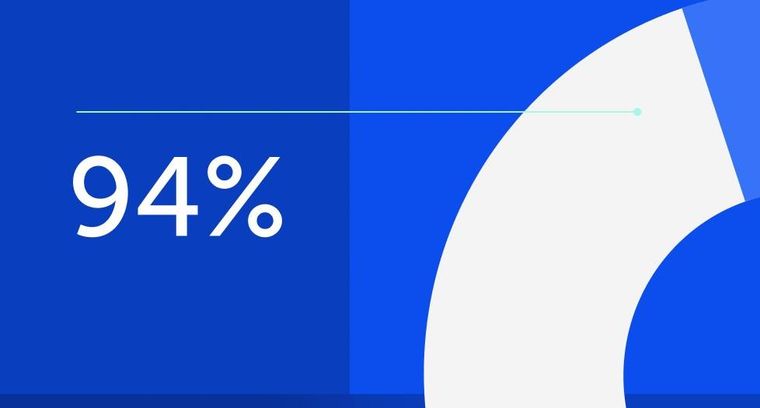
94% of researchers rate our articles as excellent or good
Learn more about the work of our research integrity team to safeguard the quality of each article we publish.
Find out more
BRIEF RESEARCH REPORT article
Front. Energy Res., 29 September 2023
Sec. Advanced Clean Fuel Technologies
Volume 11 - 2023 | https://doi.org/10.3389/fenrg.2023.1267228
This article is part of the Research TopicAdvances in Geomechanics Research and Application for Deep Unconventional ReservoirsView all 35 articles
The slide steering drilling system consisting of a bent positive displacement motor (PDM) and measurement while drilling (MWD) system is widely used to continuously implement all wellpath control operations by alternately applying the slide and compound drilling modes. Due to the large friction force on the drilling string during slide drilling in the horizontal section, there is a significant adverse impact on both the drilling speed and horizontal extension ability. To efficiently and economically drill long horizontal sections, it is essential to increase the compound drilling proportion and decrease the alternative times of the two drilling modes. According to the features of wavy or tortuous horizontal sections and wellpath calculation models, a prediction and control method for the compound drilling proportion of horizontal sections is first established, and subsequently, its influencing factors and laws are analyzed and verified using an example. Theoretical research and drilling practice have shown that the compound drilling proportion of the horizontal section depends on the build-up rate of slide drilling and the inclination and azimuth change rates of compound drilling and is independent of the target area parameters and wellpath fluctuation ratio. In order to increase the compound drilling proportion and reduce the slide drilling frequency in the horizontal section, it is necessary to increase the build-up rate of slide drilling properly and reduce the inclination and azimuth change rates of compound drilling to the greatest extent. This paper is helpful to enhance the benefit of slide steering drilling systems in horizontal wells of unconventional reservoirs.
A horizontal well is an important method to develop unconventional reservoirs, like shale gas (Guo et al., 2019; Lu et al., 2021), tight oil, gas hydrate (Zhang et al., 2022a), and even deep reservoirs (Zhang et al., 2022b; Cao et al., 2022). The slide steering drilling system composed of a bent positive displacement motor (PDM) and measurement while drilling (MWD) system is widely used in horizontal wells. This system has two working modes, namely, slide drilling mode and compound drilling mode (Samuel et al., 2005; Guan et al., 2021). By alternatively applying these two modes, it can continuously implement wellpath control operations without tripping operations. Currently, longer horizontal wells are being drilled to develop unconventional oil and gas (Guo et al., 2019; Lu et al., 2021; Yu et al., 2021; Ma et al., 2022). Because the drillstring does not rotate in the slide drilling mode, the friction force on the drillstring not only decreases the weight-on-bit transmission efficiency and causes low drilling speed but also influences the horizontal extension ability (Maidla and Haci, 2004; Samuel, 2010; Zhu et al., 2019).
