- 1Guangdong Hongye Building Materials Technology Co., Ltd., Yunfu, Guangdong, China
- 2State Key Laboratory of Silicate Materials for Architectures, Wuhan University of Technology, Wuhan, China
- 3School of Civil Engineering and Architecture, Wuhan University of Technology, Wuhan, China
- 4Faculty of Civil Engineering and Geosciences, Delft University of Technology, Delft, Netherlands
- 5Shenzhen Sez Construction Group Co., Ltd., Shenzhen, Guangdong, China
As a kind of solid waste, using Prestressed High-Strength Concrete Pile Waste Concrete (PPWC) as the replacement for limestone filler in asphalt concrete can not only reduce the accumulation of PPWC and increase its utilization but also avoid the increased road construction costs and environmental degradation associated with limestone mining. This study aims to investigate the effect of using PPWC filler to replace limestone filler on the road performance of asphalt concrete. Firstly, PPWC was ground into filler particles with a diameter less than 0.075 mm. The particle characteristics such as surface morphology, particle size distribution and chemical composition of PPWC filler and limestone filler were compared. Then, PPWC filler was used to replace limestone filler with different volume fractions to prepare asphalt concrete, and the water damage resistance, high-temperature rutting resistance, low-temperature crack resistance, fatigue resistance and adhesion performance of asphalt concrete were tested. The results showed that PPWC filler has a smaller particle size and rougher surface than limestone filler, and it contains Ca(OH)2 produced by hydration. The addition of PPWC filler can effectively improve the mechanical properties of asphalt concrete without reducing its water damage resistance. PPWC filler can improve the high-temperature rutting resistance and low-temperature crack resistance of asphalt concrete, but reduce its low-temperature fatigue resistance. The low content of PPWC filler will enhance the adhesion between asphalt mortar and aggregate. However, when the content of PPWC filler exceeds 50%, Ca (OH)2 in PPWC will reduce the adhesion between acid asphalt mortar and alkaline basalt aggregate. Therefore, the use of PPWC as filler in asphalt mixtures provides a reliable solution for the sustainable development of road materials.
1 Introduction
Prestressed High-Strength Concrete Pile (PHC pile), as a type of hollow cylindrical precast concrete pile, is widely used in foundation engineering of bridges, tunnels and other buildings to improve the stability of buildings (Liu et al., 2019; Li et al., 2021; Li et al., 2023). China is the world’s largest producer of PHC pile, with a production volume reaching 486.28 million meters in 2022 (Chen et al., 2019). However, for two main reasons, China generates a significant amount of waste PHC pile each year. On the one hand, during the manufacturing process, PHC pile may develop defects, such as cracks or non-compliance with specifications. These defects can render PHC pile unusable for construction, thus becoming waste materials. On the other hand, aging buildings or structures may require maintenance, renovation, or demolition. In such cases, PHC pile may need to be removed and replaced, resulting in the generation of a significant amount of waste pile (Yu et al., 2021). Sua-iam and Makul (2023) used PHC pile waste concrete (PPWC) to replace natural aggregates to prepare green self-compacting concrete. The results show that PPWC can improve the compressive strength of concrete and can significantly reduce the production cost of high-performance concrete. However, there are still few studies on the recycling of PPWC in roads and construction engineering, and a large amount of PPWC is accumulated in factories and cannot be treated. Therefore, the utilization of PPWC has emerged as an essential issue that requires attention.
China’s road infrastructure construction has experienced rapid development. In 2022, the total length of China’s road network reached 5.3548 million kilometers, and the total length of expressways reached 177,300 km (Yang et al., 2023). Among these roads, asphalt concrete pavement, known for its advantages of low noise, high comfort, and easy construction, is the primary road surface material (Yang et al., 2022; Gong et al., 2023; Lv et al., 2023; Xie et al., 2023). Especially in the construction of expressways in China, the proportion of asphalt concrete pavement exceeds 90% (Cui et al., 2021; Li et al., 2022b; Osuolale et al., 2023). Typically, asphalt concrete is composed of asphalt, aggregates, and mineral fillers (Taherkhani and Vahabi Kamsari, 2020; Jia et al., 2022). The shape and size of mineral fillers can impact asphalt’s flowability, consequently influencing the construction performance of asphalt concrete (Xing et al., 2019; Zhang et al., 2020; Belayali et al., 2023). Moreover, mineral fillers can fill the voids in asphalt concrete, enhancing its strength and thus improving the durability of road structures (Amirbayev et al., 2022; Russo et al., 2022; Wei et al., 2022). Limestone filler is the most commonly used mineral filler. However, mineral resources are being depleted due to the rapid development of the road industry, resulting in increased costs and environmental degradation associated with limestone extraction (Liu N. et al., 2023; Ou et al., 2023). Therefore, the adoption of more sustainable materials as alternatives to limestone fillers to reduce mineral resource consumption and mitigate environmental impacts is crucial (Liu et al., 2018; Liu J. et al., 2023). Which is also consistent with the goal of sustainable development, prompting the road industry to pay more attention to environmental protection and resource conservation (Yang et al., 2021; Sun et al., 2023).
