- 1Energy Technology Group, University of Southampton, Southampton, United Kingdom
- 2The Faraday Institution, Didcot, United Kingdom
Much focus of dual energy-storage systems (DESSs) for electric vehicles (EVs) has been on cost reduction and performance enhancement. While these are important in the development of better systems, the environmental impacts of system and component-level choices should not be overlooked. The current interest in EVs is primarily motivated by environmental reasons such as climate change mitigation and reduction of fossil fuel use, so it is important to develop environmentally sound alternatives at the design stage. Assessing the environmental impact of developmental and mature chemistries provides valuable insights into the technologies that need to be selected now and which to develop for the future. This paper presents a cradle-to-gate (i.e., all raw material and production elements are considered; however, the “use” phase and recycling are not) lifecycle assessment of a DESS with Li-ion and aqueous Al-ion cells and that of one with Li-ion cells and supercapacitors. These are also compared to a full Li-ion EV battery in terms of their environmental impact for both a bus and car case study. Key findings show that the use of a DESS overall reduces the environmental impacts over the vehicle lifetime and provides an argument for further development of aqueous Al-ion cells for this application.
1 Introduction
The transition to electric vehicles (EVs) in place of internal combustion engines (ICEs) is ongoing throughout the developing world. Many environmental impact assessments have found that while the initial resource use of an EV battery is higher than that for ICEs (Dolganova et al., 2020; Verma et al., 2022; Xia and Li, 2022), overall, the use of EVs reduces the environmental impacts of cars and other vehicles. Various Li-ion-based batteries have been used in EVs and assessed environmentally, with lithium–iron–phosphate (LFP) often being seen as overall better for the environment than nickel–manganese–cobalt (NMC) batteries (Feng et al., 2022; Xia and Li, 2022). The use of an energy storage system (ESS) occupies a significant portion of the overall environmental impact of a vehicle, and it is essential to explore different options for electrifying our vehicles. A dual energy storage system (DESS), often called a hybrid energy storage system (HESS), in the context of an electric vehicle (EV), is an energy storage system composed of a high-energy (HE) component and a high-power (HP) component. The use of the term DESS is to avoid confusion with hybrid electric vehicles (HEV), which refer to a combination of electric and internal combustion power sources. There is also some use of a DESS within an HEV, which may cause further confusion of the definitions (Song et al., 2018a). Within a DESS, the high-energy component provides energy for cruising and other low-power maneuvers, and the high-power component provides additional (or all) power for acceleration along with being a sink for energy generated from braking—limiting the demand on the HE part and extending its lifetime (Lencwe et al., 2022). In this work, the life cycle assessment is topology-agnostic; however, a schematic of a typical DESS is shown in Figure 1.
Usually, the HE component is an energy-dense battery, such as lithium-ion, with the HP component being provided by supercapacitors (often called ultracapacitors). The use of DESSs in EVs is not widely adopted, with many discussions of use cases based on different driving styles and different vehicle applications, which are summarized in Table 1. There is a range of configurations for DESSs, depending on the specific scenario and vehicle scale, from a city bus driving on a normal route (Ostadi and Kazerani, 2015) to a sports car being driven aggressively (Zhu et al., 2020). While the adoption of DESSs is in its infancy, some parallels can be made with conventional hybrid (internal combustion engine—battery) systems (Sankarkumar and Natarajan, 2021). From Table 1, it is clear that the number of (1–38,406), voltage (136–444 V), and capacity (0.9–115 kWh) of the Li-ion cells as well as the capacitance of the SCs vary widely depending on application. Factors that can impact the configurations are the criteria that are optimized, such as minimizing weight, cost, and charge time. However, there may also be a desire to keep battery replacements to a minimum or reduce the number of charge/discharge cycles or state of charge optimization over the vehicle’s lifetime. The article’s focus is highlighted in Table 1. Ensuring the overall battery’s and DESS’s state of health is also a driving factor in system configuration (Song et al., 2015a; Zhang et al., 2018). Overall, only one study was found to use environmental impact as a key driver (Venkateswaran et al., 2020), instead of a reported output or “bonus” to the other optimizations. For example, two papers optimizing a DESS for the Tesla Model S report differences in power requirements of ∼120 kW in the supercapacitors and a ∼9-Wh difference in battery-provided energy. The higher power and energy demanding result considered optimizing for cost reduction (Zhu et al., 2018), whereas the other took a balanced look at cost, mass, and volume reduction to provide a different result (Zhu et al., 2020).
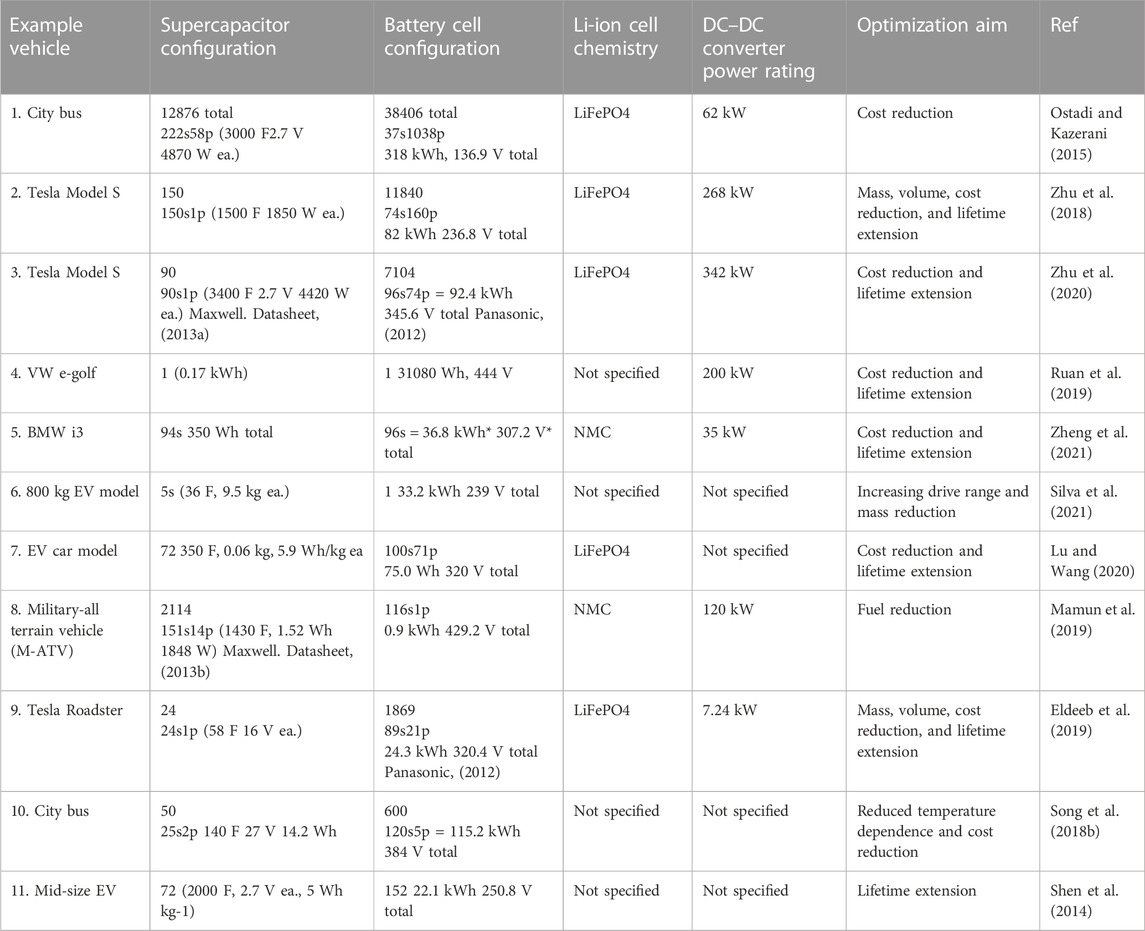
TABLE 1. Summary of optimized SC/battery DESSs from literature and, where available, the configuration (no. in series X, no. in parallel, Y) will be stated as XsYp, as well as Li-ion cell chemistry.
