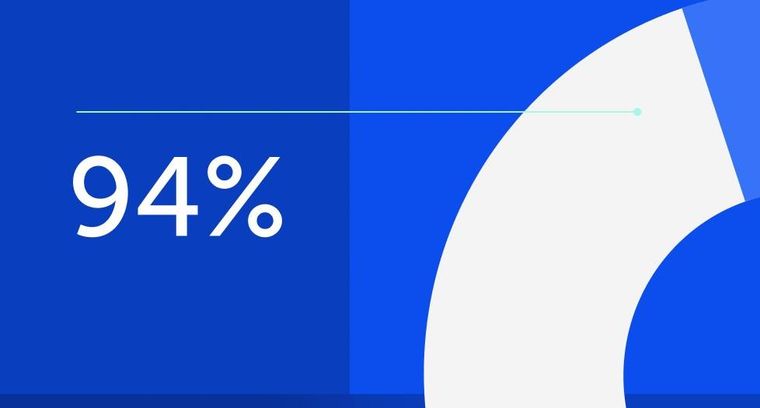
94% of researchers rate our articles as excellent or good
Learn more about the work of our research integrity team to safeguard the quality of each article we publish.
Find out more
REVIEW article
Front. Energy Res., 29 December 2023
Sec. Advanced Clean Fuel Technologies
Volume 11 - 2023 | https://doi.org/10.3389/fenrg.2023.1338715
This article is part of the Research TopicAdvances in Geomechanics Research and Application for Deep Unconventional ReservoirsView all 35 articles
This article presents an effective method for improving the structure and performance of coal rock masses, thereby facilitating coalbed methane extraction—the grouting solidification technique. A systematic review is conducted on grouting solidification materials, process methods, evaluation techniques, and other related aspects. In conclusion, it is emphasized that the grouting solidification technique requires further refinement in its system, and its continued significance in the dynamically evolving energy and coal industry is underscored. This is crucial for ensuring the efficient development and sustainable utilization of coal and coalbed methane resources.
Currently, coal resources are an indispensable and crucial component of China’s energy structure (Teng et al., 2016). With the continuous exploitation of coal mining resources and the advancement of coalbed methane industrialization in China, the exploration and development of coal resources and coalbed methane are gradually advancing into deeper, structurally complex fractured soft coal seams. However, the unique mechanical properties of fractured soft coal seams, such as their friability, high Poisson’s ratio, low Young’s modulus, and strong plasticity, pose significant challenges to mining and extraction operations (Zhang et al., 2022). Grouting solidification technology is currently an effective approach to improving the structure and performance of coal-rock masses. This technology involves injecting grout uniformly into cracks or voids under the influence of hydraulic or pneumatic pressure. The grout permeates, fills, and fractures, expelling air and moisture from the fractures in the coal-rock mass. Once the grout solidifies, the originally loose rock mass or fractures consolidate into a cohesive, strong, waterproof, and chemically stable new rock mass (Xie, 2021).
Fractured soft coal seams are a type of coal seam characterized by unique geological features, with their cohesion coefficient (f-value) being less than 1. These coal seams typically undergo compression and kneading during geological tectonic movements, resulting in loose, soft, and friable coal bodies with a lower content of rock minerals. Consequently, they exhibit reduced mechanical strength, compressive resistance, and a propensity for expansion upon contact with water. The mechanical properties manifest as a higher Poisson’s ratio and lower Young’s modulus, making them prone to deformation, collapse, susceptibility to external stress, and the potential occurrence of geological phenomena such as folding and sliding (Zhou et al., 2016). In coal mining, dealing with fractured soft coal seams requires specialized engineering techniques to ensure the stability and safety of the mine. Excavating and supporting these coal seams necessitate a comprehensive consideration of their unique properties. Additionally, fractured soft coal seams often contain coalbed methane, making them prone to sudden occurrences of coal and gas outbursts. This phenomenon, known as outburst, is particularly evident during construction, drilling, and other engineering operations in fractured soft coal seams. It can lead to phenomena such as wall contraction, wall collapse, and even the ejection of holes under gas pressure and dynamic excitations, resulting in engineering accidents such as stuck drilling and buried drilling (Guo et al., 2020). The unique properties of fractured soft coal seams require the adoption of innovative engineering methods and technologies to ensure the safety and feasibility of mines and underground projects. Grouting solidification technology plays a pivotal role in this field, providing a reliable solution for the safe development of coal seams and the extraction of coalbed methane. Its application can be extended and adapted based on the specific conditions of different coal mines (Li et al., 2021).