There have been studies reporting solid waste can be used in place of mineral filler in asphalt concrete (Habibnejad Korayem et al., 2020; Das and Singh, 2021; Liu N. et al., 2023). Paul et al. (2021) used fly ash (FA) and glass powder (GP) to replace limestone filler in steel slag asphalt mixture, and investigated the water damage resistance and rutting resistance of asphalt concrete. The findings indicate that FA and GP greatly increased the stiffness of steel slag asphalt concrete, resulting in enhanced anti-rutting performance, but slightly reduced the water damage resistance of asphalt concrete. Osuolale et al. (2023) used bamboo leaf ash (BLA) as filler in asphalt mixture and investigated the road performance of asphalt concrete. They found that in addition to enhancing asphalt concrete’s volume stability, rutting resistance, and low-temperature cracking resistance, BLA filler can also strengthen the adhesion between asphalt mortar and aggregate, but the fatigue life and anti-skid performance of asphalt concrete were reduced. Yang et al. (2021) used diatomite and bauxite residues to replace the traditional mineral fillers in asphalt concrete and studied the mechanical properties, anti-aging properties and leaching characteristics of porous asphalt mixtures. They found that asphalt concrete’s aging and raveling resistance can be improved by using diatomite and bauxite residue fillers, but the leaching concentration of heavy metals in asphalt concrete also increased, which may be raise the risk of environmental pollution. Zhang et al. (2018) used red mud in place of limestone fillers to prepare asphalt concrete, and systematically studied its anti-rutting performance. The results show that red mud filler can increase the complex modulus and phase angle of asphalt mortar, enhance the elastic behavior of asphalt mortar, and lead to the significant improvement of rutting resistance of asphalt concrete at high-temperature. The influence of coal gangue filler on the road performance and crack healing ability of asphalt concrete were investigated by Li et al. (2022a). The findings indicate that coal gangue filler was beneficial to enhance asphalt concrete’s low-temperature crack resistance. When the content of coal gangue filler was 50%, asphalt concrete showed the best microwave self-healing capacities.
In conclusion, using solid waste materials instead as mineral fillers can maximize the use of waste resources, lower the cost of raw materials, and enhance the working properties of asphalt concrete. However, the research on using PPWC as the filler in asphalt concrete remains limited. The effect of PPWC filler on the asphalt concrete’s road performance awaits further investigation.
This study used PPWC as filler to prepare asphalt concrete to evaluate the impact of replacing limestone filler with PPWC filler in asphalt concrete on the road performance of asphalt concrete. Firstly, by using the planetary ball mill, PPWC was crushed into powder with a particle size less than 0.075 mm. Both the PPWC filler and the limestone filler’s particle characteristics were investigated. Then, asphalt concrete was prepared by using PPWC filler to replace limestone fillers with different volume ratios (25%, 50%, 75%, and 100%). Then, Standard Marshall tests, immersion Marshall tests, freeze-thaw splitting tests, rutting tests, bending beam tests, indirect tensile fatigue tests and Cantabro tests were conducted to investigate the water damage resistance, high-temperature rutting resistance, low-temperature crack resistance, fatigue resistance and adhesion performance of asphalt concrete with different PPWC filler contents. The study results will provide a theoretical basis for the application of PPWC filler in asphalt concrete. The research process is shown in Figure 1.
2 Materials and methods
2.1 Raw materials
SBS-modified asphalt from China’s Hebei Province was selected as the basis asphalt. Its basic properties were tested according to the Chinese standard JTG E20-2011 (China, 2011), Table 1 lists the results. The basalt aggregate came from a quarry in the Chinese province of Hubei’s Jingshan City. Its basic properties were tested according to the Chinese standard JTG E42-2005 (China, 2005), Table 2 displays the results. The quarry in Wuhan, Hubei Province, China provided the limestone filler, while a PHC pile producer in Yunfu, Guangdong Province, China provided the PPWC. PPWC was ground at 500 rpm for 40 min to a particle diameter of less than 0.075 mm.
The basic properties of PPWC and limestone filler were assessed in accordance with Chinese standard JTG-E42-2005 (China, 2005). Table 3 displays the results. It demonstrated that the density of the PPWC filler was slightly lower than that of the limestone filler. The hydrophilic coefficient, which is used to evaluate the filler’s adhesive properties to the asphalt binder, is the ratio of the filler’s volume in water to that of the filler’s volume in kerosene. According to the results, PPWC filler has a hydrophilic coefficient of 0.78, which means that it has a stronger affinity for asphalt than for water and satisfies the standards’ requirements.
