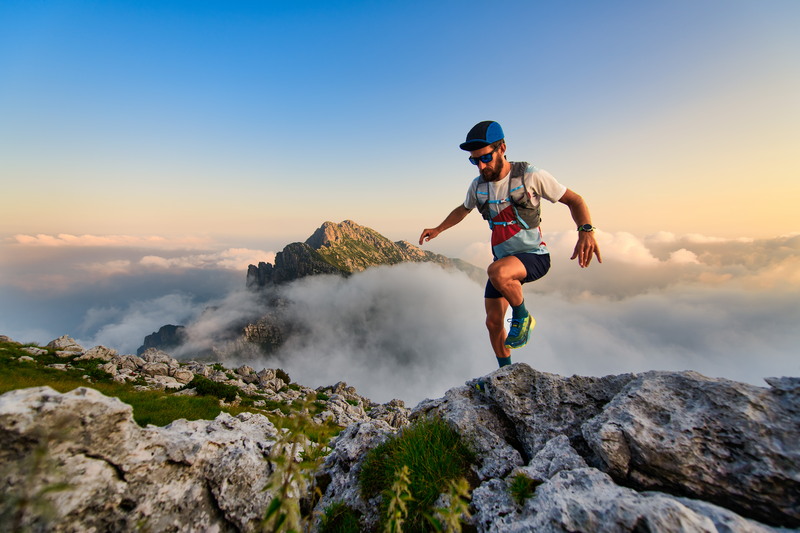
94% of researchers rate our articles as excellent or good
Learn more about the work of our research integrity team to safeguard the quality of each article we publish.
Find out more
EDITORIAL article
Front. Energy Res. , 30 June 2023
Sec. Process and Energy Systems Engineering
Volume 11 - 2023 | https://doi.org/10.3389/fenrg.2023.1238721
This article is part of the Research Topic Optimal Design and Efficiency Improvement of Fluid Machinery and Systems View all 18 articles
Editorial on the Research Topic
Optimal design and efficiency improvement of fluid machinery and systems
Fluid machinery plays a pivotal role in facilitating human development by encompassing vital equipment such as water turbines, wind turbines, pumps, torque converters, and low-pressure fans. However, despite its extensive applications, practical engineering encounters several challenges, including suboptimal equipment efficiency, unstable operation, and system discrepancies. The introduction of concepts such as “carbon peak” and “carbon neutrality” has further underscored the significance of high-efficiency fluid machinery in energy conservation and carbon reduction efforts. As a result, the advancement of fluid machinery technology has garnered substantial global attention and emerged as a crucial research area in the realm of energy-saving and carbon reduction. This Research Topic specifically focuses on the design and optimization of fluid machinery and its associated systems, employing experimental and numerical calculation methods to enhance operational efficiency, safety, and economic benefits. Notably, following a rigorous peer-to-peer review process, 17 articles have been accepted for inclusion in this Research Topic, which encompass the following categories.
Qi et al. conducted an optimization study on centrifugal pumps to enhance theirperformance. They combined entropy generation theory with particle swarm optimization to compare and analyze the energy losses between the original and optimized models. As a result, the pump efficiency increased by 3.89%. The optimization method employed in this research offers valuable support to the theory of centrifugal pump optimization. In order to improve the operational optimization of water pump production models, Xu et al. compared various indicators, including inventory, productivity, and delivery rate of water pumps, among traditional make-to-order (MTO) model, make-to-stock (MTS) model, and MTO and MTS model. Following a comprehensive evaluation, the MTO and MTS production model was determined as the most favorable choice for pumps. Sun et al. acknowledged the significant changes in the geometric characteristics of leading edge erosion on wind airfoils. They explored the impact of different blade shapes on the aerodynamic performance of NACA series airfoils under various working conditions. The results indicated that an optimal blade thickness range exists when considering leading edge erosion. Tian et al. conducted a study on the optimal design of submersible mixers using the coupled CFD-DEM method within the Euler-Lagrange framework. They examined the solid-liquid two-phase flow field of submersible mixers installed at different heights and analyzed the motion characteristics of particles, the extent of mixing, and the reasons for aggregation. The article demonstrated that adjusting the installation position of submersible mixers can enhance their energy utilization efficiency. Furthermore, Tian et al. utilized installation position parameters as design variables and performed a multi-objective optimized design using the Non-dominated Sorting Genetic Algorithm (NSGA-II). The results revealed an improvement of approximately 0.47% in mixing efficiency compared to pre-optimization values. To address the limitation of using a single type of parameter as the design parameter, Chen et al. selected a typical mixed-flow pump as the research subject and improved its efficiency using the Taguchi method. Their aim was to overcome the decrease in the optimization upper limit. Cheng et al. investigated the internal flow and rotor force characteristics of Canned Motor Pumps (CMP) under different radial clearances of front or back wear-rings and varying volute partitions. They discovered that adding a clapboard to the volute can enhance the balance of the radial force, providing a theoretical basis and reference for the hydraulic optimization of CMP.
