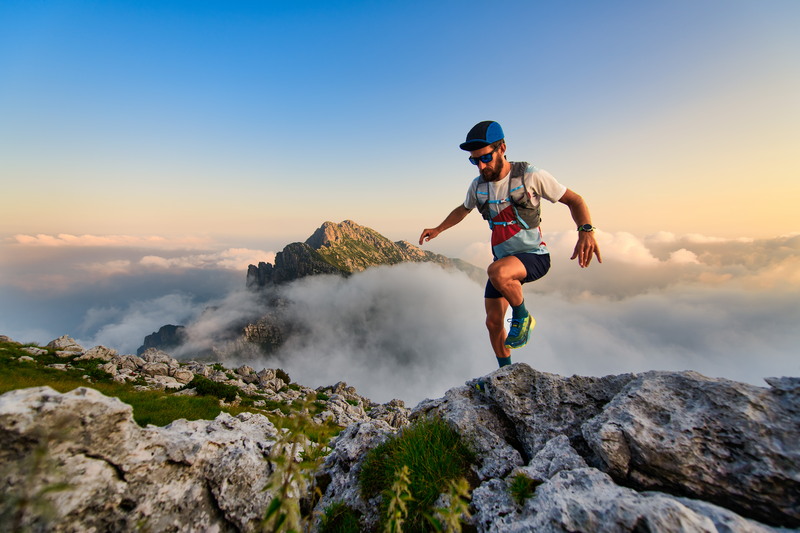
94% of researchers rate our articles as excellent or good
Learn more about the work of our research integrity team to safeguard the quality of each article we publish.
Find out more
REVIEW article
Front. Energy Res. , 04 December 2023
Sec. Nuclear Energy
Volume 11 - 2023 | https://doi.org/10.3389/fenrg.2023.1264168
This article is part of the Research Topic Numerical and Experimental Studies on Small/Micro Nuclear Reactors View all 10 articles
Heat pipe cooled reactors (HPCRs) have broad application prospects due to their advantages, such as high power density, compact structure, lower cost, and easy modular assembly. Numerous countries have engaged in extensive research and development of HPCR conceptual designs. The heat from the reactor is removed by high temperature heat pipes (HTHPs), which generally employ alkali metals as the working fluid, such as potassium, sodium, and lithium. Understanding the thermal-hydraulic performance of HTHPs is essential for the safe and efficient operation of a reactor. Therefore, the objective of this paper is to provide a comprehensive review of HPCR conceptual designs developed by various countries in recent years. The research progress of HTHPs on flow and heat transfer performance is reviewed, with an emphasis on both transient and steady-state characteristics. Research progress, as well as the issues that need to be focused on in future research, are discussed in detail.
The history of the heat pipe (HP) concept can be traced back to 1944, which was developed initially by Gaugler Richard (1944). In 1963, George M. Grover invented a stainless sodium HP and proposed the term ‘‘heat pipe” as the prelude of contemporary HP research. A paper on the study for HP was put out by Grover et al. (1964) the next year. Since then, HP has been attracting increasing the interest and attention of worldwide scholars due to its remarkable characteristics such as compact structure, robustness, higher thermal conductivity and longevity (Wang et al., 2020b). HPs offer excellent heat transfer capabilities and a broad operating temperature range, extending from −60°C to over 2,000°C, according to the choice of the working fluid in the pipe. The high temperature heat pipes (HTHPs), which utilize alkali metals such as sodium and potassium as working fluids, can efficiently operate at temperatures ranging from 400°C to 1,200°C (Sun et al., 2022b). The alkali high latent heat of vaporization allows the HP heat transfer power to approach the kilowatt level (Guo et al., 2023). As a result, the heat pipe cooled reactor (HPCR) system design has extensively utilized HTHPs employing alkali metals (Li et al., 2023b).
The thermosyphon (wickless HP) has found widespread use in a variety of industries because of its relatively straightforward manufacturing methods and high heat conductivity. It is believed to have a higher heat transfer limit as a result of its capacity to hold larger quantities of working fluid, even assuring sufficient fluid supply to the evaporator via gravity (Liu et al., 2022). The conventional wick HP (capillary driven) is most commonly used in nuclear systems, as shown in Figure 1. Typically, the axial length of a HP is commonly divided into three sections: the evaporator section, the adiabatic section, and condenser section. The working fluid absorbs heat from the evaporator section and transforms into a gaseous state through a phase change process. The vapor then travels through the vapor chamber to the condenser section, where it is exposed to a colder environment, leading it to revert to a liquid state. The wick structure, found inside the HP, enables the transportation of the condensed liquid back to the evaporator section. This continuous cycle ensures efficient heat.
In the past two decades, HTHP research has attracted significant attention from various countries in the field of nuclear systems. Based on the published literature, this paper examines the domestic and international research progress and significant outcomes of the HPCR system and the thermal performance of alkali metal HTHP. Additionally, we analyze the shortcomings of previous research and make pertinent recommendations for future research.
In low-power applications, nuclear reactors often require specific characteristics, such as compact size, lightweight design, sustained power output over extended periods, and a focus on safety, reliability, and simplicity of systems. Additionally, it is essential for these reactors to operate autonomously without reliance on human intervention or external agencies in abnormal conditions. Instead, they should rely on inherent safety measures within the core design to self-regulate and restore normal operation or initiate a safe shutdown. Future development efforts will prioritize reactor types that possess high inherent safety, feature simple and compact structures, operate at low pressures, exhibit a high degree of automation, have long core lifetimes, and offer good economic viability. HPCRs offer numerous technical advantages that can contribute to achieving these objectives. In recent years, HP technology has been employed in both domestic and international nuclear reactor conceptual designs and has also been utilized to enhance the reliability of existing safety systems. This chapter will provide an overview of research conducted by various countries on the application of HP technology.
The US has been at the forefront of HP research and has contributed significantly to aerospace and energy. American universities and research institutions have been instrumental in promoting and advancing this field of study. Numerous prestigious academic institutions have established state-of-the-art research facilities and programs to advance HP technology. These include MIT, Stanford University, Los Alamos National Laboratory (LANL), and the California Institute of Technology (Caltech). With the help of these well-known institutions and others across the country, the United States has made great strides in HP study and continues to push the boundaries of this useful technology.
The US had pioneered the use of HTHP cooling with alkali metals in nuclear power devices since the 1980s.These advancements are documented in Table 1. One notable development is the Heat pipe Power System (HPS), which was conceptualized and developed at LANL specifically for space applications. The HPS comprises multiple independent models, each possessing promising economic and operational features.
Originally, the primary objective of the SP100 space nuclear reactor was to serve as an orbital power supply for the United States Strategic Defense Initiative (SDI) during the 1980s (Demuth, 2003). The project was initially sponsored by a consortium consisting of the US Department of Defense, the US Department of Energy, and NASA. However, as the SDI program diminished in importance following the dissolution of the Soviet Union, the focus of the SP100 mission shifted more towards meeting the needs of NASA. In the early 1990s, as NASA ambitious missions faced scrutiny and there was a growing preference for more pragmatic endeavors, the SP100 program was ultimately discontinued. Nonetheless, the preliminary safety analysis conducted for the SP100 nuclear power system, considering scenarios such as unprotected reactivity insertion and unprotected loss of heat sink, demonstrated that the lithium-cooled reactor coupled with the Stirling cycle exhibited satisfactory performance and resilience in the face of accidents (Jin et al., 2022).
In 1997, the initial model of the HPS underwent a successful test, demonstrating favorable conditions. However, it fell short of achieving the originally set heating power target (Houts et al., 1998). Subsequently, a series of experiments were conducted, which yielded highly successful demonstrations (Poston et al., 2000). The Safe Affordable Fission Engine (SAFE) was a HPS reactor specifically designed for generating electricity in space environments (Poston et al., 2002). The SAFE-400 was a 400 kWt reactor that has been specifically designed to be coupled with a 100 kWe Brayton power system. It consisted of 127 identical molybdenum modules. Another derivative design of the HPS, known as the Heat pipe-Operated Mars Exploration Reactor (HOMER), had been adapted for electricity generation during Mars exploration missions (Poston, 2001). The concept of a Martian Surface Reactor for the application of the Martian or Lunar surface power system to promote of human attempts to explore extraterrestrial efforts was initially proposed at MIT (Bushman et al., 2004). The reactor core could produce 1.2 MWt and 0.1 MWe power, operating in a fast spectrum. The reactor was cooled by a lithium HP that was also attached to the power conversion apparatus.
The Scalable AMTEC Integrated Reactor Space (SAIRS) nuclear system utilized a fast neutron spectrum, employing technology developed at the University of New Mexico (UNM). The cooling system for SAIRS involved the use of sodium HPs (El-Genk and Tournier, 2004). The power system of the HPCR with segmented thermoelectric module converters (HP-STMCs) was designed to continue operating even in the event of a unit failure, albeit with a reduction in thermal power output. This system incorporated lithium HPs and was designed with sufficient margins to ensure reliable performance (El-Genk, 2008). The modular HPCR for Lunar Evolutionary Growth-Optimized (LEGO) reactor was developed at the Idaho National Laboratory (INL). This reactor design had the capability to provide a 110 kWe with an efficiency of 6.7% (Bess, 2008). The LEGO reactor design offers improved reliability and safety compared to a single reactor configuration due to its unit design. Each unit in the LEGO system was capable of generating 5 kW of power. This modular approach enhanced the overall system reliability and safety by allowing for redundancy and easier maintenance and replacement of individual units.
The Heat Pipe Encapsulated Nuclear Heat Source (HP-ENHS) reactor was a conceptual design that relied heavily on passive safety features to prevent and mitigate accidents. The reactor incorporated HPs as part of its design to enhance the passive safety mechanisms. These passive safety measures were intended to minimize the reliance on active systems and human intervention during abnormal events, ensuring a high safety level in the reactor operation (Greenspan, 2008). The Special Purpose Reactor (SPR) conceptualized by LANL was an innovative small nuclear reactor (SMR) that offers several advantages. These advantages included significantly improved passive decay heat removal capability, the absence of positive void reactivity coefficient, a smaller and lighter reactor design, and a more robust core for safe transportation. These features made the SPR an appealing option for various applications that require a compact and reliable nuclear power source (Sterbentz et al., 2017). The SPR, designed by LANL, had a nominal core 5 MWt. Utilizing the Brayton thermodynamic cycle, the SPR was capable of producing approximately 2 MWe. This efficient conversion of thermal energy to electrical energy made it suitable for a range of applications that require a compact and high-performance power source (McClure et al., 2015). The expected operational lifespan of the core was designated as 5 years.
MIT had developed a novel reactor concept known as the Fluoride-Salt-Cooled High-Temperature Reactor (FHR) to support human exploration endeavors in extraterrestrial environments (Sun et al., 2016). The proposed design featured a fast spectrum, lithium HPCR utilizing UN fuel, with a thermal output capacity of 1.2 MWt. To generate electrical power, thermionic energy conversion technology was employed, resulting in a DC output of 125 kWe and an AC transmission capability of 100 kWe. The integration of the reactor assembly, power conversion units, and radiators are facilitated through HPs, eliminating the need for a liquid coolant loop in the system. Furthermore, CFD analysis indicated the system exhibits excellent thermal hydraulic characteristics (Wang et al., 2016).
