- Department of Chemical, Metallurgical and Materials Engineering, Tshwane University of Technology, Pretoria, South Africa
In the past decade, high entropy alloys have been a research field of interest largely attributed to the enormous possibilities in alloy compositions, solid solution microstructures, and enhanced properties. The progress accomplished so far in the innovative growth and development of the mechanical, nanomechanical, chemical, electrochemical properties for energy storage systems using high entropy alloys on the nanoscale has limited reports in the literature. Mastering the synthesis of high entropy alloys is the deciding factor, if not the holy grail, when interested in a new material. For nanoparticles, in particular, this is true. Hence, the study on the production of high entropy alloy nanoparticles (HE-NPs) and the impact of synthesis on the structure of the resulting nanomaterial is valid for newly emerging components like HEA-NPs and the linkages between synthesis, structure, and property are essential for creating HEA-NP-based applications for energy storage applications, requiring the creation of a fundamental protocol to enable their mass manufacture and efficiency in service. In this study, we have presented a straightforward review of high entropy alloys, recent advances in high entropy nanoparticles and their various syntheses for energy and catalysis applications.
1 Introduction
The fundamental concept of alloying in material engineering was based on the tactic of sparingly combining a few minor elements with major elements for centuries (Dąbrowa et al., 2016; George et al., 2019; Marques et al., 2021). However, different alloys which are made from different primary elements like Iron, Aluminum. Nickel, Copper, and Zinc have increased the overall number of alloys, most of which have already been found and studied and are severely constrained in their use of principal elements (Li H. et al., 2021). As a result, innovative alloying ideas have been in high demand since they significantly expand the compositional possibilities for creating new materials both at the micro and nanoscale (Stepanov et al., 2018; Moghaddam et al., 2021). Traditional alloys have one or two primary components that are selected based on a specific property criterion, and other minor alloying components are included to further improve their properties. High-entropy alloys (HEAs), which Yeh et al. presented in 2004, constitute a revolutionary alloy idea design (Chen et al., 2018). Opening up a wide, uncharted arena of alloy compositions and the possibility of influencing solid solution phase stability through the management of configurational entropy are the two main novelties of this alloy design (George et al., 2020). HEAs are described as “those comprising five or more primary elements in equimolar ratios” (Jien-Wei, 2006). The following clause broadens the definition to include “principal elements with the concentration of each element being between 35 and five atomic percentage,” which circumscribes the criterion for equimolar concentrations. As a result, HEAs need not be equimolar to greatly expand the number of compositions (Sathiyamoorthi and Kim, 2022), or to change the features of the base HEA and create more HEAs.
HEAs may additionally contain minor elements. This definition based on composition merely specifies elemental concentrations and does not limit the amount of entropy in the system (Moghaddam et al., 2021). Additionally, this concept does not stipulate that there must be only a single-phase SS observed (Miracle and Senkov, 2017). The entropy definition based on the concept of “high entropy” is motivated by the size of the entropy. A different definition so distinguishes SSS,ideal and R, which is the total configurational molar entropy in an idyllic solid solution and gas constant, respectively. Low entropy alloys have their configurational molar entropy less than 0.69R while higher entropies’ configurational molar entropy is greater than 1.61R. Using the Boltzmann equation, estimating the configurational molar entropy is made easy, yet it needs atoms to occupy many lattice configurations (Fu et al., 2021).
Rarely does this happen in metallic solutions. Additionally, this definition suggests that an alloy has one value of configurational entropy. Entropy in an alloy, however, can vary as the temperature varies. The impact of temperature can be little, yet giving minute adjustments to the short-range atomic ordering, or it could be dramatic, resulting in a chemical separation between parent and product phases at a first-order phase transformation (Tomilin and Kaloshkin, 2015). The first two definitions are paradoxical in some situations. The common consensus is that a greater composition restriction is beneficial for developing innovative alloys; hence, there is no need to rigidly adhere to the specifications and innovative design of HEAs. It is generally agreed that HEAs have four primary characteristics that set them apart from other alloys: high entropy, severe lattice distortion, slow diffusion, and cocktail effect (Li et al., 2016). The thermodynamic perspective on high entropy involvement in influencing the formation of simple solid solutions in HEA is a positive characteristic feature. In particular, the Gibbs free energy of mixing determines whether it may triumph over other reactions (Cao et al., 2020). Most of the entropy for HEAs is configurational entropy. For a random quinary equimolar solution, intermetallic compounds that are stoichiometric; their configurational entropy is 1.61R (R 14 8.31 J/K mol). The equation
Kulkarni and Chauhan (2015) indicated that diffusional interactions should not be disregarded when describing diffusion in HEAs. According to Verma et al. (2017), the interdiffusion fluxes of different components in HEAs can be increased or decreased based on the diffusional interactions between diffusing components and the configuration of their concentration gradients. HEAs include the atomic sizes of numerous principal elements that can differ greatly, and seriously alter the lattice. X-ray diffraction and TEM with great resolution can intuitively demonstrate and quantify this distortion (Senkov et al., 2018). The HEAs’ mechanical, optical, electrical, and chemical characteristics are all impacted by the distortion feature, and an irregular lattice restricts atom movement. Due to this strong barrier created by significant lattice distortion, stress corrosion cracking occurs via a separate process. Dislocation motion and deformation are thus strongly hindered (Han et al., 2020). The thermodynamic stability of HEAs is further decreased by substantial lattice distortion, which may impact the film’s capacity to passivate alloy surfaces. Ranganathan (2003) was the one who first hypothesized the cocktail effect. The author thought that HEAs might exhibit unforeseen properties that are not the sum of their parts. Nonetheless, since HEAs first appeared at the beginning of the twenty-first century, their superior mechanical characteristics have led to extensive research into and application in numerous engineering fields. High Entropy Alloys have been extensively employed in a variety of technical fields, including high-strength construction materials, corrosion-resistant coating materials and energy storage applications as one of the three major material systems in the world (Li et al., 2019). For instance, HEAs are extremely durable and strong at higher temperatures. They can also sustain stability and a very long lifespan in a range of hostile conditions. The special functional characteristics of HEAs have drawn more attention in recent years, and their range of applications has increased. This study shall concentrate on using HEAs as advanced energy storage materials (Wang Q. et al., 2021).
2 High entropy nanomaterials
Nanomaterials and nanostructures play a critical role in the recent advancement of some key technologies (Liu et al., 2020). Nanomaterials differ from microsized and bulk materials not only on the scale of their characteristic dimensions but also because they may possess new physical properties and offer new possibilities for various technical applications (Huang and Liaw, 2019). When the characteristic dimensions of a semiconductor reduce to below a certain size, quantum confinement leads to an increased band gap (Okulov et al., 2020). The band gap can be controlled by simply varying the dimensions of the material, so the optical absorption and emission spectra can be tuned to meet the specific requirements of the desired applications.
Hence, the research and development of new technologies, as well as the improvement of current technologies, can benefit from smaller sizes or dimensions (Glasscott et al., 2019). For instance, nanoparticles are suitable medication delivery vehicles due to their small size. Furthermore, mobile phones can now perform a wide range of tasks due to the reduction in the size of electrical gadgets. There are fewer flaws in nanoparticles than in their bulk counterparts, and they have substantially better mechanical strength. However, some uses of nanomaterials may be negatively affected by their small size and high specific surface area, especially in applications for energy storage and conversion where nanomaterials have various benefits (Yan et al., 2022). The specific surface area, surface energy, and surface chemistry all play crucial roles in energy conversion and storage because these processes entail physical interaction and/or chemical reactions at the surface or interface. Surface effects can also affect the thermodynamics of heterogeneous reactions at the interface, the surface energy and surface chemistry, the nucleation and subsequent growth when phase transitions are present (Jiang et al., 2021). Surface effects are not just restricted to kinetics and rates. As well as accommodating dimensional changes brought on by some chemical reactions and phase transitions, nanomaterials’ reduced dimensions may also provide more favorable mass, heat, and charge transfer (Hu et al., 2019). The fabrication of HEA nanoparticles (HEA-NPs) by carbothermal shock was described by Hu et al. (2019), which sparked research on nanoscale high-entropy materials (HEMs). High-entropy oxides (HEOs), high-entropy nitrides (HENs), high-entropy borides (HEBs), high-entropy silicides (HESs), high-entropy metallic glasses (HEMGs), high-entropy metal-organic frameworks (HE-MOFs), and other HEMs, which are now included in the broad definition of the “high entropy” concept, especially for energy storage applications (Hussain et al., 2021; Porodko et al., 2022). High entropy nanomaterials have chemical and physical properties that enable superior catalytic performances.
The catalytic performance in the hydrogen evolution reaction is influenced by the principal components at volcano plots, while the minor components slightly impact the adsorption-free energies. Hence, the catalytic performances of alloys are reported to be primarily determined by principal elements present in the alloying composition, while minor elements slightly influence the properties of the alloy. For high entropy materials on the nanoscale, the electrocatalytic performance is influenced by the interactions of multiple elements in the material composition (Li W. et al., 2021). Wang et al. (2020) reported that HEA nanoparticles are potential candidates for energy and electrocatalysis applications due to their high active sites per mass ratio. The authors fabricated HEA NPs using a continuous droplet-to-particle process as opposed the hollow structured fabrication method restricted to two or three elements. The decomposition of a gas-blowing agent, in which a significant amount of gas is produced in situ to “puff” the droplet during heating, is what allows the formation of the hollow HEA nanoparticles. This process is then followed by the decomposition of the metal salt precursors and the nucleation/growth of multimetallic particles. These hollow HEA nanoparticles are attractive candidates since they have a high active sites per mass ratio. These HEA NP materials, therefore, show superior electrocatalytic performance attributed to their active sites, enhanced synergetic transitions during metal interactions, the sluggish diffusion effect, the high entropy stabilization effect and random or irregular atom arrangements. High entropy stabilization effects result in a thermodynamically stable high entropy material for electrocatalysis, making high entropy materials potential materials for heterogeneous catalysis (Zhivulin et al., 2021).