A further distinguishing factor is the ratio of HE:HP components: whether the HP component is being used purely for power-smoothing or as the main contributor to all high-power needs (such as accelerations). For a power-smoothing application, the HP component makes up a smaller proportion of the DESS. Both options show improvements in terms of the overall lifetime of the energy storage system and cost savings; however, there has not been an environmental assessment into which DESS version has the fewest environmental impacts over the lifetime of the vehicle used. This will be addressed as the focus of the assessment presented in this paper. There has been an initial life cycle assessment, LCA, looking at a DESS with two types of Li-ion batteries, a high-power and high-energy version, which showed environmental benefits compared to a single type of the Li-ion battery (Sanfélix et al., 2015); however, it was noted that the emissions produced through manufacturing were higher than that of a HE-only Li-ion battery pack (a 50% increase for CO2 emissions and almost double for the impact on water acidification), and environmental benefits were only seen if the lifetime of the car could be doubled. Many LCAs have been performed for different Li-ion battery configurations (Peters et al., 2017; Ellingsen et al., 2018; Peters and Weil, 2018), as well as for capacitors and supercapacitors (SCs) (Smith et al., 2018; Cossutta et al., 2020; Sperling and Kivelä, 2022); however, these have not been evaluated within a DESS from an environmental perspective. The manufacturing process is a key source of emissions for Li-ions, and if emissions can be reduced at production by using different HP components, while providing the same lifetime extension, then the overall environmental impacts can be further reduced. Continued reliance on lithium batteries will put more pressure on the already politicized mining of associated minerals and may increase the costs beyond the lifetime extension benefits. Therefore, looking at non-lithium, lower cost, and easier-to-produce options for the high-power component of a DESS is crucial to making them accessible.
This paper specifically considers two case studies, a city bus (example 10) and an electric vehicle (EV) modeled as a 1,100 kg car (example 7), taking data from earlier studies (Song et al., 2018b; Lu and Wang, 2020). These DESSs have different output suggestions for the proportion of HE:HP components as well as the overall power and energy required. The city bus requires 150 kW from the HP component, while the EV requires 19.9 kW. Here, a lifecycle assessment approach is used to analyze the environmental impacts of dual energy storage systems proposed for each case study, namely, a supercapacitor/Li-ion (SC/Li-ion) based on the literature results reported. This study further evaluates the use of an aqueous Al-ion/Li-ion configuration as an emerging high-power battery technology. Aluminum is an attractive material for battery applications in EVs due to its high charge storage capacity of 2980 mA h g−1/8046 mA h cm−3 and relative abundance (Elia et al., 2021; Verma and Kumar, 2021). Aluminum ions are readily solvated in both aqueous and non-aqueous (organic or ionic liquid) solvents with a number of materials, including TiO2, MoO3, C, and Al being suggested as positive electrodes, while negative electrode materials include Fe-, Mn-, Cu-, and V-complexes (Melzack and Wills, 2022; Pan et al., 2022) Aqueous Al-ion batteries are one of a number of metal–ion systems being investigated utilizing water as the electrolyte (Wu et al., 2022). This aqueous Al-ion technology has already been identified as potentially having fewer environmental impacts per kW than some supercapacitors and, as such, is a good case study to test the methodology of comparing environmental impacts within DESS design (Melzack et al., 2021). The dual energy storage systems will be compared to a Li-ion-only configuration. The aim is to evaluate the environmental perspective alongside battery chemistry to link these two aspects during new energy storage device development. This LCA is for the cradle-to-gate section of the product lifecycle, using the methodology set out in Potocnik (2013) and Siret et al. (2018). Therefore, this assessment includes the mining and production of raw materials through to manufacture, but it does not include the use phase or any second-life applications or end-of-life activities (such as recycling).
2 Study design
2.1 Life cycle assessment
The life cycle assessment (LCA) looks at the cradle-to-gate aspects of the product’s life cycle. It, therefore, only considers the mining and production of raw materials and manufacture. The process used when performing the LCA is illustrated in Figure 2. First, the components for the product are defined—in this case the components within each DESS, and then the raw material required is identified along with the transportation required and other manufacturing inputs such as energy. The functional unit (FU) is then defined; in this case, the FU is per overall DESS—the analysis will then compare each system throughout the vehicle lives. The impact assessment is then performed by using the openLCA software and the European Union’s Environmental Footprint (EUEF) described below.
2.2 Components within the DESS
The LCA will cover three different ESS designs for each case study. First, a fully HE Li-ion battery pack will be assessed using lithium–iron–phosphate (LFP) cells. These have been described in Majeau-Bettez (2011) and normalized in Peters and Weil (2018), which provides detailed data sets for the LCA comparison. The battery pack modeled has an energy density of 88 Wh kg−1—based on the total mass of the whole battery pack. These cells will also form the HE component of the further two DESS configurations.
The second configuration composes the LFP cells for the HE component and a supercapacitor for the HP component. The supercapacitor will be based on the Maxwell BCAP series (Maxwell, 2019a; Maxwell, 2019b). The third configuration will use the Al-ion aqueous cells described in Holland et al. (2018) as the HP component. These cells have an energy density of 15 Wh kg−1 of the active material and a power density of 300 W kg−1 of the active material.
2.3 Raw material inventory, energy, and infrastructure
This section describes the raw material inventory for the three components modeled: the Li-ion battery pack, the supercapacitor, and the aq. Al-ion battery. These have been modeled using openLCA 1.10.3 software (Ciroth, 2007) with datasets from ecoinvent 3.2 (Wernet et al., 2016) and GaBi Thinkstep (GaBiThinkstep, 2022). The openLCA manual states:
OpenLCA is an open-source software for life cycle assessment (LCA) and sustainability assessment. It has been developed by GreenDelta since 2006 (www.greendelta.com). As an open-source software, it is freely available, without license costs (www.openlca.org). The source code can be viewed and changed by anyone. Furthermore, the open-source nature of the software makes it very suitable for use with sensitive data. The software, as well as any models created, can be shared freely if allowed by the database license.
The software takes datasets of products (flows) and processes, some of which have been compiled elsewhere (such as the ecoinvent and GaBi). Furthermore, the inventory for the Li-ion battery pack modeled in Majeau-Bettez (2011) has been adapted from the dataset made available in Peters and Weil (2018). The supercapacitor inventory is adapted from Cossutta et al. (2020); however, as this study presents an LCA for 5 F Maxwell supercapacitors, there is likely more packaging and other supporting materials assessed than would be present in a single 140-F supercapacitor, for example. This would make the resulting overall mass slightly higher than that in reality, which makes this a conservative assessment. A single 5F supercapacitor is 2.1 g (Maxwell. 2, 2013), and the data are scaled to 1 kg. The aqueous Al-ion cell inventory is taken from Melzack et al. (2021), a single battery is about 25 g, and again this is scaled to 1 kg.
A summary of the key components is provided. Table 2 summarizes the Li-ion battery pack, Table 3 summarizes the SC, and Table 4 summarizes the Al-ion cell, with full inventories found in earlier studies (Peters and Weil, 2018; Cossutta et al., 2020; Melzack et al., 2021). Both the batteries (Li-ion and Al-ion) require a similar amount of energy (∼60 MJ) per kilogram, whereas the supercapacitor only requires 37 MJ per kilogram. We can also see that the amount of the electrolyte required per kilogram is similar for the Al-ion and supercapacitor (about 0.25 kg), while the amount required for the Li-ion is about half—0.12 kg. The amount of additional water was not provided in the inventory for supercapacitors, which introduces some limitations for the comparison already; however, as the overall mass of SCs required in the model is low, it is assumed this will have a negligible impact compared to the 380-kg water per kg Li-ion required.
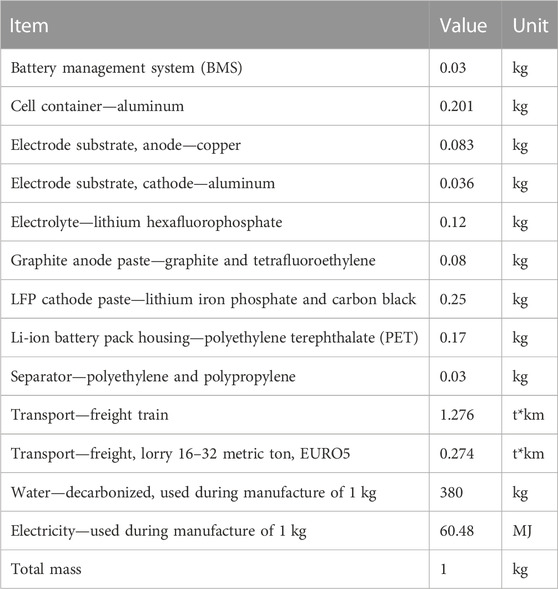
TABLE 2. Summary of Li-ion battery pack components from Majeau-Bettez et al. (2011) and Peters and Weil (2018) normalized to 1 kg.