2.2 Preparation of asphalt concrete
The SMA-13 gradation was designed and the oil-aggregate ratio was defined as 5.6% based on Marshall design according to the Chinese standard JTG D50-2017 (China, 2017), and five kinds of asphalt concrete were prepared by replacing 25%, 50%, 75%, and 100% volume of limestone filler with PPWC filler. Considering the low content of fillers in asphalt concrete, their influence on aggregate gradation selection was minimal. Therefore, the gradation of the five kinds of asphalt concrete was the same, as shown in Figure 2.
2.3 Experimental methods
2.3.1 Particle characteristics
Scanning electron microscopy (SEM, Zeiss Gemini 300, Carl Zeiss AG, Germany) and laser particle size analyzer (Mastersizer 3,000, Malvern Panalytical, Germany) were used to examine the surface morphology and particle size distribution of PPWC and limestone filler. X-ray fluorescence (XRF) and X-ray diffraction (XRD) tests were used to determine the chemical composition and phase distribution of the two fillers.
2.3.2 Water damage resistance
According to the Chinese standard JTG E20–2011 (China, 2011), standard Marshall test, immersion Marshall test, and freeze-thaw splitting test were conducted, with six parallel samples for each test. The Retained Marshall Stability (RMS) and Tensile Strength Ratio (TSR) were retained to assess the water damage resistance performance of the asphalt concrete.
When testing the RMS, the Marshall specimens with a diameter of 101.6 mm and a thickness of 63.5 mm were immersed in a constant temperature water tank at 60°C for 48 h. The RMS of the asphalt concrete was determined using the following equation:
Where MS0 is the average Marshall stability of asphalt concrete, kN; MSn is the average Marshall stability after soaking in a constant temperature water tank at 60°C for 48 h, kN.
In the test of TSR, the Marshall specimen with a diameter of 101.6 mm and a thickness of 63.5 mm was frozen at −18°C for 16 h, and then placed in a constant temperature water tank at 60°C for 24 h. Finally, the Marshall specimen was kept in a constant temperature water tank at 25°C for 2 h to test its splitting tensile strength (STS). The TSR of the asphalt concrete was determined using the following equation:
Where STS0 is the average STS of asphalt concrete, MPa; STSn is the average STS of asphalt concrete after freeze-thaw damage, MPa.
2.3.3 High-temperature rutting resistance
According to the Chinese standard JTG E20–2011 (China, 2011), the asphalt concrete slab with a size of 300 × 300 × 50 mm was prepared, and a wheel tracking device was used to conduct the rutting test to evaluate the high-temperature rutting resistance of asphalt concrete. The width of the wheel was 50 mm and the load was 0.7 MPa. At 60°C. The wheel moved back and forth in the central area of the asphalt concrete slab at a speed of 42 times/min for 60 min to obtain dynamic stability and rutting depth.
2.3.4 Low-temperature crack resistance
According to the Chinese standard JTG E20–2011 (China, 2011), asphalt concrete beams with a size of 250 mm × 30 mm × 35 mm were prepared to conduct bending beam test at −10°C to test the low-temperature cracking resistance of asphalt concrete.
2.3.5 Fatigue resistance
The Marshall specimen with a diameter of 101.6 mm and a thickness of 63.5 mm was cut to a thickness of 40 mm, and the fatigue life of five kinds of asphalt concrete was tested by indirect tensile fatigue test. The test temperature was set to 15°C. Before the test, the stress level is determined according to the splitting strength of asphalt concrete.
2.3.6 Adhesion performance
According to the Chinese standard JTG E20–2011 (China, 2011), the impact of PPWC filler on asphalt-aggregate adhesion performance was evaluated by Cantabro test. The Marshall specimen with a diameter of 101.6 mm and a thickness of 63.5 mm was immersed in a constant temperature water tank at 20°C for 20 h and taken out. After being placed at room temperature for 24 h, it was placed in a Los Angeles tester and rotated at the speed of 30 r/min for 300 revolutions. The scattering loss is calculated according to the following equation:
Where ΔS is the scattering loss of asphalt concrete, m0 is the mass of Marshall specimen when it is taken out from the water tank, m1 is the residual mass of Marshall specimen after rotation.
3 Results and discussions
3.1 Particle characteristics of filler
3.1.1 Surface morphology of filler
The micro-morphology of PPWC and limestone filler is depicted in Figures 3A, B after being magnified 10,000 times, respectively. It is clear that the PPWC filler’s surface is covered in the gel products created by hydration, and it has a rougher surface than the limestone filler. The study by Zhao et al. (2021) found that filler with rougher surfaces is beneficial for increasing the density, stability and skid resistance of asphalt concrete. The limestone filler, in comparison, has an uneven surface made up of smooth flakes. The abundant angularity on the surface of PPWC fillers can enhance the interaction forces between asphalt and filler particles, thereby improving the mechanical properties of asphalt concrete.
3.1.2 Particle size distribution of filler
Figure 4 displays the particle size distribution curves for the two fillers. The results indicate that PPWC filler has a smaller average particle size (12.53 μm) than limestone filler (15.49 μm) and a larger specific surface area (1.78 m2/g) than limestone filler (1.45 m2/g). This may be because in comparison to limestone filler, PPWC filler has a rougher surface as well as smaller particle size and density.