2.1 Fabrication routes of high entropy nanomaterials (HE-NPs)
2.1.1 Physical vapour deposition method
A physical process, such as heat evaporation or an impact process, will transform the particles that are to be deposited in physical vapor deposition (PVD) operations from a solid to a gaseous state (Baptista et al., 2018a; Vu et al., 2019). Mostly, the substrate is deposited in a vacuum chamber with a gas pressure below approximately 10–1 mbar (Pinto et al., 2018). The techniques used in PVD deposition are shown in the flowchart of the PVD Process in Figure 1. Heating raises the kinetic energy of the atoms or molecules in a solid or liquid (Schneider et al., 2000; Baptista et al., 2018b). More atoms can overcome the energy of separation and can avoid evaporation as the temperature rises. According to the temperature at which the atoms evaporate, for example, for copper, the average kinetic energy of the evaporated atoms is about 0.2 eV (Reichelt and Jiang, 1990). The primary components of evaporated particles include atoms, molecules, and clusters of various sizes and compositions (Wang X. et al., 2021; Stuart and Stan, 2021). A laser beam or an arc discharge can heat the evaporator and cause it to evaporate. When compared to thermal evaporation, the composition and energy of the vapour particles are different. Surface particles and secondary electrons will detach from the target when it is bombarded with ions with energies of over 30 eV (Ali et al., 2019; Gupta et al., 2021). This action is known as sputtering. The ejected particles, which are primarily molecules and atoms, will deposit on the substrate and the vacuum chamber wall to form the film. High entropy alloy films can be easily deposited using physical vapor deposition via magnetron co-sputtering. High entropy nanomaterials can also be obtained in tuneable shape and size using ionic liquids in place of traditional solid substrates in the top-down technique (Sun et al., 2021). Ionic liquids serve as suspension mediums and stabilizers for low melting points and vapor pressure. For example, high entropy CrMnFeCoNi nanoparticles were fabricated using ionic liquids via vapor deposition technique with an extraordinary oxygen reduction reaction observed. The material, although amorphous in structure, showed complete compositional homogeneity (Garzón-Manjón et al., 2018).
Hence, crystalline high entropy materials on the nanoscale can be obtained by using the appropriate manufacturing routes, such as ex situ vacuum annealing, in situ electron beam irradiation, and vapour deposition techniques.
2.1.2 Laser deposition method
In the technique of “laser cladding,” a heating source—a laser beam—is employed to melt the coating material onto the substrate (Boddu et al., 2001; Arif et al., 2021; Zhu et al., 2021). To create an alloy-clad layer, several metals and alloys can be placed on the substrate as shown in Figure 2. Due to the inherent characteristics of laser radiation, high input energy, low distortion, and the avoidance of unwanted phase change are all advantages of laser cladding in addition to the ability to selectively clad small areas (Santo, 2008; Singh et al., 2020). These factors have led to its successful usage in the restoration of specific molds’ metal components. Controlled shape, little diffusion of the substrate elements into the coating, fine microstructure, and low porosity in the deposited layer of the laser cladding technique were discussed by Wang et al. (1997) as the characteristic features of the laser cladding process. AlCoCrCuNi compositional system nanoparticles were fabricated by Mao et al. (2018). The authors investigated the influence of aluminum on the nanomaterial microstructure and properties. A single Cu-rich face-centered cubic (FCC) phase to FCC + M3Al-type L12 phase structure was observed, followed by the FCC + body-centered cubic (BCC) phases as the Al content increased. The targets’ nominal chemical compositions greatly differed from those of the nanoparticles, which were spherical and ranged in size from 110 nm to 180 nm on average.
When the microstructure changed from a pure FCC phase to an FCC + BCC phase, both the corrosion resistance and the soft magnetic behavior declined. In the technique of “laser cladding,” a heating source—a laser beam—is employed to melt the coating material onto the substrate (Liu et al., 2017; Siddiqui and Dubey, 2021). To create an alloy-clad layer, several metals and alloys can be placed on the substrate. Due to the inherent characteristics of laser radiation, high input energy, low distortion, and the avoidance of unwanted phase change are all advantages of laser cladding in addition to the ability to selectively clad small areas (Santo, 2008; Tamanna et al., 2019). These factors have led to its successful usage in the restoration of specific molds’ metal components. The M3Al-type L12 phase contributed to the best corrosion resistance and the least amount of soft magnetic properties to the FCC matrix. The authors concluded that the laser cladding process makes it simple to create multicomponent nanoparticles with compositions and structures that can be adjusted (Weng et al., 2014; Liu et al., 2021).
2.1.3 Mechanical alloying and spark plasma sintering
Mechanical alloying (MA) followed by sintering (HEAs) is one of the most popular methods for creating nanocrystalline high-entropy alloys (Taha et al., 2019; Vaidya et al., 2019). As a well-known solid-state, nonequilibrium, top-down approach to producing nanocrystalline materials, mechanical alloying (MA) involves the milling of elemental powders on the micro or nanoscale to achieve alloying at an atomic scale (Suryanarayana, 2001; Suryanarayana, 2019). The MA process is described by the repeated fusing and splintering of powder particles entrapped between the milling media to an extent which depends on the mechanical attributes of powder constituents (Sundaresan and Froes, 1987; Benjamin, 1992). The main advantages of MA include improved solid solubility, room temperature processing, and homogeneous alloy production. High-density HEA pellets from milled powders have primarily been produced by spark plasma sintering (Sundaresan and Froes, 1987; Koch, 1998). The manufacturing of HEAs utilizing MA does, however, present several difficulties, including contamination during milling and high susceptibility to oxidation (Courtney, 1995; Murty and Ranganathan, 1998; Nagesha et al., 2013). A uniaxial press, punch electrodes, vacuum chamber, regulated atmosphere, DC pulse generator, and position, temperature, and pressure measurement devices support the sintering machine shown in Figure 3. Setting the holding time, ramp rate, pulse duration, pulse current and voltage allows for control of the sintering temperature. Spark plasma, spark impact pressure, joule heating, and an electrical field diffusion effect could all be produced by the DC pulse discharge. Compared to traditional hot pressing, SPS sintering is aided by the on-off DC pulse voltage. Pressure is applied to aid in the material’s plastic flow (Kessel et al., 2010). Sintered samples are fabricated via SPS by taking a known quantity of dried, and milled powder samples in a cylindrical dye, lined with a graphite sheet which facilitates easy removal of the sintered compact (Munir et al., 2006; Mogale and Matizamhuka, 2020). The chiller is switched on the compressor and the machine and the die containing the powder sample are placed inside the SPS chamber. Then, set the specific pattern (time-temperature data) needed for the experiment to follow, and thereafter, the required atmospheres such as Vacuum, Argon, etc., are maintained inside the chamber (Saheb et al., 2012; Yurlova et al., 2014). The power is set to the maximum in Auto mode and the required load to be applied on the die is also set. Also, the z-axis position is zero and then the timer is switched on and finally, the SINTER button is pressed to start the sintering process (Guillon et al., 2014; Matizamhuka, 2016). For measuring the temperature in SPS, two types of instruments are used: a thermocouple for sintering temperatures below 1,000°C and a pyrometer for sintering temperatures over 1,000°C. As the SPS process is characterized by high heating and cooling rates (Hungria et al., 2009; Hu et al., 2020). A high DC Pulse passed between graphite electrodes and axial pressure is simultaneously applied from the beginning of the sintering cycle. The sample is heated by Joules-heating, in which the sparking among the particles of sintered material leads to a faster heat and mass transfer instantaneously. After sintering, the power is switched off, and the sample is allowed to cool (Dudina et al., 2019; Abedi et al., 2021).
2.1.4 Other fabrication techniques
In the case of pure HE-NPs, the colloidal approach is frequently employed as a precise and efficient method to produce nano-objects with regulated structure (size and shape). It is predicated on the presence of surfactants dissolved in an organic environment at a specific temperature and at the reduction of metallic precursors by a reducing agent. Equimolar CoCrFeNiMn HE-NPs have recently been produced using this colloidal method. The authors stated that the method in recent times has become a competitive method for synthesizing stable HE-NP colloids without the need for ligands to stabilize the process (Waag et al., 2019). To synthesize HE-NPs in the solid solution phase, without phase segregation like core-shell or Janus structures, the synthesis temperature specifically turned out to be important, according to Da Silva et al. (2022).
Kheradmandfard et al. (2021) studied the first high-entropy oxide (HEO) (Mg, Cu, Ni, Co, Zn) O nanoparticles using a novel ultrafast easy green microwave-assisted approach. The outcomes showed that the single-phase rocksalt structure of the HEO nanoparticles included equal amounts of all five metallic elements. The average particle size was 44 nm, while the range of particle sizes was 20–70 nm. The HEO nanoparticles showed outstanding lithium storage abilities with the impressive stability as was proved during 1,000 cycles at 1 A/g when utilized as anode materials for Li-ion batteries. With its amazing benefits, such as its ultrafast speed (few minutes), low temperature, nanoscale and high-purity products, and low cost, the approach suggested in this study is a superb synthesis methodology for use in newly developed high-entropy ceramics, especially for Li-ion batteries.
Li H. et al. (2020) effectively reviewed the various formation mechanisms and synthesis of HE-NPs with their accompanying challenges. The authors stated there are polymer-mediated methods comprising template synthetic strategies, scanning probe block copolymer lithography, and high entropy metal-organic frameworks (MOFs) while other fabrication routes are listed below.
2.1.4.1 Chemical technique
Chemical fabrication of high entropy nanomaterials includes Nanodroplet-Mediated Electrodeposition, Wet chemical technique, Dealloying and alloying process. High entropy alloys fabricated at the nanoscale using wet chemical methods are prepared in a special solution by reducing or mixing metal salts with some capping agents for the regulation of crystal aggregation and growth. Singh and Srivastava (2015) studied the fabrication and electron microscopy of HE-NPs using wet chemical synthesis. The average particle sizes of the nanomaterial were 26.7 ± 3.3 nm, and the results showed that the nanomaterial was fairly uniformly distributed with a solid solution FCC structure observed. Liu et al. (2019) also fabricated a PtAuPdRhRu HE-NPs using wet chemical synthesis with an average particle size of ˜ 3 nm, and the authors reported that the nanoparticle had high electrocatalytic activities for hydrogen evolution reactions.
