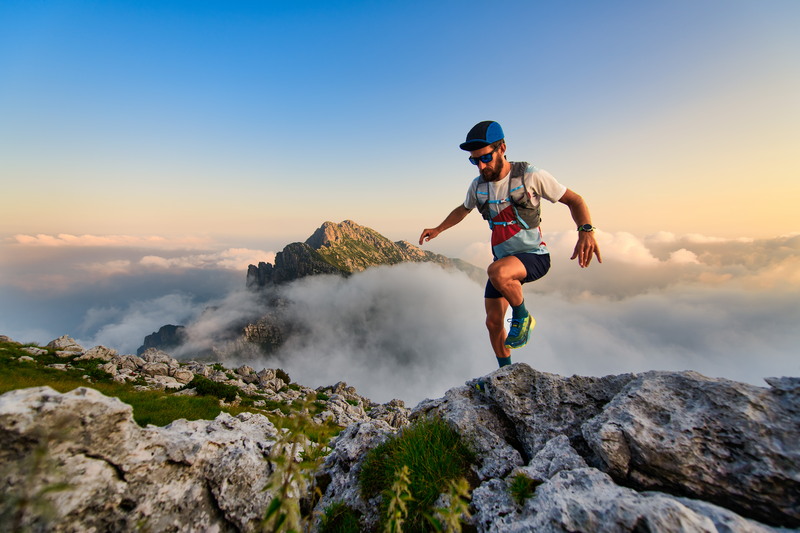
95% of researchers rate our articles as excellent or good
Learn more about the work of our research integrity team to safeguard the quality of each article we publish.
Find out more
ORIGINAL RESEARCH article
Front. Energy Res. , 18 January 2024
Sec. Process and Energy Systems Engineering
Volume 11 - 2023 | https://doi.org/10.3389/fenrg.2023.1324876
This article is part of the Research Topic Mechanisms and Applications of Coupled Technologies in Unconventional Resources for Enhancing Oil/Gas Recovery View all 5 articles
Introduction: The hot water chemical flooding technology effectively improves the fluidity ratio and enhances the horizontal and vertical oil displacement efficiency of the reservoir through the synergistic effect of thermal energy and chemicals, which can further enhance the recovery rate on the basis of throughput thermal recovery.
Methods: Based on the geological reservoir parameters of Bohai B oilfield, an oil recovery system evaluation experiment and scheme design study were carried out. Injection parameters such as hot water temperature, chemical agent concentration, and chemical agent dosage that affect the oil recovery effect of hot water chemical flooding were optimized and designed. The development characteristics and effects of two thermal recovery technologies, namely multi thermal fluid throughput and hot water chemical flooding, were compared and analyzed.
Results: The results show that with the increase of temperature, the effect of chemical agents on improving the water-oil mobility ratio and reducing the viscosity of crude oil is weakened, and the thermal energy plays a leading role in enhancing oil recovery, but when the temperature is higher than 115°C, the improvement of oil recovery is slowed down, and the comprehensive economic indicators decline rapidly. As the concentration of chemical agent increases, the enhanced oil recovery increases monotonously. When the concentration is 1500 mg/L, the comprehensive economic indicators reach the peak and then decline, indicating that the efficiency of chemical agent decreases. The total amount of chemical agent shall be controlled within 0.25 ∼ 0.30 PV. The case calculation shows that hot water chemical flooding can expand the effective radius from 80 m to 400 m, more effectively use the reserves between injection and production wells, increase the oil recovery by 4.8 percentage points, and increase the oil yield by 31.7 m3/t per ton of agent.
Discussion: It is suggested that Bohai B Oilfield can adopt hot water chemical flooding after the multiple thermal fluid huff and puff to continuously guarantee the oilfield production.