This article aims to delve into the principles, materials, construction methods, and practical applications of the principles of fragmented soft and deep coal seam grouting solidification technology. Through a comprehensive discussion of this critical technology, the intention is to provide a deeper understanding and practical guidance for addressing challenges in the development of coal seams. In the ever-changing energy and coal industry landscape, grouting solidification technology will continue to play a crucial role in ensuring the efficient development and sustainable utilization of coal and coalbed methane resources.
Grouting solidification agents are a crucial component in grouting technology, and the rational selection of these agents plays a key role in the grouting process and the subsequent reinforcement and modification effects. Grouting solidification agents are formulated liquids composed of main agents, solvents, and additives. Regardless of the specific formulation, each grouting agent has unique applications based on factors such as particle size, mechanical properties, chemical characteristics, construction processes, and cost-effectiveness, making it impractical to satisfy all grouting scenarios uniformly. The selection of grouting materials should be based on the characteristics of the crushed soft coal seam, the geological conditions of the actual construction target of the crushed soft coal seam, the expected goals after grouting, injection method requirements, density requirements, setting time and viscosity, cost, hydrogeological conditions, and environment. The comprehensive performance of the slurry material should be considered based on influencing factors, and different slurries should be selected to ensure the coal seam solidification effect.
Grouting solidification materials suitable for fractured soft coal seams should meet the following requirements:
1) The grout should have good flowability, low viscosity, and good injectability, capable of penetrating into fine cracks;
2) The grout’s gelation time should be controllable through temperature, additives, and other methods;
3) The density of the grout should be similar to that of the fractured soft coal seam being reinforced and modified;
4) The grout should be of low toxicity or non-toxic, odorless, and environmentally non-polluting;
5) The grout should be easy to formulate, and the grouting process should be straightforward;
6) The grout should exhibit good stability, maintaining its basic properties for an extended period under normal temperature and pressure;
7) The grout should not corrode grouting equipment or the coal seam;
8) The consolidation formed by the injected grout into the coal seam should have sufficient strength and stability, allowing for extraction operations;
9) The grout should have a broad source, and its cost should be low.
According to the characteristics of grouting solidification agents, as shown in Figure 1, these agents are mainly divided into two major categories: inorganic grouting solidification agents and organic grouting solidification agents. Inorganic grouting solidification agents include clay-based, cement-based, water glass (sodium silicate) based, cement-clay hybrid, and cement-water glass hybrid agents. These agents are characterized by low cost and easy availability. However, they have a slow curing time, and the larger particle size of their grout reduces permeability, making it challenging for the grout to penetrate into minute pores. Additionally, the curing process is irreversible, causing significant harm to coal seams. Organic grouting solidification agents, including acrylamide-based, polyurethane-based, methyl methacrylate-based, epoxy resin-based, and lignin-based agents, exhibit better permeability, and their gelation time is adjustable. However, the materials used in these agents are relatively more expensive (Gen and g, 2019).
FIGURE 1. Classification of grouting solidification agents (Gen and g, 2019).
The clay-based solidification slurry originally referred to a grouting material formed by mixing clay with water in certain proportions, representing the most primitive form of grouting solidification material. With the development of grouting solidification, engineers have modified clay slurry based on different grouting requirements. This involves incorporating additives such as water glass, cement, and solidification agents in varying proportions, giving rise to a category known as clay-based solidification slurry. Clay, with a composition that includes complex components such as silicate minerals, forms dispersed clay particles with negative charges when mixed with water. The edges of cracks in coal seams often carry a certain positive charge. When injected into underground fissures, these clay particles undergo electrostatic action, hydration reactions, and ion exchange, binding and solidifying the cracks. However, the initial viscosity of the clay-based slurry is relatively high, the injection range is limited, and the strength of the consolidation formed after solidification is low, making it less favorable for extraction operations (Zhang et al., 1995).