The incorporation of a gas-blowing agent and transient high-temperature heating enabled for the first time by Wang et al. (2020), is a continuous “droplet-to-particle” approach of producing hollow HEA nanoparticles with homogeneous mixing of up to eight different components as shown in Figure 4. Metal chloride salts homogeneously dissolved in ethanol, together with citric acid, which serves as a blowing agent, were used to create an aerosol stream with particles as tiny as 1 m in diameter. The droplets are then conveyed by argon at a flow rate of 5 L min1 across the heating zone of a tube furnace.
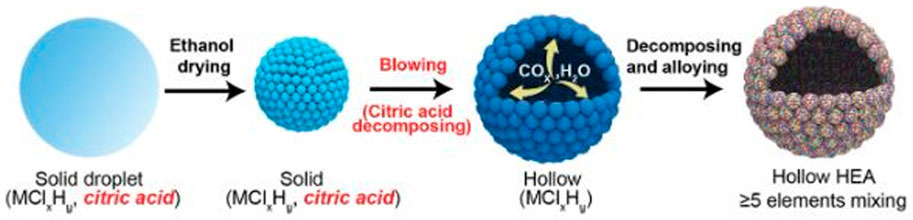
FIGURE 4. Schematic Diagram of droplet-to-particle evolution method of fabricating hollow high entropy alloy nanoparticles (Wang et al., 2020).
The nanodroplet-mediated Potentiostatic electrodeposition using electrolytes that are nonaqueous solvents for the fabrication of PtPdRhRuCe HE-NPs but similar to carbothermal-shock produces amorphous microstructures, according to Yao L. et al. (2018). The method comprises using shock metal salt, which is covered by carbon nanofibers and followed by rapid quenching to produce nanoparticles with applications in catalysis and energy storage. While dealloying and alloying chemical methods of synthesizing high entropy nanoporous materials with ligament sizes of about 3 nm contain polyelemental particle systems like Pd, Al, Co, Ni, Fe, Cu, Au and Mo (Chen et al., 2016). Chemical dealloying can also be used to fabricate High entropy nano oxides (Np-HEOs) (Qiu et al., 2019). The process adds reactants to small volumes where the size and composition can be controlled independently while forcing the reactant to form single particles comprising five or more transition metal ions using dip-pen lithography. This influences the HE-NPs to facilitate magnetic, hybrid chemical and electronic interactions for diverse applications such as plasmonic, catalysis and biological imaging (Song et al., 2021; Wang H. et al., 2022).
2.1.4.2 Nonequilibrium technique
The nonequilibrium techniques of fabricating HE-NPs include the strategies for fast-moving bed pyrolysis, electro-shock synthesis, and carbothermal shock. Carbothermal shock involves using high reaction temperature alongside fast cooling and heating rates for the formation of the HE-NPs on oxygenated carbon substances. The method is similar to vapor deposition and can create homogeneous components. Quinary HEA-NPs were synthesized on the aligned electrospun carbon nanofibers (ACNFs) based on a carbothermal shock (CTS) method by Xu et al. (2020). CTS, a quick and controllable method, is worthy to be further promoted for HEA-NPs synthesis, other methods include sol-gel combustion, mechanical grinding and laser-synthesis. The authors stated that unstable nanoparticles/carbonaceousnanomaterial synthesis results in inhomogeneous mass and charge transfer across the electrode/electrolyte interface. High-entropy alloy nanoparticles (HEA-NPs) are rarely reported in supercapacitors. They used a self-designed collector for aligned CNFs in conjunction with an appropriate CTS current direction. The FeNiCoMnMg HEA-NPs/ACNFs electrodes with a 5 mM precursor concentration exhibited excellent electrochemical performance, with a high capacitance of 203 F/g and a specific energy density of 21.7 Wh/kg. These results suggest that carbonaceous nanomaterials, such as HEA-NPs, are interesting candidates for energy storage applications.
Asanova et al. (2021) developed HE-NP by using thermal decomposition of the metal salt precursor and the results showed that in methanol oxidation, the nanomaterial possessed excellent electrocatalytic activities. Yao Y. et al. (2018) created a method for fabricating HE-NPs by shock metal salt that is covered in carbon nanofibers by thermally shocking the precursor metal salt and loading the mixtures onto carbon supports to solve the cooling rate constraints and control the particle size, composition, phase and variety of physical and chemical properties the HE-NPs present. The authors concluded that using carbothermal shock synthesis completely mixes the synthesized high entropy alloy through the precursor with several metal salts. Therefore, the process involves the assembling of metal salt precursors into a dissolved mixture and then distributing the resulting droplets in hole grooves containing carbon support by a carbon injector. Then the decomposition of the metal salt precursors follows using high reaction temperature and fast cooling and heating rates (−105 K/s).
Fast-moving bed pyrolysis for synthesizing HE-NPs comprises about ten immiscible elements such as rhodium, manganese, gold, cobalt, platinum, nickel, iridium, copper, tin, and palladium. The process with fast cooling and heating rates, and low free energy under high reactive temperature is similar to the carbothermal shock; however, compared to the Carbothermal shock process, which is divided into two stages, the fast-moving bed pyrolysis method is divided into three stages. The first stage is moving the precursors to monomers, then the second stage is moving the monomers to nuclei and finally the nuclei to nanocrystals. Gao et al. (2020) reported on the synthesis of MnCoNiCuRhPdSnIrPtAu HE-NPs using fast-moving bed pyrolysis to immobilize the nanoparticles on three granular support systems, namely,; carbon black and graphene oxide, zeolite and
On the other hand, the electro-shock method, which was accomplished by reducing the number of metal salt precursors to water nanodroplets suspended in an organic solvent, including cobalt (II) chloride (CoCl2), manganese (II) chloride (MnCl2), chromium (III) chloride (CrCl3), nickel (II) chloride (NiCl2), and vanadium trichloride (VCl3). In particular, the procedure can encourage the collision of nanodroplets with a biased electrode and facilitate the transfer of metal salt precursors to form nucleation. This procedure was utilized to demonstrate that metal salt precursors can quickly transform into HEAs with precisely controllable stoichiometric ratios using an electro-shock lasting in the range of 100 ms. For example, Glasscott et al. (2019) studied the electrosynthesis of HE-NPs. The authors used a typical nanodroplet filled with precursors of equal molar content, such as CoCl2, MnCl2, CrCl3, NiCl2, and VCl3, (resulting in a total of 40 mM of metal salt) to hit the carbon fiber ultramicroelectrodes (UMEs, radium of 4 mm). Due to UME’s microscale size, less background current was present, which made it simpler to see a nanodroplet collision. Additionally, as the metal salts in the nanodroplets were electrolyzed, the electrode’s current decreased. The amount of charge that was transferred during the reduction phase, Qred, was calculated by integrating the current vs. time curve for the blip-type response. This number is comparable to the initial charge of a nanodroplet, Qini, which was equal the total charge required to deplete every metal precursor ion.
2.2 Properties of high entropy nanomaterials (HE-NPs)
Energy storage materials and devices require conversion systems that are available when needed. These conversion systems depend on selecting the most suitable catalysts, which help increase reaction rates and storage efficiencies. Catalytic activity is not limited to the surface adsorption energy, d-band center theory, and the electronic structures for reaction intermediates and molecules, hence modifying the composition of the high entropy alloys can optimize the electronic structures and surface adsorption energy, which enhances the catalyst performance (Tomboc et al., 2020). The properties of HE-NPs for catalytic applications were experimentally characterized using different equipment, tools and software listed in Table 1.
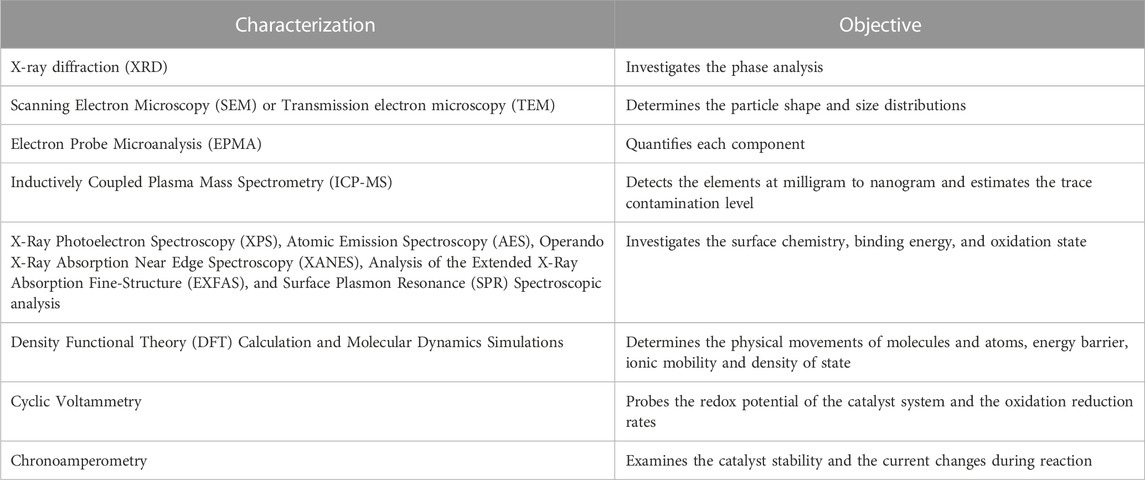
TABLE 1. Tabular Representation of Various Characterization Tools for Determining the Properties of HE-NPs for catalytic Applications.