Bohai Bay is rich in heavy oil resources. For heavy oil with formation crude viscosity less than 350 mPa·s, cold production technologies such as water flooding, polymer flooding and moderate sand production are mainly used for development (Zhang et al., 2007; Liang et al., 2012; Xie et al., 2016). However, for heavy oil with viscosity greater than 350 mPa s, cold production technology is difficult to use, and the current utilization ratio is only 13%. In order to explore effective development methods for offshore heavy oil, field experiments were conducted on various thermal recovery technologies such as multiple thermal fluid huff and puff, steam huff and puff, and steam flooding in oilfields such as Nanbao and Lvda in the Bohai (Tang et al., 2011; Cheng-xiang et al., 2012; Liang et al., 2014; Zhu et al., 2016; Zhong et al., 2019; Zheng et al., 2020). These thermal recovery methods have injection temperatures greater than 240°C, and the Bohai Oilfield is mostly a loose sandstone reservoir, Therefore, during the testing process, multiple wells encountered problems such as steam channeling, sand production, and string failures, which seriously affected the stimulation effect of thermal recovery (Dong et al., 2013; Jiang et al., 2014).
In order to avoid the problem of high-temperature thermal recovery, another relatively low temperature thermal recovery method - hot water drive has been proposed (Al-Hadhraml and Blunt, 2001; Alajmi and Gharbi, 2009; Wen et al., 2012; Guo and Zhou, 2019). The research results and field applications indicate that due to the low enthalpy value of hot water, its heating and viscosity reduction effect is insufficient, and the low viscosity of hot water is easy to break through during the displacement process, resulting in a decrease in the swept volume and swept efficiency of hot water. These shortcomings seriously affect the mining efficiency of hot water flooding.
In response to the problem of hot water flooding, it is proposed to add chemical agents to hot water (Wu et al., 2017). Commonly used chemicals include surfactants, hydrocarbons, alkalis and other chemicals. These chemicals can change the interface characteristics of crude oil-water-rock system, improve the wettability of rocks, reduce the surface tension of oil-water interface, and reduce residual oil saturation, So as to achieve the goal of improving heavy oil recovery (Okasha et al., 1998; Luo and Torabi, 2013; O'Carroll and Sleep, 2009; Li, 2011; Mukherjee et al., 2014). The combined action of surfactant and hot water can reduce the surface tension of oil/liquid and solid-liquid interfaces to improve the recovery efficiency of heavy oil (Schram and Smith, 1985; Lin et al., 2015). Injecting propane additives near the dew point of hot water (Pathak et al., 2011) can achieve higher oil recovery. The alkaline solution penetrates into the crude oil to form a water in oil (W/O) lotion, which reduces the fluidity of the water phase, transfers the injected hot water to the unspoiled reservoir, and improves the coverage of water (Pei et al., 2013; Taghavifar et al., 2016). Although chemical agents such as surfactants, hydrocarbons and alkalis can solve the problem of insufficient viscosity reduction in hot water flooding, this technology has no obvious effect on water breakthrough. Therefore, this article applies experimental techniques to screen suitable chemical agents to solve problems of insufficient hot water viscosity reduction and hot water breakthrough, and designs a reasonable hot water chemical flooding scheme for Bohai B Oilfield.
Hot water chemical flooding can effectively improve the mobility ratio, enhance the horizontal and vertical oil displacement efficiency of the reservoir, and further improve the oil recovery on the basis of huff and puff thermal recovery. The mechanism of EOR by hot water chemical flooding mainly includes four aspects.
① After the hot fluid is injected into the formation, its heat is transmitted to the heating zone, and the viscosity of crude oil in the heating zone is reduced.
② The chemical agent accumulates at the front edge of the displacement and reacts with the colloidal asphaltene in the heavy oil, reducing the viscosity of the heavy oil.
③ Adding a certain concentration of chemical agent to hot water increases the viscosity of the displacement phase and expands the swept volume during the displacement process.
④ Chemical agents reduce the interfacial tension between oil and water, improving oil washing efficiency.
Compared with hot water flooding or huff and puff methods, the technical advantages of hot water chemical flooding are mainly manifested in five aspects.