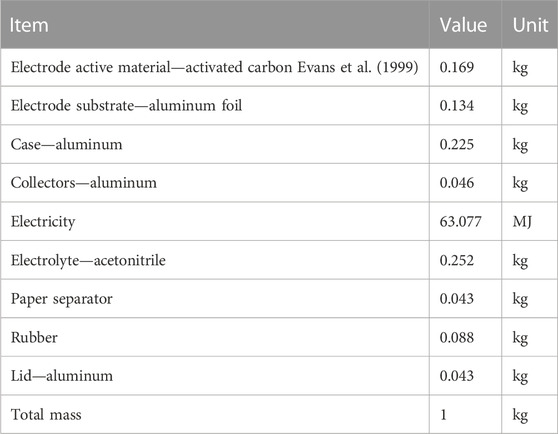
TABLE 3. Summary of supercapacitor components normalized to 1 kg from Cossutta et al. (2020).
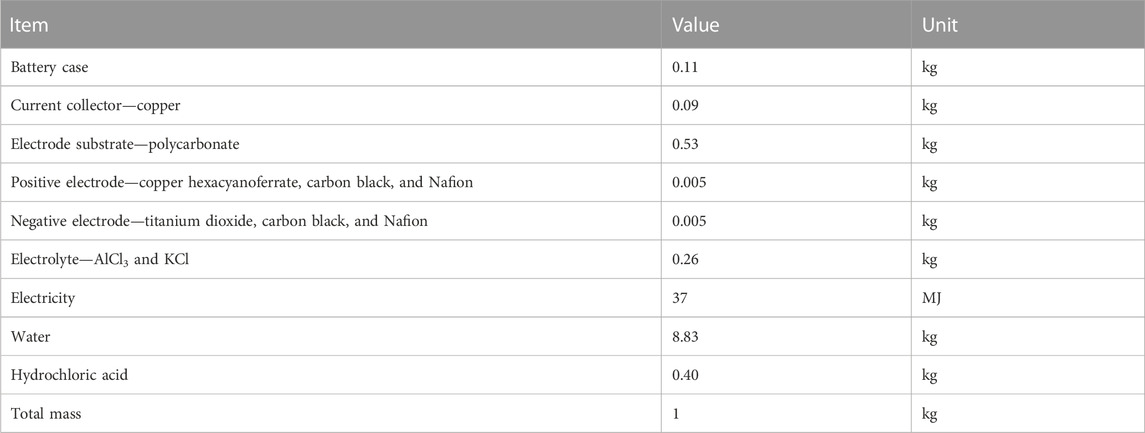
TABLE 4. Summary of aqueous Al-ion cell components normalized to 1 kg from Melzack et al. (2021).
2.4 Cases
The functional unit (FU) used for this study will be the overall mass required to achieve a DESS of appropriate power and capacity to match the vehicle’s needs.
2.4.1 City bus
A city bus will be assessed based on that described in Song et al. (2018b). For this case, the proposed DESS is 50 × 140 F supercapacitors in a 25s2p configuration, alongside 600 LFP cells in a 120s5p configuration, as described in Song et al. (2018b). The equivalent battery-only ESS and a DESS using the Li-ion/Al-ion has been calculated as follows: data interpreted from Figure 7 in Song et al. (2018b) suggest that the SC array provides a maximum power of 150 kW, with an assumed power density of 5.7 kW kg−1 taken from the BCAP150F, which was the closest comparable Maxwell supercapacitor (Maxwell, 2019b). The total mass of the SC component in this example is, therefore, 26.3 kg. A similar approach was taken for the Al-ion high-power component. Given the power density of 300 W kg−1 of the cells and the 150-kW requirement, a mass of 500 kg of the active material is needed for the HP component for the Al-ion/Li-ion system. When taking into account the support materials and battery casing (Melzack et al., 2021), a total of 833.3 kg of the Al-ion cell mass was required. The BMS and casing mass is assumed to be identical across cases as this is based on the battery system, with the additional casing required for the Al-ion included in the 833.3 kg mass. Additionally, as shown in Table 2, 3% of the total mass is for the BMS (battery management system), which has been added in an additional column. It is assumed that the BMS will remain constant for all cases.
2.4.2 EV
Lu and Wang (2020) describes the DESS optimization for an electric vehicle of 1,100 kg (mass without any ESS). The proposed DESS is 7,100 LFP cells in a 100s71p layout, with 72 SC cells—no configuration given. Again, an additional mass equivalent to 3% of the Li-ion mass is added to model the BMS (as listed in Table 2) The supercapacitors modeled in this paper were based on the Maxwell BCAP0350 (Maxwell, 2019b), with state 4.6 kW kg−1. Given that the total mass of the SCs used is 4.32 kg, a total of 19.9 kW is delivered as regenerative breaking capability by the SCs. For the Al-ion/Li-ion case, given that the Al-ion cell has a power density of 300 W kg−1, a mass of 66.24 kg of the active material is required for the Al-ion HP component, which equates to 1,100 kg of total battery mass. The battery-only case described in the paper uses only the 71,000 LFP cells with no additional cells.
A summary of the cases is shown in Table 5.
However, the lifetime of both the energy systems and the vehicles must be considered in order to understand the full environmental impacts of the ESSs. For the city bus, analysis showed that with the Li-ion only ESS, the battery pack would be replaced once within a 10-year vehicle lifetime; however, with the DESS model, this replacement was not necessary (Song et al., 2018b). Therefore, we can, in theory, double the battery mass required for this bus over a 10-year period, while keeping the DESS at the same size. For a Tesla Model S, work from Zhu et al. (2020) assessing battery degradation shows that the degradation of the Li-ion battery pack is halved when using an optimized DESS with supercapacitors, compared to Li-ion only, over one drive cycle. Again, this can be used to estimate the number of battery replacements required over the vehicle’s lifetime.
2.5 Cycle life and replacement modeling
In each case presented, beginning of life (BOL) and end of life (EOL) are modeled. For each vehicle lifetime modeled, the corresponding number of Li-ion batteries, supercapacitors, and Al-ion replacements required will be calculated based on the average cycle life of each component. At BOL, there are no replacements required, and it is assumed the vehicle has not been used. At EOL, the replacement rates for the Li-ion-only and SC/Li-ion cases are taken from the respective studies. For the city bus, Li-ion-only replacement values are taken from Song et al. (2018b), and taking into account 124 miles and 34 drive cycles per day for the bus, during the 10 year lifetime modeled, two replacements would be needed. The projected lifetime of 10 years for the supercapacitor noted in Maxwell et al. (2019b) means that no replacements are required during the lifetime. The addition of the supercapacitor further eliminates the need for Li-ion replacements. The Al-ion battery will perform the same as the supercapacitor and, thus, eliminate the need for Li-ion replacements in the Al-ion/Li-ion case. Cycle life data from Holland et al. (2018) indicate a lifetime of 1,750 full cycles for the Al-ion cell, but based on Song et al. (2018b), the supercapacitor (and thus the Al-ion battery in this case) never completes a full cycle. It is, therefore, assumed that two replacements for a 10-year lifetime will provide a conservative estimate. For the electric car example, the lifetimes are stated in charge/discharge cycles, assuming a 240 km per charge. The stated lifetime of the Li-ion system is 5,129 cycles, whereas the lifetime for the SC/Li-ion system is 6,241 cycles (Lu and Wang, 2020), offering a 20% lifetime extension. The EOL modeled is, therefore, the SC/Li-ion lifetime, therefore requiring one replacement of the Li-ion-only system during this lifetime. The Al-ion/Li-ion system will be modeled as one Al-ion replacement over the lifetime. Table 6 summarizes the replacement rates.
