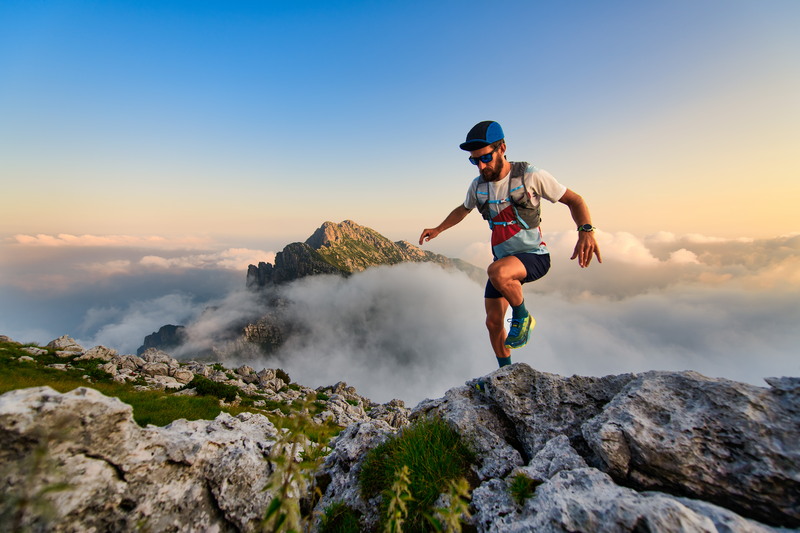
94% of researchers rate our articles as excellent or good
Learn more about the work of our research integrity team to safeguard the quality of each article we publish.
Find out more
BRIEF RESEARCH REPORT article
Front. Energy Res. , 14 November 2023
Sec. Advanced Clean Fuel Technologies
Volume 11 - 2023 | https://doi.org/10.3389/fenrg.2023.1270607
In recent years, field test and industrialized application of ASP (alkaline/surfactant/polymer) flooding has been carried out in oilfields, which has obtained an obvious effect on increasing oil and decreasing water and good economic efficiency. However, due to the large proportion of alkali in the ASP flooding system, there are problems such as severe scaling and high cost during field tests, which restrict the promotion of ASP flooding. In order to reduce the amount of alkali used, achieve the goal of reducing scaling and costs, and meanwhile improve emulsification performance while maintaining interfacial activity, a multicomponent emulsion flooding system was developed by combining emulsifier HEFR2 with petroleum sulfonate and sacrificial agent LSCP1 with NaOH.Through laboratory experiments, the water extraction rate, particle diameter, Tsi value, and interfacial activity of the multicomponent emulsion flooding system were tested under different conditions. The results show that when the mass ratio of petroleum sulfonate to emulsifier HEFR2 is between 3:1 and 5:1, and the mass ratio of sacrificial agent LSCP1 to NaOH is between 3:1 and 7:1, the multicomponent emulsion flooding system can maintain good emulsification stability and interfacial activity. The multicomponent emulsion flooding system significantly reduces the amount of alkali used, and the cost of chemical agents is 11% lower than that of the ASP flooding system. At the same time, it achieves the goal of improving the stability of emulsifiers, maintains interfacial activity and reduces costs. This technology has broad application prospects.
ASP flooding increases the oil recovery by about 20% (Guo et al., 2022). Nevertheless, the existence of alkali causes serious scaling (Hui et al., 2021; Cheng, 2022). At the same time, the production cost of ASP flooding is relatively high (Wu, 2020; Wang et al., 2022a). For this reason, NaCO3 replaces NaOH to form a weak alkali ASP flooding system (Hong et al., 2021; Jiang, 2022). However, many block tests have proved that its recovery rate is about 3% lower than that of strong alkali ASP flooding (Dong, 2020), and the scale is still serious (Cui et al., 2020; Xu et al., 2022). At the same time, a large amount of research work has been carried out on SP (polymer, surfactant) flooding (Bai et al., 2023). There are some problems, such as a decrease in oil recovery of about 4% (Zuo et al., 2023), a large amount of surfactant usage (Song et al., 2023), high performance requirements for surfactants (Zhou et al., 2023).