Westinghouse Electric Company was currently engaged in the development of the eVinci microreactor, targeting decentralized generation markets and microgrids. This innovative technology was specifically designed to cater to a variety of applications, including military deployments, remote communities, and remote industrial mines, among others (Maioli et al., 2019). The core design of the eVinci microreactor consisted of a solid monolithic block incorporating three distinct types of channels to accommodate fuel, neutron moderators, and HPs. This versatile design enabled the reactor to support a wide range of electric power levels, ranging from 200 kWe to 25 MWe. The reactor was designed with a lifespan of 5–10 years and incorporates inherent safety features that ensure safe operation even in the absence of active controls or external interventions (Zohuri and McDaniel, 2019). Westinghouse had successfully conducted initial demonstration tests of alkali metal HTHPs utilizing Iron, Chromium, and Aluminum (FeCrAl) alloys. This advancement in HP technology facilitated the implementation of a Low-Enriched Uranium (LEU) micro-reactor core, combined with an open-air Brayton thermodynamic power conversion cycle (Swartz et al., 2021).
(Hernandez et al., 2019) conducted a comprehensive fuel cycle and neutronic analysis of a conceptual design that bore resemblance to the Westinghouse eVinci HPCR. The study they conducted offers valuable insights into the behavior of the reactor fuel cycle and neutron dynamics. The examined concept incorporates low-enriched urania rods and utilizes potassium HPs for core heat removal. The research findings demonstrated that the HPCR design has the potential to operate continuously for over 10 years without the need for refueling. Moreover, the study suggested that this design was more suitable as a nuclear battery, emphasizing its capacity for decentralized power generation rather than serving as a centralized power source.
The KRUSTY was conceived as a crucial progression in the development of space reactors, aiming for successful deployment in space missions (McClure et al., 2020). KRUSTY served as a prototype for testing a 5 kWt Kilopower space reactor. Kilopower reactor designs make use of HPs to transmit fission energy from a solid fuel block in an effective method. These reactors were developed primarily for basic, low-power (1–10 kWe) space and surface power systems (Poston and Mcclure, 2017). The KRUSTY reactor underwent successful final testing in March 2018.
Texas A&M University (TAMU) recently proposed a micro-reactor design known as the Heat Pipe Cooled Yttrium Hydride Moderated Micro Reactor (HPCYHR). This innovative concept utilized HPs for cooling and employs yttrium hydride as a moderator. The reactor design incorporated low-enriched uranium fuel (Alawneh et al., 2022). For the purpose to investigate the heat transfer characteristics of the HPCYHR, commercial software such as STAR-CCM+ was employed. The power distribution obtained from neutronics calculations was employed in the simulations. The outcomes showcased that the reactor could be operated safely for over 11 years, producing a 3 MWt.
The Aurora power plant developed by Oklo is a liquid metal reactor with a capacity of 1.5 MWe, incorporating HPs to effectively conduct fission heat from the reactor core to generation system. Oklo estimated expenditure for constructing the entire power plant and its infrastructure was approximately $10 million. It was important to note that this cost excluded expenses related to fuel and land, as these would be obtained through separate programs established by the Department of Energy. The requested license and initial fuel load had a duration of 20 years (Adamas, 2020). DeWitte mentioned that Oklo planned to construct reactors that were significantly smaller in scale compared to those being developed by TerraPower (Clifford, 2021).
In April 2019, NuScale made an announcement regarding the development of a “simple and inherently safe compact HPCR” with a power range of 1–10 MWe. This innovative design requires minimal site infrastructure, enables rapid deployment, and features full automation during power operation. Collaborative partners involved in this project include Additech, INL and Oregon State University. It is worth noting that this project emerged following the request for ideas and designs by both the SDI and the Department of Energy (WNA, 2020).
Compared to the US, the research and development of HPCR came to a relatively late stage in China. In recent years, various domestic scientific research institutions such as Xi’an Jiaotong University (XJU) and Shanghai Jiao Tong University (SJTU) had actively engaged in numerous conceptual designs for HPCRs. Table 2 shows the main HPCR conceptual design for China in the recent decade.
A concept for a Mars surface HPCR had been proposed, employing lithium HP cooling, multiple Stirling engine conversions, a potassium HP radiator for heat dissipation, and Martian soil shielding (Yao et al., 2016a). The control mechanism is implemented through a rotating control drum. A lithium HPCR was specifically designed to operate at a 2.4 MWt, with a primary focus on achieving an extended lifespan and minimizing noise emissions (Sun et al., 2018a). The Monte Carlo program was employed to evaluate the power distribution and reactivity feedback, of core. The results demonstrated that the designed parameters were satisfactory. (Feng et al., 2022) introduced a megawatt-class HPCR moderated by zirconium hydride. The introduction of a moderator was found to have no substantial impact on the radial and axial power distribution as well as the power peak factor. Additionally, the results indicated that incorporating moderators was advantageous in reducing the thickness and weight of the shielding. To assess feasibility, a preliminary thermal analysis was conducted, revealing that zirconium hydride remains stable within the HPCR. Additionally, the analysis showed that yttrium hydride demonstrated superior thermal stability.
Zhang et al. (2020) developed a HPCR incorporating the use of integrated HP fuel modules. A moderated thermal-neutron spectrum reactor is designed with the 3.2 MWt. The design comprises 234 HP-Fuel elements, where each element consists of a central lithium HP surrounded by highly enriched UN fuel pellets, with cladding on both radial sides. A design idea of 40 kWe nuclear reactor power for Mars surface (NRPMS) was proposed by the China Institute of Atomic Energy (CIAE) (Yao et al., 2016b). The results indicated that the proposed nuclear reactor power scheme is both reasonable and feasible. It demonstrates the capability to meet the safety requirements and achieve the desired operational lifetime. Wang et al. (2020a) presented a preliminary design for a 25 kWe heat pipe cooled reactor power source (HPCRPS). The steady-state and transient performance of the system was analyzed by using a thermal-hydraulic analysis code. The results indicate that all the designed parameters meet the necessary safety requirements. Sun et al. (2018b) developed a design for a 120 kWe lithium heat pipe reactor power source (LHPRPS), intended for various applications. In order to provide shielding, tungsten and water are utilized on both sides of the reactor core. The designed core parameters have been assessed to meet the safety requirements, ensuring the neutronic safety of the reactor.
In the study conducted by Liu et al. (2019), a potassium heat pipe cooled reactor power source system (PHPCRPS) with a power output of 50 kWe was proposed. The HPCR design proposed by the researchers is deemed reasonable and reliable. The residual heat removal system designed for the reactor exhibits a sufficient safety margin to effectively dissipate the decay heat. Furthermore, the study conducted by Chai et al. (2022) introduced a conceptual design for a moderated micro nuclear reactor cooled by heat pipe (MHPR). The MHPR concept was built upon a softened neutron spectrum, which had the potential to enhance the utilization of thermal neutrons and reduce fuel inventory. The reactor had a total 3.5 MWt and its estimated core lifetime was 8.2 years without the need for refueling.
In the study by Ma and Hu (2023), an optimized heat pipe cooled traveling wave reactor (HPTAWR) was developed. This reactor design incorporated a neutron breeding wave to achieve Uranium-Plutonium breeding. The results of the study demonstrated that the HPTWR optimized could attain a power output of 70 MWt and sustain continuous operation for 46 years using lithium HPs. The propagation of the traveling wave in the reactor caused a flattening of the axial power distribution, leading to a gradual decrease in the temperature peak of the HP wall. At the end of the cycle, the temperature peak reached approximately 1784.6 K. This reduction in thermal stress enhanced the safety of the HP wall. Additionally, the study proposed a design for a 65.5 MWt HPTWR (Ma and Hu, 2022). The HPTWR design incorporated an ignition fuel with 14% enrichment and a breeding fuel with 8.5% enrichment. With this configuration, the reactor could operate for 59 years without the need for refueling. This design fulfilled the requirements of utilizing low-enriched fuel while achieving a high power output.
Guo et al. (2023) proposed a compact HPCR design where the ceramic metal composite (CERMET) fuel was used (HPR-CF) from the China Academy of Engineering Physics (CAEP). The CERMET fuel offered several advantages such as high temperature resistance and thermal conductivity. The HPR-CF had excess reactivity that allows it to operate at high temperatures and sustain a thermal power output of 3 MWt for over 3,000 days. In the study by Li et al. (2023a), a design concept for a multi-purpose HPCR was introduced. This micro-reactor employed an enrichment level of 19.75% and had the capability to operate for over 5 years at a 2 MWt without requiring refueling. Monte Carlo simulations were utilized to calculate various parameters, including reactivity, burnup, power distribution, and temperature coefficient, under both normal and accident conditions. The analysis of neutron physics revealed that the preliminary design of the lithium heat pipe cooled modular fast reactor (HPCMR) met the requirements of both economy and safety. This conceptual design held the potential to support future applications in Chinese manned lunar base (Hu et al., 2013). The utilization of HPs in the reactor design allows for a more compact core structure, leading to a reduction in the overall mass of the reactor. This compactness facilitated easier launch and deployment. Additionally, the application of HPs provided redundancy in the system, as damage to certain HPs did not impact the overall energy transfer. This design feature helped to avoid single-point failures and ensured the long-term operation of the reactor without the need for regular maintenance.
XJU had proposed a novel design for the NUclear Silence ThermoElectric Reactor (NUSTER), which utilizes HPs. The study demonstrated that the core components, such as HPs, matrix, and fuel rods, exhibited significant thermal margins during normal operating conditions, indicating their ability to operate with ample safety margins (Huang et al., 2022). The findings indicated that the core design proposed for the Unmanned Portable Reactor in Silence (UPR-S), which operated on the NUSTER power system, successfully fulfilled the criteria of criticality safety and operational longevity (Du et al., 2021). Nonetheless, in the event of a failure of the two adjacent HPs in the 1/8 reactor core, it had been observed that the temperature of the Molybdenum matrix surpasses its temperature threshold, leading to a notable escalation in average thermal stress. These findings underscored the necessity for future design improvements, particularly in terms of optimizing the matrix material (Liu et al., 2022). Furthermore, a novel reactor core design denoted as UPR-SL, had been introduced, utilizing a low-enriched uranium fuel. This design was built upon the foundation of the pre-existing HPCR design, UPR-S (Wu et al., 2023). To reduce the enrichment level of fuel, a high-density UN fuel had been employed as a substitute for the original UO2 fuel. Additionally, an alternative variant of the NUSTER power system, known as NUSTER-10, had been introduced (Tang et al., 2020; Tang et al., 2021).
The concept of HPCR was initially proposed by Grover’s patent in 1965 (Grover George et al., 1967). After 2 years, the European Atomic Energy Community presented a HPCR design based on Grover’s original concept (Fiebelmann, 1968). However, in recent years, few studies have been proposed for HPCR designs in Europe from the published literature. In Japan, in addition to government investments, several universities and research institutions had undertaken research in the field of space nuclear reactors. These academic institutions had dedicated manpower and resources to contribute to the advancement and development of space nuclear reactor technology. Moreover, HP technology had been employed to improve the reliability of safety systems in the International Thermonuclear Experimental Reactor (ITER). By implementing HPs, the safety systems of ITER had been enhanced, ensuring efficient heat transfer and overall system reliability (Kovalenko et al., 1995). Additionally, Japan had utilized loop HP (Mochizuki et al., 2014a) technology and conducted thorough system simulation calculations to verify the effectiveness of this design approach. This technology had also been widely adopted in pressurized water reactors in Ukraine, demonstrating its broad applicability and success in practical applications. Furthermore, they proposed a conceptual design for dealing with decay heat removal after reactor shutdown based on the HP with water working fluid (Mochizuki et al., 2014b; Randeep et al., 2014). The designed system, when coupled with HP cooling and initial gravity feed water charge, could effectively reduce the temperature of the nuclear core to below 100°C in less than 6 h. The implementation of a fully passive operational mode had the potential to enhance the safety of nuclear power facilities.