① The chemical agent contacts with the formation oil at the front edge of the displacement, the hydrophilic group penetrates into the oil phase, breaks up the spatial network structure formed by asphaltene and colloid, and the hydrophilic group introduces water molecules to make the dispersed heavy oil form an oil-in-water dispersion system, achieving dispersion and stable viscosity reduction, helping the hot water to flow continuously to the cold oil region, and improving the flow ability of crude oil in the affected range (Xiao et al., 2020).
② Hot water chemical flooding can reduce the interfacial tension between oil and water and improve the oil washing efficiency through the synergism of heat and chemistry. Chemicals increase the viscosity of the water phase, improve the mobility ratio, slow the fingering phenomenon, and expand the swept volume.
③ In the huff and puff mode, due to the superimposition of high-temperature gas, the heating is mainly for the upper oil layer. Under the action of gravity, hot water chemical flooding can heat and displace the middle and lower parts of the oil layer, improving the thermal sweep volume and crude oil recovery.
④ After several rounds of huff and puff, the temperature within the heating radius of the reservoir has been increased to a certain extent, but due to the depleted development mode, the reservoir energy has decreased rapidly, resulting in a sharp decline in production in the later stage of multiple rounds of huff and puff. Hot water chemical flooding can recharge the formation energy and continuously ensure the oil field production on the basis of using residual heat energy.
⑤ Compared with steam above 300°C, the temperature of hot water chemical flooding is generally controlled below 180°C. During the injection process, the temperature rise of the wellbore is relatively low and stable, reducing the damage of casing and downhole sealing device, reducing the boiler water consumption index, and providing a safe and economic solution for the medium and long-term thermal recovery development of the oilfield. At the same time, the heat loss of hot water is lower than that of high-temperature steam, which improves the utilization efficiency of heat energy.
B Oilfield is located in the central of the Bohai, characterized by high porosity and permeability, with an average porosity of 35% and an average permeability of 4,245 mD. The viscosity of crude oil in the formation is 700∼850 mPa·s, with a wax content of 2%∼8%, and a resin and asphaltene content of 20%∼50%. The oilfield was put into operation in September 2005 and developed using natural energy. Due to the high viscosity of crude oil and insufficient natural energy, the production capacity of conventional oil wells is low. In order to increase the production capacity of a single well and improve the development effect, multiple thermal fluid huff and puff field tests were carried out in the southern of B oilfield in 2008. After the implementation of thermal recovery, the daily oil production of the first round of huff and puff increased from 200 m3/d in the cold production rise to 640 m3/d, with a significant increase in production effect. After entering the second round of huff and puff at the end of 2013, the contribution of thermal recovery to production decreased, which was basically the same as that of cold production (Figure 1). The main reasons for the analysis are limited offshore platform space, large reservoir burial depth, and large well inclination. The cyclic injection huff and puff mode is adopted, resulting in severe steam channeling and large heat loss. Moreover, multiple rounds of high-temperature hot fluid injection also bring problems such as wellhead uplift.
FIGURE 1. Production performance curve of multi thermal fluid huff and puff thermal recovery in the southern area of B oilfield.
In order to further enhance the oil recovery rate of the oilfield, research on hot water chemical flooding technology has been carried out around B oilfield.
According to the performance of viscosity reduction performance, water compatibility, thermal stability, oil/water interfacial activity and other indicators under different temperature and concentration conditions, the chemical agents used in hot water chemical flooding are screened and evaluated. The range of temperature and concentration is mainly determined based on the reservoir and fluid physical parameters of the target block. The evaluation criteria of Bohai B Oilfield are shown in Table 1. The experimental temperature is 55°C and the viscosity of the experimental crude oil is 710 mPa·s.
Based on the above evaluation criteria, five chemical agents with codes of DN, HJ, HXH, RE20 and RE22 were selected for test evaluation. The test results are shown in Table 2. It can be seen from the table that DN chemical agent has good performance, so DN chemical agent is selected for key parameter test.