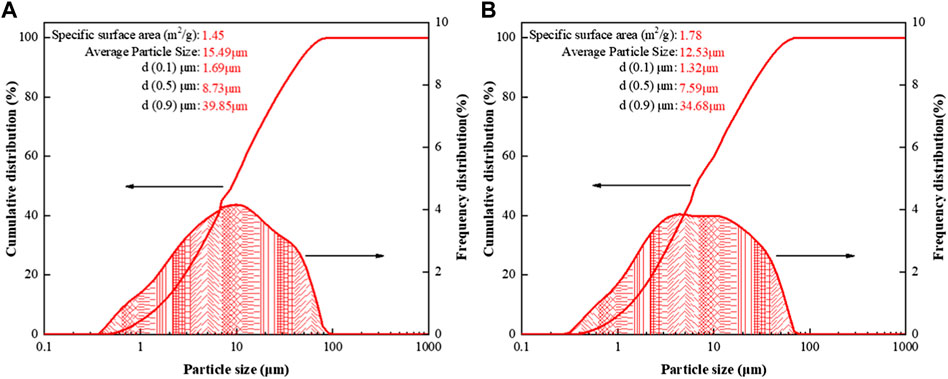
FIGURE 4. Particle size distribution curves of the two fillers, (A) limestone filler, (B) PPWC filler.
3.1.3 Chemical composition of filler
Figure 5 shows the oxide composition of PPWC and limestone fillers. It can be observed that the main oxides in both PPWC filler and limestone filler are CaO and SiO2. Since calcium carbonate makes up the majority of limestone filler, its CaO content is larger (58.87%) than that of PPWC (37.17%). However, The SiO2 content of PPWC filler (34.31%) is larger than that of limestone filler (18.98%), which may be due to the existence of SiO2-rich aggregates such as sand and crushed stone in PPWC.
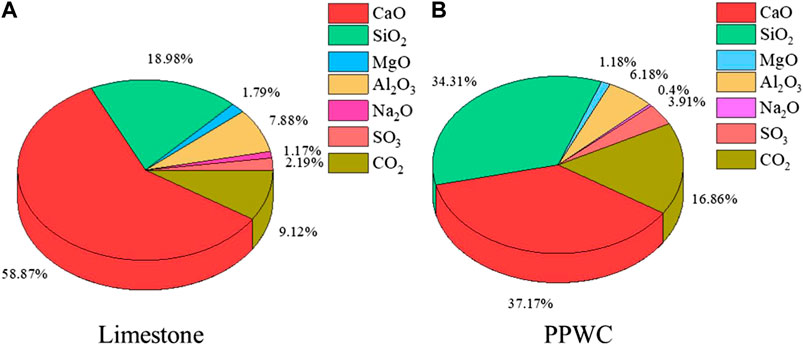
FIGURE 5. The oxide composition of PPWC filler and limestone filler, (A) Limestone filler, (B) PPWC filler.
Figure 6 shows the XRD curves for PPWC filler and limestone filler. The results show similar mineral compositions between the two fillers, with SiO2 and CaCO3 as the major crystalline phases. The diffraction peak of Ca (OH)2 is apparent on the PPWC’s XRD curve, though. This may be related to the hydration of the cement during the production of PHC piles. As the cementitious material for the preparation of PHC piles, the CaO contained in the cement will react with H2O to form Ca (OH)2.
3.2 Road performance
3.2.1 Water damage resistance
The RMS results of asphalt concrete are shown in Figure 7. It is evident that the Marshall stability of asphalt concrete increased with the increase of PPWC filler content. Compared with limestone filler asphalt concrete, the Marshall stability of asphalt concrete increased by 4.9%, 10.8%, 16.7%, and 20.6% respectively when PPWC filler was used to replace 25%, 50%, 75%, and 100% volume of limestone filler. The RMS of the five kinds of asphalt concrete had no significant difference, which is about 93%, meeting the requirements of the Chinese standard JTG/T 3350-03-2020 (higher than 85%). According to the results, using PPWC filler can improve asphalt concrete’s stability, which may be due to the rougher surface of PPWC filler than limestone filler, so the friction between PPWC filler particles and asphalt is stronger, thereby enhancing the structural stability of asphalt concrete.
The TSR results of asphalt concrete are shown in Figure 8. It is evident that as the content of PPWC filler rose, the splitting strength of asphalt concrete also increased. When the content of PPWC filler increased from 25% to 100%, compared with limestone filler asphalt concrete, the splitting strength of Marshall specimens before freeze-thaw damage increased by 3.2%, 14%, 20.4%, and 25.8%, respectively, which was consistent with the trend of Marshall stability. The TSR of the five kinds of asphalt concrete is very close, all around 92.5%, which satisfies the requirements of the Chinese standard JTG/T 3350-03-2020 (higher than 80%). Combined with the results of RMS, it is shown that the incorporation of PPWC filler can significantly enhance the mechanical properties of asphalt concrete without reducing its water damage resistance.