The research results indicate that the more stable the emulsion, the better the oil displacement effect (Cheng et al., 2023; Xu et al., 2023). Studies have shown that emulsified systems can improve oil recovery by 5–10 percentage points, compared to non-emulsified systems (Yan et al., 2023), and emulsification has a greater impact on oil displacement than interfacial tension and viscosity control (Wang et al., 2022b; Su et al., 2022). Compared with ultra-low interfacial tensionemulsification effect occupies the main part for improving oil recovery (Wu, 2017). The main reason is that the emulsion plays a role in profile control and water plugging and the carrying effect (Wang et al., 2012). During the migration process, stable emulsions can extract crude oil through emulsified carrying (Chen et al., 2023). Therefore, improving emulsification is the key to improving oil recovery (Li et al., 2020). Based on the above understanding, a chemical agent HEFR2 (a non ionic surfactant with strong emulsification effect) was added to the oil displacement system. The emulsification ability of the oil displacement system has been improved by compounding the surfactant petroleum sulfonate with HEFR2. In order to reduce the scaling hazards caused by NaOH, the proportion of NaOH was significantly reduced. At the same time, a chemical agent LSCP1 (a sacrificial agent) was added to the oil displacement system, resulting in the development of a multicomponent emulsion oil displacement system. Research has shown that the stability of emulsions is closely related to their oil displacement ability (Zhao et al., 2023). Currently, there are several methods for studying the stability of emulsions in the laboratory (Zhang et al., 2023): the method of measuring the water extraction rate through reagent bottles (Wang et al., 2022c), the method of directly observing the particle diameter of emulsions through a microscope (Qu et al., 2021), and the method of calculating the stability of emulsions through a stability analyzer (Liu et al., 2019). The bottle test method evaluates the stability of the emulsion by observing its water release rate (the percentage of the volume of water separated to the total volume) (Lu et al., 2022). The higher the water extraction rate, the poorer the stability of the emulsion (Wang et al., 2022d). The bottle test method has the advantages of simple operation and no need for other specialized instruments (Yang et al., 2017). Research has shown that the larger the diameter of droplets in an emulsion, the more likely it is to aggregate and merge, resulting in poorer stability of the emulsion. Conversely, the better the stability of the emulsion (Ren et al., 2021). Therefore, biological fluorescence microscopy is commonly used in laboratories to directly observe the droplet size of emulsions, which is a convenient and fast method (Zhou et al., 2017). The Turboscan Lab stability analyzer uses a pulsed near-infrared light source to reflect the stability of the emulsion by measuring the differences in light transmission and scattering of the water layer, oil layer, and emulsion layer (Liu et al., 2022). The stability analyzer can timely and accurately monitor the separation process inside the emulsion and reduce the influence of human factors (Wang et al., 2018; He et al., 2021).
This article mainly aims to achieve the following objectives: (1) Study the emulsification stability and interfacial activity; (2) Find the optimal mass ratio between petroleum sulfonates and HEFR2, as well as between LSCP1 and NaOH; (3) Evaluate and compare the chemical agent costs to the ASP flooding system.
Experimental materials: The polymer was hydrolyzed polyacrylamide with relative molecular weight of 19 million (Daqing Refining and Chemical Company); The surfactant is petroleum sulfonate with effective concentration of 50% (Daqing Refining and Chemical Company); The alkali is NaOH (analytical reagent); The sacrificial agent was LSCP1(Jinzhou Quanrui Reagent Co., Ltd.); The emulsifier is HEFR2 (Daqing Kaipu Chemical Company); Experimental oil: It is degassed and dehydrated crude oil at the oil station of Block W in D Oilfield, with a viscosity of 9.9 mPa·s, a density of 851 kg/m3 and a wax content of 17.8% at 45°C.
Experimental oil: It is degassed and dehydrated crude oil at the combined station of Block W in Daqing Oilfield, with a viscosity of 9.9 mPa·s, a density of 851 kg/m3 and a wax content of 17.8% at 45°C. Experimental water: the emulsion was made of clean water, and the sewage used for diluting chemicals was injected into Daqing oilfield with a salinity of 6099.46 mg/L, The mineralization degree of water in the simulated formation is 6778 mg/L.
Experimental equipment: Turbiscan Lab Expert stability analyzer (French Formulaction Company), Axiostar Plus bioluminescence microscope (Germany Jenoptik Company, magnification 1000 times), PT-3000 Homogenizer (Shanghai Huayan Instrument Equipment Company.), DE-100LA high-speed shear dispersion emulsifying machine (Nantong Clare Company), HWY-10 multi-functional cycle constant temperature water bath (Zhengzhou North and South Instrument Company), TX-500C interfacial tensiometer (Kono Industries, United States of America), Magnetic stirrer, electric stirrer, electronic balance (sensitivity 0.1 mg).
At an experimental temperature of 45°C, the fixed polymer concentration was 2000 mg/L. According to the following conditions, the multi-component emulsion flooding system was prepared, and then it was mixed with crude oil in a 9:1 mass ratio, and a high-speed shear emulsification machine was used, It maintained a shear rate of 3000r/min and a shear time of 30min to prepare an emulsion.
1) LSCP1 and NaOH were mixed in a 5:1 mass ratio, with a concentration of 1.2%. Petroleum sulfonates and emulsifier HEFR2 were mixed in a 2:1, 3:1, 4:1, 5:1, 6:1 mass ratio, with a concentration of 0.3%.