Based on the selected chemicals, the physical and chemical properties and solution properties were tested to evaluate the application performance of the chemicals. Among them, the viscosity concentration relationship, viscosity temperature relationship, viscosity reduction rate, and adsorption respectively characterize several performance indicators such as chemical agents increasing displacement phase viscosity, temperature resistance, and reducing heavy oil viscosity, which are closely related to the oil increase effect and are also important parameters required in formulating development plans.
At the temperature of 55°C, the viscosity of the oil displacement system before and after shearing is tested with the Wuyin stirrer under the condition of 20s at the first gear. The test results (Figure 2) show that the viscosity of the solution decreases after shearing, but the retention rates for different concentrations are above 60%. The higher the concentration, the greater the viscosity. Solutions with a concentration greater than 1500 mg/L have a viscosity of nearly 10 mPa·s after shearing, indicating good viscosity increasing performance.
FIGURE 2. Relationship between viscosity and concentration of suitable agents for hot water chemical flooding.
Figure 3 shows the viscosity of chemical agents with different concentrations at different temperatures (after shearing). With the increase of temperature, the viscosity of the chemical agent decreases gradually. When the temperature rises to above 100°C, the decrease tends to be stable, and the viscosity retention rate is above 50% at 170°C, which has good temperature resistance.
FIGURE 3. Relationship between viscosity and temperature of suitable agents for hot water chemical flooding.
Mix the oil sample and chemical agent system according to the oil-water ratio of 1:1, put it on the thermostatic magnetic stirrer, and mix it, measure the viscosity of the mixed system and calculate the viscosity reduction rate. It can be seen from the test results (Figure 4) that with the increase of the concentration of chemical agent, the viscosity reduction rate of the system increases sharply, reaching the peak at the concentration of 1,500 mg/L. After reaching the peak value, with the increase of the concentration, the viscosity reduction rate of the system is basically constant in the low temperature (T = 55°C) environment. In the high temperature (T = 115°C, 175°C) environment, the viscosity reduction rate of the system is reduced instead. The main reason is that when the temperature is above 115°C, the viscosity of crude oil is close to that of the chemical agent system. At this time, the viscosity of the chemical agent and crude oil mixture system measured by the high temperature and high pressure rheometer is mainly affected by the chemical agent itself.
FIGURE 4. Relationship between concentration and viscosity reduction rate of suitable agents for hot water chemical flooding.
Add the oil sand and chemical agent solution into a grinded conical flask with a stopper according to the solid-liquid ratio of 1:10, shake it evenly and put it in a constant temperature box at different temperatures, shake the solution of the conical flask evenly after 48h, pour it into a centrifuge tube, centrifuge for about 30min, take out the supernatant in the upper layer of the centrifuge tube, mix it well, and then use the ultraviolet spectrophotometer to measure the concentration of the oil displacement agent in the supernatant. According to the test results (Figure 5), the static adsorption capacity of the chemical agent gradually decreases with the increase of temperature, especially when the temperature is higher than 100°C, the adsorption capacity decreases rapidly. This is because the thermal movement of the molecules increases with the increase of temperature, which leads to the chemical agent molecules easily leaving the oil sand surface without forming adsorption.
Based on the selected chemicals, oil displacement experiments were carried out to compare the effect of precipitation and oil increase under different temperature and chemical concentration conditions, so as to provide reference for field application. The experimental conditions are as follows: 1) Core: the size of cylindrical core is 3.8 cm × 60 cm, gas permeability of 2,000 mD, porosity of 35%, oil saturation of 65%; 2) Timing of conversion: water content 70%; 3) Injection rate: 0.5 mL/min; 4) End of experiment: water content is 95%.
The main process of the experiment is to measure the permeability of the core with gas, saturate the water after vacuum extraction, measure the permeability with water, and perform hot water flooding after saturating the oil. When the water content reaches 70%, perform hot water chemical flooding, and when the water content reaches 95%, the oil displacement ends.
