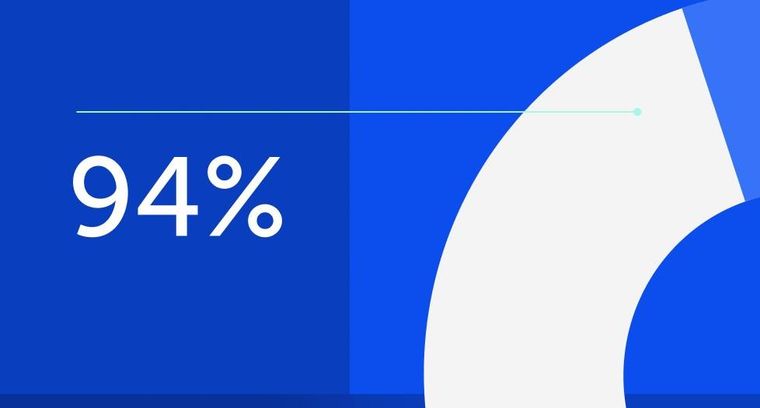
94% of researchers rate our articles as excellent or good
Learn more about the work of our research integrity team to safeguard the quality of each article we publish.
Find out more
ORIGINAL RESEARCH article
Front. Energy Res., 30 June 2023
Sec. Smart Grids
Volume 11 - 2023 | https://doi.org/10.3389/fenrg.2023.1190174
This article is part of the Research TopicRecent Advances in Flexibility Analysis and Regulation Technology of Clean Energy SystemView all 7 articles
Electrification of processes and utilities is considered a promising option towards the reduction of greenhouse gas emissions from the chemical industry. Therefore, electricity demand is expected to increase steeply. Since the sources of future low-carbon electricity are variable in nature, there is a need for strategies to match availability and demand. Literature identified the flexibility of chemical processes as one promising strategy to address variability. This study aims to provide insights into how stakeholders from the power sector and the chemical industry consider flexibility in chemical processes and to identify key benefits and bottlenecks. For this article, we combined a review of peer-reviewed and grey literature with stakeholder interviews to map and describe the state of the art of flexible chemicals production, and to identify requirements for further research. The main drivers to investigate the flexibility potential are first, the contribution to energy system reliability, and second, potential cost savings for the industry. Main limitations are considered to be first, the uncertain economic performance of flexible processes due to investment costs, reduced production and uncertain revenues from flexible operation, and second, the complexity of the implementation of flexibility.
To limit the impact of climate change on ecosystems and on life on Earth, joint efforts are needed to cap the concentration of greenhouse gases (GHG) in the atmosphere. Consequently, all sectors of the world’s economic system must stop emitting GHG like carbon dioxide (CO2) as soon as possible. The urge to speed up the decrease of GHG emissions has been stated in several reports at international level, such as the latest IPCC report (Skea et al., 2022), the IEA’s roadmap towards net zero by 2050 (International Energy Agency, 2021) or in the pledges made during COP27 in Egypt (United Nations Secretaty-General, 2022). In 2019, 44% of global CO2 emissions were caused for the generation of electricity and heat (IEA, 2021). To reach the net zero CO2 emission goal, a key pathway is a deployment of renewable energy sources (RES) like solar power and wind energy.
However, these energy sources, are inherently variable, hence scheduling or influencing how much electricity is produced at a given moment is difficult. To guarantee a stable electricity supply, intake and outtake from the power grid must be balanced. Grid balancing is required in the short and long term (to address seasonal imbalances), so with increasing RES deployment, there is an increased requirement for options that can supply balancing services at all timescales (Blanco and Faaij, 2018).
Looking at the global CO2 emissions resulting from fuel combustion, the industrial sector accounts for 39% (IEA, 2021), and after cement and iron and steel production, the chemical industry is the third largest industrial emitter (IEA, 2022). Therefore, it is necessary to defossilize the chemical industry to reach emission reduction goals. Industry’s GHG emissions are caused by the fossil-fueled generation of heat and electricity required in the process(es) and by the use of fossil carbon as a feedstock. Typical examples are the use of naphtha in the production of olefins, natural gas to produce ammonia, limestone to produce cement or the use of coal in steel production. Therefore, solutions must be found to decrease the energetic and non-energetic use of fossil carbon.
Direct electrification of processes and utilities such as heat is considered a promising alternative to replace fossil-based sources of process energy (TNO et al., 2021) and hydrogen from water electrolysis (indirect electrification) is foreseen to play a crucial role, as a carbon emission-free energy carrier and as a feedstock (Bazzanella and Ausfelder, 2017; CEFIC, 2019). In scenarios where electrification and low-carbon hydrogen are implemented in the European production of ammonia, methanol, ethylene, propylene, chlorine, benzene, toluene and xylene to achieve a CO2 emission reduction of 84% by 2050, 16.6 EJ of low-carbon electricity are required, i.e., 135% of the expected European electricity production in 2050 (Bazzanella and Ausfelder, 2017). Another estimation is that the decarbonization of global ammonia, methanol, olefins and aromatics production in 2050 with an assumed growth of demand of 50% would require 65 EJ of low-carbon electricity, and 14 EJ of fossil fuels (resulting in 0.2 billion tons of CO2), which is a 6.6-fold increase of the current energy demand (12 EJ) (Eryazici et al., 2021).
The foreseen increase in electricity consumption of the chemical industry, and the intermittency of low-carbon electricity consolidate the need for options to address problems in matching source and demand. One option that has been identified in literature, to offer flexibility on the demand side, is to adjust the production schedule of chemical plants according to the available electricity generation (Klaucke et al., 2017). Flexible production of chemicals has therefore gained attention in literature as an option for both, short-term grid balancing via demand side management (DSM) (Otashu and Baldea, 2018) and mid- or long-term balancing as a form of energy storage in chemical bonds (Schiffer and Manthiram, 2017; De Luna et al., 2019), often referred to as Power-to-Chemicals.
Industrial demand side management has been discussed in literature (Paulus and Borggrefe, 2011; Olsthoorn et al., 2015; Shoreh et al., 2016; Shafie-Khah et al., 2019; Richstein and Hosseinioun, 2020; Siddiquee et al., 2021; Lashmar et al., 2022; Leinauer et al., 2022), but little attention has been paid to the chemical industry (the authors know of one study by Klaucke et al. (2017) available in German). It is not clear which impact flexible production of chemicals could have on the industry and on the power sector, and if both sectors have a common perspective on flexibility. Regarding the expected steep increase in electricity demand in the chemical industry and the importance of flexibility for the stability of the future electricity grid, it is crucial to address this knowledge gap.
In this article, we map and describe the state of the art of flexible chemicals production as a measure to cope with variable electricity supply. We present the potential benefits, limitations and requirements and identify where further research is needed. We combine a review of peer-reviewed and grey literature with stakeholder interviews to provide an overview of expectations and requirements from different perspectives, to detect options for synergies or bottlenecks. The paper shows that the discussions about flexibility in peer-reviewed literature and within the power sector are to a large extent not mirrored in industrial publications from the chemical industry. The analysis of industry publications and stakeholder interviews added several requirements and limitations for actual deployment as seen by industrial stakeholders that were not considered in previous scientific studies. This paper, therefore, provides valuable insights for future sector-coupling between the power sector and the chemical industry.