3.2.2 High-temperature rutting resistance
Rutting test can assess the rutting resistance of asphalt concrete at high-temperatures. The dynamic stability and rutting depth of five kinds of asphalt concrete slabs are depicted in Figure 9 based on the results of the rutting test. It can be seen that the dynamic stability of asphalt concrete improved and the depth of rutting decreased with an increase in PPWC filler content. Compared with limestone filler asphalt concrete, when the content of PPWC filler increased from 25% to 100%, the dynamic stability of asphalt concrete increased by 1.2%, 3.7%, 4.8%, and 6.3% respectively, and the rutting depth decreased from 3.32 mm to 3.21 mm, 3.08 mm, 2.93 mm, and 2.81 mm respectively. The dynamic stability of the five kinds of slab specimens is higher than 5,000 times/mm, which is sufficient for engineering application. The modification effect of filler on asphalt can significantly affect the high-temperature stability of asphalt concrete. Compared to limestone filler, PPWC filler has smaller particles, rougher surface and greater specific surface area, so its adsorption capacity for asphalt is stronger than that of limestone filler. The free asphalt in asphalt concrete is transformed into structural asphalt under the adsorption of PPWC filler, thereby enhancing the stiffness of asphalt mortar. Therefore, the use of PPWC filler to replace limestone filler can make asphalt concrete have stronger deformation resistance at high temperatures, so as to increase asphalt concrete’s resistance to rutting at high temperatures and reduce the permanent deformation of asphalt concrete under high temperature rutting.
3.2.3 Low-temperature crack resistance
Table 4 shows the test results of low-temperature crack resistance of five kinds of asphalt concrete. Ultimate flexural tensile strength can represent the mechanical strength of asphalt concrete at low-temperature. Ultimate flexural tensile strain can characterize the deformability of asphalt concrete at low-temperature. The stiffness modulus, which measures the toughness of asphalt concrete, is the ratio of ultimate flexural tensile strength to ultimate flexural strain. It is evident that the influence of PPWC filler on ultimate flexural tensile strength and ultimate flexural tensile strain is inconsistent. With the increase of PPWC filler content, the ultimate flexural tensile strength and stiffness modulus of asphalt concrete increased, the ultimate flexural tensile strain of asphalt concrete decreased. This shows that at low-temperature, PPWC filler enhanced the mechanical strength of asphalt concrete, but reduced the toughness of asphalt concrete, resulting in a decrease in its deformability. This may be due to the hardening effect of PPWC filler on asphalt. PPWC filler is a kind of material with large specific surface area and rough surface. Its adsorption on asphalt enhances the stiffness of asphalt mortar, thus enhancing the strength of asphalt concrete. However, the ductility and fluidity of asphalt mortar decrease with the increase of stiffness at low-temperature, making asphalt concrete more prone to brittle failure, thus reducing the ultimate bending tensile strain.
3.2.4 Fatigue resistance
The fatigue life and fitting results of asphalt concrete under different stress levels are shown in Figure 10. As the stress level increased, it can be seen that asphalt concrete’s fatigue life decreased. At the same stress level, the fatigue life of asphalt concrete decreased with the increase of PPWC filler content. As a kind of viscoelastic material, asphalt has a certain ability to repair micro-cracks. However, PPWC filler will harden asphalt mortar and reduce the response rate of asphalt concrete to stress, thus weakening the healing ability of asphalt to strain cracks, resulting in more brittle cracks in asphalt concrete under stress, which is in agreement with the findings of the bending strain test. Under the action of cyclic load, the brittle cracks in asphalt concrete continue to develop, which eventually leads to brittle fracture of asphalt concrete. Therefore, the asphalt concrete with higher PPWC filler content exhibits worse fatigue resistance.
3.2.5 Adhesion performance
Figure 11 shows the results of the Cantabro test. ΔS can characterize the adhesive capacity between asphalt mortar and aggregate. The smaller ΔS indicates the stronger adhesive capacity between asphalt mortar and aggregates. It is evident that the ΔS of asphalt concrete decreased first and then increased with the increase of PPWC content. When the content of PPWC filler was less than 50%, the ΔS of asphalt concrete was lower than that of limestone filler asphalt concrete, indicating that the adhesion between basalt aggregate and asphalt mortar was stronger. However, when the content of PPWC filler exceeded 50%, ΔS began to increase, indicating that the adhesion between basalt aggregate and asphalt mortar was weakened. PPWC filler has rough surface and high specific surface area. Therefore, the addition of low content of PPWC filler can improve the adsorption between filler and asphalt, enhance the compactness and cohesion of asphalt mortar, thereby improve the adhesion between asphalt mortar and basalt aggregate and reduce the ΔS of asphalt concrete. However, basalt is the typical alkaline aggregate. When high content of PPWC filler was added to asphalt, the Ca (OH)2 produced by hydration in PPWC will reduce the acidity of asphalt mortar (Meng et al., 2023), thereby reducing the adhesion between asphalt mortar and basalt aggregate, resulting in the increase of ΔS.