2) petroleum sulfonate and emulsifier HEFR2 were mixed in a 4:1 mass ratio with a concentration of 0.3%. The sacrificial agent LSCP1 and NaOH were mixed in a mass ratio of 1:1, 3:1, 5:1, 7:1, and 9:1, respectively, with a concentration of 1.2%.
Take 50 mL of the prepared emulsion, place it in a constant temperature water bath at 45°C, record the changes in the liquid level of the emulsion during the experiment, and observe the amount of water precipitated below the emulsion at regular intervals until the volume of oil and water no longer changes. Calculate the water release rate according to formula (1). The higher the water extraction rate is, the more unstable the emulsion is.
In the formula: qw is the water evolution rate of the emulsion within a certain period of time, %;Vw is the volume of emulsion effluent, mL;Vo is the total volume of water in the emulsion, mL.
Pour the prepared emulsion into a preheated test tube, place it in a 45°C constant temperature oven, and use a dropper to quickly suck out the emulsion at regular times. Drop it onto a glass slide, and then place it on a stage. Adjust the aperture level of the microscope and control the accuracy knob to make the droplets clear in the field of view; To ensure the accuracy of the data, the number of droplets measured in each group should be greater than 50, followed by image processing and statistical analysis of particle diameters of different sizes.
Using a Turboscan Lab Expert stability analyzer, the intensity of backscattered light in the emulsion was recorded over time. At the same time, the Turboscan Easysoft data processing software of the stability analyzer was used to calculate the intensity changes of backscattered light in different parts of the emulsion. According to formula (2), the stability parameter Tsi of the emulsion and the migration rate of the droplet were calculated (Huang et al., 2016). During the experiment, the incident wavelength was tested at 800 nm, The scanning time interval is 45 s, the scanning time is 2 h, and the testing temperature is all 45°C.
In the formula, Tsi is the stability coefficient, Xi is the average value of the backscattered light intensity for each scan of the instrument,Xbs is the average value of xi,n is the number of scans.
At an experimental temperature of 45°C, the polymer concentration was uniformly 2000 mg/L. Petroleum sulfonate and HEFR2 were mixed in a 4:1 mass ratio, with mixture concentrations of 0.05%, 0.1%, 0.2%, and 0.3%, respectively. LSCP1 and NaOH were mixed in a 1:1, 3:1, 5:1, 7:1, and 9:1 mass ratio, with mixture concentrations of 0.4%, 0.6%, 0.8%, 1.0%, 1.2%, and 1.4%, respectively. The multicomponent composite system was mixed with crude oil in a 9:1 mass ratio, and a high-speed shear emulsification machine was used, It maintained a shear rate of 3000 r/min and a shear time of 30 min to prepare an emulsion. Measure the interfacial tension of the emulsions prepared under different conditions and create interfacial activity diagrams.
Figure 1 shows a photo of the water extraction of the emulsion at 3 h under different mass ratios. It can be seen that as the mass ratio of petroleum sulfonate to emulsifier HEFR2 increases, the color of the emulsion in the test tube gradually becomes lighter, and the oil-water interface becomes clearer, indicating that the stability of the emulsion gradually weakens. That is to say, the water release rate will increase with the decrease in the mass of emulsifier HEFR2. When the mass ratio of petroleum sulfonate to emulsifier HEFR2 is 2:1 at 3 h, the water extraction rate is less than 5%. When the mass ratio is 3:1, the water extraction rate is less than 10%. When the mass ratio is 4:1, the water extraction rate is less than 15%. When the mass ratio is 5:1, the water extraction rate is less than 25%; When the mass ratio is 6:1, the water extraction rate significantly increases, and the water extraction rate has exceeded 35% after 3 h. The water extraction rate with a 2:1 mass ratio of petroleum sulfonate and HEFR2 is 45.5%, while the water extraction rate with a mass ratio of 6:1 reaches 69.8%, with a difference of 24.3% between the two. The smaller the mass ratio of surfactant to HEFR2, the lower the water precipitation rate and better the emulsification effect when the mass ratio of emulsifier HEFR2 is large; The main reason is that when the mass of HEFR2 is high, it shows strong hydrophilicity. When the oil and water just contact, HEFR2 will quickly diffuse to the oil-water interface layer and adsorb on it. Together with petroleum sulfonate, it is closely arranged on the oil-water interface, increasing the strength of the interface facial mask.
FIGURE 1. Water extraction rate under different ratio of surfactant to HERF2. (A) Water extraction rate changing curve. (B) Picture of emulsions under different ratio.