The remainder of this paper is organized as follows. Section 2 describes the methodology that was chosen for this study. Section 3 presents the state of the art in literature and the perspective of industrial stakeholders. Finally, Section 4 provides the conclusions and recommendations for further research.
For this article, we reviewed peer-reviewed and grey literature (i.e., reports of knowledge institutes, industrial associations and consulting firms) to analyse if and how flexibility in chemical processes has been studied and whether there are differences in the way it is discussed in the chemical industry and the energy sector. We complemented the literature review with stakeholder interviews.
In the literature review, we included publications that discuss flexibility in the context of the energy transition and did not consider studies that address industrial demand response in general, unless one or more chemical processes were included in the study. Using a keyword search as well as the snowball method, we found 44 peer-reviewed publications that matched the scope.
For the analysis of industry publications and for the interviews, stakeholders from the Dutch industry were selected. In the Netherlands, the chemical sector has the highest energy demand in the industrial sector, both in terms of energy use (43%) and in terms of feedstock (97%) (TNO et al., 2021), and it accounted for 11% of total electricity demand in 2018 (TenneT, 2021). As a result, the chemical industry was responsible for 44% of the Dutch industrial GHG emissions (OECD, 2021). The Dutch industry comprises five large petrochemical clusters, including the Port of Rotterdam (PoR) where the entire value chain is covered from chemical building blocks (for instance propylene, ethylene, benzene) to high-value chemicals (for instance, PVC, polyols, acetic acid). The PoR has five oil refineries (85 million tonnes total distillation capacity), one olefins plant (annual ethylene production of 900 kt/year) and seven sub-clusters, including an ethylene cluster, a propylene cluster, an aromatics cluster and a chlorine cluster. In 2021, the chemical industry at the PoR accounted for 4% of the Dutch GHG emissions (Statistics Netherlands, 2022; Port of Rotterdam, 2023). The Dutch clusters are similar (in terms of the type of processes, capacities and feedstocks) to other petrochemical clusters inside Europe (like Antwerp, Tarragona, Lyon or Hoechst) and outside Europe (e.g., in Texas, and Shanghai), where both, building blocks and intermediates are produced. The Dutch chemical industry is representative of the global chemical sector and key insights gained in this study can also apply in different geographical contexts. It is also important to note that as the Dutch power and chemical sectors are subject to European climate targets, the use of flexibility as a potential demand response option is relevant beyond the Dutch boundaries.
The interview series consisted of six interviews with a total of eight participants (see Table 1) and were conducted in October/November 2021. The interviews were aimed to verify and complement information from literature and are not a representative survey of the Dutch industry.
The interviews with stakeholders from the petrochemical industry aimed to 1) identify whether electrification and hydrogen use play a role in their current GHG emission mitigation strategies, 2) understand whether they have considered flexible production as a viable option to handle intermittent electricity supply, and 3) to find out whether they have considered the possibility of generating revenues from providing grid balancing services to the grid as an interesting business opportunity. The main objectives for the interview with stakeholders from the power sector were to 1) understand which role grid operators assign to the chemical industry as a provider for demand response (DR) or other grid stabilizing services and, 2) find out whether they have identified specific barriers for collaborating with the chemical sector. The interviews were semi-structured, the questions and notes can be found in the supplementary material. Relevant information for this study was extracted from the notes after the interviews took place.
Literature and interviews were analysed and compared regarding identified potential benefits (Table 3), requirements (Table 4), and expected limitations and trade-offs (Table 5). Based on the literature study and the interviews, knowledge gaps were identified.
Literature studied flexibility of chemical processes in the context of the energy transition from different perspectives, namely, from the energy system perspective (Paulus and Borggrefe, 2011; Gruber, 2017; Nayak-Luke et al., 2018; Gusain et al., 2020; Richstein and Hosseinioun, 2020; Tuinema et al., 2020; Mukelabai et al., 2021; Kiviluoma et al., 2022) and from the industry perspective (remaining studies in Table 2). The studies had different objectives, such as the identification of requirements and challenges (Zhang and Grossmann, 2016; Riese and Grünewald, 2020), the quantification of aggregated flexibility potential (Klaucke et al., 2017) and the analysis of the potential of a single plant or process (Table 2). The majority of publications analyze the flexibility potential of a single industry or process, partly including the application for demand response. Despite the number of publications, the range of production processes that have been studied is limited to mainly electrochemical processes, with most of these studies focusing on chlorine production. Chlorine production is a process based on electrochemical conversion, with electricity costs having a high share in overall production costs [50%–70% (euro chlor 2022)], which may explain the attention given to the process. Furthermore, the process does not require continuous operation and has a high installed capacity, which means that flexible capacity is likely to influence grid reliability (Paulus and Borggrefe, 2011; Gruber, 2017; Klaucke et al., 2017). Next to the production of chlorine, publications cover the production of hydrogen, ammonia, methane, methanol, synthetic natural gas, ethylene oxide and formic acid. The studies considered either the process designed as implemented in the industry today (Gruber 2017; Otashu and Baldea (2018; 2019; 2020; Otashu et al., 2021; Richstein and Hosseinioun, 2020; Kelley et al., 2022; Bruns et al., 2021), modifications to the design aiming to increase flexibility [Brée et al. (2020; 2019); Bruns et al. (2022a); Hofmann et al. (2022); Bruns et al. (2022b); Germscheid et al. (2022); Lahrsen et al. (2022); Di Pretoro et al. (2022); Hochhaus et al. (2023); Klaucke et al. (2023)] or they propose a completely new design (Nayak-Luke et al., 2018; Fischer and Freund, 2020; Chen and Yang, 2021; Mukelabai et al., 2021; Bruns et al., 2022b; Herrmann et al., 2022; Samani et al., 2022; Semrau and Engell, 2023). All authors used modelling for simulation or optimization to study the flexibility potential, capturing the complexity of the processes with varying levels of detail, ranging from a simplified representation as a battery to dynamic process modelling. Only one study (Brée et al., 2020) compared options to increase the flexibility capacity of an existing process by using auxiliary units, namely, a water electrolyzer, a fuel cell and a redox flow battery. Optimization has often been used to find the least cost solutions with regard to the cost of production or electricity costs, using historical data for electricity prices and market prices from different balancing markets. Not all studies considered investment costs in their models.
TABLE 2. List of publications that analyze the flexibility potential of individual processes, showing the product(s) they were focusing on and if they considered a design based on existing process technology or a new process design.