4 Conclusion
This study aims to evaluate the effect of using PPWC filler to replace limestone filler in asphalt concrete on its road performance. Firstly, limestone and PPWC fillers’ chemical and physical characteristics were examined. Then, five kinds of asphalt concrete were prepared by using PPWC filler to replace different volume of limestone filler (0, 25%, 50%, 75%, and 100%), and their road performance were tested. Based on the test results, the main conclusions are as follows.
(1) PPWC filler has a smaller particle size, lower density and rougher surface when compared to limestone filler. PPWC filler contains Ca (OH)2 from hydration and has a lower CaO content than limestone filler.
(2) The addition of PPWC filler can improve the Marshall stability of asphalt concrete, but there is no significant difference in RMS and TSR of five kinds of asphalt concrete, indicating that the addition of PPWC filler can effectively improve the mechanical properties of asphalt concrete without reducing its water damage resistance.
(3) The use of PPWC filler to replace limestone filler can make asphalt concrete have stronger deformation resistance at high temperatures. The hardening effect of PPWC on asphalt concrete improves the low temperature crack resistance of asphalt concrete, but the fatigue resistance decreases.
(4) The rough surface of PPWC filler will enhance the adhesion between asphalt mortar and basalt aggregate. However, when the content of PPWC filler exceeds 50%, Ca (OH)2 in PPWC will reduce the acidity of asphalt mortar, thus reducing the adhesion between asphalt mortar and the alkaline basalt aggregate.
The above conclusions show that PPWC filler can be used to replace limestone filler in asphalt concrete to maximize resource utilization, reduce raw material costs, and enhance road performance, thereby providing a new solution for the sustainable development of the road industry.
5 Limitations and further study
In this paper, the effect of PPWC filler on the road performance of asphalt concrete is studied. However, the effect of PPWC on the performance of basis asphalt is still unclear, and the performance of PPWC filler asphalt concrete in the service process needs to be further verified. In the future study, the influence of PPWC filler on the performance of asphalt mortar will be further studied, and the PPWC filler concrete will be applied to the pavement engineering to verify its durability.
Data availability statement
The original contributions presented in the study are included in the article/Supplementary material, further inquiries can be directed to the corresponding author.
Author contributions
BT: Conceptualization, Writing–original draft. XY: Conceptualization, Writing–original draft. SX: Methodology, Writing–review and editing. ZZ: Methodology, Writing–review and editing. YZ: Methodology, Writing–review and editing. JJ: Investigation, Writing–review and editing. LF: Investigation, Writing–review and editing. LT: Investigation, Writing–review and editing.
Funding
The author(s) declare financial support was received for the research, authorship, and/or publication of this article. This work was supported by the National Natural Science Foundation of China (52108416), the National Natural Science Foundation of China (No. 52308464), Hubei Science and Technology Innovation Talent and Service Project (No. 2022EHB006).
Conflict of interest
Author BT is employed by Guangdong Hongye Building Materials Technology Co., Ltd. Authors JJ, LF, and LT is employed by Shenzhen Sez Construction Group Co., Ltd.
The remaining authors declare that the research was conducted in the absence of any commercial or financial relationships that could be construed as a potential conflict of interest.
Publisher’s note
All claims expressed in this article are solely those of the authors and do not necessarily represent those of their affiliated organizations, or those of the publisher, the editors and the reviewers. Any product that may be evaluated in this article, or claim that may be made by its manufacturer, is not guaranteed or endorsed by the publisher.
References
Amirbayev, Y., Yelshibayev, A., and Nugmanova, A. (2022). Characterization of asphalt bitumens and asphalt concretes modified with carbon powder. Case Stud. Constr. Mater. 17, e01554. doi:10.1016/j.cscm.2022.e01554
Belayali, F., Maherzi, W., Benzerzour, M., and Abriak, N.-E. (2023). Influence of the physical and chemical characteristics of sediment fillers on the properties of mastic asphalt. Powder Technol. 421, 118393. doi:10.1016/j.powtec.2023.118393
Chen, Z., Xiao-Yu, B., Ming-Yi, Z., and De-Zi, M. (2019). Study on bearing behavior and Q-s curve model of rock-socketed PHC pipe piles based on ultimate load tests. Journal of Guangxi University(Natural Science Edition.
China, M.O.T.O.T.P.S.R.O (2011). Standard test methods of bitumen and bituminous mixtures for highway engineering: JTG E20-2011.
China, M.O.T.O.T.P.S.R.O (2017). Specifications for design of highway asphalt pavement. JTG D50-2017.