Cement-based solidification slurry refers to a grouting solidification material formed by mixing powdered rigid inorganic solidifying materials (main components) with other modifying materials (such as polyurethane, resins, styrene-butadiene latex, fly ash, water glass, carbon nanotubes, etc.) in a certain proportion with water. The silicate, aluminate, and ferric-aluminate components in cement undergo a hydration reaction with water, forming precipitates. These precipitates crystallize and fix the free water in the system, filling the fissures in the coal seam, ultimately forming a high-strength consolidated structure. Cement-based solidification slurry has advantages such as high strength of the consolidated structure, good deformation resistance, strong water plugging ability, environmental friendliness, cost-effectiveness, ease of construction, and wide applicability. Consequently, it is currently the most widely used and abundant grouting material. It can be used for water plugging and well consolidation in coal seams. However, the initial viscosity of cement-based solidification slurry is relatively high, making it challenging to inject into fine cracks in coal seams (Ruan, 2005).
Sodium silicate-based slurry consists primarily of a sodium silicate aqueous solution (water glass) as the main agent, with the addition of coagulants (such as calcium chloride, sodium aluminate, silicon tetrafluoride, and formaldehyde) to form a gel. Sodium silicate slurry is an inorganic grouting material that has been used relatively early in grouting technology. It is characterized by its low cost, good penetrability, ease of construction, and environmental friendliness. However, its mechanical strength is relatively low, and it can be modified by mixing with cement (Chao et al., 2016).
Acrylamide-based solidification slurry is generally composed of crosslinking agents such as N, N′-methylenebisacrylamide, initiators, reducers, retarding agents, and other components. Acrylamide-based solidification agents initiate the chain reaction by the initiator to form free radical active centers. Once the monomer free radicals are formed, they undergo polymerization with acrylamide monomers, leading to chain growth. Simultaneously, the amide groups of acrylamide form hydrogen bonds with functional groups on the coal surface, such as hydroxyl groups, bonding the coal particles. This process aims to improve the mechanical properties of coal and rock. The initial viscosity of acrylamide-based solidification slurry is adjustable, facilitating pumping into formations with initially low permeability (KAROL, 1990). Acrylamide-based slurry offers adjustable gelation time, making it less susceptible to impurities’ interference. The permeability of the slurry remains consistent during the grouting process. After solidification, the slurry becomes impermeable, demonstrating good durability and stability. The construction operation is straightforward, and the cost is low (Feng, 2007), Therefore, it is applied in the grouting reinforcement of tunnel support and coal mine excavation tunnels.
Polyurethane-based solidification slurry is primarily composed of polyisocyanate prepolymers, polyether polyols, and other catalytic additives in specific proportions. Surfactants and other modifiers can be added to achieve lower viscosity, ensuring the slurry’s uniform dispersion in water. Consequently, it exhibits good injectability and diffusion. Its strong bonding with coal makes it easily diffusible, effectively consolidating a large area. After solidification, it attains high compressive strength, demonstrating stable physical and chemical properties. It can incorporate flame retardants to prevent spontaneous combustion in coal bodies, ensuring safe use in tunnel reinforcement, underground safety reinforcement, roof reinforcement, and other safety-related production activities. However, polyisocyanates have inherent toxicity and corrosiveness, requiring careful handling and storage (Hou et al., 2022).
Epoxy resin-based grouting materials are typically composed of epoxy chloropropane, bisphenol A or polyols, curing agents, modifiers, fillers, diluents, and other components. The viscosity of epoxy resin is generally high, but it can be adjusted over a wide range by adding diluents. After curing, epoxy resin forms a highly cross-linked structure with low toughness and poor ductility, making it suitable for subsequent fracturing construction. The most commonly used type is bisphenol A epoxy resin, synthesized from propylene oxide and epichlorohydrin, with epoxy groups at both ends of the molecule. Common curing agents include amines and anhydrides. This type of grouting material is widely used in crack reinforcement and consolidation grouting of foundations and concrete structures. However, it has some limitations. For certain engineering applications, the bonding strength of such grouting materials is susceptible to external factors. Additionally, the raw materials are not widely available, mechanical properties need improvement, it is relatively expensive, and it possesses toxicity, all of which limit its application (Yang and Gao, 2000).