When the mass of HEFR2 is small, the water separation rate increases significantly, and the stability of the emulsion becomes poor. The reason is that the quality of HEFR2 is small, which makes it impossible to fully contact the oil-water system, weakens the strength of the interfacial facial mask, and makes small droplets of the emulsion easy to gather and merge into larger droplets, thus destroying the stability of the emulsion. At the same time, the surfactant molecules adsorbed on the oil-water interface reach saturation, and the HEFR2 molecules in the oil phase will diffuse towards the water phase, increasing the oil-water separation rate and damaging the stability of the emulsion. Therefore, when the mass ratio of petroleum sulfonates to HEFR2 is 6:1, the water evolution rate significantly increases. When the mass ratio of surfactant to HEFR2 is between 2:1 and 5:1, the water evolution rate is lower than 25%, which is at a lower level; Therefore, the reasonable mass ratio range of surfactant to HEFR2 is determined to be between 2:1 and 5:1.
The stability coefficient of the surfactant and HEFR2 under different mass ratios varies with time, as shown in Figure 2. It can be seen that as the mass of emulsifier HEFR2 increases, the Tsi value decreases, and the emulsification stability of the multicomponent composite oil displacement system increases. When the mass ratio of surfactant to HEFR2 is 6:1, the Tsi value reaches the highest value of 15.2 at 90 min. When the mass ratio of surfactant to HEFR2 is 5:1, the Tsi value at 90 min is 10.4, a decrease of 31.58% compared to 6:1. When the mass ratio of surfactant to HEFR2 is 4:1, 3:1, and 2:1, respectively, the Tsi value at 90 min is between 8.6 and 9.6, which is relatively close. The decrease is 36.8%–43.5% compared to the mass ratio of surfactant to HEFR2 at 6:1, indicating that when the mass ratio of petroleum sulfonate to emulsifier HEFR2 reaches 3:1, the proportion of emulsifier HEFR2 is further increased, and the change in Tsi value is very small, indicating that the emulsification stability of the system tends to be stable.
FIGURE 2. Tsi curves and the percentage of particle diameters. (A) Tsi curves. (B) The percentage of particle diameters.
According to the research results, the smaller the average particle size of the emulsion, the more stable the emulsion is. When different mass ratios of surfactant and emulsifier HEFR2 are used, the proportion of different particle sizes in the emulsion is shown in Figure 2. The droplet photo of the emulsion at 30 min is shown in Figure 3.
From Figure 2, it can be seen that when the mass ratio of surfactant to emulsifier HEFR2 is 3:1, the proportion of small particles with particle diameters below 15 um in the emulsion is 42.8%, and the proportion of large particles with particle diameters above 30 um is 23.4%. From Figure 3, it can also be seen that the particle distribution in its emulsion is relatively uniform, with fewer particles with larger diameters.
When the mass of emulsifier HEFR2 continues to be increased until the mass ratio of surfactant to emulsifier HEFR2 reaches 2:1, the proportion of small particles with particle diameters below 15 um in the emulsion is 43.2%, and the proportion of large particles with particle diameters above 30 um is 22.6%. Compared with the mass ratio of surfactant to HEFR2 at 3:1, the proportion of small particles increases by only 0.4%, and the proportion of large particles decreases by only 0.8%, with little change. Corresponding to Figure 3, it can be seen that the average particle diameter of emulsion droplets slightly decreases, and the number of droplets with larger particle diameters slightly decreases. Overall, there is little change compared to the mass ratio of surfactant to emulsifier HEFR2 at 3:1. Explanation 3:1 is the critical point for the mass ratio of surfactant to emulsifier HEFR2. At this point, increasing the mass of emulsifier HEFR2 will not significantly increase the stability of the emulsion.
When the mass of emulsifier HEFR2 is reduced until the mass ratio of surfactant to emulsifier HEFR2 reaches 5:1, the proportion of small particles with a diameter below 15um in the emulsion is 39.5%, and the proportion of large particles with a diameter above 30um is 28.8%. When the mass ratio of the same surfactant to HEFR2 is 3:1, the proportion of small particles decreased by only 3.3%, while the proportion of large particles increased by only 5.4%, with little change. Corresponding to Figure 3, it can be seen that the distribution of emulsion droplets is relatively uniform, and the number of droplets with large particle diameters is still relatively small. This indicates that when the mass ratio of surfactant to emulsifier HEFR2 is between 3:1 and 5:1, the emulsion is relatively stable.
When the mass of emulsifier HEFR2 continues to be reduced until the mass ratio of surfactant to emulsifier HEFR2 reaches 6:1, the proportion of small particles with particle diameters below 15um in the emulsion decreases to 21.8%, and the proportion of large particles with particle diameters above 30um increases to 51.3%; Compared with the mass ratio of surfactant to HEFR2 at 5:1, the proportion of small particles decreased significantly by 17.7%, while the proportion of large particles increased significantly by 22.5%, showing a significant change. Corresponding to Figure 3, it can be seen that the particle diameter of its emulsion droplets has significantly increased overall, and the distribution has become uneven, with a significant increase in the number of droplets with large particle diameters. Explanation 5:1 is the critical point for the mass ratio of surfactant to emulsifier HEFR2. Continuing to reduce the mass of emulsifier HEFR2 at this point will significantly decrease the stability of the emulsion. Therefore, when the mass ratio of surfactant to emulsifier HEFR2 is between 3:1 and 5:1, the emulsion can remain stable.