Starting from 2017, Toshiba Energy Systems and Solutions Corporation had been researching and studying a Mobile-Very-small reactor for Local Utility in X-mark (MoveluX) as a viable distributed energy source. The main concept behind MoveluX revolved around utilizing a sodium HP cooling system and a calcium hydride-moderated core. This design approach aimed to streamline the reactor system, enhance inherent safety, and strengthen nuclear security (Kimura and Asano, 2020). This compact reactor design was capable of generating a thermal power output of 10 MWt and an electrical power output ranging from 3 to 4 MWe by utilizing a Helium turbine with a Brayton cycle (Du et al., 2022).
Allaf et al. (2023) investigated the safety aspects of the novel Micro Research Reactor cooled by Heat Pipes (MRR-HP) design. The unique design feature of the MRR-HP was the incorporation of dual sets of HPs within the monolithic block. The HPs for working fluid water were utilized for normal operation, while fluid potassium HPs were employed during the accident and post-accident scenarios. The implementation of water HPs enables efficient cooling of the reactor, thereby maintaining the fuel temperature below the threshold of 423K.
In Korea, a Hybrid micro modular reactor, which combined the capabilities of renewable energy and energy storage systems, had been designed utilizing potassium HP technology (Choi et al., 2020). The H-MMR offered increased flexibility and efficiency in electricity and thermal generation, capable of producing 10 MWe and 18 MWt through load following strategies. To ensure safety, the RVACS had been specifically designed to effectively remove accident residual heat by cooling the reactor vessel. The Korea Atomic Energy Research Institute had created a conceptual HPCR design that might be used to generate electricity continuously in space and be deployed on a launch vehicle on the lunar surface. This design employed high-assay low-enriched uranium fuel with an enrichment level of 19.5 wt% (Choi et al., 2022). The design objectives for the nuclear reactor core were set to achieve a compact size, with a mass of under 1,200 kg, a height below 5 m, and a diameter less than 2 m. Additionally, the intended operational lifespan of the reactor core was planned to exceed 10 years, while providing a thermal power output of 5 kWt.
Since the application of HTHP, there has been considerable interest in investigating the heat transfer performance of HTHPs in order to optimize their design. However, there are complex flow and heat transfer processes in the HTHP system. In this section, we summarize the impact of several factors on the heat transfer performance of alkali metal HTHPs, which can be mainly divided into transient and steady characteristics. For the research of transient characteristics, the literature on startup and oscillation conditions is reviewed. When all of the working fluid in HP has melted, there is continuous gas flow in the condensing section, and the liquid can keep going back to the evaporation section. The heat transfer capacity of evaporation section and condensing section is the same, and HP will switch to steady-state operation. The thermal performance of HP under steady-state conditions is significantly influenced by several factors, including the presence of non-condensable gas (NCG), different parameters, limitations, and the filling ratio.
Startup condition plays an essential role in the performance and reliability of HP system. Ensuring efficient heat transfer and working fluid flow within the HP is essential to achieve stable operation during startup. Various factors, such as the charging amount, types of working fluids, inclination angle, and temperature variations, significantly influence startup. Many researchers have conducted extensive studies investigating these factors and their impact on startups.
Some researchers experimentally explored the impact of inclination angles on the startup performance of HP. Ma et al. (2022a) focused on experimentally investigating temperature variations of a sodium HP under near 0° during the frozen startup. The HP position of positive and negative angles was shown in Figure 2 to their research. Their findings highlighted the challenges posed by negative inclination angles, where gravity impeded the flow of liquid from the condenser to the evaporator. This leaded to more pronounced temperature differences and higher startup power requirements compared to horizontal and positive inclination cases. On the other hand, positive inclination angles exhibited periodic temperature oscillations during startup. Guo et al. (2014) found that increasing the inclination angle in the condensing section increased the temperature rise, thereby facilitating the startup of the HP. Wang et al. (2020c) performed research on the effect of heating powers on the frozen startup performance of a potassium HP in addition to the influence of inclination angles. According to their research, a successful frozen startup requires the right matching of inclination angle and heating power. Guo et al. (2018) discovered that the frozen startup time of a Na-K gravity-driven HP increases in proportion to the inclination angle. They further observed that as the inclination angle increases from 0° to 50°, the startup and heat transfer performance of the HP improves, while the temperature difference decreases. A slight decrease was observed when the inclination angle exceeded 60°. However, the experimental results of (Ping et al., 2015) indicated that there was negligible influence on restart characteristic for sodium HP under different angles because the curves for temperature raising almost coincide. Niu et al. (2016) conducted experiments and found that the sodium HTHP can be smoothly started at various angles. Furthermore, they observed that the starting time of the HTHP decreased with an increase in heating power. However, the angle had little effect on the starting time.
In addition, many researchers also have studied the influence of types working fluid on startup. Sun et al. (2020) conducted an analysis on working fluid in the HP and found that the presence of a liquid pool at the bottom of the HPs leads to a nonlinear temperature reactivity coefficient, indicating the influence of the working fluid on startup dynamics. Another research investigated by Lu et al. (2017) was the charging amount in sodium HPs. Their study revealed that increasing the charging amount from 22.6 g to 26 g resulted in a successful startup, highlighting the significance of the charging ratio in enhancing the startup performance of the HP. Han et al. (2019) conducted a study on the startup performance of potassium HPs with and without a wick structure. Their experiments showed that during startup and heating, wickless HP s operated under intermittent boiling conditions, with decreasing intensity of boiling as the liquid filling decreased. In their study, it was noteworthy that the impact of the inclination angle on the heat transfer performance of the HP was found to be negligible.
For the operation limitations of HTHP, (Chen et al., 2022b) observed the occurrence of the sonic limit during the startup process of frozen cesium HPs. However, they found that this limit disappeared as the heating power was increased. Deng et al. (2023) developed a hardware-in-the-loop test platform capable of dynamically adjusting the heating power of the HP in real-time, taking into account the effect of temperature feedback. During the frozen start-up process of the sodium HP under the temperature feedback heating mode, they identified five distinct stages based on the evolution of power and the state of the sodium vapor. These stages included the transient start-up phase, during which the sonic limit and viscosity limit were observed. Guo et al. (2021) prepared a cesium HP and conducted a study on its heat transfer and start-up performance. Their findings revealed that the cesium HP exhibited a rapid start-up speed and demonstrated good temperature equalization characteristics. Ma et al. (2023) discovered that a significant increase in heat flux could lead to unstable conditions when the heat flux surpassed 40% of the capillary limit critical heat flux.
In conclusion, the frozen startup of HPs presents complex challenges in their operation. The cost is too high to study only through experimental methods. Therefore, many researchers have developed a series of simulation codes for the frozen startup of HPs.
Ma et al. (2022b) employed a numerical approach to simulate the system startup process. They developed a two-dimensional HP model and coupled it with an open-air Brayton cycle model using the Heat Pipe Reactor TRANsient analysis code, HPRTRAN. The model was validated through startup experiments, confirming its accuracy and reliability. Additionally, the startup of the reactor could be controlled by implementing intermittent drum motion, introducing reactivity in a stepwise manner. This control strategy effectively mitigated large power fluctuations and power peaks within the core. Yuan et al. (2016b) had developed a specialized transient analysis code called TAPIRS for simulating the startup process of HPCR from a frozen state. This code had been extensively used to study the system transient performance during the startup process, ranging from zero cold power to full power.
Huaqi et al. (2022) established transient analysis models for HTHPs starting from a frozen state. The results of the study indicated that the predicted trends obtained using the HPCR code were reasonable, and the deviation from experimental data was less than 2%. This finding further supported the applicability and effectiveness of the transient models for HPs. Additionally, the transient performance of sodium HTHP was numerically simulated in the context of a molten salt reactor (Wang et al., 2013). Numerical results obtained using a FORTRAN code demonstrated that sodium HTHP achieved successful startup and were capable of rapidly removing residual heat from the fuel salt during steady-state conditions in the event of an accident.
Zhang et al. (2021c) developed a three-stage frozen startup model to accurately depict the thermal behavior of NaK HPs throughout the startup process. The findings of the study indicated that the temperature rise rate of the condenser in the HP increased as the initial temperature rises. This relationship was beneficial for overcoming the sonic limitation of the HP at a faster rate. Qiu et al. (2022) developed a transient analysis program HEART for NUSTER. A startup scheme based on the analysis of transient thermohydraulic behavior during cold start-up was proposed for a three-stage HPCR with high safety. Hu et al. (2022) developed a network code in Python specifically for ultra-high temperature lithium HPs. The study found that increasing the wall thickness and wick thickness of a HP leaded to an increase in the transition time. Conversely, increasing the length of the condensation section had a beneficial effect in reducing the transition time.
Zhong et al. (2021) investigated the startup characteristics of the MegaPower system using the HPR transient analysis code called HPRTRAN. During the startup process of a HPCR, there might be significant power fluctuations and the occurrence of a “temperature platform,” which could hinder the reactor startup. In comparison, the use of an interval rotating control drum as opposed to a continuous rotating control drum was considered a safer and more feasible scheme for starting the reactor. Zhang et al. (2021b) wrote a HPSTAC program to investigate the startup process of NaK HP. The starting ambient temperature mainly affected the heating rate of the condensing section. The input heat flux had a threshold effect on the starting stages of the HP. As the heating power increases, the outer wall temperature of the HP rose slightly, the start-up time of the condensing section decreased, and the equivalent heat transfer coefficient of the HP and the surface heat transfer coefficients of the evaporation and condensing zones increased linearly with the heating power. Yuan et al. (2016a) wrote the TAPIRS program in FORTRAN language to simulate the transient behavior of a HPCR system based on SAIRS. The model was validated by comparing the full power parameters with the literature, and the maximum relative error was less than 6%.
There is potential application for HPCR under marine condition. Therefore, there has been some experimental research for alkali metal HTHP in recent years. Guo et al. (2023) showed that the fuel temperature and the reactor power would change periodically with a similar period as the HP temperature oscillation depending on the simulated results. The buffer layer with a lower thermal diffusion coefficient was found to mitigate the temperature and power oscillations, but it would increase the operating temperature of the reactor, which might compromise the safety of the reactor system. Teng et al. (2020) showed that swinging motion had little effect on the start-up performance of the sodium HP, but it caused small-amplitude periodic temperature fluctuations especially at the evaporator. The frequency of temperature fluctuation was almost the same as the swing. Additionally, the amplitude of temperature fluctuation increases with the swing amplitude. Sun et al. (2022a) showed that the temperature fluctuation had the same period as the periodic swing. Periodic swing did not significantly affect the heat transfer of HTHP when the condenser length was appropriate, but the thermal resistance increased slightly compared to the steady state. Under periodic swing condition, if the condenser is too long, the HTHP is more likely to fail. Wang and Li (2023) investigated the HTHP for potassium working fluid in the CFD method. They concluded that the influence of the filling ratio is more significant to equivalent thermal resistance than the rolling period. The filling ratio refers to the proportion of the working fluid volume in relation to the HP volume.
The alkali metal inside the HP is activated by the neutron irradiation in the reactor, which produces inert gas constantly. The inert gas, or NCG, hinders the normal condensation of alkali metal working fluid in HTHP at the phase interface and increases the thermal resistance. This phenomenon is disadvantageous to the isothermal property and heat transfer effectiveness. Therefore, it is important to study the effect of NCG on the heat transfer performance of HTHPs.