Melamine-formaldehyde resin-based solidification slurry is typically composed of urea, formaldehyde, a certain amount of curing agent (mainly acid and acidic salts), and other modifiers or a combination with other resins. It has a wide range of material sources, low cost, low viscosity, and forms a consolidated structure with high compressive strength after reaction. However, it tends to be brittle with low toughness, making it prone to cracking, which is advantageous for subsequent fracturing construction. On the downside, its resistance to permeation is relatively poor. The slurry contains a significant amount of formaldehyde, resulting in an irritating odor during construction. This can pose a certain carcinogenic risk to humans and lead to environmental and groundwater pollution. Moreover, the acidic nature of the curing agent can corrode grouting equipment and pipelines (Wang, 2011).
In the practical implementation of grouting solidification technology, the theory of grouting has undergone continuous development. However, the engineering design parameters of grouting solidification technology are often based on engineering experience, and theoretical development lags behind practice, making it challenging to provide guidance for the engineering design of grouting solidification technology. Grouting theory is a comprehensive application of interdisciplinary knowledge, involving fluid mechanics, polymer chemistry, rock mechanics, and other disciplines. Depending on the geological characteristics and objectives of the construction site, the selection of grouting parameters and materials may vary. Different grouting methods can lead to different grouting effects (Wang et al., 2017). There are three main injection theory models: Permeation Grouting Theory, Compaction Grouting Theory, and Fracture Grouting Theory as shown in Figure 2.
1) Permeation Grouting Theory
FIGURE 2. Different types of injection theory models (Wang, 2017). (A) Permeation Grouting (B) Compaction Grouting (C) Fracture Grouting.
Assumptions of Permeation Grouting Theory: ①The injection and diffusion of the slurry will not alter the fractures in the grouted medium or affect the skeletal structure; ②The slurry is assumed to be a continuous point or linear entity; ③The construction medium is considered isotropic (Zhang, 2022). During the construction process, the injected slurry permeates the construction medium, filling internal voids or fractures without disrupting the internal structure of the construction medium. After solidification, this process effectively enhances the mechanical properties of the construction medium. In the theory of permeation grouting, the diffusion forms of the slurry mainly include spherical diffusion and columnar diffusion (LI et al., 2016).
As shown in Figure 3, spherical diffusion is the radial spread of grouting material from the injection point in all directions, forming a spherical zone of influence around the injection point. It provides relatively uniform coverage in all directions, effectively filling voids and cracks around the injection point. Spherical diffusion is suitable for applications that require a consistent and isotropic (equal in all directions) distribution of injected material. Columnar diffusion involves the axial spread of grouting material from injection points arranged in a columnar distribution into a cylindrical zone of influence within the construction media. This diffusion pattern directs the spread more prominently in a specific direction, forming a cylindrical zone of influence. Columnar diffusion is advantageous when targeting specific planes or directions (e.g., along tunnels or pipelines). It is applicable in situations where material injection needs to be guided along a specific path, such as tunnel excavation or creating barriers along particular geological features (LI et al., 2016). The choice between spherical and columnar diffusion depends on the specific requirements of the project, including geological conditions, desired outcomes, and the need for uniformity or directed applications.
(2) Compaction Grouting Theory
FIGURE 3. Schematic diagram of slurry infiltration and diffusion forms (LI et al., 2016). (A) Spherical diffusion (B) Columnar diffusion.
Compaction grouting theory involves continuously injecting a large amount of grouting material with poor diffusivity into the construction medium by increasing the injection pressure within a certain range. As the grouting volume increases, the pressure exerted by the slurry on the grouting medium steadily rises, leading to compaction and consolidation without causing fracturing damage. This process aims to strengthen the construction medium and improve its resistance to permeation (Zhan et al., 2010).
(3) Fracture Grouting Theory
Fracture grouting theory involves increasing the injection pressure after compaction grouting until the slurry fractures and creates cracks within the construction medium. This process aims to increase the grouting volume, thereby using fracturing technology to improve the actual range of grouting solidification. (Li et al., 2014).