When the mass ratio of surfactant to HEFR2 is 2:1, the interfacial tension value ranges from 1.362 × 10-2 mN/m, the interface tension slowly decreases to 1.032 × 10-2 mN/m, never reaching ultra-low interfacial tension. As the proportion of surfactants increases, the interfacial tension decreases significantly. When the mass ratio of surfactant to HEFR2 is between 3:1 and 6:1, the interfacial tension decreases to the order of 10–3 mN/m after 15 min, and it basically reaches dynamic equilibrium after about 30 min.
Through comprehensive analysis of experimental data such as water precipitation rate, particle diameter size observed under a microscope, stability coefficient Tsi, and interfacial tension, the test results were basically consistent. When the mass ratio of surfactant to HEFR2 is 6:1, the water evolution rate, stability coefficient Tsi, and average particle diameter of the emulsion system all increase, and the stability of the emulsion system deteriorates; When the mass ratio of surfactant to HEFR2 is 2:1, the interfacial activity decreases significantly; When the mass ratio of surfactant to HEFR2 is between 3:1 and 5:1, the water evolution rate, stability coefficient Tsi, and average particle diameter of the emulsion change very little. This indicates that when the mass ratio of petroleum sulfonate to emulsifier HEFR2 is between 3:1 and 5:1, the emulsion can maintain good emulsification stability and interfacial activity.
Maintain the mass ratio of surfactant to HEFR2 at 3:1, the concentration of the mixture at 0.3%, and the polymer concentration at 2000 mg/L. Change the mass ratio of LSCP1 to NaOH between 1:1 and 9:1. When the mass ratio of LSCP1 to NaOH is between 3:1 and 7:1, as the proportion of LSCP1 continues to increase, the proportion of NaOH continues to decrease, the water extraction rate decreases, the average particle size of the emulsion gradually decreases, and Tsi decreases.
When the mass ratio of LSCP1 to NaOH is 7:1, the water extraction rate reaches the lowest value of 49.81%, the average particle size reaches the lowest value of 13.6, and the stability coefficient Tsi reaches the lowest value of 8.1; At the same time, the water extraction rate remains below 50%, and the average particle diameter of the emulsion remains at 15 μm Below, Tsi remains below 10, both at relatively low levels, indicating that the emulsion is relatively stable in this range.
When the mass ratio of LSCP1 to NaOH reaches 9:1, the water extraction rate significantly increases, reaching a maximum of 55.29%. The average particle diameter of the emulsion also increases, and the stability coefficient Tsi increases to 12.7. The overall stability of the emulsion decreases, indicating that a low NaOH content is not conducive to the stability of the emulsion.
When the mass ratio of LSCP1 to NaOH is 1:1, the water extraction rate significantly increases, reaching 53.62%. The average particle diameter of the emulsion also increases, and the stability coefficient Tsi increases to 9.4. The stability of the emulsion decreases, indicating that high NaOH content is not conducive to the stability of the emulsion.
The main reason for this situation is that when the mass of the NaOH is too large, it will reduce the overall viscosity of the system, increase the ion concentration of the emulsion system, compress the double electron layer on the surface of the droplet, increase the collision probability of the emulsion, accelerate the stratification, aggregation, and merging of the emulsion, and increase the particle size of the emulsion. The combination of these effects reduces the stability of the emulsion system. At the same time, when the quality of alkali is too low, a small amount of alkali cannot generate surface active substances with crude oil, which is not conducive to improving the stability of the emulsion.
Based on the comprehensive experimental data, it can be concluded that as the mass ratio of LSCP1 to NaOH changes, adding too much or too little NaOH is not conducive to the stability of the emulsion. When the mass ratio of LSCP1 to NaOH is between 3:1 and 7:1, the stability of the emulsion is better.
Figure 4 shows the interfacial activity diagram of the multicomponent composite oil displacement system under different mass ratios of LSCP1 and NaOH.It can be seen that when the mass ratio of LSCP1 to NaOH is 3:1, the ultra-low interfacial activity range of the composite oil displacement system is the widest. Only when the mixed concentration of LSCP1 and NaOH is less than 0.6%, the ultra-low interfacial tension cannot be achieved. When the mass ratio of LSCP1 to NaOH reaches 1: 1, although the content of NaOH increases, the range of ultra-low interfacial tension decreases. This indicates that an excessive amount of NaOH added is actually detrimental to maintaining interfacial activity.
When the mass ratio of LSCP1 to NaOH is 9:1, the interfacial tension can only decrease to below 10−3 mN/m when the mixture concentration of the two is close to 1.2%, and the mixture concentration of surfactant and HEFR2 exceeds 0.1%.This indicates that the interfacial activity decreases with the NaOH content decreases.