An analysis of companies’ sustainability roadmaps (DBI Gas-und Umwelttechnik GmbH et al., 2020; DNV GL 2020; Eneco 2021; RWE AG 2022; Uniper 2022; Nobian Industrial Chemicals B.V. 2022; bp p.l.c. 2022; Netbeheer Nederland 2021; Vattenfall 2021; Engie 2022; Total SE 2020; Dow 2022; Huntsman Corporation 2022; Eastman 2021; BASF 2022; ExxonMobil 2022; SABIC 2022; Dupont 2022; Lyondellbasell 2021; Kirby et al., 2022; Yara International ASA 2021; Avantium 2020; Air Liquide, 2021; Shin-Etsu Chemical Co. Ltd.2022; Air Products and Chemicals Inc, 2021; Vattenfall AB 2022) depicted in Figure 1 shows that the possibility of operating processes flexibly is not only being discussed in literature, but it is also on the agenda of industrial stakeholders from the energy sector domain. Especially grid operators have been highlighting potential benefits already for some years, and are interested in further developing the implementation (Berenschot et al., 2015; TenneT 2018; TenneT and vemw 2021; TenneT 2021). However, how the topic is being discussed among stakeholders from the power sector is different from what studies in literature are focusing on. In literature, studies assess the flexibility of individual processes (Table 2), whereas reports from the power sector focus on the estimation of the flexibility potential of the entire industrial sector. However, the Power to Products project (Berenschot et al., 2015) is an example project where several companies across industry and power sector assessed a possible implementation route and the business case of flexibility. They concluded that there is no general answer for the business case, as the assessment differs per case. Two out of five cases were positive, the remaining three were depending on future developments, e.g., market developments.
FIGURE 1. Consideration of flexibility in companies’ sustainability roadmaps, and company domains. A list of selected companies is shown in Table 6 in the Appendix.
In the selected company roadmaps from the chemical domain (for a list of companies see Table 6 in the appendix), flexibility is barely discussed, as shown in Figure 1. The roadmaps predominantly address GHG emission reduction measures, where electrification is considered a potential solution (among others), but the intermittency of the electricity supply is not mentioned, and neither are potential measures to cope with it, like flexibility. The lack of discussion around flexibility might point out that the awareness of the topic in the chemical industry is low.
To identify which assumptions exist about flexibility, we present potential benefits of flexibility, requirements and its limitations and trade-offs in the rest of this section. We compare what is being stated in peer-reviewed and grey literature to what is stated in industrial roadmaps, complemented with insights from the stakeholder interviews. Findings from stakeholder interviews are referenced with letters a to f that refer to Table 1 in Section 2.
Three potential benefits were identified (see Table 3). The first addresses power grid reliability. Power grid reliability as a reason for flexibility was mentioned by both, stakeholders from the power sector and the chemical industry [b, d, e, f], [DNV GL (2020)]. Studies looking at the consequences of fluctuations in electricity supply generally argue that flexibility in chemical processes can make an important contribution to the reliability of the grid since the chemical industry is among the largest industrial electricity consumers and therefore, the potential capacity available for grid balancing is high [Klaucke et al. (2017); Bruns et al. (2021); Zhang and Grossmann (2016)]. Klaucke et al. (2017) found that there was a significant DR potential in Germany for processes such as chlorine production. Results were based on a potentially flexible share of the nominal capacity multiplied by the installed capacity, and the results did not account for time-dependent conditions influencing the availability of a plant for DR, such as maintenance or production targets settled with customers. Gruber (2017) quantified the contribution of industrial flexibility for grid congestion reduction on regional level in Germany until 2030 but included only one chemical process in her study, chlorine production. Each process was represented by its available flexible capacity, defined as the difference between installed capacity and nominal capacity. Unlike in Klaucke et al. (2017), the study accounted for ramping times, duration of the change of operational mode and resulting changes in efficiencies, the frequency of shifting and times of non-availability due to maintenance, the time of the day and the season. The resulting potential is therefore lower than the potential found by Klaucke et al (2017). In addition to the potential flexibility of the processes, the potential flexibility of components like motors, pumps, ventilation systems, and heat or cooling storage has also been quantified. Taking hydrogen production from water electrolysis as another example, two studies [Tuinema et al. (2020); Gusain et al. (2020)] looked at the impact of a large-scale PEM electrolyser on system reliability: In Tuinema et al. (2020), a 1 MW electrolyser was found to have a positive effect on frequency stability (on a time scale of milliseconds to seconds), since it was able to respond faster to deviations than conventional generators. Gusain et al. (2020) showed that flexible operation could be used for grid balancing (on a time scale of 5–15 min) and that it had little impact on the lifetime of the electrolyser. The rising interest in hydrogen use from across all sectors indicates that the hydrogen production volume will increase in the future, hence it is important to assess the flexibility of the process. However, findings for water electrolysis can only give insights about (the parts of) the chemical processes that are based on electricity. The applicability to processes that are based on heat, such as the majority of current processes in petrochemistry, is limited.
TABLE 3. Potential benefits of flexibility according to peer-reviewed/grey literature and industry publications/interviews. Bold text indicates an agreement between the two.
Studies looking at the consequences of fluctuations in electricity supply from the perspective of the (chemical) industry point out that flexibility could also help industries to cope with fluctuations in electricity generation (Den Ouden et al., 2017; Wong and Van Dril, 2020) and enable a disconnection from the power grid by consuming electricity generated from RES that industries generate themselves. This would reduce the load on the electricity grid. As a beneficial side effect, it would also enable a decrease in industrial CO2 emissions, as shown in the case of ammonia production. For instance, by using an electrolyzer and a storage tank for hydrogen (Nayak-Luke et al., 2018), or with a reversible solid oxide fuel cell stack integrated with the Haber Bosch process (Mukelabai et al., 2021). The ability to cope with fluctuating electricity supply was also the motivation for Fischer and Freund (2020) to investigate the methanation of CO2 from renewable electricity as a form of chemical energy storage. The reactor was able to operate with a fluctuating hydrogen inflow between 50% and 100% of the maximum inflow. How this range relates to the intermittency of renewable electricity generation was not specified further.
The second benefit assigned to flexibility is the potential to decrease overall system costs. In the case of the power system, flexibility can increase the reliability of the grid in a more cost-effective way than installing backup power generation plants (Stork et al., 2018; TenneT, 2021). Reduction of system costs was also shown in Ganzer and Mac Dowell (2020) where the production of fuels and chemicals was studied as an integrated system (including feedstock production and process energy generation) from solely air, water and electricity from renewable sources. They found that the intermittency of electricity generation lead to additional costs (up to two-thirds of the total cost) compared to continuously available electricity because storage capacity was necessary to operate the system throughout the year. Assuming it was possible to vary the operation of one of the possible production routes by 50% to shift production between seasons, the flexible production route became the most cost-efficient option.
Reduced system costs were also found by Klyapovskiy et al. (2021), where the potential contribution of flexible production and consumption of hydrogen in an industrial cluster was quantified. The authors found that adapting hydrogen production and consumption to the availability of locally generated electricity decreased the operational costs of the energy system of the cluster by approximately 50%.