Grouting technology is a widely used geological engineering method in various fields such as underground engineering, construction, mining, and civil engineering. It involves injecting specific liquids or slurries into underground rocks or soils to improve their engineering properties, enhance geological stability, control water inflow, reinforce foundations or rock layers, and improve the mechanical properties of soils or rocks. Grouting technology allows for in-situ reinforcement or modification of the construction medium, enabling the construction medium within the grouting range to be connected with the grouting material to form a unified whole, achieving the purpose of reinforcement or modification (Hu et al., 2022). The history of grouting technology can be traced back to 1802 when French engineers first used the method of manual pounding to inject clay slurry into the walls of the port of Dieppe for reinforcement. Subsequently, grouting technology continued to evolve, introducing materials such as cement, water glass, polyurethane, and others, becoming crucial for reinforcement and waterproofing in fields like mining and construction. With the development of the chemical industry, the diversity of grouting materials increased, expanding the application scope of grouting technology and significantly improving its effectiveness (Xiao et al., 2021).
Currently, grouting technology is widely applied in various fields, including grouting in mine shafts, plugging water inrush points, restoring flooded mines, grouting in shafts to block water in aquifers or along water-bearing faults, curtain grouting for water cutoff, reducing mine water inflow, bottom grouting for solidification to prevent water inrush, and more (Chen, 2019). In these applications, grouting technology has achieved favorable results, providing reliable solutions for engineering safety and stability.
Grouting process is an essential part of grouting consolidation technology, and it is matched with grouting materials to achieve optimal grouting effects. When grouting, the construction technology needs to be reasonably selected based on comprehensive considerations such as the geological structural conditions of the construction medium, the depth and scope of grouting, the goals expected to be achieved after grouting, environmental factors, and the project budget. Currently, the grouting consolidation technology includes the following processes: single-stage grouting consolidation process, multi-stage grouting consolidation process, layered and staged grouting consolidation process, and “concentric ring” grouting consolidation process (YANG et al., 2022).
The single-stage grouting consolidation process involves drilling holes into the construction medium to the required depth. Based on the needed volume of grout, the entire range of reinforcement and modification is achieved in one go by grouting through a single hole (Zhou et al., 2010).
The multiple-stage grouting consolidation process involves conducting additional grouting sessions immediately after the first grouting session if the expected results are not achieved. The second grouting session supplements the initial one, filling unreinforced cracks and expanding the grouting area. If the desired effect is still not achieved, a third grouting session can be performed (Xu, 2017).
The staged grouting consolidation process involves injecting grout in stages based on the permeation mechanism of the grouting consolidation process, particularly the theory of spherical diffusion. It includes grouting and consolidating the shallow areas of the boreholes first. After effectively reinforcing the soft conditions in the shallow area of the boreholes, additional boreholes are drilled, and the process is repeated in multiple stages to reinforce large areas of the construction medium (Zhang et al., 2018).
The “concentric ring” grouting consolidation process is designed for situations where some fragmented coal layers are challenging to support during drilling. Initially, a small-scale pre-consolidation is performed on the boreholes, and then larger-diameter boreholes are used for expanding and reinforcing specific sections. Finally, the reinforced boreholes are employed to inject grout and consolidate the construction medium (Zhang et al., 2019).
After the completion of grouting solidification, it is essential to conduct a comprehensive evaluation of the grouting effect. Currently, the primary evaluation methods include analytical methods, borehole inspection methods, and geophysical methods (Wang et al., 2019).
The analytical method involves systematically organizing construction information obtained during the grouting solidification process, including grouting pressure, grouting velocity, total grout volume, reinforcement volume, and water inflow before and after grouting. Through the analysis and comparison of these data with simulated numerical values, a rational evaluation of the grouting solidification effect is conducted (Pang, 2008).
The borehole inspection method involves drilling holes in the deep-seated zones of grouting solidification during and after the construction process. The evaluation is based on the difficulty of drilling, water and sand inflow in the detection hole, filling status of cracks in the borehole, and experimental measurements on samples extracted. This comprehensive assessment helps judge the effectiveness of grouting solidification (Shao, 2020).