Some researchers have pointed out that the actual wellpath of a horizontal section drilled by the slide steering drilling system is always in a wavy or tortuous shape, and the wellpath tortuosity influences the wellpath calculation, drag, and torque on the drillstring (Samuel et al., 2005; Samuel, 2010; Brands and Lowdon, 2012; Noshi and Schubert, 2019; Samuel et al., 2021). Some models have taken the wellpath tortuosity into account to enhance the calculation precision of the wellpath (Samuel et al., 2005; Noshi and Schubert, 2019) and the prediction precision of drag and torque on the drillstring (Samuel, 2010; Brands and Lowdon, 2012). Some researchers have realized that the wellpath tortuosity and drilling efficiency are influenced by the build-up rate of slide drilling and the inclination and azimuth change rates of compound drilling. Some models have been established to predict the build-up rate of slide drilling (Williams et al., 1989; Shi et al., 2017; Liu et al., 2019) or inclination and azimuth change rates of compound drilling (Peng and Di Qinfeng, 2000; Guo et al., 2013; Koulidis et al., 2021). Although it is well known that increasing the compound drilling proportion is the key to achieving fast and cost-effective drilling, the prediction and control method for the compound drilling proportion is still lacking.
In order to enhance the benefit of a slide steering drilling system, a prediction and control method for the compound drilling proportion of horizontal sections is established, and subsequently, its influencing factors and laws are analyzed.
As shown in Figure 1, the actual wellpath of the horizontal section drilled by a slide steering drilling system is always in a wavy or tortuous shape (Samuel et al., 2005; Noshi and Schubert, 2019). Because the inclination and azimuth commonly fluctuate slowly under compound drilling, the slide drilling must be alternated to decrease (or increase) the inclination and azimuth and control the wellpath within the target area once the drill bit is near the boundary lines of the horizontal target area. For a long horizontal section, two drilling modes may alternate multiple times. Then, the actual horizontal section has more control cycles. In one wavy cycle or control cycle, two drilling modes alternate once.
FIGURE 1. Actual wellpath of the horizontal section. (A) Vertical projection plot; (B) horizontal projection plot.
Suppose that the compound drilling tends to increase inclination and azimuth simultaneously, and then take the rectangular horizontal target area and the first wellpath control cycle as an example. The target half-width is set as a, and the target half-height is b; for the compound drilling interval, the starting point is No. 0 point, the lowest point on the vertical projection plot (the far left point on the horizontal plot) is No. 1 point, and the endpoint is No. 2 point; and for the slide drilling interval, the starting point is No. 2 point, the highest point (the far right point on the horizontal plot) is No. 3 point, and the last point is No. 4 point. To reduce the alternate times of slide and compound drilling, let the inclinations of the highest and lowest points on the vertical projection plot be equal to the target inclination and the azimuths of the far left and right points on the horizontal plot be equal to the target azimuth. All node parameters of the actual horizontal section are presupposed and shown in Figure 1. For the compound drilling interval, the key parameters include the compound drilling length
According to the wellpath calculation methods (Guan et al., 2021), the actual shapes of compound and slide drilling intervals are closest to the cylindrical spiral line and the inclined arc line, respectively. The cylindrical spiral method (curvature radius method) and inclined arc method (minimum curvature method) are applied alternatively to calculate all wellpath parameters of the actual horizontal section. According to the presupposed node parameters in Figure 1, the first wellpath control cycle from No. 0 point to No. 4 point can be divided into four intervals, and then all vertical depth increments
As shown in Figure 1, while drilling the horizontal section, the actual horizontal wellpath must be controlled within the target area, and then the actual wellpath of the horizontal section must meet the inequality constraint as follows:
or
If the designed target inclination
Considering the allowed inclination bias
From Eqs 6, 7, it can be observed that
(1) Once the target half-width a and target half-height b are given, the maximum allowed inclination bias
(2) Once the build-up rate
In one wellpath control cycle of the horizontal section, the allowed compound drilling length is
If the build-up rate
According to Eq. 9, the upper limit of the compound drilling proportion
Because the inclination change rate
According to Eq. 10, it can be observed that the compound drilling proportion of the horizontal section depends on the build-up rate
According to the actual horizontal drilling data, the target area is set at 1.0 m (target half-height) × 6.0 m (target half-width), and then the key parameters of slide and compound drilling are set as follows: the build-up rates
FIGURE 2. Compound drilling results vs. build-up rate. (A) Compound/slide drilling lengths; (B) compound drilling proportion; (C) compound/slide drilling lengths; (D) compound drilling proportion.
If the inclination change rate of compound drilling increases, the compound drilling length
Taking 1.25° bent PDM as an example, the build-up rate of slide drilling is set at 7.5°/30 m, the inclination change rate of compound drilling is set at 0.5°–1.5°/30 m, and the azimuth change rate is set at 0.3°/30 m, and then the drilling results are estimated using Eqs 7, 8 and shown in Figures 2C, D. In the legend zone, “SD” and “CD” represent “slide drilling” and “compound drilling,” respectively, but the numbers represent the inclination change rates (unit: °/30 m) of compound drilling.