The third benefit is the reduction of production costs for individual industries, compared to continuous production. Two options to reduce production costs have been identified. First, by avoiding production during periods of high electricity prices via an active adaption of operation (Otashu and Baldea 2018; Otashu et al., 2021; Brée et al. (2019; 2020; Kelley et al., 2022; Bruns et al., 2022a), and second by process operation for power grid frequency regulation (Otashu and Baldea, 2020; Hoffmann et al., 2021; Samani et al., 2022), for which the electricity grid operator pays the plant operator. The first option is also seen as a possibility to overcome the electricity cost barrier that is attributed to electrification (Den Ouden et al., 2017). Note that the resulting economic performance strongly depends on the required investment and on assumptions about future electricity prices, like shown in the case of chlorine production with process modifications to increase process flexibility [Brée et al. (2019; 2020)]. Not only existing technology has been studied, but also novel production processes such as a fully electrified methanol production (Chen and Yang, 2021). Assuming a fully renewable electricity generation, the authors found that a flexible operation process decreased the levelised cost of methanol by 21% and 34% for the two electricity generation profiles chosen. Flexibility was achieved with flexible equipment (electrolyzer and methanol synthesis unit) and buffer facilities for energy and material flows. As discussed before, flexibility could enable a disconnection from the power grid by consuming electricity generated from RES that industries generate themselves. This could be financially beneficial for industries in three ways. First, it might lead to electricity cost savings if the electricity generated onsite is cheaper than the electricity purchased from the grid. Second, costs related to the grid connection of industries can be avoided (Roelofsen et al., 2020), and last, independence from electricity market prices would increase (Leinauer et al., 2022), which reduces the risk induced by the uncertainty of the development of electricity prices.
Flexible operation of chemical industries itself comes with requirements, deploying it for grid stabilizing services requires additional conditions. An overview is presented in Table 4.
TABLE 4. Requirements according to peer-reviewed/grey literature and industry publications/interviews. Bold text indicates an agreement between the two.
A fundamental requirement for flexible process operation is that the process, including all technical components, can be operated safely in a range of operating conditions while maintaining the quality of the product within a range that is acceptable for the company that owns the plant, and with an efficiency that is high over varying loads. There are several types of flexibility in chemical engineering, as described and analyzed by Bruns et al. (2020) and Luo et al. (2022). Key technical requirements for the kind of flexibility relevant to the application in the context of this article are the ability to, first, vary the electrical load of the process; second, to meet required ramping rates [TenneT and vemw (2021)] (the rate determines the qualification for grid stabilizing services); and third, the ability to react to requested changes in operation within a specific response time. The duration for which the flexibility can be offered is an important parameter, as well (Paulus and Borggrefe, 2011). If the change in electrical load is aimed to be a service that can be provided to an electricity grid operator, the specific values of the requirements described above are defined by the grid operator. Additionally, a data exchange infrastructure needs to be in place (Paulus and Borggrefe (2011), and sufficient grid capacity is a prerequisite [e].
Offering demand response capacity can be achieved in two ways, by increasing electricity intake, or by decreasing electricity demand. In case of the latter, if it is technically possible to increase production at a later point in time to make up for the production reduction, this is referred to as load shifting. Otherwise, if the production cannot be recovered, it is referred to as load relinquishment. If load shifting is considered, there needs to be a strategy that allows for it, such as installing excess capacity units for the process (Richstein and Hosseinioun (2020). However, Richstein and Hosseinioun (2020) indicated that the financial benefit for larger overcapacities decreases with increasing size of overcapacity since the most expensive electricity hours are avoided first. Hence, the amount of additional capacity that can be installed in a financially viable manner is limited. Another strategy to maintain the production volume that has been proposed is to use storage facilities, such as product buffers [a], (Arnold and Janssen (2016). Hence, products need to be storable [c]. Buffers come with additional investment, spatial requirements, and possible safety risks that need to be taken into account when this flexibility strategy is assessed.
In order for flexibility to be cost-effective for the industry there needs to be a business case, a level playing field between conventional, continuous operation and flexible operation (Baetens et al. (2021); Riese and Grünewald (2020); Den Ouden et al. (2017). This is influenced by the market price of the product, the electricity price, and the service payments from the grid operator, if applicable. Additional investment costs and fixed costs are relevant for the assessment of a business case, as well (Paulus and Borggrefe, 2011), and it has to be taken into account that efficiency of production might go down [a] and that losses in production need to be balanced by the revenues [f]. Due to long investment cycles, bridging technologies are needed that are economically feasible even for a short period of operation [f].
For assessing the potential capacity a plant can allocate for flexible operation, detailed knowledge of the process (including its nonlinear behaviour (Otashu and Baldea, 2019) and understanding of power system economics are required (Zhang and Grossmann, 2016). It is often claimed that in market design models the consumer’s perspective needs to be considered, and integration and dependencies must be accounted for (Zhang and Grossmann, 2016). As stated in Gusain et al. (2020), studies often focus either on device physics and simplify the power grid side of the challenge, or represent the power grid in great detail, but oversimplify the technical behaviour of the device, when it is required to consider both. Accurate modelling of flexibility and integration of production and energy management is required on the industry side (Zhang and Grossmann, 2016), together with refined planning capabilities as most processes in the chemical industry are currently running continuously (TenneT, 2021).
In order to facilitate the contribution of flexible plants to grid reliability under the condition of an existing business case for the offering party, there needs to be a market for flexibility, and plant operators should have access to DR programs (TenneT, 2021). The former depends on the electricity market design, while the latter depends on the regulations set by the regulator. According to Stork et al. (2018), changes are required to attain an attractive electricity tariff structure that promotes participation for the industry, as it is currently partly disincentivising flexible operation by offering tariff discount for stable consumption patterns (TenneT, 2021). For a study on different tariffs and their impact on the amount of flexibility offered by the industry, and the investments in flexibility that can be expected we refer to Richstein and Hosseinioun (2020). An important criterion for access to the market is the minimum capacity that needs to be offered to the grid operator (Leinauer et al., 2022), and it would be beneficial to relax the availability requirements for the plant [c]. In this regard, marketing the flexibility via an aggregator is seen as an advantageous option as they have access to a portfolio of available flexibility [c] and because aggregators provide know-how. Technical standards for connecting the two parties would help reduce the complexity of, e.g., the required IT systems (Leinauer et al., 2022). Participation needs to be promoted and metering and pre-qualification requirements should be designed in such a way that these requirements do not discourage participation in DR programs (TenneT, 2021).
Another requirement is the alignment of the grid operators’ time horizon for planning grid stabilizing services to the time horizon of plant operators, as this is currently an issue [a], [TenneT and vemw (2021)]. The requirements for such cooperation should become more flexible [a].
Transparency and timely information about prices (TenneT, 2021) is required and participants need to be informed about hardware and software requirements timely [TenneT and vemw (2021)].
Table 4 shows that there is large agreement on technical requirements, namely, on the core requirements for flexibility, the ability to vary the power load and ramp processes up and down at a required rate. Excess capacities and/or storage facilities as flexibility strategies were also named by stakeholders and literature. The remaining technical requirements discussed in the previous sections were named by either the industry or in literature but were not contradictory. Both groups agree that a business case is required for the implementation of flexibility. Due to the investment cycle duration in industry, economically feasible short-term bridging technologies were named as an economical requirement by one industrial stakeholder. Organisational requirements that were named by both groups are the need for a market for flexibility, and for industries to have access to this market and to DR programs. An attractive tariff structure, including pre-qualification requirements that do not disincentivise participation, is also regarded as a requirement from both sides. Literature considers the need for further promotion in the industry as a requirement for the deployment of flexibility, while industrial stakeholders rather referred to the need to redesign standards and regulations, and advocated for more transparency and security for planning ahead of time.