The geophysical method involves measuring the resistivity and electromagnetic characteristics of the construction media before and after grouting. Through comparative analysis, this method evaluates the effectiveness of grouting solidification (Liu et al., 2022).
The grouting solidification of fragmented coal seams holds significant importance for increasing production and ensuring safety in the exploitation of coal and coalbed methane resources. Currently, drawing insights from grouting technologies across various industries, substantial research achievements have been made in the grouting solidification techniques for fragmented coal seams. The rational selection of grouting materials and processes can be achieved by considering the specific geological conditions of individual coal seams. However, challenges persist in the current approach.
1) The classification of fragmented coal seams primarily relies on the coal’s firmness coefficient. In the grouting solidification process, the target medium for injection is predominantly the fractures. Before undertaking grouting solidification for fragmented coal seams, it is imperative to thoroughly consider parameters such as coal-rock strength, joint parameters, coal body integrity, crack width and length, as these factors have a tangible impact on the actual effectiveness of grouting solidification. This consideration provides a theoretical basis for the selection of grouting solidification materials.
2) For grouting materials, a prolonged setting time and excellent stability are required. Currently, existing grouting materials that meet these requirements are characterized by high costs and the potential to induce groundwater contamination and trigger coal spontaneous combustion. Future grouting solutions should primarily focus on the development of novel grouting materials that are safe, environmentally friendly, and cost-effective, addressing the shortcomings associated with the current options.
3) For the grouting process, it is essential to tailor the grouting parameters to different crack widths. The selection of appropriate grouting techniques should be based on the actual conditions, gradually forming a comprehensive set of process standards.
4) The current evaluation of grouting effectiveness often relies on qualitative and subjective assessments, lacking standardized, quantitative, and easily operational criteria. In the future, the evaluation of grouting effectiveness should introduce personalized and quantitative standards, taking into account various factors such as the nature of the target medium, distinct mechanical and joint parameters within the same medium, and specific engineering requirements. This approach aims to provide a more accurate and systematic assessment of the grouting outcomes.
ZG: Writing–original draft. ZS: Methodology, Writing–review and editing. JW: Writing–review and editing, Investigation. Zi: Conceptualization, Writing–review and editing, Writing–original draft. ZY: Investigation, Writing–review and editing. LH: Investigation, Writing–original draft. LX: Investigation, Writing–review and editing. FH: Investigation, Writing–review and editing.
The author(s) declare financial support was received for the research, authorship, and/or publication of this article. This study received funding from: North China Oilfield Company by a North China Oilfield Company Collaborative Research Project “Efficient Transformation Technology Research and Application of Medium and High-Rank Coal Reservoirs” (2020-HB-XQ07); China National Petroleum Corporation by a China National Petroleum Corporation Forward-looking Foundational Project “Technological Research on Low-Damage and Efficient Development of Coalbed Methane: Supporting Engineering” (2021DJ2305); North China Oilfield Company by a North China Oilfield Company Research Project “Key Technology Research on Efficient Fracturing for Coalbed Methane Production” (2022-HB-M07). The funders were not involved in the study design, collection, analysis, interpretation of data, the writing of this article or the decision to submit it for publication.
Authors ZG, JW, ZY, LX, and FH were employed by PetroChina North China Oilfield Engineering Technology Research Institute.
The remaining authors declare that the research was conducted in the absence of any commercial or financial relationships that could be construed as a potential conflict of interest.
All claims expressed in this article are solely those of the authors and do not necessarily represent those of their affiliated organizations, or those of the publisher, the editors and the reviewers. Any product that may be evaluated in this article, or claim that may be made by its manufacturer, is not guaranteed or endorsed by the publisher.
Chao, F., Xia, R., and Rong, C. (2016). Etc. Preparation and properties of PU/silicate organic-inorganic hybrid materials by in situ method. China Plast. Ind. 44 (07), 7–10.
Chen, Y. (2019). Formation mechanism of the collapse column of 19109 working face in Jinggong No.1 Mine Evaluation of governance effects.