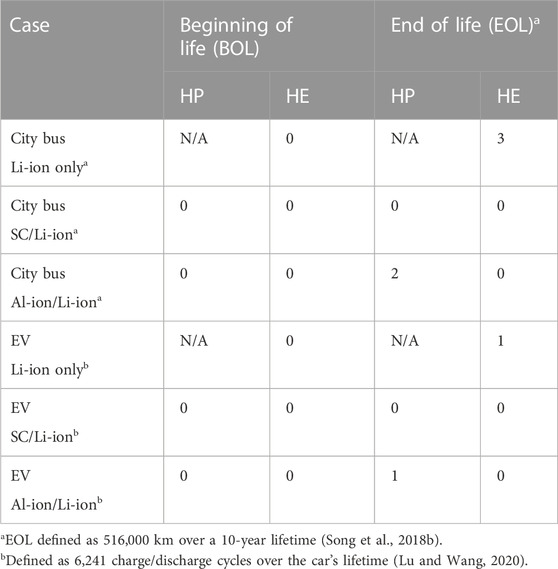
TABLE 6. Replacements required for each component in the energy storage system based on differing lifetime estimates.
3 Results
Using openLCA (Ciroth, 2007) and the European Union’s Environmental Footprint (EUEF) midpoint analysis (Siret et al., 2018), a cradle-to-gate analysis was performed. The fuel consumption and usage of the systems during the car’s lifetime are not considered; only the procurement of raw materials and manufacturing of the energy storage systems are considered. The impacts of production for all required components (including replacement batteries) were assessed over 19 impact categories, including acidification, carcinogenic properties, climate impact, land usage, ozone impact, and energy resource. Respiratory particulates are also calculated as part of the EUEF; however, with regards to nanoparticles (TiO2 in the Al-ion and graphene in the SCs modeled are nanopowders), this assessment criterion is not fully accurate, as the calculations do not take into account nanoparticulates currently and, therefore, do not consider the full range of particulates produced during manufacture (Salieri et al., 2018). For the purpose of this assessment, the main impact categories—climate change, acidification, and resource use—are presented in Tables 7, 8, with the impacts shown graphically in Figure 3 for the city bus and in Figure 4 for the EV. Full results of all impact categories are shown in the Supplementary Information. For the SC/Li-ion case modeled, no replacements are needed, and so BOL and EOL are plotted as a single value. The replacement of the Al-ion battery over the lifetime increases the environmental impacts; however, they are still consistently lower than those of the equivalent Li-ion case.
Initially, it is worth noting that the ratio of HP:HE in the DESSs described is different in both cases. The city bus has a mass ratio of ∼1:1200, and the car has a mass ratio of ∼1:131 for the SC: Li-ion. The differences in these outcomes are likely due to the driving use cases used to optimize the DESSs and the likely different uses of a DESS, with the car using the HP for all high-power cases and the bus for “topping up” with the higher demand accelerations.
When looking at environmental impacts, the results at BOL are within one order of magnitude for all the cases presented. Therefore, it is fair to say that for a vehicle with a short overall lifetime (defined as less than 5 years for the city bus and less than ∼5000 cycles for the EV), there is no strong environmental reason to use a DESS. Furthermore, a DESS is often more expensive than using just one type of a battery (Lu and Wang, 2020; Vukajlović et al., 2020; Zhu et al., 2020). Al-ion cells, although adding an appreciable mass to the DESS, have comparable environmental impacts per kW output (Melzack et al., 2021) to the SC. It should be noted that the added mass was not factored into the vehicle lifetime data. The resulting environmental impacts are roughly the same to one significant figure across all BOL cases. When looking at resource use, the Al-ion/Li-ion seems the worst option for the low-use case; however, as this study does not take into account recycling and re-use, it is likely that the ease of recycling of Al-ion compared with Li-ion batteries (Bi et al., 2019) would lead to a more sustainable result. However, this is beyond the scope of this study.
We see the impact of the lifetime extension provided by the DESS when assessing the EOL results. This impact is shown most strongly with the SC/Li-ion DESS for both case studies. For the city bus example, at EOL, the SC/Li-ion would have just under a third of the environmental impact of the Li-ion-only option. Specifically, looking at the climate change impact, for the Li-ion-only option at end-of-life, the emissions are around 25,446 kg CO2 eq. compared to 7936 kg CO2 eq. for the SC/Li-ion DESS. For the EV, there is a ∼50% reduction in all impact categories reported. This reduction in impacts is mostly true for both the Al-ion/Li-ion EOL cases. The city bus case study shows that the Al-ion/Li-ion at EOL has 35% of the emissions of the Li-ion EOL in climate change impacts and 70% of Li-ion EOL’s resource use (minerals and metals). This high use of minerals and metals comes from the contribution of the copper current collectors in the Al-ion cell, and while not considered within this study, the recycling and re-use of copper in the future would reduce this impact. For the EV case study, the resource use (minerals and metals) is higher for the Al-ion/Li-ion EOL than for the Li-ion EOL, with 0.063 and 0.039 kg Sb eq., respectively. Overall, the impacts reported for the Al-ion/Li-ion EOL for the EV are slightly lower than that for the Li-ion-only EOL case—the climate change impact is 72% that of the Li-ion-only case, while the impact of acidification is 90% that of the Li-ion-only case. In this example, we can see the impact of the ratio of HP:HE and the difference it makes on the environmental output for the DESS.
For the city bus case study, Al-ion could provide the HP component of a DESS in the future, as it provides similar environmental benefits to the SC but has the advantage of being cheaper, safer, and easier to produce (Melzack et al., 2021; Melzack and Wills, 2022). However, the electric vehicle assessed, with higher reliance on the HP component, would benefit environmentally from an SC/Li-ion DESS. For the EV example, it is useful to discuss the measures needed to make the Al-ion/Li-ion DESS a viable environmental option as this will inform future development of the technology. The first option is an increase in the lifetime of the Al-ion battery such that no replacements are needed over the vehicle lifetime—this would lead to the BOL = EOL results, as seen for the SC/Li-ion examples in both case studies. However, if this were not achievable, looking at the impact that is above that of Li-ion-only—minerals and metals—we can inspect the data for the key contributor to this category. From Melzack et al. (2021), we can see that the key contributors are the copper current collector and the battery casing, made mainly from PEEK (polyether ether ketone). The battery casing for the Al-ion cell is ∼11% wt compared to those of the SC and Li-ion casing, which are around 20% of the total mass. The casings for SC and Li-ion, however, are made of aluminum, a low-impact metal with many established routes for production and recycling, which minimizes the overall environmental impact of the case used. The copper current collectors, as mentioned previously, are assumed to be primary copper; a simple improvement in terms of the resource use here is to switch to secondary (or recycled) copper for the current collectors, which will minimize the impact and have no design implications. Changing the copper source within the openLCA software to 75% recycled copper reduces the impact of the minerals and metals to 0.047 kg Sb eq. at EOL—still higher than the 0.39 kg Sb eq. for the Li-ion-only EOL case. At 100% recycled copper, the impact becomes 0.043 kg Sb eq.—at which point the next highest contributor takes over.
Other options in terms of reducing the overall impact of the EV EOL case using Al-ion would be to look at overall improvements in terms of the active material used within the batteries (Melzack, 2022). Currently, only ∼0.6% of the mass of the battery is active material—the rest is support, binders, casing, etc. However, within a fully commercial cell, the mass percentage of the active material is closer to 30% (Ellingsen et al., 2014; Peters and Weil, 2018). With a higher active material %, the overall amount of support materials reduces, which in turn reduces the environmental impacts, maintaining the active material mass required of 66.24 kg for the Al-ion component. A 30% active material mass percentage in the Al-ion component reduces the overall mass of that component to 220.8 kg and the impact of the mineral and metal resource category to 0.054 kg Sb eq. Combining this active material increase with 75% recycled copper for the current collectors, we arrive at a value of 0.025 kg Sb eq.—below that of the Li-ion-only EOL. These changes require the development of the Al-ion battery electrode in order to accommodate and use more active material throughout the battery life and testing to ensure that the increased material loading does not degrade the battery performance (Melzack, 2022).
3.1 Sensitivity analysis
A key uncertainty within the analysis, which is the subject of a sensitivity analysis, includes the transported distances of the raw materials (calculated in t*km with various transport methods in Tables 2–4). A second uncertainty is the electricity mix used within the production.