Resulting from the requirements, there are limitations to flexibility, and resulting trade-offs that need to be considered, as shown in Table 5.
TABLE 5. Identified limitations and trade-offs according to peer-reviewed/grey literature and industry publications/interviews. Bold text indicates an agreement between the two.
Most chemical processes are designed to operate continuously. Deviating from the nominal operational mode can impose safety risks (TenneT, 2021). Often, already installed processes might not be able to increase their electric load because they are already operating at their maximum production capacity during nominal operational mode (Leinauer et al., 2022), so there is limited available capacity for a further increase. There is also a limit as to whether the process can be shut down, which is the amount of time required to start up a process again [d]. For increasing or decreasing electricity consumption according to external signals, the ramping time of the plants could be limiting if it is not sufficiently fast [c], (TenneT, 2021). Ramping times differ per process and depend on the time that is required to stabilize the process after ramping up or down. Especially thermal process units are subject to these limitations, for the time required to heat up or cool down and to reach equilibrium conditions.
Another limitation to offering DR capacity lies in the complexity of the implementation of flexibility [b, f] including the requirement to schedule different operational modes to integrate production planning and operation (TenneT, 2021). Studies that investigated scheduling (Otashu and Baldea, 2020) found that the availability of the plant might not match with the moments in time when the grid requires the load change. Otashu and Baldea (2018) emphasize that the operation requires integrated planning, scheduling and control due to operational limitations of the plant, which requires a complex IT system (Leinauer et al., 2022). The uncertainty in electricity price forecasts poses an additional difficulty for the planning of operation if electricity prices are taken into account, as the planning might need to be changed spontaneously if the forecast was not correct.
Industrial symbiosis is another limitation to flexibility that is often overlooked. Chemical production is often clustered, and in such clusters, production plants are highly interlinked with one another, which leads to interdependencies. This increases the complexity (Wong and Van Dril, 2020) and must be taken into consideration (Zhang and Grossmann, 2016; Kelley et al., 2022) by evaluating if there are downstream processes that are designed for a constant specific mass flow that would not be supplied during flexible operation.
As described previously, there are two types of demand response. If load shifting is not possible, there is a clear trade-off, namely, the value of relinquished production versus the value of offering the demand reduction as a service (Leinauer et al., 2022) or decreasing electricity costs [d], (TenneT, 2021). When considering a potential increase in electricity consumption when there is surplus electricity available, another trade-off is observed. Since chemical processes are commonly operated at their maximum capacity, financial investment would be needed for the installation of additional equipment or storage capacities, or for replacing the old units with bigger ones (Klaucke et al., 2017). Brée et al. (2019, 2020) found that the economic performance of a process that was modified to increase flexibility depends strongly on the investment costs that were required. The higher the investment costs, the longer the payback times. The two economic trade-offs discussed here were also identified in Paulus and Borggrefe (2011), one of the first studies that investigated the balancing requirements in the German electricity market and analyzed the potential contribution of DR from industrial electricity consumers, including chlorine production.
As mentioned before, uncertainty in market prices increases the difficulty of planning flexible operation. Uncertainties are therefore a barrier for the industry to consider flexible operation as valuable for them (Samani et al., 2022). Such uncertainties include first, the electricity price and long-term development in the price (Brée et al., 2019), second, the amount of money paid for grid-balancing services (Leinauer et al., 2022), third, the hydrogen price, in case of operation with auxiliary units (Brée et al., 2020), and last, the development of the markets they are involved in (Zhang and Grossmann, 2016). These uncertainties impose a risk on the process operators, because payback times are difficult to determine [c], and the financial compensation from electricity cost savings might be too low to make a positive business case for flexible operation (Leinauer et al., 2022). This was also mentioned in the Power to Products project report on industrial DR in the Netherlands (Berenschot et al., 2015).
Another trade-off is that non-optimal operation can degrade the equipment and lead to a decrease in efficiency [a], (Arnold and Janssen, 2016). The latter can imply higher electricity consumption, and would therefore reduce the potential financial benefit of flexible operation [d]. Samani et al. (2022) added that the absence of an adaptive control architecture for flexible operation also increases the difficulty to maintain a stable efficiency. Deviation from optimal operating conditions can also degrade the quality of the product (Leinauer et al., 2022), which can lead to additional economic losses.
Since doubts exist about the business case of flexibly operating production, industries’ disposition to consider flexible operation appears currently limited, with some industrial stakeholders pointing out that “normal” production would likely be prioritised over operation for DR [b, c].
If companies alter the production volume in order to adjust their electricity consumption according to the availability of electricity, they might not be able to fulfil delivery obligations set by their customers. In addition to the doubts about the economic performance mentioned before, organisational obligations can be another reason for companies to prioritize “normal” production over offering DR (Leinauer et al., 2022).
For the assessment of potential participation in DR programs of the grid operator, accurate modelling of the process is required. If this assessment is done by a third party, companies might need to share data, but it is doubtful that industries are willing to share data with third parties due to confidentiality concerns (Zhang and Grossmann, 2016; Otashu et al., 2021). For participation in DR programs, the grid operator requires to set up an IT connection with collaborating entities, and it is reported that industrial partners were concerned about the safety of such an IT connection because it could allow other entities to interfere with their processes [c].
Additionally, knowledge of energy markets is required. If this knowledge is not available within the company, an external service provider could be necessary. Some companies might object to a potential dependency on this service provider (Leinauer et al., 2022). It was reported that companies perceive the lack of information about bidding strategies of competing parties as a barrier to offering grid stabilizing services (Leinauer et al., 2022).
Another organisational limitation is related to the innovations that are required when flexibility should be implemented. The (physical) implementation of innovations happens mostly during the construction phase, so opportunities are bound to the investment cycle of the respective plants (Arnold and Janssen (2016) and companies are hesitant to abandon these cycles because otherwise the lifetime of existing assets would be reduced, which has economic disadvantages [f].
One grid operator claimed that the awareness of the opportunities of offering DR is low among industrial stakeholders in general (TenneT, 2021).
Although there is not much information available yet, regulations can also be a barrier to the deployment of flexibility. An example is the minimum power requirement for the provision of grid stability services. If that is considerably high [like 1 MW in the case of Belgium (Samani et al., 2022)], it will not be met by all parties (TenneT, 2021) and constitutes a barrier to offering flexibility. The required installation of qualified metering equipment for participation in DR programs is also regarded as an additional effort (TenneT, 2021). Even though some regulatory requirements and limitations were mentioned, regulations seem to be a minor concern. We believe this might be because stakeholders from the chemical industry focused on financial, organizational and technical aspects since they were closer to their expertise, although several of the aspects named are partly a direct consequence of regulation.
This study provided insights into how the flexibility of chemical processes is considered in the context of the energy transition and identified key benefits and bottlenecks.
The main drivers to consider the industries’ flexibility potential are first, the contribution to energy system reliability by balancing electricity generation and demand, and second, potential cost savings for the industry due to the possibility to adapt the production to fluctuations in the electricity price. The main limitations are a), the uncertain economic performance of flexible processes due to investment costs, reduced production and uncertain revenues from flexible operation, and b), the complexity of the implementation. The interest in flexibility is expected to grow as the increasing electrification of the chemical industry is considered. However, it is uncertain whether the benefits outweigh the limitations, and to what extent the benefits are worth the effort that has to be made to fulfil the requirements of the flexible operation of chemical processes.