In terms of previous studies of noncondensing gases, (Shaubach and Gernet, 1992) found that a sodium HP can operate stably under design conditions when the non-condensable gas pressure is below 0.01 bar, and a small amount of non-condensable gas has a negligible effect on the steady-state heat transfer performance of the HP. Matsushita (1975) found that the condensation heat transfer coefficient of the HP decreases significantly with the increase of non-condensable gas content in the tube, and a 5% volume fraction of non-condensable gas can reduce the steam condensation rate by 20% and affect the liquid working fluid reflux. Fukuzawa and Fujiie (1978) found that too much non-condensable gas would build up at the end of the HP’s condensing section, leading to a sharp temperature drop there. As the power increased, the drop shifted further into the condensing section, and the gas had less effect. Ponnappan et al. (1990) found that the sodium HTHP could start easily from the frozen state under the NCG loading. Another experiment (Ponnappan and Chang, 1994) investigated the startup performance in vacuum and gas-loaded modes, which the latter took significantly longer. The sodium HTHP in vacuum mode, on the other hand, exhibited rough start-up behavior as seen by high temperature spikes at the evaporator and heater during the frozen start-up process. Zhang et al. (2023) experimentally explored the influence of NCG existence on sodium HTHP. The maximum heat transfer rate under the sonic limit is found to be reduced due to the presence of NCG in the HP. The influence of inner wick structure is negligible to the HTHP sonic limit.
In addition, establishing code modeling is an effective way for analyzing the influence of NCG. Zhang et al. (2022) used the thermal resistance network method to model NCG heat transfer and studied its effect on the steady-state heat transfer of a lithium HTHP. The results indicated that NCG reduced the effective heat transfer length, isothermality and efficiency of the HP. Moreover, as the NCG volume fraction increased, the temperature drop in the NCG region became larger, and the overall temperature of the HP also rose. Another numerical investigation (Zhang et al., 2021) tested the generation of NCG for lithium HTHP under neutron irradiation condition. The amount of helium produced by NCG increased with the development of liquid filling ratio and lithium enrichment. Moreover, The helium production was seldom impacted by the working temperature of the lithium HP. Wang et al. (2022) created a mathematical and physical model for how NCG affected the heat transfer of a lithium HTHP and developed a transient analysis code, HPTAC-NCG. During the steady-state operation, the temperature drop in the NCG region increased with the NCG volume fraction, and the HP average temperature increased, which could cause overheating and drying out at the evaporator bottom. As the evaporator input power increased, the NCG volume fraction for the same mass decreased, but increasing the input power alone was not economical to counteract the negative effects of NCG.
The HP thermal performance was mainly affected by the parameters of geometry and thermal-hydraulic characteristics. In the experiment, (Dussinger et al., 2005) compared the compatibility of titanium/potassium and titanium/cesium, taking into account the different physical chemistry properties of different alkali metals. This research further confirmed that these HPs could meet the performance requirements for radiator systems. The steady-state performance of sodium HP was investigated by Guillen and Turner (2022). They found the sodium HP with screen-covered grooves was generally superior to that of open grooves in a vertical gravity-assisted orientation. The different wick configuration arrangement is showed in Figure 3. Under the condition of horizontal orientation at 650°C, the performance limit of the annular wick was 15% higher than that of the screen-covered grooved wick. Based on this, it was stated that the annular type has a high-performance limit below 777°C and that the screen-covered grooved wick has a high-performance limit above 777°C, but there were no experimental results conducted above 777°C.
The oscillating HP consists of capillary tubes that are meandering and partially filled with a working fluid. The fluid exhibits oscillatory behavior and propels forward when subjected to thermal loading. For the oscillating HP, (Ji et al., 2020) found that the temperature difference and thermal resistance between the evaporator and condenser first decreased and then increased with the heat input. In their investigation, the NaK HTHP demonstrated the capability to transport 3169 W of heat while achieving a thermal resistance of 0.08°C/W. The heat transfer performance of the HPs improved with an increase in the potassium mass fraction. This enhancement was attributed to the effects of the saturated vapor pressure gradient, viscosity, and wettability (Ji et al., 2022; Wu et al., 2022; Wu et al., 2023) experimentally investigated the heat transfer performance of NaK oscillating HP. Their results showed that the thermal resistance of HP dropped at first, then increased with the filling ratio When the inclination angles were between 30° and 90°. The minimum value was obtained at 48% filling ratio.
Tian et al. (2021) investigated how the heat transfer performance of potassium HP varies with the inclination angle and the filling ratio. They discovered that overheating in the evaporator results from insufficient working fluid and increasing power. Wang et al. (2021) examined how the HP heat transfer performance changes with the heating power and the inclination angle. They observed that overheating occurs when the power surpasses a limit and that increasing the inclination angle improves heat transfer for low filling ratio HP, but has no significant effect for high filling ratio HP. Therefore, they recommended that the heating power should be regulated to avoid overheating in the HP design. Mantelli et al. (2017) showed that the sodium thermosyphon could transport 250 W more heat power on average at an incline position (10°) than at a vertical position, for the same adiabatic section temperature. The thermosyphon could transport 250 W more heat power on average at an incline position (10°) than at a vertical position, for the same adiabatic section temperature.
Yang et al. (2022) investigated how different parameters affect the heat transfer performance of potassium HTHP. The heat transfer performance of HP can be improved by increasing the wicking mesh and the filling charge amount. The latter can also prevent overheating at the evaporation section. Kang et al. (2019) fabricated a sodium HTHP and studied the thermal performance. The HP thermal resistance reached a minimum of 0.11°C/W at a heat load of 790 W and an inclination angle of +90°C, which favored heat transfer.
Guo et al. (2018) studied how the heat transfer performance of a high temperature thermosyphon was affected by charging it with sodium-potassium alloy. The condenser had a higher heat transfer efficiency at high heating temperatures. The temperature difference at the condenser decreased with increasing heating temperature. Below 825°C, the temperature distribution was more uniform with a short condenser length and a large inclination angle. Above 825°C, these factors had no more advantages. The experimental study of (Liu et al., 2020) explored the factors affecting the heat transfer performance of potassium HTHP. The heat transfer performance improved with the increase in heating power. Zhang et al. (2020) studied the isothermal characteristics and start-up performance of cesium HP. The cesium HP could start normally at a furnace temperature of 330 ∼ 630°C. The start-up time was shorter at higher furnace temperatures. Wang et al. (2022) conducted experimental and numerical studies on the effect of hydrogen permeation on the heat transfer of sodium HTHP. The model was validated by experimental tests. The experiments showed that the top end of an LMHP dropped to below 400°C after hydrogen inactivation, with the evaporator heating temperature at 950°C. The heat transfer was negatively affected by the gas blanket formed by the hydrogen migration along the condensate in the condenser.
For the numerical method, (Tian et al., 2022a) investigated how the heat transfer of Na and K HP was affected by different parameters using the improved thermal resistance network method. The HP was influenced by different types of wicks, such as main line, channel, wire mesh, and sintering. Zhang et al. (2022) proposed a heat pipe cooled Advanced Reactor Transient analysis code (HEART). HEART could successfully predict the steady-state performance of the NUSTER, which showed that the solid-state core could flatten the temperature well. Ge et al. (2022) developed a code for HPCR analysis called TAPIRSD, which was validated by the experimental data of the KRUSTY prototype of the Kilopower space reactor. The TAPIRSD code results agreed with the experimental data, despite the larger temperature oscillation amplitude. The peak and valley value errors were less than 2%, which showed the accuracy and reliability of the improved model and code.
Sun et al. (2022b) simulated the thermal behavior of potassium HP at high temperature. A liquid pool formed at the bottom of the evaporator in the vertical and inclined cases. This increased the local thermal resistance and the peak temperature at the beginning part, which was 200 K higher than the rest part of the HP. Mao et al. (2022) numerical the heat transfer lithium HP with solid-liquid-gas three-phase coupled model. The tube wall temperature dropped sharply in the steady state operation, while the vapor temperature and pressure were almost constant. This showed that the lithium HP had good isothermal properties. Yu et al. (2022) established the CFD analysis model of sodium HP. Under uniform heating, the velocity of vapor chamber changed linearly in the evaporation section and decreases in the condensing section with increasing pressure. The heating power also affected the vapor flow pressure drop and velocity. The liquid phase flow pressure drop was the main factor in the two-phase flow pressure drop for horizontal and inclined HPs. The gas flow velocity dominated the gas-liquid shear effect.
Internal fluid conditions affect the HP performance. The heat transfer limits for HPs and thermosiphon using the equations are shown in Table 3. The heat transfer performance limits for capillary HPs are viscous, sonic, entrainment, boiling, and capillary limits. When the vapor velocity approaches sonic or supersonic conditions during startup or steady state, a phenomenon known as “vapor choking” takes place. This creates the sonic limit. Only capillary wick HPs are affected by the capillary limit, which occurs when the maximum capillary drive pressure is smaller than the difference in pressure between vapor and liquid (Chi, 1976). The viscosity limit happens when the pressure gradient is lower than the viscous force. The entrainment limit happens when the vapor flow disrupts the countercurrent liquid flow. The boiling limit happens when the radial heat flux is too high and affects the fluid flow by boiling (Nemec et al., 2013).
Ivanovskii et al. (1977) performed the experiments on two sodium heat pipes equipped with distinct composite wicks in order to investigate the impact of wick structure on the sonic limit at 1,500–3,000 W of heating power. Faghri et al. (1991) found the capillary limit for an evaporator tilt angle of 5.7°, which was affected by copper contamination in the working fluid and dry evaporator wicks that caused gases that could not be condensed. Clack (2019) studied the performance limits under different heat fluxes for the sodium HP. This HP started to stay stable when the heat flux reached 84 W/cm2. The temperature exhibited a consistent upward trend, suggesting the occurrence of HP dry-out. Subsequently, after a duration of 45 s, the HP encountered a failure event. Kemme (1966) researched the heat transfer limits for the potassium and sodium HP. The experimental results showed that a momentum interaction between vapor and returning liquid at lower temperatures could severely limit heat transfer and may even influence HP startup. Significant improvements in heat transfer capability and HP startup behavior could be achieved through the implementation of a two-component wick structure.
According to experiments of (Ma et al., 2023), at the evaporator end, the capillary limit results in a rapid increase in temperature of around 5 K/s, whereas the condenser and adiabatic sections experience a decrease in temperature. To recover from the capillary limit, a HP can increase the positive inclination or decrease the heating power. Walker et al. (2013) investigated at the capability of a sodium HP and a grooved wick HP to function at their capillary limits. At 846 W, 546 W, and 346 W of operational power, the evaporator reached its capillary limit, with further increases of 0.25 cm, 1.52 cm, and 2.54 cm, respectively. The capillary limit was reached for the self-venting sodium HP when the evaporator raised 7.62 cm at 3.4 kW of power and 12.7 cm at 1.4 kW.
Wang et al. (2021) found that the condensation limit only happens when natural air convection and thermal radiation cool the potassium HP condenser section. The viscosity limit is simple to achieve when the HP is in its startup phase at a low-temperature state. This is because both the friction and vapor viscosity forces are considerable for a HP with a high L/D ratio. When it comes to the sonic limit in a high-temperature state, it takes place at the condenser intake because the temperature was lower than the temperature in the surrounding area. After the sonic limit, there was a brief increase in temperature, followed by a steep decline brought on by the force of friction. When the cooling power is increased, the HP will reach its primary heat transfer limit, referred to as the entrainment limit. Chen et al. (2022a) found that the modulated heating mode is better than the constant heating mode, which can prevent the capillary limit, maintain good temperature uniformity, and raise the operating temperature and the effective length of cesium HP.