Cui, P., Wu, S., Xiao, Y., Hu, R., and Yang, T. (2021). Environmental performance and functional analysis of chip seals with recycled basic oxygen furnace slag as aggregate. J. Hazard. Mater. 405, 124441. doi:10.1016/j.jhazmat.2020.124441
Das, A. K., and Singh, D. (2021). Evaluation of fatigue performance of asphalt mastics composed of nano hydrated lime filler. Constr. Build. Mater. 269, 121322. doi:10.1016/j.conbuildmat.2020.121322
Gong, X., Liu, Q., Wang, H., Wan, P., Chen, S., Wu, J., et al. (2023). Synthesis of environmental-curable CO2-based polyurethane and its enhancement on properties of asphalt binder. J. Clean. Prod. 384, 135576. doi:10.1016/j.jclepro.2022.135576
Habibnejad Korayem, A., Ziari, H., Hajiloo, M., Abarghooie, M., and Karimi, P. (2020). Laboratory evaluation of stone mastic asphalt containing amorphous carbon powder as filler material. Constr. Build. Mater. 243, 118280. doi:10.1016/j.conbuildmat.2020.118280
Jia, Y., Yang, Y., Zhou, T., Gao, Y., Wang, S., and Wei, Z. (2022). Stiffening effect of filler on asphalt mastic composite: a new insight based on nearest surface function. Constr. Build. Mater. 344, 128177. doi:10.1016/j.conbuildmat.2022.128177
Li, G., Chen, X., Zhang, Y., Zhuang, Z., and Lv, Y. (2023). Studies of nano-SiO2 and subsequent water curing on enhancing the frost resistance of autoclaved PHC pipe pile concrete. J. Build. Eng. 69, 106209. doi:10.1016/j.jobe.2023.106209
Li, J., Cao, Y., Sha, A., Song, R., Li, C., and Wang, Z. (2022a). Prospective application of coal gangue as filler in fracture-healing behavior of asphalt mixture. J. Clean. Prod. 373, 133738. doi:10.1016/j.jclepro.2022.133738
Li, J., Yu, J., Wu, S., and Xie, J. (2022b). The mechanical resistance of asphalt mixture with steel slag to deformation and skid degradation based on laboratory accelerated heavy loading test. Mater. Basel 15. doi:10.3390/ma15030911
Li, L., Yang, C., and Li, J. (2021). Corrosion initiation life of laterally loaded PHC pipe piles served in marine environment: theoretical prediction and analysis. Constr. Build. Mater. 293, 123457. doi:10.1016/j.conbuildmat.2021.123457
Liu, J., Wang, Z., Jia, H., Jing, H., Chen, H., Zhou, L., et al. (2023a). Characteristics and properties of asphalt mortar containing FO filler. Constr. Build. Mater. 392, 132039. doi:10.1016/j.conbuildmat.2023.132039
Liu, N., Liu, L., Li, M., and Sun, L. (2023b). Effects of zeolite on rheological properties of asphalt materials and asphalt-filler interaction ability. Constr. Build. Mater. 382, 131300. doi:10.1016/j.conbuildmat.2023.131300
Liu, X., Zhang, M., Shao, L., and Chen, Z. (2018). Effect of volcanic ash filler on thermal viscoelastic property of SBS modified asphalt mastic. Constr. Build. Mater. 190, 495–507. doi:10.1016/j.conbuildmat.2018.09.101
Liu, Z., Bu, L., Wang, Z., and Hu, G. (2019). Durability and microstructure of steam cured and autoclaved PHC pipe piles. Constr. Build. Mater. 209, 679–689. doi:10.1016/j.conbuildmat.2019.03.166
Lv, Y., Wu, S., Li, N., Cui, P., Wang, H., Amirkhanian, S., et al. (2023). Performance and VOCs emission inhibition of environmentally friendly rubber modified asphalt with UiO-66 MOFs. J. Clean. Prod. 385, 135633. doi:10.1016/j.jclepro.2022.135633
Meng, Y., Lai, J., Mo, S., Fang, G., Deng, S., Wei, X., et al. (2023). Investigating the deterioration mechanism of adhesion between asphalt and aggregate interface under acid rain erosion. Appl. Surf. Sci. 639, 158171. doi:10.1016/j.apsusc.2023.158171
Osuolale, O. M., Arinkoola, A. O., and Olawuyi, O. A. (2023). Performance evaluation of bamboo leaf ash and steel slag powder as alternative filler in asphaltic mixes. J. Eng. Res., 100117. doi:10.1016/j.jer.2023.100117
Ou, L., Li, R., Zhu, H., Zhao, H., and Chen, R. (2023). Upcycling waste phosphogypsum as an alternative filler for asphalt pavement. J. Clean. Prod. 420, 138332. doi:10.1016/j.jclepro.2023.138332
Paul, D., Suresh, M., and Pal, M. (2021). Utilization of fly ash and glass powder as fillers in steel slag asphalt mixtures. Case Stud. Constr. Mater. 15, e00672. doi:10.1016/j.cscm.2021.e00672
Russo, F., Veropalumbo, R., Pontoni, L., Oreto, C., Biancardo, S. A., Viscione, N., et al. (2022). Sustainable asphalt mastics made up recycling waste as filler. J. Environ. Manag. 301, 113826. doi:10.1016/j.jenvman.2021.113826