Despite large expectations in literature, the techno-economic feasibility of flexible operation in the chemical industry is still unclear. It is also unclear what revenue models for flexibility could look like, including required CO2 price levels and network tariffs or monetary incentives, and how companies can cope with uncertainties of market prices that affect their decision-making regarding whether to invest in flexibility.
Even though some frameworks have been proposed to quantify the flexibility of chemical processes, an established methodology is still lacking. Local interconnections of the process need to be included in the assessment to account for industrial symbiosis and interdependencies between single industries, and to get insights into whether these interconnections could provide opportunities to exploit synergies.
There is a lack of knowledge on how the flexibility of current chemical processes can be increased, beyond electrolysis-based industries, such as chlorine production or water electrolysis. It has been suggested to investigate options for electrification of process heat for flexible use and to consider strategies to increase the flexibility of future processes, such as distributing production.
The impact of future technologies and alternative process designs on the flexibility potential is unknown, too. It is important to close this knowledge gap due to the upcoming changes in the industry that are necessary for meeting GHG emission targets and because this knowledge is needed to assess future developments in the electricity market.
The limitations and open questions should be addressed in future research, to explore if and how flexibility in the chemical industry can play a role in achieving future grid reliability.
Table 6 provides a list of company roadmaps that are included in the analysis shown in Figure 1 and described in Section 3. Some roadmaps are joint roadmaps from several companies, such as the one published by Gasunie and Tennet, or by Netbeheer Nederland.
TABLE 6. Supplementary information to Figure 1 in Section 3: Consideration of flexibility in companies’ roadmaps towards sustainability. Roadmaps included in the analysis and respective domain. Some companies are involved in more than one roadmap.
The original contributions presented in the study are included in the article/Supplementary Material, further inquiries can be directed to the corresponding author.
The studies involving human participants were reviewed and approved by the Delft University of Technology Ethics Committee. The patients/participants provided their written informed consent to participate in this study.
SB, MC, and AR contributed to the conception and design of the study. SB conducted the literature review and the interviews, analysed the data and wrote the first draft of the manuscript. All authors contributed to the article and approved the submitted version.
This work is part of the RELEASE project and by the Dutch Research Council (NWO) (project number 17621).
The authors declare that the research was conducted in the absence of any commercial or financial relationships that could be construed as a potential conflict of interest.
All claims expressed in this article are solely those of the authors and do not necessarily represent those of their affiliated organizations, or those of the publisher, the editors and the reviewers. Any product that may be evaluated in this article, or claim that may be made by its manufacturer, is not guaranteed or endorsed by the publisher.
The Supplementary Material for this article can be found online at: https://www.frontiersin.org/articles/10.3389/fenrg.2023.1190174/full#supplementary-material
DR, demand response; DSM, demand side management; GHG, greenhouse gases;PEM, proton exchange membrane; PoR, Port of Rotterdam; RES, renewable energy sources.
Air Products and Chemicals Inc, (2021). Allentown, Pennsylvania, United States: Air Products and Chemicals Inc. Sustainable growth for a sustainable future.
Arnold, K., and Janssen, T. (2016). Demand side management in industry-necessary for a sustainable energy system or a backward step in terms of improving efficiency?Ind. Summer Study Proc., 339–350.
Baetens, J., Vandevelde, L., and Van Eetvelde, G. (2021). Ph.D. thesis. Ghent, Belgium: Ghent University.Electrical flexibility in the chemical process industry
Bazzanella, A., and Ausfelder, F. (2017). Low carbon energy and feedstock for the European chemical industry.
Berenschot, C. E. Delft, and Ispt, (2015). Power to products - eindreport. Victoria, 3000, Australia: ISPT.
Blanco, H., and Faaij, A. (2018). A review at the role of storage in energy systems with a focus on Power to Gas and long-term storage. Renew. Sustain. Energy Rev.81. doi:10.1016/j.rser.2017.07.062
Brée, L. C., Bulan, A., Herding, R., Kuhlmann, J., Mitsos, A., Perrey, K., et al. (2020). Techno-economic comparison of flexibility options in chlorine production. Industrial Eng. Chem. Res.59, 12186–12196. doi:10.1021/acs.iecr.0c01775
Brée, L. C., Perrey, K., Bulan, A., and Mitsos, A. (2019). Demand side management and operational mode switching in chlorine production. AIChE J.65, e16352. doi:10.1002/aic.16352
Bruns, B., Di Pretoro, A., Grünewald, M., and Riese, J. (2021). Flexibility analysis for demand-side management in large-scale chemical processes: An ethylene oxide production case study. Chem. Eng. Sci.243, 116779. doi:10.1016/j.ces.2021.116779
Bruns, B., Di Pretoro, A., Grünewald, M., and Riese, J. (2022a). Indirect demand response potential of large-scale chemical processes. Industrial Eng. Chem. Res.61, 605–620. doi:10.1021/acs.iecr.1c03925
Bruns, B., Grünewald, M., and Riese, J. (2022b). Optimal design for flexible operation with multiple fluctuating input parameters. Comput. Aided Chem. Eng.51, 859–864. doi:10.1016/B978-0-323-95879-0.50144-2
Bruns, B., Herrmann, F., Polyakova, M., Grünewald, M., and Riese, J. (2020). A systematic approach to define flexibility in chemical engineering. J. Adv. Manuf. Process.2. doi:10.1002/amp2.10063
Chen, C., and Yang, A. (2021). Power-to-methanol: The role of process flexibility in the integration of variable renewable energy into chemical production. Energy Convers. Manag.228, 113673. doi:10.1016/j.enconman.2020.113673
Dbi Gas- und Umwelttechnik GmbH, (2020). “Institute of energy and climate research (IEK),” in Phase II-pathways to 2050. A joint follow-up study by Gasunie and TenneT of the infrastructure outlook 2050 (Aachen, Germany: IAEW at RWTH Aachen University).
De Luna, P., Hahn, C., Higgins, D., Jaffer, S. A., Jaramillo, T. F., and Sargent, E. H. (2019). What would it take for renewably powered electrosynthesis to displace petrochemical processes?Science364. doi:10.1126/science.aav3506
Den Ouden, B., Lintmeijer, N., Van Aken, J., Afman, M., Croezen, H., Van Lieshout, M., et al. (2017). Electrification in the Dutch process industry. https://cedelft.eu/publications/electrification-in-the-dutch-process-industry/.
Di Pretoro, A., Bruns, B., Negny, S., Grünewald, M., and Riese, J. (2022). Demand response scheduling using derivative-based dynamic surrogate models. Comput. Chem. Eng.160, 107711. doi:10.1016/j.compchemeng.2022.107711
Dnv, G. L. (2020). DE mogelijke bijdrage van industriële vraagrespons aan leveringszekerheid. https://www.dnv.nl/Publications/de-mogelijke-bijdrage-van-industriele-vraagrespons-aan-leveringszekerheid-190655.
Dupont, (2022). Sustainability Roadmap. Empowering the world with essential innovations to thrive. Wilmington, Delaware, United States: Dupont.