Figures 6–8 shows the results of oil displacement test based on the reservoir and fluid physical properties of Bohai B Oilfield. In order to more accurately analyze the effect of chemical agent dosage on enhanced oil recovery in hot water chemical flooding, two parameters of chemical agent enhanced oil recovery ratio and unit pore volume chemical agent enhanced oil recovery value are defined, in which chemical agent enhanced oil recovery ratio = (hot water chemical flooding enhanced oil recovery−hot water flooding enhanced oil recovery)/hot water chemical flooding enhanced oil recovery, EOR value of unit pore volume chemical agent = EOR value of hot water chemical flooding/pore volume of injected chemical agent slug.
It can be seen from the figure that under different temperatures, hot water chemical flooding can increase oil recovery by 5%–12% on the basis of hot water flooding. However, with the increase of temperature, the contribution of chemical agents to the oil recovery of hot water chemical flooding decreases, from 65% at 55°C to 20% at 175°C. The oil recovery value of unit chemical agent also decreases correspondingly, and the decrease is large when the temperature is higher than 115°C, which means that with the increase of temperature, heat gradually plays a leading role in enhancing oil recovery, and the role of chemical agent is weakened. The main reason is that under low temperature conditions, chemical agent plays a dual leading role in reducing viscosity and increasing water phase viscosity. Under high temperature conditions, thermal energy plays a leading role in reducing viscosity. The mobility of chemical agent decreases with the increase of temperature, resulting in a reduction in its ability to expand the swept volume. Therefore, the extent of enhancing oil recovery decreases with the increase of temperature.
At different concentrations of chemical agents, with the increase of the concentration of chemical agents, the range of enhanced oil recovery increases. When the concentration is greater than 1,500 mg/L, the range of enhanced oil recovery slows down, but the value of enhanced oil recovery of the amount of chemical agent per unit pore volume decreases from 15.5% of 1,500 mg/L to 13.7% of 2,500 mg/L, indicating that the concentration of chemical agent increases, the amount of chemical agent increases, but the efficiency decreases.
The hot water chemical flooding scheme has been designed for the three well groups B7, B1 and B2 in Bohai B Oilfield. The block has experienced multiple thermal fluid huff and puff development in the early stage. Therefore, the multiple thermal fluid huff and puff scheme is taken as the basic scheme for comparison of oil increase effect. On this basis, the chemical agent injection concentration, hot water temperature The chemical dosage and other parameters are optimized and the best recommended scheme is finally proposed.
Figure 9 shows the oil increase effect of hot water chemical flooding compared with the huff and puff method of multi-component thermal fluid under the same temperature (115°C) and different chemical agent concentrations. With the increase of the concentration of chemical agent, the enhanced oil recovery increases synchronously, but the rising range gradually decreases after the concentration exceeds 1,500 mg/L; Due to the constant temperature and injection volume, the enhanced oil recovery of hot water flooding is constant on the basis of multiple thermal fluid huff and puff. The oil increase per ton of agent reaches the peak at 1,500 mg/L. The calculated results are in good agreement with the results of indoor experiments, and the recommended injection concentration of chemical agent is 1,500 mg/L.
Figure 10 shows the oil increase effect of hot water chemical flooding compared with the huff and puff method of multi-component thermal fluid under the same injection concentration (1,500 mg/L) and different injection temperatures. With the increase of injection temperature, the extent of enhanced oil recovery by hot water flooding increases, and the extent of enhanced oil recovery by chemical agent decreases, which is consistent with the results of laboratory test. The sum of the two, that is, the overall enhanced oil recovery of hot water chemical flooding increases with the increase of temperature, but the increase gradually decreases when the temperature is higher than 115°C, and the increase of oil per ton agent and the comprehensive index increase after 115°C. 115°C is recommended as the injection temperature of hot water chemical flooding.
FIGURE 10. Comparison of optimization results of injection temperature of hot water chemical flooding in Bohai B Oilfield.