Li H. et al. (2020) prepared a nanoporous high–performance Al96Cu1Ni1Pt1X1 high entropy where x was varied between V, Ti, Mn, Au, Co, Ir, and Mo (1 at%) using a melt-spinning technique. Composition and structural characterization were achieved using XRD, SEM, XPS, and TEM. The results of the analysis are displayed in Figure 5. The HE-NP has a bimodal porous structure with nano ligaments. A highly active Oxygen Reduction Reaction (ORR) np-AlCuNiPtMn catalyst was developed with a 0.945 V half-wave potential in an acidic media and mass activity of about 16 fold higher than benchmark Pt/C catalysts.
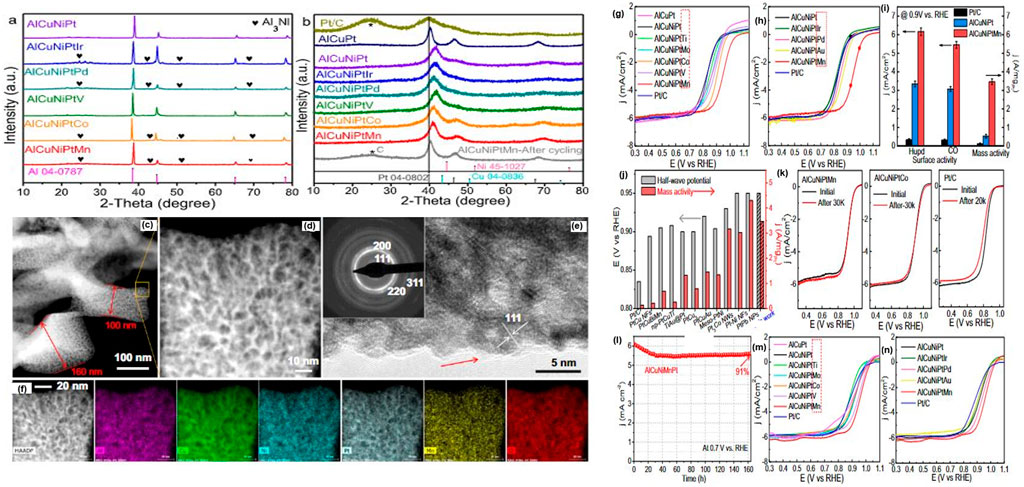
FIGURE 5. (A, B) XRD graphs of the precursor HE-NPs before and after etching in 0.5 M NaoH solution (C–F) SEM and TEM Micrographs of the np-AlCuNiPtMn HE-NP. (G–N) Oxygen Polarization curves of the HE-NPs (Li S. et al., 2020)
Qui et al. (2019) fabricated a nanoporous senary, octonary and senary all-non-noble HE-Np by dealloying the precursor alloys. The XRD, TEM and HER Polarization data presented in Figure 6 showed the HE-Np had uniformly distributed 3 nm nano-ligaments and enhanced catalytic activity with long-term durability for electrocatalysis and CO oxidation.
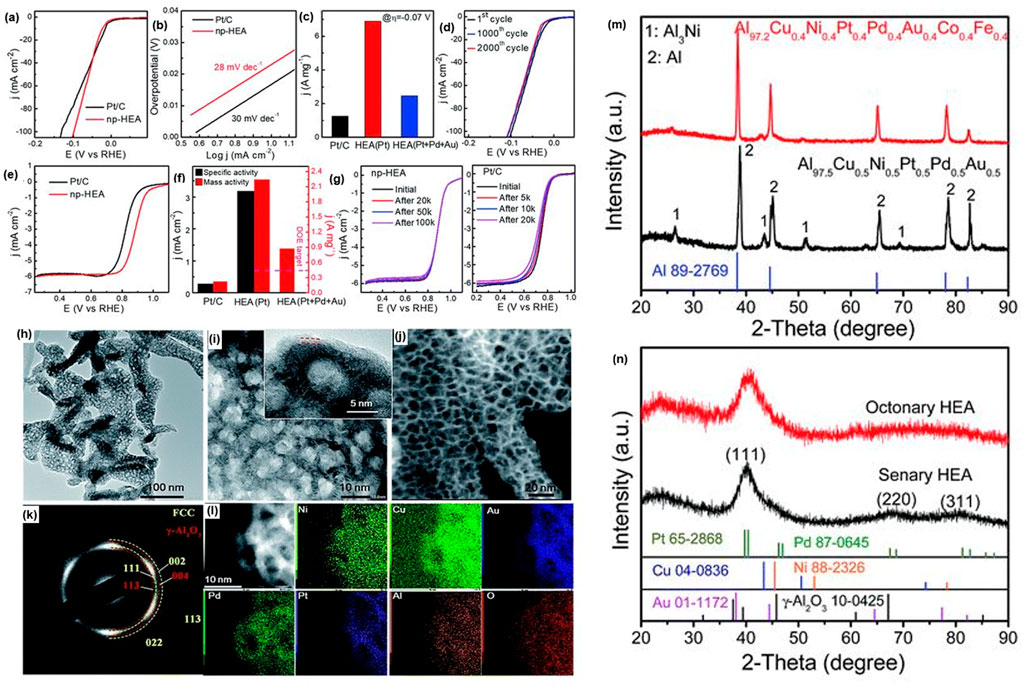
FIGURE 6. (A–G) HER Polarization curves, (H–L) TEM micrographs of the HEA-NP, (M, N) XRD graphs of the octonary and precursor senary alloy before and after dealloying in 0.5 M NaOH solution.
3 Application of high entropy nanomaterials
Although it is currently quite difficult, the creation of highly active and stable catalysts is important for the conversion of renewable energy, and the numerous elemental compositional combinations of HE-NPs offer several possibilities. Hence, due to their advantages in catalytic applications such as carbon dioxide reduction, water electrocatalysis and oxygen reduction, some newly developed catalysts based on HEAs with amazing catalytic activity, excellent product selectivity, and good durability have recently attracted a lot of research interest. To highlight the significant potentials of HEAs in the application of energy conversion, this study concentrates on discussing the catalytic conversion reactions of the hydrogen evolution reaction (HER) while just highlighting the oxygen reduction reaction (ORR), oxygen evolution reaction (OER), CO2 reduction reaction (CO2RR), and ammonia (NH3) decomposition.
3.1 Electrocatalytic hydrogen evolution reaction
There is an immediate need for the development and effective use of renewable and clean energy resources due to the widely anticipated depletion of the world’s fossil fuel reserves and the significant growth in greenhouse gas emissions and other environmental pollutions (Chen et al., 2020; Yao et al., 2021). Different approaches have been used to deal with the issues. Future changes to how we live could be influenced by one of them, the ability to store energy effectively, as well as the possibility of producing power and fuels like hydrogen using solar energy (Feng et al., 2021). Hydrogen (H2) as the most prevalent element in the Universe, is found in large quantities in water and organic substances (Zhang et al., 2021). It is a sustainable energy for solving the world’s fossil fuel and environmental pollution challenges (Lin et al., 2022). The simplest and lower energy density by volume necessitates a larger storage tank. The very low ignition temperature of the flammable gas, hydrogen, is a major contributor to the risk connected with using it. Hydrogen has an atomic mass of 1.00794 due to its small molecular size and corrosive nature (Hydrogen Council, 2020; Yu et al., 2021).
Hydrogen with one proton and one electron make up the colorless, odorless, and flammable gas, which has an atomic mass of 1.008 (rounded up). The main safety issue is that if a leak goes unnoticed, and the gas builds up in a small area, it could eventually catch fire and explode (Abe et al., 2019; Andersson and Grönkvist, 2019). Compared to hydrocarbons, hydrogen gas has a better energy density by weight, which can cause mechanical failure and leakage in some materials; it can escape through materials (Andersson and Grönkvist, 2019; Howarth and Jacobson, 2021; Kovač et al., 2021). To illustrate the most cutting-edge hydrogen generation methods, various hydrogen production paths and technologies have been explored and contrasted. The four primary categories of hydrogen production pathways in the literature are electrolysis, photolysis, biolysis, and thermolysis (Abdin et al., 2020; Dawood et al., 2020; Yue et al., 2021).
The electrocatalytic hydrogen evolution reaction has received a lot of attention as one of the most promising methods of producing artificial hydrogen (Lu et al., 2022). Due to their distinct microstructures and unheard-of physicochemical features, HE-NPs have recently gained impressive scientific attention in the hydrogen evolution reaction process (HER) (Feng et al., 2022). It is generally known that catalysts made of noble metals, such as Ru and Pt, can increase the kinetics of the HER and lower electrochemical overpotentials for very effective water spitting (Ma et al., 2020). The HE-NPs with economic transition metals have received a lot of attention in the quest to create an effective catalyst that trades off low cost and efficiency (Fan et al., 2022). Furthermore, an efficient method for analyzing interfacial reactions and electrode dynamics in the HER is through electrochemical impedance spectroscopy (EIS) and one of the main elements influencing HER kinetics is rapid electron transport (Cai et al., 2021; Wang R. et al., 2022). Jia et al. (2020) stated that for the creation of hydrogen, electrochemical water splitting offers an appealing method. However, its uses are greatly hampered by the lack of a high-performance, cost-effective electrocatalyst. In this article, a multinary high-entropy intermetallic (HEI) with multiple non-noble elements and an unusual regularly organized structure is described.
This material can act as a highly effective electrocatalyst for hydrogen evolution. With an overpotential of 88.2 mV at a current density of 10 mA cm-2 and a Tafel slope of 40.1 mV dec−1, this HEI demonstrates exceptional alkalinity activities that are equivalent to those of noble catalysts. Theoretical studies show that startling atomic configurations and chemical complexity work in synergy to change the electrical structure. Additionally, a special site-isolation effect is made possible by the distinctive L12-type ordered structure to further stabilize the H2O/H* adsorption/desorption, which significantly lowers the energy barrier of hydrogen evolution.