Through the above experiments, it can be seen that adding too much or too little NaOH has a negative impact on the interfacial activity. When the mass ratio of LSCP1 to NaOH is between 3:1 and 7:1, it exhibits good interfacial activity. The reason is that when the content of NaOH is too high, it will cause the PH value of the displacement fluid to be too high, which will accelerate the decomposition of surface active components and weaken the interfacial activity of the displacement system; On the contrary, if the content of NaOH is too low, it cannot generate surface active substances with crude oil, which is not conducive to maintaining interfacial activity.
Based on a comprehensive consideration of the ratio and price of chemical agents, a preliminary cost analysis was conducted. The prices of chemical agents are calculated using industrial product prices, with the price of LSCP1 per ton being 23% of the price of NaOH and HEFR2 per ton being 97% of the price of petroleum sulfonates. Through preliminary calculation, the chemical agent cost of ASP flooding is 213 yuan/t. When the mass ratio of LSCP1 to NaOH is 3:1, and the mass ratio of surfactant petroleum sulfonate to emulsifier HEFR2 is 5:1, the chemical agent cost of the multi component composite emulsion flooding system is 189 yuan/t, which is 11.26% lower than ASP flooding. When the mass ratio of LSCP1 to NaOH is 7:1, and the mass ratio of surfactant petroleum sulfonate to emulsifier HEFR2 is 3:1, the chemical agent cost of the multicomponent composite emulsion flooding system is 176 yuan/t, which is 17.37% lower than ASP flooding. At the same time, the use of alkali has been significantly reduced in the multi element composite emulsion oil displacement system, which will reduce scaling problems, reduce production management difficulties, reduce maintenance costs, and improve hidden economic benefits in the actual production process.
1) By adding sacrificial agent LSCP1 and emulsifier HEFR2, the emulsification performance of the oil displacement system can be improved, interfacial activity can be maintained, and the use of NaOH can be significantly reduced.
2) When the mass ratio of petroleum sulfonate to emulsifier HEFR2 is between 3:1 and 5:1, and the mass ratio of sacrificial agent LSCP1 to NaOH is between 3:1 and 7:1, the multi component composite emulsion oil displacement system can maintain good emulsification stability and interfacial activity.
3) The cost of the multi component composite emulsion flooding system has decreased by more than 11% compared to ASP flooding (Wang et al., 2020).
The original contributions presented in the study are included in the article/supplementary material, further inquiries can be directed to the corresponding authors.
MZ: Writing original draft—review and editing. WW: Editing.
This work was supported by the School of Petroleum Engineering, Northeast Petroleum University and No. 1 Oil Production Plant of Daqing Oilfield.
Author MZ was employed by PetroChina Daqing Oilfield Company.
The remaining authors declare that the research was conducted in the absence of any commercial or financial relationships that could be construed as a potential conflict of interest.
All claims expressed in this article are solely those of the authors and do not necessarily represent those of their affiliated organizations, or those of the publisher, the editors and the reviewers. Any product that may be evaluated in this article, or claim that may be made by its manufacturer, is not guaranteed or endorsed by the publisher.
Bai, M., Wu, W., Zhang, Z., and Lu, L. (2023). Research on parameter optimization of polymer-surfactant binary compound flooding in conglomerate reservoirs. Contemp. Chem. Ind. 52 (5), 1248–1251.
Chen, Y., Li, X., Zhang, M., Chang, X., and Wu, Y. (2023). Experimental study on factors affecting emulsification and demulsification of oil-in-water emulsion. Contemp. Chem. Ind. 52 (5), 1103–1120. (in Chinese). doi:10.3969/j.issn.1671-0460.2023.05.021
Cheng, J. (2022). Progress of key technologies of ternary compound scaling control. Oil Drill. Prod. Technol. 44 (5), 540–545.
Cheng, J., Wu, J., Wu, H., Liu, X., He, J., and Jia, S. (2023). Alkali-free three-component emulsification flooding system. Acta Pet. Sin. 44 (4), 636–646. doi:10.7623/syxb202304006
Cui, C., Zhou, Z., and He, Z. (2020). Enhance oil recovery in low permeability reservoirs: optimization and evaluation of ultra-high molecular weight HPAM/phenolic weak gel system. J. Petroleum Sci. Eng. 195 (4), 107908. doi:10.1016/j.petrol.2020.107908
Dong, D. (2020). Application of sand and scale control pump with long plunger and short pump barrel in weak alkali ternary compound flooding. Petroleum Petrochem. Energy Conservation 10 (11), 4–6.
Guo, Y., Liu, J., and Jin, P. (2022). Discussion on the application timing of chemical scale removal measures in ternary composite flooding. World Pet. Ind. 29 (4), 67–70.