Figure 11 shows the oil increase effect of hot water chemical flooding compared with the huff and puff method of multi-component thermal fluid under the conditions of different chemical agent dosage. According to the calculation results, with the increase of the amount of chemical agent, the overall oil recovery rate of hot water chemical flooding increases, but the increase gradually decreases. The peak value of oil increase per ton of chemical agent is 0.25 PV, and the peak value of comprehensive index is 0.3 PV. The recommended chemical injection volume is 0.25∼0.30 PV based on the comprehensive consideration of ton polymerization and oil increase and comprehensive indicators.
FIGURE 11. Comparison of optimization results of chemical agent dosage for hot water chemical flooding in Bohai B Oilfield.
Based on the optimization results of injection parameters, the recommended schemes of three well groups B7, B1 and B2 under the optimal parameters are calculated. Compared with multi-element thermal fluid huff and puff, the effective radius of hot water chemical flooding has been expanded (Figure 12), from an average of 80 m to about 400 m for huff and puff. For offshore well spacing of 350m, the reserves between injection and production wells can be effectively utilized.
The oil increase results of the recommended scheme are shown in Figure 13. The cumulative oil increase is 18.1 × 104 m3 (including 41% oil increase by hot water flooding and 59% by chemical agents), the recovery rate increases by 4.8%, the oil increase by 31.7 m3/t per ton agent, and the comprehensive index is 62 m3%/t. Therefore, from the perspective of oil increase effect, hot water chemical flooding can be used as an effective replacement method for the subsequent development of multi-element thermal fluid huff and puff.
FIGURE 13. Annual oil increase and cumulative oil increase curve of recommended scheme of hot water chemical flooding in Bohai B Oilfield.
Hot water chemical flooding organically combines hot water flooding with chemical flooding. The thermal energy carried by hot water and the role of chemical agents in dispersing asphaltene and colloid aggregates jointly reduce the viscosity of crude oil, and the chemical agents increase the viscosity of water phase to further improve the water-oil mobility ratio. The thermal energy also has the role of improving the oil washing efficiency, which not only expands the wave and volume, but also improves the oil washing efficiency, and improves the oil recovery through the physical and chemical synergy.
Injection temperature and chemical agent concentration are the key factors that affect the oil increase effect and economic benefits of hot water chemical flooding. The results of laboratory experiments and numerical simulation show that with the increase of temperature, the thermal energy in hot water chemical flooding increases oil recovery, but the effect of chemical agent is weakened; With the increase of chemical agent concentration, the enhanced oil recovery increases, but when the concentration is greater than a certain value, the enhanced oil recovery value of chemical agent per unit pore volume and the increased oil value per ton of agent will decrease. Therefore, the reasonable injection temperature and chemical agent concentration should be selected according to the specific oilfield characteristics.
The calculation results of the recommended scheme of hot water chemical flooding in the south area of Bohai B Oilfield show that compared with the multiple thermal fluid huff and puff method, the hot water chemical flooding can improve oil recovery by 4.8%, increase oil yield by 31.7 m3/t per ton, and have better technical and economic indicators. Therefore, the hot water chemical flooding can be used as the subsequent effective replacement method of the multiple thermal fluid huff and puff, providing a new idea for the effective development of offshore heavy oil.
The original contributions presented in the study are included in the article/Supplementary Material, further inquiries can be directed to the corresponding author.
ZJ: Conceptualization, Data curation, Writing–original draft. LD: Investigation, Writing–original draft. ZW: Methodology, Formal analysis, Writing–original draft. ZQ: Data curation, Formal analysis, Writing–original draft. WL: Software, Formal analysis, Writing–review and editing. WZ: Software, Methodology, Writing–review and editing.
The author(s) declare that no financial support was received for the research, authorship, and/or publication of this article.
We thank the support of “Independent Prospective Basic Project of State Key Laboratory of Offshore Oil Exploitation in 2023,” “Key technologies for large-scale application of chemical flooding in offshore oil fields,” and “Research on key technologies for thermal recovery and mobile thermal injection in offshore multi-layer oil reservoirs.”