Feng, Z. (2007). Material development and research of osmosis and diffusion on chemical grouting for extraordinary cracked coal and rockmass [D]. Doctoral thesis. Coal Science Research Institute.
Geng, G. (2019). Application research of grouting material in coal mining. Shanxi Chem. Ind. 39 (02), 122–124. doi:10.16525/j.cnki.cn14-1109/tq.2019.02.43
Guo, W., Ma, Z., and Bai, E. (2020). Current status and prospect of coal mining technology under buildings, water bodies and railways, and above confined water in China. Coal Sci. Technol. 48 (09), 16–26. doi:10.13199/j.cnki.cst.2020.09.002
Hou, K., Wang, S., and Yao, S. (2022). etc. Research progress on modification of polyurethane grouting materials in mines. Coal Sci. Technol. 50 (10), 28–34. doi:10.13199/j.cnki.cst.2021-0501
Hu, S., Liu, Q., and Li, S. (2022). etc. Advance and review on grouting critical problems in fractured rock mass. Coal Sci. Technol. 50 (01), 112–126. doi:10.13199/j.cnki.cst.2021-0103
Li, J., Li, G., and Haijin, H. (2021). etc. Technology of across-goaf drainage of coalbed methane from a lower coal seam group and its primary application: taking Sihe mine field as an example. Coalf. Geol. Explor. 49 (04), 96–104. doi:10.3969/j.issn.1001-1986.2021.04.012
Li, S., Zhang, W., and Zhang, Q. (2014). etc. Research on advantage-fracture grouting mechanism and controlled grouting method in water-rich fault zone. Rock Soil Mech. 35 (03), 744–752. doi:10.16285/j.rsm.2014.03.030
Li, S., Liu, R., and Zhang, Q. (2016). etc. Protection against water or mud inrush in tunnels by grouting: a review. J. Rock Mech. Geotechnical Eng. 8 (5), 753–776. doi:10.1016/j.jrmge.2016.05.002
Liu, S., Chen, J., and Xu, Z. (2022). Study on the effect of karst grouting based on indoor geophysical model test. Railw. Eng. 62 (12), 158–161. doi:10.3969/j.issn.10031995.2022.12.31
Pang, T. (2008). Experimental study of whole process grouting used in tunnel passing through existing structures. Rock Soil Mech. 29 (12), 3451–3458. doi:10.16285/j.rsm.2008.12.008
Ruan, W. (2005). Research on diffusion of grouting and basic properties of grouts. J. Geotechnical Eng. (01), 69–73. doi:10.3321/j.issn:1000-4548.2005.01.011
Shao, H. (2020). Analysis and treatment of cracks in high roller compacted concrete arch dams. Water conserv. Tech. Superv. (05), 202–205. doi:10.3969/j.issn.1008-1305.2020.05.055
Teng, J., Qiao, Y., and Song, P. (2016). Analysis of exploration, potential reserves and high efficient utilization of coal in China. Chin. J. Geophys. 59 (12), 4633–4653. doi:10.6038/cjg20161224
Wang, D. (2011). Mechanism of hydrodynamically chemical grouting in porous media [D]. Doctoral thesis. China University of Mining and Technology.
Wang, L. (2017). Study of grouting technology's mechanism and application in subgrade reinforcement [D]. Master’s thesis. Shan Dong University. doi:10.3969/j.issn.1671-1815.2017.23.020
Wang, X., Qin, Q., and Su, P. (2017). Etc. Research status and development tendency of fractured surrounding rock grunting reinforcement technology. Sci. Technol. Eng. 17 (23), 122–131.
Wang, X., Qin, Q., and Xiong, Z. (2019). Etc. Comprehensive evaluation for grouting effect of fractured surrounding rock in deep roadway. Chin. J. Undergr. Space Eng. 15 (02), 576–582.
Xiao, Z., Yang, Z., and Long, J. (2021). etc. The development trend and application of grouting support materials. Industrial Minerals Process. 50 (05), 38–41+8. doi:10.16283/j.cnki.hgkwyjg.2021.05.010
Xie, C. (2021). Experimental study on coal model reinforced by new polyurethane/water glass double liquid slurry grouting [D]. Master’s thesis. Anhui University of Science and Technology. doi:10.26918/d.cnki.ghngc.2020.000289
Xu, J. (2017). Application of double liquid multiple splitting grouting reinforcement and rectification of soft soil foundation. Constr. Technol. 46 (S1), 145–149.