A unique paradigm for creating innovative electrocatalysts with enhanced reaction activity is revealed by such an HEI method. Li and Chen (2021) described the dealloying and melt-spinning method for the fabrication of FeCoNiAlTi HE-NPs for electrocatalytic hydrogen evolution reactions. The results showed that there were no elemental changes but there was homogeneity with excellent activity as HER catalyst. The nanomaterial showed a Tafel slope of 40.1 mV/dec indicating that the material is a superior electrocatalyst, keeping adequate over potentials without amplifications showing that the nanomaterial has an excellent hydrogen evolution reaction stability. The authors concluded that the FeCoNiAlTi HE-NPs is a strong potential for HER electrocatalyst attributed to their environmental friendliness, low-cost and catalytic activities.
Gao et al. (2020) mentioned that for the creation of hydrogen, electrochemical water splitting offers an appealing method. However, its uses are greatly hampered by the lack of a high-performance, cost-effective electrocatalyst. In this article, a multinary high-entropy intermetallic (HEI) with multiple non-noble elements and an unusually regularly organized structure was developed. The authors stated that the material can act as a highly effective electrocatalyst for hydrogen evolution. With an overpotential of 88.2 mV at a current density of 10 mA cm2 and a Tafel slope of 40.1 mV dec−1, this HEI demonstrates exceptional alkalinity activities that are equivalent to those of noble catalysts. Theoretical studies show that startling atomic configurations and chemical complexity work in synergy to change the electrical structure.
Zhang et al. (2018) detailed that transition metals and their alloys are projected to have significant catalytic activity for the hydrogen evolution reaction because of their partially filled d orbitals, which are suited for electron uptake and loss. However, their employment as electrocatalysts in both acidic and alkaline electrolytes is constrained by poor corrosion resistance. Here, we provide proof that the very corrosion-resistant high entropy alloy (HEA, Ni20Fe20Mo10Co35Cr15) can behave as a very stable electrocatalyst for the hydrogen evolution reaction in both basic and acidic solutions. The HEA only requires an overpotential of 107 mV in acidic solutions and 172 mV in basic solutions at current densities of 100 mA cm-2, which is significantly better than that of the dual-phase counterpart and even on par with that of the Pt sheet. The HEA only requires an overpotential of 107 mV in acidic solutions and 172 mV in basic solutions at current densities of 100 mA cm-2 for the hydrogen evolution reaction in both acidic and alkaline solutions. Which are much better than those of the dual-phase counterpart and even on par with those of Pt sheets and the majority of reported nanostructured noble-metal-free catalysts.
Intriguing electrochemical energy storage characteristics are anticipated for high entropy spinel oxides (HEO), a novel class of material stabilized by contributions from configurational entropy, according to Talluri et al. (2021). A reverse co-precipitation method was used to create the first spinel (CrMnFeCoNi)3O4 HEO nanoparticle-based supercapacitor electrode material. The phase-pure spinel structure was validated by the X-ray diffraction study. The oxidation states of the cations in spinel HEO were determined using X-ray photoelectron spectroscopy. HEO nanoparticles had a homogenous cation distribution and a smooth spherical shape, according to scanning electron microscopy and electron dispersive X-ray spectroscopy results. On the spinel HEO-based supercapacitor electrode material, electrochemical energy storage characteristics were further investigated with results showing that at a current density of 0.5 A g-1, the HEO electrode had a capacitance of 239 F g-1 and a specific energy of 24.1 Wh kg-1. From 0.5 to 25 A g-1, a rate capability of 38% was seen. After 1,000 cycles, the retention of the capacitance was found to be 76%. For 1,000 cycles, the columbic efficiency remained at 86%, showing that HEO had strong charge-discharge reversibility. HEO electrodes were discovered to have solution resistance (Rs) and charge transfer (Rct) values of 0.96 and 1.56, respectively. The use of pure spinel-type HEO nanoparticles in supercapacitor was described for the first time, providing a starting point for subsequent research into other HEOs.
4 Summary and outlook
Attributed to their high surface area, which leads to parasitic interactions with the electrolyte, especially during the first cycle, known as the first cycle irreversibility, and their tendency to aggregate, the high entropy nanomaterials are limited in energy storage devices. Therefore, future initiatives seek to develop the intelligent assembly of nanomaterials into controlled-geometry architectures. Additionally, it is important to combine nanomaterials with complementary functions, such as graphene’s high electronic conductivity or MXenes’ high operating voltage and strong redox activity of oxides. Building complex electrode topologies involve innovative manufacturing techniques, including 3D printing, spray deposition, and other methods. Devices composed of nanomaterials should be produced using already known processes such as 3D printing, roll-to-roll manufacturing, self-assembly from solutions, atomic layer deposition, and other advanced techniques. Co-sputtering from elemental or alloy targets into ionic liquids allows for the fabrication of multinary NP libraries with adjustable compositional diversity. How to increase HEA-NPs yields and separate them from ionic liquids for intended uses, however, is still a mystery and should be further investigated. Despite the potential for applications in a wide range of industries, there are still significant gaps between laboratory research and real-world engineering applications of High entropy alloys on the micro and nanoscale. While actual applications must be justified by considering a combination of several features, laboratory research concentrates on one or two fundamental properties that are important to a particular application. For instance, HE-NPs used for energy conversion applications must also have excellent strength and ductility to maintain structural integrity under difficult conditions. To close the gaps, additional application-driven or application-focused research that examines all-important qualities is needed. Benchmarking against commercial materials, if available, is another critical step in establishing the validity of HE-NPs in specific applications.
5 Conclusion
The development of high-performance high entropy nanomaterials is essential despite the advancement of current energy conversion and storage technologies and devices because it is challenging to simultaneously achieve high levels of energy conversion and adequate energy storage. To avoid the requirement for restacking, maintain a high surface area, and allow target molecules and ions to intercalate, the proper design of HE-NPs is very important. Additionally, it may be necessary to take into account the energy and environmental implications of the production of nanomaterials in addition to high entropy-based nanomaterials. Although these newly developed, HE-NPs show promise for the creation of high-performance electrocatalytic applications, there are still many obstacles to be solved.
Author contributions
DM: Conceptualization, Writing of Original draft, Review and Editing PP: Supervision, Writing of Original draft, Review and Editing.
Conflict of interest
The authors declare that the research was conducted in the absence of any commercial or financial relationships that could be construed as a potential conflict of interest.
Publisher’s note
All claims expressed in this article are solely those of the authors and do not necessarily represent those of their affiliated organizations, or those of the publisher, the editors and the reviewers. Any product that may be evaluated in this article, or claim that may be made by its manufacturer, is not guaranteed or endorsed by the publisher.
References
Abdin, Z., Zafaranloo, A., Rafiee, A., Merida, W., Lipinski, W., and Khalilpour, K. R. (2020). Hydrogen as an energy vector. Renew. Sustain. energy Rev. 120, 109620. doi:10.1016/j.rser.2019.109620
Abe, J. O., Popoola, A., Ajenifuja, E., and Popoola, O. M. (2019). Hydrogen energy, economy and storage: Review and recommendation. Int. J. Hydrogen Energy 44 (29), 15072–15086. doi:10.1016/j.ijhydene.2019.04.068
Abedi, M., Asadi, A., Vorotilo, S., and Mukasyan, A. S. (2021). A critical review on spark plasma sintering of copper and its alloys. J. Mater. Sci. 56 (36), 19739–19766. doi:10.1007/s10853-021-06556-z
Ali, N., Teixeira, J. A., Addali, A., Saeed, M., Al-Zubi, F., Sedaghat, A., et al. (2019). Deposition of stainless steel thin films: An electron beam physical vapour deposition approach. Materials 12 (4), 571. doi:10.3390/ma12040571
Andersson, J., and Grönkvist, S. (2019). Large-scale storage of hydrogen. Int. J. Hydrogen Energy 44 (23), 11901–11919. doi:10.1016/j.ijhydene.2019.03.063
Arif, Z. U., Khalid, M. Y., Ur Rehman, E., Ullah, S., Atif, M., and Tariq, A. (2021). A review on laser cladding of high-entropy alloys, their recent trends and potential applications. J. Manuf. Process. 68, 225–273. doi:10.1016/j.jmapro.2021.06.041
Asanova, T., Asanov, I., Yusenko, K., La Fontaine, C., Gerasimov, E., Zadesenets, A., et al. (2021). Time-resolved study of pd-os and pt-os nanoalloys formation through thermal decomposition of [pd (nh3) 4] [oscl6] and [pt (nh3) 4] [oscl6] complex salts. Mater. Res. Bull. 144, 111511. doi:10.1016/j.materresbull.2021.111511
Baptista, A., Silva, F., Porteiro, J., Miguez, J., Pinto, G., and Fernandes, L. (2018b). On the physical vapour deposition (pvd): Evolution of magnetron sputtering processes for industrial applications. Procedia Manuf. 17, 746–757. doi:10.1016/j.promfg.2018.10.125
Baptista, A., Silva, F., Porteiro, J., Miguez, J., and Pinto, G. (2018a). Sputtering physical vapour deposition (pvd) coatings: A critical review on process improvement and market trend demands. Coatings 8 (11), 402. doi:10.3390/coatings8110402
Benjamin, J. (1992). Fundamentals of mechanical alloying. Mater. Sci. Forum 88-90, 1–18. doi:10.4028/www.scientific.net/MSF.88-90.1
Boddu, M. R., Landers, R. G., and Liou, F. W. (2001). “Control of laser cladding for rapid prototyping--a review,” in 2001 International Solid Freeform Fabrication Symposium, Austin, Texas, August 6-8, 2001.