Tian et al. (2022b) investigated the heat transfer limits for sodium HTHP and the models were evaluated. They found that the model of Chi matched the experiments at 0° with a relative error of 19.0%, and the effective length of the HP affected the model accuracy. However, the model of Chi did not work for the inclined conditions. The research carried out by Zhang et al. (2022) analyzed the amount of heat that could be transferred by a liquid metal sodium HTHP when positioned at a variety of horizontal angles. The startup performance was impacted by its continuous flow limit. Since the transition temperature increased with increasing horizontal angle, the HP was more vulnerable to the continuous flow limit at large angles. Wei et al. (2021) found that the sonic limit was shown to be the most important factor in sodium HP heat transmission between 500°C and 650°C, whereas the carrying limit was determined to be the most important factor in operating temperatures over 650°C.
Zhao et al. (2021) experimentally and numerically studied the start-up process and tested the temperature and heat flux under steady condition. The experiment results showed that the length-to-diameter ratio, heating heat flow, and operating temperature affected the acoustic velocity limit of HTHP. Guo et al. (2022) proposed an improved model for the HP in simulation, which accounted for the heat conductance in the wall, the vapor flow in the vapor space, and the liquid flow in the wick based on the network method. The model was confirmed by comparing it to data collected from experiments on a copper-water HP. This model was used to examine the sodium HP. The HP was functional at all positive inclination angles. However, its capillary limit was reached at an inclination angle over 30°. Dutra et al. (2023) developed a numerical sodium HP model based on VOF and verified it with experimental data. The experiments confirmed the results and obtained the capillary limits for several cases. These results showed that Sockeye could compute the temperature distribution in HPs and predict the capillary limit.
The Geyser Boiling phenomenon, or intermittent boiling, is an instability phenomenon that several researchers observed since 1965 during the thermosyphons’ operation. It happens when a vapor bubble forms and releases in the evaporator liquid pool, pushing a lot of liquid at high speed to the condenser’s upper regions. The bursting of this bubble can induce significant vibrations in the thermosyphon, with the magnitude depending on the filling ratio. This phenomenon is attributed to the abrupt generation and expansion of vapor resulting from a fall in the hydraulic head, which might potentially induce vibration and cause damage to the pipes (Jafari et al., 2017). Although it does not affect the thermal performance, it should be avoided because it damages the condenser end cap.
Yang et al. (2022) found that HPs containing 50 g of potassium exhibit a severe geyser boiling phenomenon at angles of 45° and 90°, which could pose a risk to safe operation. Manoj et al. (2012) focused on studying the impact of filling ratio on the thermal efficiency of sodium HPs. The results indicated that sodium HPs with a liquid filling rate of 40% exhibited lower heat transfer resistance and better isothermal properties compared to other filling ratios. Mantelli et al. (2017) found that the geyser boiling effect mostly happened in cases with a thermosyphon filling ratio (it is the proportion of working fluid to total evaporator volume in their report) over 100%. In all cases, the effect of geyser boiling occurs mainly at the start of the operation (start-up).
Cisterna et al. (2020) studied the sodium two-phase thermosyphons for different heat transfer on different filling ratios. The researchers suggested the existence of an optimal filling ratio range that can prevent Geyser Boiling and evaporator dry-out in thermosyphons. They proposed an approximate filling ratio of 0.7 as the best value within this range. Thermosyphons with smaller filling ratios were found to have lower start-up temperatures. Moreover, they also proposed a theoretical model that can predict the minimum heat flux for a bubble release, for a given saturation temperature and departure diameter (Cisterna et al., 2021; Zhang et al., 2021) tested the ability to initiate heat transfer and the maximum allowable heating power of a Na-K alloy HP subjected to forced convection cooling. Geyser boiling in the HP improved heat transfer capacity compared to natural convection cooling, especially at lower temperatures and the minimum working temperature. Furthermore, the average temperature of the condensing section improved with the increasing mass flow rate of the Na-K alloy working fluid. In contrast, the average temperature of the evaporating unit changed very slightly with a tiny change in the boiling temperature.
In this paper a comprehensive review has been performed on the design and progress of HPCR for different countries. Numerous micro HPCR design concepts are proposed for space power, marine exploration, etc. The design target varies across different HPCR applications. For the application of space, the power density and thermal-electric conversion efficiency are ensured by adopting appropriate working fluid and conversion types. In the context of space exploration, the power density and thermal-electric conversion efficiency are maintained by the selection of suitable working fluids and conversion methods. In addition, maintaining a low mass is important in order to minimize launch costs. For underwater applications, providing a power source that exhibits low noise levels and has a long lifespan is of utmost significance for energy provision. The system’s thermal performance and conversion efficiency must account for the additional force caused by ocean conditions during the HPCR design procedure. In the future, it is necessary for the HPCR more compact and smaller, which is consistent with its multipurpose design concept. The energy conversion method must be highly efficient and guarantee a low specific mass. The type of working fluid for alkali metal should be carefully considered based on the operating temperature. In addition, the enrichment of uranium is a major concern. It is effective to use the high enrichment uranium (EU) for lowing the toll mass of HPCR. Despite the fact that the HPCR is not created with commercial usage in mind, the spread of high EU has become a policy issue for many nations. There have been designs for LEU systems with a lower mass in recent years, but it is unlikely that they are substantially lighter than the HEU system. A moderated option typically necessitates substantially higher development costs, time, and risk, in addition to shorter lifetimes and lower dependabilities. As a result, the design of the enrichment process poses a significant difficulty for HPCR.
For the transient characteristic of alkali metal HTHP, the startup process has a significant impact on thermal performance. In terms of inclination research, researchers have realized that temperature variation is influenced by different angles. However, the research results of the effects of inclination on the startup are inconsistent. Developing an analysis code is an effective method to the startup process. In the future, more experimental research for different angles is needed to analyze the mechanism of HTHP. The use of simulation codes not only enhances our understanding of the complex phenomena occurring during frozen startup but also facilitates the design and development of more efficient and reliable HP systems. In order for the developing code to be validated, adequate experimental data are required. The rolling condition in low amplitude is negligible to the heat transfer performance of HTHP. It is essential that relevant research on various kinds of HP and thermal-hydraulic parameters be carried out under ocean conditions.
In static conditions, the thermal performance of HTHP is affected by a variety of parameters, including NCG, inclination, filling ratio, and so on. The existence of NCG inner HP poses a significant impact on heat transfer and the flowing of the working fluid. Nevertheless, it is challenging to investigate the influence of the NCG in experiments for its generation. One of the directions of future research is the design of sufficient experiments and measurements of NCG under different fluids. In addition, the applicability of traditional HP limitation equations is a significant concern. Creating a general equation or modification is an effective strategy. The fluid filling ratio has a major impact on the heat transfer performance. Especially, the geyser boiling, occurring in a high filling ratio, is rarely researched in high temperature range. In the future, it is still necessary to study the geyser boiling for HTHP in experiment and numerical simulation.
In practical application, the HP must possess the ability to endure exceedingly elevated temperatures and tremendous heat flux while concurrently ensuring the preservation of effective heat transfer. Furthermore, the heat pipe is commonly engineered with varying angles and shapes to uphold the necessary specifications, exerting a substantial influence on its reliability. Furthermore, the durability of the HP service is influenced by factors such as corrosion, creep, thermal fatigue, and other related phenomena. In contrast, aside from the experimental test, there are currently no established procedures available for evaluating the service life. The development of a service life evaluation method is of utmost importance and requires immediate attention.
EW: Conceptualization, Funding acquisition, Investigation, Methodology, Supervision, Writing–original draft, Writing–review and editing. TR: Conceptualization, Investigation, Methodology, Resources, Supervision, Writing–original draft, Writing–review and editing. LL: Conceptualization, Investigation, Methodology, Resources, Supervision, Writing–original draft, Writing–review and editing.
The author(s) declare that no financial support was received for the research, authorship, and/or publication of this article.
All authors would like to express thanks to Harbin Engineering University for the funding.
The authors declare that the research was conducted in the absence of any commercial or financial relationships that could be construed as a potential conflict of interest.
All claims expressed in this article are solely those of the authors and do not necessarily represent those of their affiliated organizations, or those of the publisher, the editors and the reviewers. Any product that may be evaluated in this article, or claim that may be made by its manufacturer, is not guaranteed or endorsed by the publisher.
Adamas, R. (2020). Oklo has filed first combined license application (COLA) with the NRC since 2009. Available at: https://atomicinsights.com/oklo-has-filed-first-combined-license-application-cola-with-the-nrc-since-2009/.
Alawneh, L. M., Vaghetto, R., Hassan, Y., and White, H. G. S. (2022). Conceptual design of a 3 MWth yttrium hydride moderated heat pipe cooled micro reactor. Nucl. Eng. Des. 397, 111931. doi:10.1016/j.nucengdes.2022.111931
Allaf, M., Okamoto, K., Suzuki, S., and Erkan, N. (2023). Conceptualization of the micro research reactor cooled by heat pipes (MRR-HP), part-II: safety analyses. J. Nucl. Sci. Technol. 60 (08), 881–899. doi:10.1080/00223131.2022.2159560
Bess, J. (2008). “Basic LEGO reactor design for the provision of lunar surface power,” in 2008 international conference on advances in nuclear power plants (United States: Idaho National Lab).
Bushman, A., Carpenter, D. M., Ellis, T., Gallagher, S., Hershcovitch, M. D., Hine, M. C., et al. (2004). The martian surface reactor: an advanced nuclear power station for manned extraterrestrial exploration. Massachusetts Institute of Technology. Center for Advanced Nuclear Energy Systems. http://hdl.handle.net/1721.1/67634.
Chai, X., Guan, C., Deng, J., Zhang, T., and Liu, X. (2022). Preliminary conceptual design of a moderated micro nuclear reactor core cooled by heat pipe. Ann. Nucl. Energy 179, 109399. doi:10.1016/j.anucene.2022.109399
Chen, H.-X., Guo, Y.-X., Yuan, D.-Z., and Ji, Y. (2022a). Experimental study on frozen startup and heat transfer characteristics of a cesium heat pipe under horizontal state. Int. J. Heat. Mass Transf. 183, 122105. doi:10.1016/j.ijheatmasstransfer.2021.122105
Chen, H.-X., Guo, Y.-X., Yuan, D.-Z., and Ji, Y. (2022b). Thermal performance of a medium temperature cesium heat pipe at different inclination angles. Int. Commun. Heat. Mass Transf. 138, 106363. doi:10.1016/j.icheatmasstransfer.2022.106363
Chi, S. W. (1976). Heat pipe theory and practice: a sourcebook. Hemisphere Pub. Corp. https://www.osti.gov/biblio/5467269.
Choi, S. H., Lee, S. N., Jo, C. K., and Kim, C. S. (2022). Conceptual core design and neutronics analysis for a space heat pipe reactor using a low enriched uranium fuel. Nucl. Eng. Des. 387, 111603. doi:10.1016/j.nucengdes.2021.111603
Choi, Y. J., Lee, S., Jang, S., Son, I. W., Kim, Y., Lee, J. I., et al. (2020). Conceptual design of reactor system for hybrid micro modular reactor (H-MMR) using potassium heat pipe. Nucl. Eng. Des. 370, 110886. doi:10.1016/j.nucengdes.2020.110886
Cisterna, L. H. R., Cardoso, M. C. K., Fronza, E. L., Milanez, F. H., and Mantelli, M. B. H. (2020). Operation regimes and heat transfer coefficients in sodium two-phase thermosyphons. Int. J. Heat. Mass Transf. 152, 119555. doi:10.1016/j.ijheatmasstransfer.2020.119555
Cisterna, L. H. R., Milanez, F. H., and Mantelli, M. B. H. (2021). Prediction of geyser boiling limit for high temperature two-phase thermosyphons. Int. J. Heat. Mass Transf. 165, 120656. doi:10.1016/j.ijheatmasstransfer.2020.120656
Clark, A. J. (2019). Failures and implications of heat pipe systems. Albuquerque, NM, and Livermore, CA (United States): OSTI. doi:10.2172/1569523
Clifford, C. (2021). Oklo has a plan to make tiny nuclear reactors that run off nuclear waste. Available at: https://www.cnbc.com/2021/06/28/oklo-planning-nuclear-micro-reactors-that-run-off-nuclear-waste.html.