He, Y., Liu, Y. T., and Chai, R. K. (2021). Study on stability of crude oil emulsion based on multiple light scattering principle. J. Xi 'an Shiyou Univ. Nat. Sci. Ed. 36 (6), 30–43. (in Chinese). doi:10.3969/j.issn.1673-064X.2021.06.005
Hong, G., Yan, J., Chen, T., Ma, B., Liu, D., and Qi, L. (2021). Application of oilfield scaling and chemical descaling agents. Contemp. Chem. Ind. 50 (10), 2501–2504.
Huang, X., Wang, X., Lu, L., Liu, J., and Ming, K. (2016). Technical progress of multi-scale study on the stability of oil-water emulsion. Chem. Ind. Prog. 35 (1), 26–33.
Hui, F., Liu, Y., Lei, X., and Sun, M. (2021). Research progress of oilfield scaling and descaling methods. Energy Environ. Prot. 43 (4), 188–196.
Jiang, Z. (2022). Research on the technology of adding chemicals to prevent scaling at the injection end of weak alkali ternary composite flooding. Oil Gas Field Surf. Eng. 41 (6), 15–19.
Li, Z., Yun, Q., Tang, W., Liu, Z., Guo, Y., and Lou, Q. (2020). Phase behavior of petroleum sulfonate and the effect of its emulsification on enhanced oil recovery. Oil Field Chem. 37 (3), 468–473. doi:10.19346/j.cnki.1000-4092.2020.03.016
Liu, M., Liu, X., Wu, Y., Xie, L., Yang, H., and Zhang, B. (2019). Review of influence for stability of heavy oil-in-water emulsions. J. Liaoning Shihua Univ. 39 (4), 11–18. (in Chinese). doi:10.3969/j.issn.1672-6952.2019.04.003
Liu, Q., Leng, D., Zhao, Z., Shi, T., and Luo, N. (2022). Research on the stability of crude oil emulsion containing polymer by multiple light scattering method. Oil Gas Field Surf. Eng. 41 (11), 41–44. (in Chinese). doi:10.3969/j.issn.1006-6896.2022.11.008
Lu, C., Zhao, Y., Zhao, C., Li, L., and Jin, H. (2022). Gaoqing River. Study on statistical model of oil-water separation of crude oil emulsion in NaCl ASP flooding. Petrochem. Ind. 51 (10), 1203–1210. (in Chinese). doi:10.3969/j.issn.1000-8144.2022.10.009
Qu, H., Wu, Q., Zhang, G., Wang, H., and Dai, Q. (2021). Progress of effects on crude oil emulsification and emulsion stability and demulsification technology. Prog. Fine Petrochem. Industry 22 (6), 6–10. (in Chinese). doi:10.3969/j.issn.1009-8348.2021.06.002
Ren, X., He, L., Song, A., Yao, B., and Zhao, X. (2021). Oil emulsion particle size detection algorithm based on connected domain labeling. Comput. Appl. Softw. 38 (7), 196–201. (in Chinese). doi:10.3969/j.issn.1000-386x.2021.07.032
Song, W., Qiang, L., and Zeng, Z. (2023). Mechanism of enhanced oil reovery by surfactant in polymer-surfactant dual composite flooding. Oilfield Chem. 40 (1), 76–80. doi:10.19346/j.cnki.1000-4092.2023.01.013
Su, Y., Gen, L., Chen, Y., Zhang, L., Zhang, W., and Wang, K. (2022). Effect of emulsification degree on enhanced oil recovery of oil flooding systems. Petrochem. Ind. 51 (1), 62–68. (in Chinese). doi:10.3969/j.issn.1000-8144.2022.01.010
Wang, K., Li, G., and Zhang, B. (2018). Opposite results of emulsion stability evaluated by the TSI and the phase separation proportion. Colloids Surfaces, A. Physicochem. Eng. Aspects 558, 558402–558409. doi:10.1016/j.colsurfa.2018.08.084
Wang, K., Pi, Y., Wu, Y., and Jiao, G. (2012). Effect of emulsification Performance of ternary composite System on oil displacement. Sci. Technol. Eng. 10 (12), 2428–2431.