Cai, Z-X., Goou, H., Ito, Y., Tokunaga, T., Miyauchi, M., Abe, H., et al. (2021). Nanoporous ultra-high-entropy alloys containing fourteen elements for water splitting electrocatalysis. Chem. Sci. 12 (34), 11306–11315. doi:10.1039/d1sc01981c
Cao, B., Wang, C., Yang, T., and Liu, C. (2020). Cocktail effects in understanding the stability and properties of face-centered-cubic high-entropy alloys at ambient and cryogenic temperatures. Scr. Mater. 187, 250–255. doi:10.1016/j.scriptamat.2020.06.008
Chen, J., Zhou, X., Wang, W., Liu, B., Lv, Y., Yang, W., et al. (2018). A review on fundamental of high entropy alloys with promising high–temperature properties. J. Alloys Compd. 760, 15–30. doi:10.1016/j.jallcom.2018.05.067
Chen, P-C., Liu, X., Hedrick, J. L., Xie, Z., Wang, S., Lin, Q. Y., et al. (2016). Polyelemental nanoparticle libraries. Science 352 (6293), 1565–1569. doi:10.1126/science.aaf8402
Chen, Z., Qing, H., Zhou, K., Sun, D., and Wu, R. (2020). Metal-organic framework-derived nanocomposites for electrocatalytic hydrogen evolution reaction. Prog. Mater. Sci. 108, 100618. doi:10.1016/j.pmatsci.2019.100618
Courtney, T. H. (1995). Process modeling of mechanical alloying (overview). Mater. Trans. JIM 36 (2), 110–122. doi:10.2320/matertrans1989.36.110
Da Silva, C. M., Amara, H., Fossard, F., Girard, A., Loiseau, A., and Huc, V. (2022). Colloidal synthesis of nanoparticles: From bimetallic to high entropy alloys. Nanoscale 14 (27), 9832–9841. doi:10.1039/d2nr02478k
Dąbrowa, J., Kucza, W., Cieślak, G., Kulik, T., Danielewski, M., and Yeh, J. W. (2016). Interdiffusion in the fcc-structured al-co-cr-fe-ni high entropy alloys: Experimental studies and numerical simulations. J. Alloys Compd. 674, 455–462. doi:10.1016/j.jallcom.2016.03.046
Dawood, F., Anda, M., and Shafiullah, G. (2020). Hydrogen production for energy: An overview. Int. J. Hydrogen Energy 45 (7), 3847–3869. doi:10.1016/j.ijhydene.2019.12.059
Dudina, D. V., Bokhonov, B. B., and Olevsky, E. A. (2019). Fabrication of porous materials by spark plasma sintering: A review. Materials 12 (3), 541. doi:10.3390/ma12030541
Fan, L., Ji, Y., Wang, G., Chen, J., Chen, K., Liu, X., et al. (2022). High entropy alloy electrocatalytic electrode toward alkaline glycerol valorization coupling with acidic hydrogen production. J. Am. Chem. Soc. 144 (16), 7224–7235. doi:10.1021/jacs.1c13740
Feng, D., Dong, Y., Nie, P., Zhang, L., and Qiao, Z. A. (2022). Conicumgzn high entropy alloy nanoparticles embedded onto graphene sheets via anchoring and alloying strategy as efficient electrocatalysts for hydrogen evolution reaction. Chem. Eng. J. 430, 132883. doi:10.1016/j.cej.2021.132883
Feng, G., Ning, F., Song, J., Shang, H., Zhang, K., Ding, Z., et al. (2021). Sub-2 nm ultrasmall high-entropy alloy nanoparticles for extremely superior electrocatalytic hydrogen evolution. J. Am. Chem. Soc. 143 (41), 17117–17127. doi:10.1021/jacs.1c07643
Fu, Y., Li, J., Luo, H., Du, C., and Li, X. (2021). Recent advances on environmental corrosion behavior and mechanism of high-entropy alloys. J. Mater. Sci. Technol. 80, 217–233. doi:10.1016/j.jmst.2020.11.044
Gao, S., Hao, S., Huang, Z., Yuan, Y., Han, S., Lei, L., et al. (2020). Synthesis of high-entropy alloy nanoparticles on supports by the fast moving bed pyrolysis. Nat. Commun. 11 (1), 2016. doi:10.1038/s41467-020-15934-1
Garzón-Manjón, A., Meyer, H., Grochla, D., Loffler, T., Schuhmann, W., Ludwig, A., et al. (2018). Controlling the amorphous and crystalline state of multinary alloy nanoparticles in an ionic liquid. Nanomaterials 8 (11), 903. doi:10.3390/nano8110903
George, E. P., Curtin, W., and Tasan, C. C. (2020). High entropy alloys: A focused review of mechanical properties and deformation mechanisms. Acta Mater. 188, 435–474. doi:10.1016/j.actamat.2019.12.015
George, E. P., Raabe, D., and Ritchie, R. O. (2019). High-entropy alloys. Nat. Rev. Mater. 4 (8), 515–534. doi:10.1038/s41578-019-0121-4
Glasscott, M. W., Pendergast, A. D., Goines, S., Bishop, A. R., Hoang, A. T., Renault, C., et al. (2019). Electrosynthesis of high-entropy metallic glass nanoparticles for designer, multi-functional electrocatalysis. Nat. Commun. 10 (1), 2650–2658. doi:10.1038/s41467-019-10303-z
Guillon, O., Gonzalez-Julian, J., Dargatz, B., Kessel, T., Schierning, G., Rathel, J., et al. (2014). Field-assisted sintering technology/spark plasma sintering: Mechanisms, materials, and technology developments. Adv. Eng. Mater. 16 (7), 830–849. doi:10.1002/adem.201300409
Gupta, G., Tyagi, R., Rajput, S., Saxena, P., Vashisth, A., and Mehndiratta, S. (2021). Pvd based thin film deposition methods and characterization/property of different compositional coatings-a critical analysis. Mater. Today Proc. 38, 259–264. doi:10.1016/j.matpr.2020.07.132
Han, C., Fang, Q., Shi, Y., Tor, S. B., Chua, C. K., and Zhou, K. (2020). Recent advances on high-entropy alloys for 3d printing. Adv. Mater. 32 (26), 1903855. doi:10.1002/adma.201903855
Howarth, R. W., and Jacobson, M. Z. (2021). How green is blue hydrogen? Energy Sci. Eng. 9 (10), 1676–1687. doi:10.1002/ese3.956
Hu, J., Shen, H., Jiang, M., Gong, H., Xiao, H., Liu, Z., et al. (2019). A dft study of hydrogen storage in high-entropy alloy tizrhfscmo. Nanomaterials 9 (3), 461. doi:10.3390/nano9030461
Hu, Z-Y., Zhang, Z-H., Cheng, X-W., Wang, F. C., and Li, S. L. (2020). A review of multi-physical fields induced phenomena and effects in spark plasma sintering: Fundamentals and applications. Mater. Des. 191, 108662. doi:10.1016/j.matdes.2020.108662
Huang, E-W., and Liaw, P. K. (2019). High-temperature materials for structural applications: New perspectives on high-entropy alloys, bulk metallic glasses, and nanomaterials. MRS Bull. 44 (11), 847–853. doi:10.1557/mrs.2019.257
Hungria, T., Galy, J., and Castro, A. (2009). Spark plasma sintering as a useful technique to the nanostructuration of piezo-ferroelectric materials. Adv. Eng. Mater. 11 (8), 615–631. doi:10.1002/adem.200900052
Hussain, I., Lamiel, C., Ahmad, M., Chen, Y., Shuang, S., Javed, M. S., et al. (2021). High entropy alloys as electrode material for supercapacitors: A review. J. Energy Storage 44, 103405. doi:10.1016/j.est.2021.103405
Hydrogen Council (2020). Path to hydrogen competitiveness: A cost perspective. Belgium: Hydrogen Council.
Jia, Z., Yang, T., Sun, L., Zhao, Y., Li, W., Luan, J., et al. (2020). A novel multinary intermetallic as an active electrocatalyst for hydrogen evolution. Adv. Mater. 32 (21), 2000385. doi:10.1002/adma.202000385
Jiang, R., Da, Y., Han, X., Chen, Y., Deng, Y., and Hu, W. (2021). Ultrafast synthesis for functional nanomaterials. Cell. Rep. Phys. Sci. 2 (1), 100302. doi:10.1016/j.xcrp.2020.100302
Jien-Wei, Y. (2006). Recent progress in high entropy alloys. Ann. Chim. Sci. Mat. 31 (6), 633–648. doi:10.3166/acsm.31.633-648
Kessel, H., Hennicke, J., Kirchner, R., and Kessel, T. (2010). Rapid sintering of novel materials by fast/sps—further development to the point of an industrial production process with high cost efficiency. FCT Systeme GmbH, Geinberg, 96528.