If the build-up rate of slide drilling increases, the compound drilling length
The LS3-3 horizontal well is located in China. The designed horizontal section is approximately 1200 m. The target area is 1.0 m (target half-height) × 6.0 m (target half-width). Target inclination is 88.15°, and target azimuth is 161.29°. Bottom-hole assembly (BHA) and drilling parameters are described as follows: BHA: φ152.4 mm PDC bit + φ127 mm bent PDM (1.25 for the first run and 1° for the second run) + float valve + Φ148 mm stabilizer + LWD + Φ96 mm non-magnetic drill pipe. Drilling parameters: weight on bit 30 kN, top drive speed 50 r/min, and drilling fluid flowrate 18 L/s.
The statistical horizontal section length is 1,138.66 m, and the alternation time of two drilling modes is 58 in total. Wellbore curvature (dogleg severity) and inclination change rate are shown in Figure 3. For the compound drilling, the inclination mainly increases and the azimuth mainly maintains the same change rate; the average inclination and azimuth change rates are approximately 0.5°/30 m and 0.2°/30 m, respectively; the cumulative length is 1,036.9 m; the average interval length is 17.9 m/time; the maximum interval length is 66.5 m; and the compound drilling proportion is 91.1%. For slide drilling, the build-up rates are approximately 7.5°/30 m and 6.0°/30 m for the first and second runs, respectively; the cumulative length is 101.8 m; the average interval length is 1.8 m/time; the maximum interval length is 3.4 m; and the slide drilling proportion is 8.9%.
Based on the statistical results, the build-up rate of slide drilling is set at 6.0°–7.5°/30 m and the inclination and azimuth change rates of compound drilling are set at 0.5°/30 m and 0.2°/30 m, respectively; the wellbore fluctuation ratio (amplitude of fluctuation vs. target height) is set at 0.5–0.6. The drilling results of the horizontal section are estimated and shown in Table 1. Here,
Eq. 10 can estimate the compound drilling proportion. The theoretical prediction results show that the slide drilling length is approximately 11.5–15.6 m and the compound drilling length is approximately 158.8–175.5 m in one cycle. The compound drilling proportion is approximately 91.8%–93.3%. The actual drilling results show that the compound drilling length is approximately 17.9 m/time, the slide drilling length is approximately 1.77 m/time, and the compound drilling proportion is approximately 91.1%. The compound drilling proportion is in good agreement with the theoretical results, but the compound drilling and slide drilling lengths are less than the theoretical values. One reason is that the actual wellpath has a lagging effect while alternating compound or slide drilling modes (Su, 2000). Another reason is that the target half-height is only 1.0 m. As a result, the directional drilling engineer had to increase the wellpath adjustment frequency and shorten the interval lengths to avoid missing of the target.
The bottom-hole assembly and drilling parameters should be optimized totally to properly increase the build-up rate of slide drilling and reduce the inclination and azimuth change rates of compound drilling to the greatest extent. To achieve this purpose, BHA with two stabilizers (one stabilizer fixed near the drill bit and the other stabilizer fixed above the bent PDM) and medium weight-on-bit (WOB) are recommended (Peng and Di Qinfeng, 2000; Guo et al., 2013; Koulidis et al., 2021). At the same time, more attention should be paid to the formation. The lithology and mechanical properties of the pay zone also have a significant influence on drilling results (Yin et al., 2021; Zhu et al., 2021; Cao et al., 2022).
(1) The compound drilling proportion of the horizontal section is independent of the target parameters and the wellbore fluctuation amplitude but depends on the build-up rate of slide drilling and the inclination and azimuth change rates of compound drilling.
(2) The compound drilling proportion of the horizontal section can be estimated by the build-up rate of slide drilling and the inclination and azimuth change rates of compound drilling.
(3) To enhance the compound drilling proportion of the horizontal section and reduce the adjustment frequency of slide drilling, it is necessary to increase the build-up rate of slide drilling and reduce the inclination and azimuth change rates of compound drilling.
The original contributions presented in the study are included in the article/Supplementary material; further inquiries can be directed to the corresponding authors.