Wang, K., Zhang, W., Zhuang, Y., Gen, L., and Su, Y. (2020). Effect of alkali and surfactant dosage on the stability of weak base ternary system emulsion. J. Northeast Petroleum Univ. 44 (4), 48–55. (in Chinese). doi:10.3969/j.issn.2095-4107.2020.04.007
Wang, Q. J., Zhang, X. Q., Sun, X. M., Yang, X., and Pei, M. (2022c). Research progress on characterization methods for petrochemical oil-water emulsion stability. J. Environ. Sci. 13 (6), 30–38. doi:10.16803/j.carolcarrollnki
Wang, W., Wang, X., Wang, Y., Jiang, B., and Song, H. (2022a). Size-controlled, hollow and hierarchically porous Co2Ni2 alloy nanocubes for efficient oxygen reduction in microbial fuel cells. React. Chem. Eng. 7, 653–662. doi:10.1039/d1re00480h
Wang, W., Wang, X., Wang, Y., Long, B., and Song, H. (2022d). A spherical multishell hollow carbon-based catalyst with a controllable N-species content for the oxygen reduction reaction in air-breathing cathode microbial fuel cells. React. Chem. Eng. 7, 978–986. doi:10.1039/d1re00528f
Wang, W., Wang, Y., Wang, X., Long, B., and Song, H. (2022b). Engineering hollow core-shell N-C@Co/N-C catalysts with bits of Ni doping used as efficient electrocatalysts in microbial fuel cells. ACS Appl. Mater. Interfaces 14, 41912–41923. doi:10.1021/acsami.2c09230
Wu, H. (2020). Study on the effect of SY-J scale remover on the removal of scale in ternary composite oil pipeline cleaning. Chem. Eng. 34 (8), 88–89.
Wu, Z. (2017). Effects of surfactant's emulsifying capacity and interracial activity on oil displacement in low-permeability reservoir. Oilfield Chem. 34 (1), 119–125. doi:10.19346/j.cnki.1000-4092.2017.01.025
Xu, C., Zhang, H., Kang, Y., Zhang, J., Bai, Y., Zhang, J., et al. (2022). Physical plugging of lost circulation fractures at microscopic level. Fuel 317, 123477. doi:10.1016/j.fuel.2022.123477
Xu, C., Zhang, H., She, J., Jiang, G., Peng, C., and You, Z. (2023). Experimental study on fracture plugging effect of irregular-shaped lost circulation materials. Energy 276, 127544. doi:10.1016/j.energy.2023.127544
Yan, M., Dong, Y., Liu, Q., and Chen, Y. (2023). Laboratory study on enhanced oil recovery by chemical flooding with microemulsion. Contemp. Chem. Ind. 52 (5), 1212–1223. (in Chinese). doi:10.3969/j.issn.1671-0460.2023.05.041
Yang, F., Wang, Y., Zhang, L., and Zhang, L. (2017). Effects of physicochemical conditions on stability of shengli crude oil emulsion. J. Petrochem. Univ. 30 (6), 27–31.
Zhang, S., Yang, S., and Yu, C. (2023). Experimental study on stability of water-in-oil emulsion blocking agent. Tianjin Sci. Technol. 50 (4), 35–39. (in Chinese). doi:10.3969/j.issn.1006-8945.2023.04.009
Zhao, X., and Qi, L. (2023). Stability study and application progress of water-in-oil emulsions in enhanced oil recovery. Oilfield Chem. 40 (2), 363–373. (in Chinese). doi:10.19346/j.cnki.1000-4092.2023.02.027
Zhou, Q., Zhang, S., and Zhou, W. (2023). Evaluation and study of injection performance of binary system of anti-salt polymer and surfactant. Special Oil Gas Reservoirs 30 (1), 120–125.
Zhou, Z., Kang, W., Wu, R., Lin, X., and Yang, H. (2017). Stability of betaine amphiphilic polymer emulsion liquid system under high salt conditions. J. Petrochem. Univ. 30 (6), 32–36.
Keywords: emulsion flooding system, mass ratio, emulsion stability, interfacial activity, reduce costs
Citation: Zhiqiang M and Wenxiang W (2023) Research on the ratio of multicomponent emulsion flooding system. Front. Energy Res. 11:1270607. doi: 10.3389/fenrg.2023.1270607
Received: 01 August 2023; Accepted: 23 October 2023;
Published: 14 November 2023.
Edited by:
Chengyuan Xu, Southwest Petroleum University, ChinaReviewed by:
Shafirah Samsuri, University of Technology Petronas, MalaysiaCopyright © 2023 Zhiqiang and Wenxiang. This is an open-access article distributed under the terms of the Creative Commons Attribution License (CC BY). The use, distribution or reproduction in other forums is permitted, provided the original author(s) and the copyright owner(s) are credited and that the original publication in this journal is cited, in accordance with accepted academic practice. No use, distribution or reproduction is permitted which does not comply with these terms.
*Correspondence: Man Zhiqiang, bWFuXzE5MzZAMTYzLmNvbQ==; Wu Wenxiang, ZHlkZTIwMDVAMTYzLmNvbQ==
Disclaimer: All claims expressed in this article are solely those of the authors and do not necessarily represent those of their affiliated organizations, or those of the publisher, the editors and the reviewers. Any product that may be evaluated in this article or claim that may be made by its manufacturer is not guaranteed or endorsed by the publisher.
Research integrity at Frontiers
Learn more about the work of our research integrity team to safeguard the quality of each article we publish.