Koch, C. (1998). Intermetallic matrix composites prepared by mechanical alloying—A review. Mater. Sci. Eng. A 244 (1), 39–48. doi:10.1016/s0921-5093(97)00824-1
Kovač, A., Paranos, M., and Marciuš, D. (2021). Hydrogen in energy transition: A review. Int. J. Hydrogen Energy 46 (16), 10016–10035. doi:10.1016/j.ijhydene.2020.11.256
Kulkarni, K., and Chauhan, G. P. S. (2015). Investigations of quaternary interdiffusion in a constituent system of high entropy alloys. AIP Adv. 5 (9), 097162. doi:10.1063/1.4931806
Li, H., Lai, J., Li, Z., and Wang, L. (2021a). Multi-sites electrocatalysis in high-entropy alloys. Adv. Funct. Mater. 31 (47), 2106715. doi:10.1002/adfm.202106715
Li, H., Zhu, H., Zhang, S., Zhang, N., Du, M., and Chai, Y. (2020a). Nano high-entropy materials: Synthesis strategies and catalytic applications. Small Struct. 1 (2), 2000033. doi:10.1002/sstr.202000033
Li, K., and Chen, W. (2021). Recent progress in high-entropy alloys for catalysts: Synthesis, applications, and prospects. Mater. Today Energy 20, 100638. doi:10.1016/j.mtener.2021.100638
Li, S., Tang, X., Jia, H., Li, H., Xie, G., Liu, X., et al. (2020b). Nanoporous high-entropy alloys with low Pt loadings for high-performance electrochemical oxygen reduction. J. Catal. 383, 164–171. doi:10.1016/j.jcat.2020.01.024
Li, W., Xie, D., Li, D., Zhang, Y., Gao, Y., and Liaw, P. K. (2021b). Mechanical behavior of high-entropy alloys. Prog. Mater. Sci. 118, 100777. doi:10.1016/j.pmatsci.2021.100777
Li, Z., Pradeep, K. G., Deng, Y., Raabe, D., and Tasan, C. C. (2016). Metastable high-entropy dual-phase alloys overcome the strength–ductility trade-off. Nature 534 (7606), 227–230. doi:10.1038/nature17981
Li, Z., Zhao, S., Ritchie, R. O., and Meyers, M. A. (2019). Mechanical properties of high-entropy alloys with emphasis on face-centered cubic alloys. Prog. Mater. Sci. 102, 296–345. doi:10.1016/j.pmatsci.2018.12.003
Lin, H. J., Lu, Y. S., Zhang, L. T., Liu, H. Z., Edalati, K., and Révész, Á. (2022). Recent advances in metastable alloys for hydrogen storage: A review. Rare Met. 41 (6), 1797–1817. doi:10.1007/s12598-021-01917-8
Liu, D., Liu, H., Ning, S., and Chu, Y. (2020). Chrysanthemum-like high-entropy diboride nanoflowers: A new class of high-entropy nanomaterials. J. Adv. Ceram. 9 (3), 339–348. doi:10.1007/s40145-020-0373-x
Liu, J., Yu, H., Chen, C., Weng, F., and Dai, J. (2017). Research and development status of laser cladding on magnesium alloys: A review. Opt. Lasers Eng. 93, 195–210. doi:10.1016/j.optlaseng.2017.02.007
Liu, M., Zhang, Z., Okejiri, F., Yang, S., Zhou, S., and Dai, S. (2019). Entropy-maximized synthesis of multimetallic nanoparticle catalysts via a ultrasonication-assisted wet chemistry method under ambient conditions. Adv. Mater. Interfaces 6 (7), 1900015. doi:10.1002/admi.201900015
Liu, Y., Ding, Y., Yang, L., Sun, R., Zhang, T., and Yang, X. (2021). Research and progress of laser cladding on engineering alloys: A review. J. Manuf. Process. 66, 341–363. doi:10.1016/j.jmapro.2021.03.061
Lu, Y., Xu, S., Zhang, L., Hu, Q., Song, J., Zhang, F., et al. (2022). The characteristics of excellent electrocatalytic hydrogen evolution for feconi based high entropy alloys. Sustain. Mater. Technol. 33, e00455. doi:10.1016/j.susmat.2022.e00455
Ma, P., Zhao, M., Zhang, L., Wang, H., Gu, J., Sun, Y., et al. (2020). Self-supported high-entropy alloy electrocatalyst for highly efficient h2 evolution in acid condition. J. Materiomics 6 (4), 736–742. doi:10.1016/j.jmat.2020.06.001
Mao, A., Ding, P., Quan, F., Zhang, T., Ran, X., Li, Y., et al. (2018). Effect of aluminum element on microstructure evolution and properties of multicomponent al-co-cr-cu-fe-ni nanoparticles. J. Alloys Compd. 735, 1167–1175. doi:10.1016/j.jallcom.2017.11.233
Marques, F., Balcerzak, M., Winkelmann, F., Zepon, G., and Felderhoff, M. (2021). Review and outlook on high-entropy alloys for hydrogen storage. Energy and Environ. Sci. 14 (10), 5191–5227. doi:10.1039/d1ee01543e
Matizamhuka, W. (2016). Spark plasma sintering (sps)-an advanced sintering technique for structural nanocomposite materials. J. South. Afr. Inst. Min. Metallurgy 116 (12), 1171–1180. doi:10.17159/2411-9717/2016/v116n12a12
Miracle, D. B., and Senkov, O. N. (2017). A critical review of high entropy alloys and related concepts. Acta Mater. 122, 448–511. doi:10.1016/j.actamat.2016.08.081
Mogale, N. F., and Matizamhuka, W. R. (2020). Spark plasma sintering of titanium aluminides: A progress review on processing, structure-property relations, alloy development and challenges. Metals 10 (8), 1080. doi:10.3390/met10081080
Moghaddam, A. O., Shaburova, N. A., Samodurova, M. N., Abdollahzadeh, A., and Trofimov, E. A. (2021). Additive manufacturing of high entropy alloys: A practical review. J. Mater. Sci. Technol. 77, 131–162. doi:10.1016/j.jmst.2020.11.029
Munir, Z., Anselmi-Tamburini, U., and Ohyanagi, M. (2006). The effect of electric field and pressure on the synthesis and consolidation of materials: A review of the spark plasma sintering method. J. Mater. Sci. 41 (3), 763–777. doi:10.1007/s10853-006-6555-2
Murty, B., and Ranganathan, S. (1998). Novel materials synthesis by mechanical alloying/milling. Int. Mater. Rev. 43 (3), 101–141. doi:10.1179/imr.1998.43.3.101
Okulov, A. V., Joo, S-H., Kim, H. S., Kato, H., and Okulov, I. V. (2020). Nanoporous high-entropy alloy by liquid metal dealloying. Metals 10 (10), 1396. doi:10.3390/met10101396
Pinto, G., Silva, F., Porteiro, J., Miguez, J., Baptista, A., and Fernandes, L. (2018). A critical review on the numerical simulation related to physical vapour deposition. Procedia Manuf. 17, 860–869. doi:10.1016/j.promfg.2018.10.138
Porodko, O., Fabián, M., Kolev, H., Lisnichuk, M., Zukalova, M., Vinarcikova, M., et al. (2022). A novel high entropy spinel-type aluminate mal2o4 (m= zn, mg, cu, co) and its lithiated oxyfluoride and oxychloride derivatives prepared by one-step mechanosynthesis. Z. für Phys. Chem. 236 (6-8), 713–726. doi:10.1515/zpch-2021-3106
Qiu, H-J., Fang, G., Gao, J., Wen, Y., Lv, J., Li, H., et al. (2019). Noble metal-free nanoporous high-entropy alloys as highly efficient electrocatalysts for oxygen evolution reaction. ACS Mater. Lett. 1 (5), 526–533. doi:10.1021/acsmaterialslett.9b00414
Reichelt, K., and Jiang, X. (1990). The preparation of thin films by physical vapour deposition methods. Thin Solid Films 191 (1), 91–126. doi:10.1016/0040-6090(90)90277-k
Saheb, N., Iqbal, Z., Khalil, A., Hakeem, A. S., Al Aqeeli, N., Laoui, T., et al. (2012). Spark plasma sintering of metals and metal matrix nanocomposites: A review. J. Nanomater. 2012, 1–13. doi:10.1155/2012/983470
Santo, L. (2008). Laser cladding of metals: A review. Int. J. Surf. Sci. Eng. 2 (5), 327–336. doi:10.1504/ijsurfse.2008.021345
Sathiyamoorthi, P., and Kim, H. S. (2022). High-entropy alloys with heterogeneous microstructure: Processing and mechanical properties. Prog. Mater. Sci. 123, 100709. doi:10.1016/j.pmatsci.2020.100709
Schneider, J. M., Rohde, S., Sproul, W. D., and Matthews, A. (2000). Recent developments in plasma assisted physical vapour deposition. J. Phys. D Appl. Phys. 33 (18), R173–R186. doi:10.1088/0022-3727/33/18/201
Schuh, B., Mendez-Martin, F., Völker, B., George, E., Clemens, H., Pippan, R., et al. (2015). Mechanical properties, microstructure and thermal stability of a nanocrystalline cocrfemnni high-entropy alloy after severe plastic deformation. Acta Mater. 96, 258–268. doi:10.1016/j.actamat.2015.06.025
Senkov, O. N., Miracle, D. B., Chaput, K. J., and Couzinie, J. P. (2018). Development and exploration of refractory high entropy alloys—A review. J. Mater. Res. 33 (19), 3092–3128. doi:10.1557/jmr.2018.153
Siddiqui, A. A., and Dubey, A. K. (2021). Recent trends in laser cladding and surface alloying. Opt. Laser Technol. 134, 106619. doi:10.1016/j.optlastec.2020.106619
Singh, M. P., and Srivastava, C. (2015). Synthesis and electron microscopy of high entropy alloy nanoparticles. Mater. Lett. 160, 419–422. doi:10.1016/j.matlet.2015.08.032
Singh, S., Goyal, D. K., Kumar, P., and Bansal, A. (2020). Laser cladding technique for erosive wear applications: A review. Mater. Res. Express 7 (1), 012007. doi:10.1088/2053-1591/ab6894
Song, J-Y., Kim, C., Kim, M., Cho, K. M., Gereige, I., Jung, W. B., et al. (2021). Generation of high-density nanoparticles in the carbothermal shock method. Sci. Adv. 7 (48), eabk2984. doi:10.1126/sciadv.abk2984
Stepanov, N., Yurchenko, N. Y., Zherebtsov, S., Tikhonovsky, M., and Salishchev, G. (2018). Aging behavior of the hfnbtatizr high entropy alloy. Mater. Lett. 211, 87–90. doi:10.1016/j.matlet.2017.09.094