Eastman, (2021). A better circle 2020 Sustainability Report. Kingsport, Tennessee, United States: Eastman.
Eryazici, I., Ramesh, N., and Villa, C. (2021). Electrification of the chemical industry—Materials innovations for a lower carbon future. MRS Bull.46. doi:10.1557/s43577-021-00243-9
euro chlor, (2022). Chlorine production is an energy intensive process. Brussels, Belgium: euro chlor.
Fischer, K. L., and Freund, H. (2020). On the optimal design of load flexible fixed bed reactors: Integration of dynamics into the design problem. Chem. Eng. J.393, 124722. doi:10.1016/j.cej.2020.124722
Ganzer, C., and Mac Dowell, N. (2020). A comparative assessment framework for sustainable production of fuels and chemicals explicitly accounting for intermittency. Sustain. Energy Fuels4, 3888–3903. doi:10.1039/c9se01239g
Germscheid, S. H., Mitsos, A., and Dahmen, M. (2022). Demand response potential of industrial processes considering uncertain short-term electricity prices. AIChE J.68. doi:10.1002/aic.17828
Gruber, A.-M. (2017). Zeitlich und regional aufgelöstes industrielles Lastflexibilisierungspotenzial als Beitrag zur Integration Erneuerbarer Energien. https://www.ffe.de/veroeffentlichungen/zeitlich-und-regional-aufgeloestes-industrielles-lastflexibilisierungspotenzial-als-beitrag-zur-integration-erneuerbarer-energien/.
Gusain, D., Cvetkovic, M., Bentvelsen, R., and Palensky, P. “Technical assessment of large scale PEM electrolyzers as flexibility service providers,” in Proceedings of the 2020 IEEE 29th International Symposium on Industrial Electronics (ISIE), Delft, Netherlands, June 2020.
Herrmann, F., Grünewald, M., Meijer, T., Gardemann, U., Feierabend, L., and Riese, J. (2022). Operating window and flexibility of a lab-scale methanation plant. Chem. Eng. Sci.254, 117632. doi:10.1016/j.ces.2022.117632
Hochhaus, T., Bruns, B., Grünewald, M., and Riese, J. (2023). Optimal scheduling of a large-scale power-to-ammonia process: Effects of parameter optimization on the indirect demand response potential. Comput. Chem. Eng.170, 108132. doi:10.1016/j.compchemeng.2023.108132
Hoffmann, C., Hübner, J., Klaucke, F., Milojević, N., Müller, R., Neumann, M., et al. (2021). Assessing the realizable flexibility potential of electrochemical processes. Industrial Eng. Chem. Res.60, 13637–13660. doi:10.1021/acs.iecr.1c01360
Hofmann, M., Müller, R., Christidis, A., Fischer, P., Klaucke, F., Vomberg, S., et al. (2022). Flexible and economical operation of chlor-alkali process with subsequent polyvinyl chloride production. AIChE J.68. doi:10.1002/aic.17480
Huntsman Corporation, (2022). Brightening the horizon innovative solutions for a low-carbon economy. Sustainability report 2020. Texas, United States: Huntsman Corporation.
International Energy Agency, (2021). Paris, France: IEA.Net zero by 2050 - a roadmap for the global energy sector
Kelley, M. T., Do, T. T., and Baldea, M. (2022). Evaluating the demand response potential of ammonia plants. AIChE J.68. doi:10.1002/aic.17552
Kirby, M., Parsons, H., Zimmerman, V., Siew, R., and White, E. (2022). Responsible energy. Shell plc sustainability report 2021. https://reports.shell.com/sustainability-report/2021/.
Kiviluoma, J., O’Dwyer, C., Ikäheimo, J., Lahon, R., Li, R., Kirchem, D., et al. (2022). Multi-sectoral flexibility measures to facilitate wind and solar power integration. IET Renew. Power Gener.16, 1814–1826. doi:10.1049/rpg2.12399
Klaucke, F., Karsten, T., Holtrup, F., Esche, E., Morosuk, T., Tsatsaronis, G., et al. (2017). Demand Response Potenziale in der chemischen Industrie. Chemie-Ingenieur-Technik89, 1133–1141. doi:10.1002/cite.201600073
Klaucke, F., Müller, R., Hofmann, M., Weigert, J., Fischer, P., Vomberg, S., et al. (2023). Chlor-alkali process with subsequent polyvinyl chloride ProductionCost analysis and economic evaluation of demand response. Industrial Eng. Chem. Res.62, 7336–7351. doi:10.1021/acs.iecr.2c04188
Klyapovskiy, S., Zheng, Y., You, S., and Bindner, H. W. (2021). Optimal operation of the hydrogen-based energy management system with P2X demand response and ammonia plant. Appl. Energy304, 117559. doi:10.1016/j.apenergy.2021.117559
Lahrsen, I. M., Hofmann, M., and Müller, R. (2022). Flexibility of epichlorohydrin production—increasing profitability by demand response for electricity and balancing market. Processes10, 761. doi:10.3390/pr10040761
Lashmar, N., Wade, B., Molyneaux, L., and Ashworth, P. (2022). Motivations, barriers, and enablers for demand response programs: A commercial and industrial consumer perspective. Energy Res. Soc. Sci.90, 102667. doi:10.1016/j.erss.2022.102667
Leinauer, C., Schott, P., Fridgen, G., Keller, R., Ollig, P., and Weibelzahl, M. (2022). Obstacles to demand response: Why industrial companies do not adapt their power consumption to volatile power generation. Energy Policy165, 112876. doi:10.1016/j.enpol.2022.112876
Luo, J., Moncada, J., and Ramirez, A. (2022). Development of a conceptual framework for evaluating the flexibility of future chemical processes. Ind. Eng. Chem. Res.61. doi:10.1021/acs.iecr.1c03874
Lyondellbasell, (2021). LyondellBasell announces goal of achieving net zero emissions by 2050. Rotterdam, Netherlands: Lyondellbasell.
