by leveraging the capabilities of Deepsearch.
5 Conclusion
The main research goal of this paper is to create a one-of-a-kind digital twin system that combines a physics-driven system and a data-driven system. This would make testing and deploying robots faster and easier. The robot planning and scheduling test cases illustrated that using this model of digital twin helped to save development time and only required the 3D model of the facility. In addition, this system also had the huge support to simulate a wide variety of robots, ranging from wheeled, quadrupled, and custom robots. Finally, using the extension architecture has made the system remarkable facile and user-intuitive, facilitating seamless acquisition and usage.
This work opens up a new opportunity for researchers to develop new robotic solutions for NPP’s. It also enables organizations to prototype and visualize the process before actual deployment and serves as a training platform for operators to learn using robots. It will also help NPPs to think of new areas where robots can be deployed seamlessly, helping to reduce human presence in harsh environments and improving the efficiency and economics of operations.
Data availability statement
The raw data supporting the conclusion of this article will be made available by the authors, without undue reservation.
Author contributions
HV: Conceptualization, Methodology, Software, Writing–original draft. SK: Software, Writing–original draft. HS: Software, Writing–original draft. FZ: Funding acquisition, Resources, Supervision, Writing–review and editing, Conceptualization, Project administration, Methodology.
Funding
The author(s) declare financial support was received for the research, authorship, and/or publication of this article. The authors would like to thank the U.S. Department of Energy, Office of Nuclear Energy, Distinguished Early Career Program for funding this work, Award number DE-NE0009306.
Conflict of interest
The authors declare that the research was conducted in the absence of any commercial or financial relationships that could be construed as a potential conflict of interest.
Publisher’s note
All claims expressed in this article are solely those of the authors and do not necessarily represent those of their affiliated organizations, or those of the publisher, the editors and the reviewers. Any product that may be evaluated in this article, or claim that may be made by its manufacturer, is not guaranteed or endorsed by the publisher.
References
Apte, P. (2021). Digital twins of nuclear power plants. New York City: American Society of Mechanical Engineers.
Fraunhofer Institute for Material Flow and Logistics IML (2020). Str - future-proof autonomous Transport systems. Available at: https://www.iml.fraunhofer.de/en/fields_of_activity/material-flow-systems/machines_and_facilities/research_projects/str.html.
Grieves, M. W. (2023). “Digital twins: past, present, and future,” in The digital twin (Cham: Springer), 97–121.
Hesu, A., Kim, S., and Zhang, F. (2023). Preference-based multi-robot planning for nuclear power plant online monitoring and diagnostics. Nucl. Sci. Eng., 1–18. doi:10.1080/00295639.2023.2239635
Iqbal, J., Tahir, A. M., ul Islam, R., and un Nabi, R. (2012). “Robotics for nuclear power plants—challenges and future perspectives,” in 2012 2nd international conference on applied robotics for the power industry (CARPI) (IEEE), Zurich, Switzerland, 11-13 September 2012, 151–156.
Jharko, E., Meshcheryakov, R., and Promyslov, V. (2021). “Aspects of nuclear power plant digital decommissioning,” in 2021 International Siberian Conference on Control and Communications (SIBCON) (IEEE), Russia, Kazan, May 13-15, 2021, 1–6.
NRC (2023). NRC Guidelines. Available at: https://www.nrc.gov/reactors/operating/oversight/rop-description.html
NVIDIA (2023c). Dynamic control interface. Available at: https://docs.omniverse.nvidia.com/py/isaacsim/source/extensions/omni.isaac.dynamic_control/docs/index.html.
NVIDIA (2023e). Nvidia extensions overview. Available at: https://docs.omniverse.nvidia.com/extensions/latest/index.html.
NVIDIA (2023f). Nvidia isaac sim. Available at: https://docs.omniverse.nvidia.com/isaacsim/latest/overview.html.
NVIDIA (2023g). Nvidia omniverse. Available at: https://www.nvidia.com/en-us/omniverse/.
NVIDIA (2023h). Nvidia physx. Available at: https://nvidia-omniverse.github.io/PhysX/physx/5.3.0/index.html.
NVIDIA (2023i). Occupancy map generation. Available at: https://docs.omniverse.nvidia.com/isaacsim/latest/advanced_tutorials/tutorial_advanced_occupancy_map.html.
NVIDIA (2023j). Ros bridge. Available at: https://docs.omniverse.nvidia.com/isaacsim/latest/ext_omni_isaac_ros_bridge.html.
OpenAI (2023). Chatgpt. Available at: https://www.openai.com/.
Schillinger, P., Bürger, M., and Dimarogonas, D. V. (2018a). “Decomposition of finite ltl specifications for efficient multi-agent planning,” in Distributed Autonomous Robotic Systems: The 13th International Symposium (Springer), London, UK, November 7-9, 2016, 253–267.
Schillinger, P., Bürger, M., and Dimarogonas, D. V. (2018b). Simultaneous task allocation and planning for temporal logic goals in heterogeneous multi-robot systems. Int. J. robotics Res. 37, 818–838. doi:10.1177/0278364918774135
Singh, M., Srivastava, R., Fuenmayor, E., Kuts, V., Qiao, Y., Murray, N., et al. (2022). Applications of digital twin across industries: a review. Appl. Sci. 12, 5727. doi:10.3390/app12115727
Tugal, H., Abe, F., Caliskanelli, I., Cryer, A., Hope, C., Kelly, R., et al. (2023). “The impact of a haptic digital twin in the nuclear industry and potential applications,” in 2023 IEEE International Conference on Advanced Robotics and Its Social Impacts (ARSO) (IEEE), Berlin, Germany, June 5-7, 2023, 134–139.
USD (2021). Universal scene description. Available at: https://openusd.org/.
Vitalli, R., and Moreira, J. (2023). Mathematical modeling of digital twins and industry 4.0 technologies for measuring pipe wall thickness at angra 1 nuclear power plant. J Artif Intell Mach Learn Data Sci 1, 72–77.
Wang, W., Liu, M., and Li, J. (2022). Research and realization of virtual-real control of robot system for off-heap detector assisted installation based on digital twin. IEEE J. Radio Freq. Identif. 6, 810–814. doi:10.1109/jrfid.2022.3209715
WSC (1995). Wsc inc., nuclear power plant simulation. Available at: https://www.ws-corp.com/default.asp?PageID=2&PageNavigation=Nuclear-Power-Plant-Simulation.
Keywords: digital twin, nuclear power plants, robotics, simulation, power plant operation, component inspection
Citation: Vairagade H, Kim S, Son H and Zhang F (2024) A nuclear power plant digital twin for developing robot navigation and interaction. Front. Energy Res. 12:1356624. doi: 10.3389/fenrg.2024.1356624
Received: 15 December 2023; Accepted: 20 March 2024;
Published: 10 April 2024.
Edited by:
Turgay Korkut, Sinop University, TürkiyeReviewed by:
V. P. Singh, Karnatak University, IndiaXingguang Duan, Beijing Institute of Technology, China
Copyright © 2024 Vairagade, Kim, Son and Zhang. This is an open-access article distributed under the terms of the Creative Commons Attribution License (CC BY). The use, distribution or reproduction in other forums is permitted, provided the original author(s) and the copyright owner(s) are credited and that the original publication in this journal is cited, in accordance with accepted academic practice. No use, distribution or reproduction is permitted which does not comply with these terms.
*Correspondence: Fan Zhang, ZmFuQGdhdGVjaC5lZHU=