Demuth, S. F. (2003). SP100 space reactor design. Prog. Nucl. Energy 42 (3), 323–359. doi:10.1016/S0149-1970(03)90003-5
Deng, J., Wang, T., Liu, X., Zhang, T., He, H., and Chai, X. (2023). Experimental study on transient heat transfer performance of high temperature heat pipe under temperature feedback heating mode for micro nuclear reactor applications. Appl. Therm. Eng. 230, 120826. doi:10.1016/j.applthermaleng.2023.120826
Du, S., Li, Y., Sun, T., Jun, W., Liu, X., Su, G., et al. (2022). Research on the development trend of micro nuclear reactor technology. Nucl. Power Eng. 43 (04), 1–4. doi:10.13832/j.jnpe.2022.04.0001
Du, X., Tao, Y., Zheng, Y., Wang, C., Wang, Y., Qiu, S., et al. (2021). Reactor core design of UPR-s: a nuclear reactor for silence thermoelectric system NUSTER. Nucl. Eng. Des. 383, 111404. doi:10.1016/j.nucengdes.2021.111404
Dussinger, P. M., Anderson, W. G., and Sunada, E. T. (2005). “Design and testing of titanium/cesium and titanium/potassium heat pipes,” in 3rd international energy conversion engineering conference (San Francisco, California: American Institute of Aeronautics and Astronautics).
Dutra, B., Merzari, E., Acierno, J., Kraus, A., Manera, A., Petrov, V., et al. (2023). High-fidelity modeling and experiments to inform safety analysis codes for heat pipe microreactors. Nucl. Technol. 2023, 1–25. doi:10.1080/00295450.2023.2181040
El-Genk, M. S. (2008). Space nuclear reactor power system concepts with static and dynamic energy conversion. Energy Convers. Manag. 49 (3), 402–411. doi:10.1016/j.enconman.2007.10.014
El-Genk, M. S., and Tournier, J.-M. P. (2004). “SAIRS” — scalable amtec integrated reactor space power system. Prog. Nucl. Energy 45 (1), 25–69. doi:10.1016/j.pnucene.2004.08.002
Faghri, A., Buchko, M., and Cao, Y. (1991). A study of high-temperature heat pipes with multiple heat sources and sinks: Part II—analysis of continuum transient and steady-state experimental data with numerical predictions. J. Heat. Transf. 113 (4), 1010–1016. doi:10.1115/1.2911194
Feng, K., Wu, Y., Hu, J., Jin, X., Gu, H., and Guo, H. (2022). Preliminary analysis of a zirconium hydride moderated megawatt heat pipe reactor. Nucl. Eng. Des. 388, 111622. doi:10.1016/j.nucengdes.2021.111622
Fiebelmann, P. (1968). Nuclear reactor. Available at: https://lens.org/114-677-671-705-043.
Fukuzawa, Y., and Fujiie, Y. (1978). Performance characteristics of potassium heat pipe loaded with argon. J. Nucl. Sci. Technol. 15 (2), 109–119. doi:10.1080/18811248.1978.9735497
Gaugler Richard, S. (1944). Heat transfer device. Available at:https://lens.org/039-405-146-456-723.
Ge, L., Li, H., Tian, X., Ouyang, Z., Kang, X., Li, D., et al. (2022). Improvement and validation of the system analysis model and code for heat-pipe-cooled microreactor. Energies 15 (7), 2586. doi:10.3390/en15072586
Greenspan, E. (2008). Solid0Core heat-pipe nuclear batterly type reactor. United States: Univ. of California. doi:10.2172/940911
Grover, G. M., Cotter, T. P., and Erickson, G. F. (1964). Structures of very high thermal conductance. J. Appl. Phys. 35 (6), 1990–1991. doi:10.1063/1.1713792
Grover George, M., Busse Claus, A., and Bohdansky, J. (1967). Nuclear reactor with thermionic converter. Available at: https://lens.org/070-424-404-776-402.
Guillen, D. P., and Turner, C. G. (2022). Assessment of screen-covered grooved sodium heat pipes for microreactor applications. Nucl. Technol. 208 (8), 1301–1310. doi:10.1080/00295450.2021.1977085
Guo, H., Guo, Q., Yan, X. K., Ye, F., and Ma, C. F. (2018a). Experimental investigation on heat transfer performance of high-temperature thermosyphon charged with sodium-potassium alloy. Appl. Therm. Eng. 139, 402–408. doi:10.1016/j.applthermaleng.2018.04.139
Guo, Q., Guo, H., Yan, X., Ye, F., Wang, X., and Ma, Z. (2014). Experimental study of start-up performance of sodium-potassium heat pipe. J. Eng. Thermophys. 35 (12), 2508–2512.
Guo, Q., Guo, H., Yan, X. K., Ye, F., and Ma, C. F. (2018b). Influence of inclination angle on the start-up performance of a sodium-potassium alloy heat pipe. Heat. Transf. Eng. 39 (17-18), 1627–1635. doi:10.1080/01457632.2017.1370325
Guo, X., Guo, Y., Guo, S., Wang, G., Li, Z., Li, R., et al. (2023a). Concept design and neutronics analysis of a heat pipe cooled nuclear reactor with CERMET fuel. Ann. Nucl. Energy 192, 109974. doi:10.1016/j.anucene.2023.109974
Guo, Y., Chen, H., Yuan, D., Li, L., Wang, L., Wang, Y., et al. (2021). Startup and heat transfer performance of medium temperature cesium heat pipe. Chem. Industry Eng. Prog. 40 (11), 5981–5987. doi:10.16085/j.issn.1000-6613.2020-2293
Guo, Y., Su, Z., Li, Z., Wang, K., and Liu, X. (2022). An improved model of the heat pipe based on the network method applied on a heat pipe cooled reactor. Front. Energy Res. 10. doi:10.3389/fenrg.2022.848799
Guo, Y., Su, Z., Li, Z., Yu, J., and Wang, K. (2023b). Research on the effect of heat pipe temperature oscillation on heat pipe cooled reactor operation. Ann. Nucl. Energy 182, 109587. doi:10.1016/j.anucene.2022.109587
Han, Z., Chai, B., Wei, G., Bi, K., Feng, B., and Long, Y. (2019). Test study for starting performance of high-temperature gravity potassium heat pipes with and without wick. Atomic Energy Sci. Technol. 53 (01), 38–44. doi:10.7538/yzk.2018.youxian.0345
Hernandez, R., Todosow, M., and Brown, N. R. (2019). Micro heat pipe nuclear reactor concepts: analysis of fuel cycle performance and environmental impacts. Ann. Nucl. Energy 126, 419–426. doi:10.1016/j.anucene.2018.11.050
Houts, M. G., Poston, D. I., and Emrich, W. J. (1998). Heatpipe power system and heatpipe bimodal system development status. AIP Conf. Proc. 420 (1), 1189–1195. doi:10.1063/1.54911
Hu, C., Yu, D., He, M., Li, T., and Yu, J. (2022). Design and heat transfer performance analysis of ultra-high temperature lithium heat pipe. Nucl. Power Eng. 43 (03), 21–27. doi:10.13832/j.jnpe.2022.03.0021
Hu, G., Zhao, S., Sun, Z., and Yao, C. (2013). “A heat pipe cooled modular reactor concept for manned lunar base application,” in International conference on nuclear engineering (Chengdu, China: Nuclear and Emerging Technologies for Space).
Huang, J., Wang, C., Tian, Z., Guo, K., Su, G. H., Tian, W., et al. (2022). Preliminary conceptual design and analysis of a 100 kW <sub>e</sub> level Nuclear Silent Thermal-Electrical Reactor (NUSTER -100). Int. J. Energy Res. 46 (14), 19653–19666. doi:10.1002/er.8542
Huaqi, L., Zeyu, O., Xiaoyan, T., Li, G., Da, L., Xiaoya, K., et al. (2022). The development of high temperature heat-pipe transient model for system analysis of heat pipe cooled microreactor. Prog. Nucl. Energy 146, 104145. doi:10.1016/j.pnucene.2022.104145
Ivanovskii, M. N., Prosvetov, V. V., Sorokin, V. P., Chulkov, B. A., and Yagodkin, I. V. (1977). Investigation of the evaporation process and sonic limits in sodium heat pipes. J. Eng. Phys. 33, 1306–1310. doi:10.1007/BF00860904
Jafari, D., Filippeschi, S., Franco, A., and Di Marco, P. (2017). Unsteady experimental and numerical analysis of a two-phase closed thermosyphon at different filling ratios. Exp. Therm. Fluid Sci. 81, 164–174. doi:10.1016/j.expthermflusci.2016.10.022
Ji, Y., Wu, M., Feng, Y., Liu, H., Yang, X., Li, Y., et al. (2022). Experimental study on the effects of sodium and potassium proportions on the heat transfer performance of liquid metal high-temperature oscillating heat pipes. Int. J. Heat. Mass Transf. 194, 123116. doi:10.1016/j.ijheatmasstransfer.2022.123116
Ji, Y., Wu, M., Feng, Y., Yu, C., Chu, L., Chang, C., et al. (2020). An experimental investigation on the heat transfer performance of a liquid metal high-temperature oscillating heat pipe. Int. J. Heat. Mass Transf. 149, 119198. doi:10.1016/j.ijheatmasstransfer.2019.119198
Jin, Z., Wang, C., Liu, X., Dai, Z., Tian, W., Su, G., et al. (2022). Operation and safety analysis of space lithium-cooled fast nuclear reactor. Ann. Nucl. Energy 166, 108729. doi:10.1016/j.anucene.2021.108729
Kang, S.-W., Yeh, H.-M., Tsai, M.-C., and Wu, H.-H. (2019). Manufacture and test of a high temperature heat pipe. J. Appl. Sci. Eng. 22 (4), 493–499. doi:10.6180/jase.201909_22(3).0010
Kimura, R., and Asano, K. (2020). Ensuring criticality safety of vSMR core during transport based on its temperature reactivity. Nucl. Sci. Eng. 194 (3), 213–220. doi:10.1080/00295639.2019.1685352
Kovalenko, V., Khripunov, V., Antipenkov, A., and Ulianov, A. (1995). Heat-pipes-based first wall. Fusion Eng. Des. 27, 544–549. doi:10.1016/0920-3796(95)90170-1
Li, J., Cai, J., and Li, X. (2023a). Conceptual design and feasibility analysis of a megawatt level low enriched uranium heat pipe cooled reactor core. Ann. Nucl. Energy 181, 109576. doi:10.1016/j.anucene.2022.109576
Li, J., Hu, Z., Jiang, H., Guo, Y., Li, Z., Zhuge, W., et al. (2023b). Coupled characteristics and performance of heat pipe cooled reactor with closed Brayton cycle. Energy 280, 128166. doi:10.1016/j.energy.2023.128166
Liu, H., Gan, W., Yao, H., Wang, X., Wang, Y., and Zhu, Y. (2022b). Visualization and heat transfer comparative analysis of two phase closed thermosyphon. Appl. Therm. Eng. 217, 119172. doi:10.1016/j.applthermaleng.2022.119172
Liu, L., Liu, B., Xiao, Y., Gu, H., and Guo, H. (2022a). Preliminary thermal and mechanical analysis on the reactor core of a new heat pipe cooled reactor applied in the underwater environment. Prog. Nucl. Energy 150, 104306. doi:10.1016/j.pnucene.2022.104306
Liu, X., Sun, H., Tang, S., Wang, C., Tian, W., Qiu, S., et al. (2019). Thermal-hydraulic design features of a micronuclear reactor power source applied for multipurpose. Int. J. Energy Res. 43 (9), 4170–4183. doi:10.1002/er.4542
Liu, X., Tian, Z., Wang, C., Su, G., Tian, W., and Qiu, S. (2020). Experimental study on heat transfer performance of high temperature potassium heat pipe. Nucl. Power Eng. 41 (S1), 106–111. doi:10.13832/j.jnpe.2020.S1.0106
Lu, Q., Han, H., Hu, L., Chen, S., Yu, J., and Ai, B. (2017). Preparation and testing of nickel-based superalloy/sodium heat pipes. Heat Mass Transf. 53 (11), 3391–3397. doi:10.1007/s00231-017-2105-5
Ma, K., and Hu, P. (2022). Preliminary conceptual design and neutroncis analysis of a heat pipe cooled traveling wave reactor. Ann. Nucl. Energy 168, 108907. doi:10.1016/j.anucene.2021.108907
Ma, K., and Hu, P. (2023). Preliminary neutronics and thermal analysis of a heat pipe cooled traveling wave reactor. Ann. Nucl. Energy 190, 109876. doi:10.1016/j.anucene.2023.109876
Ma, Y., Yu, H., Huang, S., Zhang, Y., Liu, Y., Wang, C., et al. (2022a). Effect of inclination angle on the startup of a frozen sodium heat pipe. Appl. Therm. Eng. 201, 117625. doi:10.1016/j.applthermaleng.2021.117625
Ma, Y., Yu, H., Wang, X., Zhang, Y., Huang, S., Wang, C., et al. (2023). Experimental study on sodium Screen-Wick heat pipe capillary limit. Appl. Therm. Eng. 227, 120397. doi:10.1016/j.applthermaleng.2023.120397
Ma, Y., Zhong, R., Yu, H., Huang, S., Tian, C., He, X., et al. (2022b). Startup analyses of a megawatt heat pipe cooled reactor. Prog. Nucl. Energy 153, 104405. doi:10.1016/j.pnucene.2022.104405
Maioli, A., Detar, H., Haessler, R., Friedman, B., Belovesick, C., Cobel, J., et al. (2019). Modernization of technical requirements for licensing of advanced non-light water reactors Westinghouse eVinciTM micro-reactor licensing modernization project demonstration. Avaliable at: https://www.nrc.gov/docs/ML1922/ML19227A322.pdf.