Lv et al. conducted a numerical analysis of the internal flow and pressure pulsation characteristics of a submersible tubular electric pump device. The validity of the numerical simulation was confirmed through physical model testing. Their findings indicate that the impeller of the submersible tubular electric pump is primarily responsible for the inlet pressure pulsation of the impeller. Guo et al. investigated the fluid movement law, energy transfer, and loss mechanism in the impeller of an axial flow pump. They successfully identified the main cause of hydraulic losses in the impeller flow passage. This research provides valuable insights into understanding the flow field structure within the impeller of the axial flow pump. Liu et al. (Liu et al., 2023) studied the flow characteristics and evolution of vorticity force in liquid nitrogen cavitation flow using a two-phase flow model and an improved thermal cavitation model. Their research reveals the internal flow mechanism of fluid machinery and offers theoretical guidance for the design of such machinery. Tian et al. examined the internal flow characteristics of low-head bulb perfusion pumps and analyzed the entropy production of essential components. They discovered that the water entropy production head decreases gradually and then increases, with the ratio of entropy production at the impeller to total entropy production being the largest. Xu et al. presented an adaptive mesh refinement technique for simulating compressible flows. This technique effectively refines the mesh in regions containing shock waves and vortices. Numerical results demonstrate that the proposed technique successfully captures shock waves and vortices, leading to improved solution accuracy.
Hong et al. introduced a two-dimensional vortex model to gain insights into the characteristics of shedding vortices in a blade-divergent passage. They proposed a negative circulation unsteady flow control technique as a means to compensate for the viscous effect. The study revealed that this technique is more efficient than conventional flow control methods in mitigating shedding vortex strength. Xu et al. developed an electro-hydraulic composite drive winch and energy recovery system for mobile cranes. Based on electric construction machinery equipped with high-pressure energy-density electric energy storage units, this system incorporates a control strategy to ensure high torque output even at near-zero speeds. Li et al. presented a flywheel-based boom energy regeneration system for hydraulic excavators (HEs) utilizing load sensing systems. In a typical digging and dumping cycle, the energy-saving rate achieved with this system is approximately 32.7% higher compared to conventional load-sensing systems. This method holds promise for the development of energy-efficient HEs. To enhance the uniformity of water distribution under low pressure conditions, Qureshi et al. introduced the aeration jet method for the design of an aeration impact sprinkler. They also presented the structural details of the aeration impact sprinkler. The study demonstrated the feasibility of this method in reducing the operational pressure of sprinklers and improving water uniformity coefficient. Considering the insufficient accuracy of existing cavitation fault feature identification, (Chen et al., 2023) constructed a cavitation state recognition model. By combining current and vibration signals and leveraging information fusion theory, this model aims to improve the recognition rate of cavitation states and enhance anti-interference performance.
In summary, this Research Topic encompasses a wide range of research articles focused on the optimal design and efficiency improvement of fluid machinery and systems. The published articles delve into various aspects of this field, exploring innovative approaches and methodologies. Notably, there is a growing trend towards integrating advanced technologies such as the Internet of Things (IoT) and next-generation communication technologies to enhance the performance and intelligence of fluid machinery. By highlighting these advancements, this Research Topic aims to enrich people’s understanding of fluid machinery and elevate its application level across diverse fields. The knowledge shared through this Research Topic of articles will contribute to the continuous improvement and evolution of fluid machinery, driving innovation and progress in various industries. Ultimately, the goal is to optimize the performance, efficiency, and intelligence of fluid machinery, enabling its widespread application and benefiting society as a whole.
All authors listed have made a substantial, direct, and intellectual contribution to the work and approved it for publication.
LJ was supported by the China Postdoctoral Science Foundation (No.2022TQ0127). YY was supported by the Natural Science Foundation of Jiangsu Province (No. BK20220587).
The authors declare that the research was conducted in the absence of any commercial or financial relationships that could be construed as a potential conflict of interest.
All claims expressed in this article are solely those of the authors and do not necessarily represent those of their affiliated organizations, or those of the publisher, the editors and the reviewers. Any product that may be evaluated in this article, or claim that may be made by its manufacturer, is not guaranteed or endorsed by the publisher.
Keywords: fluid machinery and system, design and optimization, efficiency improvement, unsteady flow, computational fluid dynamics
Citation: Ji L, Agarwal RK, Kan K, Tao R, Yang Y and Presas A (2023) Editorial: Optimal design and efficiency improvement of fluid machinery and systems. Front. Energy Res. 11:1238721. doi: 10.3389/fenrg.2023.1238721
Received: 12 June 2023; Accepted: 23 June 2023;
Published: 30 June 2023.
Edited and reviewed by
Ellen B. Stechel, Arizona State University, United StatesCopyright © 2023 Ji, Agarwal, Kan, Tao, Yang and Presas. This is an open-access article distributed under the terms of the Creative Commons Attribution License (CC BY). The use, distribution or reproduction in other forums is permitted, provided the original author(s) and the copyright owner(s) are credited and that the original publication in this journal is cited, in accordance with accepted academic practice. No use, distribution or reproduction is permitted which does not comply with these terms.
*Correspondence: Yang Yang, eWFuZ195YW5nQHl6dS5lZHUuY24=
Disclaimer: All claims expressed in this article are solely those of the authors and do not necessarily represent those of their affiliated organizations, or those of the publisher, the editors and the reviewers. Any product that may be evaluated in this article or claim that may be made by its manufacturer is not guaranteed or endorsed by the publisher.
Research integrity at Frontiers
Learn more about the work of our research integrity team to safeguard the quality of each article we publish.