For the Li-ion components, the total transportation required comes to 1.55 t*km/kg of the battery pack, which is just under half of that for the aq. Al-ion battery—3.59 t*km/kg of the battery pack. The Li-ion transportation assumes only lorries and trains are used, whereas the Al-ion transportation assumes lorries and barges are used. The supercapacitor paper does not list the transportation assumptions, and none were used during the calculation of the overall impacts—as the overall mass of SCs was small, it was assumed the transport impacts would be negligible. To evaluate the sensitivity of the analysis to transport, the CityBus BOL and EOL studies will be carried out with no transport for all three cases, and for double the current amount of assumed transportation, which will be compared with the original result in Figure 5 for BOL and Figure 6 for EOL. For all cases, the overall changes in the 19 impact categories are found in the supplementary data—with the range of change from ±0%–10% of the baseline. The largest change seen in BOL is the acidification impact for Al-ion/Li-ion at 10% above the baseline (36.7 mol compared to 33.5 mol). The use of barge transport here, and not for the Li-ion system, is likely the key reason for this change. It is difficult to explicitly log every journey taken and with which vehicle for these studies. The ranges presented through this analysis do not change the overall take-away from this study at EOL—with the SC/Li-ion and AL-ion/Li-ion cases still having reduced impacts over all categories compared to the Li-ion system—around a third of the Li-ion EOL values (apart from Al-ion/Li-ion resource use minerals and metals, which is at two-thirds that of the EOL Li-ion only). For the BOL cases, however, the Al-ion/Li-ion system for acidification, climate change, and fossil use becomes more impactful when looking at the double transport assumption (by 4.66 mol, 477 kg CO2 eq., and 8136 MJ, respectively). Therefore, when looking at the BOL comparison, the Al-ion/Li-ion system may have higher environmental impacts than the Li-ion-only system, with reduced impacts seen only after the lifetime of the vehicle.
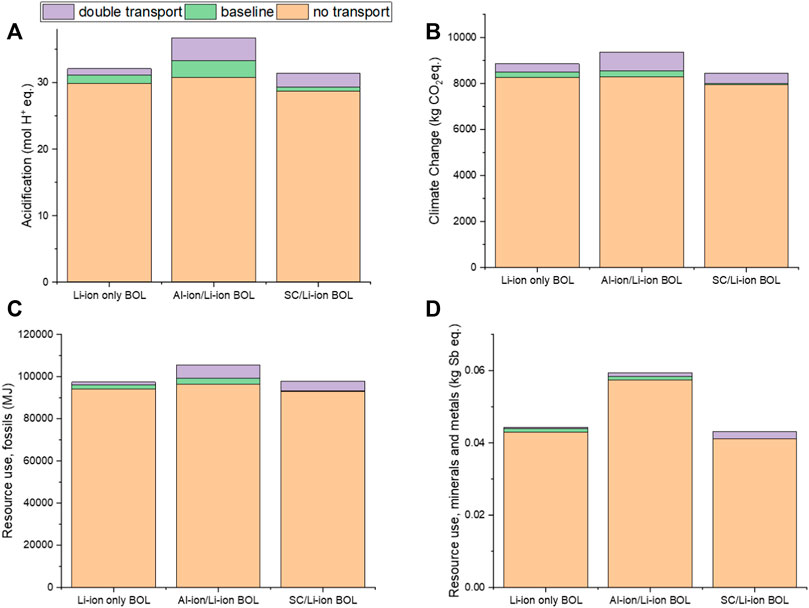
FIGURE 5. Sensitivity to transportation of raw materials for the BOL city bus for (A) acidification, (B) climate change, (C) fossil use, and (D) mineral and metal use.
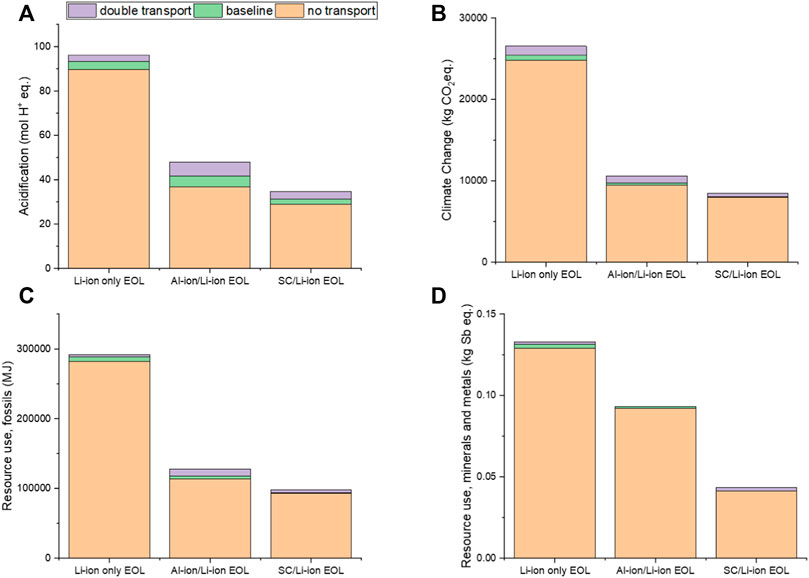
FIGURE 6. Sensitivity to transportation of raw materials for the EOL city bus for (A) acidification, (B) climate change, (C) fossil use, and (D) mineral and metal use.
The electricity mix assumed for the baseline calculations is a mix of 80% renewable and 20% fossil fuel-based. The BOL city bus cases underwent a sensitivity analysis, which looked at 100% renewable (wind-powered) and 100% fossil fuel-based (mixed). Figure 7 shows the results of this analysis, which, for both the acidification and climate change impacts, show that the renewable option has the least impact, with a 0%–1% increase in impact when compared to the baseline. This is somewhat expected as the baseline is 80% renewable. For the fossil-fuel-only option, the impacts increase by nearly 50% acidification (from 31.8 to 55.7 mol for the Li-ion and from 29.3 to 56.6 mol for the SC/Li-ion). The impacts on climate change increase by an order of magnitude—from 8481 to 28196 kg for the Li-ion and from 7990 to 28700 kg for the SC/Li-ion. When considering the Al-ion/Li-ion case though, the fossil fuel case increases the impacts substantially, placing it as the most impactful DESS with this electricity mix. For acidification, it increases from 33 to 81 mol, and for climate change impacts, it increases from 8,536 to 45,028 kg. This shows that the electricity use has a clear impact on these categories, and for the Al-ion/Li-ion case, specifically, this must be chosen carefully in order to ensure the most sustainable outcome—considering that acidification is already a high-impact category for the Al-ion/Li-ion case.
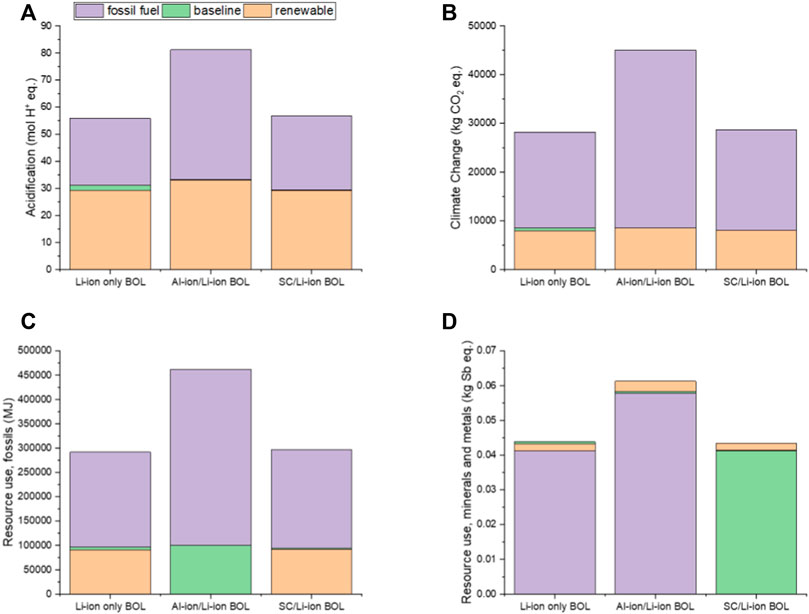
FIGURE 7. Sensitivity to electricity mix for the BOL city bus for (A) acidification, (B) climate change, (C) fossil use, and (D) mineral and metal use.