Manoj, R., Kumar, M. C., NarasimhaRao, R., Narasimha, K. R., and Suresh, P. V. S. (2012). PERFORMANCE EVALUATION OF SODIUM HEAT PIPES THROUGH PARAMETRIC STUDIES. Front. Heat Pipes 3, 043003. doi:10.5098/fhp.v3.4.3003
Mantelli, M. B., Uhlmann, T., Cisterna, L. H., Marengo, M., and Eskilsson, P. (2017). “Experimental study of a sodium two-phase thermosyphon,” in 9th world conference on experimental heat transfer, fluid mechanics and thermodynamics (Iguazu Falls, Brazil: MECHANICAL POWER ENGINEERING DEPARTMENT).
Mao, S., Zhou, T., Liu, W., Wei, D., and Xue, C. (2022). Numerical simulation of three-phase coupling for high-temperature lithium heat pipe. Nucl. Power Eng. 43 (06), 37–42. doi:10.13832/j.jnpe.2022.06.0037
Matsushita, T. (1975). “The effects of noncondensable gas in the heatpipes,” in 11th international symposium on space technology and science (Tokyo, Japan: AGNE Publishing, Inc).
McClure, P. R., Poston, D. I., Dasari, V., and Reid, R. S. (2015). Design of megawatt power level heat pipe reactors. USA: Los Alamos National Lab. LANL. doi:10.2172/1226133
McClure, P. R., Poston, D. I., Gibson, M. A., Mason, L. S., and Robinson, R. C. (2020). Kilopower project: the KRUSTY fission power experiment and potential missions. Nucl. Technol. 206 (Suppl. 1), S1–S12. doi:10.1080/00295450.2020.1722554
Mochizuki, M., Singh, R., Nguyen, T., and Nguyen, T. (2014a). Heat pipe based passive emergency core cooling system for safe shutdown of nuclear power reactor. Appl. Therm. Eng. 73 (1), 699–706. doi:10.1016/j.applthermaleng.2014.07.004
Mochizuki, M., Singh, R., Nguyen, T., and Saito, Y. (2014b). An emergency core cooling system (ECCS) for nuclear power reactor using passive loop heat pipe. J. Jpn. Inst. Electron. Packag. 5, 180–184. doi:10.5104/jiep.15.180
Nemec, P., Čaja, A., and Malcho, M. (2013). Mathematical model for heat transfer limitations of heat pipe. Math. Comput. Model. Dyn. Syst. 57 (1), 126–136. doi:10.1016/j.mcm.2011.06.047
Niu, T., Zhang, Y., Hou, H., Wang, Y., and He, Z. (2016). Properties of high-temperature heat pipe and its experimental. Acta Aeronautica Astronautica Sinica 37 (S1), 59–65. doi:10.7527/S1000-6893.2016.0165
Ping, Y., Hong, Z., Hui, X., and Yan, S. (2015). Restart characteristics of high-temperature sodium heat pipe. Proc. CSEE 35 (02), 404–410. doi:10.13334/j.0258-8013.pcsee.2015.02.019
Ponnappan, R., Boehman, L. I., and Mahefkey, E. T. (1990). Diffusion-controlled startup of a gas-loaded liquid-metal heat pipe. J. Thermophys. Heat. Transf. 4 (3), 332–340. doi:10.2514/3.185
Ponnappan, R., and Chang, W. S. (1994). Startup performance of a liquid-metal heat pipe in near-vacuum and gas-loaded modes. J. Thermophys. Heat. Transf. 8 (1), 164–171. doi:10.2514/3.516
Poston, D. I. (2001). The heatpipe-operated Mars exploration reactor (HOMER). AIP Conf. Proc. 552, 797–804. doi:10.1063/1.1358010
Poston, D. I., Gibson, M. A., Godfroy, T., and McClure, P. R. (2020). KRUSTY reactor design. Nucl. Technol. 206 (Suppl. 1), S13–S30. doi:10.1080/00295450.2020.1725382
Poston, D. I., Kapernick, R. J., and Guffee, R. M. (2002). Design and analysis of the SAFE-400 space fission reactor. AIP Conf. Proc. 608 (1), 578–588. doi:10.1063/1.1449775
Poston, D. I., and Mcclure, P. R. (2017). White paper – use of LEU for a space reactor. United States: Idaho National Lab.INL. doi:10.2172/1375148
Poston, D. I., Voit, S. L., Reid, R. S., and Ring, P. J. (2000). The heatpipe power system (HPS) for Mars outpose and manned Mars missions. AIP Conf. Proc. 504 (1), 1327–1334. doi:10.1063/1.1290947
Qiu, S., Zhang, Z., Zhang, Z., Wang, C., Guo, K., Tian, W., et al. (2022). Study on thermal-hydraulic characteristics of ocean silent heat pipe cooled reactor. Atomic Energy Sci. Technol. 56 (06), 989–1004. doi:10.7538/yzk.2022.youxian.0339
Randeep, S., Masataka, M., Thang, N., and Yuji, S. (2014). “Heat pipe applications in cooling nuclear fuel,” in International heat transfer conference (Kyoto, Japan: U.S. Department of Energy National Laboratory operated by Battelle Energy Alliance, LLC).
Shaubach, R. M., and Gernet, N. J. (1992). Sodium heat pipe with sintered wick and artery: effects of noncondensible gas on performance. AIP Conf. Proc. 246 (1), 1153–1161. doi:10.1063/1.41778
Sterbentz, J. W., Werner, J. E., Hummel, A. J., Kennedy, J. C., O'Brien, R. C., Dion, A. M., et al. (2017). Preliminary assessment of two alternative core design concepts for the special purpose reactor. Idaho Falls, ID (United States): Idaho National Lab.INL.
Sun, H., Liu, X., Liao, H., Wang, C., Zhang, J., Tian, W., et al. (2022a). Experiment study on thermal behavior of a horizontal high-temperature heat pipe under motion conditions. Ann. Nucl. Energy 165, 108760. doi:10.1016/j.anucene.2021.108760
Sun, H., Pellegrini, M., Wang, C., Suzuki, S., Okamoto, K., Tian, W., et al. (2022b). CFD simulation based on film model of high temperature potassium heat pipe at different positions: horizontal, vertical, and 45° inclined. Prog. Nucl. Energy 154, 104442. doi:10.1016/j.pnucene.2022.104442
Sun, H., Wang, C., Liu, X., Tian, W., Qiu, S., and Su, G. (2018a). Reactor core design of micro nuclear power source applied for underwater vehicle. Atomic Energy Sci. Technol. 52 (04), 646–651. doi:10.7538/yzk.2017.youxian.0465
Sun, H., Wang, C., Ma, P., Liu, X., Tian, W., Qiu, S., et al. (2018b). Conceptual design and analysis of a multipurpose micro nuclear reactor power source. Ann. Nucl. Energy 121, 118–127. doi:10.1016/j.anucene.2018.07.025
Sun, H., Zhang, R., Wang, C., Deng, J., Tian, W., Qiu, S., et al. (2020). Reactivity feedback evaluation during the start-up of the heat pipe cooled nuclear reactors. Prog. Nucl. Energy 120, 103217. doi:10.1016/j.pnucene.2019.103217
Sun, K., Hu, L.-W., and Forsberg, C. (2016). Neutronic design features of a transportable fluoride-salt-cooled high-temperature reactor. J. Nucl. Eng. Radiat. Sci. 2 (3), 031003. doi:10.1115/1.4032873
Swartz, M. M., Byers, W. A., Lojek, J., and Blunt, R. (2021). “Westinghouse eVinci™ heat pipe micro reactor technology development,” in 28th International conference on nuclear engineering, virtual conference, ASME. doi:10.1115/ICONE28-67519
Tang, S., Wang, C., Liu, X., Tian, Z., Su, G. H., Tian, W., et al. (2020). Experimental investigations on start-up performance of static nuclear reactor thermal prototype. Int. J. Energy Res. 44 (4), 3033–3048. doi:10.1002/er.5134
Tang, S., Wang, C., Zhang, D., Tian, W., Su, G., and Qiu, S. (2021). Thermoelectric performance study on a heat pipe thermoelectric generator for micro nuclear reactor application. Int. J. Energy Res. 45 (8), 12301–12316. doi:10.1002/er.6450
Teng, W., Wang, X., and Zhu, Y. (2020). Experimental investigations on start-up and thermal performance of sodium heat pipe under swing conditions. Int. J. Heat. Mass Transf. 152, 119505. doi:10.1016/j.ijheatmasstransfer.2020.119505
Tian, Z., Liu, X., Wang, C., Zhang, D., Tian, W., Qiu, S., et al. (2021). Experimental investigation on the heat transfer performance of high-temperature potassium heat pipe for nuclear reactor. Nucl. Eng. Des. 378, 111182. doi:10.1016/j.nucengdes.2021.111182
Tian, Z., Wang, C., Guo, K., Zhang, D., Tian, W., Qiu, S., et al. (2022a). Parameters sensitivity analys is and optimization of high-temperature heat pipe for heat pipe reactor. Nucl. Power Eng. 43 (06), 85–92. doi:10.13832/j.jnpe.2022.06.0085
Tian, Z., Zhang, J., Wang, C., Guo, K., Liu, Y., Zhang, D., et al. (2022b). Experimental evaluation on heat transfer limits of sodium heat pipe with screen mesh for nuclear reactor system. Appl. Therm. Eng. 209, 118296. doi:10.1016/j.applthermaleng.2022.118296
Walker, K. L., Tarau, C., and Anderson, W. G. (2013). “High temperature heat pipes for space fission power,” in 11th international energy conversion engineering conference (San Jose, CA: AIAA).