Authors ZJ, LD, ZW, ZQ, WL, and WZ were employed by CNOOC Research Institute Co., Ltd.
All claims expressed in this article are solely those of the authors and do not necessarily represent those of their affiliated organizations, or those of the publisher, the editors and the reviewers. Any product that may be evaluated in this article, or claim that may be made by its manufacturer, is not guaranteed or endorsed by the publisher.
Alajmi, A. F., and Gharbi, R. (2009). “Experimental evaluation of heavy oil recovery by hot water injection in a middle eastern reservoir,” in SPE Middle East Oil and Gas, Manama, Bahrain, March, 2009.
Al-Hadhraml, H. S., and Blunt, M. J. (2001). Thermally induced wettability alteration to improve oil recovery in fractured reservoirs. SPE Res Eval Eng 4, 179–186. doi:10.2118/71866-pa
Cheng-xiang, Qi, Jing-song, Li, Jiang, J., et al. (2012). Multi-factor orthogonal optimization study on the injection-and-production parameters of multi-thermal-fluid huff & puff for recovering offshore heavy oil. Special Oil Gas Reservoirs 19 (5), 86–89.
Dong, S., Zhang, H., Gongming, Ji, et al. (2013). Test and analysis of sand control screen corrosion in thermal production wells using multiple thermal fluids. Chem. Eng. Oil Gas 42 (3), 287–289.
Guo, D., and Zhou, Z. (2019). Study on the development effect of thermal water flooding in Shallow and thin heavy oil reservoirs in block A of Ala Xin’a area. J. Yangtze Univ. Sci. Ed. 16 (8), 23–27.
Jiang, J., Gong, R., Li, J., et al. (2014). Study on cross well steam channeling regularity of horizontal well multi-component thermal fluid stimulation in heavy reservoir. Oil Gas Field Dev. 32 (5), 45–48.
Li, A. (2011). Study on hot water and hot chemical flooding in heavy oil reservoir of block Cao4, Le’an oilfield. Petroleum Geol. Recovery Effic. 18 (3), 64–66.
Liang, D., Guozhi, F., Zeng, X., et al. (2014). Evaluation of two thermal methods in offshore heavy oilfield development. Pet. Drill. Tech. 42 (1), 95–99.
Liang, D., Zeng, X., and Fang, M. (2012). Productivity evaluation and influence factor analysis for adequate sanding production wells. Special Oil Gas Reservoirs 19 (5), 66–68.
Lin, R., Zhou, G., Yang, K., et al. (2015). Laboratory experiment on hot water and surfactant flooding. Petroleum Geol. recovery Effic. 22 (4), 114–117.
Luo, W., and Torabi, F. (2013). “Coupling of solvent and hot water to improve heavy oil recovery:experimental and simulation studies,” in SPE Heavy Oil Conference-Canada, Calgary, Alberta, Canada, June, 2013.
Mukherjee, S., Suss, M. P., and Gmbh, W. H. (2014). “Performance evaluation and design aspects of polymer and hot water co-injection in an offshore heavy oil field under challenging conditions,” in SPE EOR Conference at Oil and Gas West Asia, Muscat, Oman, March 2014.
O’Carroll, D. M., and Sleep, B. E. (2009). Role of NAPL thermal properties in the effectiveness of hot water flooding. Transp. porous media 79 (3), 393–405. doi:10.1007/s11242-008-9329-2
Okasha, T. M., Menouar, H. K., and Abu-Khamsin, S. A. (1998). Oil recovery from tarmat reservoirs using hot water and solvent flooding. J. Can. Petroleum Technol. 37 (4), 33–40. doi:10.2118/98-04-03
Pathak, V., Babadagli, T., and Edmunds, N. R. (2010). “Hot solvent injection for heavy oil/bitumen recovery: an experimental investigation,” in Canadian unconventional resources and international petroleum conference, Calgary, Alberta, Canada, October, 2010.