For the resource use, fossils, the impacts are somewhat expected, with the use of fossil fuel-based electricity increasing this impact the most. The Al-ion/Li-ion DESS is again an outlier as the baseline case here has the least impact. The increases in impacts due to fossil fuel-based electricity match quite closely to the increases in climate change impacts—with around 200% increase for Li-ion and SC/Li-ion and around 400% increase from baseline for the Al-ion/Li-ion category. The minerals’ and metals’ impacts are interesting as for all three DESSs, and the fossil fuel option does not have the highest impact. However, the largest change from the minimum to maximum impact in this category is only 5%, showing that the electricity mix does not have a large impact on the overall resources used.
4 Discussion
When assessing the environmental impacts of products, it is important to understand the limitations of the functional unit and approach used. For this case, the size of the ESSs was calculated and assessed based on values from literature. From looking purely at the energy storage systems, using any DESS provides an environmental advantage in terms of the city bus assessed—but only over a long enough lifetime. This holds true even as Li-ion battery development extends the useful lifetime since the DESS will always offer an advantage. However, for the electric car assessed, the SC/Li-ion had the least environmental impacts, with the Al-ion/Li-ion mostly reducing impacts compared to Li-ion-only, except for the resource use of copper in the current collector. For vehicles with high mileage requirements over their lifetime, a SC/Li-ion DESS appears to have a clear environmental (and financial since Li-ion batteries are expensive (Larcher and Tarascon, 2015)) advantage at both HP:HE ratios. However, for short mileage requirements, the benefit may not be seen in the lifetime of the vehicle—but may still preserve the DESS for second-life uses. This study does not take into account the growing field of second-life uses for car batteries once they have reached 80% capacity and are no longer fit for their initial function. Grid storage and home-batteries for photovoltaics are applications that are currently being studied (Shahjalal et al., 2022). A DESS would likely have a longer second lifetime compared to a Li-ion ESS; however, this has not yet been studied. Therefore, using these energy storage systems in EVs may not just depend on their use in the EV but over the whole lifetime of the DESS. This does add mass to the overall system—which is a non-trivial consequence.
A limitation of this study is that the full electricity use and fuel-saving impacts are not taken into account over the vehicle’s operational lifetime. This study only assesses the cradle-to-gate portion of the life cycle. A further limitation is that the Al-ion cells are still lab-based, and therefore there are many assumptions made in this scale-up—which are discussed in Melzack et al. (2021). Further uncertainties are introduced when modeling the use-case, such as electricity mixes, driving consistency, and temperature ranges (Onat and Kucukvar, 2022). Furthermore, as illustrated in this study, and shown in Table 1, there is a vast range in the make-up of proposed DESSs (varying numbers of cells and supercapacitors with varying overall performance needs), and the choice with the least environmental impact may depend on the overall design and use assumptions of the DESS.
It is important to understand that the Li-ion battery pack and supercapacitors are already commercial technologies compared to the Al-ion development stage. Given that the environmental improvements are already comparable with the SC DESS, this shows that there is potential for further improvements with development of cell design, as shown with the EV example—increasing the active material and using recycled metals in the current collector (Melzack, 2022). These are key areas of research that are strongly supported by this work.
A further consideration in developing DESS systems is balancing operational requirements with environmental impact and safety. Environmental and safety aspects are linked to some degree in terms of the impact on acidification and climate change. Operational safety of DESS systems needs to incorporate a discussion on control topologies, which is beyond the scope of this work. Using aqueous, non-toxic materials should provide advantages in reducing the likelihood and impact of thermal events, and further work should be done in this area during the development of such systems.
When looking at existing LCAs of Li-ion batteries, the functional units vary. For example, Peters et al. (2017) evaluates the kgCO2 eq. per Wh produced over the batteries’ lifetime—these specific comparisons are assessed within previous work (Melzack et al., 2021; Melzack, 2022). Cossutta et al. (2020) reports on the impacts per five capacitors, while the functional units of this study are per DESS. However, we can convert results into per kg values if we make some assumptions. For supercapacitors, the production phase states that 1.06E-1 kgCO2 eq. are produced per five capacitors. Assuming the capacitor assessed is a Maxwell 5F capacitor (Maxwell. 2, 2013), the mass of five capacitors is equal to 10 g. In this study, 4.32-kg SCs are required for the EV case; therefore, based on Cossutta et al. (2020), kgCO2 eq. would be produced. Based on (19), which looked at capacitors (not SCs) per kg, a capacitor produced 3.8 kgCO2 eq., which, scaled to this study’s 4.32 kg, gives 16.5 kgCO2 eq. Isolating the 4.32 kg of SCs required for the EV in this study, the EUEF method used gives a total emission of 28.7 kgCO2 eq. The value calculated in this study is intermediate to those it has been compared to, and there are many factors that can cause discrepancies, including the specific capacitors analyzed being different, there are differences in transportation calculations and electricity mixes used in manufacturing, as well as the different calculation methods and software used. It is important, therefore, to understand these limitations when comparing LCA works and use them to understand trends and ranges to aid our design development.
5 Conclusion
This study looked at the practical use case of a dual energy storage system (DESS) in a city bus and an EV of 1,100 kg. Supercapacitors and aqueous Al-ion cells are assessed as the HP components of the DESS. For the electric vehicles assessed, the use of a DESS extended the energy system’s overall lifetime and reduced the environmental impacts of the energy storage system, compared to a Li-ion-only ESS—apart from the Al-ion/Li-ion for the mineral and metal impact category, where it uses 163% of that of the Li-ion-only option within the EV. Overall, the SC version of the DESS has lower environmental impacts. Given the SC assessed is commercially available, the mostly comparable results of the lab-based aqueous Al-ion technology are promising in terms of its potential sustainable development—with clear development directions such as using recycled copper and redesigning the battery casing being attainable options. It is likely that as this technology develops, its overall mass will reduce and become a viable option for future DESSs. Further work should include looking at the whole life cycle, including use-phase and end-of-life, to gain a complete picture of the overall impacts of the DESS within EVs. This must be done in a way that is sensitive to locations of manufacture and use, with the electricity mix used during both the manufacture and the lifetime of the EV being analyzed and understood. Furthermore, the end-of-life and second-life usage must be explored, and recycling options for the different ESSs need to be realistic to build a pragmatic understanding of where we are and what infrastructure needs to be put in place for the future.
This study strongly argues for the development of the DESS for all EVs as the life-extension compared to a Li-ion-only ESS has been proven by multiple studies (Masih-Tehrani et al., 2013; Song et al., 2015a; Song et al., 2018b; Ruan et al., 2019; Yang et al., 2020; Zhu et al., 2020; Silva et al., 2021; Zheng et al., 2021) and directly links to a reduced environmental impact. Even for low-usage cars, this implementation of the DESS would increase the lifetime of both the second-hand electric car market and further second-life applications. We need to design our energy storage with a holistic, multi-use, and sustainable viewpoint. We should no longer design energy storage systems for an EV, but for a lifetime of uses, of which EVs are the first use—and a DESS is the best solution for that. Furthermore, the development of aqueous Al-ion HP components shows potential for a further reduced environmental impact as the technology advances and active material loading increases.
Data availability statement
The datasets presented in this study can be found in online repositories. The names of the repository/repositories and accession number(s) can be found below: 10.5258/SOTON/D2145.
Author contributions
NM: conceptualization, data curation, formal analysis, investigation, methodology, and writing–original draft. RW: conceptualization, supervision, and writing–review and editing. AC: writing–review and editing.
Funding
The author(s) declare financial support was received for the research, authorship, and/or publication of this article. This work was funded by UKRI under an STFC Studentship and the EPSRC Faraday Training Grant EP/S514901/1.
Acknowledgments
The open access datasets provided through Jens Peters (Peters and Weil, 2018) were also greatly appreciated.
Conflict of interest
The authors declare that the research was conducted in the absence of any commercial or financial relationships that could be construed as a potential conflict of interest.
The author(s) declared that they were an editorial board member of Frontiers at the time of submission. This had no impact on the peer review process and the final decision.