Mukelabai, M. D., Gillard, J. M., and Patchigolla, K. (2021). A novel integration of a green power-to-ammonia to power system: Reversible solid oxide fuel cell for hydrogen and power production coupled with an ammonia synthesis unit. Int. J. Hydrogen Energy46, 18546–18556. doi:10.1016/j.ijhydene.2021.02.218
Nayak-Luke, R., Bañares-Alcántara, R., and Wilkinson, I. (2018). Green ammonia: Impact of renewable energy intermittency on plant sizing and levelized cost of ammonia. Industrial Eng. Chem. Res.57, 14607–14616. doi:10.1021/acs.iecr.8b02447
Nederland, Netbeheer (2021). Hague, Netherlands: Netbeheer Nederland.Samenvatting: Het energiesysteem van de Toekomst
Nobian Industrial Chemicals, B. V. (2022). Amersfoort, Netherlands: Nobian Industrial Chemicals B.V.Sustainability Report 2021. Grow greener together
Oecd, (2021). Policies for a carbon-neutral Industry in The Netherlands (OECD). Paris, France: OECD. doi:10.1787/6813bf38-en
Olsthoorn, M., Schleich, J., and Klobasa, M. (2015). Barriers to electricity load shift in companies: A survey-based exploration of the end-user perspective. Energy Policy76, 32–42. doi:10.1016/j.enpol.2014.11.015
Otashu, J. I., and Baldea, M. (2019). Demand response-oriented dynamic modeling and operational optimization of membrane-based chlor-alkali plants. Comput. Chem. Eng.121, 396–408. doi:10.1016/j.compchemeng.2018.08.030
Otashu, J. I., and Baldea, M. (2018). Grid-level “battery” operation of chemical processes and demand-side participation in short-term electricity markets. Appl. Energy220, 562–575. doi:10.1016/j.apenergy.2018.03.034
Otashu, J. I., and Baldea, M. (2020). Scheduling chemical processes for frequency regulation. Appl. Energy260, 114125. doi:10.1016/j.apenergy.2019.114125
Otashu, J. I., Seo, K., and Baldea, M. (2021). Cooperative optimal power flow with flexible chemical process loads. AIChE J.67. doi:10.1002/aic.17159
Paulus, M., and Borggrefe, F. (2011). The potential of demand-side management in energy-intensive industries for electricity markets in Germany. Appl. Energy88, 432–441. doi:10.1016/j.apenergy.2010.03.017
Port of Rotterdam, (2023). CO2 emissions port of Rotterdam fell by over 4% in 2022. Rotterdam, Netherlands: Port of Rotterdam.
Richstein, J. C., and Hosseinioun, S. S. (2020). Industrial demand response: How network tariffs and regulation (do not) impact flexibility provision in electricity markets and reserves. Appl. Energy278, 115431. doi:10.1016/j.apenergy.2020.115431
Riese, J., and Grünewald, M. (2020). Challenges and opportunities to enhance flexibility in design and operation of chemical processes. Hoboken, New Jersey, United States: Wiley. doi:10.1002/cite.202000057
Roelofsen, O., Somers, K., Speelman, E., and Witteveen, M. (2020). Plugging in: What electrification can do for industry. New York, NY, USA: McKinsey & Company.
Sabic, (2022). Reimagining ESG. Toward a circular economy. Sustainability Report 2021. Riyadh, Saudi Arabia.
Samani, A. E., De Kooning, J. D., Urbina Blanco, C. A., and Vandevelde, L. (2022). Flexible operation strategy for formic acid synthesis providing frequency containment reserve in smart grids. Int. J. Electr. Power Energy Syst.139, 107969. doi:10.1016/j.ijepes.2022.107969
Schiffer, Z. J., and Manthiram, K. (2017). Electrification and decarbonization of the chemical industry. Joule1, 10–14. doi:10.1016/j.joule.2017.07.008
Semrau, R., and Engell, S. (2023). Process as a battery: Electricity price aware optimal operation of zeolite crystallization in a continuous oscillatory baffled reactor. Comput. Chem. Eng.171, 108143. doi:10.1016/j.compchemeng.2023.108143
Shafie-Khah, M., Siano, P., Aghaei, J., Masoum, M. A., Li, F., and Catalao, J. P. (2019). Comprehensive review of the recent advances in industrial and commercial DR. IEEE Trans. Industrial Inf.15. doi:10.1109/TII.2019.2909276
Shin-Etsu Chemical Co. Ltd, (2022). Shin-etsu group and climate change. Chiyoda City, Tokyo, Japan: Shin-Etsu Chemical Co. Ltd.
Shoreh, M. H., Siano, P., Shafie-khah, M., Loia, V., and Catalão, J. P. (2016). A survey of industrial applications of Demand Response. Electr. Power Syst. Res.141. doi:10.1016/j.epsr.2016.07.008
Siddiquee, S. M., Howard, B., Bruton, K., Brem, A., and O’Sullivan, D. T. (2021). Progress in demand response and it’s industrial applications. Front. Energy Res.9. doi:10.3389/fenrg.2021.673176
Skea, J., Shukla, P. R., Reisinger, A., Slade, R., Pathak, M., Al Khourdajie, A., et al. (2022). Mitigation of climate change summary for policymakers climate change 2022 working group III contribution to the sixth assessment report of the intergovernmental panel on climate change. https://www.ipcc.ch/report/ar6/wg3/.
Statistics Netherlands, (2022). Greenhouse gas emissions 2.1 percent higher in 2021. Netherlands: Statistics Netherlands.
Stork, M., de Beer, J., Lintmeijer, N., and den Ouden, B. (2018). Roadmap for the Dutch chemical industry towards 2050. https://www.vnci.nl/Content/Files/file/Downloads/VNCI_Routekaart-2050.pdf.
TenneT, , and vemw, (2021). Industrial flexibility is a key building block for a reliable and affordable grid. Arnhem, Netherlands: TenneT.
Tuinema, B. W., Adabi, E., Ayivor, P. K., Suárez, V. G., Liu, L., Perilla, A., et al. (2020). Modelling of large-sized electrolysers for realtime simulation and study of the possibility of frequency support by electrolysers. IET Generation, Transm. Distribution14, 1985–1992. doi:10.1049/iet-gtd.2019.1364
United Nations Secretaty-General, (2022). Statement by the secretary-general at the conclusion of COP27 in sharm el-sheikh. New York, NY, United States: United Nations Secretaty-General.
Vattenfall, (2021). Vattenfall en Nobian dragen met flexibele chloorproductie bij aan stabiliteit van het stroomnet. Solna, Sweden: Vattenfall.
Wong, L., and Van Dril, A. (2020). Decarbonisation options for large volume organic chemicals production, PBL Netherlands Environmental Assessment Agency, Hague, Netherlands.
Yara International, A. S. A. (2021). Yara sustainability report 2021. Growing a nature-positive food future. Oslo, Norway: Yara International ASA.
Keywords: flexibility, energy management, chemical production, demand side management, demand response, energy transition, DSM, DR
Citation: Bielefeld S, Cvetković M and Ramírez A (2023) Should we exploit flexibility of chemical processes for demand response? Differing perspectives on potential benefits and limitations. Front. Energy Res. 11:1190174. doi: 10.3389/fenrg.2023.1190174
Received: 20 March 2023; Accepted: 19 June 2023;
Published: 30 June 2023.
Edited by:
Yingjun Wu, Hohai University, ChinaReviewed by:
Julia Riese, Ruhr University Bochum, GermanyCopyright © 2023 Bielefeld, Cvetković and Ramírez. This is an open-access article distributed under the terms of the Creative Commons Attribution License (CC BY). The use, distribution or reproduction in other forums is permitted, provided the original author(s) and the copyright owner(s) are credited and that the original publication in this journal is cited, in accordance with accepted academic practice. No use, distribution or reproduction is permitted which does not comply with these terms.
*Correspondence: Svenja Bielefeld, cy5lLmJpZWxlZmVsZEB0dWRlbGZ0Lm5s
Disclaimer: All claims expressed in this article are solely those of the authors and do not necessarily represent those of their affiliated organizations, or those of the publisher, the editors and the reviewers. Any product that may be evaluated in this article or claim that may be made by its manufacturer is not guaranteed or endorsed by the publisher.
Research integrity at Frontiers
Learn more about the work of our research integrity team to safeguard the quality of each article we publish.