Sua-Iam, G., and Makul, N. (2023). Recycling prestressed concrete pile waste to produce green self-compacting concrete. J. Mater. Res. Technol. 24, 4587–4600. doi:10.1016/j.jmrt.2023.04.101
Sun, X., Ou, Z., Zhao, T., Qin, X., Jin, J., Yu, H., et al. (2023). Interaction state and element leaching of waste incineration fly ash-asphalt mortar based on fillerization. Constr. Build. Mater. 398, 132463. doi:10.1016/j.conbuildmat.2023.132463
Taherkhani, H., and Vahabi Kamsari, S. (2020). Evaluating the properties of zinc production wastes as filler and their effects on asphalt mastic. Constr. Build. Mater. 265, 120748. doi:10.1016/j.conbuildmat.2020.120748
Wei, Z., Jia, Y., Wang, S., Li, Z., Li, Y., Wang, X., et al. (2022). Utilization of iron ore tailing as an alternative mineral filler in asphalt mastic: high-temperature performance and environmental aspects. J. Clean. Prod. 335, 130318. doi:10.1016/j.jclepro.2021.130318
Xie, J., Chen, J., Hu, L., Wu, S., Wang, Z., Li, M., et al. (2023). Preparation, thermochromic properties and temperature controlling ability of novel pellets in ultra-thin wearing course. Constr. Build. Mater. 389, 131797. doi:10.1016/j.conbuildmat.2023.131797
Xing, B., Fan, W., Zhuang, C., Qian, C., and Lv, X. (2019). Effects of the morphological characteristics of mineral powder fillers on the rheological properties of asphalt mastics at high and medium temperatures. Powder Technol. 348, 33–42. doi:10.1016/j.powtec.2019.03.014
Yang, B., Li, H., Zhang, H., Sun, L., Harvey, J., Tian, Y., et al. (2021). Environmental impact of solid waste filler in porous asphalt mixture. Constr. Build. Mater. 303, 124447. doi:10.1016/j.conbuildmat.2021.124447
Yang, C., Wu, S., Cui, P., Amirkhanian, S., Zhao, Z., Wang, F., et al. (2022). Performance characterization and enhancement mechanism of recycled asphalt mixtures involving high RAP content and steel slag. J. Clean. Prod. 336, 130484. doi:10.1016/j.jclepro.2022.130484
Yang, C., Wu, S., Xie, J., Amirkhanian, S., Zhao, Z., Xu, H., et al. (2023). Development of blending model for RAP and virgin asphalt in recycled asphalt mixtures via a micron-Fe3O4 tracer. J. Clean. Prod. 383, 135407. doi:10.1016/j.jclepro.2022.135407
Yu, J.-L., Zhou, J.-J., Gong, X.-N., and Zhang, R.-H. (2021). Shaft capacity of prestressed high strength concrete (PHC) pile-cemented soil column embedded in clayey soil. Soils Found. 61, 1086–1098. doi:10.1016/j.sandf.2021.05.006
Zhang, J., Li, P., Liang, M., Jiang, H., Yao, Z., Zhang, X., et al. (2020). Utilization of red mud as an alternative mineral filler in asphalt mastics to replace natural limestone powder. Constr. Build. Mater. 237, 117821. doi:10.1016/j.conbuildmat.2019.117821
Zhang, J., Liu, S., Yao, Z., Wu, S., Jiang, H., Liang, M., et al. (2018). Environmental aspects and pavement properties of red mud waste as the replacement of mineral filler in asphalt mixture. Constr. Build. Mater. 180, 605–613. doi:10.1016/j.conbuildmat.2018.05.268
Keywords: PHC pile waste concrete, filler, particle characteristics, asphalt concrete, road performance
Citation: Tu B, Yang X, Xu S, Zhao Z, Zhou Y, Jiang J, Fan L and Tu L (2023) Road performance evaluation of prestressed high-strength concrete pile waste powder as alternative filler in asphalt concrete. Front. Energy Res. 11:1314242. doi: 10.3389/fenrg.2023.1314242
Received: 10 October 2023; Accepted: 31 October 2023;
Published: 10 November 2023.
Edited by:
Meng Jia, Shandong University of Science and Technology, ChinaReviewed by:
Fan Zhang, Aalto University, FinlandWentong Wang, Shandong University of Science and Technology, China
Copyright © 2023 Tu, Yang, Xu, Zhao, Zhou, Jiang, Fan and Tu. This is an open-access article distributed under the terms of the Creative Commons Attribution License (CC BY). The use, distribution or reproduction in other forums is permitted, provided the original author(s) and the copyright owner(s) are credited and that the original publication in this journal is cited, in accordance with accepted academic practice. No use, distribution or reproduction is permitted which does not comply with these terms.
*Correspondence: Xinkui Yang, eWFuZ3hrQHdodXQuZWR1LmNu