Publisher’s note
All claims expressed in this article are solely those of the authors and do not necessarily represent those of their affiliated organizations, or those of the publisher, the editors, and the reviewers. Any product that may be evaluated in this article, or claim that may be made by its manufacturer, is not guaranteed or endorsed by the publisher.
Abbreviations
aq. Al-ion, aqueous aluminum ion; BMS, battery management system; BOL, beginning of life; DESS, dual energy storage system; EOL, end of life; ESS, energy storage system; EUEF, European Union Environmental Footprint; EV, electric vehicle; HE, high energy; HESS, hybrid energy storage system; HEV, hybrid electric vehicle; HP, high power; LCA, life cycle assessment; LFP, lithium–iron–phosphate; Li-ion, lithium ion; NMC, nickel–manganese–cobalt; PEEK, polyether ether ketone; SC, supercapacitor.
References
Bi, H., Zhu, H., Zu, L., He, S., Gao, Y., and Peng, J. (2019). Combined mechanical process recycling technology for recovering copper and aluminium components of spent lithium-iron phosphate batteries. Waste Manag. Res. 37 (8), 767–780. doi:10.1177/0734242x19855432
Ciroth, A. (2007). ICT for environment in life cycle applications openLCA — a new open source software for life cycle assessment. Int. J. Life Cycle Assess. 12 (4), 209–210. doi:10.1065/lca2007.06.337
Cossutta, M., Vretenar, V., Centeno, T. A., Kotrusz, P., McKechnie, J., and Pickering, S. J. (2020). A comparative life cycle assessment of graphene and activated carbon in a supercapacitor application. J. Clean. Prod. 242, 118468. doi:10.1016/j.jclepro.2019.118468
Dolganova, I., Rödl, A., Bach, V., Kaltschmitt, M., and Finkbeiner, M. (2020). A review of life cycle assessment studies of electric vehicles with a focus on resource use. Resour 9 (3), 32. doi:10.3390/resources9030032
Eldeeb, H. H., Elsayed, A. T., Lashway, C. R., and Mohammed, O. (2019). Hybrid energy storage sizing and power splitting optimization for plug-in electric vehicles. IEEE Trans. Industry Appl. 55 (3), 2252–2262. doi:10.1109/tia.2019.2898839
Elia, G. A., Kravchyk, K. V., Kovalenko, M. V., Chacón, J., Holland, A., and Wills, R. G. A. (2021). An overview and prospective on Al and Al-ion battery technologies. J. Power Sources 481, 228870. doi:10.1016/j.jpowsour.2020.228870
Ellingsen, L. A., Holland, A., Drillet, J.-F., Peters, W., Eckert, M., Concepcion, C., et al. (2018). Environmental screening of electrode materials for a rechargeable aluminum battery with an AlCl3/EMIMCl electrolyte. Materials 11 (6), 936. doi:10.3390/ma11060936
Ellingsen, L. A.-W., Majeau-Bettez, G., Singh, B., Srivastava, A. K., Valøen, L. O., and Strømman, A. H. (2014). Life cycle assessment of a lithium-ion battery vehicle pack. J. Industrial Ecol. 18 (1), 113–124. doi:10.1111/jiec.12072
Evans, M. J. B., Halliop, E., and MacDonald, J. A. F. (1999). The production of chemically-activated carbon. Carbon 37 (2), 269–274. doi:10.1016/s0008-6223(98)00174-2
Feng, T., Guo, W., Li, Q., Meng, Z., and Liang, W. (2022). Life cycle assessment of lithium nickel cobalt manganese oxide batteries and lithium iron phosphate batteries for electric vehicles in China. J. Energy Storage 52, 104767. doi:10.1016/j.est.2022.104767
GaBi (2022).GaBi software system and database for life cycle engineering. Editor Thinkstep (Germany2015: Leinfelden-Echterdingen).
Holland, A., McKerracher, R. D., Cruden, A., and Wills, R. G. A. (2018). An aluminium battery operating with an aqueous electrolyte. J. Appl. Electrochem. 48 (3), 243–250. doi:10.1007/s10800-018-1154-x
Larcher, D., and Tarascon, J. M. (2015). Towards greener and more sustainable batteries for electrical energy storage. Nat. Chem. 7 (1), 19–29. doi:10.1038/nchem.2085
Lencwe, M. J., Chowdhury, S. P. D., and Olwal, T. O. (2022). Hybrid energy storage system topology approaches for use in transport vehicles: a review. Energy Sci. Eng. 10 (4), 1449–1477. doi:10.1002/ese3.1068
Lu, X., and Wang, H. (2020). Optimal sizing and energy management for cost-effective PEV hybrid energy storage systems. IEEE Trans. Industrial Inf. 16 (5), 3407–3416. doi:10.1109/tii.2019.2957297
Majeau-Bettez, G., Hawkins, T. R., and Strømman, A. H. (2011). Life cycle environmental assessment of lithium-ion and nickel metal hydride batteries for plug-in hybrid and battery electric vehicles. Environ. Sci. Technol. 45 (10), 4548–4554. doi:10.1021/es103607c
Mamun, A., Liu, Z., Rizzo, D. M., and Onori, S. (2019). An integrated design and control optimization framework for hybrid military vehicle using lithium-ion battery and supercapacitor as energy storage devices. IEEE Trans. Transp. Electrification 5 (1), 239–251. doi:10.1109/tte.2018.2869038
Masih-Tehrani, M., Ha'iri-Yazdi, M.-R., Esfahanian, V., and Safaei, A. (2013). Optimum sizing and optimum energy management of a hybrid energy storage system for lithium battery life improvement. J. Power Sources 244, 2–10. doi:10.1016/j.jpowsour.2013.04.154
Melzack, N. (2022). Advancing battery design based on environmental impacts using an aqueous Al-ion cell as a case study. Sci. Rep. 12 (1), 8911. doi:10.1038/s41598-022-13078-4
Melzack, N., Wills, R., and Cruden, A. (2021). Cleaner energy storage: cradle-to-gate life cycle assessment of aluminum-ion batteries with an aqueous electrolyte. Front. Energy Res. 9 (290). doi:10.3389/fenrg.2021.699919
Melzack, N., and Wills, R. G. A. (2022). A review of energy storage mechanisms in aqueous aluminium technology. Front. Chem. Eng. 4. doi:10.3389/fceng.2022.778265
Onat, N. C., and Kucukvar, M. (2022). A systematic review on sustainability assessment of electric vehicles: knowledge gaps and future perspectives. Environ. Impact Assess. Rev. 97, 106867. doi:10.1016/j.eiar.2022.106867
Ostadi, A., and Kazerani, M. (2015). A comparative analysis of optimal sizing of battery-only, ultracapacitor-only, and battery–ultracapacitor hybrid energy storage systems for a city bus. IEEE Trans. Veh. Technol. 64 (10), 4449–4460. doi:10.1109/tvt.2014.2371912
Pan, W.-D., Liu, C., Wang, M.-Y., Zhang, Z.-J., Yan, X.-Y., Yang, S.-C., et al. (2022). Non-aqueous Al-ion batteries: cathode materials and corresponding underlying ion storage mechanisms. Rare Met. 41 (3), 762–774. doi:10.1007/s12598-021-01860-8
Peters, J. F., Baumann, M., Zimmermann, B., Braun, J., and Weil, M. (2017). The environmental impact of Li-Ion batteries and the role of key parameters – a review. Renew. Sustain. Energy Rev. 67, 491–506. doi:10.1016/j.rser.2016.08.039
Peters, J. F., and Weil, M. (2018). Providing a common base for life cycle assessments of Li-Ion batteries. J. Clean. Prod. 171, 704–713. doi:10.1016/j.jclepro.2017.10.016
Potocnik, J. (2013). Commission Recommendation of 9 April 2013 on the use of common methods to measure and communicate the life cycle environmental performance of products and organisations Text with EEA relevance. Official J. Eur. Union 56. doi:10.3000/19770677.L_2013.124.eng
Ruan, J., Song, Q., and Yang, W. (2019). The application of hybrid energy storage system with electrified continuously variable transmission in battery electric vehicle. Energy 183, 315–330. doi:10.1016/j.energy.2019.06.095
Salieri, B., Turner, D. A., Nowack, B., and Hischier, R. (2018). Life cycle assessment of manufactured nanomaterials: where are we? NanoImpact 10, 108–120. doi:10.1016/j.impact.2017.12.003
Sanfélix, J., Messagie, M., Omar, N., Van Mierlo, J., and Hennige, V. (2015). Environmental performance of advanced hybrid energy storage systems for electric vehicle applications. Appl. Energy 137, 925–930. doi:10.1016/j.apenergy.2014.07.012
Sankarkumar, R. S., and Natarajan, R. (2021). Energy management techniques and topologies suitable for hybrid energy storage system powered electric vehicles: an overview. Int. Trans. Electr. Energy Syst. 31 (4), e12819. doi:10.1002/2050-7038.12819
Shahjalal, M., Roy, P. K., Shams, T., Fly, A., Chowdhury, J. I., Ahmed, M. R., et al. (2022). A review on second-life of Li-ion batteries: prospects, challenges, and issues. Energy 241, 122881. doi:10.1016/j.energy.2021.122881
Shen, J., Dusmez, S., and Khaligh, A. (2014). Optimization of sizing and battery cycle life in battery/ultracapacitor hybrid energy storage systems for electric vehicle applications. IEEE Trans. Industrial Inf. 10 (4), 2112–2121. doi:10.1109/tii.2014.2334233
Silva, L. C. A., Eckert, J. J., Lourenço, M. A. M., Silva, F. L., Corrêa, F. C., and Dedini, F. G. (2021). Electric vehicle battery-ultracapacitor hybrid energy storage system and drivetrain optimization for a real-world urban driving scenario. J. Braz. Soc. Mech. Sci. Eng. 43 (5), 259. doi:10.1007/s40430-021-02975-w
Siret, C., Tytgat, J., Ebert, T., and Mistry, M. (2018). Product environmental footprint category rules for high specific energy rechargeable batteries for mobile applications. The advanced rechargeable and lithium batteries association. USA, RECHARGE.