Stuart, B. W., and Stan, G. E. (2021). Physical vapour deposited biomedical coatings. Coatings 11, 619. doi:10.3390/coatings11060619
Sun, L., Yuan, G., Gao, L., Yang, J., Chhowalla, M., Gharahcheshmeh, M. H., et al. (2021). Chemical vapour deposition. Nat. Rev. Methods Prim. 1 (1), 5–20. doi:10.1038/s43586-020-00005-y
Sundaresan, R., and Froes, F. (1987). Mechanical alloying. Jom 39 (8), 22–27. doi:10.1007/bf03258604
Suryanarayana, C. (2001). Mechanical alloying and milling. Prog. Mater. Sci. 46 (1-2), 1–184. doi:10.1016/s0079-6425(99)00010-9
Suryanarayana, C. (2019). Mechanical alloying: A novel technique to synthesize advanced materials. Research 2019, 4219812. doi:10.34133/2019/4219812
Taha, M. A., Youness, R. A., and Zawrah, M. F. (2019). Review on nanocomposites fabricated by mechanical alloying. Int. J. Minerals, Metallurgy, Mater. 26 (9), 1047–1058. doi:10.1007/s12613-019-1827-4
Talluri, B., Aparna, M. L., Sreenivasulu, N., Bhattacharya, S. S., and Thomas, T. (2021). High entropy spinel metal oxide (CoCrFeMnNi) 3O4 nanoparticles as a high-performance supercapacitor electrode material. J. Energy Storage 42, 103004. doi:10.1016/j.est.2021.103004
Tamanna, N., Crouch, R., and Naher, S. (2019). Progress in numerical simulation of the laser cladding process. Opt. Lasers Eng. 122, 151–163. doi:10.1016/j.optlaseng.2019.05.026
Tomboc, G. M., Kwon, T., Joo, J., and Lee, K. (2020). High entropy alloy electrocatalysts: A critical assessment of fabrication and performance. J. Mater. Chem. A 8 (30), 14844–14862. doi:10.1039/d0ta05176d
Tomilin, I., and Kaloshkin, S. (2015). High entropy alloys’—‘semi-impossible’regular solid solutions? Mater. Sci. Technol. 31 (10), 1231–1234. doi:10.1179/1743284715y.0000000028
Tsai, K-Y., Tsai, M-H., and Yeh, J-W. (2013). Sluggish diffusion in co–cr–fe–mn–ni high-entropy alloys. Acta Mater. 61 (13), 4887–4897. doi:10.1016/j.actamat.2013.04.058
Vaidya, M., Muralikrishna, G. M., and Murty, B. S. (2019). High-entropy alloys by mechanical alloying: A review. J. Mater. Res. 34 (5), 664–686. doi:10.1557/jmr.2019.37
Verma, V., Tripathi, A., and Kulkarni, K. N. (2017). On interdiffusion in fenicocrmn high entropy alloy. J. Phase Equilibria Diffusion 38 (4), 445–456. doi:10.1007/s11669-017-0579-y
Vu, T. D., Chen, Z., Zeng, X., Jiang, M., Liu, S., Gao, Y., et al. (2019). Physical vapour deposition of vanadium dioxide for thermochromic smart window applications. J. Mater. Chem. C 7 (8), 2121–2145. doi:10.1039/c8tc05014g
Waag, F., Li, Y., Ziefuß, A. R., Bertin, E., Kamp, M., Duppel, V., et al. (2019). Kinetically-controlled laser-synthesis of colloidal high-entropy alloy nanoparticles. RSC Adv. 9 (32), 18547–18558. doi:10.1039/c9ra03254a
Wang, H., Wang, H., Zhang, S., Zhang, Y., Xia, K., Yin, Z., et al. (2022a). Carbothermal shock enabled facile and fast growth of carbon nanotubes in a second. Nano Res. 15 (3), 2576–2581. doi:10.1007/s12274-021-3762-8
Wang, K-L., Zhu, Y-M., Zhang, Q-B., and Sun, M. L. (1997). Effect of rare Earth cerium on the microstructure and corrosion resistance of laser cladded nickel-base alloy coatings. J. Mater. Process. Technol. 63 (1-3), 563–567. doi:10.1016/s0924-0136(96)02684-2
Wang, Q., Wang, W., Li, Y., Tan, L., and Yang, K. (2021a). Biofunctional magnesium coating of implant materials by physical vapour deposition. Biomater. Transl. 2 (3), 248–256. doi:10.12336/biomatertransl.2021.03.007
Wang, R., Huang, J., Zhang, X., Zhang, Z., Gao, T., Xu, L., et al. (2022b). Two-dimensional high-entropy metal phosphorus trichalcogenides for enhanced hydrogen evolution reaction. ACS Nano 16 (3), 3593–3603. doi:10.1021/acsnano.2c01064
Wang, X., Guo, W., and Fu, Y. (2021b). High-entropy alloys: Emerging materials for advanced functional applications. J. Mater. Chem. A 9 (2), 663–701. doi:10.1039/d0ta09601f
Wang, X., Dong, Q., Qiao, H., Huang, Z., Saray, M. T., Zhong, G., et al. (2020). Continuous synthesis of hollow high-entropy nanoparticles for energy and catalysis applications. Adv. Mater. 32 (46), 2002853. doi:10.1002/adma.202002853
Wang, Z., Guo, S., and Liu, C. T. (2014). Phase selection in high-entropy alloys: From nonequilibrium to equilibrium. Jom 66 (10), 1966–1972. doi:10.1007/s11837-014-0953-8
Weng, F., Chen, C., and Yu, H. (2014). Research status of laser cladding on titanium and its alloys: A review. Mater. Des. 58, 412–425. doi:10.1016/j.matdes.2014.01.077
Xu, X., Du, Y., Wang, C., Guo, Y., Zou, J., Zhou, K., et al. (2020). High-entropy alloy nanoparticles on aligned electronspun carbon nanofibers for supercapacitors. J. Alloys Compd. 822, 153642. doi:10.1016/j.jallcom.2020.153642
Yan, W., Jiang, H., Yi, W., Zhao, C., Xia, Y., Cong, H., et al. (2022). High-entropy-alloy nanoparticles synthesized by laser metallurgy using a multivariate MOF. Mater. Chem. Front. 6, 2796–2802. doi:10.1039/d2qm00588c
Yang, T., Zhao, Y., Tong, Y., Jiao, Z. B., Wei, J., Cai, J. X., et al. (2018). Multicomponent intermetallic nanoparticles and superb mechanical behaviors of complex alloys. Science 362 (6417), 933–937. doi:10.1126/science.aas8815
Yao, L., Wu, Q., Zhang, P., Zhang, J., Wang, D., Li, Y., et al. (2018a). Scalable 2d hierarchical porous carbon nanosheets for flexible supercapacitors with ultrahigh energy density. Adv. Mater. 30 (11), 1706054. doi:10.1002/adma.201706054
Yao, R. Q., Zhou, Y. T., Shi, H., Wan, W., Zhang, Q., Gu, L., et al. (2021). Nanoporous surface high-entropy alloys as highly efficient multisite electrocatalysts for nonacidic hydrogen evolution reaction. Adv. Funct. Mater. 31 (10), 2009613. doi:10.1002/adfm.202009613
Yao, Y., Huang, Z., Xie, P., Lacey, S. D., Jacob, R. J., Xie, H., et al. (2018b). Carbothermal shock synthesis of high-entropy-alloy nanoparticles. Science 359 (6383), 1489–1494. doi:10.1126/science.aan5412
Yu, M., Wang, K., and Vredenburg, H. (2021). Insights into low-carbon hydrogen production methods: Green, blue and aqua hydrogen. Int. J. Hydrogen Energy 46 (41), 21261–21273. doi:10.1016/j.ijhydene.2021.04.016
Yue, M., Lambert, H., Pahon, E., Roche, R., Jemei, S., and Hissel, D. (2021). Hydrogen energy systems: A critical review of technologies, applications, trends and challenges. Renew. Sustain. energy Rev. 146, 111180. doi:10.1016/j.rser.2021.111180
Yurlova, M., Demenyuk, V., Lebedeva, L. Y., Dudina, D. V., Grigoryev, E. G., and Olevsky, E. A. (2014). Electric pulse consolidation: An alternative to spark plasma sintering. J. Mater. Sci. 49 (3), 952–985. doi:10.1007/s10853-013-7805-8
Zhang, D., Shi, Y., Zhao, H., Qi, W., Chen, X., Zhan, T., et al. (2021). The facile oil-phase synthesis of a multi-site synergistic high-entropy alloy to promote the alkaline hydrogen evolution reaction. J. Mater. Chem. A 9 (2), 889–893. doi:10.1039/d0ta10574k
Zhang, G., Ming, K., Kang, J., Huang, Q., Zhang, Z., Zheng, X., et al. (2018). High entropy alloy as a highly active and stable electrocatalyst for hydrogen evolution reaction. Electrochimica Acta 279, 19–23. doi:10.1016/j.electacta.2018.05.035
Zhang, H., Pan, Y., and He, Y-Z. (2011). Synthesis and characterization of feconicrcu high-entropy alloy coating by laser cladding. Mater. Des. 32 (4), 1910–1915. doi:10.1016/j.matdes.2010.12.001
Zhivulin, V. E., Trofimov, E. A., Gudkova, S. A., Pashkeev, I. Y., Punda, A. Y., Gavrilyak, M., et al. (2021). Polysubstituted high-entropy [land](cr0. 2mn0. 2fe0. 2co0. 2ni0. 2) o3 perovskites: Correlation of the electrical and magnetic properties. Nanomaterials 11 (4), 1014. doi:10.3390/nano11041014
Keywords: high entropy alloys, energy storage applications, nanomaterials, catalysis, energy
Citation: Modupeola D and Popoola P (2023) High entropy nanomaterials for energy storage and catalysis applications. Front. Energy Res. 11:1149446. doi: 10.3389/fenrg.2023.1149446
Received: 21 January 2023; Accepted: 08 March 2023;
Published: 20 March 2023.
Edited by:
Sunday Olayinka Oyedepo, Covenant University, NigeriaReviewed by:
Huai-Jun Lin, Jinan University, ChinaTolutope Oluwasegun Siyanbola, Covenant University, Nigeria
Copyright © 2023 Modupeola and Popoola. This is an open-access article distributed under the terms of the Creative Commons Attribution License (CC BY). The use, distribution or reproduction in other forums is permitted, provided the original author(s) and the copyright owner(s) are credited and that the original publication in this journal is cited, in accordance with accepted academic practice. No use, distribution or reproduction is permitted which does not comply with these terms.
*Correspondence: Dada Modupeola, ZGFkYWR1cGVvbGFAZ21haWwuY29t; Patricia Popoola, cG9wcG9sYUFQSUB0dXQuYWMuemE=