Yang, L., and Gao, B. (2000). Experiment study of concrete element remedy by chemical grouting. Archit. Technol. (06), 385–386. doi:10.3969/j.issn.1000-4726.2000.06.011
Yang, R. K., Zhang, S., and Tao, W. P. (2022). Etc. Application of sectional grouting by polymer material in sand reinforcement. J. Munic. Technol. 40 (05), 146–150. doi:10.19922/j.1009-7767.2022.05.146
Zhan, Y., Song, X., and Chen, M. (2010). Research progress on grouting theory in rock mass. Roadbed Proj. (02), 20–22. doi:10.3969/j.issn.1003-8825.2010.02.008
Zhang, C., Liang, J., and Yang, J. (2019). etc. Sealing mechanism of slurry materials considering temporal and spatial variation of viscosity. Chin. J. Geotechnical Eng. 41 (05), 974–980. doi:10.11779/CJGE201905022
Zhang, J., Li, S., and Zhang, X. (2018). etc. Model test on grouting diffusion in rock and soil layered medium. J. Zhejiang Univ. Eng. Sci. 52 (05), 914–924. doi:10.3785/j.issn.1008-973X.2018.05.011
Zhang, K., Zeng, X., and Zhang, L. (1995). Etc. Testing and study of water shut-off by solidifid clay mud. Explor. Eng. Geotech. Drill. Eng. (01), 18–20.5.
Zhang, Q., Li, Q., and Fan, X. (2022). etc. Current situation and development trend of theories and technologies for coal and CBM co-mining in China. Nat. Gas. Ind. 42 (06), 130–145. doi:10.3787/j.issn.1000-0976.2022.06.011
Zhang, Z. (2022). Study of mechanism and technology of high-pressure fracturing grouting in roadway in 1000m deep coalmine [D]. Doctoral thesis. China Coal Research Institute. doi:10.27222/d.cnki.gmkzy.2021.000012
Zhou, B., Jinwei, H., and Zhang, C. (2016). Analysis on borehole instability under coupled multiple stress and dynamic sealing technology in soft coal seam. Coalf. Geol. Explor. 44 (04), 161–166. doi:10.3969/j.issn.1001-1986.2016.04.031
Keywords: grouting solidification, deep coal reservoir modification, coalbed methane extraction, grouting materials, grouting process
Citation: Guangbo Z, Suian Z, Wei J, Xiao Z, Yang Z, Haoyu L, Xiaohua L and Huili F (2023) Grouting solidification technology for fractured soft coal seams and its application in coalbed methane (coal mine gas) extraction. Front. Energy Res. 11:1338715. doi: 10.3389/fenrg.2023.1338715
Received: 15 November 2023; Accepted: 12 December 2023;
Published: 29 December 2023.
Edited by:
Peng Tan, CNPC Engineering Technology R&D Company Limited, ChinaReviewed by:
Shuheng Tang, China University of Geosciences, ChinaCopyright © 2023 Guangbo, Suian, Wei, Xiao, Yang, Haoyu, Xiaohua and Huili. This is an open-access article distributed under the terms of the Creative Commons Attribution License (CC BY). The use, distribution or reproduction in other forums is permitted, provided the original author(s) and the copyright owner(s) are credited and that the original publication in this journal is cited, in accordance with accepted academic practice. No use, distribution or reproduction is permitted which does not comply with these terms.
*Correspondence: Zhang Xiao, emhhbmd4aWFvQGN1cC5lZHUuY24=
Disclaimer: All claims expressed in this article are solely those of the authors and do not necessarily represent those of their affiliated organizations, or those of the publisher, the editors and the reviewers. Any product that may be evaluated in this article or claim that may be made by its manufacturer is not guaranteed or endorsed by the publisher.
Research integrity at Frontiers
Learn more about the work of our research integrity team to safeguard the quality of each article we publish.