HC: writing–original draft. CX: writing–review and editing. KH: writing–review and editing. YG: writing–original draft. YS: writing–original draft and funding acquisition. BZ: formal analysis and writing–review and editing.
The author(s) declare that financial support was received for the research, authorship, and/or publication of this article. This study was supported by the Major Project of National Science and Technology “Development of Rotary Steerable Drilling System (2016ZX05022-002)” and Major Project of China National Petroleum Corporation “Research and application of key technologies for exploration and development of medium and high maturity continental shale oil (2019E-2605).” The funder was not involved in the study design, collection, analysis, interpretation of data, the writing of this article, or the decision to submit it for publication. This research was also sponsored by Beijing Nova Program.
Authors HC, CX, and YG were employed by the company Engineering and Technology Research Institute, CNPC Xinjiang Oilfield Company. Author KH was employed by the company Development Company, CNPC Xinjiang Oilfield Company.
The remaining authors declare that the research was conducted in the absence of any commercial or financial relationships that could be construed as a potential conflict of interest.
All claims expressed in this article are solely those of the authors and do not necessarily represent those of their affiliated organizations, or those of the publisher, the editors, and the reviewers. Any product that may be evaluated in this article, or claim that may be made by its manufacturer, is not guaranteed or endorsed by the publisher.
Brands, S., and Lowdon, R. (March 2012). Scaled tortuosity index: quantification of borehole undulations in terms of hole curvature, clearance and pipe stiffness. Proceedings of the IADC/SPE drilling conference and exhibition, San Diego, California, USA.
Cao, L., Sun, J., Zhang, B., Lu, N., and Xu, Y. (2022). Sensitivity analysis of the changing law of temperature profile in the production string of the high-pressure high temperature gas well considering the coupling relation among the gas flow friction, gas properties, temperature and pressure. Front. Phys. 10, 1050229. doi:10.3389/fphy.2022.1050229
Guan, Zhichuan, Chen, Tinggen, and Liao, Hualin (2021). Theory and Technology of drilling engineering. Singapore: Springer.
Guo, X., Li, Y., Li, J., Feng, M., and Duan, H. (2019). Discovery of fuling shale gas field and its prospects. Front. Energy 13 (2), 354–366. doi:10.1007/s11708-018-0581-z
Guo, Zonglu, Gao, Deli, and Zhang, Hui (2013). Analysis and optimization of holding-inclination capability of steerable assembly with single bend and two stabilizers. Pet. Drill. Tech. 41 (6), 19–24.
Koulidis, A., Kelessidis, V., and Ahmed, S., (May 2021). Exploitation of field drilling data with an innovative drilling simulator: highly effective simulation of rotating and sliding mode. Proceedings of the SPE/IADC Middle East drilling Technology conference and exhibition, Abu Dhabi, UAE.
Liu, H., Ma, T., Chen, P., Wang, X., and Wang, X. (2019). Mechanical behaviors of bottom hole assembly with bent-housing positive displacement motor under rotary drilling. Arabian J. Sci. Eng. 44, 6029–6043. doi:10.1007/s13369-017-2564-5
Lu, N., Zhang, B., Wang, T., and Fu, Q. (2021). Modeling research on the extreme hydraulic extension length of horizontal well: impact of formation properties, drilling bit and cutting parameters. J. Petroleum Explor. Prod. 11 (3), 1211–1222. doi:10.1007/s13202-021-01106-4
Ma, T., Liu, J., Fu, J., and Wu, B. (2022). Drilling and completion technologies of coalbed methane exploitation: an overview. Int. J. Coal Sci. Technol. 9 (1), 68. doi:10.1007/s40789-022-00540-x
Maidla, E., and Haci, M. (January 2004). Understanding torque: the key to slide-drilling directional wells. Proceedings of the IADC/SPE drilling conference, Dallas, Texas, USA.
Noshi, C. I., and Schubert, J. J. (March 2019). Calculating a tortuosity index metric using machine learning techniques, Proceedings of the SPE/IADC international drilling conference and exhibition, Hague, The Netherlands.
Peng, Guorong, and Di Qinfeng, (2000). Predication of steering ability of the slide steering assembly in compounding drilling mode. Pet. Drill. Tech. 28 (6), 4–5.