Pei, H., Zhang, G., Ge, J., Jin, L., and Ma, C. (2013). Potential of alkaline flooding to enhance heavy oil recovery through water-in-oil emulsification. Fuel 104 (2), 284–293. doi:10.1016/j.fuel.2012.08.024
Schramm, L. L., and Smith, R. G. (1985). The influence of natural surfactants on interfacial charges in the hot-water process for recovering bitumen from the Athabasca oil sands. Colloids surfaces 14 (1), 67–85. doi:10.1016/0166-6622(85)80042-1
Taghavifar, M., Fortenberry, R., De Rouffignac, E., Sepehrnoori, K., and Pope, G. A. (2016). Heavy-oil recovery by combined hot water and alkali/cosolvent/polymer flooding. SPE J. 21 (1), 74–86. doi:10.2118/170161-pa
Tang, X., Ma, Y., and Sun, Y. (2011). Research and field test complex thermal fluid huff and puff technology for offshore viscous oil recovery. China Offshore Oil Gas 23 (3), 185–188.
Wen, Y., Kang, S., Li, Y., et al. (2012). Pilot test study on hot water flooding in area 160 of ansai oil field. Petroleum Geol. Eng. 26 (6), 117–119.
Wu, Y., Xu, T., and Lin, C. (2017). Experiment on the thermochemical complex flooding system for low-permeability heavy oil reservoirs. Petroleum Geol. Oilfield Dev. Daqing 36 (2), 107–110.
Xiao, Sa, Sun, Y., Wang, S.-hua, et al. (2020). Analysis of physical properties of heavy oil in Bohai sea and study on development measures. Xinjiang Oil Gas 16 (4), 70–77.
Xie, X., Kang, X., Zhang, X., et al. (2016). Chemical flooding potential evaluation method in offshore heavy oilfields and its application. China Offshore Oil Gas 28 (1), 69–74.
Zhang, X., Sun, F., Guozhi, F., et al. (2007). A research on influence factors of polymer flooding and its field testing in Bohai heavy oil fields. China Offshore Oil Gas 19 (1), 30–34.
Zheng, W., Tan, X., Wang, T., et al. (2020). A new method to determine initial production of steam stimulation in offshore heavy oilfield. Xinjiang Pet. Geol. 41 (3), 344–348.
Zhong, L., Wang, C., Liu, J., et al. (2019). Nitrogen assist-ed steam stimulation technology for mid-deep heavy oil reservoirs. Xinjiang Pet. Geol. 40 (2), 194–198.
Keywords: heavy oil, hot water chemical flooding, chemical agent evaluation, scheme design, numerical simulation
Citation: Jian Z, Dan L, Wensheng Z, Qichen Z, Liqi W and Zhijie W (2024) Research on hot water chemical flooding technology in Bohai heavy oil field. Front. Energy Res. 11:1324876. doi: 10.3389/fenrg.2023.1324876
Received: 20 October 2023; Accepted: 11 December 2023;
Published: 18 January 2024.
Edited by:
Zhilin Cheng, Xi’an Shiyou University, ChinaReviewed by:
Liping Cui, SINOPEC Petroleum Exploration and Production Research Institute, ChinaCopyright © 2024 Jian, Dan, Wensheng, Qichen, Liqi and Zhijie. This is an open-access article distributed under the terms of the Creative Commons Attribution License (CC BY). The use, distribution or reproduction in other forums is permitted, provided the original author(s) and the copyright owner(s) are credited and that the original publication in this journal is cited, in accordance with accepted academic practice. No use, distribution or reproduction is permitted which does not comply with these terms.
*Correspondence: Liang Dan, bGlhbmdkYW5AY25vb2MuY29tLmNu
Disclaimer: All claims expressed in this article are solely those of the authors and do not necessarily represent those of their affiliated organizations, or those of the publisher, the editors and the reviewers. Any product that may be evaluated in this article or claim that may be made by its manufacturer is not guaranteed or endorsed by the publisher.
Research integrity at Frontiers
Learn more about the work of our research integrity team to safeguard the quality of each article we publish.