Wang, C., Liu, X., Liu, M., Tang, S., Tian, Z., Zhang, D., et al. (2021). Experimental study on heat transfer limit of high temperature potassium heat pipe for advanced reactors. Ann. Nucl. Energy 151, 107935. doi:10.1016/j.anucene.2020.107935
Wang, C., Sun, H., Tang, S., Tian, W., Qiu, S., and Su, G. (2020a). Thermal-hydraulic analysis of a new conceptual heat pipe cooled small nuclear reactor system. Nucl. Eng. Technol. 52 (1), 19–26. doi:10.1016/j.net.2019.06.021
Wang, C., Sun, K., Hu, L.-W., Qiu, S., and Su, G. H. (2016). Thermal-hydraulic analyses of transportable Fluoride salt–cooled high-temperature reactor with CFD modeling. Nucl. Technol. 196 (1), 34–52. doi:10.13182/NT15-42
Wang, C., Tang, S., Liu, X., Su, G. H., Tian, W., and Qiu, S. (2020b). Experimental study on heat pipe thermoelectric generator for industrial high temperature waste heat recovery. Appl. Therm. Eng. 175, 115299. doi:10.1016/j.applthermaleng.2020.115299
Wang, C., Zhang, D., Qiu, S., Tian, W., Wu, Y., and Su, G. (2013). Study on the characteristics of the sodium heat pipe in passive residual heat removal system of molten salt reactor. Nucl. Eng. Des. 265, 691–700. doi:10.1016/j.nucengdes.2013.09.023
Wang, C., Zhang, L., Liu, X., Tang, S., Qiu, S., and Su, G. H. (2020c). Experimental study on startup performance of high temperature potassium heat pipe at different inclination angles and input powers for nuclear reactor application. Ann. Nucl. Energy 136, 107051. doi:10.1016/j.anucene.2019.107051
Wang, C., Zhang, Z., Zhang, M., Li, P., Tian, Z., Tian, W., et al. (2022). Numerical evaluation of non-condensable gas influence on the heat transfer characteristics of high-temperature lithium heat pipe during reactor operation. Ann. Nucl. Energy 173, 109077. doi:10.1016/j.anucene.2022.109077
Wang, E., and Li, L. (2023). Numerical analysis of high temperature potassium heat pipe under marine condition. Int. Commun. Heat. Mass Transf. 147, 106978. doi:10.1016/j.icheatmasstransfer.2023.106978
Wang, X., Shi, Y., Liu, T., Wang, S., Wang, K., Chen, H., et al. (2022c). CFD modeling of liquid-metal heat pipe and hydrogen inactivation simulation. Int. J. Heat. Mass Transf. 199, 123490. doi:10.1016/j.ijheatmasstransfer.2022.123490
Wei, G., Chai, B., Han, Z., Zhang, Y., Feng, B., Bi, K., et al. (2021). Experimental study on heat transfer performance of high temperature sodium heat pipe. Atomic Energy Sci. Technol. 55 (06), 1039–1046. doi:10.7538/yzk.2021.youxian.0115
WNA (2020). Generation IV nuclear reactors. Available at: https://world-nuclear.org/information-library/nuclear-fuel-cycle/nuclear-power-reactors/generation-iv-nuclear-reactors.aspx.
Wu, M., Ji, Y., Feng, Y., Liu, H., and Yang, X. (2023a). Experimental study on the effects of filling ratios on heat transfer characteristics of liquid metal high-temperature oscillating heat pipes. Int. J. Heat. Mass Transf. 209, 124153. doi:10.1016/j.ijheatmasstransfer.2023.124153
Wu, M., Ji, Y., Feng, Y., Yang, X., Li, Y., and Liu, Q. (2022). “Experimental investigation on the effects of inclination angle on heat transfer performance of a liquid metal high-temperature oscillating heat pipe,” in ASME 2021 heat transfer summer conference. Virtual (ASME). doi:10.1115/HT2021-63718
Wu, Y., Zheng, Y., Tao, Y., Liu, X., Du, X., and Wang, Y. (2023b). The low-enriched uranium core design of a MW heat pipe cooled reactor. Nucl. Eng. Des. 404, 112195. doi:10.1016/j.nucengdes.2023.112195
Yang, H., Wang, C., Zhang, D., Zhang, J., Tian, W., Qiu, S., et al. (2022). Parameter sensitivity study on startup characteristics of high temperature potassium heat pipe. Nucl. Eng. Des. 392, 111754. doi:10.1016/j.nucengdes.2022.111754
Yao, C., Hu, G., Zhao, S., Xie, J., Guo, J., and Gao, J. (2016a). Scheme research of Mars surface nuclear reactorpower. Atomic Energy Sci. Technololgy 50 (08), 1449–1455. doi:10.7538/yzk.2016.50.08.1449
Yao, C., Zhao, S., Hu, G., Xie, J., Guo, J., and Gao, J. (2016b). “Scheme research of Mars surface nuclear reactor power,” in 20th pacific basin nuclear conference (Beijing, China: Spinger).
Yu, Q., Zhao, P., and Ma, Y. (2022). CFD analysis on characteristics of high temperature heat pipe. Nucl. Power Eng. 43 (02), 70–76. doi:10.13832/j.jnpe.2022.02.0070
Yuan, Y., Gou, J., Shan, J., Zhang, B., and Zhang, B. (2016a). Startup characteristics of heat pipe cooled space reactor. Atomic Energy Sci. Technol. 50 (06), 1054–1059. doi:10.7538/yzk.2016.50.06.1054
Yuan, Y., Shan, J., Zhang, B., Gou, J., Zhang, B., Lu, T., et al. (2016b). Study on startup characteristics of heat pipe cooled and AMTEC conversion space reactor system. Prog. Nucl. Energy 86, 18–30. doi:10.1016/j.pnucene.2015.10.002
Zhang, H., Ye, F., Guo, H., and Yan, X. (2021d). Sodium-potassium alloy heat pipe under Geyser Boiling experimental study: heat transfer analysis. Energies 14 (22), 7582. doi:10.3390/en14227582
Zhang, J., Tian, Z., Wang, C., Tian, W., Guo, K., Qiu, S., et al. (2022c). Study on heat transfer limitationof liquid metal high-temperature heat pipe. Atomic Energy Sci. Technol. 56 (10), 2024–2031. doi:10.7538/yzk.2021.youxian.0806
Zhang, K., Yue, K., Yan, X., and Tong, W. (2020b). Study on lsothermal characteristics of gravity cesium heat pipe. ACTA METROL. SIN. 41 (01), 26–31. doi:10.3969/j.issn.1000-1158.2020.01.06
Zhang, M., Miao, Q., Zhang, S., Ma, Y., Ding, S., Zhang, Z., et al. (2023). Experimental study of non-condensable gas effects on sonic limit of sodium heat pipe. Appl. Therm. Eng. 232, 120970. doi:10.1016/j.applthermaleng.2023.120970
Zhang, M., Wang, C., Sun, H., Dai, Z., Zhang, D., Tian, W., et al. (2021a). Non-condensable gas generation behavior in high-temperature lithium heat pipe under irradiation. Atomic Energy Sci. Technol. 55 (06), 1024–1030. doi:10.7538/yzk.2020.youxian.0482
Zhang, M., Wang, C., Tian, Z., Guo, K., Tian, W., Su, G., et al. (2022a). Study on influence of non-condensable gas on heat transfer characteristics of high temperature lithium heat pipe. Atomic Energy Sci. Technol. 56 (06), 1094–1103. doi:10.7538/yzk.2021.youxian.0901
Zhang, W., Zhang, D., Wang, C., Tian, W., Qiu, S., and Su, G. H. (2020a). Conceptual design and analysis of a megawatt power level heat pipe cooled space reactor power system. Ann. Nucl. Energy 144, 107576. doi:10.1016/j.anucene.2020.107576
Zhang, Z., Chai, X., Wang, C., Sun, H., Zhang, D., Tian, W., et al. (2021b). Numerical investigation on startup characteristics of high temperature heat pipe for nuclear reactor. Nucl. Eng. Des. 378, 111180. doi:10.1016/j.nucengdes.2021.111180
Zhang, Z., Wang, C., Guo, K., Huang, J., Qiu, S., Su, G. H., et al. (2022b). HEART, a specific code for thermal-electrical analysis of heat pipe cooled nuclear reactor. Int. J. Therm. Sci. 179, 107666. doi:10.1016/j.ijthermalsci.2022.107666
Zhang, Z., Wang, C., Sun, H., Zhang, D., Qiu, S., Su, G., et al. (2021c). Analysis of startup characteristics for alkali metal high temperature heat pipe. Atomic Energy Sci. Technol. 55 (06), 1015–1023. doi:10.7538/yzk.2020.youxian.0464
Zhao, J., Yuan, D., Tang, D., Cao, K., and Ji, Y. (2021). Analytical and experimental study of the high temperature heat pipe sonic limitation. J. Eng. Thermophys. 42 (03), 700–705.
Zhong, R., Ma, Y., Deng, J., Liu, Y., Chai, X., and Wang, J. (2021). Reactor startup characteristics of heat pipe cooled reactor with multiple feedback mechanism. Nucl. Power Eng. 42 (S2), 104–108. doi:10.13832/j.jnpe.2021.S2.0104
Zohuri, B., and McDaniel, P. (2019). Design and analysis of core design for small modular reactors. Adv. Smaller Modul. React. 2019, 187–217. doi:10.1007/978-3-030-23682-3_9
Keywords: heat pipe, alkali metal, heat pipe reactor, heat transfer performance, conceptual design
Citation: Wang E, Ren T and Li L (2023) Review of reactor conceptual design and thermal hydraulic characteristics for heat pipe in nuclear systems. Front. Energy Res. 11:1264168. doi: 10.3389/fenrg.2023.1264168
Received: 20 July 2023; Accepted: 23 November 2023;
Published: 04 December 2023.
Edited by:
Vivek P. Utgikar, University of Idaho, United StatesReviewed by:
Xiaodong Sun, University of Michigan, United StatesCopyright © 2023 Wang, Ren and Li. This is an open-access article distributed under the terms of the Creative Commons Attribution License (CC BY). The use, distribution or reproduction in other forums is permitted, provided the original author(s) and the copyright owner(s) are credited and that the original publication in this journal is cited, in accordance with accepted academic practice. No use, distribution or reproduction is permitted which does not comply with these terms.
*Correspondence: Lei Li, bGlsZWloZXVAaHJiZXUuZWR1LmNu
Disclaimer: All claims expressed in this article are solely those of the authors and do not necessarily represent those of their affiliated organizations, or those of the publisher, the editors and the reviewers. Any product that may be evaluated in this article or claim that may be made by its manufacturer is not guaranteed or endorsed by the publisher.
Research integrity at Frontiers
Learn more about the work of our research integrity team to safeguard the quality of each article we publish.