Robello, Samuel. (March 2010). Friction factors: what are they for torque, drag, vibration, bottom hole assembly and transient surge/swab analyses? Proceedings of the IADC/SPE drilling conference and exhibition, New Orleans, Louisiana, USA.
Robello, Samuel, Jonathan Dale, Lightfoot, and William, Turner. (September 2021). Mechanical and geometrical tortuosities: vanishing and appearing tortuosities. Proceedings of the SPE annual technical conference and exhibition, Dubai, UAE.
Robello, Samuel, Kaiwan, Bharucha, and Yuejin, Luo. (February 2005). Tortuosity factors for highly tortuous wells: A practical approach. Proceedings of the SPE/IADC drilling conference, Amsterdam, The Netherlands.
Shi, Yucai, Guan, Zhichuan, Zhao, Hongshan, and Huang, Genlu (2017). A new method for build-up rate prediction of bottom-hole assembly in well drilling. J. China Univ. Petroleum 41 (1), 85–89.
Williams, J. B., Apostal, M. C., and Haduch, G. A. (October 1989). An analysis of predicted wellbore trajectory using a three-dimensional model of a bottomhole assembly with bent sub, bent housing, and eccentric contact capabilities. Proceedings of the SPE annual technical conference and exhibition, San Antonio, Texas.
Yin, Q., Wu, J., Jing, H., He, M., and Meng, Q. (2021). Shear mechanical responses of sandstone exposed to high temperature under constant normal stiffness boundary conditions. Geomechanics Geophys. Geo-Energy Geo-Resources 7, 35 doi:10.1007/s40948-021-00234-9
Yu, R., Guo, W., Ding, L., Wang, M., Cheng, F., Zhang, X., et al. (2021). Quantitative characterization of horizontal well production performance with multiple indicators: A case study on the weiyuan shale gas field in the sichuan basin, China. Front. Earth Sci. 15 (2), 395–405. doi:10.1007/s11707-021-0885-x
Zhang, B., Jiang, R., Sun, B., Lu, N., Hou, J., Bai, Y., et al. (2022a). Establishment of the productivity prediction method of Class III gas hydrate developed by depressurization and horizontal well based on production performance and inflow relationship. Fuel 308, 122006. doi:10.1016/j.fuel.2021.122006
Zhang, B., Lu, N., Guo, Y., Wang, Q., Cai, M., and Lou, E. (2022b). Modeling and analysis of sustained annular pressure and gas accumulation caused by tubing integrity failure in the production process of deep natural gas wells. J. Energy Resour. Technol. 144 (6), 063005. doi:10.1115/1.4051944
Zhu, C., He, M., Zhou, Y., Qin, X. z., and Yin, Q. (2021). Numerical investigation on the fatigue failure characteristics of water-bearing sandstone under cyclic loading. J. Mt. Sci. 18 (12), 3348–3365. doi:10.1007/s11629-021-6914-0
Keywords: slide steering drilling system, compound drilling, slide drilling, horizontal section, wellpath control, build-up rate, inclination change rate
Citation: Chu H, Xiong C, Hu K, Guo Y, Shi Y and Zhang B (2023) Enhancing the benefit of slide steering drilling systems in horizontal wells of unconventional reservoirs. Front. Energy Res. 11:1267228. doi: 10.3389/fenrg.2023.1267228
Received: 26 July 2023; Accepted: 11 September 2023;
Published: 29 September 2023.
Edited by:
Xiaojin Zheng, Princeton University, United StatesCopyright © 2023 Chu, Xiong, Hu, Guo, Shi and Zhang. This is an open-access article distributed under the terms of the Creative Commons Attribution License (CC BY). The use, distribution or reproduction in other forums is permitted, provided the original author(s) and the copyright owner(s) are credited and that the original publication in this journal is cited, in accordance with accepted academic practice. No use, distribution or reproduction is permitted which does not comply with these terms.
*Correspondence: Yucai Shi, c2hpeXVjYWlAdXBjLmVkdS5jbg==; Bo Zhang, emhhbmdib3VwY0AxMjYuY29t
Disclaimer: All claims expressed in this article are solely those of the authors and do not necessarily represent those of their affiliated organizations, or those of the publisher, the editors and the reviewers. Any product that may be evaluated in this article or claim that may be made by its manufacturer is not guaranteed or endorsed by the publisher.
Research integrity at Frontiers
Learn more about the work of our research integrity team to safeguard the quality of each article we publish.