Smith, L., Ibn-Mohammed, T., Koh, S. C. L., and Reaney, I. M. (2018). Life cycle assessment and environmental profile evaluations of high volumetric efficiency capacitors. Appl. Energy 220, 496–513. doi:10.1016/j.apenergy.2018.03.067
Song, Z., Hofmann, H., Li, J., Han, X., and Ouyang, M. (2015b). Optimization for a hybrid energy storage system in electric vehicles using dynamic programing approach. Appl. Energy 139, 151–162. doi:10.1016/j.apenergy.2014.11.020
Song, Z., Hofmann, H., Li, J., Hou, J., Zhang, X., and Ouyang, M. (2015a). The optimization of a hybrid energy storage system at subzero temperatures: energy management strategy design and battery heating requirement analysis. Appl. Energy 159, 576–588. doi:10.1016/j.apenergy.2015.08.120
Song, Z., Li, J., Han, X., Xu, L., Lu, L., Ouyang, M., et al. (2014). Multi-objective optimization of a semi-active battery/supercapacitor energy storage system for electric vehicles. Appl. Energy 135, 212–224. doi:10.1016/j.apenergy.2014.06.087
Song, Z., Li, J., Hou, J., Hofmann, H., Ouyang, M., and Du, J. (2018b). The battery-supercapacitor hybrid energy storage system in electric vehicle applications: a case study. Energy 154, 433–441. doi:10.1016/j.energy.2018.04.148
Song, Z., Zhang, X., Li, J., Hofmann, H., Ouyang, M., and Du, J. (2018a). Component sizing optimization of plug-in hybrid electric vehicles with the hybrid energy storage system. Energy 144, 393–403. doi:10.1016/j.energy.2017.12.009
Sperling, M., and Kivelä, T. (2022). Concept of a dual energy storage system for sustainable energy supply of automated guided vehicles. Energies 15 (2), 479. doi:10.3390/en15020479
Venkateswaran, V. B., Saini, D. K., and Sharma, M. (2020). Environmental constrained optimal hybrid energy storage system planning for an Indian distribution network. IEEE Access 8, 97793–97808. doi:10.1109/access.2020.2997338
Verma, J., and Kumar, D. (2021). Metal-ion batteries for electric vehicles: current state of the technology, issues and future perspectives. Nanoscale Adv. 3 (12), 3384–3394. doi:10.1039/d1na00214g
Verma, S., Dwivedi, G., and Verma, P. (2022). Life cycle assessment of electric vehicles in comparison to combustion engine vehicles: a review. Mater. Today Proc. 49, 217–222. doi:10.1016/j.matpr.2021.01.666
Vukajlović, N., Milićević, D., Dumnić, B., and Popadić, B. (2020). Comparative analysis of the supercapacitor influence on lithium battery cycle life in electric vehicle energy storage. J. Energy Storage 31, 101603. doi:10.1016/j.est.2020.101603
Wang, K., Wang, W., Wang, L., and Li, L. (2020). An improved SOC control strategy for electric vehicle hybrid energy storage systems. Energies 13 (20), 5297. doi:10.3390/en13205297
Wernet, G., Bauer, C., Steubing, B., Reinhard, J., Moreno-Ruiz, E., and Weidema, B. (2016). The ecoinvent database version 3 (part I): overview and methodology. Int. J. Life Cycle Assess. 21 (9), 1218–1230. doi:10.1007/s11367-016-1087-8
Wu, D., Li, X., Liu, X., Yi, J., Acevedo-Peña, P., Reguera, E., et al. (2022). 2022 Roadmap on aqueous batteries. J. Phys. Energy 4 (4), 041501. doi:10.1088/2515-7655/ac774d
Xia, X., and Li, P. (2022). A review of the life cycle assessment of electric vehicles: considering the influence of batteries. Sci. Total Environ. 814, 152870. doi:10.1016/j.scitotenv.2021.152870
Yang, B., Zhu, T., Zhang, X., Wang, J., Shu, H., Li, S., et al. (2020). Design and implementation of Battery/SMES hybrid energy storage systems used in electric vehicles: a nonlinear robust fractional-order control approach. Energy 191, 116510. doi:10.1016/j.energy.2019.116510
Zhang, L., Hu, X., Wang, Z., Sun, F., Deng, J., and Dorrell, D. G. (2018). Multiobjective optimal sizing of hybrid energy storage system for electric vehicles. IEEE Trans. Veh. Technol. 67 (2), 1027–1035. doi:10.1109/tvt.2017.2762368
Zheng, C., Wang, Y., Liu, Z., Sun, T., Kim, N., Jeong, J., et al. (2021). A hybrid energy storage system for an electric vehicle and its effectiveness validation. Int. J. Precis. Eng. Manufacturing-Green Technol. 8, 1739–1754. doi:10.1007/s40684-020-00304-5
Zhu, T., Lot, R., Wills, R. G. A., and Yan, X. (2020). Sizing a battery-supercapacitor energy storage system with battery degradation consideration for high-performance electric vehicles. Energy 208, 118336. doi:10.1016/j.energy.2020.118336
Keywords: aluminum-ion, lifecycle assessment, environmental impact assessment, hybrid energy-storage system, dual energy-storage system, supercapacitor
Citation: Melzack N, Wills RGA and Cruden AJ (2024) An environmental perspective on developing dual energy storage for electric vehicles—a case study exploring Al-ion vs. supercapacitors alongside Li-ion. Front. Energy Res. 11:1266670. doi: 10.3389/fenrg.2023.1266670
Received: 25 July 2023; Accepted: 06 December 2023;
Published: 04 January 2024.
Edited by:
Asim Mumtaz, University of York, United KingdomReviewed by:
Kai Yang, University of Surrey, United KingdomJaya Verma, Indian Institute of Technology Delhi, India
Mohit Bajaj, Graphic Era University, India
Copyright © 2024 Melzack, Wills and Cruden. This is an open-access article distributed under the terms of the Creative Commons Attribution License (CC BY). The use, distribution or reproduction in other forums is permitted, provided the original author(s) and the copyright owner(s) are credited and that the original publication in this journal is cited, in accordance with accepted academic practice. No use, distribution or reproduction is permitted which does not comply with these terms.
*Correspondence: N. Melzack, bi5tZWx6YWNrQHNvdG9uLmFjLnVr